Integrating toyota production system for sustainability and competitive advantage in medical device software design
Abstract
This research explores the integration of the Toyota Production System (TPS) and sustainability into the software design and development processes of a medium-sized medical device company dealing with resource constraints and evolving customer requirements. Through an analysis of TPS principles and how they relate to manufacturing and software development challenges, the research seeks to strengthen efficiency and competitiveness. It provides an adaptable implementation plan that fosters a competitive strategy and promotes sustainability through efficient software practices. The paper presents a roadmap for systematically integrating TPS and sustainability in alignment with international best practices, positioning the company to thrive in the expanding medical software market. This framework addresses immediate operational issues while laying the groundwork for long-term success and compliance with industry standards.
Keywords
INTRODUCTION
Numerous companies have focused on improving operations through efficient approaches and sustainable practices in the present competitive business landscape. The Toyota Production System (TPS), which employs lean concepts and continuous improvement programs to boost productivity across areas, is widely regarded as a transformative approach. Originally developed for manufacturing, it is known that TPS has transcended its automotive roots to find applications in sectors such as software, healthcare and construction. In software design and development in the medical device industry, challenges such as prolonged lead times and suboptimal resource utilization are prevalent. By applying lean manufacturing methods, organizations can align their management activities with TPS principles, streamline processes, and achieve greater overall efficiency. TPS emphasizes a process-based approach and waste reduction, significantly enhancing operational effectiveness and paving the way for lean software development techniques. This approach aims to reduce lead times and improve product quality while addressing the complexities of software development, including material modeling, code development, and parameter modifications. In medical device manufacturing, where efficiency and sustainability are paramount, incorporating TPS principles into software design and development processes can yield substantial benefits.
The significance of this research lies in its potential to streamline software design and development procedures within the medical device manufacturing process. By applying TPS concepts and lean software development, this study provides valuable insights for organizations seeking to enhance their software development processes. It explores how TPS methodologies contribute to waste reduction, increased efficiency, and the cultivation of sustainability as a competitive advantage. The study aims to identify practical benefits through qualitative examination, making it a valuable resource for researchers and industry practitioners alike.
The objectives of this research are to analyze manufacturing and software design processes, assess the application of TPS principles and sustainability strategies in software development, identify challenges and opportunities aligned with TPS benefits, and develop a systematic framework for achieving a competitive advantage. The study proposes an implementation strategy for a manufacturing medical device company, referred to as a medical device company, to maintain confidentiality. While the central hypotheses include that addressing software development challenges with TPS practices improves lead times and enhances development quality, the ongoing research stage of the software development process limits the feasibility of hypothesis testing. Instead, the study will provide insights by analyzing best practices and literature to guide software development improvements based on successful TPS and lean methodologies.
This research examines the theoretical feasibility of using TPS principles in the development of medical device software. Specifically, it attempts to provide a conceptual framework for better efficiency, quality, and compliance in medical device software development by examining how the concepts of TPS map into the unique requirements of this industry. While this study presents a theoretical framework for applying TPS principles to medical device software development, it is important to acknowledge its limitations. First, the research references relevant case studies from existing literature, as a full-scale implementation or case study was not feasible due to the company's early developmental stage, which requires additional time for data collection and compliance with strict medical device regulations. Additionally, the focus on the initial stages of product development may not fully capture the complexities that arise in later phases of the product lifecycle. Second, specific company data could not be included due to data confidentiality constraints. Third, the simulation tool analysis aimed to test the frameworks and TPS principles, providing valuable insights; however, it was limited by factors such as modeling expertise and data availability. Finally, the study does not delve into broader business considerations, including finance, sales, and marketing. Despite these limitations, this research serves as a valuable starting point for organizations seeking to optimize their medical device software development processes, offering a conceptual foundation for future empirical studies and more comprehensive investigations.
Literature review
Companies strive for long-term sustainability through advancements in operations, strategy and products. TPS principles emphasize continuous improvement and waste reduction, which have demonstrated effectiveness in manufacturing and show potential for software development. Sustainability is necessary for long-term success that combines social, environmental and economic factors. The study examines TPS and sustainability synergies in medical device manufacturing software design and development. It examines fundamental elements, advantages, challenges, and opportunities to ensure superior quality.
TPS and its foundation
The TPS traces its roots to the innovative work in automated looms of Sakichi Toyoda and Kiichiro Toyoda who perpetuate this legacy[1]. TPS was developed under Kiichiro’s leadership to solve economic issues and it embodies continuous improvement, waste reduction and respect for people, all of which are essential for organizational effectiveness[2]. Originally developed for lean manufacturing, TPS greatly improves operational effectiveness, product quality and revenue generation[3].
The Toyota Way 4P model, a pyramid-shaped framework, emphasizes philosophy, process, people, and partners. Its foundation is a mindset focused on providing value to society and consumers. It builds on lean principles to reduce waste and improve operational efficiency. The Toyota Way incorporates fourteen principles, including long-term decision-making, workflow optimization, and a “pull” system[4,5]. Techniques such as visual control facilitate issue identification, while reliable technology supports target achievement; equitable task distribution, prompt issue resolution, and standardized procedures further promote efficiency. Developing informed leaders, building cohesive teams, establishing robust partnerships, and conducting continuous evaluations are essential to constructing a robust framework for organizational success and efficiency. This approach aligns with Toyota’s fourteen management principles, which emphasize long-term perspectives, problem-solving and leadership[6]. The TPS is a structured and organized methodology of production that maintains emphasis on efficiency and quality. Conceptually, it may be envisioned, for descriptive purposes, as a house with four key components: the first pillar is automation with human intelligence or Jidoka, the second pillar is eliminating waste or just-in-time, with the roof for customer focus, the foundation is standardization and operational stability and the center is the heart, its people. The guiding principles of the TPS are continuous improvement, customer satisfaction, high quality at lower cost, and in the shortest period. While similar to lean production, TPS focuses on the system as a whole rather than the various tools[5].
Benefits of the TPS
Studies indicate that implementing TPS in practice leads to significant improvements. Lean manufacturing techniques, which are essential to TPS, help improve revenue, product quality and operational performance[7,8]. Companies that use TPS see significant improvements in quality, lead time, cost, and employee engagement[4]. TPS focuses on aspects such as continuous improvement, waste reduction, and adaptability[3,5]. TPS can facilitate improved supply chain management, consumer satisfaction, and employee empowerment[9-11]. Additionally, it can help with cost reduction, environmental sustainability, and overall organizational performance[5,11,12]. TPS also guarantees a secure workplace and harmonizes company goals with customer demands[11,13].
TPS in the software design and development
Applying the TPS to software design reveals similarities between customer-centric methods and waste elimination[14] which recognize the challenges associated with software development. Through a just-in-time strategy, Kaizen for continuous improvement, and successful collaboration in cross-functional teams, TPS concepts are highlighted to increase productivity and quality[15]. Lean software development emphasizes minimum non-value-added processes, continuous testing and incremental delivery[16]. Integrating TPS principles with lean approaches ensures that software solutions are of high quality, offer greater productivity, and are focused on their customers.
Sustainability in software development from the perspective of a medical device company
Numerous studies have explored the intersection of software development and sustainability. A particular study highlights the potential of integrating sustainability dimensions and waste management into software development processes[17]. Another study emphasizes the crucial role of technology adoption in promoting sustainable development, and compares structured and agile software development methodologies in terms of their potential to contribute to sustainability goals[18-20].
This is consistent with TPS principles as supported by research that demonstrates the positive relationship between lean processes and manufacturing sustainability[21]. Applying TPS principles improves sustainability and organizational performance by increasing productivity and reducing waste. For instance, an organization that specializes in orthopedic and surgical instruments in the medical device business may gain an edge over its competitors by optimizing its software development, minimizing waste, and implementing TPS-based sustainable processes[22].
