Recent advances in electrocatalysts for anion exchange membrane water electrolysis: design strategies and characterization approaches
Abstract
With the growing demand for sustainable energy, hydrogen is recognized as a key clean energy carrier that can stabilize renewable sources such as solar and wind. Traditional hydrogen production primarily relies on grey hydrogen from fossil fuels, which produces significant CO2 emissions. In contrast, anion exchange membrane water electrolysis (AEMWE) offers a promising pathway to green hydrogen, combining the zero-gap design of proton exchange membrane water electrolysis with the alkaline environment of alkaline water electrolysis. This configuration allows AEMWE to operate with lower KOH concentrations, enhancing safety and enabling
Keywords
INTRODUCTION
With the rising global energy demand, environmental issues have emerged due to the overuse of fossil fuels and the associated gas emissions[1-8]. To tackle these energy problems, a variety of alternative energy sources, including solar[9-13], wind[14-16], and hydropower[17-19], are being explored. However, they encounter obstacles including lower energy density than fossil fuels, and stability and reliability issues due to their reliance on weather conditions[20]. Hydrogen, capable of functioning as a fuel, offers a viable solution as an energy carrier for fluctuating renewable sources, thanks to its sustainability, non-toxic properties, high energy density, and ease of storage[21-27]. Nevertheless, most industrial hydrogen production currently relies on grey hydrogen, which results in significant CO2 emissions due to the steam methane reforming process[28-31]. To produce green hydrogen, water electrolysis technology has been advanced in conjunction with renewable energy sources, providing the potential for net zero-carbon emissions[32-34].
Utilizing water electrolysis with intermittent power from renewable energy sources offers an effective pathway for producing green hydrogen on a large scale[35-37]. Low-temperature water electrolysis technologies are categorized based on the electrolyte type of the electrolyzer, including alkaline water electrolysis (AWE) and proton exchange membrane water electrolysis (PEMWE). AWE presents several benefits over PEMWE, including the use of affordable, non-precious metal catalysts that exhibit long-term durability and excellent electrochemical efficiency in an alkaline environment, along with minimized corrosion concerns[38-40]. Owing to these benefits, AWE has recently gained recognition as a promising water electrolysis system, leading to substantial efforts in research and development within this field[41-43].
Anion exchange membrane water electrolysis (AEMWE) is a cutting-edge system that merges the zero-gap configuration of PEMWE with the alkaline conditions employed in AWE, providing both high efficiency and affordability[44-46]. The AEMWE provides a safety benefit by operating with 1 M or lower KOH concentrations, in contrast to traditional AWEs, which demand more severe and corrosive conditions with higher KOH concentrations[47]. Also, the polymer-based anion exchange membrane (AEM) in the AEMWE, which acts as both a separator and an ion conductor, is easier to manage and less hazardous than
Figure 1. Schematic diagram of electrolyte category, in situ analysis, and electrode design for AEMWE. Reproduced with permission from[58]. Copyright 2023 John Wiley & Sons. AEMWE: Anion exchange membrane water electrolysis.
FUNDAMENTAL PRINCIPLE FOR AEMWE
AEM water electrolyzer mechanism and structure
AEMWE, as a promising technological approach, combines features of AWE and PEMWE. It utilizes anion-exchange membranes as solid electrolytes, with closely integrated membrane electrode assemblies (MEA), allowing the use of cost-effective, non-precious metal catalysts. Additionally, AEMs provide outstanding gas impermeability and minimize gas crossover, achieving hydrogen purity levels as high as 99.99%, which is crucial for the performance of electrolyzers[59,60]. As depicted in Figure 2A[59], the fundamental operation of a single water electrolyzer cell, but in real applications, a system consists of multiple cells assembled into a stack[61,62]. A separator is employed to maintain a gap between the anode and cathode within a water electrolyzer, avoiding the crossover of H2 and O2 gases. Consequently, the AEMWE system is quite similar to conventional AWE. The main distinction between AWE and AEMWE is the replacement of traditional diaphragms with an AEM. Furthermore, the AEMWE provides multiple benefits, including the use of low-cost transition metal catalysts in place of high-cost precious metals, and the ability to operate with deionized (DI) water or low-concentration alkaline solutions rather than highly concentrated ones[63].
Figure 2. (A) Schematic illustration showing the operating principle of AEMWE[59]. Copyright 2024 American Chemical Society; (B) Photograph of the assembled AEM water electrolyzer[64]. Copyright 2020 Elsevier; (C) HER and OER mechanism under acidic and alkaline environments[72]. Copyright 2023 Elsevier; (D) Cross-sectional schematic of an AEM pure water electrolysis system[82]. Copyright 2019 American Chemical Society; (E) Schematic and (F) photograph of the AEM seawater electrolyzer device[90]. Copyright 2024 The American Association for the Advancement of Science. AEMWE: Anion exchange membrane water electrolysis; AEM: anion exchange membrane; HER:hydrogen evolution reaction; OER: oxygen evolution reaction.
As illustrated in Figure 2B[64], the typical components of an AEM water electrolyzer include current collectors at the cathode and anode materials such as a gas diffusion layer (GDL), an AEM serving as the separator, bipolar plates, and end plates[65,66]. At the cathode, the HER takes place, producing H2 and OH- from the H2O reduction. Meanwhile, at the anode, the OER occurs, resulting in the formation of O2 and
In the context of water electrolysis, the main bottleneck for efficient water splitting is the slow kinetics of the OER, requiring substantial efforts to address this challenge[67-69]. Apart from the slow kinetics of the OER or HER, along with issues with increased overpotential and stability, AEM needs to exhibit excellent ion conductivity to support the creation of exceptionally effective electrocatalysts[70,71].
HER and OER mechanism
Water electrolysis consists of two half-reactions, HER and OER, both of which are influenced by the surface behavior of the electrocatalyst. The intermediates formed during these reactions depend on the pH of electrolytes [Figure 2C][72].
The cathodic HER follows several steps, primarily proceeding through two main reaction routes: the Volmer-Tafel and Volmer-Heyrovsky mechanisms[73]. Initially, the Volmer step leads to generating adsorbed hydrogen atoms (Had). The generated Had can either react with an H+/H2O and an electron to produce an H2 molecule, known as the Heyrovsky step, or combine with a neighboring atom to form H2, referred to as the Tafel step, based on the surface coverage of Had. In acidic environments, H+ ions serve as the charge carriers, moving from the anode to the cathode, and the adsorption energy of the H atom on the surface of the catalyst is a key factor influencing catalytic performance. On the other hand, in alkaline conditions, OH- ions act as charge carriers, and because additional energy is needed for H2O splitting, alkaline HER experiences greater overpotentials due to higher energy barriers relative to acidic HER[74]. Thus, optimizing alkaline HER electrocatalysts requires focusing on key factors, including H atom adsorption, H2O dissociation, and desorption of OH- ions[75].
The anodic OER involves a four-proton-coupled electron transfer, which acts as the main limiting factor in water electrolysis due to its higher energy barrier than the HER. The commonly accepted OER mechanisms are the adsorbate evolution mechanism and the lattice oxygen-mediated mechanism (LOM)[76]. The adsorbate evolution mechanism is a traditional OER mechanism, proposing that O2 is produced from adsorbed H2O, whereas the LOM posits that O2 originates from both the lattice oxygen in the catalyst and adsorbed H2O[77]. According to an adsorbate evolution mechanism, in a basic environment, OH- radical, or in acidic conditions, the H2O molecule, initially adsorbs onto the metal active sites (M), creating M-OH. This intermediate then undergoes deprotonation, resulting in the formation of M-O. Subsequently, there are two primary pathways for generating O2. In the first pathway, H2O molecules or OH- ions adsorb onto M-O, leading to product M-OOH, which subsequently experiences a deprotonation to release O2. In the second pathway, two M-O species combine directly to produce O2. Unlike the AEM mechanism, the last step in the LOM involves the direct coupling of O-O free radicals without the formation of M-OOH. Thus, the LOM mechanism has the potential to overcome the constraints imposed by adsorption-energy scaling relationships.
Pure water and seawater electrolysis
AEMWE has garnered significant interest as an emerging technology, using a considerably lower concentration of KOH as the electrolyte compared to traditional AWE, while still attaining a substantially higher current density[78-80]. However, challenges persist, such as the formation of K2CO3 due to the reaction between KOH and CO2 from the air, which diminishes electrolyzer performance, along with the issue of waste electrolyte management[81]. Lately, the implementation of pure water as an electrolyte has been proposed to resolve these challenges in an eco-friendly way, without sacrificing stability [Figure 2D][82]. From a cost-efficiency perspective, using pure water, which is about 30 times less expensive than an alkaline solution, has demonstrated greater economic advantages over alkaline-based options[78]. Moreover, selecting DI water enables a more straightforward system design and eases maintenance, resulting in lower operational expenses. In addition, the lack of corrosive electrolytes reduces the requirement for specialized equipment, enhancing water management and electrolyte handling. Despite these advantages, some difficulties remain in pure water-based AEMWE, such as limited ionic conductivity, degradation of the triple phase boundary, impurities in the water, and the need for high overpotential[83-85]. Therefore, addressing these challenges will require innovative material design and optimization of electrode configurations to enhance performance and maintain the long-term stability of pure water-based AEMWE systems.
With freshwater resources becoming increasingly limited, the ocean offers a virtually endless supply, and the hydrogen energy it holds is of significant importance to humanity[86]. Utilizing variable renewable energy for hydrogen production via seawater electrolysis can effectively make use of surplus electricity during times of reduced demand[87-89]. This approach also offers benefits such as straightforward and economical equipment, along with environmentally friendly and efficient production, highlighting its potential for large-scale practical applications [Figure 2E and F][90]. Furthermore, hydrogen produced from seawater electrolysis can serve as a fuel to generate high-purity freshwater, representing an eco-friendly technology that integrates hydrogen production with seawater desalination.
