A low-cost inorganic oxide as dual-functional electrolyte additive towards long cycling Li-rich Mn-based cathode materials
Abstract
Li-rich Mn-based cathode materials (LRM) have received great attention owing to their high capacity and low cost. However, the mismatch between the widely used carbonate electrolyte and the LRM cathode and lithium metal anode causes a series of problems, such as electrolyte continuous oxidation, cathode structure degradation, and Li dendritic growth. Herein, inorganic oxide B2O3 is introduced as a dual-functional high-voltage electrolyte additive to construct stable cathode electrolyte interphase and solid electrolyte interphase for Li||LRM batteries. The modified interface derived from the additive can induce dendrite-free Li deposition, stabilize cathode structure, and inhibit transition metal dissolution. Moreover, the adverse side reactions are mitigated, thus enhancing Li+ transport rate and reducing interface impedance. With the addition of B2O3 into the carbonate electrolyte, the Li||LRM battery exhibits an enhanced discharge capacity of 221 mAh g-1 after 200 cycles, equaling a capacity retention of 92.1%. When the upper cut-off voltage is increased to 5 V, a superior capacity retention of > 85% can still be achieved after 150 cycles at 1 C. In addition, the low cost of B2O3 benefits for commercial application. This work offers new guidance for the research of low-cost, high-voltage dual-functional additives for advanced lithium metal batteries.
Keywords
INTRODUCTION
The rapid development of electric vehicles and portable electronic devices has brought great opportunities for the new energy industry while also raising the need to elevate the energy density of lithium (Li)-ion batteries[1,2]. In general, increasing the specific capacity of the active materials and operating voltage of the battery system are effective strategies to improve the battery energy density[3]. For anode materials, graphite, widely used in the commercial field, is unable to provide higher capacity. The lithium metal anode (LMA) with the highest specific capacity and lowest potential [3,860 mAh g-1, 3.04 V vs. Standard Hydrogen Electrode (SHE)] has received widespread attention in recent years[4,5]. For cathode materials, the commonly used LiFePO4 has a low specific capacity (~170 mAh g-1), while high-nickel ternary cathode materials such as LiNixCoyMn1-x-yO2 and LiNixCoyAl1-x-yO2 (x ≥ 0.8) have limited room for further specific capacity increase[6,7]. Among a series of cathode materials, Li-rich Mn-based layered oxides (LRM,
However, for lithium-metal batteries, many interface issues between the electrodes and electrolytes need to be solved[11]. Firstly, the compatibility between LMA and conventional carbonate electrolytes is insufficient. The solid electrolyte interphase (SEI) formed in the initial cycle is difficult to inhibit the side reactions on the lithium metal surface, resulting in poor Coulombic efficiency (CE). Meanwhile, with the continuous and uneven plating/stripping of Li+, it will induce the Li dendrites and dead Li, which significantly deteriorate the cycling life and safety of lithium-metal batteries[5,12]. In addition, for the LRM cathode, the lattice oxygen needs to be activated at a high voltage to participate in the redox reaction (> 4.5 V). However, when the voltage exceeds 4.3 V, the decomposition of carbonate electrolytes is intensified due to the low voltage tolerance, producing various harmful by-products[13]. These problems caused by electrolytes will eventually lead to low CE and continuous capacity attenuation of Li||LRM batteries, bringing great challenges to their practical application.
To improve the interfacial stability, various optimization strategies have been explored. For LMA, it is an available way to suppress Li dendrites by reducing local current density and volume change through three-dimensional skeleton structure[14-16]. Artificially creating lithiophilic SEI can also improve the uniformity of the deposited Li[17,18]. For comparison, constructing a functional SEI on the surface of LMA via electrolyte additives is a simple and effective method. Especially, the special components contained in the SEI (Li-N, Li-S-O species, etc.) can play an important role in inhibiting the generation of Li dendrites, inducing uniform Li deposition, and stabilizing the interfaces[19,20].
