Influence of solid waste gypsum and additives on the properties of sulfoaluminate cement-fly ash-gangue ternary binder
Abstract
With rapid economic and social development, significant amounts of coal-based and gypsum solid waste are generated daily. However, the high cost of sulfate aluminum cement has limited its widespread application. Notably, when the dosage of desulfurized gypsum reached 8%, the strength of the cementitious material at different ages approached or even exceeded that of pure sulfate aluminum cement. The sulfate aluminum cement-coal-based solid waste gypsum cementitious material prepared in this study demonstrated high compatibility with various admixtures. Specifically, when the proportions of sulfate aluminum cement, coal gangue powder, ultrafine coal ash, and desulphurization gypsum in the cementitious material were 67%, 15%, 10%, and 8%, respectively, and the dosages of the polycarboxylate water reducer, boric acid, and lithium carbonate were 0.25%, 0.25%, and 0.15%, respectively, with a water-to-binder ratio of 0.35, the strength of the cementitious material at different ages met the requirements of 425 sulfate aluminum cement. This study innovatively utilizes solid waste gypsum to enhance the strength of sulfate aluminum cement-coal-based solid waste cementitious material and employs an admixture ternary compound to enhance the performance of sulfate aluminum cement-coal-based solid waste-solid waste gypsum cementitious material. These approaches contribute to improving the utilization rate of solid waste gypsum and reducing the cost of sulfate aluminum cement.
Keywords
INTRODUCTION
With the rapid development of various industries in China, the mining and consumption of coal have increased significantly, leading to substantial amounts of coal gangue and fly ash. However, effectively treating coal-based solid waste remains a challenge. Reusing coal-based solid waste as an admixture in cement offers a promising solution. It not only reduces the environmental harm caused by coal-based solid waste but also lowers the cost of cement[1-3].
Solid-waste gypsum, mainly comprising phosphogypsum and flue gas desulfurization gypsum, is generated in chemical plants or smelters through specific processes. However, due to the considerable amount of solid gypsum waste produced during these processes, it is commonly disposed of as waste. The accumulated solid waste gypsum poses significant environmental risks by polluting water and soil. Substituting solid waste gypsum for traditional gypsum in sulfoaluminate cement (SAC) can regulate the properties and hydration products of SAC. This substitution reduces the amount of clinker, decreases the use of natural gypsum, and increases the consumption of solid waste gypsum. Consequently, it saves land and mineral resources while mitigating the environmental harm caused by solid waste gypsum[4,5].
Water-reducing agents play a crucial role in reducing the amount of water required while maintaining excellent workability and enhancing the strength and durability of cement-based materials[6]. Retarders delay the setting and hardening of cement slurry without affecting the composition and properties of the hydration products[7]. Early strength agents promote the early strength development of cement and shorten the setting time to meet the demand for external forces on cement[8].
García-Maté et al. reported that fly ash can decrease the cohesiveness of SAC but does not react with the hydration products of SAC[9]. The greater the number of voids in the structure of SAC, the lower the strength. The voids decreased with a lower water-to-binder ratio, resulting in higher strength. The water-to-binder ratio of SAC typically ranges from 0.45 to 0.65. A fly ash content below 15% had a positive effect on the binder system by reducing the porosity of the binder material. However, when the fly ash content reached 30%, the SAC was diluted, and the strength of the binder system was reduced. Huang et al. reported that soluble phosphorus can combine with aluminum ions in the hydration system of SAC, consuming aluminum ions and reducing the driving force for the precipitation of SAC[10]. It can also inhibit the hydration of SAC, prolong the setting time, reduce the early compressive strength, and result in higher expansion. The addition of calcium hydroxide and aluminum sulfate to the hydration system can neutralize the acidity of phosphogypsum and eliminate its adverse effects on SAC. Gao et al. investigated the effects of desulfurized gypsum on the properties of SAC containing ground-granulated blast furnace slag[11]. The hydration rate, setting time, mechanical strength, pore structure, and hydration products of SAC with desulfurized gypsum were examined. The results indicated that desulfurized gypsum can promote hydration and improve the mechanical strength of SAC with ground granulated blast furnace slag; however, the dosage of desulfurized gypsum should not exceed 6%. Zhang et al. reported that the hydration process of ultrafine SAC-based grout materials could be divided into acceleration, retardation, and stable periods[12]. Naphthalene-based water-reducing agents delay the acceleration and stable periods of hydration of ultrafine SAC-based grout materials while promoting the hydration of the retardation period. In comparison to naphthalene-based water-reducing agents, polycarboxylate water-reducing agents exhibited minimal impact on the hydration of the retardation period, significantly prolonging the stable hydration period.
In this study, phosphogypsum and desulfurized gypsum were utilized to adjust the properties of the SAC-coal-based solid waste binder material, with semi-hydrated gypsum used for comparison purposes. After determining the appropriate dosage of solid-waste gypsum, a tri-component combination comprising a water-reducing agent, retarder, and early strength agent was employed to further adjust the properties of the binder material. Finally, the water-to-binder ratio was fine-tuned to meet the specifications of grade 425 cement. This research offers valuable insights into the comprehensive utilization of coal-based solid waste and solid waste gypsum.
EXPERIMENTAL
Raw materials
SAC was sourced from Zibo Yunhe Cement Co., Ltd. Ultra-fine fly ash with a fineness of 1340 mesh (equivalent to 10 microns or 1250 mesh) was acquired from Qingyun Kangjing Building Materials Co., Ltd. Coalgangue powder was obtained from Lingshou Chunfang Mine Product Processing Factory. Phosphogypsum and desulfurized gypsum were procured from Hubei Zhimeitang New Materials Technology Co., Ltd. Semi-hydrated gypsum was sourced from Shandong Yousuo Chemical Technology Co., Ltd. Tap water served as the experimental water source, and the physical-mechanical properties of SAC were assessed using a water-to-binder ratio of 0.5, as outlined in Table 1. Additionally, the physical properties of the SAC-coal-based solid waste binder material, featuring a fixed content of 10% ultrafine fly ash and 15% coal gangue powder, are detailed in Table 2.
