Evaluation of asymmetric poly(vinylidene fluoride)-coated polyimide separator with three-dimensionally homogeneous microporous structure for high-safety lithium-ion battery
Abstract
Safety hazards associated with separators in lithium-ion batteries are more pronounced in light of the significant improvement of energy density of batteries, hindering their wide application. In this research, asymmetric poly (vinylidene fluoride) (PVDF)-coated polyimide separators with three-dimensionally homogeneous microporous (3DHM API/PVDF) structure are prepared, in which a PVDF layer with a thickness of
Keywords
INTRODUCTION
Recently, lithium-ion batteries (LIBs) have become indispensable power sources for portable electronics and electric vehicles owing to their high energy density, extended service life, and minimal self-discharge[1]. However, their safety concerns have been the primary hindrances impeding their widespread applications. To address the above issues, numerous strategies have been implemented, including using flame retardant additives[2], advancing separator designs[3,4], enhancing electrode protection[5,6], and developing all-solid-state electrolyte membranes[7]. The separator employed in LIBs, serving as an ionic conductor while functioning as an electronic insulator, exerts a notable influence on their performances, particularly with regard to safety and power density[3,8]. A suitable separator for large-scale LIBs with high safety standards should possess optimal porosity and outstanding wetting performance to facilitate enhanced ion transport and reduced cell impedance. Furthermore, it should exhibit excellent thermal endurance, preventing shrinkage or melting[9,10]. When the LIBs are operated at elevated temperatures, several exothermic reactions are easily induced, including decomposition of the solid-electrolyte interface (SEI), parasitic reactions of the electrolyte, and internal short circuits. Although the decomposition of SEI and electrolyte leads to heat accumulation in LIBs, the rate of temperature increase in the cells is acceptable. However, the internal short circuit triggered by separator shrinkage generates a large short-circuit current, resulting in catastrophic heat accumulation and temperature increase of LIBs. Separators are the main components of cells that physically separate electrodes and prevent internal short circuits, but their shrinkage or complete collapse inevitably occurs owing to inferior thermal stability. Consequently, it is of paramount importance to optimize the stability of the separator under elevated temperatures to enhance the safety performance of LIBs.
Porous polyolefin separators, composed of polyethylene (PE), polypropylene (PP), and their composites such as triple PP/PE/PP separators and PP/PE, are currently the most prevalent in the field of LIBs. These microporous membranes exhibit attractive qualities, such as superior chemical properties, outstanding mechanical strength, and low cost. However, their poor thermal stability is one of the most significant factors that result in safety hazards of batteries. Specifically, PE and PP separators exhibit melting points of 140 and 165 °C, respectively[11], and partly shrink or completely collapse at elevated temperatures, leading to high short-circuit current and catastrophic thermal runaway. During the past decades, considerable research has been devoted to improving thermal stability of separators, such as developing those with novel materials and modifying them with high melting-point polymers[12-15]. Mitsubishi Paper Japan developed non-woven fabric separators with high dimensional stability at 180 °C[16]. The coin cell of LiMn2O4/Graphite using as-prepared separators showed superior rate and cycle performance than a cell with PP separators, resulting in a discharge capacity of 16 mAh for non-woven fabric separators, significantly surpassing the
Due to its high thermal stability, polyimide (PI) has been increasingly used as a single polymer membrane[11,19-24] to improve thermal stability of batteries. Although PI separators increase safety performances at thermal abuse conditions, they show a negligible effect on relieving heat release under electrochemical abuse, such as serious overcharge. Thermal shutdown separators automatically cut off transport paths of Li+ at elevated temperatures, inhibiting rapid heat accumulation in batteries[25]. Sun et al. prepared a novel three-layer separator[20]. Polybenzimidazole-sheath@polyimide-core nanofibers (PBI@PI) with high strength provide structural support and keep dimensional stability at elevated temperatures. While PBI nanofibers melt at high temperatures, they act as a barrier to the transport of Li+, thereby providing a shutdown function for the separator. Wu et al. reported on sandwich-type PI/Poly (vinylidene fluoride) (PVDF)/PI separators prepared by electrospinning, which combines the advantages of PI and PVDF[22]. The PI outer layers demonstrate excellent thermal stability, while the interlayer of PVDF can melt and form a non-porous film that effectively shuts down the battery. However, compared with interconnected macroporous nanofiber structure, three-dimensionally homogeneous microporous (3DHM) materials have interconnected microporous structure, facilitating formation of 3D Li+ transport paths and uniformity of lithium deposition[26,27]. Moreover, ultrathin pore walls ensure the entire surface is modified uniformly[28-30].