Apart from the LMA, building a passivation layer is also effective for cathode materials, but the conventional coatings are difficult to finely control, which may reduce the total capacity and increase the interface impedance[21-23]. Using highly concentrated electrolytes to reduce the proportion of free solvents is beneficial to mitigate solvent oxidation and construct the inorganic components of the cathode electrolyte interface (CEI), but it has inferior interface wettability and high cost[24]. By adding a small number of functional additives into the electrolyte, and then participating in the formation of CEI during cycling, the oxidative decomposition of the electrolyte can be effectively inhibited even under high-voltage conditions. Among the additives commonly used to modify the CEI, B-containing additives have garnered significant attention, including lithium bis(oxalate)borate (LiBOB)[25,26], LiBF4[3], lithium difluoro(oxalate)borate (LiDFOB)[27], etc. However, numerous studies have shown that the use of B-containing salts as additives can mitigate the electrolyte decomposition at high voltage, but they mainly enhance the performance of the cathode side without significantly influencing the LMA[3,25,28]. Moreover, high cost may also hinder their widespread application. Therefore, it is urgent to explore a low-cost additive that can improve both the performance of LMA and LRM cathodes under high voltage.
Given the positive effects of B-containing lithium salts on improving cycling performance, coupled with the low cost of oxides, B2O3 is regarded as a potential high-voltage additive. Herein, we introduce inorganic oxide B2O3 as a dual-function high-voltage additive. This additive can preferentially decompose on the surface of the LMA and LMR cathode, participating in the formation of CEI/SEI composed of B-containing species during the initial cycle, which can restrain the electrolyte decomposition on both electrodes. Furthermore, the formed CEI protective layer can hinder TM dissolution and help maintain the structural stability of LRM. A low-impedance SEI is also generated on the anode, which facilitates the migration of Li+ and suppresses the growth of Li dendrites. Hence, through the combination of the modified CEI and SEI, this dual-functional additive can improve the overall electrochemical performance of Li||LRM batteries in a wide temperature range.
EXPERIMENTAL SECTION
Preparation of electrolytes and LRM cathodes
The electrolytes were prepared in a glove box filled with argon, and the concentrations of water and oxygen were controlled to be < 1 ppm. The blank electrolyte (BE) was purchased from Guangdong Canrd New Energy Technology Co., Ltd (China) and consisted of 1 M LiPF6 dissolved in ethylene carbonate (EC): dimethyl carbonate (DMC): ethyl methyl carbonate (EMC) solvents (1:1:1, by weight). Then, B2O3 additives with different amounts of 0.25, 0.5, 1, and 1.5 wt% were introduced into the BE and denoted as B-0.25,
Characterization
The cycled electrodes were disassembled from batteries, soaked in the DMC for approximately 6 h, and then dried naturally in the glove box for subsequent analyses. The surface morphologies of samples were observed by the scanning electron microscopy (SEM, Hitachi SU-70) and transmission electron microscope (TEM, Talos F200). The crystal structure was analyzed by X-ray diffraction (XRD, Bruker-axs). Raman spectroscopy (Xplora) was employed to characterize the phase change. Surface chemical compositions were analyzed using X-ray photoelectron spectroscopy (XPS, PHI Quantum 2000) with a calibration of
Electrochemical measurements
The electrochemical tests were conducted in coin cells, where the separator was a Celgard 2500 microporous membrane. Linear sweep voltammetry (LSV) was performed in the electrochemical workstation (CHI660E, Shanghai Chenhua Instrument Corp), using stainless steel sheets as the working electrode, Li foil as both the counter electrode and reference electrode, with a scanning rate of 0.5 mV s-1. Li||Cu batteries composed of copper foil, separators, Li foil, and electrolytes were used to evaluate the Li plating/stripping behavior. These batteries were first activated at 0.1 mA cm-2 for three cycles, followed by testing at 1 mA cm-2. For polarization difference assessment, Li||Li symmetric batteries were employed, with Li foil as both the working electrode and counter electrode, at the current densities of 0.5, 1, and 2 mA cm-2. The Tafel curves were obtained by testing the Li||Li symmetric batteries after ten cycles under a current density of
RESULTS AND DISCUSSION
Characterization of the electrolytes
To observe the dispersion state of the additive, 0.5 wt% of B2O3 was added into the BE, and then left to stand for one day. The results indicate that the electrolyte remains clear and transparent, with no visible deposits
Figure 1. (A) Optical photos of the laser beam passing through BE. (B-D) Laser beam passing through (B) upper, (C) middle and (D) lower parts of B-0.5. (E) Oxidation and (F) reduction stability of BE and B-0.5 by LSV at a scan rate of 0.5 mV s-1.
