Electroplating of Ni-W coating on Zn surface for durable Zn ion batteries
Abstract
Aim: Aqueous zinc (Zn)-ion batteries have gained recognition as a promising energy storage solution due to their abundant zinc resources, cost-effectiveness, high energy density, and inherent safety. However, their practical application is significantly limited by issues such as dendrite formation and parasitic side reactions, which undermine the stability, efficiency, and longevity of Zn anodes. Methods: In this study, we present a novel approach by introducing a nanocrystalline nickel-tungsten (Ni-W) coating onto Zn anodes via electrodeposition. This coating acts as a functional interface, regulating Zn dissolution and deposition, suppressing dendrite growth, and minimizing side reactions. Additionally, W enhances Zn2+ ion adsorption, reduces nucleation energy barriers, and promotes uniform Zn growth along the Zn (002) crystallographic plane. Results: The compact morphology of the Ni-W layer further serves as a protective barrier, improving electrode stability during extended cycling. The
Keywords
INTRODUCTION
Among various metal-based secondary batteries, aqueous zinc-ion batteries (AZIBs) have emerged as a viable alternative for next-generation energy storage due to their abundance of zinc resources, cost-effectiveness, high theoretical capacity of 820 mAh g-1[1-3] and inherent safety provided by aqueous electrolytes. These attributes position AZIBs as an attractive solution for large-scale renewable energy storage systems, offering environmental benefits over conventional batteries that rely on organic electrolytes. Despite their potential, AZIBs face critical challenges, particularly at the zinc anode. Dendrite formation, driven by the "tip effect" during repetitive zinc plating and stripping cycles[4-6], remains a significant issue, leading to unstable cycling behavior[7]. Furthermore, side reactions such as hydrogen evolution reactions (HER), corrosion, and passivation[8,9] reduce both efficiency and lifespan, severely limiting the commercial viability of AZIBs[10]. To mitigate these issues, several approaches have been developed[11,12], including surface modification[13-16], structural optimization[17,18], electrode engineering[19-21], and electrolyte/separator regulation[19,22], effectively reducing dendrite formation and unwanted side reactions[23-25]. These challenges necessitate the development of advanced materials and engineering strategies to stabilize the zinc anode[26,27].
Researchers have made considerable strides in improving the stability of Zn anodes through alloying and applying protective surface coatings[28]. Zinc-nickel alloys[29,30], for example, are widely recognized for their corrosion resistance and structural stability[31,32]. Their low susceptibility to hydrogen embrittlement further enhances their applicability in environments prone to degradation[33].
Among the emerging solutions, tungsten-based alloys have demonstrated remarkable potential as protective coatings in zinc-ion batteries. Tungsten offers several exceptional properties, including a high melting point (3,410 °C), low thermal expansion coefficient (4.3 × 10-6 C-1), and excellent thermal conductivity
In zinc-based batteries, tungsten’s properties contribute significantly to improved stability and longevity. The addition of tungsten to the electrode enhances corrosion resistance, a critical factor in maintaining electrode integrity in aqueous electrolytes. Its strong bonding and high melting point help prevent structural degradation during repeated charge and discharge cycles. Furthermore, tungsten's ability to regulate zinc deposition effectively reduces dendrite formation, minimizing the risk of short circuits and extending battery lifespan[38,39].
This paper examines the effects of nickel-tungsten (Ni-W) alloy coatings on Zn foil under varying tungsten ratios while maintaining a constant nickel concentration, focusing on their impact on zinc anode stability. By promoting uniform ion transport and forming a durable alloy with zinc, Ni-W shows potential to improve both the efficiency and durability of AZIBs.
In this study, a nanocrystalline Ni-W alloy coating was developed through electrodeposition to address these challenges[40]. By forming a durable alloy with zinc, the Ni-0.1W@Zn layer enhances uniform Zn deposition and promotes controlled Zn growth along crystallographic planes. This design improves corrosion resistance, suppresses dendrite formation, and ensures electrode stability during cycling. The
MATERIALS AND METHODS
Experimental details
The electrodeposition bath composition was adjusted[37-41], and deposition was conducted in galvanostatic mode using a two-electrode setup. Zinc foil, with an exposed surface area of 4 cm × 4.5 cm and a thickness of 0.1 mm, served as the cathode substrate, while a platinum electrode functioned as the anode. Ni-W coatings were plated onto the zinc foil at four concentrations (0.05, 0.1, 0.15, and 0.2 M) and for four varying durations (180, 300, 600, and 900 s). For comparison, Ni was deposited on the zinc foil at a concentration of 0.07 M. The resulting findings are summarized in Tables 1-3.
