Efficient degradation of epoxy resin and recovery of carbon fibers from CFREP in mix-solvent system
Abstract
Recycling of carbon fiber reinforced epoxy resin (CFREP) is challenging due to its thermosetting property, in which amine-cured one shows more difficulty due to the hard C–O bond or C–N bond breaking via simple solvolysis. Here, a mix-solvent system with low concentrated catalyst is developed for chemical recycling carbon fiber (CF) reinforced dicyandiamide (DICY) cured CFREP, where the portion of tetrahydrofuran (THF), H2O and ZnCl2 is 8.1:0.9:0.5. The strong swelling ability of THF facilitates the incorporation of H2O and ZnCl2 into the covalent matrix, resulting in the removal of as high as 99.0% epoxy resin (EP) polymers after 5 h at 230 °C. The system can be reused three times and is scalable. The degraded product is the oligomers containing N and the unit of bisphenol A, which can be further hydrogenated to (alkyl)cyclohexane, a constituent of jet fuel. The recovered CFs still maintain their structure and a tensile strength of 87%.
Keywords
INTRODUCTION
Carbon fiber reinforced epoxy resin (CFREP) is widely used in aircraft, wind turbine blades, vehicles, sports products and more due to its excellent mechanical, chemical and thermal properties, which originate from its three-dimensional covalent network of epoxy resins (EPs) and strong combination between resin and carbon fibers (CFs). Due to these structural properties, CFREP is both insoluble and infusible, meaning the waste CFREP cannot be melted and recast into new forms. Meanwhile, the price of normal CFs reaches $20-25 per kilogram and even $80 for aerospace-grade CFs, much higher than metals such as carbon steel or aluminum, priced at only $0.5 and $2 per kilogram[1]. Therefore, the recovery of CFs in CFREP is important. In addition, similar to most kinds of plastics, disposing of waste CFREP in landfills will cause environmental pollution due to its very long degradation time. To solve the problem, different methods such as mechanical recycling[2], pyrolysis[3] and chemical recycling[4] are proposed. Compared with mechanical recycling, which leads to CF shortening, and pyrolysis, which requires temperatures of up to 450-550 °C, chemical recycling shows a great advantage in avoiding the destruction of CF and energy consumption.
Generally, chemical recycling of CFREP was carried out in supercritical fluid[5], such as supercritical water, alcohol or ketone; melted strong bases, such as KOH[6]; strong oxidizers, such as nitric acid mixed with
In this work, a low-concentrated catalytic system containing 5.3% ZnCl2 is used with a mixed solvent of tetrahydrofuran (THF) and H2O. The products of DEP were investigated by Fourier transform infrared spectroscopy (FTIR), nuclear magnetic resonance (NMR), and elemental analysis, from which a possible route for decomposing EP and its composites was proposed. The structures and properties of recovered CFs (rCF) were also investigated. The choice of EP is BPA diglycidyl ether (DGEBA) and the curing agent is dicyandiamide (DICY). Their structures and the cured EP are present in Scheme 1. This system selectively cleaves N–CN–N and COO bonds (which exist in the oxidized part), while C–O and C–C bonds remain intact under mild conditions (230 °C, 5 h). After degradation, CFs can be retained and recycled; meanwhile, DEP preserves BPA structure, which can be converted into cycloalkane and its derivatives, over traditional Ru-based catalysts. The whole process is shown in Scheme 2.
Scheme 1. Chemical structures of DGEBA, DICY and cured EP. DGEBA: Bisphenol A diglycidyl ether; DICY: dicyandiamide; EP: epoxy resin.
EXPERIMENTAL
Materials
CFREP prepreg (WP-1021), containing 40% DGEBA type EP (Bisphenol A diglycidyl ether, DICY curing agent) and 60% CF, was bought from Shandong Weihai Guangwei Carbon Fiber Co. Ltd. (China). ZnCl2 was bought from Shanghai Boer Chemical Reagents CO., Ltd. THF was bought from Shanghai Titan Scientific Co., Ltd. RuCl3 was bought from Sigma Aldrich. Activated carbon powder was bought from SCM Industrial Chemical Co. Ltd. The synthesis of related solid catalysts is shown in the Supplementary Materials. All chemicals were used as received unless otherwise stated. The as-received CFREP prepreg clothes were hardened at 140 °C, 0.1 MPa, and then cut into 1 cm × 1 cm pieces for use.
