Soft robots built for extreme environments
Abstract
Soft material robots are uniquely suited to address engineering challenges in extreme environments in new ways that traditional rigid robot embodiments cannot. Soft robot material flexibility, resistance to brittle fracture, low thermal conductivity, biostability, and self-healing capabilities present new solutions advantageous to specific environmental conditions. In this review, we examine the requirements for building and operating soft robots in various extreme environments, including within the human body, underwater, outer space, search and rescue sites, and confined spaces. We analyze the implementations of soft robotic devices, including actuators and sensors, which meet these requirements. Besides the structure of these devices, we explore ways to expand the use of soft robots in extreme environments with design optimization, control systems, and their future applications in educational and commercial products. We further discuss the current limitations of soft robots recognizing challenges to compliance, strength, and control. With this in mind, we present arguments for the future of robotics in which hybrid (rigid and soft) structures meet complex environmental needs.
Keywords
INTRODUCTION
Robotic systems are widely used in industrial settings such as manufacturing[1], construction[2], retail[3], agriculture[4], and healthcare[5]. Robots can improve product quality, reduce labor costs, and, most importantly, increase human safety in hazardous industrial settings[6]. Robotic systems can carry out inspection and monitoring on job sites as they allow for terrain navigation, automated detection of defects, and data acquisition[7]. These systems reduce the risk of human injury caused by heavy equipment or hazardous materials, including chemicals or industrial waste[8]. Robotic devices can improve healthcare via efficient drug delivery[9], minimally invasive surgeries[10], and rehabilitation wearables[11]. Robots can reduce risks to humans and improve performance in complex or otherwise unsafe environments. In this paper, we explore the advantages of considering the material composition of robots, specifically soft materials, when designing for tasks in extreme environments.
The field of soft robotics research has rapidly evolved in the last decades after pioneering works in the 1990s through the early 2010s[12]. However, pneumatic soft actuators were first introduced in 1950 when McKibben developed a soft braided actuator for an orthotic appliance[13]. McKibbens muscles[14], otherwise called pneumatic artificial muscle (PAM) actuators, consist of a mesh-constrained elastomeric bladder that increases longitudinal stiffness to expand radially and contract linearly[15]. More generally, soft robots are composed of low-modulus materials including polymers, elastomers, or gels[16]. These materials provide flexibility[17], resistance to brittle fracture[18], biostability[19], and self-healing capabilities[19]. These properties allow soft robot structures to withstand highly variable conditions and may fill performance gaps that traditional machines cannot accommodate.
In this paper, we aim to compare the utility of soft robots in specific environments to more traditional, rigid robots (Section “COMPARING RIGID AND SOFT ROBOT PROPERTIES”). This review will outline current state-of-the-art soft robotic actuators, accompanying sensors, and control methods for operation specifically within challenging environments [Figure 1]. These environments include the human body (Section “SOFT ROBOTS INSIDE THE HUMAN BODY”), marine environments (Section “SOFT ROBOTS FOR MARINE ENVIRONMENTS”), space exploration (Section “SOFT ROBOTS FOR SPACE EXPLORATION”), and search and rescue sites including confined spaces (Section “SOFT ROBOTS FOR SEARCH, RESCUE, AND CONFINED SPACES”). Design methods using topology optimization, control system strategies, and considerations for end users of potential commercial and educational products represent areas of growth in soft robotics research (Section “EXPANDING THE USE OF SOFT ROBOTS IN EXTREME ENVIRONMENTS”). Altogether, this review presents strategies for developing robotic devices in extreme environments and opportunities for the future of this field.
Figure 1. This review focuses on the challenges and opportunities of engineering soft actuators and soft sensors in extreme environments including inside the human body[20], marine exploration[21], space exploration[22], and search, rescue, and confined spaces[23]. [Images are licensed under CC BY 4.0. http://creativecommons.org/licenses/by/4.0/].
COMPARING RIGID AND SOFT ROBOT PROPERTIES
Rigid and soft robots have properties that make them effective in different environments. Traditional robotic systems have decades of development to support their application in many fields. Control systems for rigid robots can be programmed to perform multiple actions and can be accurately modeled through kinematic and dynamic models[24]. Soft robots have been developed for impact resistance which makes them advantageous for more unpredictable environments[25]. However, most soft robotic actuators require changes to the structure of the actuator to perform different actions[26]. This is because soft actuators usually perform a single action and need to be constructed with multiple parts to perform more than one type of motion[26]. The control and modeling of soft robots are challenging as these structures consist of nonlinear systems that are challenging to represent mathematically due to material nonlinearities[27]. In terms of physical strength, soft robots are prone to buckling due to their soft material composition which may prevent them from carrying heavy loads[26]. Thus, rigid robots may be more advantageous when precise motions or the ability to lift heavy loads are required. Soft robots also have limitations regarding actuation speed and accuracy depending on the material and actuator type. Despite these limitations, soft robotics research is rapidly evolving, and new structures continually improve upon these shortcomings. Table 1 summarizes these benefits by comparing the advantages of soft and rigid materials for applications requiring flexibility, resistance to brittle failure, thermal insulation, biocompatibility, and self-healing capabilities in extreme environments.
Summary of benefits of properties of soft materials over traditional rigid materials in devices for certain applications in extreme environments
Property and desired quality | Soft materials | Rigid materials |
Flexibility and elasticity: Low Young’s modulus | (Silicone elastomer, PDMS, rubber, low-density polyethylene) E = 104 to 109 Pa[28] | Metals or hard plastics E = 109 to 1012 Pa[28] |
Resistance to brittle failure: high ductility | Silicone rubber: 80% to 530%[29] | Al: 65%, Fe: 43%[30] |
Lightweight: low density | SR-1610, Douglas and Sturgess 1.15 g/cm3; Dragon skin, Smooth-On 1.08 g/cm3; Ecoflex 00-10, Smooth-On 1.03 g/cm3; HS-IV, Dow Corning 1.11 g/cm3; Candle Gel, Endless Possibilities 0.98 g/cm3; Tin-Sil, US Composites 1.07 g/cm3; Semicosil 921, Wacker Solution 1.10 g/cm3; 8116SS plastic, M-F Manufacturing 0.99 g/cm3; CF11, Nusil Technologies 1.04 g/cm3[31] | Steel 7.8 g/cm3, iron 7.9 g/cm3, aluminum 2.7 g/cm3, copper 8.9 g/cm3, brass 8.5 g/cm3[32] |
Thermal insulation: low conductivity | Silicone rubber: 0.06 to 6.5 W/mK[33] | Al: 210 W/mK, Fe: 76.2 W/mK, high carbon steel: 19-52 W/mK, low carbon steel: 25.3-93 W/mK, stainless steel: 10-34.3 W/mK[34-38] |
Biocompatibility | Natural protein-based materials such as gelatin can help with biointegration and are absorbable[39]. Coating surfaces with polymeric biomaterials can enhance cellular attachment[40]. Silicone rubber has excellent biocompatibility[41] | Ti alloys can be biocompatible[42]. Generally, corrosion of metallic implants may jeopardize the mechanical stability of the device and the integrity of surrounding tissue. Metal traces can disturb homeostasis[42] |
Self-healing ability | Self-healing damages that occur during operation can extend service life by (a) creating reversible crosslinks in thermoplastics and (b) introducing healing agents into cracks | - |
Pneumatic and hydraulic-driven soft actuators composed of elastomeric materials can withstand compressive loads and enable impact absorption due to their deformable structure[25]. Durability and puncture resistance can be further enhanced in elastomeric composites with fiber or fabric reinforcements[43]. Fabric-reinforced composite materials allow for tunable mechanical properties including improved tear and puncture resistance in pneumatic networks[43]. Flexible and deformable material compositions enable bending, torsion, expansion, and contraction motions in soft robots[44]. Soft robotic systems are commonly fabricated from materials with an elastic modulus, E, ranging from 104 to 109 Pa, providing flexibility compared to rigid robots, which comprise materials with elastic moduli within 109 to 1012 Pa[28].
Soft robots also offer unique qualities including extrinsic or intrinsic self-healing properties, making them beneficial for operations in unpredictable environments. Extrinsic self-healing materials consist of healing agents added to a base material while intrinsic self-healing materials have inherent healing capabilities. Materials with intrinsic healing characteristics have dynamic covalent interactions where covalent bonds can break and reform[45]. These covalent bonds are strong (150-550 kilojoules per mole). Due to high bond strengths, these self-healing materials usually require external stimuli (heat or light) to activate their healing characteristics[45]. Self-healing polymers with mechano-reversible bonds can form after breakage by the rebinding reactive functional groups[45]. Other self-healing soft robots have been implemented using polymer networks that employ a thermoreversible Diers-Alder reaction to re-form after damage due to sharp objects or overloading[45]. Cheng et al. proposed a self-healing dielectric elastomer actuator (DEA)-driven soft robot that operates on land and in water[46]. The ion-to-dipole interactions between the charge carriers and the fluorinated polymer matrix within the ionic electrode of the DEA allow the electrode to self-heal from damage in aqueous or dry land environments. Kashef Tabrizian et al. propose a soft actuator that comprises shape memory alloy (SMA) wire reinforcements within a castor oil-based self-healing polymer able to heal large incisions. Diers-Alder covalent bonds and weak hydrogen interactions relink and enable the restoration of damaged material surfaces[47]. The ability of soft robots to withstand impact from external forces provides advantages that increase their operational life.
Soft robots can not only operate despite external disturbances but also use these conditions to their advantage. The integration of soft materials to build robotic systems has enabled the development of new actuation and sensing techniques that leverage environmental conditions to function. Environmental inputs for soft robots range from pressure[48], chemical[49], electrical[50], and magnet-driven systems[51] to temperature[52], acoustics[53], and light[54] [Table 2].
Summary of soft robot actuation mechanisms and their application examples in extreme environments
Actuation mechanism | Description | Examples in extreme environments |
Magnetics![]() | Uses variations in magnetic fields to actuate. Materials: ferrogels, ferromagnetic particles, iron-based alloys, nickel-based alloys, and iron-oxide nanoparticles (magnetite)[55] | Body: magnetic hydrogels for tissue engineering[56] and drug delivery[56] Marine: untethered swimming soft bots composed of magnetic sheets[57] Space: a growing robot for antenna applications[58] Search, rescue, and confined spaces: magnetics-driven jumping soft robot[59] |
Electrics![]() | Uses variations in electric fields to actuate. Materials: DEAs[60], hydrogels, liquid metals, conductive polymers, IPMC, SMP, dielectric fluids, and nanoparticles[61] | Body: DEAs for artificial muscles[62] Marine: DEA-based soft fish robot[63], hydrogel stingray bot[64], and IPMC manta ray[65] Space: DEA soft robotic arm[66] Search, rescue, and confined spaces: micro IPMC actuators for pipe applications[67] |
Light![]() | Uses different sources of light to actuate or perform different motions. Materials: photoactive LCP and hydrogels[68] | Body: PDMS in drug delivery[69] Marine: PDMS composite fish bot with nIR light irradiation stimulation[69], UV-driven LCP bots[70] Space: crawl, squeeze, and jump bots[71] Search, rescue, and confined spaces: climbing light-driven soft robot[72] |
Chemical![]() | Uses chemicals to actuate or perform different motions. Include variations in pH levels as well as combustion reactions. Materials: pH-responsive hydrogels[73], pH-responsive polymers[74], pH-responsive nanoparticles[75], nitrous oxide, propane, methane, and butane for combustion reactions[76] | Body: pH-responsive hydrogel for drug delivery[75], pH-responsive polymers for cancer imaging and therapy[77] Marine: combustion-driven underwater jumping robot[78] Space: combustion-driven robot that can jump using butane and oxygen[22] Search, rescue, and confined spaces: combustion-driven jumping bot using butane and oxygen[79] |
Temperature![]() | Uses variations in temperature levels to perform different motions. Materials: supramolecular hydrogels[80] and thermoresponsive polymers[81] such as SMP | Body: temperature-responsive hydrogels for drug delivery applications[82] Marine: SMA octopus robotic arm bending[83] Space: SMP planetary exploration bot[84] Search, rescue, and confined spaces: programmable thermal actuator crawling bot[85] |
Acoustics![]() | Uses variations in sound frequencies to actuate[53] | Body: ultrasound robots navigate mouse brain[53] Marine: fish bot for underwater exploration[86] Search, rescue, and confined spaces: ultrasound actuators for ultrasound imaging applications[87] |
Pressure![]() | Uses variations in pressure to actuate or perform different motions. These systems include pneumatically driven and hydraulically driven systems. Materials: elastomeric polymers (silicone, PDMS)[88] | Body: PAM cardiac sleeve[89], hydraulic endoscope[90] Marine: underwater fauna collection bellows-type grippers[91] Space: deployable and storable pneumatic arm[92] Search, rescue, and confined spaces: soft vine robot[93] and growing soft robot[94] |
Recent developments in soft robotics have focused on design techniques that prioritize optimization and efficiency. Several soft robot designs are implemented through bio-inspiration and bio-mimicry[95] including locomotion, such as crawling, jumping, aerial motion, and swimming. These actuation mechanisms are inspired by biological organisms including worms, aquatic creatures, and animals that can perform these motions.
New soft robot design developments that increase sustainability have also been explored. For example, using sustainable materials and resources such as biomaterial elastomers and solar power may help reduce the ecological footprint of soft robots[96]. Biodegradable materials can be used in implantable devices or seawater applications. These materials include biodegradable polyurethanes, polyesters, hydrogels, and gelatin-based gels[96]. Fabrication techniques including additive manufacturing also reduce waste. Three-dimensional (3D) printing methods including fused deposition modeling, direct ink writing, selective laser sintering, inkjet, and digital light processing[97] have been explored. These techniques enable the design of complex multi-material structures with limited material waste[97].
Sensing mechanisms have recently been demonstrated to monitor and detect the shape and position of soft robots and the surrounding environment[98]. These methods range from adding resistive, capacitive, and optical sensors[98] to triboelectric nanogenerators[99]. Hegde et al. describe multimodal sensor systems created for soft robotic applications such as temperature sensing and tactile force sensing networks[98]. The modeling and control of soft robots have also seen new developments. Several models including continuum mechanics models, using finite element method (FEM) techniques for 3D continuum models, geometric models, and discrete models, have been implemented to mathematically represent the structure and motions of soft robots[100]. Other soft robot control system implementations include bistable systems, which create soft logic modules eliminating the need for external rigid components[101]. These new advances in design, sensing, and control allow soft robots to become more efficient for use in extreme environments.
Each environment discussed in this paper presents unique design challenges and opportunities. For example, the human body is a complex mechanochemical environment as tissues and organs have physical characteristics such as viscoelastic properties, stiffnesses, and structures that vary widely[102]. Even the development of wearable devices, worn outside the body, presents challenges such as comfort and safety, which are discussed at length in another review paper[103]. The benefit of using soft materials in implantable devices is that mechanical properties can be tuned to compliance-match human tissues. This can prevent immune responses and rejection internally with the potential to biodegrade after use[104]. Engineering in marine environments is challenging because of the need to withstand high pressure and salinized fluids during deep ocean exploration[105]. Soft robots are beneficial in underwater environments due to their soft structures which reduce disruptions to marine life. Hydraulic actuation mechanisms can reduce the pressure differential in devices and aid in underwater locomotion[106]. Space is a challenging ultrahigh vacuum environment with high-energy particles and radiation. Significant pressure differences in space compared to the atmospheric pressure on Earth can influence the structural integrity of robots[22]. Soft robots may be useful for space exploration due to their durability in extreme temperatures and their ability to deploy from a small size. Finally, confined spaces that necessitate navigation through narrow areas and obstructions such as debris, and collapsed structures pose a danger to humans conducting search, rescue, and inspections[107]. Soft robots allow for increased mobility and adaptability on obstructed surfaces and enclosed spaces due to their size, flexibility, and unique locomotion techniques [108]. For these reasons, the use of soft robots in these environments is explored.
