Understanding oxidation resistance of Pt-based alloys through computations of Ellingham diagrams with experimental verifications
Abstract
Thermodynamic calculations of Ellingham diagrams and the forming oxides have been performed relevant to the Pt-based alloys Pt82Al12M6 (M = Cr, Hf, Pt, and Ta). The predicted Ellingham diagrams indicate that the elements Hf and Al are easy to oxidize, followed by Ta and Cr, while Pt is extremely difficult to oxidize. Oxidation experiments characterized by X-ray diffraction (XRD) and electron probe micro-analyzers verify the present thermodynamic predictions, showing that the best alloy with superior oxidation resistance is Pt82Al12Cr6, followed by Pt88Al12 due to the formation of the dense and continuous α-Al2O3 scale on the surface of alloys; while the worse alloy is Pt82Al12Hf6 followed by Pt82Al12Ta6 due to drastic internal oxidation and the formation of deleterious HfO2, AlTaO4, and Ta2O5. The present work, combining computations with experimental verifications, provides a fundamental understanding and knowledgebase to develop Pt-based superalloys with superior oxidation resistance that can be used in ultra-high temperatures.
Keywords
INTRODUCTION
Aiming to design ultra-high-temperature materials for use in harsh environments has led to the development of Pt-based superalloys. These superalloys are superior to Ni-based superalloys since Pt has a higher melting point (2,042 K for Pt vs. 1,728 K for Ni[1]) and is more chemically inert for outstanding oxidation resistance, c.f., the predicted Ellingham diagrams[2] in the present work. Currently, a higher application temperature is urgently needed in gas turbine sections to improve engine efficiency and reduce fuel consumption and carbon dioxide emissions for a greater thrust. For example, the current application temperature of Pt-based superalloys can be extended to 1,350 °C (1,623 K)[3]. Although Pt-based alloys are expensive, they are the most reliable materials under ultrahigh temperatures and are widely used as bonding coating alloys in the thermal barrier coating (TBC) system and in the aerospace engine nozzle. The excellent oxidation resistance of Pt-based superalloys is their great advantage. The oxidation behavior of pure Pt has been fully investigated[4]; however, the oxidation of Pt-Al-based alloys is far from fully understood.
The Pt-Al system is one of the widely used superalloys, fueling up considerable studies such as the strength and creep properties[5,6]. The mechanism of oxidation resistance for pure Pt and Pt-Al alloys is quite different. It shows that the Pt-Al alloy can be further stabilized at high temperatures in terms of the L12-based γ’ phase by adding alloying elements such as Cr, Hf, and Ta. Especially, Cr can form the dense and continue Cr2O3 coating to provide a protective scale on Cr-containing alloys; Hf is a reactive element to reduce the growth of a thermally grown Al2O3 scale in alloys such as the NiAlCr and NiAlPt[7]; additionally, Ta can hinder ion diffusion and improve oxidation resistance in, e.g., the Ni-10Al alloy[8]. One of the purposes of the present work is to develop a series of Pt-Al-based alloys with strong oxidation resistance used as bonding coating in the TBC system. Notably, oxidation resistance for an alloy of interest is an important indicator to determine whether it can be applied to high temperatures or not[9,10], with the best oxide being α-Al2O3 (represented by Al2O3 in the present work if no further explanation), which will be formed on the surface of Al-containing alloys at high temperatures (> 1,100 °C)[11-13]. Here, Al2O3 usually acts as the oxidation resistance barrier of the alloys at high temperatures, thus further preventing oxidation inside the alloys[14,15].
In the present work, four alloying elements, Al, Cr, Hf, and Ta, are selected to investigate oxidation resistance of the Pt-based alloys. The forming mechanism of Al2O3 and other oxides is understood by the predicted Ellingham diagrams[2] with experimental verifications. Here, the free energy (or partial pressure of gas species) versus temperature diagram, i.e., the Ellingham diagram, is a predictive tool to tailor thermodynamic stability of oxides that form in the present Pt-based alloys[16]. In addition, the oxidation kinetic curves are also measured to examine the formation rates of oxides. The present computations of Ellingham diagrams with experimental verifications provide fundamentals to develop Pt-based superalloys with superior oxidation resistance that can be used in ultra-high temperatures.