The same EP and the virgin CF (vCF) were obtained by sonicating the suspension of as-received CF cloth in THF at room temperature for 1 h. After sonication, the vCF was separated and washed with THF, and then dried at 60 °C overnight. Rotating vaporization was applied to recover THF and the uncured EP was hardened in a 140 °C air blast drying oven for 3 h.
The degradation of CFREP
The degradation reaction was conducted in a Teflon-lined autoclave with a volume of 30 mL. In each experiment, 1 g CFREP, different proportions of ultra-pure water, organic solvent and amount of ZnCl2 were added. The autoclave was pressurized by 2 MPa N2 and then reacted for a period of time. After the reaction, the autoclave was cooled down in cool water.
rCF was washed with the same organic solvent as that used in degradation experiment, and dried at 100 °C overnight. The degradation rate (Dr.%) is calculated by
where m0 means the mass of CFREP before degradation, m1 refers to the mass of recycling CF (rCF), and 40% indicates the CFREP includes 40% resin and 60% CF, which is given by the company. All experiments were repeated three times and the Dr.% was averaged.
The washing solution mentioned above and the reaction solution were merged, and then the organic solvent was collected by rotary evaporation at 50 °C and ultra-pure water was added to precipitate the DEP and dissolve ZnCl2 in the residue. The DEP was washed with ultra-pure water until no white precipitate was detected in the filtrate when saturated K2CO3 solution was added. After that, the DEP was dried at 110 °C for 12 h, yielding yellow solid powder [Supplementary Figure 1], which was used for further characterization and reaction.
The cycling stability was investigated. After each reaction, the solution was collected after separating CF, and then another part of CFREP was added for the next run without separation of DEP.
A 10-time scaling-up experiment was conducted in a 500 mL autoclave made by Anhui Kemi Instrument Co., LTD. Materials 10 g CFREP (2 cm × 2 cm pieces), 134 mL THF (considering the density of THF is 0.896 g/mL, the mass of 134 mL THF is 120.0 g), 13.4 mL ultra-pure water and 7.4 g ZnCl2 were added with mechanical stirring of 400 rpm. In order to make mass transfer easier, except CFREP, other chemicals were used approximately 15 times the amount compared to small tests. The reaction and treatment processes were the same as mentioned above.
Hydrogenation of DEP
Hydrogenation reaction was conducted in the same brand of autoclave as mentioned above. Materials 0.5 g DEP, 0.1 g catalyst and 5 g or no solvent were added and pressurized by 2 MPa H2. The reaction temperature was raised to 250 °C, and the reaction was continued for a period of time at the target temperature. After reaction, the autoclave was cooled down in water.
Characterization
The qualitative analysis of the product was performed using gas chromatography-mass spectrometry (GC-MS) with an Agilent Technologies 7890A GC system coupled with an Agilent Technologies 5975C inert MSD and Triple-Axis Detector. The quantitative analysis was handled on GC, Agilent Technologies 7890B GC system. The VARIO EL CUBE elemental analyzer was employed to measure the mass of C, H, N in DEP. 1H-NMR and 13C-NMR were carried out using an AVANCE III 400 Super Conducting Fourier NMR Spectrometer. A FTIR Nexus INVENIO S + Hyperion3000 was used to analyze the different functional groups in EP and DEP. The Raman spectrum was recorded using an invia reflex laser micro-Raman spectrometer with a 633 nm laser, in order to characterize the change of CF after degradation. Thermal gravimetric analysis (TGA-8000) was performed to analyze the decomposed temperature of EP and DEP. The morphology and cross-sectional area of vCF and rCF were confirmed by a scanning electron microscope. The tensile strength and module are tested by EXCEED tensile testing machine Model E42.
RESULTS AND DISCUSSION
The evaluation of degradation system
Polar aprotic solvents, such as THF, dimethylformamide (DMF) and acetone, and protic solvents, such as ethanol, are first selected and worked with H2O as a mix-solvent, because previous works have shown the ability of polar aprotic solvents to swell polymers and enhance catalyst accessibility. The degradation reaction was conducted at 230 °C for 5 h under N2 atmosphere and the results were shown in Table 1. It can be seen that polar aprotic solvents show much better degradation behaviors than protic solvents (ethanol). A worse Dr.% in DMF is probably due to its hydrolysis and low interaction energy[8], leading to toxic gases such as carbon monoxide and dimethylamine. Acetone shows the same Dr as THF, but the side reaction (self-aldol condensation) makes it hard to recycle, limiting its usage. THF plays an important role in degradation of EP. THF has a good swelling ability. During degradation, THF molecules are relatively easy to infiltrate and expand in the thermosetting covalent network; the repelling force between atoms weakens the covalent bond in resin.
