Green hydrogen from alkaline water electrolysis: bridging the gaps between laboratory research and industrial applications
Abstract
Green hydrogen, generated through water electrolysis powered by renewable energy, holds immense potential for achieving climate neutrality. Among the various water electrolysis technologies, the alkaline water electrolyzer (AWE) is the most mature and widely adopted in the industry. However, its efficiency is limited by the low performance of its Ni-based electrodes. While numerous high-performance electrocatalysts have been meticulously designed and demonstrated in laboratory settings using three-electrode systems, their adoption in practical AWE systems remains rare. This disconnect arises from the overlooked gap between laboratory research and industrial application. In this perspective, we identify and analyze three critical gaps between these two domains and offer strategic recommendations to bridge them, paving the way for more effective implementation of advanced electrocatalysts in industrial AWE.
Keywords
CURRENT STATUS OF RESEARCH ON WATER ELECTROLYSIS
In the face of climate change, hydrogen is widely regarded as the most promising sustainable energy carrier for replacing fossil fuels[1]. Currently, most commercial hydrogen is produced through methane steam reforming, a process that releases significant amounts of greenhouse gases, primarily carbon dioxide[2]. This production method yields gray hydrogen, or blue hydrogen if combined with carbon capture and storage technology, neither of which is sustainable for large-scale, long-term use. Green hydrogen offers a viable solution, as it is produced via water electrolysis powered by renewable electricity (e.g., solar and wind energy). However, the low energy efficiency (electricity-to-hydrogen conversion) of industrial water electrolyzers results in high production costs for green hydrogen, estimated at approximately USD 4-5.5 per kilogram of H2[3]. This cost makes green hydrogen less competitive with gray or blue hydrogen, which costs around USD 2 per kilogram of H2[4]. Consequently, the limited market penetration of green hydrogen, accounting for less than 5% of global H2 production, remains a significant challenge.
To date, alkaline water electrolyzers (AWEs) remain the most robust and durable devices for industrial-scale electrochemical water electrolysis[5,6]. While proton-exchange membrane water electrolyzers (PEMWEs) can theoretically achieve higher catalytic activity due to the use of ion-conducting polymer membranes, which offer greater conductivity than the diaphragms in AWEs, the instability of these membranes remains a significant challenge. Additionally, the highly corrosive acidic environment in PEMWEs limits the selection of electrocatalysts to expensive and non-sustainable platinum-group metals (PGMs), such as platinum (Pt) for cathodes and iridium oxide (IrO2) for anodes. This environment also necessitates the use of acid-tolerant bipolar plates, which are more costly than those used in AWEs. Consequently, AWEs are at least 50% cheaper to manufacture than PEMWEs[7].
Despite its advantages, the AWE suffers from poor efficiency, primarily due to the limited electrochemical performance of its electrodes, among other engineering and technical challenges. To address this, researchers have explored alternatives to the conventional nickel-coated perforated stainless steel (SS) used in industrial AWEs, including PGMs such as ruthenium (Ru)[8-11]. In the early stages, the synthesis and evaluation of electrode catalysts were predominantly conducted under controlled laboratory conditions. More recently, there has been growing recognition of the importance of evaluating electrodes under industrially relevant conditions using fully assembled water electrolyzer devices, as the standards and operating parameters of industrial-scale water electrolysis differ significantly from those commonly employed in laboratory research [Table 1][12-14]. However, the gaps between laboratory research and industrial application remain insufficiently addressed.
Representative operating parameters and key performance standards for industrial and lab-scale water electrolyzers
Key performance standards | |||||||
Working conditions | Stability | Cost and scalability | System integration | ||||
Current density | Temperature | Electrolyte | |||||
Water splitting scale | Industrial water splitting | 200-600 mA/cm2 or higher | 70-90 °C | 20-30 wt% KOH | ≥ 100,000 h | High priority | Large-scale zero-gap cell |
Lab-scale water splitting | ≤ 100 mA/cm2, typically 10 mA/cm2 | Typically room temperature | Typically 0.1-1 M KOH | Typically a few hours/days | Typically not applicable for scalable production | Typically H-cell or three-electrode setup |
In this perspective, we summarize three key gaps drawing on our research experience in electrode development for AWEs. Furthermore, we offer practical recommendations to close these gaps, aiming to guide future research efforts in designing water-splitting electrocatalysts for real-world applications.
