Recent progress on metal-organic framework-based separators for quasi-solid-state lithium metal batteries
Abstract
Although lithium-ion batteries are emerging as one of the leading energy storage technologies due to their high energy density, high specific capacity, and fast charging speed, major challenges remain regarding the use of liquid electrolytes. These electrolytes directly affect the safety and durability of the batteries. While alternative materials such as rigid solid-state electrolytes have been developed to improve safety, they often suffer from poor ionic conductivity and inadequate interfacial contact with the electrodes. These issues hinder the production and widespread application of lithium-ion batteries. To overcome these disadvantages, quasi-solid-state electrolytes, which include both liquid and solid components, have been extensively researched. Among these, metal-organic frameworks (MOFs) with diverse morphological designs and porous structures are considered promising materials for the fabrication of high-performance quasi-solid-state electrolytes. This review summarizes recent research on MOF-based separators for lithium metal batteries, including native MOFs, MOF composites, and MOF derivatives. The fabrication processes and mechanisms for enhancing the electrochemical performance of each separator material are discussed. Furthermore, the prospects of this promising material for lithium metal batteries are provided.
Keywords
INTRODUCTION
The increasing demand for high-energy-density batteries in portable electronics, electric vehicles, and grid-scale energy storage has driven the development of advanced lithium-based energy storage systems. Lithium-ion batteries (LIBs), widely used for their high energy density and long cycle life, typically rely on liquid electrolytes (LEs) due to their excellent ionic conductivity (~10-3 S cm-1)[1-4]. However, LEs suffer from inherent limitations, including high reactivity with lithium metal and cathode materials, decomposition at high voltages, and the risk of dendrite formation leading to short-circuiting and safety hazards[5-10]. These challenges have prompted significant research into alternative electrolyte systems.
The research on fabrication and application of quasi-solid-state electrolytes (QSSEs) has emerged as a promising approach, integrating the mechanical stability of solid-state electrolytes (SSEs)[11], with the high ionic conductivity of LEs. QSSEs consist of a porous solid matrix infused with a small amount of LEs, offering improved thermal stability, enhanced mechanical properties, and effective lithium dendrite suppression[12,13]. Among the various solid matrices explored, metal-organic frameworks (MOFs) have attracted significant attention due to their high porosity, tunable pore structure, and chemical versatility, making them ideal hosts for LE confinement in quasi-solid-state lithium metal batteries (QSSLMBs)[14-17].
MOFs, composed of metal nodes and organic linkers[18], provide a well-defined porous structure that facilitates efficient ion transport while maintaining mechanical robustness[19]. By tailoring MOF structures and surface functionalities, researchers have achieved enhanced ionic conductivity, uniform lithium-ion distribution, and improved interfacial stability within QSSEs[5,20,21]. Recent studies have demonstrated that MOF-based separators not only suppress lithium dendrites but also improve electrolyte retention and electrochemical stability, addressing critical challenges in QSSLMBs[15,17,22-28].
This review systematically explores the design, fabrication, and electrochemical performance of MOF-based separators in QSSLMBs. We discuss various MOF synthesis strategies, their structural characteristics, and their impact on battery performance. The review also examines MOF-based separators in different configurations, including pristine MOFs, MOF composites, and MOF derivatives. Furthermore, we highlight theoretical and experimental insights into ion transport mechanisms within MOFs and their role in mitigating common battery failure modes. Finally, we discuss challenges and future directions for the commercialization of MOF-based separators, including cost considerations, scalability, and environmental impact. By providing a comprehensive analysis of recent advancements, this review aims to guide future research on MOF-based QSSEs, facilitating the development of next-generation high-performance lithium metal batteries (LMBs).
A BRIEF INTRODUCTION OF QSSLMBS
QSSLMBs combine the high energy density of lithium metal anodes with the improved safety of QSSEs[29,30]. Unlike traditional LE-based LIBs, QSSLMBs use QSSEs that reduce leakage, flammability, and dendrite formation risks[31,32]. These electrolytes, often polymers, gels, or composites, maintain structural integrity while facilitating lithium-ion transport[29,33]. This design enhances safety, enables high electrochemical performance, and extends cycle life[1,34], making QSSLMBs promising for next-generation energy storage in applications such as electric vehicles and portable electronics[2,35].
Basic configuration
QSSLMBs consist of several key components that combine advantages of solid and LEs. The lithium metal anode provides a high theoretical capacity (3,860 mAh g-1) and low electrochemical potential (-3.04 V vs. standard hydrogen electrode)[36,37]. The cathode, typically lithium intercalation materials (e.g.,
Figure 1. Schematic illustration of QSSLMBs assembled with: (A) Quasi-solid polymer electrolyte (QSPE) and NCM/LFP cathode; (B) QSPE and S cathode; (C) MOF-based QSSE and NCM/LFP cathode. (A) is quoted with permission from Fang et al.[49]; (B) from Wang et al.[50]; and (C) from Chang et al.[13]. QSSLMBs: Quasi-solid-state lithium metal batterie; NCM: LiNi1-x-yCoxMnyO2; LFP: LiFePO4; MOF: metal-organic frameworks; QSSEs: quasi-solid-state electrolytes.
The QSSE facilitates efficient ion transport while minimizing leakage, flammability, and dendrite growth risks[31,42]. The separator, usually a microporous membrane, prevents short-circuit between the anode and cathode[43]. MOF-based separators are particularly promising due to their thermal stability, tunable pore size, and high ionic conductivity[21,44-46]. Current collectors, typically copper for the anode and aluminum for the cathode, enable efficient electron transport[47].
Key design considerations for QSSLMBs include optimizing electrolyte composition for conductivity and stability[48], treating the anode surface to reduce dendrites[41], and using advanced cathode materials to enhance energy density and cycle life[1,49,50]. This integration of materials science and electrochemical engineering aims to overcome the limitations of conventional lithium-ion and solid-state batteries[51,52].
Working principle
In QSSLMBs, the QSSE is typically a solid matrix (e.g., polymers, inorganic particles, MOFs) infused with a LE, thus facilitating ion transport[13,53,54], suppressing dendrite growth[55,56], enhancing electrode contact for improved ionic conductivity[57,58], and stabilizing the solid electrolyte interface (SEI) to prevent continuous electrolyte decomposition[59,60].
During discharge, lithium ions move from the lithium metal anode through the QSSE to the cathode, while electrons flow through the external circuit[61]. During charging, lithium ions return to the anode and deposit as lithium metal[62-64]. Ion transport occurs through the liquid-filled QSSE pores, enabling electrochemical reactions and delivering power to devices[65].
The solid matrix reduces electrolyte leakage and dendrite-induced short circuits, improving battery safety, cycling stability, and lifespan[66-68]. Overall, QSSLMBs function similarly to conventional LIBs, as depicted in Figure 2, offering a balance of electrochemical efficiency and mechanical stability.
Figure 2. Schematic of the working mechanism of a gel-polymer-based lithium battery. This figure is quoted with permission from Liang et al.[65].
Ionic transport mechanism
Ion transport in QSSLMBs is crucial for their performance and efficiency. QSSEs typically consist of a solid matrix infused with LEs, facilitating continuous ionic pathways, reducing interfacial resistance, and promoting uniform ion distribution[31,48,69-71].
Lithium ions (Li+) migrate through the QSSE by hopping between available sites in the solid matrix, influenced by the structural and chemical characteristics of the electrolyte material[72-76] [Figure 3A]. Incorporating MOFs into the QSSE enhances ion transport due to their high porosity, large surface area, and tunable pore structures. Functionalized MOFs lower the activation energy for ion hopping, improving mobility[77-82].
Figure 3. Schematic illustration of: (A) Li-ion transport via hopping effect in the solid-matrix channels of QSSLMBs; (B) The importance of liquid components in surface engineering of QSSE; (C) The effect of Li-MOF on lithium-ion conduction and the crystallinity of the polyethylene oxide (PEO) matrix; (D) Improvement of the adhesion and ionic contact for better Li-ion transport by modifying the surface chemistry of the MOFs; (E) Three proposed Li conduction mechanisms in MOF-based QSSEs; (F) Ionic conductivities of MOF-688(Mn) and MOF-688(Al) obtained from experimental measurements, and theoretical calculations using Green-Kubo relations (GK), Nernst-Einstein equation (NE), and simple hopping model (hopping). (A) is quoted with permission from Chang et al.[13]; (B) from Zheng et al.[86]; (C) from Zhang et al.[90]; (D) from Zhang et al.[97]; (E and F) from Hou et al.[103]. QSSLMBs: Quasi-solid-state lithium metal batterie; QSSEs: quasi-solid-state electrolytes; MOF: metal-organic frameworks.
LEs in the QSSE further improve ionic conductivity by ensuring continuous ion flow and reducing interfacial resistance. This liquid phase also mitigates dendrite formation and electrolyte degradation, enhancing cycling stability [Figure 3B][13,83-86].
Ion transport in MOF-based QSSEs depends on the morphology and crystallinity of MOFs. High crystallinity and well-defined pores create continuous conduction pathways, boosting ionic conductivity[87-90] [Figure 3C]. The tunable MOF structures allow for incorporating dopants or secondary phases, improving conductivity and stability[91-93].
Electrode-electrolyte interfaces also play a critical role in ion transport. Engineering these interfaces reduces charge transfer resistance and enhances performance. In MOF-based QSSEs, modifying MOF surface chemistry or adding interfacial layers improves adhesion and ionic contact, minimizing impedance
Both experimental and theoretical studies provide insights into Li+ transport in MOF-based QSSEs.
In summary, ion transport in QSSLMBs involves a complex interaction of material properties, structural design, and interfacial engineering, offering enhanced ion transport through their unique structural and chemical features. The combination of experimental and theoretical approaches has advanced the understanding of ionic conduction in MOF-based QSSEs, facilitating the optimization of QSSLMBs for high-energy-density applications.
Current challenges
QSSLMBs offer a promising path to high-energy-density and safer energy storage. However, several challenges remain. A major issue is achieving high ionic conductivity in QSSEs. While LEs typically show conductivities of 10-3 to 10-2 S/cm[104,105], maintaining comparable conductivity when integrated into a solid matrix is difficult. The rigid solid matrix, often polymers, inorganic particles, or MOFs, limits ion mobility[106-108]. Ensuring uniform distribution and retention of the liquid component is also vital to prevent phase separation and leakage, which can cause performance degradation and safety risks.
Lithium dendrite formation during cycling is another key challenge, as dendrites can penetrate the separator, leading to short circuits and thermal runaway. While the solid matrix of a QSSE can inhibit dendrite growth, its effectiveness depends on the mechanical properties and material uniformity[109-111]. The QSSE must endure the mechanical stress of lithium plating and stripping while maintaining flexibility to accommodate volume changes during cycling. Additionally, developing QSSEs capable of forming a stable and uniform SEI is crucial for preventing electrolyte decomposition and ensuring long-term cycling stability[112,113].
Interfacial stability between the QSSE and the electrodes is another area of concern. The interfaces must facilitate efficient ion transport and prevent detrimental side reactions. While much attention has been devoted to the challenges posed by lithium metal anodes due to their high reactivity and propensity for unstable interfaces[108,114,115], the QSSE-cathode interface also presents significant challenges. Poor contact, interfacial side reactions, and the structural instability of cathode materials during cycling can lead to increased interfacial resistance and capacity degradation[116-118]. Strategies such as surface coatings, functional interlayers, and MOF modifications can improve interfacial compatibility and reduce resistance at both electrode interfaces. However, these approaches introduce complexities and potential new failure modes that must be carefully addressed.
The fabrication and scalability of QSSEs with consistent and reproducible properties also present significant challenges. The synthesis of MOFs with desired porosity and chemical functionality requires precise control over the conditions, and scaling up these processes for industrial production can be complex and costly[33,110,119-121] [Figure 4]. While Ni-based MOFs have been widely explored, other metal precursors, such as Zn, Zr, and Cu, offer alternative design possibilities, each with distinct cost implications. For instance, Zr-based MOFs tend to have higher raw material costs due to the expense of zirconium precursors, whereas Zn and Cu-based MOFs may provide cost advantages in large-scale production[122,123]. Furthermore, the choice of organic ligands, such as terephthalic acid, imidazolates, and carboxylates, can significantly influence the overall material cost and process efficiency[123,124]. Additionally, integrating MOFs into composite electrolytes must ensure uniform dispersion of the liquid component to maintain high ionic conductivity and mechanical stability. The cost and environmental impact of these advanced materials are further considerations, as MOFs and other solid matrix components often involve expensive and
Figure 4. (A) Raw material cost and utility cost required for Ni-based MOF’s synthesis; (B) Material cost contributions (linker, metal salts, and solvents) of four MOFs manufactured at 2.5 million kg/year by solvothermal synthesis methods. (A) is quoted with permission from Ong et al.[120]; (B) from DeSantis et al.[121]. MOF: Metal-organic frameworks.
Thermal stability and chemical compatibility of QSSEs with the lithium metal anode and high-voltage cathodes are crucial for safe battery operation. The QSSE must endure high temperatures and reactive environments without degrading. While MOFs offer good thermal stability, they must be carefully selected and modified to prevent degradation under operational conditions[108,113]. Additionally, the QSSE must prevent side reactions with high-voltage cathodes to maintain performance and safety over extended cycles[51].
The long-term cycling stability and reliability of QSSLMBs also require extensive validation under
In conclusion, while QSSLMBs offer a promising route to safer and more efficient energy storage, addressing challenges in optimizing ionic conductivity, preventing dendrite formation, ensuring interfacial stability, achieving scalable fabrication, and maintaining thermal and chemical stability is essential. Continued research, particularly leveraging unique properties of MOFs, will be key to advancing QSSLMBs for practical use.
General strategies for designing QSSEs
Designing QSSEs for LMBs involves integrating innovative strategies to enhance ionic conductivity, mechanical stability, and electrochemical performance. One approach is incorporating a LE or ionic liquid into a solid inorganic electrolyte matrix, combining high ionic conductivity of the LE with structural stability of the solid matrix [Figure 5A][128]. For instance, Zhang et al. improved ion transport and suppressed dendrite formation by integrating a TFSI [bis(trifluoromethanesulfonyl)imide]-based ionic liquid into a garnet-like Li7La3Zr2O12 (LLZO) framework, achieving a stable and conductive QSSE[129].
Figure 5. (A) Integrating TFSI-based ionic liquid into a garnet-like Li6.75Al0.25La3Zr2O12 (LALZO) framework for better ion transport and suppression of lithium dendrite formation; (B) The development of MOF-based QSSEs; (C) PEO-based QSSE for high-performance NMC622//Li batteries; (D) Constructing PTFE@LATP composite solid electrolytes with three-dimensional network for high-performance lithium batteries; (E) Schematic illustration of the porous LATP-PVDF-HFP membrane preparation process and the in-situ polymerization; (F) Isostructural Li-MOF expansion for high ionic conductive QSSE. (A) is quoted with permission from Kaur et al.[128]; (B) from Lin et al.[130]; (C) from Homann et al.[132]; (D) from Wang et al.[133]; (E) from Liu et al.[134]; and (F) from Butreddy et al.[136]. MOF: Metal-organic frameworks; QSSEs: quasi-solid-state electrolytes; PEO: polyethylene oxide; PTFE: polytetrafluoroethylene; LATP: lithium aluminum titanium phosphate; TFSI: trifluoromethylsulfonyl; PVDF: polyvinylidene fluoride; HFP: hexafluoro propylene.