Degradation of CFREP in different mix-solvents
Entry | Organic Solv. | Degradation rate/% |
1 | THF | > 99.99 |
2 | Acetone | > 99.99 |
3 | DMF | 84.16 |
4 | EtOH | 52.45 |
Zinc ions are a kind of mild Lewis acid and can coordinate with the amino group in EP and weaken C–N bonds. In previous works, ZnCl2 is proven to weaken and break C–N bond in the covalent network of CFREP[17,18], but high-concentrated ZnCl2 was used and led to the hydrolysis or alcoholysis, the released protons would corrode the reactors. So, decreasing the dosage of ZnCl2 may solve the problem in mix-solvent systems.
Other zinc salts or Lewis acids were also considered. The degradation mechanism using ZnSO4 or ZnBr2 is the same as using ZnCl2. ZnSO4 is less soluble than ZnCl2, which may influence the degradation. ZnBr2 is more expensive, and bromine ions may cause pollution. Zn(NO3)2 has oxidation properties due to NO3- and may cause nitration of the benzene ring, which should be avoided. AlCl3 can hydrolyze in H2O and is unsuitable for this mix-solvent system. La(OTf)3 is too expensive for widespread use. In summary, ZnCl2 was chosen for our study.
Figure 1A shows the influence of ZnCl2 concentration. A high ZnCl2 concentration effectively degrades EP, which is consistent with other works. When the concentration gets lower to 5.26%, the Dr maintained over 99%, and even when no catalyst is added, it also reaches 44.03%, showing that mix-solvents can swell efficiently and the dosage of ZnCl2 can be reduced. Then, the influence of THF/H2O was investigated. The result in Figure 1B indicates that the portion of THF and H2O showed a synergistic effect on the degradation process. THF is a good solvent for EP and makes EP easily swollen. In order to break the C–N bond, nucleophiles are necessary. H2O is not only a type of good nucleophile, but it can also increase the solubility of catalysts (ZnCl2). The good swelling ability of THF facilitates the transferring of catalyst and
Figure 1. Effect of (A) concentration of catalyst in degradation system, with no catalyst added, 44.07% Dr was achieved, (B) portion, (C) temperature, (D) time: 1 g × 40% CFREP; 2 MPa N2 and (A) 230 °C; 5 h; 0.5 g ZnCl2; (B) 10% H2O; 5 h; 0.5 g ZnCl2; (C) 10% H2O; 230 °C; 5 g ZnCl2; (D) 10% H2O;
Furthermore, the influence of reaction temperature and time was investigated. Figure 1C shows that Dr rises from 50.1% to over 99% when the reaction temperature increases from 210 to 230 °C. Figure 1D shows the degradation time also played a significant role because the degradation process takes place gradually from the outer surface into the resin interior. It took 4 h to degrade the EP on CFREP completely.
The cycling stability of the degradation system is also investigated; after each reaction, the CF was collected and removed from the solution. In the next run, another 1 g CFREP was added into the solution. The results shown in Figure 2 indicate the Dr remains near 99% after three cycles. Solvent cycling can reduce solvent usage, and the homogeneous ZnCl2 catalyst does not need to be extracted from the solvent, which is an advantage compared to previously reported works. In order to explore whether this degradation system is available industrially, a scaling-up experiment was conducted. The concentration of ZnCl2 is the same as that in a small bench; the Dr was reduced to 93% after prolonging the reaction time to 6 h. This high Dr shows a potential industrial application.
