Development of catalysts and reactor designs for CO2 electroreduction towards C2+ products
Abstract
Recent research on the electrocatalytic CO2 reduction reaction (eCO2RR) has garnered significant attention given its capability to address environmental issues associated with CO2 emissions while harnessing clean energy to produce high-value-added products. Compared to C1 products, C2+ products provide greater energy densities and are highly sought after as chemical feedstocks. However, the formation of the C-C bond is challenging due to competition with the formation of H-H and C-H bonds. Therefore, to elevate the selectivity and yield of C2+ fuels, it is essential to develop more advanced electrocatalysts and optimize the design of electrochemical cell configurations. Of the materials investigated for CO2RR, Cu-based materials stand out due to their wide availability, affordability, and environmental compatibility. Moreover, Cu-based catalysts exhibit promising capabilities in CO2 adsorption and activation, facilitating the formation of C2+ compounds via C-C coupling. This review examines recent research on both electrocatalysts and electrochemical cells for CO2 electroreduction to C2+ compounds, introducing the core principles of eCO2RR and the reaction pathways involved in generating C2+ products. A key focus is the categorization of Cu-based catalyst designs, including defect engineering, surface modification, nanostructure engineering, and tandem catalysis. By analyzing recent studies on eCO2RR with Cu-based catalysts, we aim to elucidate the mechanisms behind enhanced selectivity for C2+ compounds. Additionally, various types of electrolytic cells are discussed. Lastly, the prospects and limitations of utilizing Cu-based materials and electrocatalytic cells for CO2 reduction are highlighted for future research.
Keywords
INTRODUCTION
The significant release of CO2 from the use of fossil fuels has brought about its accumulation in the atmosphere, disrupting the global carbon cycle and causing serious environmental and climate issues, including the greenhouse gas effect and rising sea levels[1-7]. Consequently, there is a growing interest in converting CO2 into valuable carbon-based compounds to reduce atmospheric CO2 concentrations and tackle energy challenges[8,9]. Various approaches have been investigated by researchers to transform CO2 into valuable carbon-based compounds, including chemical conversion[10], biotransformation[11], photocatalysis[12,13], and electrocatalysis[14-16]. Among these approaches, the eCO2RR stands out as a promising technique, leveraging renewable electricity to mitigate CO2-related environmental problems while generating high-value-added products[17-19].
In aqueous electrolyte media, electrocatalytic CO2 reduction reaction (eCO2RR) products can be classified into two main categories: (i) 2e- products, such as carbon monoxide (CO) and formate (HCOO-), and (ii) multi-electron transfer products, including methanol (CH3OH), methane (CH4), ethanol (C2H5OH), and ethylene (C2H4)[20,21]. Compared to 2e- products, multi-electron transfer products are preferred due to their higher economic value, serving as crucial feedstock and specialized chemicals [Figure 1A][22].
Figure 1. (A) Market size and price of CO2RR products; (B) Faradaic efficiency and corresponding overpotential; (C) Maximum faradaic efficiency and current density. This figure is quoted with permission from Kibria et al. Copyright (2019) John Wiley and Sons[22]. CO2RR: CO2 reduction reaction.
However, achieving selective CO2 reduction into C2+ multi-carbon products remains challenging due to several factors: (1) the competitive and undesirable H2O reduction, (2) the large C-C coupling activation barrier, and (3) the difference in overpotential for the formation of crucial CO intermediates and C2+ species, resulting in lower current densities and selectivity compared to C1 products [Figure 1B and C][23-27]. Therefore, developing advanced electrocatalysts is essential for enhancing both the selectivity and activity for C2+ production[28,29].
This review provides a detailed examination of strategies designed to control C-C coupling and
FUNDAMENTAL INSIGHTS INTO CO2 REDUCTION REACTION MECHANISMS
CO2 is a highly stable molecule, primarily due to its strong C=O bond, which has a bond dissociation energy of 750 kJ mol-1[30]. Converting CO2 into desired products requires very challenging conditions and substantial energy input. This transformation involves multi-electron transfer steps, such as 2-, 4-, 6-, 8-, or even 18-electron processes, resulting in a range of possible products [Figure 2][31].
Figure 2. Overview of the reaction routes of CO2RR for both C1 and C2+ products. This figure is quoted with permission from Trogadas et al. Copyright (2023) John Wiley and Sons[31]. CO2RR: CO2 reduction reaction.
These products can be categorized into two groups according to the quantity of carbon atoms: C1 products, including CO, CH4, HCOOH, and CH3OH; C2 products, including acetate, C2H4, and C2H5OH; C3 products, including propanol (C3H7OH) and acetone (CH3COCH3); and C4+ products[32]. Table 1 summarizes the thermodynamic half-reaction of CO2 conversion and the associated standard potential to produce specific products[33]. The reaction mechanism for eCO2RR involves several key steps: CO2 adsorption onto the catalyst surface, electron and proton transfer, the formation of reactive intermediates, and the desorption of the final products. The performance and selectivity of this process are heavily dependent on factors such as the choice of catalyst material, the composition of the electrolyte, and the applied potential[34]. A critical aspect of determining reaction pathways and product distributions lies in understanding the binding energies of intermediates on the catalyst surface. Additionally, operating conditions, including the pH and temperature of the electrolyte, play a significant role in influencing reaction dynamics and product selectivity.
MECHANISM FOR C2+ PRODUCTS
C2+ products typically possess higher energy densities than C1 products, making them essential feedstocks in numerous chemical industries [33]. Consequently, the CO2 reduction reaction (CO2RR) into valuable C2+ products is highly desirable. A critical step in achieving multi-carbon products during CO2RR is the coupling of two C1 intermediates to form a C-C bond. The *CO intermediate plays a pivotal role in this process: it can either undergo C-C coupling with another *CO species to produce C2+ products, such as ethanol, ethylene, and n-propanol, or it can strongly adsorb on the catalyst surface and proceed through hydrogenation to form C1 products such as CH4[35]. However, the selective generation of C2+ products faces substantial challenges. First of all, a C-C coupling process requires significant energy barriers, and the formation of C2+ products involves multiple proton-electron transfer steps, which are inherently slow and kinetically hindered[36-39]. In contrast, competing reactions involving H-H and C-H bond formation occur more readily due to their lower energy barriers and simpler reaction pathways[40-42]. These results in decreased activity and selectivity for C2+ product formation during CO2 reduction. Generally, the process of C2+ product formation involves four key steps: (1) *CO formation; (2) C-C bond formation; (3) C-C coupling; and (4) product desorption[43]. An important aspect of generating C2+ products is maintaining a substantial amount of *CO on the surface, as a higher concentration of CO promotes C-C coupling, thereby boosting the production of C2+ compounds. The C-C bond formation in CO2 reduction can occur via two distinct mechanisms: the Eley-Rideal (E-R) and the Langmuir-Hinshelwood (L-H) mechanisms[24]. In the
CATALYST DESIGN FOR PROMOTING THE REACTION PATHWAY FOR C2+ PRODUCTS
To date, Copper (Cu) stands out as one of the rare metal catalysts capable of efficiently converting CO2 into valuable multi-carbon products[51]. This is attributed to its distinctive 3d electronic structure, which provides optimal *CO binding energy and suppresses HER activity, thereby promoting C-C coupling[52]. Furthermore, Cu-based catalysts stand out as the most promising option for CO2 reduction to C2+ products, offering an optimal balance of environmental sustainability, economic feasibility, and superior selectivity. While alternative catalysts may offer lower costs, none rival the unique ability of Cu to facilitate the production of high-value multi-carbon products. However, challenges remain, including limited selectivity for certain products and insufficient electrochemical durability. To address these issues, substantial efforts have been dedicated to improving Cu-based catalysts[53-55]. In the following part, we explore various design strategies to enhance the efficiency of Cu-based catalysts for the selective conversion of CO2 into C2+ [Table 2].
Summary of catalysts for the reduction of CO2 to C2+ products
Catalyst | Main C2products (FE) | Current density | Reactor type | Ref. | |
Defect engineering | Cu/CeO2-x-4 | C2H4: 30% @-1.2 VRHE | - | H-cell | [58] |
Cu/CeO2 | C2H4: 78.3% @ -1.0VRHE | -16.8 mA cm-2 @-1.0VRHE | H-cell | [59] | |
1.0% I-CuO | C2H4: 50.2% @-1.2 VRHE | JC2H4: -9 mA cm-2 @-1.2VRHE | H-cell | [60] | |
Sn-doped CuO(VO) | C2H4: 48.5% ± 1.2% @-1.1 VRHE | - | H-cell | [61] | |
Cu SAs/UIO-H2 | C2H5OH: 46.28% @-0.66 VRHE | - | Flow cell | [62] | |
GB-Cu | C2H4: 38% @-1.2 VRHE | JC2H4: -37 mA cm-2 @-1.2 VRHE | Flow cell | [65] | |
GB-Cu29.6 | C2+products: 73.2% @-3.8 VRHE | -303.61 mA cm-2 @-3.8 VRHE | MEA cell | [66] | |
GB-Cu-IV | C2+products: 68.2% @-1.28 VRHE | JC2+: -0.768 A cm-2 @-1.28 V | Flow cell | [67] | |