Plating bath formulation and conditions for Ni-W deposition on Zinc foil
Chemicals | Bath composition [M (mol/l)] | Purpose |
Nickel sulfate (NiSO4·6H2O) | 0.07 | Ni source |
Sodium tungstate (Na2WO4·2H2O) | 0.05, 0.1, 0.15, 0.2 | W source |
Trisodium citrate dihydrate (Na3C6H5O7·2H2O) | 0.58 | Complexed for Ni and W |
Ammonium chloride (NH4Cl) | 0.58 | To increase current efficiency |
Sodium bromide (NaBr) | 0.2 | Improve conductivity |
Plating bath formulation and conditions for Ni deposition on Zinc foil
Chemicals | Bath composition [M (mol/l)] | Purpose |
Nickel sulfate (NiSO4·6H2O) | 0.07 | Ni source |
Sodium tungstate (Na2WO4·2H2O) | - | W source |
Trisodium citrate dihydrate (Na3C6H5O7·2H2O) | 0.58 | Complexed for Ni and W |
Ammonium chloride (NH4Cl) | 0.58 | To increase current efficiency |
Sodium bromide (NaBr) | 0.2 | Improve conductivity |
Electrodeposition parameters for depositing Ni and Ni-W coating on Zn foil
Parameters | Ni | Ni-W |
Plating time (s) | 180, 300, 600, 900 | 180, 300, 600, 900 |
Current density (A/cm2) | 1.8 | 1.8 |
Anode material | Pt mesh | Pt mesh |
Temperature (°C) | 25 | 25 |
Preparation of Ni@Zn foil and Ni-W@Zn foil
Ni@Zn and Ni-W@Zn foils were prepared through constant-potential electrodeposition. Before deposition, high-purity Zn foils (99.9%) measuring 4 cm × 4.5 cm were thoroughly cleaned with acetone to remove any surface contaminants. The cleaned foil was then mounted on an acrylic plate to allow coating on one side only. Ni and Ni-W electrodeposition was performed for 180, 300, 600, and 900 s in an electrolyte solution. Deionized water was used to dilute the nickel concentration to 0.07 M, while sodium tungstate
Material characterizations
The morphology of Ni@Zn foil, Ni-W@Zn foil, and bare-Zn foil was determined through scanning electron microscopy (SEM) with Energy Dispersive X-ray (EDX) mapping to determine the elemental distribution. The phase analysis of electrodes was obtained by X-ray diffraction (XRD). The optimal Ni-W@Zn samples were analyzed using X-ray Fluorescence (XRF) to determine the elemental composition of the nanoparticles. The surface roughness was identified using a confocal laser scanning microscope (CLSM).
Electrochemical measurements
The electrochemical performance tests were conducted using 2 M ZnSO4 electrolyte packaged in CR2032 coin batteries. The ionic conductivity of bare-Zn, Ni@Zn, and Ni-W@Zn foils was characterized by electrochemical impedance spectroscopy (EIS) at frequencies ranging from 0.01 Hz to 100 kHz. Cyclic voltammetry (CV) tests were performed at a scan rate of 0.1 mV s-1 and a voltage range of 0.2-1.6 V. The Tafel curve and linear scanning voltammetry (LSV) measurements used a three-electrode system, with bare-Zn, Ni@Zn, and Ni-W@Zn as the working electrodes, platinum as the counter electrode, and Ag/AgCl as the reference electrode, respectively. The scanning rate was set to 0.1 mV s-1 (CHI 660e, Chenhua, China). Full cells were assembled using V2O5 as the cathode to evaluate the effectiveness of the Ni@Zn and Ni-W@Zn foils as anodes. The V2O5 cathodes were prepared by mixing the active material, conductivity agent, and PVDF binder in a weight ratio of 7:2:1, then pressed onto carbon paper using a doctor blade and dried under vacuum at 80 °C for 12 h. The diameter of the electrodes was 14 mm. The cell also included the integration of polypropylene microporous separators (GF/D 47 mm). Long-cycle stability during the charge-discharge process of bare-Zn, Ni@Zn, and Ni-W@Zn foil symmetrical cells was tested at 1 mA cm-2. The performance of bare-Zn||Cu, Ni@Zn||Cu, and Ni-W@Zn||Cu asymmetrical cells, along with bare-Zn||V2O5, Ni@Zn||V2O5, and Ni-W@Zn||V2O5 full cells, was evaluated using the NEWARE system over a voltage range of 0.2-1.6 V.