Physical properties of SAC
Compressive strength/MPa | Setting time/min | Flowability/mm | |||
1 day | 3 days | 7 days | 28 days | ||
21.6 | 23.7 | 24.8 | 31.9 | 5.9 | 164 |
Physical properties of SAC-coal-based solid waste cementitious material
Compressive strength/MPa | Setting time/min | Flowability/mm | |||
1 day | 3 days | 7 days | 28 days | ||
16.2 | 18.9 | 19.2 | 28.5 | 4.5 | 118 |
The main chemistry of SAC is shown in Table 3.
Chemical composition of SAC (%)
SiO2 | Al2O3 | CaO | SO3 | K2O | Fe2O3 |
6.472 | 14.924 | 57.096 | 18.385 | 1.001 | 1.804 |
The properties of SAC are shown in Table 4.
Basic properties of SAC
Initial setting time/min | Final setting time/min | 1 day compressive strength/MPa | 3 days compressive strength/MPa | 28 days compressive strength/MPa |
10-15 | 15-20 | 30.0 | 42.5 | 45.0 |
Based on Figure 1, it is evident that the secondary fly ash and primary fly ash utilized in this experiment possess identical compositions. However, the ultrafine fly ash employed in this study includes plagioclase feldspar and calcium carbonate. Furthermore, the coal gangue powder utilized in this experiment comprises various minerals, including kaolinite, plagioclase feldspar, muscovite, and chlorite.
Phosphogypsum and desulfurization gypsum test data are shown in Table 5.
Phosphogypsum and desulfurization gypsum test data
Test items | Phosphogypsum | Desulfurization gypsum |
0.3 mm material retained | 2.47% | 0.53% |
0.15 mm material retained | 5.35% | 1.13% |
Bulk density | 700 g/L | 759 g/L |
pH | 6~7 | 7 |
Attached water | 0.703% | 0.798% |
Soluble anhydrous gypsum | 0 | 0 |
β-hemihydrate gypsum | 75.017% | 86.535% |
Dehydrated gypsum | 10.238% | 5.997% |
Cl- | < 0.04% | |
Total phosphorus | < 0.3% | |
Soluble phosphorus | < 0.05% |
Gypsum content in mix design
To design the mix proportions with the addition of gypsum and comprehensively study its influence on the hydration performance of the SAC-coal-based solid waste binder system, a replacement ratio of 25% (15% coal gangue powder + 10% ultrafine coal ash) of SAC-coal-based solid waste binder material was selected for the experiment[13]. Three types of gypsum - semi-hydrated gypsum, phosphogypsum, and desulfurized gypsum - were used to partially replace the cement in the mix design. The gypsum content ranged from 0% to 12% in increments of 2% for each group. In total, there were 18 groups with specific mix design schemes, as listed in Table 6.
Gypsum content in the mix design
Numbered | SAC/% | Coal gangue powder/% | Ultrafine fly ash/% | Gypsum/% |
T1 | 73 | 15 | 10 | 2 |
T2 | 71 | 15 | 10 | 4 |
T3 | 69 | 15 | 10 | 6 |
T4 | 67 | 15 | 10 | 8 |
T5 | 65 | 15 | 10 | 10 |
T6 | 63 | 15 | 10 | 12 |
Admixture content in the mix design
In this experiment, the performance of the binder material was adjusted by incorporating a ternary composite comprising a water reducer, retarder, and an early strength agent. The admixture content was determined based on the solid waste gypsum content.
Experimental methods
Setting Time: Due to the nonstandard consistency of the water-to-cement ratio used in the experiment, which could yield inflated results, the slump cone test method commonly employed at construction sites was adopted.
Flowability: The flowability of the binder material was assessed using the cement paste consistency test method outlined in “Test methods for uniformity of concrete admixtures” (GB/T 8077), with a water-to-cement ratio (w/c) of 0.5.
Mechanical Performance: The binder material was cast with a water-to-cement ratio of 0.5, and its compressive strength at 1, 3, 7, and 28 days was determined according to the “Test method for strength of hydraulic cement mortar” (GB/T 17671-1999, ISO method).
Analysis of Hydration Products: X-ray diffractometry (XRD) was employed to analyze the mineral composition of the cement clinker, utilizing an X’Pert3 powder X-ray diffractometer (PANalytical, Germany) with a scanning speed of 2 (°)/min and a step size of 0.02°, covering a scan range of 0°-80°. Quantitative analysis was conducted using a refined method based on full-peak pattern analysis. Loading Powder Diffraction File (PDF) standard cards containing the respective phases, the entire spectrum was analyzed while controlling the calculated convergence scale factor (R-factor) below 15% to ensure the reliability of the results. The area ratios of the diffraction peaks corresponding to each phase above the baseline were calculated to determine the mass fraction of each phase, generating a quantitative analysis report.
RESULTS AND DISCUSSION
Influence of gypsum on the physical properties of SAC-coal-based solid waste binder material
Figure 2A illustrates that with an escalation in the semi-hydrated gypsum content, the setting time of the binder material decreases. When the semi-hydrated gypsum content increased from 0% to 12%, the setting time of the binder material decreased by 1.3 min, marking a decrease rate of 28.4%. Conversely, as the phosphogypsum content increased, the setting time initially rose and subsequently declined. Upon increasing the phosphogypsum content from 0% to 2%, the setting time of the binder material surged by
Figure 2. Effect of gypsum on setting time and fluidity of SAC-coal-based solid waste cementitious materials. SAC: Sulfoaluminate cement.