SOFT ROBOTS INSIDE THE HUMAN BODY
The human body is a dynamic environment of systems responsible for coordinated biological functions. About 55%-60% of human body weight consists of fluid including water[109] blood, interstitial fluids, and gastric acid[110]. These fluids have viscosities, densities, and pH levels that must be maintained for homeostasis[111]. Contamination of body fluids upon contact with heavy metals or other harmful materials can result in infections and illnesses such as heavy metal poisoning[112]. Additionally, the internal temperature of the human body must be regulated at 36.1 to 37.8 °C[113]. The gut microenvironment consists of microbiomes and bacteria used for digestion and preventing diseases[114]. Gut bacteria help digest dietary fiber and cellulose, provide vitamins, and destroy toxins[115]. However, unwanted bacteria can cause disease due to dysbiosis after antibiotic treatment or surgery[115]. Maintaining the biological microenvironment surrounding implanted devices helps prevent negative impacts on homeostasis.
Implantable robotic devices include assistive devices[116], minimally invasive surgical tools[117], and drug delivery vehicles[118]. They are designed to (1) avoid inflammatory responses due to contact between the device and biological fluids, which can lead to thromboembolism; (2) leverage biocompatible and biodegradable materials; and (3) have a high safety factor by being reliable and durable for long periods[104]. Soft robots can largely meet these requirements as they are often designed to mimic biological functions using biocompatible materials with stiffnesses similar to human tissues[104]. While the human body is a highly complex environment, we see (1) infection reduction; (2) compliance matching; and (3) biocompatibility as ways in which soft robots can address engineering challenges in the body.
Embodiments of soft actuators in vivo
Shifting material composition from metals to soft elastomers and hydrogels is the most distinct difference between traditional rigid and soft robots. Silicone rubbers are commonly used to build soft robots given their robust elastomeric material properties[119]. Silicone is stable at low and high operating temperatures (> 150 °C[120]), in different oxidation states, in water and chemicals, and is an electrical insulator[121]. Silicone elastomers have similar mechanical properties to human muscles[122]. However, silicone can elicit a harmful immune response when implanted for long periods[123]. Biocompatibility and biodegradability of soft material chemistry are vital for the long-term stability of implantable devices.
Hydrogel actuators are widely used for building biomedical devices[124]. Hydrogels have high water content leading to swelling and deswelling responses which is useful for soft actuator function[125]. Hydrogel materials can be stimulated by various inputs including environmental parameters such as pH, temperature, light, humidity, and electricity[126]. These materials have low thermal conductivities and can be used for devices where thermal insulation and regulation of body temperatures are required[127]. For instance, polyacrylamide hydrogels composed of 88 wt% water have a thermal conductivity of 0.57 ±
Silicone fluid pressure-driven soft actuators have long been used in implantable assistive devices and wearables[131]. Movements induced by pneumatic actuation, such as bending, twisting, and expansion, can be achieved by mechanical programming using fiber reinforcements[132]. PAM actuators have a large specific power of about 10 kW/kg[133] and similar energy efficiency to human muscle[133]. Specifically, muscles have an efficiency of about 40% while PAMs have an efficiency of about 49%. PAMs can be used to mimic the contractile motion of the heart[89] in indirect cardiac compression [134] [Figure 2A] and ventricular assistive devices[135] [Figure 2B]. Hu et al. designed a PAM-based device to support diaphragm function using biocompatible polyurethane composites [Figure 2C][136]. As a pneumatic actuator, PAMs usually have high payloads but may suffer from noise and poor power consumption performance[137]. However, they can recapitulate biological functions allowing soft robotic devices to safely integrate with the body by conforming to organ surfaces and preventing disturbances to other biological processes.
Figure 2. Use of PAMs in implantable soft robots. (A) Soft pneumatic cardiac sleeve to aid with cardiac compression for heart failure[134]; (B) Soft ventricular assist device composed of McKibbens actuators to aid in left ventricle contraction[135]; (C) PAM diaphragm to help the contraction of the diaphragm for respiratory issues[136]. [Images (A-C) are licensed under CC BY 4.0. http://creativecommons.org/licenses/by/4.0/.] PAMs: Pneumatic artificial muscles.
Hydraulic actuators use fluid pressure[138] and mechanical programming to perform similar movements to PAMs[138] but can generate higher output forces[139]. Hydraulic actuators can be seamlessly added to endoscopes that typically have fluid lines attached[140]. Traditional endoscopes require frequent maintenance and complex sterilization processes. Hydraulic-based actuators may reduce these issues with low-cost material composition[90]. A hydraulically actuated endoscope for gastric screening includes water-jet actuators to enhance the bending motion for improved imaging[90]. Thus, hydraulic actuators used in endoscopes can facilitate better imaging, earlier disease detection, and safer endoscopy for patients[90].
In addition to implantable devices, research into drug delivery vehicles and minimally invasive surgical tools using soft materials devices has been sustained because of the promise of early detection and treatment of disease. Soft material microtools can be actuated by temperature gradients[52], magnetic fields[51], chemical reactions[49], acoustic fields[53], or electrical signals[50]. Untethered microrobot designs can navigate through vascular systems, adhere to soft tissues, and deliver site-specific drugs[141]. These can be fabricated from thermally responsive materials such as poly(N-isopropyl acrylamide) and its derivatives. Untethered, ultrasound-actuated bubble-driven microrobots facilitate slow drug release via hydrogel tissue adhesion[141] or flow through the bloodstream[53] [Figure 3A]. Magnetically-driven soft actuators composed of biodegradable silk proteins and magnetite nanoparticles[142] can navigate through narrow regions within the human body[143]. Targeted drug delivery devices, such as one made from biodegradable poly(aspartic acid) and a zinc and iron core[20], can be magnetically guided to specific locations, such as the stomach where gastric acids trigger propulsion and drug release [Figure 3B].
Figure 3. Soft robotic microtools designed for use in vivo. (A) Untethered acoustically driven bubble bots controlled by ultrasound into a mouse brain[53]; (B) Untethered magnetically driven targeted drug delivery devices that are propelled by gastric acid[20]; (C) Tethered stiff-soft photothermal microgripper at the tip of an optical fiber controlled by a light polymerized gel that can swell or shrink either due to temperature or pH[146]. [Images (A-C) are licensed under CC BY 4.0. http://creativecommons.org/licenses/by/4.0/.]
Free-floating microdevices sense and respond to the body’s environment by performing medical tasks with minimal disruption to the biological microenvironment. Hu et al. propose a soft millirobot for targeted drug delivery applications composed of a bilayer adhesive body, a mussel-inspired hydrogel layer, and an octopus-inspired magnetic structural layer enabling the robot to adhere to a catheter and travel to the targeted area using an external magnetic field[144]. In another study, Yang et al. propose a millipede-inspired soft drug delivery robot that can release drugs at a targeted area in the stomach[145]. The robot employs Helmholtz coils which allow magnetic fields to be generated to perform precisely controllable movements. The millipede-inspired legs of the robot reduce contact between the robot and the ground, reducing friction and enabling movement across wet surfaces[145], such as tissue and organs.
In minimally invasive procedures, tethered devices can leverage endoscopes for signaling capabilities and power sources from the fiber[54]. Hydrogels grown on optical fibers can be stimulated by either pH[146]
Soft sensors for biomedical applications
Sensors can monitor biological functions to report on health and disease[150]. Silicon-based technologies have been crucial for advancing biomedical sensing as constructs are small and not susceptible to noise[151]. However, due to the rigidity of silicon, constructs can be difficult to conform to tissue or attach to organ surfaces, causing discomfort to patients[152]. Additionally, common circuit components may result in poor transduction (i.e., signal mismatch) between the device and biological tissues[153]. There exists a need to explore soft, flexible sensors for monitoring body conditions to gather accurate data while preventing harm or discomfort to patients.
Hydrogel-based materials have been investigated in biomedical sensor design because of their soft structure and response to external stimuli[124]. Hydrogels consist of polymer chain networks that can swell in aqueous conditions. Environmentally responsive hydrogels can detect glucose levels and can be used for touch, stress, stretch, and pH level sensing[124]. Zhai et al. propose a glucose sensor comprising platinum nanoparticles/polyaniline hydrogel hetero-structured electrodes which allow for physiologically relevant sensitivity and rapid response when detecting changes in glucose levels[154]. Noninvasive methods of glucose monitoring have been developed for diabetic patients to avoid anxiety and pain from traditional, invasive fingerstick procedures[155]. For instance, Lin et al. demonstrated how hydrogel-based patches with electrochemical glucose sensing can be safely placed on a skin surface to detect changes in glucose levels from sweat[155]. This hydrogel strategy allows for accurate noninvasive sensing in a wearable sensor design. Such sensors can be paired with actuating devices to deliver therapeutics in response to illness or disease.
Tactile sensors have also been developed for soft robotic biomedical applications. Qiu et al. describe the application of force, pressure, and tactile sensors including haptic feedback for robot-assisted minimally invasive surgery (RMIS)[156] [Figure 4A]. Tactile sensing can detect tissue palpation to identify tumors, lumps, vessels, or other abnormalities within the human body[156]. Qasaimeh et al. describe the development of a tactile sensor made of polyvinylidene fluoride (PVDF) for minimally invasive surgery applications to sense the pulses of arteries[157]. The PVDF material was used as it is a piezoelectric material and can be used to sense a wide range of frequencies. Thus, the sensor can detect different loads by varying voltage levels from the PVDF sensing elements. The sensor also features a tooth-like structure, enabling it to grasp and hold soft tissues[157]. Li et al. propose an implantable and degradable tactile soft sensor for intracranial pressure detection[158] [Figure 4B]. The sensor is made of silk fibroin protein and is unaffected by temperature changes or tissue environments[158].
Figure 4. Soft sensors for biomedical applications within the human body. (A) Force and pressure sensors for surgical procedures[156]; (B) Composition and application of an implantable and biodegradable tactile sensor to detect intracranial pressure[158]; (C) Silicone-composed crack sensor cantilever to measure the cardiac contractility[161]. [Images (A-C) are licensed under CC BY 4.0. http://creativecommons.org/licenses/by/4.0/.]
Soft electronic sensors, or electronic skin sensors, are made from biocompatible and biodegradable polymers to mimic the properties of human skin and can sense changes in strain, pressure, shear force, temperature, and humidity[159]. Elastomers integrated with inorganic, conductive fillers can be used as resistive strain sensors measuring signal changes with stretching to monitor cardiac rhythm, tendon rehabilitation, and physiological data[160]. Kim et al. have developed silicone rubber cantilever sensors to measure cardiac tissue contractility by detecting strain changes in cardiomyocytes cultured on the cantilever[161] [Figure 4C]. Polydimethylsiloxane (PDMS)-based soft sensors have been used as a dielectric layer for capacitive-based pressure sensors[162]. A tissue-adhesive piezoelectric soft sensor was developed to adhere to the surface of the biological tissue and monitor vitals including blood pressure, heart rate, and respiratory signals during surgery[163]. However, soft electronic skin sensors usually rely on external power sources which increases power consumption and design complexity. These examples demonstrate the wide variety of biological signals that can be detected by soft material sensors to further enhance the performance of implantable soft robots.
SOFT ROBOTS FOR MARINE ENVIRONMENTS
Robotic devices are being investigated for ocean exploration applications including inspection, offshore operations, and biological sampling[164]. Robots designed to perform operations in marine environments must withstand extreme conditions such as high hydrostatic pressure[105], and rough, uneven, and delicate terrains[165]. Hydrodynamic perturbations in underwater environments create challenges when traveling to the pelagic and benthic regions of the ocean[21]. In addition to swimming, marine robots must also be capable of capturing and investigating delicate materials and objects without damaging them and the surrounding environments (i.e., coral reefs)[21]. Examples of traditional underwater robotic systems include autonomous underwater vehicles and remotely operated underwater vehicles[166]. To offer new utility to these vehicles and address some shortcomings of current end effectors, soft robots have been developed for applications in marine environments[21]. These efforts aim to offer greater mobility, resistance to high pressure, impact-bearing capabilities, and reduced disruptions to marine life.
Soft actuators for marine environments
Since terrain in marine environments can be unstructured and delicate, soft robots need to deform according to the environment, bear impact loads, and absorb energy in collision cases. Actuation mechanisms for marine environments allow for different motion speeds underwater. Pneumatic actuation mechanisms for underwater soft robot applications have been widely implemented as pneumatic actuators enable close-to-neutral buoyancy and large deformations[167]. Hydraulic actuators usually have faster response speeds than other actuators for underwater applications as the environment in which they operate is a liquid medium. This allows hydraulic underwater soft actuators to generate a large thrust force. They also have better incompressibility than pneumatic actuators as they involve high-pressurized fluid. This increases impact durability and actuation efficiency[168]. Chemical reaction mechanisms have also been used in underwater soft robots. For example, decomposition, redox, catalytic, combustion, and hypergolic chemical reactions can be implemented to propel soft robots by generating gas or heat. However, chemical actuation usually has long reaction times and cannot operate for long periods due to the need for replacing reaction materials[167]. The speeds of underwater soft robots also depend on the pressure level within the region of water the soft robot is traveling in, the material composition, and the structure of the soft robot. The biomimetic structural designs of soft robots have been extensively explored to allow for higher-performance locomotion underwater[169]. This includes soft robotic biomimetic fish[170], jellyfish[171], and octopus[172]. These soft systems can also travel underwater easily and prevent disruptions to biological life while performing ecological monitoring and data collection[173].
Galloway et al. developed a bellows-type soft gripper that can deform and retrieve delicate samples of benthic fauna[91]. The gripper has two elastomeric compartments[174] creating bidirectional bending by pressurized fluid or vacuum[91]. Another robot can achieve jet propulsion motion by expanding and contracting its origami structure with fluid [Figure 5, origami jellyfish (jet propulsion)][173]. Other traditional jet actuators composed of rigid parts are reported to be susceptible to impact damage[175]. Therefore, developing jet actuators composed of soft materials allows for increased impact-bearing capabilities.
Figure 5. Underwater travel speed comparison of various soft robots. (0.42 cm/s) Soft robotic manta ray composed of IPMC that can move underwater[65]. (1.158 cm/s) Soft robotic origami jellyfish that allows for fluidic jet propulsion[173]. (2.5-2.8 cm/s) Soft robotic jellyfish composed of SMAs to allow for motion in underwater environments[177]. (3.72 cm/s) Soft robotic fish composed of dielectric elastomers that can move forward when actuated[180]. (All images are licensed under CC BY 4.0. http://creativecommons.org/licenses/by/4.0/.) IPMC: Ionic polymer metal composites; SMAs: shape memory alloys.
Smart, low-modulus materials that respond to external stimuli by deforming, changing elasticity, and propelling have also been used for underwater applications. SMAs[176], known for their high power-to-weight ratio and requiring low voltage levels for actuation, have been incorporated as actuators into soft robots. They also have low noise and high force-to-weight ratios. However, they may have lower response speeds and poor power consumption performance[137]. Cruz Ulloa et al. describe the development of a swimming robot that can travel underwater by SMA actuation when enclosed within a layer of silicone[177]
DEAs, consisting of a complaint capacitor structure, deform when an external electric field is applied[178]. They have been explored for underwater soft robotic devices due to their density similar to that of water[179]. Shintake et al. propose a soft robotic fish that achieves forward motion by the actuation of DEAs[180]. This robot has compliant structures, rapid actuation response, and low water absorption [Figure 5, soft robotic fish (DEAs)][180]. Christianson et al. propose fluid electrode DEAs that display increased flexibility by achieving a maximum curvature of 12.5 ± 0.4 m-1 of a 73 mm bimorph that was actuated with an electric field of 20 mV·m-1. A Froude efficiency of 52% and a swimming speed of 1.9 mm/s was also achieved[181]. In another study, a soft robot manta ray composed of an ionic polymer metal composites (IPMC) wing achieved complex 3D deformation underwater. The IPMC-based wing displayed a maximum twist angle of 15.5º and had free-swimming capabilities[65] [Figure 5, soft robotic manta ray (IPMC)].
Soft sensors for underwater environments
Sensors monitor environmental changes and external pressure signals in marine environments[182]. Liquid metal sensors have a metallic conductivity of about 3.4 × 106 S/m and low modulus liquidity which make them candidates for deformable elastomer-based building materials in soft robots. Their use can also prevent damage such as cracks from underwater deformation movements due to elasticity and self-healing characteristics[183]. Lin et al. also describe using liquid metal-based sensors for the control of a soft robotic fish[184] [Figure 6A]. The sensors comprise elastomeric fluidic channels with filled conductive liquid metal, eutectic gallium-indium (eGaIn), and can detect applied strain through changes in electrical resistance.
