Intelligent behaviors of hydrogel and liquid crystalline polymer aggregations and collectives: a mini-review
Abstract
Responsive materials exhibit intelligence through their intrinsic ability to autonomously sense and respond to external stimuli. These materials have the potential to form robotic swarms characterized by high flexibility, robust scalability, and fault tolerance. Among various responsive materials, hydrogels and liquid crystalline polymers are particularly advantageous due to their capability for reversible morphological transformations in response to external stimuli, including light, heat, electric field, and magnetic field. While numerous reviews have summarized magnetic swarm robotics, a comprehensive analysis of swarm aggregation behaviors in hydrogel- and liquid crystal-based polymer systems remains lacking. This review addresses this gap by examining (sub)millimeter-scale swarm robots, the fundamental mechanical properties of hydrogels and liquid crystalline polymers following aggregation and assembly, and the respective advantages and limitations of these materials in swarm robotics. Additionally, future research directions in this emerging field are discussed.
Keywords
INTRODUCTION
Group behavior encompasses the interaction patterns among individuals within a collective, typically comprising two or more members coordinating to achieve a shared objective. These behaviors range from relatively simple actions, such as avian migration and fish schooling, to highly complex phenomena, including human cooperation and social organization[1]. The advantages of collective behavior are multifaceted; for instance, birds use vocalizations to signal food sources, while ants employ pheromone trails to guide foraging activities[2]. Division of labor further optimizes resource acquisition, as seen in ant colonies, where specialized worker groups undertake distinct tasks such as foraging and nest construction. Additionally, collective behavior enhances defense mechanisms; for example, fish engage in coordinated movements for migration, predation, and predator avoidance[3-6]. Fire ants exemplify the benefits of such coordination by interlinking their bodies to form buoyant rafts, ensuring survival during floods[7,8]. These collective traits, which surpass individual capabilities, facilitate environmental adaptability and enhance survival prospects.
Collective behavior is not confined to the animal kingdom. In biological systems, cellular communities exhibit coordinated behaviors, such as signal transmission via direct contact[9]. Moreover, robotic swarms have demonstrated emergent cooperative behaviors, with substantial research focusing on micron- and nanometer-scale magnetic robotic groups[10-16]. However, despite the prevalence of swarm behaviors at millimeters and larger scales in nature, such as in ant colonies and fish schools, comparatively fewer studies have explored swarm robotics at these scales.
Robotic swarms achieve complex collective behaviors through decentralized interactions, wherein individual agents operate autonomously, giving rise to emergent behaviors that exceed the sum of individual contributions. Typically, swarm members exhibit independent cognition, enabling sophisticated decision-making and problem-solving. A critical factor in facilitating such emergent intelligence is physical intelligence, which refers to the capacity of a system to respond to external stimuli based on the intrinsic properties of its constituent materials, rather than relying on external circuitry or computational algorithms[17,18]. For robotic swarms to exhibit physical intelligence, their constituent materials must possess stimulus-responsive properties. Among these, liquid crystalline polymers (LCPs) are particularly promising due to their ability to undergo reversible morphological transformations or locomotion in response to stimuli such as light, heat, electricity, and magnetic fields[18-24]. Similarly, hydrogels have emerged as viable candidates due to their responsiveness to light, temperature, and chemical stimuli, as well as their advantageous properties, including self-healing, biocompatibility, controllability, and biodegradability[7,25-32]. This review provides a comprehensive analysis of swarm robotics employing hydrogels and LCPs, highlighting their potential to advance the development of physically intelligent robotic systems.
INTRODUCTION TO HYDROGELS AND LIQUID CRYSTALLINE POLYMERS
Hydrogels and LCPs are both soft materials. Hydrogels consist of hydrophilic polymer networks that retain water within their structure. They are particularly attractive due to their softness, high water content, and biocompatibility[33-38]. By incorporating responsive chemical groups, hydrogels can be designed to exhibit sensitivity to various stimuli, including pH[27], temperature[39,40], light[41-45], electric fields[46], and chemical signals[25]. The actuation capability of hydrogels primarily arises from swelling-induced volume changes. Swelling is driven by modifications in hydrogel properties, such as phase separation [e.g., poly(N-isopropylacrylamide), pNIPAM] or changes in hydrophilicity (e.g., protonation or deprotonation of carboxylic acid groups). When cooling from high temperature to low temperature, the hydrogen bonds between polymer segments in the pNIPAM layer dissociate, and the chains become solvated by water molecules, causing the pNIPAM layer to absorb water and swell [Figure 1A][47]. Similarly, LCPs exhibit significant potential for applications in soft robotics due to their ability to undergo reversible shape deformations in response to external stimuli such as light, heat, electricity, and magnetic fields. The anisotropic nature of calamitic liquid crystals enables LCPs to change shape as a consequence of variations in the scalar order parameter induced by external stimuli[18-24]. Utilizing this mechanism,
Figure 1. Shape changes of hydrogel and LCP actuators. (A) The pNIPAM layer swells and shrinks at low and high temperatures, respectively. Reproduced with permission from ref.[47]. Copyright 2018, Royal Society of Chemistry (RSC). (B) The LCN film oscillates under UV irradiation. (C) The sunlight focused by the lens causes the thin film to oscillate. Reproduced with permission from ref.[48] under the CC -NC license. Copyright 2017, The Authors, published by Wiley-VCH.