LSV was conducted to verify the redox behavior of the electrolyte containing B2O3 at a scanning rate of
Plating/Stripping behavior of Li metal
Symmetric cells are usually used to verify the cycling performance of LMA[15]. Herein, Li||Li symmetric cells were assembled and cycled at different current densities to evaluate the polarization behavior during Li plating/stripping processes. As shown in Figure 2A-D and Supplementary Figure 2, the polarization potential of the cells with BE exhibits a clear increase after 250 h at 0.5 mA cm-2 and 90 h at 1 mA cm-2, respectively. Differently, at the same test conditions, the symmetric cells with B-0.5 still maintain stable and reduced overpotential after long-term cycling. In addition, there is a slightly higher overpotential of both samples in the initial stage, which remains stable after a period of cycling. This phenomenon is closely related to the original state of the lithium metal and the subsequent SEI formation[20]. Furthermore, when the current density is increased to 2 mA cm-2, the cell with B-0.5 still exhibits better cycling performance than that with BE [Supplementary Figure 2A and B]. The polarization voltages after 50 and 100 h at different current densities are compared and shown in Supplementary Figure 2C and D. As the current density increases, the polarization gap between the two electrolytes also becomes larger. The above improvement effects are related to the high-quality SEI derived from B-0.5 (further analyzed in the subsequent sections), which is beneficial for accelerating the rapid migration of Li+ at the interface. As a result, the compatibility between the electrolyte and LMA is enhanced.
Figure 2. (A-D) Cycling performance of Li||Li symmetric cells at different current densities: (A and B) 0.5 mA cm-2 and 0.5 mAh cm-2, (C and D) 1 mA cm-2 and 1 mAh cm-2. (E) Tafel plots of Li||Li symmetric cells in different electrolytes. (F) Nyquist plot for Li||Li symmetric cells after ten cycles at 1 mA cm-2 and 1 mAh cm-2.
The exchange current density and EIS were tested to understand the differences of SEI layers formed in BE and B-0.5. According to the test results of Li||Li symmetric cells after ten cycles, the exchange current density with B-0.5 is four times larger than that of BE, as shown in Figure 2E, revealing the enhanced reaction kinetics at the Li electrode/electrolyte interface in B-0.5. The rapid charge transfer ability helps suppress the uneven plating and uncontrollable dendritic growth of lithium metal. EIS tests also confirm that the additive is beneficial for reducing the interface impedance due to the highly conductive SEI layer [Figure 2F]. Therefore, the cells in B-0.5 show better rate performance than the BE, as presented in Supplementary Figure 3.
Li||Cu cells were used to further evaluate CE during the Li plating/stripping process. As presented in Supplementary Figure 4 and Figure 3A and B, at the conditions of 1 mA cm-2 and 1 mAh cm-2, it can be seen that the CE of Li||Cu cell with B-0.5 is obviously higher than that with BE after 50 cycles. Moreover, the nucleation overpotential decreases from 283 to 179 mV after adding B2O3, as shown in
Figure 3. (A and B) Li plating/stripping voltage profiles with different electrolytes at the 15th, 25th and 35th cycles under the conditions of 1 mA cm-2 and 1 mAh cm-2. (C) Polarization voltages at different cycles (0.3 mAh cm-2). (D and E) Morphology of Li deposited on Cu substrate after ten cycles in Li||Cu cells with (D) BE and (E) B-0.5 at 1 mA cm-2. (F-K) XPS spectra for Li||Li symmetric cells after ten cycles with (F-H) BE and (I-K) B-0.5.
Besides, the deposition morphology of lithium metal in the two electrolytes was investigated using SEM. The lithium metal deposited on the Cu substrate appears to be loose and porous with severe dendritic growth in the BE electrolyte, as shown in Figure 3D, which accounts for the poor cycling performance and low CE. In comparison, a denser and flatter plating surface without obvious Li dendrites is obtained when using a B-0.5 electrolyte [Figure 3E]. The high ionic conductivity at the interface of the cell with B-0.5 would reduce the nucleation overpotential and enable the uniform deposition of lithium metal, thereby preventing the risk of short circuits[15].