MATERIALS AND METHODS
Ellingham diagram
An Ellingham diagram[2] is a plot regarding the change of the standard Gibbs energy (ΔGo) as a function of temperature for a given reaction, evaluating the equilibrium phases obtained by chemical reactions. In the present work, the calculated Ellingham diagrams can judge whether the Pt-based alloys (i.e., metals M = Al, Cr, Hf, Pt, and/or Ta) can be oxidized or not in terms of the following two reactions (scenarios),
where s, l, and g indicate the solid, liquid, and gas phases, respectively. Here, (i) ay > bx, indicating the oxidation is from MaOb to MxOy; (ii) the oxygen gas species O2 is selected due to its extreme dominance in comparison with the other oxygen species of O1 and O3[17]; and (iii) the reactions are under the total pressure of 1 atm with 1 mole of O2. Under the assumptions of (a) ideal gas with O2 being the dominant gas species and (b) the activities of liquids and solids as unity, the ΔGo of equation (1) or (2) at equilibrium can be determined by the activity of oxygen (
where R is the gas constant, and T is the absolute temperature. By setting the reference pressure and the total pressure Pref = Ptot = 1 atm (105 Pa), then,
Reactions of one mole of O2 (g) from metal and/or metal oxide to metal oxide. The mole fractions of oxygen content, x(O), in oxides, and the
No. | Metals | x(O) | Reactions | |
1 | Pt | 0.50 to 0.67 | 1.279e + 08 | 2PtO + O2 = 2PtO2 |
2 | Cr | 0.60 to 0.71 | 1.151e + 08 | |
3 | Pt | 0.50 | 2.036e + 07 | 2Pt + O2 = 2PtO |
4 | Ni | 0.50 | 1.306e - 04 | 2Ni + O2 = 2NiO |
5 | Cr | 0.60 | 4.660e - 14 | |
6 | Ta | 0.71 | 4.426e - 16 | |
7 | Al, Ta | 0.60 to 0.67 | 1.939e - 16 | |
8 | Al | 0.60 | 8.256e - 24 | |
9 | Hf | 0.67 | 1.553e - 25 | Hf + O2 = HfO2 |
Thermodynamic database and thermodynamic calculations
Calculating Ellingham diagrams requires a thermodynamic database (TDB) for the present
The enthalpy of formation (ΔH) of equation (4) was predicted by the density functional theory (DFT)-based first-principles calculations using the Vienna Ab initio Simulation Package (VASP)[21]. The ion-electron interaction was described by the projector augmented wave (PAW) method[22], and the exchange-correlation (X-C) functionals were described by the local density approximation (LDA)[23] and the generalized gradient approximation (GGA) improved for densely packed solids and their surfaces (PBEsol)[24]. Other details of first-principles calculations are given in Table 2, as well as the default settings used by the software DFT Tool Kits (DFTTK)[25], including crystal structures of the three oxides, the used k-point meshes, the employed plane-wave cutoff energy, and the selected potentials for elements Al, Ta, and O. In addition, Table 2 also lists the DFT results reported by the Materials Project (MP)[26] and the Open Quantum Materials Database (OQMD)[27] using the X-C functional of GGA-PBE[28]. It shows that the (ΔH) value by PBEsol (-13490 J per 6-mole-atoms) is roughly in the middle of these (ΔH) values and hence was selected for equation (4) and implemented into SSUB5 together with the heat capacity of AlTaO4 estimated by the Neumann-Kopp rule[29,30].
