Towards ultrastretchability, multimodal instability, and static nonreciprocity in kirigami metamaterials
Abstract
Kirigami, known for its ultra-softness, ultra-lightness, and high stretchability, is at the forefront of research in advanced materials and structural design. However, its inherent flexibility and sensitivity pose significant challenges for mechanical characterization, as conventional rigid-body assumptions are inadequate. Key hurdles include developing flexible tensile mechanics and designing high-curvature structures to prevent fracture at cut edges. Despite advancements in nanoscale synthesis and large-scale deployable kirigami systems that enhance geometric and material design, the lack of robust models to describe complex in-plane and out-of-plane buckling under extreme conditions hampers further theoretical and applied progress. Current reciprocal mechanics theories struggle to capture the nonlinearities, multi-stability, and asymmetry characteristic of kirigami deformation. Static nonreciprocity offers a promising alternative by distinguishing forward and reverse mechanical responses, breaking time-reversal symmetry, and providing deeper mechanical insights. Moving forward, establishing a framework based on nonreciprocal properties will be essential to overcoming existing challenges, driving breakthroughs in kirigami mechanics, and enabling innovative applications in areas such as soft robotics, deployable systems, and flexible electronics.
Keywords
INTRODUCTION
With the rapid advancement of cutting-edge technologies, the operational environments for engineering materials, structural systems, and high-end equipment have become increasingly complex[1]. This often requires the evaluation of mechanical responses under extreme conditions. To meet the stringent requirements of unconventional service environments, a diverse array of advanced materials and structures with extreme physical properties has been developed. These include ultra-soft, ultra-light, highly sensitive, and highly stretchable materials, as well as those exhibiting novel anomalous physical effects[2,3]. Kirigami, a traditional paper-cutting art form celebrated as a cultural treasure, has recently found applications in scientific research. Kirigami-based metamaterials exhibit a unique set of exceptional properties, including extensive elastic tunability, remarkable stretchability, ultra-softness, ultra-lightness, and high sensitivity, along with diverse geometric and topological transformations[4,5]. The fabrication of kirigami metamaterials is relatively simple and scalable, enabling large-scale production. Moreover, these materials possess distinct mechanical features such as reconfigurability, self-assembly, and multi-stability[6-8]. As a result, kirigami metamaterials have emerged as a frontier of research in advanced solid materials and structures, offering programmability and a wide range of potential applications beyond the capabilities of conventional materials[9,10].
Kirigami, as a prominent class of advanced structural materials, is rapidly advancing towards enhanced lightweighting, flexibility, integration, functionalization, and intelligence. In this context, the application scope of kirigami metamaterials has expanded significantly, ranging from highly stretchable kirigami devices on the atomic scale to large-scale deployable metamaterials and mechanisms with exceptional packing efficiency [Figure 1][11-17]. The inherent multiscale characteristics of these structures span several orders of magnitude[18-21], establishing kirigami metamaterials as an effective design strategy for modulating and enhancing the key mechanical properties of materials and structures. For instance, in soft robotics, kirigami structures enable the design of grippers and actuators that combine precise control and adaptability, offering solutions for manipulating delicate objects or operating in confined, unstructured environments. In deployable systems, their geometric tunability allows for highly efficient packing and reliable reconfiguration, making them ideal for space-based technologies such as solar arrays and antenna systems. Furthermore, in flexible electronics, kirigami metamaterials facilitate the creation of highly stretchable and durable wearable devices, foldable displays, and energy-harvesting systems by integrating electrical conductivity with mechanical resilience. Currently, researchers have underscored the importance of giving equal priority to the geometric and material design aspects of kirigami metamaterials[22-24]. By leveraging interdisciplinary insights from physics, chemistry, biology, and materials science, this field seeks to elucidate the mapping relationships between critical scientific problems across domains and the unique mechanics of kirigami metamaterials. Such an interdisciplinary approach is poised to inject fresh momentum into the advancement of kirigami metamaterials, paving the way for novel applications in areas such as tunable advanced metamaterials, soft robotics, microelectronic devices, nanocomposites, triboelectric generators, solar photovoltaics, and stretchable electronics[25-27].
Figure 1. Multiscale properties and deformation modes of kirigami metamaterials. Nanoscale[11]: Graphene kirigami enables the fabrication of resilient, tunable microscale structures with customizable mechanical properties, exploiting the unique bending stiffness of the material; Sub-microscale[12]: A kirigami-inspired approach enhances the elasticity and multifunctionality of nanocomposites, enabling predictable tensile behavior, high strain tolerance, and stable electrical conductance, with applications in stretchable electronics and plasma-based devices; Micron-scale[13]: Microscopic kirigami-based metasheet robots enable electronically configurable shape morphing, achieving dynamic locomotion and programmable deformation, with potential applications in reconfigurable micromachines and biomedical devices; Millimeter-scale[14]: Kirigami-patterned soft grippers enable precise, rapid, and scalable object manipulation, offering modular and remotely actuated solutions for robotics, haptics, and biomedical applications; Centimeter-scale[15]: Kirigami-based metamaterials enable rapid, reversible shape morphing with load-bearing capacity and self-healing properties, facilitating multifunctional soft robots that autonomously reconfigure for diverse tasks; Decimeter-scale[16]: Bioinspired kirigami metasurfaces on footwear outsoles enhance friction and grip, reducing the risk of slips and falls, particularly on slippery surfaces such as ice; and Meter-scale[17]: Soft deployable reflectors based on kirigami/origami structures enable large-scale, compact beam steering mechanisms, suitable for applications in sensing, imaging, and solar tracking.