However, in seawater electrolysis, alongside HER and OER, there is competition between the OER and the chlorine evolution reaction (ClER). In mild alkaline seawater electrolytes, the ClER, which produces hypochlorite through a two-electron process, is more thermodynamically favorable than the OER via a
To summarize, KOH-based electrolytes face two major limitations: the formation of K2CO3 due to interaction between KOH and CO2 in the air and high waste electrolyte management costs. To address these challenges, pure water, and seawater electrolytes have been proposed alternatives. Pure water electrolytes are approximately 30 times cheaper than KOH and less corrosive, simplifying equipment design and maintenance. However, their low ionic conductivity and high overpotential remain significant challenges, requiring innovative electrode and material designs. Seawater electrolytes offer a sustainable solution by integrating hydrogen production and desalination using an abundant resource. While economically advantageous and compatible with simple equipment, issues such as ClER and catalyst degradation hinder commercialization. Optimizing catalysts and electrode structures to enhance selective oxygen intermediate adsorption is critical to overcoming these barriers. In conclusion, novel strategies to optimize the benefits and address the limitations of both pure water and seawater electrolytes will be key to the sustainable development and commercialization of AEMWE.
IN SITU CHARACTERIZATION
In situ characterization entails the real-time observation and examination of materials or systems under conditions that closely replicate actual reaction environments. This characterization enables direct monitoring and analysis of modifications in materials properties, including morphology, structure, and chemical composition, without extracting the materials from their original environment or changing the conditions[93]. Furthermore, combining multiple in situ characterization techniques, each with a distinct focus, is often valued for gaining a comprehensive understanding of the mechanisms in complex electrocatalysts.
In situ FTIR
FTIR employs infrared (IR) light to induce molecular vibration, allowing for the identification of chemical compounds based on their distinctive IR absorption characteristics [Figure 3A][94]. In the context of electrochemical studies, in situ FTIR can be utilized to detect the presence of species within solutions, and those adsorbed onto electrode surfaces. The IR absorption depends on fluctuations in the dipole moment resulting from molecular vibrations or rotations within the solution. In contrast, on electrode surfaces, the examination of adsorbed species is directed by surface selection rules, focusing on their configuration, bonding, and orientation. The two principal techniques employed in situ FTIR are thin layer mode and attenuated total reflection (ATR) mode. Thin layer mode is straightforward to design and operate, yet it offers lower sensitivity in comparison to ATR mode[95]. On the other hand, the ATR mode, which is more intricate and necessitates meticulous optical adjustment, can mitigate interference from the bulk solution, yielding more discernible spectra with superior signal-to-noise ratios[96].
Figure 3. Schematic configurations for commonly employed in situ techniques in electrochemical reactions. (A) in situ FTIR[94]. Copyright 2022 Springer Nature; (B) in situ Raman spectroscopy[99]. Copyright 2021 Springer Nature; (C) in situ SERS[104]. Copyright 2020 American Chemical Society; (D) in situ XRD[93]. Copyright 2024 American Chemical Society; (E) in situ XAS[115]. Copyright 2019 Elsevier. FTIR: Fourier-transform infrared spectroscopy; SERS: surface-enhanced Raman spectroscopy; XRD: X-ray diffraction; XAS: X-ray absorption spectroscopy.
In situ FTIR is an effective tool for gaining insights into the overall chemical properties of a sample, which can assist in the examination of catalyst structure. The selection of appropriate measurement techniques can facilitate the identification of details about the chemical composition, phase variations, and intermediates involved in electrochemical reactions, thereby enhancing the understanding of how catalyst structure relates to its performance[97].
In situ Raman & surface-enhanced Raman spectroscopy
Raman spectroscopy is a tool used to examine molecular vibrations, rotations, and other low-frequency modes within a sample[98]. In situ Raman spectroscopy allows for the concurrent observation of molecular transformations and electrochemical reactions, providing a crucial understanding of reaction mechanisms, kinetics, and the intermediates present on electrodes and electrolytes [Figure 3B][99]. Traditional in situ Raman spectroscopy can detect alterations in the bulk phase of catalysts or structural modifications, offering comprehensive insights into the catalyst’s crystalline structure, defects, and chemical bonding[100-102].
In situ Surface-Enhanced Raman Spectroscopy (SERS) is a strategy employed to detect species on catalyst surfaces by incorporating unique and specialized nanostructures, such as Ag, Au, and Cu nanoparticles (NPs)[103]. These nanostructures greatly amplify Raman signals, allowing for the detection of even minute quantities of surface species [Figure 3C][104]. The exceptional sensitivity and spatial resolution of SERS render it a powerful tool for exploring chemical reactions and intermediates on catalyst surfaces.
However, in situ Raman analysis faces challenges related to signal intensity, detection of specific species, and interference from background signals arising from solvents and electrolytes. The naturally weak Raman signals and complex chemical surroundings can impede the identification of target species, particularly at low concentrations or with faint spectral features. Moreover, ensuring device stability during dynamic electrochemical reactions and achieving high temporal resolution to capture rapid molecular changes require advanced instrumentation and data collection techniques[105,106].
In situ XRD
XRD is a powerful method for acquiring crystallographic details, including lattice parameters and phase composition[107]. In the field of electrocatalysis, in situ XRD provides significant benefits by allowing
Nevertheless, a drawback of in situ XRD is its lower sensitivity to nanostructured catalysts, especially when particle sizes are below around 5 nm. This issue stems from diffraction limitations linked to small crystallite sizes, which can impede the detailed structural characterization of these materials. Additionally, in situ XRD faces difficulties in resolving local structural characteristics because of its relatively limited spatial resolution[108,109].
In situ XAS
XAS is based on the concept that atoms absorb X-rays at energy levels that are characteristic of the specific element and its chemical surroundings[110]. The examination of metals typically involves the use of hard
In situ XAS enhances this functionality by allowing real-time tracking of structural and chemical modifications on catalyst surfaces under actual working electrochemical conditions [Figure 3E][115]. In situ XAS offers a more precise understanding of catalyst behavior during operational conditions, capturing dynamic modifications that static analyses might overlook. Furthermore, in situ EXAFS is particularly sensitive to alterations in the local coordination environment of metals, overcoming the limitation of XRD, which has difficulty detecting nanosized materials smaller than 5 nm[93].
However, it might not possess adequate sensitivity to identify slight variations across various chemical environments. Moreover, in situ XAS presents challenges, as the electrochemical cell must be precisely engineered to ensure a consistent condition while permitting X-ray penetration. Besides, the temporal resolution of in situ XAS is relatively limited, making it challenging to accurately observe and investigate reaction systems with fast kinetics or swiftly changing transient intermediates[116,117].
Overall, in situ analysis is a powerful tool for elucidating the chemical properties of reaction intermediates occurring on catalyst and electrode surfaces in the AEMWE reaction environment, along with the structural and chemical changes of the catalyst and electrode itself. Techniques such as in situ FTIR and Raman are effective tools for analyzing reaction intermediates, while in situ XRD and XAS are useful for monitoring structural changes. These insights enable a more precise understanding of electrocatalytic mechanisms in AEMWE. However, the high cost of specialized equipment, complex operation requirements, and challenging data processes limit its feasibility for large-scale applications. Therefore, addressing these challenges will require significant efforts in developing cost-effective techniques, simplifying operational setups, and advancing data processing methods.
ELECTROCATALYSTS FOR AEMWE
Constructing HER and OER electrocatalysts that feature low overpotential, robust durability, and
HER electrocatalyst for cathode
Precious metals
Precious metals, including Pt, Pd, Ru, Ir, and Rh, exhibit excellent electrocatalytic performance for HER. Nonetheless, the commercial usage of these precious metal-based electrocatalysts is limited by their rarity and high expense. To address this issue, the strategic development of electrocatalysts with reduced metal content and optimized metal utilization is crucial. For example, Hong et al.[118] synthesized Heusler-type PtRuP2 double-walled nanotube (c-PRP DWNT/C) HER catalysts using consecutive anion and dual cation exchange processes, chemical etching, and pyrolysis following attachment to carbon black [Figure 4A]. The resulting c-PRP DWNT/C-based AEM water electrolyzer demonstrated an impressive current density of
Figure 4. Precious metal-based electrocatalysts for HER in AEMWE. (A) Schematic illustration of the synthesis process of c-PRP DWNT/C; (B) in situ Ru K-edge XANES spectra and (C) in situ Pt L-edge XANES spectra for c-PRP DWNT/C[118]. Copyright 2024 John Wiley & Sons; (D) Schematic representation of the fabrication steps for Pt@S-NiFe LDH; (E) Digital images showcasing hydrogen release behavior[119]. Copyright 2023 John Wiley & Sons; (F) Polarization curves of AEM water electrolyzer using Ru SAs/WCx; (G) Durability cell voltage-time plots for the AEMWE based on Ru SAs/WCx[121]. Copyright 2024 American Chemical Society. AEMWE: Anion exchange membrane water electrolysis; XANES: X-ray absorption near-edge structure; AEM: anion exchange membrane; c-PRP DWNT/C: Heusler-type PtRuP2 double-walled nanotube; Pt@S-NiFe LDH: Pt quantum dots on sulfur-doped NiFe layered double hydroxide; Ru SAs/WCx: Ru SA catalyst anchored on tungsten carbide; SA: single-atom.
