From touching to seeing: visualized pressure sensing in electronic skins
Abstract
Electronic skins (e-skins) are desired to perceive both the intensity and spatial distribution of applied pressures. Despite the continuous progress in the design of high-performance individual pressure sensors, the acquisition of the locational information of pressures still mostly relies on the preparation of high-density sensor matrixes within e-skins, which dramatically increases device complexity and hinders the straightforward human-machine interaction. In recent years, the integration of optical pressure visualization units within e-skins has been raised as an alternative strategy for obtaining pressure distribution. By utilizing pressure-induced light emission and color change, the applied pressure could be visualized directly through the distinct optical signals, eliminating the necessity of additional data processing and display modules. In this perspective, the main strategies to achieve pressure visualization in e-skins are introduced, including their mechanism, device layout, materials, and applications. The challenges and prospects of this emerging field are also discussed.
Keywords
INTRODUCTION
Human skin can perceive tactile stimuli by both their intensity and spatial position[1]. For electronic skins (e-skins) mimicking the structure and functionality of natural skin, the tactile perception function could be achieved through the design of pressure sensors. Over the years, the pressure sensing performance of e-skins, including sensitivity, operational range, detection limit, etc., has been dramatically improved through the innovation of novel materials and structures[2-6]. On the other hand, the spatial distribution of pressures is usually obtained by constructing a sensor matrix within e-skins[7,8]. Despite the progress of micro/nanofabrication technologies and advanced backend data processing modules for device fabrication and integration, the preparation of a high-density sensor matrix is usually laborious and costly, and the reliance of data processing and display modules compromises the flexibility and portability of e-skins. The growing demand for flexible, lightweight, and miniaturized electronics has motivated efforts to pursue alternative solutions for pressure mapping acquisition. Thereinto, the integration of optical pressure visualization units within e-skins not only provides intuitive, real-time feedback toward tactile stimuli, but also eliminates the need for additional data interpretation devices and electronic displays, which opens new avenues for the applications of e-skins in resource-constrained environments[9,10].
The concept of pressure visualization stems from a broader need for a straightforward haptic perception and a user-friendly human-machine interface[11]. The commercial touch screen can visualize pressures sensitively, vividly and in high spatial resolution. However, the silicon-based integrated circuit technology is not compatible with e-skin fabrication. Pressure visualization could be achieved through pressure-induced light emission and color change [Figure 1][10]. Regarding the former, stress-photon transduction could directly induce mechanoluminescence[12,13]. Besides, the piezoelectric charges could regulate the structure of a heterojunction, and thus tailor the electroluminescent intensity and wavelength of optoelectronic nanodevices[14,15]. On the other hand, pressure-induced color change could be achieved by combining electrical pressure sensing and electrochromic units[16], and utilizing the structural color change of certain materials and structures[17]. In this perspective, the principles, representative materials, and applications of the four pressure visualization strategies will be introduced, respectively.
Figure 1. Four general strategies to achieve pressure visualization in e-skins, including mechanoluminescence[13]. Reprinted with permission, Copyright 2022, Elsevier; piezophototronics[15]. Reprinted with permission, Copyright 2013, Springer Nature; pressure-controlled electrochromism[16]. Reprinted with permission, Copyright 2021, ACS; and structural color[17]. Reprinted with permission, Copyright 2022, Springer Nature.
PRESSURE VISUALIZATION THROUGH MECHANOLUMINESCENCE
Mechanoluminescent materials can convert applied stress into light emission without electrical or optical input. When charges are generated through pressure-induced local fractures, triboelectric effects, or deformation-induced release of trapped charges transitioning from the excited state to the ground state, photons could be emitted by the energy released during these processes[18]. The mechanoluminescent materials are generally composed of a crystalline framework serving as the host and heavy metal ions as the doping activators. By selecting different types of hosts and dopants, the luminescent color, duration and stress threshold could be tailored [Figure 2A and B][19]. In addition, mechanoluminescent materials could be endowed with stretchability and processability when incorporated into elastomeric matrices[20].
Figure 2. Pressure visualization through mechanoluminescence. (A) Mechanolumine- scent spectra of SrZnSO doped with different ions; (B) Photographs of the handwritten Chinese characters on SrZnSO doped with different ions[19]. Reprinted with permission, Copyright 2020, Elsevier; (C) The design and chemical structures of the mechanoluminescent material with isostructural doping; (D) The persistent mechanoluminescence performance of the material within 0.4 s[26]. Reprinted with permission, Copyright 2024, Springer Nature.