Opportunities and challenges in integrating the TPS
TPS adoption brings a variety of possibilities and challenges. A study highlights the need for culture transformation and personnel training while addressing challenges with system integration and continuous improvement[23]. The lack of competency among the workers on the shop floor was considered as the primary barrier[24], indicating the importance of knowledge management and technical ability throughout implementation[25,26].
TPS has its roots on the Toyota philosophy, which prioritizes waste reduction, optimized processes, and continuous improvement. It is a broader framework that offers the potential for wider process improvement[5,27-29]. In contrast, Scrum is a subset of Agile with an emphasis on agility, flexibility, and collaboration. While Scrum is effective for software development[30], it may have limited applicability in other industries. TPS and Scrum both recognize the importance of continuous improvement with a focus on efficiency, but they prioritize different aspects. Scrum emphasizes short-term planning, sprints for flexibility, iteration and collaboration, while TPS is centered on long-term planning, waste reduction, customer focus and standardized work. Understanding these differences can help organizations choose the best approach or a hybrid for their specific needs, especially in industries combining software development and manufacturing.
Additionally, potential benefits such as waste reduction and revenue growth have been highlighted for technological possibilities which include improved flow, enhanced cybersecurity, data analytics, and flexibility[23]. However, challenges including data security and reluctance to change need to be addressed. Though strategy alignment and cost-benefit evaluations are essential, adopting technology such as cloud computing and 3D printing has advantages.
In summary, TPS presents advantages, but it still requires thorough planning for effective implementation[23]. This study generally provides insights on TPS applications in a variety of areas, guiding future studies and practical initiatives.
METHODS
The method employed in order to achieve the objectives of the study focuses on evaluating the application of the TPS and sustainability in software design and development at a medical device manufacturing company. The methodology that has been selected includes analysis, research data and literature reviews to provide insight on the effectiveness and importance of TPS and sustainable practices. The methodology aims to examine the relationship between TPS principles and sustainability that guide the design and implementation.
The review of the literature focuses on important factors, particularly the TPS principles, sustainability in software design and the challenges faced by medical device manufacturing. Empirical research expands on this by providing practical insights into TPS implementation. The analysis phase entails reviewing quantitative data, such as performance metrics, to identify trends and potential for improvement.
The methodology proceeds with a structured approach including reviewing TPS and sustainability concepts, assessing current processes, benchmarking best practices and analyzing existing practices and success criteria. This approach involves the development of a strategy framework for operational excellence which incorporates TPS and sustainability principles.
Document analysis, manufacturing data reports, observation, research papers and industry data are some of the data-gathering methods employed. These methodologies offer an in-depth understanding of current practices and industry standards. The relevant insights are then determined utilizing qualitative and quantitative approaches such as statistical analysis and theme analysis.
In general, this method involves an in-depth review of software design and development processes in medical device company operations with the aim of improvement.
RESULTS AND DISCUSSION
The industry position of the medical device company was analyzed through the business frameworks of Porter’s Five Forces, SWOT, VRIO, and PESTLE, which had certain insights on competitive dynamics, internal strengths and weaknesses, and external opportunities and threats. The research study also explored industry trends, studied the available literature on TPS practices, challenges, and sustainability, and checked compliance with international standards of the firm such as International Organization for Standardization (ISO) 13485 and the International Electrotechnical Commission (IEC) standards. These findings will provide a clear understanding of the business competitive situation, future areas of improvement, and opportunities for sustainable growth. In relation, internal analyses from the study on regulatory compliance and ISO will try to identify TPS alignment and sustainability challenges and opportunities using quality management system (QMS) information, production reports, and simulations. This thorough study consequently provides a basis for recommendations for future development and improvement.
Strategic analysis and market outlook
In a medical device company, a strategic analysis examines market dynamics using frameworks such as Porter’s Five Forces, PESTLE, VRIO and SWOT. Research studies provide valuable insights that guide improvements, emphasizing software development, agile practices, and industry feedback. The strategy has to be aligned with the industry benchmarks and also capitalize on new opportunities. The main firms that constitute the market shares in the global orthopedic device market are Johnson & Johnson with 20%, Medtronic with 10%, Smith & Nephew with 5%, Stryker with 18%, and Zimmer Biomet with 15% share. Additionally, 32% of their shares are spread across various businesses that are growing steadily as a result of technology improvements which demonstrate a high degree of concentration. High cost of implants is one of the ongoing challenges. The orthopedic device market in Southeast Asia was projected to grow by 6.43% yearly and reach US$0.97 billion in 2023[31-33].
Examining competition and strategic landscapes
The analysis of the competitive landscape of a medical device company, employing Porter’s Five Forces framework, reveals high entry barriers due to substantial research and development (R&D) costs and stringent regulations. Supplier bargaining power is moderate, influenced by alternative suppliers and resource uniqueness. Buyers have great influence because of alternative substitutes and collective bargaining. There is some risk of substitutes balanced by the demand for orthopedic devices in critical cases. Intense competitive competition requires innovation, effective pricing, and understanding of the market.
Externally, political factors impact operations through government regulations, necessitating compliance and adaptability. Demand is driven by social factors such as aging populations and health awareness, while costs and viability from a financial perspective are influenced by economic stability. Rapid advancements in technology offer opportunities that also require a focus on data security. Legal considerations focus on adherence to regulations and maintaining intellectual property, whereas environmental considerations influence consumer perceptions and new product development, which results in a greater focus on sustainability.
Internally, the medical device company, using the VRIO evaluation, identifies valuable but common resources such as skilled teams and established relationships. Intellectual property offers a temporary advantage, while regulatory compliance, organizational structure, and project management practices are valuable yet common. SWOT analysis highlights strengths, which are quality products, innovation, distribution network, R&D, brand reputation, and ISO 13485 certification. Weaknesses can include an inadequate level of sustainability focus with a small market share, dependence on suppliers and the concentration on the local market. The growth in demand, international markets, innovations in technology, partnerships and assistance from governments offer numerous opportunities. The competition, price sensitivity, regulations, technical obsolescence, changes in the economy, and limited international exposure are all presenting potential threats.
This study utilizes Porter’s Five Forces, SWOT, PESTLE, and VRIO frameworks to evaluate the integration of the TPS with sustainability in a medical device company software design. Porter’s analysis highlights high entry barriers due to R&D costs and regulations, limiting TPS adoption. The SWOT analysis reveals strengths in product quality but identifies weaknesses in sustainability focus and market share. PESTLE indicates that regulatory compliance and technology drive TPS implementation, while training gaps hinder progress. The VRIO framework suggests that while resources are valuable, there is a certain commonality that restricts the competitive advantage. Comparative analysis reveals inefficiencies and misalignments with lean practices. Overall, while studies on TPS and sustainability are growing, a gap remains in their effective integration into software design processes, emphasizing the need for a structured approach.
These challenges are further underscored by strategic insights from a 2020 global survey of 355 medical device industry senior managers reveal challenges with shifting regulations (74%), product development complexity (47%), pricing (37%), funding (29%), talent retention (29%), competition (24%), tech adaptation (17%), and reimbursement changes (14%)[34]. These insights primarily provide a robust understanding of challenges in the competitive medical device landscape.
In summary, integrating TPS principles with sustainability is vital for a medical device company to navigate regulatory complexities and enhance competitiveness. By adopting a structured approach to TPS, organizations can improve operational efficiency and product quality, positioning themselves for success in a rapidly evolving market.
Analysis of the current practices of a sample medical device company
The medical device company under consideration conforms with international standards, including ISO 14971 for risk management and ISO 13485 for QMS. Additionally, it complies with FDA 21 CFR Part 820, which guarantees quality and regulatory adherence for both local and U.S. markets. Its software design plans must adhere to IEC 62304, and electrical safety has to comply with IEC 60601-1, while ASTM International standards ensure material safety and approval.