MOF-based QSSEs leverage the high surface area, tunable porosity, and chemical versatility of MOFs
QSPEs are a specific subclass of QSSEs that utilize a polymer matrix, such as polyethylene oxide (PEO) or polyvinylidene fluoride (PVDF), swollen with a LE to enhance ion mobility while maintaining mechanical support. Unlike MOF-based or inorganic-supported QSSEs, QSPEs primarily rely on the polymer structure for mechanical integrity. Homann et al.[132] developed QSPE using LiTFSI incorporating PEO polymer matrix, achieving high ionic conductivity and excellent electrochemical stability [Figure 5C]. The interconnected network of the polymer matrix facilitates ion transport, maintains flexibility, and enhances compatibility with lithium metal electrodes.
Inorganic-polymer composite electrolytes combine the high ionic conductivity of inorganic materials with the mechanical flexibility of polymers [Figure 5D]. Wang et al. developed a composite electrolyte using lithium aluminum titanium phosphate (LATP) embedded in a polytetrafluoroethylene (PTFE) matrix, enhancing both ion conduction and mechanical strength[133].
In situ polymerization is another advanced strategy where MOFs or inorganic particles are uniformly dispersed within the polymer matrix during polymerization [Figure 5E][134]. Xu et al. used Li+-containing liquid monomers with a MOF-incorporated fibrous membrane for in situ polymerization, achieving superior stability and enhanced ion transport[135].
Intrinsically, lithium-ion conductive MOFs represent another promising development. These MOFs integrate lithium ions directly within their framework, ensuring stable ion conductivity. Butreddy et al. demonstrated a lithium-based MOF with both structural stability and high ionic conductivity, improving QSSE performance in LMBs[136] [Figure 5F].
Other strategies include cross-linking polymer networks to enhance dimensional stability during cycling[137-140], using nanocomposites with carbon-based materials like graphene or carbon nanotubes to improve mechanical and electrochemical properties[141], and employing electrospinning techniques to fabricate QSSEs with aligned nanofiber structures for better ion transport and mechanical performance[142].
In summary, QSSE design involves approaches such as integrating LEs into solid matrices, utilizing
PREPARATION OF MOF-BASED QSSES
Different LMBs often encounter inherent problems including shuttle effect and dendrite growth during operation[143-145]. Shuttle effect results in decreased capacity and poor cycling stability[146], while heterogeneity in surface morphology, concentration gradient and uneven electrical field distribution on the anode can often cause deposition of metal protuberances that evolve into dendrites[147]. To address these issues, separator design is an effective strategy via regulating ion fluxes and electric field distribution[148]. MOFs have abundant micro/mesopores with tunable sizes, regular structures [Figure 6A], and ample active sites
Figure 6. (A) A typical MOF structure, where metal ions and organic ligands form a regular two-dimensional framework; (B) Rich active sites on MOFs; (C) MOF modified separators regulate the electric field and guide the ion flux; (D) MOF modified separator guides the uniform metal deposition and avoids dendrite formation; Representative synthesis process of (E) UIO-66; (F) MIP-202 and (G) MIL-125 (Ti). (A and G) are quoted with permission from Liu et al.[149]; (B) from Lu et al.[152]; (C) from Fu et al.[153]; (D) from Wang et al.[154]; (E) from Lei et al.[144]; and (F) from Zhou et al.[166]. MOF: Metal-organic frameworks.
Synthesis of MOFs
MOFs have intriguing properties for various applications, including gas storage and separation[155,156], chemical catalysis[157], sensing[158], ion exchange[159], drug delivery[160], and electrolyte fillers. MOFs are often categorized into MOFs (isoreticular MOFs), zeolite-imidazolate frameworks (ZIFs), materials of Institute Lavoisier (MILs), pocket-channel frameworks (PCNs) and other series based on the structure or named after the institution firstly reporting the synthesis. This section will discuss the application of MOFs in battery separators, mostly centered on Zr-, Zn-, Cu-, and other metal ion-based MOFs.
Zr-based MOF
UIO-66 {[Zr6O4(OH)4][1,4-benzene dicarboxylate (BDC)]6} is a typical Zirconium-based MOF and one of the most representative MOFs[161], which can be used as a nano-filler in QSSEs and can be obtained via various synthesis methods[162], yet solution-process are more commonly used to obtain different Zr-based MOFs by changing the organic linkers. Lei[144]et al. prepared UIO-66 through hydrothermal method with ZrCl4 and BDC in N, N-dimethylformamide (DMF) [Figure 6E]. The as-obtained UIO-66 was added to the QSSE of Al-Se batteries to improve battery performance. Notably, tuning metal ions to ligands ratio greatly affects the structure and properties of the obtained MOFs. For example, the total N2 absorption of UIO-66 synthesized using metal ions to ligand ratios of 6:6, 6:4, and 6:3 were 12.9 mmol g-1, 12.2 mmol g-1, and
Zn-based MOF
The majority of MOFs in the ZIF series are Zn-based MOFs, with a small portion being Co-based MOFs. Zn-based MOFs commonly used in separators/QSSEs include ZIF-8, ZIF-69, and ZIF-90. ZIF-8 and ZIF-69 can be prepared at room temperature. For example, ZIF-8 is obtained by a simple one-step copolymerization of Zn (II) and 2-methylimidazole in methanol[169], and ZIF-69 can be fabricated via mixing aqueous solutions of zinc nitrate hexahydrate, 2-nitroimidazole (HNIM) and 5-chlorobenzimidazole
Cu-based MOF
Cu-based MOF is another type of commonly used MOF for battery separators. Cu-TCPP nanosheets can be obtained by solvothermal reaction of Cu(NO3)2·3H2O and 5, 10, 15, 20-tetrakis (4-carboxyphenyl) porphyrin (H2TCPP) in a mixture of DEF and ethanol[176,177], whereby HKUST-1 can be obtained via room temperature mixing of Cu(NO3)2·3H2O/PVP-K30 and H3BTC in anhydrous methanol. Reducing PVP molecular weight can transform HKUST-1 from microparticles into nanoparticles. Likewise, monitoring the feeding rate of raw materials can also control the nucleation process, preparing HKUST-1 with a size distribution in the range of 89~503 nm[178]. Additionally, adjusting the amount of template reagent cetyltrimethylammonium bromide (CTAB) during microwave-assisted synthesis resulted in HKUST-1 with graded porous defects, and thus size gradient micropores[179].
Aside from Cu-TCPP and HKUST-1, other Cu-based MOFs [e.g., coordination pillared-layer (CPL) series and Dresden University of Technology (DUT) series] are also available but not yet used as nanofillers for batteries. CPL-1 can be obtained by adding NaOH dropwise to a mixed solution of Cu(NO3)2·3H2O, pyz (Pyrazine), H2PZDC, and H2O under stirring, and then heating for 12 h[180]. CPL-2 can be synthesized by uniformly mixing H2PZDC with NaOH aqueous solution and ethanol, and slowly adding it to
MOFs based on other metals
Aside from Zr-, Zn- and Cu-based MOFs, other metal-based MOFs, including Cr-, Mg, Ti- and Al-, also deserve attention. MIL-100(Cr) can be synthesized by heating the grinded CrCl3·6H2O and H3BTC precursor with deionized water vapor in a layered hydrothermal reactor using steam assisted method[184]. MIL-101(Cr) was synthesized by hydrothermal synthesis by mixing H2BDC with CrCl3·6H2O in deionized water[185]. Dissolving Mg(CH3COO)2 and 2,5-dihydroxytryphthalic acid (H4dhtp) in a mixed solvent of DMF/ethanol/water can render Mg-MOF-74. Notably, Hu et al.[186] found that increasing the reaction time can cause the aggregation of Mg-MOF-74 nanorod seeds into well-crystallized bulk crystals with decreased grain size. The synthesis of MIL-125(Ti) is dependent on a solvothermal method[187], which can be done by quickly adding tetrabutyl titanate Ti(OC4H9)4 to H2BDC in DMF/anhydrous methanol, stirring and subsequent solvothermal reactions [Figure 6G]. Al-based MOF-303 can be prepared by slowly dissolving AlCl3·6H2O in a mixed aqueous solution of NaOH and 3,5-pyrazolecarbolic acid under ultrasonic treatment, and subsequent heating[188].
Clearly, the porosity and grain size of MOFs can be regulated by many factors, such as tuning the ratio of metal ion to organic ligand[189], reaction temperature, nucleation process, etc., influence the proton conductivity, electronic conductivity, and Lewis acid sites of the as-obtained MOFs. However, the effect of synthesis factors on different MOFs might vary, as has been discussed for the effect of metal/ligand ratio on the grain sizes of ZIF-8 and ZIF-90. Therefore, attention should be paid to the influence of various parameters when synthesizing MOFs, so as to prepare MOFs with desirable properties. In Table 1, the raw materials, topological structure, pore size, and other parameters of MOFs mentioned in this section are summarized.
Synthetic materials and characteristics of common MOFs
MOFs | Metal ion source | Organic ligand | Solvent | Structure | Micro-pore size (Å) | Surface area SBET (m2/g) | Reference |
UIO-66 | ZrCl4 | BDC | DMF | Multi-level pore structure | Tetrahedral cages: 8 Octahedral cages: 11 | 1,000-1,500 | [162] |
UIO-67 | ZrCl4/ZrCl2·8H2O | BPDC | DMF+CH3COOH | Multi-level pore structure | Tetrahedral cages: 12 Octahedral cages: 16 | 1,500-2,000 | [165] |
MIP-202(Zr) | ZrCl4 | L-aspartic | H2O | Octahedral microporous structure | Octahedral cages: 6.3 | 49.62 | [166] |
PCN-221 | ZrCl4 | TCPP | DEF+CH3COOH | Directional disordered Zr6O4(OH)4 clusters | Cube cage:19 | 463 | [167] |
PCN-222 | ZrCl2·8H2O | TCPP | DEF+ 4- tert-butylbenzoic acid | Cube 3D porphyrin framework | 11 | 2,169 | [167] |
PCN-223 | ZrCl2·8H2O | TCPP | 4-chlorobenzoic acid+HCOOH | SHP-a topology structure | 11 | 617 | [167] |
PCN-224 | ZrCl4 | TCPP | DMF+ benzoic acid | SHP topology structure | 19 | 1,334 | [167] |
MOF-808 | ZrCl2·8H2O | H3BTC | DMF+HCOOH | SPN topology structure | Tetrahedral cages:4.8 | 1,300-1,700 | [168] |
ZIF-6 | Zn(NO3)2 | Imidazole | DMF | GLS-type silicon aluminum molecular sieve network | 8.8 | - | [173] |
ZIF-8 | Zn(NO3)2 | 2-methylimidazole | CH3OH | SOD type silicon aluminum molecular sieve network | 4.31 | 1,187-1,836 | [169] |
ZIF-20 | Zn(NO3)2 | purine | DEF | RHO-type silicon aluminum molecular sieve network | 14.64 | - | [174] |
ZIF-69 | (CH3COO)2Zn | 2-nitroimidazole+ 5-Chlorobenzimidazole | CH3OH | GME topology structure | 7.8 | 1,070 | [170] |
ZIF-90 | Zn(NO3)2 | ICA+PVP | H2O+ mixed alcohols (ethanol, 2-propanol, iso-butanol, and tert-butanol) | SOD-type silicon aluminum molecular sieve network | 3.4 | 1,000-1,500 | [171] |
MOF-2 | Zn(NO3)2 | H2BDC | - | 2D-Micro porous network | - | 310 | [175] |
MOF-5 | Zn(NO3)2 | H2BDC | - | Cubic lattice structure | 15 | 2,900 | [175] |
CuTCPP | Cu(NO3)2·3H2O | H2TCPP | DEF+CH3CH2OH | 2D nanosheet | 10 | 321.92 | [176] |
HKUST-1 | Cu(NO3)2·3H2O | H3BTC | CH3OH | TBO type topological structure | Cube cages:11 Octahedral cages:5 | 1,200-1,500 | [178] |
CPL-1 | Cu(NO3)2·3H2O | Pyrazine+ H2PZDC | NaOH aqueous solution | Pillared-layer framework | 10-13 | 330-490 | [180] |
CPL-2 | Cu(ClO4)2.6H2O | H2PZDC | NaOH aqueous solution | Pillared-layer framework | 6 × 8 | 490-546 | [181] |
DUT-48 | Cu(NO3)2·3H2O | - | DMF+ CH3COOH | Cubic octahedral supramolecular 3D framework | Octahedral cages:18.7 Tetrahedral cages:14.8 Cuboctahedral cages:10.7 | 4,560 | [183] |
DUT-49 | Cu(NO3)2·3H2O | - | DMF+ CH3COOH | Cubic octahedral supramolecular 3D framework | Octahedral cages:24.8 Tetrahedral cages:17.6 Cuboctahedral cages:10.5 | 5,476 | [183] |
DUT-50 | Cu(NO3)2·3H2O | - | DMF+ CH3COOH | Cubic octahedral supramolecular 3D framework | Octahedral cages:30.7 Tetrahedral cages:21 cuboctahedral cages:10.7 | 5,476 | [183] |
MIL-100(Cr) | CrCl3·6H2O | H3BTC | - | MTN zeolite topology structure | Smaller cages:5.5-8.8 Larger cages:25-29 | 3,100 | [184] |
MIL-101(Cr) | CrCl3·6H2O | H2BDC | H2O | Enhanced MTN zeolite topology structure | Smaller cages:5.5-8.8 Larger cages:29-34 | 3,549 | [185] |
Mg-MOF-74 | Mg(CH3COO)2 | H4dhtp | DMF/ethanol/H2O | HCB topology structure | 7-13 | > 1,000 | [186] |
MIL-125(Ti) | Ti(OC4H9)4 | H2BDC | DMF/ CH3OH | HCB topology structure | 3.7-4.8 | 1,200-1,350 | [187] |
MOF-303(Al) | AlCl3·6H2O | H2PDC | NaOH aqueous solution | XHH topology structure | 6 | 900-1,000 | [188] |
Fabrication of MOF-based separators
MOF-based separators are often obtained by grafting MOFs onto different substrates (e.g., commercial polypropylene (PP) and electrospun separators) or dispersing MOFs into different matrices. In the meantime, different surface modification strategies of MOFs are also employed to improve the electrochemical performance of MOF-based separators in different batteries. In this section, several preparation methods for MOF-based separators (including QSSEs) will be introduced.
Scrape coating
One of the most straightforward way to graft MOFs onto different substrate is scrape-coating. Leng et al.[190] dispersed Ni-Co MOF, graphene and PVDF in n-methyl-2-pyrrolidone (NMP), and the slurry can be subsequently scrape-coated onto a commercial PP separator (PPS). Similarly, Razaq et al.[191] mixed ZIF-8, Super-P, and PVDF in NMP to prepare a slurry via ball milling, the obtained slurry was then scrape-coated onto Celgard 2400 to obtain ZIF-8 based separators. Wang et al.[154] prepared QSSEs using polydopamine (PDA)-modified ZIF-90 via scrape-coating assisted fabrication [Figure 7A]. ZIF-90 and PVDF-HFP were dispersed in NMP using a homogenizer; the slurry was then scrape-coated onto the electrode/glass plate. Finally, ZIF-90 modified QSSE can be obtained by injecting the ionic LE (ILE) into the scrape-coated support layer for subsequent heating, where the ILE contains 1M LiTFSI dissolved in
Figure 7. (A) Scrape coating MOF onto a commercial separator; (B) Vacuum filtration of MOFs on an electrospun separator; (C) In situ gelation of MOF with polymer precursor solution to obtain MOF-based gel polymer electrolyte; (D) Preparation of MOF-based aerogel electrolyte; (E) Increasing the number of OMSs in Zr-based MOFs via thermal activation; (F) N2 isotherms (top) and corresponding pore size distribution (bottom) of chemically-activated UiO-66; (G) Increased ion conductivity and cation transference number of electrolytes containing chemically activated MOF. (A) is quoted with permission from Wang et al.[154]; (B) from Huang et al.[143]; (C) from Zhang et al.[145]; (D,F,G) from Fu et al.[153]; and (E) from Lu et al.[152]. MOF: Metal-organic frameworks.