Figure 2B depicts that with a rise in the semi-hydrated gypsum content, the flowability of the binder material declines. Upon increasing the semi-hydrated gypsum content from 0% to 12%, the flowability of the binder material diminishes by 40 mm, reflecting a decrease rate of 33.9%. Similarly, as the phosphogypsum content increases, the flowability of the binder material initially ascends and subsequently descends. Elevating the phosphogypsum content from 0% to 2% leads to a flowability augmentation of
The primary constituent of hemihydrate gypsum is CaSO4·0.5H2O. Therefore, desulfurization gypsum can also undergo a reaction with water. Specifically, 1 mol of hemihydrate gypsum reacts with 1.5 mol of water to yield 1 mol of CaSO4·2H2O. With an increase in hemihydrate gypsum content, it rapidly reacts with a significant amount of water. Consequently, the free water within the unit volume of cementitious materials continues to diminish. Additionally, CaSO4·2H2O can react with cement particles, expediting the formation of ettringite and hastening the hydration reaction. Consequently, the setting time of cementitious materials continues to shorten. The reduction of free water within the unit volume of the cementitious material leads to a decrease in fluidity. Phosphogypsum encompasses soluble fluorine and soluble phosphorus, which can engage in a reaction with Ca(OH)2, a byproduct of cement hydration, to generate inert salts such as CaF2 and Ca3(PO4)2. These inert salts precipitate on the surface of cement particles, thereby impeding the hydration rate of cement. Hence, when the quantity of phosphogypsum is limited, the setting time of the cementitious material is extended. Due to the sluggish hydration process, an abundance of free water engages in the reaction, thereby augmenting the fluidity of the cementitious material. As the dosage continues to rise, the presence of CaSO4·0.5H2O in the cementitious system escalates, consequently absorbing a substantial portion of free water. This phenomenon leads to the commencement of a decline in both setting time and fluidity of the cementitious material. The dissolution rate of desulfurization gypsum surpasses that of anhydrite present in cement. Upon incorporating a small amount of desulfurization gypsum into the cementitious system, the ettringite precipitated in the liquid phase infiltrates the interstices between cement particles, impeding the progression of further hydration reactions. Additionally, desulfurization gypsum may harbor impurities with retarding effects, further elongating the setting time of the cement slurry. With the gradual escalation of desulfurization gypsum content, a copious amount of CaSO4·0.5H2O dissolves in the cementitious system, actively participating in the hydration reaction and consuming a significant portion of free water. As the hydration reaction progresses, generating exothermic reactions, it fosters increased ettringite formation. Consequently, the consumption of cement reaction water amplifies, resulting in a shorter setting time.
Figure 3A illustrates that at a semi-hydrated gypsum content of 6%, the 1-day strength of the binder material peaked, showcasing an increase of 3.1 MPa at a growth rate of 19.1%. Subsequently, as the semi-hydrated gypsum content rose further, the 1-day strength of the binder material began to decline. Specifically, at a semi-hydrated gypsum content of 12%, the strength decreased by 2.3 MPa, with a rate of 14.2%. Similarly, when the phosphogypsum content reached 10%, the 1-day strength of the binder material reached its pinnacle, exhibiting a 3.1 MPa increase at a growth rate of 19.1%. Nevertheless, as the phosphogypsum content continued to escalate, the 1-day strength of the binder material experienced a downturn. However, even at a phosphogypsum content of 12%, the strength remained superior to that of the binder material without gypsum. Optimal strength was achieved with an 8% desulfurized gypsum content, resulting in a 3.4 MPa surge at a growth rate of 21%. Yet, with further increments in desulfurized gypsum content, the 1-day strength of the binder material gradually declined. Nonetheless, even at a desulfurized gypsum content of 12%, the strength surpassed that of the binder material devoid of gypsum.
Figure 3. The effect of gypsum on the strength of SAC-coal-based solid waste cementitious materials at (A) 1, (B) 3, (C) 7, and (D) 28 days. SAC: Sulfoaluminate cement.
Figure 3B illustrates that at a semi-hydrated gypsum content of 8%, the 3-day strength of the binder material peaked, showcasing an increase of 4.2 MPa at a growth rate of 22.2%. Subsequently, as the semi-hydrated gypsum content rose further, the 3-day strength of the binder material began to decline. Specifically, at a semi-hydrated gypsum content of 12%, the strength decreased by 3.7 MPa at a rate of 19.6%.
Similarly, when the phosphogypsum content reached 8%, the 3-day strength of the binder material achieved its zenith, exhibiting a 2.8 MPa increase at a growth rate of 14.8%. However, as the phosphogypsum content continued to escalate, the 3-day strength of the binder material experienced a downturn. Nonetheless, even at a phosphogypsum content of 12%, the strength remained higher than that of the binder material without gypsum. Optimal strength was achieved with an 8% desulfurized gypsum content, resulting in a 4 MPa surge at a growth rate of 21.2%. Yet, with further increments in desulfurized gypsum content, the 3-day strength of the binder material gradually declined. Nonetheless, even at a desulfurized gypsum content of 12%, the strength surpassed that of the binder material devoid of gypsum.
Figure 3C reveals that at an 8% semi-hydrated gypsum content, the 7-day strength of the binder material peaked, marking a remarkable increase of 6.7 MPa at a growth rate of 34.9%. Subsequently, as the semi-hydrated gypsum content rose further, the 7-day strength of the binder material began to decline. Specifically, at a semi-hydrated gypsum content of 12%, the strength decreased by 0.3 MPa at a decrease rate of 1.6%. Similarly, when the phosphogypsum content reached 8%, the 7-day strength of the binder material achieved its zenith, showcasing an impressive 8.5 MPa increase at a growth rate of 44.3%. However, as the phosphogypsum content continued to escalate, the 7-day strength of the binder material experienced a downturn. Nevertheless, even at a phosphogypsum content of 12%, the strength remained higher than that of the binder material without gypsum. An optimal 7-day strength was attained with an 8% desulfurized gypsum content, resulting in a notable 10 MPa surge at a growth rate of 52.1%. Yet, with further increments in desulfurized gypsum content, the 7-day strength of the binder material gradually declined. Nonetheless, even at a desulfurized gypsum content of 12%, the strength surpassed that of the binder material devoid of gypsum.