RGBs-Cu | C2+products: 77.3% @400 mA cm-2 | JC2+: -353.6 ± 7.5 mA cm-2 @400mA cm-2 | Flow cell | [68] | |
Nanostructure engineering | 3DOP Cu2O–CO | C2+products: 77.0% ± 0.3% @-0.88 VRHE | JC2+: -513.7±0.7 mA cm-2 @-0.88 VRHE | Flow cell | [76] |
OD-Cu NWs | C2+products: 77.7% @-0.51 VRHE | JC2+: -233.2 mA cm-2 @-0.51 VRHE | Flow cell | [77] | |
C-CuO nanosheets | C2H4: 56.2% @-0.871 VRHE | JC2H4: -171 mA cm-2 @-0.871 VRHE | Flow cell | [78] | |
Cu2O-NS | C2+products: 81.32% @-1.2 VRHE | -187.6 mA cm-2 @-1.2 VRHE | Flow cell | [79] | |
f-Cu2O | C2H5OH: 52.6% @-0.8 VRHE | jC2H5OH: -9.1 mA cm-2 @-0.9 VRHE | H-cell | [80] | |
Cucub | C2H4: 57% @-0.75 VRHE | - | Flow cell | [81] | |
NS-D Cu | C2+products: 67.5% @-1.5 VRHE | JC2+: -25.1 mA cm-2 @-1.5 VRHE | H-cell | [82] | |
c-Cu2O | C2H4: 61.3% @-1.2 VRHE | JC2H4: -2.5 mA cm-2 @-1.2 VRHE | H-cell | [83] | |
F-Cu2O@ZIF-8 | C2H4: 74.1% @-1.2 VRHE | - | H-cell | [84] | |
Copper NPs (25 nm) | C2+products: 92.8% @-1.7 VRHE | - | MEA cell | [85] | |
Cu45.2/GDY | C2+products: 91.2% @-1.0 VRHE | JC2+: -312 mA cm-2 @-1.0 VRHE | Flow cell | [86] | |
HKUST-1-derived Cu clusters | C2H4: 45% @-1.07 VRHE | -262 mA cm-2@-1.07 VRHE | Flow cell | [87] | |
Cu2-CuN3 | C2H5OH: 51% @-1.1 VRHE | jC2H5OH: -14.4 mA cm-2 @-1.1 VRHE | H-cell | [88] | |
Surface modification | Cu foil+Gly | C2H4: 24% @-1.9 VRHE | - | H-cell | [92] |
Cu/PANI | C2H4: 43.8% @-1.08 VRHE | -28.3 mA cm-2 @-1.08 VRHE | H-cell | [93] | |
PANI/CuO NSs-25 | C2+products: 50% @-1.6 VRHE | JC2H4: -200.1 mA cm-2 @-1.6 VRHE | H-cell | [94] | |
Hydrophobic Cu dendrite | C2H4: 56% @-30 mA cm-2 | - | Flow cell | [95] | |
TP-Cu | C2H4: 18.35% @-1.1 VRHE | - | H-cell | [96] | |
Cu-D | C2+products: 64% ± 1.4% @-0.68 VRHE | JC2+: -255 mA cm-2 @-0.68 VRHE | Flow cell | [97] | |
S-Cu | C2+products: 78% @-0.9 VRHE | JC2+: -1.81 Acm-2 @-0.9 VRHE | Flow cell | [98] | |
Tandem strategy | Cu@Ag/C | C2H4: 58.03% @-0.85 VRHE | JC2H4: -49.41 mA cm-2 @-0.85 VRHE | Flow cell | [105] |
Cu90Ag10 | C2H4: 33.6% @2.2 VRHE | JC2H4: -42.70 mA cm-2 | MEA cell | [106] | |
CuAg4/EDTA | C2+products: 86.56% @-1.23 VRHE | JC2+: -10 mA cm-2 @-1.23 VRHE | H-cell | [107] | |
Cu/Ag | C2H5OH: 57.5% @-1.1 VRHE | jC2H5OH: -356.7 ± 9.5 mA cm-2 @-1.1 VRHE | Flow cell | [108] | |
Ag1–Cu1.1NDs | C2H4: 38% @-1.1VRHE | -1 mA cm-2 @-1.1 VRHE | H-cell | [109] | |
Ag65–Cu35 JNS-100 | C2H4: 54% @-1.2 VRHE | JC2H4: -2 mA cm-2 @-1.2 VRHE | H-cell | [110] | |
Cu needle-Ag | C2+products: 70% @300 mA cm-2 | JC2+: -245 mA cm-2 @300 mA cm-2 | Flow cell | [111] | |
Au/Cu | - | -15.29 mA cm-2 @-1.08 VRHE | Flow cell | [112] | |
S-2.0-Au@OD-Cu | C2H4: 40% @-300 mA cm-2 | JC2H4: -115 mA cm-2 @-0.920 VRHE | Flow cell | [113] | |
Au0.02Cu2O | C2H4: 24.4 % @-1.3 VRHE | -5.7 mA cm-2 @-1.3 VRHE | H-cell | [114] | |
Au@Cu-AuCu | 0.9 μmol cm-2 h-1 @-1.0 VRHE | - | H-cell | [115] | |
Cu99.3Au0.7 NWs | C2+products: 65.3% @-1.25 VRHE | JC2+: -12.1 mA cm-2 @-1.25 VRHE | H-cell | [116] | |
Au-Cu Janus NSs | C2+products: 67% @-0.75 VRHE | JC2+: -0.29 A cm-2 @-0.75 VRHE | Flow cell | [117] | |
Cu2O NCs-C-Copc | C2H4: 70.31 % @-0.76 VRHE | JC2H4: -226.18 mA cm-2 @-0.76 VRHE | Flow cell | [121] | |
Cu–CoPc | C2+products: 82% @480 mA cm-2 | JC2+: -394 mA cm-2 @480 mA cm-2 | Flow cell | [122] | |
Cu2O@CM | C2+products: 73.2% @-1.1 VRHE | JC2+: -52.9 mA cm-2 @-1.1 VRHE | H-cell | [123] | |
Cu NPs/Ni–N–C | C2H4: 14.27 % @-0.9 VRHE | JC2H4: -1.67 mA cm-2 @-0.9 VRHE | H-cell | [125] | |
CuO/Ni | C2+products: 81.4% @-1.1 VRHE | JC2+: -1220.8 mA cm-2 @-1.1 VRHE | Flow cell | [126] | |
Ni Pc + Cu-R | C2H4: 62 % @-500 mA cm-2 | JC2H4: -370 mA cm-2 @-500 mA cm-2 | Flow cell | [127] | |
PTF(Ni)/Cu | C2H4: 57.3% @-1.1 VRHE | JC2+: -3.1 mA cm-2 @-1.1 VRHE | H-cell | [128] | |
a-Ni/Cu-NP@CMK | C2H4: 72.3% @-1.1 VRHE | JC2H4: -294 mA cm-2 @-1.1 VRHE | Flow cell | [129] | |
Non-cu based | Ni3Al film | 1-propanol: 1.9% @-1.38 VRHE | - | H-cell | [130] |
Ni5Ga3 | C2H6: 1.3% @-0.88 VRHE | - | H-cell | [131] | |
SnS2/Sn1-O3G | C2H5OH: 82.5% @-0.9 VRHE | jC2H5OH: -14 mA cm-2 @-0.9 VRHE | H-cell | [132] |
Defect engineering
Defects are crucial surface features that significantly influence a catalyst’s performance by modifying its electronic properties and disturbing the periodic structure of the crystal, resulting in unique chemical and electronic characteristics[56,57]. Here, we highlight recently recent electrocatalysts that utilize defect engineering to enhance performance toward C2+ products and examine the influence of these defects in
Vacancy
Enhancing the performance of Cu-based electrocatalysts has largely centered on investigating the role of vacancies, the most prevalent type of defect. These studies aim to explore how vacancies can be leveraged to optimize catalytic activity toward C2+ products. Xue et al. designed Cu/CeO2-x catalysts featuring different levels of oxygen vacancies, investigating the interaction between Ce3+ and Cu species and its impact on catalytic performance[58]. The introduction of Cu into CeO2-x generated a significant number of oxygen vacancies. Various Cu/CeO2-x electrocatalysts were synthesized via the hydrothermal-reduction method [Figure 3A]. High-resolution transmission electron microscopy (HRTEM) analysis demonstrated the presence of structural defects in the Cu/CeO2-x-4 catalyst, as depicted in Figure 3B. The pristine CeO2 catalyst in Figure 3C only produces H2 and CO, regardless of the applied potential. However, the
Figure 3. (A) Graphic representation of the Cu/CeO2-x-4 catalyst synthesis; (B) HRTEM images of the Cu/CeO2-x-4 catalyst; (C) FEs of bare CeO2; (D) Cu/CeO2-x-1; and (E) Cu/CeO2-x-4. This figure is quoted with permission from Xue et al. Copyright (2024) Elsevier[58]; (F) Schematic representation of the synthetic process for Cu SAs/UIO-H2; (G) The corresponding FEs for the reduction products of Cu SAs/UIO and (H) Cu SAs/UIO-H2; (I) Long-term electrolysis of Cu SAs/UIO-H2 at -0.66 V vs. RHE. This figure is quoted with permission from Bie et al. Copyright (2024) Elsevier[62]. FE: Faradaic efficiency; HRTEM: high-resolution transmission electron microscopy; SAs: single atoms; RHE: reversible hydrogen electrode.
Grain boundary
It is well established that grain boundaries (GBs) influence the selectivity of CO2RR products[63], and a quantitative correlation has been observed between the density of GBs in Cu-based electrocatalysts and
Figure 4. (A) FEs on GB-Cu; (B) FEC2+ of GB-Cu; (C) In situ ATR-SEIRAS spectra of GB-Cu. This figure is quoted with permission from Chen et al. Copyright (2020) American Chemical Society[65]; (D) Electrochemical deposition procedure for different Cu catalysts; (E) FFT-refined aberration-corrected HAADF-STEM image of the GB-Cu29.6; (F) FEs for C2+ and (G) ECSA-normalized jC2+ of Cu with different GB densities; (H) Spatially resolved electrochemical map derived from the individual linear sweep voltammetry (LSV) curves. This figure is quoted with permission from Zhang et al. Copyright (2024) American Chemical Society[66]. FE: Faradaic efficiency; HAADF-STEM: high-angle annular dark-field scanning transmission electron microscopy; GBs: grain boundaries; ATR-SEIRAS: attenuated total reflectance-surface-enhanced infrared absorption spectroscopy; FFT: fast Fourier transform; ECSA: electrochemically active surface area.
Ding et al. introduced an innovative and straightforward salt-assisted annealing technique that induced unconventional grain fragmentation, significantly increasing the density of GBs[67]. The optimized electrocatalysts attained a maximum FEC2+ of 70.0% for the H-type cell and 68.2% for the flow cell, achieving a jC2+ of 0.768 mA cm-2 at -1.28 V vs. RHE, surpassing the performance of most previously reported counterparts. To investigate the correlation between GBs and the selectivity of the catalysts for C2+ products, in situ Raman spectroscopy and Density functional theory (DFT) calculations were conducted. The results indicated that a greater GB density generates additional active sites for CO2RR, resulting in a higher concentration of *CO intermediate. This, in turn, promotes C-C coupling and ultimately increases C2+ production. Kong et al. prepared small Cu nanoparticles (NPs) with enhanced small GBs (RGBs-Cu) using spatial confinement and in situ electroreduction[68]. Figure 5A illustrates the schematic of the synthesis process for RGBs-Cu electrocatalysts, while HRTEM images reveal the numerous GBs present in the catalysts. CO2RR electrolysis using the RGBs-Cu electrode was conducted using flow cells with different concentrations of KOH. Notably, elevating the KOH concentration to 2 and 3 M resulted in an additional enhancement of the FE for C2+ products, achieving 77.3% at a current density of 400 mA cm-2 in 2 M KOH [Figure 5B]. Additionally, RGBs-Cu reached a maximum C2+-to-C1 (C2+/C1) ratio of 2.57 at 400 mA cm-2, which notably exceeded the control sample’s ratio of 0.75 [Figure 5C]. Moreover, RGBs-Cu demonstrated exceptional stability, maintaining consistent C2+ selectivity of 60% over 134 h at a total current density of
Figure 5. (A) Overview of the fabrication process of RGBs-Cu sample; (B) FEC2+ of RGBs-Cu with different electrolyte concentrations; (C) C2+/C1 product selectivity of RGBs-Cu and PGBs-Cu; (D) Evaluation of the long-term stability of the RGBs-Cu electrode at
Nanostructure engineering
Bulk Cu-based electrocatalysts suffer from limited exposed active sites and poor electronic structure, resulting in low CO2RR performance towards C2+[69,70]. To address these challenges, nanostructure engineering approaches-such as morphology control, facet optimization, and confinement effects-have appeared as powerful strategies to strengthen their catalytic efficiency for CO2RR.
