Recent advances of cobalt-free and nickel-rich cathode materials for lithium-ion batteries
Abstract
In order to satisfy the rapidly increasing demands for a large variety of applications, there has been a strong desire for low-cost and high-energy lithium-ion batteries and thus for next-generation cathode materials having low cost yet high capacity. In this regard, the research of cobalt (Co)-free and nickel (Ni)-rich (CFNR) layered oxide cathode materials, able to meet the low-cost and high-capacity requirements, has been extensively pursued but remains challenging largely due to the elimination of Co and high content of Ni in these materials. Herein, we systematically review the challenges and recent advances of CFNR cathode materials on these important aspects. Specifically, we first clarify the role of Co in Ni-rich layered oxides and the possibility of its elimination to fabricate CFNR cathode materials. We then discuss the methods developed to synthesize these cathode materials. This is followed by the elucidation about their degradation mechanisms and the research progress of modification strategies achieved in enhancing the properties for these materials. Finally, we discuss the current challenges and future prospects of CFNR cathode materials as the next-generation cathode materials for low-cost and high-energy lithium-ion batteries.
Keywords
INTRODUCTION
Since their first commercialization by Sony in 1991, lithium-ion batteries (LIBs) have been used for a large variety of applications, including portable electronic devices, electric vehicles, and renewable energy storage systems[1-4]. To satisfy the rapidly increasing demands for these applications, lowering the cost and enhancing the energy density have been two important tasks for LIBs[5]. These, in turn, continuously propelled the research and development of the cathode materials of LIBs because they are the core component accounting for more than half of the cost and largely determining the energy density of LIBs[5].
LiCoO2 (LCO) was the cathode of Sony’s LIBs in 1991 and has been predominantly employed in LIBs for 3C (Computer, Communication, Consumer) electronic devices[1,2]. However, owing to the inherently scarce resource of cobalt (Co) [Figure 1A] and the rapid expansion in production capacity of LIBs, the cost of Co continued to increase over the past decade [Figure 1B]. In conjunction with the environmental unfriendliness of Co, this indeed triggered a vigorous desire for lowering the Co content in cathode materials[1,3,4]. In this regard, by substituting the Co of LCO with other transition metals (TM), the resultant layered oxides, such as lithium nickel cobalt manganese oxide (LiNixCoyMnzO2) and lithium nickel cobalt aluminum oxide (LiNixCoyAlzO2), have shown their great opportunity in lowering Co content and have become an important family of cathode materials for LIBs[1,3,4].
Figure 1. (A) Abundances of cobalt, nickel, manganese, magnesium, and aluminum on the earth’s crust. (B) Price chart of raw cobalt, nickel, and copper in the past decade (2012 to August 2022), (C) Energy density and cobalt content of typical layered oxides, ranging from LiCoO2 (LCO) to LiNixMnyCozO2 (NMC-xyz) of increasing nickel content. This figure is quoted with permission from Lee et al.[1].
It is known that nickel (Ni) is the key element that determines the capacity and energy density of layered oxides[3,5], with LiNiO2 (LNO) possessing a high theoretical specific energy density of ~1,050 Wh kg-1[6]. Thus, along with the aforementioned consideration of lowering the cost of LIBs, the percentage of Ni has been increased and that of Co decreased in layered oxides to realize lower cost and higher energy density for LIBs[1,3,5]. As shown in Figure 1C, the energy density enhancement of LiNixCoyMnzO2 upon the simultaneous increase and decrease of its Ni and Co contents, respectively, represents a good example of such kind (with respect to LCO)[1,3,4]. Moreover, the complete elimination of Co while further increasing the Ni content, resulting in the so-called Co-free and Ni-rich (CFNR) layered oxides as the next-generation cathode materials, has been considerably investigated in recent years to meet the ultimate goal of low-cost and high-energy LIBs[7-11]. In this sense, for example, extensive studies demonstrated that LiNixM1-xO2 (x ≥ 90%, M represents a metal other than Co) can achieve an ultrahigh specific capacity (≥ 200 mAh g-1) and energy density (800 Wh kg-1) with its cost estimated to be less than 20 $ kWh-1[3,5,9,10,12-19].
Nevertheless, an immediate concern about the feasibility of the CFNR design can be logically put forward, which is associated with a prevailing belief about the essentiality of Co[1,20] and the issues from a high Ni content (such as cation mixing[7,21], side reactions[15,21,22], and microcracking[9,13]) in layered oxide cathode materials. This has indeed spurred the extensive research of CFNR cathode materials in recent years, and with their achievements and issues reviewed but sporadically[1-4]. In this paper, therefore, we systematically and comprehensively review the aspects, covering the essentiality of Co, synthesis methods, degradation mechanisms, and modification strategies, of CFNR cathode materials. Specifically, we begin our discussion about clarifying the role of Co in and the possibility of its elimination from the Ni-rich layered oxides. This is followed by a discussion about the synthesis methods, the degradation mechanisms, and the research progress of modification strategies achieved in enhancing the properties of CFNR cathode materials. Finally, the current challenges and future prospects of these materials are summarized, which would encourage more research and development on them as the next-generation cathode materials for low-cost and high-energy LIBs.
THE ROLE OF COBALT IN NICKEL-RICH CATHODE MATERIALS
Largely owing to its advantages of good electronic conduction and low Li/Ni mixing, Co is considered an essential element for Ni-rich layered oxides, such as the widely used commercial cathode materials of
Figure 2. (A) Formation energy (Ef) of one pair of Ni/Li exchange in LiNi1/3Mn1/3Co1/3O2 (333), LiNi0.4Mn0.4Co0.2O2 (442), LiNi0.5Mn0.5O2 (550), LiNi0.6Mn0.2Co0.2O2 (622), and LiNi0.7Mn0.15Co0.15O2 (71515) with zigzag TM arrangements. The local configurations of Ni/Li exchanges with the lowest and highest Ef are shown in each material. The shaded areas show the general trend of the Ef variation for the Ni/Li exchange, and the schematics at the bottom represent the nonequivalent ion environment for the antisite Li ion in the TM layer. This figure is quoted with permission from Zheng et al.[26]. (B) Differential capacity as a function of cell voltage (dQ/dV vs. V) of 2nd charge and discharge of LiNiO2, LiNi0.95Al0.05O2, LiNi0.95Mn0.05O2, LiNi0.95Mg0.05O2, and LiNi0.95Co0.05O2. This figure is quoted with permission from Li et al.[27]. (C) The c-axis lattice parameter changes in the as-prepared samples obtained from Rietveld refinements. The lattice changes of the c axes of NC64 (LiNi0.6Co0.4O2), NMC622 (LiNi0.6Mn0.2Co0.2O2) and NM64 (LiNi0.6Mn0.4O2) were 5.0%, 2.9% and 1.0%, respectively. This figure is quoted with permission from Liu et al.[28].
However, recent studies raised a question about the effectiveness and necessity of Co in Ni-rich layered oxides[1,2]. For example, when compared to magnesium (Mg), manganese (Mn), and aluminum (Al), the 5% substitution of Co was found ineffective in suppressing the multiphase transition during the electrochemical process of LNO [Figure 2B][2,3,27]. Also, as shown in Figure 2C, upon delithiation (charge), the Ni-rich
SYNTHESIS OF CFNR CATHODE MATERIALS
Broadly, as for conventional layered oxides, CFNR cathode materials can be synthesized in either a solid or wet state. In a typical solid-state reaction procedure, a CFNR cathode material is obtained by mixing its raw reactant materials first, followed by sintering the mixture thus prepared at a high temperature and in an oxygen atmosphere[32-35]. Using this process, for example, Croguennec et al. synthesized LiNi1-xTixO2 by sintering its raw material mixture of Li2O, NiO, and TiO2 under an oxygen gas flow at 800-870 °C[35]. Usually, the solid-state reaction methods have the distinct advantage of ease of operation but the disadvantage of nonuniform elemental distribution and potential generation of impurity phases for the products. In this regard, CFNR cathode materials have been extensively researched (and even mass-produced) in a wet state. Particularly, in these methods, they are synthesized by preparing their precursors first, followed by calcinating the resultant precursors with a lithium source under the conditions of a high temperature and an oxygen atmosphere. Moreover[36-40], the precursors of the CFNR layered oxides can be obtained through various approaches, including electrolytic, sol-gel, hydrothermal, and co-precipitation methods.
Specifically, in a typical electrolytic method, two nickel metal plates are used as both the cathode and anode that are immersed in an aqueous electrolyte. Upon stirring the electrolyte, a current is applied to oxidize the anode to extract Ni ions into the electrolyte, which are transported towards the cathode under the electric field and the electrolyte stirring. At the cathode, the reduction of water generates hydroxide ions (and hydrogen gas) which interact with the Ni ions from the anode to form nickel hydroxide [Ni(OH)2]. Using this approach[39], Ji et al. synthesized a LNO cathode by sintering the as-prepared Ni(OH)2 as the precursor with a mixed salt of LiOH-LiNO3 as the lithium source under a flowing oxygen atmosphere at 700 °C[39]. The LNO thus obtained possessed an excellent layered structure and hence a high capacity of 235.2 mAh g-1 upon charge/discharge at 0.1 C and a good capacity retention of ~80.2% after cycling at 1 C for 100 cycles.