Figure 3D illustrates that at an 8% semi-hydrated gypsum content, the 28-day strength of the binder material peaked, exhibiting a notable increase of 9.6 MPa at a growth rate of 37.1%. Subsequently, as the semi-hydrated gypsum content escalated, the 28-day strength of the binder material commenced a downward trajectory. Specifically, at a semi-hydrated gypsum content of 12%, the strength decreased by
Hydration mechanism analysis
Samples labeled S1 with fixed proportions of 15% coal gangue powder and 10% ultrafine fly ash, along with varying proportions of semi-hydrated gypsum at 6% (S2), 8% (S3), and 10% (S4), underwent XRD analysis at a curing age of 28 days. The XRD results of samples cured for 28 days without gypsum and the XRD spectra of the cementitious materials are depicted in Figure 4A. Similarly, XRD analysis was conducted on samples with fixed proportions of 15% coal gangue powder and 10% ultrafine fly ash, along with phosphogypsum at 6% (S5), 8% (S6), and 10% (S7), at a curing age of 28 days. The XRD results of samples cured for 28 days without gypsum and the XRD spectra of the cementitious materials are displayed in Figure 4B.
Figure 4. XRD pattern of the hydration products. (A) the XRD results of the samples cured for 28 days without gypsum and the XRD spectra of the cementitious materials; (B) the XRD results of the samples cured for 28 days without gypsum and the XRD spectra of the cementitious materials; (C) the XRD results of the samples cured for 28 days without gypsum and the XRD spectra of the cementitious materials; (D) the XRD patterns of the cementitious materials.
Additionally, XRD analysis was performed on samples with fixed proportions of 15% coal gangue powder and 10% ultrafine fly ash, along with desulfurized gypsum at 6% (S8), 8% (S9), and 10% (S10), at a curing age of 28 days. The XRD results of samples cured for 28 days without gypsum and the XRD spectra of the cementitious materials are presented in Figure 4C. Lastly, samples with fixed proportions of 15% coal gangue powder, 10% ultrafine fly ash, and 8% desulfurized gypsum were subjected to XRD analysis at curing ages of 1 day (S11), 3 days (S12), 7 days (S13), and 28 days. The XRD patterns of the cementitious materials are illustrated in Figure 4D. Quantitative analysis of ettringite in the hydration products of cementitious materials using the Rietveld method is summarized in Table 7.
Rietveld quantitative analysis of the ettringite content in the hydration products of cementitious materials
Numbers | Specific gravity of ettringite |
S1 | 41.6 |
S2 | 54.3 |
S3 | 57.6 |
S4 | 59.8 |
S5 | 52.7 |
S6 | 52.4 |
S7 | 52.8 |
S8 | 49.9 |
S9 | 43.9 |
S10 | 49.4 |
S11 | 50.8 |
S12 | 51.3 |
S13 | 52.3 |
With a consistent amount of coal-based solid waste and an increasing quantity of semi-hydrated gypsum, the proportion of ettringite in the hydration products of the cementitious materials gradually rose, while the strength of the cementitious system initially increased and then decreased. This phenomenon occurs because as the content of semi-hydrated gypsum in the cementitious system rises, more ettringite is formed. Additionally, the presence of sulfate ions in the cementitious system enhances the activity of ultrafine fly ash[14,15]. This activation promotes the formation of the gel through the pozzolanic reaction, enhances the bonding between the particles, and leads to a denser overall structure. With the increase of hemihydrate gypsum content from 0% to 8%, the dissolution of hemihydrate gypsum consumes the free water in the cementitious material. Gypsum actively participates in the hydration reaction, resulting in the formation of more ettringite. Calcium sulfate reacts with CH [Ca(OH)2] and AH3 [Al(OH)3] in cement to form additional ettringite, which contributes to the strength improvement. However, when the content of hemihydrate gypsum increases from 8% to 10%, the strength of cementitious materials decreases due to excessive expansion and fracture of cement caused by excessive formation of ettringite.
With a consistent amount of coal-based solid waste and an increasing quantity of phosphogypsum, the proportion of ettringite in the hydration products of the cementitious materials initially rose and then stabilized, while the strength of the cementitious system first increased and subsequently decreased. As the phosphogypsum content increased from 0% to 6%, the augmentation of ettringite and the activation of ultrafine fly ash by sulfate ions in the cementitious system improved interparticle bonding and overall structural density, resulting in strength enhancement. However, as the phosphogypsum content increased from 6% to 10%, the ettringite mass remained relatively stable despite the initial strength increase. This is attributed to the continuous generation of ettringite due to the sufficient gypsum content in the cementitious materials. Additionally, sulfate ions in phosphogypsum activate the activity of ultrafine fly ash in cementitious materials, leading to the generation of c-s-h gel. Consequently, although the strength of the cementitious materials increased, the proportion of ettringite in the hydration products did not significantly rise.
With a constant amount of coal-based solid waste and increasing desulfurized gypsum, the proportion of ettringite in the hydration products of the cementitious materials initially increased, followed by a decrease and subsequent increase. Conversely, the strength of the cementitious system initially rose and then declined. At lower desulfurized gypsum content, the reaction involving CaSO4·0.5H2O in desulfurized gypsum, water in the cementitious system, and cement particles reduced free water per unit volume and boosted ettringite formation, enhancing cementitious material strength. As desulfurized gypsum content increased, sulfate ions from its dissolution heightened ultrafine fly ash activity, depleting calcium hydroxide and reducing ettringite formation. However, the cementitious material densified, improving overall structural density and, thus, strength. With further desulfurized gypsum increase, an abundance of calcium sulfate in the hydration environment continuously generated ettringite. Additionally, calcium sulfate underwent secondary hydration with CH and AH3 in the cement to form ettringite. Excessive ettringite generation caused expansion, leading to decreased strength of the cementitious materials[16,17].
