Recent advances and challenges of fluid manipulation on microstructured surfaces
Abstract
Microstructured surfaces play a pivotal role in fluid manipulation, leveraging their unique chemical and physical properties to exert precise control over fluid behavior. These structures significantly influence fluid wettability, adhesion, mobility, and dynamic behavior, offering broad prospects in microfluidics, biomedicine, energy, materials science, and other fields. Despite existing challenges related to stability, wear resistance and manufacturing processes, the field of microstructured fluid control holds substantial promise for future advancements. This review surveys the latest advancements in microstructured surface fluid control technology, spanning from the design and fabrication of microstructured surfaces to their applications and deployment across various domains. We initially explore the design principles and fabrication methods of microstructured surfaces, and delve into the strategies employed for fluid manipulation by modulating surface chemistry and morphography. Additionally, the applications of microstructured surfaces in microfluidic control, biomedical engineering, energy harvesting, and environmental monitoring are further emphasized and discussed, showcasing the significant contributions to technological innovation. Finally, the current technical challenges and potential applications of liquid manipulation on microstructured surfaces are featured, and their prospects are discussed based on the current development.
Keywords
INTRODUCTION
The manipulation of fluids on microstructured surfaces is of crucial importance in various fields such as aerospace[1,2], electronic information[3], automotive energy[4-6], and healthcare[7], attracting widespread academic attention. For instance, in microfluidic systems, the controllable manipulation of fluids can significantly enhance operational efficiency, making complex and precise fluid management, which holds promise for applications in biochips, drug delivery systems, and integrated laboratory platforms (commonly known as “lab-on-a-chip” technology)[8-11]. Through the adept regulation of fluid dynamics at micro and nanoscale interfaces, innovative sensors and actuators are emerging, heralding transformative applications in environmental surveillance, energy transmutation, and precision fabrication. Moreover, the control of fluids on microstructured surfaces plays a pivotal role in elucidating and emulating natural fluid phenomena, thereby furnishing a robust theoretical framework and practical underpinning for the field of bionic engineering[12-14].
Against this backdrop, research on microstructured surface fluid manipulation has experienced explosive growth and is poised for further development. For researchers in this field, it is essential to understand the following questions: What are the mechanisms of fluid dynamics on microstructured surfaces? Only with correct theoretical guidance can the accuracy of research outcomes be ensured. Based on these theories, how should microstructured surfaces be designed? Many biological surfaces have evolved to possess special wetting properties, and biomimetic preparation of surfaces is a commonly used method. In 2002, the micro-nano composite structure on the lotus leaf surface was proven to be the critical factor for achieving high apparent contact angles and low adhesion[15]. This work first highlighted the impact of multi-scale microstructures on superhydrophobic properties. With the advancement of nanotechnology, microstructured surfaces with characteristics such as orderliness and periodicity have been fabricated using various physical and chemical methods. By designing microstructures with different shapes and arrangements, they can possess distinct properties and functions. Common fabrication methods include laser ablation[16-21], chemical etching[22,23], template methods[24-26], three-dimensional (3D) printing[27-31], etc. Furthermore, how can the various microstructured surfaces designed and fabricated be applied in real-world problems? The ultimate goal of scientific research is to address issues encountered in social development, and utilizing these tools to solve relevant problems is one of the means to promote societal progress. In summary, a review and summary of the design, fabrication, and fluid manipulation on microstructured surfaces will provide better guidance for research in microstructured surface fluid dynamics.
In this review, we first introduce the wetting mechanisms of fluids on various microstructured surfaces. Subsequently, the fabrication of different microstructured surfaces and their fluid manipulation research is focused upon, with their fluid manipulation performances being compared. Furthermore, an overview of the pivotal applications of microstructured surface fluid manipulation across different fields is provided. In conclusion, the future of microstructured surface fabrication and application is projected, with discussions focusing on potential developments and their implications [Figure 1].
FUNDAMENTAL PRINCIPLES OF MANIPULATION ON MICROSTRUCTURED SURFACE
Wettability, also known as wetting property, can be defined as the tendency of a liquid to spread over a solid substrate. It describes the degree of contact between liquid and solid phases. Under equilibrium conditions, governed by thermodynamic laws, it depends on the surface energy and interfacial energies at the solid/liquid interface. When the three phases-solid, liquid, and vapor-are in balance, drawing a tangent line at the triple phase boundary where the gas/liquid interface meets the solid, the angle formed between this tangent and the solid-liquid intersection line is called the contact angle (θ). The concept of contact angles was initially proposed by Young in 1805[32]. The angles are widely utilized to characterize interfacial phenomena, wetting/dewetting of solid surfaces, capillary penetration in porous media, coatings, etc[33,34]. Generally, the contact angle is used to measure the extent of liquid's wetting ability towards solids: when θ > 90°, the solid surface is considered hydrophobic, and larger values of θ indicate poorer wetting; when θ < 90°, the surface is deemed hydrophilic, with smaller values suggesting enhanced wetting capability. In recent years, Liu et al.[35,36] have redefined the wettability of liquid and introduced new boundaries for hydrophilicity and hydrophobicity set at 65°, instead of 90° predicted by Yang’s equation, which is called the intrinsic wetting threshold of water (θ*). Formation of the contact angle is an external manifestation of the balanced surface tensions among solid, liquid, and vapor interfaces.
Assuming ideal conditions where a pure liquid wets and spreads on an inert smooth solid surface, the driving force Fd(t) for wetting is expressed as
Where γab denotes the interfacial tension between phases a and b, with subscripts s, l, and v representing solid, liquid, and vapor phases, respectively. θ (t) signifies the contact angle at time t. At equilibrium, liquid spreading ceases. Thus, the droplet at this point experiences no net driving force, Fd (t) = 0. Under this condition, Young’s equation becomes
Where θ is the equilibrium contact angle, often referred to as the intrinsic contact angle since Young’s equation applies ideally to surfaces.
To accurately describe the contact angle of droplets on actual rough surfaces, Wenzel et al.[37] built upon Young’s framework by introducing a roughness factor, quantifying liquid wettability on roughened surfaces:
Where r represents the surface roughness, denoting the ratio of the contact area between the droplet and the rough surface to that of a smooth surface; θr denotes the apparent contact angle of the droplet. Physical roughness gradients lead to differing contact angles on either side of the droplet, generating a gradient in surface free energy[38]
Here,
Subsequently, Cassie and Baxter extended Wenzel’s work by considering chemically heterogeneous surfaces, proposing a composite contact model[43]:
Where f1 and f2 denote ratios of the contact areas of the liquid with substance 1 and substance 2 to the total contact area; θ1 and θ2 are the intrinsic contact angles for substances 1 and 2, respectively. Gradients in chemical composition change the contact angle of droplets on the surface, resulting in changes in surface energy:
For surfaces with chemical component gradients, droplets demonstrate a tendency to move spontaneously toward the hydrophilic end. A larger value of dE indicates a greater surface energy gradient, making the droplet’s movement toward the hydrophilic region more pronounced.
FABRICATION AND FLUID MANIPULATION OF MICROSTRUCTURED SURFACES
The distinction among isotropic, anisotropic, and intelligent microstructured surfaces is essential due to their unique properties and applications. The isotropic surface has a uniform microstructure and exhibits uniform wetting behavior in all directions, and the hydrophilicity and adhesion of droplets can be adjusted by changing the surface chemistry or morphology, which is suitable for self-cleaning coating research. Anisotropic surfaces, with their directional microstructures, enable precise control over liquid flow direction and speed, which is crucial for advanced technologies such as microfluidic chips and biosensors. Intelligent microstructured surfaces could respond to external stimuli by dynamically adjusting their wetting behavior, providing real-time control for applications such as adaptive optics and lab-on-a-chip devices. Herein, we will discuss in detail from the following three aspects.
Fabrication method
Many natural materials have excellent physical and chemical properties due to the existence of surface microstructure. The microstructure surface generally has the characteristics of order and periodicity, and it can have different properties and realize different functions by designing the microstructure with various shapes and arrangements. Because microstructure surface has broad application prospects in water collection, microfluidic equipment, energy collection and transfer, heat transfer, aerospace and other fields, it is particularly important to study its preparation methods and properties. Several common methods for preparing microstructure surfaces will be introduced here[44-46].
Etching method
Etching refers to the process technology of uniformly removing the bare film or surface substance on the substrate surface using physical or chemical methods under the protection of the mask, including wet and dry etching. Wet etching is to use the chemical reaction between a specific solution and the film to remove the part of the film that is not covered by the photoresist mask, and achieve the purpose of etching. Dry etching is the use of radio frequency (RF) power to generate ions and electrons with high reactivity of the reaction gas, physical bombardment and chemical reaction on the silicon wafer to selectively remove unwanted areas. The etched material becomes a volatile gas, which is extracted by the extraction system, and finally etched to the required depth according to the design graphic requirements. Traditional laser etching may have the problem of uneven etching depth. In order to improve this process, multi-beam laser etching technology can be used. By precisely controlling the energy, angle and pulse frequency of multiple laser beams, a more uniform etching on the surface of the microstructure can be achieved.
Template method
Template method is based on the spatial limit of template to control the size, morphology and structure of synthetic nanomaterials. In practical application, the microstructure etched on the surface is generally extended to prepare the replica template with resin or artificial rubber and other materials through the replica technology, and then the material surface with a specific structure is prepared under the guidance of the replica template. Template method has the advantages of flexible synthesis of nanomaterials, simple experimental devices, mild operating conditions, accurate control of the size, morphology and structure of nanomaterials, and preventing the occurrence of nanomaterials agglomeration. In the hard template method, the partial filling of raw materials will cause the product to discontinue in the pore, resulting in structural defects. Additionally, removing the formwork may cause partial tunnel structure collapse or affect product properties. Thus, it is essential to design a more reasonable template structure to improve the stability of the template and ease of removal while minimizing the impact on the structure and performance of the product. Additionally, it is important to explore a wider range of formwork materials, especially those with special properties and functions, to meet the needs of different application scenarios.