Ru has garnered significant interest as a more affordable alternative to Pt, exhibiting comparable energy barriers for water splitting and hydrogen binding strengths. For instance, Wang et al.[120] designed an innovative Ru-based hybrid HER catalyst, featuring atomically layered Ru nanoclusters with adjacent Ru single atomic sites anchored onto a Ni hydr(oxy)oxide substrate (NS-Ru@NiHO/Ni5P4), synthesized via electrochemical deposition method. Theoretical studies demonstrated that the H2O molecules preferentially dissociate at the single-atom (SA) Ru sites, followed by *H adsorption facilitated by bridging Ru-H activation in Ru nanoclusters, which enhances the kinetics of the Volmer-Heyrovsky HER mechanism. As a result, the assembled AEM water electrolyzer exhibited a current density of 1.0 A cm-2 at a low cell voltage of 1.7 V. Lin et al.[121] presented a Ru SA catalyst anchored on tungsten carbide (Ru SAs/WCx) for HER, fabricated via dopamine-assisted molecular assembly followed by pyrolysis. They proposed that the SA Ru sites exhibit a puncture effect that effectively mitigates OH- blockages, significantly enhancing the HER performance in alkaline conditions. Moreover, density functional theory (DFT) calculations indicated that the isolated Ru atoms reduce the local OH- binding energy, thereby alleviating OH- blockages and forming dual-functional interfaces involving Ru atoms and the support, which facilitates H2O dissociation. As a result, the AEM water electrolyzer incorporating Ru SAs/WCx revealed a current density of 1.0 A cm-2 at a cell voltage of just 1.79 V, as evidenced by Figure 4F. Furthermore, the electrolyzer exhibited remarkable stability, operating for 190 h at 1.0 A cm-2 with minimal performance degradation [Figure 4G]. Yao et al.[122] introduced a Ni SA-modified Ru NP catalyst with a defective carbon bridging structure (UP-RuNiSAs/C) synthesized via a unique unipolar pulse electrodeposition (UPED) technique. Unlike traditional continuous potentiostatic deposition, the UPED method minimizes concentration polarization, enabling precise control over the deposition of Ni SA onto defect-rich carbon through periodic pulses. Theoretical calculations indicated that incorporating NiSAs into the Ru nanocrystalline framework substantially lowers the adsorption energy of OHad on Ru. Additionally, the carbon bridge effect of defective carbon facilitates OH- charge redistribution between Ni and Ru, further reducing OHad adsorption on Ru. The optimized AEM electrolyzer using the UP-RuNiSAs/C catalyst achieved a cell voltage of just 1.95 V at a current density of
Os, the densest and most affordable metal in the Pt group, possesses a similar electronic structure to Pt but is seldom utilized in water electrolysis due to its poor proton adsorption ability. However, its limited catalytic performance can be improved by further adjustments to its electronic structure. For example, Li et al.[123] reported a phosphorus-doped Os (P-Os) catalyst for alkaline HER using a rapid 20 s microwave plasma technique. Both theoretical calculations and experimental data confirmed that the modulation of the electronic structure at the Os sites, facilitated by p-d orbital hybridization between P and Os, enhances H2O dissociation and optimizes hydrogen intermediate adsorption/desorption, thereby improving catalytic performance. Therefore, an AEM electrolyzer with the optimized P-Os cathode attained current densities of 500 and 1000 mA cm-2 at 1.86 and 2.02 V, respectively, and operated continuously at 500 mA cm-2 for over 100 h, indicating its potential for industrial applications.
Non-precious metals
Transition metals possessing a d-electronic configuration, particularly Ni, Co, and Fe, are commonly investigated as HER electrocatalysts due to their promising catalytic characteristics. In particular, alloying or doping Ni with additional elements seeks to modify its electronic structure, thereby enhancing its catalytic performance for HER. For instance, Li et al.[124] developed a freestanding binder-free hierarchical electrode using a simple in situ approach, where Ni NPs were encapsulated within N-doped carbonized wood (Ni@NCW) [Figure 5A]. The carbonized wood, with an ordered hierarchical 3D porous structure, serves as an ideal carbon matrix for catalyst nucleation and active component loading, promoting efficient mass diffusion. The incorporation of N-doped carbon nanotubes in the carbonized wood further facilitates electron transfer within the electrode and enhances the durability of the active metal components. Owing to these advantageous properties, an AEM water electrolyzer utilizing the freestanding Ni@NCW electrode operated at a lower cell voltage of 2.43 V to reach an industrial-scale current of 4.0 A, maintaining remarkable stability at 4.0 A for 18 h [Figure 5B and C]. Lee et al.[125] designed Ni-Mo catalysts (Ni3Mo) as the cathode for an AEM water electrolyzer through a co-precipitation method to form hydroxides, followed by pyrolysis under H2 flow. Notably, after applying a mild activation process by maintaining a current density of 50 mA cm-2 for 6 h, the cell demonstrated its best performance, achieving 1.82 V at 1 A cm-2, surpassing the performance of the 40 wt% Pt/C catalyst. It was observed that a considerable amount of Mo dissolved from the cathode and migrated to other parts of the cell. As depicted in Figure 5D, DFT calculations revealed that Mo dissolution occurs from the surface of Ni3Mo, but the redeposition of MoO3 onto the surface is thermodynamically favored. The dissolution of Mo enhances water dissociation on the Ni3Mo surface, while the adsorbed MoO3 species reduce hydrogen adsorption, thereby improving the HER activity. Chen et al.[126] synthesized a hierarchical composite electrocatalyst consisting of heterogeneous
Figure 5. Transition metal-based electrocatalysts for HER in AEMWE. (A) Schematic showing the fabrication process of Ni@NCW; (B) Chronopotentiometric curves for Ni@NCW under multiple potentials; (C) Chronopotentiometric curve at 4.0 A and the digital image of AEM water electrolyzer utilizing Ni@NCW[124]. Copyright 2023 John Wiley & Sons; (D) Schematic depicting the HER process on
Apart from Ni-based electrocatalysts, other transition metal-based catalysts show great potential as
OER electrocatalyst for anode
Precious metals
Precious metals and metal oxides have been regarded as highly effective electrode materials for OER, with RuO2 and IrO2 often seen as the benchmark electrocatalysts for OER. However, because of the high costs and dissolution issues associated with these materials, various modification strategies have been suggested to enhance electrocatalyst activity and stability while reducing expenses. For example, Du et al.[58] designed hollow Co-based N-doped porous carbon spheres decorated with ultrafine Ru nanoclusters (HS-RuCo/NC) as effective OER catalysts by pyrolyzing bimetallic zeolite imidazolate frameworks loaded with Ru (III) ions [Figure 6A]. Both theoretical and experimental investigation indicated that the synergistic interaction between the in situ-formed RuO2 coupled with Co3O4 helped optimize the electronic structure of the
Figure 6. Precious metal-based electrocatalysts for OER in AEMWE. (A) Scheme of the fabrication procedure for Ru-O/N-C-NH3[58]. Copyright 2023 John Wiley & Sons; (B) Schematic illustrating the structure and corrosion-resistant approach of RuMoNi electrocatalyst; (C) Polarization curves of the AEM water electrolyzer with RuMoNi in 1.0 M KOH + seawater at 20 °C and 6.0 M KOH + seawater at 60 °C; (D) Long-term stability test of the AEM water electrolyzer using RuMoNi at 500 mA cm-2 in a 1.0 M KOH + seawater electrolyte; (E) Performance comparison of the RuMoNi-catalyzed electrolyzer with other reported AEM seawater electrolyzers[130]. Copyright 2023 Springer Nature; Durability tests for Co3-xPdxO4 catalysts on MnO2-coated Ni foam substrates at (F) 200 mA cm-2 and (G) 1 A cm-2 in natural seawater electrolyte[131]. Copyright 2023 John Wiley & Sons. AEMWE: Anion exchange membrane water electrolysis; OER: oxygen evolution reaction; AEM: anion exchange membrane.
In addition to Ru, theoretical calculations indicate that Pd exhibits excellent capabilities for H2O adsorption and dissociation, which can contribute to improved OER catalytic performance. For instance, Wang et al.[131] introduced a proton-adsorption-enhancing approach for synthesizing palladium-doped cobalt oxide
Non-precious metals
Ni-based oxides, among transition metal-based OER catalysts, have shown superior OER performance due to their high-water oxidation potential, surpassing other catalysts. For example, Park et al.[132] constructed a three-dimensional unified electrode by electrodepositing nickel-iron oxyhydroxide (NiFeOOH) directly onto a GDL to serve as the anode in an AEM water electrolyzer [Figure 7A]. Unlike traditional electrodes, which are typically composed of separate catalysts and GDL, this single-component integrated electrode enhanced the electrical connectivity between the catalyst and GDL, resulting in improved performance and stability. As shown in Figure 7B, the unified AEM water electrolyzer revealed exceptional current density, achieving 3.6 A cm-2 at 1.9 V. Even with a non-noble metal catalyst, the performance of this unified AEMWE was twice as high as that of a conventional AEM water electrolyzer with a noble metal catalyst. Moreover, even with AEM degradation, the unified AEM water electrolyzer demonstrated stable performance, maintaining a current density of 500 mA cm-2 for 100 h and 3000 mA cm-2 for 24 h. Thangavel et al.[133] designed highly efficient OER catalysts by anchoring Ni3N particles onto an electrochemically reconstructed amorphous oxy-hydroxides surface, leading to V-NiFe(OOH)/Ni3N structures. This distinctive amorphous-crystalline interface, abundant in active sites, significantly improved electron transport and accelerated OER kinetics at the electrode-electrolyte interface. As seen in Figure 7C, to pinpoint the actual active sites and intermediates of the V-NiFe(OOH)/Ni3N catalysts, in situ Raman spectroscopy measurements were carried out. The in situ Raman analysis revealed a substantial increase in peak intensity after 1.35 V, which was associated with the formation of FeOOH from Fe2O3 reconstruction, acting as the true catalytic phase during OER. Additionally, the elevating intensity of NiOOH peaks at higher overpotentials revealed the continuous formation of NiOOH during OER, suggesting that the catalyst was both chemically stable and electrically conductive. This structural synergy contributed to the enhanced activity of the V-NiFeOOH/Ni3N catalyst. As a result, the AEM water electrolyzer using the
Figure 7. Ni-based electrocatalysts for OER in AEMWE. (A) Schematic illustration of the conventional electrode and unified electrode; (B) Polarization curves of AEM water electrolyzer based on the unified electrode[132]. Copyright 2022 American Chemical Society; (C) in situ Raman spectra of V-NiFeOOH/Ni3N catalysts in 1 M KOH; (D) Schematic illustration of AEM ultrapure water electrolyzer setup; (E) Polarization curves of AEM water electrolyzer using V-NiFeOOH/Ni3N catalysts in ultrapure water-electrolyte[133], Copyright 2022 John Wiley & Sons; (F) Scheme of creating nanofoam-like NiFeM catalysts; Multiple polarization curves of NiFeM catalysts in (G) 0.1 M KOH and (H) pure DI water[134]. Copyright 2024 John Wiley & Sons. AEMWE: Anion exchange membrane water electrolysis; OER: oxygen evolution reaction; AEM: anion exchange membrane.
