Polymer-based electrolytes for high-voltage solid-state lithium batteries
Abstract
Increasing the charging cut-off voltage of lithium batteries is a feasible method to enhance the energy density. However, when batteries operate at high voltages (> 4.3 V), the degradation of liquid organic carbonate electrolyte is accelerated and may cause safety hazards. Polymer-based electrolytes with inherently high safety and good electrochemical stability can prevent the electrolyte degradation in high-voltage solid-state lithium batteries. This paper provides a comprehensive and in-depth review of the design strategies, recent developments, and scientific challenges associated with polymer-based electrolytes for high-voltage applications. Emphases are placed on the interfacial compatibility between electrolytes and cathodes, such as mechanical contacts and interface chemical stability, which are critical to the lifespan of high-voltage lithium batteries. Moreover, guidelines for the future development of high-voltage solid-state lithium batteries are also discussed.
Keywords
INTRODUCTION
The current development of electric vehicles is constrained by various factors such as limited driving range, short battery lifespan, and slow charging speed, as outlined in previous studies[1]. The predominant focus for addressing these challenges has been on enhancing the high-voltage tolerance of batteries. Polymer-based electrolytes stand out among various electrolytes due to their excellent processability, simple preparation procedures, and high safety[2,3]. However, these electrolytes in batteries are not universally applicable, as the strong oxidative/reductive nature of electrodes often challenges the realization of long-term, high energy density batteries[4,5]. Therefore, it is crucial to develop polymer-based electrolytes[6] with a wide electrochemical window and achieve compatibility between polymer electrolytes (PEs) and electrodes[7,8].
PEs can be classified into three categories: solid (SPEs), gel (GPEs) and composite PEs (CPEs) [Table 1]. In the 1880s, Wright and Fenton et al. initiated research on SPEs. The initial SPE matrix was polyethylene oxide (PEO), which could form ion-conductive polymers with electrical conductivity varying with temperature[9,10]. Lately, Vashisht and Armand applied polymers such as PEO and polyphenylene oxide (PPO) in solid-state batteries, introducing a new class of electrolytes, SPEs, which garnered attention[11]. However, SPEs exhibit a notable and critical flaw: notoriously low ionic conductivity that fails to meet practical application requirements[8,12]. Therefore, in 1975, Feuillade et al. added plasticizers to the polymer-salt system, in which the liquid content exceeded 20-30 wt.%, thereby introducing a new polymer system-GPEs[13-15]. GPEs combine the advantages of liquid and solid electrolytes. The liquid component exhibits excellent ion transport capacity and promotes good interface contact. It wets the gaps between electrode particles and between the electrode and the electrolyte, facilitating the formation of effective interfaces[16-18]. However, in order to adapt to the high-voltage cathode to achieve high-voltage lithium batteries, its electrochemical stability needs to be improved. In 1982, fillers were added to PEs for the first time to improve the mechanical properties and interface stability of the electrolytes[19]. For instance, Croce et al. employed nanoceramic powders as fillers to enhance the ionic conductivity of PEO-based PEs[20]. Subsequently, research on CPEs commenced. However, challenges such as the high cost of nanomaterials and difficulties in their dispersion in polymer matrices raised questions about the feasibility of industrial-scale application.
Comparison of various types of polymer electrolytes
Polymer electrolytes | Advantages | Disadvantages |
Solid polymer electrolytes (SPEs) | Good mechanical properties | Low ionic conductivity Poor interfacial compatibility |
Composite polymer electrolytes (CPEs) | Good ionic conductivity | Poor interfacial compatibility Difficult to disperse fillers |
Gel polymer electrolytes (GPEs) | Good ionic conductivity Good interface contact | Poor mechanical strength |
In recent years, researchers have conducted extensive studies on PEs, particularly focusing on the high-voltage performance, which is crucial for achieving high energy density in lithium batteries. The application of high-voltage PEs in lithium batteries must meet the following two criteria: (1) wide electrochemical window: > 4.3 V (vs. Li/Li+), to match the high-voltage cathode material, so that it is not easily oxidized and decomposed at high potentials; and (2) Good interface compatibility: forming stable interfaces with the cathode and anode to ensure the normal operation of batteries and improve their performances.
This paper reviews the latest progress of polymer-based electrolytes for high-voltage lithium batteries [Table 2]. Combined with the selection of polymer functional monomers and electrolyte preparation strategies, the properties of PEs are customized. Importantly, this review not only provides insights into the high-voltage design of PEs but also emphasizes the significance of addressing the polymer electrolyte-electrode interfaces. It discusses effective approaches targeting the polymer electrolyte-electrode interfaces, combining our research progress in the field of polymer batteries with updated developments, focusing on the industrial scalability, cycling stability, and safety issues of polymer batteries.
Progress of high-voltage polymer electrolytes
PEs | Polymer matrix | Liquid electrolyte | Preparation method | ESW (V) | σ (S cm-1) | t+ | Positive electrode | Voltage range (V) | Cycling lifespan (rate) | Ref. |
SPE | C5-POE-F | LiTFSI/DMF | Solution casting | 5 | 1 × 10-4 | - | NCM811 | 3.6-4.35 | 200 (0.15 C) | [28] |
SPE | PVC/POEA/AN | LiODFB | Solution casting | 4.6 | 4.47 × 10-5 (60 °C) | 0.32 (60 °C) | LCO | 3-4.3 | 150 (0.5 C, 60 °C) | [32] |
SPE | PHMO | LiTFSI | Solution casting | 4.6 | 1.26 × 10-4 | 0.52 | NCM811 | 3.0-4.3 | 250 (0.2 C) | [140] |
SPE | PDADMAFSI | LiFSI/PYR13FSI | Solution casting | 5.4 | 8 × 10-4 | 0.44 | NCM811 | 3-4.6 | 120 (0.1 mA cm-2) | [141] |
SPE | PVDF-HFP/PAN/UiO-66-SO3Li | LiTFSI/EMIMTFSI | Solution casting | 5 | 7.5 × 10-4 | 0.65 | NCM811 | 3-4.3 | 150 (0.2 C) | [142] |
SPE | PME/LiPVFM | LiTFSI/SN | Solution casting | 5 | 3.57 × 10-4 | 0.62 | LCO | 3-4.45 | 225 (0.5 C) | [143] |
CPE | SiO2/VEC | LiTFSI | Solution casting | 5 | 1.35 × 10-3 | 0.55 | LCO | 3-4.5 | 200 (0.1 C) | [48] |
CPE | PEGDA/LLZO | LiDFOB/EC/DMC | Solution casting | 5.13 | 1.25 × 10-3 (55 °C) | 0.57 | LCO | 3-4.3 | 200 (0.2 C) | [57] |
CPE | PEO-PVDF-HFP/LATP | LiTFSI/ACN | Solution casting | 5.21 | 1.67 × 10-4 | 0.49 | NCM811 | 2.5-4.2 | 400 (0.5 C) | [144] |
CPE | PVDF-HFP/Ce-NCATP | LiTFSI/DMF | Solution casting | 5 | 2.16 × 10-3 | 0.88 | NCM811 | 3-4.3 | 200 (0.2 C) | [145] |
CPE | PVDF/g-C3N4 | LiFSI/DMF | Solution casting | 4.7 | 6.9 × 10-4 | 0.49 | NCM811 | 2.5-4.3 | 1,700 (1 C) | [146] |
CPE | PDOL/YSZ | LiPF6/LiTFSI | Solution casting | 4.9 | 2.75 × 10-4 | 0.65 | NCM622 | 2.8-4.3 | 800 (0.5 C) | [49] |
GPE | PVDF/HEC | LiTFSI/PEGDME | Solution casting | 5.25 | 7.8 × 10-4 | - | LNO | 3.5-5 | 200 (0.2 C) | [147] |
GPE | PAN@LAGP/PEGDA | LiTFSI/DMF | Solution casting | 5 | 3.7 × 10-4 | - | NCM811 | 2.8-4.3 | 270 (0.5 C) | [148] |
SPE | UFF/PEO/PAN | LiTFSI | Electrospinning | 4.9 | 6.8 × 10-5 | 0.5 | NCM811 | 2.8-4.3 | 100 (0.35 mA cm-2) | [149] |
CPE | γ-Al2O3-PPO | LiBOB-LiTFSI/NMP/SN | Electrospinning | 5.6 | 3.38 × 10-4 | 0.7 | NCM622 | 2.8-4.3 | 120 (0.3 C) | [150] |
GPE | PVDF-HFP/BaTiO3 | LiPF6/EC/DMC | Electrospinning | 5.1 | 5.2 × 10-3 | 0.7 | NCM532 | 2.5-4.5 | 200 (5 C) | [151] |
SPE | CA-PEGMEA | LiFSI/SN/FEC | Thermal crosslinking | 4.9 | 1.9 × 10-3 | 0.56 | NCM622 | 2.8-4.3 | 250 (0.1 C) | [152] |
SPE | UPyMA/PEGDA | LiTFSI/NML | Thermal crosslinking | 5.2 | 3.42 × 10-4 (20 °C) | 0.66 | LCO | 3.0-4.6 | 1,000 (0.5 C) | [153] |
SPE | CA-PEG/LLZTO | LiTFSI/Li DFOB | Thermal crosslinking | 4.9 | 1.63 × 10-3 (30 °C) | 0.4 | LCO | 3-4.5 | 100 (0.2 C) | [31] |
SPE | PETEA | LiPF6/FEC/FEMC/TFTFE | Thermal crosslinking | 5.6 | 6.4 × 10-4 | 0.48 | LLO | 2-4.8 | 200 (0.5 C) | [154] |
SPE | P(VEC-co-TFEMA) | LiTFSI | Thermal crosslinking | 5.7 | 5.02 × 10-5 | 0.44 | NCM811 | 3.0-4.5 | 300 (0.1 C) | [155] |
SPE | PS/Sn(Oct)2 | LiTFSI | Thermal initiation | 5 | 1.5 × 10-4 | 0.78 | LLO | 2-4.6 | 100 (0.1 C) | [156] |
GPE | MMA/TEGDMA/ETPTA | LiDFOB/FEC | Thermal crosslinking | 5.65 | 2.24 × 10-4 | 0.48 | NCA | 3-4.5 | 200 (0.2 C) | [64] |
GPE | UPyMA/TEGDA | LiFSI/FEC/EMC/EGMEA | Thermal crosslinking | 5.9 | 2.2 × 10-3 | 0.75 | NCM811 | 2.8-4.7 | 500 (0.5 C) | [157] |
GPE | LiNO3/DMAA | LiPF6/EC/DEC/FEC | Thermal crosslinking | - | - | 0.57 | NCM622 | 3-4.3 | 400 (1 C) | [158] |
GPE | DOL-PEE | LiTFSI/LiDFOB/FEC | Thermal crosslinking | 4.5 | 2.36 × 10-3 | 0.6 | NCM622 | - | 300 (0.5 C) | [159] |
GPE | TFEMA-PETA | LiTFSI/LiDFOB/FEC | Thermal crosslinking | 4.89 | 1.88 × 10-3 | 0.61 | LCO | 3-4.5 | 500 (1 C) | [160] |
