Uncertainty aware design space modeling for sample efficiency in material design of bainitic steels
Abstract
Optimizing sampling efficiency is crucial for solving complex material design challenges, especially with a limited experimental budget. This study focuses on improving sampling efficiency by reducing the search space for carbide-free bainitic steels through the uncertainty-aware modeling of constraints. These constraints include avoiding the formation of undesirable competing phases such as carbides, ferrite, and martensite, as well as accounting for practical limitations on phase transformation durations. Experimental data, obtained through dilatometry and metallography, inform most constraints, except for the presence of carbides. To model these constraints, we use machine learning (ML) models trained on a combination of newly acquired experimental data and experimental data from the literature. Predicting properties in unexplored regions of the design space can lead to inaccuracies. Thus, reliable uncertainty quantification is essential to avoid excluding parts of the design space due to overconfident erroneous predictions. To address this, we employ conformal prediction (CP), a distribution-free framework that provides calibrated post-hoc uncertainty estimates for the different ML models, ensuring reliable extrapolations without prematurely excluding viable design regions. This approach achieves a reduction ranging from 80% to more than 99% depending on the strictness of the employed criteria reduction in the search space, greatly enhancing sampling efficiency without compromising reliability.
Keywords
INTRODUCTION
Iterative optimization loops, such as Bayesian optimization, are an effective tool for material discovery and property optimization[1]. These approaches rely on surrogate models as computationally efficient approximations of the true objective function. Since evaluating the true objective requires costly experiments, surrogate models facilitate property estimation in the design space by using prior knowledge and experimental data[2–7]. With each iteration, newly acquired data refines the approximation of the surrogate model, enabling more informed sampling[1]. The search space, often represented as a hypercube, includes all possible input configurations considered during optimization. It is a crude approximation of the true design space, which is an optimized subset of configurations that meet specific criteria and constraints set by the design objectives.
In steel, different microstructures can form despite having the same chemical composition by varying process parameters, such as heat treatment. Depending on the microstructure, diverse mechanisms may govern the same property, resulting in multiple process-microstructure-property relationships[8,9]. For this reason, steels are classified into different types[10]. Beyond that, when multiple microstructures coexist, their properties mostly do not exhibit simple additive behavior[11–13], creating significant modeling challenges, which can lead to poor generalization abilities of models. In material design, especially when using methods that rely on model predictions, such as Bayesian optimization, this can lead to sampling in uninformative or practically infeasible regions, reducing optimization efficiency and wasting resources. To address this, a preselection of a steel type is necessary, allowing models to generalize property predictions more effectively.
In the present work, we focus on carbide-free bainitic (CFB) steel, a promising and cost-effective type of advanced high-strength steel. Its microstructure is primarily composed of bainitic ferrite and retained austenite, with minimal carbide content[14]. Rather than optimizing for specific properties, this work focuses on classifying points within the search space as either CFB or non-CFB. Additionally, we incorporate constraints based on industrial manufacturing requirements, in particular, the bainitic phase transformation time. These constraints lead to non-trivial boundaries of the design space[15], within which chemical compositions and heat treatment parameters can be optimized for desired properties. This ensures that Bayesian optimization focuses exclusively on industrially feasible samples that lead to valid CFB steels. Some methods actively model the valid design space either during [16] or before optimization [6]. However, these approaches often rely on the intentional generation of non-valid samples to refine boundary definitions, which can be resource-intensive. In our work, we model the individual physical processes required to produce CFB steel, breaking down the overall classification problem (CFB vs. non-CFB steel) into simpler sub-problems. This modular approach facilitates the integration of domain-specific knowledge or physics and enables more effective use of experimental data. For instance, a prerequisite for achieving CFB steel is a complete transformation to austenite without the formation of carbide or ferrite. This constraint can be modeled independently of subsequent processing steps, enabling the use of physical models or literature data unrelated to bainitic steel.
As the availability of accurate physical models is limited for the given problems, we use machine learning (ML) models to predict the constraints from experimental data produced in the present work and from the literature. However, ML models often perform poorly when the distribution of the training data differs from that encountered during testing or deployment (e.g., novel material compositions or processing parameters). This is referred to as distribution shifts[17,18] and requires the model to extrapolate. In such cases, learned correlations of the model from the training data may no longer hold, leading to inaccurate predictions. One approach to addressing this issue is to improve model generalization and extrapolation capabilities by incorporating physical knowledge, although this can be challenging and is not always feasible [19]. Alternatively, distribution shifts can be detected, and the confidence levels of predictions can be adjusted accordingly to account for uncertainty. By providing uncertainty estimates, we mitigate the risk of incorrect decisions resulting from overconfident, erroneous predictions by ML models. In our application, this ensures that potentially valuable material compositions, for which the ML models are uncertain or unreliable, are not prematurely discarded.
Uncertainty estimates in practical applications often suffer from calibration issues - this refers to a mismatch between the predicted uncertainty intervals and the actual probability that the true value falls within those intervals[20]. For example, if a model predicts a 90% confidence interval, but the true value only falls within the interval 70% of the time, the model is considered poorly calibrated. This undermines the reliability of predictions and can lead to suboptimal decisions. To address this, we employ conformal prediction (CP)[21,22], a distribution-free method that calibrates uncertainty estimates to guarantee valid prediction intervals with specified coverage probabilities. To further increase robustness regarding distribution shifts, we extend this approach with distance-aware uncertainty estimates[23]. By incorporating a distance metric between the test data points and the training data, we assign higher uncertainty scores to test points that are far away from our training set.
Using this framework, we evaluate the performance of various ML models - including Gaussian processes regression, random forests (RFs), gradient boosting machines, linear and polynomial regression, neural networks (NNs), and support vector machines (SVM)- for predicting the aforementioned constraints. The models are compared in terms of predictions and prediction intervals. To the best of our knowledge, no prior work has emphasized the importance of addressing distributional uncertainty arising from distribution shifts in the Bayesian optimization for material discovery of material compositions and process parameters. For a confidence level of 90%, the search space can be reduced by 80%.
Importantly, this method serves as a versatile extension to any predictor within the Bayesian optimization framework, offering uncertainty estimates that are more robust to distributional shifts.
MATERIALS AND METHODS
Design problem
In the present work, we are modeling the design space of CFB steels. In this steel type, the carbide precipitation is suppressed during bainitic transformation by adding silicon [24] or aluminum [25,26], and it is defined as having at least 1 wt.% silicon. The retained austenite is stabilized by carbon, which is redistributed during the bainitic transformation from bainitic ferrite to retained austenite [14]. We place a lower limit of carbon concentration to ensure some retained austenite. Additionally, considered alloying elements are Si, Mn, Cr, Mo, Al and V, excluding critical raw elements such as Ni, W and Co [Table 1]. Furthermore, CFB steel is intended to exhibit relatively low overall alloying content. Therefore, the total concentration of alloying elements, denoted as
Search space
C | Si | Mn | Cr | Al | V | Mo | ||||
Unit | wt.% | wt.% | wt.% | wt.% | wt.% | wt.% | wt.% | wt.% | ℃ | ℃/s |
Min | 0.2 | 1 | 0 | 0 | 0 | 0 | 0 | 1.2 | 250 | 0.1 |
Max | 1 | 4 | 4 | 4 | 4 | 0.5 | 4 | 10 | 600 | 25 |
Figure 1. Temperature profile (in black) for the processes leading to the formation of CFB, along with time/temperature regions where constraints apply: (A) isothermal holding (austempering) and (B) continuous cooling. Colored regions indicate phases: Ferrite/Pearlite (F/P), Bainite (B), and Martensite (M). The constraints are enumerated by C1-C7. CFB: Carbide-free bainite.