We wonder whether there is a strategy that combines 3DHM structure, functional polymeric coating and thermally stable membrane that can be employed to prepare a separator suitable with thermal shutdown function for high-safety LIBs. Based on the design mentioned above, SiO2 nanoparticles (300 nm) were introduced and then etched by hydrofluoric acid (HF) to form 3DHM structure. Functional PVDF coating with a thickness of 6 μm can melt and form an insulating film to close pores and block ion transfer at high temperatures, terminating the electrochemical process under abuse conditions. A single polymer membrane comprising PI with a thickness of 17 μm and a highly porous structure was utilized. The membrane exhibited high thermal stability. As a result, the asymmetric 3DHM cross-linked PVDF-coated polyimide (3DHM API/PVDF) separator exhibits good thermal stability and shutdown functions. The interconnected microporous structure of the separator facilitates formation of 3D Li+ transport paths and uniformity of lithium deposition, suppressing lithium dendrite growth.
EXPERIMENTAL
Materials: PVDF, Methyl-2-pyrrolidone (NMP), and Poly(vinylidenefluoride-hexafluoropropylene) (PVDF-HFP) were purchased from Aladdin Industrial Co, China. Sulfolane was purchased from Meryer (Shanghai) Biochemical Technology Co., Ltd. HF (48.0%-55.0% w/w in water) was obtained from Energy Chemical. Spherical silica particles (300 nm) were obtained from KE-S30, Nippon Shokubai. LiNi0.8Co0.15Al0.05O2
Preparation of 3DHM API/PVDF separators: The 3DHM API/PVDF separator was fabricated by etching a silica-based sacrificial template. PVDF and silica particles were placed in an oven at 60 °C for an hour before use. Additionally, 0.5 g PVDF was dissolved in 2 g NMP to obtain a clear solution. Then, 0.5 g silica particles were added to the solution, and the mixture was stirred to obtain a homogeneous slurry. The final slurry was cast onto porous polyimide film with a coating thickness of 5-10 μm and subjected to a vacuum oven drying process at 60 °C for 12 h to obtain an asymmetric composite membrane consisting of porous PI, SiO2 and PVDF, denoted as API/PVDF-SiO2. The template SiO2 was removed by HF, and the obtained asymmetric membrane with 3DHM structure was washed thoroughly with deionized water, marked as 3DHM API/PVDF. The resulting membrane was then placed in a vacuum oven at 60 °C for 12 h to ensure evaporation of the water. The fabricated separator was cut into circles with diameters of 16 mm and stored in a glove box for further characterization.
