Design strategy towards flame-retardant gel polymer electrolytes for safe lithium metal batteries
Abstract
The emergence of lithium metal batteries (LMBs) as a promising technology in energy storage devices is attributed to their high energy density. However, the inherent flammability and leakage of the internal liquid organic electrolyte pose serious safety risks when exposed to heat. In response to this challenge, gel polymer electrolytes (GPEs) have been developed to mitigate leakage and enhance nonflammability by incorporating flame-retardant groups, thereby improving the safety of LMBs. This review commences with a brief analysis of the thermal runaway mechanism specific to LMBs, emphasizing its distinctions from that of lithium-ion batteries. Following this, the various methods employed to assess the safety of LMBs are discussed, including flammability, thermal stability, and abuse assessment. The following section categorizes recent research on safe GPEs according to different flame retardancy levels providing a concise overview of each category. Finally, the review explores current advancements in developing safety-oriented GPEs and considers potential future research directions.
Keywords
INTRODUCTION
The rapid surge in interest in lithium-ion batteries (LIBs) has been driven by the increasing demand for energy storage devices, particularly in the context of electric vehicles and other emerging fields[1-4]. Nevertheless, due to the limited energy density of LIBs, they can no longer meet the escalating demand. In light of this, lithium (Li) metal has emerged as a promising alternative owing to its high energy density (3,860 mAh g-1) and low overpotential (-3.04 V vs. the standard hydrogen electrode). Consequently, lithium metal appears to be a suitable candidate for replacing the graphite anode in LIBs[5-9], and lithium metal batteries (LMBs) are being hailed as the candidate for next-generation batteries[10-15]. However, the development of LMBs is impeded by a series of safety concerns[16-19], particularly under extreme conditions such as thermal abuse[20-22] (e.g., high-temperature exposure), mechanical abuse[23-25] (e.g., nail penetration), and electrical abuse[26-29] (e.g., short-circuit, overcharge and overdischarge). These conditions can potentially elevate the internal temperature of the battery, leading to a chain of exothermic reactions and gas generation, ultimately resulting in uncontrollable overheat - a phenomenon known as thermal runaway of the battery[30-32]. Hence, while LMBs offer promising potential, addressing the safety concerns is crucial to ensure their successful development and commercialization.
The process of solving the thermal runaway problem in LMBs begins with a thorough consideration of the specific steps involved in thermal runaway. When thermal runaway occurs in a battery, it initiates with the decomposition of the solid electrolyte interphase (SEI), subsequently leading to electrolyte parasitic reactions at the anode and cathode, and culminates with the melting of the diaphragm, resulting in a short-circuit due to direct contact between the cathode and anode[33-35]. This subsequent rupture of the cell and leakage of electrolyte, exacerbated by the heat buildup, ultimately presents a flammable and explosive risk due to the leaked organic molecules[36,37]. Consequently, a comprehensive understanding of the thermal runaway mechanism highlights the critical role of the electrolyte within the entire process. Therefore, addressing the issue of LMB thermal runaway hinges on the imperative step of enhancing the safety of the electrolyte. Improving and optimizing the electrolyte can effectively impede the thermal runaway by preventing SEI decomposition, inhibiting parasitic reactions, and averting diaphragm melting. By employing innovative technologies to elevate electrolyte safety, the risk of thermal runaway in LMBs under extreme conditions can be reduced, thereby providing a more dependable foundation for large-scale applications.
Currently, the high mobility of conventional liquid electrolytes (LEs) poses a risk of leakage, despite the addition of flame retardants such as phosphoric groups, fluorine, and cyclophosphonitrile, which has improved the thermal safety[17,38,39]. Solid-state electrolytes (SSEs) have attracted attention due to their excellent electrode compatibility and superior mechanical properties, yet they suffer from relatively low ionic conductivity at room temperature[40,41]. In response to this challenge, gel polymer electrolytes (GPEs) have emerged as a promising solution, as they form by adding LE to the polymer matrix. This approach not only addresses the leakage-prone problem but also maintains high ionic conductivity, positioning them as the next-generation electrolyte to drive the commercialization of LMBs[42]. However, the flammability of LE poses a potential safety hazard for GPEs[43,44]. To enhance the safety of GPEs, two approaches are currently being pursued. Firstly, nonflammability is achieved by adding flame-retardant additives to reduce the fire risk[45]. Secondly, flame-retardant functional groups are grafted onto the polymer backbone of GPEs through molecular design to enhance the overall safety and pave the way for commercializing high-performance batteries[18].
As shown in Figure 1, this review focuses on the essential role of understanding the thermal runaway mechanism in ensuring the safety of LMBs. Thus, a comprehensive discussion of this mechanism is provided. An in-depth understanding of the thermal runaway mechanism is imperative for addressing this critical issue systematically. Subsequently, the paper delves into the discussion of current battery safety tests and characterizations, encompassing flammability, thermal stability, and abuse assessment. By comparing and briefly understanding these tests, this review aims to identify test methods more suitable for various types of thermal runaway experiments to more effectively evaluate the overall safety of batteries. The subsequent focus is on the recent progress on GPE-based LMBs, which briefly categorizes and introduces different flame-retardant functional groups. This discussion also elucidates the role of these groups in addressing the thermal safety of GPEs-based LMBs. Finally, this review delves into current research on safe GPEs and provides insights into potential future developments.
THERMAL RUNAWAY MECHANISM
In-depth studies of thermal runaway mechanisms are crucial for understanding and preventing battery safety risks. One valuable source of insights in this regard is the study of LIBs due to their structural similarities. The thermal runaway process in LIBs is typically initiated by electrical, mechanical, and thermal abuse, resulting in the buildup of heat and eventual runaway [Figure 2A and B]. It involves distinct stages, including heat generation, diffusion, and thermal runaway. The heat generation stage is characterized by increased cell temperature triggering SEI decomposition, thereby initiating parasitic reactions and heat release[46,47]. Subsequently, the thermal diffusion stage ensues as the diaphragm of the battery melts at around 130 °C, causing the electrodes to come into contact and leading to short-circuits, which, in turn, intensify the heating process[48]. Finally, during the thermal runaway stage (typically above 200 °C), the pyrolysis of organic solvents gives rise to free radicals, setting off electrolyte combustion and cathode decomposition. This leads to an accelerated release of heat and the gas accumulation, which may ultimately culminate in combustion and explosion.
Figure 2. Schematic diagram of thermal runaway process of LMBs. (A) Schematic diagram of reaction mechanism of LMBs; (B) Schematic diagram of thermal runaway process of LMBs.
The risk of thermal runaway in LMBs is substantially higher due to the reactive nature of lithium metal. The irregular deposition of lithium can lead to the formation of dendrites, which can damage the diaphragm, resulting in internal short-circuits and ultimately accelerating thermal runaway and combustion[49]. Even controlled lithium deposition may cause the dead lithium accumulation, leading to heat release and temperature elevation upon SEI formation[50]. The significance of the electrolyte in the thermal runaway process is well-established, with various observations underscoring its crucial role across all three stages as a heat transfer medium. Consequently, developing electrolytes exhibiting exceptional thermal stability is of paramount importance to enhance battery resistance to thermal runaway. The achievement of this challenging objective will establish a robust groundwork for enhanced battery safety and broader utilization, necessitating interdisciplinary research partnerships and groundbreaking scientific and technological innovations.
SAFETY ASSESSMENT OF LMBS WITH GPES
The safety assessment of LMBs is essential for making cross-sectional comparisons of various materials at different times. This assessment generally involves three key aspects: (1) characterization of flammability; (2) characterization of thermal stability; and (3) assessment under conditions of abuse, including thermal, electrical, and mechanical abuse. By evaluating these factors, the safety of LMBs can be comprehensively analyzed and understood.
Characterization of flammability
Self-extinguishing time
Self-extinguishing time (SET) is the standard method for evaluating the flammability of electrolytes[51]. Flame resistance is measured by determining the duration of sustained combustion per unit mass of electrolyte after removing an external ignition source. This can be calculated with[52]:
Where t is the time taken from ignition to extinction, and m is the mass of the electrolyte. When SET
Limiting oxygen index
The limiting oxygen index (LOI) is a significant metric for assessing the flame retardancy of an electrolyte. It indicates the minimal concentration needed for a sample to burn steadily in an O2/N2 gas mixture[54].