ROBOT SWARM BASED ON HYDROGELS AND LIQUID CRYSTALLINE POLYMERS
Swarm robotics refers to a collective of robots that interact with one another, leading to emergent behaviors distinct from those of individual units. Unlike simple robot assemblages, swarm robots exhibit dynamic inter-individual interactions that give rise to unique and complex collective phenomena. Swarm robotics has been extensively explored across different scales, from large-scale electronic robotic swarms to microscale systems such as magnetic microrobot swarms. Currently, huge efforts have been devoted to magnetic swarm robots[12,49-51], which operate at the micro- to nanometer scale and are typically actuated by rotating or oscillating magnetic fields, as well as magnetic field gradients. Given the abundance of reviews on magnetic swarm robotics[52-56], this review will instead focus on robotic swarms composed of (sub)millimeter-scale hydrogels[25,27,28,30,57] and LCPs.
Swarm behaviors of hydrogel-based robotic systems
Hydrogels have been widely investigated for their applications in soft robotics, interfaces, and functional devices for instance smart windows. While numerous reviews have addressed hydrogel classification and robotic actuation modes[58-63], this section will specifically examine the swarm behaviors exhibited by hydrogel-based robotic systems. Most hydrogel-based robotic swarms rely on Belousov-Zhabotinsky (BZ) reaction-driven oscillatory swelling, apart from those employing magnetic actuation[27,64,65].
The BZ reaction is a non-equilibrium oscillatory chemical process. The process involves the oxidation of an organic chemical, such as malonic acid or citric acid, by an oxidizing agent, typically bromate ions, in the presence of a catalyst under acidic conditions. Catalysts commonly used include metal ions or metal complexes with high redox potentials, such as cerium ions, ferroin, or ruthenium tris(2,2′-bipyridine) (Ru(bpy)32+). During the reaction, the catalyst undergoes spontaneous redox oscillations, resulting in periodic color changes in the stirred solution and the formation of concentric or spiral wave patterns under stationary conditions. The propagation of the oxidized state in the medium is known as a "chemical wave". This reaction can be utilized to induce periodic changes in hydrogel swelling and deswelling without requiring external stimuli. Self-oscillating polymer hydrogels consist of a polymeric network in which catalysts, such as Ru2+/Ru3+-containing complexes, were covalently immobilized. In the presence of reactants, the polymer underwent spontaneous cyclic soluble-insoluble transitions or swelling-deswelling oscillations[30,66]. Large populations of hydrogel beads suspended in BZ reaction solutions exhibited oscillatory behaviors, with their rhythmic synchronization depending on the exchange rate of signaling molecules. Adjusting the stirring speed modulated the signaling exchange rate [Figure 2A]: at low exchange rates, weak coupling through the activator’s diffusion gradually synchronized the oscillators, whereas at high stirring rates, synchronization occurred only when the particle density exceeded a critical threshold[28].
Figure 2. Oscillating hydrogel collectives based on BZ reactions. (A) The hydrogels exhibit different oscillating behaviors with different stirring speeds. Reproduced with permission from ref.[28]. Copyright 2009, AAAS. (B) Oscillating hydrogels with changing sizes. (C) The oscillating hydrogels exhibit different size thresholds in the isolated form and collectives. Reproduced with permission from ref.[25] under the CC BY-NC-ND license. Copyright 2024, The Authors, published by PNAS.
Swarm behaviors in liquid crystalline polymer-based robotic systems
In contrast to the relatively simple swelling-based actuation mechanisms of hydrogels, LCPs offer more programmable deformation modes due to the anisotropic, rod-shaped molecular structures of LC mesogens. The molecular alignment of LCPs can be precisely engineered, enabling them to bend, twist, and morph into three-dimensional (3D) structures upon exposure to external stimuli such as heat, light, electricity, or magnetic fields[7,18]. For instance, LCP films can transition between flat, curled, spiral, twisted, and buckled configurations depending on their molecular alignment. A typical example of programmed LCP deformation involves the splay configuration, in which LC molecules align parallel to the film surface on one side while being perpendicular on the other[48]. This gradient in molecular orientation induces asymmetric shrinkage or expansion across the film’s thickness, leading to controlled bending motions upon thermal or photothermal stimulation. By strategically selecting the illumination angle, LCP films can exploit feedback loops and self-shadowing effects to achieve sustained oscillatory bending[19,48]. A notable study on collective LCP behavior involved two LCP film strips connected by an LCP joint [Figure 3A][67]. These interconnected films exhibited synchronized oscillations over time, displaying either in-phase or anti-phase rhythmic movements depending on their initial positions.