Optical pressure sensing based on mechanoluminescent systems has been studied for more than 20 years[21], with the sensitivity, linearity, and response time greatly improved with time. Since mechanoluminescence is a spatially localized process, it could be applied for mapping the spatial distribution of pressures. However, mechanoluminescence is a transient process (mostly in nanosecond range)[22,23], which poses a great challenge for signal collection. In recent years, efforts have been devoted to extending the afterglow time in mechanoluminescence. For inorganic systems, trap engineering by co-doping hetero-ions has been widely adopted[24,25], which slows down the annihilation of generated photons. Besides, various organic systems with persistent mechanoluminescence have been developed. Representatively, Xie et al. raised an isostructural doping strategy to suppress non-radiative transitions, and encouraged the spin-orbital coupling within the system [Figure 2C]. An ultralong mechanoluminescent lifetime (up to 384.1 ms) was achieved [Figure 2D][26]. Except for pressure mapping, the mechanoluminescent system was also applied for collision warning[25], anti-counterfeiting[24] and structural health monitoring[27]. Despite these advancements, the capture and recording of mechanoluminescence still relies on high-speed camaras, rather than naked eyes. Besides, mechanoluminescent pressure sensing usually suffers from high detection limit (kPa level) and low signal-to-noise ratios.
PRESSURE-TAILORED ELECTROLUMINESCENCE IN OPTOELECTRONIC DEVICES
Electroluminescent light emission relies on the recombination of electrons and holes at a heterojunction, including a Schottky barrier or p-n junction, when an electric field is applied[28,29]. When piezoelectric materials are introduced to build the optoelectronic system, pressure-induced piezoelectric potential could be superimposed to the bandgap at the heterojunction, and the light emission property could be tailored[14]. In 2013, Pan et al. raised the concept of piezophototronics by developing a light-emitting diode (LED) matrix based on the heterojunction between a piezoelectric n-ZnO nanowire array and the p-GaN film. A compressive strain of 0.15% enhances the light emission intensity by ~400%. Additionally, an ultrahigh spatial resolution of ~2.7 μm (6,350 dpi) and fast response time of 180 ms for pressure mapping were achieved[15]. Since then, a series of piezophototronic LED matrixes were prepared, including InGaN/GaN quantum wells [Figure 3A and B][30], n-ZnO/poly(3,4-ethylenedioxythiophene):poly(styrenesulfonic acid) (PEDOT:PSS) hybrids[31], n-ZnO/p-Si heterojunctions[32], ZnO/3-(4-biphenyl)-4-phenyl-5-tert-butylphenyl-1,2,4-triazole (TAZ) heterostructures[33], etc., with improved spatial resolution, contrast ratio, and device integration. Despite the progress, the panel size for the piezophototronic LED matrixes is usually small (several hundreds of μm), posing great challenges in large-area pressure mapping.
Figure 3. Pressure visualization through piezophototronic electroluminescence. (A) Device layout of a piezophototronic pressure mapping visualization system; (B) Pixelated display of pressure distribution with increased pressure[30]. Reprinted with permission, Copyright 2015, ACS; (C) The mechanism of the refractive index change due to the piezoelectric polarization effect; (D) The laser emission spectra of the CdS nanobelt upon different strains; (E) The relationship between emission wavelength and the change of effective reflection index caused by piezoelectric polarization effect[34]. Reprinted with permission, Copyright 2019, ACS.
Piezophototronic pressure sensing could also be achieved by stress-induced modulation of the lasing spectra of a piezophototronic device. Ma et al. achieved a strain-induced refractive index change utilizing the piezoelectric polarization of the [001] orientation of the CdS nanobelts [Figure 3C]. A redshift of 2.9 nm in lasing spectra occurs at a strain of 0.41% [Figure 3D and E][34]. Peng et al. tailored the whispering gallery lasing mode of GaN microwires and achieved a reliable linear relationship between wavelength variation and applied strain[35]. Yin et al. developed a dual-wavelength InGaN/GaN multiple quantum wall. The ratio of the two emission peaks could be modulated by a tensile strain, resulting in a color change from light blue to turquoise[36]. Despite these advances, the piezophototronic wavelength change is limited, which usually relies on spectrometers for data acquisition. There are also attempts to regulate the photoluminescent spectra of quantum dots through pressure-induced dimension change[37,38], while the ultrahigh activation stress (in GPa level) and the difficulty in device integration hinder its application in e-skins.
