A scalable, robust and high-sensitivity fiber sensor for real-time body temperature monitoring
Abstract
The fibrous temperature sensor with excellent flexibility, comfort, and ease of integration into fabrics is particularly suitable for body temperature monitoring. However, the detection stability of existing fibrous temperature sensors is greatly affected by external factors such as pressing, bending, twisting, pH, humidity, and human movement. Here, we propose a fibrous temperature sensor based on an optimized scalable ionic liquid immersion process. The proposed sensor exhibited excellent temperature response characteristics, good linearity, a high sensitivity of 2.61%/°C, and can resist disturbances caused by pressing, bending, and twisting deformation. Moreover, it can work normally in acidic and alkaline environments with good reliability and stability. To demonstrate its application potential, we successfully integrated the sensor into firefighter suits, sports wristbands, and infant suits for real-time temperature monitoring and early warning.
Keywords
INTRODUCTION
With the rapid development of flexible electronic technology, wearable sensors that can monitor real-time human physiological information such as heart rate, pulse, respiration, and posture have emerged[1-10]. Among various physiological parameters, human body temperature is a significant physiological indicator widely used for assessing various diseases[11-13]; for instance, it can promptly reflect the state of a patient’s physical body during infection or inflammation[14]. For individuals working in high-temperature environments or in hot outdoor conditions, such as firefighters and athletes, monitoring body temperature can help avoid skin burns, heatstroke, and a series of physiological issues caused by excessive body temperature, such as dehydration, increased cardiac load, and damage to the liver and kidney[15,16]. Therefore, real-time and long-term monitoring of body temperature is significant.
Various wearable temperature sensors have been developed to detect the temperature changes of the human body or real-time temperature monitoring of specific parts[17-23]. Among them, fibrous temperature sensors have attracted widespread attention due to their intrinsic characteristics, including ease of integration into textiles and improved comfort and biocompatibility[24-32]. However, in human body temperature monitoring scenarios, fibrous temperature sensors are subject to stress, bending, twisting, pH, humidity, and human motion, all of which affect their detection sensitivity. Therefore, achieving fibrous temperature sensors with high stability and resistance to external disturbances remains a challenge. Even though previous research has reported that inserting the fabric in a coiled or S-shaped pattern could enhance the resistance of fibrous temperature sensors to stress and strain[33,34], this insensitivity is not an inherent characteristic of the device, and its electrical performance may still change under external impact. Moreover, even slight temperature fluctuations near physiological levels could cause severe body trauma, making high sensitivity a basic requirement for real-time body temperature monitoring.
Herein, a fibrous temperature sensor with high sensitivity, excellent reliability and stability has been developed. Continuous mass production of the sensor was realized through a scalable ionic liquid immersion process. The fibrous temperature sensor is resistant to external stress and strain, barely disturbed with bending and twisting deformation, and can operate normally in both acidic and alkaline environments, effectively meeting the demands for human body temperature monitoring in various environments. For applications in diverse scenarios, we integrated the sensor into the firefighting suits and designed a multilayer temperature sensing system to monitor both firefighters’ body and ambient temperatures. This system provides timely warnings of overheating in high-temperature and high-humidity environments. Furthermore, we incorporated the fibrous temperature sensors into sports wristbands and infant suits, enabling real-time monitoring of body temperature changes during human movement, as well as real-time monitoring and early warning of infant fever.
EXPERIMENTAL
Materials
Cotton yarns were purchased from Jiangxi Yousheng Ribbon Co., Ltd. Ecoflex was purchased from Smooth-On, Inc. The ionic liquid, 1-Ethyl-3-methylimidazolium bis (trifluoromethylsulfonyl)imide, was purchased from Shanghai Macklin Biochemical Technology Co., Ltd.
Fabrication of the fibrous temperature sensor
In the fabrication of the fibrous temperature sensor, a dual-layered approach was employed on a scalable production line to ensure the functional and protective layers were seamlessly integrated on the surface of cotton yarn. The process commenced with the ionic liquid, 1-Ethyl-3-methylimidazolium bis (trifluoromethylsulfonyl)imide, which was carefully poured into the dipping tank of the continuous production line. Subsequently, two constituents of Ecoflex, a biocompatible and flexible polymer, were thoroughly mixed and degassed in a vacuum oven for a duration of 5 min. This step was critical in eliminating air bubbles, ensuring a smooth and uniform coating. The mixture was then transferred into another dipping tank, ready for the next phase of the dip-coating process.