To accurately characterize the cross-scale, multi-level, ultra-soft, highly sensitive, and stretchable mechanical behaviors of kirigami metamaterials under complex conditions, there is an urgent need for a new conceptual framework. This framework should incorporate appropriate loading and deformation parameters, along with the nonlinear and asymmetric interactions between material and structural properties. Addressing the limitations of current models and design paradigms is crucial for advancing kirigami metamaterial mechanics and enhancing their engineering applications. Furthermore, this research direction challenges foundational concepts in related fields such as extreme materials, structural mechanics, and metamaterials. A thorough understanding of in-plane tensile mechanics is crucial for exploiting the exceptional properties of kirigami metamaterials. Key research areas include the study of in-plane and out-of-plane tensile buckling instabilities, as well as the analysis of local-global coupled buckling mechanics under strain constraints. These aspects are essential for developing a robust mechanical framework for kirigami metamaterials. Many of the extreme properties of kirigami metamaterials stem from their static nonreciprocal mechanisms[28]. Current mechanical theories have difficulty fully capturing the complex behaviors seen during deformation, including strong geometric dependencies, pronounced nonlinearities, buckling instabilities, and multi-stability[29]. Thus, exploring the mechanics of kirigami metamaterials through the lens of static nonreciprocity is imperative. In this Perspective, we aim to exploit nonreciprocal mechanisms to address challenges related to deformation processes and different modes of buckling instability. By doing so, we seek to pave the way for a deeper understanding and broaden the application potential of kirigami metamaterials across diverse scientific and engineering domains.
RECENT ADVANCES IN KIRIGAMI METAMATERIALS
In-plane flexible stretching of kirigami
Early research on the flexible stretching of kirigami metamaterials predominantly centered on the analysis of their in-plane tensile behaviors [Figure 2][30-33]. This involved leveraging data from tensile experiments and numerical simulations to explore the scaling laws that effectively establish dimensionless geometric variable relationships within the design space of kirigami metamaterials. Such investigations have shed light on the evolution of critical in-plane mechanical properties, such as stiffness, as influenced by geometric configurations. However, the common use of linear cut designs has often resulted in severe stress concentrations at the cut edges, leading to catastrophic fracture failures. To address this issue, innovative deformation strategies, particularly those based on curved cut designs, have become an urgent area of focus for advancing the field[34,35].
Figure 2. (A) In-plane deformations of kirigami metamaterials during the initial phase, as shown in the force-displacement curve. This stage is characterized by buckling bifurcations and the transition from 2D to 3D microstructures[30]; (B) In-plane deformations of thicker kirigami metamaterials, where the structural thickness is ten times the beam width to prevent out-of-plane buckling, satisfying the plane strain condition[31-33].
Specifically, scaling analyses provide a quantitative framework for describing these metamaterials, effectively revealing the underlying physical principles and mechanical behaviors throughout the tensile process, particularly focusing on in-plane stretching. Beam model-based theories, which consider bending, membrane, and shear deformation energies, utilize energy and variational principles to derive closed-form solutions for essential mechanical properties such as stiffness, flexibility, and ductility. This approach offers a precise method for analyzing the in-plane tensile mechanics of kirigami metamaterials. The initial development of scaling laws for kirigami metamaterials identified three distinct phases in tensile mechanical response: the initial phase, the softening phase, and the hardening phase, as illustrated in Figure 2A[30]. The transition from the initial phase to the softening phase is governed by buckling bifurcations, enabling the formation of buckled microstructures transitioning from two- (2D) to three-dimensional (3D). The hardening phase emerges when the deformation mode shifts from bending-dominated to stretching-dominated behavior. Despite these findings, the mechanical responses in the softening and hardening stages were predominantly investigated through experimental methods. Additionally, scaling laws were applied to quantitatively describe the in-plane stiffness of specific kirigami structures[15,31]. In advancing the framework, a scaling analysis approach was formulated to address in-plane deformation exclusively, with structural thickness set at ten times the beam width to prevent out-of-plane buckling, satisfying the plane strain condition [Figure 2B][32]. Extending the unit cells horizontally and vertically resulted in the formation of periodic kirigami metamaterials. Building on these principles, a model based on curved beam theory and plane strain elasticity was developed to capture the in-plane tensile mechanics of 1D periodic kirigami metamaterials with curved cuts[32,33]. Exact closed-form solutions were obtained for stiffness, flexibility, and ductility across various dimensionless geometric parameters. Validation through molecular dynamics simulations, finite element analyses, and experimental testing confirmed the accuracy and robustness of this framework[32]. The introduction of complex curved designs significantly expanded the structural design space, providing multiple degrees of freedom and enabling optimized configurations tailored to specific mechanical requirements[33].
Out-of-plane multimodal instability of kirigami
The analysis of out-of-plane tensile buckling instability in kirigami metamaterials has primarily relied on empirical design approaches, including scaling analyses, simulations, and experimental studies, to elucidate the formation mechanisms of buckled structures [Figure 3][36,37]. Despite these efforts, there remains a significant gap in reliable mechanical models to address key challenges, such as the diverse buckling modes induced by tensile loading, the critical conditions for mode transitions, and the extreme elasticity observed in post-buckling deformation. There is a pressing need for comprehensive research into the mechanics of buckling instability in kirigami metamaterials.