Figure 3. LCP collectives connected physically or via capillary forces. (A) Connected LCP oscillators with Huygens’ synchrony. They can oscillate in in-phase or anti-phase modes. Reproduced with permission[67]. Copyright 2021, Springer Nature. (B) Coupled photo-oscillators excited with two orthogonal laser beams. Reproduced with permission under the CC BY 4.0 license[70]. Copyright 2024, The Authors, published by Wiley-VCH. (C) Liquid crystal polymer actuators with reconfigurable assembly driven by optocapillarity. (D) Numerical simulation of the Gibbs free energy in the two-actuator system during the transformation. Reproduced with permission under the CC BY 4.0 license[71]. Copyright 2020, The Authors, published by Springer Nature.
LC elastomers (LCEs) can be coupled via intermediate substances to form self-oscillatory systems. For instance, two identical LCE fibers connected by a spring constitute a self-oscillating coupled system[68]. When exposed to uniform and continuous light, the LCE undergoes light-induced contraction, leading to a reduction in length and the generation of a driving force. Over time, periodic contraction and relaxation cycles occur, during which the driving and damping forces vary, thereby sustaining self-excited oscillations within the system[68]. In a more complex system, three mutually coupled LCE spring oscillators connected by springs and placed within a linear temperature gradient exhibit coupling interactions. In strongly interacting systems, the motion states of the oscillators influence one another, invariably resulting in fully synchronized oscillatory modes. Conversely, in weakly interacting systems, the degree of synchronization can be modulated by adjusting the magnitude and direction of the initial velocities, allowing for the emergence of fully synchronized, partially synchronized, or asynchronous oscillatory modes[69].
Additionally, coupled LC networks (LCNs) can function in fluidic environments to facilitate liquid propulsion. In one experimental setup, an LCE strip was fixed at one end and immersed in water[70]. Two orthogonal laser beams were employed to irradiate the strip - one targeting its bottom surface and the other its central region [Figure 3B]. The laser irradiation converted light energy into thermal energy, inducing bending in the LCE strip. As the strip bent, it partially shielded the beam, reducing light absorption and lowering its temperature. Subsequently, the central laser beam irradiated the bent strip again, prompting it to bend in the opposite direction. This sequence of bending motions resulted in a unidirectional oscillatory movement, analogous to the beating of natural cilia. Furthermore, two oscillating LCE strips could be coupled via interactions with the surrounding liquid medium, achieving synchronized motion similar to the hydrodynamic coupling observed in cilia. By varying the power, position, and direction of the laser beams, the bending direction, amplitude, and oscillation frequency of the LCE strips could be precisely controlled, thereby enabling self-oscillation and facilitating fluid propulsion.
Beyond direct mechanical coupling, robots can also interact through alternative mechanisms, such as capillary forces, to control the assembly and reconfiguration of LCN sheets. Hu et al. utilized azobenzene-functionalized LC polymer (azo-LCP) and employed UV and visible light to irradiate photo-deformable LCP (azo-LCP) actuators, inducing transitions between planar and curved states [Figure 3C][71]. The bending direction of the actuator modulated the curvature of the surrounding liquid surface, thereby altering the direction and magnitude of the capillary forces. These capillary interactions among actuators resulted in diverse assembly morphologies, including end-to-end, side-by-side, and T-shaped configurations[71]. The assembled structures demonstrated high reversibility. Using tweezers, researchers manually separated two actuators from their original linear configuration. However, upon release, the actuators spontaneously reassembled into their initial linear structure. Moreover, by alternating UV and visible light irradiation, the actuators could be programmed to undergo complex reconfigurations, such as transitioning from a linear arrangement to L- or Z-shaped structures [Figure 3D]. When actuators were positioned at different liquid interfaces and their assembly was controlled through light irradiation, the construction of 3D ordered structures was achieved. This mechanism also enabled selective assembly; for example, when four of six actuators were irradiated with UV light, they assembled into a stable array, while the remaining two unirradiated actuators remained separate[71].