Aside from Ni, other transition metals, including Co, Fe, Cu, and Cu, could also enhance OER performance. For instance, Zhao et al.[135] utilized a high-entropy Co and Mo co-doped NiFe hydroxide (Co, Mo-NiFe LDH) as a precursor, leveraging the in situ leaching of Mo atoms during OER operation to create Co-doped NiFe oxyhydroxide (Co, VM-NiFe OOH) with coexisting cation vacancies. The reconfiguration process from Co, Mo-NiFe LDH to Co, VM-NiFe OOH was monitored using in situ electrochemical spectroscopy. In situ Raman spectroscopy showed that Co doping reduced the energetic barrier for oxidation, while the vacancies formed by Mo leaching generated more high-valence active species, enhancing OER performance
Figure 8. Other transition metal-based electrocatalysts for OER in AEMWE. (A-C) Time-resolved in situ Raman spectra of catalysts in 1.0 M KOH[135]. Copyright 2023 John Wiley & Sons; (D) Schematic diagram showing the fabrication process of the chemically etched CuCoO4 catalyst[63]. Copyright 2020 Elsevier; In situ Co K-edge XAS spectra of Co@MXene at 1 mA cm-2 and 10 mA cm-2 in (E) XANES and (F) FT-EXAFS[138]. Copyright 2024 Elsevier; (G) Polarization curves, (H) Chronopotentiometric curves, and energetic efficiency of AEM water electrolyzer based on Co4Fe3@N-doped graphitic carbon catalyst[139]. Copyright 2024 American Chemical Society. AEMWE: Anion exchange membrane water electrolysis; OER: oxygen evolution reaction; XAS: X-ray absorption spectroscopy; XANES: X-ray absorption near-edge structure; FT-EXAFS: Fourier-transformation extended X-ray absorption fine structure; AEM: anion exchange membrane.
Bifunctional electrocatalyst for both cathode and anode
Bifunctional electrocatalysts are crucial for efficient water electrolysis, as they catalyze both HER and OER simultaneously, reducing energy losses and improving overall efficiency for sustainable hydrogen production. Additionally, bifunctional electrocatalysts are essential for creating a cost-effective, compact, and efficient water electrolyzer, streamlining design by eliminating the need for separate catalysts and ensuring balanced performance[140]. Thus, numerous bifunctional catalyst materials were carefully developed and constructed to fulfill the specific and challenging requirements of AEMWE.
For example, Tran et al.[141] proposed a tunable engineering strategy to modify the structure of Ni layered double hydroxide (LDH) through an in situ doping method involving dual transition metals, Mn and Fe, followed by partial substitution or surface adsorption with atomic Pt, resulting in the development of the PtSA-Mn,Fe-Ni LDH bifunctional electrocatalyst [Figure 9A]. The incorporation of Pt SAs, combined with the co-doping of transition metal moieties into the Ni LDH framework, resulted in a synergistic interaction that enhanced electrochemical performance by increasing the number of electroactive sites and improving structural stability. To gain deeper insights into the origin and factors contributing to its remarkable HER and OER activity and stability, in situ Raman spectroscopy was employed. As revealed in Figure 9B, the in situ Raman spectra of PtSA-Mn,Fe-Ni LDHs during HER at varying potentials showed a reduction in NiO mode peak intensities as the potential shifted from OCP to the HER range, indicating the reduction of Ni(OH)2 to Ni. Even at a potential more negative than -0.2 V, unreduced Ni(OH)2 was still detected, suggesting its structural stability under H2-evolving conditions. As illustrated in Figure 9C, the in situ Raman spectra of PtSA-Mn,Fe-Ni LDHs during OER showed no significant structural changes up to 1.25 V, but at 1.3 V and above, the intensity of NiOOH-related vibration modes increased, indicating the conversion of Ni(OH)2 to NiOOH as the catalytically active phase, with the appearance of a new Ni-O stretching peak and a broad feature assigned to superoxide species. Utilizing the optimized structure, the AEM water electrolyzer stack with PtSA-Mn,Fe-Ni LDHs as both the anode and cathode achieved a cell voltage of 1.79 V at
Figure 9. Bifunctional electrocatalysts for HER/OER in AEMWE. (A) Scheme of the fabrication processes for PtSA-Mn, Fe-Ni LDHs on NF; In situ Raman spectra of PtSA-Mn, Fe-Ni LDHs for (B) HER and (C) OER processes in an alkaline environment; (D) Long-term stability test of AEM water electrolyzer employing PtSA-Mn, Fe-Ni LDH catalysts for both anode and cathode[141]. Copyright 2024 American Chemical Society; (E) Synthesis illustration of CoN/VN@NF and P-CoVO@NF; (F) Durability test at 1.76 V under 70 °C[144]. Copyright 2024 John Wiley & Sons; (G) Polarization curves of AEM water electrolyzer equipped with bifunctional Ni/NiO@Ru-NC electrocatalyst; (H) Chronopotentiometric curve of AEM water electrolyzer using bifunctional Ni/NiO@Ru-NC electrocatalyst at
Summary of the detailed performance metrics of electrocatalysts for different types of AEMWE
Strategy | Electrocatalysts | Electrolyte | Performance about activity or stability | Ref. |
Precious metal electrocatalysts for HER | c-PRP DWNT/C | 1.0 M KOH | 9.4 A cm-2 at 2.0 V 1.0 A cm-2 for ~270 h | [118] |
Pt@S-NiFe LDH | 1.0 M KOH | 100 mA cm-2 at 1.62 V | [119] | |
NS-Ru@NiHO/Ni5P4 | 1.0 M KOH | 1.0 A cm-2 at 1.7 V | [120] | |
Ru SAs/WCx | M KOH | 1.0 A cm-2 at 1.79 V 1.0 A cm-2 for 190 h | [121] | |
UP-RuNiSAs/C | 1.0 M KOH | 1.0 A cm-2 at 1.95 V 1.0 A cm-2 for 250 h | [122] | |
P-Os | 1.0 M KOH | 500 mA cm-2 at 1.86 V 1.0 A cm-2 at 2.02 V 500 mA cm-2 for 100 h | [123] | |
Non-precious metal electrocatalysts for HER | Ni@NCW | 1.0 M KOH | 4.0 A at 2.43 V 4.0 A for 18 h | [124] |
Ni3Mo | 1.0 M KOH | 1.0 A cm-2 at 1.82 V | [125] | |
NiMoOx@CMK-3 | 1.0 M KOH | 1.0 A cm-2 at 1.965 V 1.0 A cm-2 for 400 h | [126] | |
B, V-Ni2P | 1.0 M KOH | 500 mA cm-2 at 1.78 V 1.0 A cm-2 at 1.92 V | [127] | |
Fe2P-Co2P/NPC | 1.0 M KOH | 1.0 A cm-2 at 1.73 V 1.0 A cm-2 for 1000 h | [128] | |
WS2 superstructure | 1.0 M KOH | 1.0 A cm-2 at 1.70 V 1.0 A cm-2 for 1000 h | [129] | |
Precious metal electrocatalysts for OER | HS-RuCo/NC | 1.0 M KOH | 1.0 A cm-2 at 2.07 V 500 mA cm-2 for 100 h | [58] |
RuMoNi | 1.0 M KOH + seawater | 1.0 A cm-2 at 1.72 V 500 mA cm-2 for 240 h | [130] | |
Co3-xPdxO4 | 1.0 M phosphate buffer solution + natural seawater | 200 mA cm-2 for 450 h 1.0 A cm-2 for 20 h | [131] | |
Non-precious metal electrocatalysts for OER | NiFeOOH | 1.0 M KOH | 3.6 A cm-2 at 1.9 V 500 mA cm-2 for 100 h 3.0 A cm-2 for 24 h | [132] |
V-NiFe(OOH)/Ni3N | 1.0 M KOH | 685 mA cmgeo-2 at 1.85 V 685 mA cmgeo-2 for 500 h | [133] | |
NiFeMn | 0.1 M KOH | 2.0 A cm-2 at 1.7 V | [134] | |
NiFeCu | Pure water | 1.2 A cm-2 at ~ 2.3 V | [134] | |
Co, VM-NiFe OOH | 1.0 M KOH | 2.0 A at 1.94 V 2.0 A for 130 h | [135] | |
CCO | 1.0 M KOH | 1.39 A cm-2 at 1.8 V 500 mA cm-2 for 64 h | [64] | |
CCO* | 1.0 M KOH | 1.4 A cm-2 at 1.85 V 500 mA cm-2 for ~12 h | [136] | |
CoFeCe0.5 | 1.0 M KOH | 2.7 A cm-2 at 1.8 V | [137] | |
Co@Mo2CTx | 1.0 M KOH | 2.11 A cm-2 at 1.8 V 2.11 A cm-2 for ~700 h | [138] | |
Co4Fe3@N-doped graphitic carbon | 1.0 M KOH | 139% higher energy efficiency | [139] | |
Bifunctional electrocatalysts | PtSA-Mn,Fe-Ni LDH | 1.0 M KOH | 500 mA cm-2 at 1.79 V 500 mA cm-2 for 600 h | [141] |
Ru-BOx-OH-300 | 1.0 M KOH + seawater | 500 mA cm-2 at 1.73 V 1.0 A cm-2 at 1.95 V 500 mA cm-2 and 1.0 A cm-2 for 400 h | [142] | |
Fe2P2S6 NCs | 1.0 M KOH | 370 mA cm-2 at 1.8 V 300 mA cm-2 for 24 h | [143] | |
CoVO@NF | 1.0 M KOH | 500 mA cm-2 at 1.76 V 500 mA cm-2 for 1000 h | [144] | |
Ni/NiO@Ru-NC | 1.0 M KOH | 100 mA cm-2 at 1.595 V 500 mA cm-2 for 50 h | [145] |
Overall, the development of electrocatalysts is crucial for advancing AEMWE technology. AEMWE electrodes are broadly classified into HER electrocatalysts for the cathode, OER electrocatalysts for the anode, and bifunctional electrocatalysts for both electrodes. Additionally, electrocatalysts are further categorized based on the type of metal used, distinguishing between precious and non-precious metals. A comprehensive understanding of the relationship between catalyst composition, structure, and activity is imperative to facilitate the rational design of the next-generation electrocatalysts, thereby enabling the widespread implementation of AEMWE technology.
