Sustainable synthesis of Fe-MOR zeolite for efficient capture of CO2
Abstract
Selective adsorption of carbon dioxide (CO2) is significant for carbon neutrality, where searching for efficient CO2 adsorbents is very important. In addition, coal fly ash (CFA) is one of the largest industrial solid wastes with environmental damages, where conversion of the wastes into costly functional materials is attractive. This work showed sustainable synthesis of Fe-containing mordenite (Fe-MOR) zeolite from the CFA waste under solvent-free conditions, and this zeolite is an efficient capturer for CO2 in the mixture of CO2/N2 (15/85, v/v), giving adsorption capacity of 2.07 mmol/g and separation coefficient of 58.9 at 298 K. Very interestingly, the capture of CO2 in the mixture of CO2/N2 (15/85, v/v) is recyclable. This work not only solved the accumulation and pollution of CFA but also prepared a highly efficient adsorbent of Fe-MOR zeolite, which would open a door for utilizing environmentally unfriendly solid wastes as value-added functional materials in the future.
Keywords
INTRODUCTION
The rapid increase of greenhouse gases, particularly carbon dioxide (CO2), is one of the global problems that could increase the likelihood and severity of natural disasters such as wildfires, heatwaves, and droughts[1-8]. Since renewable energy resources are still being developed and thus fossil fuels will remain the dominant energy source for a long time, it is crucial to efficiently curb CO2 emissions[9-17]. At present, great efforts have been made in developing efficient technologies for capturing CO2[18-22]. Among them, it is generally believed that solid porous adsorbents with low cost, high capacity and selectivity of CO2 are critical.
Zeolites, as a class of typically solid porous adsorbents with ordered micropores, are widely employed in fields such as catalysis, ion exchange, adsorption, and separation due to their high surface areas, large micropore volumes, and good stabilities[23-26]. In recent years, capturing CO2 by zeolites has become a hot topic due to their excellent stability for zeolite frameworks[3,4,18,27-32]. For example, Zhou et al. first reported that Fe-containing mordenite (Fe-MOR) zeolite synthesized from the “acid co-hydrolysis route” had narrowed microchannels, which was efficient for CO2 adsorption and separation[33]. However, this method, which uses tetraethyl orthosilicate (TEOS) as a starting raw material and generates wastewater in the hydrothermal synthesis, incurs relatively high costs. In addition, conventional synthesis of Fe-MOR zeolite failed to obtain these narrowed microchannels under hydrothermal conditions due to the formation of aggregated Fe species. Thus, it is highly desirable to develop a simple and sustainable route for synthesizing Fe-MOR zeolite with high capacity and selectivity of CO2.
Recently, we developed a simple and sustainable route for solvent-free synthesis of zeolites, which completely avoided using water solvents[34-38], where the aggregation of Fe species was effectively hindered[39]. Therefore, it offers the possibility of preparing Fe-containing zeolites without aggregation of Fe species under solvent-free conditions. Considering that coal fly ash (CFA), mainly containing silica, alumina, and iron oxides, one of the largest industrial solid wastes emitted from the combustion of coal powder, is environmentally unfriendly[40-45], it is really sustainable for the conversion of the CFA waste into highly efficient adsorbent of Fe-MOR zeolite under solvent-free conditions.
This work, for the first time, showed a simple and sustainable synthesis of Fe-MOR zeolite from CFA waste under solvent-free conditions. As expected, the Fe-MOR zeolite exhibited good adsorption capacity for CO2 (2.07 mmol/g at 298 K), high separation coefficient (58.9 at 298 K), and excellent recyclability. These features, plus sustainable synthesis, are helpful for potential applications of this zeolite in the future.
EXPERIMENTAL
Solvent-free synthesis of Fe-MOR zeolite from CFA
Experimental sections, including materials and characterizations [Supplementary Materials].
For the solvent-free synthesis of Fe-MOR zeolite from CFA (Fe-MOR-CFA), the CFA and NaOH powder were mixed at a mass ratio of 1:1.2, calcined at 800 °C for 2 h, cooled to room temperature, and ground into a fine powder at room temperature[37]. The chemical composition of the CFA and the activated CFA by alkali fusion were measured with X-ray fluorescence (XRF) [Supplementary Table 1].