Figure 3. Geometric design and tensile instability modes of kirigami[37]. Illustration of the different buckling modes in kirigami metamaterials under tensile loading, including symmetric and asymmetric configurations, with emphasis on how geometric design influences buckling behavior. The scale bars represent 5 mm. Color bar represents the magnitude of von Mises stress normalized by the material’s elastic modulus.
Existing models of in-plane tensile mechanics can effectively predict critical mechanical metrics such as stiffness, flexibility, and ductility. However, these models are generally applicable to thicker kirigami metamaterials or limited to the initial response phase of thin structures where buckling is considered[38]. For thin kirigami metamaterials, the triggering mechanisms of buckling instability, the formation of post-buckling configurations, and the ultimate deformation limits remain inadequately characterized. Recent findings indicate that elastic kirigami metamaterials display a wide range of buckling modes, as shown in Figure 3, including both symmetric and asymmetric configurations[37]. Theoretical exploration of tensile buckling instability has largely employed beam, plate, and shell models, utilizing energy principles and variational methods to analyze critical parameters such as buckling force, buckling displacement, and post-buckling evolution. In beam-based analyses, a skewed beam approach has been used to describe the total potential energy for symmetric buckling, leading to the derivation of a scaling law for the critical buckling force[37,39]. A sinusoidal beam theory has also been applied, focusing on the overall energy considerations without distinguishing between symmetric and asymmetric buckling, resulting in a direct scaling law for the critical buckling force[40]. For plate models, the Föppl-von Kármán theory has been extended to investigate buckling instability, albeit limited to specific kirigami frameworks[41]. The critical buckling displacement has been represented using scaling laws. Further advancements include the study of local buckling instability at cut edges, where the local post-buckling behavior has been modeled as an e-cone shape under isometric constraints[42,43]. By neglecting the contribution of membrane energy and applying isometric mapping, both the first and second fundamental forms of the deformed surface were derived, incorporating normal curvature. A governing equation for normal curvature was formulated based on the boundary conditions. In the context of shell models, the instability mechanics of kirigami metamaterials have been examined for both symmetric and asymmetric buckling modes[36]. Under tensile loading, the complex central deformation of the symmetrically buckled kirigami structure was equivalently modeled as an inverse bending problem of a cylindrical shell. By specifying the driving moment of the cylindrical shell, the elastic deformation energy was calculated, and using energy principles and variational methods, expressions for critical buckling stress and strain in both symmetric and asymmetric buckling modes were derived.
However, the buckling instability behavior of kirigami is often constrained by geometric symmetry designs and minimum energy principles, resulting in buckling modes being limited to symmetric and antisymmetric forms[36,44]. These limitations not only reduce design flexibility but also restrict its potential for broader functional applications. The introduction of deep learning technology provides a powerful tool for overcoming these bottlenecks [Figure 4]. In particular, convolutional neural networks (CNNs) and recurrent neural networks (RNNs), known for their advantages in handling complex nonlinear problems, have become an efficient tool for the analysis and design of kirigami buckling behavior. Specifically, CNNs can be employed to classify buckling modes of kirigami under different geometric designs, encompassing symmetric, antisymmetric, and asymmetric buckling behaviors[45]. Through high-precision recognition of buckling modes, designers can rapidly identify geometric parameters associated with desired performance. Meanwhile, RNNs excel in predicting the constitutive relationships of materials during stretching and buckling processes[39]. By integrating experimental data and geometric information, RNNs accurately forecast the mechanical responses of materials under various loading and deformation conditions, thereby offering theoretical support for programmable kirigami design. The use of deep learning not only expands the buckling mode space of kirigami, but also highlights the critical influence of geometric parameters on buckling behavior[39]. Certain geometric parameters significantly enhance the sensitivity of buckling modes, enabling controllability, while others render the buckling modes stable or even inert. This geometry-dependent behavior provides valuable guidance for target-driven designs, allowing kirigami to balance tensile performance and buckling behavior, thereby meeting diverse functional requirements.
Figure 4. Deep learning-based framework (CNN + RNN) for kirigami design[39]. (A) Kirigami dataset and neural network modeling, where CNNs classify geometric configurations and buckling modes to extract key design parameters; (B) Parameter design through forward and target-driven approaches to optimize geometric configurations for enhanced mechanical behaviors such as improved buckling modes and stability; (C) Evolving kirigami structures for specific functionalities, enabling tailored designs for improved tensile performance, controlled buckling behavior, and expanded application potential. CNN: Convolutional neural network; RNN: recurrent neural network.