GAPS BETWEEN LABORATORY RESEARCH AND INDUSTRIAL APPLICATIONS
Gaps between evaluation devices
The catalytic performance of electrode catalysts for water splitting must be evaluated using appropriate devices. Currently, most electrode catalysts prepared in laboratories are tested under mild conditions (e.g., room temperature) using a standard three-electrode system comprising a working electrode, counter electrode, and reference electrode [Figure 1A]. This setup is simple and effective for characterizing the intrinsic catalytic performance of nanomaterials at the electrode level and for exploring their catalytic mechanisms. However, the ohmic resistance from the electrolyte solution between the cathode and anode, along with contact resistance, can cause voltage drops, commonly referred to as iR drops. These drops vary significantly across tests and laboratories due to differences in electrode arrangement and connections. To address this variability, researchers typically compensate the recorded voltage for the iR drop, allowing a more accurate assessment of the intrinsic performance of electrocatalysts. Consequently, the overpotentials reported in the literature often do not reflect the true performance of the catalysts under practical conditions.
Figure 1. Schematics of water-splitting setups at three different levels. (A) A three-electrode setup at the electrode level; (B) A single-cell AWE at the cell level; (C) A stationary AWE system at the system level. The photos in (A and B) depict setups used in the authors’ laboratory, while the photo in (C) is reprinted from Nel Hydrogen. GDL: Gas diffusion layer; AWE: alkaline water electrolyzer.
Despite its usefulness, the three-electrode system configuration cannot be directly applied to evaluate practical water-splitting scenarios, where the actual cell voltage is more relevant than theoretical values in demonstrating the real-world performance of electrode catalysts. To bridge this gap, a more integrated AWE setup is used to test electrodes under industrially relevant conditions. As shown in Figure 1B, the single-cell AWE serves as the core unit of a stationary water electrolyzer system [Figure 1C]. In this setup, reactants and gas products flow continuously in and out of the anodic and cathodic compartments, which are separated by a separator. This continuous flow operation enhances gas removal and collection, improving mass transport efficiency, while the separator ensures separation of the hydrogen (H2) and oxygen (O2) gas products. Depending on the electrolyzer technology, the separator can be either an ion-exchange membrane, such as proton-exchange membrane (PEM) or anion-exchange membrane (AEM), or a diaphragm. A key challenge in AWE design is minimizing the ohmic cell resistance between electrodes, which can be achieved by positioning them close to the separator in a zero-gap configuration[15-17]. Although PEMWEs and AEM water electrolyzers (AEMWEs) can operate at higher current densities (≥ 1 A/cm2) than AWEs (0.2-0.6 A/cm2), these technologies face significant challenges. PEMWEs depend on expensive noble metals, while AEMWEs suffer from membrane instability due to ionic conductivity loss caused by reactions between -OH groups and CO2. Unlike membrane-based electrolyzers, such as AEMWEs, where close contact between the catalyst and membrane in the catalyst-coated membrane (CCM) configuration is essential for optimal performance, porous diaphragm-based AWE systems do not require such an intimate interface. Consequently, the catalyst-coated substrate (CCS) approach, valued for its simplicity and scalability, is more commonly adopted in industrial AWE electrode fabrication[5]. As a result, AWE technology - built on stable diaphragms that have evolved from asbestos-based materials to advanced polymer-ceramic composites, such as AGFA’s Zirfon, a polysulfone-ZrO2-poly(phenylene sulfide) composite, for improved durability and performance[5,18], - continues to dominate the electrolyzer market.
While we emphasize the importance of evaluating electrode catalysts in single-cell AWE setups under realistic conditions, the three-electrode configuration remains invaluable for initial screening of electrocatalysts before advancing to AWE testing. Therefore, we recommend using both configurations in laboratory research to develop water-splitting electrocatalysts. Electrocatalysts showing promising performance in the three-electrode configuration should subsequently be tested in single-cell AWEs under industrially relevant conditions. Whenever possible, evaluation using multi-cell stacks in kilowatt (kW)-scale AWE systems is encouraged to assess the practical potential of developed electrocatalysts for megawatt (MW)-scale applications.