As a typical run for the solvent-free synthesis of Fe-MOR zeolite, 0.534 g of CFA fine powder, 0.879 g of solid silica, and 0.1 g of MOR zeolite as seeds were ground for 10 min. Subsequently, the obtained power was poured into an autoclave, and 1.2 g of H2O was added. The product was finally crystallized at 175 °C for 10 h and designated as Fe-MOR-CFA. The yield of the Fe-MOR-CFA zeolite is approximately 90%. The Si/Al ratio and Fe content of the Fe-MOR-CFA zeolite were 6.9 and 0.77 wt.% by inductively coupled plasma optical emission spectroscopy (ICP-OES) measurements, which was consistent with the result of XRF
For comparison, Fe-MOR zeolite was synthesized from an “acidic co-hydrolysis route” accordingly[33], which was designated as Fe-MOR-ACH. The Si/Al ratio and Fe content of the Fe-MOR-ACH zeolite were 6.5 and 0.73 wt.% by ICP-OES measurements.
Gas adsorption
Adsorption data for CO2 and N2 at 273 and 298 K were carried out in the Physical Adsorption Analyzer [Beishide Instrument Technology (Beijing) Co., Ltd., China]. Adsorption selectivity was based on ideal adsorbed solution theory (IAST)[33] for CO2/N2 (15/85, v/v), determined by:
Where x and y were the mole fraction of absorbate in the adsorption and gas phases, respectively. The subscripts i and j were on behalf of CO2 and N2.
Isosteric heat of adsorption[46] was calculated from the Clausius-Clapeyron equation to predict the interactions between the adsorbate and the adsorbent, using the CO2 adsorption-desorption at 273 and
Where P was the pressure, R was the ideal gas constant, 8.314 kJ/mol, C was the constant, T was the temperature, K, and ∆Hs was calculated from slopes of plots of In Pvs. 1/T of fixed loading.
The recyclability of single-component CO2 adsorption was obtained on the Weight Method Vacuum Steam Absorption [Beishide Instrument Technology (Beijing) Co., Ltd., China].
CO2 dynamic adsorption profiles for sole composition at 298 K were measured on the Gravity Vacuum Vapor Sorption Test Report [Beishide Instrument Technology (Beijing) Co., Ltd., China]. Firstly, 0.06~
The CO2/N2 breakthrough separations were performed in a multi-component adsorption breakthrough curve analyzer [Beishide Instrument Technology (Beijing) Co., Ltd., China] at 298 K. Firstly, 0.4~1.0 g of as-synthesized powder was placed in the quartz tubing (6 mm diameter) and then purged with He flow (5 mL/min) for 2 h at 573 K. The mixture (CO2/N2: 15/85, v/v) flows without water condition, with water condition and the presence of SO2 (1,000 ppm) were then introduced at 3.0 mL/min at 298 K. The flow rates of all gas mixtures were regulated by mass flow controllers; the humidity was controlled and detected using a multi-component adsorption breakthrough curve analyzer, and the CO2 and N2 concentrations from the adsorbent bed were continuously monitored with a gas analytical mass spectrometer. Besides, the zeolite was regenerated in situ in the column with a 5 mL/min flow at 573 K for 2 h.
RESULTS AND DISCUSSION
Figure 1 displayed the schematic representation of solvent-free synthesis of Fe-MOR-CFA zeolite. Figure 2 showed the X-ray diffraction (XRD) pattern, scanning electron microscopy (SEM) image, N2 sorption isotherms, and 27Al magic-angle spinning (MAS) nuclear magnetic resonance (NMR) spectrum of Fe-MOR-CFA zeolite. The XRD pattern of the Fe-MOR-CFA zeolite [Figure 2A] displayed peaks with good resolution in the range of 5°-40°, which are well consistent with those of the simulated MOR structure
Figure 1. Schematic representation of solvent-free synthesis of Fe-MOR-CFA zeolite from coal fly ash. Fe-MOR-CFA: Fe-containing mordenite zeolite from coal fly ash.