As illustrated schematically, the sample is heated up to an austenitization temperature, typically above 800 ℃ and held for a duration
The requirement for the sample to be only bainitic (B) can be expressed by a list of constraints, which are listed below and, if applied to the search space, yield the design space. As can be seen in Figure 1, both processes have windows for the process parameters, which are composition-dependent.
C1 - Homogeneity of austenitization
For the present modeling approach of CFB steels, a complete transformation to the austenite phase without the formation of additional phases such as carbides or ferrite is necessary. This can be expressed as
where
However, predictions from CALPHAD databases are not without limitations. To account for uncertainties, it is common practice to include a safety margin of 50 ℃. Applying this margin to both the upper and lower bounds of a temperature range results in an effective window of 100 ℃. For practical applications, this temperature window should lie between 800 and 1,200 ℃, resulting in the constraint
This constraint is implicitly fulfilled in most works considering CFB steels.
C2 - Bainite start temperature
The occurrence of bainite is limited by a maximum temperature, the bainite start temperature
with
C3 - Martensite start temperature of the initial alloy
The martensite start temperature is the lower limit of the process window for the isothermal process. This boundary is given by
There are a multitude of models for the martensite start temperature available in literature based on ML and thermodynamic modeling [29,33] with reasonable prediction accuracy. However, none of them are provided in an executable form and ready to use out of the box.
C4 - Bainite transformation time
Depending on the chemical composition (
Composition of all alloying elements in wt.% of model alloys
Name | C | Si | Mn | Cr | Mo | Al | V |
S1 | 0.21 | 1.64 | 0.87 | 1.19 | 0.64 | 0.03 | 0.11 |
S2 | 0.30 | 1.65 | 0.88 | 1.18 | 0.67 | 0.03 | 0.11 |
S3 | 0.41 | 1.66 | 0.88 | 1.21 | 0.67 | 0.03 | 0.11 |
S4 | 0.52 | 1.71 | 0.91 | 1.22 | 0.69 | 0.04 | 0.11 |
S5 | 0.60 | 1.65 | 0.88 | 1.19 | 0.67 | 0.03 | 0.11 |
S6 | 0.39 | 3.09 | 0.92 | 1.24 | 0.69 | 0.03 | 0.10 |
S7 | 0.39 | 1.5 | 1.94 | 0.52 | 0.67 | 0.03 | 0.10 |
S8 | 0.38 | 1.15 | 0.90 | 1.19 | 0.67 | 0.03 | 0.11 |
S9 | 0.82 | 1.37 | 0.31 | 0.01 | 0.56 | 0.84 | 0.00 |
S10 | 0.45 | 2.99 | 0.23 | 0.12 | 1.86 | 0.03 | 0.02 |
S11 | 0.65 | 1.83 | 0.38 | 0.29 | 1.56 | 0.02 | 0.01 |
S12 | 0.41 | 1.52 | 0.91 | 1.21 | 0.67 | 0.09 | 0.48 |
S13 | 0.69 | 2.59 | 0.65 | 0.59 | 0.00 | 0.01 | 0.00 |
S14 | 0.39 | 1.52 | 3.39 | 0.53 | 0.73 | 0.01 | 0.09 |
S15 | 0.69 | 3.03 | 1.02 | 0.12 | 0.84 | 2.01 | 0.00 |
S16 | 0.73 | 3.25 | 1.36 | 0.00 | 0.45 | 1.91 | 0.00 |
S17 | 1.05 | 1.58 | 2.47 | 0.04 | 0.65 | 1.24 | 0.04 |
S18 | 1.11 | 1.69 | 2.58 | 0.09 | 0.01 | 2.42 | 0.00 |
S19 | 0.70 | 3.86 | 1.99 | 0.04 | 0.05 | 1.22 | 0.02 |
S20 | 0.57 | 3.99 | 1.16 | 0.02 | 0.86 | 1.30 | 0.00 |
S21 | 0.70 | 0.00 | 0.63 | 0.59 | 0.00 | 2.59 | 0.00 |
Several works have attempted to predict this property using purely data-driven, phenomenological, or physics-based models [34–38], but with little to no extrapolative prediction quality and none that are ready to use out of the box.
C5 - Martensite start of retained austenite for the isothermal case
The martensite start temperature is the same phenomenon as in constraint C3, but for the retained (=remaining) austenite after the bainitic phase transformation. During this transformation, the retained austenite is enriched with carbon, which lowers its martensite start temperature. This can be expressed as
where
C6 - Critical cooling rate of ferrite and pearlite
The critical cooling rate is the lowest cooling rate at which F/P can occur. It is determined from a continuous cooling transformation (CCT) diagram.
When designing new steels, it provides information about the process windows. There have been efforts to predict the occurrence of phases during continuous cooling, either with regression[34,35] or other ML methods [36–38].
C7 - Martensite start of retained austenite for the continuous cooled case
Constraint C7 represents the martensite start temperature of retained austenite in the continuous cooling process. Modeling this would require predicting the kinetics of carbide-free bainite formation and the redistribution of carbon in retained austenite as functions of the cooling rate. Currently, there is neither a suitable predictive model nor sufficient data available to address this, and hence it was excluded from this work. As a result, the predictions in this study do not account for a maximum cooling rate, which will result in an overestimation of the design space size for continuously cooled carbide-free bainite.
Data generation for C1 - homogeneity of austenitization
The stability and occurrence of carbides, austenite, and ferrite phase is modeled in thermodynamic databases. The MatCalc Software[28] and database (mc_fe version 2.061 [39]) are used to calculate equilibrium temperature scans for a surrogate model to increase in evaluation speed. The MatCalc simulation considers the following phases in the scan for the austenitization temperature: liquid, austenite, ferrite, cementite, and several other carbides (M6C, M7C3, M23C6, LAVES_Phase, K_CARB, and FCC_A1#01). For each alloy composition, a temperature scan of equilibrium calculations is performed starting at a temperature of 1,873 ℃ and a step size of 2 ℃.
Evaluation of carbon redistribution for C4
For a given isothermal holding temperature (
The carbon enrichment of the retained austenite stabilizes it against martensite transformation during cooling to room temperature. This explains the difference between the martensite start of the initial alloy
Experimental data
The data used in this work consists of experimental data from literature, as well as experimental data produced in this work. The experimental details for the production of the samples are described in Ref. [31]. The alloys were fabricated using a high-frequency remelting furnace (HRF), the "PlatiCast-600-Vac," from the Linn High Therm GmbH, Germany [40,41]. Approximately 450 g of each alloy, shaped into 26.5 mm × 26.5 mm × 90 mm ingots, was melted using high-purity raw materials. The process took place in a pure alumina crucible under an argon atmosphere at five atmospheres overpressure. The molten material was centrifugally cast into a cold copper mold, resulting in highly homogeneous samples due to the combination of inductive melting, centrifugal casting, and rapid solidification.
Chemical composition analyses, detailed in Table 2, are performed using optical emission spectroscopy (OES, model OBLF QSG 750). To ensure a consistent initial microstructure, the raw samples underwent heat treatment in an argon-purged chamber furnace. This included diffusion annealing at 1,200 ℃ for four hours, achieved with a heating rate of 300 ℃/s. Following this, the samples were removed from the furnace and allowed to cool freely to room temperature. To further refine the coarse-grained microstructure, a normalization annealing was conducted at 960 ℃ - at least 50 ℃ above the previously calculated Ae3 temperature - for 50 min, followed by free cooling to room temperature. Metallographic examination of the resulting ingots confirmed a uniform microstructure.