Figure 2. Cycling stability of degradation system. Reaction conditions: 1 g × 40% CFREP; 8.1 g THF; 0.9 g H2O; 2 MPa N2; 230 °C; 5 h;
Characterization of degraded product (DEP)
The catalytic cleavage of chemical bonds in EP was investigated by FTIR and the spectra of raw material (EP) and DEP were shown in Figure 3 (Up). In EP, peak (a) at 3,428 cm-1 represents the associated -OH in the covalent network, and the shoulder at 3,200 cm-1 belongs to the -NH-, indicating a bit of NH groups. Peaks (b), (c) and (d) at 2,964, 2,929 and 2,871 cm-1 belong to -CH3 in BPA structure, -CH2- and CH in glycerin-like structure. Specifically, the peaks (e) at 2,161 and 2,204 cm-1 in EP represent the -CN group in curing agents. The peak (f) at 1,754 cm-1 belongs to the ester carbonyl group instead of the amide carbonyl group in EP, indicating part of EP is oxidized, which is marked in Figure 3 (Down). The peak (g) at
Figure 3. (Up) FTIR spectra of EP and DEP; (Down) C–N and C–O bond cleavage of EP in degradation reaction. FTIR: Fourier transform infrared spectroscopy; EP: epoxy resin; DEP: decomposed epoxy resin.
In the FTIR spectrum of DEP, peaks (a), (b), (c), (d), (h), (i), (j), (k), (q) and (r) remain unchanged, indicating the BPA structure did not break during degradation. Peaks (m), (n), (o) and (p) decline due to C–O and C–N breakage. Peaks (e), (f), (g) and (l) almost disappear, indicating that: firstly, the -CN group in curing agents was probably hydrolyzed to -COOH, and decarboxylic reaction took place; secondly, the ester bond was hydrolyzed; thirdly, the C=N bond was removed. These results demonstrated that the breakage of C–N and ester bonds happens, and the site of bond breakage is shown in Figure 3 (Down).
The specific carbon skeleton structures of DEP were analyzed by 1H-NMR [Figure 4] and 13C-NMR
These results show that the carbon skeleton in DGEBA remains intact, while the signal of the curing agent is not obvious, which means that part of the curing agent was removed during degradation. It can be concluded that the degradation system mainly breaks the C–N and ester bonds in CFREP, with no C–C or benzene rings being cleaved, which is consistent with the FTIR results.
Elemental analysis was employed to obtain the element components of EP and DEP
The molecular weight of DEP and its distribution were investigated using the GPC method and the results are shown in Supplementary Figure 4. The Mw of DEP is 495 Daltons, higher than that of DGEBA (Mw = 340.01 and Mn = 192) but lower than that of BPA (mole mass = 228.291). This indicates that DEP contains a few glycerol and curing agent pieces, which contribute to the lower Mn. According to Mw and Mn values, it can be inferred that DEP contains a BPA structure, small amounts of glycerol and curing agent fragments, and portions of EP that include one DGEBA structure and one curing agent structure.
Characterization of CF
The morphology of vCF and rCF is observed by scanning electron microscopy (SEM) [Figure 5]. CFREP is decomposed and CF is recovered in a small bench reactor. Because of the scaling effect, EP remained on rCF in the scaling-up experiment [Supplementary Figure 6]. A SEM image showed that the resin is almost removed and the surface of CFs is smooth. Only a little residual resin appears on rCF, proving that resin is almost removed during degradation.
Figure 5. SEM images of (A) vCF and (B) rCF. Reaction condition: 1 g × 40% CFREP; 8.1 g THF; 0.9 g H2O; 2 MPa N2; 5 h; 230 °C. SEM: Scanning electron microscopy; vCF: virgin carbon fiber; rCF: recovered carbon fiber; CFREP: carbon fiber reinforced epoxy resin; THF: tetrahydrofuran.
Furthermore, Raman spectroscopy was employed to evaluate the graphitization degree of vCF and rCF. As shown in Figure 6, the characteristic peak at approximately 1,590 cm-1 (G band) corresponds to an ideal graphite lattice, while that at ~1,360 cm-1 (D band) corresponds to graphite lattice with defects. The ratio of peak height (IG/ID) is indicative of defects in carbon materials. The IG/ID of rCF is 0.895 and that of vCF is 0.907, indicating the solvothermal degradation process only caused a tiny damage to CF.
Figure 6. Raman spectra of (A) rCF and (B) vCF. rCF: Recovered carbon fiber; vCF: virgin carbon fiber.
The tensile strength and modulus of rCF and vCF were measured for comparison
Utilization of DEP to valuable chemicals
According to the analysis of FTIR and NMR spectra, it is confirmed that the BPA structure remains unchanged after degradation. So, valuable chemicals such as phenol, benzene or cyclohexane and their derivatives would be obtained through hydrogenation and hydrogenolysis.