RESULTS AND DISCUSSION
The electrodeposition process for a nanocrystalline Ni-W on Zn foils is outlined in Figure 1A. Ni and Ni-W electrodeposition was performed for 180, 300, 600, and 900 s in an electrolyte solution. The solutions used for Ni-W and Ni deposition, as detailed in Tables 1-3, were fully dissolved in deionized water to ensure clarity and consistency. To determine the optimal tungsten concentration and deposition time, rate performance tests were conducted to assess the electrochemical efficiency of the coatings. These tests evaluated the specific capacity across various tungsten concentrations and deposition times, providing critical insights into their correlation and performance trends. As shown in Supplementary Figure 1, the results reveal a correlation between specific capacity and both tungsten concentration and deposition time, with the combination of a 0.1 M tungsten concentration and a 300 s deposition time delivering the highest specific capacity. This outcome highlights an optimal balance between coating quality and electrochemical performance, emphasizing the importance of fine-tuning deposition parameters to achieve maximum efficiency in Zn-ion battery anodes. The optimal condition of 0.1 M tungsten concentration and 300 s deposition time provides the highest specific capacity, emphasizing the importance of deposition parameters. To evaluate the effects of tungsten concentration and deposition time, morphological analysis was conducted to examine the surface structure and coating quality of Zn electrodes. As shown in Figure 1B, SEM images illustrate the results for deposition times of 180, 300, 600, and 900 s at a tungsten concentration of 0.1 M. At 180 s [Supplementary Figure 2], the Ni-W layer was insufficient to fully cover the Zn foil. Prolonged deposition times, such as 600 and 900 s [Supplementary Figure 3], led to the formation of tungsten oxide, resulting in non-uniform adhesion and reduced coating quality, particularly when the tungsten concentration exceeded 0.15 M. Additionally, deposition times below 300 s were found to be suboptimal due to hydrogen gas adsorption on the Zn surface, causing surface cracks and voids
Figure 1. (A) Schematic illustration of preparation procedure and mechanism simulations of Ni-0.1W@Zn. SEM images and cross-section of (B) Bare-Zn, (C) Ni@Zn and (D) Ni-0.1W@Zn. (E) Element mapping images of Ni-0.1W@Zn. and (F) XRD patterns of Bare-Zn, Ni@Zn and Ni-0.1W@Zn.
SEM characterization reveals that Ni@Zn [Figure 1C] exhibits a polygonal structure with rough facets, whereas Ni-0.1W@Zn [Figure 1D] forms a semi-spherical and more compact morphology. This distinct morphological evolution upon tungsten incorporation highlights its critical role in facilitating uniform Zn deposition and enhancing surface compactness, both of which are essential for improved cycling stability. SEM-EDX element mapping [Figure 1E and Supplementary Figure 5] confirms that Ni and W are uniformly distributed across the Ni-0.1W@Zn surface, forming a highly compact and homogeneous layer approximately 5 µm thick. XRF [Supplementary Figure 6] analysis further substantiates tungsten incorporation, revealing a tungsten content of 5.03%, indicating its successful integration within the bulk structure. Complementary energy-dispersive X-ray spectroscopy (EDS) analysis identifies a higher tungsten content of 12.51%, suggesting preferential enrichment near the coating surface. These findings not only verify the presence of tungsten but also underscore its strategic localization, which enhances Zn2+ ion adsorption, promotes uniform Zn deposition, and suppresses dendrite formation.
The optimized coating thickness of approximately 5 µm ensures efficient electron transport and minimizes internal resistance, critical for achieving high-performance Zn-ion batteries[43]. Tungsten incorporation significantly enhances structural stability during prolonged cycling, making Ni-0.1W@Zn highly suitable for long-term applications. In contrast, the Ni@Zn coating exhibits a considerably thicker layer (approximately 13 µm), as shown in cross-sectional SEM analysis [Supplementary Figure 7]. While providing surface coverage, this excessive thickness increases internal resistance and hinders efficient electron transport. Moreover, the absence of tungsten in Ni@Zn results in insufficient suppression of dendrite growth and limited structural stability during extended cycling. Conversely, the Ni-0.1W@Zn coating, with its optimized thickness and tungsten incorporation, delivers superior electron transport and reduced resistance, ensuring efficient Zn plating and stripping cycles[44]. These properties position Ni-0.1W@Zn as a more effective and reliable anode material for Zn-ion batteries. SEM analysis further highlights the uniform and dense morphology of the Ni-W coating, which is vital for controlling Zn deposition and mitigating dendrite growth. These structural attributes significantly enhance anode stability, addressing challenges associated with uncontrolled Zn growth during extended cycling. The optimized morphology and compositional features establish Ni-0.1W@Zn as a promising material for developing durable, high-performance energy storage systems.
Additionally, XRD analysis [Figure 1F] confirms the presence of Ni and W coatings on Zn foil. Distinct peaks are observed for the Ni (200) crystallographic plane at 2θ = 44.52° in a face-centered cubic structure and for tungsten at 2θ = 43.19°, aligning with the Joint Committee on Powder Diffraction Standards (JCPDS). The average particle size of nickel nanoparticles, calculated from the Ni (111) peak at 2θ = 44.54° using the Scherrer equation, is approximately 27 nm. The nanoscale particle size shortens diffusion paths for ions and electrons, enhancing reaction kinetics and increasing rate capability. Furthermore, the structural flexibility of nanoparticles accommodates volume changes during charge and discharge cycles, minimizing degradation and improving cycling stability. These features are particularly valuable for applications requiring high energy density and extended cycle life[45].