3D printing method
Three-dimensional printing is an additive manufacturing method, based on digital model files, the use of metals, polymers and other materials, with layer-by-layer printing, stacking, and forming a physical object. This technique is the embodiment of the close combination of digital and manufacturing. Although 3D printing has unique advantages in manufacturing complex microstructure surfaces, there is currently a contradiction between its speed and accuracy. To improve this process, dual-material 3D printing technology can be used. In production applications, 3D printing also can be closely integrated with computer-aided design (CAD) software.
Isotropic microstructured surface
Controlling material surface wettability hinges on micro-nano structuring and chemical alterations[47,48]. Designing precise microstructures enables regulation of superhydrophobic, superhydrophilic, or other specialized wetting characteristics of liquids. Moreover, wettability enhancement techniques are advancing towards crafting and refining multi-scale, multi-layer composite micro-textures and biomimetic functional surfaces[46,49-51].
Han et al.[52] combined specific biomimetic morphology and inherent properties of paraffin to prepare a moth-eye nanocolumn structure instead of a porous structure, coated with solid paraffin for waterproofing, and the surface has self-cleaning, anti-icing, anti-reflection and self-healing properties [Figure 2A]. The stability of superhydrophobic surface has always been one of the factors limiting its application. Dai et al.[53] prepared polydimethylsiloxane (PDMS) microcilia with magnetic field assistance, and then modified nano-sized particles with excellent hydrophobicity through the expansion process. The substrate has mechanical stability against ultrasonic treatment, sandpaper wear and high-speed water impact [Figure 2B]. Liu et al.[28] used two-photon polymerization-based 3D printing technology to prepare triple-entry structures that are super water-repellent to both water and organic solvents. On the basis of the prepared triple entrance structure, micro-open capillaries are constructed to realize liquid directional diffusion, which can be applied to microfluidic platforms and lab-on-a-chip [Figure 2C]. Shi et al.[54] propose a thermodynamically based model to predict controllable wetting regions, reveal that the gradual transition of the wetting state is the result of the accumulation of droplets at the nanoscale, and establish a link between the dynamics of the microscale solid-liquid interface and the condensation occurring in the nanostructure. With the deepening of research, Jiang et al.[55] achieved the manipulation of liquid immersion behavior at high-temperature surfaces and applied it to heat transfer. They constructed a multi-textured material with different thermal and geometric properties, conductive, protruding columns that act as thermal Bridges to facilitate heat transfer, embedded heat insulation films to absorb and evaporate liquids, and underground U-shaped channels to vent steam. The seamless integration of these heterogeneous elements greatly increases the Leidenfrost effect value without sacrificing high heat transfer capacity [Figure 2D]. Zhang et al.[56] proposed a top-constrained self-branching (TCSB) method for preparing biomimetic superhydrophobic four-branched microstructures, and modified the microstructures with hydrophilic microspheres to verify that hydrophilic spires play a key role in air layer recovery during extremely low underpressure recovery [Figure 2E]. Wilhelm et al.[57] propose an innovative fabrication method for a biomimetic superhydrophobic egg beater structure with controllable surface topography. It can precisely control the structure size, the number of beater arms, the structure distance, etc., and study its influence on hydrophobicity and water adhesion [Figure 2F]. Wang et al.[58] constructed different structures on the substrate surface in two-dimensional (2D) dimensions: a wear-resistant structure on the micron scale; The superhydrophobic structure is constructed on the nanoscale to design materials with both wear resistance and superhydrophobic properties, which solves the problem of superhydrophobic surface stability to a certain extent.
Figure 2. SEM photos of isotropic microstructure surface and contact angle photos of water droplets. (A) Biomimetic nanocolumn array prepared by template method. Copyright 2020, ACS[52]; (B) Microciliary array prepared by self-assembly method under magnetic field. Copyright 2020, Wiley[53]; (C) 3D printing technology based on two-photon polymerization to manufacture reentrant structures. Copyright 2018, Wiley[28]; (D) Multi-structure composite surface prepared by etching and electrospinning. Copyright 2020, Springer Nature[55]; (E) Top-bound Self-branched (TCSB) Bionic superhydrophobic four-branched microstructures. Copyright 2022, ACS[56]; (F) Superhydrophobic egg beater microstructure prepared by Immersed Surface Accumulation 3D printing process. Copyright 2010, Wiley[57]. 3D: three-dimensional.
Anisotropic microstructured surface
Some natural surfaces with special structures provide important prototypes for the study of directional liquid transport on 2D materials[59]. The directional infusion capacity of these 2D natural surfaces is closely related to their micro and nanosurface structures. Isotropic microstructures are often used to design and adjust the wetting and adhesion properties of liquids on solid surfaces. The controlled driving of liquids requires asymmetric forces, so the design of anisotropic microstructures becomes necessary[60-63].
Zhao et al.[64] developed a surface-reconfigurable superamphiphilic organic hydrogel for unidirectional liquid transport, inspired by the functional surfaces of pitcher plants and rice leaves. Due to the surface reconfiguration of heterogeneous networks, organic hydrogels can achieve a highly adaptive wetting transition between superhydrophilic and superlipophilic. Juan et al.[65] used a series of probe liquids, including non-volatile ionic liquids, to investigate the source of the microscopic liquid residues by studying the directional self-transport of droplets on an anisotropic completely dispersed surface consisting of radially aligned microstripes [Figure 3A]. Bai et al.[66] also prepared a radially structured surface of shell-like superhydrophobic origami (S-SLO) with multiple parallel and double asymmetric channels to improve fluid collection and enhance condensation through directional fluid manipulation and the collaboration of radiative cooling layers, resulting in a 56% improvement in directional drainage efficiency [Figure 3B]. Zhang et al.[67] combined shark skin surface and ciliary structure of water strider leg to prepare a superhydrophobic surface with anisotropic structure by phase transformation method, on which droplet can be lossless transported [Figure 3C]. Similarly, inspired by the shark skin surface microstructure, we use the template method to prepare a flexible surface with a V-shaped prism structure, and the direction of liquid transport on the surface is adjusted by changing the curvature of the film[68] [Figure 3D]. Liu et al.[69] fabricated a tilted sector array tube (TSAT) that exhibits excellent unidirectional liquid transport over a wide range of liquid surface tension and injection velocity. In addition, it enables anti-gravity climb, circuit isolation and chemical reaction control [Figure 3E]. Feng et al.[70] were inspired by the surface structure of the Araucaria leaf and prepared a surface with a 3D ratchet structure, on which liquids with different surface tensions can be transported rapidly and directionally [Figure 3F]. Si et al.[29] prepared an open micro and macro dual-scale array through advanced 3D printing technology, and realized one-way transport of liquid without external force or energy through a simple model. The internal Laplace pressure differential driving mechanism is explained by the basic formula. The findings suggest innovative microfluidic applications, such as liquid mode, unidirectional transport without external forces and antigravity, that will contribute to the development of smart laboratory chip devices, microfluidic integrated systems, and advanced biochemical microreactors.
Figure 3. Directional liquid transport on the surface of anisotropic microstructures. (A) Self-transport of oil droplets on a highly oil-phobic radial microtextured surface. Copyright 2016, AAAS[65]; (B) Directional collection of liquid on an asymmetric double-channel hydrophilic surface. Copyright 2023, Wiley[66]; (C) Lossless unidirectional transport of liquid on an ultra-stable superhydrophobic surface with a highly ordered scaly structure. Copyright 2022, ACS[67]; (D) Unidirectional transport of liquid on a V-shaped prism array. Copyright 2023, ACS[68]; (E) Unidirectional transport of liquid in a tilted fan-shaped array tube. Copyright 2016, Wiley[69]; (F) Mimics the micro-junction on the surface of a South American pine leaf Directional transport of liquids with different surface tension. Copyright 2021, AAAS[70].
Huang et al.[71] coated a liquid perfluoropolyether (PFPE) polymer brush on an anisotropic fully hydrophobic surface to achieve non-destructive, rapid directional self-transport of microscopic liquid residues. Since the surface with micropatterns enables lossless droplet self-transport, can drive droplet directional motion, and precisely locates it in the central region where analysis is required, it can serve as a very ideal intelligent platform for chemical and biological analysis without the loss of analyte quality. The lossless self-transport properties of micropatterned surfaces can greatly advance their application in various fields, for example, in biological and chemical analysis, digital microfluidics, etc. Li et al.[72] reported a flexible topological catheter in which liquid can be transported spontaneously, rapidly and in a directional manner. Unlike the capillary-induced liquid transport on the diode film, the liquid transport in the liquid diode is mainly regulated by the interaction of surface effects and volume effects. In addition, the durability and stability of the diodes in long-term bending and twisting operations were tested, a strategy that has broad applications in the transportation of a wide range of liquids, such as low surface tension liquids, medical solutions and lubricants.