Significant percentages of nonconforming products are used as is (7.96%), scrapped (8.22%), and require rework (9.61%); nonetheless, the production analysis identifies opportunities for improvement. Main root causes involve human error, setup/trial piece issues, and process challenges. Corrective and Preventive Action (CAPA) reports highlight human factors (80%) that impact quality systems, recalls, and standards, with corrective action taken.
Resolving human errors, improving product quality, and optimizing operational efficiency may be accomplished simultaneously by adhering to continuous improvement objectives and implementing TPS principles which include error-proofing and standard work. Adhering to best practices and gradually implementing TPS integration can assist a company in demonstrating its commitment to regulatory compliance, continuous improvement and efficient medical device manufacturing.
The recent advancement in the development of software for medical device companies underlines an urgent need to integrate QMS and lean methodology synergistically. New approaches have been developed that merge principles from the TPS in combination with ISO standards, such as ISO 13485 and ISO 14971, in an effort to promote better operational efficiencies, regulatory compliance, and risk management. They maximize the product life cycle from design through development and building onto distribution by using value stream mapping, just-in-time practice, and continuous improvement. Additionally, they introduce a comprehensive set of metrics to monitor performance at each stage, fostering a data-driven approach to quality and risk management. Such innovations address the specific challenges faced by medical device manufacturers and contribute to the advancement of best practices in quality engineering and risk management within complex industries.
Comparative analysis and strategic alignment
In this section, a comprehensive analysis comparing best practices in the medical device industry with TPS principles is evaluated to highlight the possible advantages of methods based on lean manufacturing where the alignment of risk management, quality management, regulatory compliance and customer-centric approaches was studied.
Comparison with TPS principles and medical device industry best practices
Industry best practices and TPS principles comparison: commonalities exist between medical device industry practices and TPS principles emphasizing waste reduction and standardized work processes for improved efficiency.
Survey on effectiveness of FDA regulations: of the 107 healthcare executives interviewed, 41% reported being neutral, 18% considered the regulations ineffective, and 7% found them very ineffective, indicating a range of viewpoints on FDA regulations[35]. Addressing possible regulatory loopholes might improve flexibility and competitiveness in medical device company operations.
TPS integration compatibility with international standards: Table 1 compares how the TPS aligns with ISO 13485, IEC 62304, and IEC 60601-1 standards. The table highlights key areas where TPS practices can be integrated to ensure compliance, enhance quality management, improve processes, manage risks, maintain documentation and traceability, meet regulatory requirements, and develop personnel competence. It offers insights into the compatibility and potential benefits of adopting TPS principles within the medical device industry.
TPS compatibility factors with the international standards analysis
ISO 13485 | ISO 14971 | IEC 62304 | IEC 60601-1 | |
Quality management | The quality management principles and techniques outlined in ISO 13485 can be complemented by TPS. It can enable Orthopaedic International to continuously improve process effectiveness and enhance product quality | To ensure that effective risk management procedures are included into the quality management system, TPS can supplement ISO 14971. However, it is important to consider the guidelines outlined in ISO 14971 | TPS can enhance the development of robust software life cycle processes outlined in IEC 62304 | TPS can support the fundamental requirements for basic safety and performance as stated in IEC 60601-1 for medical equipment |
Process improvement | TPS focuses on continuous improvement, waste reduction, and operational efficiency, which align with ISO 13485’s goal of enhancing process effectiveness | TPS can support the identification, assessment, and control of risks in the entire product lifecycle as specified in ISO 14971 | To increase quality and efficiency, TPS principles may be included into software development processes | To optimize operational efficiency and improve processes related to electrical medical equipment, TPS can be useful when aligned with IEC 60601-1 |
Risk management | To ensure the identification, assessment, and mitigation of hazards related to medical devices, TPS can be aligned with risk management procedures outlined in ISO 13485 | TPS aligns with the principles and process framework specified in ISO 14971 for effective risk management of medical devices | TPS implementation should consider risk management requirements outlined in IEC 62304 for software-related risks | TPS to support the risk management processes specified in IEC 60601-1 to ensure electrical safety and essential performance of medical electrical equipment |
Documentation and traceability | TPS practices are aligned with ISO 13485’s documentation and traceability requirements for quality management processes | TPS considers the documentation and traceability requirements outlined in ISO 14971 for the management of risk information and decision-making | TPS implementation supports the documentation and traceability needs specified in IEC 62304 for software development activities | TPS practices ensure that documentation and traceability requirements specified in IEC 60601-1 are met for medical electrical equipment |
Regulatory compliance | TPS can be implemented in a manner that does not compromise the organization’s ability to meet regulatory requirements set forth by ISO 13485 | TPS can help ensure compliance with regulatory requirements specified in ISO 14971 for risk management of medical devices | TPS implementation supports compliance with regulatory requirements outlined in IEC 62304 for software used in medical devices | TPS practices can aligned with regulatory requirements stated in IEC 60601-1 for medical electrical equipment |
Training and competence | TPS implementation can consider training needs to ensure employees are competent in meeting ISO 13485 requirements | TPS will consider the training needs outlined in ISO 14971 to ensure personnel are adequately trained in risk management principles and practices | TPS principles can be incorporated into training programs to enhance the competence of personnel involved in software development processes compliant with IEC 62304 | TPS can support the training and competence requirements specified in IEC 60601-1 for personnel involved in medical electrical equipment activities |
Compatibility with standards | Alignment of TPS practices to the standard requirements to ensure no compromise in meeting regulatory and safety requirements | Ensure the identification, assessment, and mitigation of risks associated with medical devices in a way that TPS is aligned with risk management practices specified in ISO 13485 to minimize potential harm to patients and enhance product safety | Ensure no conflict with or compromise the organization’s ability to meet the regulatory and safety requirements mandated by IEC 62304 in TPS implementation | While maintaining safety and regulatory compliance requirements, TPS practices should be in line with those outlined in IEC 60601-1 |
Comparative analysis of best practices and TPS principles: a thorough comparison explores regulatory compliance, quality management, risk mitigation, documentation, and customer-centric approaches; also, as shown in Table 2, it demonstrates how TPS can promote operational excellence and continuous improvement within a medical device company.
Best practices compared to TPS principles analysis
Best practices | Company practices | TPS/Lean application | TPS practices |
Regulatory compliance | Follow safety guidelines, implement quality management | Eliminate waste, ensure compliance, use visual management | Visual organization, error-proofing, waste reduction |
Robust quality management | Implement a comprehensive quality system | Apply continuous improvement, conduct root cause analysis | Continuous improvement, root cause analysis |
Risk management | Integrate risk mgmt. with TPS conduct assessments | Proactively identify risks, implement error-proofing | Proactive risk identification, error-proofing |
Documentation and traceability | Maintain accurate documents, streamline processes | Implement electronic document management | Electronic document management, streamlined processes |
Adherence to regulations | Observe statutory requirements, standardize work processes | Use standardized work instructions aligned with regulations | Standardized work processes, compliance |
Customer-centric approach | Address customer needs, use value stream mapping | Reduce lead times, improve delivery schedules | Value stream mapping, timely delivery |
Cross-functional collaboration | Encourage collaboration, teamwork, and empowerment | Bring representatives together for process improvements | Team empowerment, collaborative process improvements |
Technological adaptation | Keep up with advancements, incorporate lean tools | Use automation and digital solutions for optimization | Automation, digital solutions for efficiency |
TPS principles alignment with sustainability: Table 3 identifies the link between TPS principles and sustainability goals such as minimizing environmental impact, energy efficiency improvement, and stakeholder engagement. International standards guiding the current practices of the medical device company are based on quality management, risk management, and safety requirements. However, such standards are not focused explicitly on addressing sustainability. By integrating TPS philosophies, the company can enhance its operational competitiveness and market positioning while adhering to local regulatory laws. This approach not only mitigates environmental impacts but also fosters long-term sustainability within the business and the industry, ultimately ensuring the delivery of quality and safe products. Table 3 emphasizes that it is not a matter of choosing between TPS principles and sustainability goals; rather, it highlights their interconnection, demonstrating how TPS implementation can facilitate sustainable practices that address environmental, social, and economic challenges.