With fixed proportions of coal gangue powder, ultrafine fly ash, and desulfurized gypsum at 15%, 10%, and 8%, respectively, the proportion of ettringite in the hydration products initially increased and subsequently decreased, while the strength of the cementitious materials continued to rise with the curing age. The addition of semi-hydrated gypsum reduced the overall free water content in the cementitious system, and the ample calcium sulfate content enabled it to participate in hydration reactions, generating ettringite. Moreover, sulfate ions activated ultrafine fly ash, fostering pozzolanic reactions and enhancing cementitious material formation, thereby boosting strength at different curing ages compared to samples without desulfurized gypsum. Strength notably increased from 3 to 7 days of curing, while the proportion of ettringite in hydration products showed only slight growth. This is because ultrafine fly ash is already activated during the first 3 to 7 days of curing, leading to the significant generation of cementitious materials and only a slight increase in the proportion of ettringite in hydration products. With increased curing age, the strength of the cementitious materials rises; however, the proportion of ettringite decreases. This is because the ultra-fine fly ash has strong activity. When enough sulfate ions are in the cementitious system, more gels are continuously generated through the pozzolanic reaction. However, excessive gel and excessive ettringite lead to expansion and fracture of cement, resulting in a decrease in the strength of cementitious materials.
Effects of ternary composite incorporation of water reducers on the properties of cementitious materials
To comprehensively and systematically examine the influence of water reducer dosage on the hydration performance of a sulfate-aluminate cement-coal-based solid waste-solid waste gypsum cementitious system, various percentages of lignosulfonate sodium, naphthalene-based, and polycarboxylate water reducers were introduced to the cementitious system. The water reducer dosages ranged from 0% to 3% in increments of 0.05%, resulting in 18 groups. As depicted in Figure 5A and B, an increase in the water reducer dosage led to progressive improvements in fluidity and setting time of the cementitious material. The water-reducing effect followed the sequence of polycarboxylate, naphthalene-based, and lignosulfonate sodium water reducers, while the retarding effect followed the sequence of polycarboxylate, lignosulfonate sodium, and naphthalene-based water reducers.
Figure 5. (A) Influence of water reducer on the setting time of cementitious materials; (B) Influence of water reducer on the flowability of cementitious materials; (C) Influence of retarder on the setting time of cementitious materials; (D) Influence of retarder on the flowability of cementitious materials.
With the increase in polycarboxylate water reducer dosage from 0% to 0.3%, the fluidity of the cementitious material increased by 145 mm, marking a growth rate of 112.9%, while the setting time increased by 7.8 min, reflecting a growth rate of 147.9%. As for the naphthalene-based water reducer dosage, an increase from 0% to 0.3% led to a fluidity increase of 83 mm, at a growth rate of 70.3%, and a setting time increase of 2.0 min, at a growth rate of 38.5%. Similarly, with an increase in lignosulphonate sodium dosage from 0% to 0.3%, the fluidity of the cementitious material rose by 73 mm, indicating a growth rate of 61.9%, and the setting time extended by 9.7 min, reflecting a growth rate of 183.0%.
The molecular structure of lignosulfonate sodium contains retarding groups (hydroxyl and ether bonds) that inhibit the early hydration of cement, reduce chemically bound water, and increase the amount of free water, thereby enhancing the fluidity and setting time of the cementitious material[18-20]. The mechanism of naphthalene-based water reduction involves electrostatic repulsion and steric hindrance. Electrostatic repulsion encompasses dispersion and lubrication effects. The dispersion effect arises from the oriented adsorption of naphthalene-based water reducer molecules onto cement particle surfaces, inducing a uniform charge distribution. This, in turn, triggers electrostatic repulsion, disrupting the flocculation structure between cement particles. Consequently, encapsulated free water is released, enhancing its utilization in the cementitious material. This process improves fluidity, setting time, and water drainage rate, thereby reducing the stone content of the cementitious material. The lubrication effect stems from the hydrophilic groups of naphthalene-based water reducer molecules adsorbed on cement particle surfaces, forming a stable solvation water film with water molecules within the cementitious material. This reduces flow resistance between cement particles, facilitating lubrication and enhancing the material’s flowability. The free hydrophilic branches of naphthalene-based water reducer molecules, when adsorbed on the surface of cement particles, create steric hindrance during mutual approach. As cement particles draw closer, greater branch overlap occurs, intensifying steric hindrance. This prevents close particle contact, disrupts particle flocculation, enhances cement particle flow, and promotes the flowability of the cementitious material. With the action of electrostatic repulsion, an increase in polycarboxylate water reducer dosage enhances the fluidity and setting time of the cementitious material while decreasing stone content. Beyond electrostatic repulsion and steric hindrance theories, the grafting copolymer side chain retarding effect constitutes a unique water-reducing mechanism of the polycarboxylate water reducer, contributing to its higher water-reducing rate compared to lignosulfonate sodium and naphthalene-based water reducers. The retarding effect of the grafted copolymer side chains encompasses the phenomenon where certain side chains attached to the polycarboxylate water reducer molecule not only induce steric hindrance but also, in an alkaline environment, may undergo breakage, releasing polycarboxylic acid with dispersing properties. This acid can effectively disperse cement particles and enhance fluidity[21-24]. Compared to naphthalene-based and lignosulfonate sodium water reducers, polycarboxylate water reducers offer greater advantages for the fluidity and setting time of SAC-coal-based solid waste-solid waste gypsum cementitious materials. Consequently, the polycarboxylate water reducer was chosen for further experimentation.