Characterizations: The surface and cross-section morphologies of all these asymmetric separators and lithium metal were observed by a scanning electron microscope (SEM, Zeiss Gemini300). The thermogravimetric analysis (TGA) was conducted using a PerkinElmer simultaneous thermal analyzer (STA 6000). The heating rate was 10 °C min-1 in a nitrogen atmosphere. The thermal shrinkage of the separator was determined from the dimensional changes after thermal treatments for 30 min from 50 to 275 °C. The degree of thermal shrinkage was calculated by: Shrinkage = (A0 - A1)/A0 × 100%, where A0 and A1 are the areas of the separator before and after thermal treatment. The tensile strength of the separators (with a size of 10 mm × 100 mm) was measured using an electronic universal testing machine (MTS E43.104) with a tensile speed of 1 mm S-1. The porosity and pore-size distributions of the separators were analyzed using a mercury porosimeter (Conta PoreMaster 33). The contact angle of the membrane was measured on CSCDIC-200S (Sindin, Dongguan). PP and 3DHM API/PVDF separators were immersed in liquid electrolyte for three min to measure liquid electrolyte uptake. The separators were then quickly weighed after removing any excess solution using filter paper. The experiment utilized circular samples with a
RESULTS AND DISCUSSION
The manufacturing process of the 3DHM API/PVDF separator is shown schematically in Figure 1. The slurry composed of PVDF/SiO2 nanoparticles was cast on the porous PI film, and the resulting film was denoted as API/PVDF-SiO2. After the etching of silica by HF, the 3DHM API/PVDF separator formed. The separator structures and properties are of paramount importance in the battery performance[31]. The pristine PI film consists of interlinked branches with a pore size of 0.5-2 µm [Figure 2A]. Figure 2B-F illustrates the superficial and cross-section SEM images of both sides of API/PVDF-SiO2. The unmodified side of the API/PVDF-SiO2 [Figure 2B] remained the structure of the pristine PI film, and the modified side was fully covered with SiO2 nanoparticles [Figure 2C], clearly distinguishing it from the pristine PI film. From the cross-sectional images [Figure 2D-F], the unmodified and modified layers exhibit loose and dense characteristics, respectively.
Figure 2. SEM images of (A) the pristine PI film and (B-F) the surface and cross-sectional SEM images of API/PVDF-SiO2, (B) the unmodified side, (C) the modified side, (D) the upper section, (E) the overall cross-section and (F) the lower section.
In the further steps, API/PVDF-SiO2 was etched in HF to remove the template of SiO2, generating porous structure. As displayed in Figure 3A, the surface of the unmodified side preserves the porous structure of the PI membrane. The layer that has been modified exhibits a uniform porous structure with a pore size of approximately 300 nm [Figure 3B and C]. These pores are arranged orderly on a large scale, and the 3DHM API/PVDF with a smooth surface retains the integrity of API/PVDF-SiO2 [Figure 3D-F], indicating that the etching process does not destroy the original structure. The thickness of the PVDF coating is about 6 µm. The smooth surface and uniform thickness of the PVDF coating layer contribute to a superior interface with electrodes and ensure an adequate flow of electrolyte which are essential elements for the practical applications of lithium batteries. Moreover, 3DHM in the membrane can form lots of uniform paths for Li+ transports, and facilitate homogeneous Li dispersion at anodes, suppressing lithium dendrite growth and enhancing cycling stability.
Figure 3. Surface and cross-sectional SEM images of 3DHM API/PVDF separator (A) the unmodified side, (B and C) the modified side, (D) the upper section, (E) the overall cross-section and (F) the lower section.
Thermal stability is a crucial factor in the safe operation of LIBs. TGA-differential scanning calorimetry (DSC) analysis of 3DHM API/PVDF separators indicates a heat flow change at about 172 °C [Figure 4], corresponding to a melting process of the PVDF layer in 3DHM API/PVDF. A single endothermic peak is observed in the DSC profiles of PP at 165 °C. This is ascribed to melting of PP materials. Similarly, PP/PE/PP displays two distinct heat absorption peaks at 137 and 161 °C, corresponding to the melting of PE and PP, respectively. The DSC results prove that the high thermo-stability of 3DHM API/PVDF is attributed to the PVDF coating and PI film.