CONCLUSION AND OUTLOOK
Hydrogen, recognized as a sustainable and eco-friendly energy source, is emerging as a leading fuel due to its wide range of applications. Among the various water electrolysis systems, AEMWE is the most recent innovative system, integrating the zero-gap design of PEMWE with the alkaline environments of AWE, resulting in outstanding activity. In this review, the key elements of the AEM water electrolyzer, such as reaction mechanisms for HER and OER, and cell assemblies, have been reviewed. This discussion was complemented by a detailed examination of in situ characterization analyses, including in situ FTIR, Raman spectroscopy, XRD, and XAS. Furthermore, we have highlighted recent advancements in approaches aimed at improving the efficiency of HER, OER, and bifunctional electrocatalysts, emphasizing designs that utilize both precious and abundant transition metals. The aforementioned studies have effectively addressed the limited use of precious metals and the relatively low activity of non-precious metals through diverse nanotechnology, developing high-performance electrocatalysts. These catalysts apply not only to alkaline electrolytes but also to pure water and seawater electrolytes, showing environmentally friendly and commercially viable properties. Moreover, various in situ characterizations provided a deeper understanding of the complex mechanisms of AEMWE.
AEMWE has seen significant progress; however, several challenges still need to be promptly addressed:
Developing non-precious metal catalysts with high electrocatalytic activity and robust durability remains a challenge. Their long-term structural and chemical stability under alkaline conditions remains insufficient, and achieving a low overpotential at current densities exceeding 1 A cm-2 is not yet optimal. Enhancing the activity of electrocatalysts can be facilitated by tailoring morphologies, introducing defects, and optimizing interfaces. Although industrial-level current densities have been achieved for AEMWE, the stability test durations, along with the KOH concentration and operating temperature, still fall short of industrial standards. In this context, regulating the wettability of HER electrocatalysts or electrodes is critical for improving HER stability. Effective surface modification is essential to optimize aerophobicity for hydrogen production and wettability for better reactant adsorption. Furthermore, during the OER process in AEMWE, catalyst dissolution and subsequent irregular redeposition can adversely affect long-term stability. To address this issue, strategies such as interface control between the catalyst layer and the membrane, or the design of stability-focused structures like core-shell catalysts, are proposed to mitigate dissolution and improve AEMWE durability.
In addition to electrocatalysts, there have been recent advancements in ion-conductive membranes for AEMWE, focusing on improving hydroxide conductivity and resistance to alkaline conditions. These improvements have greatly accelerated the development of AEMWE. The recently developed AEMWE technology allows for a reduction in electrolyte concentration and, in certain instances, enables the direct use of pure water as the electrolyte. Researchers have constructed various advanced AEMs using molecular design techniques. However, issues such as limited OH- ions conductivity and insufficient chemical stability continue to pose significant challenges. In summary, for AEMWE to be effective, ion-conductive membranes should possess high OH- ions conductivity, minimal hydrogen permeability, excellent alkaline durability, and robust mechanical strength.
The progress of in situ characterization techniques is essential for investigating electrochemical reactions. However, there are challenges associated with improving in situ characterization. The bubbles produced during water electrolysis frequently disrupt in situ measurements, leading to inaccuracies in data analysis. Furthermore, although DFT calculations offer valuable insights into the adsorption energies of intermediate and potential reaction mechanisms, the simplified material models and reaction conditions employed in these simulations often fail to capture the actual reaction dynamics. To gain a deeper understanding of these complex systems, advanced data analysis techniques driven by artificial intelligence can be utilized. These methods can handle and interpret vast amounts of high-dimensional data, reveal underlying patterns, and develop predictive models. Therefore, combining machine learning with in situ characterizations can enhance the effectiveness and thoroughness of analysis, while also extending the utilization of these methods to more practical and challenging conditions.
DECLARATIONS
Authors’ contributions
Proposed the topic of this review: Kim, S. Y.
Manuscript writing: Kim, J. H.
Data curation: Kim, J. H.; Jo, H. J.; Han, S. M.; Kim, Y. J.
Availability of data and materials
Not applicable.
Financial support and sponsorship
This research was supported by the National Research Foundation (NRF) of Korea (Grant numbers 2022M3H4A1A01012712).
Conflicts of interest
Kim, S. Y. is an Associate Editor of the journal Energy Materials and was not involved in any part of the editorial process, including reviewer selection, manuscript handling, or decision-making. The other authors declare that they have no conflicts of interest.
Ethical approval and consent to participate
Not applicable.
Consent for publication
Not applicable.
Copyright
© The Author(s) 2025.
REFERENCES
1. Zhou, P.; Navid, I. A.; Ma, Y.; et al. Solar-to-hydrogen efficiency of more than 9% in photocatalytic water splitting. Nature 2023, 613, 66-70.
2. Kim, J. H.; Kim, J.; Ma, J.; et al. Spontaneous metal-chelation strategy for highly dense Ni single-atom catalysts with asymmetric coordination in CO2 electroreduction. Small 2025, 21, 2409481.
3. Ma, J.; Ahn, S. H.; Kim, S. Y. Integration of earth-abundant cocatalysts for high-performance photoelectrochemical energy conversion. J. Energy. Chem. 2024, 88, 336-55.
4. Ma, J.; Cho, J. H.; Lee, C.; et al. Unraveling the harmonious coexistence of ruthenium states on a self-standing electrode for enhanced hydrogen evolution reaction. Energy. Environ. Mater. 2024, 7, e12766.
5. Cho, J. H.; Ma, J.; Lee, C.; et al. Crystallographically vacancy-induced MOF nanosheet as rational single-atom support for accelerating CO2 electroreduction to CO. Carbon. Energy. 2024, 6, e510.
6. Lee, J. K.; Seo, J. H.; Lim, J.; Park, S.; Jang, H. W. Best practices in membrane electrode assembly for water electrolysis. ACS. Mater. Lett. 2024, 6, 2757-86.
7. Kim, J. H.; Kang, E. S.; Kim, J. H. Effect of sulfur contents in NiZnS composite photocatalysts on solar water splitting. Korean. J. Met. Mater. 2023, 61, 284-90.
8. So, S. H.; Sung, S. J.; Yang, S. J.; Park, C. R. Where to go for the development of high-performance H2 storage materials at ambient conditions? Electron. Mater. Lett. 2023, 19, 1-18.
9. Han, S.; Dhungel, S. K.; Park, S.; et al. Integration of subcells in III-V//Si tandem solar cells. Trans. Electr. Electron. Mater. 2023, 24, 132-9.
10. Jang, W. J.; Jang, H. W.; Kim, S. Y. Recent advances in wide bandgap perovskite solar cells: focus on lead-free materials for tandem structures. Small. Methods. 2024, 8, 2300207.
11. Cho, J. H.; Ma, J.; Kim, S. Y. Toward high-efficiency photovoltaics-assisted electrochemical and photoelectrochemical CO2 reduction: strategy and challenge. Exploration 2023, 3, 20230001.
12. Massiot, I.; Cattoni, A.; Collin, S. Progress and prospects for ultrathin solar cells. Nat. Energy. 2020, 5, 959-72.
13. Jang, W. J.; Kim, E. H.; Cho, J. H.; Lee, D.; Kim, S. Y. Elucidating the role of alkali metal carbonates in impact on oxygen vacancies for efficient and stable perovskite solar cells. Adv. Sci. 2024, 11, 2406657.
14. Peng, X.; Liu, Z.; Jiang, D. A review of multiphase energy conversion in wind power generation. Renew. Sustain. Energy. Rev. 2021, 147, 111172.
15. Pryor, S. C.; Barthelmie, R. J.; Bukovsky, M. S.; Leung, L. R.; Sakaguchi, K. Climate change impacts on wind power generation. Nat. Rev. Earth. Environ. 2020, 1, 627-43.
16. He, W.; Shan, C.; Fu, S.; et al. Large harvested energy by self-excited liquid suspension triboelectric nanogenerator with optimized charge transportation behavior. Adv. Mater. 2023, 35, 2209657.
17. Stefenon, S. F.; Ribeiro, M. H. D. M.; Nied, A.; et al. Time series forecasting using ensemble learning methods for emergency prevention in hydroelectric power plants with dam. Electric. Power. Syst. Res. 2022, 202, 107584.
18. Bertasini, D.; Battista, F.; Rizzioli, F.; Frison, N.; Bolzonella, D. Decarbonization of the European natural gas grid using hydrogen and methane biologically produced from organic waste: a critical overview. Renew. Energy. 2023, 206, 386-96.
20. Tong, D.; Farnham, D. J.; Duan, L.; et al. Geophysical constraints on the reliability of solar and wind power worldwide. Nat. Commun. 2021, 12, 6146.
21. Jun, S. E.; Lee, J. K.; Jang, H. W. Two-dimensional materials for photoelectrochemical water splitting. Energy. Adv. 2023, 2, 34-53.
22. Fan, L.; Tu, Z.; Chan, S. H. Recent development of hydrogen and fuel cell technologies: a review. Energy. Rep. 2021, 7, 8421-46.