Multimodal instability of kirigami under strain constraints
The study of buckling instability in kirigami metamaterials under strain constraints has primarily focused on surface instability evolution, such as wrinkling and warping[46-49]. However, the potential for multifunctional integration in kirigami metamaterials has not been fully explored, and there is a lack of a mechanical design paradigm that incorporates high flexibility, high ductility, high compressibility, and multifunctional integration. There is an urgent need to explore new types of kirigami metamaterials or mechanisms that simultaneously feature extreme properties and multifunctional integration. Strain constraint is a common design strategy in the buckling instability mechanics of thin film/substrate structures[50]. Through strain-constrained design, 3D configurations are formed on the surface, which can impart unique physical properties to the surface and have a wide range of applications in modern technology. As the scope of research continues to expand, the introduction of kirigami patterns into thin films or substrates, combined with strain-constraint strategies, has led to the development of strain-constrained kirigami metamaterials [Figure 5][46,47]. These metamaterials are no longer limited to simple thin film/substrate models, enabling extreme mechanical behaviors with high flexibility, ductility, compressibility, and multifunctional integration. Nonlinear numerical simulations have been employed to develop models for plane strain beams of kirigami metamaterials, revealing potential buckling instability behaviors under flexible substrate strain constraints. These simulations can then be applied to interface smart adhesion[51]. Other research has focused on designing microstructures for flexible substrates and constructing strain-constrained kirigami metamaterials[52,53]. In these structures, substrates with microstructures are placed on rigid supports, while thin films are adhered to the substrates. When strain is applied along the horizontal direction, the surface exhibits a sinusoidal wrinkling pattern. In this structure, the Föppl-von Kármán equation is used to describe the membrane deformation, while the Winkler foundation is employed to simulate the kirigami substrate. Additionally, thin films with kirigami patterns can adhere to pre-stretched flexible substrates, and under strain constraints, the resulting kirigami metamaterials exhibit bistability, multi-stability, and self-assembly characteristics[46,47,54]. By designing different kirigami patterns for the thin films, the buckling instability modes of the kirigami metamaterials under strain constraints become highly diverse, offering a new paradigm for the mechanical design of metamaterials[38].
Figure 5. Multimodal instability of kirigami metamaterials under strain constraints[46,47]. Buckling behaviors, including wrinkling, bistability, and multi-stability, emerge in kirigami metamaterials under strain constraints, showcasing their potential for extreme flexibility, ductility, and multifunctional integration.
Static nonreciprocal kirigami via nonlinear instability
The behaviors of kirigami metamaterials are strongly influenced by mechanical directionality, exhibiting distinct responses in the forward and reverse processes [Figure 6A and B][55,56]. Additionally, this is accompanied by the coupling of constitutive material properties and geometric symmetry[57,58]. Research on the tensile instability of static nonreciprocal kirigami metamaterials has primarily concentrated on simple in-plane deformation modes. This narrow design space significantly limits the ability of kirigami metamaterials to break the time-reversal symmetry and the topological protection of microstructural reversibility. The lack of consideration for diverse nonlinear buckling modes, which induce substantial nonreciprocity, hinders a full understanding of the origins of the extreme physical and mechanical properties observed in these materials[59]. Therefore, there is an urgent need to develop diverse buckling instability theories for kirigami metamaterials based on static nonreciprocal mechanisms.
Figure 6. Static nonreciprocal and reciprocity behavior of kirigami metamaterials[29,55,56]. (A) Static nonreciprocal and reciprocity mechanisms of kirigami metamaterials; (B) Mechanical responses of kirigami structures differ in forward and reverse directions due to the coupling of material properties, geometric symmetry, and nonlinear buckling instabilities; (C) Static nonreciprocity arises from in-plane snap-through buckling of vertical beams, leading to distinct displacement-force curves. The angle of the vertical beams controls the symmetry and nonreciprocal behavior, which is critical for applications in tunable devices and soft robotics. Nonreciprocal behavior is analyzed using models such as the discrete spring model and in-plane tensile mechanics; (D) For reciprocal kirigami, the displacement-force curve response is linear.
Static nonreciprocity, as an important mechanical response property, has significant potential in applications such as tunable topological dynamic devices, energy control, soft metamaterials, imaging technology, soft robotics, and microelectronics, drawing considerable attention from the scientific community[29]. Currently, the design of kirigami metamaterials provides a powerful means of achieving static nonreciprocity, and more importantly, the development of a mechanics model for kirigami metamaterial based on static nonreciprocal mechanisms is also progressing[55]. A specific type of asymmetric and highly nonlinear kirigami metamaterial, based on static nonreciprocal mechanisms, has been explored. This kirigami structure consists of horizontal and vertical beams, with the angle of the vertical beams controlling the symmetry of the kirigami metamaterial [Figure 6C][29]. Notably, when the angle is zero, the structure exhibits symmetry. The system was subjected to equal magnitude reverse tensile testing, a method commonly used to experimentally assess static nonreciprocity in certain kirigami metamaterials that are not under compression. The experimental testing revealed significant static nonreciprocity in the displacement-force curve [Figure 6C and D], a characteristic that directly results from in-plane snap-through buckling instability of the microstructural vertical beams. The displacement characterization based on static nonreciprocity is defined through both forward and reverse mechanical processes, capturing the displacements at the ends of the kirigami structure in each direction and incorporating their coupling effects. A simplified discrete spring model indicates that this displacement characteristic is the result of the fine-tuned collaboration between structural asymmetry, material nonlinearity, and other factors[56]. Further studies on the equivalent modulus of the kirigami metamaterials based on static nonreciprocity showed that the discrete spring model is overly simplistic, providing accurate results only under small input forces[56]. By applying the static nonreciprocal mechanism and nonlinear beam theory, an in-plane tensile mechanics model for kirigami metamaterials was developed, followed by a mathematical expression for the modulus[29,56].
PERSPECTIVE
Challenges in designing kirigami metamaterials for large deformations with strong geometric dependence
Kirigami metamaterials have emerged as a frontier topic in the field of advanced materials and intelligent structures. Cutting-edge research on kirigami metamaterials has brought to light their unique deformation characteristics under unconventional environmental conditions, including extreme softness, hypersensitivity, super-extensibility, and complex nonlinear couplings. Consequently, elucidating the deformation mechanisms of kirigami metamaterials and investigating the underlying principles governing their extraordinary mechanical properties hold promise for revolutionary advances in the adaptive control and design of materials, structures, and devices. To date, the kinematic and geometric deformation properties of kirigami metamaterials have predominantly been analyzed under the rigid body assumption. However, due to the unconventional service environments of these metamaterials, even slight external perturbations can lead to substantial discrepancies between predicted behavior and actual observations. For example, deviations exceeding 20% in kirigami metamaterial-based biological heart monitoring devices[60]. As a result, it is essential to develop flexible tensile mechanics methodologies to counteract the adverse effects introduced by the rigid body assumption.