The primary function of separators is to prevent the cathode and anode from coming into contact, which can cause electrical short circuits. Additionally, the separators should remain stable within the battery, even in battery-related accidents. Therefore, any thermal shrinkage of the separator can significantly affect the thermal stability of the battery. To evaluate the thermal shrinkage of as-prepared separators, a series of thermal treatments ranging from 50 to 275 °C were carried out for half an hour and the results are shown in Figure 5. PP and PP/PE/PP remained intact below 50 °C, exhibiting no deformation
Figure 5. Optical photos and shrinkage of PP, PP/PE/PP and modified layers of 3DHM API/PVDF separators before and after the thermal treatments for 30 min at different temperatures. (A1-A3) before the thermal treatment, (B1 and B2) 50 °C; (B3) 150 °C;
In LIBs, the "shutdown" feature of separators is useful to prevent thermal runaway reactions, limiting further lithium-ion transport through the separator and temperature rise in short-circuited cells[32,33]. The shutdown temperature should be lower than the melting point of the separators, and the difference should be wide enough to prevent internal short circuits[15]. To visualize the shutdown process of 3DHM API/PVDF, the morphologies of the modified layer and unmodified side were imaged by SEM after heat treatment. As shown in Figure 7A1, the modified side of 3DHM API/PVDF exhibits homogeneous pores, and after heat treatment at 150 °C for 0.5 h, the morphology did not change [Figure 7B1]. With increasing heat treatment temperature from 150 to 175 °C, the PVDF partially melted and the pores in the modified side became smaller [Figure 7C1]. When the heat treatment increased to 200 °C or above, the pores disappeared and were blocked by the melted PVDF [Figure 7D1, Supplementary Figure 1]. However, the pores structure of the unmodified side remained unaltered prior to and following the heat treatment
Figure 7. The modified side and unmodified side SEM images of 3DHM API/PVDF separators before and after the thermal treatments for 30 min.
As shown in Figure 8A, the tensile strength of the PI membrane was 22.2 MPa in the vertical direction and 21.3 MPa in the transverse direction, respectively. The PVDF coating on the PI membrane elevated the tensile strength to 41.0 MPa, which would facilitate the operability of the 3DHM API/PVDF in lithium battery assembly. The porosity of PP is 62.7%, while that of 3DHM API/PVDF is 80.8% [Figure 8B], indicating an improved capacity for liquid electrolyte uptake. The PVDF coating on one side of the separator can help retain the electrolyte and promote the transport of Li+ ions. The pore size distribution of PP and 3DHM API/PVDF is presented in Supplementary Figure 2. The average PP separator pore size is 0.088 μm, which is in close proximity to the data provided by the manufacturer (0.064 μm). The pore size distribution of 3DHM API/PVDF exhibits two peaks. The first peak, at 100 nm, corresponds to the modification layer. The value is smaller than the particle size of the silica template (300 nm), which may be attributed to the presence of multilayer stacking. However, if the PVDF coating is very thin, it may be possible to detect pores of 300 nm. The 1 μm pore in 3DHM API/PVDF is derived from the PI membrane. Sufficient electrolyte wetting in LIBs has been pointed out as a critical factor, which helps to maintain its endurance and facilitates smooth diffusion[34]. The contact angle was used to characterize the wettability of the separator in the electrolyte. The height between the needle points of the dropper and the separator was ~2 mm. The angle was measured and recorded as soon as the electrolyte contacts the separator interface. Figure 8C-E shows that the contact angles of PP and PP/PE/PP are 46° and 49°, respectively, while that of 3DHM API/PVDF is 24°. It can be concluded that the electrolyte is more easily absorbed by the 3DHM API/PVDF membrane than by the PP separator. The outstanding affinity of the PVDF polymer for electrolyte solutions makes this possible, which is inherent to the material[35]. The contact angle significantly decreases to 12° for the PI film [Figure 8F], indicating the increase in the wettability of the base film with the electrolyte. Therefore, the 3DHM API/PVDF membrane exhibits good wettability, which accelerates the infiltration of electrolyte.
Figure 8. Stress-strain curves (A) and porosity (B) of PP and 3DHM API/PVDF. Contact angle for PP, PP/PE/PP separator, 3DHM API/PVDF membrane and PI film. (C) PP separator, (D) PP/PE/PP separator, (E) 3DHM API/PVDF membrane and (F) PI film.
