Recent progress of waste plastic upcycling based on multifunctional zeolite catalysts
Abstract
The chemical upcycling method is a promising strategy to alleviate the pollution problem of waste plastics by tapping into their intrinsic value and converting them into high value-added products. Zeolite-based catalysts are one of the surprising and efficient classes of thermocatalytic materials that have recently attracted considerable attention for waste plastic upcycling. They are designed for targeted applications with a wide range of adjustable acidic sites, multiple pore structures, and synergistic interactions with surface metals. In this review, we categorize plastics being converted into different high-value products and introduce the role of zeolite-based catalysts in the thermal upcycling of plastics. The structure-performance relationships of zeolite-based catalysts in catalytic reactions are discussed in depth. Finally, the future development of these multifunctional catalysts applied to the upcycling of plastics is outlined.
Keywords
INTRODUCTION
Annual global production of plastics has exceeded 460 million tons, but only about 9% are recycled[1,2]. The large amount of plastic waste generated accumulates in landfills and has leaked into the natural environment, especially the marine ecosystem, threatening the survival of nature’s creatures[3-5]. Even microplastics have entered the human body through the biological chain, whose potential impact cannot be ignored[6,7]. Projections suggest an accumulation of approximately 12 billion tons of plastic waste in nature by 2050, should the improper management of plastic waste persist[8,9]. Efficiently and rationally managing these waste plastics is an urgent global challenge. Conventional recycling strategies, such as incineration, landfill or mechanical recycling, are generally downcycling methods, and the process is energy-intensive and inefficient[10,11]. In contrast, the chemical upcycling method taps into the intrinsic value of plastics as carbon-based resources and recycles them into high-value products such as monomers, fuel oils, and chemicals[12-15]. It not only alleviates the pollution problem of waste plastics but also significantly increases the economic value of the product and realizes sustainable development[16,17]. Consequently, it is one of the key promising means of addressing plastic pollution.
In the chemical upcycling process, thermocatalytic strategies have been proposed to convert plastic polymers with greater efficiency and selectivity by activating high-energy bonds in the polymer backbone[18-20]. Zeolite-based catalysts are an important class of heterogeneous catalysts for the thermocatalytic degradation of plastics[21-23]. As crystalline porous materials, zeolites are characterized by outstanding thermal stability, unique pore structure, and tunable elemental composition and acidity, extensively employed in the petrochemistry field[24,25]. When they cooperate with metals, the metal active sites can be well dispersed in various forms (single atoms, ions, clusters, nanoparticles, etc.) in their skeleton, pores, or outer surface[26,27]. Once the polymer diffuses into the interior of the catalyst, it interacts with active sites on the catalyst surface. These active sites can be metal sites or acidic centers of zeolites, which can trigger chemical reactions on plastic molecules, such as cleavage, oxidation, hydrogenation, etc., thus promoting the degradation of plastics[28]. The structure of zeolite-based catalysts (including the type and dispersion of metal, acidity and pore structure of zeolite, etc.) can be rationally designed to maximize the interaction between metal and zeolite, thus enhancing the synergistic effect[22,29,30]. As a result, further excellent catalytic activity, selectivity and stability in catalytic reactions are demonstrated.
In recent years, plenty of articles have been reporting remarkable progress in the catalytic conversion of various plastics by the zeolite-based catalysts, such as the conversion of polyolefins or polyesters into value-added products (aromatics, gasoline, diesel, etc.), which have been evidenced to have potential applications
WASTE PLASTIC UPCYCLING TO LIQUID FUEL
Recycling waste plastics into liquid fuels is a unique and practical technology for producing alternative energy sources. Jahirul et al. analyzed and evaluated pyrolysis oils from high-density polyethylene (HDPE) and polypropylene (PP) containing gasoline with a calorific value in the range of 42-45 MJ/kg and diesel with the cetane index of 60 and 44, respectively, which are within the approved range for automotive fuel[36,37]. Studies have shown that if the world’s waste plastics were all upcycled into fuel, about 3.5 billion barrels of oil could be saved annually[38,39]. Plastics show great potential for fuel applications, but low yields, the presence of waxes, and the high energy consumption of the production process are still factors that prevent their practical application. The introduction of zeolite-based catalysts, which can further increase oil production and optimize oil composition, has attracted the attention of researchers.
Polyolefin plastic upcycling
Catalytic cracking to produce liquid fuels
For polyolefin plastics, the catalytic cracking reaction is a process dominated by the carbonyl ion mechanism[40]. In this process, the polymer chain is first adsorbed onto the Brønsted acid sites (BASs) of the catalyst and protonated to form a carbonium ion intermediate, followed by β-cleavage to produce alkanes and carbonium ions[41]. After continuous attack and cleavage, the molecular weight of the polymer chain decreases. Additionally, the intermediate carbonium ion can be rearranged through hydrogen transfer, forming isomers[42]. In contrast to pyrolysis, introducing a catalyst to catalytic cracking can markedly reduce the temperature of the reaction, decrease its duration, and result in a limited distribution of hydrocarbons[21,22,39,43]. The catalytic performance is mainly affected by the acidity and pore structure of the catalyst. Wherein, the acid sites are responsible for cleavage, and the pore structure influences the contact of the acid sites with the substrate molecules and controls the product distribution.
Fuel standards have been set in countries around the world. These include specific characteristics of oils such as composition, volatility and octane number. Researchers are working to find suitable catalysts for degrading plastics to produce oils with ratios of saturated hydrocarbons, olefins and aromatics close to those of conventionally produced oils. The performance of microporous zeolites such as ZSM-5 and HY for catalytic cracking has been reported in the literature[44-46]. Limited by their acidity and microporous structure, they are more likely to produce light or aromatic hydrocarbons. In order to generate liquid fuels in higher yields, mesoporous silica-aluminate was introduced to enhance the accessibility of the acid sites by allowing the polymer chains to enter the pores directly. Unfortunately, they cannot exhibit shape selectivity[47]. Ratnasari et al. achieved efficient conversion of waste plastics by staged catalysis using
Catalytic hydrocracking to produce liquid fuels
The liquid oil produced by catalytic cracking over zeolite-based catalysts contains olefins, which have double bonds that are unsuitable for fuels for engine combustion. When hydrogenation sites are introduced, olefins are instantaneously hydrogenated to a saturated liquid product that can be used directly as fuels[52-54]. Additionally, the octane number of oil products is an important criterion for evaluating the quality of oil products. In general, the more branched the hydrocarbons, the higher the octane number.
Hydrogenolysis refers to the mechanism by which C−C bond cleavage and hydrogenation occur on a monofunctional metal catalyst. Usually, metal-dominated hydrogenolysis requires longer reaction times and higher reaction temperatures. Pt/SrTiO3 can be completely converted to polyethylene (PE) by continuous hydrogenolysis for 96 h at 170 psi H2, 300 °C to obtain lubricating oil or wax[55]. The catalyst mSiO2/Pt/SiO2 at 1.38 MPa H2 and 250 to 300 °C for 24 h gives a 38% yield of C12-C16[56]. Ru has generally higher hydrogenolytic activity than Pt. High-yield C5-C30 liquid can be obtained by Ru/C hydrogenolysis of polyolefins under relatively mild conditions (200-250 °C, 20-50 bar H2)[57]. Under similar reaction conditions, Ru/CeO2 yielded liquid oil C5-C21 in 77% yield[58]. In addition, Ru also showed significant hydrogenolysis activity on TiO2, Nb2O5 and other supports[59,60]. However, the strong interaction between polymer and catalyst during hydrogenolysis can easily lead to excessive cracking and produce a large amount of light gas with low value. Therefore, the hydrogenolysis products tend to be widely distributed. In contrast to the slower monofunctional hydrogenolysis, catalysis between metal and acid sites via bifunctional tandem is essential for rapid polymer conversion. The pore selectivity of zeolites favors narrow product distribution. Secondly, the hydrogenolysis catalyst has no isomerization ability, resulting in products that are mostly linear hydrocarbons. The acidic site of the zeolite is useful for obtaining the product with a high degree of isomerization and improving the quality of the oil. Consequently, hydrocracking is a key process for converting waste polyolefins into value-added fuels. The distribution of liquid oil products can be altered by specifically designing the active sites of the catalysts [Figure 2A][61].