Confinement effect
Confinement structures in Cu-based electrocatalysts can enhance C2+ selectivity by increasing the retention time of intermediates such as *CO/*COH by facilitating C-C coupling reactions[71,72]. Consequently, significant research has focused on tailoring the Cu surface with specialized confinement morphologies to optimize both the activity and selectivity for C2+ product formation. Fan et al. fabricated three-dimensional (3D) ordered porous cuprous oxide cuboctahedra (3DOP Cu2O-CO) through a hard templating method[73]. This method successfully created a structure characterized by ordered macropores that are interconnected with mesoporous channels throughout the Cu2O cuboctahedra. The 3DOP-Cu2O-CO configuration offers the benefits of uniformly distributed and interconnected pore channels. Consequently, these electrocatalysts demonstrated superior performance in CO2RR compared to control catalysts lacking ordered porous architectures. Notably, 3DOP-Cu2O-CO achieved a significant electrochemical double-layer capacitance of 2.9 mF cm-2, with a maximum C2+ FE of 73.4% at -1.4 V vs. RHE in an H-cell, and 81.7% at -1.0 A cm-2 using a flow-type cell. Finite element method (FEM) simulations demonstrated that the structured pore architecture of 3DOP Cu2O-CO capably confines and holds adequate *CO for adsorption during the CO2 reduction process, thereby facilitating the strong dimerization required for C2+ product formation. Liu et al. designed distinctive Cu-based catalysts with a cavity structure, achieved through in situ electrochemical reduction of Cu2O cavities[74]. Both transmission electron microscopy (TEM) and scanning electron microscopy (SEM) analyses confirmed the presence of cavity architecture. FEM simulations also confirmed that the cavity structure significantly enhances the concentration of CO intermediates at the reaction site, thereby promoting the C-C coupling reaction. These Cu cavity catalysts demonstrated excellent C2+ FE of 75.6 ± 1.8% and achieved jC2+ of 605 ± 14 mA cm-2 in a microfluidic flow cell. Moreover, the experimental
Morphology/facet effect
Aside from confinement engineering, the morphology and crystal facets of Cu-based electrocatalysts have a fundamental role in influencing CO2 electroreduction activity and product selectivity. For example, Wu et al. revealed a correlation between the structural dimensions of oxide-derived Cu (OD-Cu) electrocatalysts and their ability to selectively produce C2+ products[77]. Their study involved the synthesis of three distinct nanostructures: one-dimensional nanowires (NWs), two-dimensional nanosheets (NSs), and 3D nanoflowers (NFs), all of which displayed notable resistance to structural degradation [Figure 6A]. Initial evaluations of the CO2RR activity and the electrochemical characteristics of the OD-Cu catalysts were conducted using H-cell systems. As demonstrated in Figure 6B, the product distribution from CO2RR over the OD-Cu catalysts was evaluated across a potential range from -0.6 V to -1.4 V vs. RHE. Of the three morphologies, OD-Cu NWs achieved the highest preference for C2+ products, reaching a maximum FE of 50.2% at -1.4 V vs. RHE, which notably surpassed the performance of OD-Cu NSs (35.6%) and NFs (13.3%). Additionally, the performance of OD-Cu catalysts was additionally evaluated with flow cells. Notably,
Figure 6. (A) Diagram illustrating the preparation of OD-Cu catalysts with different morphologies; (B) FEC2+ of OD-Cu NWs using
Moreover, Cu-based catalysts with a two-dimensional NS morphology are appealing due to their plentiful low-coordination edge sites, which are frequently regarded as essential for improving catalytic performance. Xie et al. synthesized Cu NSs derived from CuO during CO2RR, having an average size of approximately
Facet engineering is essential in defining the catalyst's activity toward desired products. This can be achieved through various methods. Yang et al. explored the impact of morphology on the performance of Cu2O catalysts for the production of liquid products[80]. Cu2O electrocatalysts with various morphologies were synthesized using PVP as a capping agent. A schematic representation of the synthesized catalysts, including cube-shaped Cu2O (c-Cu2O), tetrakaidecahedron-shaped Cu2O (t-Cu2O), and flower-like Cu2O
Dong et al. proposed a novel mechanism elucidating the link between the crystal facets of Cu2O and the formation of distinct reduction products[83]. Through a combination of theoretical calculations and experimental validation, they supported their findings. The exposed Cu atoms on the (100) facet displayed a dense Cu4O1 surface coordination, which enhanced the adsorption of *CO intermediates. Consequently,
Figure 7. (A) Preparation of Cu2O nanoparticles and Cu2O@ZIF-8 composites; (B) FEC2H4 of Cu2O nanoparticles with different facets; (C) FE of products on F-Cu2O at different potentials. This figure is quoted with permission from Luo et al. Copyright (2022) John Wiley and Sons[84]; (D) Schematic illustration for the synthesis of various Cu2O; (E) C2+ and C1 faradaic efficiencies; (F) jC2+ on Cu-D and Cu-P; (G) Durability analysis for the Cu-D and Cu-P electrodes at 300 mA cm-2.This figure is quoted with permission from Niu et al. Copyright (2021) American Chemical Society[97]. FE: Faradaic efficiency.
Size effect
Another approach to develop electrocatalysts is controlling the size of electrocatalysts. Reducing the size increases the surface-to-volume ratio, thereby enhancing the utilization of metal atoms. Additionally, the number of undercoordinated sites increases, leading to a perturbed electronic structure and enhanced activity.
Merino-Garcia et al. investigated the selectivity and activity of the catalyst based on the size of the Cu particles, which were synthesized with sizes ranging from 25 nm to 80 nm[85]. Cu particles of different sizes were mixed with a binder and isopropanol to prepare a GDE by depositing the mixture onto carbon paper. The electrode with 25 nm Cu particles exhibited significantly better performance compared to those with Cu particle sizes of 40-60 nm and 60-80 nm, achieving a remarkably high ethylene FE of 92.8% and a production rate of 1,148 μmol m-2 s-1. This enhanced performance is attributed to an increase in the fraction of under-coordinated sites as the particle size decreases. Furthermore, Rong et al. explored the size effects of Cu catalysts, ranging from SAs to nanoclusters, using a facile acetylenic-bond-directed site-trapping approach[86]. Three different catalysts of varying sizes were synthesized: single-atoms (~0.1 nm), subnanometric clusters (0.5~1 nm) and nanoclusters (1~1.5 nm). They demonstrated that increasing the size of Cu nanoclusters enhanced both catalytic activity and selectivity toward C2+ products. The electrocatalytic performance was assessed in a three-compartment flow cell. Among the synthesized catalysts, the optimized Cu-based nanoclusters with a size of 1-1.5 nm exhibited the best performance, achieving a FEC2+ of 91.2%, a partial current density of 312 mA cm-2, and moderate stability lasting approximately 22 h. Nam et al. synthesized Cu clusters using copper benzene-1,3,5-tricarboxylate
Surface modification
While earlier studies primarily concentrated on aspects such as composition, morphology, size, crystal structure, and internal electronic properties, recent research has shifted toward optimizing the surface microenvironment. Surface modification has emerged as a powerful strategy to improve CO2 reduction to C2+ products through the adjustment of properties such as hydrophobicity, electronic structure, and the adsorption energy of CO2RR intermediates on the catalyst surface[89-91]. Introducing molecules such as
Xie et al. introduced a strategy for modifying Cu electrodes using amino acids. After modifying the surface of Cu NWs with a series of amino acids, the CO2RR performance toward the generation of C2+ products significantly improved[92]. Theoretical calculations suggested that -COOH and -NH2 groups in amino acids enhance the C2+ selectivity by stabilizing and transforming *CHO intermediates while inhibiting the HER. Wei et al. applied polyaniline (PANI) to modify the catalytic performance and selectivity of Cu[93]. By coating a PANI thin film, approximately 50 nm thick, on the Cu electrode, the chemical environment of the Cu surface was altered, resulting in an excellent C2+ FE of 60%, which is almost four times higher than that of the bare Cu electrode at -1.1 V vs. RHE. Similarly, Ma et al. explored the effect of polymer modification on the CO2 electroreduction performance and C2+ selectivity using PANI[94]. PANI NPs were coated on the surfaces of CuO NSs by a wet-chemical polymerization method. The PANI/CuO NSs hybrids were optimized by controlling the loading amount of PANI. The electrocatalytic performance toward CO2RR was evaluated using a three-electrode H-type cell. Compared to CuO NSs without the PANI, the optimized catalysts demonstrated excellent selectivity and durability, achieving a FE of up to 66.4% and long-term stability of 92 h at -1.6 V vs. RHE. Consequently, decorating CuO NSs with PANI NPs not only boosts their stability but also increases local *CO surface coverage, owing to the distinctive relationship between the
Tandem strategy
Among the various strategies to boost the activity of electrochemical CO2 reduction, the tandem strategy has been acknowledged as a promising strategy. Tandem catalysts are designed with dual active sites, allowing them to influence intermediates and achieve faster reaction rates compared to Cu monometallic components[99-101]. Important intermediates formed at one active site can be transported to another site to engage in subsequent electrochemical reduction. In particular, the *CO intermediate is essential for the generation of C2+ products[102]. Zn, Ag, and gold (Au) provide additional CO to amplify *CO surface coverage on Cu active sites, promoting C-C coupling and elevating C2+ product formation. However, if *CO undergoes further reduction without coupling to form *CHO or *COH, CH3OH or CH4 will be produced. Therefore, enhancing *CO intermediate coverage and facilitating coupling reactions is a key strategy to improve selectivity for C2+ products[103,104].
Ag-based
Ag is known for its high activity in CO production and is one of the most commonly used metals as a component in tandem catalysts. Although its CO selectivity is lower than that of Au, it is suitable for use in tandem catalysts from a cost perspective.
Recently, Duan et al. fabricated Cu@Ag/C via in-situ electrochemical reconstruction of
Figure 8. (A) FE distribution of C2H4 on Cu/C and Cu@Ag/C catalysts; (B) FECO on Cu/C and Cu@Ag/C catalysts; (C) FE of various products on Cu@Ag/C at various potentials. This figure is quoted with permission from Duan et al. Copyright (2024) Elsevier[105]; (D) Schematic illustration of three types of tandem catalysts; (E) FEs of products on layered Cu/Ag; (F) Partial current density of ethanol on Cu, mixed CuAg, layered Ag/Cu, and layered Cu/Ag catalysts. This figure is quoted with permission from Luan et al. Copyright (2024) American Chemical Society[108]; (G) Schematic diagrams of Cu needle-Ag tandem catalysts; (H) FEs for H2, C2H4, CH4, HCOO-,
In a tandem catalyst system, two main pathways are involved: (1) CO2 is first reduced to CO by a metal with high CO selectivity, and (2) the generated CO then migrates to neighboring Cu sites, where it undergoes
Au-based
Similar to Ag, Au is particularly noted for its high selectivity towards CO, as it efficiently weakens CO2 bonds and promotes the formation of CO intermediates. Bimetallic Au-Cu tandem catalysts have shown improved catalytic performance, with Au facilitating efficient CO production and Cu driving the subsequent C-C coupling, which is necessary to produce higher-value C2+ products. For example,
Figure 9. (A) Rate of C2+ production on Au-Cu and Cu electrodes; (B) Dependence of the molar ratio of C2+ alcohols to hydrocarbons and of (C) alcohols to (CO + > 2e- products) on Au-Cu and Cu as a function of potential; (D) Diagram depicting phase transformation and structural reconstruction of Au-Cu during the CO2RR process. This figure is quoted with permission from Zhu et al. Copyright (2022) Elsevier[115]; (E) Total current density of Cu, Au@Cu core-shell, and Au-Cu Janus electrocatalysts; (F) FEC2+ of three different catalysts. (G) Comparison of optimal FEC2+ obtained by using Au@Cu core-shell, Au-Cu Janus, and Cu NPs; (H) jC2+ of Au@Cu
Molecular catalysts and single-atom catalysts based
Bimetallic systems integrating Cu with other CO-producing metals, including Au and Ag, have been extensively studied as electrocatalysts for C2+ production, as mentioned above[118-120]. However, a significant challenge with these catalysts is the potential for changes in composition and morphology during operation, which can alter both their physical and electronic properties. These variations complicate the insights into catalytic behavior and hinder the development of effective design principles to enhance catalytic performance. Consequently, substantial studies have concentrated on developing tandem catalysts that employ CO-producing molecular catalysts and single-atom catalysts (SACs). Liu et al. developed
Figure 10. (A) Fabrication of CoTPP-Cu2O@CM NWs array; (B) FEC2+ of CoTPP-Cu2O@CM, Cu2O@CM, CoTPP-CM, and Cu mesh; (C) jC2+ of CoTPP-Cu2O@CM, Cu2O@CM, CoTPP-CM, and Cu mesh; (D) Stability test of CoTPP-Cu2O@CM for 15 h. This figure is quoted with permission from Min et al. Copyright (2024) John Wiley and Sons[123]; (E) Graphic representation of PTF(Ni)/Cu; (F) Total current densities on PTF(Ni)/Cu and PTF/Cu catalysts; (G) FEs for the production of C2H4 and CH4 on PTF(Ni)/Cu and PTF/Cu catalysts at different potentials; (H) jC2H4 of PTF(Ni)/Cu. This figure is quoted with permission from Meng et al. Copyright (2021) John Wiley and Sons[128]. CoTPP: cobalt(II) tetraphenylporphyrin; PTF: porphyritic triazine framework.