Enthalpy of formation (H) for the reaction of “Al2O3 + Ta2O5 = AlTaO4” based on DFT-based first-principles calculations at 0 K according to MP[26], OQMD[27], and the present work, where the IDs of MP and OQMD are also listed. The final cutoff energy for accurate energy is 520 eV, and the other details are the default ones adopted by DFTTK[25]
Oxides | Space group | ID and notes | X-C functionals | Total energy (eV/atom) | H (J/6-mole-atoms) |
Al2O3 (4 × 4 × 4)a | MP-1143 | PBE | -7.48 | ||
OQMD-1234774 | PBE | -7.477 | |||
This work | PBEsol | -7.388 | |||
This work | LDA | -8.313 | |||
Ta2O5 (6 × 5 × 1)b | Pmmn | MP-1539317 | PBE | -9.77 | |
OQMD-1739439 | PBE | -9.759 | |||
This work | PBEsol | -9.621 | |||
This work | LDA | -10.605 | |||
AlTaO4 (4 × 4 × 5)c | C12/m1 | MP-14333 | PBE | -8.84 | -13990 |
OQMD-6370 | PBE | -8.837 | -16692 | ||
This work | PBEsol | -8.714 | -13490d | ||
This work | LDA | -9.669 | -11091 |
In the present work, thermodynamic calculations were performed by using the Thermo-Calc software[31] and the presently built TDB (i.e., the TDB file, as shown in the Supplementary Material). Rather than calculating ΔGo directly for each reaction in Table 1, equilibrium calculations were performed in the present work using the following conditions for each reaction: (i) the total pressure fixed at 1 atm; (ii) 1 mole of O2; and (iii) the dormant gas and other phases, which were excluded in the reactions of interest; see more details and a macro tcm file in our recent work[18].
Experiments
The ingots were prepared by arc-melting. Then, the ingots were subjected to vacuum heat treatments. It was determined that the alloys include the L12-type γ’-Pt3Al phase. The square samples with the dimensions of
Table 3 shows the chemical composition of these alloys by the photoelectric direct reading spectrograph. Figure 1 shows the overall oxidation kinetic curves of the four different samples at 1,300 °C. The type of oxidation kinetics of these samples is parabolic. As it can be observed, the oxidation rate is initially high and gradually lowers with increasing oxidation time. NiCoCrAlY is the current most used bonding coating alloy in the TBC system. The melting point of the NiCoCrAlY alloy is only ~1,400 °C. The oxidation layer of NiCoCrAlY alloys is easily peeled off and disabled quickly at 1,300 °C.
Figure 1. The oxidation kinetics of four Pt-based alloys and NiCoCrAlY after oxidation at 1,300 °C for 100 h in an air atmosphere.
Measured chemical compositions of the as-prepared alloys
Alloys | Al (at. %) | M (at. %) | Pt (at. %) |
Pt88Al12 | 11.78 | 0 | Balance |
Pt82Al12Cr6 | 11.82 | 6.21 | Balance |
Pt82Al12Hf6 | 11.64 | 6.17 | Balance |
Pt82Al12Ta6 | 11.72 | 6.06 | Balance |
In addition, the Pt82Al12Cr6 and Pt88Al12 alloys show a relatively stable stage after exposure for 20 h. Note that in the diffusion-controlled thickening process of alumina (Al2O3), the mass gain of the Al2O3 scale should follow a parabolic law at the test temperatures according to the classical oxidation theory[32]. The results of oxidation kinetics regarding mass gain with respect to oxidation time can be approximately expressed as[33]:
where Δm is mass gain of the sample in mg, A is the surface area of the sample in cm2, kp is the parabolic rate constant in mg2/(cm4·h), and t is the oxidation time.
RESULTS AND DISCUSSION
Ellingham diagrams to tailor oxidation resistance
Figure 2 shows the predicted Ellingham diagrams for the nine reactions, as shown in Table 1. The lower the
Figure 2. Predicted Ellingham diagrams for 9 reactions (see also Table 1) with one mole of oxygen gas (mainly the O2) and the total pressure fixed at 1 atm. Here, the reaction No. 4 to form NiO is for reference only.