TPS and sustainability alignment analysis
TPS principles | Sustainability goals |
Continuous improvement | Environmental impact reduction, energy efficiency, waste management, carbon footprint reduction, supply chain sustainability, social responsibility, stakeholder engagement, sustainable innovation, sustainable practices |
Waste reduction | Environmental impact reduction, waste management |
Standardized processes | Environmental impact reduction, waste management, supply chain sustainability, sustainable practices |
Visual management | Stakeholder engagement |
Pull systems | Supply chain sustainability |
Value stream mapping | Environmental impact reduction, supply chain sustainability |
Kaizen | Continuous improvement, sustainable innovation |
Just-in-time production | Energy Efficiency, waste management, supply chain sustainability |
Error proofing | Environmental impact reduction, sustainable practices |
Cross-functional teams | Stakeholder engagement, sustainable practices |
Empowered employees | Social responsibility, sustainable practices |
Customer focus | Social responsibility, stakeholder engagement, sustainable practices |
Correlation study between TPS and sustainability: a study revealed a good link between strategic quality management and lean procedures, leading to sustainable and adaptable company operations[36].
Business model archetypes for sustainability: the diverse archetypes of sustainable business models fall into three categories: technological, social, and organizational. Each category represents a different strategy in value creation with decreased environmental impact. Technological archetypes focus on innovation in the processes of production, efficiency in the use of materials, and energy conversion. Social archetypes focus on stakeholder welfare and community development. Organizational archetypes emphasize the structure and operation of businesses. If adopted, these archetypes can enable the possibility of a better future and enhancement of economic performance for businesses. The eight sustainable archetypes provide a guide for organizations to establish business models aligned with sustainability principles[37].
Industry case studies and lean implementation examples
A study reveals that lean principles significantly benefit the medical device industry, resulting in a 50%-55% reduction in defects, a 48% decrease in cycle time and a 20% reduction in compliance audit efforts[23]. Medtronic Xomed reported a 97% reduction in production lead time, a 54% decrease in order-to-shipment lead time, and a 38% reduction in the cost of shipped products, with additional achievements including a 40% increase in productivity, an 85% reduction in scrap, and a 57% reduction in rework. Baxter Healthcare reduced costs by $1 million with improved inventory turns from 25.5 to 41.9 and experienced a 74% improvement in the overall production lead time[38]. With the use of lean practices and methodologies, the medical device manufacturer may use these cases as benchmarks to improve productivity and overall operational performance.
Alignment of TPS principles with software design and development
The analysis evaluates the implementation of TPS principles to several software design and development phases, including requirements analysis, design, coding, testing, maintenance and continuous improvement. The goal of this integrated strategy [Table 4], is to achieve sustainable software development while maximizing efficiency and enhancing product quality. Table 4 also presents useful applications of TPS principles in the context of software development.
TPS principles and software design and development alignment analysis
TPS | Requirements analysis/spec | Design and architecture | Coding and implementation | Testing and validation | Maintenance and support |
Continuous improvement | Solicit stakeholder feedback | Review and enhance design | Use flexible coding methods | Refine and expand test cases | Identify areas for improvement, apply upgrades |
Waste reduction | Eliminate unnecessary requirements | Minimize design complexities | Eliminate unnecessary code | Implement efficient testing | Optimize maintenance by prioritizing issues |
Standardized processes | Follow standardized approaches | Adhere to design principles | Implement coding standards | Follow standardized testing procedures | Establish maintenance procedures |
Visual management | Use visual techniques for communication | Create visual representations | Utilize visual aids for code understanding | Use visual representations for tracking | Track system performance visually |
Pull systems | Adopt pull-based approach | Implement pull system for design | Apply pull-based development | Implement pull system for testing | Utilize pull-based approach for maintenance |
Value stream mapping | Map value stream to identify waste | Perform VSM for optimization | Apply VSM for coding | Utilize VSM for testing | Apply VSM for maintenance |
Kaizen | Encourage continuous improvement | Apply Kaizen principles | Encourage developers to practice Kaizen | Implement Kaizen principles in testing | Embrace Kaizen for ongoing improvement |
Just-in-time production | Apply JIT principles for delivery | Ensure timely design work | Minimize upfront coding, focus on functionality | Perform testing as needed | Address issues promptly for JIT support |
Error proofing | Apply error-proofing techniques | Incorporate measures in design | Implement techniques in coding | Utilize measures during testing | Implement techniques in maintenance |
Cross-functional teams | Foster collaboration for effective communication | Encourage collaboration between teams | Promote collaboration with developers and testers | Foster collaboration between testers and support teams | Promote collaboration with support teams and customers |
Empowered employees | Encourage ownership and insights | Empower employees in decision-making | Allow autonomy in coding processes | Empower testers for high-quality software | Empower support teams for effective solutions |
Customer focus | Gather and include customer requirements | Align architecture with customer needs | Prioritize customer requirements in coding | Test to meet customer expectations | Provide ongoing support for customer needs |
Software design and development process flowchart
The suggested software development process incorporates TPS principles throughout five phases where it seamlessly integrates with existing processes for continuous improvement in medical device manufacturing. TPS tools assist in the systematic requirement gathering process in Phase 1. Phase 2 concentrates on TPS for standardized work in software design. Phase 3 of the TPS methodology focuses on enhanced implementation and testing to ensure continuous improvement. Phase 4 integrates TPS into verification, validation, and regulatory compliance, and Phase 5 involves external audits and compliance monitoring to ensure long-term improvement [Figure 1].
This strategy guarantees an organized software development process following industry standards. Utilizing TPS tools such as value stream mapping and Kanban reduces lead times and eliminates non-value-added processes. Emphasizing ISO 13485 compliance through the implementation of TPS-based risk analysis techniques such as hazard analysis and failure mode and effects analysis (FMEA) which facilitate problem-solving and productivity to improve customer satisfaction and competitiveness.
Phase 1 integrates TPS into software development, emphasizing the stakeholder engagement, waste elimination and risk analysis [Figure 2]. TPS tools such as value stream mapping, just-in-time, and Kanban enhance process efficiency. Risk management, utilizing TPS principles, focuses on preventive measures, employing tools such as SIPOC, VOC, QFD, FMEA, and hazard analysis. The strategy strives for an efficient software development process that is consistent with customer-focused and preventative philosophy of TPS[39-44].
Figure 2. Phase 1 - process flowcharts of software design and development. Source: the authors’ work.
Phase 2 [Figure 3] standardizes software design architecture, modules, interfaces, and data models, aligning choices with TPS principles. Transparent documentation fosters collaborative understanding. The review process supports continuous improvement, with TPS integration presenting as a framework for clarity and effectiveness.
Figure 3. Phase 2 - process flowcharts of software design and development. Source: the authors’ work.
Phase 3 [Figure 4] employs optimized environments and standardized coding processes to promote TPS in software development and testing. Testing emphasizes early defect detection and continuous improvement, which is in line with TPS’s quality-centric approach.
Figure 4. Phase 3 - process flowcharts of software design and development. Source: the authors’ work.
Phase 4 [Figure 5] includes TPS in the verification and validation of software design, documentation and regulatory submissions. A customer-centric approach assures user acceptability testing, and documentation procedures encourage transparency and accuracy.
Figure 5. Phase 4 - process flowcharts of software design and development. Source: the authors’ work.