The cotton yarn, initially dipped into the ionic liquid, underwent a drying process through a heating tube set at a temperature of 180 °C. This high-temperature regime was pivotal in setting the foundation for the subsequent Ecoflex layer, ensuring the stability of the yarn during the encapsulation process. Following this, the partially dried fiber was immersed into the well-mixed Ecoflex solution. To refine the layer and eliminate any excess material, the fiber was guided through a micro-pinhole, precisely 0.5 mm in inner diameter. This step was instrumental in achieving a consistent and refined layer of Ecoflex. The final stage of the fabrication process involved curing and shaping the fiber within the heating tube at the same elevated temperature of 180 °C. This ensured the Ecoflex layer fully adhered to the cotton yarn, completing the encapsulation and providing the necessary protection to the sensor. Throughout this process, the fiber was meticulously moved through the scalable production line at a controlled speed of 1 meter per minute. This pace allowed for the uniform distribution of both the ionic liquid and Ecoflex, thereby enhancing the sensor’s performance and longevity.
Characterization and measurement
To establish a connection during testing, a copper wire with a diameter of 50 μm and a length of approximately 5 cm was selected to interface with the fiber core of the fibrous temperature sensor. First, the outermost Ecoflex coating of the fiber was carefully removed using a scalpel to expose the conductive core. The exposed section was then immersed in an ionic liquid until evenly impregnated, after which the conductive core was securely connected to the copper wire. The interface was sealed with ultraviolet (UV)-curing adhesive to ensure complete curing and prevent leakage of the ionic liquid. The cross-section of the fibrous temperature sensor was characterized using an optical microscope (CX40M, Shunyu Optical Technology Co., Ltd.). The electrical signals of the sensor were recorded by a multimeter (DMM6500, Tec Technology Co., Ltd.). The environments for temperature-sensing performance tests were created using an environmental test chamber (MC-800L, Min Testing Instrument and Equipment Co., Ltd). The current-voltage (I-V) curves were recorded on a source meter (2450, Oupuda Technology Co., Ltd.). The pressing and twisting performance of the fibrous temperature sensor was evaluated using a universal testing machine at an ambient temperature of 25 °C.
RESULTS AND DISCUSSION
The fibrous temperature sensor was developed using cotton yarn as the substrate due to its suitability for modification, low cost, skin-friendliness, and the ability of the ionic liquid to permeate through the gaps in the cotton fibers by capillary action, maintaining its stability. The ionic liquid, 1-ethyl-3-methylimidazolium bis (trifluoromethanesulfonyl)imide salt, was choose as the temperature sensing material and embedded into the cotton yarns through a simple and continuous dip-coating process. This liquid was renowned for its thermal stability and ionic conductivity, essential for accurate temperature sensing. It has the ability to maintain electrical conductivity under varying temperatures, allowing for the detection of temperature changes through the measurement of electrical resistance or impedance. Furthermore, to protect the ionic liquid on the surface of the cotton yarn and prevent it from falling off during use, the ionic liquid-modified cotton yarn was coated with Ecoflex, a biocompatible material suitable for encapsulating the sensor. Ecoflex was chosen for its elasticity, waterproof properties, and tear resistance, which are desirable for a wearable sensor that needs to withstand various physical stresses. The encapsulation provided by Ecoflex also plays a role in the temperature sensing mechanism by creating a stable environment that allows for the accurate detection of temperature changes without interference from external factors.
In order to facilitate the continuous and mass production of the fibrous temperature sensor, we designed and built a continuous impregnation plant [Figure 1A]. In detail, the cotton yarns were sequentially passed through dipping tanks equipped with ionic liquids and Ecoflex for the continuous production of functional and encapsulation layers. To facilitate the coating of Ecoflex and winding, a drying step was inserted after each dipping process. In addition, to ensure the even coating of Ecoflex on the fiber surface, the velocity of fibers that pass through the dipping tank was strictly controlled with the traction of the motor, and a micro-needle hole with appropriate size was introduced after dipping. The cross-sectional optical micrograph of the fibrous temperature sensor clearly demonstrated the core-shell structure that comprises a sensing core and a protective layer [Figure 1B]. Through this impregnation plant, the fibrous temperature sensors could be fabricated on a large scale with a high degree of automation [Figure 1C]. Moreover, they could be stitched and embroidered using a commercial sewing machine [Figure 1D].