Figure 2. (A) XRD pattern; (B) SEM image; (C) N2 sorption isotherms; and (D) 27Al MAS NMR spectrum of the Fe-MOR-CFA zeolite. XRD: X-ray diffraction; SEM: scanning electron microscopy; MAS: 27Al magic-angle spinning; NMR: nuclear magnetic resonance; Fe-MOR-CFA: Fe-containing mordenite zeolite from coal fly ash.
Ultraviolet-visible (UV-vis) and electron spin resonance (ESR) techniques were used to investigate the chemical state of Fe species. UV-vis spectra of the Fe-MOR-CFA and Fe-MOR-ACH zeolites displayed two monomer bands centered at 210-220 nm and 250-265 nm, respectively [Figure 3A]. The 210-220 nm band was assigned to tetrahedrally coordinated Fe3+ ions, while the 250-265 nm band was attributed to isolated Fe3+ ions with higher coordination[47,48]. Notably, no peaks between 300 and 400 nm in the Fe-MOR-CFA and Fe-MOR-ACH zeolites were associated with oligonuclear FexOy clusters[49]. Their ESR spectra [Figure 3B] exhibited the signal at g = 4.3 associated with isolated Fe3+ ions with tetrahedral coordination and the signal at g = 2.0 related to Fe species inside microporous channels[33,50]. The above results revealed that the aggregated Fe species were excluded in these zeolites, confirming the feasibility of solvent-free synthesis of Fe-MOR-CFA zeolite from CFA.
Figure 3. (A) UV-vis and (B) ESR spectra of Fe-MOR-CFA and Fe-MOR-ACH zeolites. UV-vis: Ultraviolet-visible; ESR: electron spin resonance; Fe-MOR-CFA: Fe-containing mordenite zeolite from coal fly ash; Fe-MOR-ACH: Fe-containing mordenite from acidic co-hydrolysis route.
Supplementary Figures 6 and 7 exhibited the XRD patterns and SEM images of the Fe-MOR-CFA zeolite samples with different ratios of the MOR zeolite seeds to SiO2 in the mixture of initial raw materials from 0 to 0.20. Notably, when no MOR zeolite seeds were added (a ratio of 0), the crystal size of the Fe-MOR-CFA zeolite was very large (with a diameter larger than 3 μm). However, when the zeolite seeds were included, the crystal sizes significantly decreased (with a diameter of less than 0.5 μm). These results suggested that a suitable ratio of the MOR zeolite seeds to SiO2 is significant for adjusting zeolite crystal sizes.
Supplementary Figure 8 showed the effect of the Fe-MOR-CFA zeolite on the Na2O/SiO2 ratios in the mixture of initial raw materials. Pure Fe-MOR-CFA zeolite could be obtained when the ratios of Na2O/SiO2 were adjusted from 0.22 to 0.26 [Supplementary Figure 8A and B]. When the ratios were higher than 0.29, the ANA phase was observed in the zeolite product [Supplementary Figure 8C]. Therefore, the Na2O/SiO2 ratios should be seriously regulated in the solvent-free synthesis of the Fe-MOR-CFA zeolite.
Figure 4 showed the crystallization process of the Fe-MOR-CFA zeolite explored by XRD and SEM techniques. Firstly, very weak peaks of MOR zeolite before crystallization were observed, which was related to the MOR zeolite seeds in the mixture of initial raw materials [Figure 4A(a)]. A series of peaks associated with MOR structure appeared when the crystallization time was 4 h [Figure 4A(b)]. Meanwhile, a few Fe-MOR-CFA zeolite crystals could be observed obviously from the SEM image [Figure 4B(b)], which was extremely consistent with the XRD pattern. The zeolite crystals formed quickly from 4 to 6 h, as observed from both XRD patterns and SEM images [Figure 4A(c) and B(c)]. The XRD intensity of the obtained samples did not change after the crystallization for 10 h, meaning a full crystallization [Figure 4A(e)]. Accordingly, more Fe-MOR-CFA zeolite crystals could be attained [Figure 4B(e)]. The dependence of the Fe-MOR-CFA zeolite crystallinity on crystallization time was shown in Supplementary Figure 9.
