Innovative design of moulds by additive manufacturing for sustainable processing of expanded polymers
Abstract
This present work explores how the Additive Manufacturing (AM) technique can be leveraged to create innovative moulds for expanded polymers (EPs). Traditional steam-chest moulding tools, typically made from cast aluminium alloys due to their high thermal diffusivity and good castability, can be replaced with lighter moulds. These new moulds are precisely designed and produced using laser-powder bed fusion technology, resulting in significantly reduced thermal capacity and optimised steam distribution throughout the part volume. The general design approach is outlined, and the performance of this innovative solution is demonstrated through a case study. Experimental tests on the prototype moulds and moulding equipment revealed substantial reductions in cycle times and energy consumption compared to traditional steam-chest moulding methods for producing the same product. The tests also demonstrate that the evolution of the moulds influences the machines currently used in the process. These could be revisited and redesigned to improve further the performance provided by the new AM moulds even more.
Keywords
INTRODUCTION
Steam-chest moulding is one of the most important processes for producing expanded polymer (EP) products. Polypropylene, polystyrene, and polyurethane beads are injected into a mould, melted by steam pressure and temperature, and then cooled to form the desired shape[1,2]. This fast, efficient, and highly automated process is crucial in modern manufacturing. It significantly influences the production of various products in sectors such as packaging, building insulation, and impact protection, owing to their well-established thermal and acoustic insulation and shock absorption properties[1,3].
Their wide diffusion on the market, in terms of tons produced per year, makes research about the manufacturing technology of EP strategic, especially when targeting the energy, wastes, and cycle times of the forming process.
The moulds used in the steam-chest process must possess specific characteristics. First, they must be able to endure the recurring heating and cooling cycles required by the moulding process. Second, they must be capable of permitting the steam to flow into the moulding chamber to sinter the polymer beads. Finally, they must resist the compression loads generated by the closure pressures of the mould halves.
The moulds for EP steam-chest moulding are traditionally built with massive aluminium-alloy castings machined by conventional chip-removing processes.
During moulding, the moulds are heated by the steam flow injected through nozzles in the forming chamber filled with the polymer beads. On cooling, water sprays are adopted to speed up the part’s temperature drop, allowing its extraction. The continued thermal fluctuations induced by every process cycle, which are fatally extended to the massive moulds’ volume, promote consistent energy wastes and longer production cycles.
Increasing energy savings, reducing moulding times, and making the process more environmentally friendly are the driving factors for innovation in the steam-chest moulding field. The use of low-conductive metals for mould production or the adoption of suitable coating, as well as the design of moulds without the conventional steam chest, which is replaced by injectors and nozzles for steam and cooling media, respectively, have been claimed by some patents filed[4,5].
Various authors have proposed using heating media, such as microwaves or additional hot air flows, to shorten moulding times and reduce energy consumption[2,6]. Recently, approaches based on metal Additive Manufacturing (AM) have been proposed to improve mould efficiency[7-10].
The AM technique offers broader design freedom and the ability to fabricate impossible shapes for conventional manufacturing technologies. This ability could be exploited to design innovative, lighter, and energetically more efficient moulds.
The present work aims to describe how AM techniques, joined with novel design strategies, can make possible the fabrication of moulds that significantly improve the energy efficiency of the steam-chest moulding process, reducing cycle times and steam consumption. In the following sections, the design strategies for the manufacturing of innovative lighter moulds will be discussed. Through the description of a case study, it will also be demonstrated that significant improvements in the energy efficiency of the forming process can be achieved.
STEAM-CHEST PROCESS AND MOULDS
Traditionally, steam chest presses are designed to host planar-facing surfaces equipped with specific compartments. These compartments are fixed to the two parts of the mould, ensuring a sealed chamber - the chest - behind the cavity of each mould half. One of the two press ends is fixed, while the other moves to close and open the mould cavity during each cycle. The forming process foresees five main steps [Figure 1].
After the “mould closure”, the sintering cavity is filled with polymer beads. Once this “filling” step is finished, heated steam delivered through the chest into the mould cavity at up to 150 °C is used to melt or sinter the beads. During the so-called “cooking” step, the mould cavity is maintained under a constant pressure of up to 8 bar to promote the interdiffusion of the polymer chains and the creation of physical links among the polymer beads, promoting a sort of sintering of the beads into a single solid part. The “cooling” step starts with steam evacuation and continues with the action of water sprays on the external mould surfaces to speed up this phase. Finally, the cycle ends with “mould opening” and the extraction of the moulded product[1].