SACs are a unique type of catalyst with well-defined coordination and distinct electronic structures[124]. Among the SACs, Ni SACs demonstrate excellent conversion of CO2 to CO, making them particularly appealing for use in tandem catalysts. For instance, Zhang et al. developed a highly C2H4 selectivity tandem catalyst by simply mixing colloidal Cu NPs and Ni SACs (Cu NPs/Ni-N-C)[125]. The colloidal Cu NPs were first synthesized using Tetradecylphosphonic acid (TDPA) as a capping agent, allowing precise control over the size and shape of the NPs. The optimized Cu NPs/Ni-N-C catalyst exhibited excellent performance for C2H4 production, achieving a FE of 14.52%, a jC2H4 of -1.67 mA cm-2, and a C2H4/CH4 ratio of 20.1 at -0.9 V vs. RHE. Zhang et al. developed CuO/Ni tandem catalysts, composed of CuO and Ni SAs, aimed at enhancing C2+ production[126]. They investigated three strategies for fabricating tandem catalytic electrodes: layer-by-layer spraying, adjacent nanostructures, and physical mixing. Among these, the adjacent nanostructure electrode demonstrated superior efficiency by promoting more effective CO generation at the Ni sites, thereby increasing the local CO concentration near the Cu sites and enhancing C2+ product formation. Consequently, the CuO/Ni SA tandem catalyst attained an impressive jC2+ of 1,220.8 mA cm-2, along with a high FE for C2+ products at 81.4%. Among the FEC2+, FE towards C2H4 resulted in 54.1% and 28.8% for
Non-Cu-based catalysts
Cu is the primary metal known to produce C2+ products; however, recent studies indicate that several
ELECTROCHEMICAL CELLS FOR CO2RR
In addition to catalysts, electrochemical cell design is another crucial factor affecting the CO2 reduction. There are three types of reactors for the eCO2RR conversion, including an H-type cell, flow cell and MEA cell, as shown in Figure 11[133]. Notable advancements have been made in the design and fabrication of electrolytic cells to attain highly efficient C2+ production. Here, we briefly explore the advantages and disadvantages of each electrolytic cell with examples.
Figure 11. (A) H-cell, (B) flow-cell, and (C) MEA-cell configurations for eCO2RR. This figure is quoted with permission from She et al. Copyright (2022) John Wiley and Sons[133]. eCO2RR: electrocatalytic CO2 reduction reaction; MEA: membrane electrode assembly.
H-type cells
H-type cells are widely utilized for lab-based experiments due to their simple assembly, ease of operation, and low cost. These have distinct cathode and anode chambers, separated by an ion-exchange membrane. During the reaction, CO2 gas is bubbled through the aqueous catholyte, where dissolved CO2 molecules are adsorbed onto the electrocatalyst surfaces and subsequently reduced[134,135]. However, a key limitation of
GDE flow cells
Flow cells have been introduced to address the limitations of H-type cells. A standard flow cell comprises five primary components: flow field plates, support plates, ion exchange membranes, cathode and anode GDEs, and electrolytes[140]. Catholyte and anolyte are continuously circulated through the peristaltic pump. Moreover, CO2 gas directly feeds into the cathode, significantly improving mass transport and boosting production rates[141-144]. As a result, the thermodynamics and kinetics of CO2RR in flow cells differ significantly from those in traditional H-type cells, making flow cells more favorable for large-scale commercial applications[145-147]. An important aspect of flow cells is the GDEs, which improve CO2RR performance by forming porous hydrophobic channels that facilitate the transport of CO2 gas to the catalyst-electrolyte interface, thus creating a stable gas-solid-liquid three-phase environment[135,147,148]. GDEs primarily comprise three layers: the GDL, the current collector (CC), and the CL. The GDL offers numerous porous channels for efficient CO2 transport and serves as a stable support for the catalyst[149]. The CC enables efficient electron transport and reduces internal resistance, while the CL serves as the primary reaction zone, where the gas-solid-liquid three-phase interface is established and CO2RR primarily occurs[150]. Owing to these advantages, the selectivity for C2+ is higher than for an H-cell. For example, Wang et al. developed a single-atom Ga catalyst anchored on F-doped Cu2O mesoporous catalyst (Ga1-F/Cu2O), and assessed its CO2RR performance in a flow cell, as depicted in Figure 12A[151]. Using flow cells, the
Figure 12. (A) Flow cell used in electrochemical tests; (B) FE values of CO2RR products on Ga1-F/Cu2O-2; (C) C2+ product yield rates at different applied current densities of F/Cu2O, Ga1-F/Cu2O-1, Ga1-F/Cu2O-2, and Ga1-F/Cu2O-3. This figure is quoted with permission from Wang et al. Copyright (2024) John Wiley and Sons[151]; (D) FEs of H2, C1, and C2+ on CuxO and various B-CuxO samples measured with H-cell; (E) FEs of CO2RR products on CuxO and 5% B-CuxO measured with flow cells. This figure is quoted with permission from Yang et al. Copyright (2024) Elsevier[152]; (F) FEC2H4 for the 3D CTPI (tetrahydro-phenanthrolinium/SSC-modified Cu NPs on Cu/PTFE) as well as 3D CI (SSC modified-Cu NPs on Cu/PTFE); (G) jC2H4 for 3D CTPI (tetrahydro-phenanthrolinium/SSC-modified Cu NPs on Cu/PTFE) and 3D CI (SSC modified-Cu NPs on Cu/PTFE); (H) Full-cell energy efficiency and jC2H4 with different CO2 concentrations; (I) Durability measurement of 3D CTPI catalyst at 220 mA cm-2.This figure is quoted with permission from Ozden et al. Copyright (2020) American Chemical Society[166]. FE: Faradaic efficiency; CO2RR: CO2 reduction reaction; NPs: nanoparticles; 3D: three-dimensional; PTFE: polytetrafluoroethylene; CTPI: catalyst/tetrahydro-phenanthrolinium/ionomer; SSC: short-side-chain.
For example, Wang et al. reported a Pd-doped Cu/Cu2O catalyst designed to enhance C-C coupling for improved C2+ product formation[155]. eCO2RR tests of the Pd-doped Cu/Cu2O catalyst were conducted in an acidic electrolyte (pH = 2). The optimized catalyst achieved a maximum FE of 64.0% for C2+ products, with a corresponding C2+ partial current density of 407.1 mA cm-2 at -2.18 V vs. RHE. Additionally, it exhibited a high single-pass CO2 conversion efficiency of 73.2% and excellent electrochemical stability, maintaining performance for approximately 150 h.
MEA cells
MEA cells are a promising reactor design for industrial-scale CO2 reduction. They are double-electrode configurations that do not require a reference electrode[156]. Instead of using potential control as in H-type cells, MEA cells are regulated by current or voltage. Their configuration is similar to that of flow cells, but with a key distinction: in MEA cells, the anode and cathode are positioned directly on opposite sides of an ion-exchange membrane, forming a compact, sandwich-like structure[157-159]. This membrane promotes the transfer of ions and circumvents products’ crossover. Additionally, this cell design allows CO2 to be continuously delivered to the cathode and the electrolyte to be supplied to the anode, while eliminating the need for a separate catholyte at the cathode[133,160,161]. CO2 can be delivered to the cathode in two ways: by pumping a CO2-saturated solution into the cathodic compartment or by directly introducing CO2 gas, with or without added humidity[162]. This approach increases the concentration of reactants at the catalyst surface, resulting in higher reaction rates[163-165]. As a result, the MEA configuration simplifies the overall structure of the electrolytic cell, reduces mass and electron transfer resistance, and enhances energy efficiency, thereby positioning it as a more practical alternative for industrial applications. For example, Ozden et al. fabricated high-performance electrodes with a tetrahydro-phenanthrolinium-modified hierarchical adlayer with
Microfluidic electrolytic cells
Microfluidic electrolytic cells (MECs) consist of two chambers for electrolyte flow, separated by GDEs. The reaction products are carried out of the electrocatalytic cells along with the flowing liquid electrolyte. MECs provide several benefits, including (1) the ability to conveniently and rapidly adjust operating conditions and (2) a simple and efficient process for collecting final products[146]. These features make MECs highly suitable for evaluating catalyst performance under various conditions. However, the lack of separation between the anode and cathode allows products to migrate in opposite directions under electromagnetic forces, potentially leading to the oxidation of final products at the anode. This can reduce product selectivity and decrease the overall energy efficiency of the system.
Solid-state electrolytes electrolyzer
Solid-state electrolyzers represent a novel class of electrochemical CO2 cells, ideal for producing liquid products with high purity and concentration and have recently attracted significant research attention. In these systems, the cathode and anode are separated by an anion exchange membrane (AEM) and a cation exchange membrane (CEM), respectively, while a porous solid electrolyte layer with various functional groups serves as an intermediate channel[167,168]. The ions generated during the CO2RR process recombine with protons in this intermediate channel to form the desired liquid product, which is then collected by N2 purging. While this design facilitates easy separation of the liquid products, the inclusion of the solid electrolyte layer introduces additional resistance, leading to a substantial increase in the overall cell voltage.
IN-SITU/OPERANDO CHARACTERIZATION TECHNIQUES
Cu-based catalysts undergo changes in their oxidation state during the CO2RR, making catalyst characterization and performance evaluation quite challenging. To investigate the CO2RR mechanism,
In-situ/operando Fourier transform infrared spectroscopy
Fourier Transform Infrared (FT-IR) spectroscopy utilizes infrared light to induce molecular vibrations, enabling the identification of chemical compounds through their unique infrared absorption profiles. These absorption patterns result from dipole moment changes caused by molecular vibrations or rotations within a solution. In in-situ FT-IR applications, two primary approaches are used: thin-layer mode and attenuated total reflection (ATR) mode[169]. Thin-layer mode offers simplicity in design and operation but is less sensitive than ATR mode. ATR mode, while more complex and requiring precise optical alignment, minimizes interference from the bulk solution, producing spectra with higher clarity and signal-to-noise ratios. In-situ/Operando FT-IR is a highly effective tool for examining CO2RR, as it directly observes reaction intermediates and provides detailed insights into their adsorption configurations
Figure 13. Schematic illustrations of in-situ/operando techniques in CO2RR. (A) In-situ ATR-FT-IR spectroscopy; (B) In-situ/operando Raman spectroscopy. This figure is quoted with permission from Dutta et al. Copyright (2023) Elsevier[175]. (C) In-situ/operando XAS. This figure is quoted with permission from Song et al. Copyright (2023) John Wiley and Sons[180]. CO2RR: CO2 reduction reaction; XAS: X-ray absorption spectroscopy; ATR-FT-IR: attenuated total reflectance Fourier-transform infrared.
In-situ/operando Raman spectroscopy
In-situ/operando Raman spectroscopy is operated in confocal mode within a chemical reaction cell setup [Figure 13B]. By utilizing this technique to track changes in the appearance, intensity, or disappearance of specific Raman peaks, it is possible to observe shifts in oxidation states and infer the underlying reaction mechanism[175]. A significant challenge in in-situ Raman measurements is enhancing detection limits without compromising the electrochemical responses in liquid electrolytes. Given the weak signals in conventional Raman spectroscopy, surface-enhanced Raman spectroscopy (SERS) was developed to offer higher sensitivity and reduce interference from water when detecting surface metal species[176,177]. In general, Raman scattering from molecules adsorbed onto the rough surfaces of plasmonic metal nanostructures is significantly enhanced. However, SERS is constrained by the type and morphology of the material, with effective enhancement occurring only with specific metals and rough surfaces[178]. Moreover, the technique has limited spatial resolution because of the excitation wavelength. To address these challenges,
While in-situ/operando Raman spectroscopy has made significant advancements in the field of CO2RR, several challenges persist: (1) the liquid flow can interfere with detection, and (2) high current densities may affect the Raman signal.