Cylindrical dilatometer samples with a diameter of 4 mm and a length of 10 mm are produced. The heat treatment and measurement is done with a TA Instruments DIL 805 A dilatometer in vacuum. The samples are austenitized for 30 min at 960 ℃ with a heating rate of 2 K/s. The bainite start temperature was measured for selected compositions, with the methods described in Ref. [31]. The region of carbide free bainitic steels was determined with various isothermal and continuous cooled experiments by observing the region of ferrite/pearlite and martensite.
The evaluation of the martensite start temperature of the initial alloy, the martensite start temperature of the retained austenite phase and the occurrence of the F/P phase is done with the tangent method [42] and supported by metallography.
ML models
The ML models used in this work include Gaussian process regression (GPR) [43,44], linear regression, polynomial regression, logistic regression, RFs [45], gradient boosting machines [XGBoost, light gradient boosting machine (LGBM)] [46,47], NNs [48], monotone NNs[49], and SVM[50]. A full list can be seen in Table 3. There are fundamentally two types of models: local models, which predict the target based on its proximity to neighboring data points, and global models, which capture overarching trends in the data.
List of employed ML models
Task | Models |
ML: Machine learning; RF: random forest; SVM: support vector machine; NN: neural network; GPR: Gaussian process regression; RBF: LGBM: light gradient boosting machine. | |
Classification | Logistic regression; RF; XGBoost; SVM; NN |
Regression - local | GPR (RBF kernel); RF; LGBM |
Regression - global | Linear regression; polynomial regression; NN; monotone NN; GPR (RBF kernel + LM); GPR (polynomial kernel); |
Each of the constraints (C1 to C6) corresponds to a classification problem, where the task is to determine whether the input sample should be accepted or rejected. However, the way experimental data is reported in the literature, combined with the nature of the experiments producing this data, results in a significant class imbalance. For example, more data points are reported with a transformation time of less than three hours than with a time greater than three hours, due to the high cost of the experiments. Thus, we use regression models to predict continuous values for constraints C2 to C6, which are then thresholded to classify the samples into binary categories (accept/reject).
Except for C1, where data is sampled from a thermodynamic model, no physics-based models for the remaining constraints significantly outperform ML approaches. Since this work evaluates points across the entire search space defined in Table 2, the model operates in an extrapolative regime, which presents challenges in ensuring reliable predictions beyond the training domain. For constraints C2 to C5, we assume that the quantities follow (at least approximately) a general trend and exhibit monotonicity. For example, if an alloy with 2 wt.% Mn fails to satisfy constraint C4, increasing Mn to 4 wt.% is also assumed to fail C4. This highlights a key challenge for local models, which may struggle to capture such trends in regions with sparse data or when extrapolating beyond the training domain. As a result, global models are better suited for addressing these constraints.
Another issue is the substantial degree of extrapolation required by the models, potentially resulting in inaccurate predictions. Thus, we also require reliable uncertainty estimation to avoid premature exclusion of valid samples. Popular methods for uncertainty estimation include probabilistic and Bayesian approaches (e.g., GPR). One advantage of GPRs with appropriate kernel functions is their ability to express a relationship between distance from the training data and uncertainty [51]. In GPR, predictions take the form of a Gaussian distribution
Uncertainty quantification
In this section, we summarize key sources of uncertainty and how CP provides calibrated uncertainty estimates for both probabilistic and deterministic models. Additionally, we augment the uncertainties with distance measures, e.g., Mahalanobis distance, to detect distribution shifts between the training data and data encountered during deployment. This allows us to adjust uncertainty estimates in extrapolated regions. By doing so, the uncertainty estimates are based on the proximity of the current input to the training data. This adaptation is especially useful for deterministic models, where we initially assume constant uncertainty.
Prediction uncertainties can arise from several sources [52,53], each representing a distinct type of uncertainty, as illustrated in Figure 2. Figure 2A stems from the inherent variability or noise in the data. This uncertainty is caused by random variations or measurement uncertainties, as shown by the scattered data points around the true function.
In contrast, Figure 2B originates from the model’s limited understanding of the data-generating process, e.g., when the model is underfitting the data and is unable to capture the complexity of the underlying function. Additionally, Figure 2C occurs when there is a mismatch between training and test distributions, e.g., when certain regions of the input space are sparsely sampled or fall outside the range of the training data (i.e., extrapolation regions). In such cases, the model exhibits higher uncertainty in underrepresented areas, reflecting its limited knowledge. Accounting for this uncertainty is crucial to prevent overconfident predictions in unexplored regions of the design space, which are underrepresented in the training data. Failure to address this issue may lead to the premature exclusion of potentially valuable compositions. In the following, we describe our proposed method to account for such sources of uncertainty.
To quantify prediction uncertainty, we employ prediction intervals, which define the range within which the true value is expected to fall with a specified probability,
Uncertainty quantification methods often fail to guarantee such calibrated prediction intervals, i.e., intervals that reliably contain the true value with the stated probability [54]. Even GPR, an established probabilistic method for uncertainty estimation, produces uncalibrated prediction intervals in practice due to model misspecification[20,55].
CP
CP[21,22,56] calibrates prediction intervals from an uncertainty heuristic
To illustrate the CP workflow, Figure 3 compares two uncalibrated uncertainty heuristics, the calibration process through CP, and the resulting calibrated uncertainty estimates. Figure 3A shows overconfident estimates
Figure 3. Calibration of uncertainty estimates using CP. Overconfident (A) and underconfident (B) prediction intervals are scaled with the split CP framework (C and D) to achieve a specified coverage with tight bounds (E and F). CP: Conformal prediction.
1. We select an uncertainty heuristic
2. Next, we calculate the deviation between the model’s predictions and the true observed values on a separate calibration set. For regression tasks, we compute residuals
3. We compute the calibration factor
4. For regression models, the prediction intervals are constructed as
For
Extensions for distribution shifts
For the GPR, we use its predictive variance as the uncertainty heuristic u(x). For deterministic models, we assume a uniform uncertainty of u(x)=1. In both cases, CP addresses aleatoric and model uncertainty [Figure 2] by calibrating intervals without requiring additional model adaptations. In the simplest scenario with
where d(x*) reflects the increased uncertainty for distant data points. We analyze several methods to estimate this distance:
To handle the need for a separate calibration set in split CP, which is typically not used during model training, we employ cross CP (CCP) [21], which allows for the full dataset to be used for training. The dataset is divided into K folds, where K-1 folds are used for model training and distance prediction, and the remaining fold is used for calibration. This process is repeated for each fold, with final prediction intervals obtained through averaging.
Modeling workflow and metrics
The modeling workflow, illustrated in Figure 4, evaluates prediction models and distance estimators for computing the constraints (C1-C4, C6). Due to the limited size of the experimental datasets [Table 4], we adopt a 10-fold cross-validation strategy to select the optimal prediction and distance model. The dataset is split into training and test sets, with the test set used exclusively for computing performance metrics. The split is performed based on materials (same alloy compositions), ensuring that no material in the test set overlaps with the training set. For regression tasks with limited data (C2-C6), we improve cross-validation robustness by stratifying based on discretized target with five bins, ensuring a balanced representation across folds to improve model robustness and generalization. Thus, we avoid overly optimistic results by evaluating the model’s ability to extrapolate to novel material compositions, rather than predicting changes driven solely by treatment temperature variations. Table 4 summarizes the number of materials, and the number of total data samples for each constraint. Each training fold is further divided into a "proper training set" and a "calibration set" used for CCP (5-folds). The prediction model is trained using the proper training set only, avoiding contamination of the calibration set used for CP.
Figure 4. Overview of the model selection and evaluation process for the ML models and distance-aware cross-CP. ML: Machine learning; CP: conformal prediction.