A sample of a certain size is fixed vertically in a combustion cylinder; a mixed gas flow is introduced, the top of the sample is ignited, and the minimum O2 concentration required for continuous combustion of the sample is recorded (expressed as the value of the volume percentage occupied by O2). A high oxygen index indicates a good flame retardancy of the material. It is generally recognized that when the LOI of the sample is < 21%, the material is flammable; 21% ≤ LOI ≤ 28%, the material is combustible; and LOI > 28%, the material is nonflammable[55]. The LOI of a polymer correlates with its char formation rate during combustion, specific enthalpy of combustion and elemental composition. Polymers with lower oxygen and higher halogen content generally exhibit an increased LOI, indicating improved flame retardancy.
Total heat release and heat release rate
The micro-combustion calorimeter (MCC) is highly effective in assessing the flame retardancy of materials by measuring their total heat release (THR) and heat release rate (HRR)[56]. This method not only proves to be an excellent choice for testing the flame retardancy of materials but also serves as a valuable tool for evaluating the potential fire hazards associated with these materials.
According to THR and HRR, we can quantitatively determine the fire hazard of the material. Higher values indicate a greater fire hazard, while lower values indicate a decreased hazard.
Other methods
Currently, the most prevalent technique for evaluating the flammability of materials involves direct ignition in air, wherein the material is brought into direct contact with a source of ignition to ascertain whether it ignites[57,58]. If the sample does not ignite, it is categorized as nonflammable; conversely, if it catches fire, it is deemed flammable. This method is widely employed to assess the flammability of various materials and is pivotal in determining their fire safety characteristics.
Characterization of thermal stability
Thermal stability, a critical property affecting the safety of electrolytes, is determined by various factors such as the elements present, molecular bonding energies, structural stability, and intermolecular interactions[59,60]. To gain a comprehensive insight into the thermal behavior of electrolytes across different temperature ranges, techniques such as thermogravimetric analysis (TGA) and differential scanning calorimetry (DSC) are employed. TGA enables the identification of material losses, intermediates, and decomposition processes, while DSC provides valuable information on thermal decomposition, crystallization temperatures (Tc), and glass transition temperatures (Tg). Additionally, DSC assesses the reactivity level through heat uptake and exothermic effects. By analyzing the DSC curve, as illustrated in Figure 3A, researchers can evaluate the thermal behavior of the electrolyte based on exothermic and endothermic peaks. The intensity of these peaks serves as an indicator of the extent of the thermal behavior exhibited by the electrolyte[61].
In addition, battery thermal stability is measured by the exothermic rate and cumulative heat release at different temperatures[62]. Adiabatic accelerated calorimetry (ARC) determines the critical temperature associated with the thermal runaway of the battery [Figure 3B][32]. Parameters include the self-exothermic onset temperature (T1), which indicates the thermal safety threshold of the battery; the thermal runaway onset temperature (T2), which implies that the battery will be rapidly ignited; and the maximum thermal runaway temperature (T3), which reflects the internal reactive energy release during thermal runaway. These parameters provide valuable insight into understanding and identifying the thermal runaway behavior of batteries in various systems.
Assessment under abuse
The thermal runaway of batteries is typically caused by three types of abuse: mechanical, electrical, and thermal. Mechanical abuse involves subjecting the battery to external forces such as collision, extrusion, and nail penetration. Electrical abuse encompasses internal and external short-circuits, overcharge and overdischarge. Thermal abuse involves subjecting the battery to external heating. These three types of abuse are interconnected rather than mutually exclusive, as shown in Figure 3C. Mechanical abuse can lead to electrical abuse, specifically through damage to the battery’s interior due to external stresses, resulting in an internal short-circuit. Subsequently, electrical abuse can result in thermal abuse. When a short-circuit occurs within the battery, a significant amount of heat is generated, triggering chemical reactions at higher temperatures and releasing even more heat. This is equivalent to the battery being continuously heated by an external heat source, thus constituting thermal abuse. In addition, overcharging triggers an oxidation reaction of the cathode electrolyte, releasing gases such as O2. Along with the release of heat, the temperature of the battery rises rapidly, leading to a thermal runaway reaction, which mainly results from the intense reaction between the cathode and the electrolyte at high temperatures. At the same time, long-term overdischarge will inevitably cause the negative potential of the LMBs to continue to rise until it reaches the decomposition potential of the SEI. This will lead to SEI rupture and generate more heat, further accelerating the thermal runaway process and ultimately causing battery combustion or even explosion. Consequently, evaluating the safety performance of the battery under abusive conditions is crucial for ensuring its safe operation.
Mechanical abuse
(1) Crush tests
Extrusion deforms the battery structure, causing failures of internal components, such as diaphragm rupture or rupture of positive and negative materials, which can lead to internal short-circuit. Consequently, this internal short-circuit generates a substantial amount of Joule heat, ultimately causing the decomposition of the internal materials of the single cell. According to the national standard GB 38031-2020, the testing procedure involves placing the fully charged battery between the extrusion plates, which extrude the battery at a speed of not more than 2 mm s-1. When the battery voltage drops to 0 V, the deformation amount reaches 15%, or the extrusion pressure reaches 100 kN and is maintained for 10 min. Following the extrusion, the battery is observed for one hour, and if no explosion or fire occurs during this period, it is identified as safe.
(2) Nail penetration tests
The cell penetration test is conducted to simulate the thermal runaway process of a battery by artificially inducing an internal short-circuit[63]. This is achieved by subjecting the battery to a constant current charge of 1C until it reaches the final voltage. Subsequently, a high-temperature steel needle, 5-8 mm in diameter, is driven through the battery at a speed of (25 ± 5) mm s-1 in a direction perpendicular to the battery pole piece. The needle is then left in the battery for observation for 1 h. If the battery does not explode or catch fire during this time, the test is considered successful.
Electrical abuse
LMBs may be overcharged or overdischarged when used in a battery pack because of the different capacities of the varying cells in the pack and the difficulty of keeping the state-of-charge (SOC) of each cell the same. Consequently, it is inevitable that the cells in the battery pack will be overcharged or overdischarged to a certain extent[64].
(1) Overcharge test
During the charging process, it is crucial to ensure that the charging current and voltage are within the recommended limits. Excessive current and voltage can result in overcharge, significantly affecting the battery life and even leading to safety hazards. To avoid these risks, it is recommended that the battery is initially charged at a constant current of 1 C to 1.1 times the termination voltage of the battery in accordance with GB 38031-2020. If the battery does not exhibit signs of explosion or fire during this test, it can be deemed safe. This testing approach is essential for ensuring the integrity and safety of the charging process.
(2) Overdischarge test
The thermal effect of overdischarge, when compared with overcharge, is relatively less severe; however, it can lead to catastrophic outcomes for the battery, especially in cases of high-current or repeated overdischarge, which can significantly affect the battery. To assess the battery’s response, it was fully charged at a rate of 1 C, followed by a 1 C discharge for 90 min per GB 38031-2020. The battery was then observed for an additional hour, during which there were no incidents of explosion, fire, or leakage, indicating the successful passing of the test.
Thermal abuse
During use, batteries are often subjected to elevated temperatures due to factors such as high contact resistance, inadequate heat dissipation, accidental heating, or extreme climatic conditions. As the external temperature increases, the internal temperature of the battery also rises. If the internal temperature reaches a critical threshold, the battery’s diaphragm may melt and rupture, or exothermic reactions inside the battery may further elevate the temperature, potentially leading to safety hazards. This chain of events underscores the critical importance of managing heat within battery systems to ensure safe and reliable operation[65].
(1) Heating test
To evaluate the safety performance of a battery under high-temperature conditions, a heating test is conducted. According to the national standard GB 38031-2020, this process involves placing a fully charged battery in a temperature chamber and gradually heating it from room temperature to 130 °C at a fixed rate. Subsequently, the battery is maintained at this temperature for 30 min to assess its reaction - whether it explodes or catches fire. This test aims to simulate the high-temperature situation that the battery may encounter during usage and ascertain its safety under such conditions.
Experience is the teacher of action, and understanding the thermal runaway mechanism of LMBs can help people deepen their understanding of thermal runaway. At the same time, understanding the safety characteristics of LMBs is an important part of leading research into electrolytes to prevent thermal runaway. Through in-depth study of these mechanisms and characteristics, people have begun to actively explore flame-retardant GPEs with excellent thermal safety, and these new GPEs will be introduced one by one below.
