Guiding lithium growth direction by Au coated separator for improving lithium metal anode
Abstract
Lithium metal is the most promising anode for next-generation batteries due to its highest theoretical capacity and lowest electrochemical potential. However, its dendritic growth hinders its practical use due to the consequent poor reversibility, potential short-circuit, and safety concerns. Suppressing lithium dendrite is difficult since dendritic growth is thermodynamically and kinetically favorable. Herein, we guide lithium to uniformly deposit along the opposite direction to normal by a nanolayer Au coating on a commercial polypropylene separator. It prevents lithium dendrites from piercing the separator, instead of inhibiting dendrites growth only. Au is lithiophilic, and lithium is calculated to be more attracted to Au and is confirmed to uniformly deposit on Au at the separator side rather than on the current collector side. Furthermore, Au also regulates the morphology of deposited lithium from a mossy state to a bulky state. In this work, the symmetric cell with the designed structure achieves excellent electrochemical performances of a long-life cycle over 2,000 h at 1 C for 1 mA h cm-2. Pairing with LiFePO4 cathode as a full cell, lithium metal anode with Au-modified polypropylene separator exhibits extraordinary performance with a high Coulombic efficiency of 99.23% over 800 cycles at 1 C.
Keywords
INTRODUCTION
With the increasing demands for chargeable devices, including portable devices and large-scale grid, batteries with high-energy density (over 500 W h kg-1) are urgently needed. Lithium metal is expected to be the ideal anode for the next-generation high-performance batteries, with its light-weight (0.53 g cm-3), ultrahigh specific capacity (theoretically 3,860 mA h g-1), and the lowest electrochemical potential
Naturally, lithium protrusions are usually generated during lithium deposition due to uneven electric field and ion concentration. They are in a higher electrical field to attract more Li+ flux. The continuous preferential growth on tips leads to the growth of irregular lithium, as dendrites. Once lithium dendrites grow enough, they will pierce the separator and reach the other electrode to cause short-circuit, posing safety hazard.
Consecutive strategies have been proposed to weaken and eliminate lithium dendritic growth[1-8]. Conductive scaffold with a high surface area is a common strategy to reduce the local current density, which can also accommodate the deposited lithium and buffer large volume change of anode during cycling. The scaffold materials are usually carbon and Cu[1,9-11]. However, lithium deposition is usually hindered by the poor affinity of Cu or carbon with lithium due to high nucleation barrier. Because an extensive electric field is on the 3D scaffold surface, and the local current density and Li+ ion flux continuously decrease inside it[12], lithium mainly deposits on the surface rather than inside the scaffold, which cannot fully use the structure. Therefore, lithiophilic promoters, such as Si, Au[13], Ag[14], and ZnO[15-19], have been used to regulate lithium deposition. The modified scaffolds provide both an even distribution of electric fields and uniformly distributed nucleation sites as 3D hosts. Additionally, compressive stress is ubiquitous and cannot be easily relieved. It has been considered to relate to lithium plating morphology, making lithium dendrites emerge anywhere on the substrate surface[20]. When lithium grows in a common direction, the localization stress concentration would assist dendrite growth in piercing the separator[21,22]. This means that managing the compressive stress will greatly alleviate the dendrite growth.
Safety concerns usually come from inevitable dendrites piercing the soft separator. Natural solid electrolyte interphases (SEI) crack and regenerate during cycles, and lithium prefers to grow from exposed sites underlying cracked SEI, which intensifies its dendritic morphology growth. LiF coating[4], supramolecular polymer[7], inorganics[23], and alloy with lithium metal[24] are usually used to form an ultra-strong SEI. Separators are key components of rechargeable batteries; Al2O3[25], SiO2[26], and a water-borne nanosized molecular sieve[27] were coated on the separator to enhance mechanical strength so that dendrites can be suppressed. Surface grafting technology[28-30] enhances the wettability and heat resistance of separators to improve battery performance. Solid-state electrolytes are also believed to prevent lithium dendrite growth from the current collector to the opposite electrode due to their superior mechanical strength[8,31-33].