23. Jun S, Choi S, Kim J, Kwon KC, Park SH, Jang HW. Non-noble metal single atom catalysts for electrochemical energy conversion reactions. Chin. J. Catal. 2023, 50, 195-214.
24. Krevor, S.; de, C. H.; Gasda, S. E.; et al. Subsurface carbon dioxide and hydrogen storage for a sustainable energy future. Nat. Rev. Earth. Environ. 2023, 4, 102-18.
25. Shang, Y.; Chen, S.; Chen, N.; et al. A universal strategy for high-voltage aqueous batteries via lone pair electrons as the hydrogen bond-breaker. Energy. Environ. Sci. 2022, 15, 2653-63.
26. Allendorf, M. D.; Stavila, V.; Snider, J. L.; et al. Challenges to developing materials for the transport and storage of hydrogen. Nat. Chem. 2022, 14, 1214-23.
27. Jun, S. E.; Kim, Y. H.; Kim, J.; et al. Atomically dispersed iridium catalysts on silicon photoanode for efficient photoelectrochemical water splitting. Nat. Commun. 2023, 14, 609.
28. Guo, J.; Zheng, Y.; Hu, Z.; et al. Direct seawater electrolysis by adjusting the local reaction environment of a catalyst. Nat. Energy. 2023, 8, 264-72.
29. Xie, H.; Zhao, Z.; Liu, T.; et al. A membrane-based seawater electrolyser for hydrogen generation. Nature 2022, 612, 673-8.
30. Teitsworth, T. S.; Hill, D. J.; Litvin, S. R.; et al. Water splitting with silicon p-i-n superlattices suspended in solution. Nature 2023, 614, 270-4.
31. Wan, Y.; Zhou, L.; Lv, R. Rational design of efficient electrocatalysts for hydrogen production by water electrolysis at high current density. Mater. Chem. Front. 2023, 7, 6035-60.
32. Zang, Y.; Lu, D. Q.; Wang, K.; et al. A pyrolysis-free Ni/Fe bimetallic electrocatalyst for overall water splitting. Nat. Commun. 2023, 14, 1792.
33. Wu, R.; Xu, J.; Zhao, C. L.; et al. Dopant triggered atomic configuration activates water splitting to hydrogen. Nat. Commun. 2023, 14, 2306.
34. Lin, G.; Zhang, Z.; Ju, Q.; et al. Bottom-up evolution of perovskite clusters into high-activity rhodium nanoparticles toward alkaline hydrogen evolution. Nat. Commun. 2023, 14, 280.
35. Wang, S.; Lu, A.; Zhong, C. J. Hydrogen production from water electrolysis: role of catalysts. Nano. Converg. 2021, 8, 4.
36. Yang, J.; Jang, M. J.; Zeng, X.; et al. Non-precious electrocatalysts for oxygen evolution reaction in anion exchange membrane water electrolysis: a mini review. Electrochem. Commun. 2021, 131, 107118.
37. Bulakhe, S.; Shinde, N.; Kim, J.; Mane, R. S.; Deokate, R. Recent advances in non-precious Ni-based promising catalysts for water splitting application. Int. J. Energy. Res. 2022, 46, 17829-47.
38. Wan, L.; Xu, Z.; Xu, Q.; et al. Key components and design strategy of the membrane electrode assembly for alkaline water electrolysis. Energy. Environ. Sci. 2023, 16, 1384-430.
39. Vincent, I.; Bessarabov, D. Low cost hydrogen production by anion exchange membrane electrolysis: a review. Renew. Sustain. Energy. Rev. 2018, 81, 1690-704.
40. Hu, X.; Yin, Y.; Liu, W.; Zhang, X.; Zhang, H. Cobalt phosphide nanocage@ferric-zinc mixed-metal phosphide nanotube hierarchical nanocomposites for enhanced overall water splitting. Chin. J. Catal. 2019, 40, 1085-92.
41. Miller, H. A.; Bouzek, K.; Hnat, J.; et al. Green hydrogen from anion exchange membrane water electrolysis: a review of recent developments in critical materials and operating conditions. Sustain. Energy. Fuels. 2020, 4, 2114-33.
42. Abbasi, R.; Setzler, B. P.; Lin, S.; et al. A roadmap to low-cost hydrogen with hydroxide exchange membrane electrolyzers. Adv. Mater. 2019, 31, 1805876.
43. Li, C.; Baek, J. The promise of hydrogen production from alkaline anion exchange membrane electrolyzers. Nano. Energy. 2021, 87, 106162.
44. Du, N.; Roy, C.; Peach, R.; Turnbull, M.; Thiele, S.; Bock, C. Anion-exchange membrane water electrolyzers. Chem. Rev. 2022, 122, 11830-95.
45. Li, Q.; Molina, V. A.; Peltier, C. R.; et al. Anion exchange membrane water electrolysis: the future of green hydrogen. J. Phys. Chem. C. 2023, 127, 7901-12.
46. Santoro, C.; Lavacchi, A.; Mustarelli, P.; et al. What is next in anion-exchange membrane water electrolyzers? ChemSusChem 2022, 15, e202200027.
47. Sulaiman RR, Wong WY, Loh KS. Recent developments on transition metal-based electrocatalysts for application in anion exchange membrane water electrolysis. Int. J. Energy. Res. 2022, 46, 2241-76.
48. Gohil, J. M.; Dutta, K. Structures and properties of polymers in ion exchange membranes for hydrogen generation by water electrolysis. Polym. Adv. Technol. 2021, 32, 4598-615.
49. Varcoe, J. R.; Atanassov, P.; Dekel, D. R.; et al. Anion-exchange membranes in electrochemical energy systems. Energy. Environ. Sci. 2014, 7, 3135-91.
50. Feng, H.; He, X.; Su, Q.; Li, M. Poly (aryl quinuclidinium) anion exchange membrane water electrolysis based on the mature industry chain of alkaline water electrolysis. Int. J. Hydrogen. Energy. 2025, 98, 915-22.
51. Li, X.; Han, B.; Cao, S.; Bai, H.; Li, J.; Du, X. In-situ reconstitution of Ni(III)-based active sites from vanadium doped nickel phosphide/metaphosphate for super-stable urea-assisted water electrolysis at large current densities. J. Colloid. Interface. Sci. 2025, 680, 665-75.
52. Janani, G.; Surendran, S.; Lee, D.; et al. Aggregation induced edge sites actuation of 3D MoSe2/rGO electrocatalyst for high-performing water splitting system. Aggregate 2024, 5, e430.
53. Janani, G.; Surendran, S.; Moon, D. J.; et al. Ambipolar nature accelerates dual-functionality on Ni/Ni3N@NC for simultaneous hydrogen and oxygen evolution in electrochemical water splitting system. Adv. Sustain. Syst. 2024, 8, 2400059.
54. Chen, P.; Hu, X. High-efficiency anion exchange membrane water electrolysis employing non-noble metal catalysts. Advd. Energy. Mater. 2020, 10, 2002285.
55. Chen, J.; Aliasgar, M.; Zamudio, F. B.; et al. Diversity of platinum-sites at platinum/fullerene interface accelerates alkaline hydrogen evolution. Nat. Commun. 2023, 14, 1711.
56. Liao, F.; Yin, K.; Ji, Y.; et al. Iridium oxide nanoribbons with metastable monoclinic phase for highly efficient electrocatalytic oxygen evolution. Nat. Commun. 2023, 14, 1248.
57. Shah, A. H.; Zhang, Z.; Huang, Z.; et al. The role of alkali metal cations and platinum-surface hydroxyl in the alkaline hydrogen evolution reaction. Nat. Catal. 2022, 5, 923-33.
58. Du, J.; Chen, D.; Ding, Y.; Wang, L.; Li, F.; Sun, L. Highly stable and efficient oxygen evolution electrocatalyst based on Co oxides decorated with ultrafine Ru nanoclusters. Small 2023, 19, 2207611.
59. Ghorui, U. K.; Sivaguru, G.; Teja, U. B.; et al. Anion-exchange membrane water electrolyzers for green hydrogen generation: advancement and challenges for industrial application. ACS. Appl. Energy. Mater. 2024, 7, 7649-76.
60. Sheng, W.; Zhou, X.; Wu, L.; et al. Quaternized poly(2,6-dimethyl-1,4-phenylene oxide) anion exchange membranes with pendant sterically-protected imidazoliums for alkaline fuel cells. J. Membr. Sci. 2020, 601, 117881.
61. Felgenhauer, M.; Hamacher, T. State-of-the-art of commercial electrolyzers and on-site hydrogen generation for logistic vehicles in South Carolina. Int. J. Hydrogen. Energy. 2015, 40, 2084-90.
62. Jang, M. J.; Yang, S. H.; Park, M. G.; et al. Efficient and durable anion exchange membrane water electrolysis for a commercially available electrolyzer stack using alkaline electrolyte. ACS. Energy. Lett. 2022, 7, 2576-83.
63. Gao, B.; Zhao, Y.; Du, X.; et al. Modulating trinary-heterostructure of MoS2 via controllably carbon doping for enhanced electrocatalytic hydrogen evolution reaction. Adv. Funct. Mater. 2023, 33, 2214085.
64. Park, Y. S.; Yang, J.; Lee, J.; et al. Superior performance of anion exchange membrane water electrolyzer: ensemble of producing oxygen vacancies and controlling mass transfer resistance. Appl. Catal. B. Environ. 2020, 278, 119276.
65. Zhang, J.; Wu, Q.; Song, J.; Xu, C.; Chen, S.; Guo, Y. 3D transition metal boride monolithic electrode for industrial hectoampere-level current anion exchange membrane water electrolysis. Nano. Energy. 2024, 128, 109923.
66. Wan, L.; Pang, M.; Le, J.; et al. Oriented intergrowth of the catalyst layer in membrane electrode assembly for alkaline water electrolysis. Nat. Commun. 2022, 13, 7956.