After ten cycles of Li||Li symmetric cells with a current density of 1 mA cm-2 and a capacity of 1 mAh cm-2, the SEI composition on the surface of Li electrodes is analyzed by XPS to gain a deeper understanding of how the additive B2O3 helps to regulate the plating morphology and improve the reaction kinetics. As shown in Figure 3F-K, in F 1s XPS spectra, the content of LiF derived from BE is higher than that from
Electrochemical performance of Li||LRM cells
To identify the optimal additive amount, the electrochemical properties of the Li||LRM cells with the electrolytes containing various amounts of B2O3 were evaluated. As shown in Supplementary Figure 7, the Li||LRM cell with B-0.5 electrolyte (B-0.5-cell) exhibits the best performance in the voltage range of 2-4.8 V at 1 C. Therefore, the electrolyte with 0.5 wt% of B2O3 additive is used in the following part. As depicted in Figure 4A, the Li||LRM cell with BE (BE-cell) exhibits a capacity retention of only 73.7% after 200 cycles at
Figure 4. Electrochemical performances of Li||LRM cells in BE and B-0.5: (A) Cycling performance at 1 C. (B and C) Charge-discharge curves in (B) BE and (C) B-0.5. (D) Average charge/discharge voltage during cycling. (E) Leakage current during 4.8 V constant-voltage floating tests after 100 cycles. (F) Self-discharge curves after 100 cycles. (G) Rate performance.
Furthermore, the leakage current and self-discharge behavior were tested to assess the high-voltage stability at 4.8 V. The results show that the introduction of B2O3 evidently reduces the leakage current after 100 cycles [Figure 4E]. In the self-discharge tests conducted after 50 and 100 cycles, the voltage of BE-cells drops below 3.3 V after five days, and below 2 V after ten days [Figure 4F and Supplementary Figure 8]. In comparison, the B-0.5-cells can maintain a slower trend of voltage drop. The smaller leakage current and lower self-discharge level reveal that the CEI derived from B-0.5 has better stability under high voltage and helps to reduce the side reactions.
In addition, the rate capability was conducted under different current densities, as shown in Figure 4G. The B-0.5-cell exhibits better rate performance, and the discharge capacities are 278, 257, 239, 217, 202, and
The cycling performance under severe conditions is evaluated to comprehensively verify the effectiveness of the additive. The B-0.5-cell maintains a better cycling performance under a high mass loading of
Morphological and structural changes of LRM cathode
For deep insights into the effect of the additive on stabilizing LRM cathodes under high voltage, the cycled cells were disassembled and evaluated. Upon cycling, the continuous decomposition of electrolyte will lead to the generation of HF, which corrodes the cathodes and damages the CEI film, ultimately resulting in the dissolution of TM. For the prepared LRM materials, the proportion of Mn is approximately four times higher than that of Ni and Co, and considering the possible testing errors, the content of Mn migrating to the anode can serve as a crucial indicator to reflect the dissolution degree of TM. In this context, the inductively coupled plasma (ICP) tests were performed to verify the content of Mn on the anode surface after cycling. Figure 6A shows that the content of the dissolved Mn element in B-0.5 is noticeably lower than that in BE. This result is attributed to the stable and durable CEI formed on the cathode surface and fewer harmful species including HF in B-0.5, thereby inhibiting the dissolution of TM and alleviating the structural degradation of LRM. In addition, the cathodes were tested by Raman spectroscopy to investigate the effect of the additive on phase change after 150 cycles. As depicted in Figure 6B, the vibrations near 495 and 600 cm-1 are attributed to the bending (Eg) and stretching (A1g) modes of the layered structure, while the vibration at ~640 cm-1 corresponds to the characteristic peak of the spinel structure[37-39]. The larger blue shift of the A1g peak indicates that more phase transitions have occurred in the LRM cathode from the BE-cell, which further reveals the beneficial effect of the additive in restraining the structural change of cathode material upon cycling.
Figure 6. (A) The ICP test results of Mn element dissolved and deposited on LMA in BE-cell and B-0.5-cell after 200 cycles. (B) Raman spectra of the cathode material before and after cycling. (C) Variation of (003) peak during the initial two cycles by in-situ XRD tests.
The structural evolution of the LRM cathode in the first two cycles was also examined by in-situ XRD tests in Figure 6C and Supplementary Figure 17. Wherein, the angular variation of (003) diffraction peak is closely related to the intercalation/deintercalation behavior of Li+ during the charging and discharging processes. In the early stage of charging, the extraction of Li+ from the lithium layer causes an increase in the electrostatic repulsion between the oxygen layers, which results in the expansion of lithium layer spacing and the shift of (003) peak towards a low angle. As the voltage is gradually raised to around 4.5 V, Li+ in the TM layer is extracted along with the activation of oxygen for charge compensation, and the (003) peak gradually moves back to the high-angle direction. Afterward, during the subsequent discharge stage, the extracted Li+ is embedded back into the TM and lithium layers, corresponding to the movement of the (003) peak to the low and high angles, respectively. In the following cycles, the change of the (003) peak shows a similar trace as in the first cycle. Compared with the initial position, the (003) peak of the LRM cathode in B-0.5-cell shows a smaller average angle shift (0.175° and 0.185° in B-0.5 and BE), indicating the reduced volume change along the c-axis, which reveals the enhanced stability of the LRM cathode in B-0.5 electrolyte [Figure 6C][20]. Supplementary Figure 18 shows the XRD patterns of the initial LRM cathode and the cycled electrodes after 200 cycles in different electrolytes. The diffraction peaks of (003) and (104) in BE exhibit weaker signals, reflecting the more serious structural deterioration. Additionally, the (003) peak in BE also shows a more pronounced leftward shift, which can be ascribed to the higher consumption of active Li and larger polarization. The lack of active Li leads to an increased interlayer, resulting in a larger angle deviation.