To comprehensively and systematically examine the impact of retarder dosage on the hydration performance of the SAC-coal-based solid waste-solid waste gypsum cementitious system, with a fixed dosage of 0.25% polycarboxylate water reducer, different proportions of inorganic retarder borax and organic retarder sodium gluconate were introduced into the cementitious system. Retarder dosages ranged from 0% to 0.25% in increments of 0.05%, constituting a total of ten groups. As depicted in Figure 5C and D, an increase in borax dosage markedly prolonged the setting time of the cementitious material, concurrently enhancing fluidity and reducing stone content. Specifically, when the borax dosage rose from 0% to 0.25%, the setting time surged by 105.3 min. Subsequently, with further increments in borax dosage, the setting time exhibited a significant rise. Correspondingly, the fluidity of the cementitious material increased by
This is because the addition of borax to the cementitious material results in the formation of small calcium borate crystals in the paste, which create an enveloping layer on the surface of the cement particles, slowing down the hydration rate of the SAC. When the borax dosage is excessively low, the calcium borate may not fully cover the surface of the cement particles, resulting in an insignificant retarding effect. As the borax dosage increases, the density of calcium borate on the surface of the cement particles gradually grows, leading to a gradual prolongation of the setting time of the cementitious material. Consequently, the increasing amount of free water that cannot participate in the hydration reactions contributes to the enhanced fluidity of the cementitious material and an increased water bleeding rate. However, when the dosage is excessively high, the calcium borate layer on the surface of the clinker particles becomes overly dense, impeding the hydration reaction of the cement particles and resulting in excessive retardation or even no setting[25-28]. Sodium gluconate can create an enveloping layer within the cement and its hydration products, thereby slowing down the hydration rate of the cement and reducing the formation rate of ettringite, which extends the setting time. Initially, when the dosage of sodium gluconate is relatively small, the enveloping layer formed is thin, resulting in an insignificant retarding effect. However, upon reaching a certain dosage threshold, the thickness of the enveloping layer increases, effectively delaying cement hydration. As the dosage of sodium gluconate continues to increase, it reacts with the hydration products, leading to the formation of more calcium gluconate crystals. This process results in a thinner enveloping layer and a decrease in the retarding effect[29-31].
To comprehensively and systematically investigate the impact of early strength agent dosage on the hydration performance of a SAC-coal-based solid waste-solid waste gypsum cementitious system, various percentages of lithium carbonate and calcium formate were added to the system, with early strength agent dosages ranging from 0% to 0.25% in increments of 0.05%, totaling ten groups. As depicted in Figure 6A and B, as the dosage of lithium carbonate and calcium sulfate increased, the setting time and fluidity of the cementitious material progressively decreased. However, the incorporation of lithium carbonate resulted in a more pronounced decrease in setting time and fluidity compared to the incorporation of calcium formate. As illustrated in Figure 6C-F, with a constant dosage of polycarboxylate water reducer and borax retarder, the strength of the cementitious material at various ages initially rose and then decreased as the dosage of lithium carbonate increased. At a lithium carbonate dosage of 0.15%, the strength of the cementitious material at various ages peaked, surpassing that of pure SAC. However, with further increases in lithium carbonate dosage, the strength at various ages began to decline. Conversely, with an increase in calcium sulfate dosage, the strength of the cementitious material at 1 day continued to rise, while those at 3 and 28 days gradually decreased.
Figure 6. (A) Influence of early strength agent on the flowability of cementitious materials; (B) Influence of early strength agent on the setting time of cementitious materials; (C) Influence of early strength agent on the 1 day strength of cementitious materials; (D) Influence of early strength agent on the 3 days strength of cementitious materials; (E) Influence of early strength agent on the 7 days strength of cementitious materials; (F) Influence of early strength agent on the 28 days strength of cementitious materials.
When sodium sulfate dissolves in water, it reacts with calcium hydroxide in the cementitious system to form gypsum dihydrate. This compound can further react with anhydrous calcium sulfate in cement clinker, facilitating the formation of ettringite and aluminum hydroxide gel, thus enhancing the strength of the cementitious material after 1 day. However, the addition of sodium sulfate depletes calcium hydroxide in the cementitious material, reducing its content. Consequently, sodium sulfate only contributes to the strength of the cementitious material on 1 day and does not support subsequent strength development[32,33]. Conversely, the addition of lithium carbonate accelerates the rate of ettringite formation in cementitious materials, thereby promoting early strength. Within a certain dosage range, lithium carbonate positively influences the strength at various ages of the cementitious material[34-39]. While sodium sulfate does not facilitate the later strength development of SAC-coal-based solid waste-solid waste gypsum cementitious materials, an appropriate dosage of lithium carbonate promotes strength across various ages.
To comprehensively study the influence of the water-to-binder ratio on the hydration performance of SAC-coal-based solid waste-solid waste gypsum cementitious systems, a fixed dosage of 0.25% polycarboxylate water reducer, 0.25% borax retarder, and 0.15% lithium carbonate early strength agent were maintained, while varying the water-to-binder ratio from 0.5 to 0.3, decreasing by 0.5 in each group, totaling five groups.
In Figure 7A, with the aforementioned fixed dosages, a decrease in the water-to-binder ratio resulted in reduced fluidity and setting time of the cementitious material. Specifically, as the water-to-binder ratio fell from 0.5 to 0.3, the fluidity decreased from 237 to 194 mm, representing a reduction of 43 mm at a rate of 18.1%, and the setting time decreased by 33.7 min, indicating a drop of 56.7%. Higher water-to-binder ratios resulted in fewer cement particles per unit volume, leading to larger distances between the particles.
Figure 7. (A) Influence of water-to-cement ratio on the flowability and setting time of cementitious materials; (B) Influence of water-to-cement ratio on the strength of cementitious materials at different ages.