PRESSURE VISUALIZATION THROUGH PRESSURE-CONTROLLED ELECTROCHROMISM
Electrochromism is a phenomenon in which the color or transparency of certain materials could be tailored by electric field-triggered redox reactions[39]. By integrating electrochromic units into an electrical pressure sensing system, the color-shifting behavior of electrochromic materials could be regulated through the pressure-induced variation of the electrical field[40,41]. Early attempts in this field relied on the series connection of piezoresistive pressure sensing and electrochromic units. The pressure-derived resistance variation of the sensor tailors the voltage division within the circuit, and the color of the electrochromic material is adjusted accordingly. In 2015, Chou et al. raised this pressure visualization strategy and achieved a continuous color regulation from dark red to pale blue (with a wavelength change of 260 nm) within a pressure range of 0-200 kPa [Figure 4A-C][42]. Kim et al. integrated a strain sensor and four electrochromic patches within an Arduino circuit. Upon adherence to human skin, the device could characterize the skin deformation visually in a stepwise manner[43]. Yue et al. integrated the pressure sensing and electrochromic module within a multi-layer structure, by which the applied pressure could be visualized on the same patch[44]. Bi et al. achieved self-powered pressure visualization by integrating a triboelectric nanogenerator and an electrochromic device[45]. Despite the distinct optical contrast, pressure visualization through the above-mentioned circuit design is based on the holistic color shifting of the electrochromic patch, and the spatial mapping of applied pressure cannot be realized.
Figure 4. Pressure visualization through pressure-controlled electrochromism. (A) The schematic layout, circuit layout and photos of a pressure sensor integrated electrochromic device; (B) The absorption spectra of the device with increased pressure; (C) The color variation of the electrochromic device when different handshake forces were applied[42]. Reprinted with permission, Copyright 2015, Springer Nature; (D) The schematic illustration (left) and working mechanism (right) of iontronic pressure visualization device; (E) The visualization and erasing process of the trace of dynamic forces[46]. Reprinted with permission, Copyright 2024, ACS.
Recently, a novel strategy for pressure mapping visualization utilizing pressure-controlled electrochromism has been raised. By sandwiching the electrochromic film between the electrode layer and the ionic gel of an iontronic pressure sensor, the electrochromic color shift could be achieved through pressure-controlled regulation of the interfacial charge transfer at the iontronic interface [Figure 4D]. Since the electrochromic color shift can be maintained for several hours or even days, the visible pressure mapping information could be more easily recorded and analyzed[46,47]. In addition, the pressure-derived coloration could be erased by inverting the applied voltage, rendering repeatable use of the device [Figure 4E].
PRESSURE VISUALIZATION UTILIZING STRUCTURAL COLOR CHANGE
Compared with electroluminescence and electrochromism which rely on external power supply, pressure visualization through deformation-controlled structural color change (mechanochromism) is dramatically energy-saving without the need of electrical wiring[48]. The structural colors of certain materials and structures stem from their periodic micro/nanostructures, with their size comparable to the wavelength of visible light[49,50]. Upon deformation, the critical size of these micro/nanostructures was changed, rendering color variation[51,52]. Photonic crystals are a kind of smart material with periodic arrangements of multiple substances with different refractive indices[53]. Wang et al. prepared a mechanochromic system based on a photonic crystal self-assembled by three chiral liquid crystal phases [Figure 5A]. A full-spectra color regulation was achieved when the strain increased from 0% to 90% [Figure 5B][54]. Yao et al. prepared a cephalopod-inspired mechanochromic system by dispersing liquid metal droplets into the polydimethylsiloxane (PDMS) matrix. The tensile strain could extend the droplets to a plate structure, by which the infrared (IR) reflectance changed[55]. Photonic crystals based on various types of copolymers and photo-responsive elastomers could also be applied for mechanochromic pressure visualization[56-58]. Besides, mechanochromic effects based on structural design of conventional materials are also reported. A light shutter with parallel microcracks was prepared on an Ecoflex elastomer. The size of microcracks could be tailored by applied longitudinal strain, which controls the transmittance of the underlying fluorescence. By cross-stacking two parallel crack arrays on the same substrate, the distinguishment of transverse and longitudinal strain could be achieved[59]. The construction of nanosphere or nanopillar arrays on elastomers also endows the e-skin with mechanochromic properties[60,61]. With a simple structure and distinct readout, mechanochromic e-skins have been enabled with a wide range of applications, including bio-signals sensing[62], wound healing monitoring [Figure 5C][17], structural health monitoring[63] and flexible displays[64]. Despite these advantages, pressure visualization utilizing structural color relies on external lighting for function, with the color readout greatly affected by the type, intensity and position of the light source.