All these strategies above focus on eliminating lithium dendrites by stopping their growth. In these strategies, lithium deposits in a common direction from the current collector side to the separator side. Herein, we design a nanolayer Au-modified polypropylene separator (AuPP), guiding uniform lithium deposition by lithiophilic Au and regulating the deposition direction. In this design, lithium grows from AuPP to the Cu side, along an opposite direction unlike common strategies, which reduces the probability of piercing the separator. Lithium ions prefer to deposit on the lithiophilic Au layer rather than on the lithiophobic Cu foil. Besides, lithiophilic promoters, Au, provide homogeneous lithium nucleation sites. Additionally, the uneven compressive stress from lithium plating can be relieved by the nether soft AuPP, which could effectively mitigate lithium dendrite growth by reducing its driving force. In this work, the synergistic effects of regulated lithium deposition direction and uniformly deposited lithium morphology by the Au layer, along with relieved residual stress by soft AuPP, contribute to excellent electrochemical performances of lithium metal anodes.
EXPERIMENTAL
Preparation of separator with Au nanolayer.
The commercial Polypropylene (PP) (Celgard, USA) was used as a substrate. Au nanolayer was deposited on the substrate by a Turbomolecular pumped coater (Q150T Plus, UK) at 20 mA for 120 s.
Thickness measurement of Au nanolayer
A flat silicon wafer was used to substitute the PP as a substrate for Au to sputter on at the same condition as the preparation of AuPP. The Tape covers half of the silicon wafer to make a step between the wafer and sputtered Au. This thickness was measured by an atomic force microscope (AFM) (INNOVA, US).
Characterization
The scanning electron microscope (SEM) images were characterized using a Phenom ProX microscope (US), and the energy dispersive X-ray analysis (EDS) mappings were tested by an energy dispersive spectrometer (Phenom ProX microscope, US). X-ray diffraction (XRD) data were obtained from Bruker AXS diffractometer (UK). Optical video was characterized by a digital microscope (Dino-Lite Edge, China).
Electrochemical measurements
All coin cells were assembled using CR2025 coin-type cells in an Ar-filled glove box with the atmospheric condition of < 0.1 ppm oxygen and < 0.01 ppm H2O. PP was employed as the separator. All electrochemical tests were carried out in an electrolyte of 1 M lithium bis (trifluoromethanesulfonyl) imide (LiTFSI,
To study CE, coin cells were assembled with PP or AuPP as the separator, Cu as the working electrode, and lithium foil as the counter electrode. Au is placed facing the Cu side. Cells were cycled at various currents with a charging cutoff voltage of 1 V. For the symmetric cells, lithium foils were placed on two sides of PP or AuPP. Full cells were assembled with LiFePO4 cathodes (4.2 mg cm-2). An amount of 1 mA h cm-2 lithium has been deposited on the AuPP and PP at 1 mA cm-2 as anodes in advance, corresponding with the negative/positive capacity ratio (N/P) ratio of 1.4. The cells were cycled between 2.5 and 4.0 V vs. Li+/Li. The current density here is 170 mA g-1 for 1 C.
Calculation method
All our calculations were performed using the plane-wave Vienna Ab initio Simulation Package (VASP)[34,35]. A projector augmented-wave (PAW) pseudopotential method was applied to describe interactions between core and valence electrons[36]. A kinetic energy cutoff of 500 eV and a Γ-centered
is calculated in terms of the total energy of the substrate with an adsorbed Li (Esub+Li) and the bare substrate
RESULTS AND DISCUSSION
The morphology of deposited lithium on the AuPP and Cu is schematically illustrated in Figure 1A and B. A nanolayer Au is sputtered on the PP separator. In this design, lithium deposits on Cu and grows towards the separator without AuPP, while with AuPP, lithium deposits on AuPP and uniformly grows in the opposite direction to the current collector side. To confirm this hypothesis, in-situ optical observation was conducted, as shown in Supplementary Video 1 and Figure 1C. Cu, AuPP, and lithium foil have been stacked tightly and immersed in the electrolyte to simulate the real cell condition. A current density of
Figure 1. Schematic illustration of lithium depositing on (A) Cu and (B) AuPP. (C) Optical images of cross-section view of the simulated cell after lithium depositing for 0, 15 and 20 min. (D) Calculated binding energy of a lithium ion with Cu and Au. The contact angles of molten lithium with (E) Cu and (F) Au.