Figure 7B depicts that when the water-cement ratio was 0.4, the 28-day strength of the cementitious material exceeded 42.5 MPa, reaching 49.8 MPa. Similarly, when the water-cement ratio was 0.35, the 3-day strength surpassed 42.5 MPa, reaching 43.6 MPa, with the strength at each age exceeding the requirements for 425 SAC. As the water-to-binder ratio decreases, the strength of the cementitious materials at each age continues to rise. This is because the gel produced by hydration becomes insufficient to fill the gaps between the particles, and the excess evaporated water leaves more voids, leading to a decrease in strength. Conversely, with a low water-to-binder ratio, the distances between the cement particles are smaller, allowing the gel produced by cement hydration to easily fill the gaps between the particles. Additionally, fewer voids remain after evaporation, resulting in an increase in strength with a decrease in the water-to-binder ratio.
CONCLUSION
With increasing amounts of semi-hydrate gypsum, phosphogypsum, and desulfurization gypsum, the strength of the cementitious material at different ages initially rises and then declines. When the doses of sulfate aluminum cement, coal gangue powder, ultrafine coal ash, and desulfurization gypsum in the cementitious material were 67%, 15%, 10%, and 8%, respectively, the strength at 1 and 3 days resembled that of pure sulfate aluminum cement, while the strength at 7 and 28 days far surpassed that of pure sulfate aluminum cement. This proportion effectively reduces the cost of sulfate aluminum cement. The compatibility of the sulfate aluminum cement-coal-based solid waste-solid waste gypsum cementitious material with admixtures is excellent. When the doses of sulfate aluminum cement, coal gangue powder, ultrafine coal ash, and desulphurization gypsum in the cementitious material were 67%, 15%, 10%, and 8%, respectively, and 0.25% polycarboxylate water reducer, 0.25% borax, and 0.15% lithium carbonate were added, the strength at each age of the sulfate aluminum cement-coal-based solid waste-solid waste gypsum cementitious material surpassed that of pure sulfate aluminum cement. Additionally, the setting time and flowability were superior to those of pure sulfate aluminum cement. With a water-to-binder ratio of 0.35, the strength at each age met the requirements of the 425 sulfate aluminum cement. This experimental ratio allows for the consumption of a large amount of coal-based solid waste and solid waste gypsum, which is significant for environmental protection efforts.
DECLARATIONS
Authors’ contributions
Responsible for testing and writing papers: Pan Y
Responsible for providing ideas and modifying papers: Li H, Yang T
All authors agree to the publication of the paper.
Availability of data and materials
Not applicable.
Financial support and sponsorship
This work was supported by the basic research and development plan of Shanxi Province (free exploration) project (project number: 202203021221041).
Conflicts of interest
All authors declared that there are no conflicts of interest.
Ethical approval and consent to participate
Not applicable.
Consent for publication
Not applicable.
Copyright
© The Author(s) 2024.
REFERENCES
1. Feng F, Li L, Zhang J, Yang Z, Chi X. Strength prediction of coal-based solid waste filler based on BP neural network. Front Mater 2021;8:767031.
2. Wei Z, Yang K, He X, Zhang J, Hu G. Experimental study on the optimization of coal-based solid waste filling slurry ratio based on the response surface method. Materials 2022;15:5318.
3. Zhao X, Yang K, He X, Wei Z, Yu X, Zhang J. Study on mix proportion optimization and microstructure of coal-based solid waste (CSW) backfill material based on multi-objective decision-making model. Materials 2022;15:8464.
4. Zhou Y, Xie L, Kong D, Peng D, Zheng T. Research on optimizing performance of desulfurization-gypsum-based composite cementitious materials based on response surface method. Constr Build Mater 2022;341:127874.
5. Dong M, Li J, Lang L, Chen X, Jin J, Ma W. Recycling thermal modified phosphogypsum in calcium sulfoaluminate cement: evolution of engineering properties and micro-mechanism. Constr Build Mater 2023;373:130823.
6. Júnior LUD, dos Santos Lima GT, Silvestro L, Ruviaro AS, Gleize PJP, de Azevedo ARG. Influence of polycarboxylate superplasticizer and calcium sulfoaluminate cement on the rheology, hydration kinetics, and porosity of Portland cement pastes. J Build Eng 2023;68:106120.
7. Jing H, Xu M, Gao M, Li M, Dai S. Effect of compounding retarder and PCE on the early properties and hydration of high-belite sulphoaluminate cement. Appl Sci 2022;12:10731.
8. Zhou H, Qi X, Ma C, et al. Effect and mechanism of composite early-strength agents on sulfoaluminate cement-based UHPC. Case Stud Constr Mat 2023;18:e01768.
9. García-maté M, De la Torre A, León-reina L, Aranda M, Santacruz I. Hydration studies of calcium sulfoaluminate cements blended with fly ash. Cement Concrete Res 2013;54:12-20.
10. Huang Y, Qian J, Lu L, et al. Phosphogypsum as a component of calcium sulfoaluminate cement: hazardous elements immobilization, radioactivity and performances. J Clean Prod 2020;248:119287.
11. Gao D, Zhang Z, Meng Y, Tang J, Yang L. Effect of flue gas desulfurization gypsum on the properties of calcium sulfoaluminate cement blended with ground granulated blast furnace slag. Materials 2021;14:382.
12. Zhang J, Wang X, Jin B, Zhang X, Li Z, Guan X. Effect of superplasticizers on hydration kinetics of ultrafine sulfoaluminate cement-based grouting material. Thermochim Acta 2021;703:178988.
13. Pan Y, Yi H, Yang T, Li R, Li H. Study on sulphoaluminate cement-coal-based solid waste cementitious material. Non Metallic Ore 2023,46:98-101+6. Available from: https://xueshu.baidu.com/usercenter/paper/show?paperid=1u740j10t87j02q0db190490dx350678&site=xueshu_se&hitarticle=1. [Last accessed on 25 Jun 2024]
14. Mondal SK, Clinton C, Ma H, Kumar A, Okoronkwo MU. Effect of class C and class F fly ash on early-age and mature-age properties of calcium sulfoaluminate cement paste. Sustainability 2023;15:2501.