Figure 1. Fabrication and structural characterization of the fibrous temperature sensor. (A) Schematic illustration of continuous fabrication of the fibrous temperature sensor; (B) Cross-sectional optical micrograph of the fibrous temperature sensor. Scale bar,
The sensing mechanism of the fibrous temperature sensor is intricately linked to the temperature-dependent conductive behavior of the ionic liquid, 1-ethyl-3-methylimidazolium bis (trifluoromethanesulfonyl) imide salt. This behavior is governed by the Vogel-Tammann-Fulcher (VTF) law, which describes the temperature dependence of the viscosity and the ionic conductivity of the liquid[35-37]. As the temperature increases, the ionic mobility within the liquid also increases due to the decreased viscosity. This enhanced mobility allows ions to move more freely, leading to an increase in conductivity. The VTF law captures this non-Arrhenius temperature dependence of conductivity, where the conductivity does not increase linearly with temperature but rather follows a more complex exponential relationship. This change in conductivity is directly measured by the sensor, providing a means to correlate resistance changes with temperature fluctuations. In order to study the electrical characteristics of the developed fibrous temperature sensors, The I-V characteristic curves of the fibrous temperature sensor at different temperatures were measured. Under a fixed voltage of 10 V, the current exhibited a increase from 0.185 μA at 0 °C to 2.526 μA at 100 °C [Figure 2A]. The resistance of fibrous sensors decreased gradually with increased temperature from 0 to 100 °C, exhibiting a notable negative temperature coefficient behavior in Figure 2B. The response time and recovery time of the fibrous temperature sensor were also investigated and measured by a conventional method. The results are shown in Figure 2C. The response time and recovery time of the sensor were calculated to be 6 and 8 s, respectively, which showed that the temperature sensor has a rapid response to temperature variations and is beneficial for real-time skin temperature monitoring. To achieve an effective measurement of human body temperature, the response curve of the fibrous temperature sensor from 25 to 40 °C was investigated in detail. The heating and cooling curves between 25 and 40 °C were measured for the fibrous temperature sensor [Figure 2D]. The results indicated that the sensor display high resilience during the heating and cooling process. As shown in Figure 2E, the fibrous temperature sensor exhibited good linearity and high sensitivity (|ΔR|/R0/ΔT = 2.61%/°C), indicating that the sensor’s resistance change is proportional to the temperature variation within the tested range of 25 to 40 °C. This linear relationship is crucial for the accurate and reliable monitoring of body temperature, as it enables the sensor to provide precise temperature readings based on the measured resistance changes. Compared to the existing fibrous temperature sensors, the temperature sensor we prepared has excellent temperature sensing performance with the highest sensitivity in temperatures ranging from 25 to 40 °C [Figure 2F and Supplementary Table 1].
Figure 2. Characterization and sensing performance of the fibrous temperature sensor. (A) I-V curves of the temperature responses of the fibrous temperature sensors from 0 to 100 °C; (B) Temperature response curve of three individual fibrous temperature sensors from 0 to 100 °C; (C) Response time of the fibrous temperature sensor; (D) Resistance change response of the fibrous temperature sensor from 25 to 40 °C when heating and cooling; (E) Linear correspondence of the value of electric resistance variation rate with temperature for the fibrous temperature sensor from 25 to 40 °C; (F) Comparison of temperature sensitivity between this work and other work reported in references[24,25,33,34,38,39].
Subsequently, the resistance of the fibrous temperature sensor to external interference, including pressing, bending, twisting, pH, and humidity, was investigated. The temperature response of the sensor was examined under a range of compressive forces from 0 to 10 N. This was done to simulate the effects of mechanical stress that the sensor might encounter in practical applications. The results showed that the fibrous temperature sensor maintains its original performance across the entire range of applied forces, demonstrating its robustness under mechanical stress [Figure 3A]. We also assess the sensor’s temperature detection capabilities under different bending angles varying from 0° to 360° at room temperature. This test was crucial to evaluate the sensor’s flexibility and durability. The evaluations confirmed that the fibrous temperature sensor can withstand severe bending without affecting its detection results, highlighting its flexibility and reliability [Figure 3B]. Moreover, the sensor was twisted to varying degrees, and its resistance was monitored throughout the process. The results show that the fibrous temperature sensor can withstand twisting without compromising its temperature-sensing capabilities [Supplementary Figure 1A]. Meanwhile, the stability of the temperature sensor under different pH levels was investigated. The results indicate that the fibrous temperature sensor could resist interference from liquids of varying acidity and alkalinity [Figure 3C]. Furthermore, the temperature measurement capability remains stable when tested at different relative humidity levels [Supplementary Figure 1B]. Even after 200 heating and cooling cycles from 25 to 40 °C, no significant degradation of performance was observed. This indicates that the sensor has excellent sensing stability and longevity, which are critical for long-term applications [Figure 3D].