Figure 6. Soft sensors for underwater soft robot applications. (A) Liquid metal-based sensor composed of elastomeric fluidic channels with filled conductive liquid metal eGaIn to measure strain and provide feedback to control the soft robotic fish[184]; (B) IPMC material which can be used as a sensor under bending deformation. IPMC sensors can detect changes in deformation, pressure, velocity, and humidity[185]. [All images (A and B) are licensed under CC BY 4.0. http://creativecommons.org/licenses/by/4.0/.] IPMC: Ionic polymer metal composites.
IPMC materials have been implemented for underwater sensing applications due to their soft structures and ability to generate output voltages with no applied power. They can be used as sensors to detect changes in deformation, pressure, velocity, and humidity[185] [Figure 6B]. In addition, IPMC devices can perform tasks without the need for protective waterproofing[186]. They were implemented as sensors for a biomimetic underwater vehicle to measure the amplitude and frequency of waves[186]. IPMC devices have also been used for bioinspired sensing[187], for example, to develop an artificial fish lateral line for the detection of source localization in underwater environments[188]. Thus, the development of IPMC sensors allows for efficient sensing in underwater environments for soft robotic devices.
SOFT ROBOTS FOR SPACE EXPLORATION
The environmental conditions of extraterrestrial settings present distinct challenges for robot operations. Microgravity can incur mechanical effects that alter the behavior of robots compared to earth-bound operations[22]. Space environments have extreme temperature fluxes due to the absence of a medium for heat transfer. Therefore, space robots must be able to transfer heat through conduction or radiation between spacecraft and the surrounding environment[22] or be thermally insulated to regulate device temperature[22]. Robots in space may be exposed to high-energy particles and radiation because of the absence of a geomagnetic field[22]. This radiation can result in disturbances in electrical equipment including semiconductor components[22]. Durability and redundancy in design are important considerations for robots as the ability to fix or replace components is non-trivia, and thus self-healing properties of soft devices enable the longer-term service in unmanned environments[189].
Soft actuators for space environments
The tasks a robot may need to perform in space range from assembly to locomotion to sampling, dictating the actuation mechanism used in design [Figure 7A]. Deformability, impact-bearing capability, and resistance to brittle failure are important features needed to negotiate unstructured space environments[22]. Compliant soft microsatellite grippers can conform to capture irregular space debris[190]. Areas with large amounts of cosmic radiation may cause materials to become rigid and brittle[22]. Soft robots must be able to operate in extreme temperatures in space, such as regions without sunlight that can reach temperatures in the range of -200 to -150 °C[22]. Also, the surface temperature of spacecraft in direct sunlight ranges from 97 to 127 °C. Therefore, using materials that can maintain their properties and characteristics over a wide range of temperatures is important for soft robotic applications in space. For instance, temperature-resistant elastomers such as silicone can be used for high-temperature applications[22]. Ogliani et al. display the material properties of silicone elastomers with different crosslinking densities through thermogravimetric analysis by testing these elastomers up to 700 °C in a nitrogen atmosphere[191]. This study depicts how removing the sol fraction of PDMS increases the thermal stability of silicone elastomers. Porte et al. describe how elastomers that are commonly used in soft robotics including EcoFlex 00-30, Dragon Skin 10, Smooth-Sil 950, and Sylgard 184, were tested under temperatures ranging from -40 to 140 °C[192]. The results of the test depict how generally as the temperature rises, the stiffness of the material also increases[192]. While some elastomeric materials have material properties that depend significantly on temperature variances, materials such as fiber materials, including Kevlar, and organic materials, such as polyimide and Teflon, have high-temperature tolerances[22].
Figure 7. (A) Overview of various soft robots for different space exploration applications[22]; (B) Soft robotic arm composed of pneumatic links and can be stored in a small package for space applications[92]; (C) Soft robotic solar-driven soft actuator[193]; (D) Dielectric elastomer soft robotic inchworm that can perform running and jumping motions[195]. [Images (A-D) are licensed under CC BY 4.0. http://creativecommons.org/licenses/by/4.0/.]
Fluidic actuation mechanisms can be used in soft robotic actuators for space applications as they are adaptable and may generate high output forces with low energy input[22]. Zhang et al. propose a soft robotic gripper with pneumatic actuators designed for low air pressure[48]. This actuator is fabricated from carbon fiber reinforced polymer laminates which allows it to be stable in two actuation states. The gripper also has a low total energy consumption (~1.85 J) for every grasping motion. Palmieri et al. propose a deployable soft arm made of pneumatic inflatable links that can be stored in a small package for reduced weight and volume during shipping [Figure 7B][92].
Solar-driven soft robots can be used for space applications for their efficient energy systems. Mirvakili et al. developed a solar-driven soft robot consisting of a pressure chamber containing a low boiling point liquid
Electrically driven soft actuators can also be used for space applications as they can be lightweight, easily transportable, and durable[194]. To verify if these actuators will perform well in low-pressure environments, DEAs, composed of silicone rubber sandwiched between two carbon black layers, were deflection tested. Actuator displacement was tested under different pressure conditions by applying a constant voltage to the sample in a vacuum chamber. Testing showed sample strain was only minimally affected by vacuum chamber pressure. Therefore, DEAs may be useful in variable-pressure environments[194]. Additionally, Jing et al. propose a DEA-driven inchworm soft robot that can achieve both forward running and jumping motions [Figure 7D][195]. These mechanisms may be advantageous for planetary exploration on unstructured surfaces to efficiently traverse the landscape and avoid obstructions.
Current advances in building habitats in these environments include producing sustainable resources such as food. Romano et al. propose using concentrations of the lunar regolith stimulant mixed with cow manure to study the effects on the earthworm species, Eisenia Fetida, to prepare moon soil[196]. In another study, Giordano et al. present a method of biofortification with iodine from four different species of microgreens to provide adequate nutrition using terrestrial resources[197]. Caporale et al. also study the use of different substrates including Mojave Mars regolith stimulant for the cultivation of soybean to create resources and food in space environments[198]. These methods would help astronauts to survive during long-term space missions as the next step for extraterrestrial environment exploration[197]. Soft robots can facilitate this work in space. For example, Hammond et al. propose a hybrid soft material robot end-effector that can help in the bonding and de-bonding of conical structural components for building larger space equipment[199]. The robot uses twisted and coiled artificial muscles for actuation which have a higher force-to-weight ratio than other actuation methods[199]. In another study, Molaei et al. propose cable-driven continuum robots that would help to build sustainable structures in space environments for planetary habitats[200]. Soft robots can aid in developing structures for space missions and for habits in space environments.
Soft sensors used in space environments
Soft sensors can be used for monitoring equipment, environmental conditions, or feedback sensing on soft robots. IPMCs can be used as sensors for space equipment as they can conform to the structure of the equipment to provide more detection area on these structures[201]. Equipment damage or defects are sensed through changes in IPMC bending and resulting voltage differentials. IPMCs can also be used for vibration monitoring in satellites. Satellite vibration can affect orbiting trajectories, disrupting the aim of instruments attached to the satellite. It is proposed that IPMC sensors be placed on the structure to record vibration data for vibration modeling to monitor the health of the spacecraft. These models can help determine the impacts on the structure, trajectories, and instrument tasks based on vibration[201].
Flexible sensors have been proposed for soft space robots and astronaut health monitoring devices. These applications require high accuracy, adaptable geometry, and efficient energy systems[202]. Fu et al. developed flexible pressure sensors composed of ceramic nanofibers which provide high-temperature resistivity as they can withstand temperatures up to 370 °C. These ceramic sensors have quick response speeds of less than
Figure 8. Soft sensors for space environment applications. (A) Ceramic nanofiber flexible pressure sensor with high-temperature resistant characteristics. The device structure, a thermal image of the sensor that is tested at 370 °C, and the capacitance to pressure sensitivities for tests at 30, 370, and 30 °C after burning are displayed[202]; (B) Triboelectric all-textile sensor array to monitor aerial pulse waves and respiratory signals and can be worn around the neck, as a wristband, fingerstall, or integrated into a sock[203]. [All images (A and B) are licensed under CC BY 4.0. http://creativecommons.org/licenses/by/4.0/.]
SOFT ROBOTS FOR SEARCH, RESCUE, AND CONFINED SPACES
Natural and man-made environments often create conditions that are unsafe for humans to enter during search and rescue operations[108]. Confined spaces that are fully enclosed or have limited entryways include pipes, mines, tanks, and pits[204]. These spaces may contain toxic gases, fumes, and dust, potentially causing negative health impacts to humans[204]. Thus, robots have been developed to conduct search, rescue, and inspection operations in these environments[205]. They must be able to navigate through narrow areas and obstructions such as rubble, debris, dust, darkness, and collapsed structures[93]. Soft robots can minimize friction for gripping, moving, and sensing operations to prevent further damage to the search and rescue site[93]. Thus, they offer new design solutions for increased mobility on rough and obstructed surfaces and enclosed spaces through their distinct actuation mechanisms[131], thereby reducing health and safety risks in these critical rescue operations.
Soft actuators used for search, rescue, and confined space applications
To navigate confined spaces and rough obstructed terrains, robots must be able to conform elastically to avoid surface wear, absorb energy, and bear impact loads on collision. Additionally, these devices must be compact and able to travel in narrow spaces. Some soft robot designs proposed for search and rescue are growing-type robots that can grow axially with directional control to steer the robot[206]. The growing mechanism of these robots can be achieved by continuous additive manufacturing or pneumatic actuation[108]. However, buckling can cause growing robots to move in unexpected directions as they can retract, resulting in disturbances to the environment. Vine-like robots are another class of growing robots that only undergo internal friction and can also feed cables through the center of the actuator[108]. El-Hussieny et al. propose a soft vine robot built from a polyethylene tube that extends from the tip once air pressure is applied [Figure 9, Vine robot][207]. The robot can be steered by applying air pressure to serial PAM oriented around the structure’s circumference. These robots can conform to the surrounding environment without impacting obstructions and preventing further destruction.
Figure 9. Diameter comparison of search and rescue and pipe inspection soft robots for confined space applications (Worm robot,
Burrowing and locomoting robots with fluid-driven actuators have also been developed for search, rescue, and confined space operations. For instance, worm-inspired soft robots using pneumatic actuators have been developed for the maintenance, repair, and inspection of pipelines leveraging their high flexibility and elasticity, high load capacity, lightweight, and low cost [Figure 9, Worm robot][208]. Wang et al. prototyped a soft pipe robot with a soft hexagonal prism structure[209]. It can perform different motions with choreographed inflation patterns to comply with pipe paths [Figure 9, Pipe robot]. A challenge to soft pipe robots is the limited distance they can travel. For instance, some pipe soft robots, such as cable-based soft robots[210], must be tethered to an actuation[211]. These limitations can be overcome by employing wireless control and self-powered mechanisms to travel through these constrained environments. For example, a soft robot that performs leak detection within pipes was built with wireless charging capabilities using inductive coils[212]. Wang et al. propose a wirelessly controlled soft robot, WASER, which uses radio frequency (RF)-based heating systems to achieve rapid actuation[213]. The actuator also allows for feedback using high-power wireless energy. The authors discuss how the WASER soft robot can also be used for applications in enclosed spaces.
Usevitch et al. describe the development of an inflatable octahedron truss structured robot that can change shape and move using roller modules while maintaining a constant volume, eliminating the need for an air supply[214]. This helps maintain the compactness of the soft robot and achieve locomotion. Tolley et al. describe the development of an untethered pneumatic actuator that achieves a jumping motion via combustion of butane into pneumatic chambers[79]. The robot can reach a height of 0.6 meters in less than a second. This soft body structure absorbs energy upon landing, increases its impact-bearing capability, and reduces risks to human safety. Thus, the development of explosive-driven soft robotic devices could provide new opportunities for soft robotic locomotion while avoiding obstructions in search and rescue environments[215]. In another study, Mazzolai et al. describe a tendon-driven soft robotic arm with suction cups for grabbing objects in confined environments. The soft robot mimics the motion of octopus tentacles and can achieve bending and twisting motions[216] [Figure 9, Octopus robot]. These soft robots have actuation systems that allow them to transform to different diameter sizes for travel through different-sized pipes. For instance, the pneumatic axial elongation actuation of the worm-inspired soft robots impacts the distance the soft robot can move[208]. The radial expansion of the soft robot also allows it to expand to the size of the pipe it is traveling through[208]. Similarly, the axial bending deformation, flexion, and extension motion through the pneumatic actuation of the soft pipe robot enable travel through pipes with different diameter sizes by expansion[209]. These examples suggest that using actuation mechanisms that allow for easy and efficient robot size deformation is advantageous in constricted environments. Pneumatically actuated soft robots seem to be more beneficial and versatile as they can change size simply by inflation or deflation and are more controlled. Other actuation mechanisms of soft robots, such as tendon-based actuation, may not be as easily deformable in terms of size and instead can only be built for a specific application.
Soft sensor designs used for search and rescue and confined space applications
Soft pressure and strain sensors were developed for monitoring and inspection operations in hazardous and confined environments. Soft grippers with sensing capabilities can sense object orientations and deformation when collecting specimens[108]. These sensors include 3D strain sensing printed ionic conductive gels[108]. The flexibility of the gel helps the sensor to be easily integrated within the soft gripper for accurate sensing. Other integrated sensing technologies are discussed in the literature review by Milana on soft robots for infrastructure protection[108].
Soft pressure sensors have also been developed using conductive elastomer composites that have conductive fillers with piezoresistive characteristics[159]. Capacitor-based soft sensors can be used as self-healing pressure sensors and can detect changes in external pressure applied by changes in the capacitance of the material[217]. Zhang et al. describe a capacitive-based pressure sensor using the self-healing material, polyacrylic acid/betaine, thus extending the sensor’s operating life. The sensor is developed using two conductive fabrics with an ionotronic layer between them that is composed of self-healing material[218] [Figure 10A]. When pressure is applied to the sensor, the change in the capacitance of the material can be used to detect the changes in the pressure[218]. Georgopoulou et al. also propose using self-healing piezoresistive strain sensor fiber composites (ShSFCs) as an electronic skin to detect deformation and damage on a soft robot. The sensor was tested using a tendon-based soft actuator in which the electric signal output of the sensor was recorded before damage, after damage, and after healing. The signal output displayed that the sensor was able to regain its performance after healing[219] [Figure 10B]. Other self-healing soft sensors are discussed in a literature review by Khatib et al.[217].
Figure 10. Soft sensors for search and rescue environments. (A) Self-healing polyacrylic acid/betaine pressure sensor material composition and capacitance variations based on different pressure level loads, response time at a loading pressure of 0.36 kPa, and dynamic loading and unloading at different pressure levels[218]; (B) ShSFC-based electronic skin sensor that is attached to a tendon-based soft robotic actuator. The electrical signal of the sensor recorded before damage, after damage, and after healing is also displayed[219]. [All images (A and B) are licensed under CC BY 4.0. http://creativecommons.org/licenses/by/4.0/.] ShSFC: Self-healing piezoresistive strain sensor fiber composite.
EXPANDING THE USE OF SOFT ROBOTS IN EXTREME ENVIRONMENTS
So far, this paper has explored the benefits of soft robots in extreme environmental conditions because of their material composition, actuation mechanisms, and adaptability. However, challenges and limitations to using soft robots persist. Topology optimization tools may be used to strengthen the design and function of these robots to expand their usage. Special considerations for soft robots in terms of control systems and the extreme environments described should also be considered. Finally, as the field develops and prototypes become commercial products, it will benefit these efforts to address challenges for end users during early research.