To achieve an in-depth understanding of the enhanced electrochemical performance, the surface morphology of the LMA disassembled from the cycled Li||LRM cells is checked after 200 cycles. The morphology of the fresh LMA is tested by SEM and shown in Supplementary Figure 19. The whole surface is flat with slight streaky traces caused by mechanical processing. However, after long-term cycling, clearly different features are presented on the LMA surface in distinct electrolytes. Without an additive in BE, the anode surface appears to be distinctly black, with numerous mossy Li dendrites covered by side products
Figure 7. SEM images of LMAs disassembled from Li||LRM cells after 200 cycles with (A) BE and (C) B-0.5 electrolytes, wherein (B) and (D) are the corresponding locally enlarged images. SEM images of LRM particles after 200 cycles in (E) BE and (F) B-0.5 electrolytes. XPS spectra of the cycled LRM cathodes in (G-I) BE and (J-L) B-0.5 electrolytes.
The chemical composition of CEI on the cathode surface was identified by XPS [Figure 7G-L and Supplementary Figure 21]. The two peaks in F 1s XPS spectra correspond to LiF and C-F/P-F, and the stronger LiF signal indicates that more lithium salts are consumed in BE[31]. The O 1s XPS spectra contain three peaks, corresponding to C-O, C=O and TM-O. With the introduction of B2O3, the C-O peak is slightly stronger than that in BE, which is related to the products caused by the additive[25,40]. In P 2p XPS spectra, the two peaks represent LixPOyFz and PO43- species[31,41]. In the battery system, the substances containing
The improvement mechanism of the above proposed dual-functional electrolyte additive is schematically shown in Figure 8A and B, and summarized below: (I) The B2O3 additive can facilitate the formation of stable and durable SEI and CEI layers on the surface of cathodes and anodes. The regulated interface films can avoid the direct contact of electrode and electrolyte, thereby restraining the side reactions; (II) The generated B-F species can reduce the presence of HF; (III) The highly conductive SEI can suppress the Li dendrites growth; and (IV) The uniform and durable CEI can also stabilize the cathode structure and alleviate the dissolution of TM. These improvements ultimately enhance the electrochemical performance of cells.
Figure 8. (A and B) Schematic illustrations of Li||LRM batteries using (A) BE and (B) B-0.5 electrolytes. (C) Cycling performance of Li||LRM batteries with 0.5 wt% different additives in the same electrolyte. (D) Cost comparison of different additives (Note: data from Manufacturer of Shanghai Aladdin Co., Ltd.).
Apart from the significant advance on improving performance, cost-effectiveness also needs to be considered for a good high-voltage additive. As depicted in Figure 8C, several conventional additives containing B were employed for the cycling tests in the voltage range of 2-4.8 V at 1 C. It is observed that, with the same amount of addition, the discharge capacity with B2O3 is evidently higher than other electrolytes after 200 cycles. Besides, the price of B2O3 is seven times lower than other additives [Figure 8D and Supplementary Table 1]. Its combined advantages of improved performance and low cost make it promising in commercial applications.
CONCLUSIONS
In summary, the inorganic oxide B2O3 is employed as a dual-functional additive in the carbonate electrolyte to enhance the performance of Li||LRM batteries by constructing durable CEI/SEI films. The B2O3 additive can participate in the interface reactions to form the functional protective layers containing B substances. The thin and uniform CEI formed on the cathode side can effectively maintain a stable layered structure of LRM with less TM dissolution and alleviate the continuous electrolyte decomposition. Moreover, the robust SEI formed on the LMA can regulate the deposition morphology with fewer dendrites, improve the CE during Li deposition and stripping process, and enhance the Li+ transport kinetics. Hence, the enhanced cycling property is achieved. Specifically, the Li||LRM battery using the B2O3-containing electrolyte displays a high discharge capacity of 221 mAh g-1 after 200 cycles at 1 C with a high capacity retention of 92.1%. After increasing the upper cut-off voltage to 5 V, more than 85% capacity retention can still be obtained after 150 cycles at 1 C. This work proposes the use of low-cost inorganic oxide as a dual functional additive, providing an attractive new approach for the design and development of the high-voltage electrolyte.