Figure 3. Robust performance of the fibrous temperature sensor. (A) Dependence of temperature and resistance response on external pressing, the pressing force varied from 0 to 10 N. T0 and T correspond to the temperature measurement before and after pressing, respectively, |ΔT| = |T - T0|. Error bars are standard deviations of the results from at least three samples; (B) Dependence of temperature and resistance response on bending angle, with the bending angle varying from 0° to 360°. T0 and T correspond to the temperature measurement before and after bending respectively, |ΔT| = |T - T0|. Error bars are standard deviations of the results from at least three samples; (C) Dependence of temperature and resistance response on pH, with the pH varying from 0 to 14. T0 corresponds to the temperature measurement in pH = 7, |ΔT| = |T - T0|. Error bars are standard deviations of the results from at least three samples; (D) Temperature sensing cyclic tests of the fibrous temperature sensor from 25 to 40 °C.
To demonstrate the potential of the fibrous temperature sensor for human body temperature monitoring applications, we have incorporated the fibrous temperature sensor systems in daily textile products to provide temperature monitoring and early warning [Figure 4A]. As shown in Figure 4B, an intelligent firefighter suit was successfully constructed by integrating with a dual-layer temperature sensing structure to monitor both the environment and the wearer’s body temperature simultaneously. The system workflow of the firefighter suit and the signal amplification circuit of the fiber-based temperature sensor are shown in Supplementary Figure 2A and B. To validate the performance of this intelligent firefighter suit, a temperature-controllable electric heating plate was placed on the firefighter suit to simulate external heat sources. The specific scenario of the wearer’s entry into a high-temperature area or approach to a heat source was simulated by gradually increasing the temperature of the electric heating plate. Figure 4C exhibits the temperature changes of the heating plate during the experiment and the temperature curves of the dual-layer temperature sensing structure in the protective suit. Supplementary Figure 2C shows the alarm process of a firefighting suit. As the temperature of the electric heating plate gradually rises, the fibrous temperature sensor near the fire-resistant layer can timely perceive the changes in the external environmental temperature. When the wearer is in a high-temperature environment for an extended period and there is an abnormal increase in body temperature, the fibrous temperature sensor near the body can timely find the changes in body temperature and issue a warning [Supplementary Video 1].
Figure 4. Application scenarios of the fibrous temperature sensor. (A) Schematic illustration of potential applications of the fibrous temperature sensor. The fibrous temperature sensor systems could provide temperature monitoring and early warning in various fields, including firefighting, sports activities, and infant care; (B) Photograph of the fibrous temperature sensor integrated into the firefighting suit. The unique double-layer temperature-sensitive structure was integrated into the smart firefighting suit. Scale bar, 12 cm; (C) Temperature curves of the dual-layer temperature sensing structure in the protective suit. When the temperature of the electric heating plate rises gradually, the outer fibrous temperature sensor can sense the change of the external temperature in time. When the firefighter’s internal temperature is abnormal, it can provide a timely warning; (D) Photograph of the fibrous temperature sensor integrated into the wristband. Scale bar, 1 cm; (E) Temperature curves of the wrist when running. The subject was asked to run for
Moreover, to verify the potential of the fibrous temperature sensor as a wearable device, the temperature sensor was screwed into a wristband and worn on the wrist to monitor the body temperature changes during exercise [Figure 4D]. During the experiment, the subject was asked to run for 10 min. The body temperature was recorded with both a fibrous temperature sensor and an infrared thermometer. Figure 4E shows the temperature change of the user during the sport. From the beginning to the end of the test, the fibrous temperature sensor measured that the body temperature of the user changed by 0.8 °C, which was consistent with the measurement results of the infrared thermometer. We also constructed an infant suit with body temperature monitoring and a fever alarm using the fibrous temperature sensor. As shown in Figure 4F, we designed the following experiment using an infant model. To simulate the condition of an infant with a fever, we placed a heating unit on the model dressed in the infant suit. The temperature of the heating unit was monitored by a K-type thermocouple. Figure 4G shows the real-time temperature changes of the heating unit and the measurement curve of the fibrous temperature sensor which demonstrates the sensor’s ability to monitor the infant body temperature and trigger an alarm through the alarm lamp in case of abnormalities [Supplementary Video 2]. These experiments demonstrate that the fibrous temperature sensor integrated into the fabric can accurately monitor changes in skin surface temperature.