Intelligent microstructured surface
Because of the unadjustable structure, the traditional microstructure surface cannot dynamically control the surface fluid behavior, so its practical application in many fields is limited. Therefore, the researchers add the responsiveness factor to the surface of the microstructure, and use the external field to accurately control the surface fluid, so that it has a broader prospect in practical application[73-75]. In contrast to traditional fluid manipulation methods, intelligent response surfaces utilize the material responsive characteristics to external stimuli to manipulate the fluid, without complex mechanical components and large amounts of energy input. Intelligent response surfaces can change their physical and chemical properties, such as surface wettability and roughness, in response to external stimuli (such as temperature, light, electric, or magnetic fields, etc.). In terms of fluid manipulation, this adjustability enables precise control of the transport direction, velocity, and shape[76-79].
Material composition, microstructure, and the type and intensity of external stimuli all affect surface properties. The type of intelligent response surface response to external stimuli is determined by its basic material. For instance, surfaces fabricated with thermally responsive polymers such as poly-N-isopropylacrylamide (PNIPAM) experience a phase transition upon temperature variation, thereby altering the surface wettability[80]. A composite surface containing magnetic nanoparticles (NPs) will respond to magnetic fields[81]. The surface microstructure (roughness, porosity, and texture direction) significantly influences its performance. A response surface with nanoscale roughness may augment the superhydrophobicity or superhydrophilicity of the surface, thus influencing the contact angle and fluid on surface flow behavior. Different external stimuli (such as temperature, light, electric field, and magnetic field) will initiate different response mechanisms of intelligent response surfaces. For example, temperature stimulation predominantly affects surface properties by modifying the material’s molecular conformation or inducing a phase transition, whereas light stimulation may rely on photochemical reactions or photothermal effects[82-84]. Additionally, the intensity of the external stimulus is crucial; insufficient intensity may not elicit a significant response, while excessive intensity may result in material damage or an uncontrollable response. According to this, the researchers designed different intelligent response surfaces to accurately control the surface fluid, so that it has a broader prospect in practical application.
External forces responsive microstructure surface
Mechanical bending, stretching and other deformation is a very simple operation for the solid microstructure surface, but the impact of this series of operations on the surface properties of the microstructure cannot be ignored. The deformation of the material will cause the change of the parameters between the surface microstructure and even the change of the surface chemical composition, resulting in the change of the surface wetting property, wave absorption property and electrical conductivity[85-87].
In 2011, Wu et al.[88] found that superhydrophobic surfaces with unidirectional curved microstructures could cause changes in contact Angle adhesion. With the increase of surface curvature, the contact angle of the droplet on the surface increases from 150° to 160°, and the adhesive force also increases gradually. Later, Ma et al.[89] studied droplet wettability on the surface of titanium tube with superhydrophobic TiO2 nanotube array coating, and found that the contact angle of droplet on convex surface was larger than that on flat surface, and that on concave surface was smaller than that on flat surface. On the basis of considering the droplet radius and droplet size, the relation between the intrinsic contact angle of the droplet and the apparent antenna is established. These findings provide a theoretical basis for determining the natural contact angle of opaque or transparent tubular substrates. Hu et al.[90] constructed a new structural fiber and realized ultra-fast spreading of liquid on the surface of the fiber. It is believed that the macroscopic conical structure determines the spreading direction of the liquid, and the concave surface and orientation of micro-ridges/valleys affect the capillary rise rate. By reducing the internal angle of the concave curve, the speed of liquid directional spreading can be further accelerated. The results of this study open up a new direction for the fabrication of microfluidic and liquid manipulated fiber systems.
Yang et al.[17] introduced a columnar array by utilizing the microstructured template of ethylene vinyl acetate, subsequently modifying it to achieve super hydrophobic properties [Figure 4A]. By stretching and relaxing the film, the adhesion of the liquid on the surface can be changed, and the droplet can be transferred at a fixed point. However, the surface needs to be superhydrophobic modified with fluoride to achieve this property. Lee et al.[91] treated polyolefin surfaces with plasma and formed nanoscale ridges during strain release of the substrate [Figure 4B]. By stretching and reshrinking polymer NPs, surface structural characteristics can be controlled without cracking or delamination of the substrate, and transitions to different wetting states can be achieved programmatically, starting from a single surface. This parallel, photolithographic technology enables precise control of the wetting state and is used in a variety of areas such as advanced water collection, self-cleaning systems and directional water delivery.
Figure 4. Tensile response of the microstructure surface. (A) A stretchable fluorine-free superhydrophobic surface for droplet transfer. Copyright 2019, Springer[17]; (B) Surfaces with nanoscale ridges can be stretched and released to control the wetting state of droplets on the surface. Copyright 2018, Wiley[91].
Photo-responsive microstructure surface
In recent years, the strategy of manipulating droplets using photothermal effect has been developed, and has been widely used because of the advantages of high spatiotemporal resolution, flexible control and fast response of optical response. Light can be easily focused into a tiny beam and used as a local heating source, allowing flexible control of the droplet, which is conducive to controlling its directional movement. In addition, due to its high reconfigurability, the modulator can dynamically adjust the light beam to form an optical array and realize the parallel operation of multiple droplets, ensuring the high throughput of real-time online analysis and biochemical analysis. Therefore, optical strategies based on photothermal effects are expected to be widely used in controlling droplet behavior[92-95].
A light-responsive slippery lubricant-infused porous surface (SLIPS), composed of selective lubricants and a super-hydrophobic Fe3O4/PDMS micropillar-arrayed film by Chen et al.[96], allows remote actuation of underwater gas bubble in arbitrary horizontal directions via unilateral near infrared (NIR) stimuli loading/discharge [Figure 5A]. Li et al.[97] studied the droplet evaporation crystallization process caused by the photothermal effect of an infrared laser with a focusing wavelength of 1550 nm. It is found that when the focused light is turned on, the interface temperature of the droplet rises rapidly, and violent evaporation occurs, increasing the concentration of substances in the droplet, and eventually crystallization. Compared with natural evaporation and flat plate uniform heating, the photothermal effect of focused laser beam can promote droplet evaporation and crystallization. At 100 mW of laser power, the time for the droplet to complete evaporative crystallization is seven times shorter than the time for natural evaporation. Hwang et al.[98] proposed to control droplet motion by controlling Marangoni flow [Figure 5B]. A temperature gradient is used on the droplet surface to generate a surface tension gradient that drives the droplet. The irradiation position can be precisely controlled by NIR laser to realize the local heating of the droplet and the change of the direction of thermal capillary convection, and the droplet always moves from the heated side to the non-heated side. In addition, because the droplets are directly heated by the polypyrrole (PPy)/NPs inside, even in spherical droplets with small contact areas, there is a strong thermal capillary propulsion, resulting in directional motion. Gao et al.[92] proposed a photoresponsive organic gel surface (POS) obtained by embedding Fe3O4 NPs in PDMS and injecting lubricating oil [Figure 5C]. Under the irradiation of NIR (wavelength 808 nm), the irradiated part of POS can quickly generate a local dynamic temperature gradient, and the droplet directional transport can be carried out by tilting plane, mixed droplet and curved path.
Figure 5. Photoresponse to directional liquid transport on the surface of the microstructure. (A) Remote photothermal drives underwater bubbles in any direction. Copyright 2019, Wiley[96]; (B) The droplet motion is driven by light-driven Marangoni flow propulsion. Copyright 2019, Wiley[98]; (C) Light-induced droplet movement on POS surface. Copyright 2018, Wiley[92].
Electrically responsive microstructure surface
Controlling the directional movement of droplets on solid surfaces by introducing surface wettability gradients or external stimuli has attracted considerable attention. However, due to the slow speed of continuous movement and response of the droplet on the surface of the structure, its directional fast transport still has some challenges. As a non-destructive, fast, simple and reversible external stimulation induction method, electric field has shown unique advantages in the regulation of material surface wetting properties[99-101].
Our group developed a porous polystyrene (PS) film with gradient structure prepared by electric field and breathing pattern method under the humidity field gradient, and realized the titrating movement of underwater oil[22]. When the electric field is applied, the contact area between the droplet and the surface of the gradient structure is reduced, resulting in a decrease in the corresponding viscous resistance between the droplet and the surface of the gradient structure, thus driving the underwater oil droplet to move in a directional and continuous manner. This work provides a new method for controlling and realizing unidirectional movement of underwater oil droplets, and has a broad application prospect in the design of new intelligent interface materials. In addition to realizing an electric field driving oil droplets on a 2D surface, we also propose a new strategy for efficient collection of oil droplets on an anisotropic porous cone surface using an electric field[23]. Under the combined action of Laplace pressure, buoyancy force and electric field, the directional movement of oil droplets along the surface of a cone with a PS-coated gradient hole is realized. With the help of buoyancy, the downward direction of the cone tip is more conducive to the directional movement of the underwater oil droplets. In addition, we combined the superhydrophobic NPs with the boundary electro-elastomer, stretched the dielectric elastomer film by electric field, changed the distance between the surface superhydrophobic NPs, and regulated the dynamic wetting and adhesion of droplets on the surface[102] [Figure 6A].
Figure 6. Directional transport of liquid on the surface of microstructure in response to electric field. (A) Droplet adhesion and movement control on the surface of micro-nano multistage structures in response to an electric field. Copyright 2020, Wiley[102]; (B) Out-of-plane electrostatic charging control. Copyright 2019, Wiley[104]; (C) A high-speed “one-piece” lossless droplet operation via triboelectrophoresis on a microstructured surface with a superhydrophobic coating. Copyright 2023, Wiley[106]; (D) In situ-controlled wetting and movement of droplets injected with Joule thermal response paraffin with a sandwich structure. Copyright 2021, Wiley[107].