Figure 2A-C illustrates bare-Zn, Ni@Zn, and Ni-0.1W@Zn electrodes soaked in a 2 M ZnSO4 electrolyte for 14 days to evaluate their chemical stability. The SEM images of the electrodes after soaking, as shown in Figure 2D-F, reveal a uniform surface on Ni-0.1W@Zn, whereas Zn dendrites are more pronounced on the bare-Zn and Ni@Zn surfaces. This indicates that the Ni-0.1W@Zn coating effectively minimizes Zn dendrite formation and controls crystal growth, contributing to enhanced battery longevity[46-48].
Figure 2. Optical image of initial state of (A) Bare-Zn and (B) Ni@Zn and (C) Ni-0.1W@Zn compared with after soaked and immersed in 2M ZnSO4 electrolyte for 14 days. SEM images of (D) Bare-Zn, (E) Ni@Zn and (F) Ni-0.1W@Zn immersed in 2M ZnSO4 electrolyte for 14 days of surface. Contact angles of (G) Bare-Zn, (H) Ni@Zn and (I) Ni-0.1W@Zn and (J) Tafel curve of Bare-Zn, Ni@Zn and Ni-0.1W@Zn.
Figure 2G-I shows contact angle measurements for bare-Zn, Ni@Zn, and Ni-0.1W@Zn with 2 M ZnSO4 electrolyte, measuring 110.45°, 129.63°, and 71.10°, respectively. The significantly lower contact angle of
To verify the positive effects of the Ni-W coating on zinc metal anodes, long-term cycling stability tests were conducted at a constant current density of 1 mA cm-2 and a capacity of 0.5 mAh cm-2. While the initial cycles exhibited relatively high voltage polarization, the overpotential for Zn plating/stripping with
Figure 3. (A) Cycling stability of Bare-Zn, Ni@Zn and Ni-0.1W@Zn in symmetrical cells at 1 mA cm-2; (B) enlarged voltage profiles of Ni@Zn and Ni-0.1W@Zn at 1 mA cm-2; (C) Cycling stability of Bare-Zn, Ni@Zn and Ni-0.1W@Zn in symmetrical cells at
Figure 4A-C presents the morphologies of Bare-Zn, Ni@Zn, and Ni-0.1W@Zn anodes in symmetric cells at 1 mA cm-2. The Bare-Zn surface exhibits an uneven texture with prominent Zn flakes and dendrites, which appear after 100 h in bare-Zn cells and after 400 h in Ni@Zn cells [Supplementary Figure 10]. These changes reflect progressive dendrite growth and surface degradation over time. In contrast, the Ni-0.1W@Zn anode retains a smooth and uniform surface even after 2,000 h, demonstrating its effectiveness in achieving consistent Zn deposition and minimizing by-product formation during plating and stripping. Further analysis, as shown in Supplementary Figure 11, examines the morphologies of Bare-Zn, Ni@Zn, and Ni-0.1W@Zn electrodes at a higher current density of 2 mA cm-2. On Bare-Zn and Ni@Zn surfaces, zinc dendrites gradually grow and cluster into large protrusions due to uncontrolled Zn plating and stripping, leading to the formation of Zn flakes and unwanted side reactions. In contrast, SEM images of the Ni-0.1W@Zn anode reveal a highly uniform Zn deposition, effectively suppressing dendrite growth and reducing the occurrence of side reactions. Laser confocal microscopy in Figure 4D-F and
Figure 4. SEM images of (A) Bare-Zn after 100 h at 1 mA cm-2 and (B) Ni@Zn after 400 h at 1 mA cm-2 and (C) Ni-0.1W@Zn after 2,000 h at 1 mA cm-2. The laser confocal microscopy images of (D) Bare-Zn (E) Ni@Zn and (F) Ni-0.1W@Zn after plating/stripping.
Further evaluation of the Ni-0.1W@Zn anode was conducted in full cells paired with V2O5 as the cathode, as shown in Figure 5A. CV curves at 1 mV s-1 demonstrate significantly enhanced electrochemical capacity in Ni-0.1W@Zn||V2O5 cells. The Nyquist plots for full cells using bare-Zn, Ni@Zn, and Ni-0.1W@Zn anodes, tested before and after cycling [Figure 5B], reveal that the charge transfer resistance of bare-Zn (119.0 Ω) and Ni@Zn (90.0 Ω) is markedly higher than that of Ni-0.1W@Zn (45.0 Ω). These findings confirm the superior charge transfer ability of the Ni-0.1W@Zn anode. The reduced impedance highlights enhanced Zn2+ ion transference number and improved charge transfer kinetics, both critical for achieving stable and uniform Zn plating/stripping. The incorporation of tungsten generates a uniform electric field across the electrode surface, enabling homogeneous Zn deposition while effectively suppressing dendrite formation. This well-regulated deposition mechanism ensures efficient Zn cycling and high reversibility, contributing to the improved cycling stability of the Ni-0.1W@Zn anode. These results underscore the importance of the Ni-W coating in optimizing Zn2+ transport, stabilizing Zn deposition, and addressing challenges in Zn-ion battery performance and durability.