One of the main challenges in mould design is to introduce and distribute water steam into the mould cavity as evenly, quickly, and efficiently as possible. In this regard, a set of small nozzles is integrated into the mould’s surfaces to allow water vapour to enter. Their number and arrangement significantly influence the distribution of the steam, hence the quality of the surfaces and of the moulded component, especially when the part geometry is complex.
These nozzles, which are different in size according to specific needs, are distributed on the surface of the mould at a distance of about 25 millimetres from each other. An additional task for these steam nozzles is expelling air from the cavity during mould filling. Sometimes, they are helpful during the vacuum phase generation inside the cavity to assist in cooling. Indeed, a lower pressure can help expel hot fluids and accelerate temperature reduction in the cavity. The vacuum technique[11] is not always used because it depends on the moulded polymer material. Still, it can potentially reduce the impact of the massive volume of the mould on the cycle. One drawback of designing mould with discrete nozzles is represented by the fact that their imprints are often clearly visible on the surface of the moulded products, impairing the aesthetic aspect [Figure 2].
ADDITIVE MANUFACTURING DESIGN OF MOULDS
AM techniques enable the production of physical parts directly based on three-dimensional (3D) CAD models using materials such as polymers, ceramics, and metal alloys. The maturity reached by AM and its high level of dimensional accuracy allows us to consider this technique as one of the most suitable techniques for the manufacturing of limited numbers of small- to medium-size parts featuring complex shapes[12-18]. In this regard, the opportunities offered by AM for mould design and fabrication are of significant importance and will be described in the present article.
Among the existing AM technologies for metallic parts production, powder bed fusion (PBF), which encompasses laser (L-PBF) or electron beam (EB-PBF) applications, is the most adopted process. According to this manufacturing route, the physical object is generated by selectively melting the part profile on different layers of the metallic powder (approximated as the 2D slices of the object). These thin layers of material are added one on top of the other and become connected, generating a solid body defined by the geometric digital CAD model. The material subjected to PBF processes features a fine microstructure that can provide excellent mechanical properties under optimised process conditions, often exceeding those of the reference cast counterparts[19,20]. With this assumption, it is suggested that the proposed moulds could sustain a service life at least comparable to that of the traditional cast moulds.
Considering the design of moulds for the steam foaming technology, the two main design concepts to be targeted are the reduction of the wall thickness of the cavity and the creation of a sort of porous wall for the diffused water steam access to the cavity. As discussed, reducing the walls’ thickness increases the energy efficiency during the heating and cooling phases, reducing the heat losses related to the mass of the mould walls (to be heated and cooled together with the moulded parts). Creating small holes uniformly distributed on the mould cavity surfaces, replacing the distinct nozzles, allows a more homogeneous steam flow, speeding up the different moulding steps and achieving a more homogeneous sintering process of the polymer beads. Adopting these design features also implies the afterthought of the steam-chest compartment currently adopted on the moulding press, which could potentially be reduced in volume and integrated with other mould auxiliaries.
By a careful numerical analysis of the fluid flows during the steps of the moulding process, it is possible to design special chambers featuring thin walls and equipped with optimised inlet/outlet ports, directly integrated into the mould, which can replace the conventional chest of the traditional aluminium cast moulds. It is also possible to ensure the required structural strength by exploiting 3D lattice structures that support the thin walls of the cavity or specific ribs that can be inserted within the inner volume of the chamber without impairing the fluid flow of steam and cooling water during the process[7,9,10].
Finally, the described design requirements must be tuned, considering the choice of the most suitable material for the mould. Cast aluminium alloys are the standard materials for traditional steam-chest moulds due to their excellent castability, high thermal diffusivity, and low heat inertia. However, the ability to design thinner walls might favour the choice of different materials with higher strength. Even materials with lower thermal conductivity and heat capacity than aluminium could become competitive considering the lower amount of energy to be dissipated with the new mould design. Accordingly, alloys such as the type 316 stainless steel, commercially pure Ti, or the more popular Ti-6Al-4V alloy, could be favourably considered.