The sol-gel method is characterized by the formation of a sol-gel network (as the precursor) from a solution containing the metal ions of the target cathode material, in which the sol-gel network is deduced through an appropriate means, such as hydrolysis reaction or chelating reaction[30,36,38]. In this method, a lithium source can be directly included into the precursor during the sol-gel formation, ensuring a uniform distribution of Li+, bulk elements, and doping elements in the final cathode material[36,38]. For example, Kong et al. acquired a Cu-doped LNO gel precursor by dissolving LiCH3COOH, Ni(CH3COOH)2, and Cu(NO3)2 in ethanol at
In a hydrothermal process, the reaction of the precursor synthesis is carried out at a high temperature and under a high pressure self-generated in a closed system. By doing this, Essehli et al. firstly prepared a
Using the co-precipitation method to synthesize a precursor is based on the co-precipitation of the bulk and doping elements of a target cathode material, in which an aqueous metal ion solution (with a designed stoichiometric ratio between the bulk and doping elements), a chelating agent (such as ammonium hydroxide), and a precipitant (such as NaOH or KOH) are simultaneously pumped into a continuously stirred reactor to precipitate all metal ions together into a mixed hydroxide as the precursor. In this procedure, while the coordination between the chelating agent and the metal ions is essential for ensuring the homogeneous elemental distribution, regulating the pH of the entire reaction system is critical for adjusting/optimizing the size and morphology of the primary/secondary particles of the precursor. Typically, a reaction time of over 20 hours is needed to achieve a high tap density and large secondary particles for the precursor. Using this approach, for instance, Cui et al. produced a spherical and large-sized Ni0.94Al0.05Mg0.01(OH)2 precursor (over 10 µm) from an aqueous solution containing NiSO4, Al(NO3)3, and MgSO4 using an ammonia-containing KOH solution to control the pH (11.0-11.5) and with a reaction time of 45-50 h[41]. The LiNi0.94Al0.05Mg0.01 cathode material was obtained by calcinating the as-synthesized precursor with LiOH as the lithium source at 690 °C and under oxygen for 15 h. This cathode material consisted of element-uniformly-distributed, spherical, and large-sized secondary particles, presenting a high capacity of 210 mAh g-1 upon the charge/discharge at C/3 in 2.8-4.4 V along with a capacity retention up to 89% after cycling for 100 cycles.
As seen above, a range of methods have been developed for synthesizing CFNR cathode materials and are advantageous and disadvantageous on different aspects. In particular, the electrolytic method can produce cathode materials with a high purity and well-layered structure but requires extra efforts to deal with its accompanying hydrogen byproducts and electrolyte wastes; The sol-gel method ensures a uniform elemental distribution for the cathode materials but is relatively time-consuming (for solvent evaporation) and difficult to scale up; The hydrothermal strategy can obtain highly crystalline and large-particle-sized cathode materials but encounters with poor scalability and safety concerns (due to its high temperature-/high pressure-related reactions); The co-precipitation technique has the advantages of homogeneous distribution of elements, spherical shape and large size of dense particles, low cost, ease for continuous operation, and excellent scalability for production but needs to manage its liquid wastes. Overall, although different approaches should be selected to meet the varied property requirements for a specific cathode material, co-precipitation has been widely employed for the large-scale production of commercial layered oxide cathode materials including CFNR.
DEGRADATION OF CFNR CATHODE MATERIALS
Despite the significant advancements in the research of CFNR cathode materials, obstacles are still hindering the commercialization of these materials because of their degradations, mainly including crystal structure instability, phase transition, surface side reactions, and microcracking[4,20,42]. To obtain stable structural, mechanical, thermal, and electrochemical properties for CFNR cathode materials, it is of great importance to understand the mechanisms behind their degradations, which are comprehensively discussed as follows.
Crystal structure instability
A stable crystal structure is essential for Ni-rich layered oxide cathode materials including CFNR. Ideally, these materials should possess a well-defined crystal structure, where all elements in the lattice only play their unique roles without affecting each other. However, this is challenged by the issues mainly including Li/Ni mixing and oxygen loss of these materials, leading to their crystal structure instability.
Li/Ni mixing inherently exists in and has been attributed to similar ionic radii, superexchange interaction, magnetic frustration, and kinetic advantage of Ni-rich layered oxides[3,20,42].
Specifically, same as their prototype of LNO, Ni-rich layered oxides have an α-NaFeO2-type hexagonal layered crystal structure (R
Figure 3. (A) Model of the layered structure with R
Superexchange interaction refers to the enhanced exchange between two TM cations, one from the TM layer and the other from the Li layer, through a bridged anion (i.e., O2-) of a layered oxide[26,49]. Through its unpaired spin electrons, the p orbitals of this intervening oxygen can bind with the d orbitals of the TM cations to form σ bonds. Using a Ni-rich layered oxide as the example [Figure 3B][26], the antisite Ni2+ in the Li layer tends to form a 180°-exchange interaction stronger with the Ni2+ than those with other metal ions in the TM layer. Consequently, the preference of this interaction (due to its low energy) can enhance the Li/Ni mixing, which, in turn, makes the Ni-involved exchange interaction “super”, resulting in the so-called superexchange interaction.
Magnetic frustration originates from the strong magnetic interaction due to the conflicting electron spins of TM ions in the hexagonal lattice of a TM layer. Using three triangularly placed Ni3+ (having their d shells half-filled) as the example [Figure 3C][25], the Ni3+ in the center of the hexagonal lattice has a spin state parallel (in the same direction) to those of its three surrounding Ni3+ at the apexes of the lattice. This arrangement of conflicting electron spins is a higher-energy and hence unstable state, leading to the so-called magnetic frustration that strengthens the Li/Ni mixing[50,51].
Kinetic advantage represents a situation in which the migration of Ni2+ from the TM layer to the Li layer has a low barrier in energy. Particularly, with LiNi1-xCoxO2 as the example[52], the migration of Ni2+ from the TM layer to the Li layer is favorable to follow a route of Oh (octahedral Ni site)-Td (tetrahedral site)-Oh (octahedral Li site) [Figure 3D(i)] owing to its low energy barrier of between 0.303 and 0.598 eV for the Li 0% (fully delithiated) and Li 100% (fully lithiated) states, respectively [Figure 3E(i)]. Even upon the oxygen loss of LiNi1-xCoxO2, Ni2+ can also find a favorable path of Oh (Ni site)-Vo (oxygen vacancy)-Oh (Li site) for migration [Figure 3D(ii)] because of its low energy barrier of between 0.567 and 0.617 eV for the Li 100% (fully lithiated) and Li 0% (fully delithiated) states, respectively [Figure 3E(ii)][52]. In this regard, compared to the migration of Co (e.g., with a high energy barrier in the route of Oh-Td-Oh of 1.6 eV for Li0.5CoO2[53]), that of Ni2+ has a remarkably lower energy barrier and thus is considered kinetically advantageous for Li/Ni mixing[52].
Due to the strengthened Li/Ni mixing by the factors above, the crystal structures become unstable (with a decreased c parameter)[54], the Li+ diffusion pathways are blocked (by the antisite Ni2+ in the Li slab)[1], the surface metals are lost (due to the migration of antisite Ni2+ to the particle surface)[26], and the layered structure is damaged (to disordered spinel and eventually rock salt)[55,56] for Ni-rich layered oxides.
Apart from Li/Ni mixing, oxygen loss is another important cause influencing the crystal structure instability of Ni-rich layered oxides[55]. Using the prototype of these materials (i.e., LNO) as the example, upon delithiation, its oxygen arrangement is transformed from the original face-centered cubic (O3, ABCABC) structure to the final hexagonal close-packed structure (O1, ABAB) [Figure 4A][55,57]. This transformation is accompanied by oxygen loss, which can be quantitatively interpreted by the formation energy of oxygen vacancy with thermodynamic calculations[58]. As can be seen in Figure 4B, the formation energy of oxygen vacancy of LNO decreases rapidly from 1.8 eV for the fully lithiated state to 0.35 eV for the 75% delithiated state, providing a strong driving force for oxygen loss.
Figure 4. (A) Atomic models of O3 phase (space group R
Furthermore, oxygen loss promotes Li/Ni mixing, as depicted in Figure 4C, in which the oxygen loss-deduced vacancies (denoted as Vo) can reduce the energy barrier for the migration of their adjacent Ni ion from the Ni layer to the Li layer. Following the path of Oh-Td-Oh [Figure 4C], the migration energy barriers for a half-delithiated LNO with and without oxygen vacancies are calculated and plotted in Figure 4D[58], showing the strong effect of oxygen vacancies in reducing the energy barrier for Ni migration and thus enhancing the Li/Ni mixing.
As a result, along with the promoted Li/Ni mixing, oxygen loss destroys the crystal structures and produces unwanted gases, jointly leading to inferior electrochemical performance, poor thermal stability, and even safety hazards for Ni-rich layered oxides[52,55-60].