Figure 5. Pressure visualization utilizing structural color. (A) Molecular structures and optical images of the three chiral liquid crystal phases to construct the photonic crystal; (B) The photographs of the photonic crystal with increased strain[54]. Reprinted with permission, Copyright 2024, Wiley-VCH; (C) Application of mechanochromic devices. Top: Bandages based on a mechanochromic device to indicate the pressure distribution on the underlying skin. Bottom: A color-shifting plaster based on a mechanochromic device[17]. Reprinted with permission, Copyright 2022, Springer Nature.
CHALLENGES AND PROSPECTS
In this perspective, we highlighted the recent developments in visualized pressure sensing on e-skins. Four general pressure visualization strategies were discussed, including their mechanisms, materials and structural design, and applications. Each pressure visualization strategy has its unique advantages and disadvantages in terms of spatial resolution, optical contrast, onset pressure, pressure mapping area, duration of optical signals, energy consumption, etc. [Table 1]. Through visualized pressure sensing, an explicit signal output is acquired, and additional data processing and display modules are no longer necessary. These traits render e-skins with greatly improved portability and interactivity, which intrigues many researchers to delve into this field in recent years.
The general traits of four types of pressure visualization strategies
Strategy | ||||
Mechano-luminescence | Piezophototronics | Pressure-controlled electrochromism | Structural color | |
Type of optical signal | Transient luminescence | Intensity/wavelength change | Color change | Color/transparency change |
Spatial resolution | ~1 mm | ~3 μm | Several mm | Several mm |
Optical contrast | Ultrahigh | Several times in intensity, or ~3 nm in wavelength | High (several hundreds of nm in wavelength) | High (several hundreds of nm in wavelength) |
Onset pressure | Several kPa | Several MPa | ~1 kPa | Hundreds of kPa |
Pressure mapping area | Large | Small (several hundred μm) | Large | Large |
Duration | Low (several μm) | Lasting | Lasting (several hours) | Lasting (several months) |
Energy consumption | Ultralow (self-power) | High | Low (constant bias) | Ultralow (self-power) |
Despite these prospects, there are still challenges in the development of e-skins with pressure visualization functionalities. In terms of pressure sensing performance, the sensitivity, detection limit, and pressure resolution of optical pressure sensors are generally inferior to electrical ones. At present, data acquisition of most optical pressure sensors still relies on external optical analyzers, which is disadvantageous to system integration. The performance of optical pressure sensors should be further improved for pressure visualization by the naked eye. Besides, the combination of electrical and optical pressure sensing could potentially provide more information of tactile input, compared to single-modal sensing. However, the information obtained by optical pressure sensors generally overlaps with electrical pressure sensors in the current design of bimodal sensors. Efforts are needed to adequately utilize the bimodal pressure sensing signals for more advanced biomedical sensing and human-machine interaction. Advanced data processing tools, such as pattern recognition and machine learning, could potentially play an important role in this respect[65-67]. Besides, the energy consumption of pressure visualization devices could be reduced by developing novel piezoelectric and triboelectric systems[68-70].
With continuous advancements, future pressure visualization devices will enable groundbreaking applications in intelligent robotics, wearable devices, and next-generation flexible displays. By fostering deeper integration and innovation in electroluminescent and electrochromic systems, these devices are poised to redefine interaction technologies and play a pivotal role in energy-efficient architectures, healthcare, and smart interfaces.
DECLARATIONS
Authors’ contributions
Original draft writing: Li, X.; Wu, Z.; Chen, Z.
Revision and supervision: Shi, J.
Availability of data and materials
Not applicable.
Financial support and sponsorship
This work was supported by the Program of the National Natural Science Foundation of China (Grant Number 22109104) and Natural Science Foundation of Top Talent of SZTU (Grant Number GDRC202101)
Conflicts of interest
All authors declared that there are no conflicts of interest.