The shape of the product drives the design of the mould. At the same time, polymer material and manufacturing process conditions influence the geometry of some of its features, e.g., avoiding undercutting surfaces and evaluating thermal and structural stresses. When the mould is manufactured using AM techniques, additional attention is required for the design owing to some peculiar effects related to the physical environment where material layers grow during the AM process. Indeed, the powder fusion process in the L-PBF technique produces thermal stresses and geometrical issues, such as the need to use supports on overhang surfaces, that must be addressed. This is especially important when thinned walls and holes along different growth directions have to be designed.
On the other hand, the enhanced degree of freedom from manufacturing constraints provided by AM allows the placement of material only where it is required and the design of the shape of functional parts (those surfaces and structural elements that play a functional role in the mould), focusing on their optimal performance. For the moulds described here, two main surfaces must be considered in the design: the surface in direct contact with the EP beads, devoted to defining the shape of the moulded product, and the surface adopted to fix the mould and ensure connections to the press machine. Once these functional surfaces have been defined, the remaining volume of the mould can be designed according to expected working conditions and the thermal and structural properties of the selected material.
As stated, reducing the mould wall thickness in contact with the EP beads can be counterbalanced by selecting alternative materials and creating an offset surface to that of the mould cavity to form a stiffer and stronger sandwich panel using a lattice structure or by adding ribs. In the first case, the mould will include a reduced-volume fluid chamber, which can replace the traditional and more massive chest chamber. In contrast, in the second case, a traditional configuration of an open mould is obtained to be inserted in conventional systems equipped with the steam chest.
Figure 3 shows an example of this strategy applied to a mould for EP boxes. The depicted mould was fabricated by L-PBF using the sandwich design approach described above. At the design stage, the lattice pattern was optimised to distribute the fluid flow along the sandwich panel space uniformly and to guarantee a homogeneous thermal flow delivered to the polymer beads using computer fluid dynamics (CFD) simulations. The CFD design criteria have already been discussed in a previous paper[9]. The design solution is evidently influenced by the specific shape of the product to be moulded. Objects with sharp-edged surfaces are more challenging than parts with smooth surfaces when a homogeneous flow of steam and cooling water has to be guaranteed within the process chamber. The moulds of the case study presented here have been manufactured with a Ti-6Al-4V alloy by a Renishaw AM250 L-PBF system equipped with a pulsed fibre laser at a power of 200 W. After process optimisation, the parts were printed adopting a hatch spacing (representing the distance between two adjacent laser tracks) of 95 µm and a point distance (representing the distance between two consecutive pulses upon laser scanning) of 65 µm, with a layer thickness of 60 µm. The L-PBF printing process took 52 and 47 h to generate the female and male moulds, respectively, which were then subjected to an annealing process and final machining of the matching surfaces; it must be specified that the vast majority of the EP parts do not have particular concerns about geometrical accuracy since a required precision of about 0.2 mm for parts having a size of about 500 mm is generally accepted. The L-PBF printed mould described here could quickly satisfy this requirement.
Figure 3. A case study of EP moulds with an integrated sandwich chamber for the fluid flow. One-half of the mould has been sectioned to highlight the reduced volume of the process chamber and the presence of the lattice structure. The external side of the moulded part measures 150 mm in length. EP: Expanded polymer.
For this specific case study, the CAD model was built using PTC Creo parametric software. Any model that must be produced was generated starting from the polymer part’s final geometry, appropriately scaled to consider the material’s shrinkage. To maintain the proper flexibility of the CAD model and take advantage of the model symmetry, any single part was duplicated and assembled together. The features that differed between the models were generated at the assembly level and associated with the corresponding parts.
A second feature related to the design for optimal performance offered by AM lies in the possibility of inserting a wide number of tiny holes in the CAD model, homogeneously distributed onto the surface of the mould cavity, which can replace the discrete steam nozzles. These diffused inlet holes, with a diameter that can be sized down to a few hundred micrometres, are directly printed with the mould without additional cost and printing time. The diffused distribution of small holes increases the overall flow area for the fluids and produces a more uniform texture on the surface of the moulded product. The different aesthetical results provided by the diffused holes compared with discrete nozzles are shown in Figure 4. In this regard, other aesthetic textures might also be obtained by shaping the channels using various sections instead of cylindrical holes.