Phase transition
Along with their delithiation upon charge, Ni-rich layered oxide cathode materials, including CFNR, undergo a phase-transition sequence of Hexagonal 1 (H1) - Monoclinic (M) - Hexagonal 2 (H2) - Hexagonal 3 (H3) - Hexagonal 4 (H4) [Figure 5A][4,61]. The oxygen arrangement of the H1, M, H2, and H3 phases is in an O3 type but that of the H4 phase is in an O1 type. The presence of these phases during the charge/discharge of LNO, as an example, has been verified by the in-situ synchrotron diffraction, as shown in Figure 5B. Although a complete reversibility is desired for the transition between these phases, the real situation is complicated. Specifically, at a high delithiation state (x > 0.95), the layered slip of the H3 phase results in the formation of the H4 phase (NiO2, CdI2-type structure), unfortunately creating lattice mismatch and volume changes that can impede Li+ transport and degrade the cathode materials[23]. In practice, therefore, the cutoff voltage during charge (i.e., the depth of delithiation) is usually limited to avoid the appearance of the H4 phase for these materials[7,8,11].
Figure 5. (A) Schematic diagram of the structural evolution (H1 → M → H2 → H3 → H4) during the charging of layered LiNiO2 materials. This figure is quoted with permission from Li et al.[4]. (B) Contour maps of in situ synchrotron diffraction of LNO collected during the first cycle. Cell voltage as a function of state of charge or discharge of the first cycle, which is aligned with the diffraction patterns (i). XRD patterns of selected scattering angle regions: 4.68°-5.48° (ii), 9.59°-10.45° (iii), and 11.36°-12.26° (iv). Based on the refinement results, the phases in each region are labeled in (i). The peak splitting for phase M is also indicated in (iii) and (iv). This figure is quoted with permission from Li et al.[61]. (C) Illustration of the reactions of the surface residual lithium of a LiNi0.96Mg0.02Ti0.02O2 (NMT) cathode with H2O and CO2 in the air, forming LiOH and Li2CO3, respectively. This figure is quoted with permission from
During lithiation/delithiation, largely owing to their smaller change in lattice structure (using the c-axis parameter change as the example as shown in Figure 5A), the transition among the H1 → M → H2 phases is more reversible than that between the H2 → H3 phases[11,62]. Indeed, upon the increased depth of delithiation, the H2 → H3 transition can cause a large anisotropic contraction (as schematically presented by the dramatic decrease in the c-axis parameter in Figure 5A) and hence the collapse of the layered structure. This structural strain, in turn, induces inter-/intra-granular cracking, loss of interparticle contact, and loss of active materials through defect and rock-salt formation, thereby leading to inferior and irreversible electrochemical performance for the cathode materials[1,63]. Therefore, owing to its great impact on the structure stability and electrochemical performance, the H2 → H3 phase transition for Ni-rich layered oxide cathode materials, including CFNR, has been extensively studied and should be paid more attention in the future research[9,11].
Surface side reactions
An ideal surface able to ensure the stable mechanical, thermal, and electrochemical properties is required for Ni-rich layered oxide cathode materials including CFNR. In practice, however, this remains challenging because of the possible surface side reactions of these materials attributable to their high reactivities with the electrolyte and the environment.
On the one hand, the high reactivity of these materials refers to Ni3+/4+ generated upon their delithiation to a highly-charged state, which can react with the electrolyte to produce the undesirable species such as Ni2+, O2, and CO2[15,42]. While the generated Ni2+ can enhance the Li/Ni mixing to deteriorate the crystal structure, the generated O2 means oxygen loss and induced crystal structure instability for these materials; both have been discussed under Section "Crystal structure instability". Moreover, all gases produced imply the gassing inside the battery that may cause serious safety hazards[46]. The surface of the cathode materials is prone to erosion/dissolution by HF derived from the LiPF6 decomposition and hydrolysis of the electrolyte, leading to the loss of active TM and, hence, the capacity degradation for these materials[64]. Also, the dissolved TM can be reduced into metals and participate in forming a solid electrolyte interface (SEI) on the anode. These will hinder the Li+ intercalation into the anode and disrupt the original cathode/anode capacity ratio, thereby raising the impedance and deteriorating the battery performance[64].
On the other hand, the high reactivity of these materials is expressed by their environmental instability. Specifically, the residual lithium on the surface of these materials, which is left during the material synthesis[46,65], can initiate some unwanted side reactions, such as those with H2O and CO2 in the air to form LiOH and Li2CO3, respectively [Figure 5C][15]. In the subsequent slurry process for electrode preparation, the LiOH and Li2CO3 thus formed can react with polyvinylidene fluoride (PVDF), the commonly used binder for cathodes, to form gels that will increase the difficulty and even disable the production of the electrodes[65,66]. Therefore, cathode materials without any side reactions with the electrolyte and the environment are highly desired.
Microcracking
Mechanical stability/integrity of Ni-rich layered oxide cathode materials including CFNR play an important role in ensuring their stable electrochemical performance. This is, however, affected by a mechanical degradation mechanism (called microcracking) that occurs during the charge/discharge of these materials[67,68]. Typically, the secondary particles of layered oxides comprise multiple primary particles in the size of sub-micrometers (even nanometers)[7,67]. Upon charge/discharge, the Li+ intercalation/deintercalation into/out of these materials may cause expansion and contraction in volume for their primary particles, resulting in intragranular fracturing within and intergranular fracturing between the primary particles (i.e., microcracking) as marked in Figure 5D by red and blue arrows, respectively[9]. The continuous expansion and contraction of the primary particles exacerbate the growth of the intergranular fractures (microcracks) to form isolated particles. Without contact with the electrolyte, these isolated particles cannot undergo Li+ intercalation/deintercalation and hence become electrochemically inactive. As a result, microcracking will deteriorate the mechanical stability/integrity and degrade the electrochemical performance of the cathode materials[67,68].
Moreover, upon charge/discharge cycling, the proliferation of microcracks allows the electrolyte to infiltrate/penetrate into the newly formed surfaces, making the surface side reactions, as discussed under Section "Surface side reactions", occur inside the particles of the cathode materials, further degrading their electrochemical performance and even causing safety issues for batteries[55]. Therefore, mechanically stable/complete cathode materials able to suppress such kind of microcracking are highly desired.
The degradation mechanisms of Ni-rich layered oxide cathode materials including CFNR discussed above can occur individually and interact with each other. The appearance of one mechanism may trigger others to occur, jointly deteriorating the structural, mechanical, thermal, and electrochemical properties of these materials and even deducing safety hazards for their batteries. Therefore, when researching a new strategy for improving the properties for CFNR cathode materials, these degradation mechanisms should be thoroughly considered/addressed.
MODIFICATION FOR CFNR CATHODE MATERIALS
In order to enhance the structural, mechanical, thermal, and electrochemical properties of CFNR cathode materials towards their practical applications, considerable efforts have been made in recent years to address the degradations of these materials, as discussed above[2,3,41,68-73]. Among them, the modification strategies of bulk-phase doping, surface coating, and single crystallization have been extensively studied, to be elucidated as follows.
Bulk-phase doping
Bulk-phase doping refers to incorporating small amounts (typically less than 5%) of additional elements as dopants into the host lattice of a cathode material without introducing impurity phases. With this strategy, substantial efforts have been made to dope non-Co elements into Ni-rich layered oxides to fabricate CFNR cathode materials[2,3,18,19,44,74-81]. This has been demonstrated to be effective in stabilizing the crystal structure and suppressing the phase transition to enhance the properties for CFNR cathode materials[7,9]. In this regard, as schematically presented in Figure 6A, bulk-phase doping has been realized for CFNR cathode materials on a range of locations including Ni-site (TM layer), Li-site (Li layer), Ni/Li dual-sites, O-site, and interstitial sites[16,27,71,72,77,81-85].
Figure 6. (A) Schematic diagram of possible doping sites on a CFNR cathode material. (B) Capacity retention of the Ni-rich
Ni-site doping has been considerably studied for CFNR cathode materials owing to its effectiveness in strengthening the metal-oxygen binding thus suppressing the Li/Ni mixing, oxygen loss, and phase transition[16,19,36,77,84,86]. It can be carried out either during the synthesis of precursors or in the calcination of the pre-formed precursors. In the former, the dopant ions are introduced into the bulk metal salt solution to prepare precursors, followed by calcinating the precursors thus obtained with a lithium source to produce the cathode materials[8,41,87]. This allows the uniform distribution of dopants in the cathode materials. The latter physically mixes the dopants with the pre-formed precursors and a lithium source, followed by calcination to produce the cathode materials[9,10,16,30]. A large variety of metal ions having ionic radii similar to that of Ni3+ (0.56 Å) have been employed for Ni-site doping, which, depending on their valence states, can be classified into low- and moderate-valence dopants, respectively.
Fe3+ and Al3+ are frequently used low-valence dopants for Ni-site doping for CFNR cathode materials[18,38,77,88,89]. For example, Xi et al. used Fe3+ as the dopant to replace Co3+ of NCM811 to prepare a new CFNR cathode material of LiNi0.8Fe0.1Mn0.1O2[89]. With a traditional co-precipitation method, Fe was first incorporated into the hydroxide precursor with Ni and Mn, followed by calcinating the resultant precursor with LiOH to produce the target LiNi0.8Fe0.1Mn0.1O2. Even without Co, this material realized a low energy barrier of Li+ diffusion (0.969 eV), similar to that of NCM811 (0.979 eV), thus exhibiting a high capacity of 202.6 mA h g-1 at 0.1 C in 3.0-4.5 V and a capacity retention up to 81.1% after 10 C cycling for 150 cycles in 3.0-4.3 V.