Currently, the majority of kirigami metamaterial designs rely on linear incisions, which often result in severe stress concentrations at the tips of the cuts, making these regions particularly vulnerable to fracture and failure. To mitigate such catastrophic risks, innovative deformation design strategies, including those based on curved cuts, are critically needed. Kirigami metamaterials with curved designs typically exhibit high-curvature features, display multiple topological transformation modes, and interact strongly with regions of high curvature [Figure 2]. The pronounced nonlinear response of the material and its strong dependence on geometric configuration further complicate the formulation of a scientific framework for flexible tensile mechanics, thereby hindering practical engineering applications. This challenge constitutes a major technical bottleneck in the development of kirigami metamaterials. Therefore, resolving the design challenges and flexible tensile mechanics issues inherent to kirigami metamaterials is an urgent priority and remains one of the most critical fundamental scientific problems in this field.
The critical need for reliable models in multimodal in-plane and out-of-plane instabilities of kirigami
Kirigami metamaterials exhibit versatility across a wide range of scales, from the atomic level to large-scale deployable structures for space applications, highlighting their immense potential [Figure 1]. However, these studies reveal significant scientific challenges, particularly in understanding and controlling buckling instabilities within kirigami metamaterials. Currently, most researches on their buckling behavior rely on empirical design approaches rooted in experiments, simulations, and scaling analyses. As a result, critical aspects such as stiffness variations, mechanisms triggering buckling, and the progression of post-buckling instabilities remain insufficiently understood.
While some researchers have posited that kirigami metamaterials only exhibit out-of-plane buckling with a single mode, the reality is far more nuanced. In practice, diverse nonlinear buckling modes, including both in-plane and out-of-plane deformations, are central to the mechanical behavior of kirigami metamaterials
Challenges of nonlinear and asymmetric behavior in kirigami: the need for static nonreciprocal mechanisms
In elastic materials and structures, reciprocity (also known as Maxwell-Betti reciprocity or the reciprocal theorem) is a fundamental principle rooted in Noether’s theorem, which states that each symmetry corresponds to a conservation law, and vice versa. The Maxwell–Betti theorem [Figure 6] is mathematically formulated as:
where FA (FB) is the applied force at point A (B) and uAB (uBA) is the displacement at point B (A) induced by FA (FB). This principle provides a robust framework for solving problems in elasticity theory. Static nonreciprocity (FAuBA ≠ FBuAB) refers to the phenomenon where force transmission is unimpeded in the forward mechanical process but significantly hindered in the reverse process [Figure 6]. In simpler terms, if a material or physical entity exhibits different deformation behaviors in one direction compared to the opposite direction, this is termed a static nonreciprocal mechanism (i.e., the mechanical responses differ between forward and reverse processes). The static nonreciprocal mechanism differentiates between forward and reverse mechanical processes, revealing deeper mechanical insights that traditional theories for kirigami metamaterial (which do not distinguish between forward and reverse processes) and existing research methodologies fail to uncover. Design methods inspired by static nonreciprocal mechanisms are becoming a focal point in the field of extreme property materials and metamaterials.
As the applications of kirigami metamaterials continue to expand, they encounter increasingly complex and extreme service environments. Conventional mechanical analysis methods for kirigami metamaterials struggle to fully capture their new characteristics, such as pronounced asymmetry and nonlinearity. These methods fall short in accurately explaining the complex mechanical behaviors involved during deformation, including strong geometric dependence, significant geometric and material nonlinearity, instability phenomena (e.g., lateral buckling, surface wrinkling, snap-through instability), and multistable states (including bistability). Additionally, reciprocity is an intrinsic property of materials and structures, protected by time-reversal symmetry and the reversibility of microscopic structures. Breaking these two symmetries to achieve static nonreciprocity and thereby realize extreme physical properties in kirigami metamaterials is extremely challenging.
Moreover, research on static nonreciprocal kirigami metamaterials must consider the coupling of physical quantities during forward and reverse mechanical processes and special forms of energy [Figure 6]. This poses significant challenges not only for formulating the control equations for buckling and instability but also for solving them effectively. Current studies based on static nonreciprocal mechanisms primarily focus on simple in-plane deformation modes. This narrow design space restricts the ability of kirigami metamaterials to overcome the topological protection imposed by symmetry, neglecting the substantial contributions from various nonlinear buckling instability modes (such as in-plane, out-of-plane buckling, symmetric and antisymmetric buckling, lateral buckling, surface wrinkling, and snap-through instability). Consequently, existing approaches fail to fully capture the extraordinary physical properties and mechanical characteristics of kirigami metamaterials, which go beyond those of conventional materials and structures.