CONCLUSIONS
To summarize, we developed a robust and high-sensitivity fibrous temperature sensor based on a scalable ionic liquid immersion process. Due to the temperature sensitivity of the ionic liquid, the fabricated sensor exhibited excellent temperature response characteristics, good linearity, and a high sensitivity of 2.61%/°C. Simultaneously, it is insensitive to pressing, bending and twisting deformations and can work normally in acidic or alkaline environments. The sensor has good reliability and stability, enabling body temperature monitoring and early warning in complex environments such as fire rescue sites to protect the health of firefighters, human movement and judge the intensity of the exercise accordingly, and fever warnings of infants and young children. In short, the fibrous temperature sensor we proposed can be integrated into different textiles to realize body temperature monitoring in various scenarios.
DECLARATIONS
Acknowledgments
The authors would like to thank Yuwei Wang for their helpful discussion and assistance.
Authors’ contributions
Conception of the idea, experimental design, and supervision of the research project: Tao, G.
Conduct of the experiments and manufacturing and characterization of the fibers: Li, P.
Data analysis and manuscript writing: Tao, G.; Yuan, Q.; Li, P.
Contribution to the experiments and manuscript discussion: Li, P.; Zhou, J.; Cui, Y.; Ouyang, J.; Su, Z.; Zou, Y.; Liang, J.; Wang, F.; He, K.; Liu, Y.; Zeng, Z.; Fang, F.; Hou, C.; Zhou, N.; Peng, T.; Yuan, Q.; Tao, G.
Availability of data and materials
All data are available in the main text or the Supplementary Materials. Information requests should be directed to the corresponding authors.
Financial support and sponsorship
This work was supported by the National Key Research and Development Program of China (Grant No. 2022YFB3805805), the National Natural Science Foundation of China (Grant Nos. T2425018 and 62175082), the Interdisciplinary Research Program of Huazhong University of Science and Technology (Grant No. 2023JCYJ039), the Open Project Program of Wuhan National Laboratory for Optoelectronics (Grant No. 2023083), and Huazhong University of Science and Technology Double First-Class Funds for Humanities and Social Sciences (Sports Industry Research Center of Huazhong University of Science and Technology).
Conflicts of interest
All authors declared that there are no conflicts of interest.
Ethical approval and consent to participate
The study was conducted in accordance with the ethical guidelines and approved by the Medical Ethics Committee of Tongji Hospital Affiliated to Tongji Medical College of Huazhong University of Science and Technology. All participants were informed about the experimental procedure and signed the informed consent forms prior to participation.
Consent for publication
Not applicable.
Copyright
© The Author(s) 2025.
Supplementary Materials
REFERENCES
1. Sundaram, S.; Kellnhofer, P.; Li, Y.; Zhu, J. Y.; Torralba, A.; Matusik, W. Learning the signatures of the human grasp using a scalable tactile glove. Nature 2019, 569, 698-702.
2. Libanori, A.; Chen, G.; Zhao, X.; Zhou, Y.; Chen, J. Smart textiles for personalized healthcare. Nat. Electron. 2022, 5, 142-56.
3. Zhao, X.; Zhou, Y.; Xu, J.; et al. Soft fibers with magnetoelasticity for wearable electronics. Nat. Commun. 2021, 12, 6755.
4. Li, P.; Yang, M.; Liu, Y.; et al. The rise of intelligent fabric agent from mass-produced advanced fiber materials. Sci. Bull. 2024, 69, 3644-7.
5. Fan, W.; He, Q.; Meng, K.; et al. Machine-knitted washable sensor array textile for precise epidermal physiological signal monitoring. Sci. Adv. 2020, 6, eaay2840.
6. Luo, Y.; Li, Y.; Sharma, P.; et al. Learning human–environment interactions using conformal tactile textiles. Nat. Electron. 2021, 4, 193-201.