Vacuum filtration
Vacuum filtration is also applicable to grafting MOF particles onto different substrates. Liu et al.[192] prepared an asymmetric Cu-TCPP/MXene composite separator using vacuum filtration. Similarly, Huang et al.[143] used an electrospun separator to vacuum filtrate mixed UIO-66/carboxymethyl cellulose (CMC) aqueous dispersion, obtaining a UIO-66-based separator [Figure 7B]. Han et al.[193] also prepared MOFs@PVDF-based QSSEs using vacuum filtration method. Mg-MOF-74/polyethylene pyrrolidone dispersed in ethanol was filtered by a PVDF membrane; immersing the MOFs@PVDF membrane in the electrolyte solution can render MOFs@PVDF-based QSSEs.
In-situ gelation method
Lei et al.[144] prepared UIO-66-based QSSE by in-situ gelation. Firstly, AlCl3 and acrylamide were mixed in methylene chloride (MC) for the complexation between acrylamide and AlCl3, and then UIO-66 and AIBN (initiator) were added. Subsequently, the solution was poured onto aluminum foil and placed in a glove box for solidification and polymerization, obtaining MOF@GPE (gel polymer electrolyte). Similarly, Zhang et al.[145] introduced HKUST-1 to prepare QSSE [Figure 7C]. Benzophenone (BP) (photoinitiator),
Aside from hydrogels, MOF aerogels can also be adopted to prepare QSSEs. Due to the excellent liquid storage capacity and high tensile strength of aerogels, batteries using aerogel QSSE have excellent performance. Fu et al.[153] introduced NH2-UIO-66 into bacterial cellulose (BC)-modified aerogel electrolytes to optimize the performance of high-pressure LMBs [Figure 7D]. Aqueous MOF dispersion was added into BC dispersed in deionized water. After freeze-drying, hot press and immersing in an electrolyte containing lithium ions, NH2-UIO-66@BC composite aerogel electrolyte is obtained.
Incorporating MOFs into battery electrolytes can be realized by either grafting MOFs onto separators (e.g., coating and filtration) or dispersing them in gel electrolytes. However, uniform dispersion of MOFs on separators (or in QSSEs) should be guaranteed to fully harvest the merits of MOF-based separators for LMBs.
Activation of MOF-based separators
Aside from tunable structures, the numerous open metal sites (OMSs) of MOFs used in separators are also pivotal to improving electrochemical performance in batteries. OMSs of MOFs can anchor anions, catalyze and adsorb by-products, suppress shuttle effects, and improve ion mobility. Increasing the number of OMSs can significantly increase the electrochemical performance of MOF-based separators. Activating MOFs, therefore, should be considered to create more OMSs. The common methods (e.g., thermal activation and chemical activation) to activate MOFs for separators/QSSEs will be narrated in this section.
Thermal activation
Lu et al.[152] obtained UIO-66 with more Lewis acid sites and high activation area through thermal activation [Figure 7E]. UIO-66 can be thermally activated without collapsing the initial structure, and the thermal activation condition of UIO-66 was optimized to 300 °C for 24 h. The thermally activated UIO-66 has an increased number of active sites, enabling GPE with higher ion conductivity and cation transference numbers for QSSLMB. Férey et al.[194] utilized thermal activation to increase the specific surface area and volume of MIL-101 (Cr) micropores, resulting in excellent adsorption performance. Xu et al.[195] used a simple thermal activation method to clean the coordination water molecules inside the framework of synthesized Mn-MOF-1 with methanol, and then heated it at 120 °C to obtain an activated sample with more OMSs. MOFs with poor stability can be thermally activated in a protective atmosphere. Zhang et al.[196] conducted thermal activation under different protective atmospheres, and found that using CO resulted in the highest activity of CuBTC [1,3,5-benzenetricarboxylic acid (BTC)], forming more pores and effective
Chemical activation
MOF-based separators can increase the transference number of cations and ionic conductivity, which can be realized via chemical activation of MOFs by grafting anionic organic ligands[197]. Fu et al.[153] replaced BDC with 2-aminoterepthalic acid when synthesizing UIO-66, producing NH2-UIO-66 with smaller pores [Figure 7F], larger specific surface area, higher ion conductivity [Figure 7G], and more Lewis acid sites, effectively accelerating ion conduction and inhibiting dendrite growth, enabling improved performance in LMBs. Planchais et al.[198] introduced -COOH groups into UIO-66 to improve the hydrophilicity of UIO-66, resulting in better proton conductivity. Yang et al.[199] also modified commercial glass fibers (GF) with carboxyl functionalized UiO-66-(COOH)2 (UC), rendering a novel ion selective separator (UC/GF) that suppresses polyiodides shuttle and improves ionic conductivity in zinc iodine batteries. Another common chemical activation method is to introduce sulfonic acid groups on MOFs. Ruan et al.[200] replaced H2BDC with H2BDC-SO3Na during the synthesis of UIO-66, successfully preparing UiO-66-SO3H with more Lewis acid sites and a higher number of micropores, offering more active sites. In addition to introducing active functional groups, metalizing MOFs is also viable for chemical activation. By adding a mixed solution of FeCl3 and DMF to MOF-525 and MOF-545 and subsequent heating, Morris et al.[201] successfully prepared metalized MOF-525-Fe and MOF-545-Fe, with increased porosity and extremely high stability while retaining the properties of the original MOFs. Kim et al.[202] also exposed the active sites of HKUST-1 and Cu-MOF-2 by immersing in MC, which can replace impurities coordinating the active sites, thus exposing the active sites of HKUST-1 and Cu-MOF-2 after the self-decomposition of MC.
Chemical activation of MOFs can not only remove guest molecules from the active site, but also introduce defects on the organic ligand. Controlling the generation of ligand defects within UiO-66 can increase the ionic conductivity by nearly three orders of magnitude[163], emphasizing the importance of chemical activation of MOFs to design superior QSSE. In addition to thermal activation and chemical activation, other methods to activate MOFs include solvent exchange[203,204], freeze-drying[205,206], supercritical CO2 exchange[206], etc.[207], offering new possibilities of MOF modification toward favorable MOF-based separators or QSSEs.
Challenges and strategies in industrial scale-up of MOFs
Although substantial research has been dedicated to MOFs[208-212], there are limited options for commercially available MOFs. Key considerations for scalable MOF production include the selection of metal ions and organic linkers, the use of industrial hydrothermal reactors, and adoption of green solvents and synthesis methods. For large-scale MOF synthesis, choosing metal ions that are both accessible and cost-effective is critical, with metal oxides and sulfates generally preferred due to their stability, while chlorides and nitrates pose corrosion and safety risks, respectively. Simple organic linkers such as terephthalic acid are also advantageous for their availability and cost-efficiency[213]. The most commonly used hydrothermal or solvothermal synthesis is highly suitable for scaling and adaptable for industrial continuous stirred tank reactors, as demonstrated by McKinstry et al., who achieved a production rate of approximately 1,000 kg m-3 per day of high-quality MOF-5 using a scalable system[214]. However, this approach often requires large amounts of solvent. Mechanochemistry presents a promising alternative, producing MOFs through mechanical mixing with minimal or no solvent, which is both environmentally friendly and energy efficient. Klimakow et al. produced copper-based MOFs (HKUST-1 and MOF-14) using a ball mill and minimal ethanol, while Tanaka et al. created ZIF-8 via solvent-free grinding, thus reducing potential impurities[215,216]. When solvents are required, green options such as water are preferred to organic solvents to reduce toxicity; for example, Chen et al. synthesized a zirconium-based MOF (UiO-66-NO2) in water, and Cadot et al. achieved a high-quality nickel-based MOF with a 92% yield in an aqueous solution, yielding 680 kg m-3 per day[217,218]. Overall, careful selection of metal sources, synthesis techniques, and solvent types will be essential for scalable, cost-effective, and sustainable MOF production, enabling practical industrial applications.
THE APPLICATION OF MOF-BASED SEPARATORS IN QSSLMBS
Incorporating MOFs into separators addresses key challenges such as improving ionic conductivity[193,219], enhancing mechanical stability[220,221], and suppressing dendrite formation[222,223], thereby boosting the performance and safety of LMBs[220,224]. This section explores the use of pristine MOFs[220,225], MOF composites[226,227], and MOF derivatives[228,229] as separators in different types of QSSLMBs, highlighting their distinct advantages and recent advances.
Original MOF-based separators
Pristine MOFs, used as separators, offer high porosity and large surface area, facilitating efficient
Figure 8. (A) Schematic representation of Li+ transportation through MIL-101(Cr)/PP separator; (B) Schematic illustration for the configuration of the designed “Li+ desolvated electrolyte”; (C) The linear sweep voltammetry (LSV) curves of typical “Li+ solvated ether-based electrolytes” and “desolvated electrolyte”; (D) The discharge capacity against cycle number collected from Li//NCM-811 full-cells using “Li+ desolvated electrolyte”; (E and F) Desolvation energy of Li(EC)4+ to Li(EC)3+ and EC molecule in bulk LE and UiO-66 pores, respectively; (G) The UiO-66-modified PP separator for Li-S batteries; (H) Geometries of atomic model configurations and (I) corresponding adsorption energy between polysulfides and UiO-66; (J) Molecular surface electrostatic potential (ESP) of UiO-66 and polysulfides; (K) The HKUST-1-modified GF separator for Li-O2 batteries. (A) is quoted with permission from Li et al.[230]; (B-D) from Chang et al.[231]; (E and F) from Sheng et al.[232]; (G-J) from Fan et al.[235]; (H) from Fan et al.[238]. EC: Ethylene carbonate; GF: glass fibers.
Original MOFs have been demonstrated to significantly expand the electrochemical window, enabling their stable operation in high-voltage batteries such as Li//NCM (lithium nickel manganese cobalt oxides) batteries[231-234] . Chang et al.[231] reported a novel LE comprising desolvated Li+ (referred to as “desolvated Li+ electrolyte”) by exploring interactions between Li+ and TFSI- ions with dimethoxyethane (DME) solvent in the narrow (~2.9 Å) channels of ZIF-7 MOF. Unlike conventional LEs, this novel electrolyte consists of a “frozen-like” inactive solvent and crystalline lithium salt, primarily composed of desolvated Li+ [Figure 8B]. As a result, the electrochemical stability of the desolvated Li+ electrolyte is significantly enhanced, extending from 3.8 V to 4.5 V [Figure 8C]. High-voltage LMBs (LiNi0.8Co0.1Mn0.1O2//Li) using this electrolyte exhibit excellent retained capacity 170 mAh g-1 over 200 cycles [Figure 8D]. Remarkably, the cathode-electrolyte interphase layer is barely detectable on the NCM-811 cathode surface, likely due to the absence of free solvent in the desolvated Li+ structure.
To gain deeper insight into the desolvation mechanism and its role in stabilizing Li0, Sheng et al.[232] employed density functional theory (DFT) calculations to model the dissociation and reduction of solvated Li+ within UiO-66 MOF channels and bulk LE [LiPF6 in ethylene carbonate (EC)]. The energy required to dissociate Li(EC)4+ to Li(EC)3+ and one EC molecule on UiO-66 is approximately 16.8 kJ mol-1, significantly lower than the corresponding energy in bulk electrolyte (50.2 kJ mol-1) [Figure 8E]. This suggests that
Original MOFs are also widely used as effective separators in Li-S batteries[235-237]. Fan et al. synthesized uniform UiO-66 (Zr) MOF particles via solvothermal reaction for Li-S batteries[235] [Figure 8G]. UiO-66 effectively mitigates the shuttle effect due to its strong physical and chemical interactions with dissolved polysulfides. Li-S cells with UiO-66-coated PPSs maintained a specific capacity of 586 mAh g-1 after 500 cycles at 0.5 C, with a Coulombic efficiency near 100%. DFT simulations reveal that Li2Sn (4 < n < 8) species penetrate UiO-66’s ~9.1 Å pores and interact with the pore walls, reducing pore size and preventing further polysulfide infiltration [Figure 8H]. Adsorption energy calculations indicate strong chemisorption, with values below -2 eV for all polysulfides except S8 [Figure 8I]. This is attributed to strong interactions between Li+ ions and oxygen atoms in UiO-66, as well as between S atoms and MOF hydrogen atoms. Electrostatic potential (ESP) mapping confirms these interactions, showing Coulombic attraction between Li+ and
MOFs with small pore sizes have also emerged as effective filtration materials for suppressing anion shuttling in lithium-oxygen (Li-O2) batteries. For example, Fan et al.[238] fabricated a HKUST-1 MOF-coated GF separator to inhibit redox-active ion transport associated with I-/I3- species in Li-O2 cells [Figure 8K]. The three-dimensional stacking and interwoven structure of HKUST-1 serve as a physical barrier against anion migration. Additionally, HKUST-1 exhibits multiple Lewis acid sites, while I-/I3- species are characterized as Lewis bases. This combination of physical barrier modification and Lewis acid-base interactions effectively impedes the transport of I-/I3- ions while preserving Li+ conductivity and ensuring the chemical stability of the separator. The HKUST-1/GF separator demonstrates high ionic conductivity
The varying pore sizes and compositions of original MOFs significantly affect the ionic conductivity of QSSEs in LMBs. During the synthesis of Mg-based MOFs, Aubrey et al.[239] modified the linkers, producing Mg2(dobdc) and Mg2(dobpdc) with pore sizes of 13 Å and 21 Å, respectively [Figure 9]. Mg2(dobpdc) shows an ionic conductivity of ~10-4 S cm-1, more than double that of Mg2(dobdc), due to its larger pores and higher surface area, which enhance Li salt absorption and inhibit side reactions. This highlights the critical role of pore size and composition in improving ionic conductivity in MOF-based QSSEs. Additionally, ionic conductivity is influenced by the MOF framework’s structural properties and interfacial effects from trace solvents retained in the pores[240,241].
Figure 9. Pore structure and surface modification of Mg2(dobdc) and Mg2(dobpdc) as QSSEs. This figure is quoted with permission from Aubrey et al.[239]. QSSEs: Quasi-solid-state electrolytes.
MOF composites-based separators
MOF composites combining MOFs with other materials such as polymers or inorganic particles leverage synergistic effects to optimize ionic conductivity, mechanical strength, and thermal stability, providing enhanced performance for QSSLMBs. For example, incorporating MOFs into polymer matrices has significantly improved separator performance[242-246]. Lu et al.[242] developed a hybrid separator by integrating a bifunctional MOF material (MOF-2) into a PEO matrix. MOF-2, prepared from two different functionalized UiO-66 materials containing carboxyl and amine groups, respectively, in combination with PEO [Figure 10A] showed higher ionic conductivity (5.20 × 10-4 S/cm) than pristine PEO (1.11 × 10-4 S/cm). This improvement is likely due to the presence of MOFs, which disrupt the arrangement of PEO chains, reducing the crystallinity of the electrolyte. Additionally, MOFs can serve as supplementary ion channels, enhancing lithium-ion transport. Interestingly, the ionic conductivity of QSSE with MOF-2 surpassed that of QSSE containing individual MOFs such as UiO-66-COOH or UiO-66-NH2. In MOF-2, amide bonds formed between acid and amino groups create long MOF chains within the QSSE, facilitating rapid ion transport through a network where the polymer serves as the primary conduction channel. As such, LiFePO4||Li full cells assembled with this composite separator showed 98.45% capacity retention at
Figure 10. (A) Bifunctional MOF doped PEO composite electrolyte (PEO-MOF-2) for fast ionic transport; (B) Cycling stability of full cells with PEO-MOF-2 at 1 C; (C) SEM images of the Co3O4-350 polyhedron and Co3O4-350/PI/LLZO separator; (D) The cycling performances of Li-S cells using varied separator at room temperature; (E) Schematic illustration of Ni-MOF/MWCNT-coated PE separator for blocking lithium polysulfide migration to the lithium anode in the Li-S cell; (F) Charge and discharge curves of the Li-S cell with Ni-MOF/MWCNT-coated separator at 0.2 C rate. (A and B) are quoted with permission from Lu et al.[242]; (C and D) from Zhou et al.[247]; and (E and F) from Lee et al.[253]. MOF: Metal-organic framework; PEO: polyethylene oxide; MWCNTs: multi-walled carbon nanotubes; SEM: scanning electron microscope; PE: polyethylene.