67. Chang, J.; Wang, G.; Yang, Z.; et al. Dual-doping and synergism toward high-performance seawater electrolysis. Adv. Mater. 2021, 33, 2101425.
68. Chang, J.; Xiao, Y.; Xiao, M.; Ge, J.; Liu, C.; Xing, W. Surface oxidized cobalt-phosphide nanorods as an advanced oxygen evolution catalyst in alkaline solution. ACS. Catal. 2015, 5, 6874-8.
69. Chen, D.; Park, Y. S.; Liu, F.; Fang, L.; Duan, C. Hybrid perovskites as oxygen evolution electrocatalysts for high-performance anion exchange membrane water electrolyzers. Chem. Eng. J. 2023, 452, 139105.
70. Yoon, K.; Lee, K.; Jeong, J.; et al. Improved oxygen evolution reaction kinetics with titanium incorporated nickel ferrite for efficient anion exchange membrane electrolysis. ACS. Catal. 2024, 14, 4453-62.
71. Zhai, P.; Wang, C.; Zhao, Y.; et al. Regulating electronic states of nitride/hydroxide to accelerate kinetics for oxygen evolution at large current density. Nat. Commun. 2023, 14, 1873.
72. Lakshmi, K. S.; Vedhanarayanan, B.; Lin, T. Electrocatalytic hydrogen and oxygen evolution reactions: role of two-dimensional layered materials and their composites. Electrochim. Acta. 2023, 447, 142119.
73. Liu, Y.; Wang, Q.; Zhang, J.; et al. Recent advances in carbon-supported noble-metal electrocatalysts for hydrogen evolution reaction: syntheses, structures, and properties. Adv. Energy. Mater. 2022, 12, 2200928.
74. Yin, Z.; Liu, X.; Chen, S.; Ma, T.; Li, Y. Interface engineering and anion engineering of Mo-based heterogeneous electrocatalysts for hydrogen evolution reaction. Energy. Environ. Mater. 2023, 6, e12310.
75. Anantharaj, S.; Noda, S.; Jothi, V. R.; Yi, S.; Driess, M.; Menezes, P. W. Strategies and perspectives to catch the missing pieces in energy-efficient hydrogen evolution reaction in alkaline media. Angew. Chem. Int. Ed. 2021, 60, 18981-9006.
76. Gao, L.; Cui, X.; Sewell, C. D.; Li, J.; Lin, Z. Recent advances in activating surface reconstruction for the high-efficiency oxygen evolution reaction. Chem. Soc. Rev. 2021, 50, 8428-69.
77. Wang, X.; Zhong, H.; Xi, S.; Lee, W. S. V.; Xue, J. Understanding of oxygen redox in the oxygen evolution reaction. Adv. Mater. 2022, 34, 2107956.
78. Shaik, S.; Kundu, J.; Yuan, Y.; et al. Recent progress and perspective in pure water-fed anion exchange membrane water electrolyzers. Advanced. Energy. Materials. 2024, 14, 2401956.
79. Brüesch, P.; Christen, T. The electric double layer at a metal electrode in pure water. J. Appl. Phys. 2004, 95, 2846-56.
80. Li, D.; Motz, A. R.; Bae, C.; et al. Durability of anion exchange membrane water electrolyzers. Energy. Environ. Sci. 2021, 14, 3393-419.
81. Li, D.; Park, E. J.; Zhu, W.; et al. Highly quaternized polystyrene ionomers for high performance anion exchange membrane water electrolysers. Nat. Energy. 2020, 5, 378-85.
82. Xu, D.; Stevens, M. B.; Cosby, M. R.; et al. Earth-abundant oxygen electrocatalysts for alkaline anion-exchange-membrane water electrolysis: effects of catalyst conductivity and comparison with performance in three-electrode cells. ACS. Catal. 2019, 9, 7-15.
83. Xu, Q.; Zhang, L.; Zhang, J.; et al. Anion exchange membrane water electrolyzer: electrode design, lab-scaled testing system and performance evaluation. EnergyChem 2022, 4, 100087.
84. Lindquist, G. A.; Oener, S. Z.; Krivina, R.; et al. Performance and durability of pure-water-fed anion exchange membrane electrolyzers using baseline materials and operation. ACS. Appl. Mater. Interfaces. 2021, 13, 51917-24.
85. Lei, C.; Yang, K.; Wang, G.; et al. Impact of catalyst reconstruction on the durability of anion exchange membrane water electrolysis. ACS. Sustain. Chem. Eng. 2022, 10, 16725-33.
86. Gao, F.; Yu, P.; Gao, M. Seawater electrolysis technologies for green hydrogen production: challenges and opportunities. Curr. Opin. Chem. Eng. 2022, 36, 100827.
87. Wang, Y.; Wang, M.; Yang, Y.; et al. Potential technology for seawater electrolysis: Anion-exchange membrane water electrolysis. Chem. Catal. 2023, 3, 100643.
88. Burton, N.; Padilla, R.; Rose, A.; Habibullah, H. Increasing the efficiency of hydrogen production from solar powered water electrolysis. Renew. Sustain. Energy. Rev. 2021, 135, 110255.
89. Schrotenboer, A. H.; Veenstra, A. A.; uit, B. M. A.; Ursavas, E. A green hydrogen energy system: optimal control strategies for integrated hydrogen storage and power generation with wind energy. Renew. Sustain. Energy. Rev. 2022, 168, 112744.
90. Hu, H.; Zhang, Z.; Liu, L.; et al. Efficient and durable seawater electrolysis with a V2O3-protected catalyst. Sci. Adv. 2024, 10, eadn7012.
91. Khan, M. A.; Al-attas, T.; Roy, S.; et al. Seawater electrolysis for hydrogen production: a solution looking for a problem? Energy. Environ. Sci. 2021, 14, 4831-9.
92. Kim, H. W.; Yun, T.; Hong, S.; Lee, S.; Jeong, S. Retardation of wetting for membrane distillation by adjusting major components of seawater. Water. Res. 2020, 175, 115677.
93. Song, J.; Qian, Z.; Yang, J.; Lin, X.; Xu, Q.; Li, J. In situ/operando investigation for heterogeneous electro-catalysts: from model catalysts to state-of-the-art catalysts. ACS. Energy. Lett. 2024, 9, 4414-40.
94. Wang, M.; Liu, S.; Ji, H.; Yang, T.; Qian, T.; Yan, C. Salting-out effect promoting highly efficient ambient ammonia synthesis. Nat. Commun. 2021, 12, 3198.
95. Szentirmai, V.; Wacha, A.; Németh, C.; et al. Reagent-free total protein quantification of intact extracellular vesicles by attenuated total reflection Fourier transform infrared (ATR-FTIR) spectroscopy. Anal. Bioanal. Chem. 2020, 412, 4619-28.
96. Rupprechter, G. Operando surface spectroscopy and microscopy during catalytic reactions: from clusters via nanoparticles to meso-scale aggregates. Small 2021, 17, 2004289.
97. Lai, W.; Ma, Z.; Zhang, J.; Yuan, Y.; Qiao, Y.; Huang, H. Dynamic evolution of active sites in electrocatalytic CO2 reduction reaction: fundamental understanding and recent progress. Adv. Funct. Mater. 2022, 32, 2111193.
98. López-Lorente, Á. I. Recent developments on gold nanostructures for surface enhanced Raman spectroscopy: particle shape, substrates and analytical applications. a review. Anal. Chim. Acta. 2021, 1168, 338474.
99. Lee, W. H.; Han, M. H.; Ko, Y. J.; Min, B. K.; Chae, K. H.; Oh, H. S. Electrode reconstruction strategy for oxygen evolution reaction: maintaining Fe-CoOOH phase with intermediate-spin state during electrolysis. Nat. Commun. 2022, 13, 605.
100. Jiang, J.; Sun, F.; Zhou, S.; et al. Atomic-level insight into super-efficient electrocatalytic oxygen evolution on iron and vanadium co-doped nickel (oxy)hydroxide. Nat. Commun. 2018, 9, 2885.
101. Chen, S.; Li, W.; Jiang, W.; et al. MOF encapsulating N-heterocyclic carbene-ligated copper single-atom site catalyst towards efficient methane electrosynthesis. Angew. Chem. 2022, 134, e202114450.
102. Geng, S.; Zheng, Y.; Li, S.; et al. Nickel ferrocyanide as a high-performance urea oxidation electrocatalyst. Nat. Energy. 2021, 6, 904-12.
103. Zhang, Y.; Ze, H.; Fang, P.; et al. Shell-isolated nanoparticle-enhanced Raman spectroscopy. Nat. Rev. Methods. Primers. 2023, 3, 36.
104. Chen, J.; Liu, G.; Zhu, Y. Z.; et al. Ag@MoS2 core-shell heterostructure as SERS platform to reveal the hydrogen evolution active sites of single-layer MoS2. J. Am. Chem. Soc. 2020, 142, 7161-7.
105. Radjenovic, P. M.; Zhou, R.; Dong, J.; Li, J. Watching reactions at solid-liquid interfaces with in situ raman spectroscopy. J. Phys. Chem. C. 2021, 125, 26285-95.
106. Yoo, R. M. S.; Yesudoss, D.; Johnson, D.; Djire, A. A review on the application of in-situ Raman spectroelectrochemistry to understand the mechanisms of hydrogen evolution reaction. ACS. Catal. 2023, 13, 10570-601.
107. Holder, C. F.; Schaak, R. E. Tutorial on powder X-ray diffraction for characterizing nanoscale materials. ACS. Nano. 2019, 13, 7359-65.
108. Magnussen, O. M.; Drnec, J.; Qiu, C.; et al. In situ and operando X-ray scattering methods in electrochemistry and electrocatalysis. Chem. Rev. 2024, 124, 629-721.