GPE | PEGDE-PEA | LiPF6/DMC/FEC | Thermal crosslinking | 4.8 | 7 × 10-4 | 0.47 | LCO | 3-4.35 | 150 (0.2 C) | [161] |
GPE | TFPO-PEE | LiDFOB/LiTFSI | Thermal crosslinking | 5.1 | 3.98 × 10-3 | 0.59 | NCM622 | 4.5 | 300 (0.5 C) | [162] |
GPE | ETPTA/SN | LiTFSI-LiDFOB/FEC | Thermal crosslinking | 5.4 | 1.08 × 10-3 | 0.64 | LCO | 3.0-4.3 | 300 (0.5 C) | [163] |
GPE | PEGDA/PETA/PPO | LiPF6/EMC/FEC | Thermal crosslinking | 4.5 | 8.676 × 10-4 | 0.65 | NCM811 | 2.8-4.3 | 400 (1 C) | [164] |
GPE | PMBA | LiTFSI-LiBOB/EC/EMC | Thermal crosslinking | 5.64 | 1.385 × 10-3 | 0.63 | NCM622 | 3.0-4.3 | 700 (1 C) | [65] |
GPE | DAP-PETEA | LiPF6/FEC/FEMC/HTE | Thermal crosslinking | 5.5 | 2 × 10-3 | 0.43 | LLO | 2-5 | 200 (0.5 C) | [165] |
SPE | PVC-TF3 | LiTFSI/NMP | Thermal initiation | 4.9 | 3 × 10-4 (60 °C) | 0.76 | NCM811 | 2.5-4.3 | 150 (0.1 C) | [166] |
SPE | B-PEGMA/VC/AN | LiTFSI | Thermal initiation | 5.1 | 9.24 × 10-4 (25 °C) | 0.86 | NCM811 | 2.8-4.3 | 100 (0.5 C) | [167] |
GPE | PCUMA | LiDFOB/EC/DMC | Thermal initiation | 5 | 1.27 × 10-3 | 0.44 | LCO | 3-4.45 | 200 (0.5 C) | [168] |
CPE | P(MVE-MA) | LiDFOB/PC | Thermal initiation | 5.2 | 1.34 × 10-3 | 0.54 | LCO | 2.75-4.45 | 700 (1 C, 60 °C) | [169] |
CPE | LATP/PEO/PAN | LiTFSI/DMF | Thermal initiation | 4.5 | 6.26 × 10-4 (60 °C) | 0.82 | NCM622 | 2.8-4.3 | 120 (0.5 C) | [170] |
SPE | IL/OFHDODA/VEC | LiTFSI | UV | 5.08 | 1.37 × 10-3 | 0.4 | NCM523 | 2.8-4.5 | 200 (0.5 C) | [30] |
GPE | P(AMPSLi-MPEGA-AN) | LiPF6/EC/PC | UV | 5.06 | 2.5 × 10-3 | - | LCO | 3-4.4 | 120 (0.2 C) | [66] |
GPE | SN | LiTFSI/LiDFOB | Eutectic gels | 4.8 | 1.87 × 10-3 | 0.64 | LCO | 3-4.45 | 200 (1 C) | [171] |
HIGH-VOLTAGE POLYMER ELECTROLYTES
High-voltage solid polymer electrolytes
SPEs comprise lithium salts and polymer matrices, devoid of liquid solvents, exhibiting high safety, excellent mechanical properties, and good processability[2,3,21]. Among them, PEO stands out as the earliest studied and most widely applied SPE matrix of PEs. However, its poor oxidation stability limits its matching with the high-voltage cathode, mainly due to the unstable lone pair electrons of the ether oxygen atoms on the PEO chains[22-24]. Introducing antioxidant groups into polymer chains has proven effective in enhancing the high-voltage stability of polymer-based electrolytes. For instance, Yang et al. improved the electrochemical stability window (ESW) from 4.05 to 4.3 V by replacing the terminal group -OH of polyethylene glycol with a more stable -OCH3 group[25]. This demonstrates that introducing strong antioxidant groups is an efficient strategy. To further demonstrate the impact of group substitution on ESW, Pandian et al. calculated the effect of substituent modification on PEO surfaces on ESW by density functional theory (DFT), as shown in Figure 1A[26]. CF3 and CN functional groups have higher oxidation stability and can provide a wider ESW. Fluorination and cyano functional groups have been shown to have antioxidant properties[27].
Figure 1. SPEs with antioxidant functional groups. (A) Effect of various functional groups (substituted at C1 carbon) on the oxidation and reduction potentials (eV) of PEO (EO5) electrolyte. This figure is quoted with permission from Pandian et al.[26] Copyright 2018 American Chemical Society. (B) LSV curve of Li|P(IL-OFHDODA-VEC)|carbon. (C) ESW of PIL, POFHDODA, PVEC, P(IL-OFHDODA), P(IL-VEC), and P(OFHDODA-VEC). This figure is quoted with permission from Tang et al.[30] Copyright 2023 Royal Society of Chemistry. (D) LSV of PGL and CA-PGL at a scan rate of 0.5 mV s-1. (E) Electrostatic potential of poly(CA-PEG). This figure is quoted with permission from Lv et al.[31] Copyright 2021 Royal Society of Chemistry. (F) Preparation diagram and characterization of PVCN-SPE.[32] Copyright 2022, Elsevier.
Sun et al. introduced a strong electron-withdrawing trifluoroacetic acid group on poly-oxalate (POE), which enhanced the electronegativity of the highest occupied molecular orbital (HOMO), and the HOMO electrons were transferred to the oxalate center, thereby improving the oxidation stability[28]. Benefiting from this, the fluorine-terminated SPEs remained stable until voltages above 5 V, while the non-fluorine-terminated SPEs were oxidized at 4.8 V. Xie et al. further confirmed that the F atom transfers electrons to the middle of the polymer main chains, thereby preventing the decomposition and oxidation of the chains, and increasing the oxidation potential of the SPEs[29]. In addition to introducing fluorinated groups to improve the oxidation stability of the electrolytes, the formation of fluorinated crosslinked network structure not only improves the oxidation resistance of the electrolyte but also enhances the mechanical properties. Tang et al. also improved the oxidative stability of SPEs using a polyfluorinated crosslinking agent[30]. The SPEs exhibited good oxidation resistance through the multi-fluorinated segment induced electron-withdrawing effect and the constructed crosslinked network structure for electron effect transmission. The fluorinated SPEs can achieve a wide ESW of 5.08 V, as shown in Figure 1B. As demonstrated in Figure 1C, 2,2,3,3,4,4,5,5-diacrylate (OFHDODA) is the key to improving the electrochemical stability of SPE. The fluorine atoms with strong electron absorption properties can reduce the HOMOs and the lowest unoccupied molecular orbitals (LUMOs) of the fluorinated electrolytes, thus making the electrolytes show better oxidation resistance and reduction resistance.
Figure 2. Fillers for improving the oxidation potential of CPEs. (A) Schematic diagram of preparing the CPE membrane from VEC precursor with Li salt and nanoparticles. (B) Molecular electrostatic potential energy mappings of PVEC and TFSI-. And Intermolecular interaction in CPE by DFT calculation. (C) ESW of the as-involved electrolyte. This figure is quoted with permission from Wang et al.[48] Copyright 2022 Elevier. (D) Improving PDOL performance by YSZ. (E) Electrochemical floating analysis of cells assembled with NCM622 cathode for SE and CSE. This figure is quoted with permission from Yang et al.[49] Copyright 2022 Wiley. (F) Schematic illustration of in-situ fabricated LCO/electrolyte/Li cells. (G) Linear sweep voltammetry (LSV) curves of PGPE and A-PGCE. This figure is quoted with permission from Cai et al.[57] Copyright 2022 Elevier. (H) LSV curves of the PEO/LiTFSI and PEO/LSTZ electrolytes. This figure is quoted with permission from Xu et al.[59] Copyright 2019 National Academy of Sciences of the United States of America.
In addition to the fluorine group, the strong electron-absorbing -C≡N group can also improve the oxidation stability of the electrolyte. Lv et al. prepared cyano-enhanced high-voltage SPEs by in-situ copolymerization of ethyl 2-cyanoacrylate (CA) and polyethylene glycol methyl acrylate (PEG)[31]. The SPEs form a stable interface layer rich in -C≡N and LiF on the surface of the LiCoO2 (LCO) cathode, thereby improving the oxidation stability of ethylene oxide (EO) and inhibiting its decomposition. The wide ESW of the SPEs can reach 4.9 V [Figure 1D]. As shown in Figure 1E, the electrostatic potential of poly (CA-PEG) calculated by DFT shows that the negative electrostatic potential of -C≡N is much lower than that of EO segments, indicating strong interaction between the positive electrode and -C≡N, thus slowing the decomposition of EO segments. The team also synthesized rigid-flexible SPEs by crosslinking reaction of rigid poly (ethylene carbonate), flexible polyoxyethylene bis (amine) (POEA) and antioxidant aminopropionitrile (AN) without initiator. The preparation method and electrolyte characterization are shown in Figure 1F[32]. The polymer exhibits a wide ESW and excellent thermal stability. In summary, introducing antioxidant functional groups is an effective method to enhance the oxidative potential of SPEs. Therefore, to design high-voltage-resistant SPEs, attention should be paid to selecting antioxidant groups, molecular structure design, and structural charge distribution. However, despite the excellent high-voltage stability exhibited by SPEs, their interface contacts limit their development, which will be discussed in detail in the following sections.
High-voltage composite polymer electrolytes
CPEs are composed of polymers, lithium salts and inorganic fillers, which have good processability and flexibility[33,34]. Inorganic fillers will adsorb trace water and impurities in polymers, improving the oxidation resistance of CPEs and increasing the electrochemical window[35,36]. According to the ionic conductivity of inorganic fillers, they can be classified into inert and active fillers. Commonly used inert fillers are silicon dioxide (SiO2)[37-39], alumina (Al2O3)[40], titanium oxide (TiO2)[41,42], magnesium oxide (MgO)[43], and zinc oxide (ZnO)[44]; active fillers are garnet type, NASICON type, and perovskite type[45]. Next, we will discuss the influence of different fillers on realizing high-voltage CPEs.