Phase 5 [Figure 6] includes external audits, compliance monitoring, and finalization. TPS principles drive systematic compliance, foster continuous improvement, and embed that in the organizational culture. The finalization process reflects TPS principles, ensuring operational excellence and quality assurance in software design and development.
Figure 6. Phase 5 - process flowcharts of software design and development. Source: the authors’ work.
The TPS principles are integrated into the proposed software design and development process flowchart of the medical device company to enhance its efficiency, quality, and compliance. A five-phase structured approach has been outlined, starting from requirement gathering and going up to regulatory submission, incorporating TPS tools such as value stream mapping, risk assessment, and continuous improvement. By aligning with TPS practices, the company will enhance workflows and reduce waste to ensure its overall process meets industry standards such as ISO 13485 and IEC 62304. The flowchart focuses on high-quality medical software devices by detailing the process in systematic and efficient ways that could help improve customer satisfaction and organizational competitiveness.
Measurement and metrics
Metrics are essential in software development for improving processes, planning projects, and measuring product quality[45,46]. The medical device manufacturer may improve quality and efficiency by aligning TPS metrics with software metrics. The emphasis is on waste reduction, cycle time, and value stream analysis, which is integrated with software metrics for code quality, defect density, test coverage and productivity. Figure 7 illustrates how this connection increases customer happiness and streamlines procedures.
Figure 7. TPS and software measurement process and metrics. Source: the authors’ work. TPS: Toyota Production System.
Proposed metrics
The proposed TPS-process metrics offer key performance indicators for evaluating the software development process, including cycle time, lead time, productivity, defect density, code churn, Work in Progress (WIP), throughput, takt time, Andon calls, changeover time, Jidoka, Kanban usage, poka-yoke, production flexibility and overall labor efficiency. These metrics assess speed, quality, resource utilization, workflow management, error prevention, continuous improvement, adaptability and overall resource effectiveness. The proposed TPS-Product Metrics provide indicators for assessing software product attributes and performance, including lines of code, function points, cyclomatic complexity, memory usage, response time, First-Time Yield (FTY), defect rate, scrap rate, productivity per labor hour, product development time and supplier lead time. These metrics offer insights into product complexity, functionality, codebase complexity, memory usage, user experience, quality, efficiency, time-to-market, and supply chain responsiveness.
The proposed TPS-project metrics use schedule variance, effort variance, resource utilization, Kaizen implementation rate, project lead time, and project cost variance. These metrics also provide information on project success, resource allocation, continuous improvement, project duration and budget compliance.
The proposed TPS-Quality Metrics examine defect density, reliability, test coverage, maintainability, usability, bottleneck rate, Overall Equipment Effectiveness (OEE), and equipment downtime. These metrics measure software durability, accuracy of tests, reliability, maintainability, usability, overall efficiency, bottleneck identification and equipment downtime.
The proposed TPS-customer metrics provide measures such as net promoter score (NPS), customer feedback ratings, customer lead time, customer satisfaction, and customer returns. These metrics evaluate customer loyalty, sentiment, order fulfillment time, satisfaction levels, and return rates, promoting consumer relationships, loyalty and long-term success [Figure 7 and Table 5].
Proposed TPS metrics
Details | Measurement | ||
TPS process metrics | Cycle time | Time to complete a task | End time - start time |
Lead time | Time from task initiation to completion | End time - start time | |
Productivity | Work completed per unit of time or effort | Work completed/Time or effort expended | |
Defect density | Defects per unit of code size | Number of defects/Code size | |
Code churn | Frequency of code changes | Number of code changes over time | |
WIP | Tasks in progress | Count of tasks in progress | |
Throughput | Rate of work completion | Units completed/Time taken | |
Takt time | Time of production per required rate | Production time/Required rate | |
Andon calls | Frequency of issue alerts | Count of Andon calls | |
Changeover time | Time to switch production processes | End time - start time | |
Jidoka usage | Adoption of autonomation | Measure utilization of Jidoka | |
Kanban usage | Effectiveness of work-in-progress control | Adherence to Kanban principles | |
Poka-yoke (Error-proofing) | Number of error-proofing mechanisms | Count of error-proofing mechanisms | |
Production flexibility | Ability to adapt to changes | Measure adaptability and response time | |
Overall labor efficiency | Overall labor efficiency | (Total actual labor hours)/(total available labor hours) × 100 | |
TPS product metrics | LOC | Total lines of code in the software | Count of total lines of code |
Function points | Measure of software functionality | Calculate based on user interactions, data inputs/outputs, and processing requirements | |
Cyclomatic complexity | Codebase complexity measure | Measure the number of independent paths | |
Memory usage | Memory consumed during execution | Measure memory utilization during execution | |
Response time | Software reaction speed | Measure the time from user action to software response | |
FTY | Percentage of defect-free products on the first attempt | (Defect-free products/Total products) × 100 | |
Defect rate | Number of defects in a time period | Number of defects/Total products | |
Scrap rate | Proportion of discarded products due to defects | (Defective products/Total produced Products) × 100 | |
Productivity per labor hour | Output per labor hour | Total output/Total labor hours | |
Product development time | Time from product conception to launch | Time of product launch - time of product conception | |
Supplier lead time | Time for suppliers to provide materials | End time - start time | |
TPS project metrics | Schedule variance | Actual vs. planned schedule | Schedule variance = planned schedule - actual schedule |
Effort variance | Disparity between estimated and actual effort | Effort variance = estimated effort - actual effort | |
Resource utilization | Efficiency of resource allocation | (Actual resource usage/Total available resources) × 100% | |
Kaizen implementation Rate | Rate of implemented Kaizen initiatives | (Implemented Kaizen initiatives/Total Kaizen initiatives) × 100 | |
Project lead time | Time to complete a project | Project completion date - project start date | |
Project cost variance | Budgeted vs. actual project costs | Actual project cost - budgeted project cost | |
TPS quality metrics | Defect density | Defect rate per code size or functionality | (Number of defects)/(size of code or functionality) |
Test coverage | Proportion of code subjected to automated testing | (Lines of code covered by tests/Total lines of code) × 100% | |
Reliability | Consistency of software performance | Measure the frequency of failures over a specified period | |
Maintainability | Ease of modifying or extending software | Measure factors like code readability, complexity, and ease of change | |
Usability | Ease of use and user satisfaction | Measure through user feedback surveys and usability testing | |
OEE | Equipment efficiency gauge | OEE = availability × performance × quality | |
Bottleneck rate | Rate of bottleneck limiting production output | (Output of bottleneck process/Total output) × 100 | |
Equipment downtime | Non-operational time due to maintenance or breakdowns | End time - start time | |
TPS customer metrics | NPS | Customer loyalty and willingness to recommend | Calculate based on customer surveys |
Customer feedback ratings | Ratings and feedback about the product | Collect feedback through surveys or feedback mechanisms | |
Customer lead time | Time to fulfill customer orders | End time - start time | |
Customer satisfaction | Level of satisfaction expressed by customers | (Number of satisfied customers)/(Total number of customers) × 100 | |
Customer returns | Rate of product returns due to defects | (Number of products returned by customers)/(Total number of products sold to customers) |
Proposed key phase metrics
The proposed metrics play a pivotal role in systematically evaluating and optimizing each phase of software design and development. To promote effective development, the metrics in Phase 1 placed a significant emphasis on effective requirement gathering with the implementation of TPS principles including comprehensive risk analysis.
Moving into Phase 2, the metrics shift their focus to the creation of precise and efficient software design specifications. Evaluating code quality, testing effectiveness, and compliance to configuration management requirements where Phase 3 and Phase 4 metrics adhere to software development processes, testing and verification/validation activities efficiently.
Advancing to Phase 5, the metrics extend their scope to cover external audits, ensuring compliance, and finalizing design and development aspects. Monitoring deployment success, audit readiness, compliance adherence, corrective actions and deployment success rates are all considered essential factors. At the same time, ensuring that all quality and regulatory requirements are satisfied is the primary objective.