Dataset for the constraints; for material-specific quantities, the number of materials is equal to the number of data points
Constraint | Target quantity | Additional features | Number of materials | Number of data points |
C1 | - | - | 800,000 | |
C2 | Co, Ni | 154 | ||
C3 | Co, Cu, Ni, W | 1167 | ||
C5 | Co, Cu, Ni, W | 1,181 | 1,251 | |
C4 | Co, Cu, Ni | 55 | 261 | |
C6 | Co, Cu, Ni, B, W | 194 |
To address prediction target variation across several orders of magnitude - such as bainite transformation times (C4) and critical cooling rates (C6) - we apply a base-10 logarithmic transformation
where
Metrics
For classification models, we report their predictive accuracy. The performance of the regression models is evaluated using the mean absolute error (MAE) and the coefficient of determination
where
The quality of CP uncertainty estimates and distance models is evaluated using the
where
RESULTS AND DISCUSSION
Experimental results
The combined experimental results for the sample produced in the present work are listed in Table 2 and shown in Figure 5. The experimental uncertainty for the martensite start temperature of the initial alloy is 20 ℃; for the retained austenite it is 30 ℃, and for the logarithmic transformation times it is 0.2 log(s). The martensite start temperature (MS) of the initial alloy is indicated by a dashed blue line on both temperature axes, serving as a reference. This temperature defines the lower limit of the isothermal holding temperatureTiso, with the restricted region of Tiso shaded in red. On the vertical axis, the martensite start temperature of the retained austenite MS, RA is shown in blue. The bainite start temperatures of the alloys, already published in Ref. [31], are indicated as green dashed lines. At the bainite start temperature BS, no bainite forms, resulting in MS= MS, RA. As the temperature decreases, carbon enrichment occurs, leading to a stabilizing effect that lowers the martensite start temperature. This decrease continues until the martensite start temperature falls below the detection limit. For consistency, these undetectable points are marked at 50 ℃ in Figure 5. This trend is observed across all produced samples.
Figure 5. Experimental results for logarithmic bainitic transformation time
The bainitic transformation time spans several orders of magnitude due to the strong influence of material composition and thermodynamic parameters on the kinetics of the phase transformation. To better illustrate this behavior, log10(t90%) represents the time required to achieve 90% of the bainitic transformation, which is illustrated in Figure 5. This logarithmic representation provides a clearer comparison of the transformation times across different samples.
The transformation times typically exhibit a characteristic C-shaped behavior, which can be observed in several of the samples. Samples S1 to S5, for example, were specifically designed to study the effect of varying carbon content on transformation kinetics. As shown in Figure 5, increasing the carbon content leads to a significant increase in transformation time. For samples S14, S17, and S18, the bainitic phase transformation did not complete at any isothermal holding temperature, leaving the martensite start temperature (MS) of the initial alloy as the only usable data point. The composition of S14 is identical to that of S7, except for an increased manganese content. This difference highlights the strong influence of manganese on transformation kinetics, as its presence significantly delays the bainitic transformation. The too slow transformation kinetics of S17 and S18 can be explained by their very high carbon content of over 1 wt.%. For the remaining samples, no clear correlation between transformation time and material composition is evident.
The process window for CFB steels, highlighted in green in Figure 5, is defined by the following conditions: The isothermal holding temperature exceeding the martensite start temperature, the martensite start temperature of the retained austenite being below the detection limit, and the transformation completing within 10,800 s. The region between the red and green areas represents a high probability that the isothermal holding temperature within this range will also produce carbide-free bainite. However, this assumption has not been experimentally validated. Depending on the material composition, the process window can vary significantly: it can be quite large (e.g., for samples S9, S11, and S13) or even non-existent (e.g., for samples S14, S17 and S18).
Dataset
The primary classification task in this study is to determine whether the steel type is CFB for a given chemical composition and heat treatment parameters. However, by decomposing the problem into multiple constraints, the available data for each constraint can be expanded by incorporating data from other steel groups, assuming that the underlying physical phenomena are consistent. For instance, the formation of ferrite or pearlite is not influenced by whether or not bainite is subsequently formed. Similarly, the bainite start temperature is independent of whether the steel is bainitic or CFB.
The dataset and models utilized in this study are publicly accessible through the associated Zenodo repository (Code and datasets will be published upon acceptance). The dataset for the austenitization condition is produced with MatCalc on a grid with eight grid points for each dimension and the limits listed in Table 2. The total alloy content limit
For the bainite start temperature, the dataset is taken from Ref. [31]. The dataset for martensite start temperatures
The constraints are a combination of material-specific quantities, which depend solely on composition (C1, C2, C3, C6), and process-dependent quantities (C4, C5). For the process-dependent quantities, this leads to a dataset that is sparse across most dimensions, except for temperature. To provide a clearer representation of the datasets, the number of materials, the number of data points and additional features to C, Si, Mn, Cr, Mo, Al, V and
Modeling results
With the datasets presented in Table 4, we assess the performance of the different ML models listed in Table 3 with 10-fold cross-validation. For each constraint, the best-performing model is selected for subsequent investigations.
The first condition C1, austenitization, is a classification task. The training data is obtained from simulations, and the ML models act as surrogate models to replace time-intensive simulations for novel input compositions. The results for the different ML models are summarized in Table 5, with NNs achieving over 97% accuracy on the test set splits, and the desired
Results for constraint C1 (homogeneity of austenitization) using ML models with 10-fold cross-validation and distance-weighted cross-CP
Metric | Logistic Regression | RF | XGBoost | SVM | |
The best model is underlined. ML: Machine learning; CP: conformal prediction; RF: random forest; SVM: support vector machine; NN: neural network. | |||||
accuracy ( | |||||
cov (90%) | |||||
set size ( |
Figure 6. Calibration curve and confusion matrix for the classification task (C1). Predicted test values versus true values for the constraints treated as regression problems (C2-C6).
For the other constraints, the training data is sourced from experimental results, introducing a higher degree of variability and uncertainty compared to purely simulation-based data as is the case for C1. Additionally, the data does not span the entire design space, requiring the models to extrapolate. To account for distribution shifts, we use distance-aware CP.
The bainite start temperature (C2), martensite start temperature (C3), and martensite start temperature of the retained austenite (C5) are grouped together as they all focus on a transition temperature. For these constraints, we assume that the problem is monotonic with respect to each alloy element. The performance of the ML regression models is listed in Tables 6-8. The test prediction performance of the best ML regression models is shown in Figure 6B-D. Green points correspond to predictions within the 90% coverage region (
Results for constraint C2 (bainite start temperature) using ML models with 10-fold cross-validation and distance-weighted cross-CP
Metric | Linear regression | Polynomial regression | GPR (Polynomial) | NN (Monotone) | GPR (RBF) | RF | LGBM | |
The best model is underlined. ML: Machine learning; CP: conformal prediction; GPR: Gaussian process regression; RBF: LM: linear mean; NN: neural network; RF: random forest; LGBM: light gradient boosting machine; MAE: mean absolute error; PIW: prediction interval width. | ||||||||
R2 ( | ||||||||
MAE ( | ||||||||
cov (90%) | ||||||||
PIW ( |
Results for constraint C3 (martensite start temperature) using ML models with 10-fold cross-validation and distance-weighted cross-CP
Metric | Linear regression | Polynomial regression | GPR (Polynomial) | NN (Monotone) | GPR (RBF) | RF | LGBM | |
The best model is underlined. ML: Machine learning; CP: conformal prediction; GPR: Gaussian process regression; RBF: LM: linear mean; NN: neural network; RF: random forest; LGBM: light gradient boosting machine; MAE: mean absolute error; PIW: prediction interval width. | ||||||||
R | ||||||||
MAE ( | ||||||||
cov (90%) | ||||||||
PIW ( |
Results for constraint C5 (martensite start temperature of retained austenite) using ML models with 10-fold cross-validation and distance-weighted cross-CP
Metric | Linear Regression | Polynomial Regression | GPR (Polynomial) | NN (Monotone) | GPR (RBF) | RF | LGBM | |
The best model is underlined. ML: Machine learning; CP: conformal prediction; GPR: Gaussian process regression; RBF: LM: linear mean; NN: neural network; RF: random forest; LGBM: light gradient boosting machine; MAE: mean absolute error; PIW: prediction interval width. | ||||||||
R | ||||||||
MAE ( | ||||||||
cov (90%) | ||||||||
PIW ( |
When comparing the results for C2, C3 and C5, it is important to consider that we report results for local and global models shown in Table 3. However, local methods are less desirable due to their poor extrapolation behavior beyond the training data. Tree-based models (RF and LGBM) extrapolate using piecewise constant behavior in regions without training data. Also, GPR with an RBF kernel reverts back to the mean of the training data when extrapolating. Both behaviors fail to account for the physical constraints inherent in the system. For GPR with an RBF kernel, this limitation can be addressed by implementing a linear mean (LM) function, ensuring better alignment with the physical knowledge of the constraints. For the three constraints, the inclusion of quadratic features in polynomial regression has led to worse performance compared with linear regression, which can be attributed to overfitting. The coverage for all constraints and models remains close to the desired 90%, validating the reliability of CP. GPR with an RBF kernel and LM shows the best performance in terms of the MAE and the smallest PIW, for all three constraints. It combines the flexibility of local models (such as GPR with RBF, RF, and LGBM), which on average outperform global models, with the ability of global models to effectively capture broader trends. We selected the GPR with an RBF kernel and LM because of the lower MAE and PIW for the final evaluation for these cases. The similarity in model results for the two martensite start temperature problems is expected because they share a significant fraction of their training data.