As two examples, Figure 3 shows the formed phases as a function of
Figure 3. Formed phases for two representative alloys of Pt82Al12Cr6 and Pt82Al12Hf6 at 1,300 °C as a function of the partial pressure of O2 gas (
Summary of the oxides formed in the Pt-rich alloys at 1,300 °C according to the present thermodynamic calculations and the present oxidation experiments
Verifications by oxidation experiments
Pt88Al12
Figure 4 shows the patterns of X-ray diffraction (XRD) of the Pt88Al12 alloy, which was oxidized at 1,300 °C. Both Al2O3 and fcc-based Pt are identified by XRD. Moreover, a few metastable scales of θ-Al2O3 are also detected, mainly due to the incomplete phase transition to the stable α-Al2O3 during the cooling process of the sample[34]. Note that the present thermodynamic calculations predict only the stable α-Al2O3, albeit four kinds of Al2O3 (α-, δ-, γ-, and κ-Al2O3) are included in the SSUB5 database; see also Table 4.
Figure 4. Surface XRD results of the alloy Pt88Al12 after oxidation at 1,300 °C for 100 h. XRD: X-ray diffraction.
Figure 5 shows the EPMA elemental maps of Pt88Al12 oxidized at 1,300 °C for 100 h. Obviously, the light areas are fcc phase (mainly Pt), and the dark areas are Al2O3 according to the EPMA analysis; see Figure 5A. The Al2O3 layer is not fully dense. Figure 6 shows the cross-sectional EPMA of Pt88Al12 after oxidation at 1,300 °C for 100 h. The oxide scale on the Pt88Al12 surface is continuous and intact, which is from 10.1 to 13.3 μm in thickness, as shown in Figure 6A. However, the discontinuous Pt-rich layer is also observed outside the oxide layer, which is probably due to the deposition of the Pt vapor above 1,000 °C[10].
Figure 5. Surface morphologies and distribution of elements from EPMA of the alloy Pt88Al12 after 100 h oxidation in air at 1,300 °C. (A) Surface morphology; (B1)-(B3) Pt, Al, and O map distribution, respectively; (C) Linear distribution of Pt, Al, and O.
Figure 6. Cross-sectional morphologies and distribution of elements from EPMA EPMA mapping images Pt88Al12 after 100 h oxidation in air at 1,300 °C. (A) Cross-sectional morphology; (B1)-(B3) Pt, Al, and O map distribution, respectively; (C) Linear distribution of Pt, Al, and O. EPMA: Electron probe micro-analyzer.
Pt82Al12Cr6
Figure 7 shows the XRD patterns of the Pt82Al12Cr6 alloy after oxidation at 1,300 °C for 100 h. It reveals that the α-Al2O3 is the major phase in the oxide layer with small peaks identified as Pt, indicating that Cr promotes the formation of α-Al2O3. Different from the case of Pt88Al12, after oxidation at 1,300 °C for 100 h, the Pt82Al12Cr6 alloy exhibits a smooth and dense surface. No spallation or crack is observed, and the Al2O3 scale adheres well with the base alloy [Figure 8]. Comparing and analyzing the XRD and EPMA results on the surface of the sample after oxidation in Figures 7 and 8, respectively, indicates that a dense Al2O3 layer forms on the surface of Pt82Al12Cr6, and the surface of the alloy does not have the element Cr.
Figure 7. Surface XRD results of the alloy Pt82Al12Cr6 after oxidation at 1,300 °C for 100 h. XRD: X-ray diffraction.
Figure 8. Surface morphologies at EPMA of the alloy Pt82Al12Cr6 after 100 h oxidation in air at 1,300 °C. (A) Surface morphology; (B1)-(B4) Pt, Al, O, and Cr map distribution, respectively; (C) Linear distribution of Pt, Al, O, and Cr. EPMA: Electron probe micro-analyzer.