Gaps between electrode syntheses
Electrodes are the core components of water electrolyzers. Electrocatalysts for electrode preparation are typically synthesized either in powdered form or directly grown on a current collector substrate [Figure 2A]. In the former approach, powdered electrocatalysts are applied to the substrate using polymer binders such as Nafion, which inevitably increases resistance, masks active sites, and hinders mass transport[19,20]. Furthermore, conductive additives, such as nanocarbon materials, are often required to enhance the electrocatalyst’s conductivity. However, when used as anodes, these carbon additives are prone to oxidation and degradation at high potentials, leading to diminished electrode performance[21]. Moreover, the weak adhesive strength provided by binders poses significant challenges under high current densities and prolonged operation, as the coated catalyst layer may gradually peel off, reducing catalytic efficiency over time. Techniques such as hot-pressing powdered catalysts to form dense layers on substrates can help mitigate these issues, but they also negate the benefits of the high surface area of nanostructured powders[22]. Thus, while powdered electrocatalysts with precise control over nanoparticle shape, size, and mass loading are valuable for fundamental research, they are less suitable for practical water electrolysis applications. In this regard, self-supporting electrodes, with electrocatalysts directly grown in situ on the substrate surface, offer a simplified preparation process, strong catalyst-substrate integration, and excellent stability, making them a highly attractive alternative for high-current-density water electrolysis[20,23,24].
Figure 2. (A) Schematic illustration of conventional powdery catalysts coated onto current collectors (which also serve as substrates), and self-supported electrodes with catalysts grown in-situ on current collectors (substrates). Reproduced with permission from ref.[20]. Copyright 2020, Wiley-VCH; (B) Self-supported electrode of NiMoN@NiFeN grown on NF via a hydrothermal strategy. Reproduced with permission from ref.[25]. Copyright 2019, Nature Publishing Group; (C) Self-supported electrode of SnS2 grown on SS made through immersion treatment followed by annealing. Reproduced with permission from ref.[27]. Copyright 2020, American Chemical Society; (D) Self-supported electrode of Cu2S nanorod grown on top of Cu mesh synthesized from immersion and ion-exchange strategy. Reproduced with permission from ref.[28]. Copyright 2019, American Chemical Society; (E) Self-supported electrode of Ru@Cu-TM nanorods grown on Ti mesh with Ru nanoparticles uniformly electrodeposited onto Cu nanoplatelets by applying a fixed current. Reproduced with permission from ref.[31]. Copyright 2023, Nature Publishing Group. CM: Cu mesh; SS: stainless steel mesh; TM: Ti mesh; NF: Ni foam.
The synthesis of self-supporting electrodes for water splitting is a hot topic in current research. Most synthesis methods rely on hydro/solvothermal strategies[25], in which a small substrate is immersed in a solution of catalyst precursors inside a Teflon-lined stainless-steel autoclave [Figure 2B]. However, because hydro/solvothermal reactions occur in sealed environments at high pressures and temperatures, scaling up for industrial AWE applications is challenging and potentially hazardous. Thus, alternative synthesis strategies that are simpler and safer need to be developed. Two promising approaches that we would like to highlight for producing industrial-scale electrodes are immersion processing and electrodeposition.
Immersion processing resembles hydro/solvothermal reactions but does not require high temperatures or pressures. In this method, the substrate is immersed in a solution containing catalyst precursors or one that can corrode, deposit on, or react with the substrate. Moreover, electrode upscaling can be readily accomplished by proportionally increasing the substrate size and adjusting the volume of precursor solutions accordingly. For example, Yin et al. prepared a highly active amorphous Ni-Fe hydroxide layer for the oxygen evolution reaction (OER) by immersing nickel foam in a ferric nitrate solution at room temperature. They demonstrated that the activity of the catalyst layer could be tuned by adjusting the immersion time and precursor concentration[26]. In some cases, additional post-immersion treatments, such as annealing, are necessary. For instance, we prepared a SnS2/SS electrode by immersing an SS mesh in a SnS2 molecular precursor solution, followed by annealing [Figure 2C]. By varying the Sn/S precursor ratio, the composition could be altered from SnS2 to SnS[27]. In another example, we grew Cu2S nanorod arrays on a copper mesh (CM) by first immersing it in a solution of NaOH and (NH4)2S2O8 to form Cu(OH)2 nanowires, followed by immersion in Na2S for ion exchange [Figure 2D][28].
Electrodeposition enables the rapid growth of uniform nanoscale morphologies and allows precise control over the composition by adjusting the applied electric potential or current[29,30]. Unlike immersion methods, which often require post-treatment to enhance adhesion, electrodeposited active materials can be directly tailored during the deposition process. For example, we previously electrodeposited Ru nanoparticles onto a Cu nanoplatelet array grown on a Ti mesh (TM). By varying the applied voltage or current, we optimized the Ru deposition parameters to achieve the desired properties [Figure 2E][31].