Besides polymer-MOF composites, inorganic-MOF composites have also been explored for their superior mechanical and thermal properties[247,248]. Suriyakumar et al.[248] coated a mixture of UiO-66-NH2 and SiO2 particles on a commercial Celgard 2320 membrane, enhancing thermal stability, wettability, ionic conductivity, and electrochemical window, producing higher discharge capacity in Li-S cells. This is attributed to the electrostatic and/or hydrogen-bonding interactions between the polysulfides and
Additionally, MOFs combined with carbon-based materials have shown promising results in enhancing both mechanical properties and lithium-ion transport for LMBs[227,249-254]. Bai et al.[227] created a separator based on Cu-MOF@Graphene oxide (HKUST-1@GO), acting as an effective ion sieve in Li-S batteries that selectively screened Li+ ions while preventing polysulfide shuttling. The three-dimensional channel structure of HKUST-1@GO contains highly ordered micropores with size (approximately 9 Å) significantly larger than lithium polysulfides (Li2Sn, 4 < n ≤ 8) (2.09-2.39 Å), making the separator highly suitable for adsorbing and blocking polysulfides. The Li-S battery with this MOF-based separator exhibits a low-capacity decay rate (0.019% per cycle over 1,500 cycles), with virtually no capacity loss after the first 100 cycles. Lee et al.[253] also used multi-walled carbon nanotubes (MWCNTs) combined with Ni-based MOF to create separator membranes for Li-S batteries [Figure 10E]. Ni-MOF particles effectively block lithium polysulfide shuttling due to strong interactions, while MWCNTs allow the reuse of reactive intermediates due to their high conductivity. Specifically, the Lewis acidic Ni2+ sites in Ni-MOF foster strong interactions with polysulfide anions, whose lone electron pairs impart soft Lewis basicity. As a result, Ni-MOF effectively traps lithium polysulfides through Lewis acid-base interactions. Additionally, MWCNTs not only compensate for the low electronic conductivity of Ni-MOF and enhance the electronic conductivity of trapped lithium polysulfides for subsequent electrochemical reactions, but also act as a physical barrier against lithium polysulfide migration. These synergistic effects result in a high discharge capacity of 1,358 mAh g-1 at the initial cycle for Li-S batteries [Figure 10F].
Similar to original MOFs, MOF composite-based separators also demonstrate excellent electrochemical stability under high-voltage operation. Chang et al.[10] developed a separator based on CuBTC MOF and poly(sodium 4-styrenesulfonate). Using advanced space-resolution spectroscopies, the prepared electrolyte exhibited significant aggregation beyond the standard saturation state (exceeding the lithium salt solubility limit) and primarily contained solvent-depleted contact ion pairs [Figure 11A]. This unique electrolyte structure significantly reduces solvent decomposition, resulting in exceptional electrochemical stability exceeding 5.4 V versus Li/Li+ [Figure 11B]. Consequently, electrolyte decomposition on cathode was significantly suppressed while a thin and stable SEI layer was simultaneously formed on lithium metal anode during cycling, rendering high-voltage Li//NCM811 with long-term cycling performance, maintaining 170 mAh g-1 after 400 cycles [Figure 11C].
Figure 11. (A) The proposed design idea of further depleting solvent molecules within Li+ solvation sheath; (B) LSV curves of typical electrolyte and the prepared solvent-depleted electrolyte in CuBTC MOF-PSS; (C) Cycling performance of the Li//NCM-811 half-cell using the MOF-based electrolyte; (D) Molecular structures at different angles and the sizes of Ru(acac)3; (E and F) Schematic structures of UiO-66-(COOLi)2 and DMSO located in UiO-66-(COOLi)2. (A-C) is quoted with permission from Chang et al.[10]; (D-F) from Wang et al.[255]. MOF: Metal-organic framework; LSV: linear sweep voltammetry; DMSO: dimethyl sulfoxide; PSS: polystyrene sulfonate.
MOF composite-based separators have also been successfully applied in Li-O2 batteries, delivering remarkable performance enhancements. For instance, Wang et al.[255] synthesized a MOF gel by combining UiO-66 with Li-COOH and coated it onto a PPS for Ru(acac)3@Li-O2 batteries. Through size and kinetic simulations, the pore size distribution of the gel MOF [UiO-66-(COOLi)2] was primarily below 6.5 Å and between 11.0-13 Å, which is mostly smaller than the 12.6 Å length of Ru(acac)3 [Figure 11D]. This size exclusion effect effectively inhibits the Ru(acac)3 transport. When Ru(acac)3 moves through the smaller channels, the polar -COO- groups within the MOF tend to adsorb polar dimethyl sulfoxide (DMSO) molecules while repelling nonpolar Ru(acac)3 molecules[255] [Figure 11E and F]. Simultaneously, the negatively charged -COO- groups in the MOF channels facilitate the uniform transport of lithium ions, thereby improving the battery’s overall performance. Notably, the Ru(acac)3@Li-O2 battery equipped with the MOF gel separator exhibited an ultralong cycle life of 410 cycles at a current density of 0.5 A g-1, significantly superior to batteries using conventional Celgard separators.
Figure 12. (A) Schematic illustration of the synthesis process of DSxHNC and DSxHNC/KB@PPS [ketjen black (KB)] and schematic representation of L-S battery employing the DSxHNC/KB@PPS; (B) Galvanostatic charge/discharge voltage profiles of
MOF derivatives-based separators
MOF derivatives, which include chemically modified or transformed MOFs into other functional materials, represent an advanced approach in separator design. These derivatives often exhibit increased ionic conductivity, improved thermal stability, light weight, and high porosity addressing specific challenges in LMBs, especially Li-S batteries. Converting MOFs into porous carbon or metal oxide materials is a common strategy.
For example, Guang et al.[256] prepared double-shelled hollow N-doped porous carbon polyhedrons (DSxHNC) derived from ZIF-8@ZIF-67 core-shell nanocrystals by high-temperature treatment
Li et al. enhanced the separation efficiency of Celgard 2325 membranes by NiCo2S4@C[257] [Figure 12D], which was formed through heat treatment of Ni-Co-PTA in Ar gas and subsequent solvothermal reaction with Na2S. The highly porous NiCo2S4@C nanocomposite not only possesses exceptional physical adsorption capabilities but also exhibits excellent polar chemical adsorption for Li polysulfides through interactions between the Ni and Co cations and S anions. Moreover, the NiCo2S4@C composite features three-dimensional electrical conductivity, abundant porosity, and a high specific surface area, significantly improving ionic/electronic conductivity and Coulombic efficiency. As such, NiCo2S4@C separators ensured Li-S batteries with a high initial capacity of 880 mAh g-1 at 0.5 C [Figure 12E] and excellent cycling stability, maintaining a capacity of up to 700 mAh g-1 after 200 cycles.
Additionally, other MOF derivatives have been synthesized and applied as effective separators in QSSLMBs. These include Co-based MOF-derived vertical Co9S8 hollow nanowall arrays grown on a Celgard separator[229], oxygenated MOF-derived nitrogen-doped microporous carbon (OMNC)[258], and Ni-MOF-derived bamboo-like conductive carbon nitride[259]. All these materials share high porosity, excellent electrical conductivity, and superior ion transport properties, making them highly advantageous for use as separators in QSSLMBs. Despite these promising characteristics, research and application of MOF derivative-based separators in other lithium battery systems, such as Li-O2 and high-voltage Li//NCM cells, remain limited. A comprehensive and systematic analysis of the challenges and advantages associated with using MOF derivatives in these advanced battery systems is essential to accelerate their practical implementation in the near future.
CONCLUSIONS AND OUTLOOKS
This review provides a comprehensive overview of the development of MOF-based QSSEs in recent years. In addition to the fundamental aspects of MOF-based QSSEs (application concepts, compositions, Li-ion transport mechanisms, and typical fabrication methods), the recent progress of three main types of
Comparison of advantages and disadvantages of different types of MOF-based QSSEs
Type of MOF-based QSSEs | Advantages | Disadvantages |
Original MOF-based separators | • Various structures and chemical compositions • High porosity • Wide electrochemical window • High mechanical strength • High thermal stability | • Low flexibility • Complex manufacturing process |
MOF composites-based separators | • Good interface compatibility • Good solubility of lithium salts • High flexibility | • Low ionic conductivity • Relatively low mechanical strength • Relatively low oxidation potential |
MOF derivatives-based separators | • High ionic and electrical conductivity • Wide voltage window • High lithium-ion transference number | • Complex manufacturing process • Relatively low mechanical strength • Relatively low porosity |
Summary of original MOF-based separators
MOFs | Lithium salts | Type of batteries | σ (mS cm-1) | Electrochemical window (V) | Initial capacity (a mAh g-1 _ b C rate) | Capacity retention (a%_b cycles) | References |
MIL-101(Cr) | LiPF6 | Li//LFP | - | - | 71_5 | 99_200 | [230] |
UiO-66 | LiTFSI | Li-S | - | - | 587_0.5 | 99.85_500 | [235] |
UiO-66 | LiTFSI | Li-S | - | - | 1239_0.2 | 84_200 | [236] |
UiO-66-NH2 | LiClO4 | Li//LFP | 0.207 | 4.52 | 136_1 | 97_500 | [237] |
UiO-66 | LiOtBu | - | 0.018 | - | - | - | [240] |
MIL-121 | LiClO4 | 0.091 | - | - | - | [241] | |
MOF-688 | LiTFSI | - | 0.34 | - | - | - | [102] |
UiO-66 | LiPF6 | Li//LFP | 0.06 | 5.2 | 127_0.2 | 88.2_100 | [161] |
MIL-100(Fe) | LiClO4 | - | 0.9 | - | - | - | [177] |
UiO-67 | LiClO4 | - | 0.65 | - | - | - | [177] |
UiO-66 | LiClO4 | - | 0.18 | - | - | - | [177] |
MOF-5 | LiClO4 | - | 0.13 | - | - | - | [177] |
HKUST-1 | LiClO4 | - | 0.38 | - | - | - | [177] |
Summary of MOF composite-based separators
MOFs | Other materials | Type of batteries | σ (mS cm-1) | Electrochemical window (V) | Initial capacity a (mAh g-1 _ b C rate) | Capacity retention (a%_b cycles) | References |
HKUST-1 | GO | Li-S | - | - | 1126_0.5 | 72_100 | [227] |
UiO-66-NH2@UiO-66-COOH | PEO | Li//LFP | 0.52 | 5 | 152.3_1 | 98.45_100 | [242] |
HKUST-1 | polystyrene sulfonate (PSS) | Li-S | 0.0105 | - | 1278_0.5 | 60.6_500 | [243] |
UiO-66 | Nafion | Li-S | - | - | 1127.4_0.1 | 75.5_200 | [244] |
Cu-BTC | NSP | Li-S | - | - | 1279_1 | 78.2_1000 | [245] |
UiO-66 | SO3Li | Li-S | - | - | 1020_0.5 | 56.8_500 | [246] |
Co-MOF | PI/LLZO | Li-S | - | - | 1132_0.1 | 55.6_200 | [247] |
UiO-66-NH2 | SiO2 | Li-S | - | - | 1400_0.1 | 42.9_100 | [248] |
Zn-MOF | GO | Li-S | - | - | 1118_1 | 70_200 | [249] |
Co(acac)2 | PAN | Li-S | - | - | 1102_0.2 | 91.5_50 | [250] |
Ni-MOF | MWCNT | Li-S | - | - | 1183_0.2 | 87.1_300 | [253] |
N-Ti3C2 | MXene | Li-S | - | - | 1018_0.5 | 70.3_500 | [254] |
Summary of MOF derivative-based separators
MOFs | MOF derivatives | Type of batteries | σ (mS cm−1) | Electrochemical window (V) | Initial capacity (a mAh g-1 _ b C rate) | Capacity retention (a%_b cycles) | References |
Co-MOF | Co9S8 nanowall | Li-S | - | - | 1385_0.1 | 85.9_200 | [229] |
ZIF-8@ZIF-67 | DSxHNC | Li-S | - | - | 1592.9_0.2 | 66_100 | [256] |
Ni-Co-PTA MOF | NiCo2S4@C | Li-S | - | - | 1000_0.5 | 83_100 | [257] |
ZIF-8 | OMNC | Li-S | - | - | 1257.1_0.5 | 59_300 | [258] |
Performance advantages and contributions
MOF-based separators offer distinct advantages that overcome key challenges in QSSLMBs. These separators serve as robust physical barriers that effectively suppress dendrite formation on lithium metal anodes, mitigating risks of short circuits and enhancing battery durability. Their high surface area and tunable pore structures facilitate efficient ion transport, resulting in improved ionic conductivity and enhanced electrochemical performance. Original MOF-based separators have high ionic conductivity and good thermal stability due to the excellent physical and chemical adsorption properties of MOFs, which can trap trace LE within the nano-sized pores. MOF composite-based separators show excellent Li dendrite suppression and good interface compatibility with electrode surfaces. Additionally, MOF-derived materials provide versatility in composition and functionality, allowing for tailored designs that optimize the ionic conductivity and interface compatibility between separators and electrode materials, thereby maximizing battery efficiency.
Challenges and future directions
Despite the significant progress, several challenges remain to be addressed. The nature of trace solvents, which do not enter MOF pore structures and are highly flammable, presents challenges. Developing methods to balance these trace solvents in the system without affecting battery performance is an important future direction. Additionally, lithium dendrite formation and growth may occur during prolonged battery cycling, particularly at high current densities. The accumulation of lithium dendrites and the expansion of cracks can happen at MOF grain boundaries, surface defects, and connecting pores. MOF composite-based QSSEs exhibit high flexibility and good interface compatibility, but their thermal stability and low ionic conductivity limit their application in high-energy-density batteries. Although MOF derivative-based QSSEs have good electrochemical properties, the complex fabrication methods, low mechanical stability, decreased pore size, and undesirable interactions between LEs and by-products from MOF derivative synthesis make it challenging to design and apply them to specific LMBs. Furthermore, challenges remain in the production of MOFs for QSSEs. The cost of metal salts and linkers is a notable issue. The use of environmentally unfriendly solvents or cumbersome fabrication processes hinders large-scale production of MOFs and MOF-based QSSEs.
Future outlook and research opportunities
With outstanding advantages in safety and high energy density, MOF-based QSSEs show great promise for LMBs. Additionally, due to their flexibility and portability, these QSSEs can be applied in specific fields such as mobile electronic devices, drones, and more. Currently, MOF-based QSSLMBs are still in the early stages of research and development, and this new technology is not yet suitable for mass production. The following are deeper discussions on future directions for the development and commercialization of these batteries:
• Exploration of novel MOF structures and compositions: Exploring novel MOF structures and compositions is critical for improving the performance and cycling stability of batteries. Future research should focus on developing MOFs with tailored pore sizes, surface functionalities, and ion-conducting frameworks to address specific challenges and improve the performance of various LMBs, such as
• Development of innovative synthesis techniques: Conventional MOF synthesis often involves complex procedures and hazardous solvents. Future efforts should prioritize the development of cost-effective, scalable, and environmentally sustainable synthesis methods. Green synthesis approaches, such as
• In-depth study of Li-ion transport mechanisms: The Li-ion transport mechanism in MOF-based QSSEs directly affects battery performance and lifespan. Different types of MOFs have distinct Li-ion transport pathways. While some reports have identified main ion transport pathways in MOF-based QSSEs, the ion transport mechanisms will be more complex when MOFs are composited. This requires advanced methods for analysis and evaluation, such as MD simulations, solid-state NMR, in-situ X-ray photoelectron spectroscopy, in-situ Raman spectroscopy, and more.