As shown in Figure 9A, the electrolyte uptake of 3DHM API/PVDF is 494%, whereas that of PP is only 320%. Figure 9B illustrates the impedance spectra of batteries utilizing PP and 3DHM API/PVDF, respectively. The ionic conductivity of PP and 3DHM API/PVDF is 0.65 and 0.68 mS cm-1, respectively [Figure 9C]. It is evident that 3DHM API/PVDF exhibits enhanced ionic conductivity compared to PP, attributed to its superior wetting performance and enhanced Li+ ion transport. The change in impedances and ionic conductivity at different elevated temperatures clearly reflect the temperature-responsive behavior of the separators. Figure 9D and E illustrates the impedance of the PP and 3DHM API/PVDF across a temperature range of 60 to 200 °C. As displayed in Figure 9D, the blank PP separator exhibits a Z’ value of 55.1 Ω at 60 °C, which is slightly diminished to 34.7 Ω at 90 °C. The viscosity reduction of the liquid electrolyte at elevated temperatures can be attributed to this phenomenon. Further increases in temperature to 120 °C result in an internal short circuit in the cell, potentially attributable to thermal shrinkage of the PP. This finding is consistent with the results of thermal stability testing. As displayed in Figure 9E, the 3DHM API/PVDF separator exhibits a Z’ value of 6.45 Ω at 60 °C, followed by a gradual decline to 4.0, 1.73, and 1.72 Ω at 90, 120, and 150 °C, respectively. The lower impedance value indicates that the 3DHM API/PVDF has superior compatibility with the liquid electrolyte than PP. However, the Z’ value increases to 25.8 Ω at 175 °C, possibly due to the melting of PVDF and the shutdown function of the separator. This value further increases to 26.8 Ω at 200 °C due to the further shutdown of the pores. Figure 9F summarizes the ionic conductivity of PP and 3DHM API/PVDF at high temperatures. The cell assembled with 3DHM API/PVDF did not exhibit any internal short circuits during the test temperature, which can be attributed to the excellent thermal stability of 3DHM API/PVDF.
Figure 9. (A) Electrolyte uptake of PP and 3DHM API/PVDF. Impedance spectra (B) and ionic conductivity (C) of PP and 3DHM API/PVDF at 25 °C. (D) Impedance spectra of PP separator at 60 to 120 °C (Inset is an enlarged view). (E) Impedance spectra of 3DHM API/PVDF separator at 60 to 200 °C (Inset is an enlarged view). (F) Temperature-dependence ionic conductivity of PP and 3DHM API/PVDF.
The dendrite-suppressing capability of separators was tested in Li symmetric cells at a current density of
Figure 10. Cycle performance of Li symmetric cells using 3DHM API/PVDF and PP with a current density of 0.2 mA cm-2 (A) and
Figure 11. The different transmission routes of lithium ions and the thermal response characteristics of the PP and 3DHM API/PVDF.
A comparative investigation was conducted on the cycling and rate performance of the NCA/Li coin cell with 3DHM API/PVDF or PP separators. The objective of this investigation was to evaluate the effects of the modified separator on the electrochemical performance of the cells. As can be seen in Figure 12, the first discharge capacity of the 3DHM API/PVDF separator-based battery is ~172 mA hg-1 at the current density of 0.1 C, which is comparable with a PP membrane [Figure 12A and B]. The 3DHM API/PVDF separators show higher cycling stability than PP separators displayed in Figure 12C with a discharge capacity of
Figure 12. The electrochemical performance of the NCA/separator/Li battery with a 3DHM API/PVDF separator and a PP membrane at 25 °C. The charge-discharge curves of batteries with (A) 3DHM API/PVDF separator and (B) PP membrane at rates of 0.1 and 2 C. (C) the cycle performance and (D) the rate performance of the battery.