Ethical approval and consent to participate
Not applicable.
Consent for publication
Not applicable.
Copyright
© The Author(s) 2025.
REFERENCES
1. Yang, J. C.; Mun, J.; Kwon, S. Y.; Park, S.; Bao, Z.; Park, S. Electronic skin: recent progress and future prospects for skin-attachable devices for health monitoring, robotics, and prosthetics. Adv. Mater. 2019, 31, 1904765.
2. Zhang, Y.; Yang, J.; Hou, X.; et al. Highly stable flexible pressure sensors with a quasi-homogeneous composition and interlinked interfaces. Nat. Commun. 2022, 13, 1317.
3. Yang, R.; Dutta, A.; Li, B.; et al. Iontronic pressure sensor with high sensitivity over ultra-broad linear range enabled by laser-induced gradient micro-pyramids. Nat. Commun. 2023, 14, 2907.
4. Shi, J.; Wang, L.; Dai, Z.; et al. Multiscale hierarchical design of a flexible piezoresistive pressure sensor with high sensitivity and wide linearity range. Small 2018, 14, 1800819.
5. Niu, H.; Wei, X.; Li, H.; et al. Micropyramid array bimodal electronic skin for intelligent material and surface shape perception based on capacitive sensing. Adv. Sci. 2024, 11, 2305528.
6. Sun, G.; Wang, P.; Jiang, Y.; et al. Bioinspired flexible, breathable, waterproof and self-cleaning iontronic tactile sensors for special underwater sensing applications. Nano. Energy. 2023, 110, 108367.
7. Li, Z.; Yang, J.; Zhang, Y.; et al. Ultrafast readout, crosstalk suppression iontronic array enabled by frequency-coding architecture. npj. Flex. Electron. 2024, 8, 9.
8. Li, P.; Xie, L.; Su, M.; et al. Skin-inspired large area iontronic pressure sensor with ultra-broad range and high sensitivity. Nano. Energy. 2022, 101, 107571.
9. Bi, S.; Jin, W.; Han, X.; et al. Flexible pressure visualization equipment for human-computer interaction. Mater. Today. Sustain. 2023, 21, 100318.
10. Zhao, K.; Zhao, Y.; Qian, R.; Ye, C.; Song, Y. Recent advances in interactive mechanosensory electronics with luminescence/coloration outputs for wearable applications. ACS. Mater. Lett. 2023, 5, 3093-116.
11. Gao, S.; Dai, Y.; Nathan, A. Tactile and vision perception for intelligent humanoids. Adv. Intell. Syst. 2022, 4, 2100074.
12. Chang, S.; Zhang, K.; Peng, D.; Deng, Y.; Shan, C. X.; Dong, L. Mechanoluminescent functional devices: developments, applications and prospects. Nano. Energy. 2024, 122, 109325.
13. Wang, W.; Wang, Z.; Zhang, J.; Zhou, J.; Dong, W.; Wang, Y. Contact electrification induced mechanoluminescence. Nano. Energy. 2022, 94, 106920.
14. Bao, R.; Tao, J.; Pan, C.; Wang, Z. L. Piezophototronic effect in nanosensors. Small. Sci. 2021, 1, 2000060.
15. Pan, C.; Dong, L.; Zhu, G.; et al. High-resolution electroluminescent imaging of pressure distribution using a piezoelectric nanowire LED array. Nature. Photon. 2013, 7, 752-8.
16. Yu, Z.; Cai, G.; Liu, X.; Tang, D. Pressure-based biosensor integrated with a flexible pressure sensor and an electrochromic device for visual detection. Anal. Chem. 2021, 93, 2916-25.
17. Miller, B. H.; Liu, H.; Kolle, M. Scalable optical manufacture of dynamic structural colour in stretchable materials. Nat. Mater. 2022, 21, 1014-8.
18. Zhuang, Y.; Xie, R. J. Mechanoluminescence rebrightening the prospects of stress sensing: a review. Adv. Mater. 2021, 33, e2005925.
19. Chen, C.; Zhuang, Y.; Tu, D.; Wang, X.; Pan, C.; Xie, R. J. Creating visible-to-near-infrared mechanoluminescence in mixed-anion compounds SrZn2S2O and SrZnSO. Nano. Energy. 2020, 68, 104329.