From the SEM images of the morphology of pristine PP and AuPP, Au is sputtered conformally on the PP membrane [Supplementary Figure 1A and B]. The typical stretched pore-forming structure of the PP separator is maintained, and its permeability will not be affected. Sputtering is an industrial method, so sputtering Au on the PP could be easily achieved on a large scale, as shown in the inset in
To analyze the lithium nucleation and deposition behavior, a small amount of lithium of 0.2 mA h cm-2 at
Figure 2. Nucleation and growth behavior of Li depositing on the Cu and AuPP. Top view of deposited lithium of 0, 0.2 and
From cross-section view of deposited lithium on Cu in Figure 2G, lithium grows from Cu foil but in wide size distribution, implying different growth times at these lithium sites. From the cross-section view of the AuPP [Figure 2H], lithium grows from the Au instead of the Cu current collector and tightly connects. The element mapping of lithium on the AuPP is conducted to clarify the lithium distribution
The voltage profile of symmetric Li|Li cells with and without AuPP of a capacity of 1 mA h cm-2 at
Figure 3. Electrochemical performance of cells with/without AuPP. (A) Voltage profiles for symmetrical Li|Li cells with PP and AuPP. (B) Rate performance of symmetrical Li cells with PP and AuPP. Coulombic efficiency of half-cells Li|Cu for 1 mA h cm-2 at (C)
The morphology evolution of deposited lithium after cycles at 1 mA cm-2 of 1 mA h cm-2 is evaluated, as shown in Figure 4. After one cycle, deposited lithium on AuPP [Figure 4A] remains flat and dense, and no lithium is deposited on the opposite Cu [Figure 4D]. This verifies that lithium prefers to plate on the AuPP rather than on the Cu. In contrast, deposited lithium of the cell with PP on Cu is uneven and of different sizes [Figure 4J] due to the lithiophobic trait of Cu and uneven lithium nucleation. No lithium deposit is on the opposite PP [Figure 4G]. After five and ten cycles, the lithium morphology significantly differs on AuPP [Figure 4B and C] and Cu [Figure 4K and L]. There are also massive residual SEIs on the underlying Cu, especially after ten cycles, which have consumed too much electrolyte and will lead to dead lithium from dendrites, causing short life and low CE for cells. These results demonstrate the mechanism discussed above of this design: Au lowers the nucleation barrier and provides uniform nucleation sites for lithium depositing, and lithium prefers to deposit on Au and grows to the Cu side.
Figure 4. Top view of morphology of deposited lithium and Cu foil in the cells with AuPP and deposited lithium and separator in the cells without AuPP after cycles at 1 mA cm-2 for 1 mA h cm-2 after 1st, 5th and 10th cycles. (A-C) Deposited lithium on the AuPP. (D-F) Cu in cells with AuPP. (G-I) Separator in cells without AuPP. (J-L) Deposited lithium on Cu in cells without AuPP.