Gaps between electrode evaluations
The performance evaluation of electrodes for water splitting is a critical aspect of electrode development. Currently, most electrode catalysts are tested under mild laboratory conditions in a three-electrode system [Table 1], with iR compensation often applied to reduce variations between laboratories and test setups, allowing researchers to focus on intrinsic catalyst performance. However, these mild conditions do not reflect the operational environment of industrial AWEs [Table 1], raising concerns about the reliability of catalyst screening under such settings[13]. In addition to operating conditions, water quality significantly impacts catalyst stability and performance. While most laboratory studies utilize high-purity water, industrial applications must account for impurities such as Fe ions and Cl-, which can accelerate catalyst degradation and affect long-term operation[32]. These combined factors contribute to the deterioration of catalyst structures and active phases, alter reaction kinetics, and intensify mass transport limitations[29]. Consequently, catalysts that perform well under laboratory conditions may fail to deliver comparable performance in industrially relevant environments.
For example, Pascuzzi et al. investigated the stability of thin NiFe-(oxy)hydroxide films during alkaline water oxidation at a current density of 100 mA/cm2 under varying temperatures and KOH concentrations[33]. While anodic polarization at 25 °C caused minimal degradation, a higher temperature
Figure 3. (A) Performance differences between a three-electrode setup and an AWE in evaluating the same NiFe@NF electrode for OER. Reproduced with permission from ref.[31]. Copyright 2023, Nature Publishing Group; (B) Structural modification differences between a three-electrode setup and an AWE in evaluating the same Ru@Cu-TM electrode for HER. Reproduced with permission from ref.[31]. Copyright 2023, Nature Publishing Group. AWE: Alkaline water electrolyzer; NF: Ni foam; OER: oxygen evolution reaction; TM: Ti mesh; HER: hydrogen evolution reaction.
The discrepancies between laboratory and industrial conditions affect not only OER catalysts but also hydrogen evolution reaction (HER) catalysts at the cathode. Unlike OER, where oxidative potentials can continuously degrade electrode components, HER occurs under reductive conditions, which are generally more stable once preconditioning is complete. However, even HER catalysts can undergo significant morphological changes under harsh AWE conditions. In recent work, we observed that Cu nanoplatelets grown on Ti substrates retained their structure after 200 h of HER operation at 200 mA/cm2 in a three-electrode system but transformed into bundle-like nanowires after only 24 h in an industrial AWE setup. After four weeks, only nanowires remained. This transformation was attributed to the accelerated formation of soluble Cu-OH species in highly alkaline media and their redeposition under negative potentials
Another factor often overlooked due to technical challenges is the impact of pressure on water electrolysis. Ju et al. reported that cell voltage decreases monotonically with increasing pressure from 1 to 15 bar at constant temperature but fluctuates between 15 and 30 bar[15]. Higher pressure reduces bubble size, minimizing resistance caused by gas bubble blockage[39,40]. While building pressurized AWE systems for laboratory testing is complex, an alternative approach is to use a more concentrated electrolyte (e.g., 11 M KOH, 43 wt% at 20 °C) for atmospheric testing at temperatures up to 120 °C. After a preconditioning period of several hours, constant current or potential measurements at elevated current densities (e.g.,
DISCUSSION AND PERSPECTIVES
The development of efficient electrode catalysts for water splitting has been a highly active area of research for many years. To date, numerous electrocatalysts have demonstrated superior catalytic performance compared to the Ni electrodes currently used in industrial AWEs. However, transitioning these laboratory-developed catalysts into industrial applications remains a significant challenge. To assess catalysts for industrial alkaline water electrolysis, it is essential to conduct experiments under conditions that closely replicate real-world operations. This includes the use of flow-cell reactors operating at high current densities, exposure to dynamic power inputs, and implementation of accelerated aging protocols involving thermal and impurity-related stress. Key challenges involve mitigating ohmic losses, scaling up laboratory synthesis methods to roll-to-roll manufacturing processes, achieving long-term stability, and integrating operando diagnostic tools with system components. Moreover, the use of cost-effective materials and adherence to safety standards, such as managing thermal runaway risks and byproduct handling, must be validated through pilot-scale testing. This paper has summarized three key gaps between laboratory research and industrial applications. To bridge these gaps, we encourage academic researchers to consider the following aspects in their work on water-splitting electrocatalyst design:
(1) Prioritize stability, scalability, and practical performance over ultra-low overpotentials: Although achieving ultra-low overpotentials in the laboratory has been a common goal, it should not be the sole focus for catalysts intended for industrial use. Researchers must recognize that stability, scalability, and producibility under industrial conditions are equally important. The pursuit of reducing overpotential by a few tens of millivolts is often of limited practical significance when evaluations are conducted under mild laboratory conditions. For instance, McCrory et al. found that the overpotential difference among the top-performing HER catalysts in 1 M NaOH was only 225 mV at 10 mA/cm2[41], while Ehlers et al. demonstrated that this difference could be achieved by simply increasing the operating temperature of an AWE by approximately 50 °C (equivalent to 4.5 mV/°C)[13]. Some might argue that catalysts performing well under mild conditions could still excel in industrial AWEs. However, our recent studies on Ru-based HER electrodes showed that this is not always the case. For example, Ru-Cu nanoheterostructures outperformed Ru@Cu-TM electrodes in a three-electrode system but did not guarantee better performance under industrially relevant AWE conditions[31,42]. This suggests that factors such as mass transport processes on the electrode surface may become more critical under harsher conditions. Therefore, whenever possible, we recommend screening electrode catalysts directly in AWE devices.
(2) Incorporate intermittent operation into stability evaluations: Stability is a critical metric for determining the practical applicability of electrodes. As noted, stability assessments under industrially relevant conditions in AWE equipment are strongly recommended. While researchers have made significant progress in this area, more attention should be given to the intermittent operation that mimics real-world conditions. For instance, Li et al. demonstrated a NiFe-based anode with stable performance for an impressive 19,000 h of continuous operation[43]. However, industrial AWEs often operate under varying loads due to the fluctuating power supply from renewable energy sources. Recent studies have highlighted that intermittent operation places even greater stress on electrodes than continuous operation[13]. Therefore, intermittent testing should complement conventional continuous stability tests to provide a more realistic evaluation of electrode performance. To more accurately replicate the intermittent nature of renewable energy sources, a practical approach is to power the tested electrolyzer with a solar panel under natural sunlight over consecutive days or longer, thereby more closely simulating real-world fluctuations in renewable energy supply[13].
(3) Focus on understanding catalyst deactivation and failure mechanisms: Beyond reporting performance metrics, understanding the mechanisms of catalyst deactivation under industrial AWE conditions is essential for guiding real-world applications. The mechanisms of activity and degradation vary depending on the operating conditions and environments. Researchers should prioritize investigations under industrially relevant conditions, preferably using AWE devices, and leverage operando techniques to monitor physical and chemical transformations, bubble evolution and transport, and electrode surface dissolution during operation. Developing predictive models to simulate long-term catalyst degradation can also provide valuable insights for designing more robust and durable electrocatalysts.
(4) Evaluate electrodes in practical AWE systems at kW scale: While laboratory-scale single-cell AWE setups can simulate many industrial conditions, their small size, low power load, and operation at atmospheric pressure are far removed from the conditions of MW-scale AWE plants. To bridge this gap, electrodes should be tested in stack-level AWEs at kW scale. Such evaluations generate data that are more representative for calculating the levelized cost of hydrogen production and assessing the feasibility of scaling up to MW-level implementation. Establishing performance metrics for kW-scale and especially MW-scale AWE systems remains a significant challenge. However, the report by the International Renewable Energy Agency (IRENA) provides valuable insights, including proposed targets for AWE by 2050 [Table 2][44]. In addition, several previous studies offer useful guidelines for facilitating the transition from laboratory research to industrial-scale applications[14,45,46].