Figure 4. Examples of surfaces of EP parts moulded with distinct steam nozzles (A) and with the use of a network of small holes (B). These features are highlighted in the figure with red and white arrows, respectively. EP: Expanded polymer.
In a further design solution, the traditional open mould is still considered, but the structural integrity of the wall with reduced thickness in contact with the EP beads is guaranteed by a net of ribs. Even though the creation of an optimised chest chamber designed “ad hoc” could be considered, this solution allows the insertion of the mould into the traditional chest chamber of already existing moulding presses without any modification of the traditional plant.
Finally, the design of the moulds must be bound to the AM fabrication rules. The main limitation is the size of the printing chamber available in the current commercial L-PBF machines. A further aspect to be considered is the definition of the orientation of the parts on the building platform to reduce the required supports and avoid the presence of these supports on the functional surfaces of the mould[21]. This last condition is primarily targeted to guarantee the quality of the surface in contact with EP beads and to avoid the need for post-production machining of the surfaces. To consider the volume available on the AM machines and the orientation rules, the mould might further be split into several bodies to be fitted in a frame and mechanically joined to form a single mould [Figure 5].
TESTING
Some of the design and manufacturing concepts discussed here have been applied to the production of industrial moulds, which showed very promising performance results during service[10]. The significant reduction in the mould’s mass produces a remarkable shortening of cycle times and a decrease in energy consumption. Figure 6 shows the performance comparison in terms of the times for the different moulding steps between a traditional massive mould and an innovative mould for producing the lid, which is also illustrated in the figure.
Figure 6. Comparison of cycle times between traditional and innovative AM moulds for producing the lid for food boxes shown on the right. AM: Additive Manufacturing.
The research roadmap also involved investigating all the moulding process parameters to achieve the best fine-tuning for the new mould configuration. For this purpose, a testing campaign was organised at the JSP’s Innovative Centre in Düsseldorf (Germany) to perform comparative tests on an instrumented EP moulding machine equipped with a vast number of sensors and specific software for the acquisition, storage, and analysis of the process data, including the evaluation of the equivalent CO2 footprint generated by the process.
A specific mould was produced for the testing campaign, featuring a reference-shaped cavity used at the JSP Innovative Centre for the testing activities on polymer materials, moulds and process parameters.
Figure 7 shows several views of the mould adopted for the testing campaign. It allows the creation of a
Figure 7. Mould adopted for the testing campaign. (A) General views of the two mould’s halves; (B) detail of the centre of the mould cavity; and (C) shape of an EP moulded part. EP: Expanded polymer.
The tests were conducted in different stages between June 2023 and February 2024, using commercial polymer beads of expanded polypropylene (EPP). The main objective of the investigation was the comparison between a traditionally built mould, made by an aluminium casting with wall thickness in the range of 12-15 mm, equipped with discrete steam nozzles (herewith called baseline mould), and a 3D printed innovative mould featuring the same cavity, but differing by the thinner walls (2 mm) and the presence of diffused holes for the steam delivery to the polymer beads [Figure 7]. Both moulds were equipped on both sides with thermocouples for temperature monitoring and sensors for foam pressure and temperature. Sensors for measuring water, steam and air flows were added to the specific valves of the moulding machine.
Several moulding process configurations have been investigated, as summarised in Table 1. The first condition (BR) refers to a moulding process carried out with the standard parameters generally adopted for industrial mass production. All the following tests described in the table took advantage of the sensors implemented in the moulding machine to achieve optimised conditions. Moreover, during the first test campaign in the Summer of 2023, it was observed that, especially with the lighter moulds produced by AM, after the rapid action of the cooling water, the temperature measured in the mould cavity and in the EP moulded part could rose again due to heat back-diffusion from the baseplate and other parts of the system which were still hot. Therefore, a thermal insulation layer was implemented to prevent this effect, and a new test campaign was organised in early 2024 to investigate conditions B6 and S3.3 [Table 1].