In-situ/operando XAS
XAS is also an effective technique for investigating the electronic structure and coordination environment of materials[179]. It is generally divided into two regions: X-ray absorption near-edge structure, which provides insights into the electronic structure of atomic orbitals, such as the oxidation state of the element and symmetry, and extended X-ray absorption fine structure, which helps analyze the local coordination environment, including the coordination number, coordinating elements, and interatomic distances. Electrochemical reactions typically involve chemical adsorption and electron transfer, which lead to structural and oxidation state changes in catalysts. These changes are reversible and challenging to track accurately with ex-situ characterization methods. In contrast, in-situ/operando XAS offers the advantage of precisely detecting changes in the oxidation state and local structure of catalyst elements, monitoring catalyst reconfiguration during electrolysis, and identifying the active sites of the catalysts [Figure 13C][180].
CONCLUSION AND FUTURE PERSPECTIVES
Utilizing CO2 reduction in combination with renewable energy sources to generate high-energy density C2+ hydrocarbons presents a promising approach for advancing a sustainable society. In this review, we have provided an overview of the latest developments that facilitate greater selectivity and higher production rates for C2+ products, through methods such as catalyst tuning and electrochemical reactor design. For the catalyst-tuning, we divided into four main strategies including defect engineering, nanostructure design, surface modifications, and tandem catalysis with various CO-producing metals and provided a detailed examination of the prevailing methods used. Following this, we explored the design of electrochemical reactors, covering the commonly used H-cell, flow cell, and MEA cell, along with their key characteristics, advantages, and disadvantages. Despite the progress made, achieving low-cost and high-efficiency CO2 reduction to high-value products remains a significant challenge. Therefore, we conclude with a discussion on future research directions and the key obstacles to be addressed: (1) Many advanced and efficient electrocatalysts possess specialized nanostructures and are typically produced through multi-step processes on a laboratory scale. However, scaling up these techniques with conventional laboratory methods is often impractical. Consequently, there is an urgent need for innovative technologies to enable the large-scale synthesis of Cu-based catalysts with high selectivity, activity, and stability, which will involve careful selection of electrochemical conditions for industrial-scale CO2 electrocatalytic reduction; (2) Achieving industrial feasibility for CO2 reduction technology requires electrocatalysts to maintain stability for tens of thousands of operational hours[181]. However, Cu-based catalysts face significant stability issues, particularly in aqueous electrolytes, where issues such as high atom mobility, particle aggregation, and structural degradation often restrict their lifespan to less than 100 h under CO2RR conditions[182]. Consequently, achieving long-term stability with Cu-based catalysts remains a key challenge. Research into effective strategies for anchoring Cu-based catalysts on specific supports with strong metal-support interactions is necessary to preserve their structure and enhance long-term durability; (3) Cu-based electrocatalysts have demonstrated considerable potential for CO2RR, especially in facilitating the production of valuable C2+ products. Despite extensive research aimed at improving the selectivity of Cu-based catalysts for C2+ products, their performance remains limited. Therefore, the rational design of novel and efficient electrocatalysts with unique electronic structures and catalytic properties is essential. High-entropy alloys (HEAs), which consist of multiple metal elements, have emerged as promising candidates for CO2RR due to their tunable surface compositions and high configurational entropy. Despite their theoretical advantages, experimental evidence demonstrating the performance of Cu-based HEAs in CO2RR remains limited, with most studies confined to computational simulations. Experimental validation of Cu-based HEAs for electrochemical CO2 reduction to C2+ products would not only bridge the gap between computational studies and practical applications but also pave the way for the design of next-generation catalysts with enhanced C2+ efficiency and selectivity; (4) From a catalyst perspective, a deeper understanding of the
In summary, while notable advancements have been made, there is still considerable work to be done in developing high-performance CO2-to-C2+ systems. Continued efforts will be crucial in paving the way toward a carbon-neutral future.
DECLARATIONS
Authors’ contributions
Proposed the topic of this review: Kim, S. Y.
Prepared the manuscript: Ma, J.
Availability of data and materials
Not applicable.
Financial support and sponsorship
This research was supported by the National Research Foundation of Korea (NRF), funded by the Korean government (2022M3H4A1A04096380, 2022M3H4A1A01012712).
Conflicts of interest
Kim, S. Y. is an Associate Editor of the journal Energy Materials and was not involved in any steps of editorial processing, notably including reviewer selection, manuscript handling and decision-making. The other author declares that there are no conflicts of interest.
Ethical approval and consent to participate
Not applicable.
Consent for publication
Not applicable.
Copyright
© The Author(s) 2025.
REFERENCES
2. Fan, X.; Rabelo, M.; Hu, Y.; Khokhar, M. Q.; Kim, Y.; Yi, J. Factors affecting the performance of HJT silicon solar cells in the intrinsic and emitter layers: a review. Trans. Electr. Electron. Mater. 2023, 24, 123-31.
3. Cho, J.; Kim, B.; Ryu, S.; et al. Multifunctional green solvent for efficient perovskite solar cells. Electron. Mater. Lett. 2023, 19, 462-70.
4. Muradov, N. Low to near-zero CO2 production of hydrogen from fossil fuels: status and perspectives. Int. J. Hydrogen. Energy. 2017, 42, 14058-88.
5. Detz, R. J.; Ferchaud, C. J.; Kalkman, A. J.; et al. Electrochemical CO2 conversion technologies: state-of-the-art and future perspectives. Sustainable. Energy. Fuels. 2023, 7, 5445-72.
6. Das, T. K.; Jesionek, M.; Çelik, Y.; Poater, A. Catalytic polymer nanocomposites for environmental remediation of wastewater. Sci. Total. Environ. 2023, 901, 165772.
7. Khokhar, M. Q.; Yousuf, H.; Jeong, S.; et al. A review on p-type tunnel oxide passivated contact (TOPCon) solar cell. Trans. Electr. Electron. Mater. 2023, 24, 169-77.
8. Anwar, M. N.; Fayyaz, A.; Sohail, N. F.; et al. CO2 utilization: turning greenhouse gas into fuels and valuable products. J. Environ. Manage. 2020, 260, 110059.
9. Peter, S. C. Reduction of CO2 to chemicals and fuels: a solution to global warming and energy crisis. ACS. Energy. Lett. 2018, 3, 1557-61.
10. Song, Q.; Ma, R.; Liu, P.; Zhang, K.; He, L. Recent progress in CO2 conversion into organic chemicals by molecular catalysis. Green. Chem. 2023, 25, 6538-60.
11. Xia, Q.; Yang, J.; Hu, L.; Zhao, H.; Lu, Y. Biotransforming CO2 into valuable chemicals. J. Clean. Prod. 2024, 434, 140185.
12. Fang, S.; Rahaman, M.; Bharti, J.; et al. Photocatalytic CO2 reduction. Nat. Rev. Methods. Primers. 2023, 3, 61.
13. Alkhatib, I. I.; Garlisi, C.; Pagliaro, M.; Al-ali, K.; Palmisano, G. Metal-organic frameworks for photocatalytic CO2 reduction under visible radiation: a review of strategies and applications. Catal. Today. 2020, 340, 209-24.
14. Ye, W.; Guo, X.; Ma, T. A review on electrochemical synthesized copper-based catalysts for electrochemical reduction of CO2 to C2+ products. Chem. Eng. J. 2021, 414, 128825.
15. Birdja, Y. Y.; Pérez-gallent, E.; Figueiredo, M. C.; Göttle, A. J.; Calle-vallejo, F.; Koper, M. T. M. Advances and challenges in understanding the electrocatalytic conversion of carbon dioxide to fuels. Nat. Energy. 2019, 4, 732-45.
16. Liu, X.; Jiao, Y.; Zheng, Y.; Jaroniec, M.; Qiao, S. Z. Building Up a picture of the electrocatalytic nitrogen reduction activity of transition metal single-atom catalysts. J. Am. Chem. Soc. 2019, 141, 9664-72.
17. Cho, J. H.; Lee, C.; Hong, S. H.; et al. Transition metal ion doping on ZIF-8 enhances the electrochemical CO2 reduction reaction. Adv. Mater. 2023, 35, 2208224.
18. Cho, J. H.; Ma, J.; Lee, C.; et al. Crystallographically vacancy-induced MOF nanosheet as rational single-atom support for accelerating CO2 electroreduction to CO. Carbon. Energy. 2024, 6, e510.
19. Nitopi, S.; Bertheussen, E.; Scott, S. B.; et al. Progress and perspectives of electrochemical CO2 reduction on copper in aqueous electrolyte. Chem. Rev. 2019, 119, 7610-72.
20. Al-rowaili, F. N.; Jamal, A.; Ba, S. M. S.; Rana, A. A review on recent advances for electrochemical reduction of carbon dioxide to methanol using metal-organic framework (MOF) and Non-MOF catalysts: challenges and future prospects. ACS. Sustainable. Chem. Eng. 2018, 6, 15895-914.
21. Wu, J.; Zhou, X. Catalytic conversion of CO2 to value added fuels: current status, challenges, and future directions. Chin. J. Catal. 2016, 37, 999-1015.
22. Kibria, M. G.; Edwards, J. P.; Gabardo, C. M.; et al. Electrochemical CO2 reduction into chemical feedstocks: from mechanistic electrocatalysis models to system design. Adv. Mater. 2019, 31, e1807166.
23. Liang, C.; Kim, B.; Yang, S.; et al. High efficiency electrochemical reduction of CO2 beyond the two-electron transfer pathway on grain boundary rich ultra-small SnO2 nanoparticles. J. Mater. Chem. A. 2018, 6, 10313-9.
24. Hussain, M. S.; Ahmed, S.; Irshad, M.; et al. Recent engineering strategies for enhancing C2+ product formation in copper-catalyzed CO2 electroreduction. Nano. Mater. Sci. 2024. DOI: 10.1016/j.nanoms.2024.09.001.
25. Ma, M.; Djanashvili, K.; Smith, W. A. Selective electrochemical reduction of CO2 to CO on CuO-derived Cu nanowires. Phys. Chem. Chem. Phys. 2015, 17, 20861-7.
26. Reske, R.; Mistry, H.; Behafarid, F.; Roldan, C. B.; Strasser, P. Particle size effects in the catalytic electroreduction of CO2 on Cu nanoparticles. J. Am. Chem. Soc. 2014, 136, 6978-86.
27. Kas, R.; Kortlever, R.; Milbrat, A.; Koper, M. T.; Mul, G.; Baltrusaitis, J. Electrochemical CO2 reduction on Cu2O-derived copper nanoparticles: controlling the catalytic selectivity of hydrocarbons. Phys. Chem. Chem. Phys. 2014, 16, 12194-201.
28. Kuhl, K. P.; Cave, E. R.; Abram, D. N.; Jaramillo, T. F. New insights into the electrochemical reduction of carbon dioxide on metallic copper surfaces. Energy. Environ. Sci. 2012, 5, 7050-9.
29. Ogura, K.; Oohara, R.; Kudo, Y. Reduction of CO2 to ethylene at three-phase interface effects of electrode substrate and catalytic coating. J. Electrochem. Soc. 2005, 152, D213.
30. Han, H.; Han, T.; Luo, Y.; Mushtaq, M. A.; Jia, Y.; Liu, C. Recent advances in α-Fe2O3-based photocatalysts for CO2 conversion to solar fuels. J. Ind. Eng. Chem. 2023, 128, 81-94.
31. Trogadas, P.; Xu, L.; Coppens, M. O. From biomimicking to bioinspired design of electrocatalysts for CO2 reduction to C1 products. Angew. Chem. Int. Ed. 2024, 63, e202314446.
32. Wang, Y.; Han, P.; Lv, X.; Zhang, L.; Zheng, G. Defect and interface engineering for aqueous electrocatalytic CO2 reduction. Joule 2018, 2, 2551-82.
33. Qiao, J.; Liu, Y.; Hong, F.; Zhang, J. A review of catalysts for the electroreduction of carbon dioxide to produce low-carbon fuels. Chem. Soc. Rev. 2014, 43, 631-75.
34. Shen, H.; Jin, H.; Li, H.; et al. Acidic CO2-to-HCOOH electrolysis with industrial-level current on phase engineered tin sulfide. Nat. Commun. 2023, 14, 2843.