Chen et al.[103] also combined the electric field with the composite surface immersed in liquid, applied and removed the electric field to control the state between the lubricant and the microstructure of the composite surface, and controlled the pinning and sliding of droplets on the surface. If the voltage is applied directly to the substrate, the substrate will be broken down, become charged and experience biological contamination as the voltage increases. Dai et al.[104] proposed an integrated method for manipulating the motion of water droplets on a superhydrophobic surface using an electrostatic field [Figure 6B]. The lossless droplet manipulation with high-speed movement and switchable pinning is realized by inducing electrostatic repulsion and gravity. Li et al.[105] demonstrated the use of electronic signals to induce the dewetting behavior of a liquid on a conductive substrate without the need for additional conductive layers. In this electrostatic mechanism of action, contrary to the electrowetting phenomenon, the interaction of the liquid substrate is not directly controlled by the electric field, but by the attachment and stripping of the field-induced ionic surfactant on the substrate; the driving voltage is only 2.5 V, the current is only a few microamps, and the critical micelle concentration of the ionic surfactant is about 0.015 times. The system can also handle common buffers and organic solvents, providing a simple and reliable microfluidic platform. Sun et al.[106] introduced a tribo-electrophoresis (TEP)-based method employing a triboelectric nanogenerator (TENG) electrostatic tweezer to efficiently enable human-droplet interactions by charging and enhancing droplet maneuverability, including pipetting alignment and stable transport, controlled solely by hand movement [Figure 6C]. Chen et al.[107] developed a Joule-heat-responsive paraffin-impregnated slippery surface (JR-PISS), featuring a superhydrophobic micropillar-arrayed elastomeric membrane and integrated transparent silver nanowire heater, enabling controllable liquid locomotion on both planar and curved surfaces through alternate 6 V electric-trigger application/discharging, due to its flexible design [Figure 6D].
Magnetism-responsive microstructure surface
Droplet control has been widely used in various fields of production and life. Major breakthroughs have been made in droplet manipulation, and different droplet transport strategies have been developed based on various external stimuli. Magnetically responsive surfaces are widely used in droplet control platforms because of their fast response speed and contactless operation[83,108,109].
Our group prepared a magnetically responsive intelligent composite surface by combining the magnetic fluid with the surface of the nano-ZnO array [Figure 7A]. The roughness of the intelligent composite surface can be changed by magnetic field, and the contact angle of the droplet on the surface can be adjusted by magnetic field. In addition, when an asymmetric magnetic field is applied below the intelligent composite surface, the droplet will have a directional motion due to the unbalanced force on both sides, and the response speed of the intelligent composite surface is less than 1 ms[110]. Wen et al.[76] used a simple, reagent-free method to fabricate a magnetically asymmetrically deformed tube microactuator that generates an asymmetric capillary force to drive a liquid through a magnetic field-induced tube deformation. These magnetic tube microactuators can drive a variety of droplets at a controlled speed and direction, up to 10 cm/s. In addition to controlling surface deformation, magnetic fields can also control the deformation of surface microstructure. Wong et al.[77], inspired by lotus leaves and pitcher plants, designed a magnetically responsive surface that can switch between superhydrophobic and slippery states. The surface consists of a series of magnetically responsive layered microcolumns made of soft polymeric material and infused with a liquid lubricant. The microcolumn can be controlled by magnetic field. When the microcolumn is perpendicular to the base, the droplet is in Cassie state and the surface is in super hydrophobic mode, similar to the lotus leaf. When the microcolumn lies flat on the substrate under the action of an external magnetic field, the droplets interact with the surface of the lubricating oil, which mimics the wet surface on the edge of the pitcher plant, on which the droplets can slide. In addition to manipulating the behavior of the droplets horizontally, the magnetic field can also control the permeability behavior of the liquid horizontally. Yun et al.[111] introduces a magnetocontrollable lubricant-infused surface (MCLIS) for liquid-solid (LS) triboelectrification switching, demonstrating sustained power generation under high humidity by toggling wetting states, unlike typical LS-TENGs which suffer from performance degradation [Figure 7B]. This innovation offers a magnetoresponsive triboelectric switching concept, expanding the applicability of TENGs in low-power domains such as wireless switches and self-powered sensors. Zhang et al.[112] showcased an active strategy on removal modes-based magnetic-responsive polydimethylsiloxane superhydrophobic microplates (RM-MPSM), enabling varied droplet removal modes (top jumping, side departure) by adjusting microplate parameters and droplet volume, facilitating droplet removal. These efficient removal modes have broad implications for applications in droplet collection, heat transfer, and anti-icing [Figure 7C]. In addition to controlling the horizontal movement of the fluid on the surface of the microstructure, the magnetic field can also control the longitudinal transmission of the fluid.
Figure 7. Directional liquid transport on the surface of the magnetic response microstructure. (A) The directional movement of droplets on the surface of the magnetic liquid impregnated nano ZnO array. Copyright 2016, ACS[110]; (B) The solid-liquid triboelectrically controlled magnetic switch to control the movement of droplets is realized by using the magnetron lubricant injected into the surface as the triboelectric layer. Copyright 2022, Elsevier[111]; (C) the effective removal of droplets on the surface of the magnetically responsive polydimethylsiloxane superhydrophobic microplate. Copyright 2024, Wiley[112].
Multiple fields respond collaboratively to the microstructure surface
Compared with the influence of a single factor on droplet control, the synergistic effect between multiple factors can show greater advantages on droplet motion control. Jun et al.[113] reported a method for controlling anisotropic wetting using a pleated dielectric elastomer actuator. The actuator is made of a carbon black electrode with mechanical buckling on the surface of the elastomer by bidirectional prestretching and relaxation process. The dielectric elastomer actuator is driven by directional anisotropy, and the hydrophobic surface of the carbon electrode is controlled by the electric field, which can realize the anisotropic wetting control. Padinjareveetil et al.[78] prepared hydrophobic microcolumn array zinc oxide films using femtosecond laser vertical cross-scanning technology. Paraffin wax was successfully injected into zinc oxide thin films by means of spin coating, thermal evaporation and condensation. An intelligent droplet motion control actuator was fabricated by integrating the composite film with a silver nanowire heater. By loading an ultra-low voltage of 12 V, the wettability of various droplets with different surface tension can be controlled in situ. This study provides a new research idea for the design of in situ droplet motion control and anti-fog and anti-ice intelligent devices for 2D/3D surfaces.
Furthermore, the fabrication of robust and durable microstructured surfaces is not only a critical requirement for withstanding extreme environments and enhancing material performance but also a key factor in extending service life, reducing maintenance costs, and driving the development of new technologies. Therefore, effectively improving the strength of microstructured surfaces has become a pressing issue that demands immediate attention.
Lu et al.[114] develop a dual-sized titanium dioxide NP suspension coated with perfluorosilane. This material maintained stable superhydrophobic properties even after being subjected to finger friction, wiping, knife scratching, and 40 cycles of sandpaper abrasion. Furthermore, Su et al.[115] successfully fabricate a superhydrophobic composite microstructured surface, which exhibits excellent hydrophobicity after undergoing various extreme environmental tests, including cyclic mechanical abrasion, ultraviolet (UV) radiation, acid-base treatment, NaCl solution immersion, temperature variations, and knife scratching. Li et al.[116] successfully fabricate a highly durable superhydrophobic coating by spraying a fluorine-free suspension composed of epoxy resin (EP), PDMS, and modified silica. The coating maintained stable superhydrophobic properties under extreme conditions, including immersion in boiling water for two hours, immersion in liquid nitrogen for one hour, exposure to intense UV radiation for 48 hours, and strong chemical corrosion. Furthermore, the coating demonstrates exceptional mechanical durability, withstanding extreme tests such as tape peeling, knife scratching, hand grinding, and 100 cycles of sandpaper abrasion, while also exhibiting self-healing capabilities against O2 plasma etching.
These researches provide new insights and methods for developing robust and durable microstructured surfaces for extreme environments, offering significant theoretical and practical implications for advancing related technological fields.
APPLICATION OF FLUID MANIPULATION ON MICROSTRUCTURED SURFACE
In recent years, the research of micro-structure surface fluid manipulation involves the intersection of chemistry, materials science, fluid mechanics, biology and other disciplines, serving the important fields of energy, information, medicine, and so on[117-120].
Anti-fog and anti-ice
The superhydrophobic surface has a special micro and nanostructure and low surface energy, which can make the water droplets form a high contact angle and a low rolling angle on the surface, so that the water droplets are easy to roll off and not easy to stay on the surface and freeze. Zhou et al.[121] pre-coated a template surface with a nanostructure with PDMS. By introducing a “reservoir” of free lubricant at the bottom, which acts as a self-replenishing oil source for the upper layer, the superhydrophobic surface becomes more stable and can heal itself under alkali erosion and O2 plasma exposure, with a higher icing delay time and faster ability to remove condensation droplets in low-temperature environments. Zhang et al.[122] prepared a photothermal synergistic three-scale solar thermal superhydrophobic surface with excellent anti-icing and de-icing properties, so that ice with a thickness of 4 mm can melt and be removed from the surface in 241 s. Zhang et al.[123] made the droplet automatically “eject” from the surface when it froze by using the high pressure generated by its own volume expansion of about 9%, by adjusting the matching of the flow field and the force gradient field. The spring-like column could store the work done by the volume expansion of the frozen droplet for several seconds as elastic energy, and then quickly release it as kinetic energy within a few milliseconds. This generates enough kinetic energy to drive the ejection of the frozen droplets.