Figure 9A shows that the thickness of the Al2O3 scale is about 7.3 μm, which is less than the scale of the
Figure 9. Cross-sectional morphologies and distribution of elements from EPMA EPMA mapping images Pt82Al12Cr6 after 100 h oxidation in air at 1,300 °C. (A) Cross-sectional morphology; (B1)-(B4) Pt, Al, O, and Cr map distribution, respectively; (C) Linear distribution of Pt, Al, O, and Cr. EPMA: Electron probe micro-analyzer.
Thermodynamic calculations [Figure 3] indicate that Cr2O3 will be formed in Pt82Al12Cr6 but at higher
Pt82Al12Hf6
Figure 10 shows the XRD results of Pt82Al12Hf6 after oxidation at 1,300 °C for 100 h, confirming the presence of Al2O3, HfO2, and a small amount of Pt on the surface after oxidation. By analyzing the EPMA results, as shown in Figure 11, we observe that the dark area mainly contains the element Hf, which is coincident with the elements O and Al. It is possible that the oxide (Al, Hf)2O3 has formed due to the solid solution of Hf in Al2O3. Therefore, we presume the presence of Al2O3 and HfO2 in the dark region, along with Pt, and possibly trace amounts of PtO2 in the bright region. In addition, it is possible that trace amounts of PtO2 are present on the surface of Pt82Al12Hf6 after oxidation at very high
Figure 10. Surface XRD results of the alloy Pt82Al12Hf6 after oxidation at 1,300 °C for 100 h. XRD: X-ray diffraction.
Figure 11. Surface morphologies at EPMA of the alloy Pt82Al12Hf6 after 100 h oxidation in air at 1,300 °C. (A) Surface morphology; (B1)-(B4) Pt, Al, O, and Hf map distribution, respectively; (C) Linear distribution of Pt, Al, O, and Hf. EPMA: Electron probe micro-analyzer.
Thermodynamic calculations show that only Al2O3 and HfO2 can form [Figure 3] due to insolubility of Hf in Al2O3 in the present database and the very high
From the cross-sectional EPMA mapping images of Pt82Al12Hf6, Figure 12A shows that no dense oxide layer is observed, but it forms internal oxides. Figure 12B shows the composition map distribution of these oxides from the surface to the alloy interior. Figure 12B and C reveals that Al and Hf are combined with O. In addition, the dispersive dark appears on the oxide regions with rich Al and O, along with some Hf, observed at a distance of about 4 μm and beyond from the surface. Due to the segregation of alloying elements in oxides, the matrix is almost pure Pt.
Figure 12. Cross-sectional morphologies and distribution of elements from EPMA EPMA mapping images Pt82Al12Hf6 after 100 h oxidation in air at 1,300 °C. (A) Cross-sectional morphology; (B1)-(B4) Pt, Al, O, and Hf map distribution, respectively; (C) Linear distribution of Pt, Al, O, and Hf. EPMA: Electron probe micro-analyzer.
In comparison with the Pt88Al12 and Pt82Al12Cr6 alloys, Pt82Al12Hf6 shows a worse oxidation resistance due to the extremely easy formation of HfO2, as indicated by the Ellingham diagrams [Figure 2], resulting in oxidation inside the alloy and the element Pt inside the scale, probably due to a decomposition of PtO2 at the scale surface after oxidation at 1,300 °C[10].
Pt82Al12Ta6
Figure 13 shows the XRD patterns of Pt82Al12Ta6, which is oxidized at 1,300 °C for 100 h. The oxide layer consists of Al2O3, AlTaO4, Ta2O5, and PtO2, agreeing with thermodynamic calculations (except for the formation of a trace amount of PtO2), c.f., Table 4.
Figure 13. Surface XRD results of the alloy Pt82Al12Ta6 after oxidation at 1,300 °C for 100 h. XRD: X-ray diffraction.