In order to quantitively analyze the yield of the product, the number of rings in DEP is first calculated because the product is mainly from BPA, as given in
Where m is the weight of DEP. A2 and A3 are defined by 1H-NMR. The peaks at 6.7 and -7.5 ppm are integrated and expressed as A2. All peaks in 1H-NMR are integrated and expressed as A3 without the peak of DMSO-d6. A2/A3 × 100% equals the portion of H atoms on benzene rings. Considering the para-distributed benzene ring contains 4 H atoms, the number of rings is the number of H atoms divided by 4. ω is the mass fraction of H atoms from elemental analysis, and m × ω/1g/mol equals the molar of total H atoms.
Here, cycloalkane and isopropyl cyclohexane are man products, which can be used as constituents of jet fuel. For oxygen removal from DEP products, various Ru-based catalysts were used. As shown in Table 2, over Ru/C, Ru/NiAl2O4 and Ru/CeO2 catalysts, the main products are all benzene ring-saturated products, with a small amount of cumene. However, the molar yields of C6 and C9 compounds are not identical, with the molar yield of C6 being higher than that of C9, indicating C–C bond cleavage between the isopropyl and benzene ring during hydrogenation. On traditional Ru/C catalysts, the molar yields of cyclohexane and isopropyl cyclohexane are almost the same, suggesting that deep cracking occurred on this catalyst, allowing for the preservation of more carbon atoms. On the other three catalysts, deep cracking of the C9 component happened, leading to the production of more cyclohexane and less iso-propyl-substituted cyclohexane.
Utilization of DEP to cycloalkanes
Entry | Cat. | Mass yield (molar yield)/% | Total mass yield. (molar yield)/% | ||
Cyclohexane | Isopropyl cyclohexane | Cumene | |||
1 | 5%Ru/C | 5.5 (22.6) | 8.0 (21.7) | 0 | 13.5 (44.3) |
2 | 5%Ru/NiAl2O4 | 5.4 (22.2) | 3.2 (8.7) | 1.9 (5.4) | 10.5 (36.3) |
3 | 5%Ru/CeO2 | 3.6 (14.9) | 1.7 (4.5) | 1.4 (4.1) | 6.7 (23.5) |
CONCLUSIONS
In conclusion, chemical recycling of BPA-based CFREP, cured with DICY, was successfully achieved using a low-concentrated ZnCl2-THF-H2O degradation system, with over 99% Dr.%. A scaling-up experiment is also conducted, demonstrating the potential for industrial application. The cleavage of specific C–N and ester C–O bonds, while preserving C–C and ether C–O–C bonds, is evidenced by FTIR and 1H-NMR. The rCF retains 87.2% of its tensile strength. DEP contains its intact BPA structure and can be hydrogenated to useful chemicals such as C6 and C9 hydrocarbons. This work introduces a mind mix-solvent system and demonstrates the recovery of valuable CFs and conversion of DEP into jet-fuel constituents.
DECLARATIONS
Acknowledgments
We sincerely thank all team members who participated in this study.
Authors’ contributions
Experiments and data analysis: Jiang, Y.
Discussion on the results: Jiang, Y., Feng, B., Liu, X., Guo, Y.
Design of the study: Wang, Y.
Availability of data and materials
The raw data supporting the findings of this study are available within the article and its Supplementary Materials. Further data is available from the corresponding authors upon reasonable request.
Financial support and sponsorship
The authors thank the National Key Research and Development Program of China (2022YFA1504903) and the NSFC of China (22072042) for their financial support.
Conflicts of interest
All authors declared that there are no conflicts of interest.
Ethical approval and consent to participate
Not applicable.
Consent for publication
Not applicable.
Copyright
© The Author(s) 2025.
Supplementary Materials
REFERENCES
1. Liu, T.; Shao, L.; Zhao, B.; Chang, Y. C.; Zhang, J. Progress in chemical recycling of carbon fiber reinforced epoxy composites. Macromol. Rapid. Commun. 2022, 43, e2200538.
2. Meng, F.; Olivetti, E. A.; Zhao, Y.; Chang, J. C.; Pickering, S. J.; Mckechnie, J. Comparing life cycle energy and global warming potential of carbon fiber composite recycling technologies and waste management options. ACS. Sustainable. Chem. Eng. 2018, 6, 9854-65.
3. Matsuda, S.; Miyake, M.; Oshima, K. Tensile fracture characteristics of carbon fibers collected from the outer and inner parts of a CFRP laminate by thermal decomposition. Compos. Struct. 2022, 292, 115603.