• Enhancing the ionic conductivity of MOF-based QSSEs: Despite studies focusing on improving Li+ conductivity, the room-temperature conductivity in most MOF-based QSSEs remains relatively low
• Enhancing cost-effectiveness and scalability: Emphasizing affordable raw materials and cost-effective synthesis techniques will enhance the commercial viability of MOF-based QSSRs. Exploring the potential and compatibility of MOFs in various battery systems can expand their applications. Collaborative efforts between academia and industry could facilitate the transition from laboratory-scale research to commercial implementation.
DECLARATIONS
Authors’ contributions
Conceived and wrote the manuscript: Nguyen, M. H.; Niu, C.; Ngo, N. M.
Reviewed the manuscript and acquired funding: Chen, J.; Park, S.
Availability of data and materials
Not applicable.
Financial support and sponsorship
This work was supported by the National Research Foundation of the Republic of Korea (Project. No. RS-2023-00217581), Samsung Research Funding & Incubation Center of Samsung Electronics (Project No. SRFC-MA2202-04), the National Natural Science Foundation of China (No. 52202320), the Shandong Excellent Young Scientists Fund Program (Overseas) (2023HWYQ-060), and the Fundamental Research Funds for the Central Universities (No. 202201013153).
Conflicts of interest
All authors declared that there are no conflicts of interest.
Ethical approval and consent to participate
Not applicable.
Consent for publication
Not applicable.
Copyright
© The Author(s) 2025.
REFERENCES
2. Goodenough, J. B.; Park, K. S. The Li-ion rechargeable battery: a perspective. J. Am. Chem. Soc. 2013, 135, 1167-76.
3. Tarascon, J. M.; Armand, M. Issues and challenges facing rechargeable lithium batteries. Nature 2001, 414, 359-67.
4. Aravindan, V.; Gnanaraj, J.; Madhavi, S.; Liu, H. K. Lithium-ion conducting electrolyte salts for lithium batteries. Chem. Eur. J. 2011, 17, 14326-46.
5. Li, M.; Wang, C.; Chen, Z.; Xu, K.; Lu, J. New concepts in electrolytes. Chem. Rev. 2020, 120, 6783-819.
6. Qian, J.; Henderson, W. A.; Xu, W.; et al. High rate and stable cycling of lithium metal anode. Nat. Commun. 2015, 6, 6362.
7. Chang, Z.; Qiao, Y.; Deng, H.; Yang, H.; He, P.; Zhou, H. A stable high-voltage lithium-ion battery realized by an in-built water scavenger. Energy. Environ. Sci. 2020, 13, 1197-204.
8. Jiao, S.; Ren, X.; Cao, R.; et al. Stable cycling of high-voltage lithium metal batteries in ether electrolytes. Nat. Energy. 2018, 3, 739-46.
9. Zheng, J.; Engelhard, M. H.; Mei, D.; et al. Electrolyte additive enabled fast charging and stable cycling lithium metal batteries. Nat. Energy. 2017, 2, 17012.
10. Chang, Z.; Qiao, Y.; Yang, H.; et al. Beyond the concentrated electrolyte: further depleting solvent molecules within a Li+ solvation sheath to stabilize high-energy-density lithium metal batteries. Energy. Environ. Sci. 2020, 13, 4122-31.
11. Lu, Y.; Tu, Z.; Archer, L. A. Stable lithium electrodeposition in liquid and nanoporous solid electrolytes. Nat. Mater. 2014, 13, 961-9.
12. Wang, Z.; Tan, R.; Wang, H.; et al. A metal-organic-framework-based electrolyte with nanowetted interfaces for high-energy-density solid-state lithium battery. Adv. Mater. 2018, 30, 1704436.
13. Chang, Z.; Yang, H.; Zhu, X.; He, P.; Zhou, H. A stable quasi-solid electrolyte improves the safe operation of highly efficient lithium-metal pouch cells in harsh environments. Nat. Commun. 2022, 13, 1510.
14. Furukawa, H.; Cordova, K. E.; O’Keeffe, M.; Yaghi, O. M. The chemistry and applications of metal-organic frameworks. Science 2013, 341, 1230444.
15. Kitagawa, S.; Kitaura, R.; Noro, S. Functional porous coordination polymers. Angew. Chem. Int. Ed. 2004, 43, 2334-75.
16. Cui, Y.; Li, B.; He, H.; Zhou, W.; Chen, B.; Qian, G. Metal-organic frameworks as platforms for functional materials. Acc. Chem. Res. 2016, 49, 483-93.
17. Wang, L.; Han, Y.; Feng, X.; Zhou, J.; Qi, P.; Wang, B. Metal-organic frameworks for energy storage: batteries and supercapacitors. Coord. Chem. Rev. 2016, 307, 361-81.
18. Yaghi, O. M.; Li, G.; Li, H. Selective binding and removal of guests in a microporous metal-organic framework. Nature 1995, 378, 703-6.
19. Vaitsis, C.; Sourkouni, G.; Argirusis, C. Metal organic frameworks (MOFs) and ultrasound: a review. Ultrason. Sonochem. 2019, 52, 106-19.
20. Lee, J.; Choi, I.; Kim, E.; Park, J.; Nam, K. W. Metal-organic frameworks for high-performance cathodes in batteries. iScience 2024, 27, 110211.
21. Zheng, Y.; Zheng, S.; Xue, H.; Pang, H. Metal-organic frameworks for lithium-sulfur batteries. J. Mater. Chem. A. 2019, 7, 3469-91.
22. Chu, Z.; Gao, X.; Wang, C.; Wang, T.; Wang, G. Metal-organic frameworks as separators and electrolytes for lithium-sulfur batteries. J. Mater. Chem. A. 2021, 9, 7301-16.
23. Chae, S.; Ko, M.; Kim, K.; Ahn, K.; Cho, J. Confronting issues of the practical implementation of Si anode in high-energy lithium-ion batteries. Joule 2017, 1, 47-60.
24. Zhou, Y.; Long, J.; Li, Y. Ni-based catalysts derived from a metal-organic framework for selective oxidation of alkanes. Chin. J. Catal. 2016, 37, 955-62.
25. Eddaoudi, M.; Moler, D. B.; Li, H.; et al. Modular chemistry: secondary building units as a basis for the design of highly porous and robust metal-organic carboxylate frameworks. Acc. Chem. Res. 2001, 34, 319-30.
26. Sun, L.; Campbell, M. G.; Dincă, M. Electrically conductive porous metal-organic frameworks. Angew. Chem. Int. Ed. 2016, 55, 3566-79.
27. Xie, Z.; Cao, B.; Yue, X.; et al. Metal organic frameworks-based cathode materials for advanced Li-S batteries: a comprehensive review. Nano. Res. 2024, 17, 2592-618.
28. Ren, J.; Huang, Y.; Zhu, H.; et al. Recent progress on MOF-derived carbon materials for energy storage. Carbon. Energy. 2020, 2, 176-202.
29. Babkova, T.; Kiefer, R.; Le, Q. B. Hybrid electrolyte based on PEO and ionic liquid with in situ produced and dispersed silica for sustainable solid-state battery. Sustainability 2024, 16, 1683.
30. Yang, S.; Zhang, Z.; Lin, J.; et al. Recent progress in quasi/all-solid-state electrolytes for lithium-sulfur batteries. Front. Energy. Res. 2022, 10, 945003.
31. Reinoso, D. M.; de, T. G. C.; Fernández-Ropero, A. J.; Levenfeld, B.; Várez, A. Advancements in quasi-solid-state Li batteries: a rigid hybrid electrolyte using LATP porous ceramic membrane and infiltrated ionic liquid. ACS. Appl. Energy. Mater. 2024, 7, 1527-38.
32. Xin, S.; You, Y.; Wang, S.; Gao, H.; Yin, Y.; Guo, Y. Solid-state lithium metal batteries promoted by nanotechnology: progress and prospects. ACS. Energy. Lett. 2017, 2, 1385-94.
33. Zhou, D.; Shanmukaraj, D.; Tkacheva, A.; Armand, M.; Wang, G. Polymer electrolytes for lithium-based batteries: advances and prospects. Chem 2019, 5, 2326-52.
34. Vineeth, S.; Soni, C. B.; Sungjemmenla; et al. A quasi-solid state polymer electrolyte for high-rate and long-life sodium-metal batteries. J. Energy. Storage. 2023, 73, 108780.
35. Xu, K. Electrolytes and interphases in Li-ion batteries and beyond. Chem. Rev. 2014, 114, 11503-618.
36. Nitta, N.; Wu, F.; Lee, J. T.; Yushin, G. Li-ion battery materials: present and future. Mater. Today. 2015, 18, 252-64.
37. Zhang, X.; Cheng, X.; Chen, X.; Yan, C.; Zhang, Q. Fluoroethylene carbonate additives to render uniform Li deposits in lithium metal batteries. Adv. Funct. Mater. 2017, 27, 1605989.
38. Manthiram, A. A reflection on lithium-ion battery cathode chemistry. Nat. Commun. 2020, 11, 1550.
39. Goodenough, J. B.; Kim, Y. Challenges for rechargeable Li batteries. Chem. Mater. 2010, 22, 587-603.
40. Zhang, H.; Eshetu, G. G.; Judez, X.; Li, C.; Rodriguez-Martínez, L. M.; Armand, M. Electrolyte additives for lithium metal anodes and rechargeable lithium metal batteries: progress and perspectives. Angew. Chem. Int. Ed. 2018, 57, 15002-27.
41. Cheng, X. B.; Zhang, R.; Zhao, C. Z.; Zhang, Q. Toward safe lithium metal anode in rechargeable batteries: a review. Chem. Rev. 2017, 117, 10403-73.
42. Lin, D.; Liu, Y.; Cui, Y. Reviving the lithium metal anode for high-energy batteries. Nat. Nanotechnol. 2017, 12, 194-206.
43. Lingappan, N.; Lee, W.; Passerini, S.; Pecht, M. A comprehensive review of separator membranes in lithium-ion batteries. Renew. Sustain. Energy. Rev. 2023, 187, 113726.
44. Valverde, A.; Gonçalves, R.; Silva, M. M.; et al. Metal-organic framework based PVDF separators for high rate cycling lithium-ion batteries. ACS. Appl. Energy. Mater. 2020, 3, 11907-19.
45. Zhao, R.; Liang, Z.; Zou, R.; Xu, Q. Metal-organic frameworks for batteries. Joule 2018, 2, 2235-59.
46. Wang, H.; Dai, H. Strongly coupled inorganic-nano-carbon hybrid materials for energy storage. Chem. Soc. Rev. 2013, 42, 3088-113.
47. Li, D.; Hu, H.; Chen, B.; Lai, W. Y. Advanced current collector materials for high-performance lithium metal anodes. Small 2022, 18, 2200010.
48. Zhao, E.; Luo, S.; Hu, A.; et al. Rational design of an in-build quasi-solid-state electrolyte for high-performance lithium-ion batteries with the silicon-based anode. Chem. Eng. J. 2023, 463, 142306.
49. Fang, L.; Sun, W.; Hou, W.; Mao, Y.; Wang, Z.; Sun, K. Quasi-solid-state polymer electrolyte based on highly concentrated LiTFSI complexing DMF for ambient-temperature rechargeable lithium batteries. Ind. Eng. Chem. Res. 2022, 61, 7971-81.
50. Wang, P.; He, X.; Lv, Z.; et al. Light-driven polymer-based all-solid-state lithium-sulfur battery operating at room temperature. Adv. Funct. Mater. 2023, 33, 2211074.
51. Manthiram, A.; Yu, X.; Wang, S. Lithium battery chemistries enabled by solid-state electrolytes. Nat. Rev. Mater. 2017, 2, 16103.
52. Dunn, B.; Kamath, H.; Tarascon, J. M. Electrical energy storage for the grid: a battery of choices. Science 2011, 334, 928-35.
53. Yao, X.; Huang, N.; Han, F.; et al. High-performance all-solid-state lithium-sulfur batteries enabled by amorphous sulfur-coated reduced graphene oxide cathodes. Adv. Energy. Mater. 2017, 7, 1602923.
54. Xiao, Q.; Yang, J.; Wang, X.; et al. Carbon-based flexible self-supporting cathode for lithium-sulfur batteries: progress and perspective. Carbon. Energy. 2021, 3, 271-302.
55. Zhai, Y.; Yang, G.; Zeng, Z.; et al. Composite hybrid quasi-solid electrolyte for high-energy lithium metal batteries. ACS. Appl. Energy. Mater. 2021, 4, 7973-82.
56. Li, Z.; Weng, S.; Fu, J.; et al. Nonflammable quasi-solid electrolyte for energy-dense and long-cycling lithium metal batteries with high-voltage Ni-rich layered cathodes. Energy. Storage. Mater. 2022, 47, 542-50.
57. Utpalla, P.; Mor, J.; Pujari, P. K.; Sharma, S. K. High ionic conductivity and ion conduction mechanism in ZIF-8 based quasi-solid-state electrolytes: a positron annihilation and broadband dielectric spectroscopy study. Phys. Chem. Chem. Phys. 2022, 24, 24999-5009.
58. Zhang, W.; Li, S.; Zhang, Y.; Wang, X.; Liu, J.; Zheng, Y. A quasi-solid-state electrolyte with high ionic conductivity for stable lithium-ion batteries. Sci. China. Technol. Sci. 2022, 65, 2369-79.
59. Yang, X.; Zhang, B.; Tian, Y.; et al. Electrolyte design principles for developing quasi-solid-state rechargeable halide-ion batteries. Nat. Commun. 2023, 14, 925.
60. Chen, Z.; Kim, G.; Kim, J.; et al. Highly stable quasi-solid-state lithium metal batteries: reinforced Li1.3Al0.3Ti1.7(PO4)3/Li interface by a protection interlayer. Adv. Energy. Mater. 2021, 11, 2101339.
61. Tian, R.; Jia, J.; Zhai, M.; et al. Design advanced lithium metal anode materials in high energy density lithium batteries. Heliyon 2024, 10, e27181.
62. Angarita-Gomez, S.; Balbuena, P. B. Insights into lithium ion deposition on lithium metal surfaces. Phys. Chem. Chem. Phys. 2020, 22, 21369-82.
63. Zinth, V.; von, L. C.; Hofmann, M.; et al. Lithium plating in lithium-ion batteries at sub-ambient temperatures investigated by in situ neutron diffraction. J. Power. Sources. 2014, 271, 152-9.
64. Koralalage, M. K.; Shreyas, V.; Arnold, W. R.; et al. Functionalization of cathode-electrolyte interface with ionic liquids for high-performance quasi-solid-state lithium-sulfur batteries: a low-sulfur loading study. Batteries 2024, 10, 155.
65. Liang, S.; Yan, W.; Wu, X.; et al. Gel polymer electrolytes for lithium ion batteries: Fabrication, characterization and performance. Solid. State. Ionics. 2018, 318, 2-18.
66. Li, W.; Li, H.; Liu, J.; et al. Systematic safety evaluation of quasi-solid-state lithium batteries: a case study. Energy. Environ. Sci. 2023, 16, 5444-53.