109. Yang, Y.; Xiong, Y.; Zeng, R.; et al. Operando methods in electrocatalysis. ACS. Catal. 2021, 11, 1136-78.
110. Arul, K. T.; Chang, H.; Shiu, H.; Dong, C.; Pong, W. A review of energy materials studied by in situ/operando synchrotron x-ray spectro-microscopy. J. Phys. D:. Appl. Phys. 2021, 54, 343001.
111. Chen, X.; Lv, S.; Gu, H.; et al. Amorphous bismuth-tin oxide nanosheets with optimized C-N coupling for efficient urea synthesis. J. Am. Chem. Soc. 2024, 146, 13527-35.
112. Xu, W.; Zeng, R.; Rebarchik, M.; et al. Atomically dispersed Zn/Co-N-C as ORR electrocatalysts for alkaline fuel cells. J. Am. Chem. Soc. 2024, 146, 2593-603.
113. Xiao, M.; Zhu, J.; Ma, L.; et al. Microporous framework induced synthesis of single-atom dispersed Fe-N-C acidic ORR catalyst and its in situ reduced Fe-N4 active site identification revealed by X-ray absorption spectroscopy. ACS. Catal. 2018, 8, 2824-32.
114. Li, X.; Cao, C.; Hung, S.; et al. Identification of the electronic and structural dynamics of catalytic centers in single-Fe-atom material. Chem 2020, 6, 3440-54.
115. Ampurdanés, J.; Chourashiya, M.; Urakawa, A. Cobalt oxide-based materials as non-PGM catalyst for HER in PEM electrolysis and in situ XAS characterization of its functional state. Catal. Today. 2019, 336, 161-8.
116. Du, Y.; Zhu, Y.; Xi, S.; et al. XAFCA: a new XAFS beamline for catalysis research. J. Synchrotron. Radiat. 2015, 22, 839-43.
117. Peng, C. K.; Lin, Y. C.; Chiang, C. L.; et al. Zhang-Rice singlets state formed by two-step oxidation for triggering water oxidation under operando conditions. Nat. Commun. 2023, 14, 529.
118. Hong, Y.; Cho, S. C.; Kim, S.; et al. Double-walled tubular heusler-type platinum-ruthenium phosphide as all-pH hydrogen evolution reaction catalyst outperforming platinum and ruthenium. Adv. Energy. Mater. 2024, 14, 2304269.
119. Lei, H.; Wan, Q.; Tan, S.; Wang, Z.; Mai, W. Pt-quantum-dot-modified sulfur-doped NiFe layered double hydroxide for high-current-density alkaline water splitting at industrial temperature. Adv. Mater. 2023, 35, 2208209.
120. Wang, K.; Cao, J.; Yang, X.; et al. Kinetically accelerating elementary steps via bridged Ru-H state for the hydrogen-evolution in anion-exchange membrane electrolyzer. Adv. Funct. Mater. 2023, 33, 2212321.
121. Lin, X.; Hu, W.; Xu, J.; et al. Alleviating OH blockage on the catalyst surface by the puncture effect of single-atom sites to boost alkaline water electrolysis. J. Am. Chem. Soc. 2024, 146, 4883-91.
122. Yao, R.; Sun, K.; Zhang, K.; et al. Stable hydrogen evolution reaction at high current densities via designing the Ni single atoms and Ru nanoparticles linked by carbon bridges. Nat. Commun. 2024, 15, 2218.
123. Li, Q.; Fu, X.; Li, H.; et al. Strong d-p orbital hybridization of Os-P via ultrafast microwave plasma assistance for anion exchange membrane electrolysis. Adv. Funct. Materials. 2024, 34, 2408517.
124. Li, D.; Cheng, H.; Hao, X.; et al. Wood-derived freestanding carbon-based electrode with hierarchical structure for industrial-level hydrogen production. Adv. Mater. 2024, 36, 2304917.
125. Lee, W.; Yun, H.; Kim, Y.; et al. Effect of activating a nickel-molybdenum catalyst in an anion exchange membrane water electrolyzer. ACS. Catal. 2023, 13, 11589-97.
126. Chen, Y.; Yue, K.; Zhao, J.; Cai, Z.; Wang, X.; Yan, Y. Effective modulating of the Mo dissolution and polymerization in Ni4Mo/NiMoO4 heterostructure via metal-metal oxide-support interaction for boosting H2 production. Chem. Eng. J. 2023, 466, 143097.
127. Zhao, T.; Wang, S.; Jia, C.; et al. Cooperative boron and vanadium doping of nickel phosphides for hydrogen evolution in alkaline and anion exchange membrane water/seawater electrolyzers. Small 2023, 19, 2208076.
128. Zhang, H.; Chen, A.; Bi, Z.; et al. MOF-on-MOF-derived ultrafine Fe2P-Co2P heterostructures for high-efficiency and durable anion exchange membrane water electrolyzers. ACS. Nano. 2023, 17, 24070-9.
129. Xie, L.; Wang, L.; Liu, X.; et al. Flexible tungsten disulfide superstructure engineering for efficient alkaline hydrogen evolution in anion exchange membrane water electrolysers. Nat. Commun. 2024, 15, 5702.
130. Kang, X.; Yang, F.; Zhang, Z.; et al. A corrosion-resistant RuMoNi catalyst for efficient and long-lasting seawater oxidation and anion exchange membrane electrolyzer. Nat. Commun. 2023, 14, 3607.
131. Wang, N.; Ou, P.; Hung, S. F.; et al. Strong-proton-adsorption co-based electrocatalysts achieve active and stable neutral seawater splitting. Adv. Mater. 2023, 35, 2210057.
132. Park, J. E.; Park, S.; Kim, M.; et al. Three-dimensional unified electrode design using a NiFeOOH catalyst for superior performance and durable anion-exchange membrane water electrolyzers. ACS. Catal. 2022, 12, 135-45.
133. Thangavel, P.; Lee, H.; Kong, T.; et al. Immobilizing low-cost metal nitrides in electrochemically reconstructed platinum group metal (PGM)-free oxy-(hydroxides) surface for exceptional OER kinetics in anion exchange membrane water electrolysis. Adv. Energy. Mater. 2023, 13, 2203401.
134. Yang, X.; Liang, J.; Shi, Q.; et al. Regulating the third metal to design and engineer multilayered NiFeM (M: Co, Mn, and Cu) nanofoam anode catalysts for anion-exchange membrane water electrolyzers. Adv. Energy. Mater. 2024, 14, 2400029.
135. Zhao, Y.; Wen, Q.; Huang, D.; et al. Operando reconstruction toward dual-cation-defects Co-containing NiFe oxyhydroxide for ultralow energy consumption industrial water splitting electrolyzer. Adv. Energy. Mater. 2023, 13, 2203595.
136. Park, Y. S.; Jang, M. J.; Jeong, J.; et al. Hierarchical chestnut-burr like structure of copper cobalt oxide electrocatalyst directly grown on Ni foam for anion exchange membrane water electrolysis. ACS. Sustain. Chem. Eng. 2020, 8, 2344-9.
137. Park, Y. S.; Liu, F.; Diercks, D.; Braaten, D.; Liu, B.; Duan, C. High-performance anion exchange membrane water electrolyzer enabled by highly active oxygen evolution reaction electrocatalysts: synergistic effect of doping and heterostructure. Appl. Catal. B. Environ. 2022, 318, 121824.
138. Park, Y. S.; Chae, A.; Choi, G. H.; et al. Unveiling the role of catalytically active MXene supports in enhancing the performance and durability of cobalt oxygen evolution reaction catalysts for anion exchange membrane water electrolyzers. Appl. Catal. B. Environ. Energy. 2024, 346, 123731.
139. Park, S.; Jun, J. H.; Park, M.; et al. Hierarchically designed Co4Fe3@N-doped graphitic carbon as an electrocatalyst for oxygen evolution in anion-exchange-membrane water electrolysis. Energy. Fuels. 2024, 38, 4451-63.
140. Aralekallu, S.; Sannegowda, L. K.; Singh, V. Advanced bifunctional catalysts for energy production by electrolysis of earth-abundant water. Fuel 2024, 357, 129753.
141. Tran, K. D.; Nguyen, T. H.; Tran, D. T.; Dinh, V. A.; Kim, N. H.; Lee, J. H. Realizing the tailored catalytic performances on atomic Pt-promoted transition metal moieties implanted layered double hydroxides for water electrolysis. ACS. Nano. 2024, 18, 16222-35.
142. Shen, L.; Wang, Y.; Shen, L.; et al. Ruthenium nanoparticles decorated with surface hydroxyl and borate species boost overall seawater splitting via increased hydrophilicity. Energy. Environ. Sci. 2024, 17, 3888-97.
143. Chang, J.; Wang, G.; Belharsa, A.; Ge, J.; Xing, W.; Yang, Y. Stable Fe2P2S6 nanocrystal catalyst for high-efficiency water electrolysis. Small. Methods. 2020, 4, 1900632.
144. Liang, Z.; Shen, D.; Wei, Y.; et al. Modulating the electronic structure of cobalt-vanadium bimetal catalysts for high-stable anion exchange membrane water electrolyzer. Adv. Mater. 2024, 36, 2408634.
Cite This Article
How to Cite
Download Citation
Export Citation File:
Type of Import
Tips on Downloading Citation
Citation Manager File Format
Type of Import
Direct Import: When the Direct Import option is selected (the default state), a dialogue box will give you the option to Save or Open the downloaded citation data. Choosing Open will either launch your citation manager or give you a choice of applications with which to use the metadata. The Save option saves the file locally for later use.
Indirect Import: When the Indirect Import option is selected, the metadata is displayed and may be copied and pasted as needed.
About This Article
Copyright
Data & Comments
Data
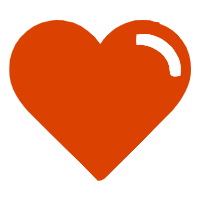
Comments
Comments must be written in English. Spam, offensive content, impersonation, and private information will not be permitted. If any comment is reported and identified as inappropriate content by OAE staff, the comment will be removed without notice. If you have any queries or need any help, please contact us at [email protected].