State-of-the-art and future KPIs for AWE technology[44]
Alkaline electrolyzers | ||
2020 | Target 2050 | |
Nominal current density | 0.2-0.8 A/cm2 | > 2 A/cm2 |
Voltage range (limits) | 1.4-3 V | < 1.7 V |
Operating temperature | 70-90 °C | > 90 °C |
Cell pressure | < 30 bar | > 70 bar |
Load range | 15%-100% | 5%-300% |
H2 purity | 99.9%-99.9998% | > 99.9999% |
Voltage efficiency (LHV) | 50%-68% | > 70% |
Electrical efficiency (stack) | 47-66 kWh/Kg H2 | < 42 kWh/Kg H2 |
Electrical efficiency (system) | 50-78 kWh/Kg H2 | < 45 kWh/Kg H2 |
Lifetime (stack) | 60,000 h | 100,000 h |
Stack unit size | 1 MW | 10 MW |
Electrode area | 10,000-30,000 cm2 | 30,000 cm2 |
Cold start (to nominal load) | < 50 min | < 30 min |
Capital costs (stack) minimum 1 MW | USD 270/kW | < USD 100/kW |
Capital costs (system) minimum 10 MW | USD 500-1,000/kW | < USD 200/kW |
In conclusion, this perspective highlights the current gaps between laboratory research and industrial applications and provides actionable recommendations for advancing electrode design for industrial water electrolysis. Significant effort is still needed to overcome these challenges and accelerate the production of green hydrogen through electrochemical water splitting. By addressing these gaps, researchers can contribute to the broader adoption of sustainable hydrogen production technologies.
DECLARATIONS
Authors’ contributions
Manuscript preparation and correction: Zhang, H.; Zuo, Y.; Huang, J.
Conception and design of the study: Zuo, Y.; Huang, J.
Availability of data and materials
Not applicable.
Financial support and sponsorship
This work was supported by the National Key Research and Development Project of China (No. 2022YFE0113800), the Thousand Talents Program for Distinguished Young Scholars and the starting grant of Chongqing University.
Conflicts of interest
All authors declared that there are no conflicts of interest.
Ethical approval and consent to participate
Not applicable.
Consent for publication
Not applicable.
Copyright
© The Author(s) 2025.
REFERENCES
1. Guerra, O. J.; Eichman, J.; Kurtz, J.; Hodge, B. Cost competitiveness of electrolytic hydrogen. Joule 2019, 3, 2425-43.
2. Liu, W.; Niu, X.; Tang, J.; et al. Energy-efficient anodic reactions for sustainable hydrogen production via water electrolysis. Chem. Synth. 2023, 3, 44.
3. Glenk, G.; Reichelstein, S. Economics of converting renewable power to hydrogen. Nat. Energy. 2019, 4, 216-22.
4. Bartels, J. R.; Pate, M. B.; Olson, N. K. An economic survey of hydrogen production from conventional and alternative energy sources. Int. J. Hydrogen. Energy. 2010, 35, 8371-84.
5. Henkensmeier, D.; Cho, W. C.; Jannasch, P.; et al. Separators and membranes for advanced alkaline water electrolysis. Chem. Rev. 2024, 124, 6393-443.
6. Li, L.; Laan, P. C. M.; Yan, X.; et al. High-rate alkaline water electrolysis at industrially relevant conditions enabled by superaerophobic electrode assembly. Adv. Sci. 2023, 10, e2206180.
7. Wang, Y.; Wen, C.; Tu, J.; et al. The multi-scenario projection of cost reduction in hydrogen production by proton exchange membrane (PEM) water electrolysis in the near future (2020-2060) of China. Fuel 2023, 354, 129409.
8. Zhao, J.; Urrego-Ortiz, R.; Liao, N.; Calle-Vallejo, F.; Luo, J. Rationally designed Ru catalysts supported on TiN for highly efficient and stable hydrogen evolution in alkaline conditions. Nat. Commun. 2024, 15, 6391.
9. Kweon, D. H.; Okyay, M. S.; Kim, S. J.; et al. Ruthenium anchored on carbon nanotube electrocatalyst for hydrogen production with enhanced Faradaic efficiency. Nat. Commun. 2020, 11, 1278.
10. Mahmood, J.; Li, F.; Jung, S. M.; et al. An efficient and pH-universal ruthenium-based catalyst for the hydrogen evolution reaction. Nat. Nanotechnol. 2017, 12, 441-6.
11. Gao, G.; Zhao, G.; Zhu, G.; et al. Recent advancements in noble-metal electrocatalysts for alkaline hydrogen evolution reaction. Chin. Chem. Lett. 2025, 36, 109557.
12. Lee, J. K.; Seo, J. H.; Lim, J.; Park, S.; Jang, H. W. Best practices in membrane electrode assembly for water electrolysis. ACS. Mater. Lett. 2024, 6, 2757-86.