Soft actuator limitations for use in extreme environments
Soft actuators have advantages and limitations that are important to understand when designing soft robots for extreme environments. Some soft actuators have drawbacks, such as tendon-driven actuators which may undergo fatigue, nonlinear friction, backlash hysteresis, and other transmitted forces[44]. Flexible fluidic actuators including PAMs and McKibben actuators require external power sources for actuation, making it difficult to build untethered systems for biomedical devices[44] and other applications in enclosed spaces. Soft pneumatic actuators also usually suffer from low actuation response speeds[137]. Soft robots have unpredictable and complex behaviors resulting in nonlinearities that make them difficult to model and control[220]. Therefore, matching actuation mechanisms to applications that achieve desired performance levels may help develop soft robots that are favorable in their operating environments. For example, Zaidi
Design and topology optimization
Design approaches for soft robots are primarily based heuristically and empirically on bioinspiration and intuitive perspectives[221]. Although traditional biomimetic and intuitive approaches have documented utility[222], their outcomes are based on initial assumptions about the structure and are greatly dependent on anthropogenic factors, such as the designers’ experience, and professional knowledge[223]. The design of soft actuators presents challenges due to the hyper-elastic and viscoelastic properties of low-modulus materials that produce highly dimensional design spaces[17]. Optimization algorithms, simulation, and analysis tools targeting more efficient design methods have been explored[224]. Topology optimization is one such method for form-finding of high-performance, lightweight, multifunctional structural designs and has been widely used in aerospace[225], automotive[226], and architecture industries[227].
Topology optimization works to identify numerically optimal structural forms by allocating material distribution that satisfies prescribed constraints within a specified design domain[223]. That domain, predefined by the user, supplies the loading and support configuration and a geometric region on which the material distribution is determined by individual design variables. For compliant mechanisms, such as grippers, the objective function typically maximizes mutual potential energy, geometric advantage, or mechanical advantage[228]. For example, a soft, cable-driven compliant gripper uses topology optimization to model interactions between grippers and objects in the form of pressure loading and friction[229]. This method has been demonstrated to design flexible thermoelectric devices with increasing output voltage and a corresponding improvement in power generation efficiency[230]. It allows for the design of multiple microstructural materials within a macrostructure geometry that has spatial variation and hierarchical structures[231]. Using these methods, nonlinear viscoelastic and even hyperelastic properties of materials used in soft robots can be considered[232]. Topology optimization techniques allow designers to improve the efficiency and performance of robot design, beneficial when developing devices to function in complex environments.
The human body is a challenging environment due to its susceptibility to tissue damage. With the increasing use of soft robots in healthcare services[104] and their interaction with fragile materials such as human tissue becoming more common[233], the safety of these robots is a growing concern[234]. In such cases, reducing the mass and inertia of these robots minimizes the risk of injury to humans during interactions. Thus, structural topology optimization is beneficial for designing lightweight medical devices[104]. The medical industry has proposed topology optimization techniques to design prosthetics and implants such as soft compliant finger prosthetics[235], soft finger-like devices[236], and bioinspired quadruped compliant legs[237]. These biomedical soft devices can mimic the stiffness, density, and structure of the body part such that they can avoid causing injury[238].
In challenging environments such as confined spaces, topology optimization can be advantageous in creating efficient designs for effective locomotion. One study developed a framework specifically for moving objects using a topology optimization method incorporating a material point method that can simulate the motion of objects[239]. Similarly, topology optimization methods have been used in aerospace and marine environments where the weight of the craft, ship, and other devices is an important consideration. Expanding the use of topology optimization in soft robot design should broaden the application space and enable rapid optimization of soft devices capable of withstanding these complex environments.
Control systems that enable soft robot use in extreme environments
Developing control systems for soft systems is a challenge as soft robots have continuous flexible structures as opposed to discrete degrees of freedom. Therefore, implementing control systems that consider the mechanical structure or properties of these devices is crucial to developing reliable and efficient systems. Many of these control strategies also require models of the soft robotic device to analyze the material dynamics of the device in response to the actuation mode. However, due to the nonlinear structure of soft robots, it can be difficult to develop mathematical models that accurately represent device deformation[240]. Finite input, output, and disturbance parameters of the control system can be set to describe actuation. Additionally, internal memory variables of the soft robot are set using state variables to control the motion of the robot across time[220]. Control systems, generally classified as open-loop (OL) and closed-loop (CL) systems[241], have utility for different soft devices in various environments.
Runciman et al. developed soft hydraulic actuators for minimally invasive surgery using an OL position control system[242]. The actuator contracts by changing the volume of the actuator without feedback from the environment. Open loop control systems for fluid-driven assistive robots can be achieved by cycling pressure to the actuators[243]. CL feedback control systems have been used for many biomedical applications. Beatty et al. developed a drug delivery device that uses CL control to change its actuation regimen to dispense the precise amount of the drug[244]. The device, composed of thermoplastic polyurethane, can monitor foreign body response by changes in the electrical impedance to determine the actuation regimen and efficiently deliver therapeutics.
Model-based (MB) controls use kinematic or dynamic modeling strategies to develop efficient control systems for the device[27]. The piecewise constant curvature model is a popular model that divides the soft robot into sections with constant curvature[245]. FEM methods divide a soft robotic structure into discrete elements to obtain a set of partial differential equations to solve at each degree of freedom[246]. In this case, FEM can efficiently evaluate the structure and model material deformations once actuated[247]. Model-free (MF) control systems rely only on feedback data from sensors [248]. MF control systems may be implemented for device applications in environments that cannot be accurately described by mathematical tools[249]. Proportional-integral-derivative (PID) control systems use a signal that consists of the sum of adjustable proportional, integral, and derivative constant factors multiplied by the error[250]. Therefore, these systems help reduce the error between the output and desired signals[250].
Adaptive control (AC) systems can be implemented as MB or MF systems[251] and allow for changes in the control signal using real-time data collected from the current conditions of the system and the environment. These control systems make changes to the control signal depending on the known parameter disturbances[252]. The AC signal allows for the desired performance index to be achieved using a feedback loop and an adaptation system which helps reduce errors in the performance of the system[252]. Model reference adaptive control (MRAC) systems use a system model to determine the error between the outputs of the actual system and the model, allowing adjustments to the control signal[253].
Reinforcement learning (RL) control systems can be implemented as MF or MB systems[254]. They are based on action and reward paradigms[255]. The system uses evaluated feedback to determine whether the behavior of the robot has improved to achieve the desired action. It also tries to maximize the reward from the evaluated feedback by implementing different actions. Li et al. developed a deep RL framework for motion control of an underwater soft robot[256]. The robot could efficiently travel through the environment by training a neural network developed using a deep RL algorithm called soft actor-critic. The soft robot was trained to move in a straight line starting from a random initial position to later learn how to travel through the unpredictable environment[256]. Table 3 displays the various control systems that can be used for soft robots.
Summary of soft robot control systems and their application examples
Control systems | Description | Examples of soft robot applications |
OL | Feedback data is not required to make changes to the system. Depends only on input to achieve the desired output. Prior knowledge of the operating environment is required for more accurate control[257] | Soft hydraulic actuator for highly repeatable results- advantageous for surgical applications[242]. Pneumatically actuated soft robotic manipulators can inflate devices to different shapes[257] |
CL | Feedback data from output is required to adjust the input signal to achieve correct output. Feedback data can be obtained by sensors to measure the current conditions of the environment and system. Prior knowledge of the operating environment is not required[257] | Drug delivery devices receive real-time feedback data from foreign body responses to change the actuation regimen to deliver the correct amount of drug to the body[244]. SMA spring bot can actuate/deform with sensors to obtain feedback data[258] |
MF | Feedback data from sensors is used to adjust input signal to achieve correct output without the use of models of device/system[248]. Can be used for devices that have complex structures/actuation mechanisms and environments that cannot be described by mathematical models[259] | Locomotion bot using MF to interact with the environment by learning the state transitions and optimized periodic control sequences[260]. Pneumatic muscle actuator soft robots can follow certain paths[261] |
MB | Modeling strategies including PCC[245] and FEM[247] to mathematically represent the device and its operation to modify the input signal to achieve the correct output[262] | Environmentally adaptive bot achieves planar motion using MB CL controllers for trajectory tracking and impedance control[262]. Uses PCC and FEM to model and simulate the device. Piezoelectric inchworm for constrained environments with MB motion control[263] |
PID | Type of MF control system that uses error between actual and desired output to modify input signal to achieve correct output[264]. Uses proportional, integral, and derivative factors that can be adjusted for more accurate control[265]. Variations include PI control system[266] | Bio-inspired underwater vehicles use four PID controllers for autonomous control[267]. The pneumatic arm can reach certain destinations or follow trajectories[268] |
AC | Can be MB or MF, depending on the application[261]. Modified input depending on known parameter disturbances. MRAC[253] uses the device model to compare the system’s actual and predicted output to adjust the control signal[253]. Other types include direct AC[269] and indirect AC[270] | A soft robotic arm that uses AC to control its position and stiffness[271]. Underwater soft robot that uses AC for visual servoing and prior knowledge of environmental impact for more accurate control[272] |
RL | Can be MB or MF, depending on the application. Evaluated feedback of output signal used to monitor system behavior and modify input signal to maximize system reward and achieve correct output[273]. RL approaches include value-based[274], policy-based, or MB and can also be either active or passive-based[274] | Motion control of the underwater robot by training a neural network developed using a deep RL algorithm for a bot to learn how to travel through unpredictable environments [256]. A caterpillar bot uses RL to travel to different environments[275] |
Future considerations of the control of soft robotic devices include artificial intelligence (AI). The AI-driven control systems and models may consider the nonlinear structure of soft robots and implement control that is similar to biological organisms[276]. An AI-driven control system may consist of a neural network with a hierarchical structure of input variables and hidden nodes that are connected and weighted based on importance[277]. There are also designs to develop neural networks for robotics such as supervised control[278], direct inverse control[279], neural AC[280], back-propagation utility[281], and adaptive critic methods[282]. These strategies allow the system to learn based on the environment and use case[283]. Machine learning algorithms can be used for the control of soft robots as the nonlinearity of soft robotic devices can be modeled and integrated into a neural network[276]. Machine learning models can also be developed to model the interaction between different actuators with complex nonlinear structures[276]. Therefore, the development of AI-driven control systems and models may allow for more robust control of soft robotic devices for extreme environments as they learn and adapt to uncertain conditions.
Future considerations for the design and use of soft robots
The application of traditional, rigid robots currently dominates in terms of availability. As soft robots continue to develop, opportunities for commercial products are increasing. Currently, soft robots are available for applications including grippers in manufacturing[284], sleep monitoring technology[285], rehabilitation exosuits[286], and search and rescue operations[287]. As commercial applications increase, their designers must also consider the end users to expand their reach and accessibility for low-cost, durable, and safe devices[288].
In 2012, as soft robotics was gaining popularity[12], Empire Robotics was founded to commercialize a particle jamming gripper. By 2016, the company closed but offered lessons learned from its commercialization efforts[289]. The team initially explored markets including space exploration, prosthetics, bottle capping, and toys, but found that industrial applications had the fewest regulatory hurdles and largest market opportunity[289]. While n = 1,000 cycles to failure are acceptable for an academic demonstration, Empire Robotics estimated that their grippers would need replacement every 70 days in industrial settings. Even with a successful product, competing design criteria (durability, size, shape, pneumatics, granularity) presented challenges for the commercial effort[289]. Despite this, the market for soft robot technologies continues to grow. In 2019, the soft robotics market was estimated to reach almost $5 billion by 2025[290]. Soft Robotics Inc. provides PneuNet (pneumatic network)-based grippers for industrial packaging and had revenue of $26.4 million in 2019 and continues to expand its offerings and use globally[16]. Future considerations for the commercialization of soft robots include their expansion into other applications including biomedical and extreme environment exploration. The soft material structure makes soft robots safe for human interaction, including in medical devices[291]. However, the fabrication and operation of these robots must also avoid actuator dysfunction which might result in safety concerns[291]. Using low-cost soft materials to build these systems can increase the accessibility of soft robots for many applications.
One arena in which soft robots are being tested for their ease of use and durability is in classrooms. Researchers at academic institutions have developed courses that engage undergraduate and graduate students in soft robot design and ideation[292,293]. The potential for low-cost prototyping materials, design-based development, and interdisciplinarity in the field has also led to the use of soft robots in K-12 education[294]. Education can be a particularly complex environment because designs must be robust and easy to use to ensure positive experiences in science, technology, engineering, and mathematics (STEM) for children[295]. Designers here must focus on simplified designs[296] and low cost to increase accessibility[297]. Additionally, progress toward safe material composition and fabrication methods[298] of soft robots for educational outreach purposes would help reduce safety risks. For instance, edible soft robotic candy actuators can be used for STEM outreach to provide students with a safe and enjoyable hands-on experience in building soft robots[299]. Designing soft actuators for engineering-based learning activities for students allows them to build and interact with these actuators safely as they learn about and consider becoming the next generation of innovators contributing to this rapidly evolving field.
CONCLUSION AND OUTLOOK
The soft robotic actuation mechanisms, sensors, and control systems that we have reviewed have benefits when compared to traditional robots for applications in extreme environments including within the human body, ocean exploration, space exploration, search and rescue sites, and confined spaces. We can identify areas where soft robots provide some advantages compared to rigid devices for use in these harsh environments. The body is a challenging environment where compliance matching of the device to biological matter such as human skin and tissue is important for comfortable human contact to prevent injuries. These requirements make biocompatible and compliant soft devices beneficial for use in and on the human body compared to rigid devices. Harsh marine and space environments benefit from having devices that are lightweight and thermally insulated to meet the weight criterion and handle extreme temperatures to function in their respective environments. Confined spaces and rough unpredictable terrains can be navigated with soft devices with impact-bearing capabilities and deformability compared to rigid robots. Self-healing capability is also a unique advantage of some soft materials that can increase operation time in challenging environments where retrieval and repair are difficult.
However, soft robots also have drawbacks. They are less powerful and precise than rigid devices due to being made of much softer and, in some cases, weaker materials. The properties of these materials, such as extensional stiffness, strength, and elasticity, can be improved[300] through reinforcement with rigid materials such as fibers[301]. These hybrid materials offer enhanced capabilities, expanding the reach of soft and hybrid robots in extreme environments. Additionally, soft robots are difficult to model and control due to their nonlinear properties and lack of a supporting structure.
As observed in nature, most fully soft organisms are small, and if larger, need a skeleton to support their weight[12]. Large, soft animals without skeletons typically exist in water or underground so that their bodies are supported by the surrounding medium. This evidence suggests that the best systems may be an integration of rigid structures and soft technologies. Thus, new types of hybrid structures have evolved that can withstand and exert more force than simple soft robots, increasing their applications in industrial settings[302]. Developing controllers and stable interfaces between the soft and rigid components is necessary in future research to control the upcoming hybrid devices[302]. Hybrid system interactions are also generally required for actuator control since soft elastic materials would require rigid microprocessors until the time microelectronics can be fully made of low-modulus and elastic materials.
Since rigid robots dominate in use and availability, we see opportunities to expand the potential of soft robots in extreme environments. This can be accomplished using design techniques such as topology optimization that can improve the efficiency, cost, and material savings, and the tunability of actuator design. Implementing control systems with AI and machine learning may allow for more robust control of complex nonlinear behaviors and better decision-making. Finally, soft robots must be expanded by designing with the end user in mind by increasing accessibility, and usability, and reducing cost. Other ways to enhance the scope of these soft devices include improving operational lifetime with durable, self-healing, elastic materials and building entire structural components including electronics and power units from sustainable materials to minimize environmental impact. Thus, there is significant potential to advance soft robots in harsh environments, and future studies must accelerate the transition of high-performance soft devices from research labs to real-world applications.
DECLARATIONS
Acknowledgments
The authors thank the Clare Boothe Luce (CBL) Research Scholars and the Grainger College of Engineering. This work was partially conducted at the Center for Integrated Nanotechnologies, an Office of Science User Facility operated for the U.S. Department of Energy (DOE) Office of Science. Sandia National Laboratories is a multimission laboratory managed and operated by National Technology & Engineering Solutions of Sandia, LLC, a wholly owned subsidiary of Honeywell International, Inc., for the U.S. DOE’s National Nuclear Security Administration under contract DE-NA-0003525. The views expressed in the article do not necessarily reflect those of the U.S. DOE or the U.S. Government.
Authors’ contributions
Conceptualization: Kulkarni, M., Golecki, H.
Writing: Kulkarni, M., Edward, S., Golecki, T., Kaehr, B., Golecki, H.
Visualization: Edward, S., Golecki, H.
All authors have read and agreed to the published version of the manuscript.
Availability of data and materials
Not applicable.