DECLARATIONS
Authors’ contributions
Conceptualization, methodology, formal analysis, investigation, data curation, writing - original draft:
Investigation, formal analysis, validation, writing - review & editing: Gao, G.; Wei, G.; Guo, W.; Lin, L.; Zhang, C.; Li, S.; Liu, Y.
Visualization, writing - review & editing: Yang, Z.; Zhang, Y.; Sa, B.
Funding acquisition, project administration, resources, supervision, writing - review & editing: Peng, D. L.;
Availability of data and materials
The data supporting our findings can be found in the Supplementary Material.
Financial support and sponsorship
The work was supported by financial support from the National Natural Science Foundation of China (Grant Nos. 52272240, 51931006, U22A20118, and 52101273), Science and Technology Planning Projects of Fujian Province of China (Grant No. 2023H0003), the Fundamental Research Funds for the Central Universities of China (Xiamen University: Nos. 20720220074 and 20720240053), Science and Technology Projects of Innovation Laboratory for Sciences and Technologies of Energy Materials of Fujian Province (HRTP-[2022]-22) and the “Double-First Class” Foundation of Materials Intelligent Manufacturing Discipline of Xiamen University.
Conflicts of interest
All authors declared that there are no conflicts of interest.
Ethical approval and consent to participate
Not applicable.
Consent for publication
Not applicable.
Copyright
© The Author(s) 2025.
Supplementary Materials
REFERENCES
2. Ryu, H. H.; Park, K. J.; Yoon, C. S.; Sun, Y. K. Capacity fading of Ni-rich Li[NixCoyMn1-x-y]O2 (0.6 ≤ x ≤ 0.95) cathodes for high-energy-density lithium-ion batteries: bulk or surface degradation? Chem. Mater. 2018, 30, 1155-63.
3. Lan, G.; Zhou, H.; Xing, L.; et al. Insight into the interaction between Ni-rich LiNi0.8Co0.1Mn0.1O2 cathode and BF4--introducing electrolyte at 4.5 V high voltage. J. Energy. Chem. 2019, 39, 235-43.
4. Ko, S.; Obukata, T.; Shimada, T.; et al. Electrode potential influences the reversibility of lithium-metal anodes. Nat. Energy. 2022, 7, 1217-24.
5. Xu, W.; Wang, J.; Ding, F.; et al. Lithium metal anodes for rechargeable batteries. Energy. Environ. Sci. 2014, 7, 513-37.
6. Huang, Y.; Liu, X.; Yu, R.; et al. Tellurium surface doping to enhance the structural stability and electrochemical performance of layered Ni-rich cathodes. ACS. Appl. Mater. Interfaces. 2019, 11, 40022-33.
7. Lee, W.; Muhammad, S.; Sergey, C.; et al. Advances in the cathode materials for lithium rechargeable batteries. Angew. Chem. Int. Ed. 2020, 59, 2578-605.
8. Zheng, H.; Han, X.; Guo, W.; et al. Recent developments and challenges of Li-rich Mn-based cathode materials for high-energy lithium-ion batteries. Mater. Today. Energy. 2020, 18, 100518.
9. Lu, Z.; Liu, D.; Dai, K.; et al. Tailoring solvation chemistry in carbonate electrolytes for all-climate, high-voltage lithium-rich batteries. Energy. Storage. Mater. 2023, 57, 316-25.
10. Wu, H.; Dong, J.; Zhang, Y.; et al. Lattice oxygen redox reversibility modulation in enhancing the cycling stability of Li-rich cathode materials. Adv. Funct. Mater. 2023, 33, 2303707.
11. Lee, H.; Nam, H.; Moon, J. H. Seamless integration of nanoscale crystalline-amorphous MoO3 domains for high-performance lithium-sulfur batteries. Energy. Storage. Mater. 2024, 70, 103551.
12. Su, H.; Chen, Z.; Li, M.; et al. Achieving practical high-energy-density lithium-metal batteries by a dual-anion regulated electrolyte. Adv. Mater. 2023, 35, e2301171.