Figure 2. (A) Overall reaction scheme for the hydrocracking of octane to paraffins with olefin intermediates diffusing between the metal and Brønsted acid sites; (B) Proposed isomerization cycle in the hydrocracking of LDPE (top) and effect of the metal-acid balance on the structure of the residual polyethylene chains (bottom); (C) Ratio of the C21+ to C4-6 products (top) and fraction of normal, monobranched, and dibranched isomers in extractables (bottom) over LDPE hydrocracking over catalysts with different metal-acid balances. These figures are quoted with permission from Vance et al.[61]. LDPE: Low-density polyethylene.
The catalytic performance of metal-acid bifunctional catalysts is strongly influenced by the metal/acid balance, mainly in the distribution of products[61,62]. The widely accepted mechanism of hydrocracking considers that the polymer undergoes dehydrogenation, protonation, isomerization, β-cleavage, and hydrogenation to ultimately produce saturated alkane molecules[63]. Specifically, the polymer is first dehydrogenated at the metal site into olefinic intermediates; then, the olefinic intermediates diffuse in the microporous channels of the acidic carrier until they encounter the BAS to be protonated and isomerized and undergo β-cleavage and rearrangement to generate alkanes and olefinic molecules; finally, the olefin is hydrogenated by the metal site to become a saturated alkane [Figure 2B]. If the BASs are higher than the metal sites, the olefinic intermediate undergoes successive isomerization and deep cracking before it encounters the hydrogenation of the metal site, so the product tends to generate more branched and gaseous products, and olefinic products may be present. Conversely, when the metal sites are more, the olefinic intermediates generated will not be isomerized in time, resulting in limited conversion of n-alkanes, so more liquid products are generated [Figure 2B and C][22,64].
The properties of the metal sites affect the hydrogenation/dehydrogenation steps. Cheng et al. found the dehydrogenation-hydrogenation function of Pt nanoparticles in the reduced state to be more active than that of Pt single atoms tightly bound to alumina binders[30]. During hydrocracking of polyolefins over Ru/acid catalysts, Ru exists predominantly in the metallic state, and the catalytic activity for PE deconstruction increases with increasing Ru[0] fraction[34,65]. However, these are characterizations of the catalyst before and after the reaction and do not fully describe the state of the catalyst at the time of the reaction. Peng et al. revealed through in situ X-ray photoelectron spectroscopy (XPS) that an electron transfer occurs between Pt and CeOx can enhance the intrinsic activity of the metal site[66]. In the final step, electrons are provided to the C=C bond to complete the hydrocracking or isomerization process. The ability of the Pt species to provide and accept sufficient electrons effectively facilitates the rapidity of the hydrogenation/dehydrogenation steps, resulting in higher activity and selectivity.
Also, the spatial distance between the metal and acid sites significantly influences the catalytic performance[30,67,68]. Olefinic intermediates cannot diffuse very far within the zeolite pores, and when the two active sites are far apart, the active sites will act alone. However, when the two active sites are too close, the diffusion limitation of the olefinic intermediates can lead to deep cracking. Liu et al. mixed Pt/WO3/ZrO2 and HY zeolite as catalysts, and hydrogenated plastics by tandem catalysis at 250 °C for 2 h[69]. Then, Liquid fuel products consisting of gasoline, diesel and kerosene were obtained with yields as high as 85%. Plastics are hydrogenated and dehydrogenated on the Pt surface, and the cracking reaction takes place at acidic sites on the HY zeolite or WO3/ZrO2 surface [Figure 3A]. When the catalyst was selected as Pt/HY + WO3/ZrO2, Pt was close to the acid site. PE was overcracked, and more light hydrocarbons of C5-C7 were produced. In contrast, when the catalyst was changed to Pt/WO3/ZrO2 + HY, the metal site was separated from the acid site and heavier products (C8-C12) were obtained. By modulating the pore structure of HY zeolites or changing the type of solid acid, the liquid product distribution can be selectively tuned to gasoline, jet fuel, and diesel [Figure 3B]. Moreover, the active metal of the loaded catalyst is on the open microenvironment, which has less influence on the intermediate generation and product selectivity and is easy to aggregate and leach on the outer surface. Aimed at controllable degradation of LDPE, Li et al. proposed a tandem catalytic mechanism on domain-limited metal and matched acidic sites to efficiently and selectively convert LDPE to naphtha with 96.8% C5-C9 hydrocarbon selectivity [Figure 3C][32]. In the proposed reaction mechanism, the acid sites of β-zeolite are responsible for cracking and isomerization, and only olefinic intermediates of the right size diffuse within the channels of Pt@S-1, encountering the Pt nanoparticles for hydrogenation, thus promoting a narrow distribution of the product. In contrast, non-shape selectivity happened on Pt/S-1 because the outer surface dominated adsorption and catalysis [Figure 3D].
Figure 3. (A) Depiction of main intermediates diffusing over Pt/WO3/ZrO2 + HY (30) catalyst (left) and Reaction selectivity in case of intimate contact between Pt particles and zeolite acid sites (right); (B) Depolymerization of LDPE over Pt/WO3/ZrO2 with various solid acid catalysts for 2 h at 250 °C. These figures are quoted with permission from Liu et al.[69]; (C) Side view model of the Pt@S-1 (left) and Pt/S-1 (right); (D) Adsorption energy of olefins and desorption of alkanes over S-1, Pt@S-1, and Pt/S-1. These figures are quoted with permission from Li et al.[32].
Ru-based catalysts have significant activity over Pt for C-C cleavage, but it is limited by the generation of too much low-value methane gas[58,65,70]. Rorrer et al. proposed the use of bifunctional metal-acid sites to promote “ideal hydrocracking” of hydrocarbons, whereby the cleavage of the intermediate C−C bond is facilitated by the β-scission pathways instead of terminal C-C cleavage, which results in lower methane production and higher liquid yields[65]. It was demonstrated that Brønsted acid carriers promote the hydrocracking of olefins, where the carbon cation intermediates facilitate the formation of transition states for non-terminal C−C bond cleavage, thus preventing the generation of excess methane from hydrocracking of terminal olefins [Figure 4A]. The acidity of the catalyst and the dispersion of Ru rather than the reducibility of Ru are the key determinants of selectivity and activity [Figure 4B].
Figure 4. (A) Liquid yield of PE and PP deconstruction as a function of the quantity of acid sites in the catalyst (estimated by NH3-TPD) and Ru dispersion (%) (estimated by CO pulse chemisorption); (B) XANES-LCF for the Ru-supported catalysts. These figures are quoted with permission from Rorrer et al.[65]; (C) Schematic illustration of the conventional impregnation and precise-impregnation approaches and TEM of p-Ru/SBA. The red circles help with the visualization of Ru NPs; (D) Schematic illustration of the conventional adsorption diagram for polymer chains on the catalyst; (E) Reducing the original entropy of polymer chains by strong localization in the space-confined catalyst. These figures are quoted with permission from Kang et al.[34]. PE: Polyethylene; PP: polypropylene; TPD: temperature-programmed desorption; XANES: X-ray absorption near-edge structure; LCF: linear combination fits; TEM: transmission electron microscopy; NPs: nanoparticles.
The importance of the entropy confinement domain on the performance of polyolefin hydrogenolysis was specifically addressed by Kang et al. Balancing the diffusion of polymers and the limiting effect of the required space, p-Ru/SBA exhibits high catalytic activity (1,106 g·gRu-1·h-1), excellent liquid selectivity with narrow product distribution, and good cycling stability and generalizability in hydrogenolysis
Polyester plastic upcycling
The non-noble metal Ni is one of the most popular hydrocracking metals due to its high hydrogenation/dehydrogenation activity and low cost. Ru-Ni/H-Beta bifunctional catalysts enabled hydrodeoxygenation (HDO) of polycarbonate (PC) monomer bisphenol A (BPA) and PC plastic waste under mild reaction conditions [Figure 5A][71]. It exhibited full conversion and > 90% selectivity to propane-2,2-diyldicyclohexane (P7) as a C15 cycloalkane in the jet fuel range. The alloy formed by Ru and Ni has strong intermetallic interactions, which facilitates the electron transfer from Ni to Ru for preferential adsorption and activation of the substrate, which is the reason for the higher activity of the Ru-Ni alloy than that of mono-metallic Ru and Ni [Figure 5B]. The Ni content promotes the high dispersibility of the Ru-Ni alloy, the Ru sites contribute to the dissociative hydrogen activation and hydrogenation of the aromatic ring, and the BAS on the zeolite surface facilitates the dissociation of the C−O bond, resulting in a mono-catalytic system for the selective conversion of PC wastes into bicyclic hydrocarbons (P7) [Figure 5C and D].