35. Zhao, K.; Quan, X. Carbon-based materials for electrochemical reduction of CO2 to C2+ oxygenates: recent progress and remaining challenges. ACS. Catal. 2021, 11, 2076-97.
36. Sun, Z.; Ma, T.; Tao, H.; Fan, Q.; Han, B. Fundamentals and challenges of electrochemical CO2 reduction using two-dimensional materials. Chem 2017, 3, 560-87.
37. Woldu, A. R.; Huang, Z.; Zhao, P.; Hu, L.; Astruc, D. Electrochemical CO2 reduction (CO2RR) to multi-carbon products over copper-based catalysts. Coord. Chem. Rev. 2022, 454, 214340.
38. Jiang, K.; Huang, Y.; Zeng, G.; Toma, F. M.; Goddard, W. A.; Bell, A. T. Effects of surface roughness on the electrochemical reduction of CO2 over Cu. ACS. Energy. Lett. 2020, 5, 1206-14.
39. Xiao, C.; Zhang, J. Architectural design for enhanced C2 product selectivity in electrochemical CO2 reduction using Cu-based catalysts: a review. ACS. Nano. 2021, 15, 7975-8000.
40. Cho, J. H.; Ma, J.; Kim, S. Y. Toward high-efficiency photovoltaics-assisted electrochemical and photoelectrochemical CO2 reduction: strategy and challenge. Exploration 2023, 3, 20230001.
41. Rhimi, B.; Zhou, M.; Yan, Z.; Cai, X.; Jiang, Z. Cu-based materials for enhanced C2+ product selectivity in photo-/electro-catalytic CO2 reduction: challenges and prospects. Nano-Micro. Lett. 2024, 16, 64.
42. Li, D.; Zhang, H.; Xiang, H.; et al. How to go beyond C1 products with electrochemical reduction of CO2. Sustainable. Energy. Fuels. 2021, 5, 5893-914.
43. Garza, A. J.; Bell, A. T.; Head-gordon, M. Mechanism of CO2 reduction at copper surfaces: pathways to C2 products. ACS. Catal. 2018, 8, 1490-9.
44. Lim, C. Y. J.; Yilmaz, M.; Arce-Ramos, J. M.; et al. Surface charge as activity descriptors for electrochemical CO2 reduction to multi-carbon products on organic-functionalised Cu. Nat. Commun. 2023, 14, 335.
45. Calle-Vallejo, F.; Koper, M. T. Theoretical considerations on the electroreduction of CO to C2 species on Cu(100) electrodes. Angew. Chem. Int. Ed. 2013, 52, 7282-5.
46. Ma, M.; Djanashvili, K.; Smith, W. A. Controllable hydrocarbon formation from the electrochemical reduction of CO2 over Cu nanowire arrays. Angew. Chem. Int. Ed. 2016, 55, 6680-4.
47. Wang, L.; Nitopi, S. A.; Bertheussen, E.; et al. Electrochemical carbon monoxide reduction on polycrystalline copper: effects of potential, pressure, and pH on selectivity toward multicarbon and oxygenated products. ACS. Catal. 2018, 8, 7445-54.
48. Rollier, F. A.; Muravev, V.; Parastaev, A.; et al. Restructuring of Cu-based catalysts during CO electroreduction: evidence for the dominant role of surface defects on the C2+ Product Selectivity. ACS. Catal. 2024, 14, 13246-59.
49. Chang, B.; Pang, H.; Raziq, F. Electrochemical reduction of carbon dioxide to multicarbon (C2+) products: challenges and perspectives. Energy. Environ. Sci. 2023, 16, 4714-58.
50. Zhang, X.; Guo, S.; Gandionco, K. A.; Bond, A. M.; Zhang, J. Electrocatalytic carbon dioxide reduction: from fundamental principles to catalyst design. Mater. Today. Adv. 2020, 7, 100074.
51. Ma, J.; Ahn, S. H.; Kim, S. Y. Integration of earth-abundant cocatalysts for high-performance photoelectrochemical energy conversion. J. Energy. Chem. 2024, 88, 336-55.
52. Meng, Y.; Ding, J.; Liu, Y.; et al. Advancements in amorphous oxides for electrocatalytic carbon dioxide reduction. Mater. Today. Catal. 2024, 7, 100065.
53. Fan, D.; Zhang, S.; Li, Y.; et al. High selective electrocatalytic reduction of carbon dioxide to ethylene enabled by regulating the microenvironment over Cu-Ag nanowires. J. Colloid. Interface. Sci. 2024, 662, 786-95.
54. Li, M.; Hu, Y.; Wu, T.; Sumboja, A.; Geng, D. How to enhance the C2 products selectivity of copper-based catalysts towards electrochemical CO2 reduction? Materials. Today. 2023, 67, 320-43.
55. Yu, H.; Wu, H.; Chow, Y. L.; Wang, J.; Zhang, J. Revolutionizing electrochemical CO2 reduction to deeply reduced products on non-Cu-based electrocatalysts. Energy. Environ. Sci. 2024, 17, 5336-64.
56. Giulimondi, V.; Mitchell, S.; Pérez-Ramírez, J. Challenges and opportunities in engineering the electronic structure of single-atom catalysts. ACS. Catal. 2023, 13, 2981-97.
57. Gu, Z.; Shen, H.; Chen, Z.; et al. Efficient electrocatalytic CO2 reduction to C2+ alcohols at defect-site-rich Cu surface. Joule 2021, 5, 429-40.
58. Xue, L.; Shi, T.; Han, C.; et al. Boosting hydrocarbon conversion via Cu-doping induced oxygen vacancies on CeO2 in CO2 electroreduction. J. Energy. Chem. 2025, 100, 66-76.
59. Fang, M.; Xia, W.; Han, S.; et al. Boosting CO2 electroreduction to multi-carbon products via oxygen-rich vacancies and Ce4+ -O2- -Cu + Structure in Cu/CeO2 for Stabilizing Cu+. ChemCatChem 2024, 16, e202301266.
60. Shen, B.; Jia, T.; Wang, H.; et al. Enhanced electrochemical CO2 reduction for high ethylene selectivity using iodine-doped copper oxide catalysts. J. Alloys. and. Compd. 2024, 980, 173550.
61. Jiang, Y.; Choi, C.; Hong, S.; et al. Enhanced electrochemical CO2 reduction to ethylene over CuO by synergistically tuning oxygen vacancies and metal doping. Cell. Rep. Phys. Sci. 2021, 2, 100356.
62. Bie, Q.; Yin, H.; Wang, Y.; Su, H.; Peng, Y.; Li, J. Electrocatalytic reduction of CO2 with enhanced C2 liquid products activity by the synergistic effect of Cu single atoms and oxygen vacancies. Chin. J. Catal. 2024, 57, 96-104.
63. Feng, X.; Jiang, K.; Fan, S.; Kanan, M. W. Grain-boundary-dependent CO2 electroreduction activity. J. Am. Chem. Soc. 2015, 137, 4606-9.
64. Bi, X.; Zhao, Y.; Yan, Y.; Wang, H.; Wu, M. Grain boundaries assisting the generation of abundant Cu+ for highly selective electroreduction of CO2 to ethanol. Green. Chem. 2024, 26, 5356-64.
65. Chen, Z.; Wang, T.; Liu, B.; et al. Grain-boundary-rich copper for efficient solar-driven electrochemical CO2 reduction to ethylene and ethanol. J. Am. Chem. Soc. 2020, 142, 6878-83.
66. Zhang, Y.; Qi, K.; Lyu, P.; et al. Grain-boundary engineering boosted undercoordinated active sites for scalable conversion of CO2 to ethylene. ACS. Nano. 2024, 18, 17483-91.
67. Ding, J.; Song, Q.; Xia, L. Unconventional grain fragmentation creates high-density boundaries for efficient CO2-to-C2+ electro-conversion at ampere-level current density. Nano. Energy. 2024, 128, 109945.
68. Kong, Y.; Yang, H.; Jia, X.; et al. Constructing favorable microenvironment on copper grain boundaries for CO2 electro-conversion to multicarbon products. Nano. Lett. 2024, 24, 9345-52.
69. Wu, W.; Tong, Y.; Chen, P. Regulation strategy of nanostructured engineering on indium-based materials for electrocatalytic conversion of CO2. Small 2024, 20, 2305562.
70. Zoubir, O.; Atourki, L.; Ait, A. H.; BaQais, A. Current state of copper-based bimetallic materials for electrochemical CO2 reduction: a review. RSC. Adv. 2022, 12, 30056-75.
71. Liu, G.; Zhan, J.; Zhang, Z.; Zhang, L. H.; Yu, F. Recent advances of the confinement effects boosting electrochemical CO2 reduction. Chem. Asian. J. 2023, 18, e202200983.
72. Kim, J. Y.; Hong, D.; Lee, J. C.; et al. Quasi-graphitic carbon shell-induced Cu confinement promotes electrocatalytic CO2 reduction toward C2+ products. Nat. Commun. 2021, 12, 3765.
73. Fan, L.; Geng, Q.; Ma, L.; et al. Evoking C2+ production from electrochemical CO2 reduction by the steric confinement effect of ordered porous Cu2O. Chem. Sci. 2023, 14, 13851-9.
74. Liu, L. X.; Cai, Y.; Du, H.; et al. Enriching the local concentration of CO intermediates on Cu cavities for the electrocatalytic reduction of CO2 to C2+ products. ACS. Appl. Mater. Interfaces. 2023, 15, 16673-9.
75. Pan, Y.; Li, H.; Xiong, J.; et al. Protecting the state of Cu clusters and nanoconfinement engineering over hollow mesoporous carbon spheres for electrocatalytical C-C coupling. Appl. Catal. B. Environ. 2022, 306, 121111.
76. Liu, C.; Zhang, M.; Li, J.; et al. Nanoconfinement engineering over hollow multi-shell structured copper towards efficient electrocatalytical C-C coupling. Angew. Chem. Int. Ed. 2022, 61, e202113498.
77. Wu, M.; Zhu, C.; Mao, J.; et al. Dimensional effect of oxide-derived Cu electrocatalysts to reduce CO2 into multicarbon compounds. Chem. Eng. J. 2024, 499, 156006.
78. Xie, H.; Xie, R.; Zhang, Z.; et al. Achieving highly selective electrochemical CO2 reduction to C2H4 on Cu nanosheets. J. Energy. Chem. 2023, 79, 312-20.
79. Wang, P.; Meng, S.; Zhang, B.; et al. Sub-1 nm Cu2O nanosheets for the electrochemical CO2 reduction and valence state-activity relationship. J. Am. Chem. Soc. 2023, 145, 26133-43.
80. Yang, F.; Yang, T.; Li, J.; et al. Boosting the electroreduction of CO2 to liquid products via nanostructure engineering of Cu2O catalysts. J. Catal. 2024, 432, 115458.
81. Gregorio GL, Burdyny T, Loiudice A, Iyengar P, Smith WA, Buonsanti R. Facet-dependent selectivity of Cu catalysts in electrochemical CO2 reduction at commercially viable current densities. ACS. Catal. 2020, 10, 4854-62.
82. Fu, Y.; Xie, Q.; Wu, L.; Luo, J. Crystal facet effect induced by different pretreatment of Cu2O nanowire electrode for enhanced electrochemical CO2 reduction to C2+ products. Chin. J. Catal. 2022, 43, 1066-73.
83. Dong, Y.; Ma, X.; Jin, Z.; et al. Full-exposed Cu site of Cu2O-(100) driven high ethylene selectivity of carbon dioxide reduction. Appl. Surf. Sci. 2024, 653, 159243.
84. Luo, H.; Li, B.; Ma, J. G.; Cheng, P. Surface modification of nano-Cu2O for controlling CO2 electrochemical reduction to ethylene and syngas. Angew. Chem. Int. Ed. 2022, 61, e202116736.