13. Han, J. G.; Lee, S. J.; Lee, J.; Kim, J. S.; Lee, K. T.; Choi, N. S. Tunable and robust phosphite-derived surface film to protect lithium-rich cathodes in lithium-ion batteries. ACS. Appl. Mater. Interfaces. 2015, 7, 8319-29.
14. Zhao, H.; Lei, D.; He, Y. B.; et al. Compact 3D copper with uniform porous structure derived by electrochemical dealloying as dendrite-free lithium metal anode current collector. Adv. Energy. Mater. 2018, 8, 1800266.
15. Yan, X.; Lin, L.; Han, X.; et al. Li dendrites inhibition realized by lithiophilic and ion/electron conductive 3D skeleton for Li metal anodes. Chem. Eng. J. 2021, 421, 127872.
16. Um, K.; Jung, C.; Nam, H.; Lee, H.; Yeom, S.; Moon, J. H. Janus architecture host electrode for mitigating lithium-ion polarization in high-energy-density Li-S full cells. Energy. Environ. Sci. 2024, 17, 9112-21.
17. Hu, A.; Chen, W.; Du, X.; et al. An artificial hybrid interphase for an ultrahigh-rate and practical lithium metal anode. Energy. Environ. Sci. 2021, 14, 4115-24.
18. Xie, Y.; Huang, Y.; Zhang, Y.; et al. Surface modification using heptafluorobutyric acid to produce highly stable Li metal anodes. Nat. Commun. 2023, 14, 2883.
19. Zhu, Z.; Liu, Z.; Zhao, R.; et al. Heterogeneous nitride interface enabled by stepwise-reduction electrolyte design for dense Li deposition in carbonate electrolytes. Adv. Funct. Mater. 2022, 32, 2209384.
20. Zheng, W. C.; Shi, C. G.; Dai, P.; et al. A functional electrolyte additive enabling robust interphases in high-voltage Li‖LiNi0.8Co0.1Mn0.1O2 batteries at elevated temperatures. J. Mater. Chem. A. 2022, 10, 21912-22.
21. Zhao, W.; Zheng, B.; Liu, H.; et al. Toward a durable solid electrolyte film on the electrodes for Li-ion batteries with high performance. Nano. Energy. 2019, 63, 103815.
22. Gao, H.; Cai, J.; Xu, G. L.; et al. Surface modification for suppressing interfacial parasitic reactions of a nickel-rich lithium-ion cathode. Chem. Mater. 2019, 31, 2723-30.
23. Liu, W.; Oh, P.; Liu, X.; et al. Nickel-rich layered lithium transition-metal oxide for high-energy lithium-ion batteries. Angew. Chem. Int. Ed. 2015, 54, 4440-57.
24. Luo, C.; Liu, Q.; Wang, X.; et al. Synergistic-effect of diluent to reinforce anion-solvation-derived interfacial chemistry for 4.5 V-class Li||LiCoO2 batteries. Nano. Energy. 2023, 109, 108323.
25. Li, J.; Li, W.; You, Y.; Manthiram, A. Extending the service life of high-Ni layered oxides by tuning the electrode-electrolyte interphase. Adv. Energy. Mater. 2018, 8, 1801957.
26. Xiao, Z.; Liu, J.; Fan, G.; et al. Lithium bis(oxalate)borate additive in the electrolyte to improve Li-rich layered oxide cathode materials. Mater. Chem. Front. 2020, 4, 1689-96.
27. Zhao, Q.; Wu, Y.; Yang, Z.; et al. A fluorinated electrolyte stabilizing high-voltage graphite/NCM811 batteries with an inorganic-rich electrode-electrolyte interface. Chem. Eng. J. 2022, 440, 135939.
28. Cheng, F.; Zhang, X.; Qiu, Y.; et al. Tailoring electrolyte to enable high-rate and super-stable Ni-rich NCM cathode materials for Li-ion batteries. Nano. Energy. 2021, 88, 106301.
29. Shi, P.; Zhang, L.; Xiang, H.; Liang, X.; Sun, Y.; Xu, W. Lithium difluorophosphate as a dendrite-suppressing additive for lithium metal batteries. ACS. Appl. Mater. Interfaces. 2018, 10, 22201-9.
30. Piao, Z.; Xiao, P.; Luo, R.; et al. Constructing a stable interface layer by tailoring solvation chemistry in carbonate electrolytes for high-performance lithium-metal batteries. Adv. Mater. 2022, 34, e2108400.