13. Ehlers, J. C.; Feidenhans’l, A. A.; Therkildsen, K. T.; Larrazábal, G. O. Affordable green hydrogen from alkaline water electrolysis: key research needs from an industrial perspective. ACS. Energy. Lett. 2023, 8, 1502-9.
14. Marquez, R. A.; Espinosa, M.; Kalokowski, E.; et al. A guide to electrocatalyst stability using lab-scale alkaline water electrolyzers. ACS. Energy. Lett. 2024, 9, 547-55.
15. Ju, W.; Heinz, M. V. F.; Pusterla, L.; et al. Lab-scale alkaline water electrolyzer for bridging material fundamentals with realistic operation. ACS. Sustain. Chem. Eng. 2018, 6, 4829-37.
16. de Groot, M. T.; Kraakman, J.; Garcia Barros, R. L. Optimal operating parameters for advanced alkaline water electrolysis. Int. J. Hydrogen. Energy. 2022, 47, 34773-83.
17. Lira Garcia Barros, R.; Kraakman, J. T.; Sebregts, C.; van der Schaaf, J.; de Groot, M. T. Impact of an electrode-diaphragm gap on diffusive hydrogen crossover in alkaline water electrolysis. Int. J. Hydrogen. Energy. 2024, 49, 886-96.
19. Xu, J.; Zhong, M.; Song, N.; Wang, C.; Lu, X. General synthesis of Pt and Ni co-doped porous carbon nanofibers to boost HER performance in both acidic and alkaline solutions. Chin. Chem. Lett. 2023, 34, 107359.
20. Sun, H.; Yan, Z.; Liu, F.; Xu, W.; Cheng, F.; Chen, J. Self-supported transition-metal-based electrocatalysts for hydrogen and oxygen evolution. Adv. Mater. 2020, 32, e1806326.
21. Katsounaros, I.; Cherevko, S.; Zeradjanin, A. R.; Mayrhofer, K. J. Oxygen electrochemistry as a cornerstone for sustainable energy conversion. Angew. Chem. Int. Ed. Engl. 2014, 53, 102-21.
22. Chen, Y.; Yu, G.; Chen, W.; et al. Highly active, nonprecious electrocatalyst comprising borophene subunits for the hydrogen evolution reaction. J. Am. Chem. Soc. 2017, 139, 12370-3.
23. Zou, X.; Wu, Y.; Liu, Y.; et al. In situ generation of bifunctional, efficient Fe-based catalysts from mackinawite iron sulfide for water splitting. Chem 2018, 4, 1139-52.
24. Zhou, H.; Hou, J.; Zhang, L.; et al. In-situ fabrication of vertical heterogeneous nickel diselenide-molybdenum diselenide architectures as bifunctional overall water-splitting electrocatalyst. J. Mater. Sci. Technol. 2024, 177, 256-63.
25. Yu, L.; Zhu, Q.; Song, S.; et al. Non-noble metal-nitride based electrocatalysts for high-performance alkaline seawater electrolysis. Nat. Commun. 2019, 10, 5106.
26. Yin, H.; Jiang, L.; Liu, P.; et al. Remarkably enhanced water splitting activity of nickel foam due to simple immersion in a ferric nitrate solution. Nano. Res. 2018, 11, 3959-71.
27. Zuo, Y.; Li, J.; Yu, X.; et al. A SnS2 molecular precursor for conformal nanostructured coatings. Chem. Mater. 2020, 32, 2097-106.
28. Zuo, Y.; Liu, Y.; Li, J.; et al. In situ electrochemical oxidation of Cu2S into CuO nanowires as a durable and efficient electrocatalyst for oxygen evolution reaction. Chem. Mater. 2019, 31, 7732-43.
29. Wang, N.; Song, S.; Wu, W.; Deng, Z.; Tang, C. Bridging laboratory electrocatalysts with industrially relevant alkaline water electrolyzers. Adv. Energy. Mater. 2024, 14, 2303451.
30. Lopez M, Ustarroz J. Electrodeposition of nanostructured catalysts for electrochemical energy conversion: current trends and innovative strategies. Curr. Opin. Electrochem. 2021, 27, 100688.
31. Zuo, Y.; Bellani, S.; Ferri, M.; et al. High-performance alkaline water electrolyzers based on Ru-perturbed Cu nanoplatelets cathode. Nat. Commun. 2023, 14, 4680.