The inert fillers cannot conduct ions. When they form a crosslinked structure with the polymer matrix through physical/chemical interactions, the crystallinity of the polymer will be reduced, which is conducive to the ion transport. In addition, some chemical groups on the surfaces of the inert fillers have Lewis acid-base interaction with the anions/cations of lithium salts, which will promote the dissociation of the lithium salts and increase the number of free lithium ions, and this interaction improves the electrochemical stability of CPEs[46,47]. Wang et al. prepared size-adjustable antioxidant CPEs using a solution casting method, as shown in Figure 2A[48]. DFT calculations revealed the reasons for the increase in the antioxidant capacity of CPEs, as shown in Figure 2B. The area around the O atom on the C=O group of poly(vinyl ethylene carbonate) (PVEC) and the O=S=O group of bis(trifluoromethylsulfonyl)imide (TFSI-) has a high electron density, indicating that the O position of these groups in CPEs can preferentially form hydrogen bonds. Through the H atoms on the SiO2 surfaces and the O atoms on the C=O and O=S=O groups in PVEC and TFSI, local intermolecular hydrogen bonding interactions can be formed. The local intermolecular interaction of hydrogen bonds in CPEs enhances the oxidation resistance, and its electrochemical window can reach 5 V [Figure 2C]. Inorganic fillers can also improve the ionic conductivity of PEs and enhance their electrochemical properties.
Compared to inert fillers, active fillers not only retain some characteristics of the inert fillers but also can directly participate in the transport of lithium ions, thereby further improving the electrochemical performance of the CPEs. Typical active fillers include oxide type (garnet type, perovskite type and NASICON type) and sulfide type fillers (Li10SnP2S12 (LSnPS), Li10GeP2S12 (LGPS), etc.)[50-52].
Garnet-type fillers are widely used in CPEs due to their high ionic conductivity, wide potential window
Although the perovskite ceramic electrolyte has high ionic conductivity (10-3 S cm-1) and high-voltage stability, it has poor compatibility with metallic lithium[58]. Xu et al. introduced Li3/8Sr7/16Ta3/4Zr1/4O3 (LSTZ) perovskite that can also exist stably in a humid environment and used it as fillers to prepare a flexible PEO/lithium bis(trifluoromethylsulfonyl)imide (LiTFSI)/LSTZ solid composite electrolyte[59]. Ta5+ in LSTZ formed a strong bond with F- in TFSI- anions, which promoted the dissociation of lithium ions and improved the ionic conductivity of the electrolyte. The introduction of LSTZ also broadened the electrochemical window of the electrolyte [Figure 2H].
High-voltage gel polymer electrolytes
GPEs generally consist of a polymer matrix, a plasticizer and a lithium salt. The polymer matrix presents a crosslinked spatial network structure to provide a supporting skeleton, the plasticizer fills the structural gap, and the lithium salt and the polymer are dissolved in the plasticizer. They are a semi-solid electrolyte that improves the ionic conductivity while preventing the leakage of organic liquids. Their preparation methods mainly include ex-situ preparation and in-situ preparation[60]. The ex-situ preparation approach is to obtain GPEs and then assemble batteries, which leads to insufficient interface contact between electrodes and GPEs, resulting in an increase in resistance and a decline in the electrochemical performance of batteries[61,62].
The in-situ preparation method is to uniformly dissolve the polymer monomer, lithium salt, plasticizer and initiator into a liquid electrolyte, and then inject it into a battery cell to induce monomer polymerization under external conditions to form a GPE[60,63]. Here, we will mainly discuss the influence of in-situ preparation method on realizing high-voltage GPEs.
The in-situ polymerization of GPEs can be classified into thermal polymerization and photopolymerization. Thermal polymerization is a free radical polymerization initiated by heat treatment, which is cured at a corresponding temperature according to different types of initiators. Sun et al. explored the conductive mechanism of liquid electrolyte and GPE[64]. Lithium difluoro (oxalate) borate (LiDFOB) was dissolved in a fluoroethylene carbonate (FEC) solvent as a liquid electrolyte (FLE). Despite its high dielectric constant, FLE exhibits low ionic conductivity and poor electrochemical performance. F-GPE was synthesized by
Figure 3. In-situ preparation of GPE. (A) Preparation and characterization of F-GPE. This figure is quoted with permission from
Photopolymerization is initiated through free radical polymerization under ultraviolet (UV) or gamma-ray irradiation, with light acting as the initiator. Zeng et al. synthesized a novel lithiated interpenetrating network GPE by blending polyethylene glycol-acrylate (MPEGA), PEGDA, and AN in the presence of lithiated 2-acrylamido-2-methylpropanesulfonic acid, followed by two stages of UV irradiation polymerization[66]. This GPE has a wide electrochemical window of 5.06 V and good thermal stability (decomposition temperature of 400 °C). Nevertheless, the fabrication of the GPE involves two rounds of UV irradiation, leading to complex procedures and increased costs. Gao et al. realized a fast and efficient photocurable GPE using UV light to irradiate ETPTA and solvent-based ionic liquid for 30 s[67]. The preparation method and electrolyte characterization are shown in Figure 3C. The formed uniform silica gel-based GPE exhibits a wide electrochemical stable voltage of 5.2 V. Although photocuring can achieve rapid polymerization of materials, large-scale use of light radiation can cause harm to the human body and is costly.
In order to achieve high-voltage solid-state lithium batteries, it is not only necessary to focus on the high-voltage stability of the PEs, but also to consider the ionic conductivity, electrode and electrolyte compatibility, and the feasibility for achieving industrial development. Compared with SPEs and CPEs, the in-situ polymerization strategy of GPEs is more likely to be commercialized due to their good processability and flexibility and the high compatibility of the preparation process with the existing liquid battery technology. GPEs do not depend on conformational interfaces and, therefore, can adapt to the volume change of the electrodes during cycling. However, careful selection of the composition of GPEs is crucial, as the chemical composition of the interface ultimately determines the lifespan of batteries.
COMPATIBILITY OF POLYMER ELECTROLYTES WITH HIGH-VOLTAGE CATHODES
The design of high-voltage batteries also needs to consider the compatibility between PEs and electrodes, normally involving two main aspects: first, poor physical contacts at the cathode-electrolyte interface lead to solid-solid contact deterioration (SPEs and CPEs). Following repeated lithium insertion/extraction cycles, the cathode undergoes phase transformation and surface reconstruction, leading to lattice mismatches and non-conformal contacts that result in high interfacial resistance[68]. This problem can be addressed through strategies such as electrolyte supplementation, deposition of external coatings, integration of electrode/electrolyte structures, and in-situ polymerization[69]. Another crucial aspect is the side reactions between the electrode material and the electrolyte, such as the decomposition of the electrolyte and the unstable cathode-electrolyte interface (CEI)/SEI due to the incompatibility between the electrolyte and the electrode[70,71]. The limited oxidative capability of the electrolyte leads to interface instability between the PE and the high-voltage cathode, causing inevitable electrolyte oxidation, degradation, and rapid capacity loss[72-74].
Interfacial physical contacts
As a critical battery component, the solid composite cathode directly determines the battery's output capacity and energy density[75,76]. However, there are compatibility challenges between high-voltage cathodes and conductive PEs[77]. Typically, porous electrodes with poor contact with the electrolyte exhibit discrete ion transport, exposing transition metal regions, which causes the electrolyte preferential decomposition into non-conductive interfaces, resulting in rapid capacity decay. This is due to the unevenness of the state of charge (SOC) within active particles and the loss of structural integrity at the sub-particle level[78], ultimately leading to sub-particle-level deactivation[79]. Conversely, cathodes with uniform contacts exhibit uniform particle-level SOC and high oxidation stability. The local microstructure of a high-loaded cathode is closely related to ion transport discreteness and capacity decay. In-depth understanding of the local structure and charge state of the cathode and their interaction with interface evolution can help achieve compatibility between the electrolyte and the cathode.
The ion transport discreteness in the cathode is influenced by its porosity. PEs have difficulty penetrating porous cathodes[80], leading to non-uniform distribution of local electric fields at heterogeneous contact points, reducing the electrochemical stability of batteries. Zhu et al. developed a liquid polymer electrolyte (LPE) composed of brush-like polymers with a main chain of polyphosphonitrile and a side chain of oligomeric EO[81]. LPE addresses issues such as electrolyte oxidation, poor lithium plating/stripping performance, and interface instability on the cathode. The flowable viscous LPE fully wets or even infiltrates the electrode to maintain good contact at the interface. LiFePO4 and Ni0.8Co0.1Mn0.1O2 (NCM811) batteries using this LPE achieve long-term stable cycling in the temperature range of 60 to 120 °C, with a Coulombic efficiency of about 100%. Increasing the surface coverage of the electrolyte and improving the inherent stability of the electrolyte are expected to achieve a stable interface. An et al. designed a high-loaded composite cathode (12 and 28.6 mg cm-2) with a fully active surface through a solvent-free in-situ liquid-solid conversion strategy[82]. As shown in Figure 4A, the dual modifications through physical structure reshaping and chemical methods enable high-loaded NCM811 batteries to exhibit an excellent lifespan exceeding 10,000 h and over 150 cycles with a cathode loading of 28.6 mg cm-2.
Figure 4. The mechanical contact between polymer-based electrolytes and electrodes. (A) High state of charge in particle scale at local contact accelerates the decomposition of electrolyte. This figure is quoted with permission from An et al.[82]. Copyright 2023 Wiley. (B) Schematic representation and electrochemical performance of solid-state batteries. This figure is quoted with permission from
Additionally, a cathode normally undergoes volume changes during the cycling process, while the deformability and wetting properties of the solid electrolyte are poor, which leads to interface gaps[83]. Therefore, achieving a flexible interface between the electrolyte and the electrode is crucial. Wang et al. utilized poly(acrylonitrile-butadiene) (PAB) polymer as a coating for LiNi0.6Mn0.2Co0.2O2 cathode material, as depicted in Figure 4B[84]. The PAB nano-soft layer can enhance the physical contact between the cathode and the solid electrolyte. Coupling the cathode with lithium metal and poly(ethylene-acrylic ester) (PEA) solid electrolyte, the solid-state battery exhibited excellent rate performance (99 mAh g-1 at 3 C) and good cycling stability (75% capacity retention after 400 cycles). Quasi-solid or gel polymer electrolytes (QSEs or GPEs) containing organic small molecule plasticizers/solvents are expected to improve interface contacts[74] and room temperature ionic conductivity[85,86]. Surface in-situ polymerization (SIP) with optimized interface interactions can enhance interface compatibility between various cathodes and PEs, offering the potential for enduring high-voltage tolerance. Chen et al. achieved durable and tunable SPEs on the cathode side through in-situ polymerization of a polymerizable ether-based electrolyte (SIP), as illustrated in
Interfacial chemical reactions
The working potential of the high-voltage cathode exceeds 4 V; the practical operation of lithium batteries is constrained by the oxidative nature of the cathode[88,89]. Intense oxidation of transition metals and irreversible loss of lattice oxygen at high charge states lead to electrolyte decomposition and reduced conductivity at the cathode-electrolyte interface[90]. Molecular structure design can enhance the antioxidant properties of PEs, aiding in constructing a stable CEI[91]. Copolymerization of multiple monomers can compensate for the limitations of individual polymers, widening the ESW. This is a critical requirement for the compatibility of PEs with high-voltage cathode materials. However, PEs containing easily oxidizable oxygen-containing groups typically exhibit narrow ESW, resulting in poor cycling stability under high potentials. Conversely, widening of the ESW up to 4.8 V can be achieved by ring-opening polymerization of oxidizable cyclic carbonates using organic metal catalysts[92]. Additionally, it is noteworthy that strong electron-withdrawing groups can further enhance the antioxidant properties of the polymer matrix[93], as previously discussed. Solid electrolytes possess stronger dendrite suppression capabilities than liquid electrolytes, offering potential for applications in high-capacity lithium metal anodes[94]. However, due to the accumulation of interface voids and volume changes during repeated lithium stripping processes, contact losses between solid electrolytes and electrodes result in large ion transport barriers, deteriorating the electrochemical performance of solid-state lithium metal batteries[95].