20. Wu, C.; Zeng, S.; Wang, Z.; et al. Efficient mechanoluminescent elastomers for dual-responsive anticounterfeiting device and stretching/strain sensor with multimode sensibility. Adv. Funct. Mater. 2018, 28, 1803168.
21. Xu, C.; Watanabe, T.; Akiyama, M.; Zheng, X. Direct view of stress distribution in solid by mechanoluminescence. Appl. Phys. Lett. 1999, 74, 2414-6.
22. Xie, Z.; Zhang, X.; Xiao, Y.; et al. Realizing photoswitchable mechanoluminescence in organic crystals based on photochromism. Adv. Mater. 2023, 35, e2212273.
23. Deng, H.; Yang, Z.; Li, G.; et al. Dynamic organic mechanoluminescence (ML): the roles of mechano-induced conformational isomer and energy transfer from ML to photoluminescence (PL). Chem. Eng. J. 2022, 438, 135519.
24. Zheng, T.; Luo, J.; Peng, D.; et al. Persistent photoluminescence and mechanoluminescence of a highly sensitive pressure and temperature gauge in combination with a 3D-printable optical coding platform. Adv. Sci. 2024, 11, e2408686.
25. Ma, Z.; Fang, S.; Zhou, B.; Yan, C.; Wang, Z. Trap-controlled, recoverable, and persistent mechanoluminescence for collision early-warning and mechanics displaying applications. Adv. Maters. Technol. 2025, 10, 2401079.
26. Xie, Z.; Xue, Y.; Zhang, X.; Chen, J.; Lin, Z.; Liu, B. Isostructural doping for organic persistent mechanoluminescence. Nat. Commun. 2024, 15, 3668.
27. Song, H.; Timilsina, S.; Jung, J.; Kim, T. S.; Ryu, S. Improving the sensitivity of the mechanoluminescence composite through functionalization for structural health monitoring. ACS. Appl. Mater. Interfaces. 2022, 14, 30205-15.
28. Jiang, W.; Lee, S.; Zan, G.; Zhao, K.; Park, C. Alternating current electroluminescence for human-interactive sensing displays. Adv. Mater. 2024, 36, e2304053.
29. Lee, S. W.; Cho, S. H.; Kang, H. S.; et al. Electroluminescent pressure-sensing displays. ACS. Appl. Mater. Interfaces. 2018, 10, 13757-66.
30. Peng, M.; Li, Z.; Liu, C.; et al. High-resolution dynamic pressure sensor array based on piezo-phototronic effect tuned photoluminescence imaging. ACS. Nano. 2015, 9, 3143-50.
31. Bao, R.; Wang, C.; Dong, L.; et al. Flexible and controllable piezo-phototronic pressure mapping sensor matrix by ZnO NW/p-polymer LED array. Adv. Funct. Mater. 2015, 25, 2884-91.
32. Li, X.; Liang, R.; Tao, J.; et al. Flexible light emission diode arrays made of transferred Si microwires-ZnO nanofilm with piezo-phototronic effect enhanced lighting. ACS. Nano. 2017, 11, 3883-9.
33. Sun, L.; Sun, N.; Li, T.; Jiang, C. Light emission enhancement of a ZnO/TAZ heterostructure piezo-OLED by means of a piezo-phototronic effect. ChemistrySelect 2022, 7, e202104353.
34. Ma, W.; Lu, J.; Yang, Z.; et al. Crystal-orientation-related dynamic tuning of the lasing spectra of CdS nanobelts by piezoelectric polarization. ACS. Nano. 2019, 13, 5049-57.
35. Peng, Y.; Lu, J.; Peng, D.; et al. Dynamically modulated GaN whispering gallery lasing mode for strain sensor. Adv. Funct. Mater. 2019, 29, 1905051.
36. Yin, Y.; Chen, R.; He, R.; et al. Strain visualization enabled in dual-wavelength InGaN/GaN multiple quantum wells micro-LEDs by piezo-phototronic effect. Nano. Energy. 2023, 109, 108283.
37. Li, B.; Liu, W.; Zhu, X.; et al. Pressure-dependent photoluminescence of CdSe/ZnS quantum dots: critical point of different pressure regimes. Phys. Lett. A. 2019, 383, 1483-6.