A key challenge in modeling the boundary condition C4, i.e., the logarithmic bainite transformation time [log10(t90%)], is the scarcity of data for transformation times exceeding the 3-hour constraint. This results in limited coverage for long-duration experiments. Additionally, transformation times span several orders of magnitude, necessitating the use of log-transformed targets to stabilize variance and improve model performance. The underlying behavior is monotonic in the chemical elements and has a C-shape in temperature. The results of the ML models are shown in Table 9, and the best-performing model is visualized in Figure 6E. Notably, data points outside the prediction interval are more frequent in regions of high or low transformation times.
Results for constraint C4 [logarithmic bainite transformation time
Metric | Polynomial regression | GPR (RBF + LM) | GPR (Polynomial) | NN (Monotone) | GPR (RBF) | RF | LGBM | |
The best model is underlined. ML: Machine learning; CP: conformal prediction; GPR: Gaussian process regression; RBF: LM: linear mean; NN: neural network; RF: random forest; LGBM: light gradient boosting machine; MAE: mean absolute error; PIW: prediction interval width. | ||||||||
R | ||||||||
MAE ( | ||||||||
cov (90%) | ||||||||
PIW ( |
While GPR with an RBF kernel achieves the lowest MAE for C4, it struggles with extrapolation, especially when constrained by the limited training data. Assuming that transformation times are approximately monotonic with respect to alloy composition, we can improve linear regression with quadratic temperature features [
The critical cooling rate of ferrite, i.e., C6, also spans several orders of magnitude. For this reason, similar to the bainite transformation time, predicting
Comparison of test results for constraint C6 [logarithmic critical cooling rate of ferrite
Metric | Linear regression | Polynomial regression | GPR (RBF) | GPR (Polynomial) | NN | XGBoost | LGBM | |
The best model is underlined. ML: Machine learning; CP: conformal prediction; GPR: Gaussian process regression; RBF: LM: linear mean; NN: neural network; RF: random forest; LGBM: light gradient boosting machine; MAE: mean absolute error; PIW: prediction interval width. | ||||||||
R | ||||||||
MAE ( | ||||||||
cov (90%) | ||||||||
PIW ( |
The results for C6 reveal notable variability in the models’ performance. Particularly noteworthy are the performances of the GPR with a polynomial kernel and the NN. Both models exhibit a high MAE, indicating poor predictions for certain data points, despite achieving high coverage and a low PIW. This highlights their failure to accurately predict a few critical samples. Among the evaluated methods, local models such as RFs, XGBoost and GPR achieve the lowest MAE scores of 0.43 ± 0.09, 0.44 ± 0.08, and 0.44 ± 0.1, respectively. This suggests that these models are better suited for capturing the nonlinear relationships in the dataset compared to linear or polynomial regression. The coverage of the CP intervals remains stable across all models, averaging close to the desired 90%, with slight variability due to the relatively small dataset size. Notably, RFs and LGBM perform very similarly; however, because of the higher R2 value, the RFs are selected.
To get insight into which features are responsible for the model prediction, SHapley Additive exPlanations (SHAP) analysis is employed [84]. The resulting SHAP values quantify the marginal contribution of each feature, where the sign of the SHAP value indicates whether the feature increases or decreases the prediction, and the magnitude reflects the strength of its influence.
The SHAP values for the prediction models are shown in Figure 7. For condition C1 [Figure 7A], high concentrations of aluminum (Al), silicon (Si), and vanadium (V) increase the likelihood of successful austenitization. However, the effect of carbon (C) remains ambiguous. This is attributed to its dual role: while carbon stabilizes austenite and lowers the austenitization temperature into the valid range, it also promotes carbide formation.
Figure 7. SHAP value analysis of models C1 to C6. Subplots (A) to (F) correspond to models C1 to C6, respectively, illustrating the contribution of each feature to the model predictions. SHAP: SHapley Additive exPlanations.
For the bainite start temperature (C2) [Figure 7B], and the martensite start temperatures (C3 and C5) [Figure 7C and D], the SHAP values exhibit a monotonic and approximately linear dependence on concentration, reflecting the LM function of the employed GPR model. Notably, in Figure 7B, carbon does not yield the highest SHAP value despite its substantial influence per wt.%. This discrepancy arises from feature distribution effects within the dataset. A similar pattern is observed for Al and V, which appear less influential due to their limited high-concentration data points.
For bainite transformation time (C4) [Figure 7E], SHAP values highlight manganese (Mn), C, and nickel (Ni) as the dominant factors contributing to prolonged transformation times, while also revealing the nonlinear influence of temperature. Finally, for the critical cooling rate (C6), the SHAP values in Figure 7F indicate complex and inconclusive trends for several elements, particularly for molybdenum (Mo).
Design space
To evaluate the reduction of the design space, the best-performing models for each constraint were applied to
The results of these evaluations for both heat treatments are summarized in Figure 9. A significant difference is observed in the percentage of predicted CFB points between the isothermal holding and continuous cooling processes. However, this discrepancy does not reflect the full reality, as the constraint C7, shown in Figure 1, was not incorporated in this study due to missing data. This results in an overestimation of design space. Solving this issue will be part of future work, either by building a data-driven literature model or by direct prediction of bainite transformation kinetics. Furthermore, the increase in space from a higher tolerance level is much larger in the continuously cooled case, which can be explained by the higher uncertainty of constraint C6. At a high tolerance, the C6 constraint does not exclude any test points.
Figure 9. Design space reduction for the different heat treatments; see text for description for tolerance.
For further analysis of the constraints, we focus on the isothermal process and select the high tolerance criterion. This approach uses the calibrated uncertainty intervals to avoid prematurely excluding viable design regions. Even with a high tolerance, the design space is only 20% of the search space, which corresponds to an 80% reduction. The final relationship between each input dimension and the acceptance percentage for the different constraints is shown in Figure 10.