Moderate-valence dopants, such as Zr4+, Ti4+, and Mn4+, are also employed for Ni-site doping for CFNR cathode materials, which is largely encouraged by their capability to form strong TM-O bonds[7,18,78,90,91]. Among them, Mn4+ has been paid more attention[7,31,78]. For instance, Sun et al. studied the effect of the Mn4+ dopant using the conventional co-precipitation process to prepare a range of Ni1-xMnx(OH)2 (0.1 ≤ x ≤ 0.5) precursors, followed by calcinating these precursors with LiNO3/LiOH to obtain the
Similarly, with its ionic radius close to that of Li+ (0.76 Å)[39], Mg2+ (0.72 Å) was extensively studied for doping the Li-site of CFNR cathode materials[85,92-95]. Indeed, Mg2+ has been demonstrated to be effective as a pillar ion in mitigating the internal stress of the crystal lattice during the anisotropic lattice contraction at a high charging state, thereby enhancing the structural stability and electrochemical performance for CFNR cathode materials[92,96]. For instance, Laine et al. used co-precipitation to incorporate varied amounts of Mg2+ into Ni(OH)2, the hydroxide precursor of LNO, followed by calcinating the precursors thus prepared with LiOH to produce Mg-doped LNO cathode materials[95]. Although having a lowered initial capacity at 0.1 C in 3.0-4.3 V, these Mg-modified materials displayed a significantly enhanced cycling stability, for example, with the boosted capacity (198.3 vs. 193.6 mAh g-1) and capacity retention (98.9% vs. 87.6%) for a 2 mol % Mg-doped LNO cathode over its pristine counterpart in the subsequent cycling for 62 cycles.
Logically, combing their benefits as elucidated above, Ni-site doping and Li-site doping have been conducted simultaneously, resulting in a range of Ni/Li dual-site doping combinations, such as Al/Mg[41,97], Ti/Mg[55,81,96], and Mn/Mg[72], to further improve the properties for CFNR cathode materials. For example, Mu et al. prepared a Ni/Mg/Mn-incorporating hydroxide precursor via co-precipitation first and then calcinated the as-prepared precursor with LiOH to synthesize a Mg/Mn-LNO cathode material[72]. Owing to the occupations of Mg2+ on the Li site and Mn4+ on the Ni site, respectively, for co-doping, the Mg/Mn-LNO cathode delivered a smooth voltage profile, enhanced structural stability, elevated self-discharge resistance, and inhibited nickel dissolution. These enabled the Mg/Mn-LNO cathode with improved cycling stability, presenting high capacity retentions of 80% after 350 cycles at C/3 and 67% after 500 cycles at 2 C in
Apart from cation doping on the metal sites, as discussed above, anion doping on the O-site has also attracted considerable attention for CFNR cathode materials, with the frequently studied anions being F, Cl, and S[84,98]. Although anion doping can be expected to enhance the properties for cathode materials, the selection of anions should be carefully considered because of their possible conflicting effects. In this regard, Kong et al. used density functional theory (DFT) to systematically investigate the effects of F, Cl, and S on the properties (including redox potential, ionic conductivity, Li/Ni exchange, lattice distortion, and Ni migration upon delithiation) of LNO as a model cathode material[84]. As schematically summarized in Figure 6C, while F can improve almost all the properties considered, it, unfortunately, facilitates the Li/Ni mixing due to its reduced energy in forming the Li/Ni defects. With their increased Li/Ni defect formation energies, in contrast, Cl and S can suppress the Li/Ni mixing and lattice distortion (especially Cl). However, concerning F, Cl- and S-dopings result in lower redox potentials for their doped LNO, which is attributed to their relatively weaker bonding strength with Li. Moreover, Cl and S have contradictory effects on the structural stability and rate capability for LNO; that is, a high doping concentration can benefit the former whereas a low one is preferred for the latter. To address the conflicting effects from anion doping, a codoping strategy by coming anion doping with cation doping has been suggested for Ni-rich layered oxide cathode materials including CFNR[84].
Unlike the doping on a specific site, such as the Ni-site, Li-site, or O-site, as discussed so far, interstitial doping refers to that within the space between varied atoms of a cathode material [Figure 6A][71,99], which is usually achieved by boron (B)[16,71]. B-doping has been considered effective in microstructurally engineering the primary particles of a cathode material. Specifically, it can dissolve (insert) into the host structure, leading to a surface-confined distribution to inhibit the growth and hence increase the aspect ratio (length/diameter) for the primary particles of the cathode material. This significantly enhances the microstructural and hence cycling stabilities for CFNR cathode materials. For example, Kim et al. doped B into LNO by firstly synthesizing a Ni(OH)2 precursor via co-precipitation and then calcinating the pre-synthesized precursor with B2O3 and LiOH to fabricate a B-doped LNO (i.e., B-LNO) cathode[71]. In a full-cell configuration (with a graphite anode), this B-LNO cathode showed an initial capacity of 200 mAh g-1 and retained this capacity up to 81% even after cycling for 300 cycles (0.5 C, 2.7-4.2 V), significantly outperforming its pristine counterpart (having a similar initial capacity but a lower capacity retention of about 71%).
Surface coating
Surface coating is a strategy that applies a protective layer on the surface of CFNR cathode materials to protect them from the direct contact with the electrolyte and the environment to suppress the side reactions for enhancing their properties[15,69,73,100]. Generally, this method can be carried out on either the secondary or primary particle surface of a target CFNR cathode material.
Secondary particle coating refers to applying a modifying material directly onto the secondary particle surface of a CFNR cathode material. This has been practiced for years with various materials, such as metals, metal oxides, polymers, and carbon/polymer composites, as illustrated below.
For coating metals on CFNR cathode materials, Chu et al. developed a method by combining solid-phase mixing with low-temperature sintering to coat a 35 nm-thick selenium (Se) metallic coating on LNO to fabricate a Se-LNO cathode [Figure 7A][73]. Owing to its stabilized interface and enhanced kinetic behavior and the suppressed phase transition, particle pulverization, and HF corrosion enabled by the Se coating, this Se-LNO cathode showed an improved rate capability (capacity at 5 C: 149.6 vs. 135.7 mAh/g) and cycling stability (capacity retention after 300 cycles at 1 C: 82.09% vs. 31.31%) over its pristine counterpart.
Figure 7. (A) Schematic diagram of the synthesis process for Se-LNO. Long-term testing of LNO and Se-LNO at 1 C and cutoff voltages of 2.8-4.3 V over 300 cycles. This figure is quoted with permission from Chu et al.[73]. (B) Schematic illustration of the advantages and cycling performance of the dual-protection PP-coating layer. This figure is quoted with permission from Kim et al.[15]. (C) Differences in mechanism and effects of low-valence (Al) and high-valence (Nb, Ta, and Mo) dopants, including the incorporation into bulk and the grain boundary coating, (D and E) Cycling performance (0.5 C, 2.7-4.3V) of half-cells featuring LNO, Al-LNO, Nb-LNO, Ta-LNO, and Mo-LNO cathodes calcined at 650 °C (D) and their respective optimized calcination temperatures (E). This figure is quoted with permission from Park et al.[10].
Inspired by the previous research about the capability of a metal oxide coating of Al2O3 to enhance the properties of layered oxides[101-105], Kang et al. used first-principles calculations to investigate how Al2O3 can improve the thermal stability of CFNR cathode materials[100]. With the archetype cathode of LNO, their study indicated that the Al2O3 deposits undergo a phase transition from the corundum-type crystalline
To pursue the polymer coating strategy for CFNR cathode materials, Kim et al. mechanically mixed
To study carbon/polymer composite coatings for CFNR cathode materials, Luu et al. prepared a graphene-ethyl cellulose (GrEC)-coated LNO cathode by firstly dispersing LNO powder in a GrEC-containing NMP solution and then casting the resultant dispersion directly onto an Al foil to fabricate the electrode[69]. The hydrophobic property of the GrEC composite was demonstrated to be effective in protecting the LNO surface from the contact with atmospheric moisture, thereby minimizing the lithium impurity generation and hence enhancing the electrochemical performance for the LNO electrode thus modified[69]. Even upon exposure to humidified CO2 for 24 h, the GrEC-coated LNO electrode delivered a capacity of 230 mAh g-1 (0.1 C, 2.8-4.6 V), slightly lower than that of the electrode without CO2 exposure (240 mAh g-1). When compared to the significant capacity degradation of the pristine LNO electrode from 240 to 180 mAh g-1 upon the CO2 exposure, this clearly highlights the effectiveness of the carbon/polymer composite coatings for CFNR cathode materials.
With respect to secondary particle coating, primary particle coating is an emerging method, in which the coating materials are directly cladded on the surface of the primary particles of a CFNR cathode material. Direct coating at the primary particle level has been demonstrated to possess some unique advantages as elucidated below.