15. Ma B, Li X, Shen X, Mao Y, Huang H. Enhancing the addition of fly ash from thermal power plants in activated high belite sulfoaluminate cement. Constr Build Mater 2014;52:261-6.
16. Zhang J, Guan X, Wang X, et al. Microstructure and properties of sulfoaluminate cement-based grouting materials: effect of calcium sulfate variety. Adv Mater Sci Eng 2020;2020:1-8.
17. Chaunsali P, Ardeshirilajimi A, Mondal P. On the interaction of class C fly ash with Portland cement–calcium sulfoaluminate cement binder. Mater Struct 2018;51:131.
18. Dvorkin L, Zhitkovsky V, Makarenko R, Ribakov Y. The influence of polymer superplasticizers on properties of high-strength concrete based on low-clinker slag Portland cement. Materials 2023;16:2075.
19. Zhong D, Liu Q, Zheng D. Synthesis of lignin-grafted polycarboxylate superplasticizer and the dispersion performance in the cement paste. Colloid Surface A 2022;642:128689.
20. Zhang Y, Zhang W, Shi X, Guo T, Chen Z. Experimental study on unconfined compressive strength of expansive soil improved by lignin and cement. E3S Web Conf 2021;236:02010.
21. Wu Y, Li Q, Li G, Tang S, Niu M, Wu Y. Effect of naphthalene-based superplasticizer and polycarboxylic acid superplasticizer on the properties of sulfoaluminate cement. Materials 2021;14:662.
22. Gu L, Li H, Yang X, Dong B, Wen Z. Leakage behavior of toxic substances of naphthalene sulfonate-formaldehyde condensation from cement based materials. J Environ Manage 2020;255:109934.
23. Wang B, Pang B. Mechanical property and toughening mechanism of water reducing agents modified graphene nanoplatelets reinforced cement composites. Constr Build Mater 2019;226:699-711.
24. Gao L, Shi Y, Xu GQ. Comparative study on the application of naphthalene water-reducing agent and polycarboxylate water-reducing agent in high-performance concrete. AMR 2011;217-8:522-6.
25. Yao J, Feng D, Wang Z, Peng C, Zhang Y, Han L. Experimental study on performance of modified cement-based building materials under high-water-pressure surrounding rock environment. Coatings 2023;13:501.
26. Lv X, Li J. A novel admixture with intensive inhibition of hydration effects for cement: impact of amino trimethylene phosphonic-based material on the hydration characteristics and performance of ordinary Portland cement. J Mater Civ Eng 2023;35:04022363.
27. Du P, Li X, Zhou Z, et al. Preparation and properties of alite-modified calcium sulfoaluminate cement. Adv Cem Res 2021;33:135-43.
28. Ke G, Zhang J. Effects of retarding admixture, superplasticizer and supplementary cementitious material on the rheology and mechanical properties of high strength calcium sulfoaluminate cement paste. ACT 2020;18:17-26.
29. Wu Y, Yuan Y, Niu M, Kuang Y. Effect of sodium gluconate on properties and microstructure of ultra-high-performance concrete (UHPC). Materials 2023;16:3581.
30. Lin C, Liu Z, Gao Y, Li Z, Zhang J, Niu H. Study on the effect and mechanism of cement-based material retarder on red mud-based hybrid alkali activated cement. J Build Eng 2023;70:106353.
31. Kryvenko PV, Gots VI, Petropavlovskyi O, Rudenko I, Konstantynovskyi OP. Complex shrinkage-reducing additives for alkali activated slag cement fine concrete. SSP 2021;321:165-70.
32. He J, Yu S, Sang G, He J, Wang J, Chen Z. Properties of alkali-activated slag cement activated by weakly alkaline activator. Materials 2023;16:3871.
33. Wang Y, Sun L, Liu S, Li S, Guan X, Luo S. Development of a novel double-sulfate composite early strength agent to improve the hydration hardening properties of Portland cement paste. Coatings 2022;12:1485.
34. He H, Wang Y, He F, Luo S, Liu S. Effect of Li2CO3 on the properties of Portland cement paste. Mater Struct 2021;54:33.
35. Deng YH, Zhang CQ, Shao HQ, Wu H, Xie NQ. Effects of different lithium admixtures on ordinary Portland cement paste properties. AMR 2014;919-21:1780-9.
36. Zhang Y, Wang Y, Li T, Xiong Z, Sun Y. Effects of lithium carbonate on performances of sulphoaluminate cement-based dual liquid high water material and its mechanisms. Constr Build Mater 2018;161:374-80.
37. Wang J, Wang Y, Yu J, et al. Effects of sodium sulfate and potassium sulfate on the properties of calcium sulfoaluminate (CSA) cement based grouting materials. Constr Build Mater 2022;353:129045.
38. Wang Y, Tang H, Su J, He H, Zhao Y, Wang J. Effect of sodium sulfate and gypsum on performances of expansive grouting material with aluminum as expansion agent. Constr Build Mater 2023;394:132212.
Cite This Article

How to Cite
Download Citation
Export Citation File:
Type of Import
Tips on Downloading Citation
Citation Manager File Format
Type of Import
Direct Import: When the Direct Import option is selected (the default state), a dialogue box will give you the option to Save or Open the downloaded citation data. Choosing Open will either launch your citation manager or give you a choice of applications with which to use the metadata. The Save option saves the file locally for later use.
Indirect Import: When the Indirect Import option is selected, the metadata is displayed and may be copied and pasted as needed.
About This Article
Special Issue
Copyright
Data & Comments
Data
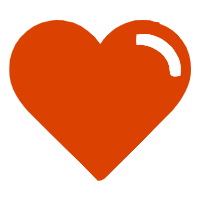
Comments
Comments must be written in English. Spam, offensive content, impersonation, and private information will not be permitted. If any comment is reported and identified as inappropriate content by OAE staff, the comment will be removed without notice. If you have any queries or need any help, please contact us at [email protected].