The interaction among LCEs can also be dynamically enhanced by shape morphing of robots. When LCEs aggregate, their shape morphing leads to distinct mechanical properties, including higher yield strength, elasticity, and programmability[7]. These characteristics make LCEs highly promising for a wide range of applications in swarm robotics. The aggregation behavior of LCEs can be achieved through various methods. One simple and effective approach is heating, which not only facilitates the aggregation process but also results in solid structures with enhanced properties. When LCE ribbons are dispersed in liquids at high concentrations and subsequently heated, they mechanically interlock due to shape changes, forming tightly packed aggregates [Figure 4]. This interlocking is driven by the transition from the nematic phase to the isotropic phase, causing the ribbons to shrink, bend, or twist along their pointing vectors. The extent of interlocking depends on several factors, such as ribbon length, concentration, and the offset angle of the LCE tapes. Longer ribbons and higher concentrations promote tighter interlocking and stronger aggregation. The aggregated LCE ribbons form a viscoelastic solid structure, with tunable storage modulus and yield stress. Both yield stress and storage modulus are influenced by factors such as ribbon length. For example, aggregates of 12-mm LCE ribbons exhibit a much higher yield stress than those of 3-mm ribbons. The offset angle also plays a significant role: aggregates formed from LCE ribbons with a 0° offset angle (pure bend) exhibit the highest yield stress and storage modulus, as bending promotes mechanical interlocking more effectively than twisting. In contrast, LCE aggregates formed with a 45° offset angle (pure twist) exhibit minimal yield stress and storage modulus, as twisting alone does not facilitate effective interlocking. When cooled, the LCE aggregates return to their original state and redisperse, although longer ribbons and higher temperatures can lead to irreversible aggregation. Additionally, when LCE ribbons are coated with liquid metal or incorporated with cells, they gain enhanced functionalities, such as photo-responsiveness, electrical conductivity, and cell culture scaffolding capabilities[7]. Dana et al. developed a method for macroscopically forming LCE clusters capable of autonomously assembling and disassembling[72]. By heating the LCE ribbons within a magnetic field to a specific temperature, shape changes occur. A rotating magnetic field is then applied to move the LCE ribbons, which collide and become entangled due to their shape transformations and the magnetic driving force. Over time, the ribbons become progressively more entangled, forming larger clusters. The curvature of the LCE ribbons affects aggregation behavior, with high-curvature ribbons (e.g., θ = 20°) being more prone to aggregation than flat ribbons or those with low curvature (e.g., θ = 10°). A certain degree of twisting further promotes physical interlocking between the ribbons, improving aggregation efficiency. At 65 °C, the aggregated clusters exhibit viscoelastic solid-like properties, stretching and deforming similarly to a spring while storing and releasing energy in response to external forces. Clusters formed from ribbons with medium curvature exhibit higher moduli, whereas those formed from ribbons with high curvature show lower moduli. Similarly, clusters formed from medium curvature ribbons have higher yield stresses, while those formed from high curvature ribbons have lower yield stresses. At 120 °C, the degree of aggregation decreases, and the clusters exhibit more liquid-like properties. These clusters are not only controllable but also adaptive. LCEs can also be mixed with magnetic particles or coated with magnetic materials to form partially magnetic regions[72], enabling movement within a rotating magnetic field. The disassembly and reformation of the clusters can be controlled by adjusting the rotational speed of the magnetic field and the shape of the LCE ribbons.
Figure 4. Switchable properties of LCP assembly. (A) The LCP changes its shape upon stimulation. (B) The assembly composed of LCP ribbons changes from dispersed to aggregated state upon stimulation. (C) Yield stress of the LCN assembly in the dispersed and aggregated states. Reproduced with permission[7]. Copyright 2024, Springer Nature.
COMPARISON BETWEEN HYDROGELS AND LIQUID CRYSTALLINE POLYMERS
Both hydrogels and LCPs are usually used to develop robots. A comparison can find their respective uniqueness. Hydrogels and LCPs have similarities and dissimilarities.
Similarities of hydrogels and LCPs
Soft and flexible: Both hydrogels and LCPs exhibit high levels of softness and flexibility, which are key qualities for soft robotics. This allows for deformation and movement in a way rigid materials cannot achieve, which is essential for applications requiring flexibility and adaptability.
Responsive to external stimuli: Hydrogels can respond to environmental factors such as changes in temperature, pH, or light by swelling or shrinking. LCPs are known to exhibit changes in their structural and mechanical properties in response to external stimuli, such as temperature and light. They can form different phases or domains that can be controlled to create motion. Both hydrogels and LCPs are actuatable.
Dissimilarities of hydrogels and LCPs
Material compositions: Hydrogels are primarily made of water and polymer chains that form a network capable of absorbing large amounts of water. They are typically with a high degree of water content and may lose water in a dry environment due to water evaporation. LCPs, on the other hand, are polymers with ordered and anisotropic structures that give rise to unique optical and mechanical properties.
Mechanism of actuation: Hydrogels generally respond through water diffusion and swelling or shrinking in response to environmental changes. This is a relatively slow process and can be limited by the water content. In contrast, LCPs change their shape due to the reorientation of their molecules in response to stimuli. This reorientation can lead to more rapid and reversible actuation compared to hydrogels.