Therefore, it is imperative to establish a comprehensive design theory and solution framework for kirigami metamaterials based on the static nonreciprocal mechanism. Expanding the design space through features such as high curvature is crucial, as it allows for a significant enhancement of nonlinearity and sensitivity in mechanical systems by leveraging diverse buckling instability modes. Achieving an accurate characterization of both in-plane and out-of-plane buckling instabilities is necessary to uncover the origins of the extreme mechanical phenomena and laws governing kirigami metamaterials. While the current manuscript introduces the potential of static nonreciprocal mechanisms in addressing these challenges, future research should focus on developing analytical and computational models that integrate the coupled effects of geometric configurations, material properties, and boundary conditions under extreme operating environments. Additionally, exploring programmable designs that actively utilize multimodal instabilities could open new pathways for dynamic control and reconfigurability in kirigami systems. Investigating interdisciplinary approaches, such as combining deep learning and multiscale simulation techniques, may further accelerate breakthroughs in understanding and applying these metamaterials. Enhancing this forward-looking perspective will not only address unresolved challenges but also set the stage for novel applications, thus reinforcing the cutting-edge nature of this research.
CONCLUSIONS
In summary, the challenges posed by in-plane and out-of-plane buckling instabilities in kirigami metamaterials are unavoidable and require urgent resolution. Despite the significant difficulty, advancing the study of buckling instabilities based on the static nonreciprocal mechanism is essential. Key issues include understanding the in-plane tensile mechanics, out-of-plane buckling behavior under tensile loading, and buckling instability under strain constraints, along with the tensile-compressive characteristics of kirigami metamaterials. These areas are critical to developing a deeper understanding of the buckling mechanisms in kirigami metamaterials and must be addressed systematically. Notably, the development of flexible tensile mechanics methods to rigorously mitigate the limitations of the rigid body assumption is widely recognized as a bottleneck issue in this field. In addition, in the context of extreme service environments, the occurrence of diverse nonlinear buckling instability modes (both in-plane and out-of-plane) and the unique conditions that trigger these instabilities present significant challenges. The absence of effective mechanical models has become a major obstacle in establishing a comprehensive mechanical theory for kirigami metamaterials. Although progress has been made in the study of kirigami metamaterials under the framework of reciprocity, there remains a considerable gap between current research outcomes and practical requirements. In contrast, the static nonreciprocal mechanism distinguishes between forward and reverse mechanical processes, uncovering deeper insights into the tensile and buckling instability behaviors of kirigami metamaterials. However, foundational research in this area is still relatively underdeveloped, and there is an urgent need to establish relevant design theories and solution frameworks.
Furthermore, the actuation methods of kirigami metamaterials play a crucial role and deserve greater attention in future research. Actuation can be achieved through various physical methods such as magnetic actuation, electrical actuation, and light-driven actuation. Incorporating these strategies not only enhances the versatility of kirigami metamaterials but also enables dynamic control of their mechanical properties and deformation behaviors under different conditions. We propose that future studies explore these actuation methods in depth, with a focus on integrating them into the development of advanced design frameworks for kirigami metamaterials. This addition would provide a more comprehensive outlook and further broaden the application potential of these materials.
DECLARATIONS
Authors’ contributions
Made substantial contributions to the conception and design of the study, and led the interpretation of results: Wang, Y.; Liu, J.
Contributed significantly to the methodology and performed data analysis and interpretation: Huang, W.
Conducted data acquisition, provided administrative and technical support, and contributed essential materials: Liu, M.; Sareh, P.
All authors have read the manuscript and approved the final version.
Availability of data and materials
Not applicable.
Financial support and sponsorship
Wang, Y. acknowledges support from the National Natural Science Foundation of China under Grant No. 12202105 and the Shenzhen Basic Research Program under Grant No. JCYJ20240813094159001. Liu, M. acknowledges start-up funding from the University of Birmingham, UK. Huang, W. acknowledges start-up funding from Newcastle University, UK.
Conflicts of interest
All authors declared that there are no conflicts of interest.
Ethical approval and consent to participate
Not applicable.
Consent for publication
Not applicable.
Copyright
© The Author(s) 2025.
REFERENCES
1. Bertoldi, K.; Vitelli, V.; Christensen, J.; van, H. M. Flexible mechanical metamaterials. Nat. Rev. Mater. 2017, 2, 17066.
2. Tao, J.; Khosravi, H.; Deshpande, V.; Li, S. Engineering by cuts: how kirigami principle enables unique mechanical properties and functionalities. Adv. Sci. 2022, 10, e2204733.
3. Yang, X.; Zhou, Y.; Zhao, H.; et al. Morphing matter: from mechanical principles to robotic applications. Soft. Sci. 2023, 3, 38.
4. Jin, L.; Yang, S. Engineering kirigami frameworks toward real-world applications. Adv. Mater. 2024, 36, 2308560.
5. Zhang, Q.; Shi, Y.; Zhao, Z. A brief review of mechanical designs for additive manufactured soft materials. Soft. Sci. 2022, 2, 2.
6. Yang, X.; Forró, C.; Li, T. L.; et al. Kirigami electronics for long-term electrophysiological recording of human neural organoids and assembloids. Nat. Biotechnol. 2024, 42, 1836-43.
7. Zhang, H.; Paik, J. Kirigami design and modeling for strong, lightweight metamaterials. Adv. Funct. Mater. 2022, 32, 2107401.
8. Meng, Z.; Liu, M.; Yan, H.; Genin, G. M.; Chen, C. Q. Deployable mechanical metamaterials with multistep programmable transformation. Sci. Adv. 2022, 8, eabn5460.
9. Wang, J.; Wang, R.; Zhu, Z.; Zhou, K.; Wang, D. Untethered kirigami soft robots with programmable locomotion. Appl. Phys. Rev. 2023, 10, 041405.