Figure 4. (A) XRD patterns and (B) SEM images of the Fe-MOR-CFA zeolite crystallized at (a) 0, (b) 4, (c) 6, (d) 8, (e) 10, and (f) 12 h, respectively. XRD: X-ray diffraction; SEM: scanning electron microscopy; Fe-MOR-CFA: Fe-containing mordenite zeolite from coal fly ash.
Quantitative porosity was analyzed using N2 and Ar sorption experiments. Both the Fe-MOR-CFA and Fe-MOR-ACH zeolites exhibited extremely low N2 and Ar uptake [Figure 5, Supplementary Figures 10 and 11, Supplementary Table 2], suggesting that both with narrowed orifices retard larger N2 (3.64 Å) and even Ar (3.4 Å)[33]. In contrast, both samples enable CO2 to enter with a small kinetic diameter (3.3 Å), as supported by CO2 sorption isotherms of the samples [Figure 5]. The CO2 adsorption capacities of the Fe-MOR-CFA zeolite at 273 and 298 K were 3.31 mmol/g and 2.93 mmol/g, respectively, which is comparable with those (3.45 and 3.09 mmol/g) of the Fe-MOR-ACH zeolite.
Figure 5. CO2 and N2 sorption isotherms of (A) Fe-MOR-CFA zeolite and (B) Fe-MOR-ACH zeolite at 273 and 298 K. Fe-MOR-CFA: Fe-containing mordenite zeolite from coal fly ash; Fe-MOR-ACH: Fe-containing mordenite from acidic co-hydrolysis route.
Figure 6A showed adsorption selectivity of CO2/N2 (15/85, v/v) calculated by single-component CO2 and N2 sorption isotherms at 273 and 298 K for Fe-MOR-CFA and Fe-MOR-ACH zeolites, giving excellent separation ability. Isosteric heats of CO2 adsorption (Qst) as a function of CO2 uptakes were analyzed [Figure 6B], giving similar values for these two zeolites. In addition, they have similar CO2 adsorption kinetics [Supplementary Figures 12 and 13], meaning similar electrostatic interaction between the iron species and CO2[33,51]. After recycling ten times, no loss for CO2 uptake at 298 K was observed for the Fe-MOR-CFA zeolite [Figure 6C], indicating its recyclability for adsorption and desorption of CO2. Furthermore, the separation efficiency of the two zeolites was evaluated by the column breakthrough separations for the mixture of CO2/N2 (15/85, v/v) at 298 K and atmospheric pressure. As shown in Figure 6D, N2 breakthrough occurred immediately, while the CO2 retaining time of Fe-MOR-CFA and Fe-MOR-ACH zeolites were 100.4 and 97.0 min/g, respectively, and their CO2 adsorption capacities were 2.07 and 2.02 mmol/g, respectively. From the breakthrough curve, the separation coefficient for Fe-MOR-CFA and Fe-MOR-ACH zeolites were calculated at 58.9 and 53.5 for CO2/N2 (15/85, v/v), respectively, where the Fe-MOR-CFA zeolite exhibited the separation coefficient even better than Fe-MOR-ACH zeolite, one of the best zeolite adsorbents of CO2 yet. The better performance might be associated with K+ and Ca2+ in the raw materials (CFA)[52]. In addition, the column breakthrough separations of the Fe-MOR-CFA zeolite with a relative humidity (RH) of 60% and the presence of SO2 (1,000 ppm) were performed at 298 K
Figure 6. (A) IAST prediction of CO2/N2 (15/85, v/v) selectivities on Fe-MOR-CFA zeolite and Fe-MOR-ACH zeolite at 273 and 298 K; (B) Isosteric heats (Qst) as a function of CO2 uptakes on Fe-MOR-CFA zeolite and Fe-MOR-ACH zeolite; (C) CO2 adsorption isotherms of Fe-MOR-CFA zeolite for ten times at 298 K; (D) Experimental column breakthrough curves for CO2/N2 (15/85, v/v) separations on Fe-MOR-CFA zeolite and Fe-MOR-ACH zeolite at 298 K. IAST: Ideal adsorbed solution theory; Fe-MOR-CFA: Fe-containing mordenite zeolite from coal fly ash; Fe-MOR-ACH: Fe-containing mordenite from acidic co-hydrolysis route.