One approach to realizing primary particle coating is conducted by crushing the secondary particles of a cathode material into primary particles first, followed by coating the primary particles thus formed with a modifying material. For instance, Brow et al. first milled the secondary particles of LiNi0.9Mn0.05Al0.05O2 into primary particles and then used H3PO4 to react with the surface residual lithium of the resultant primary particles to form a Li3PO4 layer on the primary particles[106]. Benefiting from the enhanced air stability and suppressed electrolyte-side reactions by the Li3PO4 layer, the LiNi0.9Mn0.05Al0.05O2 thus modified showed a remarkably enhanced cycling stability (especially at a high voltage) with a capacity of 180 mAh g-1
Without crushing the secondary particles, another approach for primary particle coating is achieved by forming the coating in situ during the calcination process of a cathode material. Specifically, this can be done by mixing a Ni(OH)2 precursor with LiOH and the oxide (or hydroxide) of a high-valence element (such as Nb5+, Ta5+, W6+, or Mo6+), followed by calcination under oxygen at a high temperature[9,10,14,17,70,74,76,80,107-109]. As schematically illustrated in Figure 7C, unlike the doping of low-valence elements into the bulk structure, these high-valence elements usually accumulate (due to their insolubility into the crystal structure[10]) along the interparticle boundaries and form Li-X-O compounds (due to their high electronic hybridization with oxygen[108]) there to accomplish the coating on primary particles. Since the temperature at which the content of Li-X-O compounds declines is higher for high-oxidation-state dopants, the segregation at the grain boundary can be reinforced, the size of primary particles can be refined, and the calcination temperature range can be widened for high-valence-element-doped CFNR cathode materials, thereby maintaining their highly aligned microstructure and high crystallinity over a wide calcination temperature range[10]. Furthermore, the grain size refinement achieved by high-valence-element doping dissipates the deleterious strain from abrupt lattice contraction through fracture toughening and the removal of local compositional inhomogeneities, and the enhanced cation ordering induced by the presence of high-valence elements stabilizes the delithiated structure through a pillar effect[9]. Together, these boost the cycling stability for high-valence-element-doped CFNR cathode materials. Using this strategy, Park et al. doped LNO with Nb5+, Ta5+, and Mo6+, respectively, by calcinating their oxides with a Ni(OH)2 precursor (pre-prepared via co-precipitation) and LiOH[10]. They clearly demonstrated the superior cycling stability of the resultant Nb-LNO, Ta-LNO, and Mo-LNO cathodes over the pristine and a low-valence-element-doped (i.e., Al-LNO) counterparts regardless of the calcination temperatures (either at a same temperature of 650 °C [Figure 7D] or their respective optimized calcination temperatures [Figure 7E]. Importantly, these works spotlight the excellence of primary particle coating (through high-valence-element doping) in facilitating the practical applications of CFNR cathode materials.
Single crystallization
Single crystallization is a strategy that synthesizes the CFNR cathode materials in a single crystal structure to stabilize the mechanical structure/integrity for improving the properties of these materials[110]. As discussed earlier under Section "Microcracking" and now schematically illustrated in Figure 8A, upon the microcracking during the charge/discharge of a conventional polycrystalline cathode material, its resultant intergranular fractures (microcracks) allow the electrolyte to infiltrate/penetrate into the newly formed surfaces of the material. This, in turn, promotes a series of issues including surface side reaction, surface pulverization, structure collapse, disordered phase transition, TM dissolution, and cathode/electrolyte interface (CEI) thickening, and eventually degrades the electrochemical performance and may cause safety concerns for this cathode material.
Figure 8. (A) Schematic illustration for the mechanism of single crystal structure mitigating the structure degradation and performance deterioration of LiNi0.9Mn0.1O2 (NM91), (B and C) SEM images of PC-NM91 (B) and SC-NM91 (C), (D) Half-cell cycling tests of
Although the strategies of bulk-phase doping[111,112] and surface coating[113-115] can alleviate the microcracking to some extent, single crystallization has been demonstrated to be the most effective in doing so[116,117]. Particularly, since single crystal structures can eliminate the uneven stresses deriving from the intergranular boundaries of polycrystalline structures, single crystallization has been extensively studied to suppress the microcracking-induced issues of polycrystalline materials [Figure 8A] and, more excitingly, to synthesize single crystal CFNR cathode materials in recent years[67,86,87,93,118-120].
Single crystal CFNR cathode materials can be synthesized using a solid-phase calcination process similar to polycrystalline materials. However, since the calcination temperature for a single crystal cathode material is always higher than that for its polycrystalline counterpart, which would result in lithium evaporation and serious Li/Ni mixing[68], a low-melting-point lithium salt (in addition to the lithium source used in the conventional solid-phase calcination process) is usually introduced to form a molten salt mixture to facilitate the single crystal growth through a dissolution-recrystallization mechanism[68,118,119]. For example, Dai et al. developed a LiOH-Li2SO4 molten salt method to synthesize a single crystal LiNi0.9Mn0.1O2
As seen above, various modification strategies have been considerably studied to improve the properties of CFNR cathode materials. While bulk-phase doping into various sites can stabilize the crystal structure and restrain the phase transition, surface coating on secondary and primary particles can suppress the side reactions, and single crystallization can strengthen the mechanical stability/integrity for these materials. Moreover, regarding the varied degradation mechanisms of CFNR cathode materials that may trigger each other to take place simultaneously, different modification strategies can/should be incorporated together to jointly overcome these problems to efficiently enhance the overall structural, mechanical, thermal, and electrochemical properties of these materials, towards their practical applications.
CONCLUSIONS AND OUTLOOKS
The rapidly increasing demands in lowering the cost and enhancing the energy density have continuously facilitated the research and development of new cathode materials for LIBs, to which CFNR cathode materials are considered good candidates largely owing to their low cost and high capacity. Among the diverse methods for synthesizing these materials, co-precipitation has been widely employed due to its distinct advantages over electrolytic, sol-gel, and hydrothermal approaches. However, in order for CFNR cathode materials to be practically useful for LIBs, their degradation issues, mainly including crystal structure instability, phase transition, surface side reactions, and microcracking, should be thoroughly considered and solved.
In this regard, extensive research has been conducted in the past years to address these shortcomings of CFNR cathode materials. Specifically, bulk-phase doping with non-Co elements has been performed on various sites including Ni-site, Li-site, Ni/Li dual-sites, O-site, and interstitial sites to stabilize the crystal structure and restrain the phase transition for these materials. Surface coating on either the secondary or primary particles of these materials has been demonstrated to be effective in protecting them from the direct contact with the electrolyte and the environment to suppress their side reactions. Single crystallization can synthesize these materials in a single crystal structure to strengthen their mechanical stability/integrity to overcome the microcracking-deduced problems. Provided their effectiveness has already been demonstrated and drawbacks still exist, these modification strategies are worth further investigation to better improve the structural, mechanical, thermal, and electrochemical properties for CFNR cathode materials. Moreover, since the different degradation mechanisms of these materials may interact with each other to occur simultaneously, various combinations of these modification strategies should be considered accordingly, which can jointly enhance the overall properties and indeed represent a future research direction for CFNR cathode materials. Furthermore, owing to their merits that have been demonstrated in enhancing the properties of conventional layered oxides, core-shell[121-123] and gradient-concentration structures[18,124] are worth being studied for CFNR cathode materials with new structures. Finally, towards the practically useful applications of CFNR cathode materials at the industrial level, their future research should be rationally expended with binders[125-128] and electrolytes[15,45] because the former are an essential component for electrode fabrication and the latter for cell assembly, both influencing the electrochemical performance of CFNR cathode materials.
Given their remarkable advancements accomplished in the past and the considerable research under development, it is anticipated that high-performance CFNR cathode materials will emerge as the next-generation cathode materials to meet the ultimate goal for producing low-cost and high-energy LIBs.
DECLARATIONS
Authors’ contributions
Writing - original draft: Wen L
Data analysis and interpretation: Wang X, Zeng X, Wang T, Li L, Hu Y, Yu Q
Writing - review & editing: Cheng F, Lu W
Funding acquisition, project administration, resources, supervision: Lu W
Availability of data and materials
Not applicable.
Financial support and sponsorship
This work was financially supported by Major Science and Technology Projects in Yunnan Province (grant number: 2016HE001-2016HE002).
Conflicts of interest
All authors declared that there are no conflicts of interest.
Ethical approval and consent to participate
Not applicable.
Consent for publication
Not applicable.
Copyright
© The Author(s) 2024.
REFERENCES
1. Lee S, Manthiram A. Can cobalt be eliminated from lithium-ion batteries? ACS Energy Lett 2022;7:3058-63.
2. Yu L, Liu T, Amine R, Wen J, Lu J, Amine K. High nickel and no cobalt - the pursuit of next-generation layered oxide cathodes. ACS Appl Mater Interfaces 2022;14:23056-65.
3. Kim Y, Seong WM, Manthiram A. Cobalt-free, high-nickel layered oxide cathodes for lithium-ion batteries: progress, challenges, and perspectives. Energy Stor Mater 2021;34:250-9.
4. Li H, Wang L, Song Y, et al. Understanding the insight mechanism of chemical-mechanical degradation of layered Co-free Ni-rich cathode materials: a review. Small 2023;19:e2302208.
5. Li W, Erickson EM, Manthiram A. High-nickel layered oxide cathodes for lithium-based automotive batteries. Nat Energy 2020;5:26-34.