Environmental stability: Hydrogels are sensitive to their hydration levels. Dehydration can cause loss of functionality, and they might degrade in dry environments or at high temperatures. LCPs are more stable under a wider range of environmental conditions. They typically do not rely on water content and can operate in a broader range of temperatures, which makes them more suitable for certain applications where humidity fluctuates, except for humidity-responsive LCPs that are specially designed.
Electrical conductivity: Hydrogels are often used in bioelectronics and soft robotics because they can be made electrically conductive, especially when doped with conductive materials such as graphene or carbon nanotubes. This is beneficial for integrated sensing and actuation. LCPs generally are not conductive unless modified with conductive additives, but they are often used in areas such as displays and sensors due to their optical and mechanical properties, especially when designed to have high mechanical strength and low viscosity.
Fabrication and manufacturing: Hydrogels can be easily fabricated into soft, deformable shapes via molding, 3D printing, or other techniques. Their synthesis is usually simpler and can be tuned for specific applications by altering the polymer composition or crosslinking density. LCPs require more advanced fabrication techniques, such as delicately aligning the LC mesogens and their processing can be more complex due to the need for precise control of their molecular order.
These properties lead to different aspects for hydrogels and LCPs in developing robot swarms. In robot swarm development, hydrogels would be ideal for soft, slow-changing, environment-responsive tasks where flexibility, bio-compatibility, and adaptability to wet or fluid environments are required. These could be used in large-scale, low-cost swarms that need to interact with delicate environments. On the other hand, LCPs would shine in high-precision, fast-actuating, and more structurally demanding swarm behaviors. Their stability in extreme conditions and ability to quickly change forms under external stimuli would allow for more dynamic, adaptable swarms, particularly for environments requiring rapid reconfiguration or where high mechanical performance is required.
CONCLUSION: RESEARCH CHALLENGES AND OUTLOOK
Despite intensive efforts devoted to developing hydrogel and LCP-based soft robots and actuators, challenges still exist for robot swarms based on hydrogels and LCPs. Firstly, the application scenarios need to be clarified. Swarm robots composed of magnetic micro/nanoscale robots can be applied in biomedical applications, while larger-scale drone swarms can be applied in delivering cargo and taking photos. However, up to now, there is still space to explore what exact applications these millimeter-scale robots or LCP-based robot swarms can do and what specific tasks are suitable for them. Secondly, the coupling factors need to be investigated further. Microscale magnetic robots form robot swarms due to magnetic forces, hydrodynamic forces, elastic forces, etc. Whether these forces are also applicable to millimeter-scale robot swarms and how to integrate them to develop swarms remains a challenge. In addition, whether and how these robots harvest energy and store it in efficient storage devices from the environment remains an unresolved problem[73]. In addition, there remain challenges for swarm control at different scales. For microrobots, a major challenge is the limited power supply, necessitating external energy sources such as magnetic fields or light fields. Additionally, communication within the swarm is constrained due to the absence of onboard sensors and processors. In contrast, for robot swarms at the millimeter scale or larger, a key challenge is the increased energy demand required to overcome inertia, friction, or hydrodynamic forces, depending on the surrounding medium. With the above summary, we believe the robot swarm robots based on stimuli-responsive hydrogels and LCPs will find their applications in the near future.
DECLARATIONS
Acknowledgements
The authors acknowledge financial support from the National Natural Science Foundation of China and the Start fund from the University of Science and Technology of China.
Authors’ contributions
Drafted the manuscript: Chen, D.; He, J.; Zhu, B.; Feng, W.
Conceived the review: Feng, W.
Availability of data and materials
Not applicable.
Financial support and sponsorship
This work was supported by the National Natural Science Foundation of China and the Start fund from the University of Science and Technology of China (KY2090000140).
Conflicts of interest
All authors declared that there are no conflicts of interest.
Ethical approval and consent to participate
Not applicable.
Consent for publication
Not applicable.
Copyright
© The Author(s) 2025.
REFERENCES
1. Li, S.; Dutta, B.; Cannon, S.; et al. Programming active cohesive granular matter with mechanically induced phase changes. Sci. Adv. 2021, 7, eabe8494.
2. Duan, H.; Huo, M.; Fan, Y. From animal collective behaviors to swarm robotic cooperation. Nat. Sci. Rev. 2023, 10, nwad040.
3. Berlinger, F.; Gauci, M.; Nagpal, R. Implicit coordination for 3D underwater collective behaviors in a fish-inspired robot swarm. Sci. Robot. 2021, 6, eabd8668.
4. Shaw, E. Schooling fishes: the school, a truly egalitarian form of organization in which all members of the group are alike in influence, offers substantial benefits to its participants. Am. Sci. 1978, 66, 166-75. Available from: https://www.jstor.org/stable/27848512 [Last accessed on 7 Apr 2025]
6. Parrish, J. K.; Viscido, S. V.; Grünbaum, D. Self-organized fish schools: an examination of emergent properties. Biol. Bull. 2002, 202, 296-305.