Finally, the solvent-free synthesis of the Fe-MOR-CFA zeolite was scaled up to 100-200 mL autoclaves
CONCLUSIONS
In summary, it is successful for solvent-free synthesis of Fe-MOR-CFA zeolite with high yields using solid waste of CFA as aluminum, silicon, and iron sources. This route not only consumes solid waste of CFA but also produces value-added CO2 adsorbents with high adsorption capacity, excellent separation coefficient, and good recyclability. The sustainable synthesis plus excellent features for capturing CO2 could provide a good opportunity for potential applications of the Fe-MOR-CFA zeolite in the future.
DECLARATIONS
Acknowledgments
We sincerely thank all the team members who participated in this study.
Authors’ contributions
Zeolite preparation, characterization, and the draft manuscript: Liu P
Discussion on the results: Yan K, Wang L
Design of the study, data analysis, and manuscript writing: Wu Q, Xiao FS
Availability of data and materials
Not applicable.
Financial support and sponsorship
This work was supported by the National Key Research and Development Program of China (2022YFA1503602), Shanxi-Zheda Institute of Advanced Materials and Chemical Engineering (2021SZ-AT003), and the National Natural Science Foundation of China (22288101 and 22172141).
Conflicts of interest
Wang L is the Junior Editorial Board Member of Chemical Synthesis. Both Wang L and Xiao FS are the guest editors of the Special Issue of “Zeolite for Sustainable Catalysis”, while the other authors have declared that they have no conflicts of interest.
Ethical approval and consent to participate
Not applicable.
Consent for publication
Not applicable.
Copyright
© The Author(s) 2024.
Supplementary Materials
REFERENCES
1. Varghese AM, Karanikolos GN. CO2 capture adsorbents functionalized by amine - bearing polymers: a review. Int J Greenh Gas Con 2020;96:103005.
2. Singh G, Lee J, Karakoti A, et al. Emerging trends in porous materials for CO2 capture and conversion. Chem Soc Rev 2020;49:4360-404.
3. Siegelman RL, Kim EJ, Long JR. Porous materials for carbon dioxide separations. Nat Mater 2021;20:1060-72.
4. Osman AI, Hefny M, Abdel Maksoud MIA, Elgarahy AM, Rooney DW. Recent advances in carbon capture storage and utilisation technologies: a review. Environ Chem Lett 2021;19:797-849.
5. Liu X, Wang M, Zhou C, et al. Selective transformation of carbon dioxide into lower olefins with a bifunctional catalyst composed of ZnGa2O4 and SAPO-34. Chem Commun 2018;54:140-3.
6. Lashaki M, Khiavi S, Sayari A. Stability of amine-functionalized CO2 adsorbents: a multifaceted puzzle. Chem Soc Rev 2019;48:3320-405.
7. Kolle JM, Fayaz M, Sayari A. Understanding the effect of water on CO2 adsorption. Chem Rev 2021;121:7280-345.
8. Hu Z, Wang Y, Shah BB, Zhao D. CO2 capture in metal–organic framework adsorbents: an engineering perspective. Adv Sustain Syst 2019;3:1800080.
9. Song C, Liu Q, Deng S, Li H, Kitamura Y. Cryogenic-based CO2 capture technologies: state-of-the-art developments and current challenges. Renew Sustain Energy Rev 2019;101:265-78.
10. Shehzad N, Tahir M, Johari K, Murugesan T, Hussain M. A critical review on TiO2 based photocatalytic CO2 reduction system: strategies to improve efficiency. J CO2 Util 2018;26:98-122.
11. Nikoloudakis E, López-Duarte I, Charalambidis G, Ladomenou K, Ince M, Coutsolelos AG. Porphyrins and phthalocyanines as biomimetic tools for photocatalytic H2 production and CO2 reduction. Chem Soc Rev 2022;51:6965-7045.