Fog harvest
Fog harvesting, a technique that captures water vapor or fog from the air to obtain fresh water, is being applied as a sustainable and low-cost method of drinking water acquisition in foggy areas. Ang et al.[124] propose a cascade effect that induces water collection from the active water harvesting region (AWHR) and passive water harvesting region (PWHR) through a microstructural design that results in about a threefold increase in water harvest compared to unmodified water collectors, highlighting the need to consider PWHR in future collector designs to achieve efficient water collection. The purified terephthalic acid (pTA)/silica nanofibers (SNFs)/1H,1H,2H,2H-perfluorodecanethiol (PFDT) coating prepared by Zhang et al. has excellent superhydrophobicity[125]. The coating has autogenetic hydrophilic Wenzel site during fog collection, and achieves a stable high fog collection rate of 2.13 g cm-2 h-1 during 192 h of continuous fog collection. Inspired by the behavior of the Namib Desert web-dactylated tiger to avoid thermal radiation and capture water, Zhang et al.[126] prepared a biomimetic passive water collection material [power-free cooling moisture harvester (PFCMH)] with integrated radiative cooling and heterogeneous wetting functions. In the one-month outdoor water collection experiment, the water collection system built based on PFCMH can produce about 620.4-1244.4 g m-2 fresh water every night, and about 52.2-102.5 g m-2 fresh water during the day, and the captured fresh water meets the WHO drinking water standards, and the laying of 2 m2 can meet the daily drinking water demand of an adult.
Biomedicine
Inspired by the self-driven diffusion of liquid membranes on the surface of Nepenthes, Li et al.[127] successfully prepared biomimetic microstructures on high-frequency surgical electrodes using laser etching technology, and introduced conductive oil films into the microstructures, which can promote the occurrence of spark effects, thereby preventing short circuits in the tissues of the electrodes. Additionally, suppressing heat transfer during cutting can prevent thermal damage and significantly reduce adhesion problems. Xiao et al.[128] developed a self-pumped organic hydrogel dressing with aligned hydrating gel channels for enhanced viscous fluid drainage and accelerated diabetic wound healing. In diabetic rats, compared to commercial dressings, the self-pumping organohydrogel dressing (SPD) reduced inflammation by 70.8%, improved dermal remodeling by 14.3%, and hastened healing by about 1/3 [Figure 8A]. Liang et al.[129] have proposed an innovative bionic skin sweat sensor with an advanced sensor system that can monitor a variety of biomarkers in sweat, including glucose, lactic acid, uric acid, pH, temperature and skin impedance. With the newly developed Continuous Analyte Monitoring with Real-time Engagement (CARE) system, real-time data transmission and processing are realized. Zhang et al.[130] devised a health-monitoring electrode patch featuring perspiration permeability and multi-mechanism adhesion [Figure 8B]. Its ventilation and sweat management are achieved via a conical through-hole and honeycomb micro-groove integrated design. A Laplacian liquid pressure and microgroove capillary forces drive sweat conductivity autonomously. Adhesion is ensured by an Ag/Ni microneedle array and PDMS-t adhesive, stabilizing the patch-skin contact. High-controlled microneedle-skin contact guarantees safe, reliable bioelectrical signal acquisition.
Other application
In addition, microstructure surfaces also have important applications in energy, self-cleaning, catalysis, and so on. Chen et al.[131] pioneered a hierarchical micronanostructure with high transparency, full stretchability, and superhydrophobicity for advanced bimodal TENGs, capable of harvesting mechanical and water energy [Figure 8C]. With superhydrophobic self-cleaning properties, the TENG gains additional water energy harvesting capacity, achieving 36 V and 10 μA output at 11 mL/s water flow. This bifunctional energy harvesting, alongside transparency, stretchability, and robust superhydrophobicity, positions the TENG as a promising energy source for future electronics. Inspired by the layered structure of lotus leaves, Liu et al.[132] obtained a coating that integrates surface wettability, optical structure, and temperature adaptation through a simple one-step phase separation process. The coating not only has a self-cleaning function, high infrared emission and heat-exchangeable solar reflectivity, but it can also switch between radiative cooling and solar heating. It opens up new prospects for the large-scale manufacturing of intelligent thermal regulation coatings. Li et al.[133] proposed an efficient water decomposition strategy using a bubble-guided electrode [groove-micro/nanostructured porous electrode (GMPE)] with gradient groove micro/nanostructures, inspired by nature’s directional fluid transport in pitcher plants and butterfly wings [Figure 8D]. This facilitates rapid bubble transport and detachment, achieving efficient water splitting and offering insights for gas-involved photochemical electrode design.
CONCLUSIONS
To date, the on-demand manipulation of surface fluids has made impressive strides, from material preparation methods to intelligent microfluidic devices, which has considerable significance in the realms of science and engineering and attracted extensive attention in recent years. In this review, the latest progress of fluid manipulation on the surface of microstructure is reviewed. First, the basic theory of fluid wetting state transition and directional driving on the surface of microstructure are introduced. Then, the research and application of preparation, characterization and fluid wetting of various microstructure surfaces under the guidance of the above basic theories are described. The research of fluid control on the surface of microstructures can promote the development of microfluidic technology. By precisely controlling the fluid behavior on the micro and nanoscale, miniaturized, integrated and highly sensitive fluid control can be achieved, which has a profound impact on the research and application in biomedicine, energy, materials and other fields. Fluidic manipulation of microstructure surfaces can also be used to design new types of sensors and actuators that are capable of operating under extreme conditions, such as in optical device design in space, where fluidic manipulation of microstructure surfaces can be used to manufacture optical devices and so on.
Despite significant progress in microstructured surface fluid manipulation research, challenges persist, particularly in practical problem-solving and industrial application. First, large area preparation is one of the difficulties. With the increase of the preparation area, the homogeneity and reproducibility of the structure will become worse, which will greatly affect the wetting characteristics of the surface and limit its application in industrial production. Secondly, in practical applications, high temperature and pressure, low temperature, strong corrosive solution, external impact and other factors will damage the surface of the microstructure, so that it is damaged and lose its excellent function. Consequently, the stability of microstructured surfaces has emerged as a critical issue that necessitates immediate resolution. Future research in microstructured surface fluid manipulation will prioritize innovative design, industrial scaling, and advanced fabrication techniques for a simple, stable, and high-performing process. Specifically, focus on the following three aspects:
(1) New materials and structures: Through the discovery and synthesis of new materials with excellent properties (such as superhydrophobic materials, superhydrophilic materials, and intelligent response materials, etc.), combined with innovative structural design (such as gradient structure, multistage structure, and bionic structure, etc.), the stability, durability and functionality of the microstructure surface can be significantly enhanced. For example, bionics inspired micronanostructural designs (such as the micromastoid structure on the surface of lotus leaves or the gradient hydrophobic structure of desert beetles) can effectively improve surface resistance to pollution, self-cleaning, and liquid directional transport. In addition, the introduction of smart responsive materials allows the surface of the microstructure to dynamically adapt to complex environmental changes, thus maintaining excellent performance. The development of these new materials and structures can not only solve the stability problems faced by existing microstructure surfaces in industrial applications, but also expand their application potential in microfluidic chips, biosensors and efficient water harvesting, providing important support for future multifunctional integration and intelligent fluid manipulation.
(2) Process improvement: Currently, the fabrication of microstructured surfaces primarily relies on technologies such as laser etching, chemical etching, 3D printing, and so on. While these methods offer high flexibility and precision, they still face challenges in industrial applications, including low efficiency, high costs, and process complexity. Therefore, it is necessary to optimize and improve existing processes to enhance processing efficiency, reduce production costs, and maximize economic benefits. Specific improvement measures include the following aspects: 1)Process parameter optimization. Through experimental design and data analysis, optimize key parameters such as laser power, scanning speed for laser etching, and solution concentration and reaction time for chemical etching to improve processing accuracy and efficiency; 2) Real-time Monitoring and feedback optimization. Introduce online monitoring systems (e.g., high-speed cameras or optical sensors) to provide real-time supervision of the processing. Combined with feedback control algorithms, dynamically adjust laser parameters to ensure processing precision; 3) Process integration and innovation. Integrate multiple processing technologies (e.g., laser etching and 3D printing) to develop hybrid processes that overcome the limitations of single technologies, enabling more efficient fabrication of microstructured surfaces; 4) Standardization and scalable production. Establish unified process standards and quality control systems to promote the scalable production of microstructured surfaces, further reducing costs.
(3) Integration and application of smart materials: Introducing smart materials to actively adjust the morphology, distribution, and the release and transfer of substances of the surface microstructures, thereby enhancing the controllability and dynamic tunability of fluids on these surfaces and promoting their further development in practical applications.
DECLARATIONS
Authors’ contributions
Conceptualization: Li, Y.; Zhang, Q.
Investigation: Li, Y.; Zhang Q.
Writing-original draft: Li, Y.; Zhang, Q
Writing-review & editing: Li, Y.; Zhang, C.; Li, Y.; Zhang, Q.; Li, L.; Song, F.; Tian, D.
Supervision: Li, Y.; Zhang, Q.; Li, L.; Song, F.; Tian, D.
Funding acquisition: Li, Y.; Zhang, Q.; Li, L.; Song, F.; Tian, D.
Availability of data and materials
Not applicable.
Financial support and sponsorship
This work was supported by the National Natural Science Foundation of China (22402011, 22272005, 12232019, 12272388), the Strategic Priority Research Program of Chinese Academy of Sciences (XDB0620101), the Postdoctoral Fellowship Program of CPSF (GZC20241783), the Opening fund of State Key Laboratory of Nonlinear Mechanics, and the NHC Key Laboratory of Food Safety Risk Assessment (China National Center for Food Safety Risk Assessment, 202408). The authors also thank the Youth Innovation Promotion Association, CAS.
Conflicts of interest
All authors declared that there are no conflicts of interest.