67. Liu, X.; Jia, H.; Li, H. Flame-retarding quasi-solid polymer electrolytes for high-safety lithium metal batteries. Energy. Storage. Mater. 2024, 67, 103263.
68. Lim, D.; Jeong, B.; Kim, H.; et al. Safety enhanced quasi-solid-state electrolyte based on thiol-ene click chemistry for rechargeable lithium ion batteries. Meet. Abstr. 2021, MA2021-01, 133.
69. Lin, L.; Liu, F.; Zhang, Y.; et al. Adjustable mixed conductive interphase for dendrite-free lithium metal batteries. ACS. Nano. 2022, 16, 13101-10.
70. Lu, X.; Wang, Y.; Xu, X.; Yan, B.; Wu, T.; Lu, L. Polymer-based solid-state electrolytes for high-energy-density lithium-ion batteries - review. Adv. Energy. Mater. 2023, 13, 2301746.
71. Hu, H.; Li, J.; Ji, X. Confining ionic liquids in developing quasi-solid-state electrolytes for lithium metal batteries. Chem. Eur. J. 2024, 30, e202302826.
72. Yu, D.; Tronstad, Z. C.; McCloskey, B. D. Lithium-ion transport and exchange between phases in a concentrated liquid electrolyte containing lithium-ion-conducting inorganic particles. ACS. Energy. Lett. 2024, 9, 1717-24.
73. Zhao, Y.; Song, Z.; Li, X.; et al. Metal organic frameworks for energy storage and conversion. Energy. Storage. Mater. 2016, 2, 35-62.
74. Pan, K.; Zhang, L.; Qian, W.; et al. A flexible ceramic/polymer hybrid solid electrolyte for solid-state lithium metal batteries. Adv. Mater. 2020, 32, 2000399.
75. Bao, H.; Chen, D.; Liao, B.; Yi, Y.; Liu, R.; Sun, Y. Enhanced ionic conduction in metal-organic-framework-based quasi-solid-state electrolytes: mechanistic insights. Energy. Fuels. 2024, 38, 11275-83.
76. Kim, T.; Son, D.; Ono, L. K.; Jiang, Y.; Qi, Y. A solid-liquid hybrid electrolyte for lithium ion batteries enabled by a single-body polymer/indium tin oxide architecture. J. Phys. D:. Appl. Phys. 2021, 54, 475501.
77. Wu, Z.; Yi, Y.; Hai, F.; et al. A metal-organic framework based quasi-solid-state electrolyte enabling continuous ion transport for high-safety and high-energy-density lithium metal batteries. ACS. Appl. Mater. Interfaces. 2023, 15, 22065-74.
78. Han, D.; Zhao, Z.; Wang, W.; et al. Metal organic framework optimized hybrid solid polymer electrolytes with a high lithium-ion transference number and excellent electrochemical stability. Sustain. Energy. Fuels. 2022, 6, 4528-38.
79. Dong, P.; Zhang, X.; Hiscox, W.; et al. Toward high-performance metal-organic-framework-based quasi-solid-state electrolytes: tunable structures and electrochemical properties. Adv. Mater. 2023, 35, e2211841.
80. Li, J.; Weng, Z.; Qin, Z.; et al. Recent advances in multifunctional metal-organic frameworks for lithium metal batteries. Sci. China. Chem. 2024, 67, 759-73.
81. Liu, W.; Mi, Y.; Weng, Z.; Zhong, Y.; Wu, Z.; Wang, H. Functional metal-organic framework boosting lithium metal anode performance via chemical interactions. Chem. Sci. 2017, 8, 4285-91.
82. Zhang, Q.; Xiao, Y.; Li, Q.; et al. Design of thiol-lithium ion interaction in metal-organic framework for high-performance quasi-solid lithium metal batteries. Dalton. Trans. 2021, 50, 2928-35.
83. Yang, H.; Wu, N. Ionic conductivity and ion transport mechanisms of solid-state lithium-ion battery electrolytes: a review. Energy. Sci. Eng. 2022, 10, 1643-71.
84. Li, J.; Li, F.; Zhang, L.; Zhang, H.; Lassi, U.; Ji, X. Recent applications of ionic liquids in quasi-solid-state lithium metal batteries. Green. Chem. Eng. 2021, 2, 253-65.
85. Luo, B.; Wang, Q.; Ji, W.; et al. Suppressing lithium dendrite via hybrid interface layers for high performance quasi-solid-state lithium metal batteries. Chem. Eng. J. 2024, 492, 152152.
86. Zheng, B.; Zhu, J.; Wang, H.; et al. Stabilizing Li10SnP2S12/Li interface via an in situ formed solid electrolyte interphase layer. ACS. Appl. Mater. Interfaces. 2018, 10, 25473-82.
87. Wang, W.; Chai, M.; Lin, R.; et al. Amorphous MOFs for next generation supercapacitors and batteries. Energy. Adv. 2023, 2, 1591-603.
88. Duan, S.; Qian, L.; Zheng, Y.; et al. Mechanisms of the accelerated Li+ conduction in MOF-based solid-state polymer electrolytes for all-solid-state lithium metal batteries. Adv. Mater. 2024, 36, 2314120.
89. Loo, K. L.; Ho, J. W.; Chung, C.; Moon, M.; Yoo, P. J. Ion-transporting channel-embedded MOF-in-COF structures as composite quasi-solid electrolytes with highly enhanced electrochemical properties. J. Mater. Chem. A. 2024, 12, 7875-85.
90. Zhang, Z.; Tian, L.; Zhang, H.; et al. Hexagonal rodlike Cu-MOF-74-derived filler-reinforced composite polymer electrolyte for high-performance solid-state lithium batteries. ACS. Appl. Energy. Mater. 2022, 5, 1095-105.
91. Miner, E. M.; Dincă, M. Metal- and covalent-organic frameworks as solid-state electrolytes for metal-ion batteries. Phil. Trans. R. Soc. A. 2019, 377, 20180225.
92. Hong, C. N.; Crom, A. B.; Feldblyum, J. I.; Lukatskaya, M. R. Metal-organic frameworks for fast electrochemical energy storage: mechanisms and opportunities. Chem 2023, 9, 798-822.
93. Sun, R.; Dou, M.; Chen, Z.; et al. Engineering strategies of metal-organic frameworks toward advanced batteries. Battery. Energy. 2023, 2, 20220064.
94. Yu, J.; Lin, L.; Cheng, L.; Wu, Q.; Zhao, L.; Wang, H. Engineering the interfacial compatibility of a small-molecule quinone cathode toward stable quasi-solid-state lithium-organic batteries. ACS. Sustainable. Chem. Eng. 2024, 12, 9969-77.
95. Kim, M.; Çakmakçı, N.; Song, H.; Jeong, Y. Interfacially-enhanced quasi-solid electrolyte using ionic liquid for lithium-ion battery. Mater. Res. Bull. 2024, 170, 112588.
96. Eftekhari, A. Lithium batteries for electric vehicles: from economy to research strategy. ACS. Sustainable. Chem. Eng. 2019, 7, 5602-13.
97. Zhang, Q.; Liu, B.; Wang, J.; et al. The optimized interfacial compatibility of metal-organic frameworks enables a high-performance quasi-solid metal battery. ACS. Energy. Lett. 2020, 5, 2919-26.
98. Wei, Y.; Hu, F.; Li, Y.; et al. Constructing stable anodic interphase for quasi-solid-state lithium-sulfur batteries. ACS. Appl. Mater. Interfaces. 2020, 12, 39335-41.
99. Brus, J.; Czernek, J.; Urbanova, M.; Rohlíček, J.; Plecháček, T. Transferring lithium ions in the nanochannels of flexible metal-organic frameworks featuring superchaotropic metallacarborane guests: mechanism of ionic conductivity at atomic resolution. ACS. Appl. Mater. Interfaces. 2020, 12, 47447-56.
100. Giacobbe, C.; Lavigna, E.; Maspero, A.; Galli, S. Elucidating the CO2 adsorption mechanisms in the triangular channels of the bis(pyrazolate) MOF Fe2(BPEB)3 by in situ synchrotron X-ray diffraction and molecular dynamics simulations. J. Mater. Chem. A. 2017, 5, 16964-75.
101. Hou, T.; Fong, K. D.; Wang, J.; Persson, K. A. Correction: the solvation structure, transport properties and reduction behavior of carbonate-based electrolytes of lithium-ion batteries. Chem. Sci. 2022, 13, 8205.
102. Xu, W.; Pei, X.; Diercks, C. S.; Lyu, H.; Ji, Z.; Yaghi, O. M. A metal-organic framework of organic vertices and polyoxometalate linkers as a solid-state electrolyte. J. Am. Chem. Soc. 2019, 141, 17522-6.
103. Hou, T.; Xu, W.; Pei, X.; Jiang, L.; Yaghi, O. M.; Persson, K. A. Ionic conduction mechanism and design of metal-organic framework based quasi-solid-state electrolytes. J. Am. Chem. Soc. 2022, 144, 13446-50.
104. Su, N. C.; Noor, S. A. M.; Roslee, M. F.; Mohamed, N. S.; Ahmad, A.; Yahya, M. Z. A. Potential complexes of NaCF3SO3-tetraethylene dimethyl glycol ether (tetraglyme)-based electrolytes for sodium rechargeable battery application. Ionics 2019, 25, 541-9.
105. Singh, H. P.; Kumar, R.; Sekhon, S. S. Correlation between ionic conductivity and fluidity of polymer gel electrolytes containing NH4CF3SO3. Bull. Mater. Sci. 2005, 28, 467-72.
106. Castillo, J.; Santiago, A.; Judez, X.; et al. High energy density lithium-sulfur batteries based on carbonaceous two-dimensional additive cathodes. ACS. Appl. Energy. Mater. 2023, 6, 3579-89.
107. Kwon, W. J.; Kim, H.; Jung, K.; et al. Enhanced Li+ conduction in perovskite Li3xLa/3-x□1/3-2xTiO3 solid-electrolytes via microstructural engineering. J. Mater. Chem. A. 2017, 5, 6257-62.
108. Zhu, Y.; He, X.; Mo, Y. First principles study on electrochemical and chemical stability of solid electrolyte-electrode interfaces in all-solid-state Li-ion batteries. J. Mater. Chem. A. 2016, 4, 3253-66.
109. Luo, W.; Gong, Y.; Zhu, Y.; et al. Reducing interfacial resistance between garnet-structured solid-state electrolyte and Li-metal anode by a germanium layer. Adv. Mater. 2017, 29.
110. Chen, L.; Li, Y.; Li, S.; Fan, L.; Nan, C.; Goodenough, J. B. PEO/garnet composite electrolytes for solid-state lithium batteries: from “ceramic-in-polymer” to “polymer-in-ceramic”. Nano. Energy. 2018, 46, 176-84.
111. Wan, J.; Xie, J.; Kong, X.; et al. Ultrathin, flexible, solid polymer composite electrolyte enabled with aligned nanoporous host for lithium batteries. Nat. Nanotechnol. 2019, 14, 705-11.
112. Song, K.; Chen, W. An effective solid-electrolyte interphase for stable solid-state batteries. Chem 2021, 7, 3195-7.
113. Zhou, W.; Wang, S.; Li, Y.; Xin, S.; Manthiram, A.; Goodenough, J. B. Plating a dendrite-free lithium anode with a polymer/ceramic/polymer sandwich electrolyte. J. Am. Chem. Soc. 2016, 138, 9385-8.
114. Kim, S. Y.; Cha, H.; Kostecki, R.; Chen, G. Composite cathode design for high-energy all-solid-state lithium batteries with long cycle life. ACS. Energy. Lett. 2023, 8, 521-8.
115. Zhou, B.; Fang, B.; Stosevski, I.; Bonakdarpour, A.; Wilkinson, D. P. Li host carbon materials as the negative electrode for a Li-metal battery - mechanistic and practical assessment. Meet. Abstr. 2022, MA2022-01, 667.
116. Zheng, Z.; Ye, H.; Guo, Z. Recent progress on pristine metal/covalent-organic frameworks and their composites for lithium-sulfur batteries. Energy. Environ. Sci. 2021, 14, 1835-53.
117. Chen, Y.; Wen, K.; Chen, T.; Zhang, X.; Armand, M.; Chen, S. Recent progress in all-solid-state lithium batteries: The emerging strategies for advanced electrolytes and their interfaces. Energy. Storage. Mater. 2020, 31, 401-33.
118. Chen, S.; Wen, K.; Fan, J.; Bando, Y.; Golberg, D. Progress and future prospects of high-voltage and high-safety electrolytes in advanced lithium batteries: from liquid to solid electrolytes. J. Mater. Chem. A. 2018, 6, 11631-63.
119. Chen, R.; Qu, W.; Guo, X.; Li, L.; Wu, F. The pursuit of solid-state electrolytes for lithium batteries: from comprehensive insight to emerging horizons. Mater. Horiz. 2016, 3, 487-516.
120. Ong, J. L.; Loy, A. C. M.; Teng, S. Y.; How, B. S. Future paradigm of 3D printed Ni-based metal organic framework catalysts for dry methane reforming: techno-economic and environmental analyses. ACS. Omega. 2022, 7, 15369-84.
121. Desantis, D.; Mason, J. A.; James, B. D.; Houchins, C.; Long, J. R.; Veenstra, M. Techno-economic analysis of metal-organic frameworks for hydrogen and natural gas storage. Energy. Fuels. 2017, 31, 2024-32.
122. Paul, T.; Juma, A.; Alqerem, R.; Karanikolos, G.; Arafat, H. A.; Dumée, L. F. Scale-up of metal-organic frameworks production: engineering strategies and prospects towards sustainable manufacturing. J. Environ. Chem. Eng. 2023, 11, 111112.
123. Chakraborty, D.; Yurdusen, A.; Mouchaham, G.; Nouar, F.; Serre, C. Large-scale production of metal-organic frameworks. Adv. Funct. Mater. 2024, 34, 2309089.
124. Yusuf, V. F.; Malek, N. I.; Kailasa, S. K. Review on metal-organic framework classification, synthetic approaches, and influencing factors: applications in energy, drug delivery, and wastewater treatment. ACS. Omega. 2022, 7, 44507-31.
125. Sun, C.; Liu, J.; Gong, Y.; Wilkinson, D. P.; Zhang, J. Recent advances in all-solid-state rechargeable lithium batteries. Nano. Energy. 2017, 33, 363-86.
126. Han, X.; Gong, Y.; Fu, K. K.; et al. Negating interfacial impedance in garnet-based solid-state Li metal batteries. Nat. Mater. 2017, 16, 572-9.
127. Wang, C.; Fu, K.; Kammampata, S. P.; et al. Garnet-type solid-state electrolytes: materials, interfaces, and batteries. Chem. Rev. 2020, 120, 4257-300.
128. Kaur, G.; Sharma, S.; Singh, M. D.; Nalwa, K. S.; Sivasubramanian, S. C.; Dalvi, A. Ionic liquid composites with garnet-type Li6.75Al0.25La3Zr2O12: stability, electrical transport, and potential for energy storage applications. Mater. Chem. Phys. 2024, 317, 129205.
129. Zhang, Z.; Zhang, L.; Liu, Y.; et al. Interface-engineered Li7La3Zr2O12-based garnet solid electrolytes with suppressed li-dendrite formation and enhanced electrochemical performance. ChemSusChem 2018, 11, 3774-82.
130. Lin, R.; Jin, Y.; Li, Y.; Zhang, X.; Xiong, Y. Recent advances in ionic liquids-MOF hybrid electrolytes for solid-state electrolyte of lithium battery. Batteries 2023, 9, 314.