Test dates and process conditions adopted in the testing campaign of the moulds
Date | Code | Mould | Description |
05/06/2023 | BR | Baseline | Reference process condition |
05/06/2023 | B2 | Baseline | Optimised process parameters for traditional mould, two stem inlets |
01/06/2023 | B3 | Baseline | As in B2, with reduced chest volume |
21/02/2024 | B6 | Baseline | As in B3, with thermal insulation of the mould from the baseplate |
08/08/2023 | S3 | 3D mould | As in B3 |
23/02/2024 | S3.3 | 3D mould | As in B6 |
In Table 2, an overview of the main production data is reported. Steam consumption and cycle times are the main parameters for evaluating the competitiveness of any improvement. The energy consumption could not be directly assessed but is embedded into the cost of utilities, including steam, water and air. Electrical power is also included in the costs of utilities, although its consumption was constant for all tests. The equivalent CO2 footprint related to the moulding process was evaluated by considering the amount of steam, air, water and electrical power consumed. The suppliers of the steam generator, air compressor and water recycling system provided the input power consumption per unit of output (steam, water, air flows) considering the actual efficiency of their systems. The amount of methane used is easily converted into the mass of equivalent CO2, while for the electrical power, reference is made to the parameters claimed by the national power distributor. This value of the equivalent CO2 footprint is also included in the table to assess environmental sustainability. Finally, tensile tests have been performed on samples extracted from the moulded parts to evaluate the achievable quality of the EP parts obtained.
Summary of the production data acquired in the testing campaign of the moulds
Code | Steam | Cycle time | Cost of utilities | Water | Equiv. CO2 | Strength | |||||
kg | % | sec | % | €/cycle | % | litres | % | kg/cycle | % | kPa | |
BR | 6.03 | - | 146 | - | 0.53 | - | 48.2 | - | 1.54 | - | 854 |
B2 | 4.08 | -32.3 | 116 | -22.1 | 0.39 | -27.3 | 40.2 | -16.6 | 1.20 | -22.1 | 859 |
B3 | 3.97 | -34.2 | 112 | -22.7 | 0.37 | -29.7 | 40.3 | -16.5 | 1.19 | -22.7 | 850 |
B6 | 3.56 | -41.0 | 138 | -5.7 | 0.36 | -31.9 | 20.0 | -58.5 | 1.16 | -24.7 | 969 |
S3 | 3.25 | -46.1 | 135 | -7.8 | 0.33 | -37.0 | 30.0 | -37.8 | 1.08 | -29.9 | 860 |
S3.3 | 3.03 | -49.8 | 118 | -18.9 | 0.36 | -33.2 | 50.0 | 3.7 | 1.09 | -29.2 | 969 |
From the analysis of the general data provided in Table 2, it is apparent that the cycle times and the costs of the process can be readily reduced by implementing several measures, such as an improved stem inlet configuration, a reduced chest volume, and the thermal insulation to avoid unwanted heat backflow toward the mould at the end of cycles. Moreover, adopting the 3D mould can add further advantages to stem consumption, cycle time, and CO2 footprint.
The diagram in Figure 8 underlines the behaviour of the considered parameters during the tests. There is clear evidence that innovative 3D moulds can reduce utility consumption and the corresponding cost per cycle of the process.
From Table 2 and Figure 8, it can be observed that there was a consistent consumption of water during test condition S3.3 due to an exceptionally high heat backflow despite the adoption of the thermal insulation from the mould baseplate. A careful analysis of the monitored data suggested that in the thin-walled 3D printed mould, even the residual steam contained in the connection pipes downstream of the control valves could affect mould cavity temperature due to the very low thermal inertia. More specifically, in Figure 9, two examples of the evolution of the monitored parameters (water flow and mould temperature) during cycles B6 and S3.3 are provided.
Figure 9. Evolution of process parameters during the moulding cycle for the testing condition: (A) B6, and (B) S3.3.
It becomes evident that, after the polymer bead injection, the temperature rises due to the steam inlet and rapidly drops once the water flow is activated to cool the mould system. For both conditions, the effect of the heat backflow is clearly identified by the rise in temperature on the moving side of the mould. Moreover, from Figure 9B, it can be observed that the temperature of the moving side quickly increases, so an additional flow of water was required (hence the higher water consumption mentioned above) to reach a suitable temperature for mould opening and part extraction. From this observation, it is suggested that, for future and even more optimised industrial applications, a modified moulding press design shall be adopted to improve the heat control through these light moulds featuring reduced thermal inertia.