Ethical approval and consent to participate
Not applicable.
Consent for publication
Not applicable.
Copyright
© The Author(s) 2025.
REFERENCES
1. Bába, P.; Tóth, Á.; Horváth, D. Surface-tension-driven dynamic contact line in microgravity. Langmuir 2019, 35, 406-12.
2. Nagura, R.; Watanabe, Y.; Sato, N.; et al. Water movement on the convex surfaces of porous media under microgravity. Advances. in. Space. Research. 2019, 63, 589-97.
3. Kwon, S. R.; Baek, S.; Fu, K.; Bohn, P. W. Electrowetting-mediated transport to produce electrochemical transistor action in nanopore electrode arrays. Small 2020, 16, e1907249.
4. Kim, G.; Kim, W.; Chun, H. Droplet energy harvesting is reverse phenomenon of electrowetting on dielectric. Adv. Funct. Mater. 2021, 31, 2105233.
5. Zhang, X.; Jiang, X.; Du, G.; et al. Hong J.Elastic properties and Ion-mediated domain switching of self-assembled heterostructures CuInP2S6-In4/3P2S6. Microstructures 2023, 3, 2023010.
6. Deng, S.; Wang, H.; He, L.; Wang, C. Magnetic structures and correlated physical properties in antiperovskites. Microstructures 2023, 3, 2023044.
7. Wei, X.; Wang, Y.; Liu, Y.; et al. Biomimetic design strategies for biomedical applications. Matter 2024, 7, 826-54.
8. Xu, B.; Chen, X.; Shi, Z.; et al. Electrochemical on-site switching of the directional liquid transport on a conical fiber. Adv. Mater. 2022, 34, e2200759.
9. Zhang, C.; Xiao, X.; Zhang, Y.; et al. Bioinspired anisotropic slippery cilia for stiffness-controllable bubble transport. ACS. Nano. 2022, 16(6), 9348-58.
10. Yang, X.; Qi, B.; Lu, Y.; Zhang, W.; Wang, X. Bionic surface diode for droplet steering. Droplet 2023, 2, e46.
11. Yue, C.; Dai, Q.; Yang, X.; Gachot, C.; Huang, W.; Wang, X. Controllable self-transport of bouncing droplets on ultraslippery surfaces with wedge-shaped grooves. Droplet 2024, 3, e118.
12. Li, C.; Yu, C.; Zhou, S.; Dong, Z.; Jiang, L. Liquid harvesting and transport on multiscaled curvatures. Proc. Natl. Acad. Sci. U. S. A. 2020, 117, 23436-42.
13. Dong, L. Z.; Ren, M.; Wang, Y. L.; et al. Artificial neuromuscular fibers by multilayered coaxial integration with dynamic adaption. Sci. Adv. 2022, 8, eabq7703.
14. Yang, L.; Li, W.; Lian, J.; et al. Selective directional liquid transport on shoot surfaces of Crassula muscosa. Science 2024, 384, 1344-9.
15. Feng, L.; Li, S.; Li, Y.; et al. Super-hydrophobic surfaces: from natural to artificial. Adv. Mater. 2002, 14, 1857-60.
16. Zhang, P.; Zhang, L.; Chen, H.; Dong, Z.; Zhang, D. Surfaces inspired by the nepenthes peristome for unidirectional liquid transport. Adv. Mater. 2017, 29.
17. Yang, H.; Xu, K.; Xu, C.; et al. Femtosecond laser fabricated elastomeric superhydrophobic surface with stretching-enhanced water repellency. Nanoscale. Res. Lett. 2019, 14, 333.
18. Zhang, Y.; Jiao, Y.; Chen, C.; et al. Reversible tuning between isotropic and anisotropic sliding by one-direction mechanical stretching on microgrooved slippery surfaces. Langmuir 2019, 35, 10625-30.
19. Lee, M.; Oh, J.; Lim, H.; Lee, J. Enhanced liquid transport on a highly scalable, cost-effective, and flexible 3d topological liquid capillary diode. Adv. Funct. Mater. 2021, 31, 2011288.
20. Li, J.; Zhou, X.; Tao, R.; Zheng, H.; Wang, Z. Directional liquid transport from the cold region to the hot region on a topological surface. Langmuir 2021, 37, 5059-65.
21. Sun, J.; Zhu, P.; Yan, X.; et al. Robust liquid repellency by stepwise wetting resistance. Appl. Phys. Rev. 2021, 8, 031403.
22. Tian, D.; He, L.; Zhang, N.; et al. Electric field and gradient microstructure for cooperative driving of directional motion of underwater oil droplets. Adv. Funct. Mater. 2016, 26, 7986-92.
23. Yan, Y.; Zhang, Q.; Li, Y.; et al. The highly efficient collection of underwater oil droplets on an anisotropic porous cone surface via an electric field. J. Mater. Chem. A. 2020, 8, 8605-11.
24. Sheng, Z.; Wang, H.; Tang, Y.; et al. Liquid gating elastomeric porous system with dynamically controllable gas/liquid transport. Sci. Adv. 2018, 4, eaao6724.
25. Ben, S.; Tai, J.; Ma, H.; et al. Cilia-inspired flexible arrays for intelligent transport of viscoelastic microspheres. Adv. Funct. Mater. 2018, 28, 1706666.
26. Li, Q.; Li, L.; Shi, K.; et al. Reversible Structure engineering of bioinspired anisotropic surface for droplet recognition and transportation. Adv. Sci. (Weinh). 2020, 7, 2001650.
27. Li, C.; Yu, C.; Hao, D.; Wu, L.; Dong, Z.; Jiang, L. Smart liquid transport on dual biomimetic surface via temperature fluctuation control. Adv. Funct. Mater. 2018, 28, 1707490.
28. Liu, X.; Gu, H.; Wang, M.; et al. 3D printing of bioinspired liquid superrepellent structures. Adv. Mater. 2018, 30, e1800103.
29. Si, Y.; Wang, T.; Li, C.; et al. Liquids unidirectional transport on dual-scale arrays. ACS. Nano. 2018, 12, 9214-22.
30. Zhou, S.; Yu, C.; Li, C.; Jiang, L.; Dong, Z. Droplets crawling on peristome-mimetic surfaces. Adv. Funct. Materials. 2020, 30, 1908066.
31. Dong, Z.; Vuckovac, M.; Cui, W.; Zhou, Q.; Ras, R. H. A.; Levkin, P. A. 3D printing of superhydrophobic objects with bulk nanostructure. Adv. Mater. 2021, 33, e2106068.
33. Ward, C. A.; Wu, J. Effect of contact line curvature on solid-fluid surface tensions without line tension. Phys. Rev. Lett. 2008, 100, 256103.
34. Ning, Y.; Zhang, D.; Ben, S.; et al. An innovative design by single-layer superaerophobic mesh: continuous underwater bubble antibuoyancy collection and transportation. Adv. Funct. Materials. 2020, 30, 1907027.
35. Liu, M.; Wang, S.; Jiang, L. Nature-inspired superwettability systems. Nat. Rev. Mater. 2017, 2, BFnatrevmats201736.
36. Liu, X.; Zhou, J.; Xue, Z.; et al. Clam’s shell inspired high-energy inorganic coatings with underwater low adhesive superoleophobicity. Adv. Mater. 2012, 24, 3401-5.
37. Wenzel, R. N. Resistance of solid surfaces to wetting by water. Ind. Eng. Chem. 1936, 28, 988-94.
38. Orr, F. M.; Scriven, L. E.; Rivas, A. P. Pendular rings between solids: meniscus properties and capillary force. J. Fluid. Mech. 1975, 67, 723-42.
39. Byun, D.; Hong, J.; Saputra; et al. Wetting characteristics of insect wing surfaces. J. Bionic. Eng. 2009, 6, 63-70.
40. Tian, D.; Chen, Q.; Nie, F. Q.; Xu, J.; Song, Y.; Jiang, L. Patterned wettability transition by photoelectric cooperative and anisotropic wetting for liquid reprography. Adv. Mater. 2009, 21(37), 3744-49.
44. Ju, J.; Xiao, K.; Yao, X.; Bai, H.; Jiang, L. Bioinspired conical copper wire with gradient wettability for continuous and efficient fog collection. Adv. Mater. 2013, 25, 5937.
45. Lehnert, M. S.; Monaenkova, D.; Andrukh, T.; Beard, C. E.; Adler, P. H.; Kornev, K. G. Hydrophobic-hydrophilic dichotomy of the butterfly proboscis. J. R. Soc. Interface. 2013, 10, 20130336.
46. Wang, F.; Wu, Y.; Nestler, B. Wetting effect on patterned substrates. Adv. Mater. 2023, 35, e2210745.
47. Soltani, M.; Golovin, K. Lossless, Passive Transportation of low surface tension liquids induced by patterned omniphobic liquidlike polymer brushes. Adv. Funct. Mater. 2022, 32, 2107465.
48. Feng, R.; Song, F.; Xu, C.; Wang, X.; Wang, Y. A quadruple-biomimetic surface for spontaneous and efficient fog harvesting. Chem. Eng. J. 2021, 422, 130119.
49. Xie, X.; Chen, X.; Levkin, P. A.; Feng, W. A reactive superhydrophobic platform for living photolithography. Adv. Mater. 2022, 34, e2203619.
50. Zhao, Z.; Ning, Y.; Ben, S.; et al. Liquid-assisted single-layer janus membrane for efficient unidirectional liquid penetration. Adv. Sci. (Weinh). 2022, 9, e2103765.