85. Merino-Garcia, I.; Albo, J.; Irabien, A. Tailoring gas-phase CO2 electroreduction selectivity to hydrocarbons at Cu nanoparticles. Nanotechnology 2018, 29, 014001.
86. Rong, W.; Zou, H.; Zang, W.; et al. Size-dependent activity and selectivity of atomic-level copper nanoclusters during CO/CO2 electroreduction. Angew. Chem. Int. Ed. 2021, 60, 466-72.
87. Nam, D. H.; Bushuyev, O. S.; Li, J.; et al. Metal-organic frameworks mediate Cu coordination for selective CO2 electroreduction. J. Am. Chem. Soc. 2018, 140, 11378-86.
88. Su, X.; Jiang, Z.; Zhou, J.; et al. Complementary operando spectroscopy identification of in-situ generated metastable charge-asymmetry Cu2-CuN3 clusters for CO2 reduction to ethanol. Nat. Commun. 2022, 13, 1322.
89. Tabassum, H.; Yang, X.; Zou, R.; Wu, G. Surface engineering of Cu catalysts for electrochemical reduction of CO2 to value-added multi-carbon products. Chem. Catal. 2022, 2, 1561-93.
90. Fang, M.; Wang, M.; Wang, Z.; et al. Hydrophobic, ultrastable Cuδ+ for Robust CO2 electroreduction to C2 products at ampere-current levels. J. Am. Chem. Soc. 2023, 145, 11323-32.
91. Mu, S.; Li, L.; Zhao, R.; Lu, H.; Dong, H.; Cui, C. Molecular-scale insights into electrochemical reduction of CO2 on hydrophobically modified Cu surfaces. ACS. Appl. Mater. Interfaces. 2021, 13, 47619-28.
92. Xie, M. S.; Xia, B. Y.; Li, Y.; et al. Amino acid modified copper electrodes for the enhanced selective electroreduction of carbon dioxide towards hydrocarbons. Energy. Environ. Sci. 2016, 9, 1687-95.
93. Wei, X.; Yin, Z.; Lyu, K.; et al. Highly Selective reduction of CO2 to C2+ hydrocarbons at copper/polyaniline interfaces. ACS. Catal. 2020, 10, 4103-11.
94. Ma, L.; Geng, Q.; Fan, L.; et al. Enhanced electroreduction of CO2 to C2+ fuels by the synergetic effect of polyaniline/CuO nanosheets hybrids. Nano. Res. 2023, 16, 9065-72.
95. Wakerley, D.; Lamaison, S.; Ozanam, F.; et al. Bio-inspired hydrophobicity promotes CO2 reduction on a Cu surface. Nat. Mater. 2019, 18, 1222-7.
96. Shi, T.; Liu, D.; Feng, H.; Zhang, Y.; Li, Q. Evolution of triple-phase interface for enhanced electrochemical CO2 reduction. Chem. Eng. J. 2022, 431, 134348.
97. Niu, Z. Z.; Gao, F. Y.; Zhang, X. L.; et al. Hierarchical copper with inherent hydrophobicity mitigates electrode flooding for high-rate CO2 electroreduction to multicarbon products. J. Am. Chem. Soc. 2021, 143, 8011-21.
98. Liu, Z.; Lv, X.; Kong, S.; et al. Interfacial water tuning by intermolecular spacing for stable CO2 electroreduction to C2+ products. Angew. Chem. Int. Ed. 2023, 62, e202309319.
99. Xie, L.; Jiang, Y.; Zhu, W. Cu-based catalyst designs in CO2 electroreduction: precise modulation of reaction intermediates for high-value chemical generation. Chem. Sci. 2023, 14, 13629-60.
100. Xie, G.; Guo, W.; Fang, Z.; et al. Dual-metal sites drive tandem electrocatalytic CO2 to C2+ products. Angew. Chem. Int. Ed. 2024, 63, e202412568.
101. Zhu, C.; Zhang, Z.; Qiao, R.; et al. Selective tandem CO2-to-C2+ alcohol conversion at a single-crystal Au/Cu bimetallic interface. J. Phys. Chem. C. 2023, 127, 3470-7.
102. Zhang, B.; Wang, L.; Li, D.; Li, Z.; Bu, R.; Lu, Y. Tandem strategy for electrochemical CO2 reduction reaction. Chem. Catal. 2022, 2, 3395-429.
103. Zhan, C.; Dattila, F.; Rettenmaier, C.; et al. Key intermediates and Cu active sites for CO2 electroreduction to ethylene and ethanol. Nat. Energy. 2024, 9, 1485-96.
104. Qin, Q.; Suo, H.; Chen, L.; et al. Emerging Cu-Based tandem catalytic systems for CO2 electroreduction to multi-carbon products. Adv. Mater. Inter. 2024, 11, 2301049.
105. Duan, H.; Li, W.; Ran, L.; et al. In-situ electrochemical interface of Cu@Ag/C towards the ethylene electrosynthesis with adequate *CO supply. J. Energy. Chem. 2024, 99, 292-9.
106. Jeon, Y. E.; Ko, Y. N.; Kim, J.; et al. Selective production of ethylene from CO2 over CuAg tandem electrocatalysts. J. Ind. Eng. Chem. 2022, 116, 191-8.
107. Liu, H.; Sun, C.; Wu, M.; et al. High-performance carbon dioxide reduction to multi-carbon products on EDTA-modified Cu-Ag tandem catalyst. J. Catal. 2024, 429, 115227.
108. Luan, P.; Dong, X.; Liu, L.; et al. Selective electrosynthesis of ethanol via asymmetric C-C coupling in tandem CO2 reduction. ACS. Catal. 2024, 14, 8776-85.
109. Huang, J.; Mensi, M.; Oveisi, E.; Mantella, V.; Buonsanti, R. Structural sensitivities in bimetallic catalysts for electrochemical CO2 reduction revealed by Ag-Cu nanodimers. J. Am. Chem. Soc. 2019, 141, 2490-9.
110. Ma, Y.; Yu, J.; Sun, M.; et al. Confined growth of silver-copper janus nanostructures with {100} facets for highly selective tandem electrocatalytic carbon dioxide reduction. Adv. Mater. 2022, 34, e2110607.
111. Wei, C.; Yang, Y.; Ma, H.; et al. Nanoscale management of CO transport in CO2 electroreduction: boosting faradaic efficiency to multicarbon products via nanostructured tandem electrocatalysts. Adv. Funct. Mater. 2023, 33, 2214992.
112. Morales-guio, C. G.; Cave, E. R.; Nitopi, S. A.; et al. Improved CO2 reduction activity towards C2+ alcohols on a tandem gold on copper electrocatalyst. Nat. Catal. 2018, 1, 764-71.
113. Wang, S.; Jung, H. D.; Choi, H.; Kim, J.; Back, S.; Oh, J. Delicate control of a gold-copper oxide tandem structure enables the efficient production of high-value chemicals by electrochemical carbon dioxide reduction. Nano. Energy. 2024, 130, 110176.
114. Cao, X.; Cao, G.; Li, M.; et al. Enhanced ethylene formation from carbon dioxide reduction through sequential catalysis on Au decorated cubic Cu2O electrocatalyst. Eur. J. Inorg. Chem. 2021, 2021, 2353-64.
115. Zhu, C.; Zhou, L.; Zhang, Z.; et al. Dynamic restructuring of epitaxial Au-Cu biphasic interface for tandem CO2-to-C2+ alcohol conversion. Chem 2022, 8, 3288-301.
116. Wei, Z.; Yue, S.; Gao, S.; Cao, M.; Cao, R. Synergetic effects of gold-doped copper nanowires with low Au content for enhanced electrocatalytic CO2 reduction to multicarbon products. Nano. Res. 2023, 16, 7777-83.
117. Zheng, Y.; Zhang, J.; Ma, Z.; et al. Seeded growth of gold-copper janus nanostructures as a tandem catalyst for efficient electroreduction of CO2 to C2+ products. Small 2022, 18, e2201695.
118. Huang, J.; Zhang, X.; Yang, J.; Yu, J.; Chen, Q.; Peng, L. Recent progress on copper-based bimetallic heterojunction catalysts for CO2 electrocatalysis: unlocking the mystery of product selectivity. Adv. Sci. 2024, 11, 2309865.
119. Li, Y.; Sun, Y.; Yu, M. Strategies for improving product selectivity in electrocatalytic carbon dioxide reduction using copper-based catalysts. Adv. Funct. Mater. 2024, 34, 2410186.
120. Wan, L.; Zhang, X.; Cheng, J.; et al. Bimetallic Cu-Zn catalysts for electrochemical CO2 reduction: phase-separated versus core-shell distribution. ACS. Catal. 2022, 12, 2741-8.
121. Liu, J.; Yu, K.; Qiao, Z.; Zhu, Q.; Zhang, H.; Jiang, J. Integration of cobalt phthalocyanine, acetylene black and Cu2O nanocubes for efficient electroreduction of CO2 to C2H4. ChemSusChem 2023, 16, e202300601.
122. Kong, X.; Zhao, J.; Ke, J.; et al. Understanding the effect of *CO coverage on C-C coupling toward CO2 electroreduction. Nano. Lett. 2022, 22, 3801-8.
123. Min, S.; Xu, X.; He, J.; Sun, M.; Lin, W.; Kang, L. Construction of cobalt porphyrin-modified Cu2O nanowire array as a tandem electrocatalyst for enhanced CO2 reduction to C2 products. Small 2024, 20, 2400592.
124. Chen, Y.; Ji, S.; Chen, C.; Peng, Q.; Wang, D.; Li, Y. Single-atom catalysts: synthetic strategies and electrochemical applications. Joule 2018, 2, 1242-64.
125. Zhang, L.; Wang, K.; Zhu, G.; Shi, J.; Zhu, H. Assembly of colloidal Cu nanoparticles and Ni-N-C nanocarbons to electrochemically boost cascade production of ethylene from CO2 reduction. J. Mater. Sci. 2023, 58, 17200-10.
126. Zhang, Y.; Li, P.; Zhao, C.; et al. Multicarbons generation factory: CuO/Ni single atoms tandem catalyst for boosting the productivity of CO2 electrocatalysis. Sci. Bull. 2022, 67, 1679-87.
127. Liu, M.; Wang, Q.; Luo, T.; et al. Potential alignment in tandem catalysts enhances CO2-to-C2H4 conversion efficiencies. J. Am. Chem. Soc. 2024, 146, 468-75.
128. Meng, D. L.; Zhang, M. D.; Si, D. H.; et al. Highly selective tandem electroreduction of CO2 to ethylene over atomically isolated nickel-nitrogen site/copper nanoparticle catalysts. Angew. Chem. Int. Ed. 2021, 60, 25689-96.
129. Chen, B.; Gong, L.; Li, N.; et al. Tandem catalysis for enhanced CO2 to ethylene conversion in neutral media. Adv. Funct. Mater. 2024, 34, 2310029.
130. Paris, A. R.; Bocarsly, A. B. Ni-Al films on glassy carbon electrodes generate an array of oxygenated organics from CO2. ACS. Catal. 2017, 7, 6815-20.
131. Torelli, D. A.; Francis, S. A.; Crompton, J. C.; et al. Nickel-gallium-catalyzed electrochemical reduction of CO2 to highly reduced products at low overpotentials. ACS. Catal. 2016, 6, 2100-4.
132. Ding, J.; Bin, Y. H.; Ma, X.; et al. A tin-based tandem electrocatalyst for CO2 reduction to ethanol with 80% selectivity. Nat. Energy. 2023, 8, 1386-94.
133. She, X.; Wang, Y.; Xu, H.; Chi, E. T. S.; Ping, L. S. Challenges and opportunities in electrocatalytic CO2 reduction to chemicals and fuels. Angew. Chem. Int. Ed. 2022, 61, e202211396.
134. Ewis, D.; Arsalan, M.; Khaled, M.; et al. Electrochemical reduction of CO2 into formate/formic acid: A review of cell design and operation. Sep. Purif. Technol. 2023, 316, 123811.