In essence, these metrics collectively function as a comprehensive tool to optimize the entire software development process. The application guarantees compliance with standards and regulations while concurrently enhancing the quality and performance of the final software product; refer to Table 6 for a detailed overview of the proposed metrics for each phase of software design and development.
Proposed phases metrics for software design and development
Details | Measurement and evaluation | ||
Phase 1 metrics | Gather requirements for software design and development | ||
Stakeholder Interviews | Comprehensive gathering of requirements | Count of conducted interviews | |
Time to analyze user needs | Efficiency in defining requirements | Average time for analysis | |
Compliance requirements | Alignment with regulations and standards | Count of identified requirements | |
Prioritized requirements | Focus on critical development needs | Count of prioritized requirements | |
Apply TPS principles to improve process efficiency and quality | |||
Identified waste and inefficiencies | Quantify areas for improvement | Count of identified waste | |
Non-value-added activities | Measure process streamlining | Percentage eliminated | |
Time reduction in workflows | Impact of process redesign on efficiency | Average time reduction | |
TPS implementation rate | Adoption of lean practices | Percentage implemented | |
Visual mgmt. and standardized work | Adherence to standardized processes | Percentage implemented | |
Perform risk analysis and management | |||
Identified risks | Assessment of potential threats | Count of identified risks | |
Time for risk assessment | Efficiency in risk management efforts | Average time for assessment | |
Risk control measures | Actions to minimize identified risks | Count of implemented measures | |
Risk management plan completion | Comprehensive risk mitigation planning | Completion rate of the plan | |
Phase 2 metrics | Develop software design specifications | ||
Defined system architecture | Comprehensiveness of system definition | Count of defined architecture and modules | |
Time for detailed design specifications | Efficiency in specification creation | Average time for detailed specifications | |
Accuracy of design inputs | Precision and traceability | Percentage of accurate design inputs | |
Proper documentation of design outputs | Completeness of design documentation | Percentage of properly documented outputs | |
Design review cycle time | Efficiency of review and approval | Time for review and approval | |
Design requirements traceability | Alignment of design outputs with req. | Percentage of traceability coverage | |
Identified and resolved design issues | Tracking and addressing challenges | Count of issues identified and resolved | |
Percentage of design changes | Scope of modifications during development | Percentage of design changes | |
Phase 3 metrics | Implement software development processes | ||
Code quality metrics | Evaluate code quality (complexity, duplication) | Measurement of code complexity, duplication, etc. | |
Code reviews conducted | Ensure code quality through peer review | Count of code reviews conducted | |
Version control activity metrics | Track changes and maintain code integrity | Measurement of version control activity (e.g., commits, merges) | |
Documentation completeness | Verify comprehensiveness of software documentation | Measurement of documentation completeness | |
Percentage of code and modules developed | Track progress in code development | Percentage of code and modules developed | |
Effectiveness of code reviews and peer testing | Assess impact on code quality | Measurement of defects identified and fixed during reviews and testing | |
Compliance with configuration management | Ensure adherence to best practices | Compliance assessment with configuration management practices | |
Perform unit testing, integration testing, system testing/Verify and validate software design and functionality (Phase 4) | |||
Test coverage | Measure proportion of software covered by tests | Percentage of test coverage | |
Defect density | Quantify defects per unit of software size | Number of defects per unit of software size | |
Test pass rate | Track success rate of test cases | Percentage of test cases passed | |
Test execution time | Evaluate efficiency of test execution | Measurement of test execution time | |
Test coverage achieved | Assess comprehensiveness of testing | Measurement of code coverage, requirement coverage | |
Integration tests and defects | Track progress and defects in integration testing | Count of integration tests executed and defects identified | |
Test result analysis metrics | Assess overall test results and defect leakage | Measurement of pass/fail rate, defect leakage rate | |
Phase 4 Metrics | Review and approve documentation/Prepare regulatory submission | ||
Document version control | Track document revisions and maintain version history | Monitoring of document revisions and version control activity | |
Compliance audit findings closure time | Measure time to address and resolve audit findings | Evaluation of time taken to close compliance audit findings | |
Regulatory submission approval time | Evaluate duration to obtain regulatory approvals | Assessment of duration to get regulatory submissions approved | |
Stakeholder approval cycle time | Assess efficiency of obtaining approvals | Measurement of time taken to obtain approvals from stakeholders | |
Phase 5 Metrics | Conduct external audits and inspections | ||
Preparedness for external audits | Assess readiness for external audits or inspections | Evaluation of preparedness for audits or inspections | |
Compliance with standards | Verify adherence to relevant standards and regulations | Assessment of compliance with standards and regulations | |
Number of findings identified | Track and address issues or non-compliances | Count of findings identified and addressed during audits or inspections | |
Effectiveness of corrective and preventive actions | Evaluate impact and efficiency of actions taken | Evaluation of effectiveness of corrective and preventive actions | |
Ensure compliance with standards | |||
Assessment and Improvement of Standard Compliance | Assess level of compliance and identify improvement areas | Measurement of standard compliance and improvement activities | |
Implementation of quality management systems | Establish and maintain effective quality management systems | Evaluation of implementation and effectiveness of quality management systems | |
Monitoring and reporting of compliance status | Track and report organization’s compliance status | Regular monitoring and reporting of compliance status with relevant standards | |
Finalize software design and development | |||
Deployment success rate | Measure rate of successful software deployments | Evaluation of proportion of successful software deployments | |
Production system uptime | Assess availability and reliability of production system | Measurement of time the production system remains operational | |
Response time | Evaluate the time taken for software to respond to user actions | Monitoring of time taken for software to respond to user actions | |
Number of incidents and problem resolution time | Track and address incidents and measure time to resolve problems | Count of incidents and evaluation of time taken to resolve problems | |
Customer-reported issues and resolution time | Track customer-reported issues and assess the time to resolve | Monitoring of customer-reported issues and measurement of time to resolve |
Framework and implementation strategies
The framework and implementation methodologies provided in this research seek to assist manufacturers of medical devices in adopting and implementing lean manufacturing strategies based on TPS principles. The framework considers specific challenges and peculiarities of the company alongside the software design and development area.
Existing frameworks for lean implementation
Lean frameworks highlight the need of adapting TPS strategies to specific company needs, which provides beneficial information for small and medium-sized organizations (SMEs).
Key findings from various studies on lean implementation frameworks for SMEs highlight the significance of change management in driving lean transformation[47], integrating total productive maintenance (TPM), Six Sigma, and lean for holistic operational excellence[48], and offering comprehensive frameworks guiding the structured adoption of lean practices[49]. Detailed frameworks emphasize adaptation for SME challenges in line with Plan-Do-Check-Act (PDCA) cycles[50]; some focus on monitoring, regulating, and aligning with essential success factors for sustainable implementation[51]. Theoretical frameworks can also strengthen SME commitment by offering practical lean manufacturing methods with defined performance metrics. The frameworks provide a structured approach for implementing lean principles, leading to improved efficiency, reduced waste, and enhanced overall performance. [52,53,54]. In another study, a Sustainable Lean Production Framework integrates lean Six Sigma concepts to satisfy sustainability goals[55]. Additionally, a comprehensive framework was proposed to guide organizations, across industries, in overcoming lean implementation barriers and successfully integrating lean principles into their operations. This framework consolidates various lean perspectives, including barriers, principles, tools, and performance measures[56].
Various TPS Frameworks, with the guiding principles and practices of TPS, emphasize competitiveness through productivity and waste elimination for cost reduction and growth[57]. These frameworks focus on quality, efficiency and employee development beginning with small group activities and leadership support to meet organizational objectives. Flexible workforce and cost-saving strategies are critical factors.