7. Abdelrahman, M. K.; Wagner, R. J.; Kalairaj, M. S.; et al. Material assembly from collective action of shape-changing polymers. Nat. Mater. 2024, 23, 281-9.
8. Wagner, R. J.; Such, K.; Hobbs, E.; Vernerey, F. J. Treadmilling and dynamic protrusions in fire ant rafts. J. R. Soc. Interface. 2021, 18, 20210213.
9. Blackiston, D.; Lederer, E.; Kriegman, S.; Garnier, S.; Bongard, J.; Levin, M. A cellular platform for the development of synthetic living machines. Sci. Robot. 2021, 6, eabf1571.
10. Joh, H.; Fan, D. E. Materials and schemes of multimodal reconfigurable micro/nanomachines and robots: review and perspective. Adv. Mater. 2021, 33, e2101965.
11. Sun, B.; Kjelleberg, S.; Sung, J. J. Y.; Zhang, L. Micro- and nanorobots for biofilm eradication. Nat. Rev. Bioeng. 2024, 2, 367-9.
12. Wang, Q.; Wang, Q.; Ning, Z.; et al. Tracking and navigation of a microswarm under laser speckle contrast imaging for targeted delivery. Sci. Robot. 2024, 9, eadh1978.
13. Wang, Q.; Xiang, N.; Lang, J.; Wang, B.; Jin, D.; Zhang, L. Reconfigurable liquid-bodied miniature machines: magnetic control and microrobotic applications. Adv. Intell. Syst. 2024, 6, 2300108.
14. Mayorga-Martinez, C. C.; Zelenka, J.; Pribyl, T.; et al. Programming self-assembling magnetic microrobots with multiple physical and chemical intelligence. Chem. Eng. J. 2024, 488, 150625.
15. Jiang, J.; Yang, L.; Hao, B.; Xu, T.; Wu, X.; Zhang, L. Automated microrobotic manipulation using reconfigurable magnetic microswarms. IEEE. Trans. Robot. 2024, 40, 3676-94.
16. Yang, L.; Jiang, J.; Gao, X.; Wang, Q.; Dou, Q.; Zhang, L. Autonomous environment-adaptive microrobot swarm navigation enabled by deep learning-based real-time distribution planning. Nat. Mach. Intell. 2022, 4, 480-93.
18. Feng, W.; He, Q.; Zhang, L. Embedded physical intelligence in liquid crystalline polymer actuators and robots. Adv. Mater. 2025, 37, e2312313.
19. Gelebart, A. H.; Jan, M. D.; Varga, M.; et al. Making waves in a photoactive polymer film. Nature 2017, 546, 632-6.
20. Ware, T. H.; McConney, M. E.; Wie, J. J.; Tondiglia, V. P.; White, T. J. Actuating materials. Voxelated liquid crystal elastomers. Science 2015, 347, 982-4.
21. Feng, W.; Broer, D. J.; Liu, D. Oscillating chiral-nematic fingerprints wipe away dust. Adv. Mater. 2018, 30, 1704970.
22. Babakhanova, G.; Turiv, T.; Guo, Y.; et al. Liquid crystal elastomer coatings with programmed response of surface profile. Nat. Commun. 2018, 9, 456.
23. Aharoni, H.; Xia, Y.; Zhang, X.; Kamien, R. D.; Yang, S. Universal inverse design of surfaces with thin nematic elastomer sheets. Proc. Natl. Acad. Sci. USA. 2018, 115, 7206-11.
24. Nie, Z. Z.; Zuo, B.; Wang, M.; et al. Light-driven continuous rotating Möbius strip actuators. Nat. Commun. 2021, 12, 2334.
25. Blanc, B.; Agyapong, J. N.; Hunter, I.; Galas, J. C.; Fernandez-Nieves, A.; Fraden, S. Collective chemomechanical oscillations in active hydrogels. Proc. Natl. Acad. Sci. USA. 2024, 121, e2313258121.
26. Chiang, M. Y.; Hsu, Y. W.; Hsieh, H. Y.; Chen, S. Y.; Fan, S. K. Constructing 3D heterogeneous hydrogels from electrically manipulated prepolymer droplets and crosslinked microgels. Sci. Adv. 2016, 2, e1600964.
27. Jin, D.; Wang, Q.; Chan, K. F.; et al. Swarming self-adhesive microgels enabled aneurysm on-demand embolization in physiological blood flow. Sci. Adv. 2023, 9, eadf9278.
28. Taylor, A. F.; Tinsley, M. R.; Wang, F.; Huang, Z.; Showalter, K. Dynamical quorum sensing and synchronization in large populations of chemical oscillators. Science 2009, 323, 614-7.
29. Tinsley, M. R.; Taylor, A. F.; Huang, Z.; Showalter, K. Emergence of collective behavior in groups of excitable catalyst-loaded particles: spatiotemporal dynamical quorum sensing. Phys. Rev. Lett. 2009, 102, 158301.