To assess the feasibility for practically applying this modified AuPP, full cells using LiFePO4 cathodes are tested. To better suit practical use, an amount of 1 mA h cm-2 lithium has been pre-deposited on AuPP or Cu at 1 mA cm-2 as the anode [Figure 5A]. They are the only lithium source in Li|LiFePO4 full cells. The areal density of LiFePO4 is 4.2 mg cm-2. The N/P ratio is 1.40 in our design, while it ranges from 1.03 to 1.2 in commercial lithium-ion batteries. After 800 cycles, the cell with AuPP remains at a better capacity of
Figure 5. Electrochemical performance of Li|LiFePO4 cells. (A) Cycle life of Li|LiFePO4 with PP and AuPP at 1 C. The amount of
CONCLUSIONS
In summary, we achieved uniform lithium deposition and guided its growth in an opposite direction to normal with 13.4 nm Au-modified PP. Lithium prefers to deposit on Au rather than on Cu due to a higher binding energy (3.056 to 2.500 eV), leading to the opposite lithium growth direction. Furthermore, because of the nucleation barrier close to zero and lithiophilic feature, lithium nucleates on the Au layer and grows uniformly, which can alleviate the lithium dendrite growth. This designed AuPP helps improve the electrochemical performance of lithium metal anodes. With the AuPP, symmetric cells attain a long lifespan of 2,000 h with stable voltage hysteresis, and the half cell keeps a high CE of 98.62% after 450 cycles at 1 C, three times the cell without AuPP. The full cell exhibits an excellent life of 800 cycles at 1 C when paired with a LiFePO4 cathode. In all, the preparation of AuPP can be easily scaled up, and this design achieves superior electrochemical performances for lithium metal anodes.
DECLARATIONS
Acknowledgments
SEM imaging was conducted at the Center for Advancing Materials Performance from the Nanoscale (CAMP NANO). We thank Dr. Chaowei Guo for his help with SEM. Han X acknowledges the Independent Research Project of the State Key Laboratory of Electrical Insulation and Power Equipment for financial support.
Authors’ contributions
Manuscript writing: Sun Z
Manuscript revision: Shen F, Han X
Approved the final version of the manuscript: Sun Z, Zhang Q, Wang Z, Chen Y, Wang K, Shen F, Guo J, Han X
Availability of data and materials
The following files are available free of charge. Characterization data (PDF).
Financial support and sponsorship
This work was supported by the National Key R&D Program of China (Grant No. 2020YFA0710500), and the Key Research and Development Program of Shaanxi (Program No.2022GXLH-01-23).
Conflicts of interest
All authors declared that there are no conflicts of interest.
Ethical approval and consent to participate
Not applicable.
Consent for publication
Not applicable.
Copyright
© The Author(s) 2024.
Supplementary Materials
REFERENCES
1. Zou P, Wang Y, Chiang SW, Wang X, Kang F, Yang C. Directing lateral growth of lithium dendrites in micro-compartmented anode arrays for safe lithium metal batteries. Nat Commun 2018;9:464.
2. Shen F, Zhang F, Zheng Y, et al. Direct growth of 3D host on Cu foil for stable lithium metal anode. Energy Storage Mater 2018;13:323-8.
3. Hou G, Sun Q, Ai Q, et al. Growth direction control of lithium dendrites in a heterogeneous lithiophilic host for ultra-safe lithium metal batteries. J Power Sources 2019;416:141-7.
4. Wang H, Lin D, Xie J, et al. An interconnected channel-like framework as host for lithium metal composite anodes. Adv Energy Mater 2019;9:1802720.
5. Cui C, Yang C, Eidson N, et al. A highly reversible, dendrite-free lithium metal anode enabled by a lithium-fluoride-enriched interphase. Adv Mater 2020;32:e1906427.
6. Zhu B, Jin Y, Hu X, et al. Poly(dimethylsiloxane) thin film as a stable interfacial layer for high-performance lithium-metal battery anodes. Adv Mater 2017;29:1603755.
7. Wang G, Chen C, Chen Y, et al. Self-stabilized and strongly adhesive supramolecular polymer protective layer enables ultrahigh-rate and large-capacity lithium-metal anode. Angew Chem Int Ed 2020;59:2055-60.
8. Ma J, Quhe R, Zhang Z, et al. Two-dimensional materials as a stabilized interphase for the solid-state electrolyte Li10GeP2S12 in lithium metal batteries. J Mater Chem A 2021;9:4810-21.