Financial support and sponsorship
The authors would like to acknowledge funding from the Henry Luce Foundation through the Clare Boothe Luce Undergraduate Research Awards, the National Science Foundation Award #2106286.
Conflicts of interest
All authors declared that there are no conflicts of interest.
Ethical approval and consent to participate
Not applicable.
Consent for publication
Not applicable.
Copyright
© The Author(s) 2025.
REFERENCES
1. Shneier, M. O.; Bostelman, R. V. Literature review of mobile robots for manufacturing. National Institute of Standards and Technology; 2015.
2. Siciliano, B.; Khatib, O. Springer handbook of robotics. 2nd edition. Berlin Heidelberg: Springer; 2016.
3. Rindfleisch, A.; Fukawa, N.; Onzo, N. Robots in retail: rolling out the Whiz. AMS. Rev. 2022, 12, 238-44.
4. Sparrow, R.; Howard, M. Robots in agriculture: prospects, impacts, ethics, and policy. Precision. Agric. 2021, 22, 818-33.
5. Kyrarini, M.; Lygerakis, F.; Rajavenkatanarayanan, A.; et al. A survey of robots in healthcare. Technologies 2021, 9, 8.
6. Decker, M.; Fischer, M.; Ott, I. Service robotics and human labor: a first technology assessment of substitution and cooperation. Robot. Auton. Syst. 2017, 87, 348-54.
7. Maurtua, I.; Susperregi, L.; Fernández, A.; et al. MAINBOT - mobile robots for inspection and maintenance in extensive industrial plants. Energy. Procedia. 2014, 49, 1810-9.
8. Rea, P.; Ottaviano, E. Design and development of an inspection robotic system for indoor applications. Robot. Comput. Integr. Manuf. 2018, 49, 143-51.
9. Mapara, S. S.; Patravale, V. B. Medical capsule robots: a renaissance for diagnostics, drug delivery and surgical treatment. J. Controlled. Release. 2017, 261, 337-51.
10. Omisore, O. M.; Han, S.; Xiong, J.; Li, H.; Li, Z.; Wang, L. A review on flexible robotic systems for minimally invasive surgery. IEEE. Trans. Syst. Man. Cybern. 2022, 52, 631-44.
11. Narayan, J.; Kalita, B.; Dwivedy, S. K. Development of robot-based upper limb devices for rehabilitation purposes: a systematic review. Augment. Hum. Res. 2021, 6, 4.
12. Laschi, C.; Mazzolai, B.; Cianchetti, M. Soft robotics: technologies and systems pushing the boundaries of robot abilities. Sci. Robot. 2016, 1, eaah3690.
13. Bao, G.; Fang, H.; Chen, L.; et al. Soft robotics: academic insights and perspectives through bibliometric analysis. Soft. Robot. 2018, 5, 229-41.
14. De Volder M, Moers AJM, Reynaerts D. Fabrication and control of miniature McKibben actuators. Sens. Actuators. A. Phys. 2011, 166, 111-6.
15. Robertson, M. A.; Sadeghi, H.; Florez, J. M.; Paik, J. Soft pneumatic actuator fascicles for high force and reliability. Soft. Robot. 2017, 4, 23-32.
17. Pinskier, J.; Howard, D. From bioinspiration to computer generation: developments in autonomous soft robot design. Adv. Intell. Syst. 2022, 4, 2100086.
18. Wang, H.; Totaro, M.; Beccai, L. Toward perceptive soft robots: progress and challenges. Adv. Sci. 2018, 5, 1800541.
19. Harris, H.; Radecka, A.; Malik, R.; et al. Development and characterization of biostable hydrogel robotic actuators for implantable devices: tendon actuated gelatin. In: 2022 Design of Medical Devices Conference; Minneapolis, USA: American Society of Mechanical Engineers; 2022.
21. Aracri, S.; Giorgio-Serchi, F.; Suaria, G.; et al. Soft robots for ocean exploration and offshore operations: a perspective. Soft. Robot. 2021, 8, 625-39.
22. Zhang, Y.; Li, P.; Quan, J.; Li, L.; Zhang, G.; Zhou, D. Progress, challenges, and prospects of soft robotics for space applications. Adv. Intell. Syst. 2023, 5, 2200071.
23. Li, P.; Zhang, Y.; Zhang, G.; Zhou, D.; Li, L. A bioinspired soft robot combining the growth adaptability of vine plants with a coordinated control system. Research 2021, 2021, 9843859.
24. Singh, B.; Sellappan, N.; Kumaradhas, P. Evolution of industrial robots and their applications. Int J Emerg Technol Adv Eng 2013;3:763-8. Available from: https://citeseerx.ist.psu.edu/document?repid=rep1&type=pdf&doi=a30d514efd157dba6f385135eda5d8dadc3988bf. [Last accessed on 13 Jan 2025].
25. Bilodeau, R. A.; Kramer, R. K. Self-healing and damage resilience for soft robotics: a review. Front. Robot. AI. 2017, 4, 48.
26. Schmitt, F.; Piccin, O.; Barbé, L.; Bayle, B. Soft robots manufacturing: a review. Front. Robot. AI. 2018, 5, 84.
27. Santina CD, Duriez C, Rus D. Model-based control of soft robots: a survey of the state of the art and open challenges. IEEE. Contr. Syst. Mag. 2023, 43, 30-65.
28. Rus, D.; Tolley, M. T. Design, fabrication and control of soft robots. Nature 2015, 521, 467-75.
29. Helmenstine, A. Ductility - ductile definition and examples. 2021. Available from: https://sciencenotes.org/ductility-ductile-definition-and-examples/. [Last accessed on 13 Jan 2025].
30. AZO Materials. Silicone rubber. Available from: https://www.azom.com/properties.aspx?ArticleID=920. [Last accessed on 13 Jan 2025].
31. Mansy, H. A.; Grahe, J. R.; Sandler, R. H. Elastic properties of synthetic materials for soft tissue modeling. Phys. Med. Biol. 2008, 53, 2115-30.
32. World Material. Density of metals, all common metal density chart & table PDF. Available from: https://www.theworldmaterial.com/density-of-metals/. [Last accessed on 13 Jan 2025].
33. MatWeb, Material Property Data. Overview of materials for silicon rubber. Available from: https://www.matweb.com/search/DataSheet.aspx?MatGUID=cbe7a469897a47eda563816c86a73520. [Last accessed on 13 Jan 2025].
34. MatWeb, Material Property Data. Aluminum, Al. Available from: https://www.matweb.com/search/DataSheet.aspx?MatGUID=0cd1edf33ac145ee93a0aa6fc666c0e0. [Last accessed on 13 Jan 2025].
35. MatWeb, Material Property Data. Iron, Fe. Available from: https://www.matweb.com/search/DataSheet.aspx?MatGUID=654ca9c358264b5392d43315d8535b7d&ckck=1. [Last accessed on 13 Jan 2025].
36. MatWeb, Material Property Data. Overview of materials for high carbon steel. Available from: https://www.matweb.com/search/DataSheet.aspx?MatGUID=ee25302df4b34404b21ad67f8a83e858&ckck=1. [Last accessed on 13 Jan 2025].
37. MatWeb, Material Property Data. Overview of materials for low carbon steel. Available from: https://www.matweb.com/search/DataSheet.aspx?MatGUID=034970339dd14349a8297d2c83134649&ckck=1. [Last accessed on 13 Jan 2025].
38. MatWeb, Material Property Data. Overview of materials for stainless steel. Available from: https://www.matweb.com/search/DataSheet.aspx?MatGUID=71396e57ff5940b791ece120e4d563e0&ckck=1. [Last accessed on 13 Jan 2025].
39. King, L. M.; Margherio, R. R.; Schepens, C. L. Gelatin implants in scleral buckling procedures. Arch. Ophthalmol. 1975, 93, 807-11.
40. Erturk, P. A.; Altuntas, S.; Irmak, G.; Buyukserin, F. Bioinspired collagen/gelatin nanopillared films as a potential implant coating material. ACS. Appl. Bio. Mater. 2022, 5, 4913-21.
41. Gunatillake, P. A.; Meijs, G. F. Polyurethanes in biomedical engineering. In: Encyclopedia of materials: science and technology. Elsevier; 2001. pp. 7746-52.
42. Přikrylová, J.; Procházková, J.; Podzimek, Š. Side effects of dental metal implants: impact on human health (metal as a risk factor of implantologic treatment). Biomed. Res. Int. 2019, 2019, 2519205.
43. Wang, Y.; Gregory, C.; Minor, M. A. Improving mechanical properties of molded silicone rubber for soft robotics through fabric compositing. Soft. Robot. 2018, 5, 272-90.
44. Zhang, Y.; Lu, M. A review of recent advancements in soft and flexible robots for medical applications. Int. J. Med. Robot. 2020, 16, e2096.
45. Terryn, S.; Langenbach, J.; Roels, E.; et al. A review on self-healing polymers for soft robotics. Mater. Today. 2021, 47, 187-205.
46. Cheng, Z.; Feng, W.; Zhang, Y.; et al. A highly robust amphibious soft robot with imperceptibility based on a water-stable and self-healing ionic conductor. Adv. Mater. 2023, 35, 2301005.
47. Kashef, T. S.; Terryn, S.; Cornellà, A. C.; et al. Assisted damage closure and healing in soft robots by shape memory alloy wires. Sci. Rep. 2023, 13, 8820.
48. Zhang, Z.; Ni, X.; Wu, H.; et al. Pneumatically actuated soft gripper with bistable structures. Soft. Robot. 2022, 9, 57-71.
49. Dey, K. K.; Bhandari, S.; Bandyopadhyay, D.; Basu, S.; Chattopadhyay, A. The pH taxis of an intelligent catalytic microbot. Small 2013, 9, 1916-20.
50. Miskin, M. Z.; Cortese, A. J.; Dorsey, K.; et al. Electronically integrated, mass-manufactured, microscopic robots. Nature 2020, 584, 557-61.
51. Li, J.; Li, X.; Luo, T.; et al. Development of a magnetic microrobot for carrying and delivering targeted cells. Sci. Robot. 2018, 3, eaat8829.
52. Breger, J. C.; Yoon, C.; Xiao, R.; et al. Self-folding thermo-magnetically responsive soft microgrippers. ACS. Appl. Mater. Interfaces. 2015, 7, 3398-405.
53. Del, C. F. A.; Glück, C.; Droux, J.; et al. Ultrasound trapping and navigation of microrobots in the mouse brain vasculature. Nat. Commun. 2023, 14, 5889.
54. Power, M.; Thompson, A. J.; Anastasova, S.; Yang, G. Z. A monolithic force-sensitive 3D microgripper fabricated on the tip of an optical fiber using 2-photon polymerization. Small 2018, 14, e1703964.
56. Li, Y.; Huang, G.; Zhang, X.; et al. Magnetic hydrogels and their potential biomedical applications. Adv. Funct. Mater. 2013, 23, 660-72.
57. Zhang, J.; Diller, E. Untethered miniature soft robots: modeling and design of a millimeter-scale swimming magnetic sheet. Soft. Robot. , 2018, 761-76.
58. Blumenschein, L. H.; Gan, L. T.; Fan, J. A.; Okamura, A. M.; Hawkes, E. W. A tip-extending soft robot enables reconfigurable and deployable antennas. IEEE. Robot. Autom. Lett. 2018, 3, 949-56.
59. Zhong, T.; Wei, F. A jumping soft robot driven by magnetic field. In: Liu X, Nie Z, Yu J, Xie F, Song R, editors. Intelligent Robotics and Applications. Cham: Springer International Publishing; 2021. pp. 267-74.
60. Apsite, I.; Salehi, S.; Ionov, L. Materials for smart soft actuator systems. Chem. Rev. 2022, 122, 1349-415.
61. Wang, C.; Wang, C.; Huang, Z.; Xu, S. Materials and structures toward soft electronics. Adv. Mater. 2018, 30, e1801368.
62. Brochu, P.; Pei, Q. Advances in dielectric elastomers for actuators and artificial muscles. Macromol. Rapid. Commun. 2010, 31, 10-36.
63. Shintake, J.; Shea, H.; Floreano, D. Biomimetic underwater robots based on dielectric elastomer actuators. In: 2016 IEEE/RSJ International Conference on Intelligent Robots and Systems (IROS); Daejeon, South Korea. IEEE; 2016. pp. 4957-62.
64. Qiu, Y.; Zhang, E.; Plamthottam, R.; Pei, Q. Dielectric elastomer artificial muscle: materials innovations and device explorations. Acc. Chem. Res. 2019, 52, 316-25.
65. Park, S. W.; Kim, S. J.; Park, S. H.; Lee, J.; Kim, H.; Kim, M. K. Recent progress in development and applications of ionic polymer-metal composite. Micromachines 2022, 13, 1290.
66. Branz, F.; Francesconi, A. Experimental evaluation of a dielectric elastomer robotic arm for space applications. Acta. Astronaut. 2017, 133, 324-33.
67. Vahabi, M.; Mehdizadeh, E.; Kabganian, M.; Barazandeh, F. Design and modeling of a novel in-pipe microrobot using IPMC actuators. [Internet]. In: ASME 2010 10th Biennial Conference on Engineering Systems Design and Analysis; Istanbul, Turkey. ASMEDC; 2010. pp. 281-8.
68. Nocentini, S.; Parmeggiani, C.; Martella, D.; Wiersma, D. S. Optically driven soft micro robotics. Adv. Opt. Mater. 2018, 6, 1800207.
69. Jiang, W.; Niu, D.; Liu, H.; et al. Photoresponsive soft-robotic platform: biomimetic fabrication and remote actuation. Adv. Funct. Mater. 2014, 24, 7598-604.
70. Jiang, Z. C.; Xiao, Y. Y.; Tong, X.; Zhao, Y. Selective decrosslinking in liquid crystal polymer actuators for optical reconfiguration of origami and light-fueled locomotion. Angew. Chem. Int. Ed. 2019, 131, 5386-91.
71. Ahn, C.; Liang, X.; Cai, S. Bioinspired design of light-powered crawling, squeezing, and jumping untethered soft robot. Adv. Mater. Technol. 2019, 4, 1900185.
72. Wu, J.; Ai, W.; Hou, K.; Zhang, C.; Long, Y.; Song, K. Light-driven soft climbing robot based on negative pressure adsorption. Chem. Eng. J. 2023, 466, 143131.
73. De, S.; Aluru, N.; Johnson, B.; Crone, W.; Beebe, D.; Moore, J. Equilibrium swelling and kinetics of pH-responsive hydrogels: models, experiments, and simulations. J. Microelectromech. Syst. 2002, 11, 544-55.
75. Xu, P.; Van, K. E. A.; Murdoch, W. J.; et al. Anticancer efficacies of cisplatin-releasing pH-responsive nanoparticles. Biomacromolecules 2006, 7, 829-35.
76. Loepfe, M. Combustion-driven soft machines: design, manufacturing and application. 2016. Available from: https://www.research-collection.ethz.ch/bitstream/handle/20.500.11850/117172/eth-49181-01.pdf. [Last accessed on 13 Jan 2025].
77. Gupta, P.; Vermani, K.; Garg, S. Hydrogels: from controlled release to pH-responsive drug delivery. Drug. Discov. Today. 2002, 7, 569-79.
78. He, Z.; Yang, Y.; Jiao, P.; Wang, H.; Lin, G.; Pähtz, T. Copebot: underwater soft robot with copepod-like locomotion. Soft. Robot. 2023, 10, 314-25.
79. Tolley, M. T.; Shepherd, R. F.; Karpelson, M.; et al. An untethered jumping soft robot. In: 2014 IEEE/RSJ International Conference on Intelligent Robots and Systems; Chicago, USA. IEEE; 2014. pp. 561-6.
80. Xian, S.; Webber, M. J. Temperature-responsive supramolecular hydrogels. J. Mater. Chem. B. 2020, 8, 9197-211.
81. Jochum, F. D.; Theato, P. Temperature- and light-responsive smart polymer materials. Chem. Soc. Rev. 2013, 42, 7468-83.
82. Dai, H.; Chen, Q.; Qin, H.; et al. A temperature-responsive copolymer hydrogel in controlled drug delivery. Macromolecules 2006, 39, 6584-9.