FLAME-RETARDANT GPES
The core components of GPEs typically include a polymer backbone, a liquid phase plasticizer, and a lithium salt. The polymer backbone, serving as the foundation, features a molecular structure characterized by a cross-linked network design. This structure plays a crucial role in enabling the full absorption of the plasticizer, resulting in the GPEs adopting a gel state with exceptional mechanical properties. Plasticizers and lithium salts are integral to GPEs, often referred to as the vital components that partially address the weaknesses of solid polymer electrolytes by enhancing ionic conductivity and overall battery performance. To enhance the safety features of GPEs, a common approach involves incorporating flame retardants into plasticizers or directly integrating flame-retardant groups into the polymer backbone. This modification aims to bolster the thermal stability of GPEs. Subsequently, we will expound on the various types of these flame-retardant groups and their respective functions.
Phosphates for GPEs
In the field of LMBs, organophosphates represent the earliest flame-retardant electrolytes to be extensively examined. Due to their nonflammable properties, wide temperature range, economical production cost, decent solubility of lithium salt, and low viscosity, organophosphates are widely utilized as nonflammable solvents or additives in electrolytes[66,67]. Exploring the flame-retardant mechanism of organophosphates necessitates examining the combustion chain reaction within the electrolyte as a starting point.
At high temperatures, electrolytes form flammable vapors such as gaseous carbonate solvents. These vapors decompose in a flame to produce H· radicals and react with oxygen from the cathode, producing HO· radicals. This can lead to combustion. Organic phosphates [e.g., triethyl phosphate (TEP)] have been shown to effectively prevent combustion through a free radical elimination reaction, as given in Equations (1-3). In the flame, liquid TEP evaporates into gaseous TEP. The decomposition of gaseous TEP produces phosphorus-containing free radicals, which then spontaneously capture the H· radicals generated in the chain reaction. This capture process blocks the chain reaction and achieves flame-retardant effects[68].
Phosphate additives
Although organophosphonates as flame retardants can achieve the nonflammability of electrolytes, they are plagued by a multitude of issues, particularly their lack of compatibility with Li anodes. During battery cycling, the phosphate group undergoes reduction on the electrode surface, impeding the effective formation of the SEI on the lithium metal at the negative electrode, consequently influencing the cycling performance of the battery[45]. In the case of GPEs, this undesirable reaction can be effectively curtailed due to the presence of a polymer skeleton. Based on this concept, Tan et al. proposed a successful method for achieving flame retardancy in GPEs by encapsulating the liquid flame-retardant TEP and ethylene carbonate (EC) within a polymer matrix [Figure 4A][69]. This approach not only accomplished the nonflammability of GPEs but also effectively impeded the undesirable reactivity of the flame retardant with the electrode surface through its strong interaction with the polymer backbone and lithium salt. TGA results demonstrated that the heat loss of the gel electrolyte was smaller compared with the LE [Figure 4B]. Moreover, the gel electrolyte exhibited an almost zero SET in the ignition test, signifying its excellent flame retardancy. Finally, the Li||LiNi0.8Co0.1Mn0.1 (NCM811) battery utilizing these GPEs exhibited a remarkable capacity retention of 98.7% after 300 cycles at 0.5 C while demonstrating commendable thermal stability and electrochemical performance.
Figure 4. (A) Mechanism for polymerization of VC. (B) TG analysis of different electrolytes in FRSE electrolyte system. This figure is quoted with permission from Tan et al.[69] (C) Digital image of the quasi-solid electrolyte membrane. This figure is quoted with permission from Chen et al.[71] (D) Microstructure, thermotolerance and flammability of the P(AN-DEVP)-based membrane. Thermal shrinkage of PAN and P(AN-DEVP) membranes. (E) Burning tests of PAN-GPEs and PA1D1-GPE. This figure is quoted with permission from Long et al.[72] (F) Possible flame-retardant mechanisms of NGPE; polymerized BCPN would release PO· radicals when heated, blocking the exothermic chain reactions. The inert gases, the decomposition products of polymerized BCPN (for example, N2), further inhibit the combustion process. R1 and R2 represent alkyl chains of ethers. (G) Voltage changes and the corresponding infrared thermal imaging photographs of fully charged Li||1 M LiPF6 in EC:DMC||NCM811 and Li||NGPE||NCM811 pouch cells during nail penetration tests. (H) LSV curves and the corresponding infrared thermal imaging photographs of Li||1 M LiPF6 in EC:DMC||NCM811 and Li||NGPE||NCM811 pouch cells at a scan rate of 20 mV s-1 from the open circuit voltage to 10 V. This figure is quoted with permission from Meng et al.[16].
Organic phosphates have also been used in high-concentration lithium salt electrolytes, and it has been shown that high concentrations of bis-fluorosulfonimide salts (FSI-) can effectively inhibit the parasitic reaction of phosphates with the anode[70]. Unfortunately, however, this approach does not solve the inherent problem of dendrite growth in liquid media. In order to solve the above problem, Chen et al. innovatively designed a polymer backbone to inhibit the Li dendrite growth in concentrated phosphate electrolytes[71]. The GPEs is a 5M LiFSI LE containing a flame-retardant TMP wrapped around a poly (methyl methacrylate) backbone with high mechanical properties formed by in situ polymerization using methyl methacrylate (MMA) as the monomer. This electrolyte reportedly combines the advantages of a phosphoric group-based lithium salt electrolyte with a high concentration of lithium salt and a polymer backbone to provide flame retardant, electrochemical stability, and high mechanical strength. The presence of a polymer backbone effectively overcomes the drawbacks of a highly concentrated electrolyte, as shown in Figure 4C, which minimizes the growth rate of Li dendrites using such GPEs. The results show that the assembled pouch cells can work normally, even under extreme folding and shearing conditions. Even in the extreme test where the cell was cut and the electrolyte was exposed to flame, the cell did not ignite and lit up the diode.
Phosphate-based polymer skeleton
The application of phosphates is not only limited to being used as flame retardants in GPEs but also includes using molecular design to enable the formation of polymer backbones in GPEs. In this regard, Long et al. presented a novel approach to utilizing phosphates in GPEs beyond their traditional role as flame retardants[72]. By cross-linking and polymerizing acrylonitrile and vinyl phosphate, they successfully synthesized a unique polymer backbone, poly(acrylonitrile-co-diethyl vinylphosphonate) [P(AN-DEVP)], which served as the foundation for a gel electrolyte (PA1D1-GPE) when combined with N,N-dimethylformamide as a plasticizer. The resulting porous separator demonstrated remarkable stability at high temperatures, with minimal shrinkage and no significant shape deformation at temperatures reaching 180 °C. In contrast, the commercial polypropylene (PP) separator exhibited pronounced melting under similar conditions [Figure 4D]. Furthermore, the PA1D1-GPEs displayed a LOI of only 17.0% and a short SET in ignition tests [Figure 4E], owing to the formation of a dense carbon layer post intense combustion. This carbon layer effectively insulated flammable gases and heat, preventing the further spread of combustion. Subsequent studies on pouch cells assembled with PA1D1-GPEs revealed their ability to operate normally even under bending, cutting, and pinning conditions. In combustion tests, the flexible pouch cells equipped with PA1D1-GPEs also showed an extremely short SET, highlighting the effectiveness of the unique phosphate-based backbone in enhancing safety and performance of the gel electrolyte system.
Cyclophosphonitrile-based polymer skeleton
Cyclotriphosphonitrile exhibits excellent flame-retardant properties due to its high phosphorus and nitrogen content[73]. Meng et al. innovatively designed a cyclotriphosphonitrile monomer, butenoxycyclotriphosphazene (BCPN), and introduced it into the polymer backbone for the first time[16]. This effectively strengthened the polymer into a gel state, forming a polymer matrix. This innovation led to the construction of a novel cyclotriphosphonitrile-based gel electrolyte (NGPE), utilizing a LE containing fluoromethyl 1,1,1,3,3,3-hexafluoroisopropyl ether as a cosolvent[16]. The NGPE demonstrated exceptional working performance under extreme conditions, exhibiting long-lasting durability and superior safety. Notably, in ignition tests, the NGPE displayed complete nonflammability. This was attributed to the ability of the PO· radicals generated by BCPN to spontaneously capture the hydrogen and oxygen radicals released from the thermal decomposition of the electrolyte, thus preventing the exothermic chain reaction. In addition, the generated inert gas N2 further inhibits the combustion process [Figure 4F]. Furthermore, owing to the physical properties of the NGPE, it remained leak-free during the leakage test. The high oxidative stability of NGPE effectively prevented the generation of flammable gases due to the continuous decomposition of the electrolyte, consequently averting an increase in the internal temperature of the battery. The Li|NGPE|NCM811 pouch cells exhibited no significant temperature changes during the pinning experiment [Figure 4G]. Under overcharge abuse conditions, the Li|NGPE|NCM811 pouch cells showed no significant temperature increase and current change during the test [Figure 4H]. Moreover, in the accelerating rate calorimetry (ARC) test, the Li||NGPE||NCM811 pouch cells demonstrated lower T1 and T2 and lower T3 than batteries using LEs. In addition, NGPE has achieved outstanding progress in cycling performance while maintaining a high level of safety. As reported, the assembled Li||NGPE||NCM811 coin cell demonstrated satisfactory performance following a 0.5 C cycle test. Notably, the battery exhibited a capacity retention of over 75% after 500 cycles, indicating its long-term stability. This exceptional performance can be attributed to the effective interaction of NGPE with the lithium metal and NCM811 electrodes, forming a highly stable passivation layer. Consequently, the battery demonstrates remarkably stable and durable cycling performance, thereby ensuring reliability in practical applications. Through enhancing safety and significantly improving cycle life, the advancements of NGPE have contributed positively to developing cyclic phosphonitrile-based GPEs.