These results are also consistent with the EPMA mapping analysis [Figure 14], where the dark region is
Figure 14. Surface morphologies at EPMA of the alloy Pt82Al12Ta6 after 100 h oxidation in air at 1,300 °C. (A) Surface morphology; (B1)-(B4) Pt, Al, O, and Ta map distribution, respectively; (C) Linear distribution of Pt, Al, O, and Ta. EPMA: Electron probe micro-analyzer.
Figure 15 shows the cross-section EPMA mapping of the oxidized samples, indicating that no dense oxides on the sample surface are observed. Figure 15B shows that at the interior, both Al and Ta are found in combination with O. According to Figure 15C, the dispersive gray areas are enriched with O and Ta, but almost no Al, which could be identified as Ta2O5. The dark oxidized regions with enriched Al and O, along with some Ta, are observed in the interior of the alloy, indicating the formation of Al2O3, AlTaO4, and
Figure 15. Cross-sectional morphologies and distribution of elements from EPMA EPMA mapping images Pt82Al12Ta6 after 100 h oxidation in air at 1,300 °C. (A) Cross-sectional morphology; (B1)-(B4) Pt, Al, O, and Ta map distribution, respectively; (C) Linear distribution of Pt, Al, O, and Ta. EPMA: Electron probe micro-analyzer.
CONCLUSIONS
The present work investigates the forming mechanism of oxides in the Pt-based alloys Pt82Al12M6 (M = Cr, Hf, Pt, and Ta) in terms of thermodynamic calculations with experimental verifications. The presently predicted Ellingham diagrams indicate the metals Hf and Al are easy to oxidize, followed by the metals Ta and Cr, while Pt is extremely difficult to oxidize in terms of thermodynamics. Oxidation experiments are characterized by XRD and EPMA, verifying the present thermodynamic predictions and showing that the best alloy with superior oxidation resistance is Pt82Al12Cr6 followed by Pt88Al12 by forming the dense and continuous α-Al2O3 scale on the surface of alloys after oxidation; while the worse alloy is Pt82Al12Hf6 followed by Pt82Al12Ta6 due to drastic internal oxidation and the formation of deleterious oxides of HfO2, AlTaO4, and Ta2O5.
DECLARATIONS
Authors’ contributionsInvestigation, Writing - original draft: Chong X
Writing - review & editing: Yu W
Methodology, Visualization, Writing - review and editing: Liang Y
Supervision, Data curation, Methodology, Writing - review and editing: Shang SL
Data curation, Methodology: Li C
Validation, Funding acquisition: Zhang A, Wei Y
Discussion, Funding acquisition: Gao X
Supervision, Methodology: Wang Y
Validation, Supervision: Feng J, Song H
Validation, Funding acquisition: Chen L
Conceptualization, Supervision: Liu ZK
Availability of data and materialsThe Supplementary Materials are available including the TDB file for Ellingham Diagrams calculations.
Financial support and sponsorshipThe authors would like to thank the financial support from the Rare and Precious Metals Material Genetic Engineering Project of Yunnan Province [202102AB080019-1, 202302AB080021]; Key R&D Program of Yunnan Province [202203ZA080001]; Open Project of Yunnan Precious Metals Laboratory Co., Ltd [YPML-2023050281]; Major R&D Project of Yunnan Precious Metals Laboratory Co., Ltd [YPML-2023050205] and Yunnan Fundamental Research Projects [202101AW070011, 202101BE070001-015].
Conflicts of interestAll authors declared that there are no conflicts of interest.
Ethical approval and consent to participateNot applicable.
Consent for publicationNot applicable.
Copyright© The Author(s) 2023.
Supplementary MaterialsREFERENCES
3. Potgieter JH, Maledi NB, Sephton M, Cornish LA. The platinum development initiative: platinum-based alloys for high temperature and special applications: part IV. platin Met Rev 2010;54:112-9.