Figure 5. (A) Proposed reaction mechanism for HDO of PC to P7 over 1Ru0.5Ni/H-Beta catalyst; (B) Deconvoluted XPS spectra of Ru 3p of 1Ru/H-Beta and 1Ru0.5Ni/H-Beta; (C) p-Cresol adsorbed DRIFT spectra over catalysts at 200 °C; (D) Control experiments on the conversion of BPA after catalyst passivation to investigate the role of acidic site: the catalysts were passivated with pyridine and TBP, respectively, with pyridine poisoning all active sites and TBP affecting only the surface BAS. These figures are quoted with permission from Manal et al.[71]; (E) HDO activity and (F) product distribution as a function of the metal-acid balance (nNi/nA) over Ni/HZSM-5. These figures are quoted with permission from Liu et al.[72]. HDO: Hydrodeoxygenation; PC: polycarbonate; XPS: X-ray photoelectron; BPA: bisphenol A; TBP: 2,6 tert-butylpyridine; BAS: brønsted acid site.
Without hydrogen, catalytic cracking is also applicable to other types of plastics. Additionally, oxygen content in fuel can directly affect the combustion efficiency of petrol and the level of pollution to the environment. Nasution et al. used NiO to increase the acidity of HZSM5-70 for catalytic reforming of polyethylene terephthalate (PET) pyrolysis, resulting in lower yields of unwanted oxygenated compounds (ketones, alcohols, and acids) (from 39.38% to 10.75%), and the production of petrol grade hydrocarbons[73]. Eze et al. used Kankara zeolite-Y-based catalyst for pyrolysis of mixed waste plastics [including 27 wt% HDPE, 33 wt% LDPE, 13 wt% PP, 18 wt% polystyrene (PS) and 9 wt% PET] and found that it has the potential to efficiently produce liquid fuels with a narrow carbon range[74].
Polyester plastics inevitably generate a large number of gaseous products during the thermal upcycling process. Oxygen-containing compounds in the pyrolysis oil, along with acidic properties, degrade the quality of the oil. Upcycling of polyester plastics to fuels is necessary to reduce the oxygen content of the oil. Therefore, when designing catalysts for fuel production, it is important to consider studying HDO catalysts. Currently, most of the catalysts for polyester plastics recovery by hydrogenolysis still rely on expensive precious metals. Suitable catalysts play a vital role in producing liquid oil efficiently, with high quality and low cost. Besides, investigating the processing performance of mixed plastics to convert them directly into high-quality liquid fuels is still a crucial direction to be developed.
During the thermal treatment of plastics, catalysts are easily deactivated by the oxidation of noble metals, high-temperature agglomeration and coking of acid sites. Metals on the outer surface are prone to aggregation and leaching at high temperatures, resulting in poor catalytic stability. Kang et al. demonstrated that by loading Ru onto porous materials, Ru particles do not agglomerate during hydrogenolysis[34]. Alloying precious metals with other metals is also one of the strategies to improve their stability and antioxidant properties. Bifunctional Ru-Ni alloy-supported H-Beta catalyst still showed excellent catalytic performance after five catalytic HDO runs with no change in active sites[71]. During plastic upcycling, if precious metals are insufficient for the rapid hydrogenation of olefins, these olefins will undergo multiple cracking or oligomerization at the acid sites, leading to the formation of coke and the deactivation of the acid sites. On the one hand, high-pressure hydrogen can inhibit the unfavorable coking and repolymerization reaction, and on the other hand, the precious metal loaded on the support can reduce the catalytic coking by strong hydrogenation of the intermediates. However, the detailed coke formation mechanism is still unknown. Future work should provide in-depth characterization, capturing of reaction intermediates, monitoring to identify the evolution of coke species, and a better understanding of catalyst deactivation.
WASTE PLASTIC UPCYCLING TO AROMATICS
Aromatics are one of the most basic chemicals used in chemical production[75]. The conventional process for manufacturing aromatics is naphtha reforming, which is energy-intensive and has the subsequent processing steps with a large environmental carbon footprint[76]. The production of these chemicals from carbon-based feedstocks, such as shale gas, biomass and waste plastics, has received close attention. However, in these systems, harsh processing conditions, slow rates, low yields, and high hydrogen requirements lead to high production costs[77]. Zeolite-based catalysts were found to have excellent performance in most cases for catalytic upcycling of waste plastics to aromatics[78].
Polyolefin plastic upcycling
For polyolefin plastics, the formation mechanism of aromatics has always been a hot research topic, and it is currently believed that it mainly undergoes several stages of dehydrogenation, proton transfer and aromatization[23]. On the surface of the zeolite catalyst, the BASs are the active sites for the cracking and aromatization reactions, but the dehydrogenation or proton transfer process occurs at the Lewis acid sites. The catalyst design considers the synergistic effect of the Brønsted and Lewis acid sites[79]. Lewis acid metal (e.g., Mo, Zn, and Ga) cation-modified zeolites have been shown to significantly increase aromatic yields in the dehydroaromatization of C2-C4 hydrocarbons. Vichaphund et al. synthesized different metal-modified HZSM-5 including Co, Ni, Mo, Ga and Pd for rapid catalytic pyrolysis revealing Mo/HZSM-5’s top aromatic selectivity at 97% for ion-exchange catalysts and Ga/HZSM-5’s peak at 95% for impregnated catalysts[80]. Zhou et al. found that the aromatic selectivity of Ni-modified HZSM-5 for catalytic pyrolysis of LDPE under CO2 atmosphere was significantly improved compared to the modified HZSM-5, with better anti-coking properties[81]. Unfortunately, the detailed synergistic catalytic mechanism is not discussed.
The state and dispersion of Zn species in the zeolite are strongly influenced by the preparation method and pretreatment procedure, which can directly affect the catalytic properties [Figure 6A][82]. HDPE pyrolysis vapors were aromatized over Zn/ZSM-5, and the catalyst prepared by H2 reduction had the highest aromatic yield of 53% in the liquid phase and 93% benzene, toluene and xylene (BTX) selectivity. The reaction first formed a C2-C3 alkane/olefin hydrocarbon pool, followed sequentially by oligomerization-cyclization-dehydrogenation [Figure 6B]. Both BASs in zeolites and Zn-containing Lewis acid sites catalyzed the cracking of long-chain hydrocarbons. The positive correlation between [ZnOH]+ species and bridging Zn2+ species on BTX yields suggested an important role in forming aromatic hydrocarbons, with the former contributing more [Figure 6C]. The selectivity of BTX was mainly determined by the spatial constraints of the zeolite channels and the size of the olefinic intermediates and was less sensitive to the active Zn content. Nevertheless, the increase of active Zn species in the pores heightened the diffusion resistance and decreased the production of aromatic hydrocarbons with higher branching degrees, thus improving the selectivity of BTX in the liquid. Duan et al. also catalyzed the aromatization of waste plastics using ZSM-5 nanosheets (s-ZSM-5) and Zn-modified mesoporous ZSM-5 (Zn/meso-ZSM-5) in tandem[83]. PE chains were first depolymerized to olefins on s-ZSM-5 and then catalytically converted to methylated aromatics by Zn/meso-ZSM-5 [Figure 6D]. The b-axis length was optimized for s-ZSM-5, which has a shorter diffusion path and higher straight-channel exposure than nano ZSM-5, effectively inhibiting the intermediate accumulation on the zeolite surface, maximizing the reduction of coke formation, thus improving the activity towards the cracking reaction [Figure 6E][31]. The closeness of Zn species to the acidic areas of Zn/meso-ZSM-5 proved advantageous in enhancing olefin aromatization, depending on acidic sites optimized by ZnOx for combined cyclization and dehydrogenation processes [Figure 6F]. Additionally, the distinct separation of the potent acid site in s-ZSM-5 from the ZnOx species in meso-ZSM-5 prevented the creation of unwanted saturated alkanes through deep hydrogenation.