32. Xie, H.; Zhao, Z.; Liu, T.; et al. A membrane-based seawater electrolyser for hydrogen generation. Nature 2022, 612, 673-8.
33. Etzi Coller Pascuzzi, M.; Man, A. J. W.; Goryachev, A.; Hofmann, J. P.; Hensen, E. J. M. Investigation of the stability of NiFe-(oxy)hydroxide anodes in alkaline water electrolysis under industrially relevant conditions. Catal. Sci. Technol. 2020, 10, 5593-601.
34. Sun, X.; Shen, W.; Liu, H.; et al. Corrosion-resistant NiFe anode towards kilowatt-scale alkaline seawater electrolysis. Nat. Commun. 2024, 15, 10351.
35. Zhang, W.; Yang, L.; Li, Z.; et al. Regulating hydrogen/oxygen species adsorption via built-in electric field -driven electron transfer behavior at the heterointerface for efficient water splitting. Angew. Chem. Int. Ed. Engl. 2024, 63, e202400888.
36. Wan, L.; Pang, M.; Le, J.; et al. Oriented intergrowth of the catalyst layer in membrane electrode assembly for alkaline water electrolysis. Nat. Commun. 2022, 13, 7956.
37. Wan, L.; Xu, Z.; Xu, Q.; Wang, P.; Wang, B. Overall design of novel 3D-ordered MEA with drastically enhanced mass transport for alkaline electrolyzers. Energy. Environ. Sci. 2022, 15, 1882-92.
38. Mao, J.; Liang, J.; Li, Y.; et al. Electrochemical lithiation regulates the active hydrogen supply on Ru-Sn nanowires for hydrogen evolution toward the high-performing anion exchange membrane water electrolyzer. J. Am. Chem. Soc. 2025, 147, 7711-20.
39. Sillen, C.; Barendrecht, E.; Janssen, L.; Vanstralen, S. Gas bubble behaviour during water electrolysis. Int. J. Hydrogen. Energy. 1982, 7, 577-87.
40. Zeng, K.; Zhang, D. Recent progress in alkaline water electrolysis for hydrogen production and applications. Prog. Energy. Combust. Sci. 2010, 36, 307-26.
41. McCrory, C. C.; Jung, S.; Ferrer, I. M.; Chatman, S. M.; Peters, J. C.; Jaramillo, T. F. Benchmarking hydrogen evolving reaction and oxygen evolving reaction electrocatalysts for solar water splitting devices. J. Am. Chem. Soc. 2015, 137, 4347-57.
42. Zuo, Y.; Bellani, S.; Saleh, G.; et al. Ru-Cu nanoheterostructures for efficient hydrogen evolution reaction in alkaline water electrolyzers. J. Am. Chem. Soc. 2023, 145, 21419-31.
43. Li, Z.; Lin, G.; Wang, L.; et al. Seed-assisted formation of NiFe anode catalysts for anion exchange membrane water electrolysis at industrial-scale current density. Nat. Catal. 2024, 7, 944-52.
44. IRENA. Green hydrogen cost reduction: Scaling up electrolysers to meet the 1.5°C climate goal. 2020. https://www.irena.org/-/media/Files/IRENA/Agency/Publication/2020/Dec/IRENA_Green_hydrogen_cost_2020.pdf. (accessed 8 May 2025).
45. Yang, L.; Gao, L.; Shan, G.; et al. Recent progress of enhanced bubble separation in alkaline water electrolyzer. Chem. Synth. 2023, 3, 41.
Cite This Article
How to Cite
Download Citation
Export Citation File:
Type of Import
Tips on Downloading Citation
Citation Manager File Format
Type of Import
Direct Import: When the Direct Import option is selected (the default state), a dialogue box will give you the option to Save or Open the downloaded citation data. Choosing Open will either launch your citation manager or give you a choice of applications with which to use the metadata. The Save option saves the file locally for later use.
Indirect Import: When the Indirect Import option is selected, the metadata is displayed and may be copied and pasted as needed.
About This Article
Copyright
Data & Comments
Data
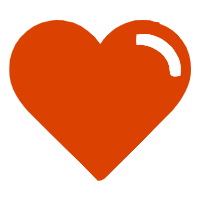
Comments
Comments must be written in English. Spam, offensive content, impersonation, and private information will not be permitted. If any comment is reported and identified as inappropriate content by OAE staff, the comment will be removed without notice. If you have any queries or need any help, please contact us at [email protected].