4. Tesfaye F, Sukhomlinov D, Lindberg D, Taskinen P, Akdogan G. Thermal stabilities and properties of equilibrium phases in the Pt-Te-O system. J Chem Thermodyn 2017;106:47-58.
5. Süss R, Freund D, Völkl R, et al. The creep behaviour of platinum-based γ/γ′ analogues of nickel-based superalloys at 1300 °C. Mat Sci Eng A 2002;338:133-41.
6. Wenderoth M, Völkl R, Yokokawa T, Yamabe-mitarai Y, Harada H. High temperature strength of Pt-base superalloys with different γ′ volume fractions. Scripta Mater 2006;54:275-9.
7. Kim D, Shang S, Li Z, Gleeson B, Liu Z. Effects of Hf, Y, and Zr on alumina scale growth on NiAlCr and NiAlPt alloys. Oxid Met 2019;92:303-13.
8. Wang H, Liu J, Lei S, et al. Effects of Ta and Y additions on the high temperature oxidation mechanisms of Ni-10Al alloy at 1100 °C. Vacuum 2023;213:112074.
9. Yang L, Wang J, Yang R, et al. Oxidation behavior of a nanocrystalline coating with low Ta content at high temperature. Corros Sci 2021;180:109182.
10. Odusote J, Cornish L, Chown L. Oxidation kinetics and mechanisms of growth of alumina scale on precipitation-hardened Pt-Al-Cr-Ru alloys. Corros Sci 2012;63:119-28.
11. Ross A, Shang S, Fang H, et al. Tailoring critical Al concentration to form external Al2O3 scale on Ni-Al alloys by computational approach. J Am Ceram Soc 2022;105:7770-7.
12. Golightly FA, Stott FH, Wood GC. The relationship between oxide grain morphology and growth mechanisms for Fe-Cr-Al and Fe-Cr-Al-Y alloys. J Electrochem Soc 1979;126:1035.
13. Messaoudi K, Huntz A, Lesage B. Diffusion and growth mechanism of Al2O3 scales on ferritic Fe-Cr-Al alloys. Mat Sci Eng A 1998;247:248-62.
14. Mora-garcía A, Mosbacher M, Hastreiter J, Völkl R, Glatzel U, Muñoz-saldaña J. Creep behavior of polycrystalline and single crystal Ni-based superalloys coated with Ta-containing NiCoCrAlY by high-velocity oxy-fuel spraying. Scripta Mater 2020;178:522-6.
15. Kaplin C, Brochu M. Effects of water vapor on high temperature oxidation of cryomilled NiCoCrAlY coatings in air and low-SO2 environments. Surf Coat Technol 2011;205:4221-7.
16. Backman L, Opila EJ. Thermodynamic assessment of the group IV, V and VI oxides for the design of oxidation resistant multi-principal component materials. J Eur Ceram Soc 2019;39:1796-802.
17. Adkison KM, Shang S, Bocklund BJ, Klimm D, Schlom DG, Liu Z. Suitability of binary oxides for molecular-beam epitaxy source materials: a comprehensive thermodynamic analysis. APL Mater 2020;8:081110.
18. Shang SL, Lin S, Gao MC, Schlom DG, Liu ZK. Predictions and correlation analyses of Ellingham diagrams in binary oxides. arXiv. [Preprint.] Aug 10, 2023. [Last accessed on 10 Oct 2023] Available from: https://arxiv.org/abs/2308.05837.
19. Thermodynamic properties of inorganic materials·pure substances. Part 1_elements and compounds from AgBr to Ba3N2.
20. Kim DE. Thermodynamic modeling and prediction of elastic and thermal expansion properties of Ni-base superalloys: application to Ni-Al-Pt-Cr-Hf system with gamma and gamma’ phases. Available from: https://etda.libraries.psu.edu/catalog/12437. [Last accessed on 10 Oct 2023].