Figure 6. (A) The percentage of Zn species over different Zn/ZSM-5 catalysts obtained by deconvolution of XPS; (B) Proposed pathway of HDPE cracking and aromatization over Zn/ZSM-5; (C) The relationship between Zn species ([ZnOH]+ and bridged Zn2+) and the yields of (a) BTX and (b) Other MAHs. These figures are quoted with permission from Qian et al.[82]; (D) Schematic diagram of reaction flow over s-ZSM-5 and Zn/meso-ZSM-5. This figure is quoted with permission from Duan et al.[83]; (E) Schematic illustration of the cascade cracking steps on the external zeolite surface and within zeolite micropores on n-ZSM-5 and s-ZSM-5 catalysts. This figure is quoted with permission from Duan et al.[31]; (F) Conversion of propylene and selectivity of different products over different catalysts. This figure is quoted with permission from Duan et al.[83]. XPS: X-ray photoelectron; HDPE: high-density polyethylene; BTX: benzene, toluene and xylene; MAHs: monoaromatic hydrocarbons.
Du et al. reported the mechanism of coupling the PE dehydrocyclization process with the hydrocracking process over Ru/HZSM-5 catalysts under solvent- and hydrogen-free conditions[33]. The synergistic interaction between Ru and HZSM-5 contributed to the excellent catalytic performance. During catalysis, the polymer chains are sequentially dehydrogenated and protonated to form carbenium ions. Optimization of the distance between the Ru and acid sites leads to the simultaneous presence of C=C bonds and carbenium ions, which promotes the generation of cycloalkanes and achieves high selectivity for cycloalkanes. Ru nanoparticles were shown to promote dehydroaromatization of cycloalkanes [Figure 7A]. In addition, the catalytic performance is affected by the shape-selective effect of the zeolite’s pores
Figure 7. (A) The role of Ru in the upcycling of HDPE over Ru/HZSM-5(300). Monocyclic aromatic yield shown by HZSM-5(300) and Ru/HZSM-5(300) in cyclohexane conversion at 280 °C for 24 h; (B) The role of zeolites in the upcycling of HDPE. Yields of volatiles/gases, liquid-phase products and insoluble hydrocarbons; (C) Selectivity for volatiles/gases and liquid-phase and (D) GPC analysis of the solid residues for HDPE upcycling conducted over Ru/SAPO-34, Ru/USY and Ru/HZSM-5(300) at 280 °C for 24 h. These figures are quoted with permission from Du et al.[33]; (E) The framework image of USY, ZSM-5 and SAPO-34. HDPE: High-density polyethylene; GPC: gel permeation chromatography.
Polystyrene plastic upcycling
Another effective route to producing valuable aromatics is catalytic pyrolysis to recover PS[84,85]. The acid site remains the main active site for the catalytic pyrolysis of PS. When BASs trigger the degradation of PS, the aromatic rings of the PS chain are protonated to produce arenium intermediates (secondary or tertiary carbocations). Aromatic compounds or short-chain polymers are obtained by β-breakage, hydrogen transfer and cyclization. Chain fragments with cationic termini, when olefins, such as styrene or α-methylstyrene, are formed, are susceptible to successive acid-catalyzed reactions, resulting in limited yields of aromatic olefins. Whereas, when benzene or aromatic hydrocarbons with saturated side chains (e.g., toluene) are formed, the products can be stable. Therefore, when acid catalysts catalyze the pyrolysis of PS, the products obtained are mainly aromatic hydrocarbons. Serrano et al. analyzed how HZSM-5 and HMCM-41 pyrolyzed PS to synthesize benzene. They discovered that a broader structure of HMCM-41 enhanced the accessibility of PS to acid sites, leading to observed enhanced activity[86]. Ojha and Vinu conducted an extensive analysis of zeolites, examining eight distinct zeolites, each differing in their silica/aluminum ratio, specific surface area, pore size distribution, surface acidity, and structural makeup, as catalysts for the targeted generation of benzene from PS waste [Figure 8][84,87]. Influenced by the acidity of zeolite surfaces and the volume of micropores, Zβ and ZY can produce up to 50 wt% benzene, recognized as the ideal catalysts for the benzene synthesis. However, evidence is scarce regarding the specific function of acid types in ZY and Zβ in selectively boosting primary protonation in this research.
Figure 8. Benzene yields obtained with each catalytic process studied in the work of Ojha and Vinu. This figure is quoted with permission from Marquez et al.[84].
The acidic sites in the zeolite-based catalysts contribute to catalyzing the aromatization reaction, and the introduction of Lewis acid metals improves the aromatization performance. The microporous channel size of HZSM-5 happens to be a perfect geometrical match for the molecular size of BTX, making it the most widely used zeolite for selective production of aromatics as a carrier for polyolefin plastics. For catalytic pyrolysis PS, zeolites with large specific surface area, large pore volume and abundant acid sites are more suitable. However, zeolite with too strong acidity will promote olefin cross-linking reaction and cannot depolymerize PS into valuable products effectively. Reasonable modification of zeolite, such as doping with other elements, can improve the acidity and amount of acid required for PS degradation. In addition, pyrolysis of PS at low temperatures has not been realized yet, and the microporosity of zeolites allows PS molecules to come into contact with the acid sites on the outer surface only. Therefore, improving the accessibility of the acid sites is also a factor to be considered in catalyst design. Avoiding the use of noble metals, precisely regulating the active sites, avoiding the consumption of additional hydrogen and suppressing unwanted side reactions remain the future directions for promoting the efficient conversion of waste plastics into value-added chemicals.
WASTE PLASTIC UPCYCLING TO PRIMARY MONOMERS
Plastics are derived from petroleum, and a key advantage of converting waste plastics into monomers is that the depolymerized monomers can be re-polymerized to produce new polymers as raw material, thus reducing the use of non-renewable resources[88,89]. Converting waste plastics into monomers is an important form of chemical recycling with a huge potential application market.
Polyester plastic upcycling
Waste plastics to monomers for closed-loop recycling are usually applied to polyester plastics. Since the
Hydrolysis is a well-proven method to achieve PET recovery, but it usually consumes large amounts of strong acids and bases, limiting its large-scale application. Kang et al. proposed a facile and effective strategy to solve the problem by microwave-assisted hydrolysis of PET into terephthalic acid (TPA) using ZSM-5 catalyst with different cations in a neutral medium. The effect on the catalytic performance of PET hydrolysis was investigated by varying the Si/Al ratio and the cationic species of the ZSM-5 catalyst to control the concentration of the Brønsted and Lewis acid sites of the catalyst [Figure 9A and B][93]. The results showed that the highest monomer recovery was achieved over the H+@ZSM-5 catalyst because the total acid concentration was the largest and BASs were dominant. Compared with the case without catalyst, the reaction time was halved, the initial temperature of the reaction was reduced to 393 K, the activation energy was reduced by a factor of 19, and the catalyst had excellent recoverability. Therefore, the active site of Brønsted acid as catalyst in H+@ZSM-5 effectively promoted PET hydrolysis by decreasing the reaction activation energy and increasing the reaction kinetics. Finally, the mechanism by which H+@ZSM-5 plays an important role in the hydrolytic depolymerization process of PET is proposed. PET hydrolytic depolymerization is generally initiated by the nucleophilic addition of water molecules to the carbonyl carbon of the ester bond. Specifically, the H+ provided by the Brønsted acid of the catalyst attacks the carbonyl group of the PET, which is converted to a hydroxyl group and a carbon cation. Subsequently, the carbon cation formed is nucleophilically attacked, which is thermodynamically favorable, by the oxygen atoms in the water molecule. The latter step then follows the typical generation of TPA and ethylene glycol (EG) via ester hydrolysis.
Figure 9. (A) Schematic of the cation exchanged ZSM-5 (H+@ZSM-5: fully proton exchanged ZSM-5, Sur-H+@ZSM-5: surface proton exchanged ZSM-5, Na+@ZSM-5: fully sodium exchanged ZSM-5, respectively; (B) TPA yield of the ZSM-5-based catalysts and their acidic site concentration plot. These figures are quoted with permission from Kang et al.[93]; (C) Mechanism of PET methanolysis over MgO/NaY catalyst; (D) Correlation of DMT yield with strong BS on catalyst. These figures are quoted with permission from Tang et al.[97]. TPA: Terephthalic acid; PET: polyethylene terephthalate; DMT: dimethyl terephthalate; BS: basic sites.