4. Zhao, Q.; Jiang, J.; Li, C.; Li, Y. Efficient recycling of carbon fibers from amine-cured CFRP composites under facile condition. Polym. Degrad. Stabil. 2020, 179, 109268.
5. Yan, H.; Lu, C.; Jing, D.; Hou, X. Chemical degradation of amine-cured DGEBA epoxy resin in supercritical 1-propanol for recycling carbon fiber from composites. Chin. J. Polym. Sci. 2014, 32, 1550-63.
6. Nie, W.; Liu, J.; Liu, W.; Wang, J.; Tang, T. Decomposition of waste carbon fiber reinforced epoxy resin composites in molten potassium hydroxide. Polym. Degrad. Stabil. 2015, 111, 247-56.
7. Das, M.; Varughese, S. A novel sonochemical approach for enhanced recovery of carbon fiber from CFRP waste using mild acid–peroxide mixture. ACS. Sustainable. Chem. Eng. 2016, 4, 2080-7.
8. Long, Y.; Su, Z.; Bai, L.; et al. Multiple promotion effect of mixed solvents on the oxidative degradation of thermosetting polymers. Green. Chem. 2023, 25, 5566-74.
9. Long, Y.; Tian, F.; Bai, L.; et al. A mild and efficient oxidative degradation system of epoxy thermosets: full recovery and degradation mechanism. Green. Chem. 2022, 24, 7082-91.
10. Liu, L.; Liu, X.; Li, X.; Xu, S.; Wang, Y. Z. An integrative chemical recycling approach for catalytic oxidation of epoxy resin and in situ separation of degraded products. Angew. Chem. Int. Ed. Engl. 2024, 63, e202405912.
11. Shen, M.; Robertson, M. L. Degradation behavior of biobased epoxy resins in mild acidic media. ACS. Sustainable. Chem. Eng. 2021, 9, 438-47.
12. Ahrens, A.; Bonde, A.; Sun, H.; et al. Catalytic disconnection of C-O bonds in epoxy resins and composites. Nature 2023, 617, 730-7.
13. Kim, Y. N.; Kim, Y.; Kim, S. Y.; et al. Application of supercritical water for green recycling of epoxy-based carbon fiber reinforced plastic. Compos. Sci. Technol. 2019, 173, 66-72.
15. Okajima, I.; Sako, T. Recycling fiber-reinforced plastic using supercritical acetone. Polym. Degrad. Stabil. 2019, 163, 1-6.
16. Wang, Y.; Cui, X.; Ge, H.; et al. Chemical recycling of carbon fiber reinforced epoxy resin composites via selective cleavage of the carbon–nitrogen bond. ACS. Sustainable. Chem. Eng. 2015, 3, 3332-7.
17. Liu, T.; Zhang, M.; Guo, X.; et al. Mild chemical recycling of aerospace fiber/epoxy composite wastes and utilization of the decomposed resin. Polym. Degrad. Stabil. 2017, 139, 20-7.
18. Deng, T.; Liu, Y.; Cui, X.; et al. Cleavage of C–N bonds in carbon fiber/epoxy resin composites. Green. Chem. 2015, 17, 2141-5.
19. Liu, T.; Guo, X.; Liu, W.; et al. Selective cleavage of ester linkages of anhydride-cured epoxy using a benign method and reuse of the decomposed polymer in new epoxy preparation. Green. Chem. 2017, 19, 4364-72.
Cite This Article
How to Cite
Download Citation
Export Citation File:
Type of Import
Tips on Downloading Citation
Citation Manager File Format
Type of Import
Direct Import: When the Direct Import option is selected (the default state), a dialogue box will give you the option to Save or Open the downloaded citation data. Choosing Open will either launch your citation manager or give you a choice of applications with which to use the metadata. The Save option saves the file locally for later use.
Indirect Import: When the Indirect Import option is selected, the metadata is displayed and may be copied and pasted as needed.
About This Article
Special Issue
Copyright
Data & Comments
Data
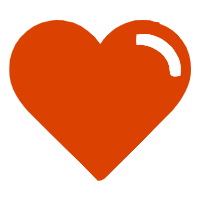
Comments
Comments must be written in English. Spam, offensive content, impersonation, and private information will not be permitted. If any comment is reported and identified as inappropriate content by OAE staff, the comment will be removed without notice. If you have any queries or need any help, please contact us at [email protected].