83. Yang, H.; Xu, M.; Li, W.; Zhang, S. Design and Implementation of a soft robotic arm driven by SMA coils. IEEE. Trans. Ind. Electron. 2019, 66, 6108-16.
84. Feng, R.; Zhang, Y.; Liu, J.; Zhang, Y.; Li, J.; Baoyin, H. Soft robotic perspective and concept for planetary small body exploration. Soft. Robot. 2022, 9, 889-99.
85. Wu, S.; Hong, Y.; Zhao, Y.; Yin, J.; Zhu, Y. Caterpillar-inspired soft crawling robot with distributed programmable thermal actuation. Sci. Adv. 2023, 9, eadf8014.
86. Katzschmann, R. K.; DelPreto, J.; MacCurdy, R.; Rus, D. Exploration of underwater life with an acoustically controlled soft robotic fish. Sci. Robot. 2018, 3, eaar3449.
87. Lindenroth, L.; Housden, R. J.; Wang, S.; Back, J.; Rhode, K.; Liu, H. Design and integration of a parallel, soft robotic end-effector for extracorporeal ultrasound. IEEE. Trans. Biomed. Eng. 2020, 67, 2215-29.
88. Walker, J.; Zidek, T.; Harbel, C.; et al. Soft robotics: a review of recent developments of pneumatic soft actuators. Actuators 2020, 9, 3.
89. Roche, E. T.; Horvath, M. A.; Wamala, I.; et al. Soft robotic sleeve supports heart function. Sci. Transl. Med. 2017, 9, eaaf3925.
90. Liu, J.; Yin, L.; Chandler, J. H.; Chen, X.; Valdastri, P.; Zuo, S. A dual-bending endoscope with shape-lockable hydraulic actuation and water-jet propulsion for gastrointestinal tract screening. Int. J. Med. Robot. 2021, 17, 1-13.
91. Galloway, K. C.; Becker, K. P.; Phillips, B.; et al. Soft robotic grippers for biological sampling on deep reefs. Soft. Robot. 2016, 3, 23-33.
92. Palmieri, P.; Melchiorre, M.; Mauro, S. Design of a lightweight and deployable soft robotic arm. Robotics 2022, 11, 88.
93. Der, M. P. A.; Djambazi, B.; Haberthur, Y.; et al. RoBoa: construction and evaluation of a steerable vine robot for search and rescue applications. In: 2021 IEEE 4th International Conference on Soft Robotics (RoboSoft); New Haven, USA. IEEE; 2021. pp. 15-20.
94. Talas, S. K.; Baydere, B. A.; Altinsoy, T.; Tutcu, C.; Samur, E. Design and development of a growing pneumatic soft robot. Soft. Robot. 2020, 7, 521-33.
95. Stella, F.; Hughes, J. The science of soft robot design: a review of motivations, methods and enabling technologies. Front. Robot. AI. 2022, 9, 1059026.
96. Hartmann, F.; Baumgartner, M.; Kaltenbrunner, M. Becoming sustainable, the new frontier in soft robotics. Adv. Mater. 2021, 33, e2004413.
97. Wang, D.; Wang, J.; Shen, Z.; et al. Soft actuators and robots enabled by additive manufacturing. Annu. Rev. Control. Robot. Auton. Syst. 2023, 6, 31-63.
98. Hegde, C.; Su, J.; Tan, J. M. R.; He, K.; Chen, X.; Magdassi, S. Sensing in soft robotics. ACS. Nano. 2023, 17, 15277-307.
99. Hajra, S.; Panda, S.; Khanberh, H.; et al. Revolutionizing self-powered robotic systems with triboelectric nanogenerators. Nano. Energy. 2023, 115, 108729.
100. Armanini, C.; Boyer, F.; Mathew, A. T.; Duriez, C.; Renda, F. Soft robots modeling: a structured overview. IEEE. Trans. Robot. 2023, 39, 1728-48.
101. Patel, D. K.; Huang, X.; Luo, Y.; et al. Highly dynamic bistable soft actuator for reconfigurable multimodal soft robots. Adv. Mater. Technol. 2023, 8, 2201259.
102. Pal, S. Mechanical properties of biological materials. In: Design of artificial human joints & organs. Boston: Springer; 2014. pp. 23-40.
103. Li-Baboud, Y. S.; Virts, A.; Bostelman, R.; et al. Evaluation methods and measurement challenges for industrial exoskeletons. Sensors 2023, 23, 5604.
104. Paternò, L.; Lorenzon, L. Soft robotics in wearable and implantable medical applications: translational challenges and future outlooks. Front. Robot. AI. 2023, 10, 1075634.
105. Yin, S.; Jia, Z.; Li, X.; Zhu, J.; Xu, Y.; Li, T. Machine-learning-accelerated design of functional structural components in deep-sea soft robots. Extreme. Mech. Lett. 2022, 52, 101635.
106. Katzschmann, R. K.; Marchese, A. D.; Rus, D. Hydraulic autonomous soft robotic fish for 3D swimming. In: Hsieh MA, Khatib O, Kumar V, editors. Experimental Robotics. Cham: Springer International Publishing; 2016. pp. 405-20.
107. Wen, T.; Hu, J.; Zhang, J.; Li, X.; Kang, S.; Zhang, N. Design, performance analysis, and experiments of a soft robot for rescue. J. Mech. Robot. 2024, 16, 071011.
109. Lukaski, H. C.; Bolonchuk, W. W. Estimation of body fluid volumes using tetrapolar bioelectrical impedance measurements. Aviat. Space. Environ. Med. 1988, 59, 1163-9.
110. Al-Shura, A. N. Holism. In: Integrative cardiovascular Chinese medicine. Elsevier; 2014. pp. 3-26. Available from: https://books.google.com/books?hl=zh-CN&lr=&id=i1gXAwAAQBAJ&oi=fnd&pg=PP1&dq=Integrative+Cardiovascular+Chinese+Medicine&ots=-N_4hWGvUg&sig=UKyIyyFsPyToM_6_RKgqxHBRUrE#v=onepage&q=Integrative%20Cardiovascular%20Chinese%20Medicine&f=false. [Last accessed on 13 Jan 2025].
111. Gaohua, L.; Miao, X.; Dou, L. Crosstalk of physiological pH and chemical pKa under the umbrella of physiologically based pharmacokinetic modeling of drug absorption, distribution, metabolism, excretion, and toxicity. Expert. Opin. Drug. Metab. Toxicol. 2021, 17, 1103-24.
112. Baldwin, D. R.; Marshall, W. J. Heavy metal poisoning and its laboratory investigation. Ann. Clin. Biochem. 1999, 36, 267-300.
113. Su, Y.; Ma, C.; Chen, J.; et al. Printable, highly sensitive flexible temperature sensors for human body temperature monitoring: a review. Nanoscale. Res. Lett. 2020, 15, 200.
114. Ogunrinola, G. A.; Oyewale, J. O.; Oshamika, O. O.; Olasehinde, G. I. The human microbiome and its impacts on health. Int. J. Microbiol. 2020, 2020, 8045646.
115. Zhang, Y. J.; Li, S.; Gan, R. Y.; Zhou, T.; Xu, D. P.; Li, H. B. Impacts of gut bacteria on human health and diseases. Int. J. Mol. Sci. 2015, 16, 7493-519.
116. Zrinscak, D.; Lorenzon, L.; Maselli, M.; Cianchetti, M. Soft robotics for physical simulators, artificial organs and implantable assistive devices. Prog. Biomed. Eng. 2023, 5, 012002.
117. Runciman, M.; Darzi, A.; Mylonas, G. P. Soft robotics in minimally invasive surgery. Soft. Robot. 2019, 6, 423-43.
118. Banerjee, S.; Saharan, V. A. Soft robots for the delivery of drugs. In: Saharan VA, editor. Computer aided pharmaceutics and drug delivery. Singapore: Springer Nature; 2022. pp. 415-38.
119. Marchese, A. D.; Katzschmann, R. K.; Rus, D. A recipe for soft fluidic elastomer robots. Soft. Robot. 2015, 2, 7-25.
120. Andriot, M.; DeGroot, J. V.; Meeks, R.; et al. Silicones in industrial applications. 2009. Available from: https://www.researchgate.net/publication/251935579_Silicones_in_Industrial_Applications. [Last accessed on 13 Jan 2025].
121. Elango, N.; Faudzi, A. A. M. A review article: investigations on soft materials for soft robot manipulations. Int. J. Adv. Manuf. Technol. 2015, 80, 1027-37.
122. Krpovic, S.; Dam-Johansen, K.; Skov, A. L. Importance of Mullins effect in commercial silicone elastomer formulations for soft robotics. J. Appl. Polym. Sci. 2021, 138, 50380.
123. Garcia, L.; Kerns, G.; O’Reilley, K.; et al. The role of soft robotic micromachines in the future of medical devices and personalized medicine. Micromachines 2021, 13, 28.
124. Banerjee, H.; Suhail, M.; Ren, H. Hydrogel actuators and sensors for biomedical soft robots: brief overview with impending challenges. Biomimetics 2018, 3, 15.
125. Ionov, L. Hydrogel-based actuators: possibilities and limitations. Mater. Today. 2014, 17, 494-503.
126. Shi, Q.; Liu, H.; Tang, D.; Li, Y.; Li, X.; Xu, F. Bioactuators based on stimulus-responsive hydrogels and their emerging biomedical applications. NPG. Asia. Mater. 2019, 11, 165.
127. Mishra, A. K.; Wallin, T. J.; Pan, W.; et al. Autonomic perspiration in 3D-printed hydrogel actuators. Sci. Robot. 2020, 5, eaaz3918.
128. Tang, N.; Peng, Z.; Guo, R.; et al. Thermal transport in soft PAAm hydrogels. Polymers 2017, 9, 688.
129. Edward, S.; Golecki, H. M. Gelatin soft actuators: benefits and opportunities. Actuators 2023, 12, 63.
130. Azevedo, H. S.; Santos, T. C.; Reis, R. L. 4 - Controlling the degradation of natural polymers for biomedical applications. In: Natural-based polymers for biomedical applications. Elsevier; 2008. pp. 106-28.
131. El-atab, N.; Mishra, R. B.; Al-modaf, F.; et al. Soft actuators for soft robotic applications: a review. Adv. Intell. Syst. 2020, 2, 2000128.
132. Byrne, O.; Coulter, F.; Glynn, M.; et al. Additive manufacture of composite soft pneumatic actuators. Soft. Robot. 2018, 5, 726-36.
133. Liang, W.; Liu, H.; Wang, K.; Qian, Z.; Ren, L.; Ren, L. Comparative study of robotic artificial actuators and biological muscle. Adv. Mech. Eng. 2020, 12, 1687814020933409.
135. Rusu, D. M.; Mândru, S. D.; Biriș, C. M.; Petrașcu, O. L.; Morariu, F.; Ianosi-Andreeva-Dimitrova, A. Soft robotics: a systematic review and bibliometric analysis. Micromachines 2023, 14, 359.
136. Hu, L.; Bonnemain, J.; Saeed, M. Y.; et al. An implantable soft robotic ventilator augments inspiration in a pig model of respiratory insufficiency. Nat. Biomed. Eng. 2023, 7, 110-23.
137. Zaidi, S.; Maselli, M.; Laschi, C.; Cianchetti, M. Actuation technologies for soft robot grippers and manipulators: a review. Curr. Robot. Rep. 2021, 2, 355-69.
138. Shi, H.; Tan, K.; Zhang, B.; Liu, W. Review on research progress of hydraulic powered soft actuators. Energies 2022, 15, 9048.
139. Runciman, M.; Franco, E.; Avery, J.; Rodriguez, B. F.; Mylonas, G. Model based position control of soft hydraulic actuators. In: 2023 IEEE International Conference on Robotics and Automation (ICRA); London, United Kingdom. IEEE; 2023. pp. 2676-82.
140. Thai, M. T.; Phan, P. T.; Hoang, T. T.; Low, H.; Lovell, N. H.; Do, T. N. Design, fabrication, and hysteresis modeling of soft microtubule artificial muscle (SMAM) for medical applications. IEEE. Robot. Autom. Lett. 2021, 6, 5089-96.
141. Lee, J. G.; Raj, R. R.; Thome, C. P.; et al. Bubble-based microrobots with rapid circular motions for epithelial pinning and drug delivery. Small 2023, 19, e2300409.
142. Deng, N.; Li, J.; Lyu, H.; Huang, R.; Liu, H.; Guo, C. Degradable silk-based soft actuators with magnetic responsiveness. J. Mater. Chem. B. 2022, 10, 7650-60.
143. Yang, Z.; Zhang, L. Magnetic actuation systems for miniature robots: a review. Adv. Intell. Syst. 2020, 2, 2000082.
144. Hu, X.; Zhou, Y.; Li, M.; Wu, J.; He, G.; Jiao, N. Catheter-assisted bioinspired adhesive magnetic soft millirobot for drug delivery. Small 2024, 20, e2306510.
145. Yang, W.; Wang, X.; Ge, Z.; Yu, H. Magnetically controlled millipede inspired soft robot for releasing drugs on target area in stomach. IEEE. Robot. Autom. Lett. 2024, 9, 3846-53.
146. Kaufman, G.; Jimenez, J.; Bradshaw, A.; et al. A stiff-soft composite fabrication strategy for fiber optic tethered microtools. Adv. Mater. Technol. 2023, 8, 2202034.
147. Zmyślony, M.; Dradrach, K.; Haberko, J.; Nałęcz-Jawecki, P.; Rogóż, M.; Wasylczyk, P. Optical pliers: micrometer-scale, light-driven tools grown on optical fibers. Adv. Mater. 2020, 32, e2002779.
148. Leber, A.; Dong, C.; Laperrousaz, S.; et al. Highly integrated multi-material fibers for soft robotics. Adv. Sci. 2023, 10, e2204016.
149. Song, S.; Fallegger, F.; Trouillet, A.; Kim, K.; Lacour, S. P. Deployment of an electrocorticography system with a soft robotic actuator. Sci. Robot. 2023, 8, eadd1002.
150. Wei, L.; Huang, J.; Yan, Y.; et al. Substrate-independent, mechanically tunable, and scalable gelatin methacryloyl hydrogel coating with drag-reducing and anti-freezing properties. ACS. Appl. Polym. Mater. 2022, 4, 4876-85.
151. Xu, Y.; Hu, X.; Kundu, S.; et al. Silicon-based sensors for biomedical applications: a review. Sensors 2019, 19, 2908.
152. Engin, M.; Demirel, A.; Engin, E. Z.; Fedakar, M. Recent developments and trends in biomedical sensors. Measurement 2005, 37, 173-88.
153. Pang, Q.; Hu, H.; Zhang, H.; Qiao, B.; Ma, L. Temperature-responsive ionic conductive hydrogel for strain and temperature sensors. ACS. Appl. Mater. Interfaces. , 2022, 26536-47.
154. Zhai, D.; Liu, B.; Shi, Y.; et al. Highly sensitive glucose sensor based on pt nanoparticle/polyaniline hydrogel heterostructures. ACS. Nano. 2013, 7, 3540-6.
155. Lin, P. H.; Sheu, S. C.; Chen, C. W.; Huang, S. C.; Li, B. R. Wearable hydrogel patch with noninvasive, electrochemical glucose sensor for natural sweat detection. Talanta 2022, 241, 123187.
156. Qiu, Y.; Ashok, A.; Nguyen, C. C.; Yamauchi, Y.; Do, T. N.; Phan, H. P. Integrated sensors for soft medical robotics. Small 2024, 20, e2308805.
157. Qasaimeh, M. A.; Sokhanvar, S.; Dargahi, J.; Kahrizi, M. PVDF-based microfabricated tactile sensor for minimally invasive surgery. J. Microelectromech. Syst. 2009, 18, 195-207.
158. Li, W.; Liu, A.; Wang, Y.; et al. Implantable and degradable wireless passive protein-based tactile sensor for intracranial dynamic pressure detection. Electronics 2023, 12, 2466.
159. Chen, J.; Zhu, Y.; Chang, X.; et al. Recent progress in essential functions of soft electronic skin. Adv. Funct. Mater. 2021, 31, 2104686.