Fluoride for GPEs
The growing interest in the flame retardancy of fluorinated solvents stems from the exceptional properties of fluorine atoms, which possess excellent oxidation resistance and are inherently resistant to oxidation[74,75]. When subjected to high temperatures, fluorinated solvents undergo pyrolysis reactions that produce fluorine radicals. These radicals can interact with the hydrogen radicals within the combustion chain reaction, effectively blocking the combustion chain reaction, as given in
Fluorinated additives
Currently, a viable strategy for achieving electrolyte nonflammability is to increase the fluorine content in electrolyte solvents. To improve the thermal stability of GPEs, it is feasible to introduce fluorinated solvents into the polymer matrix. Wu et al. have proposed an innovative approach to design a novel fluorinated electrolyte embedded in an organic polymer backbone[76]. They prepared this fluorinated electrolyte by dissolving 1 M LiPF6 in a mixture of fluorinated solvents, such as fluorinated EC (FEC), 2,2,2-trifluoroethyl carbonate and 1,1,2,3,3,3-hexafluoropropyl-2,2,2-trifluoroethyl ether [Figure 5A]. Subsequently, they formed fluorinated GPEs (HGPE) through in situ polymerization with the addition of 3 wt% of diethylallyl phosphate (DAP) and pentaerythritol tetraacrylate (PETEA). In linear scanning voltammetry (LSV) testing, the oxidation current of this GPE was as low as 5.8 V [Figure 5B]. This is attributed to the high oxidative stability of the fluorinated solvent, significantly enhancing the stability of this GPE under galvanic corrosion conditions. During the ignition test, HGPE exhibited zero SET, indicating excellent nonflammability due to the capture of hydrogen radicals by fluorine radicals, thereby reducing the risk of combustion. Furthermore, Li||Li2RuO3 (LRO) pouch cells assembled with HGPE showed no voltage and shape changes after aging at 130 °C for 2,500 s, in contrast to the voltage changes and swelling of the cells assembled with LE starting in 1,964 s [Figure 5C]. Additionally, HGPE exhibited high ionic conductivity (1.99 mS cm-1) at room temperature due to fluorinated solvents, confirming that it combines both high safety and high ionic conductivity.
Figure 5. (A) Optical images of the precursor solution (left) and the corresponding HGPE (right) after copolymerization; (B) LSV curves of 1 M LiPF6 in EC:EMC electrolyte and HGPE at a scan rate of 5 mV s-1, using platinum foil as the working electrode and Li foil as the counter and reference electrodes; (C) Open circuit voltage changes of fully charged Li||1 M LiPF6 in EC:EMC||LRO/graphite and Li||HGPE||LRO/graphite pouch cells at 130 °C during the aging time. Optical images of the pouch cells after aging at 130 °C for half an hour are shown in the inset. This figure is quoted with permission from Wu et al.[76] (D) Schematic illustration of synergistic flame-retardant mechanisms of HFBA-PETEA polymer electrolytes; (E) Infrared thermography and digital photographs of LE-based and QSE-based pouch cells upon overheating; (F) Infrared thermography of LE-based and QSE-based pouch cells upon short-circuit and nail penetration; This figure is quoted with permission from Hu et al.[77] (G) Schematic diagram of the flame-retardant gel electrolyte (FRGE); (H) Combustion tests of the LCE and FRGE; (I) Long-term cycling performance of Li||LFP cells containing different electrolytes at 0.5 C and (J) the corresponding charge/discharge curves; This figure is quoted with permission from Liu et al.[78].
Fluorinated polymer backbone
Introducing flame-retardant components into the polymer backbone can improve the thermal stability of GPEs to some extent. However, the thermal safety of GPEs still needs to be improved due to the use of conventional organic electrolytes. Hu et al. recently developed an innovative new polymer matrix using the fluorinated monomer hexafluorobutyl acrylate (HFBA) for in situ radical polymerization with a PETEA cross-linker[77]. This approach transferred the conventional liquid-phase addition of fluorinated solvents to the polymer backbone. It does not require the addition of flame retardants, and possible flammability caused by liquid organic solvents is eliminated by the gas-phase radical scavenging action of HFBA. Consequently, the resulting GPEs do not necessitate additional flame retardants. This remarkable nonflammability phenomenon can be attributed to the fact that at high temperatures, the F· radicals spontaneously formed by the fluorinated monomer HFBA effectively trap the H· radicals generated in the LE [Figure 5D]. This trapping effect blocked the chain reaction of combustion, thus terminating the further propagation of H· radicals. In the ignition test, the GPE exhibited significant nonflammability. Interestingly, it was also found that the combusted GPE formed a very dense char layer due to the presence of PETEA-HFBA chains. This highly graphitized char layer effectively isolated the oxygen and heat required for combustion. This GPE utilizing a synergistic flame-retardant mechanism between the gas and condensed phases greatly improves the thermal safety of the battery. In the next study, pouch cells with GPEs were evaluated for safety and tested for various abuse conditions. As shown in Figure 5E, when the battery was overcharged to 4.5 V, the LE pouch cell experienced significant thermal runaway, while the GPE pouch cell exhibited only a slight temperature increase. Additionally, the pouch cell with the GPE exhibited minimal temperature change after pinning compared to LEs [Figure 5F]. This clearly highlights the superior safety offered by this GPE. In subsequent heating and open flame exposure tests, the pouch cell using the GPE showed good flame resistance. This series of safety evaluation results further confirms the excellent safety performance of batteries utilizing this innovative GPE under a wide range of abuse conditions and provides a strong foundation for its reliability in real-world applications.
Fluorinated phosphates-based polymer skeleton
Liu et al. have successfully developed bifunctional GPEs by incorporating fluorine and phosphate esters, which exhibit a good synergistic effect[78]. The electrolyte composition includes a cross-linked polymer skeleton formed by poly(ethylene glycol) dimethacrylate (PEGDMA) and PETEA, to which a liquid ester electrolyte containing 2-fluoro-2-phosphonoacetate as a plasticizer is added. Furthermore, the addition of Triethyl 2-fluoro-2-phosphonoacetate (TFBA)-containing liquid ester electrolyte as a plasticizer, and the final product was produced by in-situ polymerization [Figure 5G][78]. The resulting fluorine-phosphonate-based gel electrolyte (FRGE) is reported to be translucent and exhibits zero SET, indicating its high flame retardancy [Figure 5H]. Notably, introducing phosphates has increased the decomposition temperature of FRGE compared to conventional liquid ester electrolytes, supporting its high-temperature stability. The FRGE, attributed to the synergistic effect between the fluorine groups and the polymer backbone, shows excellent electrochemical window and electrode-interface compatibility. Moreover, it effectively reduces parasitic reactions of the electrolyte on the electrode interface. The polymer backbone contributes to the high Young’s modulus of FRGE, which physically inhibits the Li dendrite growth, thus enhancing safety. Experimental validation demonstrates that the FRGE-assembled pouch cells maintain normal operation under severe conditions such as bending, pinning, and ignition. These results emphasize the high safety features resulting from the synergistic interaction among fluorine and phosphate groups and the polymer backbone. Furthermore, experimental validation shows that the Li||Li||LiFePO4 (LFP) battery assembled with FRGE maintains a high-capacity retention rate of 94.6% after 700 cycles at 0.5 C [Figure 5I and J]. This demonstrates the excellent cycling performance of the FRGE in Li||LFP batteries, reflecting its capabilities in ensuring battery safety and stability.