Figure 5. (A) CV curves of Bare-Zn// V2O5, Ni@Zn//V2O5 and Ni-0.1W@Zn//V2O5; (B) EIS curves of Bare-Zn//V2O5, Ni@Zn//V2O5 and Ni-0.1W@Zn//V2O5; (C) Charge and discharge curves of Bare-Zn//V2O5, Ni@Zn//V2O5 and Ni-0.1W@Zn//V2O5; (D) Rate performances of Bare-Zn//V2O5, Ni@Zn//V2O5 and Ni-0.1W@Zn//V2O5; and (E) Cycling stabilities of Bare-Zn//V2O5, Ni@Zn//V2O5 and Ni-0.1W@Zn//V2O5 at 1 mA cm-2.
The charge/discharge profiles of full cells at a current density of 0.3 A g-1, as shown in Figure 5C, reveal significant differences in specific capacity among the electrodes. The bare Zn anode achieves a discharge specific capacity of 117.33 mAh g-1, while the Ni@Zn anode reaches 150.06 mAh g-1.
Notably, the Ni-0.1W@Zn anode delivers the highest discharge specific capacity of 210.42 mAh g-1, demonstrating its ability to significantly enhance reversible capacity through improved Zn plating/stripping behavior. Furthermore, the Ni-0.1W@Zn anode exhibits substantially reduced voltage polarization compared to both bare Zn and Ni@Zn electrodes, aligning with CV results and further validating its superior electrochemical performance. High-rate performance testing Figure 5D shows that the Ni-0.1W@Zn battery achieves an initial capacity of 210.42 mAh g-1 at 0.3 A g-1 and maintains capacity even at 5.0 A g-1 [Supplementary Figure 13]. The Ni-0.1W@Zn||V2O5 batteries exhibit significantly improved long-term cycling performance compared to bare Zn||V2O5 and Ni@Zn||V2O5 batteries. At 1 A g-1, the Ni-0.1W@Zn anode achieves a specific capacity of 163 mAh g-1 with capacity retention exceeding 81% after 1,500 cycles [Figure 5E]. At a lower current density of 0.5 A g-1 [Supplementary Figure 14], the Ni-0.1W@Zn anode demonstrates excellent stability, retaining 89% of its capacity after 1,000 cycles. These results highlight the consistent electrochemical performance of the Ni-0.1W@Zn anode across varied operating conditions. Combined with its outstanding performance at 1 A g-1, the Ni-0.1W@Zn system demonstrates versatility and durability, making it a promising candidate for advanced Zn-ion battery applications. In contrast, bare Zn||V2O5 and Ni@Zn||V2O5 batteries show rapid capacity loss and structural degradation caused by dendrite growth and ongoing corrosion during extended cycling. Morphological analysis reveals that the Ni-0.1W@Zn anode maintains a smooth and uniform surface even after prolonged cycling
CONCLUSIONS
In summary, we successfully developed a nanocrystalline Ni-W layer on Zn foil that directs Zn deposition along specific crystal planes, effectively minimizing corrosion and suppressing by-product formation. This modification significantly enhances Zn2+/Zn reversibility, presenting strong potential for stable and high-performance AZIBs. Optimal performance was achieved using a 0.1 M Ni-W concentration with a 300 s deposition time, producing favorable surface properties and improved battery performance. The Ni-0.1W@Zn anode demonstrated exceptional cycling stability, enabling symmetric cells to operate for over 2,000 h at a current density of 1 mA cm-2 with a high CE of 98%. Additionally, these electrodes consistently outperformed both Ni@Zn and bare Zn anodes, underscoring their practicality for energy storage applications.
The nanocrystalline Ni-W coating plays a pivotal role in advancing Zn-ion battery performance by providing a uniform and compact surface that facilitates controlled Zn deposition, suppresses dendrite formation, and reduces by-product accumulation. Its superior corrosion resistance protects the Zn substrate during prolonged cycling, while its excellent electrical conductivity ensures efficient electron transport. These synergistic features enhance structural stability and enable consistent Zn plating and stripping, resulting in a longer battery lifespan and improved operational safety.
This study presents a transformative approach to overcoming the challenges associated with zinc anodes through the integration of a scalable and practical Ni-W coating. The exceptional electrochemical stability, enhanced durability, and dendrite suppression demonstrated by the Ni-0.1W@Zn anode highlight its critical importance in the development of sustainable and high-efficiency energy storage solutions. By bridging the gap between laboratory research and industrial application, this work establishes a promising foundation for next-generation battery technologies essential to the future of renewable energy systems.
DECLARATIONS
Author’s contributions
Sample fabrication and characterization: Choonha-Anothai, K.; Yang, C.
Data analysis and interpretation: Choonha-Anothai, K.; Yang, C.; Wang, M.; Dai, Z.; Kiatwisarnkij, N.; Lolupiman, K.; Qin, J.
Preparation of the manuscript and discussion: Choonha-Anothai, K.; Yang, C.; Wang, M.; Dai, Z.;
Availability of data and materials
The data supporting the findings of this study are available within this Article and its Supplementary Materials. Further data are available from the corresponding authors upon request.