160. Lyu, Q.; Gong, S.; Lees, J. G.; et al. A soft and ultrasensitive force sensing diaphragm for probing cardiac organoids instantaneously and wirelessly. Nat. Commun. 2022, 13, 7259.
161. Kim, D. S.; Choi, Y. W.; Shanmugasundaram, A.; et al. Highly durable crack sensor integrated with silicone rubber cantilever for measuring cardiac contractility. Nat. Commun. 2020, 11, 535.
162. Pignanelli, J.; Schlingman, K.; Carmichael, T. B.; Rondeau-Gagné, S.; Ahamed, M. J. A comparative analysis of capacitive-based flexible PDMS pressure sensors. Sens. Actuators. A. Phys. 2019, 285, 427-36.
163. Wang, C.; Hu, Y.; Liu, Y.; et al. Tissue-adhesive piezoelectric soft sensor for in vivo blood pressure monitoring during surgical operation. Adv. Funct. Mater. 2023, 33, 2303696.
164. Laschi, C.; Calisti, M. Soft robot reaches the deepest part of the ocean. Nature 2021, 591, 35-6.
165. Calisti, M. Soft robotics in underwater legged locomotion: from octopus–inspired solutions to running robots. In: Laschi C, Rossiter J, Iida F, Cianchetti M, Margheri L, editors. Soft robotics: trends, applications and challenges. Cham: Springer International Publishing; 2017. pp. 31-6.
166. García-Valdovinos, L. G.; Salgado-Jiménez, T.; Bandala-Sánchez, M.; Nava-Balanzar, L.; Hernández-Alvarado, R.; Cruz-Ledesma, J. A. Modelling, design and robust control of a remotely operated underwater vehicle. Int. J. Adv. Robot. Syst. 2014, 11, 1.
167. Wang, R.; Zhang, C.; Zhang, Y.; Tan, W.; Chen, W.; Liu, L. Soft underwater swimming robots based on artificial muscle. Adv. Mater. Technol. 2023, 8, 2200962.
168. Gomis-Bellmunt, O.; Campanile, F.; Galceran-Arellano, S.; Montesinos-Miracle, D.; Rull-Duran, J. Hydraulic actuator modeling for optimization of mechatronic and adaptronic systems. Mechatronics 2008, 18, 634-40.
169. Wang, R.; Zhang, C.; Zhang, Y.; et al. Fast-swimming soft robotic fish actuated by bionic muscle. Soft. Robot. 2024, 11, 845-56.
170. Zou, T.; Jian, X.; Al-tamimi, M.; Wu, X.; Wu, J. Development of a low-cost soft robot fish with biomimetic swimming performance. J. Mech. Robot. 2024, 16, 061004.
171. Luo, R.; Li, S.; Wang, F. Design and motion characteristics analysis of underwater biomimetic jellyfish based on shape memory alloy springs. Ocean. Eng. 2024, 297, 117069.
172. Gong, H.; Li, Z.; Meng, F.; Tan, B.; Hou, S. Octopus predation-inspired underwater robot capable of adsorption through opening and closing claws. Appl. Sci. 2024, 14, 2250.
173. Hu, F.; Kou, Z.; Sefene, E. M.; Mikolajczyk, T. An origami flexiball-inspired soft robotic jellyfish. JMSE. 2023, 11, 714.
174. Ma, H.; Zhou, J. Modeling, characterization, and application of soft bellows-type pneumatic actuators for bionic locomotion. Acta. Mech. Solida. Sin. 2023, 36, 1-12.
175. Chen, S.; Xu, H.; Xiong, X.; Lu, B. An underwater jet-propulsion soft robot with high flexibility driven by water hydraulics. In: 2023 IEEE International Conference on Robotics and Automation (ICRA); London, United Kingdom. IEEE; 2023. pp. 2613-9.
176. Rajput G, Vora J, Prajapati P, Chaudhari R. Areas of recent developments for shape memory alloy: a review. Mater. Today. Proc. 2022, 62, 7194-8.
177. Ulloa C, Terrile S, Barrientos A. Soft underwater robot actuated by shape-memory alloys “JellyRobcib” for path tracking through fuzzy visual control. Appl. Sci. 2020, 10, 7160.
178. Gu, G. Y.; Zhu, J.; Zhu, L. M.; Zhu, X. A survey on dielectric elastomer actuators for soft robots. Bioinspir. Biomim. 2017, 12, 011003.
179. Wang, Y.; Ma, X.; Jiang, Y.; et al. Dielectric elastomer actuators for artificial muscles: a comprehensive review of soft robot explorations. Res. Chem. Mater. 2022, 1, 308-24.
180. Shintake, J.; Cacucciolo, V.; Shea, H.; Floreano, D. Soft biomimetic fish robot made of dielectric elastomer actuators. Soft. Robot. 2018, 5, 466-74.
181. Christianson, C.; Goldberg, N. N.; Deheyn, D. D.; Cai, S.; Tolley, M. T. Translucent soft robots driven by frameless fluid electrode dielectric elastomer actuators. Sci. Robot. 2018, 3, eaat1893.
182. Fu, R.; Guan, Y.; Xiao, C.; et al. Tough and highly efficient underwater self-repairing hydrogels for soft electronics. Small. Methods. 2022, 6, e2101513.
183. Qi, X.; Zhao, H.; Wang, L.; et al. Underwater sensing and warming E-textiles with reversible liquid metal electronics. Chem. Eng. J. 2022, 437, 135382.
184. Lin, Y.; Siddall, R.; Schwab, F.; et al. Modeling and control of a soft robotic fish with integrated soft sensing. Adv. Intell. Syst. 2023, 5, 2000244.
185. Hao, M.; Wang, Y.; Zhu, Z.; He, Q.; Zhu, D.; Luo, M. A compact review of IPMC as soft actuator and sensor: current trends, challenges, and potential solutions from our recent work. Front. Robot. AI. 2019, 6, 129.
186. Shen, Q.; Wang, T.; Kim, K. J. A biomimetic underwater vehicle actuated by waves with ionic polymer-metal composite soft sensors. Bioinspir. Biomim. 2015, 10, 055007.
187. Minaian, N.; Olsen, Z. J.; Kim, K. J. Ionic polymer-metal composite (IPMC) artificial muscles in underwater environments: review of actuation, sensing, controls, and applications to soft robotics. In: Paley DA, Wereley NM, editors. Bioinspired sensing, actuation, and control in underwater soft robotic systems. Cham: Springer International Publishing; 2021. pp. 117-39.
188. Abdulsadda, A. T.; Tan, X. Underwater source localization using an IPMC-based artificial lateral line. In: 2011 IEEE International Conference on Robotics and Automation; Shanghai, China. IEEE; 2011. pp. 2719-24.
189. Levchenko, I.; Bazaka, K.; Belmonte, T.; Keidar, M.; Xu, S. Advanced materials for next-generation spacecraft. Adv. Mater. 2018, 30, e1802201.
190. Araromi, O. A.; Gavrilovich, I.; Shintake, J.; et al. Rollable multisegment dielectric elastomer minimum energy structures for a deployable microsatellite gripper. IEEE/ASME. Trans. Mechatron. 2015, 20, 438-46.
191. Ogliani, E.; Yu, L.; Mazurek, P.; Skov, A. L. Designing reliable silicone elastomers for high-temperature applications. Polym. Degrad. Stab. 2018, 157, 175-80.
192. Porte, E.; Eristoff, S.; Agrawala, A.; Kramer-Bottiglio, R. Characterization of temperature and humidity dependence in soft elastomer behavior. Soft. Robot. 2024, 11, 118-30.
193. Mirvakili, S. M.; Leroy, A.; Sim, D.; Wang, E. N. Solar-driven soft robots. Adv. Sci. 2021, 8, 2004235.
194. Menon, C.; Carpi, F.; De, R. D. Concept design of novel bio-inspired distributed actuators for space applications. Acta. Astronautica. 2009, 65, 825-33.
195. Jing, Z.; Li, Q.; Su, W.; Chen, Y. Dielectric elastomer-driven bionic inchworm soft robot realizes forward and backward movement and jump. Actuators 2022, 11, 227.
196. Romano, D.; Di, G. A.; Pucciariello, C.; Stefanini, C. Turning earthworms into moonworms: earthworms colonization of lunar regolith as a bioengineering approach supporting future crop growth in space. Heliyon 2023, 9, e14683.
197. Giordano, M.; Ciriello, M.; Formisano, L.; et al. Iodine-biofortified microgreens as high nutraceutical value component of space mission crew diets and candidate for extraterrestrial cultivation. Plants 2023, 12, 2628.
198. Caporale, A. G.; Paradiso, R.; Liuzzi, G.; Arouna, N.; De, P. S.; Adamo, P. Can peat amendment of mars regolith simulant allow soybean cultivation in mars bioregenerative life support systems? Plants 2022, 12, 64.
199. Hammond, M.; Dempsey, A.; Ward, W.; et al. A hybrid soft material robotic end-effector for reversible in-space assembly of strut components. Front. Robot. AI. 2023, 10, 1099297.
200. Molaei, P.; Pitts, N. A.; Palardy, G.; et al. Cable decoupling and cable-based stiffening of continuum robots. IEEE. Access. 2022, 10, 104852-62.
201. Krishen, K. Space applications for ionic polymer-metal composite sensors, actuators, and artificial muscles. Acta. Astronautica. 2009, 64, 1160-6.
202. Fu, M.; Zhang, J.; Jin, Y.; Zhao, Y.; Huang, S.; Guo, C. F. A highly sensitive, reliable, and high-temperature-resistant flexible pressure sensor based on ceramic nanofibers. Adv. Sci. 2020, 7, 2000258.
203. Fan, W.; He, Q.; Meng, K.; et al. Machine-knitted washable sensor array textile for precise epidermal physiological signal monitoring. Sci. Adv. 2020, 6, eaay2840.
204. Akbari, A.; Chhabra, P. S.; Bhandari, U.; Bernardini, S. Intelligent exploration and autonomous navigation in confined spaces. In: 2020 IEEE/RSJ International Conference on Intelligent Robots and Systems (IROS); Las Vegas, USA. IEEE; 2020. pp. 2157-64.
205. Greer, D.; McKerrow, P.; Abrantes, J. Robots in urban search and rescue operations. In: Australasian Conference on Robotics and Automation. Auckland. 2002. Available from: https://citeseerx.ist.psu.edu/document?repid=rep1&type=pdf&doi=f89059556985a4456bd84591aeca6879ba549c97. [Last accessed on 13 Jan 2025]
206. Blumenschein, L. H.; Koehler, M.; Usevitch, N. S.; Hawkes, E. W.; Rucker, D. C.; Okamura, A. M. Geometric solutions for general actuator routing on inflated-beam soft growing robots. IEEE. Trans. Robot. 2022, 38, 1820-40.
207. El-Hussieny, H.; Hameed, I. A.; Zaky, A. B. Plant-inspired soft growing robots: a control approach using nonlinear model predictive techniques. Appl. Sci. 2023, 13, 2601.
208. Liu, X.; Song, M.; Fang, Y.; Zhao, Y.; Cao, C. Worm-inspired soft robots enable adaptable pipeline and tunnel inspection. Adv. Intell. Syst. 2022, 4, 2100128.
209. Wang, N.; Zhang, Y.; Zhang, G.; Zhao, W.; Peng, L. Development and analysis of key components of a multi motion mode soft-bodied pipe robot. Actuators 2022, 11, 125.
210. Yeh, C.; Chen, C.; Juang, J. Soft hopping and crawling robot for in-pipe traveling. Extreme. Mech. Lett. 2020, 39, 100854.
211. Singh, G.; Patiballa, S.; Zhang, X.; Krishnan, G. A pipe-climbing soft robot. In: 2019 International Conference on Robotics and Automation (ICRA); Montreal, Canada. IEEE; 2019. pp. 8450-6.
212. Saleeby, K. S. Design of soft-body robot with wireless communication for leak detection in large diameter pipe systems. 2017. Available from: https://dspace.mit.edu/handle/1721.1/112547. [Last accessed on 13 Jan 2025].
213. Wang, J.; Song, Y.; Zadan, M.; et al. Wireless actuation for soft electronics-free robots. In: Proceedings of the 29th Annual International Conference on Mobile Computing and Networking. Madrid; Spain. ACM; 2023. pp. 1-16.
214. Usevitch, N. S.; Hammond, Z. M.; Schwager, M.; Okamura, A. M.; Hawkes, E. W.; Follmer, S. An untethered isoperimetric soft robot. Sci. Robot. 2020, 5, eaaz0492.
215. Shepherd, R. F.; Stokes, A. A.; Freake, J.; et al. Using explosions to power a soft robot. Angew. Chem. Int. Ed. Engl. 2013, 52, 2892-6.
216. Mazzolai, B.; Mondini, A.; Tramacere, F.; et al. Octopus-inspired soft arm with suction cups for enhanced grasping tasks in confined environments. Adv. Intell. Syst. 2019, 1, 1900041.
217. Khatib, M.; Zohar, O.; Haick, H. Self-healing soft sensors: from material design to implementation. Adv. Mater. 2021, 33, e2004190.
218. Zhang, W.; Wu, B.; Sun, S.; Wu, P. Skin-like mechanoresponsive self-healing ionic elastomer from supramolecular zwitterionic network. Nat. Commun. 2021, 12, 4082.
219. Georgopoulou, A.; Bosman, A. W.; Brancart, J.; Vanderborght, B.; Clemens, F. Supramolecular self-healing sensor fiber composites for damage detection in piezoresistive electronic skin for soft robots. Polymers 2021, 13, 2983.
220. Laschi, C.; Thuruthel, T. G.; Lida, F.; Merzouki, R.; Falotico, E. Learning-based control strategies for soft robots: theory, achievements, and future challenges. IEEE. Control. Syst. 2023, 43, 100-13.
221. Kim, S.; Laschi, C.; Trimmer, B. Soft robotics: a bioinspired evolution in robotics. Trends. Biotechnol. 2013, 31, 287-94.
222. Villanueva, A.; Smith, C.; Priya, S. A biomimetic robotic jellyfish (Robojelly) actuated by shape memory alloy composite actuators. Bioinspir. Biomim. 2011, 6, 036004.
223. Zhang, H.; Kumar, A. S.; Fuh, J. Y. H.; Wang, M. Y. Design and development of a topology-optimized three-dimensional printed soft gripper. Soft. Robot. 2018, 5, 650-61.
224. Chen, F.; Wang, M. Y. Design optimization of soft robots: a review of the state of the art. IEEE. Robot. Automat. Mag. 2020, 27, 27-43.
225. Zhu, J.; Zhang, W.; Xia, L. Topology optimization in aircraft and aerospace structures design. Arch. Computat. Methods. Eng. 2016, 23, 595-622.
226. Yang, R. J.; Chahande, A. I. Automotive applications of topology optimization. Struct. Optim. 1995, 9, 245-9.
227. Golecki, T.; Gomez, F.; Carrion, J.; Spencer, B. F. Bridge topology optimization considering stochastic moving traffic. Eng. Struct. 2023, 292, 116498.
228. Liu, C. H.; Chen, T. L.; Chiu, C. H.; et al. Optimal design of a soft robotic gripper for grasping unknown objects. Soft. Robot. 2018, 5, 452-65.
229. Chen, F.; Xu, W.; Zhang, H.; et al. Topology optimized design, fabrication, and characterization of a soft cable-driven gripper. IEEE. Robot. Autom. Lett. 2018, 3, 2463-70.
230. Xing, J.; Luo, Y.; Deng, Y.; Wu, S.; Gai, Y. Topology optimization design of deformable flexible thermoelectric devices for voltage enhancement. Eng. Optim. 2023, 55, 1686-703.
231. Sanders, E. D.; Pereira, A.; Paulino, G. H. Optimal and continuous multilattice embedding. Sci. Adv. 2021, 7, eabf4838.
232. Wallin, M.; Tortorelli, D. A. Nonlinear homogenization for topology optimization. Mech. Mater. 2020, 145, 103324.
233. Jumet, B.; Bell, M. D.; Sanchez, V.; Preston, D. J. A data-driven review of soft robotics. Adv. Intell. Syst. 2022, 4, 2100163.
234. Liu, B.; Sha, L.; Huang, K.; Zhang, W.; Yang, H. A topology optimization method for collaborative robot lightweight design based on orthogonal experiment and its applications. Int. J. Adv. Robot. Syst. 2022, 19, 17298814211056143.