Monomers derived from standard PET hydrolysis must undergo multiple crystallizations prior to their application in creating industrial PET. In contrast, catalytic methanolysis of PET is one of the hot spots in current research as it can achieve higher monomer yields with easier separation and purification under relatively mild conditions[94]. In the methanolysis of PET, either acidic or basic catalysts potentially have a significant effect[95]. Wherein, NaY zeolite has a high specific surface area and large pore size, provides adjustable acidic and basic sites that favor the reaction, and can be modulated in acidity and basicity when loaded with metal oxides[96]. Thus, Tang et al. utilized the MgO/NaY as a modified mesoporous catalyst for the methanolysis of PET wastes, creating an efficient and feasible way to solve the plastic crisis of PET
However, the monomer DMT, derived from the methanolysis of PET, is currently unsuitable for direct use in the PET production. In order to realize the closed-loop recycling of waste PET, the monomers of PET depolymerization must be effectively utilized. Guo et al. reported the effect of Nb-modified ZSM-5 on the hydrolysis reaction of PET monomers[98]. When Nb is stabilized on ZSM-5 in oxide form, there is interaction to generate new BAS with excellent catalytic activity and high stability for DMT hydrolysis. Over the 0.6Nb/ZSM-5 catalyst, the yield of TPA was as high as about 94%. The TPA prepared by this method is directly transferable to the production of PET, offering a hopeful pathway for catalysis.
Catalytic depolymerization to monomers is more suitable for upcycling of polyester plastics, especially PET. Chemical depolymerization of ester bonds is relatively easy. However, harsher reaction conditions, excessive solvent use and low yields are still the main obstacles limiting polyester plastics recycling. Compared to polyolefin plastics, aromatic plastics (e.g., PET) are easier to selectively hydrogenate to obtain aromatic products. In addition, the design of specific reactions (e.g., transesterification reactions) that take advantage of the properties of the ester group may produce high-value products.
Polyolefin plastic upcycling
The monomers of polyolefin plastics are light olefins, which are also the main precursors for other high value-added chemicals[75]. The market demand for ethylene and propylene has been growing annually, making the low-cost production of olefins particularly important. Catalytic cracking is a promising pathway for producing light olefins, with less energy consumption, improved process selectivity and fewer pollutants.
Based on the catalytic cracking mechanism, it can be inferred that high yields of light olefins require sufficiently small pore sizes favoring the generation of short chains, and suitable catalyst acidity favoring hydrogen transfer reactions. The improved catalyst performance can also be modulated by higher site accessibility. In previous reports, olefin production has mainly focused on ZSM-5 compared to other zeolites, with the ZSM-5 catalyst considered to be the zeolite catalyst with the highest content of light olefins produced. Wei et al. conducted naphtha catalytic cracking on modified ZSM-5, discovering that changing Fe, Cu, and La promoted aromatic production, whereas altering P and Mg enhanced light olefin synthesis[99]. The effect of containing microporous and mesoporous ZSM-5 zeolites and B-modified mesoporous zeolites on the catalytic cracking of polyolefins was first compared by Eschenbacher et al. The incorporation of mesopores accelerates the diffusion of product molecules, prevents secondary reactions, and improves the tolerance of the catalyst to coking deactivation[100]. The presence of B may increase Lewis acid sites, which reduces the aromatization activity and contributes to the cleavage of C5+ aliphatic hydrocarbons to lighter olefins, increasing the yield of C2-C4 olefins.
As seen above, zeolite-based catalysts mainly act as acidic or basic catalysts in the plastic depolymerization process, and the loaded metals can further regulate the acidity or basicity of the zeolites. The closed-loop recycling method of converting waste plastics into monomers is an attractive strategy, but most of the monomers it recovers cannot be directly converted into virgin plastics. The advantages compared to the route of synthesizing plastics from commonly used raw materials are not obvious. The introduction of low-cost and highly active heterogeneous catalytic systems and innovative reaction systems is still a hotspot of current research efforts, which combine the depolymerization process with the production of value-added molecules to create new regenerated materials with unique properties. Moreover, catalytic depolymerization for recovery to monomers is relatively difficult for most existing plastics and is not as simple as PET. It is also important to consider the generalizability of catalysts to the depolymerization of mixed plastics.
CONCLUSION AND OUTLOOK
Waste plastic recycling technologies are constantly being updated, and zeolite-based catalysts are promising catalyst candidates for promoting waste plastic upcycling. As shown in Figure 10 and Table 1, zeolite topography, acidity (intensity, density, distribution, and type), selective shape modulation of the pores, and the type of modified active species are all important factors influencing the upcycling performance of plastics. However, optimizing the design of catalysts to efficiently control the conversion of waste plastics still has much to be improved.
Figure 10. Schematic of the design and major value-added products of zeolite-based catalysts employed in the chemical recycling process of plastics.
A summary table regarding the key zeolite-based catalysts for thermal upcycling of plastics
Catalyst | Si/Al | Plastics | Reaction condition | Main products | Selectivity (wt%) | Conversion (wt%) | Ref. |
MCM-41 and ZSM-5 | MCM-41(4) ZSM-5(20) | HDPE | 500 °C | C8-C12 | 97.72 | 83.15 | [48] |
Al-SBA-15 | 5 | LDPE | 350-400 °C | C4-C10 | - | 50 | [51] |
Pt/WO3/ZrO2 + HY | 16 | LDPE | 250 °C 30 bar H2 2 h | C5-C22 | 83 | 94 | [69] |
Pt@S-1 + Beta | 25 | LDPE | 250 °C 3 MPa H2 2 h | C5-C9 | 96.8 | 99.5 | [32] |
Ru/FAU | 5.1 | PE | 200 °C 30 bar H2 16 h | C5-C32 | 67 | 100 | [65] |
Ru/H-BEA | 25 | PP | 215 °C 30 bar H2 16 h | C5-C32 | 67 | 100 | [65] |
p-Ru/SBA | - | LDPE | 230 °C 2 MPa H2 5 h | C5-C35 | - | 89.2 | [34] |
Ru-Ni/H-Beta | 12.5 | PC + BPA | 180 °C 3 MPa H2 10 h | Propane-2,2 -diyldicyclohexane | 90.2 | 99.9 | [71] |
Ni/HZSM-5 | 200 | PC | 190 °C 4 MPa H2 6 h | Propane-2,2 -diyldicyclohexane | 81.2 | 99.3 | [72] |
NiO/HZSM5-70 | 70 | PET | 450 °C 4 MPa H2 6 h | C5-C12 | 85.05 | - | [73] |
Zn/ZSM-5 | 25 | HDPE | 500 °C 20 mL/min N2 0.5 h | Aromatics | 53 | - | [82] |
s-ZSM-5 + Zn/ meso-ZSM-5 | 21 | LDPE | 400 °C 120 mL·h-1 3.3% H2/ 29.7% Ar/ 67% N2 4 h | Methylated aromatics | 60.1 | 100 | [83] |
Ru/HZSM-5 | 300 | HDPE | 280 °C 24 h | Cyclic hydrocarbons (C7-C15) | 60.3 mol | 69.6 | [33] |
MCM-41 | 42 | PS | 375 °C 0.5 h | Styrene | < 11 | 35 | [86] |
Zβ | 360 | PS | 400 °C | Benzene | 55.74 | - | [87] |
H@ZSM-5 | 25 | PET | 230 °C 0.5 h | TPA + EG | - | 98.52 | [93] |
MgO/NaY | - | PET | 200 °C 0.5 h | DMT | 91 | 99 | [97] |
B/Meso-ZSM-5 | 40 | LDPE | 600 °C 30 g/h N2 4 h | C2-C4 olefins | 86.3 | 99.2 | [100] |
First, drawing on the structure of recently developed zeolite-based catalysts is necessary for efficiently converting waste plastics into specific products. Modulating the distribution and accessibility of acid sites and enhancing synergistic interactions between components are all key factors in improving catalytic performance. Considering the effect of pore confinement on mass transfer, the influence of zeolite defects on catalytic activity is also indispensable. In addition to considering the effect of acidity and pore structure of the zeolite and metal type on the catalytic performance, it is also important to understand the complex network structure of the polymer. Increasing the contact of polymer molecules with the catalyst is one of the strategies to improve the catalytic performance. This may be achieved by designing catalysts with special morphology or multistage pore structures. Given the complexity of plastic waste, catalysts should not be insensitive to air, water or other metal contamination. Then, it is also essential to use advanced in situ characterization techniques to study in depth the conversion process of plastics on the catalyst surface, including tracking and detecting the generation of degradation products and changes in the active center and structure of the catalyst. The reaction mechanism of catalytic cracking of plastic molecules will be summarized, hoping to provide valuable guidance for designing more efficient catalysts and optimizing reaction conditions. Additionally, zeolite catalysts are prone to coking and deactivation. The stability and renewability of the catalyst is also crucial. Although many catalysts presented herein exhibit superior performance, most have been shown to produce residues and coke that eventually deactivate the catalyst. Realistic plastic waste contains additives, dyes and other impurities that tend to poison the catalyst. Therefore, studying the catalyst deactivation mechanism, drawing on the design of anti-poisoning catalysts, and considering zeolite regeneration are the growth points for new zeolite-based catalysts. Finally, tandem catalytic strategies or coupling of different catalytic technologies can be considered to break through the limitations of the original reaction and improve the degradation benefits. It is expected that applying zeolite-based catalysts for upcycling of waste plastics will achieve more satisfactory results in the future.