Nitrile for GPEs
Nitrile solvents, such as succinonitrile (SN), have gained extensive attention and application in flame retardancy in Les owing to their exceptional thermal stability, high dielectric constant, and broad electrochemical window[79]. These solvents, when subjected to high temperatures, release non-flammable inert gases, such as N2, which play a crucial role in suppressing combustion propagation and thereby averting thermal runaway incidents. Nonetheless, butanedinitrile, in particular, presents several challenges due to its lowest unoccupied molecular orbital (LUMO) and poor compatibility with Li anodes, thus restricting its applicability in lithium batteries[80]. The issue with butanedinitrile is expected to be addressed in GPEs. When the nitrile groups are incorporated into the polymer backbone, it is expected to significantly alleviate the parasitic reaction between the nitrile groups and the Li anode, thereby enhancing the suitability of such solvents in LMBs.
Based on this concept, Sun et al. successfully embedded fumaronitrile (FN) into a polymer backbone constructed from MMA and ethoxylated trimethylolpropane triacrylate (ETPTA)[81]. The free nitrile groups were grafted onto the polymer chains by reacting with C=C unsaturated bonds [Figure 6A]. Subsequently, a lithium difluoro(oxalato)borate (LiDFOB)-containing LE was introduced to regulate the compatibility of the electrode/electrolyte interface. It was reported that this GPE (FN-based GPE (FGPE)) not only effectively prevented the parasitic reaction between the nitrile groups and the Li anode, but also realized the flame-retardant properties of the electrolyte, exhibiting a prolonged period of 12 s of nonflammability in the ignition test. In addition, FGPE displays a low glass transition temperature, indicating that Li+ ions can migrate more rapidly. Pouch cells assembled with this electrolyte show excellent safety when subjected to extreme conditions such as cutting and repeated twisting, even after being cut for 12 h. Moreover, subsequent gas production experiments were conducted to evaluate its thermal stability. After a week of storage at 80 °C, the pouch cells showed little volume change and exhibited excellent thermal stability compared to the results obtained with the LE. These results demonstrate the excellent thermal stability of FGPE. In addition, the FGPE also exhibits good cycling performance [Figure 6B and C]; Li||LFP batteries assembled with this electrolyte could cycle stably at 0.5 C for 200 cycles at 60 °C and also had good capacity retention in the rate performances [Figure 6D].
Figure 6. (A) Structural formula of MMA, FN and ETPTA monomers and possible structural diagram of FGPE; (B) Cycling performances of two batteries at 60 °C; (C) Charge/discharge profiles of Li||FGPE||LFP battery at 0.5 C and 60 °C; (D) Rate performances from 0.1 to 10 C; This figure is quoted with permission from Sun et al.[81] (E) The SET of v-NBR/TAC/IL electrolyte with different weight percentages of TAC; (F) The mechanism of flame retardance of v-NBR/TAC/IL electrolyte; (G) DTG curves of v-NBR/TAC/IL,
In addition, the nitrile group can be introduced into the polymer backbone as a cross-linking agent.
Amide for GPEs
Similar to nitrile flame retardants, amide flame retardants are also nitrogen-based. When exposed to heat, they generate inert gases such as N2, effectively mitigating the risk of combustion and thermal runaway. Due to their outstanding flame-retardant properties, amide groups are extensively employed in the electrolytes of LMBs[83]. Zhu et al. developed an innovative gel electrolyte based on an amide-based skeleton, successfully synthesizing a GPE during the preparation process by mixing the LE with 3% N,N'-methylene bis (acrylamide) and polymerizing it in situ[58]. Through this method, GPEs with nonflammable properties in ignition tests were produced, attributed to forming a polymer cross-linking network by N,N'-methylene bis(acrylamide) [Figure 6H]. Furthermore, the GPEs demonstrated a significantly high Young’s modulus, effectively preventing the overgrowth of Li dendrites, thereby reducing potential safety hazards. To assess the feasibility of practical applications, the research team conducted pinning experiments on the assembled Li||lithium-rich layered oxide (LLO) pouch cells. Encouragingly, the experimental results showed that the pouch battery maintained normal operation without performance failure or burning. These experiments highlight the excellent safety features of amide-based GPEs in practical applications. Additionally, the introduction of amide groups not only improved the oxidation window of the electrolyte, but also maintained a capacity retention of up to 97.6% after 160 cycles for Li||LLO batteries assembled with this gel electrolyte, further confirming the significant impact of amide-based GPEs on battery performance. Consequently, these findings demonstrate the multifaceted benefits and potential of amide-based GPEs in enhancing both the safety and performance of LMBs.
Polyimide for GPEs
Polyimide (PI), as a polymer, shares similarities with other amides in terms of vapor phase flame retardancy[84]. If it is incorporated into the polymer backbone, it can significantly enhance the thermal safety of GPEs. Its excellent heat resistance and flame retardancy play a crucial role in augmenting the thermal safety of LMBs by effectively preventing thermal runaway. To further improve its performance and reduce potential safety risks, Zhang et al. have successfully synthesized a unique PI that exhibits the ability to cross-link and polymerize with solvents in conventional carbonate electrolytes to form a special gel electrolyte (GPE-PI10), thereby effectively reducing potential hazards arising from carbonate solvent leakage
Silicon-based for GPEs
Silicone-based GPEs typically consist of polysiloxanes and sesquisiloxanes. Silicones, known for their exceptional thermal stability and nonflammability, are thought to enhance the thermal safety of GPEs. Zhang et al. conducted the successful synthesis of a novel silicone-doped polyether-type GPEs (PTCDs) through the in-situ copolymerization of tetracyclooxy-cyclosiloxanes and 1,3-dioxolane (DOL)[86]. PTCD has been found to exhibit remarkable thermal stability, maintaining a stable state even at elevated temperatures, unlike poly(1,3-dioxolane) (PDOL) which becomes viscous at 70 °C. This thermal performance improvement highlights the efficacy of organosilicon introduction in enhancing the thermal safety of GPEs. Moreover, using PTCD in LMBs substantially enhanced cycle stability, enabling a stable operation for up to 1,000 cycles. An alternative development in this domain was introduced by Chen et al. by creating polydimethylsiloxane-based GPEs known as flame-retardant GPEs (DSHP)[87]. DSHP was synthesized via the in-situ copolymerization of bis(3-aminopropyl)-terminated polydimethylsiloxane with toluene 2,4-diisocyanate, complemented by the addition of FEC and lithium bis(trifluoromethanesulfonyl)imide (LiTFSI) as plasticizers. Noteworthy for its flame-retardant properties with an unprecedented SET value of 0, DSHP is completely noncombustible. Additionally, it possesses an exceptional self-healing capability, enabling it to spontaneously revert to its original form after being cut at 50 °C. Offering remarkable tensile properties and the ability to stretch up to four times its length, DSHP has demonstrated favorable characteristics for application in GPEs. Encouragingly, Li||LiCoO2 (LCO) pouch cells integrated with DSHP exhibited proper functionality even after being subjected to 180-degree bending, underscoring the significant safety benefits that DSHP confers upon LMBs.
Polymer composite separators
The separator plays a crucial role in thermal runaway, in addition to the electrolyte. Particularly, its thermal stability, which is the carrier of the electrolyte, is fragile, especially in the case of commonly used polymer separators (e.g., PP and polyethylene (PE) separators). When exposed to high temperatures, these separators quickly melt, thereby worsening the thermal runaway process. An emerging and noteworthy development is the introduction of a new thermally stable separator known as the polymer composite separator. This type of separator has garnered significant attention because it is formed by applying flame retardants or inorganic particles onto its surface, providing enhanced thermal stability. Moreover, this specialized separator can exhibit a state akin to GPEs following the absorption of LE. Yang et al. reported their study results on a new flame-retardant separator, in which they developed a flame-retardant polymer composite separator (DCPE) by directly applying flame-retardant coatings of decabromodiphenyl ethane (DBDPE) and CaO onto a PE separator[88]. The DCPE exhibits a dual flame-retardant mechanism and a remarkable SET of only 2.8 s upon penetration by LE. Moreover, their research findings show that the pouch cell assembled with DCPE displays a significantly prolonged thermal runaway process when subjected to a baking condition of 180 °C. This suggests the effective capability of DCPE in inhibiting thermal runaway and attenuating the heat accumulation and explosion risk.