31. Zhang, X.; Liu, G.; Zhou, K.; et al. Enhancing cycle life of nickel-rich LiNi0.9Co0.05Mn0.05O2 via a highly fluorinated electrolyte additive - pentafluoropyridine. Energy. Mater. 2022, 1, 100005.
32. Wu, D.; He, J.; Liu, J.; et al. Li2CO3/LiF-rich heterostructured solid electrolyte interphase with superior lithiophilic and Li+-transferred characteristics via adjusting electrolyte additives. Adv. Energy. Mater. 2022, 12, 2200337.
33. Qin, Y.; Wang, D.; Liu, M.; et al. Improving the durability of lithium-metal anode via in situ constructed multilayer SEI. ACS. Appl. Mater. Interfaces. 2021, 13, 49445-52.
34. Zhang, B.; Wang, L.; Wang, X.; et al. Sustained releasing superoxo scavenger for tailoring the electrode-electrolyte interface on Li-rich cathode. Energy. Storage. Mater. 2022, 53, 492-504.
35. Li, Y.; Li, W.; Shimizu, R.; et al. Elucidating the effect of borate additive in high-voltage electrolyte for Li-rich layered oxide materials. Adv. Energy. Mater. 2022, 12, 2103033.
36. Ye, C.; Tu, W.; Yin, L.; et al. Converting detrimental HF in electrolytes into a highly fluorinated interphase on cathodes. J. Mater. Chem. A. 2018, 6, 17642-52.
37. Zheng, H.; Zhang, C.; Zhang, Y.; et al. Manipulating the local electronic structure in Li-rich layered cathode towards superior electrochemical performance. Adv. Funct. Mater. 2021, 31, 2100783.
38. Li, S.; Liu, Y.; Zhang, Y.; et al. Interfacial oxygen coordination environment regulation towards high-performance Li-rich layered oxide cathode. Chem. Eng. J. 2023, 462, 142194.
39. He, W.; Liu, P.; Qu, B.; et al. Uniform Na+ doping-induced defects in Li- and Mn-rich cathodes for high-performance lithium-ion batteries. Adv. Sci. 2019, 6, 1802114.
40. Ji, Y.; Li, S.; Zhong, G.; et al. Synergistic effects of suberonitrile-LiBOB binary additives on the electrochemical performance of high-voltage LiCoO2 electrodes. J. Electrochem. Soc. 2015, 162, A7015.
41. Xu, G.; Pang, C.; Chen, B.; et al. Prescribing functional additives for treating the poor performances of high-voltage (5 V-class)
42. Wu, D.; Zhu, C.; Wang, H.; et al. Mechanically and thermally stable cathode electrolyte interphase enables high-temperature, high-voltage Li||LiCoO2 batteries. Angew. Chem. Int. Ed. 2024, 63, e202315608.
43. Fu, A.; Lin, J.; Zheng, J.; et al. Additive evolved stabilized dual electrode-electrolyte interphases propelling the high-voltage Li||LiCoO2 batteries up to 4.7 V. Nano. Energy. 2024, 119, 109095.
Cite This Article

How to Cite
Zhou, D.; Gao, G.; Yang, Z.; Guo, W.; Lin, L.; Zhang, Y.; Zhang, C.; Li, S.; Liu, Y.; Sa, B.; Wei, G.; Peng, D. L.; Lin, J.; Xie, Q. A low-cost inorganic oxide as dual-functional electrolyte additive towards long cycling Li-rich
Download Citation
Export Citation File:
Type of Import
Tips on Downloading Citation
Citation Manager File Format
Type of Import
Direct Import: When the Direct Import option is selected (the default state), a dialogue box will give you the option to Save or Open the downloaded citation data. Choosing Open will either launch your citation manager or give you a choice of applications with which to use the metadata. The Save option saves the file locally for later use.
Indirect Import: When the Indirect Import option is selected, the metadata is displayed and may be copied and pasted as needed.
About This Article
Copyright
Data & Comments
Data
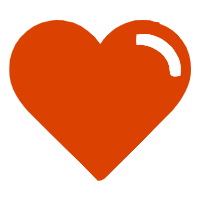
Comments
Comments must be written in English. Spam, offensive content, impersonation, and private information will not be permitted. If any comment is reported and identified as inappropriate content by OAE staff, the comment will be removed without notice. If you have any queries or need any help, please contact us at support@oaepublish.com.