235. Zheng, Y.; Cao, L.; Qian, Z.; Chen, A.; Zhang, W. Topology optimization of a fully compliant prosthetic finger: design and testing. In: 2016 6th IEEE International Conference on Biomedical Robotics and Biomechatronics (BioRob); Singapore, Singapore. IEEE; 2016. pp. 1029-34.
236. Li, D.; Chen, S.; Song, Z.; Liang, J.; Zhu, X.; Chen, F. Tailoring the in-plane and out-of-plane stiffness of soft fingers by endoskeleton topology optimization for stable grasping. Sci. China. Technol. Sci. 2023, 66, 3080-9.
237. Sun, Y.; Zong, C.; Pancheri, F.; Chen, T.; Lueth, T. C. Design of topology optimized compliant legs for bio-inspired quadruped robots. Sci. Rep. 2023, 13, 4875.
238. Al-Tamimi, A. A.; Peach, C.; Fernandes, P. R.; Cseke, A.; Bartolo, P. J. Topology optimization to reduce the stress shielding effect for orthopedic applications. Procedia. CIRP. 2017, 65, 202-6.
239. Sato, Y.; Kobayashi, H.; Yuhn, C.; Kawamoto, A.; Nomura, T.; Kikuchi, N. Topology optimization of locomoting soft bodies using material point method. Struct. Multidisc. Optim. 2023, 66, 3502.
240. Gillespie, M. T.; Best, C. M.; Townsend, E. C.; Wingate, D.; Killpack, M. D. Learning nonlinear dynamic models of soft robots for model predictive control with neural networks. In: 2018 IEEE International Conference on Soft Robotics (RoboSoft); Livorno, Italy. IEEE; 2018. pp. 39-45.
241. Goodwin, G. C.; Graebe, S. F.; Salgado, M. E. Control system design. Available from: https://www.academia.edu/23184065/CONTROL_SYSTEM_DESIGN. [Last accessed on 13 Jan 2025].
242. Runciman, M.; Avery, J.; Darzi, A.; Mylonas, G. Open loop position control of soft hydraulic actuators for minimally invasive surgery. Appl. Sci. 2021, 11, 7391.
243. Cianchetti, M.; Laschi, C.; Menciassi, A.; Dario, P. Biomedical applications of soft robotics. Nat. Rev. Mater. 2018, 3, 143-53.
244. Beatty, R.; Mendez, K. L.; Schreiber, L. H. J.; et al. Soft robot-mediated autonomous adaptation to fibrotic capsule formation for improved drug delivery. Sci. Robot. 2023, 8, eabq4821.
245. Grube, M.; Wieck, J. C.; Seifried, R. Comparison of modern control methods for soft robots. Sensors 2022, 22, 9464.
246. Tonkens, S.; Lorenzetti, J.; Pavone, M. Soft robot optimal control via reduced order finite element models. In: 2021 IEEE International Conference on Robotics and Automation (ICRA); Xi’an, China. IEEE; 2021. pp. 12010-6.
247. Ding, L.; Niu, L.; Su, Y.; et al. Dynamic finite element modeling and simulation of soft robots. Chin. J. Mech. Eng. 2022, 35, 701.
248. Youssef, S. M.; Soliman, M.; Saleh, M. A.; Mousa, M. A.; Elsamanty, M.; Radwan, A. G. Underwater soft robotics: a review of bioinspiration in design, actuation, modeling, and control. Micromachines 2022, 13, 110.
249. Vikas, V.; Grover, P.; Trimmer, B. Model-free control framework for multi-limb soft robots. In: 2015 IEEE/RSJ International Conference on Intelligent Robots and Systems (IROS); Hamburg, Germany. IEEE; 2015. pp. 1111-6.
250. Li, Y.; Ang, K. H.; Chong, G. C. Y. PID control system analysis and design. IEEE. Control. Syst. May. 2006, 26, 32-41.
251. Isidro, I. A.; Pais, D. A. M.; Alves, P. M.; Carrondo, M. J. T. 2.64 - Online control strategies. In: Comprehensive Biotechnology. Elsevier; 2019. pp. 943-51.
252. Landau, I. D.; Lozano, R.; M’Saad, M.; Karimi, A. Adaptive control: algorithms, analysis and applications. 2nd edition. London: Springer; 2011.
253. Zhang, D.; Wei, B. A review on model reference adaptive control of robotic manipulators. Annu. Rev. Control. 2017, 43, 188-98.
254. Singh, R.; Bhushan, B. Reinforcement learning-based model-free controller for feedback stabilization of robotic systems. IEEE. Trans. Neural. Netw. Learn. Syst. 2023, 34, 7059-73.
255. Lewis, F. L.; Vrabie, D. Reinforcement learning and adaptive dynamic programming for feedback control. IEEE. Circuits. Syst. Mag. 2009, 9, 32-50.
256. Li, G.; Shintake, J.; Hayashibe, M. Deep reinforcement learning framework for underwater locomotion of soft robot. In: 2021 IEEE International Conference on Robotics and Automation (ICRA); Xi’an, China. IEEE; 2021. pp. 12033-9.
257. Thuruthel, T. G.; Falotico, E.; Manti, M.; Laschi, C. Stable open loop control of soft robotic manipulators. IEEE. Robot. Autom. Lett. 2018, 3, 1292-8.
258. Fei, Y.; Xu, H. Modeling and motion control of a soft robot. IEEE. Trans. Ind. Electron. 2017, 64, 1737-42.
259. Precup, R.; Radac, M.; Roman, R.; Petriu, E. M. Model-free sliding mode control of nonlinear systems: algorithms and experiments. Inform. Sci. 2017, 381, 176-92.
260. Vikas, V.; Cohen, E.; Grassi, R.; Sozer, C.; Trimmer, B. Design and locomotion control of a soft robot using friction manipulation and motor–tendon actuation. IEEE. Trans. Robot. 2016, 32, 949-59.
261. Li, M.; Kang, R.; Branson, D. T.; Dai, J. S. Model-free control for continuum robots based on an adaptive Kalman filter. IEEE/ASME. Trans. Mechatron. 2018, 23, 286-97.
262. Patterson, Z. J.; Santina, C. D. R. D.; Modeling,. In: 2024 IEEE International Conference on Robotics and Automation (ICRA); Yokohama, Japan. IEEE; 2024, pp. 14995-5001.
263. Zheng, Z.; Kumar, P.; Chen, Y.; et al. Model-based control of planar piezoelectric inchworm soft robot for crawling in constrained environments. In: 2022 IEEE 5th International Conference on Soft Robotics (RoboSoft); Edinburgh, United Kingdom. IEEE; 2022. pp. 693-8.
264. Li, Y.; Ang, K. H.; Chong, G. C. Y. PID control system analysis and design. IEEE. Control. Syst. May. 2006, 26, 32-41.
265. Campo, A. B. PID control design. In: Katsikis V, editor. MATLAB - A Fundamental Tool for Scientific Computing and Engineering Applications - Volume 1. InTech; 2012. Available from: http://www.intechopen.com/books/matlab-a-fundamental-tool-for-scientific-computing-and-engineering-applications-volume-1/pid-control-design. [Last accessed on 14 Jan 2025].
266. Borase, R. P.; Maghade, D. K.; Sondkar, S. Y.; Pawar, S. N. A review of PID control, tuning methods and applications. Int. J. Dynam. Control. 2021, 9, 818-27.
267. Plum, F.; Labisch, S.; Dirks, J. H. SAUV-A bio-inspired soft-robotic autonomous underwater vehicle. Front. Neurorobot. 2020, 14, 8.
268. Li, H.; Xu, Y.; Zhang, C.; Yang, H. Kinematic modeling and control of a novel pneumatic soft robotic arm. Chin. J. Aeronaut. 2022, 35, 310-9.
269. Dumont, G. A.; Huzmezan, M. Concepts, methods and techniques in adaptive control. In: Proceedings of the 2002 American Control Conference (IEEE Cat. No.CH37301); Anchorage, USA. IEEE; 2002. pp. 1137-50.
270. Kaufman, H.; Bar-Kana, I.; Sobel, K. Direct adaptive control algorithms: theory and applications. New York, NY: Springer US; 1994.
271. Tonietti, G.; Bicchi, A. Adaptive simultaneous position and stiffness control for a soft robot arm. In: IEEE/RSJ International Conference on Intelligent Robots and System; Lausanne, Switzerland. IEEE; 2002. pp. 1992-7.
272. Xu, F.; Wang, H.; Chen, W.; Wang, J. Adaptive visual servoing control for an underwater soft robot. Assem. Autom. 2018, 38, 669-77.
273. Arulkumaran, K.; Deisenroth, M. P.; Brundage, M.; Bharath, A. A. Deep reinforcement learning: a brief survey. IEEE. Signal. Process. Mag. 2017, 34, 26-38.
274. Joshi, D. J.; Kale, I.; Gandewar, S.; Korate, O.; Patwari, D.; Patil, S. Reinforcement learning: a survey. In: Swain D, Pattnaik PK, Athawale T, editors. Machine learning and information processing. Singapore: Springer; 2021. pp. 297-308.
275. Ishige, M.; Umedachi, T.; Taniguchi, T.; Kawahara, Y. Exploring behaviors of caterpillar-like soft robots with a central pattern generator-based controller and reinforcement learning. Soft. Robot. 2019, 6, 579-94.
276. Wang, J.; Chortos, A. Control strategies for soft robot systems. Adv. Intell. Syst. 2022, 4, 2100165.
277. Mavrovouniotis, M.; Chang, S. Hierarchical neural networks. Comput. Chem. Eng. 1992, 16, 347-69.
278. Jain, L. C.; Seera, M.; Lim, C. P.; Balasubramaniam, P. A review of online learning in supervised neural networks. Neural. Comput. Appl. 2014, 25, 491-509.
279. Psichogios, D. C.; Ungar, L. H. Direct and indirect model based control using artificial neural networks. Ind. Eng. Chem. Res. 1991, 30, 2564-73.
280. Narendra, K. S.; Mukhopadhyay, S. Adaptive control using neural networks and approximate models. IEEE. Trans. Neural. Netw. 1997, 8, 475-85.
281. Hecht-Nielsen, R. III.3 - Theory of the Backpropagation Neural Network. In: Neural networks for perception. Elsevier; 1992. pp. 65-93.
282. Red’ko, V. G.; Prokhorov, D. V.; Burtsev, M. S. Theory of functional systems, adaptive critics and neural networks. In: 2004 IEEE International Joint Conference on Neural Networks (IEEE Cat. No.04CH37541); Budapest, Hungary. IEEE; 2004. pp. 1787-92.
283. Slotine, J. E.; Sanner, R. M. Neural networks for adaptive control and recursive identification: a theoretical framework. In: Trentelman HL, Willems JC, editors. Essays on control. Boston: Birkhäuser; 1993. pp. 381-436.
284. Low, J. H.; Khin, P. M.; Han, Q. Q.; et al. Sensorized reconfigurable soft robotic gripper system for automated food handling. IEEE/ASME. Trans. Mechatronics. 2022, 27, 3232-43.
285. Somnox. Somnox, Breathe, relax, sleep. Available from: https://somnox.com/. [Last accessed on 14 Jan 2025].
286. Awad, L. N.; Esquenazi, A.; Francisco, G. E.; Nolan, K. J.; Jayaraman, A. The ReWalk ReStore™ soft robotic exosuit: a multi-site clinical trial of the safety, reliability, and feasibility of exosuit-augmented post-stroke gait rehabilitation. J. Neuroeng. Rehabil. 2020, 17, 80.
287. Squishy Robotics. Life-saving, Cost-saving information in real time. Available from: https://squishy-robotics.com/. [Last accessed on 14 Jan 2025].
288. Mitchell, S. K.; Wang, X.; Acome, E.; et al. An easy-to-implement toolkit to create versatile and high-performance HASEL actuators for untethered soft robots. Adv. Sci. 2019, 6, 1900178.
289. Amend, J.; Cheng, N.; Fakhouri, S.; Culley, B. Soft robotics commercialization: jamming grippers from research to product. Soft. Robot. 2016, 3, 213-22.
290. Olkkola, L. S.; Townsend, V. M.; Quigley, C. Defining potential market growth of innovative applications for military and commercial use in soft robotics. Defense Technical Information Center. 2022. Available from: https://apps.dtic.mil/sti/citations/AD1160075. [Last accessed on 14 Jan 2025].
291. Wang, Y.; Wang, G.; Ge, W.; Duan, J.; Chen, Z.; Wen, L. Perceived safety assessment of interactive motions in human-soft robot interaction. Biomimetics 2024, 9, 58.
292. Sundaravadivel, P.; Ghosh, P. K.; Suwal, B. IoT-enabled soft robotics for electrical engineers. In: Proceedings of the Great Lakes Symposium on VLSI 2022. Irvine CA USA: ACM; 2022. pp. 329-32.
293. Golecki, H. M.; Robinson, J.; Cvetkovic, C.; Walsh, C. Empowering students in medical device design: an interdisciplinary soft robotics course. Biomed. Eng. Education. 2024, 4, 399-408.
294. Lamer, S.; Adnan, A.; McNeela, E.; Tran, T.; Golecki, H. Using drawings to understand impacts of soft robotics activity on elementary age students’ perceptions of robots. In: 2022 IEEE Frontiers in Education Conference (FIE); Uppsala, Sweden. IEEE; 2022. p. 1-5.
295. Medina, D. R.; Kim, J.; Ohk, K.; et al. Pre-college robotics: best practices for adapting research to outreach. In: 2023 ASEE Annual Conference & Exposition. 2023.
296. Greer, A. H.; Vauclain, W.; Lee, E.; et al. Design of a guided inquiry classroom activity to investigate effects of chemistry on physical properties of elastomers. J. Chem. Educ. 2021, 98, 915-23.
297. Finio, B.; Shepherd, R.; Lipson, H. Air-powered soft robots for K-12 classrooms. In: 2013 IEEE Integrated STEM Education Conference (ISEC). Princeton, USA. IEEE; 2013. p. 1-6.
298. Greer, A. H.; King, E.; Lee, E. H.; et al. Soluble polymer pneumatic networks and a single-pour system for improved accessibility and durability of soft robotic actuators. Soft. Robot. 2021, 8, 144-51.
299. Sardesai, A. N.; Segel, X. M.; Baumholtz, M. N.; et al. Design and characterization of edible soft robotic candy actuators. MRS. Adv. 2018, 3, 3003-9.
300. Lee, D. J.; Ryu, S. R. The influence of fiber aspect ratio on the tensile and tear properties of short-fiber reinforced rubber. 1999. Available from: https://api.semanticscholar.org/CorpusID:45044228. [Last accessed on 14 Jan 2025].
301. Motsoeneng, T.; Magagula, S.; Mohapi, M.; Lebelo, K.; Sefadi, J.; Mochane, M. 7 - Elastomer matrix based natural fiber composites. In: Fiber Reinforced Composites. Elsevier; 2021. pp. 167-85.
Cite This Article

How to Cite
Kulkarni, M.; Edward, S.; Golecki, T.; Kaehr, B.; Golecki, H. Soft robots built for extreme environments. Soft Sci. 2025, 5, 12. http://dx.doi.org/10.20517/ss.2023.51
Download Citation
Export Citation File:
Type of Import
Tips on Downloading Citation
Citation Manager File Format
Type of Import
Direct Import: When the Direct Import option is selected (the default state), a dialogue box will give you the option to Save or Open the downloaded citation data. Choosing Open will either launch your citation manager or give you a choice of applications with which to use the metadata. The Save option saves the file locally for later use.
Indirect Import: When the Indirect Import option is selected, the metadata is displayed and may be copied and pasted as needed.
About This Article
Special Issue
Copyright
Data & Comments
Data
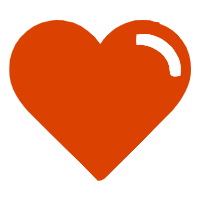
Comments
Comments must be written in English. Spam, offensive content, impersonation, and private information will not be permitted. If any comment is reported and identified as inappropriate content by OAE staff, the comment will be removed without notice. If you have any queries or need any help, please contact us at [email protected].