CONCLUSIONS AND FINAL REMARKS
The adoption of metal additive manufacturing technologies enables the utilisation of new materials and the creation of moulds with complex, advanced shapes tailored to specific manufacturing needs. This shift opens up new opportunities for innovation, even in seemingly well-established industrial sectors. Indeed, the moulding process of EP parts requires a wide use of energy during each thermal cycle. The tests demonstrated that most of this energy is wasted due to heating and cooling of the massive moulds traditionally adopted and that a light solution for the moulds positively influences the process’s carbon footprint, energy savings and cycle time.
Despite these advantages, the higher cost of AM moulds compared to traditional massive cast moulds still represents a significant entry barrier for the market. While waiting for future technology improvements and more extensive diffusion of L-PBF systems, which could lead to cost reduction, design strategies have to be developed to reduce the cost impact of the moulds produced by AM as much as possible while still keeping their substantial advantage. In the paper, several key aspects have been highlighted as follows.
1. A lower-cost mould assembly could be designed using a hybrid approach. The proposed new mould could be considered made of a structural frame of simple geometry obtained by machining with traditional route wrought parts, which assures the required stiffness to the assembly. The mould cavities, which are typically more complex in their geometry, could conveniently be produced by AM to keep all the benefits of the proposed innovation.
2. A second cost limitation relates to the large size of some popular applications, such as containers for food (fish, meat, vegetables) and other goods. Their size requires L-PBF machines with a wide building platform, which are available only in a few AM printing centres and at a comparatively higher cost. Also, for this concern, a solution could be splitting the designed mould into smaller parts to be assembled only after printing using a suitable connection method.
3. The reduction of the cycle times and peak temperature felt by the mould materials also lend themself to a change in paradigm when considering material selection. If metals with high thermal conductivity (i.e., aluminium casting alloys) were the obvious choice for traditional chest moulds, the thin-walled innovative moulds could potentially relax the constraints given by the thermal conductivity, moving to alternative materials featuring lower costs, improved stiffness, smoother surfaces after printing. An even more innovative strategy would be to address moulds printed with high-temperature polymeric resins, which could still sustain loads at temperatures up to 150 °C but are sold and can be printed at significantly lower costs than metals.
4. Finally, the tests demonstrated that the evolution of the moulds also affects the efficiency of the moulding machines currently used in the process. These machines must be revisited and redesigned according to the new AM mould requirements, especially regarding heat flow control and thermal insulation.
DECLARATIONS
Acknowledgements
The authors would like to thank Alessiohitech Srl (Medolago, Italy) for the permission to publish the results and the JSP Innovation Centre, Düsseldorf (Germany), for sharing the test data presented here.
Authors’ contributions
Study’s conception and design, data analysis and interpretation, and manuscript preparation: Viganò R, Vedani M
Availability of data and materials
Not applicable.
Financial support and sponsorship
None.
Conflicts of interest
Both authors declared that there are no conflicts of interest.
Ethical approval and consent to participate
Not applicable.
Consent for publication
Not applicable.
Copyright
© The Author(s) 2024.
REFERENCES
1. Raps D, Hossieny N, Park CB, Altstädt V. Past and present developments in polymer bead foams and bead foaming technology. Polymer 2015;56:5-19.
2. Hossieny N, Ameli A, Park CB. Characterization of expanded polypropylene bead foams with modified steam-chest molding. Ind Eng Chem Res 2013;52:8236-47.
3. Jin FL, Zhao M, Park M, Park SJ. Recent trends of foaming in polymer processing: a review. Polymers 2019;11:953.
4. Behl EK. Method of manufacturing moulded articles from cellular plastic, and a mould for carrying out the method. EP 0666796 B1. Available from: https://patents.google.com/patent/WO1994009973A1/en. [Last accessed on 6 Aug 2024].
5. Bruning J, Lang E, Ziegler M, Wacker K. 1. DE102004004657 - Energy efficient automatic molding machine for production of particulate foam products has no steam chamber and media distribution inside the tool. 2004. Available from: https://patentscope.wipo.int/search/en/detail.jsf?docId=DE104606864&_cid=P12-LYSNVP-16233-1. [Last accessed on 6 Aug 2024].