Ceramic particles are widely recognized as an effective method for enhancing the thermal safety of electrolytes. However, their utilization in practical applications has been restricted because of their limited solubility in the electrolyte. Coating ceramic particles on the separator surface has been found to successfully overcome this challenge. Roh et al. proposed a novel ceramic particle-coated polymer composite separator by encapsulating TEP in a copolymer of MMA and ethylene glycol dimethacrylate and blending it with aluminum hydroxide[89]. This flame-retardant coating was then uniformly applied onto a PE separator to develop a distinct flame-retardant polymer composite separator [flame-retardant ceramic-coated separator (F-CCS)]. The unique characteristic of F-CCS lies in its ability to exhibit a shorter SET than regular separators during ignition tests, attributed to the synergistic flame-retardant impact generated by TEP and ceramic particles. Notably, F-CCS retains 80.9% of its area at a temperature of 140 °C. To evaluate the safety of flexible pouch cells utilizing F-CCS, charge/discharge tests were carried out at 140 °C. The outcomes indicate that it demonstrates consistent voltage stability, thereby corroborating the considerable enhancement in battery safety conferred by F-CCS.
CONCLUSION AND OUTLOOK
To ensure the safety of LMBs, the strategy of introducing flame retardants into LEs or replacing conventional solvents with flame retardants has been proposed. However, this measure did not solve the inherent problem of LEs being prone to leakage. Subsequently, SSEs with non-leakage susceptibility and high mechanical strength have been proposed; nevertheless, their poor interfacial compatibility and low ion transport efficiency pose challenges in practical applications. In an attempt to compensate for these shortcomings, GPEs, which combine the advantages of both LEs and SSEs, have emerged. Figure 7 summarizes the key properties of the various electrolytes. GPEs offer non-leakage properties that reduce safety risks, while internal plasticizers address the interfacial compatibility issues of SSEs. However, the highly flammable LE in GPEs still presents a potential safety hazard. Efforts have been made to improve the safety of GPEs by developing nonflammable GPEs. The approaches include incorporating flame retardants into plasticizers or using flame retardants and grafting flame-retardant groups onto the polymer backbone. Combining these two approaches can lead to safer and more reliable GPEs. This review first provides a brief analysis of the mechanism of thermal runaway in LMBs and then introduces the characterization methods for assessing the thermal safety of batteries. Finally, it presents a categorization of various GPEs and their synthesis methods and provides suggestions for improving the safety of LMBs by combining different moieties. Despite the innovative results in secure GPEs and LMBs, comprehensive research is still needed to address the following aspects and realize truly secure and reliable GPEs and LMBs.
(1) The first prerequisite for solving the thermal runaway problem of LMBs is a thorough understanding of the evolution of this phenomenon. However, the existing research on the thermal runaway process of LMBs has yet to achieve the necessary depth. This deficiency can be attributed to the unique anode structure of LMBs, which results in a thermal runaway process different from that of LIBs. Therefore, it is essential to emphasize the need for thoroughly examining the thermal runaway process of LMBs, with a specific focus on the potential impact of dead Li generated by the anode during the cycling process. This aspect requires more detailed exploration and elucidation. Only by gaining a comprehensive understanding of these crucial processes can we effectively address the thermal runaway problem and furnish robust support for enhancing the reliability and performance of LMBs.
(2) Improving the temperature adaptability of GPEs is crucial for ensuring consistent and reliable performance across a wide temperature range. GPEs face challenges under extreme conditions as specific components may volatilize at high temperatures, leading to electrolyte failure, while at low temperatures, they may solidify, impeding effective ion transport. Currently, there is a lack of comprehensive studies on GPEs that operate optimally in varying temperatures. Therefore, research focused on enhancing the temperature adaptability of GPEs is of utmost importance for their viability in LMBs under diverse environmental conditions. It is essential to address this issue to ensure the efficient and reliable performance of LMBs, even under extreme temperatures.
(3) At present, safe GPEs still exhibit certain disadvantages in terms of ionic conductivity when compared to LEs. Despite significant advancements in research, most results remain comparable to those of LEs or show only marginal differences in ionic conductivity. Therefore, there is a pressing need for future research to overcome the current limitations in ionic conductivity and develop GPEs that significantly surpass the performance of LEs. Simultaneously, it is imperative for such innovations to prioritize safety considerations and maintain the overall reliability of the battery system.
(4) To comprehensively explore the performance and thermal runaway mechanism of LMBs, advanced characterization techniques need to be introduced to enable nondestructive observation of the internal conditions of the batteries. This urgent requirement arises from monitoring various aspects of the battery interior, such as the state of gas production, changes in the diaphragm and SEI, and the state of the electrolyte, without causing any damage to the battery. This will greatly facilitate future research and exploration of safe, rechargeable power sources. The ability to gain a more comprehensive understanding of the operating mechanism of the battery through nondestructive observation will provide strong support for performance improvements, lifespan extension, and increased safety.
DECLARATIONS
Acknowledgments
The authors acknowledge the financial support provided by the National Natural Science Foundation of China (21805018; 52002039), the Natural Science Foundation of Sichuan Province (24NSFSC4536), the Scientific Research Startup Foundation of Chengdu University of Technology (10912-KYQD2023-10240). And the authors would like to thank SCI-GO (www.sci-go.com) for the drawing schematic illustration.
Authors’ contributions
Conceptualization, visualization, methodology, writing-original draft: Yang B
Conceptualization, visualization: Li T
Formal analysis, Validation: Pan Y, Yang L
Formal analysis: Li K, Chen J
Validation: Yan Z
Investigation, writing - review & editing: Hu A
Funding acquisition, project administration, supervision: Long J
Availability of data and materials
Not applicable.
Financial support and sponsorship
This work was supported by the National Natural Science Foundation of China (21805018; 52002039), the Sichuan Science and Technology Project (18ZHSF0013) and the Scientific Research Startup Foundation of Chengdu University of Technology (10912-KYQD2023-10240).
Conflicts of interest
All authors declared that there are no conflicts of interest.
Ethical approval and consent to participate
Not applicable.
Consent for publication
Not applicable.
Copyright
© The Author(s) 2024.
REFERENCES
1. Xu J, Zhang J, Pollard TP, et al. Electrolyte design for Li-ion batteries under extreme operating conditions. Nature 2023;614:694-700.
2. Ning Z, Li G, Melvin DLR, et al. Dendrite initiation and propagation in lithium metal solid-state batteries. Nature 2023;618:287-93.
3. Wang CY, Liu T, Yang XG, et al. Fast charging of energy-dense lithium-ion batteries. Nature 2022;611:485-90.
4. He M, Chen J, Hu A, Yan Z, Cao L, Long J. Manipulating cation-water chemistry to inhibit hydrogen evolution of zinc metal anodes. Energy Stor Mater 2023;62:102941.
5. Zou R, Liu W, Ran F. Sulfur-containing polymer cathode materials: from energy storage mechanism to energy density. InfoMat 2022;4:e12319.
6. Li Z, Sami I, Yang J, Li J, Kumar RV, Chhowalla M. Lithiated metallic molybdenum disulfide nanosheets for high-performance lithium-sulfur batteries. Nat Energy 2023;8:84-93.
7. Wang G, Zhu M, Zhang Y, et al. Double interface regulation: toward highly stable lithium metal anode with high utilization. InfoMat 2022;4:e12293.
8. Zhao C, Yan Z, Zhou B, et al. Identifying the role of lewis-base sites for the chemistry in lithium-oxygen batteries. Angew Chem Int Ed 2023;62:e202302746.
9. Hu A, Chen W, Du X, et al. An artificial hybrid interphase for an ultrahigh-rate and practical lithium metal anode. Energy Environ Sci 2021;14:4115-24.
10. Hu A, Lv W, Lei T, et al. Heterostructured NiS2/ZnIn2S4 realizing toroid-like Li2O2 deposition in lithium-oxygen batteries with low-donor-number solvents. ACS Nano 2020;14:3490-9.
11. Kim MS, Zhang Z, Rudnicki PE et al. Suspension electrolyte with modified Li+ solvation environment for lithium metal batteries. Nat Mater 2022;21:445-54.
12. Hu A, Li F, Chen W, et al. Ion transport kinetics in low-temperature lithium metal batteries. Adv Energy Mater 2022;12:2202432.
13. Yin Y, Yang Y, Cheng D, et al. Fire-extinguishing, recyclable liquefied gas electrolytes for temperature-resilient lithium-metal batteries. Nat Energy 2022;7:548-59.