Constructing functional interfaces[92] and electrode modifications[96] can achieve compatibility between PEs and electrodes, where the interface components and structural characteristics directly influence the rapid transmission of lithium ions. Metal-organic frameworks (MOFs), due to their high surface area, structural stability, tunable porosity, and abundance of Lewis acid sites, have been utilized for electrode interface modification or as electrolyte fillers to enhance ion transport and charge transfer processes, thereby suppressing lithium dendrite formation[97]. Qian et al. reported a porous and robust MOF coating (MOF-199), where the sturdy MOF interfacial layer physically inhibits lithium dendrite growth[98]. Its highly polar structure promotes uniform Li+ concentration, thereby mitigating excessive SEI formation. Lithium metal batteries protected by MOF-coating achieved 97% Coulombic efficiency at a current density of 1.0 mA cm-2. Huo et al. employed cationic MOFs (CMOFs) to immobilize anions and guide uniform Li+ deposition, enabling dendrite-free solid-state batteries[99]. CMOFs, through electrostatic interactions with charge carriers and their high surface area, securely bind anions, enhancing the transference number of Li+ to 0.72[99]. Furthermore, customization with CMOFs grafted with -NH2+ groups can protect the polymer chain's ether oxygen via hydrogen bonding, widening the ESW to 4.97 V. Cui et al. achieved excellent lithium-ion transport and interface stability by utilizing a MOF layer and atomic layer deposition of Al2O3 at the modified polymer matrix interface[100]. The inert Al2O3 nano-coating enhances affinity with the lithium negative electrode and participates in forming the SEI film, reducing the diffusion barrier for lithium ions. After 500 cycles within a wide voltage range of 2.0-4.8 V, the capacity retention remained at 84.6%. Inorganic coatings can improve the electrochemical stability of the interface; however, they often involve intricate processing steps and high stiffness, making it challenging to accommodate the volume changes of the cathode during charge/discharge cycles. In-situ formation of a homogeneous electrode/electrolyte interface layer via electrochemical methods, using highly flexible polymers, can simultaneously mitigate cathode-electrolyte side reactions and enhance contacts at the solid-solid interface during the cycling process. Ma et al. performed UV-curing of FEC and triethyl phosphate (TEP) carbonate-based precursors separately on two electrodes, developing a dual-function polymer electrolyte (BDFPE) with low interfacial resistance [Figure 5A][101]. The functional additives FEC and TEP have low LUMO and high HOMO, aiding in interface formation[46]. Regulation of the electrolyte molecular structure and additive composition can achieve compatibility between the electrolyte and high-voltage cathodes, such as fluorination and nitrogenation[102]. The solid electrolyte adheres closely to the lithium metal anode and the nickel-rich cathode, facilitating continuous lithium flux and avoiding large interface transfer barriers between the electrode and electrolyte. Benefiting from the BDFPE design, Li||Li symmetric cells achieved smooth and dendrite-free lithium deposition after an extended 1,800 h of cycling at 1 mA cm-2. Qi et al. reported fluorinated and nitrided polymer electrolytes (F&NPE) composed of 2,2,3,4,4,4-hexafluorobutyl acrylate (HFBA) and N,N′-methylenebisacrylamide (MBAM), as depicted in Figure 5B[103]. Based on molecular-level design of the PE, robust CEI and SEI were simultaneously constructed. The lithium-affinitive N-(C)3 in the SEI guided uniform distribution of Li+, promoting the transport of Li+ through LiF and Li3N for uniform Li+ deposition and stripping. Additionally, antioxidative fluorination and nitrogenation moieties in the CEI suppressed parasitic reactions between the cathode and electrolyte and structural degradation of the cathode. Therefore, NCM622/F&NPE/Li cells exhibited an 85.0% capacity retention after 500 cycles at 4.5 V voltage and 0.5 C.
Figure 5. Interface chemistry between polymer electrolytes and electrodes. (A) Preparation of bidirectional functional polymer electrolytes and their assembled battery performance. This figure is quoted with permission from Ma et al.[101]. Copyright 2023 Wiley. (B) Stable interface design for NCM622/F&NPE/Li batteries and cycling performance of NCM622//Li batteries. This figure is quoted with permission from Qi et al.[103] Copyright 2023 Wiley. (C) Solid electrolyte interface formed on lithium metal electrodes and electrochemical performance of batteries. This figure is quoted with permission from Li et al.[107]. Copyright 2023 Springer Nature.
In-situ polymerization with liquid monomers, similar to conventional liquid electrolytes, exhibits excellent wetting properties. Therefore, it can permeate electrodes to achieve sufficient contact with the active material, enabling close interaction between electrodes and PEs[3,104]. Lithium batteries face challenges in cold climates due to insufficient dynamics in the electrolyte itself and at the electrode/electrolyte interfaces. At low temperatures, inadequate ion and charge transport dynamics in the electrolyte and at the electrode/electrolyte interface can lead to structural changes at the SEI[105,106]. Li et al. reported a PE, polyoxymethylene (POM), prepared by in-situ polymerization using the precursor 1,3,5-trioxane[107]. POM has a wide bandgap and can stabilize the NCM811 cathode at high voltages (e.g., > 4.4 V)[108]. PEs can form a dual-layer SEI on the lithium metal anode [Figure 5C], consisting of an amorphous LixBOyFz outer layer and an inner layer rich in LiF. LixBOyFz and LiF are excellent electron insulators with a large electrochemical window, suppressing electrolyte decomposition and dendrite formation[109]. The amorphous LixBOyFz is highly plastic, mechanically adapting to the volume changes of the electrode[110].
COMPATIBILITY OF POLYMER-BASED ELECTROLYTES WITH OTHER NEGATIVE ELECTRODES
The formation of a stable SEI layer on negative electrodes is crucial for extending the lifespan and maintaining high capacity in lithium-ion batteries (LIBs)[111]. The ideal physical thickness of a SEI layer is on the order of a few angstroms (Å), with high mechanical strength to accommodate volume expansion and contraction during charge and discharge processes[112]. Graphite is a common negative electrode material for LIBs, and the formation of its surface SEI layer is influenced by graphite type, electrolyte composition, electrochemical conditions, and temperature. The slow electrochemical processes on the graphite surface limit the fast charging performance of LIBs, including lithium desolvation in the SEI and lithium transport in the SEI[113]. Additionally, graphite's low equilibrium potential (~0.1 V vs. Li/Li+) results in a low overpotential capacity limit, forming metallic lithium when the anode potential drops below 0 V (vs. Li/Li+), leading to poor cycle stability and even safety issues. SEI composition and structure are crucial in modulating the lithium desolvation structure at the negative electrode interface and accelerating the rapid charging process of LIBs. Electrolyte additives, high-concentration electrolytes, and graphite surface coatings contribute to forming a stable SEI, preventing further electrolyte decomposition[114]. The electronic resistance increases the potential of the graphite surface and shifts the negative electrode surface potential in the stable window of the electrolyte. The electronic insulation and compact structure of the SEI prevent continuous reduction of the anode surface by the electrolyte and the intrusion of solvents into the SEI, embedding further into bulk graphite.
The specific capacity of silicon (Si) negative electrodes is ten times that of traditional graphite anodes
GAS GENERATION IN HIGH-VOLTAGE LITHIUM BATTERIES
The highly lithiated surfaces of the cathode/anode during charging/discharging processes in high-voltage lithium batteries lead to gas generation upon oxidation/reduction. Gas evolution in the battery due to swelling results in capacity decay, increased impedance, loss of cell integrity, and poses new safety risks[118]. Therefore, controlling gas generation in the cathode, anode, and electrolyte is crucial for the safe and high-performance operation of batteries.
High-voltage cathode materials are key to achieving high energy density in lithium batteries; however, the cathode side is often a significant source of battery gases. For instance, layered materials [Figure 6A], such as LixMO2, LixNiO2 (LNO), and LixMnO3 (LMO) (x < 1), are metastable kinetically and undergo oxygen activation at high voltages, leading to oxygen release[119]. Similarly, LCO undergoes irreversible phase transition to CoO2 via spinel and rock-salt structures during over-oxidation, releasing O2. Subsequently, CoO2 undergoes further oxidation, resulting in oxygen loss. Over-delithiation of the cathode generates heat and releases O2, which, in turn, accelerates electrolyte decomposition[120,121]. For instance, layered transition metal oxide cathodes can react with carbonate-based solvents [e.g., propylene carbonate (PC), ethylene carbonate (EC), ethyl methyl carbonate (EMC), diethyl carbonate (DEC), and dimethyl carbonate (DMC)] in QSEs to produce CO2[122,123]. Ring-structured solvents are prone to ring-opening reactions and decomposition; thus, selecting chain-structured carbonates in the GPE reduces gas evolution.
Figure 6. Gas evolution in lithium-ion batteries (LIBs). (A) Release of O2 and CO2 from layered transition metal oxide cathodes[110]. Copyright 2021, Elsevier. (B) Structural evolution, gas generation, and interface reactions during high-voltage charging of lithium-rich and manganese-rich layered oxide cathodes[134]. Copyright 2022, Elsevier. (C) Schematic description of the proposed electrochemical and chemical electrolyte oxidation pathways (exemplarily shown for EC)[37]. Copyright 2017, IOP Publishing. (D) Suppression of gas generation and particle fracture with carbon-coated silicon nanoparticles[138]. Copyright 2018, American Chemical Society.