38. Mo, Y.; Feng, X.; Zhang, L.; Han, R.; Bao, R.; Pan, C. Tuning the light emission of a Si micropillar quantum dot light-emitting device array with the strain coupling effect. npg. Asia. Mater. 2022, 14, 83.
39. Gu, C.; Jia, A. B.; Zhang, Y. M.; Zhang, S. X. A. Emerging electrochromic materials and devices for future displays. Chem. Rev. 2022, 122, 14679-721.
40. Yeh, M. H.; Lin, L.; Yang, P. K.; Wang, Z. L. Motion-driven electrochromic reactions for self-powered smart window system. ACS. Nano. 2015, 9, 4757-65.
41. Guo, Y.; Yin, F.; Li, Y.; Shen, G.; Lee, J. C. Incorporating wireless strategies to wearable devices enabled by a photocurable hydrogel for monitoring pressure information. Adv. Mater. 2023, 35, 2300855.
42. Chou, H. H.; Nguyen, A.; Chortos, A.; et al. A chameleon-inspired stretchable electronic skin with interactive colour changing controlled by tactile sensing. Nat. Commun. 2015, 6, 8011.
43. Kim, D. S.; Lee, Y. H.; Kim, J. W.; Lee, H.; Jung, G.; Ha, J. S. A stretchable array of high-performance electrochromic devices for displaying skin-attached multi-sensor signals. Chem. Eng. J. 2022, 429, 132289.
44. Yue, Z.; Wang, Y.; Lin, Y.; Jia, C. Fully integrated pressure-controlled electrochromic E-skins. J. Mater. Chem. A. 2021, 9, 9134-44.
45. Bi, S.; Jin, W.; Han, X.; et al. Ultra-fast-responsivity with sharp contrast integrated flexible piezo electrochromic based tactile sensing display. Nano. Energy. 2022, 102, 107629.
46. Shao, B.; Zhang, S.; Hu, Y.; et al. Color-shifting iontronic skin for on-site, nonpixelated pressure mapping visualization. Nano. Lett. 2024, 24, 4741-8.
47. Guo, Y.; Li, H.; Li, Y.; et al. Wearable hybrid device capable of interactive perception with pressure sensing and visualization. Adv. Funct. Mater. 2022, 32, 2203585.
48. Wang, J.; Zhao, K.; Ye, C.; Song, Y. Emerging interactively stretchable electronics with optical and electrical dual-signal feedbacks based on structural color materials. Nano. Res. 2024, 17, 1837-55.
49. Frka-Petesic, B.; Parton, T. G.; Honorato-Rios, C.; et al. Structural color from cellulose nanocrystals or chitin nanocrystals: self-assembly, optics, and applications. Chem. Rev. 2023, 123, 12595-756.
50. Martusciello, M.; Lanfranchi, A.; Castellano, M.; Patrini, M.; Lova, P.; Comoretto, D. Stretchable distributed bragg reflectors as strain-responsive mechanochromic sensors. ACS. Appl. Mater. Interfaces. 2024, 16, 51384-96.
51. Clough, J. M.; Kilchoer, C.; Wilts, B. D.; Weder, C. Hierarchically structured deformation-sensing mechanochromic pigments. Adv. Sci. 2023, 10, e2206416.
52. Liu, J.; Li, W.; Yu, S.; Blanchard, S.; Lin, S. Fatigue-resistant mechanoresponsive color-changing hydrogels for vision-based tactile robots. Adv. Mater. 2024, 2407925.
53. Li, T.; Liu, G.; Kong, H.; Yang, G.; Wei, G.; Zhou, X. Recent advances in photonic crystal-based sensors. Coord. Chem. Rev. 2023, 475, 214909.
54. Wang, M.; Li, X.; Yang, H.; Yang, H. Mechanochromic 3D soft photonic crystals enabled anticounterfeiting and encryption information storage. Adv. Opt. Mater. 2025, 13, 2401934.
55. Yao, B.; Xu, X.; Han, Z.; et al. Cephalopod-inspired polymer composites with mechanically tunable infrared properties. Sci. Bull. 2023, 68, 2962-72.
56. Lyu, Q.; Li, M.; Zhang, L.; Zhu, J. Structurally-colored adhesives for sensitive, high-resolution, and non-invasive adhesion self-monitoring. Nat. Commun. 2024, 15, 8419.