14. Hu A, Zhou M, Lei T, et al. Optimizing redox reactions in aprotic lithium-sulfur batteries. Adv Energy Mater 2020;10:2002180.
15. Zhou B, Li T, Hu A, et al. Scalable fabrication of ultra-fine lithiophilic nanoparticles encapsulated in soft buffered hosts for long-life anode-free Li2S-based cells. Nanoscale 2023;15:15318-27.
16. Meng Y, Zhou D, Liu R, et al. Designing phosphazene-derivative electrolyte matrices to enable high-voltage lithium metal batteries for extreme working conditions. Nat Energy 2023;8:1023-33.
17. Chen S, Zheng J, Yu L, et al. High-efficiency lithium metal batteries with fire-retardant electrolytes. Joule 2018;2:1548-58.
18. Yang B, Pan Y, Li T, et al. High-safety lithium metal pouch cells for extreme abuse conditions by implementing flame-retardant perfluorinated gel polymer electrolytes. Energy Stor Mater 2024;65:103124.
19. Li Y, Hu A, Gan X, et al. Synergy of in-situ heterogeneous interphases tailored lithium deposition. Nano Res 2023;16:8304-12.
20. Phan AL, Jayawardana C, Le PM, et al. Solvent-free electrolyte for high-temperature rechargeable lithium metal batteries. Adv Funct Mater 2023;33:2301177.
21. Wang S, Xu K, Song H, et al. A high-energy long-cycling solid-state lithium-metal battery operating at high temperatures. Adv Energy Mater 2022;12:2201866.
22. Zhou Q, Dong S, Lv Z, et al. Lithium metal batteries: a temperature-responsive electrolyte endowing superior safety characteristic of lithium metal batteries (Adv. Energy Mater. 6/2020). Adv Energy Mater 2020;10:2070023.
23. Zhu GR, Zhang Q, Liu QS, et al. Non-flammable solvent-free liquid polymer electrolyte for lithium metal batteries. Nat Commun 2023;14:4617.
24. Yuan S, Ding K, Zeng X, et al. Advanced nonflammable organic electrolyte promises safer Li-metal batteries: from solvation structure perspectives. Adv Mater 2023;35:e2206228.
25. Liu Q, Liu R, Cui Y, et al. Dendrite-free and long-cycling lithium metal battery enabled by ultrathin, 2D shield-defensive, and single lithium-ion conducting polymeric membrane. Adv Mater 2022;34:e2108437.
26. Kim J, Engelhard MH, Lu B, et al. High current-density-charging lithium metal batteries enabled by double-layer protected lithium metal anode. Adv Funct Mater 2022;32:2207172.
27. Liang J, Chen Q, Liao X, et al. A nano-shield design for separators to resist dendrite formation in lithium-metal batteries. Angew Chem Int Ed 2020;59:6561-6.
28. Sheng O, Jin C, Yang T, Ju Z, Luo J, Tao X. Designing biomass-integrated solid polymer electrolytes for safe and energy-dense lithium metal batteries. Energy Environ Sci 2023;16:2804-24.
29. Li R, Fan Y, Zhao C, et al. Air-stable protective layers for lithium anode achieving safe lithium metal batteries. Small Methods 2023;7:e2201177.
30. Huang L, Lu T, Xu G, et al. Thermal runaway routes of large-format lithium-sulfur pouch cell batteries. Joule 2022;6:906-22.
31. Zhang X, Huang L, Xie B, et al. Deciphering the thermal failure mechanism of anode-free lithium metal pouch batteries. Adv Energy Mater 2023;13:2203648.
32. Chen R, Nolan AM, Lu J, et al. The thermal stability of lithium solid electrolytes with metallic lithium. Joule 2020;4:812-21.
33. Wang J, Yang K, Sun S, et al. Advances in thermal-related analysis techniques for solid-state lithium batteries. InfoMat 2023;5:e12401.
34. Feng X, Ren D, He X, Ouyang M. Mitigating thermal runaway of lithium-ion batteries. Joule 2020;4:743-70.
35. Yang S, Hu J, Jiang F, Yuan H, Park HS, Huang J. Safer solid-state lithium metal batteries: mechanisms and strategies. InfoMat 2024;6:e12512.
36. Gou J, Zhang Z, Wang S, Huang J, Cui K, Wang H. An ultrahigh modulus gel electrolytes reforming the growing pattern of Li dendrites for interfacially stable lithium-metal batteries. Adv Mater 2024;36:e2309677.
37. Cavers H, Molaiyan P, Abdollahifar M, Lassi U, Kwade A. Perspectives on improving the safety and sustainability of high voltage lithium-ion batteries through the electrolyte and separator region. Adv Energy Mater 2022;12:2200147.
38. Lee S, Park K, Koo B, et al. Safe, stable cycling of lithium metal batteries with low-viscosity, fire-retardant locally concentrated ionic liquid electrolytes. Adv Funct Mater 2020;30:2003132.
39. Zhang L, Min F, Luo Y, et al. Practical 4.4 V Li||NCM811 batteries enabled by a thermal stable and HF free carbonate-based electrolyte. Nano Energy 2022;96:107122.
40. Hu L, Wang J, Wang K, et al. A cost-effective, ionically conductive and compressible oxychloride solid-state electrolyte for stable all-solid-state lithium-based batteries. Nat Commun 2023;14:3807.
41. Wang C, Xu BB, Zhang X, et al. Ion hopping: design principles for strategies to improve ionic conductivity for inorganic solid electrolytes. Small 2022;18:e2107064.
42. Zhao C, Pan Y, Li R, et al. A safe anode-free lithium metal pouch cell enabled by integrating stable quasi-solid electrolytes with oxygen-free cathodes. Chem Eng J 2023;463:142386.
43. Jia H, Onishi H, Wagner R, Winter M, Cekic-Laskovic I. Intrinsically safe gel polymer electrolyte comprising flame-retarding polymer matrix for lithium ion battery application. ACS Appl Mater Interfaces 2018;10:42348-55.
44. Liu K, Liu W, Qiu Y, et al. Electrospun core-shell microfiber separator with thermal-triggered flame-retardant properties for lithium-ion batteries. Sci Adv 2017;3:e1601978.
45. Jaumaux P, Liu Q, Zhou D, et al. Deep-eutectic-solvent-based self-healing polymer electrolyte for safe and long-life lithium-metal batteries. Angew Chem Int Ed 2020;59:9134-42.
46. Son K, Hwang SM, Woo S, Paik M, Song EH, Kim Y. Thermal and chemical characterization of the solid-electrolyte interphase in
47. Zhang Q, Zhang X, Yuan H, Huang J. Thermally stable and nonflammable electrolytes for lithium metal batteries: progress and perspectives. Small Science 2021;1:2100058.
48. Bandhauer TM, Garimella S, Fuller TF. A critical review of thermal issues in lithium-ion batteries. J Electrochem Soc 2011;158:R1.
49. Fu C, Venturi V, Kim J, et al. Universal chemomechanical design rules for solid-ion conductors to prevent dendrite formation in lithium metal batteries. Nat Mater 2020;19:758-66.
50. Chen J, Cheng Z, Liao Y, Yuan L, Li Z, Huang Y. Selection of redox mediators for reactivating dead Li in lithium metal batteries. Adv Energy Mater 2022;12:2201800.
51. Gan Y, Liu M, Tan R, et al. Flame-retardant crosslinked polymer stabilizes graphite-silicon composite anode for self-extinguishing lithium-ion batteries. Adv Energy Mater 2022;12:2202779.
52. Tian X, Yi Y, Fang B, et al. Design strategies of safe electrolytes for preventing thermal runaway in lithium ion batteries. Chem Mater 2020;32:9821-48.
53. Li S, Zhang S, Chai S, et al. Structured solid electrolyte interphase enable reversible Li electrodeposition in flame-retardant phosphate-based electrolyte. Energy Stor Mater 2021;42:628-35.
54. Huang Q, Li X, Zhang G, Weng J, Wang Y, Deng J. Innovative thermal management and thermal runaway suppression for battery module with flame retardant flexible composite phase change material. J Clean Prod 2022;330:129718.
55. Xie J, Qiao S, Wang Y, et al. Three-in-one fire-retardant poly(phosphate)-based fast ion-conductor for all-solid-state lithium batteries. J Energy Chem 2023;80:324-34.
56. Du Y, Liu X, Chen L, et al. 3D hierarchical fireproof gel polymer electrolyte towards high-performance and comprehensive safety lithium-ion batteries. Chem Eng J 2023;476:146605.