12. Muhammed NS, Haq B, Al Shehri D, Al-ahmed A, Rahman MM, Zaman E. A review on underground hydrogen storage: insight into geological sites, influencing factors and future outlook. Energy Rep 2022;8:461-99.
13. Fan WK, Tahir M. Recent advances on cobalt metal organic frameworks (MOFs) for photocatalytic CO2 reduction to renewable energy and fuels: a review on current progress and future directions. Energ Convers Manage 2022;253:115180.
14. Du Z, Liu C, Zhai J, et al. A review of hydrogen purification technologies for fuel cell vehicles. Catalysts 2021;11:393.
15. Dissanayake PD, You S, Igalavithana AD, et al. Biochar-based adsorbents for carbon dioxide capture: a critical review. Renew Sustain Energy Rev 2020;119:109582.
16. Chakraborty R, K V, Pradhan M, Nayak AK. Recent advancement of biomass-derived porous carbon based materials for energy and environmental remediation applications. J Mater Chem A 2022;10:6965-7005.
17. Chai Y, Gao N, Wang M, Wu C. H2 production from co-pyrolysis/gasification of waste plastics and biomass under novel catalyst Ni-CaO-C. Chem Eng J 2020;382:122947.
18. Tawalbeh M, Muhammad Nauman Javed R, Al-othman A, Almomani F. The novel contribution of non-noble metal catalysts for intensified carbon dioxide hydrogenation: recent challenges and opportunities. Energ Convers Manage 2023;279:116755.
19. Pal S, Krishna R, Das MC. Highly scalable acid-base resistant Cu-Prussian blue metal-organic framework for C2H2/C2H4, biogas, and flue gas separations. Chem Eng J 2023;460:141795.
20. Jiang L, Liu W, Wang R, et al. Sorption direct air capture with CO2 utilization. Prog Energ Combust 2023;95:101069.
21. Hu Y, Jiang Y, Li J, et al. New-generation anion-pillared metal–organic frameworks with customized cages for highly efficient CO2 capture. Adv Funct Mater 2023;33:2213915.
22. Ding H, Zhang Y, Dong Y, Wen C, Yang Y. High-pressure supersonic carbon dioxide (CO2) separation benefiting carbon capture, utilisation and storage (CCUS) technology. Appl Energy 2023;339:120975.
23. Zhou H, Yi X, Hui Y, et al. Isolated boron in zeolite for oxidative dehydrogenation of propane. Science 2021;372:76-80.
24. Xiong H, Liu Z, Chen X, et al. In situ imaging of the sorption-induced subcell topological flexibility of a rigid zeolite framework. Science 2022;376:491-6.
25. Tai W, Dai W, Wu G, Li L. A simple strategy for synthesis of b-axis-oriented MFI zeolite macro-nanosheets. Chem Synth 2023;3:38.
26. Yuan K, Jia X, Wang S, et al. Effect of crystal size of ZSM-11 zeolite on the catalytic performance and reaction route in methanol to olefins. Chem Synth 2023;4:31.
27. Sun Y, Lang Q, Fu G, et al. Highly hydrophobic zeolite ZSM-8 with perfect framework structure obtained in a strongly acidic medium. Micropor Mesopor Mat 2024;363:112839.
28. Jalali A, Ahmadpour A, Ghahramaninezhad M, Yasari E. Hierarchical nanocomposites derived from UiO-66 framework and zeolite for enhanced CO2 adsorption. J Environ Chem Eng 2023;11:111294.
29. Najafi AM, Khorasheh F, Soltanali S, Ghassabzadeh H. Equilibrium and kinetic insights into the comprehensive investigation of CO2, CH4, and N2 adsorption on cation-exchanged X and Y faujasite zeolites. Langmuir 2023;39:15535-46.
30. Kencana KS, Choi HJ, Kemp KC, Hong SB. Enhancing the CO2 adsorption kinetics on Na-RHO and Cs-MER zeolites by NH4F/H2O2 etching induced mesoporosity. Chem Eng J 2023;451:138520.