Financial support and sponsorship
This work was supported by the Thailand Science Research and Innovation Fund Chulalongkorn University (INDFF682266200010), National Research Council of Thailand (NRCT) and Chulalongkorn University (N42A660383), and National Natural Science Foundation of China (Grant Nos. 52125405 and U22A20108).
Conflicts of interest
All authors declared that there are no conflicts of interest.
Ethical approval and consent to participate
Not applicable.
Consent for publication
Not applicable.
Copyright
© The Author(s) 2025.
Supplementary Materials
REFERENCES
1. Arévalo-Cid, P.; Dias, P.; Mendes, A.; Azevedo, J. Redox flow batteries: a new frontier on energy storage. Sustain. Energy. Fuels. 2021, 5, 5366-419.
2. Shin, J.; Lee, J.; Park, Y.; Choi, J. W. Aqueous zinc ion batteries: focus on zinc metal anodes. Chem. Sci. 2020, 11, 2028-44.
3. Ghosh, M.; Vijayakumar, V.; Kurungot, S. Dendrite growth suppression by Zn2+-integrated nafion ionomer membranes: beyond porous separators toward aqueous Zn/V2O5 batteries with extended cycle life. Energy. Technol. 2019, 7, 1900442.
4. Chen, S.; Ying, Y.; Ma, L.; et al. An asymmetric electrolyte to simultaneously meet contradictory requirements of anode and cathode. Nat. Commun. 2023, 14, 2925.
5. Olbasa, B. W.; Fenta, F. W.; Chiu, S. F.; et al. High-rate and long-cycle stability with a dendrite-free zinc anode in an aqueous Zn-ion battery using concentrated electrolytes. ACS. Appl. Energy. Mater. 2020, 3, 4499-508.
6. Liu, X.; Guo, Y.; Ning, F.; et al. Fundamental understanding of hydrogen evolution reaction on zinc anode surface: a first-principles study. Nanomicro. Lett. 2024, 16, 111.
7. Cai, Z.; Wang, J.; Sun, Y. Anode corrosion in aqueous Zn metal batteries. eScience 2023, 3, 100093.
8. Qin, H.; Kuang, W.; Hu, N.; et al. Building metal-molecule interface towards stable and reversible Zn metal anodes for aqueous rechargeable zinc batteries. Adv. Funct. Mater. 2022, 32, 2206695.
9. Rosen, M. A.; Farsi, A. Battery technology: from fundamentals to thermal behavior and management. 2023. Available from: https://books.google.co.th/books?id=YpGoEAAAQBAJ [Last accessed on 18 Apr 2025]
10. Liu, Z.; Zhou, W.; He, J.; et al. Binder-free MnO2 as a high rate capability cathode for aqueous magnesium ion battery. J. Alloys. Compd. 2021, 869, 159279.
11. Zhang, N.; Wang, J.; Liu, X.; et al. Towards high-performance aqueous Zn-MnO2 batteries: formation mechanism and alleviation strategies of irreversible inert phases. Compos. Part. B. Eng. 2023, 260, 110770.
12. Hu, P.; Yan, M.; Zhu, T.; et al. Zn/V2O5 aqueous hybrid-ion battery with high voltage platform and long cycle life. ACS. Appl. Mater. Interfaces. 2017, 9, 42717-22.
13. He, H. B.; Liu, Z.; Luo, Z. X.; Zhang, Z. H.; Chen, Y.; Zeng, J. Sustainable porous biochar coated MnO2 composites as the cathode in aqueous Zn/Mn batteries. J. Alloys. Compd. 2023, 960, 170853.
14. Feng, K.; Wang, D.; Yu, Y. Progress and prospect of Zn anode modification in aqueous zinc-ion batteries: experimental and theoretical aspects. Molecules 2023, 28, 2721.
15. Chen, Y.; Li, J.; Zhang, S.; Cui, J.; Shao, M. Highly reversible zinc anode enhanced by ultrathin MnO2 cathode material film for high-performance zinc-ion batteries. Adv. Mater. Inter. 2020, 7, 2000510.
16. Cao, J.; Wang, X.; Qian, S.; et al. De-passivation and surface crystal plane reconstruction via chemical polishing for highly reversible zinc anodes. Adv. Mater. 2024, 36, e2410947.
17. Shang, Z.; Qi, H.; Liu, X.; Ouyang, C.; Wang, Y. Structural optimization of lithium-ion battery for improving thermal performance based on a liquid cooling system. Int. J. Heat. Mass. Transfer. 2019, 130, 33-41.
18. Yang, S.; Du, H.; Li, Y.; et al. Advances in the structure design of substrate materials for zinc anode of aqueous zinc ion batteries. Green. Energy. Environ. 2023, 8, 1531-52.
19. Wang, M.; Dai, Z.; Yang, C.; et al. Boosting de-solvation via halloysite nanotubes-cellulose composite separator for dendrite-free zinc anodes. Mater. Today. Energy. 2024, 46, 101736.