9. Umh HN, Park J, Yeo J, Jung S, Nam I, Yi J. Lithium metal anode on a copper dendritic superstructure. Electrochem Commun 2019;99:27-31.
10. Yi J, Chen J, Yang Z, et al. Facile patterning of laser-induced graphene with tailored Li nucleation kinetics for stable lithium-metal batteries. Adv Energy Mater 2019;9:1901796.
11. Cao Z, Li B, Yang S. Dendrite-free lithium anodes with ultra-deep stripping and plating properties based on vertically oriented lithium-copper-lithium arrays. Adv Mater 2019;31:e1901310.
12. Luo Y, Guo L, Xiao M, et al. Strategies for inhibiting anode dendrite growth in lithium-sulfur batteries. J Mater Chem A 2020;8:4629-46.
13. Pu J, Li J, Shen Z, et al. Interlayer lithium plating in Au nanoparticles pillared reduced graphene oxide for lithium metal anodes. Adv Funct Mater 2018;28:1804133.
14. Yang C, Yao Y, He S, Xie H, Hitz E, Hu L. Ultrafine silver nanoparticles for seeded lithium deposition toward stable lithium metal anode. Adv Mater 2017;29:1702714.
15. Zhang Y, Luo W, Wang C, et al. High-capacity, low-tortuosity, and channel-guided lithium metal anode. Proc Natl Acad Sci USA 2017;114:3584-9.
16. Huang S, Zhang W, Ming H, Cao G, Fan LZ, Zhang H. Chemical energy release driven lithiophilic layer on 1 m2 commercial brass mesh toward highly stable lithium metal batteries. Nano Lett 2019;19:1832-7.
17. Pu J, Li J, Zhang K, et al. Conductivity and lithiophilicity gradients guide lithium deposition to mitigate short circuits. Nat Commun 2019;10:1896.
18. Zheng H, Zhang Q, Chen Q, et al. 3D lithiophilic-lithiophobic-lithiophilic dual-gradient porous skeleton for highly stable lithium metal anode. J Mater Chem A 2020;8:313-22.
19. Tang L, Zhang R, Zhang X, et al. ZnO nanoconfined 3D porous carbon composite microspheres to stabilize lithium nucleation/growth for high-performance lithium metal anodes. J Mater Chem A 2019;7:19442-52.
20. Wang X, Zeng W, Hong L, et al. Stress-driven lithium dendrite growth mechanism and dendrite mitigation by electroplating on soft substrates. Nat Energy 2018;3:227-35.
21. Zhang D, Dai A, Fan B, et al. Three-dimensional ordered macro/mesoporous Cu/Zn as a lithiophilic current collector for dendrite-free lithium metal anode. ACS Appl Mater Interfaces 2020;12:31542-51.
22. Qin L, Wang K, Xu H, et al. The role of mechanical pressure on dendritic surface toward stable lithium metal anode. Nano Energy 2020;77:105098.
23. Liu X, Liu J, Qian T, Chen H, Yan C. Novel organophosphate-derived dual-layered interface enabling air-stable and dendrite-free lithium metal anode. Adv Mater 2020;32:e1902724.
24. Lu Z, Li W, Long Y, et al. Constructing a high-strength solid electrolyte layer by in vivo alloying with aluminum for an ultrahigh-rate lithium metal anode. Adv Funct Mater 2020;30:1907343.
25. Jeon H, Yeon D, Lee T, Park J, Ryou M, Lee YM. A water-based Al2O3 ceramic coating for polyethylene-based microporous separators for lithium-ion batteries. J Power Sources 2016;315:161-8.
26. Cho J, Jung Y, Lee YS, Kim D. High performance separator coated with amino-functionalized SiO2 particles for safety enhanced lithium-ion batteries. J Membrane Sci 2017;535:151-7.
27. Mao X, Shi L, Zhang H, et al. Polyethylene separator activated by hybrid coating improving Li+ ion transference number and ionic conductivity for Li-metal battery. J Power Sources 2017;342:816-24.