7. Kim, J.; Campbell, A. S.; de, Á. B. E.; Wang, J. Wearable biosensors for healthcare monitoring. Nat. Biotechnol. 2019, 37, 389-406.
8. Ray, T. R.; Choi, J.; Bandodkar, A. J.; et al. Bio-integrated wearable systems: a comprehensive review. Chem. Rev. 2019, 119, 5461-533.
9. Luo, L.; Wu, Z.; Ding, Q.; et al. In situ structural densification of hydrogel network and its interface with electrodes for high-performance multimodal artificial skin. ACS. Nano. 2024, 18, 15754-68.
10. Wang, W.; Yao, D.; Wang, H.; et al. A breathable, stretchable, and self-calibrated multimodal electronic skin based on hydrogel microstructures for wireless wearables. Adv. Funct. Mater. 2024, 34, 2316339.
11. Khan, Y.; Ostfeld, A. E.; Lochner, C. M.; Pierre, A.; Arias, A. C. Monitoring of vital signs with flexible and wearable medical devices. Adv. Mater. 2016, 28, 4373-95.
12. Gao, Y.; Yu, L.; Yeo, J. C.; Lim, C. T. Flexible hybrid sensors for health monitoring: materials and mechanisms to render wearability. Adv. Mater. 2020, 32, e1902133.
13. Trung, T. Q.; Lee, N. E. Flexible and stretchable physical sensor integrated platforms for wearable human-activity monitoringand personal healthcare. Adv. Mater. 2016, 28, 4338-72.
14. Beco, J.; Seidel, L.; Albert, A. Normative values of skin temperature and thermal sensory thresholds in the pudendal nerve territory. Neurourol. Urodyn. 2015, 34, 571-7.
15. Ebi, K. L.; Capon, A.; Berry, P.; et al. Hot weather and heat extremes: health risks. Lancet 2021, 398, 698-708.
16. Cheshire, W. P. J. Thermoregulatory disorders and illness related to heat and cold stress. Auton. Neurosci. 2016, 196, 91-104.
17. Liu, H.; Du, C.; Liao, L.; et al. Approaching intrinsic dynamics of MXenes hybrid hydrogel for 3D printed multimodal intelligent devices with ultrahigh superelasticity and temperature sensitivity. Nat. Commun. 2022, 13, 3420.
18. Trung, T. Q.; Ramasundaram, S.; Hwang, B. U.; Lee, N. E. An all-elastomeric transparent and stretchable temperature sensor for body-attachable wearable electronics. Adv. Mater. 2016, 28, 502-9.
19. Ren, X.; Pei, K.; Peng, B.; et al. A low-operating-power and flexible active-matrix organic-transistor temperature-sensor array. Adv. Mater. 2016, 28, 4832-8.
20. Bayindir, M.; Abouraddy, A.; Arnold, J.; Joannopoulos, J.; Fink, Y. Thermal-sensing fiber devices by multimaterial codrawing. Adv. Mater. 2006, 18, 845-9.
21. Yu, L.; Parker, S.; Xuan, H.; et al. Flexible multi-material fibers for distributed pressure and temperature sensing. Adv. Funct. Mater. 2020, 30, 1908915.
22. Su, Y.; Ma, C.; Chen, J.; et al. Printable, highly sensitive flexible temperature sensors for human body temperature monitoring: a review. Nanoscale. Res. Lett. 2020, 15, 200.
23. Li, Q.; Zhang, L. N.; Tao, X. M.; Ding, X. Review of flexible temperature sensing networks for wearable physiological monitoring. Adv. Healthc. Mater. 2017, 6, 1601371.
24. Wu, R.; Ma, L.; Hou, C.; et al. Silk composite electronic textile sensor for high space precision 2D combo temperature-pressure sensing. Small 2019, 15, e1901558.
25. Trung, T. Q.; Le, H. S.; Dang, T. M. L.; Ju, S.; Park, S. Y.; Lee, N. E. Freestanding, fiber-based, wearable temperature sensor with tunable thermal index for healthcare monitoring. Adv. Healthc. Mater. 2018, 7, e1800074.
26. Hu, X.; Tian, M.; Xu, T.; et al. Multiscale disordered porous fibers for self-sensing and self-cooling integrated smart sportswear. ACS. Nano. 2020, 14, 559-67.