Chemical reactions at the interface between the cathode and electrolyte are the primary sources of gas generation in batteries. For instance, when charging voltage exceeds 4.5 V, the escape of 1O2 from
PEs can widen the ESW of the electrolyte by crosslinking structures or grafting high-voltage-resistant groups, effectively suppressing electrochemical oxidation of the electrolyte and reducing gas evolution from layered transition metal oxide cathodes under high voltages.
The escape of negative electrode gases at low potentials is crucial for achieving high performance in LIBs[129]. Due to the absence of a stable SEI on the negative electrode surface during the initial cycles of battery operation[130], electrolyte components on the negative electrode side are prone to generating highly flammable gases (hydrogen, ethylene [C2H4), and propylene], leading to thermal runaway of the battery. In QSEs, under high voltage, EC undergoes electron transfer at the negative electrode, resulting in the electrochemical reduction and generation of lithium ethylene dicarbonate (LEDC), C2H4, and CO[131]. As shown in Figure 6C, C2H4 production on graphite surfaces can be attributed to electrolyte reduction at
Electrode surface coatings and artificial SEI layers can passivate the electrode surface. For instance, carbon [Figure 6D], ceramic[135], and atomic layer deposition coatings[136] inhibit gas generation while maintaining high ionic conductivity[137]. Using antioxidant polymers at the positive electrode and anti-reductive polymers at the negative electrode can mitigate secondary reactions at the battery interfaces, ensuring high-voltage operation of the battery. Furthermore, the design of PE compositions facilitates the formation of stable SEI layers on electrode surfaces, suppressing parasitic reactions and addressing gas generation issues[138]. To avoid continuous formation and dissolution of SEI layers, electrolyte components used for SEI formation should prioritize reduction or oxidation (with low LUMO and high HOMO). Electrolyte structure design is often employed to suppress interface reactions (including high-concentration electrolytes) to broaden the ESW and inhibit gas generation in high-concentration or locally concentrated electrolytes[139].
CONCLUSIONS AND OUTLOOK
This article reviews the research progress and challenges of PEs for high-voltage solid-state batteries. PEs need to simultaneously have broad ESW and compatibility with electrode interfaces. The high-voltage compatibility can be achieved by designing layered composite structures or interface passivation. Developing GPEs is an effective approach to addressing challenges electrolytes face under high and low temperature conditions (such as low electrochemical stability, interface degradation, electrolyte decomposition, etc.). Nonetheless, there are many aspects to be improved for high-voltage PEs, with potential solutions being detailed below:
(1) Intrinsic stability of polymer-based solid electrolytes. Intrinsic stability refers to the minimal occurrence of electrolyte decomposition reactions between polymer-based solid electrolytes and electrodes under high voltages. In polymer systems, matrices with electron-withdrawing groups generally exhibit higher stability. Therefore, strategies such as designing the polymer molecular structure, grafting electron-withdrawing groups, and increasing the degree of polymer crosslinking hold potential for stabilizing electrolytes under high-voltage conditions.
(2) Non-intrinsic stability of polymer-based solid electrolytes. For polymer-based solid electrolytes inherently unstable under high voltages, non-intrinsic high-voltage stability can be achieved by designing interface passivation layers and implementing composite electrolyte strategies. (1) The interface passivation layers can generate an ideal interfacial phase with high ionic conductivity and low electronic conductivity, dynamically suppressing electrochemical decomposition and facilitating stable operation of batteries under high voltages; and (2) constructing composite electrolytes regulates local molecular interactions, thereby delaying the high-voltage decomposition of solid electrolytes.
(3) Advanced characterization techniques and theoretical computations. Currently, solid electrolytes and the electrode/electrolyte interfaces in solid-state systems remain shrouded in mystery. Combining in-situ observations and multiscale calculations makes it possible to elucidate the interactions among polymer chains, small molecules, and ions in the system, guiding the design of novel polymer-based solid electrolytes. Additionally, advanced techniques are employed to track interface evolution and characterize interfaces under high voltages. This enables a more detailed investigation of interface reactions, ion transport across multiphase interfaces, and other complex interface behaviors.
(4) Developments of polymer-based electrolytes with high anodic stability are highly desired for enhancing the energy density of lithium batteries. The engineering parameters, such as thin electrolytes, high-loading cathodes, and suitable Negative/Positive capacity (N/P) ratios, are very important to achieve high energy density; the electrochemical performance of high-voltage batteries with the combination of these parameters is suggested to be further explored.
Therefore, the following research proposals are made for PE: For polymers such as PAN and PVDF that are compatible with 5 V-level high-voltage cathode materials, improving their negative electrode stability and room-temperature ionic conductivity are key for future research. For SPEs, reducing electrolyte thickness while ensuring mechanical performance can compensate for the low ionic conductivity, thereby enhancing rate capability and reducing the operating temperature of solid-state lithium batteries. Additionally, ceramic particle dispersing, plasticizer addition, and liquid solvent incorporation all contribute to enhancing their room temperature performance.
GPEs simultaneously address issues of low ionic conductivity and electrode-electrolyte interface contacts. Future research on GPEs will primarily focus on improving safety and reducing liquid content. For instance, polymer grafting or copolymerization with halogen and phosphate-based monomers can eliminate radicals during battery ignition, thereby achieving flame-retardant effects. Importantly, GPEs can be adapted to existing liquid battery production lines, significantly reducing production complexity and cost. Transitioning from quasi-solid-state to all-solid-state polymer batteries will gradually eliminate flammable liquid batteries, enhancing the battery safety.
DECLARATIONS
Authors’ contributions
Proposed the topic of this review: Fu J
Prepared the manuscript: Wang Z, Chen J
Collectively discussed and revised the manuscript: Wang Z, Chen J, Fu J, Li Z, Guo X
Availability of data and materials
Not applicable.
Financial support and sponsorship
This work was supported by the Natural Science Foundation of Hubei Province, China (Grant No. 2022CFA031) and Dongguan Innovative Research Team Program (2020607101007).
Conflicts of interest
All authors declared that there are no conflicts of interest.
Ethical approval and consent to participate
Not applicable.
Consent for publication
Not applicable.
Copyright
© The Author(s) 2024.
REFERENCES
1. Gao Y, Jiang J, Zhang C, Zhang W, Ma Z, Jiang Y. Lithium-ion battery aging mechanisms and life model under different charging stresses. J Power Sources 2017;356:103-14.
2. Zhou J, Qian T, Liu J, Wang M, Zhang L, Yan C. High-safety all-solid-state lithium-metal battery with high-ionic-conductivity thermoresponsive solid polymer electrolyte. Nano Lett 2019;19:3066-73.
3. Zhao Q, Liu X, Stalin S, Khan K, Archer LA. Solid-state polymer electrolytes with in-built fast interfacial transport for secondary lithium batteries. Nat Energy 2019;4:365-73.
4. Liu N, Lu Z, Zhao J, et al. A pomegranate-inspired nanoscale design for large-volume-change lithium battery anodes. Nat Nanotechnol 2014;9:187-92.
5. Jung JW, Ryu WH, Shin J, Park K, Kim ID. Glassy metal alloy nanofiber anodes employing graphene wrapping layer: toward ultralong-cycle-life lithium-ion batteries. ACS Nano 2015;9:6717-27.
6. Li J, Ma C, Chi M, Liang C, Dudney NJ. Solid electrolyte: the key for high-voltage lithium batteries. Adv Energy Mater 2015;5:1401408.
8. Manthiram A, Yu X, Wang S. Lithium battery chemistries enabled by solid-state electrolytes. Nat Rev Mater 2017;2:16103.
9. Wright PV. Electrical conductivity in ionic complexes of poly(ethylene oxide). Brit Poly J 1975;7:319-27.
10. Fenton D, Parker J, Wright P. Complexes of alkali metal ions with poly(ethylene oxide). Polymer 1973;14:589.
12. Sun C, Liu J, Gong Y, Wilkinson DP, Zhang J. Recent advances in all-solid-state rechargeable lithium batteries. Nano Energy 2017;33:363-86.
13. Feuillade G, Perche P. Ion-conductive macromolecular gels and membranes for solid lithium cells. J Appl Electrochem 1975;5:63-9.
14. Song J, Wang Y, Wan C. Review of gel-type polymer electrolytes for lithium-ion batteries. J Power Sources 1999;77:183-97.
15. Cheng X, Pan J, Zhao Y, Liao M, Peng H. Gel polymer electrolytes for electrochemical energy storage. Adv Energy Mater 2018;8:1702184.
16. Ren W, Ding C, Fu X, Huang Y. Advanced gel polymer electrolytes for safe and durable lithium metal batteries: challenges, strategies, and perspectives. Energy Stor Mater 2021;34:515-35.
17. Chen S, Wen K, Fan J, Bando Y, Golberg D. Progress and future prospects of high-voltage and high-safety electrolytes in advanced lithium batteries: from liquid to solid electrolytes. J Mater Chem A 2018;6:11631-63.
18. Xu L, Tang S, Cheng Y, et al. Interfaces in solid-state lithium batteries. Joule 2018;2:1991-2015.
19. Weston J, Steele B. Effects of inert fillers on the mechanical and electrochemical properties of lithium salt-poly(ethylene oxide) polymer electrolytes. Solid State Ion 1982;7:75-9.
20. Croce F, Appetecchi GB, Persi L, Scrosati B. Nanocomposite polymer electrolytes for lithium batteries. Nature 1998;394:456-8.
21. Yue L, Ma J, Zhang J, et al. All solid-state polymer electrolytes for high-performance lithium ion batteries. Energy Stor Mater 2016;5:139-64.
22. Yoshida K, Nakamura M, Kazue Y, et al. Oxidative-stability enhancement and charge transport mechanism in glyme-lithium salt equimolar complexes. J Am Chem Soc 2011;133:13121-9.
23. Wetjen M, Kim G, Joost M, Appetecchi GB, Winter M, Passerini S. Thermal and electrochemical properties of PEO-LiTFSI-Pyr14TFSI-based composite cathodes, incorporating 4 V-class cathode active materials. J Power Sources 2014;246:846-57.
24. Nie K, Wang X, Qiu J, et al. Increasing poly(ethylene oxide) stability to 4.5 V by surface coating of the cathode. ACS Energy Lett 2020;5:826-32.
25. Yang X, Jiang M, Gao X, et al. Determining the limiting factor of the electrochemical stability window for PEO-based solid polymer electrolytes: main chain or terminal -OH group? Energy Environ Sci 2020;13:1318-25.
26. Pandian S, Adiga S, Tagade P, Hariharan K, Mayya K, Lee Y. Electrochemical stability of ether based salt-in-polymer based electrolytes: computational investigation of the effect of substitution and the type of salt. J Power Sources 2018;393:204-10.