10. Kim, J.; Chamorro, L. P. Coupled mechanics in skin-interfaced electronics via computer vision methods. Soft. Sci. 2024, 4, 12.
12. Shyu, T. C.; Damasceno, P. F.; Dodd, P. M.; et al. A kirigami approach to engineering elasticity in nanocomposites through patterned defects. Nat. Mater. 2015, 14, 785-9.
13. Liu, Q.; Wang, W.; Sinhmar, H.; et al. Electronically configurable microscopic metasheet robots. Nat. Mater. 2025, 24, 109-15.
14. Yang, Y.; Vella, K.; Holmes, D. P. Grasping with kirigami shells. Sci. Robot. 2021, 6, eabd6426.
15. Hwang, D.; Barron, E. J.; Haque, A. B. M. T.; Bartlett, M. D. Shape morphing mechanical metamaterials through reversible plasticity. Sci. Robot. 2022, 7, eabg2171.
16. Babaee, S.; Pajovic, S.; Rafsanjani, A.; Shi, Y.; Bertoldi, K.; Traverso, G. Bioinspired kirigami metasurfaces as assistive shoe grips. Nat. Biomed. Eng. 2020, 4, 778-86.
17. Wang, W.; Li, C.; Rodrigue, H.; et al. Kirigami/origami-based soft deployable reflector for optical beam steering. Adv. Funct. Mater. 2017, 27, 1604214.
18. Wang, Y.; Wang, C.; Zhang, Y.; Tan, H. Graphene kirigami as reinforcement and interfacial bonding effect for toughness and strength of silicon-based nanocomposites. Comp. Mater. Sci. 2019, 159, 306-15.
19. Zhang, J.; Zhang, L.; Wang, Y.; Wang, Y.; Wang, C. Flexible kirigami with local cylindrical shell design for stretchable microstrip antenna. Compos. Struct. 2022, 296, 115879.
20. He, R.; Chen, Y.; Liang, J.; Sun, Y.; Feng, J.; Sareh, P. Crystallographically programmed kirigami metamaterials. J. Mech. Phys. Solids. 2024, 193, 105903.
21. Shi, P.; Chen, Y.; Feng, J.; Sareh, P. Highly stretchable graphene kirigami with tunable mechanical properties. Phys. Rev. E. 2024, 109, 035002.
22. An, N.; Domel, A. G.; Zhou, J.; Rafsanjani, A.; Bertoldi, K. Programmable hierarchical kirigami: programmable hierarchical kirigami. Adv. Funct. Mater. 2020, 30, 1906711.
23. Jin, L.; Forte, A. E.; Deng, B.; Rafsanjani, A.; Bertoldi, K. Kirigami-inspired inflatables with programmable shapes. Adv. Mater. 2020, 32, e2001863.
24. Chaudhary, G.; Niu, L.; Han, Q.; Lewicka, M.; Mahadevan, L. Geometric mechanics of ordered and disordered kirigami. Proc. R. Soc. A. 2023, 479, 20220822.
25. Dudte, L. H.; Choi, G. P. T.; Becker, K. P.; Mahadevan, L. An additive framework for kirigami design. Nat. Comput. Sci. 2023, 3, 443-54.
26. Choi, G. P. T.; Liu, L.; Mahadevan, L. Explosive rigidity percolation in kirigami. Proc. R. Soc. A. 2023, 479, 20220798.
27. Liu, Z.; Hu, X.; Bo, R.; et al. A three-dimensionally architected electronic skin mimicking human mechanosensation. Science 2024, 384, 987-94.
28. Veenstra, J.; Gamayun, O.; Guo, X.; Sarvi, A.; Meinersen, C. V.; Coulais, C. Non-reciprocal topological solitons in active metamaterials. Nature 2024, 627, 528-33.
29. Coulais, C.; Sounas, D.; Alù, A. Static non-reciprocity in mechanical metamaterials. Nature 2017, 542, 461-4.
30. Isobe, M.; Okumura, K. Initial rigid response and softening transition of highly stretchable kirigami sheet materials. Sci. Rep. 2016, 6, 24758.
31. Xu, L.; Wang, X.; Kim, Y.; Shyu, T. C.; Lyu, J.; Kotov, N. A. Kirigami nanocomposites as wide-angle diffraction gratings. ACS. Nano. 2016, 10, 6156-62.
32. Wang, Y.; Wang, C.; Tan, H. Geometry-dependent stretchability and stiffness of ribbon kirigami based on large curvature curved beam model. Int. J. Solids. Struct. 2020, 182-183, 236-53.
33. Hong, Y.; Chi, Y.; Wu, S.; Li, Y.; Zhu, Y.; Yin, J. Boundary curvature guided programmable shape-morphing kirigami sheets. Nat. Commun. 2022, 13, 530.
34. Wang, Y.; Wang, C. Effect of temperature difference on the mechanical responses of ribbon kirigami: toward the highly stretchable conductors. Int. J. Mech. Sci. 2020, 168, 105301.
35. Wang, Y.; Zhao, W.; Du, Y.; Dai, Z.; Liu, Y.; Xu, F. Substantial curvature effects on compliant serpentine mechanics. Mech. Mater. 2023, 184, 104732.
36. Wang, Y.; Wang, C. Buckling of ultrastretchable kirigami metastructures for mechanical programmability and energy harvesting. Int. J. Solids. Struct. 2021, 213, 93-102.