Moreover, of the products recovered from the thermal upcycling of plastics, the gaseous products can be used to manufacture new plastics and the liquid products can function as fuels or surfactants. However, the thermal conversion process can still negatively affect the environment, mainly due to its gas emissions and energy requirements. Firstly, greenhouse gas emissions are one of the environmental burdens of plastic upcycling. High temperatures drive the cleavage of C−C bonds making the conversion process energy intensive. The recycling process releases significant amounts of greenhouse gases. Secondly, the actual plastic waste may contain more impurities such as nitrogen, chlorine, sulfur and other elements that make plastics very durable. The presence of heteroatoms causes toxic compounds to be produced during the transformation of plastics, such as nitrogen oxides and chlorine-containing compounds (chlorobenzenes, polychlorinated biphenyls, etc.). These emissions contribute to air pollution and have a negative impact on health. Therefore, developing cost-effective catalysts and research on removing pollutants and reducing the impact on the environment is necessary.
DECLARATIONS
Authors’ contributions
Prepared and revised the manuscript: Wang X (Xiaomei Wang)
Discuss the manuscript: Xu J, Zhao M, Cui W
Revised the manuscript: Mu X, Wang X (Xiao Wang), Song S, Zhang H
Availability of data and materials
Not applicable.
Financial support and sponsorship
This work was supported by financial aid from the National Science and Technology Major Project of China (No. 2022YFB3504000), National Natural Science Foundation of China (Nos. 22020102003, 22025506 and 22271274), and Program of Science and Technology Development Plan of Jilin Province of China (Nos. 20230101035JC and 20230101022JC).
Conflicts of interest
All authors declared that there are no conflicts of interest.
Ethical approval and consent to participate
Not applicable.
Consent for publication
Not applicable.
Copyright
© The Author(s) 2024.
REFERENCES
3. Nava V, Chandra S, Aherne J, et al. Plastic debris in lakes and reservoirs. Nature 2023;619:317-22.
4. Pinheiro HT, MacDonald C, Santos RG, et al. Plastic pollution on the world’s coral reefs. Nature 2023;619:311-6.
5. Ali W, Ali H, Souissi S, Zinck P. Are bioplastics an ecofriendly alternative to fossil fuel plastics? Environ Chem Lett 2023;21:1991-2002.
6. Leslie HA, van Velzen MJM, Brandsma SH, Vethaak AD, Garcia-Vallejo JJ, Lamoree MH. Discovery and quantification of plastic particle pollution in human blood. Environ Int 2022;163:107199.
7. Landrigan PJ, Raps H, Cropper M, et al. The minderoo-monaco commission on plastics and human health. Ann Glob Health 2023;89:23.
8. Geyer R, Jambeck JR, Law KL. Production, use, and fate of all plastics ever made. Sci Adv 2017;3:e1700782.
9. Howard SA, McCarthy RR. Modulating biofilm can potentiate activity of novel plastic-degrading enzymes. NPJ Biofilms Microbiomes 2023;9:72.
10. Lau WWY, Shiran Y, Bailey RM, et al. Evaluating scenarios toward zero plastic pollution. Science 2020;369:1455-61.
12. Zhang W, Kim S, Wahl L, et al. Low-temperature upcycling of polyolefins into liquid alkanes via tandem cracking-alkylation. Science 2023;379:807-11.
13. Dong Q, Lele AD, Zhao X, et al. Depolymerization of plastics by means of electrified spatiotemporal heating. Nature 2023;616:488-94.
14. Ahrens A, Bonde A, Sun H, et al. Catalytic disconnection of C-O bonds in epoxy resins and composites. Nature 2023;617:730-7.
15. Xu Z, Munyaneza NE, Zhang Q, et al. Chemical upcycling of polyethylene, polypropylene, and mixtures to high-value surfactants. Science 2023;381:666-71.
16. Jehanno C, Alty JW, Roosen M, et al. Critical advances and future opportunities in upcycling commodity polymers. Nature 2022;603:803-14.
17. Jung JM, Cho SH, Jung S, et al. Disposal of plastic mulching film through CO2-assisted catalytic pyrolysis as a strategic means for microplastic mitigation. J Hazard Mater 2022;430:128454.
19. Jie X, Li W, Slocombe D, et al. Microwave-initiated catalytic deconstruction of plastic waste into hydrogen and high-value carbons. Nat Catal 2020;3:902-12.
20. Conk RJ, Hanna S, Shi JX, et al. Catalytic deconstruction of waste polyethylene with ethylene to form propylene. Science 2022;377:1561-6.
21. Mark LO, Cendejas MC, Hermans I. The use of heterogeneous catalysis in the chemical valorization of plastic waste. ChemSusChem 2020;13:5808-36.
22. Dong Z, Chen W, Xu K, Liu Y, Wu J, Zhang F. Understanding the structure-activity relationships in catalytic conversion of polyolefin plastics by zeolite-based catalysts: a critical review. ACS Catal 2022;12:14882-901.
23. Yuan H, Li C, Shan R, Zhang J, Wu Y, Chen Y. Recent developments on the zeolites catalyzed polyolefin plastics pyrolysis. Fuel Process Technol 2022;238:107531.
24. Zhang Q, Yu J, Corma A. Applications of zeolites to C1 chemistry: recent advances, challenges, and opportunities. Adv Mater 2020;32:e2002927.
25. He J, Wu Z, Gu Q, et al. Zeolite-tailored active site proximity for the efficient production of pentanoic biofuels. Angew Chem Int Ed Engl 2021;60:23713-21.
26. Wang H, Wang L, Xiao FS. Metal@Zeolite hybrid materials for catalysis. ACS Cent Sci 2020;6:1685-97.
27. Zhang Q, Gao S, Yu J. Metal sites in zeolites: synthesis, characterization, and catalysis. Chem Rev 2023;123:6039-106.
28. Lee WT, van Muyden A, Bobbink FD, Mensi MD, Carullo JR, Dyson PJ. Mechanistic classification and benchmarking of polyolefin depolymerization over silica-alumina-based catalysts. Nat Commun 2022;13:4850.
29. Ju C, Li M, Fang Y, Tan T. Efficient hydro-deoxygenation of lignin derived phenolic compounds over bifunctional catalysts with optimized acid/metal interactions. Green Chem 2018;20:4492-9.
30. Cheng K, Smulders LCJ, van der Wal LI, et al. Maximizing noble metal utilization in solid catalysts by control of nanoparticle location. Science 2022;377:204-8.
31. Duan J, Chen W, Wang C, et al. Coking-resistant polyethylene upcycling modulated by zeolite micropore diffusion. J Am Chem Soc 2022;144:14269-77.
32. Li L, Luo H, Shao Z, et al. Converting plastic wastes to naphtha for closing the plastic loop. J Am Chem Soc 2023;145:1847-54.
33. Du J, Zeng L, Yan T, et al. Efficient solvent- and hydrogen-free upcycling of high-density polyethylene into separable cyclic hydrocarbons. Nat Nanotechnol 2023;18:772-9.
34. Kang Q, Chu M, Xu P, et al. Entropy confinement promotes hydrogenolysis activity for polyethylene upcycling. Angew Chem Int Ed Engl 2023;62:e202313174.
35. Soltani M, Rorrer JE. Converting waste plastic to liquid organic hydrogen carriers. Angew Chem Int Ed Engl 2023;62:e202314530.