The acceptance percentage shown in Figure 10 is the probability that a point in the search space is CFB given that the value of one (in the case of Figure 10) or two (in the case of Figure 11) dimensions in the search space. For the remaining dimensions, values are sampled randomly from uniform distributions. Importantly, this percentage does not indicate the probability that a point is accepted during the process. To derive the overall acceptance rate of 20% as shown in Figure 9, the points must be aggregated, accounting for the occurrence rate.
A horizontal line in the acceptance percentage in Figure 10 for a single dimension indicates no dependency. For instance, C1 (austenitization) is completely independent of
The two-element interaction for the rejection rate is shown in Figure 11. Regardless of the specific alloying elements, low total alloy element concentrations
CONCLUSION
In this work, we present a novel approach to model design spaces for optimization problems with categorical constraints on the example of CFB steels.
• The classification problem (CFB/non-CFB) is split into physically feasible and consistent parts, constraints C1 to C6.
• For these constraints, we produce 21 more experimental data points.
• ML models are applied to predict the constraints, and we address several challenges, including limited data, class imbalances, monotonicity constraints, and robust uncertainty estimation.
• To minimize the exclusion of potentially valuable candidates due to incorrect predictions, we introduced distance-aware CP to produce calibrated uncertainty intervals for both probabilistic and deterministic models. This allows for adjusting confidence to a desired level for classification; in this work, we picked the upper 90th percentile.
• This results in a classifier for CFB. Using mean predictions for constraints reduced the design space to 2% of the total samples. However, incorporating CP-based uncertainty estimates expanded the valid design space to 20%, preserving potentially useful candidates for further exploration while allowing a higher sample efficiency in future design of CFB steel.
In the future, this framework will support the Bayesian optimization of CFB steel. Reliable uncertainty estimation will help to balance the trade-off between reducing the design space and maintaining sufficient exploration.
DECLARATIONS
Acknowledgments
We would like to thank Philipp Retzl and MatCalc Engineering GmbH for their help in setting up high throughput calculations in MatCalc.
Authors’ contributions
Made substantial contributions to conception and design of the study, and performed data analysis, interpretation and writing: Schuscha, B.; Steger, S.
Provided supervision, administrative and technical support, writing assistance and proofreading: Pernkopf, F.; Brandl, D.; Scheiber, D.; Romaner, L.
Availability of data and materials
The datasets and codes used in the present work are available at https://github.com/BerndSchuscha/bainite_boundaries.
Financial support and sponsorship
The authors gratefully acknowledge the financial support under the scope of the COMET program within the K2 Center "Integrated Computational Material, Process and Product Engineering (IC-MPPE)" (Project No. 886385). This program is supported by the Austrian Federal Ministries for Climate Action, Environment, Energy, Mobility, Innovation and Technology (BMK) and for Digital and Economic Affairs (BMDW), represented by the Austrian Research Promotion Agency (FFG), and the federal states of Styria, Upper Austria and Tyrol.
Conflicts of interest
All authors declared that there are no conflicts of interest.
Ethical approval and consent to participate
Not applicable.
Consent for publication
Not applicable.
Copyright
© The Author(s) 2025.
REFERENCES
1. Shahriari, B.; Swersky, K.; Wang, Z.; Adams, R. P.; de Freitas, N. Taking the human out of the loop: a review of Bayesian optimization. Proc. IEEE. 2016, 104, 148-75.
2. Lookman, T.; Balachandran, P.; Xue, D.; Yuan, R. Active learning in materials science with emphasis on adaptive sampling using uncertainties for targeted design. npj. Comput. Mater. 2019, 5, 21.
3. Balachandran, P. V.; Xue, D.; Theiler, J.; Hogden, J.; Lookman, T. Adaptive strategies for materials design using uncertainties. Sci. Rep. 2016, 6, 19660.
4. Shi, B.; Zhou, Y.; Fang, D.; et al. Estimating the performance of a material in its service space via Bayesian active learning: a case study of the damping capacity of Mg alloys. J. Mater. Inf. 2022, 2, 8.
5. Giles, S. A.; Sengupta, D.; Broderick, S. R.; Rajan, K. Machine-learning-based intelligent framework for discovering refractory high-entropy alloys with improved high-temperature yield strength. npj. Comput. Mater. 2022, 8, 235.
6. Khatamsaz, D.; Vela, B.; Singh, P.; Johnson, D.; Allaire, D.; Arróyave, R. Bayesian optimization with active learning of design constraints using an entropy-based approach. npj. Comput. Mater. 2023, 9, 49.
7. Moitzi, F.; Romaner, L.; Ruban, A. V.; Hodapp, M.; Peil, O. E. Ab initio framework for deciphering trade-off relationships in multi-component alloys. npj. Comput. Mater. 2024, 10, 152.
8. Bouquerel, J.; Verbeken, K.; De Cooman, B. C. Microstructure-based model for the static mechanical behaviour of multiphase steels. Acta. Mater. 2006, 54, 1443-56.
9. Bramfitt, B. L. Structure/property relationships in irons and steels. In: Metals Handbook Desk Edition. ASM International; 1998. pp. 153–73.
10. Bhadeshia, H. K. D. H.; Honeycombe, R. W. K. Steels: microstructure and properties. 4th edition. Butterworth-Heinemann; 2017. https://shop.elsevier.com/books/steels-microstructure-and-properties/bhadeshia/978-0-08-100270-4. (accessed 2025-03-10).
11. Alibeyki, M.; Mirzadeh, H.; Najafi, M.; Kalhor, A. Modification of rule of mixtures for estimation of the mechanical properties of dual phase steels. J. Mater. Eng. Perform. 2017, 26, 2683-8.
12. Prawoto, Y.; Djuansjah, J. R. P.; Shaffiar, N. B. Re-visiting the ’rule of mixture’ used in materials with multiple constituting phases: a technical note on morphological considerations in austenite case study. Comput. Mater. Sci. 2012, 65, 528-35.
13. Bouaziz, O.; Buessler, P. Mechanical behaviour of multiphase materials: an intermediate mixture law without fitting parameter. Rev. Met. Paris. 2002, 99, 71-7.
15. Low, A. K. Y.; Vissol-Gaudin, E.; Lim, Y. F.; Hippalgaonkar, K. Mapping pareto fronts for efficient multi-objective materials discovery. J. Mater. Inform. 2023, 3, 11.
16. Khatamsaz, D.; Vela, B.; Singh, P.; Johnson, D. D.; Allaire, D.; Arróyave, R. Multi-objective materials bayesian optimization with active learning of design constraints: design of ductile refractory multi-principal-element alloys. Acta. Mater. 2022, 236, 118133.
17. Quionero-Candela, J.; Sugiyama, M.; Schwaighofer, A.; Lawrence, N. D. Dataset shift in machine learning. The MIT Press; 2009. https://mitpress.mit.edu/9780262545877/dataset-shift-in-machine-learning/. (accessed 2025-03-10).
18. Malinin, A.; Gales, M. Predictive uncertainty estimation via prior networks. arXiv2018, arXiv:1802.10501. Available online: https://doi.org/10.48550/arXiv.1802.10501. (accessed on 10 Mar 2025).
19. Cuomo, S.; Di Cola, V. S.; Giampaolo, F.; Rozza, G.; Raissi, M.; Piccialli, F. Scientific machine learning through physics-informed neural networks: where we are and what’s next. J. Sci. Comput. 2022, 92, 88.
20. Papadopoulos, H. Guaranteed coverage prediction intervals with Gaussian process regression. IEEE. Trans. Pattern. Anal. Mach. Intell. 2024, 46, 9072-83.
22. Angelopoulos AN, Bates S. A gentle introduction to conformal prediction and distribution-free uncertainty quantification. arXiv2021, arXiv:2107.07511. Available online: https://doi.org/10.48550/arXiv.2107.07511. (accessed on 10 Mar 2025).