27. Zhang Z, Hu L, Wu H, et al. Fluorinated electrolytes for 5 V lithium-ion battery chemistry. Energy Environ Sci 2013;6:1806-10.
28. Sun H, Xie X, Huang Q, et al. Fluorinated poly-oxalate electrolytes stabilizing both anode and cathode interfaces for all-solid-state Li/NMC811 batteries. Angew Chem Int Ed 2021;60:18335-43.
29. Xie X, Wang Z, He S, et al. Influencing factors on Li-ion conductivity and interfacial stability of solid polymer electrolytes, exampled by polycarbonates, polyoxalates and polymalonates. Angew Chem Int Ed 2023;62:e202218229.
30. Tang L, Chen B, Zhang Z, et al. Polyfluorinated crosslinker-based solid polymer electrolytes for long-cycling 4.5 V lithium metal batteries. Nat Commun 2023;14:2301.
31. Lv Z, Zhou Q, Zhang S, et al. Cyano-reinforced in-situ polymer electrolyte enabling long-life cycling for high-voltage lithium metal batteries. Energy Stor Mater 2021;37:215-23.
32. Dong T, Zhang H, Hu R, et al. A rigid-flexible coupling poly(vinylene carbonate) based cross-linked network: a versatile polymer platform for solid-state polymer lithium batteries. Energy Stor Mater 2022;50:525-32.
33. Li S, Zhang SQ, Shen L, et al. Progress and perspective of ceramic/polymer composite solid electrolytes for lithium batteries. Adv Sci 2020;7:1903088.
34. Meng N, Zhu X, Lian F. Particles in composite polymer electrolyte for solid-state lithium batteries: a review. Particuology 2022;60:14-36.
35. Pan J, Zhao P, Wang N, Huang F, Dou S. Research progress in stable interfacial constructions between composite polymer electrolytes and electrodes. Energy Environ Sci 2022;15:2753-75.
36. Zhu Y, Cao J, Chen H, Yu Q, Li B. High electrochemical stability of a 3D cross-linked network PEO@nano-SiO2 composite polymer electrolyte for lithium metal batteries. J Mater Chem A 2019;7:6832-9.
37. Yu J, Wang C, Li S, Liu N, Zhu J, Lu Z. Li+-containing, continuous silica nanofibers for high Li+ conductivity in composite polymer electrolyte. Small 2019;15:e1902729.
38. Huang H, Ding F, Zhong H, et al. Nano-SiO2-embedded poly(propylene carbonate)-based composite gel polymer electrolyte for lithium-sulfur batteries. J Mater Chem A 2018;6:9539-49.
39. Zhao XG, Jin EM, Park J, Gu H. Hybrid polymer electrolyte composite with SiO2 nanofiber filler for solid-state dye-sensitized solar cells. Compos Sci Technol 2014;103:100-5.
40. Zhai H, Gong T, Xu B, et al. Stabilizing polyether electrolyte with a 4 V metal oxide cathode by nanoscale interfacial coating. ACS Appl Mater Interfaces 2019;11:28774-80.
41. Arya A, Sharma AL. Structural, microstructural and electrochemical properties of dispersed-type polymer nanocomposite films. J Phys D Appl Phys 2018;51:045504.
42. Cao J, Wang L, He X, et al. In situ prepared nano-crystalline TiO2-poly(methyl methacrylate) hybrid enhanced composite polymer electrolyte for Li-ion batteries. J Mater Chem A 2013;1:5955-61.
43. Masoud EM, El-bellihi A, Bayoumy WA, Mohamed EA. Polymer composite containing nano magnesium oxide filler and lithiumtriflate salt: an efficient polymer electrolyte for lithium ion batteries application. J Mol Liq 2018;260:237-44.
44. Dhatarwal P, Choudhary S, Sengwa R. Electrochemical performance of Li+-ion conducting solid polymer electrolytes based on PEO-PMMA blend matrix incorporated with various inorganic nanoparticles for the lithium ion batteries. Compos Commun 2018;10:11-7.
45. Lv F, Wang Z, Shi L, et al. Challenges and development of composite solid-state electrolytes for high-performance lithium ion batteries. J Power Sources 2019;441:227175.
46. Zhou Q, Ma J, Dong S, Li X, Cui G. Intermolecular chemistry in solid polymer electrolytes for high-energy-density lithium batteries. Adv Mater 2019;31:e1902029.
47. Wang Z, Huang X, Chen L. Understanding of effects of nano-Al2O3 particles on ionic conductivity of composite polymer electrolytes. Electrochem Solid State Lett 2003;6:E40.
48. Wang Y, Wu L, Lin Z, et al. Hydrogen bonds enhanced composite polymer electrolyte for high-voltage cathode of solid-state lithium battery. Nano Energy 2022;96:107105.
49. Yang H, Zhang B, Jing M, et al. In situ catalytic polymerization of a highly homogeneous PDOL composite electrolyte for long-cycle high-voltage solid-state lithium batteries (Adv. Energy Mater. 39/2022). Adv Energy Mater 2022;12:2201762.
50. Fu K, Gong Y, Hitz GT, et al. Three-dimensional bilayer garnet solid electrolyte based high energy density lithium metal-sulfur batteries. Energy Environ Sci 2017;10:1568-75.
51. Xie H, Yang C, Fu K, et al. Flexible, scalable, and highly conductive garnet-polymer solid electrolyte templated by bacterial cellulose. Adv Energy Mater 2018;8:1703474.
52. Bae J, Li Y, Zhang J, et al. A 3D nanostructured hydrogel-framework-derived high-performance composite polymer lithium-ion electrolyte. Angew Chem Int Ed 2018;57:2096-100.
53. Liu S, Liu W, Ba D, et al. Filler-integrated composite polymer electrolyte for solid-state lithium batteries. Adv Mater 2023;35:e2110423.
54. Xu R, Xiao Y, Zhang R, et al. Dual-phase single-ion pathway interfaces for robust lithium metal in working batteries. Adv Mater 2019;31:e1808392.
55. Li Y, Xu B, Xu H, et al. Hybrid polymer/garnet electrolyte with a small interfacial resistance for lithium-ion batteries. Angew Chem Int Ed 2017;56:753-6.
56. Choi J, Lee C, Yu J, Doh C, Lee S. Enhancement of ionic conductivity of composite membranes for all-solid-state lithium rechargeable batteries incorporating tetragonal Li7La3Zr2O12 into a polyethylene oxide matrix. J Power Sources 2015;274:458-63.
57. Cai D, Qi X, Xiang J, et al. A cleverly designed asymmetrical composite electrolyte via in-situ polymerization for high-performance, dendrite-free solid state lithium metal battery. Chem Eng J 2022;435:135030.
58. Reddy MV, Julien CM, Mauger A, Zaghib K. Sulfide and oxide inorganic solid electrolytes for all-solid-state li batteries: a review. Nanomaterials 2020;10:1606.
59. Xu H, Chien PH, Shi J, et al. High-performance all-solid-state batteries enabled by salt bonding to perovskite in poly(ethylene oxide). Proc Natl Acad Sci USA 2019;116:18815-21.
60. Ma C, Cui W, Liu X, Ding Y, Wang Y. In situ preparation of gel polymer electrolyte for lithium batteries: progress and perspectives. InfoMat 2022;4:e12232.
61. Zhu Y, Xiao S, Shi Y, Yang Y, Hou Y, Wu Y. A composite gel polymer electrolyte with high performance based on poly(vinylidene fluoride) and polyborate for lithium ion batteries. Adv Energy Mater 2014;4:1300647.
62. Zhou D, Shanmukaraj D, Tkacheva A, Armand M, Wang G. Polymer electrolytes for lithium-based batteries: advances and prospects. Chem 2019;5:2326-52.
63. Li G, Li Z, Zhang P, Zhang H, Wu Y. Research on a gel polymer electrolyte for Li-ion batteries. Pure Appl Chem 2008;80:2553-63.
64. Sun Q, Wang S, Ma Y, et al. Li-ion transfer mechanism of gel polymer electrolyte with sole fluoroethylene carbonate solvent. Adv Mater 2023;35:e2300998.
65. Chen M, Ma C, Ding Z, et al. Upgrading electrode/electrolyte interphases via polyamide-based quasi-solid electrolyte for long-life nickel-rich lithium metal batteries. ACS Energy Lett 2021;6:1280-9.
66. Zeng Y, Yang J, Shen X, et al. New UV-initiated lithiated-interpenetrating network gel-polymer electrolytes for lithium-metal batteries. J Power Sources 2022;541:231681.
67. Gao X, Yuan W, Yang Y, et al. High-performance and highly safe solvate ionic liquid-based gel polymer electrolyte by rapid UV-curing for lithium-ion batteries. ACS Appl Mater Interfaces 2022;14:43397-406.
68. Li S, Sun Y, Li N, et al. Porosity development at Li-rich layered cathodes in all-solid-state battery during in situ delithiation. Nano Lett 2022;22:4905-11.
69. Wang L, Xie R, Chen B, et al. In-situ visualization of the space-charge-layer effect on interfacial lithium-ion transport in all-solid-state batteries. Nat Commun 2020;11:5889.
70. Koerver R, Walther F, Aygün I, et al. Redox-active cathode interphases in solid-state batteries. J Mater Chem A 2017;5:22750-60.
71. Koerver R, Aygün I, Leichtweiß T, et al. Capacity fade in solid-state batteries: interphase formation and chemomechanical processes in nickel-rich layered oxide cathodes and lithium thiophosphate solid electrolytes. Chem Mater 2017;29:5574-82.
72. Zhao CZ, Zhao Q, Liu X, et al. Rechargeable lithium metal batteries with an in-built solid-state polymer electrolyte and a high voltage/loading Ni-rich layered cathode. Adv Mater 2020;32:e1905629.
73. Yan Y, Ju J, Dong S, et al. In situ polymerization permeated three-dimensional Li+-percolated porous oxide ceramic framework boosting all solid-state lithium metal battery. Adv Sci 2021;8:2003887.
74. Li Z, Zhou X, Guo X. High-performance lithium metal batteries with ultraconformal interfacial contacts of quasi-solid electrolyte to electrodes. Energy Stor Mater 2020;29:149-55.
75. Lu X, Daemi SR, Bertei A, et al. Microstructural evolution of battery electrodes during calendering. Joule 2020;4:2746-68.
76. Judez X, Eshetu GG, Li C, Rodriguez-Martinez LM, Zhang H, Armand M. Opportunities for rechargeable solid-state batteries based on Li-intercalation cathodes. Joule 2018;2:2208-24.
77. Zhao Q, Chen P, Li S, Liu X, Archer LA. Solid-state polymer electrolytes stabilized by task-specific salt additives. J Mater Chem A 2019;7:7823-30.