37. Yang, Y.; Dias, M. A.; Holmes, D. P. Multistable kirigami for tunable architected materials. Phys. Rev. Mater. 2018, 2, 110601.
38. Wang, Y.; Wang, C. Mechanics of strain-limiting wrinkled kirigami for flexible devices: high flexibility, stretchability and compressibility. Int. J. Solids. Struct. 2022, 238, 111382.
39. Zhang, Y.; Wang, Y.; Tao, Q.; Liu, Y.; Wang, C. Deep learning of buckling instability in geometrically symmetry-breaking kirigami. Int. J. Mech. Sci. 2024, 280, 109331.
40. Tang, Y.; Lin, G.; Yang, S.; Yi, Y. K.; Kamien, R. D.; Yin, J. Programmable kiri-kirigami metamaterials. Adv. Mater. 2017, 29, 1604262.
41. Moshe, M.; Esposito, E.; Shankar, S.; et al. Kirigami mechanics as stress relief by elastic charges. Phys. Rev. Lett. 2019, 122, 048001.
42. Sadik, S.; Dias, M. A. On local kirigami mechanics I: isometric conical solutions. J. Mech. Phys. Solids. 2021, 151, 104370.
43. Sadik, S.; Walker, M. G.; Dias, M. A. On local kirigami mechanics II: stretchable creased solutions. J. Mech. Phys. Solids. 2022, 161, 104812.
44. Chen, Y.; He, R.; Hu, S.; et al. Design–material transition threshold of ribbon kirigami. Mater. Design. 2024, 242, 112979.
45. Hanakata, P. Z.; Cubuk, E. D.; Campbell, D. K.; Park, H. S. Accelerated search and design of stretchable graphene kirigami using machine learning. Phys. Rev. Lett. 2018, 121, 255304.
46. Liu, M.; Domino, L.; Vella, D. Tapered elasticæ as a route for axisymmetric morphing structures. Soft. Matter. 2020, 16, 7739-50.
47. Politecnica, A. S. SBINBEN: smart bio-inspired building envelopes. 2024. https://www.youtube.com/watch?v=b8JnACyN8x4. (accessed 2025-02-27).
48. Wang, Y.; Du, Y.; Xu, F. Strain stiffening retards growth instability in residually stressed biological tissues. J. Mech. Phys. Solids. 2023, 178, 105360.
49. Wang, Y.; Li, Z.; Chen, X.; et al. Electroactive differential growth and delayed instability in accelerated healing tissues. J. Mech. Phys. Solids. 2024, 193, 105867.
50. Fan, X.; Pan, Z.; Chen, S.; et al. Design and fabrication of a reconfigurable and flexible frequency selective surface with a buckling dipole via mechanical stretching. Soft. Sci. 2021, 1, 13.
51. Zhao, R.; Lin, S.; Yuk, H.; Zhao, X. Kirigami enhances film adhesion. Soft. Matter. 2018, 14, 2515-25.
52. Shuai, Y.; Zhao, J.; Bo, R.; Lan, Y.; Lv, Z.; Zhang, Y. A wrinkling-assisted strategy for controlled interface delamination in mechanically-guided 3D assembly. J. Mech. Phys. Solids. 2023, 173, 105203.
53. Huang, X.; Hai, Y.; Li, B.; Feng, X. Wrinkling of thin films on a microstructured substrate. Mech. Adv. Mater. Struct. 2018, 25, 975-81.
54. Zhang, Y.; Yang, J.; Liu, M.; Vella, D. Shape-morphing structures based on perforated kirigami. Extreme. Mech. Lett. 2022, 56, 101857.
55. Dang, X.; Gonella, S.; Paulino, G. H. Folding a single high-genus surface into a repertoire of metamaterial functionalities. Proc. Natl. Acad. Sci. U. S. A. 2024, 121, e2413370121.
56. Shaat, M.; Moubarez, M. A.; Khan, M. O.; Khan, M. A.; Alzo'ubi, A. Metamaterials with giant and tailorable nonreciprocal elastic moduli. Phys. Rev. Appl. 2020, 14, 014005.
57. Janbaz, S.; Coulais, C. Diffusive kinks turn kirigami into machines. Nat. Commun. 2024, 15, 1255.
58. Dykstra, D. M. J.; Coulais, C. Inverse design of multishape metamaterials. Phys. Rev. Appl. 2024, 22, 064013.
59. Nassar, H.; Yousefzadeh, B.; Fleury, R.; et al. Nonreciprocity in acoustic and elastic materials. Nat. Rev. Mater. 2020, 5, 667-85.
Cite This Article
How to Cite
Download Citation
Export Citation File:
Type of Import
Tips on Downloading Citation
Citation Manager File Format
Type of Import
Direct Import: When the Direct Import option is selected (the default state), a dialogue box will give you the option to Save or Open the downloaded citation data. Choosing Open will either launch your citation manager or give you a choice of applications with which to use the metadata. The Save option saves the file locally for later use.
Indirect Import: When the Indirect Import option is selected, the metadata is displayed and may be copied and pasted as needed.
About This Article
Copyright
Data & Comments
Data
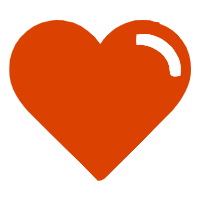
Comments
Comments must be written in English. Spam, offensive content, impersonation, and private information will not be permitted. If any comment is reported and identified as inappropriate content by OAE staff, the comment will be removed without notice. If you have any queries or need any help, please contact us at [email protected].