131. Subramani, R.; Hsu, S.; Chuang, Y.; Hsu, L.; Lu, K.; Chen, J. Fe-MIL-101 metal organic framework integrated solid polymer electrolytes for high-performance solid-state lithium metal batteries. J. Mater. Chem. A. 2024, 12, 7132-41.
132. Homann, G.; Stolz, L.; Nair, J.; Laskovic, I. C.; Winter, M.; Kasnatscheew, J. Poly(ethylene oxide)-based electrolyte for solid-state-lithium-batteries with high voltage positive electrodes: evaluating the role of electrolyte oxidation in rapid cell failure. Sci. Rep. 2020, 10, 4390.
133. Wang, Q.; Yang, A.; Ma, J.; Yao, M.; Geng, S.; Liu, F. Constructing PTFE@LATP composite solid electrolytes with three-dimensional network for high-performance lithium batteries. Electrochim. Acta. 2023, 467, 143138.
134. Liu, Y.; Xu, Y.; Zhang, Y.; Yu, C.; Sun, X. Thin Li1.3Al0.3Ti1.7(PO4)3-based composite solid electrolyte with a reinforced interface of in situ formed poly(1,3-dioxolane) for lithium metal batteries. J. Colloid. Interface. Sci. 2023, 644, 53-63.
135. Xu, Y.; Zhao, R.; Gao, L.; et al. A fiber-reinforced solid polymer electrolyte by in situ polymerization for stable lithium metal batteries. Nano. Res. 2023, 16, 9259-66.
136. Butreddy, P.; Wijesingha, M.; Laws, S.; Pathiraja, G.; Mo, Y.; Rathnayake, H. Insight into the isoreticularity of Li-MOFs for the design of low-density solid and quasi-solid electrolytes. Chem. Mater. 2023, 35, 9857-78.
137. Gong, X.; Xiao, Q.; Li, Q.; et al. Cross-linked electrospun gel polymer electrolytes for lithium-ion batteries. Chin. J. Polym. Sci. 2024, 42, 1021-8.
138. Lim, N.; Kim, E.; Park, J.; et al. Design of a bioinspired robust three-dimensional cross-linked polymer binder for high-performance Li-ion battery applications. ACS. Appl. Mater. Interfaces. 2023, 15, 54409-18.
139. Shin, W.; Cho, J.; Kannan, A. G.; Lee, Y.; Kim, D. Cross-linked composite gel polymer electrolyte using mesoporous methacrylate-functionalized SiO2 nanoparticles for lithium-ion polymer batteries. Sci. Rep. 2016, 6, BFsrep26332.
140. Röchow, E. T.; Coeler, M.; Pospiech, D.; et al. In situ preparation of crosslinked polymer electrolytes for lithium ion batteries: a comparison of monomer systems. Polymers 2020, 12, 1707.
141. Wen, J.; Zhao, Q.; Jiang, X.; et al. Graphene oxide enabled flexible peo-based solid polymer electrolyte for all-solid-state lithium metal battery. ACS. Appl. Energy. Mater. 2021, 4, 3660-9.
142. Rajamani, A.; Panneerselvam, T.; Murugan, R.; Ramaswamy, A. P. Electrospun derived polymer-garnet composite quasi solid state electrolyte with low interface resistance for lithium metal batteries. Energy 2023, 263, 126058.
143. Huang, Y.; Wang, Y.; Fu, Y. A thermoregulating separator based on black phosphorus/MOFs heterostructure for thermo-stable lithium-sulfur batteries. Chem. Eng. J. 2023, 454, 140250.
144. Lei, H.; Tu, J.; Li, S.; et al. MOF-based quasi-solid-state electrolyte for long-life Al-Se battery. J. Energy. Chem. 2023, 86, 237-45.
145. Zhang, Z.; Huang, Y.; Li, C.; Li, X. Metal-organic framework-supported poly(ethylene oxide) composite gel polymer electrolytes for high-performance lithium/sodium metal batteries. ACS. Appl. Mater. Interfaces. 2021, 13, 37262-72.
146. Li, J.; Gao, L.; Pan, F.; et al. Engineering strategies for suppressing the shuttle effect in lithium-sulfur batteries. Nano-Micro. Lett. 2023, 16, 12.
147. Aslam, M. K.; Niu, Y.; Hussain, T.; et al. How to avoid dendrite formation in metal batteries: innovative strategies for dendrite suppression. Nano. Energy. 2021, 86, 106142.
148. Bai, S.; Kim, B.; Kim, C.; et al. Permselective metal-organic framework gel membrane enables long-life cycling of rechargeable organic batteries. Nat. Nanotechnol. 2021, 16, 77-84.
149. Liu, Q.; Yang, L.; Mei, Z.; et al. Constructing host-guest recognition electrolytes promotes the Li+ kinetics in solid-state batteries. Energy. Environ. Sci. 2024, 17, 780-90.
150. Yang, L.; Chen, J.; Park, S.; Wang, H. Recent progress on metal-organic framework derived carbon and their composites as anode materials for potassium-ion batteries. Energy. Mater. 2023, 3, 300042.
151. Chen, J.; Adit, G.; Li, L.; Zhang, Y.; Chua, D. H. C.; Lee, P. S. Optimization strategies toward functional sodium-ion batteries. Energy. Environ. Mater. 2023, 6, e12633.
152. Lu, X.; Wu, H.; Kong, D.; Li, X.; Shen, L.; Lu, Y. Facilitating lithium-ion conduction in gel polymer electrolyte by metal-organic frameworks. ACS. Mater. Lett. 2020, 2, 1435-41.
153. Fu, X.; Hurlock, M. J.; Ding, C.; Li, X.; Zhang, Q.; Zhong, W. H. MOF-enabled ion-regulating gel electrolyte for long-cycling lithium metal batteries under high voltage. Small 2022, 18, 2106225.
154. Wang, D.; Jin, B.; Yao, X.; et al. Bio-inspired polydopamine-modified ZIF-90-supported gel polymer electrolyte for high-safety lithium metal batteries. ACS. Appl. Energy. Mater. 2023, 6, 11146-56.
155. Murray, L. J.; Dincă, M.; Long, J. R. Hydrogen storage in metal-organic frameworks. Chem. Soc. Rev. 2009, 38, 1294-314.
156. Li, J. R.; Sculley, J.; Zhou, H. C. Metal-organic frameworks for separations. Chem. Rev. 2012, 112, 869-932.
157. Ma, L.; Abney, C.; Lin, W. Enantioselective catalysis with homochiral metal-organic frameworks. Chem. Soc. Rev. 2009, 38, 1248-56.
158. Kreno, L. E.; Leong, K.; Farha, O. K.; Allendorf, M.; Van, D. R. P.; Hupp, J. T. Metal-organic framework materials as chemical sensors. Chem. Rev. 2012, 112, 1105-25.
159. Min, K. S.; Suh, M. P. Silver(I)-polynitrile network solids for anion exchange: anion-induced transformation of supramolecular structure in the crystalline state. J. Am. Chem. Soc. 2000, 122, 6834-40.
160. Horike, S.; Umeyama, D.; Kitagawa, S. Ion conductivity and transport by porous coordination polymers and metal-organic frameworks. Acc. Chem. Res. 2013, 46, 2376-84.
161. Yang, H.; Liu, B.; Bright, J.; et al. A single-ion conducting UiO-66 metal-organic framework electrolyte for all-solid-state lithium batteries. ACS. Appl. Energy. Mater. 2020, 3, 4007-13.
163. Taylor, J. M.; Dekura, S.; Ikeda, R.; Kitagawa, H. Defect control to enhance proton conductivity in a metal-organic framework. Chem. Mater. 2015, 27, 2286-9.
165. Liu, L.; Sun, C. Flexible quasi-solid-state composite electrolyte membrane derived from a metal-organic framework for lithium-metal batteries. ChemElectroChem 2020, 7, 707-15.
166. Zhou, L.; Pan, H.; Yin, G.; et al. Tailoring the function of battery separators via the design of MOF coatings. Adv. Funct. Mater. 2024, 34, 2314246.
167. Wu, X.; Gao, Y.; Bi, J. Understanding the structure-dependent adsorption behavior of four zirconium-based porphyrinic MOFs for the removal of pharmaceuticals. Microporous. Mesoporous. Mater. 2024, 363, 112827.
168. Furukawa, H.; Gándara, F.; Zhang, Y. B.; et al. Water adsorption in porous metal-organic frameworks and related materials. J. Am. Chem. Soc. 2014, 136, 4369-81.
169. Sun, C.; Zhang, J. H.; Yuan, X. F.; et al. ZIF-8-based quasi-solid-state electrolyte for lithium batteries. ACS. Appl. Mater. Interfaces. 2019, 11, 46671-7.
170. Zhu, X.; Chang, Z.; Yang, H.; He, P.; Zhou, H. Highly safe and stable lithium-metal batteries based on a quasi-solid-state electrolyte. J. Mater. Chem. A. 2022, 10, 651-63.
171. Shieh, F. K.; Wang, S. C.; Leo, S. Y.; Wu, K. C. Water-based synthesis of zeolitic imidazolate framework-90 (ZIF-90) with a controllable particle size. Chem. Eur. J. 2013, 19, 11139-42.
172. Kida, K.; Okita, M.; Fujita, K.; Tanaka, S.; Miyake, Y. Formation of high crystalline ZIF-8 in an aqueous solution. CrystEngComm 2013, 15, 1794-801.
173. Yu, T.; Ma, H.; Zhang, H.; Xiong, M.; Liu, Y.; Li, F. Fabrication and characterization of purified esterase-embedded zeolitic imidazolate frameworks for the removal and remediation of herbicide pollution from soil. J. Environ. Manage. 2021, 288, 112450.
174. Deneff, J. I.; Butler, K. S.; Kotula, P. G.; Rue, B. E.; Sava, G. D. F. Expanding the ZIFs repertoire for biological applications with the targeted synthesis of ZIF-20 nanoparticles. ACS. Appl. Mater. Interfaces. 2021, 13, 27295-304.
175. Xing, J.; Schweighauser, L.; Okada, S.; Harano, K.; Nakamura, E. Atomistic structures and dynamics of prenucleation clusters in MOF-2 and MOF-5 syntheses. Nat. Commun. 2019, 10, 3608.
176. Xu, G.; Yamada, T.; Otsubo, K.; Sakaida, S.; Kitagawa, H. Facile “modular assembly” for fast construction of a highly oriented crystalline MOF nanofilm. J. Am. Chem. Soc. 2012, 134, 16524-7.
177. Shen, L.; Wu, H. B.; Liu, F.; et al. Creating lithium-ion electrolytes with biomimetic ionic channels in metal-organic frameworks. Adv. Mater. 2018, 30, 1707476.
178. Wang, X. G.; Cheng, Q.; Yu, Y.; Zhang, X. Z. Controlled nucleation and controlled growth for size predicable synthesis of nanoscale metal-organic frameworks (MOFs): a general and scalable approach. Angew. Chem. Int. Ed. 2018, 57, 7836-40.
179. Qiu, S.; Du, J.; Xiao, Y.; Zhao, Q.; He, G. Hierarchical porous HKUST-1 fabricated by microwave-assisted synthesis with CTAB for enhanced adsorptive removal of benzothiophene from fuel. Sep. Purif. Technol. 2021, 271, 118868.
180. Chen, Y.; Qiao, Z.; Lv, D.; et al. Efficient adsorptive separation of C3H6 over C3H8 on flexible and thermoresponsive CPL-1. Chem. Eng. J. 2017, 328, 360-7.
181. Xiang, H.; Ameen, A.; Shang, J.; et al. Synthesis and modification of moisture-stable coordination pillared-layer metal-organic framework (CPL-MOF) CPL-2 for ethylene/ethane separation. Microporous. Mesoporous. Mater. 2020, 293, 109784.
182. Garai, B.; Bon, V.; Krause, S.; et al. Tunable flexibility and porosity of the metal-organic framework DUT-49 through postsynthetic metal exchange. Chem. Mater. 2020, 32, 889-96.
183. Kolbe, F.; Krause, S.; Bon, V.; Senkovska, I.; Kaskel, S.; Brunner, E. High-pressure in situ 129Xe NMR spectroscopy: insights into switching mechanisms of flexible metal-organic frameworks isoreticular to DUT-49. Chem. Mater. 2019, 31, 6193-201.
184. Wang, C.; Zhang, F.; Yang, J.; Li, J. Rapid and HF-free synthesis of MIL-100(Cr) via steam-assisted method. Mater. Lett. 2019, 252, 286-8.
185. Celeste, A.; Paolone, A.; Itié, J. P.; et al. Mesoporous metal-organic framework MIL-101 at high pressure. J. Am. Chem. Soc. 2020, 142, 15012-9.
186. Hu, J.; Chen, Y.; Zhang, H.; Chen, Z. Controlled syntheses of Mg-MOF-74 nanorods for drug delivery. J. Solid. State. Chem. 2021, 294, 121853.
187. Qi, C.; Xu, L.; Wang, J.; et al. Titanium-containing metal-organic framework modified separator for advanced lithium-sulfur batteries. ACS. Sustainable. Chem. Eng. 2020, 8, 12968-75.
188. Wang, Z.; Li, Z.; Zhang, X. G.; et al. Tailoring multiple sites of metal-organic frameworks for highly efficient and reversible ammonia adsorption. ACS. Appl. Mater. Interfaces. 2021, 13, 56025-34.
189. Su, Y.; Yuan, G.; Hu, J.; et al. Thiosalicylic-acid-mediated coordination structure of nickel center via thermodynamic modulation for aqueous Ni-Zn batteries. Adv. Mater. 2024, 36, 2406094.
190. Leng, X.; Zeng, J.; Yang, M.; et al. Bimetallic Ni-Co MOF@PAN modified electrospun separator enhances high-performance lithium-sulfur batteries. J. Energy. Chem. 2023, 82, 484-96.
191. Razaq, R.; Din, M. M. U.; Småbråten, D. R.; et al. Synergistic effect of bimetallic MOF modified separator for long cycle life lithium-sulfur batteries. Adv. Energy. Mater. 2024, 14, 2302897.
192. Liu, Y.; Li, L.; Wen, A.; Cao, F.; Ye, H. A Janus MXene/MOF separator for the all-in-one enhancement of lithium-sulfur batteries. Energy. Storage. Mater. 2023, 55, 652-9.
193. Han, D. D.; Wang, Z. Y.; Pan, G. L.; Gao, X. P. Metal-organic-framework-based gel polymer electrolyte with immobilized anions to stabilize a lithium anode for a quasi-solid-state lithium-sulfur battery. ACS. Appl. Mater. Interfaces. 2019, 11, 18427-35.
194. Férey, G.; Mellot-Draznieks, C.; Serre, C.; et al. A chromium terephthalate-based solid with unusually large pore volumes and surface area. Science 2005, 309, 2040-2.
195. Xu, Z.; Zhao, Y. Y.; Chen, L.; et al. Thermally activated bipyridyl-based Mn-MOFs with Lewis acid-base bifunctional sites for highly efficient catalytic cycloaddition of CO2 with epoxides and Knoevenagel condensation reactions. Dalton. Trans. 2023, 52, 3671-81.
196. Zhang, X.; Zhan, Z.; Li, Z.; Di, L. Thermal activation of CuBTC MOF for CO oxidation: the effect of activation atmosphere. Catalysts 2017, 7, 106.
197. He, Z.; Zhu, X.; Song, Y.; et al. Separator functionalization realizing stable zinc anode through microporous metal-organic framework with special functional group. Energy. Storage. Mater. 2025, 74, 103886.
198. Planchais, A.; Devautour-vinot, S.; Salles, F.; et al. A joint experimental/computational exploration of the dynamics of confined water/Zr-based MOFs systems. J. Phys. Chem. C. 2014, 118, 14441-8.