6. Deng T, Fan X, Cao L, et al. Designing in-situ-formed interphases enables highly reversible cobalt-free LiNiO2 cathode for Li-ion and Li-metal batteries. Joule 2019;3:2550-64.
7. Sun YK, Lee DJ, Lee YJ, Chen Z, Myung ST. Cobalt-free nickel rich layered oxide cathodes for lithium-ion batteries. ACS Appl Mater Interfaces 2013;5:11434-40.
8. Li W, Lee S, Manthiram A. High-nickel NMA: a cobalt-free alternative to NMC and NCA cathodes for lithium-ion batteries. Adv Mater 2020;32:e2002718.
9. Park G, Namkoong B, Kim S, Liu J, Yoon CS, Sun Y. Introducing high-valence elements into cobalt-free layered cathodes for practical lithium-ion batteries. Nat Energy 2022;7:946-54.
10. Park N, Kim S, Kim M, et al. Mechanism of doping with high-valence elements for developing Ni-rich cathode materials. Adv Energy Mater 2023;13:2301530.
11. Yoon CS, Jun D, Myung S, Sun Y. Structural stability of LiNiO2 cycled above 4.2 V. ACS Energy Lett 2017;2:1150-5.
12. Kim Y, Kim H, Manthiram A. A kinetic study on cobalt-free high-nickel layered oxide cathode materials for practical lithium-ion batteries. J Power Sources 2023;558:232633.
13. Mesnier A, Manthiram A. Synthesis of LiNiO2 at moderate oxygen pressure and long-term cyclability in lithium-ion full cells. ACS Appl Mater Interfaces 2020;12:52826-35.
14. Wang X, Zhang B, Xiao Z, et al. Enhanced rate capability and mitigated capacity decay of ultrahigh-nickel cobalt-free LiNi0.9Mn0.1O2 cathode at high-voltage by selective tungsten substitution. Chin Chem Lett 2023;34:107772.
15. Kim JM, Xu Y, Engelhard MH, et al. Facile dual-protection layer and advanced electrolyte enhancing performances of cobalt-free/nickel-rich cathodes in lithium-ion batteries. ACS Appl Mater Interfaces 2022;14:17405-14.
16. Yi M, Dolocan A, Manthiram A. Stabilizing the interphase in cobalt-free, ultrahigh-nickel cathodes for lithium-ion batteries. Adv Funct Mater 2023;33:2213164.
17. Ryu H, Park G, Yoon CS, Sun Y. Suppressing detrimental phase transitions via tungsten doping of LiNiO2 cathode for next-generation lithium-ion batteries. J Mater Chem A 2019;7:18580-8.
18. Zhang Y, Li H, Liu J, Liu J, Ma H, Cheng F. Enhancing LiNiO2 cathode materials by concentration-gradient yttrium modification for rechargeable lithium-ion batteries. J Energy Chem 2021;63:312-9.
19. Yoon CS, Kim U, Park G, et al. Self-passivation of a LiNiO2 cathode for a lithium-ion battery through Zr doping. ACS Energy Lett 2018;3:1634-9.
20. Luo Y, Wei H, Tang L, et al. Nickel-rich and cobalt-free layered oxide cathode materials for lithium ion batteries. Energy Stor Mater 2022;50:274-307.
21. Wang T, Yang J, Wang H, et al. Promoting reversibility of Co-free layered cathodes by Al and cation vacancy. Adv Energy Mater 2023;13:2204241.
22. Seong WM, Manthiram A. Complementary effects of Mg and Cu incorporation in stabilizing the cobalt-free LiNiO2 cathode for lithium-ion batteries. ACS Appl Mater Interfaces 2020;12:43653-64.
23. Cui Z, Guo Z, Manthiram A. Assessing the intrinsic roles of key dopant elements in high-nickel layered oxide cathodes in lithium-based batteries. Adv Energy Mater 2023;13:2203853.
24. Divakaran AM, Minakshi M, Bahri PA, et al. Rational design on materials for developing next generation lithium-ion secondary battery. Prog Solid State Chem 2021;62:100298.
26. Zheng J, Teng G, Xin C, et al. Role of superexchange interaction on tuning of Ni/Li disordering in layered Li(NixMnyCoz)O2. J Phys Chem Lett 2017;8:5537-42.
27. Li H, Cormier M, Zhang N, Inglis J, Li J, Dahn JR. Is cobalt needed in Ni-rich positive electrode materials for lithium ion batteries? J Electrochem Soc 2019;166:A429-39.
28. Liu T, Yu L, Liu J, et al. Understanding Co roles towards developing Co-free Ni-rich cathodes for rechargeable batteries. Nat Energy 2021;6:277-86.
29. Tian R, Yin S, Zhang H, Song D, Ma Y, Zhang L. Influence of Al doping on the structure and electrochemical performance of the Co-free LiNi0.8Mn0.2O2 cathode material. Dalton Trans 2023;52:11716-24.
30. Shen L, Du F, Zhou Q, et al. Cobalt-free nickel-rich cathode materials based on Al/Mg co-doping of LiNiO2 for lithium ion battery. J Colloid Interface Sci 2023;638:281-90.
31. Park G, Sun HH, Noh T, et al. Nanostructured Co-free layered oxide cathode that affords fast-charging lithium-ion batteries for electric vehicles. Adv Energy Mater 2022;12:2202719.
32. Zhong Q, von Sacken U. Crystal structures and electrochemical properties of LiAlyNi1-yO2 solid solution. J Power Sources 1995;54:221-3.
33. Nishida Y, Nakane K, Satoh T. Synthesis and properties of gallium-doped LiNiO2 as the cathode material for lithium secondary batteries. J Power Sources 1997;68:561-4.
34. Lin S, Fung K, Hon Y, Hon M. Crystallization kinetics and mechanism of the LixNi2-xO2 (0 < x ≤ 1) from Li2CO3 and NiO. J Crystal Growth 2002;234:176-83.
35. Croguennec L, Suard E, Willmann P, Delmas C. Structural and electrochemical characterization of the LiNi1-yTiyO2 electrode materials obtained by direct solid-state reactions. Chem Mater 2002;14:2149-57.
36. Kong X, Li D, Fedorovskaya EO, Kallio T, Ren X. New insights in Al-doping effects on the LiNiO2 positive electrode material by a sol-gel method. Int J Energy Res 2021;45:10489-99.
37. van Bommel A, Dahn JR. Analysis of the growth mechanism of coprecipitated spherical and dense nickel, manganese, and cobalt-containing hydroxides in the presence of aqueous ammonia. Chem Mater 2009;21:1500-3.
38. Kong X, Li D, Lahtinen K, Kallio T, Ren X. Effect of copper-doping on LiNiO2 positive electrode for lithium-ion batteries. J Electrochem Soc 2020;167:140545.
39. Ji H, Ben L, Yu H, Qiao R, Zhao W, Huang X. Electrolyzed Ni(OH)2 precursor sintered with LiOH/LiNiO3 mixed salt for structurally and electrochemically stable cobalt-free LiNiO2 cathode materials. ACS Appl Mater Interfaces 2021;13:50965-74.
40. Essehli R, Parejiya A, Muralidharan N, et al. Hydrothermal synthesis of Co-free NMA cathodes for high performance Li-ion batteries. J Power Sources 2022;545:231938.
41. Cui Z, Xie Q, Manthiram A. A cobalt- and manganese-free high-nickel layered oxide cathode for long-life, safer lithium-ion batteries. Adv Energy Mater 2021;11:2102421.
42. Zheng J, Ye Y, Liu T, et al. Ni/Li disordering in layered transition metal oxide: electrochemical impact, origin, and control. ACC Chem Res 2019;52:2201-9.
43. Tan X, Peng W, Luo G, et al. Chemical and structural evolution during solid-state synthesis of cobalt-free nickel-rich layered oxide cathode. Mater Today Energy 2022;29:101114.
44. Yu L, Zhao H, Sun J, Han Q, Zhu J, Lu J. Insights into micromorphological effects of cation disordering on Co-free layered oxide cathodes. Adv Funct Mater 2022;32:2204931.
45. Su L, Jarvis K, Charalambous H, Dolocan A, Manthiram A. Stabilizing high-nickel cathodes with high-voltage electrolytes. Adv Funct Mater 2023;33:2213675.
46. Cui Z, Manthiram A. Thermal stability and outgassing behaviors of high-nickel cathodes in lithium-ion batteries. Angew Chem Int Ed 2023;62:e202307243.
47. Rougier A, Saadoune I, Gravereau P, Willmann P, Delmasa C. Effect of cobalt substitution on cationic distribution in LiNi1-yCoyO2 electrode materials. Solid State Ion 1996;90:83-90.
48. Wei H, Tang L, Huang Y, et al. Comprehensive understanding of Li/Ni intermixing in layered transition metal oxides. Mater Today 2021;51:365-92.
49. Kanamori J. Superexchange interaction and symmetry properties of electron orbitals. J Phys Chem Solids 1959;10:87-98.
50. Xiao Y, Liu T, Liu J, et al. Insight into the origin of lithium/nickel ions exchange in layered Li(NixMnyCoz)O2 cathode materials. Nano Energy 2018;49:77-85.