30. Tinsley, M.; Taylor, A.; Huang, Z.; Wang, F.; Showalter, K. Dynamical quorum sensing and synchronization in collections of excitable and oscillatory catalytic particles. Phys. D. Nonlinear. Phenom. 2010, 239, 785-90.
31. Toth, R.; Taylor, A. F.; Tinsley, M. R. Collective behavior of a population of chemically coupled oscillators. J. Phys. Chem. B. 2006, 110, 10170-6.
32. Na, H.; Kang, Y. W.; Park, C. S.; Jung, S.; Kim, H. Y.; Sun, J. Y. Hydrogel-based strong and fast actuators by electroosmotic turgor pressure. Science 2022, 376, 301-7.
33. Le, X.; Lu, W.; Zhang, J.; Chen, T. Recent progress in biomimetic anisotropic hydrogel actuators. Adv. Sci. 2019, 6, 1801584.
34. Chen, Y.; Zhang, Y.; Li, H.; et al. Bioinspired hydrogel actuator for soft robotics: opportunity and challenges. Nano. Today. 2023, 49, 101764.
35. Li, W.; Guan, Q.; Li, M.; Saiz, E.; Hou, X. Nature-inspired strategies for the synthesis of hydrogel actuators and their applications. Prog. Polym. Sci. 2023, 140, 101665.
36. Jiao, D.; Zhu, Q. L.; Li, C. Y.; Zheng, Q.; Wu, Z. L. Programmable morphing hydrogels for soft actuators and robots: from structure designs to active functions. ACC. Chem. Res. 2022, 55, 1533-45.
37. Apsite, I.; Salehi, S.; Ionov, L. Materials for smart soft actuator systems. Chem. Rev. 2022, 122, 1349-415.
38. López-Díaz, A.; Vázquez, A. S.; Vázquez, E. Hydrogels in soft robotics: past, present, and future. ACS. Nano. 2024, 18, 20817-26.
39. Liu, J.; Jiang, L.; He, S.; Zhang, J.; Shao, W. Recent progress in PNIPAM-based multi-responsive actuators: a mini-review. Chem. Eng. J. 2022, 433, 133496.
40. He, J.; Zhou, Q.; Ge, Z.; et al. pH-gated switch of LCST-UCST phase transition of hydrogels. Adv. Funct. Mater. 2024, 34, 2404341.
41. Jiang, Z.; Tan, M. L.; Taheri, M.; et al. Strong, self-healable, and recyclable visible-light-responsive hydrogel actuators. Angew. Chem. Int. Ed. 2020, 59, 7049-56.
42. Ter Schiphorst, J.; Coleman, S.; Stumpel, J. E.; Ben Azouz, A.; Diamond, D.; Schenning, A. P. H. J. Molecular design of light-responsive hydrogels, for in situ generation of fast and reversible valves for microfluidic applications. Chem. Mater. 2015, 27, 5925-31.
43. Li, L.; Scheiger, J. M.; Levkin, P. A. Design and applications of photoresponsive hydrogels. Adv. Mater. 2019, 31, e1807333.
44. LeValley, P. J.; Sutherland, B. P.; Jaje, J.; et al. On-demand and tunable dual wavelength release of antibody using light-responsive hydrogels. ACS. Appl. Bio. Mater. 2020, 3, 6944-58.
45. Feng, W.; Zhou, W.; Zhang, S.; Fan, Y.; Yasin, A.; Yang, H. UV-controlled shape memory hydrogels triggered by photoacid generator. RSC. Adv. 2015, 5, 81784-9.
46. Ko, J.; Kim, C.; Kim, D.; et al. High-performance electrified hydrogel actuators based on wrinkled nanomembrane electrodes for untethered insect-scale soft aquabots. Sci. Robot. 2022, 7, eabo6463.
47. Zheng, J.; Xiao, P.; Le, X.; et al. Mimosa inspired bilayer hydrogel actuator functioning in multi-environments. J. Mater. Chem. C. 2018, 6, 1320-7.
48. Gelebart, A. H.; Vantomme, G.; Meijer, E. W.; Broer, D. J. Mastering the photothermal effect in liquid crystal networks: a general approach for self-sustained mechanical oscillators. Adv. Mater. 2017, 29, 1606712.
49. Ceron, S.; Gardi, G.; Petersen, K.; Sitti, M. Programmable self-organization of heterogeneous microrobot collectives. Proc. Natl. Acad. Sci. USA. 2023, 120, e2221913120.
51. Kim, M.; Nicholas, J. D.; Puigmartí-Luis, J.; Nelson, B. J.; Pané, S. Targeted drug delivery: from chemistry to robotics at small scales. Annu. Rev. Control. Robot. Auton. Syst. 2024, 8.