21. Kresse G, Furthmüller J. Efficient iterative schemes for ab initio total-energy calculations using a plane-wave basis set. Phys Rev B 1996;54:11169-86.
22. Kresse G, Joubert D. From ultrasoft pseudopotentials to the projector augmented-wave method. Phys Rev B 1999;59:1758-75.
23. Perdew JP, Zunger A. Self-interaction correction to density-functional approximations for many-electron systems. Phys Rev B 1981;23:5048-79.
24. Perdew JP, Ruzsinszky A, Csonka GI, et al. Erratum: restoring the density-gradient expansion for exchange in solids and surfaces. Phys Rev Lett 2008;100:136406.
25. Wang Y, Liao M, Bocklund BJ, et al. DFTTK: Density Functional Theory ToolKit for high-throughput lattice dynamics calculations. Calphad 2021;75:102355.
26. Jain A, Ong SP, Hautier G, et al. Commentary: the materials project: a materials genome approach to accelerating materials innovation. APL Mater 2013;1:011002.
27. Kirklin S, Saal JE, Meredig B, et al. The Open Quantum Materials Database (OQMD): assessing the accuracy of DFT formation energies. npj Comput Mater 2015;1:15010.
28. Perdew JP, Burke K, Ernzerhof M. Generalized gradient approximation made simple. Phys Rev Lett 1996;77:3865-8.
29. Leitner J, Voňka P, Sedmidubský D, Svoboda P. Application of neumann-kopp rule for the estimation of heat capacity of mixed oxides. Thermochimica Acta 2010;497:7-13.
30. Kopp H. III. Investigations of the specific heat of solid bodies. Phil Trans R Soc 1865;155:71-202.
31. Andersson JO, Helander T, Höglund L, Shi P, Sundman B. Thermo-Calc & DICTRA, computational tools for materials science. Calphad 2002;26:273-312.
32. Wagner C. Theoretical analysis of the diffusion processes determining the oxidation rate of alloys. J Electrochem Soc 1952;99:369.
33. Lu J, Li L, Chen Y, et al. Y-Hf co-doped AlCoCrFeNi high-entropy alloy coating with superior oxidation and spallation resistance at 1100 °C. Corros Sci 2021;182:109267.
35. Lee D, Santella M. High temperature oxidation of Ni3Al alloy containing Cr, Zr, Mo, and B. Mat Sci Eng A 2004;374:217-23.
36. Levin I, Brandon D. Metastable alumina polymorphs: crystal structures and transition sequences. J Am Ceram Soc 1998;81:1995-2012.
Cite This Article

How to Cite
Chong, X.; Yu W.; Liang Y.; Shang S. L.; Li C.; Zhang A.; Wei Y.; Gao X.; Wang Y.; Feng J.; Chen L.; Song H.; Liu Z. K. Understanding oxidation resistance of Pt-based alloys through computations of Ellingham diagrams with experimental verifications. J. Mater. Inf. 2023, 3, 21. http://dx.doi.org/10.20517/jmi.2023.17
Download Citation
Export Citation File:
Type of Import
Tips on Downloading Citation
Citation Manager File Format
Type of Import
Direct Import: When the Direct Import option is selected (the default state), a dialogue box will give you the option to Save or Open the downloaded citation data. Choosing Open will either launch your citation manager or give you a choice of applications with which to use the metadata. The Save option saves the file locally for later use.
Indirect Import: When the Indirect Import option is selected, the metadata is displayed and may be copied and pasted as needed.
About This Article
Special Issue
Copyright
Data & Comments
Data
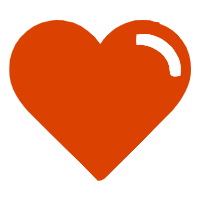
Comments
Comments must be written in English. Spam, offensive content, impersonation, and private information will not be permitted. If any comment is reported and identified as inappropriate content by OAE staff, the comment will be removed without notice. If you have any queries or need any help, please contact us at support@oaepublish.com.