135. Harthi A, Abri MA, Younus HA, Hajri RA. Criteria and cutting-edge catalysts for CO2 electrochemical reduction at the industrial scale. J. CO2. Util. 2024, 83, 102819.
136. Sajna, M.; Zavahir, S.; Popelka, A.; et al. Electrochemical system design for CO2 conversion: a comprehensive review. J. Environ. Chem. Eng. 2023, 11, 110467.
137. Kim, J.; Ahn, S. H. Recent progress in carbon dioxide electrolyzer using gas diffusion electrode. Ceramist 2021, 24, 96-108.
138. Luo, Y.; Zhang, K.; Li, Y.; Wang, Y. Valorizing carbon dioxide via electrochemical reduction on gas-diffusion electrodes. InfoMat 2021, 3, 1313-32.
139. Zhang, F. Y.; Sheng, T.; Tian, N.; et al. Cu overlayers on tetrahexahedral Pd nanocrystals with high-index facets for CO2 electroreduction to alcohols. Chem. Commun. 2017, 53, 8085-8.
140. Salvatore, D.; Berlinguette, C. P. Voltage matters when reducing CO2 in an electrochemical flow cell. ACS. Energy. Lett. 2020, 5, 215-20.
141. Chen, J.; Qiu, H.; Zhao, Y.; et al. Selective and stable CO2 electroreduction at high rates via control of local H2O/CO2 ratio. Nat. Commun. 2024, 15, 5893.
142. Lee, G.; Rasouli, A. S.; Lee, B.; et al. CO2 electroreduction to multicarbon products from carbonate capture liquid. Joule 2023, 7, 1277-88.
143. Ni, W.; Chen, H.; Tang, N.; et al. High-purity ethylene production via indirect carbon dioxide electrochemical reduction. Nat. Commun. 2024, 15, 6078.
144. Weekes, D. M.; Salvatore, D. A.; Reyes, A.; Huang, A.; Berlinguette, C. P. Electrolytic CO2 reduction in a flow cell. Acc. Chem. Res. 2018, 51, 910-8.
145. Sato, S.; Sekizawa, K.; Shirai, S.; Sakamoto, N.; Morikawa, T. Enhanced performance of molecular electrocatalysts for CO2 reduction in a flow cell following K+ addition. Sci. Adv. 2023, 9, eadh9986.
146. Ampelli, C.; Tavella, F.; Giusi, D.; Ronsisvalle, A. M.; Perathoner, S.; Centi, G. Electrode and cell design for CO2 reduction: a viewpoint. Catal. Today. 2023, 421, 114217.
147. Tufa, R. A.; Chanda, D.; Ma, M.; et al. Towards highly efficient electrochemical CO2 reduction: cell designs, membranes and electrocatalysts. Appl. Energy. 2020, 277, 115557.
148. Xing, Z.; Hu, L.; Ripatti, D. S.; Hu, X.; Feng, X. Enhancing carbon dioxide gas-diffusion electrolysis by creating a hydrophobic catalyst microenvironment. Nat. Commun. 2021, 12, 136.
149. Yang, K.; Kas, R.; Smith, W. A.; Burdyny, T. Role of the carbon-based gas diffusion layer on flooding in a gas diffusion electrode cell for electrochemical CO2 reduction. ACS. Energy. Lett. 2021, 6, 33-40.
150. Jiang, H.; Luo, R.; Li, Y.; Chen, W. Recent advances in solid-liquid-gas three-phase interfaces in electrocatalysis for energy conversion and storage. EcoMat 2022, 4, e12199.
151. Wang, J.; Ji, Q.; Zang, H.; et al. Atomically dispersed ga synergy lewis acid-base pairs in F-doped mesoporous Cu2O for efficient eletroreduction of CO2 to C2+ products. Adv. Funct. Mater. 2024, 34, 2404274.
152. Yang, C.; Wang, R.; Yu, C.; et al. Engineering stable Cu+-Cu0 sites and oxygen defects in boron-doped copper oxide for electrocatalytic reduction of CO2 to C2+ products. Chem. Eng. J. 2024, 484, 149710.
153. Chen, Q.; Wang, X.; Zhou, Y.; et al. Electrocatalytic CO2 reduction to C2+ products in flow cells. Adv. Mater. 2024, 36, 2303902.
154. Yu, J.; Xiao, J.; Ma, Y.; et al. Acidic conditions for efficient carbon dioxide electroreduction in flow and MEA cells. Chem. Catal. 2023, 3, 100670.
155. Wang, B.; Song, L.; Peng, C.; Lv, X.; Zheng, G. Pd-induced polarized Cu0-Cu+ sites for electrocatalytic CO2-to-C2+ conversion in acidic medium. J. Colloid. Interface. Sci. 2024, 671, 184-91.
156. Wang, Z.; Zhou, Y.; Qiu, P.; et al. Advanced catalyst design and reactor configuration upgrade in electrochemical carbon dioxide conversion. Adv. Mater. 2023, 35, 2303052.
157. Choi, W.; Park, S.; Jung, W.; Won, D. H.; Na, J.; Hwang, Y. J. Origin of hydrogen incorporated into ethylene during electrochemical CO2 reduction in membrane electrode assembly. ACS. Energy. Lett. 2022, 7, 939-45.
158. Rabiee, H.; Ma, B.; Yang, Y.; et al. Advances and challenges of carbon-free gas-diffusion electrodes (GDEs) for electrochemical CO2 reduction. Adv. Funct. Mater. 2025, 35, 2411195.
159. Ge, L.; Rabiee, H.; Li, M.; et al. Electrochemical CO2 reduction in membrane-electrode assemblies. Chem 2022, 8, 663-92.
160. Gawel, A.; Jaster, T.; Siegmund, D.; et al. Electrochemical CO2 reduction - the macroscopic world of electrode design, reactor concepts & economic aspects. iScience 2022, 25, 104011.
161. Lee, T.; Lee, Y.; Eo, J.; Nam, D. H. Acidic CO2 electroreduction for high CO2 utilization: catalysts, electrodes, and electrolyzers. Nanoscale 2024, 16, 2235-49.
162. Alinejad, S.; Quinson, J.; Li, Y.; et al. Optimizing the use of a gas diffusion electrode setup for CO2 electrolysis imitating a zero-gap MEA design. J. Catal. 2024, 429, 115209.
163. Larrea, C.; Torres, D.; Avilés-moreno, J. R.; Ocón, P. Multi-parameter study of CO2 electrochemical reduction from concentrated bicarbonate feed. J. CO2. Util. 2022, 57, 101878.
164. Bui, J. C.; Kim, C.; King, A. J.; et al. Engineering catalyst-electrolyte microenvironments to optimize the activity and selectivity for the electrochemical reduction of CO2 on Cu and Ag. Acc. Chem. Res. 2022, 55, 484-94.
165. Lai, W.; Qiao, Y.; Zhang, J.; Lin, Z.; Huang, H. Design strategies for markedly enhancing energy efficiency in the electrocatalytic CO2 reduction reaction. Energy. Environ. Sci. 2022, 15, 3603-29.
166. Ozden, A.; Li, F.; Garcı́a, A. F. P.; et al. High-rate and efficient ethylene electrosynthesis using a catalyst/promoter/transport layer. ACS. Energy. Lett. 2020, 5, 2811-8.
167. He, R.; Xu, N.; Hasan, I. M. U.; et al. Advances in electrolyzer design and development for electrochemical CO2 reduction. EcoMat 2023, 5, e12346.
168. Xia, C.; Zhu, P.; Jiang, Q.; et al. Continuous production of pure liquid fuel solutions via electrocatalytic CO2 reduction using solid-electrolyte devices. Nat. Energy. 2019, 4, 776-85.
169. Gong, Y.; He, T. Gaining deep understanding of electrochemical CO2RR with in situ/operando techniques. Small. Methods. 2023, 7, 2300702.
170. Delmo, E. P.; Wang, Y.; Song, Y.; et al. In situ infrared spectroscopic evidence of enhanced electrochemical CO2 reduction and C-C coupling on oxide-derived copper. J. Am. Chem. Soc. 2024, 146, 1935-45.
171. Xu, H.; Fan, Z.; Zhu, S.; Shao, M. A minireview on selected applications of in situ infrared spectroscopy in studying CO2 electrochemical reduction reaction. Curr. Opin. Electrochem. 2023, 41, 101363.
172. Chen, L.; Zhang, C.; Jiao, X. Recent advances of in situ insights into CO2 reduction toward fuels. ChemCatChem 2025, 17, e202401388.
173. Jin, L.; Seifitokaldani, A. In situ spectroscopic methods for electrocatalytic CO2 reduction. Catalysts 2020, 10, 481.
174. Katayama, Y.; Nattino, F.; Giordano, L.; et al. An in situ surface-enhanced infrared absorption spectroscopy study of electrochemical CO2 reduction: selectivity dependence on surface C-bound and O-bound reaction intermediates. J. Phys. Chem. C. 2019, 123, 5951-63.
175. Dutta, A.; Kuzume, A.; Rahaman, M.; Vesztergom, S.; Broekmann, P. Monitoring the chemical state of catalysts for CO2 electroreduction: an in operando study. ACS. Catal. 2015, 5, 7498-502.
176. Zhu, P.; Qin, Y.; Cai, X.; et al. Understanding oxidation state of Cu-based catalysts for electrocatalytic CO2 reduction. J. Mater. Sci. Technol. 2025, 218, 1-24.
177. Firet, N. J.; Smith, W. A. Probing the reaction mechanism of CO2 electroreduction over Ag films via operando infrared spectroscopy. ACS. Catal. 2017, 7, 606-12.
178. Chen, M.; Liu, D.; Qiao, L.; et al. In-situ/operando raman techniques for in-depth understanding on electrocatalysis. Chem. Eng. J. 2023, 461, 141939.
179. Celorrio, V.; Leach, A. S.; Huang, H.; et al. Relationship between Mn oxidation state changes and oxygen reduction activity in (La,Ca)MnO3 as probed by in situ XAS and XES. ACS. Catal. 2021, 11, 6431-9.
180. Song, X.; Xu, L.; Sun, X.; Han, B. In situ/operando characterization techniques for electrochemical CO2 reduction. Sci. China. Chem. 2023, 66, 315-23.
181. You, S.; Xiao, J.; Liang, S.; et al. Doping engineering of Cu-based catalysts for electrocatalytic CO2 reduction to multi-carbon products. Energy. Environ. Sci. 2024, 17, 5795-818.
182. Popović, S.; Smiljanić, M.; Jovanovič, P.; Vavra, J.; Buonsanti, R.; Hodnik, N. Stability and degradation mechanisms of copper-based catalysts for electrochemical CO2 reduction. Angew. Chem. Int. Ed. 2020, 59, 14736-46.
Cite This Article
How to Cite
Ma, J.; Kim, S. Y. Development of catalysts and reactor designs for CO2 electroreduction towards C2+ products. Energy Mater. 2025, 5, 500052. http://dx.doi.org/10.20517/energymater.2024.237
Download Citation
Export Citation File:
Type of Import
Tips on Downloading Citation
Citation Manager File Format
Type of Import
Direct Import: When the Direct Import option is selected (the default state), a dialogue box will give you the option to Save or Open the downloaded citation data. Choosing Open will either launch your citation manager or give you a choice of applications with which to use the metadata. The Save option saves the file locally for later use.
Indirect Import: When the Indirect Import option is selected, the metadata is displayed and may be copied and pasted as needed.
About This Article
Copyright
Data & Comments
Data
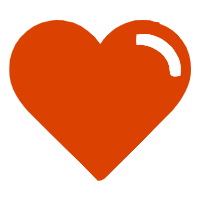
Comments
Comments must be written in English. Spam, offensive content, impersonation, and private information will not be permitted. If any comment is reported and identified as inappropriate content by OAE staff, the comment will be removed without notice. If you have any queries or need any help, please contact us at [email protected].