28. Sabetzadeh N, Falamaki C, Riahifar R, et al. Plasma treatment of polypropylene membranes coated with zeolite/organic binder layers: assessment of separator performance in lithium-ion batteries. Solid State Ion 2021;363:115589.
29. Liu M, Zhang P, Gou L, Hou Z, Huang B. Enhancement on the thermostability and wettability of lithium-ion batteries separator via surface chemical modification. Mater Lett 2017;208:98-101.
30. Pan L, Wang H, Wu C, Liao C, Li L. Tannic-acid-coated polypropylene membrane as a separator for lithium-ion batteries. ACS Appl Mater Interfaces 2015;7:16003-10.
31. Zhao Y, Yan J, Cai W, et al. Elastic and well-aligned ceramic LLZO nanofiber based electrolytes for solid-state lithium batteries. Energy Storage Mater 2019;23:306-13.
32. Cao C, Li Y, Feng Y, Peng C, Li Z, Feng W. A solid-state single-ion polymer electrolyte with ultrahigh ionic conductivity for dendrite-free lithium metal batteries. Energy Storage Mater 2019;19:401-7.
33. Han X, Gong Y, Fu KK, et al. Negating interfacial impedance in garnet-based solid-state Li metal batteries. Nat Mater 2017;16:572-9.
34. Kresse G, Hafner J. Ab initio molecular dynamics for liquid metals. Phys Rev B Condens Matter 1993;47:558-61.
35. Kresse G, Furthmüller J. Efficiency of ab-initio total energy calculations for metals and semiconductors using a plane-wave basis set. Comp Mater Sci 1996;6:15-50.
37. Perdew JP, Ruzsinszky A, Csonka GI, et al. Restoring the density-gradient expansion for exchange in solids and surfaces. Phys Rev Lett 2008;100:136406.
38. Henkelman G, Uberuaga BP, Jónsson H. A climbing image nudged elastic band method for finding saddle points and minimum energy paths. J Chem Phys 2000;113:9901-4.
Cite This Article
Export citation file: BibTeX | EndNote | RIS
OAE Style
Sun Z, Zhang Q, Wang Z, Chen Y, Wang K, Shen F, Guo J, Han X. Guiding lithium growth direction by Au coated separator for improving lithium metal anode. Energy Mater 2024;4:400047. http://dx.doi.org/10.20517/energymater.2024.03
AMA Style
Sun Z, Zhang Q, Wang Z, Chen Y, Wang K, Shen F, Guo J, Han X. Guiding lithium growth direction by Au coated separator for improving lithium metal anode. Energy Materials. 2024; 4(4): 400047. http://dx.doi.org/10.20517/energymater.2024.03
Chicago/Turabian Style
Zhouting Sun, Qihang Zhang, Zhenyu Wang, Yifei Chen, Kaiming Wang, Fei Shen, Juchen Guo, Xiaogang Han. 2024. "Guiding lithium growth direction by Au coated separator for improving lithium metal anode" Energy Materials. 4, no.4: 400047. http://dx.doi.org/10.20517/energymater.2024.03
ACS Style
Sun, Z.; Zhang Q.; Wang Z.; Chen Y.; Wang K.; Shen F.; Guo J.; Han X. Guiding lithium growth direction by Au coated separator for improving lithium metal anode. Energy Mater. 2024, 4, 400047. http://dx.doi.org/10.20517/energymater.2024.03
About This Article
Special Issue
Copyright
Data & Comments
Data
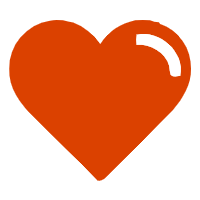
Comments
Comments must be written in English. Spam, offensive content, impersonation, and private information will not be permitted. If any comment is reported and identified as inappropriate content by OAE staff, the comment will be removed without notice. If you have any queries or need any help, please contact us at support@oaepublish.com.