20. Yin, C.; Pan, C.; Pan, Y.; Hu, J. Hierarchical spheroidal MOF-derived MnO@C as cathode components for high-performance aqueous zinc ion batteries. J. Colloid. Interface. Sci. 2023, 642, 513-22.
21. Carvalho, M. L.; Mela, G.; Temporelli, A.; Brivio, E.; Girardi, P. Sodium-ion batteries with Ti1Al1TiC1.85 MXene as negative electrode: life cycle assessment and life critical resource use analysis. Sustainability 2022, 14, 5976.
22. Zhang, Y.; Bi, S.; Niu, Z.; Zhou, W.; Xie, S. Design of Zn anode protection materials for mild aqueous Zn-ion batteries. Energy. Mater. 2022, 2, 200012.
23. Li, Y.; Guo, Y.; Li, Z.; Wang, P.; Xie, Y.; Yi, T. Carbon-based nanomaterials for stabilizing zinc metal anodes towards high-performance aqueous zinc-ion batteries. Energy. Storage. Mater. 2024, 67, 103300.
24. Liu, M.; Tian, C.; Zhang, D.; et al. Design on modified-zinc anode with dendrite- and side reactions-free by hydrophobic organic-inorganic hybrids for ultra-stable zinc ion batteries. Nano. Energy. 2022, 103, 107805.
25. Zhou, X.; Chen, R.; Cui, E.; et al. A novel hydrophobic-zincophilic bifunctional layer for stable Zn metal anodes. Energy. Storage. Mater. 2023, 55, 538-45.
26. Xu, W.; Wang, Y. Recent progress on zinc-ion rechargeable batteries. Nanomicro. Lett. 2019, 11, 90.
27. Naveed, A.; Ali, A.; Rasheed, T.; et al. Revisiting recent and traditional strategies for surface protection of Zn metal anode. J. Power. Sources. 2022, 525, 231122.
28. Mo, F.; He, N.; Chen, L.; et al. Strategies for stabilization of Zn anodes for aqueous Zn-based batteries: a mini review. Front. Chem. 2021, 9, 822624.
29. Kothanam, N.; Harachai, K.; Hom-On, C.; et al. Enhanced particle incorporation for co-electrodeposited Ni-P/diamond coatings with a pulse-stirring technique. App. Surf. Sci. Adv. 2023, 18, 100499.
31. Nady, H.; Negem, M. Electroplated Zn-Ni nanocrystalline alloys as an efficient electrocatalyst cathode for the generation of hydrogen fuel in acid medium. Int. J. Hydrogen. Energy. 2018, 43, 4942-50.
32. Lotfi, N.; Aliofkhazraei, M.; Rahmani, H.; Darband, G. B. Zinc-nickel alloy electrodeposition: characterization, properties, multilayers and composites. Prot. Met. Phys. Chem. Surf. 2018, 54, 1102-40.
33. Bernasconi, R.; Panzeri, G.; Firtin, G.; Kahyaoglu, B.; Nobili, L.; Magagnin, L. Electrodeposition of ZnNi alloys from choline chloride/ethylene glycol deep eutectic solvent and pure ethylene glycol for corrosion protection. J. Phys. Chem. B. 2020, 124, 10739-51.
34. Hristova, E.; Mitov, M.; Rashkov, R.; Arnaudova, M.; Popov, A. Sulphide oxidation on electrodeposited Ni-Mo-W catalysts. Bulg. Chem. Commun. 2008, 40, 291-4. Available from: http://www.bcc.bas.bg/bcc_volumes/volume_40_number_3_2008/Volume_40_Number_3_2008_PDF/2826-AC.pdf [Last accessed on 16 Apr 2025]
35. Allahyarzadeh, M.; Aliofkhazraei, M.; Rezvanian, A.; Torabinejad, V.; Sabour, R. A. Ni-W electrodeposited coatings: characterization, properties and applications. Surf. Coat. Technol. 2016, 307, 978-1010.
36. Tasić, G. S.; Lačnjevac, U.; Tasić, M. M.; et al. Influence of electrodeposition parameters of Ni-W on Ni cathode for alkaline water electrolyser. Int. J. Hydrogen. Energy. 2013, 38, 4291-7.
37. Zhang, X.; Qin, J.; Perasinjaroen, T.; et al. Preparation and hardness of pulse electrodeposited Ni-W-diamond composite coatings. Surf. Coat. Technol. 2015, 276, 228-32.
38. Kazimierczak, H.; Eliaz, N. Induced codeposition of tungsten with zinc from aqueous citrate electrolytes. Coatings 2023, 13, 2001.
39. Cao, J.; Zhang, D.; Yue, Y.; et al. Strongly coupled tungsten oxide/carbide heterogeneous hybrid for ultrastable aqueous rocking-chair zinc-ion batteries. Chem. Eng. J. 2021, 426, 131893.