51. Wang D, Xin C, Zhang M, et al. Intrinsic role of cationic substitution in tuning Li/Ni mixing in high-Ni layered oxides. Chem Mater 2019;31:2731-40.
52. Kim Y, Kim D, Kang S. Experimental and first-principles thermodynamic study of the formation and effects of vacancies in layered lithium nickel cobalt oxides. Chem Mater 2011;23:5388-97.
53. Reed J, Ceder G. Role of electronic structure in the susceptibility of metastable transition-metal oxide structures to transformation. Chem Rev 2004;104:4513-33.
54. Yu H, Qian Y, Otani M, et al. Study of the lithium/nickel ions exchange in the layered LiNi0.42Mn0.42Co0.16O2 cathode material for lithium ion batteries: experimental and first-principles calculations. Energy Environ Sci 2014;7:1068-78.
55. Wang C, Han L, Zhang R, et al. Resolving atomic-scale phase transformation and oxygen loss mechanism in ultrahigh-nickel layered cathodes for cobalt-free lithium-ion batteries. Matter 2021;4:2013-26.
56. Ahmed S, Bianchini M, Pokle A, et al. Visualization of light elements using 4D STEM: the layered-to-rock salt phase transition in LiNiO2 cathode material. Adv Energy Mater 2020;10:2001026.
57. Cheng J, Ouyang B, Persson KA. Mitigating the High-charge detrimental phase transformation in LiNiO2 using doping engineering. ACS Energy Lett 2023;8:2401-7.
58. Kong F, Liang C, Wang L, et al. Kinetic stability of bulk LiNiO2 and surface degradation by oxygen evolution in LiNiO2-based cathode materials. Adv Energy Mater 2019;9:1802586.
59. Wang L, Maxisch T, Ceder G. A First-principles approach to studying the thermal stability of oxide cathode materials. Chem Mater 2007;19:543-52.
60. Li L, Yu J, Darbar D, et al. Atomic-scale mechanisms of enhanced electrochemical properties of Mo-doped Co-free layered oxide cathodes for lithium-ion batteries. ACS Energy Lett 2019;4:2540-6.
61. Li H, Hua W, Liu-théato X, et al. New insights into lithium hopping and ordering in LiNiO2 cathodes during Li (De)intercalation. Chem Mater 2021;33:9546-59.
62. Ikeda N, Konuma I, Rajendra HB, Aida T, Yabuuchi N. Why is the O3 to O1 phase transition hindered in LiNiO2 on full delithiation? J Mater Chem A 2021;9:15963-7.
63. de Biasi L, Schiele A, Roca-Ayats M, et al. Phase transformation behavior and stability of LiNiO2 cathode material for Li-ion batteries obtained from in situ gas analysis and operando X-Ray diffraction. ChemSusChem 2019;12:2240-50.
64. Zhang SS. Problems and their origins of Ni-rich layered oxide cathode materials. Energy Stor Mater 2020;24:247-54.
65. Bi Y, Li Q, Yi R, Xiao J. To pave the way for large-scale electrode processing of moisture-sensitive Ni-rich cathodes. J Electrochem Soc 2022;169:020521.
66. Marchand-brynaert J, Jongen N, Dewez J. Surface hydroxylation of poly(vinylidene fluoride) (PVDF) film. J Polym Sci A Polym Chem 1997;35:1227-35.
67. Dai P, Kong X, Yang H, Li J, Zeng J, Zhao J. Single-crystal Ni-rich layered LiNi0.9Mn0.1O2 enables superior performance of Co-free cathodes for lithium-ion batteries. ACS Sustain Chem Eng 2022;10:4381-90.
68. Kaneda H, Furuichi Y, Ikezawa A, Arai H. Single-crystal-like durable LiNiO2 positive electrode materials for lithium-ion batteries. ACS Appl Mater Interfaces 2022;14:52766-78.
69. Luu NS, Meza PE, Tayamen AM, et al. Enabling ambient stability of LiNiO2 lithium-ion battery cathode materials via graphene-cellulose composite coatings. Chem Mater 2023;35:5150-9.
70. Ober S, Mesnier A, Manthiram A. Surface stabilization of cobalt-free LiNiO2 with niobium for lithium-ion batteries. ACS Appl Mater Interfaces 2023;15:1442-51.
71. Kim Y, Kim H, Shin W, Jo E, Manthiram A. Insights into the microstructural engineering of cobalt-free, high-nickel cathodes based on surface energy for lithium-ion batteries. Adv Energy Mater 2023;13:2204054.
72. Mu L, Kan WH, Kuai C, et al. Structural and electrochemical impacts of Mg/Mn dual dopants on the LiNiO2 cathode in Li-metal batteries. ACS Appl Mater Interfaces 2020;12:12874-82.
73. Chu Y, Zhou J, Liu W, Chu F, Li J, Wu F. Cobalt-free LiNiO2 with a selenium coating as a high-energy layered cathode material for lithium-ion batteries. Small Sci 2023;3:2300023.
74. Zaker N, Geng C, Rathore D, et al. Probing the mysterious behavior of tungsten as a dopant inside pristine cobalt-free nickel-rich cathode materials. Adv Funct Mater 2023;33:2211178.
75. Liu L, Zhao Y, Jiang G, et al. Dual-site lattice co-doping strategy regulated crystal-structure and microstructure for enhanced cycling stability of Co-free Ni-rich layered cathode. Nano Res 2023;16:9250-8.
76. Hu C, Ma J, Li A, et al. Structural reinforcement through high-valence Nb doping to boost the cycling stability of Co-free and Ni-rich LiNi0.9Mn0.1O2 cathode materials. Energy Fuels 2023;37:8005-13.
77. Cao H, Du F, Adkins J, et al. Al-doping induced superior lithium ion storage capability of LiNiO2 spheres. Ceram Int 2020;46:20050-60.
78. Xu T, Du F, Wu L, Fan Z, Shen L, Zheng J. Boosting the electrochemical performance of LiNiO2 by extra low content of Mn-doping and its mechanism. Electrochim Acta 2022;417:140345.
79. Sathiyamoorthi R, Shakkthivel P, Ramalakshmi S, Shul Y. Influence of Mg doping on the performance of LiNiO2 matrix ceramic nanoparticles in high-voltage lithium-ion cells. J Power Sources 2007;171:922-7.
80. Geng C, Rathore D, Heino D, et al. Mechanism of action of the tungsten dopant in LiNiO2 positive electrode materials. Adv Energy Mater 2022;12:2103067.
81. Yang Z, Mu L, Hou D, et al. Probing dopant redistribution, phase propagation, and local chemical changes in the synthesis of layered oxide battery cathodes. Adv Energy Mater 2021;11:2002719.
82. Hua W, Zhang J, Wang S, et al. Long-range cationic disordering induces two distinct degradation pathways in Co-free Ni-rich layered cathodes. Angew Chem Int Ed 2023;62:e202214880.
83. Mu L, Yang Z, Tao L, et al. The sensitive surface chemistry of Co-free, Ni-rich layered oxides: identifying experimental conditions that influence characterization results. J Mater Chem A 2020;8:17487-97.
84. Kong F, Liang C, Longo RC, et al. Conflicting roles of anion doping on the electrochemical performance of Li-ion battery cathode materials. Chem Mater 2016;28:6942-52.
85. Pouillerie C, Croguennec L, Biensan P, Willmann P, Delmas C. Synthesis and characterization of new LiNi1-yMgyO2 positive electrode materials for lithium-ion batteries. J Electrochem Soc 2000;147:2061.
86. Liu A, Zhang N, Stark JE, Arab P, Li H, Dahn JR. Synthesis of Co-free Ni-rich single crystal positive electrode materials for lithium ion batteries: part I. two-step lithiation method for Al- or Mg-doped LiNiO2. J Electrochem Soc 2021;168:040531.
87. Liu Q, Wu Z, Sun J, et al. Facile synthesis of crack-free single-crystalline Al-doped Co-free Ni-rich cathode material for lithium-ion batteries. Electrochim Acta 2023;437:141473.
88. Nie L, Wang Z, Zhao X, et al. Cation/anion codoped and cobalt-free Li-rich layered cathode for high-performance Li-ion batteries. Nano Lett 2021;21:8370-7.
89. Xi Y, Wang M, Xu L, et al. A new Co-free Ni-rich LiNi0.8Fe0.1Mn0.1O2 cathode for low-cost Li-ion batteries. ACS Appl Mater Interfaces 2021;13:57341-9.
90. Deng S, Li Y, Dai Q, et al. Structure and primary particle double-tuning by trace nano-TiO2 for a high-performance LiNiO2 cathode material. Sustain Energy Fuels 2019;3:3234-43.
91. Yoon CS, Choi M, Jun D, et al. Cation ordering of Zr-doped LiNiO2 cathode for lithium-ion batteries. Chem Mater 2018;30:1808-14.
92. Tatsumi K, Sasano Y, Muto S, et al. Local atomic and electronic structures around Mg and Al dopants in LiNiO2 electrodes studied by XANES and ELNES and first-principles calculations. Phys Rev B 2008;78:045108.
93. Liu A, Zhang N, Stark JE, Arab P, Li H, Dahn JR. Synthesis of Co-free Ni-rich single crystal positive electrode materials for lithium ion batteries: part II. one-step lithiation method of Mg-doped LiNiO2. J Electrochem Soc 2021;168:050506.