6. Allen RB, Kim BM, Miller DS. Expanding thermoplastic resin beads with very high frequency energy. EP 0425886 A2. Available from: https://patents.google.com/patent/US5128073A/en. [Last accessed on 6 Aug 2024].
7. Schütz J, Beck J, Schmiedeck M, Emmelmann C. Druckfrisch in die Zukunft der Partikelschaumverarbeitung. Kunstoffe 2018;8:70-2. Available from: https://www.hofmann-impulsgeber.de/wp-content/uploads/2020/03/Druckfrisch-in-die-Zukunft-der-Partikelschaumverarebeitung-Kunststoffe-08-2018.pdf. [Last accessed on 6 Aug 2024]
8. Biedermann M. Showcases: exploring new applications in additive manufacturing. In: Swiss AM Guide 2018. p. 4. Available from: https://ibam.swiss/wp-content/uploads/2020/12/AMGuide_2018_view.pdf. [Last accessed on 6 Aug 2024].
9. Alessio F, Alessio M, Vedani M, Viganò R. Novel concepts for the design of moulds and equipment for expanded polymer bead foams. Prog Addit Manuf 2021;6:339-46.
10. Alessio F, Alessio M, Savoldelli P, Vedani M, Viganò R. Design of additively manufactured moulds for expanded polymers. Int J Adv Manuf Technol 2023;125:4899-908.
11. McDonald K, Sun DW. Vacuum cooling technology for the food processing industry: a review. J Food Eng 2000;45:55-65.
12. DebRoy T, Wei HL, Zuback JS, et al. Additive manufacturing of metallic components - Process, structure and properties. Prog Mater Sci 2018;92:112-224.
13. Sames WJ, List FA, Pannala S, Dehoff RR, Babu SS. The metallurgy and processing science of metal additive manufacturing. Int Mater Rev 2016;61:315-60.
14. Ngo TD, Kashani A, Imbalzano G, Nguyen KTQ, Hui D. Additive manufacturing (3D printing): a review of materials, methods, applications and challenges. Compos Part B Eng 2018;143:172-96.
15. Armstrong M, Mehrabi H, Naveed N. An overview of modern metal additive manufacturing technology. J Manuf Proc 2022;84:1001-29.
16. Tebianian M, Aghaie S. Razavi Jafari NS, et al. A review of the metal Additive Manufacturing processes. Materials 2023;16:7514.
17. Durai Murugana P, Vijayananthb S, Natarajan MP, et al. A current state of metal additive manufacturing methods: a review. Mater Today Proc 2022;59:1277-83.
18. Vafadar A, Guzzomi F, Rassau A, Hayward K. Advances in metal Additive Manufacturing: a review of common processes, industrial applications, and current challenges. Appl Sci 2021;11:1213.
19. Bartolomeu F, Gasik M, Silva FS, Miranda G. Mechanical properties of Ti6Al4V fabricated by laser powder bed fusion: a review focused on the processing and microstructural parameters influence on the final properties. Metals 2022;12:986.
20. Kan WH, Chiu LNS, Lim CVS, et al. A critical review on the effects of process-induced porosity on the mechanical properties of alloys fabricated by laser powder bed fusion. J Mater Sci 2022;57:9818-65.
Cite This Article
How to Cite
Download Citation
Export Citation File:
Type of Import
Tips on Downloading Citation
Citation Manager File Format
Type of Import
Direct Import: When the Direct Import option is selected (the default state), a dialogue box will give you the option to Save or Open the downloaded citation data. Choosing Open will either launch your citation manager or give you a choice of applications with which to use the metadata. The Save option saves the file locally for later use.
Indirect Import: When the Indirect Import option is selected, the metadata is displayed and may be copied and pasted as needed.
About This Article
Special Issue
Copyright
Data & Comments
Data
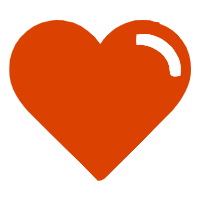
Comments
Comments must be written in English. Spam, offensive content, impersonation, and private information will not be permitted. If any comment is reported and identified as inappropriate content by OAE staff, the comment will be removed without notice. If you have any queries or need any help, please contact us at [email protected].