PVDF-HFP is another extensively studied polymer for LIBs due to its special porous and semicrystalline structure[38]. To preliminarily test the general applicability of the design, PVDF was replaced by PVDF-HFP, and 3DHM API/PVDF-HFP was obtained. As shown in Supplementary Figures 4 and 5, the morphologies and structures of API/PVDF-HFP-SiO2 and 3DHM API/PVDF-HFP are similar to API/PVDF-SiO2 and 3DHM API/PVDF. The melting temperature of 3DHM API/PVDF-HFP was 135 °C, and after the thermal treatment at 150 °C for 0.5 h, the modified layer had already melted [Supplementary Figures 6-10]. The NCA/3DHM API/PVDF-HFP separator /Li battery has also been assembled. The first discharge capacity of the cell is approximately 182 mA hg-1 at a current density of 0.1 C [Supplementary Figure 11]. The 3DHM API/PVDF-HFP separator also shows high cycling stability.
CONCLUSIONS
In summary, we prepared 3DHM API/PVDF separators. The 3DHM structure can ensure high-speed ion conductivity and homogeneous Li dispersion and suppress the dendrite growth. The incorporation of a PVDF layer imbues the separator with a thermal shutdown function at 175 °C, resulting from the material's melting and formation of a pore-free film. This thermal stability is evidenced by the membrane's lack of discernible shrinkage even at 275 °C, with the temperature differential between the shutdown and meltdown temperatures exceeding 100 °C to safeguard the safe utilization of LIBs. This work presents a strategy that combines a 3DHM structure, a functional polymeric coating, and a thermal stable membrane to prepare the separator compatible with high-security LIBs with a thermal shutdown function. The novel 3DHM API/PVDF separator may be a promising candidate for a safer LIB.
DECLARATIONS
Authors’ contributions
Research design and funding acquisition: Jin Y
Writing-original draft: Chang H
Data collection and experiment: Zhang Z, Chang H, Kang G
Data collection and analysis: Zhang Z, Chang H, Kang G
Review and editing: Jin Y, Zhang Z, Liu W
Refining the ideas and finalizing this paper: Jin Y, Zhang Z, Chang H
Availability of data and materials
The data are made available upon request to authors.
Financial support and sponsorship
This work was financially supported by the National Natural Science Foundation of China (52172245), the Key Scientific and Technological Innovation Project of Shandong (No. 2020CXGC010401), and the Major Basic Research Projects of the Shandong Natural Science Foundation (No. ZR2020ZD07).
Conflicts of interest
All authors declared that there are no conflicts of interest.
Ethical approval and consent to participate
Not applicable.
Consent for publication
Not applicable.
Copyright
© The Author(s) 2024.
Supplementary Materials
REFERENCES
1. Scrosati B, Garche J. Lithium batteries: status, prospects and future. J Power Sources 2010;195:2419-30.
2. Tian X, Yi Y, Fang B, et al. Design strategies of safe electrolytes for preventing thermal runaway in lithium ion batteries. Chem Mater 2020;32:9821-48.
3. Cho T, Tanaka M, Ohnishi H, et al. Composite nonwoven separator for lithium-ion battery: development and characterization. J Power Sources 2010;195:4272-7.
4. Kim M, Park JH. Inorganic thin layer coated porous separator with high thermal stability for safety reinforced Li-ion battery. J Power Sources 2012;212:22-7.
5. Cheng XB, Zhang R, Zhao CZ, Wei F, Zhang JG, Zhang Q. A review of solid electrolyte interphases on lithium metal anode. Adv Sci 2016;3:1500213.
6. Zheng G, Lee SW, Liang Z, et al. Interconnected hollow carbon nanospheres for stable lithium metal anodes. Nat Nanotechnol 2014;9:618-23.
7. Ma F, Zhang Z, Yan W, et al. Solid polymer electrolyte based on polymerized ionic liquid for high performance all-solid-state lithium-ion batteries. ACS Sustain Chem Eng 2019;7:4675-83.
8. Chen D, Liu T, Zhou X, Tjiu WC, Hou H. Electrospinning fabrication of high strength and toughness polyimide nanofiber membranes containing multiwalled carbon nanotubes. J Phys Chem B 2009;113:9741-8.
9. Dong G, Sun G, Tian G, Qi S, Wu D. Robust polyimide nanofibrous membrane with bonding microstructures fabricated via dipping process for lithium-ion battery separators. Energy Technol 2019;7:1801072.
