fig12
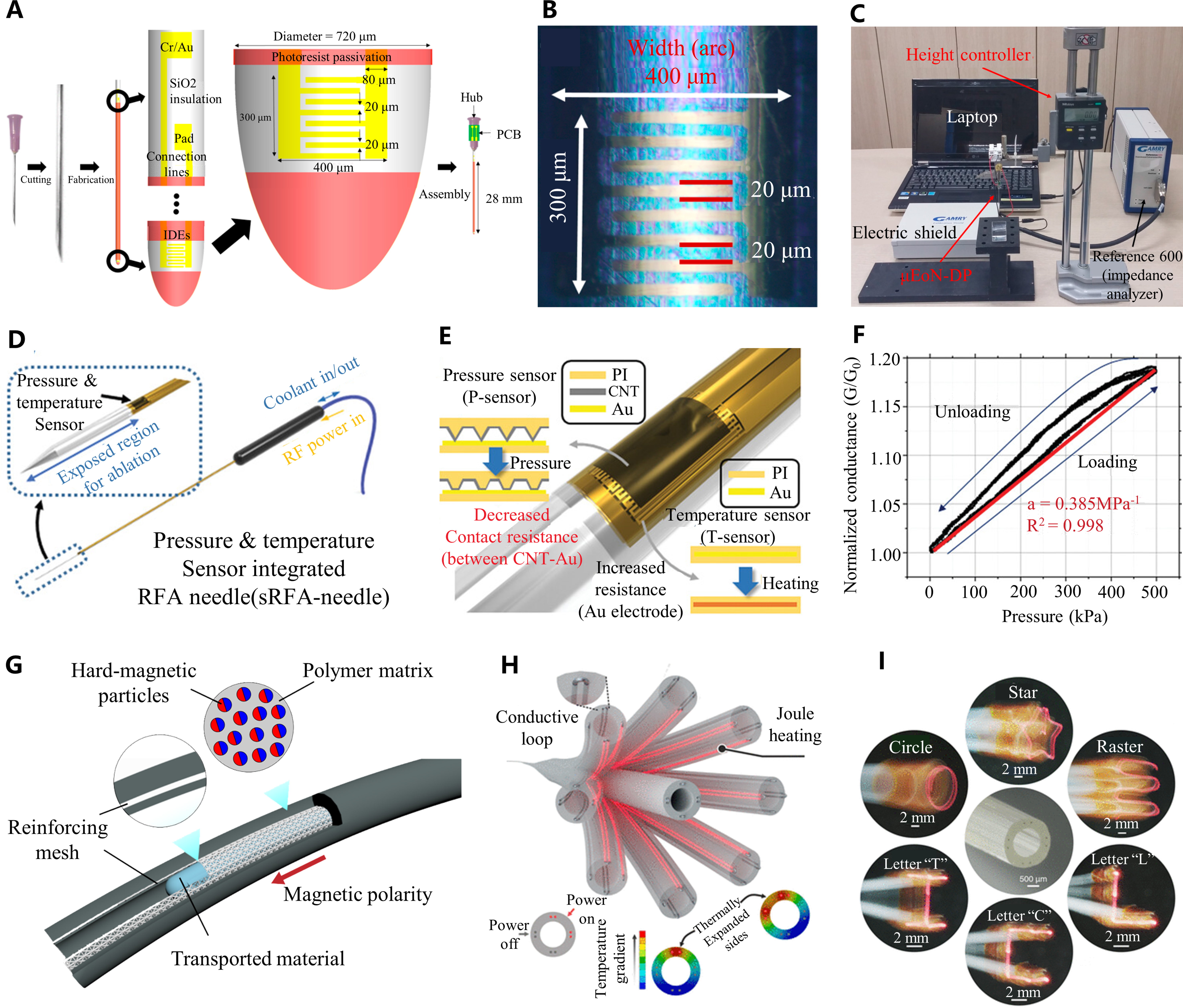
Figure 12. Principle application of micro-cylindrical sensors for surgical robots and microfiberbots. (A) Schematic design of the micro EIS-on-a-needle for depth profiling (µEoN-DP); (B) Photograph of the IDE fabricated on the curved surface of the needle; (C) Images of experimental setup. Reproduced with permission[51]. Copyright 2016, MDPI; (D) Schematic of the overall system of the sRFA-needle; (E) Schematic of the operating principles of contact resistance-based P-sensor and resistance-based T-sensor; (F) P-sensor at hydrostatic pressure. Reproduced with permission[211]. Copyright 2021, John Wiley and Sons; (G) A schematic representation of the FSCR, comprising a soft polymer matrix embedded with hard magnetic particles and reinforced with a PLA mesh. Reproduced with permission[214]. Copyright 2021, Springer Nature; (H) Schematic of fiber cantilever bending driven by thermal expansion; (I) Six tip displacement patterns captured using the slow shutter speed function of a mirrorless camera while moving a 500-μm optical fiber connected to a 650-nm LED. Reproduced with permission[112]. Copyright 2024, American Association for the Advancement of Science. EIS: Electrical impedance spectroscopy; IDE: interdigitated electrode; sFRA: sensor-integrated radiofrequency ablation; FSCR: ferromagnetic soft catheter robot; PLA: polylactide; LED: light-emitting diode.