36. Jahirul MI, Faisal F, Rasul MG, Schaller D, Khan MMK, Dexter RB. Automobile fuels (diesel and petrol) from plastic pyrolysis oil - Production and characterisation. Energy Rep 2022;8:730-5.
37. Vellaiyan S. Energy extraction from waste plastics and its optimization study for effective combustion and cleaner exhaust engaging with water and cetane improver: a response surface methodology approach. Environ Res 2023;231:116113.
38. Sharuddin SD, Abnisa F, Wan Daud WMA, Aroua MK. Energy recovery from pyrolysis of plastic waste: study on non-recycled plastics (NRP) data as the real measure of plastic waste. Energy Convers Manag 2017;148:925-34.
39. Mishra R, Kumar A, Singh E, Kumar S. Recent research advancements in catalytic pyrolysis of plastic waste. ACS Sustainable Chem Eng 2023;11:2033-49.
40. Corma A. Inorganic Solid Acids and Their use in acid-catalyzed hydrocarbon reactions. Chem Rev 1995;95:559-614.
41. Corma A, Orchillés A. Current views on the mechanism of catalytic cracking. Microporous Mesoporous Mater 2000;35-6:21-30.
42. Weitkamp J. Catalytic hydrocracking - mechanisms and versatility of the process. ChemCatChem 2012;4:292-306.
43. Miandad R, Barakat M, Aburiazaiza AS, Rehan M, Nizami A. Catalytic pyrolysis of plastic waste: a review. Process Saf Environ Prot 2016;102:822-38.
44. Coelho A, Costa L, Marques M, Fonseca I, Lemos M, Lemos F. The effect of ZSM-5 zeolite acidity on the catalytic degradation of high-density polyethylene using simultaneous DSC/TG analysis. Appl Catal A Gen 2012;413-4:183-91.
45. Santos BPS, Almeida D, Marques MDFV, Henriques CA. Petrochemical feedstock from pyrolysis of waste polyethylene and polypropylene using different catalysts. Fuel 2018;215:515-21.
46. Figueiredo AL, Araujo AS, Linares M, et al. Catalytic cracking of LDPE over nanocrystalline HZSM-5 zeolite prepared by seed-assisted synthesis from an organic-template-free system. J Anal Appl Pyrol 2016;117:132-40.
47. Serrano D, Aguado J, Escola J, Rodríguez J, San Miguel G. An investigation into the catalytic cracking of LDPE using Py-GC/MS. J Anal Appl Pyrol 2005;74:370-8.
48. Ratnasari DK, Nahil MA, Williams PT. Catalytic pyrolysis of waste plastics using staged catalysis for production of gasoline range hydrocarbon oils. J Anal Appl Pyrol 2017;124:631-7.
49. Grün M, Unger KK, Matsumoto A, Tsutsumi K. Novel pathways for the preparation of mesoporous MCM-41 materials: control of porosity and morphology. Microporous Mesoporous Mater 1999;27:207-16.
50. Ungureanu A, Dragoi B, Hulea V, et al. Effect of aluminium incorporation by the “pH-adjusting” method on the structural, acidic and catalytic properties of mesoporous SBA-15. Microporous Mesoporous Mater 2012;163:51-64.
51. Zhang Z, Gora-Marek K, Watson JS, et al. Recovering waste plastics using shape-selective nano-scale reactors as catalysts. Nat Sustain 2019;2:39-42.
52. Mosio-Mosiewski J, Warzala M, Morawski I, Dobrzanski T. High-pressure catalytic and thermal cracking of polyethylene. Fuel Process Technol 2007;88:359-64.
53. Munir D, Irfan MF, Usman MR. Hydrocracking of virgin and waste plastics: a detailed review. Renew Sustain Energy Rev 2018;90:490-515.
54. Hu K, Yang Y, Wang Y, Duan X, Wang S. Catalytic carbon and hydrogen cycles in plastics chemistry. Chem Catal 2022;2:724-61.
55. Celik G, Kennedy RM, Hackler RA, et al. Upcycling single-use polyethylene into high-quality liquid products. ACS Cent Sci 2019;5:1795-803.
56. Tennakoon A, Wu X, Paterson AL, et al. Catalytic upcycling of high-density polyethylene via a processive mechanism. Nat Catal 2020;3:893-901.
57. Jia C, Xie S, Zhang W, et al. Deconstruction of high-density polyethylene into liquid hydrocarbon fuels and lubricants by hydrogenolysis over Ru catalyst. Chem Catal 2021;1:437-55.
58. Chen L, Meyer LC, Kovarik L, et al. Disordered, sub-nanometer ru structures on CeO2 are highly efficient and selective catalysts in polymer upcycling by hydrogenolysis. ACS Catal 2022;12:4618-27.
59. Kots PA, Liu S, Vance BC, Wang C, Sheehan JD, Vlachos DG. Polypropylene plastic waste conversion to lubricants over Ru/TiO2 catalysts. ACS Catal 2021;11:8104-15.
60. Jing Y, Wang Y, Furukawa S, et al. Towards the circular economy: converting aromatic plastic waste back to arenes over a Ru/Nb2O5 catalyst. Angew Chem Int Ed Engl 2021;60:5527-35.
61. Vance BC, Kots PA, Wang C, et al. Single pot catalyst strategy to branched products via adhesive isomerization and hydrocracking of polyethylene over platinum tungstated zirconia. Appl Catal B Environ 2021;299:120483.
62. Wang W, Liu CJ, Wu W. Bifunctional catalysts for the hydroisomerization of n-alkanes: the effects of metal-acid balance and textural structure. Catal Sci Technol 2019;9:4162-87.
63. Maesen TLM, Calero S, Schenk M, Smit B. Alkane hydrocracking: shape selectivity or kinetics? J Catal 2004;221:241-51.
64. Steijns M, Froment GF. Hydroisomerization and hydrocracking. 3. Kinetic analysis of rate data for n-decane and n-dodecane. Ind Eng Chem Prod Res Dev 1981;20:660-8.
65. Rorrer JE, Ebrahim AM, Questell-santiago Y, et al. Role of bifunctional Ru/acid catalysts in the selective hydrocracking of polyethylene and polypropylene waste to liquid hydrocarbons. ACS Catal 2022;12:13969-79.
66. Peng Y, Wang X, Wang C, Bi W, Jiang Q, Tian Z. Boosting catalytic performance via electron transfer effect for hydroisomerization on a low-Pt-content PtCeOX/zeolite catalyst. Chem Catal 2023;3:100505.
67. Shi Y, Xing E, Wu K, Wang J, Yang M, Wu Y. Recent progress on upgrading of bio-oil to hydrocarbons over metal/zeolite bifunctional catalysts. Catal Sci Technol 2017;7:2385-415.
68. Luo W, Cao W, Bruijnincx PCA, Lin L, Wang A, Zhang T. Zeolite-supported metal catalysts for selective hydrodeoxygenation of biomass-derived platform molecules. Green Chem 2019;21:3744-68.
69. Liu S, Kots PA, Vance BC, Danielson A, Vlachos DG. Plastic waste to fuels by hydrocracking at mild conditions. Sci Adv 2021;7:eabf8283.
70. Lee W, Bobbink FD, van Muyden AP, et al. Catalytic hydrocracking of synthetic polymers into grid-compatible gas streams. Cell Rep Phys Sci 2021;2:100332.
71. Manal AK, Shanbhag GV, Srivastava R. Design of a bifunctional catalyst by alloying Ni with Ru-supported H-beta for selective hydrodeoxygenation of bisphenol A and polycarbonate plastic waste. Appl Catal B Environ 2023;338:123021.
72. Liu J, Wei J, Feng X, et al. Ni/HZSM-5 catalysts for hydrodeoxygenation of polycarbonate plastic wastes into cycloalkanes for sustainable aviation fuels. Appl Catal B Environ 2023;338:123050.
73. Nasution F, Husin H, Mahidin, et al. Conversion of pyrolysis vapors derived from non-biodegradable waste plastics (PET) into valuable fuels using nickel-impregnated HZSM5-70 catalysts. Energy Convers Manag 2022;273:116440.
74. Eze WU, Madufor IC, Onyeagoro GN, Obasi HC, Ugbaja MI. Study on the effect of Kankara zeolite-Y-based catalyst on the chemical properties of liquid fuel from mixed waste plastics (MWPs) pyrolysis. Polym Bull 2021;78:377-98.