10. Dong G, Liu B, Sun G, Tian G, Qi S, Wu D. TiO2 nanoshell@polyimide nanofiber membrane prepared via a surface-alkaline-etching and in-situ complexation-hydrolysis strategy for advanced and safe LIB separator. J Membr Sci 2019;577:249-57.
11. Dong G, Dong N, Liu B, Tian G, Qi S, Wu D. Ultrathin inorganic-nanoshell encapsulation: TiO2 coated polyimide nanofiber membrane enabled by layer-by-layer deposition for advanced and safe high-power LIB separator. J Membr Sci 2020;601:117884.
12. Elia GA, Ducros JB, Sotta D, et al. Polyacrylonitrile separator for high-performance aluminum batteries with improved interface stability. ACS Appl Mater Interfaces 2017;9:38381-9.
13. Liu J, Liu Y, Yang W, Ren Q, Li F, Huang Z. Lithium ion battery separator with high performance and high safety enabled by tri-layered SiO2@PI/m-PE/SiO2@PI nanofiber composite membrane. J Power Sources 2018;396:265-75.
14. Shi C, Dai J, Shen X, et al. A high-temperature stable ceramic-coated separator prepared with polyimide binder/Al2O3 particles for lithium-ion batteries. J Membr Sci 2016;517:91-9.
15. Zhu C, Nagaishi T, Shi J, et al. Enhanced wettability and thermal stability of a novel polyethylene terephthalate-based poly(vinylidene fluoride) nanofiber hybrid membrane for the separator of lithium-ion batteries. ACS Appl Mater Interfaces 2017;9:26400-6.
16. Battery properties of Li-ion battery with non-woven fabric separators. The 51th Battery Symposium in Japan, Nagoya 2010, 1b25.
17. Nishikawa S. Characterization of aramid coated fine porous pe separator. The 47th Battery Symposium in Japan, Tokyo 2006, 2e06.
18. Jung YS, Cavanagh AS, Gedvilas L, et al. Improved functionality of lithium-ion batteries enabled by atomic layer deposition on the porous microstructure of polymer separators and coating electrodes. Adv Energy Mater 2012;2:1022-7.
19. Jiang W, Liu Z, Kong Q, et al. A high temperature operating nanofibrous polyimide separator in Li-ion battery. Solid State Ion 2013;232:44-8.
20. Sun G, Liu B, Niu H, et al. In situ welding: superb strength, good wettability and fire resistance tri-layer separator with shutdown function for high-safety lithium ion battery. J Membr Sci 2020;595:117509.
21. Tan J, Kong L, Qiu Z, Yan Y. Flexible, high-wettability and thermostable separator based on fluorinated polyimide for lithium-ion battery. J Solid State Electrochem 2018;22:3363-73.
22. Wu D, Shi C, Huang S, et al. Electrospun nanofibers for sandwiched polyimide/poly (vinylidene fluoride)/polyimide separators with the thermal shutdown function. Electrochim Acta 2015;176:727-34.
23. Zhang H, Lin C, Zhou M, John AE, Zhu B. High thermal resistance polyimide separators prepared via soluble precusor and non-solvent induced phase separation process for lithium ion batteries. Electrochim Acta 2016;187:125-33.
24. Lu Z, Sui F, Miao Y, et al. Polyimide separators for rechargeable batteries. J Energy Chem 2021;58:170-97.
25. Zhang C, Li H, Wang S, et al. A polyethylene microsphere-coated separator with rapid thermal shutdown function for lithium-ion batteries. J Energy Chem 2020;44:33-40.
26. Wang B, Prinsen P, Wang H, et al. Macroporous materials: microfluidic fabrication, functionalization and applications. Chem Soc Rev 2017;46:855-914.
27. Ma D, Cao Z, Wang H, Huang X, Wang L, Zhang X. Three-dimensionally ordered macroporous FeF3 and its in situ homogenous polymerization coating for high energy and power density lithium ion batteries. Energy Environ Sci 2012;5:8538-42.