40. Pletcher, D.; Walsh, F. C. Industrial electrochemistry, 2nd ed. Chapman and Hall; 1990. Available from: https://books.google.co.th/books?id=E_u9ARrm37oC [Last accessed on 18 Apr 2025]
41. Sunwang, N.; Wangyao, P.; Boonyongmaneerat, Y. The effects of heat treatments on hardness and wear resistance in Ni-W alloy coatings. Surf. Coat. Technol. 2011, 206, 1096-101.
42. Elias, L.; Chitharanjan, H. A. Electrodeposition of laminar coatings of Ni-W alloy and their corrosion behaviour. Surf. Coat. Technol. 2015, 283, 61-9.
43. Li, B.; Li, G.; Zhang, D.; et al. Unveiling the impact of the polypyrrole coating layer thickness on the electrochemical performances of LiNi0.5Co0.2Mn0.3O2 in Li-ion battery. ChemistrySelect 2019, 4, 6354-60.
44. He, H.; Qin, H.; Wu, J.; et al. Engineering interfacial layers to enable Zn metal anodes for aqueous zinc-ion batteries. Energy. Storage. Mater. 2021, 43, 317-36.
45. You, Y.; Fang, G.; Fan, M.; Guo, J.; Li, Q.; Wan, J. Leveraging novel microwave techniques for tailoring the microstructure of energy storage materials. Microstructures 2024, 4, 2024035.
46. Baek, M.; Kim, J.; Jeong, K.; et al. Naked metallic skin for homo-epitaxial deposition in lithium metal batteries. Nat. Commun. 2023, 14, 1296.
47. Guo, X.; Zhang, Z.; Li, J.; et al. Alleviation of dendrite formation on zinc anodes via electrolyte additives. ACS. Energy. Lett. 2021, 6, 395-403.
48. Ma, L.; Zhi, C. Zn electrode/electrolyte interfaces of Zn batteries: a mini review. Electrochem. Commun. 2021, 122, 106898.
49. Li, T.; Yan, S.; Dong, H.; et al. Engineering hydrophobic protective layers on zinc anodes for enhanced performance in aqueous zinc-ion batteries. J. Energy. Chem. 2024, 97, 1-11.
50. Deng, S.; Xu, B.; Zhao, J.; Fu, H. Advanced design for anti-freezing aqueous zinc-ion batteries. Energy. Storage. Mater. 2024, 70, 103490.
51. Xu, W.; Zhang, M.; Dong, Y.; Zhao, J. Two-dimensional materials for dendrite-free zinc metal anodes in aqueous zinc batteries. Batteries 2022, 8, 293.
52. Cao, J.; Wu, H.; Zhang, D.; et al. In-situ ultrafast construction of zinc tungstate interface layer for highly reversible zinc anodes. Angew. Chem. Int. Ed. 2024, 63, e202319661.
53. Zuo, Y.; Wang, K.; Pei, P.; et al. Zinc dendrite growth and inhibition strategies. Mater. Today. Energy. 2021, 20, 100692.
54. Song, Z.; Yang, C.; Kiatwisarnkij, N.; et al. Polyethylene glycol-protected zinc microwall arrays for stable zinc anodes. ACS. Appl. Mater. Interfaces. 2024, 16, 64834-45.
55. Zhang, H.; Li, F.; Li, Z.; Gao, L.; Xu, B.; Wang, C. Surface modification induces oriented Zn(002) deposition for highly stable zinc anode. Batteries 2024, 10, 178.
56. Yang, C.; Woottapanit, P.; Geng, S.; et al. Highly reversible Zn anode design through oriented ZnO(002) facets. Adv. Mater. 2024, 36, e2408908.
57. Lim, W. G.; Li, X.; Reed, D. Understanding the role of zinc hydroxide sulfate and its analogues in mildly acidic aqueous zinc batteries: a review. Small. Methods. 2024, 8, e2300965.
58. Shang, Y.; Kundu, D. Understanding and performance of the zinc anode cycling in aqueous zinc-ion batteries and a roadmap for the future. Batteries. Supercaps. 2022, 5, e202100394.
Cite This Article

How to Cite
Download Citation
Export Citation File:
Type of Import
Tips on Downloading Citation
Citation Manager File Format
Type of Import
Direct Import: When the Direct Import option is selected (the default state), a dialogue box will give you the option to Save or Open the downloaded citation data. Choosing Open will either launch your citation manager or give you a choice of applications with which to use the metadata. The Save option saves the file locally for later use.
Indirect Import: When the Indirect Import option is selected, the metadata is displayed and may be copied and pasted as needed.
About This Article
Special Issue
Copyright
Data & Comments
Data
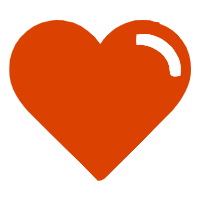
Comments
Comments must be written in English. Spam, offensive content, impersonation, and private information will not be permitted. If any comment is reported and identified as inappropriate content by OAE staff, the comment will be removed without notice. If you have any queries or need any help, please contact us at [email protected].