75. Zhang F, Zeng M, Yappert RD, et al. Polyethylene upcycling to long-chain alkylaromatics by tandem hydrogenolysis/aromatization. Science 2020;370:437-41.
76. Wang G, Zhu X, Li C. Recent progress in commercial and novel catalysts for catalytic dehydrogenation of light alkanes. Chem Rec 2020;20:604-16.
77. Perego C, Ingallina P. Recent advances in the industrial alkylation of aromatics: new catalysts and new processes. Catal Today 2002;73:3-22.
78. Tian X, Zeng Z, Liu Z, et al. Conversion of low-density polyethylene into monocyclic aromatic hydrocarbons by catalytic pyrolysis: Comparison of HZSM-5, Hβ, HY and MCM-41. J Clean Prod 2022;358:131989.
79. Dai L, Zhou N, Lv Y, et al. Pyrolysis technology for plastic waste recycling: A state-of-the-art review. Prog Energy Combust Sci 2022;93:101021.
80. Vichaphund S, Aht-ong D, Sricharoenchaikul V, Atong D. Production of aromatic compounds from catalytic fast pyrolysis of Jatropha residues using metal/HZSM-5 prepared by ion-exchange and impregnation methods. Renew Energy 2015;79:28-37.
81. Zhou S, Li P, Pan H, Zhang Y. Improvement of aromatics selectivity from catalytic pyrolysis of low-density polyethylene with metal-modified HZSM-5 in a CO2 atmosphere. Ind Eng Chem Res 2022;61:11407-16.
82. Qian K, Tian W, Yin L, Yang Z, Tian F, Chen D. Aromatic production from high-density polyethylene over zinc promoted HZSM-5. Appl Catal B Environ 2023;339:123159.
83. Duan J, Wang H, Li H, et al. Selective conversion of polyethylene wastes to methylated aromatics through cascade catalysis. EES Catal 2023;1:529-38.
84. Marquez C, Martin C, Linares N, De Vos D. Catalytic routes towards polystyrene recycling. Mater Horiz 2023;10:1625-40.
85. Wang J, Jiang J, Sun Y, et al. Recycling benzene and ethylbenzene from in-situ catalytic fast pyrolysis of plastic wastes. Energy Convers Manag 2019;200:112088.
86. Serrano DP, Aguado J, Escola JM. Catalytic conversion of polystyrene over HMCM-41, HZSM-5 and amorphous SiO2-Al2O3: comparison with thermal cracking. Appl Catal B Environ 2000;25:181-9.
87. Ojha DK, Vinu R. Resource recovery via catalytic fast pyrolysis of polystyrene using zeolites. J Anal Appl Pyrol 2015;113:349-59.
88. Coates GW, Getzler YDYL. Chemical recycling to monomer for an ideal, circular polymer economy. Nat Rev Mater 2020;5:501-16.
89. Vollmer I, Jenks MJF, Roelands MCP, et al. Beyond mechanical recycling: giving new life to plastic waste. Angew Chem Int Ed Engl 2020;59:15402-23.
90. Hou Q, Zhen M, Qian H, et al. Upcycling and catalytic degradation of plastic wastes. Cell Rep Phys Sci 2021;2:100514.
91. Tournier V, Topham CM, Gilles A, et al. An engineered PET depolymerase to break down and recycle plastic bottles. Nature 2020;580:216-9.
92. Rorrer NA, Nicholson S, Carpenter A, Biddy MJ, Grundl NJ, Beckham GT. Combining reclaimed PET with bio-based monomers enables plastics upcycling. Joule 2019;3:1006-27.
93. Kang MJ, Yu HJ, Jegal J, Kim HS, Cha HG. Depolymerization of PET into terephthalic acid in neutral media catalyzed by the ZSM-5 acidic catalyst. Chem Eng J 2020;398:125655.
94. Du J, Sun Q, Zeng X, Wang D, Wang J, Chen J. ZnO nanodispersion as pseudohomogeneous catalyst for alcoholysis of polyethylene terephthalate. Chem Eng Sci 2020;220:115642.
95. Mancini SD, Zanin M. Post Consumer pet depolymerization by acid hydrolysis. Polym Plast Technol Eng 2007;46:135-44.
96. Wang C, Xu N, Liu T, et al. Mechanical pressure-mediated Pd active sites formation in NaY zeolite catalysts for indirect oxidative carbonylation of methanol to dimethyl carbonate. J Catal 2021;396:269-80.
97. Tang S, Li F, Liu J, Guo B, Tian Z, Lv J. MgO/NaY as modified mesoporous catalyst for methanolysis of polyethylene terephthalate wastes. J Environ Chem Eng 2022;10:107927.
98. Guo B, Liu J, Tang S, Liu Y, Tian Z, Lv J. Hydrolysis of dimethyl terephthalate to terephthalic acid on Nb-modified HZSM-5 zeolite catalysts. J Chem Tech Biotech 2022;97:1695-704.
99. Wei Y, Liu Z, Wang G, et al. Production of light olefins and aromatic hydrocarbons through catalytic cracking of naphtha at lowered temperature. Stud Surf Sci Catal 2005;158:1223-30.
Cite This Article
Export citation file: BibTeX | EndNote | RIS
OAE Style
Wang X, Xu J, Zhao M, Cui W, Mu X, Wang X, Song S, Zhang H. Recent progress of waste plastic upcycling based on multifunctional zeolite catalysts. Chem Synth 2024;4:28. http://dx.doi.org/10.20517/cs.2023.67
AMA Style
Wang X, Xu J, Zhao M, Cui W, Mu X, Wang X, Song S, Zhang H. Recent progress of waste plastic upcycling based on multifunctional zeolite catalysts. Chemical Synthesis. 2024; 4(2): 28. http://dx.doi.org/10.20517/cs.2023.67
Chicago/Turabian Style
Xiaomei Wang, Jing Xu, Meng Zhao, Wenjie Cui, Xiaowei Mu, Xiao Wang, Shuyan Song, Hongjie Zhang. 2024. "Recent progress of waste plastic upcycling based on multifunctional zeolite catalysts" Chemical Synthesis. 4, no.2: 28. http://dx.doi.org/10.20517/cs.2023.67
ACS Style
Wang, X.; Xu J.; Zhao M.; Cui W.; Mu X.; Wang X.; Song S.; Zhang H. Recent progress of waste plastic upcycling based on multifunctional zeolite catalysts. Chem. Synth. 2024, 4, 28. http://dx.doi.org/10.20517/cs.2023.67
About This Article
Special Issue
Copyright
Author Biographies
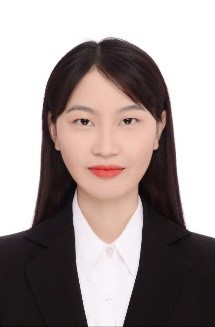
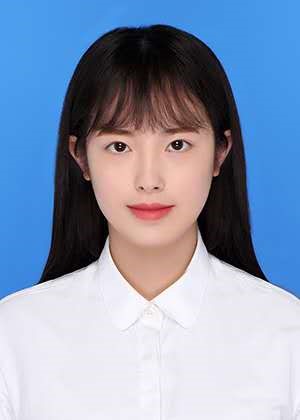
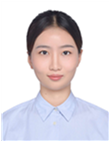
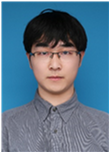
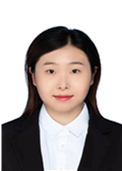
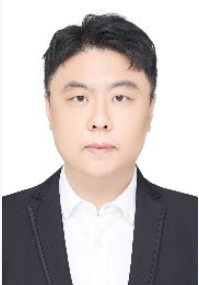

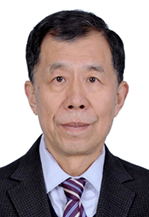
Data & Comments
Data
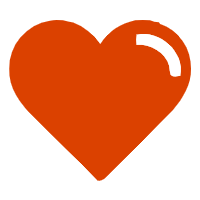
Comments
Comments must be written in English. Spam, offensive content, impersonation, and private information will not be permitted. If any comment is reported and identified as inappropriate content by OAE staff, the comment will be removed without notice. If you have any queries or need any help, please contact us at support@oaepublish.com.