28. Hatton B, Mishchenko L, Davis S, Sandhage KH, Aizenberg J. Assembly of large-area, highly ordered, crack-free inverse opal films. Proc Natl Acad Sci USA 2010;107:10354-9.
29. Phillips KR, England GT, Sunny S, et al. A colloidoscope of colloid-based porous materials and their uses. Chem Soc Rev 2016;45:281-322.
30. Stein A, Wilson BE, Rudisill SG. Design and functionality of colloidal-crystal-templated materials-chemical applications of inverse opals. Chem Soc Rev 2013;42:2763-803.
31. Lee H, Yanilmaz M, Toprakci O, Fu K, Zhang X. A review of recent developments in membrane separators for rechargeable lithium-ion batteries. Energy Environ Sci 2014;7:3857-86.
32. Laman FC, Gee MA, Denovan J. Impedance studies for separators in rechargeable lithium batteries. J Electrochem Soc 1993;140:L51-3.
33. Abraham K. Directions in secondary lithium battery research and development. Electrochim Acta 1993;38:1233-48.
34. Zhang SS. A review on the separators of liquid electrolyte Li-ion batteries. J Power Sources 2007;164:351-64.
35. Wu D, Huang S, Xu Z, et al. Polyethylene terephthalate/poly (vinylidene fluoride) composite separator for Li-ion battery. J Phys D Appl Phys 2015;48:285305.
36. Cheng XB, Peng HJ, Huang JQ, Zhang R, Zhao CZ, Zhang Q. Dual-phase lithium metal anode containing a polysulfide-induced solid electrolyte interphase and nanostructured graphene framework for lithium-sulfur batteries. ACS Nano 2015;9:6373-82.
37. Ju Z, Nai J, Wang Y, et al. Biomacromolecules enabled dendrite-free lithium metal battery and its origin revealed by cryo-electron microscopy. Nat Commun 2020;11:488.
Cite This Article
Export citation file: BibTeX | EndNote | RIS
OAE Style
Chang H, Kang G, Zhang Z, Liu W, Jin Y. Evaluation of asymmetric poly(vinylidene fluoride)-coated polyimide separator with three-dimensionally homogeneous microporous structure for high-safety lithium-ion battery. Energy Mater 2024;4:400052. http://dx.doi.org/10.20517/energymater.2023.143
AMA Style
Chang H, Kang G, Zhang Z, Liu W, Jin Y. Evaluation of asymmetric poly(vinylidene fluoride)-coated polyimide separator with three-dimensionally homogeneous microporous structure for high-safety lithium-ion battery. Energy Materials. 2024; 4(5): 400052. http://dx.doi.org/10.20517/energymater.2023.143
Chicago/Turabian Style
Hui Chang, Guohong Kang, Zengqi Zhang, Wei Liu, Yongcheng Jin. 2024. "Evaluation of asymmetric poly(vinylidene fluoride)-coated polyimide separator with three-dimensionally homogeneous microporous structure for high-safety lithium-ion battery" Energy Materials. 4, no.5: 400052. http://dx.doi.org/10.20517/energymater.2023.143
ACS Style
Chang, H.; Kang G.; Zhang Z.; Liu W.; Jin Y. Evaluation of asymmetric poly(vinylidene fluoride)-coated polyimide separator with three-dimensionally homogeneous microporous structure for high-safety lithium-ion battery. Energy Mater. 2024, 4, 400052. http://dx.doi.org/10.20517/energymater.2023.143
About This Article
Special Issue
Copyright
Data & Comments
Data
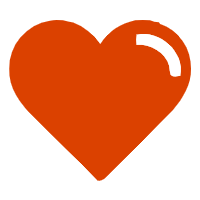
Comments
Comments must be written in English. Spam, offensive content, impersonation, and private information will not be permitted. If any comment is reported and identified as inappropriate content by OAE staff, the comment will be removed without notice. If you have any queries or need any help, please contact us at support@oaepublish.com.