57. Zhang C, Lu Z, Song M, et al. Highly oxidation-resistant ether gel electrolytes for 4.7 V high-safety lithium metal batteries. Adv Energy Mater 2023;13:2203870.
58. Zhu J, Zhang J, Zhao R, et al. In situ 3D crosslinked gel polymer electrolyte for ultra-long cycling, high-voltage, and high-safety lithium metal batteries. Energy Stor Mater 2023;57:92-101.
59. Le Mong A, Kim D. Acceleration of selective lithium ion transport of PAES-g-2PEG self-assembled flexible solid-state electrolytes for lithium secondary batteries. Energy Stor Mater 2022;47:394-407.
60. Yang SJ, Yao N, Jiang FN, et al. Thermally stable polymer-rich solid electrolyte interphase for safe lithium metal pouch cells. Angew Chem Int Ed 2022;61:e202214545.
61. Jiang FN, Cheng XB, Yang SJ, et al. Thermoresponsive electrolytes for safe lithium-metal batteries. Adv Mater 2023;35:e2209114.
62. Zhang S, Sun F, Du X, et al. In situ -polymerized lithium salt as a polymer electrolyte for high-safety lithium metal batteries. Energy Environ Sci 2023;16:2591-602.
63. Huang X, Huang S, Wang T, et al. Polyether-b-amide based solid electrolytes with well-adhered interface and fast kinetics for ultralow temperature solid-state lithium metal batteries. Adv Funct Mater 2023;33:2300683.
64. Ouyang D, Chen M, Liu J, Wei R, Weng J, Wang J. Investigation of a commercial lithium-ion battery under overcharge/over-discharge failure conditions. RSC Adv 2018;8:33414-24.
65. Zhou Z, Li M, Zhou X, Li L, Ju X, Yang L. Investigating thermal runaway triggering mechanism of the prismatic lithium iron phosphate battery under thermal abuse. Renew Energy 2024;220:119674.
66. Jiang G, Liu J, Wang Z, Ma J. Stable non-flammable phosphate electrolyte for lithium metal batteries via solvation regulation by the additive. Adv Funct Mater 2023;33:2300629.
67. Wang X, He W, Xue H, et al. A nonflammable phosphate-based localized high-concentration electrolyte for safe and high-voltage lithium metal batteries. Sustain Energy Fuels 2022;6:1281-8.
68. Zhang S, Li S, Lu Y. Designing safer lithium-based batteries with nonflammable electrolytes: a review. eScience 2021;1:163-77.
69. Tan S, Yue J, Tian Y, et al. In-situ encapsulating flame-retardant phosphate into robust polymer matrix for safe and stable quasi-solid-state lithium metal batteries. Energy Stor Mater 2021;39:186-93.
70. Xiao L, Zeng Z, Liu X, et al. Stable Li metal anode with “ion-solvent-coordinated” nonflammable electrolyte for safe Li metal batteries. ACS Energy Lett 2019;4:483-8.
71. Chen J, Yang Z, Liu G, et al. Reinforcing concentrated phosphate electrolytes with in-situ polymerized skeletons for robust quasi-solid lithium metal batteries. Energy Stor Mater 2020;25:305-12.
72. Long M, Wu G, Wang X, Wang Y. Self-adaptable gel polymer electrolytes enable high-performance and all-round safety lithium ion batteries. Energy Stor Mater 2022;53:62-71.
73. Lu D, Zhang S, Li J, et al. Transformed solvation structure of noncoordinating flame-retardant assisted propylene carbonate enabling high voltage Li-Ion batteries with high safety and long cyclability. Adv Energy Mater 2023;13:2300684.
74. Fan X, Ji X, Chen L, et al. All-temperature batteries enabled by fluorinated electrolytes with non-polar solvents. Nat Energy 2019;4:882-90.
75. Liu Y, Tao X, Wang Y, et al. Self-assembled monolayers direct a LiF-rich interphase toward long-life lithium metal batteries. Science 2022;375:739-45.
76. Wu J, Wang X, Liu Q, et al. A synergistic exploitation to produce high-voltage quasi-solid-state lithium metal batteries. Nat Commun 2021;12:5746.
77. Hu A, Chen W, Li F, et al. Nonflammable polyfluorides-anchored quasi-solid electrolytes for ultra-safe anode-free lithium pouch cells without thermal runaway. Adv Mater 2023;35:e2304762.
78. Liu F, Lan T, Chen K et al. In situ polymerized flame retardant gel electrolyte for high-performance and safety-enhanced lithium metal batteries. ACS Appl Mater Interfaces 2023;15:23136-45.
79. Das S, Bhattacharyya AJ. Influence of water and thermal history on ion transport in lithium salt-succinonitrile plastic crystalline electrolytes. Solid State Ionics 2010;181:1732-9.
80. Hu P, Chai J, Duan Y, Liu Z, Cui G, Chen L. Progress in nitrile-based polymer electrolytes for high performance lithium batteries. J Mater Chem A 2016;4:10070-83.
81. Sun Q, Wang S, Ma Y, et al. Fumaronitrile-fixed in-situ gel polymer electrolyte balancing high safety and superior electrochemical performance for Li metal batteries. Energy Stor Mater 2022;44:537-46.
82. Zhang D, Shi Y, An J, Yang S, Li B. Triallyl cyanurate copolymerization delivered nonflammable and fast ion conducting elastic polymer electrolytes. J Mater Chem A 2022;10:23095-102.
83. Zhang Q, Zhang X, Hou L, et al. Regulating solvation structure in nonflammable amide-based electrolytes for long-cycling and safe lithium metal batteries. Adv Energy Mater 2022;12:2200139.
84. Liu Y, Li C, Li C, et al. Porous, robust, thermally stable, and flame retardant nanocellulose/polyimide separators for safe lithium-ion batteries. J Mater Chem A 2023;11:23360-9.
85. Zhang H, Chen J, Liu J, et al. Gel electrolyte with flame retardant polymer stabilizing lithium metal towards lithium-sulfur battery. Energy Stor Mater 2023;61:102885.
86. Zhang Q, Liu X, Li H, et al. A multifunctional silicon-doped polyether network for double stable interfaces in quasi-solid-state lithium metal batteries. Small 2022;18:e2106395.
87. Chen Y, Ling C, Long K, et al. A siloxane-based self-healing gel electrolyte with deep eutectic solvents for safe quasi-solid-state lithium metal batteries. Chem Eng J 2024;488:150888.
88. Yang JH, Jeong YK, Kim W. Dual flame-retardant mechanism-assisted suppression of thermal runaway in lithium metal batteries with improved electrochemical performances. Adv Energy Mater 2024:2304366.
Cite This Article
Export citation file: BibTeX | EndNote | RIS
OAE Style
Yang B, Li T, Pan Y, Yang L, Li K, Chen J, Yan Z, Hu A, Long J. Design strategy towards flame-retardant gel polymer electrolytes for safe lithium metal batteries. Energy Mater 2024;4:400061. http://dx.doi.org/10.20517/energymater.2023.144
AMA Style
Yang B, Li T, Pan Y, Yang L, Li K, Chen J, Yan Z, Hu A, Long J. Design strategy towards flame-retardant gel polymer electrolytes for safe lithium metal batteries. Energy Materials. 2024; 4(5): 400061. http://dx.doi.org/10.20517/energymater.2023.144
Chicago/Turabian Style
Borui Yang, Ting Li, Yu Pan, Liu Yang, Kun Li, Jiahao Chen, Zhongfu Yan, Anjun Hu, Jianping Long. 2024. "Design strategy towards flame-retardant gel polymer electrolytes for safe lithium metal batteries" Energy Materials. 4, no.5: 400061. http://dx.doi.org/10.20517/energymater.2023.144
ACS Style
Yang, B.; Li T.; Pan Y.; Yang L.; Li K.; Chen J.; Yan Z.; Hu A.; Long J. Design strategy towards flame-retardant gel polymer electrolytes for safe lithium metal batteries. Energy Mater. 2024, 4, 400061. http://dx.doi.org/10.20517/energymater.2023.144
About This Article
Special Issue
Copyright
Data & Comments
Data
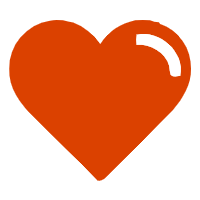
Comments
Comments must be written in English. Spam, offensive content, impersonation, and private information will not be permitted. If any comment is reported and identified as inappropriate content by OAE staff, the comment will be removed without notice. If you have any queries or need any help, please contact us at support@oaepublish.com.