57. Goni-lizoain, C.; Bonnaire, R.; Fontanier, J.; et al. Polypropylene/bis(benzoxazolyl)stilbene mechanochromic blends, an attractive feature for colorimetric strain detection. Sens. Actuat. A. Phys. 2023, 355, 114310.
58. Chen, X.; Ren, P.; Li, M.; Lyu, Q.; Zhang, L.; Zhu, J. Dynamic regulation of photoluminescence based on mechanochromic photonic elastomers. Chem. Eng. J. 2021, 426, 131259.
59. Li, J.; Yuan, Z.; Han, X.; et al. Biologically inspired stretchable, multifunctional, and 3D electronic skin by strain visualization and triboelectric pressure sensing. Small. Sci. 2022, 2, 2100083.
60. Yan, Y.; Zheng, J.; Wu, J.; et al. Bioinspired artificial photonic nanocrystal skin with high sensitivity and mechanical color change properties for camouflage and visual transmission. ACS. Appl. Nano. Mater. 2024, 7, 5329-38.
61. Zhang, Y.; Qi, Y.; Wang, R.; Cao, T.; Ma, W.; Zhang, S. Nonintrusively adjusting structural colors of sealed two-dimensional photonic crystals: immediate transformation between transparency and intense iridescence and their applications. ACS. Appl. Mater. Interfaces. 2021, 13, 13861-71.
62. Zhang, Z.; Chen, Z.; Wang, Y.; Zhao, Y. Bioinspired conductive cellulose liquid-crystal hydrogels as multifunctional electrical skins. Proc. Natl. Acad. Sci. U. S. A. 2020, 117, 18310-6.
63. Tabatabaeian, A.; Liu, S.; Harrison, P.; Schlangen, E.; Fotouhi, M. A review on self-reporting mechanochromic composites: an emerging technology for structural health monitoring. Compos. Part. A. Appl. Sci. Manuf. 2022, 163, 107236.
64. Wang, W.; Zhou, Y.; Yang, L.; et al. Flexible displays with multimode reversible switching between transparent and colorful states. Adv. Opt. Mater. 2023, 11, 2202418.
65. Niu, H.; Li, H.; Zhang, Q.; Kim, E. S.; Kim, N. Y.; Li, Y. Intuition-and-tactile bimodal sensing based on artificial-intelligence-motivated all-fabric bionic electronic skin for intelligent material perception. Small 2024, 20, 2308127.
66. Zheng, Z.; Huang, Z.; Zhang, N.; et al. Stretch-tolerant interconnects derived from silanization-assisted capping layer lamination for smart skin-attachable electronics. Mater. Today. Phys. 2024, 46, 101494.
67. Ren, X.; Wang, S.; Xiong, D.; et al. Heterogeneously assembled bionic piezoresistive sensor for spinal behavior monitoring. Chem. Eng. J. 2024, 485, 149817.
68. Feng, T.; Ling, D.; Li, C.; et al. Stretchable on-skin touchless screen sensor enabled by ionic hydrogel. Nano. Res. 2024, 17, 4462-70.
69. Li, J.; Carlos, C.; Zhou, H.; et al. Stretchable piezoelectric biocrystal thin films. Nat. Commun. 2023, 14, 6562.
Cite This Article

How to Cite
Li, X.; Wu, Z.; Chen, Z.; Shi, J. From touching to seeing: visualized pressure sensing in electronic skins. Soft Sci. 2025, 5, 16. http://dx.doi.org/10.20517/ss.2024.76
Download Citation
Export Citation File:
Type of Import
Tips on Downloading Citation
Citation Manager File Format
Type of Import
Direct Import: When the Direct Import option is selected (the default state), a dialogue box will give you the option to Save or Open the downloaded citation data. Choosing Open will either launch your citation manager or give you a choice of applications with which to use the metadata. The Save option saves the file locally for later use.
Indirect Import: When the Indirect Import option is selected, the metadata is displayed and may be copied and pasted as needed.
About This Article
Special Issue
Copyright
Data & Comments
Data
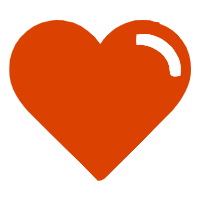
Comments
Comments must be written in English. Spam, offensive content, impersonation, and private information will not be permitted. If any comment is reported and identified as inappropriate content by OAE staff, the comment will be removed without notice. If you have any queries or need any help, please contact us at [email protected].