51. Zhou, X.; Liu, J.; Liu, W.; Steffen, W.; Butt, H. J. Fabrication of stretchable superamphiphobic surfaces with deformation-induced rearrangeable structures. Adv. Mater. 2022, 34, e2107901.
52. Han, G.; Nguyen, T. B.; Park, S.; Jung, Y.; Lee, J.; Lim, H. Moth-eye mimicking solid slippery glass surface with icephobicity, transparency, and self-Healing. ACS. Nano. 2020, 14, 10198-209.
53. Dai, Z.; Chen, G.; Ding, S.; et al. Facile formation of hierarchical textures for flexible, translucent, and durable superhydrophobic film. Adv. Funct. Mater. 2021, 31, 2008574.
54. Shi, S.; Lv, C.; Zheng, Q. Temperature-regulated adhesion of impacting drops on nano/microtextured monostable superrepellent surfaces. Soft. Matter. 2020, 16, 5388-97.
55. Jiang, M.; Wang, Y.; Liu, F.; et al. Inhibiting the Leidenfrost effect above 1,000 °C for sustained thermal cooling. Nature 2022, 601, 568-72.
56. Zhang, Y.; Hu, Y.; Xu, B.; et al. Robust underwater air layer retention and restoration on salvinia-inspired self-grown heterogeneous architectures. ACS. Nano. 2022, 16, 2730-40.
57. Barthlott, W.; Schimmel, T.; Wiersch, S.; et al. The salvinia paradox: superhydrophobic surfaces with hydrophilic pins for air retention under water. Adv. Mater. 2010, 22, 2325-8.
58. Wang, D.; Sun, Q.; Hokkanen, M. J.; et al. Design of robust superhydrophobic surfaces. Nature 2020, 582, 55-9.
59. Dai, H.; Dong, Z.; Jiang, L. Directional liquid dynamics of interfaces with superwettability. Sci. Adv. 2020, 6, e37.
60. Dai, X.; Sun, N.; Nielsen, S. O.; et al. Hydrophilic directional slippery rough surfaces for water harvesting. Sci. Adv. 2018, 4, eaaq0919.
61. Li, C.; Li, N.; Zhang, X.; Dong, Z.; Chen, H.; Jiang, L. Uni-directional transportation on peristome-mimetic surfaces for completely wetting liquids. Angew. Chem. Int. Ed. Engl. 2016, 55, 14988-92.
62. Zheng, Y.; Bai, H.; Huang, Z.; et al. Directional water collection on wetted spider silk. Nature 2010, 463, 640-3.
63. Stamatopoulos, C.; Milionis, A.; Ackerl, N.; et al. Droplet self-propulsion on superhydrophobic microtracks. ACS. Nano. 2020, 14, 12895-904.
64. Zhao, Z.; Li, C.; Dong, Z.; et al. Adaptive Superamphiphilic organohydrogels with reconfigurable surface topography for programming unidirectional liquid transport. Adv. Funct. Materials. 2019, 29, 1807858.
65. Li, J.; Qin, Q. H.; Shah, A.; Ras, R. H.; Tian, X.; Jokinen, V. Oil droplet self-transportation on oleophobic surfaces. Sci. Adv. 2016, 2, e1600148.
66. Bai, H.; Wang, X.; Li, Z.; et al. Improved liquid collection on a dual-asymmetric superhydrophilic origami. Adv. Mater. 2023, 35, e2211596.
67. Zhang, Q.; Bai, X.; Li, Y.; Zhang, X.; Tian, D.; Jiang, L. Ultrastable super-hydrophobic surface with an ordered scaly structure for decompression and guiding liquid manipulation. ACS. Nano. 2022, 16, 16843-52.
68. Li, Y.; Zhang, Q.; Wei, X.; Li, K.; Tian, D.; Jiang, L. Curvature adjustable liquid transport on anisotropic microstructured elastic film. ACS. Nano. 2023, 17, 6036-44.
69. Liu, Y.; Zhan, H.; He, X.; et al. Excellent liquid unidirectional transport inner tilted-sector arrayed tubes. Adv. Mater. Interface. 2023, 10, 2300239.
70. Feng, S.; Zhu, P.; Zheng, H.; et al. Three-dimensional capillary ratchet-induced liquid directional steering. Science 2021, 373, 1344-8.
71. Huang, S.; Li, J.; Liu, L.; Zhou, L.; Tian, X. Lossless fast drop self-transport on anisotropic omniphobic surfaces: origin and elimination of microscopic liquid residue. Adv. Mater. 2019, 31, e1901417.
72. Li, J.; Zheng, H.; Zhou, X.; Zhang, C.; Liu, M.; Wang, Z. Flexible Topological Liquid Diode Catheter. Mater. Today. Phys. 2020, 12, 100170.
73. Sun, Z.; Cao, Z.; Li, Y.; et al. Switchable smart porous surface for controllable liquid transportation. Mater. Horiz. 2022, 9, 780-90.
74. Demirörs, A. F.; Aykut, S.; Ganzeboom, S.; et al. Amphibious transport of fluids and solids by soft magnetic carpets. Adv. Sci. (Weinh). 2021, 8, e2102510.
75. Zhang, J.; Feng, H.; He, H.; et al. Analysis of water droplet motion on hydrophobic surfaces with different microstructures. J. Appl. Polymer. Sci. 2024, 141, e55516.
76. Long, Z.; Yu, C.; Cao, M.; Ma, J.; Jiang, L. Bioinspired gas manipulation for regulating multiphase interactions in electrochemistry. Adv. Mater. 2024, 36, e2312179.
77. Liang, X.; Kumar, V.; Ahmadi, F.; Zhu, Y. Manipulation of droplets and bubbles for thermal applications. Droplet 2022, 1, 80-91.
78. Padinjareveetil, A. K. K.; Pykal, M.; Bakandritsos, A.; Zbořil, R.; Otyepka, M.; Pumera, M. Real time tracking of nanoconfined water-assisted ion transfer in functionalized graphene derivatives supercapacitor electrodes. Adv. Sci. (Weinh). 2024, 11, e2307583.
79. Mazaltarim, A. J.; Bowen, J. J.; Taylor, J. M.; Morin, S. A. Dynamic manipulation of droplets using mechanically tunable microtextured chemical gradients. Nat. Commun. 2021, 12, 3114.
80. Zhang, Q.; He, L.; Zhang, X.; Tian, D.; Jiang, L. Switchable direction of liquid transport via an anisotropic microarray surface and thermal stimuli. ACS. Nano. 2020, 14, 1436-44.
81. Wang, J.; Song, X.; Wang, C.; et al. A review for design, mechanism, fabrication, and application of magnetically responsive microstructured functional surface. Int. J. Extrem. Manuf. 2025, 7, 012004.
82. Wen, K.; Chen, X.; Cheng, S.; et al. Modulation of wetting state switching of droplets on superhydrophobic microstructured surfaces by external electric field. J. Colloid. Interface. Sci. 2024, 672, 533-42.
83. Chen, Y.; Xie, A.; Cui, J.; et al. One-step facile fabrication of visible light driven antifouling carbon cloth fibers membrane for efficient oil-water separation. Sep. Purif. Technol. 2019, 228, 115769.
84. Duan, Z.; Zhu, Y.; Ren, P.; et al. Non-UV activated superhydrophilicity of patterned Fe-doped TiO2 film for anti-fogging and photocatalysis. Appl. Surf. Sci. 2018, 452, 165-73.
85. Yu, N.; Wang, S.; Liu, Y.; et al. Thermal-responsive anisotropic wetting microstructures for manipulation of fluids in microfluidics. Langmuir 2017, 33, 494-502.
86. Miao, W.; Wang, D.; Liu, Z.; et al. Bioinspired Self-Healing Liquid Films for Ultradurable Electronics. ACS. Nano. 2019, 13, 3225-31.
87. Wang, Z.; Yuan, L.; Wang, L.; Wu, T. Stretchable superlyophobic surfaces for nearly- lossless droplet transfer. Sens. Actuators. B. Chem. 2017, 244, 649-54.
88. Wu, S.; Wang, J.; Niu, L.; Yao, J.; Wu, D.; Li, A. Reversible switching between isotropic and anisotropic wetting by one-direction curvature tuning on flexible superhydrophobic surfaces. Appl. Phys. Lett. 2011, 98, 081902.
89. Ma, C.; Chen, C.; Xu, Z.; Lv, C.; Zheng, Q. Substrate curvature dependence of intrinsic contact angles. Extreme. Mech. Lett. 2021, 48, 101388.
90. Hu, B.; Duan, Z.; Xu, B.; et al. Ultrafast self-propelled directional liquid transport on the pyramid-structured fibers with concave curved surfaces. J. Am. Chem. Soc. 2020, 142, 6111-6.
91. Lee, W. K.; Jung, W. B.; Rhee, D.; et al. Monolithic polymer nanoridges with programmable wetting transitions. Adv. Mater. 2018, 30, e1706657.
92. Gao, C.; Wang, L.; Lin, Y.; et al. Droplets manipulated on photothermal organogel surfaces. Adv. Funct. Mater. 2018, 28, 1803072.
93. Kim, D. H.; Kim, S.; Park, S. R.; Fang, N. X.; Cho, Y. T. Shape-deformed mushroom-like reentrant structures for robust liquid-repellent surfaces. ACS. Appl. Mater. Interfaces. 2021, 13, 33618-26.
94. Palamà, I. E.; D’amone, S.; Biasiucci, M.; Gigli, G.; Cortese, B. Bioinspired design of a photoresponsive superhydrophobic/oleophilic surface with underwater superoleophobic efficacy. J. Mater. Chem. A. 2014, 2, 17666-75.