52. Wang, T.; Wu, Y.; Yildiz, E.; Kanyas, S.; Sitti, M. Clinical translation of wireless soft robotic medical devices. Nat. Rev. Bioeng. 2024, 2, 470-85.
53. Yang, L.; Jiang, J.; Ji, F.; et al. Machine learning for micro- and nanorobots. Nat. Mach. Intell. 2024, 6, 605-18.
54. Wang, Y.; Chen, H.; Xie, L.; Liu, J.; Zhang, L.; Yu, J. Swarm autonomy: from agent functionalization to machine intelligence. Adv. Mater. 2025, 37, 2312956.
56. Mayorga-Martinez, C. C.; Zhang, L.; Pumera, M. Chemical multiscale robotics for bacterial biofilm treatment. Chem. Soc. Rev. 2024, 53, 2284-99.
57. Zhu, Q. L.; Liu, W.; Khoruzhenko, O.; et al. Animating hydrogel knotbots with topology-invoked self-regulation. Nat. Commun. 2024, 15, 300.
58. Yuk, H.; Wu, J.; Zhao, X. Hydrogel interfaces for merging humans and machines. Nat. Rev. Mater. 2022, 7, 935-52.
59. He, Y.; Tang, J.; Hu, Y.; et al. Magnetic hydrogel-based flexible actuators: a comprehensive review on design, properties, and applications. Chem. Eng. J. 2023, 462, 142193.
60. Cheng, F. M.; Chen, H. X.; Li, H. D. Recent progress on hydrogel actuators. J. Mater. Chem. B. 2021, 9, 1762-80.
62. Puza, F.; Lienkamp, K. 3D printing of polymer hydrogels - from basic techniques to programmable actuation. Adv. Funct. Mater. 2022, 32, 2205345.
63. Dong, Y.; Ramey-Ward, A. N.; Salaita, K. Programmable mechanically active hydrogel-based materials. Adv. Mater. 2021, 33, e2006600.
64. Chen, Z.; Chen, H.; Fang, K.; Liu, N.; Yu, J. Magneto-thermal hydrogel swarms for targeted lesion sealing. Adv. Healthc. Mater. 2025, 14, e2403076.
65. Han, H.; Ma, X.; Deng, W.; et al. Imaging-guided bioresorbable acoustic hydrogel microrobots. Sci. Robot. 2024, 9, eadp3593.
66. Yoshida, R. Self-oscillating gels driven by the Belousov-Zhabotinsky reaction as novel smart materials. Adv. Mater. 2010, 22, 3463-83.
67. Vantomme, G.; Elands, L. C. M.; Gelebart, A. H.; et al. Coupled liquid crystalline oscillators in Huygens' synchrony. Nat. Mater. 2021, 20, 1702-6.
68. Du, C.; Cheng, Q.; Li, K.; Yu, Y. Self-sustained collective motion of two joint liquid crystal elastomer spring oscillator powered by steady illumination. Micromachines 2022, 13, 271.
69. Wu, H.; Zhang, B.; Li, K. Synchronous behaviors of three coupled liquid crystal elastomer-based spring oscillators under linear temperature fields. Phys. Rev. E. 2024, 109, 024701.
70. Deng, Z.; Zhang, H.; Priimagi, A.; Zeng, H. Light-fueled nonreciprocal self-oscillators for fluidic transportation and coupling. Adv. Mater. 2024, 36, e2209683.
71. Hu, Z.; Fang, W.; Li, Q.; Feng, X. Q.; Lv, J. A. Optocapillarity-driven assembly and reconfiguration of liquid crystal polymer actuators. Nat. Commun. 2020, 11, 5780.
72. Dana, A.; Benson, C.; Sivaperuman Kalairaj, M.; et al. Collective action and entanglement of magnetically active liquid crystal elastomer ribbons. arXiv 2024. Available from: https://ssrn.com/abstract=4997256 [Last accessed on 7 Apr 2025]
Cite This Article
How to Cite
Download Citation
Export Citation File:
Type of Import
Tips on Downloading Citation
Citation Manager File Format
Type of Import
Direct Import: When the Direct Import option is selected (the default state), a dialogue box will give you the option to Save or Open the downloaded citation data. Choosing Open will either launch your citation manager or give you a choice of applications with which to use the metadata. The Save option saves the file locally for later use.
Indirect Import: When the Indirect Import option is selected, the metadata is displayed and may be copied and pasted as needed.
About This Article
Copyright
Data & Comments
Data
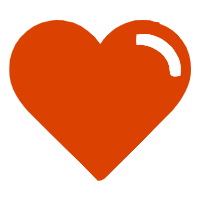
Comments
Comments must be written in English. Spam, offensive content, impersonation, and private information will not be permitted. If any comment is reported and identified as inappropriate content by OAE staff, the comment will be removed without notice. If you have any queries or need any help, please contact us at [email protected].