78. Besli MM, Xia S, Kuppan S, et al. Mesoscale chemomechanical interplay of the LiNi0.8Co0.15Al0.05O2 cathode in solid-state polymer batteries. Chem Mater 2019;31:491-501.
79. Lu X, Bertei A, Finegan DP, et al. 3D microstructure design of lithium-ion battery electrodes assisted by X-ray nano-computed tomography and modelling. Nat Commun 2020;11:2079.
80. Yang L, Zhang J, Xue W, et al. Anomalous thermal decomposition behavior of polycrystalline LiNi0.8Mn0.1Co0.1O2 in PEO-based solid polymer electrolyte. Adv Funct Mater 2022;32:2200096.
81. Zhu GR, Zhang Q, Liu QS, et al. Non-flammable solvent-free liquid polymer electrolyte for lithium metal batteries. Nat Commun 2023;14:4617.
82. An H, Liu Q, Deng B, et al. Eliminating local electrolyte failure induced by asynchronous reaction for high-loading and long-lifespan all-solid-state batteries. Adv Funct Mater 2023;33:2305186.
83. Liu Y, Liu H, Lin Y, et al. Mechanistic investigation of polymer-based all-solid-state lithium/sulfur battery. Adv Funct Mater 2021;31:2104863.
84. Wang L, Zhang X, Wang T, et al. Ameliorating the interfacial problems of cathode and solid-state electrolytes by interface modification of functional polymers. Adv Energy Mater 2018;8:1801528.
85. Liang L, Yuan W, Chen X, Liao H. Flexible, nonflammable, highly conductive and high-safety double cross-linked poly(ionic liquid) as quasi-solid electrolyte for high performance lithium-ion batteries. Chem Eng J 2021;421:130000.
86. Didwal PN, Verma R, Nguyen AG, Ramasamy HV, Lee GH, Park CJ. Improving cyclability of all-solid-state batteries via stabilized electrolyte-electrode interface with additive in poly(propylene carbonate) based solid electrolyte. Adv Sci 2022;9:e2105448.
87. Chen Y, Cui Y, Wang S, et al. Durable and adjustable interfacial engineering of polymeric electrolytes for both stable Ni-rich cathodes and high-energy metal anodes. Adv Mater 2023;35:e2300982.
88. Ni L, Zhang S, Di A, et al. Challenges and strategies towards single-crystalline Ni-rich layered cathodes. Adv Energy Mater 2022;12:2201510.
89. Liu K, Pei A, Lee HR, et al. Lithium metal anodes with an adaptive “solid-liquid” interfacial protective layer. J Am Chem Soc 2017;139:4815-20.
90. Yu X, Wang L, Ma J, Sun X, Zhou X, Cui G. Selectively wetted rigid-flexible coupling polymer electrolyte enabling superior stability and compatibility of high-voltage lithium metal batteries. Adv Energy Mater 2020;10:1903939.
91. Ding P, Wu L, Lin Z, et al. Molecular self-assembled ether-based polyrotaxane solid electrolyte for lithium metal batteries. J Am Chem Soc 2023;145:1548-56.
92. Li X, Lv M, Tian Y, et al. Negatively charged polymeric interphase for regulated uniform lithium-ion transport in stable lithium metal batteries. Nano Energy 2021;87:106214.
93. Zhou T, Zhao Y, Choi JW, Coskun A. Ionic liquid functionalized gel polymer electrolytes for stable lithium metal batteries. Angew Chem Int Ed 2021;60:22791-6.
94. Chen N, Dai Y, Xing Y, et al. Biomimetic ant-nest ionogel electrolyte boosts the performance of dendrite-free lithium batteries. Energy Environ Sci 2017;10:1660-7.
95. Lu Y, Zhao C, Yuan H, Cheng X, Huang J, Zhang Q. Critical current density in solid-state lithium metal batteries: mechanism, influences, and strategies. Adv Funct Mater 2021;31:2009925.
96. Kim J, Ma H, Cha H, et al. A highly stabilized nickel-rich cathode material by nanoscale epitaxy control for high-energy lithium-ion batteries. Energy Environ Sci 2018;11:1449-59.
97. Wang H, Zhu QL, Zou R, Xu Q. Metal-organic frameworks for energy applications. Chem 2017;2:52-80.
98. Qian J, Li Y, Zhang M, et al. Protecting lithium/sodium metal anode with metal-organic framework based compact and robust shield. Nano Energy 2019;60:866-74.
99. Huo H, Wu B, Zhang T, et al. Anion-immobilized polymer electrolyte achieved by cationic metal-organic framework filler for dendrite-free solid-state batteries. Energy Stor Mater 2019;18:59-67.
100. Cui S, Wu X, Yang Y, et al. Heterostructured gel polymer electrolyte enabling long-cycle quasi-solid-state lithium metal batteries. ACS Energy Lett 2022;7:42-52.
101. Ma Q, Fu S, Wu A, et al. Designing bidirectionally functional polymer electrolytes for stable solid lithium metal batteries. Adv Energy Mater 2023;13:2203892.
102. Yang F, Liu Y, Liu T, et al. Fluorinated strategies among all-solid-state lithium metal batteries from microperspective. Small Struct 2023;4:2200122.
103. Qi S, Li M, Gao Y, et al. Enabling scalable polymer electrolyte with dual-reinforced stable interface for 4.5 V lithium-metal batteries. Adv Mater 2023;35:e2304951.
104. Liu FQ, Wang WP, Yin YX, et al. Upgrading traditional liquid electrolyte via in situ gelation for future lithium metal batteries. Sci Adv 2018;4:eaat5383.
105. Lou S, Liu Q, Zhang F, et al. Insights into interfacial effect and local lithium-ion transport in polycrystalline cathodes of solid-state batteries. Nat Commun 2020;11:5700.
106. Zhang N, Deng T, Zhang S, et al. Critical review on low-temperature Li-ion/metal batteries. Adv Mater 2022;34:e2107899.
107. Li Z, Yu R, Weng S, Zhang Q, Wang X, Guo X. Tailoring polymer electrolyte ionic conductivity for production of low- temperature operating quasi-all-solid-state lithium metal batteries. Nat Commun 2023;14:482.
108. Zhang D, Liu Z, Wu Y, et al. In situ construction a stable protective layer in polymer electrolyte for ultralong lifespan solid-state lithium metal batteries. Adv Sci 2022;9:e2104277.
109. Li T, Zhang X, Shi P, Zhang Q. Fluorinated solid-electrolyte interphase in high-voltage lithium metal batteries. Joule 2019;3:2647-61.
110. Liang JY, Zhang XD, Zeng XX, et al. Enabling a durable electrochemical interface via an artificial amorphous cathode electrolyte interphase for hybrid solid/liquid lithium-metal batteries. Angew Chem Int Ed 2020;59:6585-9.
111. An SJ, Li J, Daniel C, Mohanty D, Nagpure S, Wood DL. The state of understanding of the lithium-ion-battery graphite solid electrolyte interphase (SEI) and its relationship to formation cycling. Carbon 2016;105:52-76.
112. Zhang Z, Li Y, Xu R, et al. Capturing the swelling of solid-electrolyte interphase in lithium metal batteries. Science 2022;375:66-70.
113. Tu S, Zhang B, Zhang Y, et al. Fast-charging capability of graphite-based lithium-ion batteries enabled by Li3P-based crystalline solid-electrolyte interphase. Nat Energy 2023;8:1365-74.
114. Heiskanen SK, Kim J, Lucht BL. Generation and evolution of the solid electrolyte interphase of lithium-ion batteries. Joule 2019;3:2322-33.
115. Dong H, Wang J, Wang V, et al. Effect of temperature on formation and evolution of solid electrolyte interphase on Si@Graphite@C anodes. J Energy Chem 2022;64:190-200.
116. Rezqita A, Sauer M, Foelske A, Kronberger H, Trifonova A. The effect of electrolyte additives on electrochemical performance of silicon/mesoporous carbon (Si/MC) for anode materials for lithium-ion batteries. Electrochim Acta 2017;247:600-9.
117. Kobayashi Y, Seki S, Mita Y, et al. High reversible capacities of graphite and SiO/graphite with solvent-free solid polymer electrolyte for lithium-ion batteries. J Power Sources 2008;185:542-8.
118. Aiken CP, Self J, Petibon R, Xia X, Paulsen JM, Dahn JR. A survey of in situ gas evolution during high voltage formation in Li-ion pouch cells. J Electrochem Soc 2015;162:A760-7.
119. Papp JK, Li N, Kaufman LA, et al. A comparison of high voltage outgassing of LiCoO2, LiNiO2, and Li2MnO3 layered Li-ion cathode materials. Electrochim Acta 2021;368:137505.
120. Ren D, Feng X, Lu L, et al. An electrochemical-thermal coupled overcharge-to-thermal-runaway model for lithium ion battery. J Power Sources 2017;364:328-40.
121. Browning KL, Baggetto L, Unocic RR, Dudney NJ, Veith GM. Gas evolution from cathode materials: a pathway to solvent decomposition concomitant to SEI formation. J Power Sources 2013;239:341-6.
122. Han JG, Kim K, Lee Y, Choi NS. Scavenging materials to stabilize LiPF6-containing carbonate-based electrolytes for Li-ion batteries. Adv Mater 2019;31:e1804822.
123. Mahne N, Renfrew SE, McCloskey BD, Freunberger SA. Electrochemical oxidation of lithium carbonate generates singlet oxygen. Angew Chem Int Ed 2018;57:5529-33.
124. Zheng X, Li X, Wang Z, et al. Investigation and improvement on the electrochemical performance and storage characteristics of LiNiO2-based materials for lithium ion battery. Electrochim Acta 2016;191:832-40.
125. Jung R, Metzger M, Maglia F, Stinner C, Gasteiger HA. Oxygen release and its effect on the cycling stability of LiNixMnyCozO2 (NMC) cathode materials for Li-ion batteries. J Electrochem Soc 2017;164:A1361-77.
126. Pham HQ, Kondracki Ł, Tarik M, Trabesinger S. Correlating the initial gas evolution and structural changes to cycling performance of Co-free Li-rich layered oxide cathode. J Power Sources 2022;527:231181.
127. Fell CR, Sun L, Hallac PB, Metz B, Sisk B. Investigation of the gas generation in lithium titanate anode based lithium ion batteries. J Electrochem Soc 2015;162:A1916-20.
128. Kanamura K, Toriyama S, Shiraishi S, Takehara Z. Studies on electrochemical oxidation of nonaqueous electrolytes using in situ FTIR spectroscopy: I. The effect of type of electrode on on-set potential for electrochemical oxidation of propylene carbonate containing 1.0 mol dm-3. J Electrochem Soc 1995;142:1383-9.