31. Jiang Y, Zhou W, He N, Yan S, Chen S, Liu J. Preparation of shaped binder-free SSZ-13 zeolite and its application in CO2 adsorption and catalysis. ChemCatChem 2022;14:e202200795.
32. Fu D, Park Y, Davis ME. Confinement effects facilitate low-concentration carbon dioxide capture with zeolites. Proc Natl Acad Sci U S A 2022;119:e2211544119.
33. Zhou Y, Zhang J, Wang L, et al. Self-assembled iron-containing mordenite monolith for carbon dioxide sieving. Science 2021;373:315-20.
34. Wu Q, Meng X, Gao X, Xiao FS. Solvent-free synthesis of zeolites: mechanism and utility. Acc Chem Res 2018;51:1396-403.
35. Wu Q, Ma Y, Wang S, Meng X, Xiao F. 110th Anniversary: sustainable synthesis of zeolites: from fundamental research to industrial production. Ind Eng Chem Res 2019;58:11653-8.
36. Ma Y, Han S, Wu Q, et al. One-pot fabrication of metal-zeolite catalysts from a combination of solvent-free and sodium-free routes. Catal Today 2021;371:64-8.
37. Liu P, Wu Q, Yan K, Wang L, Xiao FS. Solvent-free synthesis of FAU zeolite from coal fly ash. Dalton Trans 2022;52:24-8.
38. Kan X, Xiao S, Zheng Y, et al. Sustainable synthesis of ordered mesoporous materials without additional solvents. J Colloid Interface Sci 2022;619:116-22.
39. Ren L, Wu Q, Yang C, et al. Solvent-free synthesis of zeolites from solid raw materials. J Am Chem Soc 2012;134:15173-6.
40. Qian B, Zhang J, Zhou S, et al. Synthesis of (111) facet-engineered MgO nanosheet from coal fly ash and its superior catalytic performance for high-temperature water gas shift reaction. Appl Catal A Gen 2021;618:118132.
41. Park S, Kim M, Lim Y, et al. Characterization of rare earth elements present in coal ash by sequential extraction. J Hazard Mater 2021;402:123760.
42. Guan Q, Hu X, Wu D, Shang X, Ye C, Kong H. Phosphate removal in marine electrolytes by zeolite synthesized from coal fly ash. Fuel 2009;88:1643-9.
43. Yamaura M, Fungaro DA. Synthesis and characterization of magnetic adsorbent prepared by magnetite nanoparticles and zeolite from coal fly ash. J Mater Sci 2013;48:5093-101.
44. Tauanov Z, Tsakiridis PE, Mikhalovsky SV, Inglezakis VJ. Synthetic coal fly ash-derived zeolites doped with silver nanoparticles for mercury (II) removal from water. J Environ Manage 2018;224:164-71.
45. Bukhari SS, Behin J, Kazemian H, Rohani S. Conversion of coal fly ash to zeolite utilizing microwave and ultrasound energies: a review. Fuel 2015;140:250-66.
46. You J, Wang H, Xiao T, Wu X, Zhang L, Lu C. Introducing high concentration of hexafluorosilicate anions into an ultra-microporous MOF for highly efficient C2H2/CO2 and C2H2/C2H4 separation. Chem Eng J 2023;477:147001.
47. Yasumura S, Qian Y, Kato T, et al. In situ/operando spectroscopic studies on the NH3–SCR mechanism over Fe–zeolites. ACS Catal 2022;12:9983-93.
48. Romero-sáez M, Divakar D, Aranzabal A, González-velasco J, González-marcos J. Catalytic oxidation of trichloroethylene over Fe-ZSM-5: influence of the preparation method on the iron species and the catalytic behavior. Appl Catal B Environ 2016;180:210-8.
49. Zeng J, Chen S, Fan Z, Wang C, Chang H, Li J. Simultaneous selective catalytic reduction of NO and N2O by NH3 over Fe-zeolite catalysts. Ind Eng Chem Res 2020;59:19500-9.