A sample TPS roadmap for a medical device company
A specific TPS roadmap tailored to a medical device company is introduced, drawing inspiration from TPS principles. The roadmap in Figure 8 depicts a strategy that will assist the organization in managing challenges, strengthening competitiveness and embracing sustainable practices. The primary goal is to apply TPS concepts to minimize waste, increase efficiency in software design and development, provide high-quality products, and achieve long-term success. The roadmap includes specific milestones that concentrate on unique elements of TPS.
Figure 8. TPS roadmap strategy for a medical device company. Source: the authors’ work. TPS: Toyota Production System.
The roadmap shown in Figure 8 serves as a strategic guide for the company to adapt to TPS principles progressively, promoting a culture of continuous improvement and achieving improvements in productivity, quality, and customer satisfaction.
Exploring simulation tools for testing and constraints
Simulation tools have become indispensable for analyzing and optimizing complex processes across various domains, including software systems and project management. Notable studies have explored topics such as software development, resource allocation, and cost overruns, providing valuable insights into strategic project management, understanding project failures, and overseeing intricate initiatives.
The use of simulation tools has become essential in organizing and evaluating complex processes in a variety of fields such as software systems and project management. Relevant subject matter, including software development, resource allocation, and cost overruns, has been the focus of notable studies, which offer perceptions into strategic project management, comprehending project failures, and overseeing intricate initiatives[58-68]. The integration of TPS principles in software development to improve business performance and sustainability is a special area of interest for simulation practitioners, who can use these findings to create efficient methods for implementation testing and experimentation. The simulation model aims to assess TPS impact, identify bottlenecks and evaluate efficiency while considering variables such as lines of code, staff expertise, productivity, project completion, and success. Among the constraints are the requirements for modeling expertise and the limitations of the AnyLogic software version that is currently used[69,70]. The study focuses on simulation as an exploratory tool in the implementation approach of the company.
RECOMMENDATION AND CONCLUSION
The recommendations and conclusions consider the objectives of the research, analysis, and findings. Exploring TPS integration for enhanced efficiency, quality, and sustainability in the software design, development, and manufacturing processes of a medical device company. Recommendations focus on TPS process improvement, integration, sustainability, and continuous improvement.
Recommendations
TPS process improvement and manufacturing streamlining
● Utilize TPS principles
- Use of visual management, just-in-time (JIT) manufacturing and task boards for transparency.
- Employ value stream mapping, Kanban and workshops for better understanding.
- Measure progress with metrics to identify bottlenecks, save time, and reduce waste.
● Process standardization
- Forming cross-functional teams that can define procedures and thoroughly document processes.
- Conduct regular reviews and metrics to ensure consistency in software testing.
- Track progress through TPS team meetings and monthly assessments for seamless integration and continuous improvement by seeking feedback and refining the plan.
● Streamlining manufacturing complexities
- Utilize specialized teams for TPS tools, such as PDCA and value stream mapping, and task groups to handle production difficulties and ensure continuous improvement and compliance with regulations.
- Regularly review and assess metrics for efficient team establishment and improved risk assessment rates.
Integration of sustainable practices
● Embrace sustainable practices
- Integrate sustainable practices aligned with TPS principles into software development.
- Focus on awareness, relevant practices, workflow integration, and continuous monitoring.
- Monitor and assess learning session engagement for enhanced efficiency, waste reduction and continuous improvement.
Performance metrics and continuous improvement
● Establishing performance metrics
- Define efficiency, quality, satisfaction, and sustainability metrics aligned with TPS tools.
- Sustain departmental alignment, measure customer satisfaction with the NPS, analyze data using PDCA, and conduct regular reviews that can demonstrate performance by immediately adjusting to new requirements and completing audits.
● Promoting a culture of continuous improvement
- Encourage cross-functional collaboration and track participation rates.
- Establish open channels of communication and conduct frequent training sessions such as weekly “improvement huddles" to increase collaboration, reduce production cycle times and ensure continuous improvement through regular review and assessment.
Leadership and employee empowerment
● Leadership commitment
- Initiate top-level communication emphasizing TPS principles and sustainable practices.
- Enlist management as role models, integrate TPS into strategic planning, and ensure continuous improvement.
● Empowerment of employees
- Launch a communication campaign to introduce TPS principles, establish idea-sharing platforms, develop training programs and implement a recognition system.
- Conduct regular assessments to guarantee increasing engagement, improved competencies and sustained motivation.
Strategic partnerships
● Collaborate with industry experts
- Identify experts with TPS implementation experience and develop a collaboration strategy.
- Build partnerships, integrate expert opinions into the TPS strategy and maintain continuous engagement that encourages efficiency and continuous improvement.
Future studies and evaluation
● Improved experimentation studies
- Apply TPS tools and principles to enhance software development studies to ensure accurate results through validation and statistical analysis.
- Demonstrate success through improved research, methodologies, clear TPS distinctions, continuous improvement and data analysis techniques.
Conclusion
This study significantly strengthens software design and development processes by effectively integrating TPS principles and sustainability measures into medical device manufacturing. It successfully uncovered various advantageous outcomes and benefits leading to an extensive and systematic framework and a robust implementation strategy. The harmonious integration of ISO standards and TPS not only ensures operational excellence and efficiency but also contributes to heightened customer satisfaction.
The strategic analysis conducted in this study delves into the challenges, opportunities and advantages associated with applying TPS principles in software design, aligning the strategy with the dynamic landscape of the industry. The proposed frameworks with the specifically developed metrics together with the adoption of TPS principles provide a well-defined roadmap. The strategy emphasizes leadership commitment, employee empowerment and continuous improvement. The inclusion of experimental testing adds invaluable insights, providing real-world validation that is indispensable for effective implementation. In summary, an essential driver for achieving software design excellence involves the implementation of TPS principles and sustainable practices. The study provides not only useful insights but also practical recommendations to foster growth, enhance operational efficiency, and sustain competitiveness in the ever-evolving landscape of software development.
Future research
Future study directions involve looking at the long-term impact, financial and economic implications, ethics, supplier collaboration, and potential challenges associated with TPS implementation. Longitudinal studies and economic evaluations are required to ensure long-term effectiveness and financial benefits. Comprehensive study alternatives include investigating ethical factors, collaborating with suppliers and developing simulation models.
Further research into TPS integration across the manufacturing process, as well as evaluations of flexibility and scalability, contributes to sustained growth. This thorough study establishes a framework to address the evolving challenges faced by the dynamic software design and development industry.
DECLARATIONS
Acknowledgments
Sincere appreciation is extended to the Asian Institute of Management (AIM) through the Executive MBA program, which has been a major factor in completing this research study. Special thanks to Dr. Raul Rodriguez, EMBA Program Director, for his invaluable and unwavering support.
Authors’ contributions
Conceived the study, conducted analysis, and interpreted the data: Lim LR
Contributed to the research design and provided mentorship and guidance: Tan AWK
Availability of data and materials
Data used for analysis, including information from Statista, are cited in the references. Access to the Statista repository requires a subscription.
Financial support and sponsorship
None.
Conflicts of interest
Both authors declared that there are no conflicts of interest.
Ethical approval and consent to participate
Not applicable.
Consent for publication
Not applicable.
Copyright
© The Author(s) 2024.
REFERENCES
1. Socconini L. Lean Manufacturing. Step by step. Marge Books. 2021. Available from: https://www.perlego.com/%20book/2695700/lean-manufacturing-step-by-step-pdf. [Last accessed on 25 Sep 2024].
2. Dennis P. Lean production simplified: a plain-language guide to the world’s most powerful production system. 3rd ed. CRC Press; 2017. Available from: https://books.google.co.th/books/about/Lean_Production_Simplified.html?id=Lx-vCgAAQBAJ&redir_esc=y. [Last accessed on 23 Sep 2024].