27. He, H.; Liu, J.; Wang, Y.; et al. An ultralight self-powered fire alarm e-textile based on conductive aerogel fiber with repeatable temperature monitoring performance used in firefighting clothing. ACS. Nano. 2022, 16, 2953-67.
28. He, Y.; Gui, Q.; Liao, S.; Jia, H.; Wang, Y. Coiled fiber-shaped stretchable thermal sensors for wearable electronics. Adv. Mater. Technol. 2016, 1, 1600170.
29. Wang, J.; He, J.; Ma, L.; et al. Multifunctional conductive cellulose fabric with flexibility, superamphiphobicity and flame-retardancy for all-weather wearable smart electronic textiles and high-temperature warning device. Chem. Eng. J. 2020, 390, 124508.
30. Wang, Y.; Liu, J.; Zhao, Y.; et al. Temperature-triggered fire warning PEG@wood powder/carbon nanotube/calcium alginate composite aerogel and the application for firefighting clothing. Compos. Part. B. Eng. 2022, 247, 110348.
31. Wang, F.; Chen, J.; Cui, X.; Liu, X.; Chang, X.; Zhu, Y. Wearable ionogel-based fibers for strain sensors with ultrawide linear response and temperature sensors insensitive to strain. ACS. Appl. Mater. Interfaces. 2022, 14, 30268-78.
32. Zhang, Y.; Hu, Z.; Xiang, H.; Zhai, G.; Zhu, M. Fabrication of visual textile temperature indicators based on reversible thermochromic fibers. Dyes. Pigm. 2019, 162, 705-11.
33. Li, F.; Xue, H.; Lin, X.; Zhao, H.; Zhang, T. Wearable temperature sensor with high resolution for skin temperature monitoring. ACS. Appl. Mater. Interfaces. 2022, 14, 43844-52.
34. Lee, J.; Kim, D. W.; Chun, S.; et al. Intrinsically strain-insensitive, hyperelastic temperature-sensing fiber with compressed micro-wrinkles for integrated textronics. Adv. Mater. Technol. 2020, 5, 2000073.
35. Gui, Q.; He, Y.; Gao, N.; Tao, X.; Wang, Y. A skin-inspired integrated sensor for synchronous monitoring of multiparameter signals. Adv. Funct. Mater. 2017, 27, 1702050.
36. Zhang, H.; Zhang, S.; Zhang, X. Experimental discovery of magnetoresistance and its memory effect in methylimidazolium-type iron-containing ionic liquids. Chem. Mater. 2016, 28, 8710-4.
37. Sangoro, J. R.; Serghei, A.; Naumov, S.; et al. Charge transport and mass transport in imidazolium-based ionic liquids. Phys. Rev. E. 2008, 77, 051202.
38. Ge, G.; Lu, Y.; Qu, X.; et al. Muscle-inspired self-healing hydrogels for strain and temperature sensor. ACS. Nano. 2020, 14, 218-28.
Cite This Article
How to Cite
Li, P.; Zhou, J.; Cui, Y.; Ouyang, J.; Su, Z.; Zou, Y.; Liang, J.; Wang, F.; He, K.; Liu, Y.; Zeng, Z.; Fang, F.; Hou, C.; Zhou, N.; Peng, T.; Yuan, Q.; Tao, G. A scalable, robust and high-sensitivity fiber sensor for real-time body temperature monitoring. Soft Sci. 2025, 5, 13. http://dx.doi.org/10.20517/ss.2024.60
Download Citation
Export Citation File:
Type of Import
Tips on Downloading Citation
Citation Manager File Format
Type of Import
Direct Import: When the Direct Import option is selected (the default state), a dialogue box will give you the option to Save or Open the downloaded citation data. Choosing Open will either launch your citation manager or give you a choice of applications with which to use the metadata. The Save option saves the file locally for later use.
Indirect Import: When the Indirect Import option is selected, the metadata is displayed and may be copied and pasted as needed.
About This Article
Special Issue
Copyright
Data & Comments
Data
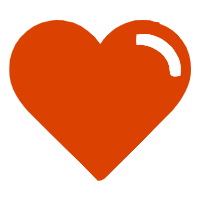
Comments
Comments must be written in English. Spam, offensive content, impersonation, and private information will not be permitted. If any comment is reported and identified as inappropriate content by OAE staff, the comment will be removed without notice. If you have any queries or need any help, please contact us at [email protected].