50. Lari GM, Mondelli C, Pérez-ramı́rez J. Gas-phase oxidation of glycerol to dihydroxyacetone over tailored iron zeolites. ACS Catal 2015;5:1453-61.
51. Liang L, Liu C, Jiang F, et al. Carbon dioxide capture and conversion by an acid-base resistant metal-organic framework. Nat Commun 2017;8:1233.
Cite This Article
Export citation file: BibTeX | EndNote | RIS
OAE Style
Liu P, Wu Q, Yan K, Wang L, Xiao FS. Sustainable synthesis of Fe-MOR zeolite for efficient capture of CO2. Chem Synth 2024;4:31. http://dx.doi.org/10.20517/cs.2023.70
AMA Style
Liu P, Wu Q, Yan K, Wang L, Xiao FS. Sustainable synthesis of Fe-MOR zeolite for efficient capture of CO2. Chemical Synthesis. 2024; 4(3): 31. http://dx.doi.org/10.20517/cs.2023.70
Chicago/Turabian Style
Pei Liu, Qinming Wu, Keping Yan, Liang Wang, Feng-Shou Xiao. 2024. "Sustainable synthesis of Fe-MOR zeolite for efficient capture of CO2" Chemical Synthesis. 4, no.3: 31. http://dx.doi.org/10.20517/cs.2023.70
ACS Style
Liu, P.; Wu Q.; Yan K.; Wang L.; Xiao F.S. Sustainable synthesis of Fe-MOR zeolite for efficient capture of CO2. Chem. Synth. 2024, 4, 31. http://dx.doi.org/10.20517/cs.2023.70
About This Article
Special Issue
Copyright
Author Biographies
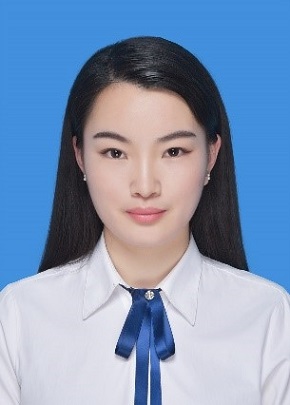
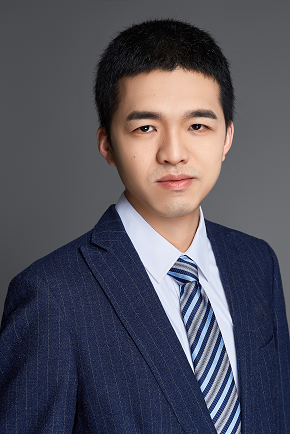
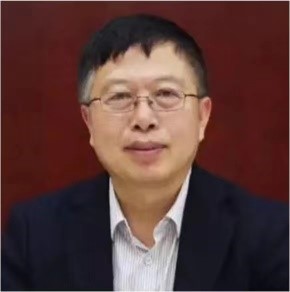
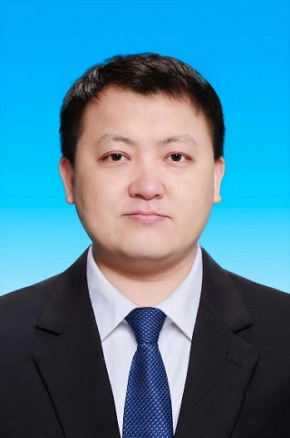
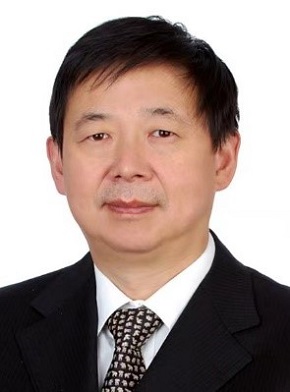
Data & Comments
Data
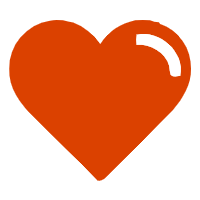
Comments
Comments must be written in English. Spam, offensive content, impersonation, and private information will not be permitted. If any comment is reported and identified as inappropriate content by OAE staff, the comment will be removed without notice. If you have any queries or need any help, please contact us at support@oaepublish.com.