95. Huang, Z.; Chen, C.; Wang, X.; et al. Light-driven locomotion of underwater bubbles on ultrarobust paraffin-impregnated laser-ablated Fe3O4-doped slippery surfaces. ACS. Appl. Mater. Interfaces. 2021, 13, 9272-80.
96. Chen, C.; Huang, Z.; Shi, L.; et al. Remote photothermal actuation of underwater bubble toward arbitrary direction on planar slippery Fe3O4 -doped surfaces. Adv. Funct. Mater. 2019, 29, 1904766.
97. Li, D.; Jiao, L.; Chen, R.; et al. Controllable light-induced droplet evaporative crystallization. Soft. Matter. 2021, 17, 8730-41.
98. Hwang, H.; Papadopoulos, P.; Fujii, S.; Wooh, S. Driving droplets on liquid repellent surfaces via light-driven marangoni propulsion. Adv. Funct. Mater. 2022, 32, 2111311.
99. Wu, J.; Li, X.; Lin, T.; et al. Electric-field-induced selective directed transport of diverse droplets. ACS. Appl. Mater. Interfaces. 2024, 16, 4126-37.
100. Zhang, Q.; Li, Y.; Cai, H.; et al. A single-droplet electricity generator achieves an ultrahigh output over 100 v without pre-charging. Adv. Mater. 2021, 33, e2105761.
101. Tang, B.; Meng, C.; Zhuang, L.; et al. Field-induced wettability gradients for no-loss transport of oil droplets on slippery surfaces. ACS. Appl. Mater. Interfaces. 2020, 12, 38723-9.
102. Li, Y.; Li, J.; Liu, L.; et al. Switchable wettability and adhesion of micro/nanostructured elastomer surface via electric field for dynamic liquid droplet manipulation. Adv. Sci. (Weinh). 2020, 7, 2000772.
103. Chen, C.; Huang, Z.; Jiao, Y.; et al. In Situ Reversible control between sliding and pinning for diverse liquids under ultra-low voltage. ACS. Nano. 2019, 13, 5742-52.
104. Dai, H.; Gao, C.; Sun, J.; et al. Controllable high-speed electrostatic manipulation of water droplets on a superhydrophobic surface. Adv. Mater. 2019, 31, e1905449.
105. Li, J.; Ha, N. S.; Liu, T.; van, D. R. M.; ‘CJ’, K. C. J. Ionic-surfactant-mediated electro-dewetting for digital microfluidics. Nature 2019, 572, 507-10.
106. Sun, J.; Zhang, L.; Gong, S.; Chen, J.; Guo, H. Mechano-driven tribo-electrophoresis enabled human-droplet interaction in 3D space. Adv. Mater. 2023, 35, e2305578.
107. Chen, C.; Huang, Z.; Zhu, S.; et al. In situ electric-induced switchable transparency and wettability on laser-ablated bioinspired paraffin-impregnated slippery surfaces. Adv. Sci. (Weinh). 2021, 8, e2100701.
108. Wang, H.; Zhang, Z.; Wang, Z.; et al. Multistimuli-responsive microstructured superamphiphobic surfaces with large-range, reversible switchable wettability for oil. ACS. Appl. Mater. Interfaces. 2019, 11, 28478-86.
109. Qin, H.; Peng, X.; Ji, J.; Li, J. A magnetically controlled microstructured surface for three-dimensional droplet manipulation. Smart. Mater. Struct. 2024, 33, 025020.
110. Tian, D.; Zhang, N.; Zheng, X.; et al. Fast responsive and controllable liquid transport on a magnetic fluid/nanoarray composite interface. ACS. Nano. 2016, 10, 6220-6.
111. Yun, S.; Cho, S.; Kim, H. W.; Cho, S. B.; Lee, S.; Yong, K. Reversible switching performance of water droplet-driven triboelectric nanogenerators using a magnetocontrollable lubricant-infused surface for sustainable power generation. Nano. Energy. 2022, 103, 107783.
112. Zhang, Y.; Wu, C.; Gu, H.; et al. An active strategy based on different droplet removal modes on polydimethylsiloxane magnetic microstructures. Small 2024, 20, e2400466.
113. Jun, K.; Kim, D.; Ryu, S.; Oh, I. K. surface modification of anisotropic dielectric elastomer actuators with Uni-and Bi-axially wrinkled carbon electrodes for wettability control. Sci. Rep. 2017, 7, 6091.
114. Lu, Y.; Sathasivam, S.; Song, J.; Crick, C. R.; Carmalt, C. J.; Parkin, I. P. Repellent materials. Robust self-cleaning surfaces that function when exposed to either air or oil. Science 2015, 347, 1132-5.
115. Su, C.; Zhou, L.; Yuan, C.; et al. Robust superhydrophobic composite fabricated by a dual-sized particle design. Compos. Sci. Technol. 2023, 231, 109785.
116. Li, D.; Wang, H.; Liu, Y.; Wei, D.; Zhao, Z. Large-scale fabrication of durable and robust super-hydrophobic spray coatings with excellent repairable and anti-corrosion performance. Chem. Eng. J. 2019, 367, 169-79.
117. Li, X.; Bista, P.; Stetten, A. Z.; et al. Spontaneous charging affects the motion of sliding drops. Nat. Phys. 2022, 18, 713-9.
118. Mendel, N.; Wu, H.; Mugele, F. Electrowetting-assisted generation of ultrastable high charge densities in composite silicon oxide-fluoropolymer electret samples for electric nanogenerators. Adv. Funct. Mater. 2021, 31, 2007872.
119. Xu, W.; Zheng, H.; Liu, Y.; et al. A droplet-based electricity generator with high instantaneous power density. Nature 2020, 578, 392-6.
120. Guo, Y.; Zhuang, L.; Feng, H.; et al. Programmable control of two-phase fluid interface relative motion in electrowetting device. Adv. Mater. Interface. 2021, 8, 2101086.
121. Zhou, X.; Sudersan, P.; Diaz, D.; et al. Chemically robust superhydrophobic surfaces with a self-replenishing nanoscale liquid coating. Droplet 2024, 3, e103.
122. Zhang, F.; Yan, H.; Chen, M. Multi-scale superhydrophobic surface with excellent stability and solar-thermal performance for highly efficient anti-icing and deicing. Small 2024, 20, e2312226.
123. Zhang, H.; Zhang, W.; Jin, Y.; et al. Freezing droplet ejection by spring-like elastic pillars. Nat. Chem. Eng. 2024, 1, 765-73.
124. Ang, B. T. W.; Zhang, J.; Lin, G. J.; Wang, H.; Lee, W. S. V.; Xue, J. Enhancing water harvesting through the cascading effect. ACS. Appl. Mater. Interfaces. 2019, 11, 27464-9.
125. Zhang, C.; Xie, H.; Du, Y.; Wu, T.; Wang, Z.; Qu, J. Bioinspired heterogeneous surface for radiative cooling enhanced power-free moisture harvesting in unsaturated atmosphere. Adv. Mater. 2025, 37, e2414389.
126. Zhang, J.; Li, B.; Zhou, Z.; Zhang, J. Durable superhydrophobic surfaces with self-generated wenzel sites for efficient fog collection. Small 2024, 20, e2312112.
127. Li, Z.; Wu, W.; Sun, J.; Li, J.; Zhang, D. Bioinspired rapid self-replenishing liquid-infused surfaces for stable anti-adhesion of electrosurgical electrodes. Chem. Eng. J. 2023, 470, 144173.
128. Xiao, W.; Wan, X.; Shi, L.; Ye, M.; Zhang, Y.; Wang, S. A viscous-biofluid self-pumping organohydrogel dressing to accelerate diabetic wound healing. Adv. Mater. 2024, 36, e2401539.
129. Liang, X.; Meng, S.; Zhi, C.; et al. Thermal transfer printed flexible and wearable bionic skin with bilayer nanofiber for comfortable multimodal health management. Adv. Healthc. Mater. 2025, 14, e2403780.
130. Zhang, Q.; Ji, K.; Huo, T.; et al. Biomimetic patch with wicking-breathable and multi-mechanism adhesion for bioelectrical signal monitoring. ACS. Appl. Mater. Interfaces. 2022, 14, 48438-48.
131. Chen, X.; Xiong, J.; Parida, K.; et al. Transparent and stretchable bimodal triboelectric nanogenerators with hierarchical micro-nanostructures for mechanical and water energy harvesting. Nano. Energy. 2019, 64, 103904.
132. Liu, B. Y.; Wu, J.; Xue, C. H.; et al. Bioinspired superhydrophobic all-in-one coating for adaptive thermoregulation. Adv. Mater. 2024, 36, e2400745.
Cite This Article

How to Cite
Download Citation
Export Citation File:
Type of Import
Tips on Downloading Citation
Citation Manager File Format
Type of Import
Direct Import: When the Direct Import option is selected (the default state), a dialogue box will give you the option to Save or Open the downloaded citation data. Choosing Open will either launch your citation manager or give you a choice of applications with which to use the metadata. The Save option saves the file locally for later use.
Indirect Import: When the Indirect Import option is selected, the metadata is displayed and may be copied and pasted as needed.
About This Article
Copyright
Data & Comments
Data
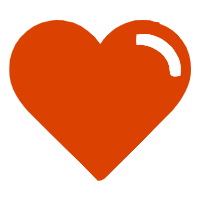
Comments
Comments must be written in English. Spam, offensive content, impersonation, and private information will not be permitted. If any comment is reported and identified as inappropriate content by OAE staff, the comment will be removed without notice. If you have any queries or need any help, please contact us at [email protected].