23. Tibshirani, R. J.; Foygel Barber, R.; Candes, E.; Ramdas, A. Conformal prediction under covariate shift. arXiv2019, arXiv:1904.06019. Available online: https://doi.org/10.48550/arXiv.1904.06019. (accessed on 10 Mar 2025).
24. Caballero, F. G. 12 - Carbide-free bainite in steels. In: Pereloma E, Edmonds DV, editors. Phase Transformations in steels. vol. 1 of Woodhead Publishing Series in Metals and Surface Engineering. Woodhead Publishing; 2012. pp. 436–67.
25. Zhu, K.; Mager, C.; Huang, M. Effect of substitution of Si by Al on the microstructure and mechanical properties of bainitic transformation-induced plasticity steels. J. Mater. Sci. Technol. 2017, 33, 1475-86.
26. Sugimoto, K. Effects of partial replacement of Si by Al on cold formability in two groups of low-carbon third-generation advanced high-strength steel sheet: a review. Metals 2022, 12, 2069.
27. Lukas, H.; Fries, S. G.; Sundman, B. Computational thermodynamics: the calphad method Cambridge University Press; 2007.
28. Kozeschnik, E. Mean-field microstructure kinetics modeling. In: Caballero FG, editor. Encyclopedia of Materials: Metals and Alloys. Oxford: Elsevier; 2022. pp. 521–6.
29. van Bohemen, S. M. C. Bainite and martensite start temperature calculated with exponential carbon dependence. Mater. Sci. Technol. 2012, 28, 487-95.
30. Leach, L.; Kolmskog, P.; Höglund, L.; Hillert, M.; Borgenstam, A. Use of Fe-C information as reference for alloying effects on BS. Metall. Mater. Trans. A. 2019, 50, 4531-40.
31. Schuscha, B.; Brandl, D.; Romaner, L.; et al. Predictive modeling of the Bainite start temperature using Bayesian inference. Acta. Mater. 2024. DOI: 10.2139/ssrn.4930824.
32. Leach, L.; Kolmskog, P.; Höglund, L.; Hillert, M.; Borgenstam, A. Critical driving forces for formation of Bainite. Metall. Mater. Trans. A. 2018, 49, 4509-20.
33. Lu, Q.; Liu, S.; Li, W.; Jin, X. Combination of thermodynamic knowledge and multilayer feedforward neural networks for accurate prediction of MS temperature in steels. Mater. Design. 2020, 192, 108696.
34. Li, M. V.; Niebuhr, D. V.; Meekisho, L. L.; Atteridge, D. G. A computational model for the prediction of steel hardenability. Metall. Mater. Trans. B. 1998, 29, 661-72.
35. Martin, H.; Amoako-Yirenkyi, P.; Pohjonen, A.; Frempong, N. K.; Komi, J.; Somani, M. Statistical modeling for prediction of CCT diagrams of steels involving interaction of alloying elements. Metall. Mater. Trans. B. 2020, 52, 223-35.
36. Geng, X.; Wang, H.; Xue, W.; et al. Modeling of CCT diagrams for tool steels using different machine learning techniques. Comput. Mater. Sci. 2020, 171, 109235.
37. Minamoto, S.; Tsukamoto, S.; Kasuya, T.; Watanabe, M.; Demura, M. Prediction of continuous cooling transformation diagram for weld heat affected zone by machine learning. Sci. Technol. Adv. Mat. 2022, 2, 402-15.
38. Huang, X.; Wang, H.; Xue, W.; et al. A combined machine learning model for the prediction of time-temperature-transformation diagrams of high-alloy steels. J. Alloys. Compd. 2020, 823, 153694.
39. Povoden-Karadeniz, E. MatCalc thermodynamic steel database, version 2.061, 2023. https://www.matcalc.at/images/stories/Download/Database/mc_fe_v2061.tdb. (accessed 2025-03-10).
40. Presoly, P.; Gerstl, B.; Bernhard, C.; et al. Primary carbide formation in tool steels: potential of selected laboratory methods and potential of partial premelting for the generation of thermodynamic data. Steel. Res. Int. 2022, 94, 2200503.
41. Presoly, P.; Pierer, R.; Bernhard, C. Identification of defect prone peritectic steel grades by analyzing high-temperature phase transformations. Metall. Mater. Trans. A. 2013, 44, 5377-88.
42. Verein Deutscher Eisenhüttenleute Unterausschuss für Metallographie, Werkstoffanalytik und -simulation. Guidelines for preparation, execution and evaluation of dilatometric transformation tests on iron alloys. Verlag Stahleisen GmbH; 1998. https://books.google.com/books/about/Guidelines_for_preparation_execution_and.html?id=R6-d0AEACAAJ. (accessed 2025-03-10).
43. Williams, C. K. I.; Rasmussen, C. Gaussian processes for regression. In: Advances in neural information processing systems. MIT Press; 1995. https://proceedings.neurips.cc/paper/1995/hash/7cce53cf90577442771720a370c3c723-Abstract.html. (accessed 2025-03-10).
46. Friedman, J.; Hastie, T.; Tibshirani, R. Additive logistic regression: a statistical view of boosting (with discussion and a rejoinder by the authors). Ann. Statist. 2000, 28, 337-407.
47. Fiedler, C.; Scherer, C. W.; Trimpe, S. Practical and rigorous uncertainty bounds for Gaussian process regression. AAAI. Conf. Artif. Intell. 2021, 35, 7349-47.
48. Goodfellow, I.; Bengio, Y.; Courville, A. Deep Learning. MIT Press; 2016. https://www.deeplearningbook.org/. (accessed 2025-03-10).
49. Kitouni, O.; Nolte, N.; Williams, M. Expressive monotonic neural networks. arXiv2023, arXiv:2307.07512. Available online: https://doi.org/10.48550/arXiv.2307.07512. (accessed on 10 Mar 2025).
50. Boser, B. E.; Guyon, I. M.; Vapnik, V. N. A training algorithm for optimal margin classifiers. In: Proceedings of the fifth annual workshop on Computational learning theory. Association for Computing Machinery, 1992; pp. 144–52.
51. D’Angelo, F.; Henning, C. On out-of-distribution detection with Bayesian neural networks. arXiv2021, arXiv:2110.06020. Available online: https://doi.org/10.48550/arXiv.2110.06020. (accessed on 10 Mar 2025).
52. Hüllermeier, E.; Waegeman, W. Aleatoric and epistemic uncertainty in machine learning: an introduction to concepts and methods. Mach. Learn. 2021, 110, 457-506.
53. Gruber, C.; Schenk, P.; Schierholz, M.; Kreuter, F.; Kauermann, G. Sources of uncertainty in machine learning - a statisticians’ view. arXiv2023, arXiv:2305.16703. Available online: https://doi.org/10.48550/arXiv.2305.16703. (accessed on 10 Mar 2025).
54. Tran, K.; Neiswanger, W.; Yoon, J.; Zhang, Q.; Xing, E.; Ulissi, Z. W. Methods for comparing uncertainty quantifications for material property predictions. Mach. Learn. Sci. Technol. 2020, 1, 025006.
55. Lahlou, S.; Jain, M.; Nekoei, H.; et al. DEUP: direct epistemic uncertainty prediction. arXiv2021, arXiv:2102.08501. Available online: https://doi.org/10.48550/arXiv.2102.08501. (accessed on 10 Mar 2025).
56. Shafer, G.; Vovk, V. A tutorial on conformal prediction. arXiv2007, arXiv:0706.3188. Available online: https://doi.org/10.48550/arXiv.0706.3188. (accessed on 10 Mar 2025).
57. Papadopoulos, H.; Proedrou, K.; Vovk, V.; Gammerman, A. Inductive confidence machines for regression. In: Machine learning: ECML 2002: 13th European conference on machine learning, Helsinki, Finland, August 19-23, 2002. Springer, 2002; pp. 345–56.