94. Weber R, Li H, Chen W, Kim C, Plucknett K, Dahn JR. In situ XRD studies during synthesis of single-crystal LiNiO2,
95. Laine P, Välikangas J, Kauppinen T, et al. Synergistic effects of low - level magnesium and chromium doping on the electrochemical performance of LiNiO2 cathodes. J Solid State Electrochem 2024;28:85-101.
96. Mu L, Zhang R, Kan WH, et al. Dopant distribution in Co-free high-energy layered cathode materials. Chem Mater 2019;31:9769-76.
97. Min K, Seo SW, Song YY, Lee HS, Cho E. A first-principles study of the preventive effects of Al and Mg doping on the degradation in LiNi0.8Co0.1Mn0.1O2 cathode materials. Phys Chem Chem Phys 2017;19:1762-9.
98. Fang L, Wang M, Zhou Q, Xu H, Hu W, Li H. Suppressing cation mixing and improving stability by F doping in cathode material LiNiO2 for Li-ion batteries: first-principles study. Colloid Surface A 2020;600:124940.
99. Li B, Yan H, Ma J, et al. Manipulating the electronic structure of Li-rich manganese-based oxide using polyanions: towards better electrochemical performance. Adv Funct Mater 2014;24:5112-8.
100. Kang J, Han B. First-principles study on the thermal stability of LiNiO2 materials coated by amorphous Al2O3 with atomic layer thickness. ACS Appl Mater Interfaces 2015;7:11599-603.
101. Woo JH, Trevey JE, Cavanagh AS, et al. Nanoscale interface modification of LiCoO2 by Al2O3 atomic layer deposition for solid-state Li batteries. J Electrochem Soc 2012;159:A1120-4.
102. Scott ID, Jung YS, Cavanagh AS, et al. Ultrathin coatings on nano-LiCoO2 for Li-ion vehicular applications. Nano Lett 2011;11:414-8.
103. Riley LA, Van Atta S, Cavanagh AS, et al. Electrochemical effects of ALD surface modification on combustion synthesized
104. Zhang X, Belharouak I, Li L, et al. Structural and electrochemical study of Al2O3 and TiO2 coated Li1.2Ni0.13Mn0.54Co0.13O2 cathode material using ALD. Adv Energy Mater 2013;3:1299-307.
105. Seok Jung Y, Cavanagh AS, Yan Y, George SM, Manthiram A. Effects of atomic layer deposition of Al2O3 on the
106. Brow R, Donakowski A, Mesnier A, et al. Mechanical pulverization of Co-free nickel-rich cathodes for improved high-voltage cycling of lithium-ion batteries. ACS Appl Energy Mater 2022;5:6996-7005.
107. Hou A, Xu S, Xu K, Zhang M, Zhao D. Comparative studies of tungsten and zirconium doping on single crystal cobalt-free cathode material. Ionics 2021;27:4241-8.
108. Cheng J, Mu L, Wang C, et al. Enhancing surface oxygen retention through theory-guided doping selection in Li1-xNiO2 for next-generation lithium-ion batteries. J Mater Chem A 2020;8:23293-303.
109. Huang G, Wang R, Lv X, et al. Effect of niobium doping on structural stability and electrochemical properties of LiNiO2 cathode for Li-ion batteries. J Electrochem Soc 2022;169:040533.
110. Li J, Zhou Z, Luo Z, et al. Microcrack generation and modification of Ni-rich cathodes for Li-ion batteries: a review. Sustain Mater Technol 2021;29:e00305.
111. Jamil S, Yu R, Wang Q, et al. Enhanced cycling stability of nickel-rich layered oxide by tantalum doping. J Power Sources 2020;473:228597.
112. Jeong M, Kim H, Lee W, Ahn S, Lee E, Yoon W. Stabilizing effects of Al-doping on Ni-rich LiNi0.80Co0.15Mn0.05O2 cathode for Li rechargeable batteries. J Power Sources 2020;474:228592.
113. Kim U, Kim J, Hwang J, Ryu H, Yoon CS, Sun Y. Compositionally and structurally redesigned high-energy Ni-rich layered cathode for next-generation lithium batteries. Mater Today 2019;23:26-36.
114. Kim U, Park J, Aishova A, et al. Microstructure engineered Ni-rich layered cathode for electric vehicle batteries. Adv Energy Mater 2021;11:2100884.
115. Uzun D, Doğrusöz M, Mazman M, et al. Effect of MnO2 coating on layered Li(Li0.1Ni0.3Mn0.5Fe0.1)O2 cathode material for Li-ion batteries. Solid State Ion 2013;249-50:171-6.
116. Qian G, Zhang Y, Li L, et al. Single-crystal nickel-rich layered-oxide battery cathode materials: synthesis, electrochemistry, and intra-granular fracture. Energy Stor Mater 2020;27:140-9.
117. Zhu J, Zheng J, Cao G, et al. Flux-free synthesis of single-crystal LiNi0.8Co0.1Mn0.1O2 boosts its electrochemical performance in lithium batteries. J Power Sources 2020;464:228207.
118. Liu J, Yuan Y, Zheng J, et al. Understanding the synthesis kinetics of single-crystal Co-free Ni-rich cathodes. Angew Chem Int Ed 2023;62:e202302547.
119. Mesnier A, Manthiram A. Heuristics for molten-salt synthesis of single-crystalline ultrahigh-nickel layered oxide cathodes. ACS Appl Mater Interfaces 2023;15:12895-907.
120. Shen J, Zhang B, Huang W, et al. Achieving thermodynamic stability of single-crystal Co-free Ni-rich cathode material for high voltage lithium-ion batteries. Adv Funct Mater 2023;33:2300081.
121. Xia Y, Chen A, Wang K, et al. Binary-compositional core-shell structure Ni-rich cathode material with radially oriented primary particles in shell for long cycling lifespan lithium-ion batteries. Mater Today Energy 2023;34:101292.
122. Song L, Jiang P, Xiao Z, et al. Core-shell structure LiNi0.8Co0.1Mn0.1O2 cathode material with improved electrochemical performance at high voltage. Ionics 2021;27:949-59.
123. Mallick S, Patel A, Sun X, et al. Low-cobalt active cathode materials for high-performance lithium-ion batteries: synthesis and performance enhancement methods. J Mater Chem A 2023;11:3789-821.
124. Zhang S, Gao P, Wang Y, Li J, Zhu Y. Cobalt-free concentration-gradient Li[Ni0.9Mn0.1]O2 cathode material for lithium-ion batteries. J Alloy Compd 2021;885:161005.
125. Jeong D, Kwon D, Kim HJ, Shim J. Striking a balance: exploring optimal functionalities and composition of highly adhesive and dispersing binders for high-nickel cathodes in lithium-ion batteries. Adv Energy Mater 2023;13:2302845.
126. Pham HQ, Kim G, Jung HM, Song S. Fluorinated polyimide as a novel high-voltage binder for high-capacity cathode of lithium-ion batteries. Adv Funct Mater 2018;28:1704690.
127. Chang B, Kim J, Cho Y, et al. Highly elastic binder for improved cyclability of nickel-rich layered cathode materials in lithium-ion batteries. Adv Energy Mater 2020;10:2001069.
Cite This Article
Export citation file: BibTeX | EndNote | RIS
OAE Style
Wen L, Cheng F, Wang X, Zeng X, Wang T, Li L, Hu Y, Yu Q, Lu W. Recent advances of cobalt-free and nickel-rich cathode materials for lithium-ion batteries. Energy Mater 2024;4:400054. http://dx.doi.org/10.20517/energymater.2024.08
AMA Style
Wen L, Cheng F, Wang X, Zeng X, Wang T, Li L, Hu Y, Yu Q, Lu W. Recent advances of cobalt-free and nickel-rich cathode materials for lithium-ion batteries. Energy Materials. 2024; 4(5): 400054. http://dx.doi.org/10.20517/energymater.2024.08
Chicago/Turabian Style
Lang Wen, Fang Cheng, Xiaoqu Wang, Xinyu Zeng, Ting Wang, Litao Li, Yuqin Hu, Qiang Yu, Wen Lu. 2024. "Recent advances of cobalt-free and nickel-rich cathode materials for lithium-ion batteries" Energy Materials. 4, no.5: 400054. http://dx.doi.org/10.20517/energymater.2024.08
ACS Style
Wen, L.; Cheng F.; Wang X.; Zeng X.; Wang T.; Li L.; Hu Y.; Yu Q.; Lu W. Recent advances of cobalt-free and nickel-rich cathode materials for lithium-ion batteries. Energy Mater. 2024, 4, 400054. http://dx.doi.org/10.20517/energymater.2024.08
About This Article
Copyright
Data & Comments
Data
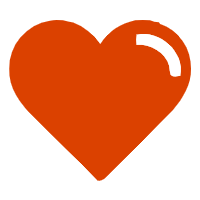
Comments
Comments must be written in English. Spam, offensive content, impersonation, and private information will not be permitted. If any comment is reported and identified as inappropriate content by OAE staff, the comment will be removed without notice. If you have any queries or need any help, please contact us at support@oaepublish.com.