199. Yang, P.; Zhang, K.; Liu, S.; et al. Ionic selective separator design enables long-life zinc-iodine batteries via synergistic anode stabilization and polyiodide shuttle suppression. Adv. Funct. Mater. 2024, 34, 2410712.
200. Ruan, Z.; Wang, X.; Yuan, X. Improved catalytic performance and stability of defected UiO-66-SO3H in the esterification reaction of cyclohexene with cyclohexanecarboxylic acid. J. Porous. Mater. 2022, 29, 1957-68.
201. Morris, W.; Volosskiy, B.; Demir, S.; et al. Synthesis, structure, and metalation of two new highly porous zirconium metal-organic frameworks. Inorg. Chem. 2012, 51, 6443-5.
202. Kim, H. K.; Yun, W. S.; Kim, M. B.; et al. A chemical route to activation of open metal sites in the copper-based metal-organic framework materials HKUST-1 and Cu-MOF-2. J. Am. Chem. Soc. 2015, 137, 10009-15.
203. Li, H.; Eddaoudi, M.; O’keeffe, M.; Yaghi, O. M. Design and synthesis of an exceptionally stable and highly porous metal-organic framework. Nature 1999, 402, 276-9.
204. Liu, J.; Culp, J. T.; Natesakhawat, S.; et al. Experimental and theoretical studies of gas adsorption in Cu3(BTC)2: an effective activation procedure. J. Phys. Chem. C. 2007, 111, 9305-13.
205. Lohe, M. R.; Rose, M.; Kaskel, S. Metal-organic framework (MOF) aerogels with high micro- and macroporosity. Chem. Commun. 2009, 6056-8.
206. Nelson, A. P.; Farha, O. K.; Mulfort, K. L.; Hupp, J. T. Supercritical processing as a route to high internal surface areas and permanent microporosity in metal-organic framework materials. J. Am. Chem. Soc. 2009, 131, 458-60.
207. Mondloch, J. E.; Karagiaridi, O.; Farha, O. K.; Hupp, J. T. Activation of metal-organic framework materials. CrystEngComm 2013, 15, 9258.
208. Oh, H.; Maurer, S.; Balderas-xicohtencatl, R.; et al. Efficient synthesis for large-scale production and characterization for hydrogen storage of ligand exchanged MOF-74/174/184-M (M = Mg2+, Ni2+). Int. J. Hydrogen. Energy. 2017, 42, 1027-35.
209. Batten, M. P.; Rubio-martinez, M.; Hadley, T.; et al. Continuous flow production of metal-organic frameworks. Curr. Opin. Chem. Eng. 2015, 8, 55-9.
210. Rubio-Martinez, M.; Avci-Camur, C.; Thornton, A. W.; Imaz, I.; Maspoch, D.; Hill, M. R. New synthetic routes towards MOF production at scale. Chem. Soc. Rev. 2017, 46, 3453-80.
211. Gaab, M.; Trukhan, N.; Maurer, S.; Gummaraju, R.; Müller, U. The progression of Al-based metal-organic frameworks-from academic research to industrial production and applications. Microporous. Mesoporous. Mater. 2012, 157, 131-6.
212. Vepsäläinen, M.; Macedo, D. S.; Gong, H.; Rubio-martinez, M.; Bayatsarmadi, B.; He, B. Electrosynthesis of HKUST-1 with flow-reactor post-processing. Appl. Sci. 2021, 11, 3340.
213. Ren, J.; Dyosiba, X.; Musyoka, N. M.; Langmi, H. W.; Mathe, M.; Liao, S. Review on the current practices and efforts towards pilot-scale production of metal-organic frameworks (MOFs). Coord. Chem. Rev. 2017, 352, 187-219.
214. Mckinstry, C.; Cathcart, R. J.; Cussen, E. J.; Fletcher, A. J.; Patwardhan, S. V.; Sefcik, J. Scalable continuous solvothermal synthesis of metal organic framework (MOF-5) crystals. Chem. Eng. J. 2016, 285, 718-25.
215. Klimakow, M.; Klobes, P.; Thünemann, A. F.; Rademann, K.; Emmerling, F. Mechanochemical synthesis of metal-organic frameworks: a fast and facile approach toward quantitative yields and high specific surface areas. Chem. Mater. 2010, 22, 5216-21.
216. Tanaka, S.; Kida, K.; Nagaoka, T.; Ota, T.; Miyake, Y. Mechanochemical dry conversion of zinc oxide to zeolitic imidazolate framework. Chem. Commun. 2013, 49, 7884-6.
217. Chen, Z.; Wang, W.; Yao, J.; et al. Toxicity of a molluscicide candidate PPU07 against Oncomelania hupensis (Gredler, 1881) and local fish in field evaluation. Chemosphere 2019, 222, 56-61.
218. Cadot, S.; Veyre, L.; Luneau, D.; Farrusseng, D.; Alessandra, Q. E. A water-based and high space-time yield synthetic route to MOF Ni2(dhtp) and its linker 2,5-dihydroxyterephthalic acid. J. Mater. Chem. A. 2014, 2, 17757-63.
219. Sánchez, L.; Acevedo-peña, P.; Aguilar-frutis, M. Á.; Reguera, E. Improving Mg2+ ionic conductivity in ZIF-8 by Cu (II) doping and mbIm incorporation into the framework. Solid. State. Ionics. 2024, 407, 116497.
220. Mu, A. U.; Cai, G.; Chen, Z. Metal-organic frameworks for the enhancement of lithium-based batteries: a mini review on emerging functional designs. Adv. Sci. 2024, 11, 2305280.
221. Zhang, M.; Wu, L.; Zhu, B.; Liu, Y. Performance enhancement of lithium-metal batteries using the three-dimensional porous network structure a metal-organic framework-aramid cellulose-MXene composite separator. Int. J. Hydrogen. Energy. 2024, 59, 263-71.
222. Shang, W.; Chen, Y.; Han, J.; Ouyang, P.; Fang, C.; Du, J. Dendrite-free Li anode enabled by a metal-organic framework-modified solid polymer electrolyte for high-performance lithium metal batteries. ACS. Appl. Energy. Mater. 2020, 3, 12351-9.
223. Wang, Z.; Du, Z.; Liu, Y.; et al. Metal-organic frameworks and their derivatives for optimizing lithium metal anodes. eScience 2024, 4, 100189.
224. Lee, D. J.; Yu, X.; Sikma, R. E.; et al. Holistic design consideration of metal-organic framework-based composite membranes for lithium-sulfur batteries. ACS. Appl. Mater. Interfaces. 2022, 14, 34742-9.
225. Phung, J.; Zhang, X.; Deng, W.; Li, G. An overview of MOF-based separators for lithium-sulfur batteries. Sustain. Mater. Technol. 2022, 31, e00374.
226. Peng, Y.; Xu, J.; Xu, J.; et al. Metal-organic framework (MOF) composites as promising materials for energy storage applications. Adv. Colloid. Interface. Sci. 2022, 307, 102732.
227. Bai, S.; Liu, X.; Zhu, K.; Wu, S.; Zhou, H. Metal-organic framework-based separator for lithium-sulfur batteries. Nat. Energy. 2016, 1, 16094.
228. Li, Y. W.; Zhang, W. J.; Li, J.; et al. Fe-MOF-derived efficient ORR/OER bifunctional electrocatalyst for rechargeable zinc-air batteries. ACS. Appl. Mater. Interfaces. 2020, 12, 44710-9.
229. He, J.; Chen, Y.; Manthiram, A. Vertical Co9S8 hollow nanowall arrays grown on a Celgard separator as a multifunctional polysulfide barrier for high-performance Li-S batteries. Energy. Environ. Sci. 2018, 11, 2560-8.
230. Li, X.; Zhang, F.; Zhang, M.; Zhou, Z.; Zhou, X. Chromium-based metal-organic framework coated separator for improving electrochemical performance and safety of lithium-ion battery. J. Energy. Storage. 2023, 59, 106473.
231. Chang, Z.; Qiao, Y.; Deng, H.; Yang, H.; He, P.; Zhou, H. A liquid electrolyte with de-solvated lithium ions for lithium-metal battery. Joule 2020, 4, 1776-89.
232. Sheng, L.; Wang, Q.; Liu, X.; et al. Suppressing electrolyte-lithium metal reactivity via Li+-desolvation in uniform nano-porous separator. Nat. Commun. 2022, 13, 172.
233. Hu, Q.; Han, G.; Wang, A.; et al. Functionalized MOF enables stable cycling of nickel-rich layered oxides for lithium-ion batteries. Chem. Eng. J. 2024, 497, 154608.
234. Chang, Z.; Yang, H.; Pan, A.; He, P.; Zhou, H. An improved 9 micron thick separator for a 350 Wh/kg lithium metal rechargeable pouch cell. Nat. Commun. 2022, 13, 6788.
235. Fan, Y.; Niu, Z.; Zhang, F.; Zhang, R.; Zhao, Y.; Lu, G. Suppressing the shuttle effect in lithium-sulfur batteries by a UiO-66-modified polypropylene separator. ACS. Omega. 2019, 4, 10328-35.
236. Han, J.; Gao, S.; Wang, R.; et al. Investigation of the mechanism of metal-organic frameworks preventing polysulfide shuttling from the perspective of composition and structure. J. Mater. Chem. A. 2020, 8, 6661-9.
237. Zhu, F.; Bao, H.; Wu, X.; et al. High-performance metal-organic framework-based single ion conducting solid-state electrolytes for low-temperature lithium metal batteries. ACS. Appl. Mater. Interfaces. 2019, 11, 43206-13.
238. Fan, Z.; He, L.; Li, X.; Xin, X. Inhibiting I-/I3- redox shuttling in Li-O2 batteries by MOF decorated separator. Mater. Res. Bull. 2023, 167, 112412.
239. Aubrey, M. L.; Ameloot, R.; Wiers, B. M.; Long, J. R. Metal-organic frameworks as solid magnesium electrolytes. Energy. Environ. Sci. 2014, 7, 667-71.
240. Ameloot, R.; Aubrey, M.; Wiers, B. M.; et al. Ionic conductivity in the metal-organic framework UiO-66 by dehydration and insertion of lithium tert-butoxide. Chemistry 2013, 19, 5533-6.
241. Zettl, R.; Lunghammer, S.; Gadermaier, B.; et al. High Li+ and Na+ conductivity in new hybrid solid electrolytes based on the porous MIL-121 metal organic framework. Adv. Energy. Mater. 2021, 11, 2003542.
242. Lu, G.; Wei, H.; Shen, C.; et al. Bifunctional MOF doped PEO composite electrolyte for long-life cycle solid lithium ion battery. ACS. Appl. Mater. Interfaces. 2022, 14, 45476-83.
243. Guo, Y.; Sun, M.; Liang, H.; et al. Blocking polysulfides and facilitating lithium-ion transport: polystyrene sulfonate@HKUST-1 membrane for lithium-sulfur batteries. ACS. Appl. Mater. Interfaces. 2018, 10, 30451-9.
244. Kim, S. H.; Yeon, J. S.; Kim, R.; Choi, K. M.; Park, H. S. A functional separator coated with sulfonated metal-organic framework/Nafion hybrids for Li-S batteries. J. Mater. Chem. A. 2018, 6, 24971-8.
245. Chang, Z.; Qiao, Y.; Wang, J.; Deng, H.; He, P.; Zhou, H. Fabricating better metal-organic frameworks separators for Li-S batteries: pore sizes effects inspired channel modification strategy. Energy. Storage. Mater. 2020, 25, 164-71.
246. Wang, Z.; Huang, W.; Hua, J.; et al. An anionic-MOF-based bifunctional separator for regulating lithium deposition and suppressing polysulfides shuttle in Li-S batteries. Small. Methods. 2020, 4, 2000082.
247. Zhou, Z.; Li, Y.; Fang, T.; et al. MOF-derived Co3O4 polyhedrons as efficient polysulfides barrier on polyimide separators for high temperature lithium-sulfur batteries. Nanomaterials 2019, 9, 1574.
248. Suriyakumar, S.; Stephan, A. M.; Angulakshmi, N.; Hassan, M. H.; Alkordi, M. H. Metal-organic framework@SiO2 as permselective separator for lithium-sulfur batteries. J. Mater. Chem. A. 2018, 6, 14623-32.
249. Bai, S.; Zhu, K.; Wu, S.; et al. A long-life lithium-sulphur battery by integrating zinc-organic framework based separator. J. Mater. Chem. A. 2016, 4, 16812-7.
250. Zhou, C.; He, Q.; Li, Z.; et al. A robust electrospun separator modified with in situ grown metal-organic frameworks for lithium-sulfur batteries. Chem. Eng. J. 2020, 395, 124979.
251. Huang, J. Q.; Zhuang, T. Z.; Zhang, Q.; Peng, H. J.; Chen, C. M.; Wei, F. Permselective graphene oxide membrane for highly stable and anti-self-discharge lithium-sulfur batteries. ACS. Nano. 2015, 9, 3002-11.
252. Lammert, M.; Glißmann, C.; Reinsch, H.; Stock, N. Synthesis and characterization of new Ce(IV)-MOFs exhibiting various framework topologies. Cryst. Growth. Des. 2017, 17, 1125-31.
253. Lee, D. H.; Ahn, J. H.; Park, M.; Eftekhari, A.; Kim, D. Metal-organic framework/carbon nanotube-coated polyethylene separator for improving the cycling performance of lithium-sulfur cells. Electrochim. Acta. 2018, 283, 1291-9.
254. Jiang, G.; Zheng, N.; Chen, X.; et al. In-situ decoration of MOF-derived carbon on nitrogen-doped ultrathin MXene nanosheets to multifunctionalize separators for stable Li-S batteries. Chem. Eng. J. 2019, 373, 1309-18.
255. Wang, B.; Liu, J.; Mao, C.; et al. A MOF-gel based separator for suppressing redox mediator shuttling in Li-O2 batteries. Small 2024, 20, 2401231.
256. Guang, Z.; Huang, Y.; Chen, C.; Liu, X.; Xu, Z.; Dou, W. Engineering a light-weight, thin and dual-functional interlayer as “polysulfides sieve” capable of synergistic adsorption for high-performance lithium-sulfur batteries. Chem. Eng. J. 2020, 383, 123163.
257. Li, B.; Pan, Y.; Luo, B.; et al. MOF-derived NiCo2S4@C as a separator modification material for high-performance lithium-sulfur batteries. Electrochim. Acta. 2020, 344, 135811.
258. Li, W.; Ye, Y.; Qian, J.; et al. Oxygenated nitrogen-doped microporous nanocarbon as a permselective interlayer for ultrastable lithium-sulfur batteries. ChemElectroChem 2019, 6, 1094-100.
Cite This Article
How to Cite
Download Citation
Export Citation File:
Type of Import
Tips on Downloading Citation
Citation Manager File Format
Type of Import
Direct Import: When the Direct Import option is selected (the default state), a dialogue box will give you the option to Save or Open the downloaded citation data. Choosing Open will either launch your citation manager or give you a choice of applications with which to use the metadata. The Save option saves the file locally for later use.
Indirect Import: When the Indirect Import option is selected, the metadata is displayed and may be copied and pasted as needed.
About This Article
Copyright
Data & Comments
Data
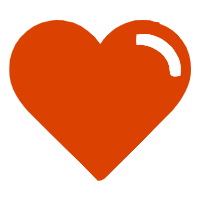
Comments
Comments must be written in English. Spam, offensive content, impersonation, and private information will not be permitted. If any comment is reported and identified as inappropriate content by OAE staff, the comment will be removed without notice. If you have any queries or need any help, please contact us at [email protected].