58. Papadopoulos, H.; Vovk, V.; Gammerman, A. Regression conformal prediction with nearest neighbours. J. Artif. Intell. Res. 2011, 40, 815-40.
59. Bishop, C. M. Pattern recognition and machine learning. Berlin, Heidelberg: Springer-Verlag; 2006. https://link.springer.com/book/9780387310732. (accessed 2025-03-10).
60. Panaretos, V. M.; Zemel, Y. Statistical aspects of Wasserstein distances. Annu. Rev. Stat. Appl. 2019, 6, 405-31.
62. Luo, C.; Zhan, J.; Wang, L.; Yang, Q. Cosine normalization: using cosine similarity instead of dot product in neural networks. arXiv2017, arXiv:1702.05870. Available online: https://doi.org/10.48550/arXiv.1702.05870. (accessed on 10 Mar 2025).
63. Damon, J.; Mühl, F.; Dietrich, S.; Schulze, V. A comparative study of kinetic models regarding Bainitic transformation behavior in carburized case hardening steel 20MnCr5. Metall. Mater. Trans. A. 2018, 50, 104-17.
64. Kumnorkaew, T.; Lian, J.; Uthaisangsuk, V.; Bleck, W. Kinetic model of isothermal Bainitic transformation of low carbon steels under ausforming conditions. Alloys 2022, 1, 93-115.
65. Lin, S.; Borgenstam, A.; Stark, A.; Hedström, P. Effect of Si on bainitic transformation kinetics in steels explained by carbon partitioning, carbide formation, dislocation densities, and thermodynamic conditions. Mater. Charact. 2022, 185, 111774.
66. Luzginova, N. V.; Zhao, L.; Wauthier, A.; Sietsma, J. The kinetics of the isothermal Bainite formation in 1 In: Microalloying for New Steel Processes and Applications. vol. 500 of Materials Science Forum. Trans Tech Publications Ltd; 2005. pp. 419–28.
67. Morawiec, M.; Ruiz-Jimenez, V.; Garcia-Mateo, C.; Grajcar, A. Thermodynamic analysis and isothermal bainitic transformation kinetics in lean medium-Mn steels. J. Therm. Anal. Calorim. 2020, 142, 1709-19.
68. Pei, W.; Liu, W.; Zhang, Y.; Qie, R.; Zhao, A. Study on kinetics of transformation in medium carbon steel Bainite at different isothermal temperatures. Materials 2021, 14, 2721.
69. Quidort, D.; Bréchet, Y. The role of carbon on the kinetics of bainite transformation in steels. Scr. Mater. 2002, 47, 151-6.
70. Quidort, D.; Brechet, Y. J. M. A model of isothermal and non isothermal transformation kinetics of bainite in 0.5% C steels. ISIJ. Int. 2002, 42, 1010-7.
71. Babasafari, Z.; Pan, A. V.; Pahlevani, F.; Moon, S. C.; Du Toit, M.; Dippenaar, R. Kinetics of bainite transformation in multiphase high carbon low-silicon steel with and without pre-existing martensite. Metals 2022, 12, 1969.
72. Ravi, A.; Kumar, A.; Herbig, M.; Sietsma, J.; Santofimia, M. J. Impact of austenite grain boundaries and ferrite nucleation on bainite formation in steels. Acta. Mater. 2020, 188, 424-34.
73. Singh, S. B.; Bhadeshia, H. K. D. H. Quantitative evidence for mechanical stabilization of bainite. Mater. Sci. Technol. 1996, 12, 610-2.
74. Sourmail, T.; Smanio, V. Influence of cobalt on Bainite formation kinetics in 1 Pct C steel. Metall. Mater. Trans. A. 2013, 44, 1975-8.
75. van Bohemen, S. M. C.; Sietsma, J. Modeling of isothermal bainite formation based on the nucleation kinetics. Int. J. Mater. Res. 2008, 99, 739-47.
76. van Bohemen, S. M. C.; Sietsma, J. The kinetics of bainite and martensite formation in steels during cooling. Mater. Sci. Eng. A. 2010, 527, 6672-6.
77. van Bohemen, S. M. C.; Hanlon, D. N. A physically based approach to model the incomplete bainitic transformation in high-Si steels. Int. J. Mater. Res. 2012, 103, 987-91.
78. van Bohemen, S. M. C. Bainite growth retardation due to mechanical stabilisation of austenite. Materialia 2019, 7, 100384.
79. Gao, B.; Tan, Z.; Tian, Y.; et al. Accelerated isothermal phase transformation and enhanced mechanical properties of railway wheel steel: the significant role of pre-existing Bainite. Steel. Res. Int. 2022, 93, 2100494.
80. Kang, J.; Zhang, F. C.; Yang, X. W.; Lv, B.; Wu, K. M. Effect of tempering on the microstructure and mechanical properties of a medium carbon bainitic steel. Mater. Sci. Eng. A. 2017, 686, 150-9.
81. Sage, A. M. Atlas of continuous cooling transformation diagrams for vanadium steels. Vanitec Publication; 1985. https://vanitec.org/technical-library/paper/atlas-of-continuous-cooling-transformation-diagrams-for-vanadium-steels. (accessed 2025-03-10).
82. Vander Voort, G. F. Atlas of time-temperature diagrams for irons and steels. ASM International; 1991. https://app.knovel.com/kn/resources/kpATTDIS05/toc. (accessed 2025-03-10).
83. United States Steel Corporation. Atlas of isothermal transformation Diagrams: 1953 Supplement. 1953. https://books.google.com/books/about/Atlas_of_Isothermal_Transformation_Diagr.html?id=8aVTAAAAMAAJ. (accessed 2025-03-10).
84. Lundberg, S. M.; Lee, S. I. A unified approach to interpreting model predictions. arXiv2017, arXiv:1705.07874. Available online: https://doi.org/10.48550/arXiv.1705.07874. (accessed 10 Mar 2025).
85. Ravi, A. M.; Navarro-López, A.; Sietsma, J.; Santofimia, M. J. Influence of martensite/austenite interfaces on bainite formation in low-alloy steels below Ms. Acta. Mater. 2020, 188, 394-405.
86. Tian, J.; Xu, G.; Zhou, M.; Hu, H.; Xue, Z. Effects of Al addition on bainite transformation and properties of high-strength carbide-free bainitic steels. J. Iron. Steel. Res. Int. 2019, 26, 846-55.
Cite This Article
How to Cite
Schuscha, B.; Steger, S.; Pernkopf, F.; Brandl, D.; Romaner, L.; Scheiber, D. Uncertainty aware design space modeling for sample efficiency in material design of bainitic steels. J. Mater. Inf. 2025, 5, 28. http://dx.doi.org/10.20517/jmi.2024.90
Download Citation
Export Citation File:
Type of Import
Tips on Downloading Citation
Citation Manager File Format
Type of Import
Direct Import: When the Direct Import option is selected (the default state), a dialogue box will give you the option to Save or Open the downloaded citation data. Choosing Open will either launch your citation manager or give you a choice of applications with which to use the metadata. The Save option saves the file locally for later use.
Indirect Import: When the Indirect Import option is selected, the metadata is displayed and may be copied and pasted as needed.
About This Article
Copyright
Data & Comments
Data
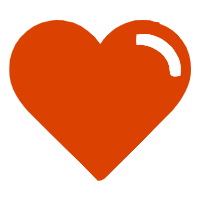
Comments
Comments must be written in English. Spam, offensive content, impersonation, and private information will not be permitted. If any comment is reported and identified as inappropriate content by OAE staff, the comment will be removed without notice. If you have any queries or need any help, please contact us at [email protected].