129. Kim Y, Park H, Warner JH, Manthiram A. Unraveling the intricacies of residual lithium in high-Ni cathodes for lithium-ion batteries. ACS Energy Lett 2021;6:941-8.
130. Jiao S, Ren X, Cao R, et al. Stable cycling of high-voltage lithium metal batteries in ether electrolytes. Nat Energy 2018;3:739-46.
131. Jung R, Metzger M, Maglia F, Stinner C, Gasteiger HA. Chemical versus electrochemical electrolyte oxidation on NMC111, NMC622, NMC811, LNMO, and conductive carbon. J Phys Chem Lett 2017;8:4820-5.
132. Zhu Z, Wang H, Li Y, et al. A surface Se-substituted LiCo [O2-δSeδ>] cathode with ultrastable high-voltage cycling in pouch full-cells. Adv Mater 2020;32:e2005182.
133. Luo K, Roberts MR, Hao R, et al. Charge-compensation in 3D-transition-metal-oxide intercalation cathodes through the generation of localized electron holes on oxygen. Nat Chem 2016;8:684-91.
134. Xu K. Electrolytes and interphases in Li-ion batteries and beyond. Chem Rev 2014;114:11503-618.
135. Li W, Li X, Chen M, et al. AlF3 modification to suppress the gas generation of Li4Ti5O12 anode battery. Electrochim Acta 2014;139:104-10.
136. Zhao K, Wang C, Yu Y, et al. Ultrathin surface coating enables stabilized zinc metal anode. Adv Mater Inter 2018;5:1800848.
137. Zhang X, Belharouak I, Li L, et al. Structural and electrochemical study of Al2O3 and TiO2 Coated Li1.2Ni0.13Mn0.54Co0.13O2 cathode material using ALD. Adv Energy Mater 2013;3:1299-307.
138. Schiele A, Breitung B, Mazilkin A, et al. Silicon nanoparticles with a polymer-derived carbon shell for improved lithium-ion batteries: investigation into volume expansion, gas evolution, and particle fracture. ACS Omega 2018;3:16706-13.
139. Tong X, Ou X, Wu N, Wang H, Li J, Tang Y. High oxidation potential ≈6.0 V of concentrated electrolyte toward high-performance dual-ion battery. Adv Energy Mater 2021;11:2100151.
140. Chang C, Yao Y, Li R, et al. Self-healing single-ion-conductive artificial polymeric solid electrolyte interphases for stable lithium metal anodes. Nano Energy 2022;93:106871.
141. Fu C, Homann G, Grissa R, et al. A polymerized-ionic-liquid-based polymer electrolyte with high oxidative stability for 4 and 5 V class solid-state lithium metal batteries. Adv Energy Mater 2022;12:2200412.
142. Yao M, Ruan Q, Pan S, Zhang H, Zhang S. An ultrathin asymmetric solid polymer electrolyte with intensified ion transport regulated by biomimetic channels enabling wide-temperature high-voltage lithium-metal battery. Adv Energy Mater 2023;13:2203640.
143. Li H, Du Y, Wu X, Xie J, Lian F. Developing “polymer-in-salt” high voltage electrolyte based on composite lithium salts for solid-state Li metal batteries. Adv Funct Mater 2021;31:2103049.
144. Yao Z, Zhu K, Li X, et al. 3D poly(vinylidene fluoride-hexafluoropropylen) nanofiber-reinforced PEO-based composite polymer electrolyte for high-voltage lithium metal batteries. Electrochim Acta 2022;404:139769.
145. Huang T, Xiong W, Ye X, et al. A cerium-doped NASICON chemically coupled poly(vinylidene fluoride-hexafluoropropylene)-based polymer electrolyte for high-rate and high-voltage quasi-solid-state lithium metal batteries. J Energy Chem 2022;73:311-21.
146. Chen L, Gu T, Ma J, et al. In situ construction of Li3N-enriched interface enabling ultra-stable solid-state LiNi0.8Co0.1Mn0.1O2/lithium metal batteries. Nano Energy 2022;100:107470.
147. Ma X, Zuo X, Wu J, et al. Polyethylene-supported ultra-thin polyvinylidene fluoride/hydroxyethyl cellulose blended polymer electrolyte for 5 V high voltage lithium ion batteries. J Mater Chem A 2018;6:1496-503.
148. Duan H, Fan M, Chen WP, et al. Extended electrochemical window of solid electrolytes via heterogeneous multilayered structure for high-voltage lithium metal batteries. Adv Mater 2019;31:e1807789.
149. He F, Tang W, Zhang X, Deng L, Luo J. High energy density solid state lithium metal batteries enabled by Sub-5 µm solid polymer electrolytes. Adv Mater 2021;33:e2105329.
150. Li J, Jing M, Li R, et al. Al2O3 fiber-reinforced polymer solid electrolyte films with excellent lithium-ion transport properties for high-voltage solid-state lithium batteries. ACS Appl Polym Mater 2022;4:7144-51.
151. Zhu M, Wu J, Liu B, et al. Multifunctional polymer electrolyte improving stability of electrode-electrolyte interface in lithium metal battery under high voltage. J Membr Sci 2019;588:117194.
152. Gong Y, Wang C, Xin M, et al. Ultra-thin and high-voltage-stable Bi-phasic solid polymer electrolytes for high-energy-density Li metal batteries. Nano Energy 2024;119:109054.
153. Wang H, Song J, Zhang K, et al. A strongly complexed solid polymer electrolyte enables a stable solid state high-voltage lithium metal battery. Energy Environ Sci 2022;15:5149-58.
154. Yang T, Zhang W, Lou J, et al. Stable LiF-rich electrode-electrolyte interface toward high-voltage and high-energy-density lithium metal solid batteries. Small 2023;19:e2300494.
155. Wang Y, Chen S, Li Z, Peng C, Li Y, Feng W. In-situ generation of fluorinated polycarbonate copolymer solid electrolytes for high-voltage Li-metal batteries. Energy Stor Mater 2022;45:474-83.
156. Yin X, Zhao S, Lin Z, et al. A propanesultone-based polymer electrolyte for high-energy solid-state lithium batteries with lithium-rich layered oxides. J Mater Chem A 2023;11:19118-27.
157. Li Z, Fu J, Zheng S, Li D, Guo X. Self-healing polymer electrolyte for dendrite-free Li metal batteries with ultra-high-voltage Ni-rich layered cathodes. Small 2022;18:e2200891.
158. Jing C, Dai K, Liu D, et al. Crosslinked solubilizer enables nitrate-enriched carbonate polymer electrolytes for stable, high-voltage lithium metal batteries. Sci Bull 2024;69:209-17.
159. Zhu J, Zhang J, Zhao R, et al. In situ 3D crosslinked gel polymer electrolyte for ultra-long cycling, high-voltage, and high-safety lithium metal batteries. Energy Stor Mater 2023;57:92-101.
160. Zhou G, Yu J, Ciucci F. In situ prepared all-fluorinated polymer electrolyte for energy-dense high-voltage lithium-metal batteries. Energy Stor Mater 2023;55:642-51.
161. Fang Z, Luo Y, Liu H, et al. Boosting the oxidative potential of polyethylene glycol-based polymer electrolyte to 4.36 V by Spatially restricting hydroxyl groups for high-voltage flexible lithium-ion battery applications. Adv Sci 2021;8:e2100736.
162. Zhu J, Zhao R, Zhang J, et al. Long-cycling and high-voltage solid state lithium metal batteries enabled by fluorinated and crosslinked polyether electrolytes. Angew Chem Int Ed 2024;63:e202400303.
163. Wang A, Geng S, Zhao Z, Hu Z, Luo J. In situ cross-linked plastic crystal electrolytes for wide-temperature and high-energy-density lithium metal batteries. Adv Funct Mater 2022;32:2201861.
164. Wang F, Liu H, Guo Y, et al. In situ high-performance gel polymer electrolyte with dual-reactive cross-linking for lithium metal batteries. Energy Environ Mater 2024;7:e12497.
165. Wu J, Wang X, Liu Q, et al. A synergistic exploitation to produce high-voltage quasi-solid-state lithium metal batteries. Nat Commun 2021;12:5746.
166. Wang C, Liu H, Liang Y, et al. Molecular-level designed polymer electrolyte for high-voltage lithium-metal solid-state batteries. Adv Funct Mater 2023;33:2209828.
167. Liu D, Lu Z, Lin Z, Zhang C, Dai K, Wei W. Organoboron- and cyano-grafted solid polymer electrolytes boost the cyclability and safety of high-voltage lithium metal batteries. ACS Appl Mater Interfaces 2023;15:21112-22.
168. Hu R, Qiu H, Zhang H, et al. A polymer-reinforced SEI layer induced by a cyclic carbonate-based polymer electrolyte boosting
169. Dong T, Zhang J, Xu G, et al. A multifunctional polymer electrolyte enables ultra-long cycle-life in a high-voltage lithium metal battery. Energy Environ Sci 2018;11:1197-203.
170. Liang JY, Zeng XX, Zhang XD, et al. Engineering janus interfaces of ceramic electrolyte via distinct functional polymers for stable high-voltage Li-metal batteries. J Am Chem Soc 2019;141:9165-9.
Cite This Article
Export citation file: BibTeX | EndNote | RIS
OAE Style
Wang Z, Chen J, Fu J, Li Z, Guo X. Polymer-based electrolytes for high-voltage solid-state lithium batteries. Energy Mater 2024;4:400050. http://dx.doi.org/10.20517/energymater.2023.130
AMA Style
Wang Z, Chen J, Fu J, Li Z, Guo X. Polymer-based electrolytes for high-voltage solid-state lithium batteries. Energy Materials. 2024; 4(4): 400050. http://dx.doi.org/10.20517/energymater.2023.130
Chicago/Turabian Style
Zixuan Wang, Jianxiong Chen, Jialong Fu, Zhiyong Li, Xin Guo. 2024. "Polymer-based electrolytes for high-voltage solid-state lithium batteries" Energy Materials. 4, no.4: 400050. http://dx.doi.org/10.20517/energymater.2023.130
ACS Style
Wang, Z.; Chen J.; Fu J.; Li Z.; Guo X. Polymer-based electrolytes for high-voltage solid-state lithium batteries. Energy Mater. 2024, 4, 400050. http://dx.doi.org/10.20517/energymater.2023.130
About This Article
Copyright
Data & Comments
Data
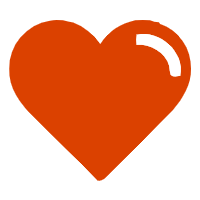
Comments
Comments must be written in English. Spam, offensive content, impersonation, and private information will not be permitted. If any comment is reported and identified as inappropriate content by OAE staff, the comment will be removed without notice. If you have any queries or need any help, please contact us at support@oaepublish.com.