3. Womack JP, Jones DT, Roos D. The machine that changed the world: the story of lean production--Toyota’s secret weapon in the global car wars that is now revolutionizing world industry. Simon and Schuster; 2007. Available from: https://books.google.co.th/books?id=9NHmNCmDUUoC&printsec%20=frontcover&source=gbs_ge_summary_r&cad=0#v=onepage&q&f=false. [Last accessed on 24 Sep 2024].
4. Liker JK, Hoseus M. Toyota culture: the heart and soul of the toyota way. New York: McGraw-Hill Publishing; 2008. Available from: https://books.google.co.th/books/about/Toyota_Culture_%20PB.html?id=7Y6jjkmqByQC&redir_esc=y. [Last accessed on 24 Sep 2024].
5. Liker JK. The Toyota way: 14 management principles from the world’s greatest manufacturer, 2nd edition. New York: McGraw-Hill; 2021. Available from: https://www.accessengineeringlibrary.com/content/book/9781260468519. [Last accessed on 25 Sep 2024].
6. Coetzee R, Van Dyk L, Van der Merwe K. Lean implementation strategies: how are the Toyota Way principles addressed? S Afr J Ind Eng 2016;27:79-91. Available from: https://journals.co.za/doi/abs/10.7166/27-3-1641. [Last accessed on 24 Sep 2024]
7. Watanabe K, Stewart TA, Raman AP. Lessons from Toyota’s long drive: a conversation with Katsuaki Watanabe. Available from: https://hbsp.harvard.edu/product/R0707E-PDF-ENG. [Last accessed on 25 Sep 2024].
8. Toma SG, Catana S, Grădinaru C. Decoding the lean enterprise. 2022. Available from: https://stec.univ-ovidius.ro/html/anale/RO/2022-2/Section%204/38.pdf. [Last accessed on 24 Sep 2024].
9. Sreekumar A. (2024). System dynamics modelling of organizational culture transformation: a study of the organizational and technical factors that affect the implementation of Toyota production system in organizations. 2024. Available from: https://dspace.mit.edu/bitstream/handle/1721.1/155610/sreekumar-anupsk-sm-sdm-2024-thesis.pdf?sequence=1&isAllowed=y. [Last accessed on 24 Sep 2024]
10. Liker JK. The Toyota way fieldbook. McGraw Hill; 2005. Available from: https://www.researchgate.net/publication/271764079_The_Toyota_Way_Fieldbook. [Last accessed on 24 Sep 2024].
11. Wada K. The evolution of the Toyota Production System. Berlin, Heidelberg, Germany: Springer; 2020. Available from: https://link.springer.com/book/10.1007/978-981-15-4928-1. [Last accessed on 24 Sep 2024].
12. Dauda JA, Ajayi S, Omotayo T, Oladiran OO, Ilori OM. Implementation of lean for small-and medium-sized construction organisational improvement. Smart Sustain Built Environ 2024;13:496-511.
13. Liker JK, Convis GL. The Toyota way to lean leadership: achieving and sustaining excellence through leadership development, 1st edition. New York: McGraw-Hill Education; 2012. Available from: https://www.accessengineeringlibrary.com/content/book/9780071780780. [Last accessed on 24 Sep 2024].
14. Subramanya SR. Adapting some rules and principles of TPS (Toyota Production System) to software development. 2012. Available from: https://citeseerx.ist.psu.edu/document?repid=rep1&type=pdf&doi=dc260e1045e69f3c6245e59a7e4001466278d777. [Last accessed on 24 Sep 2024].
15. Furugaki K, Takagi T, Sakata A, Okayama D. (2007). Innovation in software development process by introducing Toyota Production System. Available from: https://www.fujitsu.com/global/documents/about/resources/publications/fstj/archives/vol43-1/paper16.pdf. [Last accessed on 24 Sep 2024]
16. Dalla LOFB. Lean Software Development Practices and Principles in Terms of Observations and Evolution Methods to increase work environment productivity. 2020. Available from: https://www.iiardjournals.org/get/IJEMT/VOL.%206%20NO.%201%202020/Lean%20Software%20Development%20practices.pdf. [Last accessed on 24 Sep 2024].
17. Ibrahim SRA, Yahaya J, Salehudin H, Bakar NH. Towards green software process: a review on integration of sustainability dimensions and waste management. In: 2019 International Conference on Electrical Engineering and Informatics (ICEEI); 2019 Jul 9-10; Bandung, Indonesia. IEEE; 2020. pp. 128-33.
18. Al-Emran M, Griffy-Brown C. The role of technology adoption in sustainable development: overview, opportunities, challenges, and future research agendas. Technol Soc 2023;73:102240.
19. Mishra A, Alzoubi YI. Structured software development versus agile software development: a comparative analysis. Int J Syst Assur Eng Manag 2023;14:1504-22.
20. Di Pompeo D, Tucci M. Harnessing genetic improvement for sustainable software architectures. In: 2024 IEEE 21st International Conference on Software Architecture Companion (ICSA-C); 2024 Jun 4-8; Hyderabad, India. IEEE; pp. 248-9.
21. Prasad S, Khanduja D, Sharma SK. An empirical study on applicability of lean and green practices in the foundry industry. J Manuf Technol Manag 2016;27:408-26.
22. Anderson KM, Grasman SE, Ayoub K, Introne S, Smithwick K. Using lean product development to speed time to market for medical devices. Available from: https://www.researchgate.net/publication/289115860_Using_lean_product_development_to_speed_time_to_market_for_medical_devices. [Last accessed on 24 Sep 2024].
23. Foley I, McDermott O, Rosa A, Kharub M. Implementation of a lean 4.0 project to reduce non-value add waste in a medical device company. Machines 2022;10:1119.
24. Nikolić J, Dašić M, Đapan M. Smed as an indispensable part of lean manufacturing in the small and medium enterprises. Int J Qual Res 2023;17:255-70.
25. Chay TF, Xu YC, Tiwari A, Chay FS. Towards lean transformation: the analysis of lean implementation frameworks. J Manuf Technol Manag 2015;26:1031-52.
26. Pearce D, Dora M, Wesana J, Gellynck X. Determining factors driving sustainable performance through the application of lean management practices in horticultural primary production. J Clean Prod 2018;203:400-17.
27. Hastono H, Affandi A, Sunarsi D. Implementation of lean management principles for operational efficiency. Implikasi J Man Sumber Daya Manusia 2023;1:104-7.
28. Okpala C, Nwamekwe CO, Ezeanyim OC. The implementation of kaizen principles in manufacturing processes: a pathway to continuous improvement. Int J Eng Inven 2024;13:116-24. Available from: https://hal.science/hal-04669397/. [Last accessed on 24 Sep 2024]
29. Stauryla E. KANBAN implementation in manufacturing industries. 2021. Available from: https://vb.vgtu.lt/object/elaba:97399829/. [Last accessed on 24 Sep 2024].
30. Schwaber K, Sutherland J. The scrum guide. The definitive guide to scrum: the rules of the game. 2017. Available from: https://scrumguides.org/docs/scrumguide/v2020/2020-Scrum-Guide-US.pdf. [Last accessed on 24 Sep 2024].
31. Statista Market Insights. Orthopedic devices -Worldwide - Key players. 2023. Available from: https://www.statista.com/outlook/hmo/medical-technology/medical-devices/orthopedic-devices/worldwide#key-players. [Last accessed on 24 Sep 2024].
32. Statista Market Insights. Orthopedic devices - Southeast Asia. 2023. Available from: https://www.statista.com/outlook/hmo/medical-technology/medical-devices/orthopedic-devices/southeast-asia. [Last accessed on 24 Sep 2024].
33. Statista Market Insights. Orthopedic devices - Worldwide. 2023. Available from: https://www.statista.com/outlook/hmo/medical-technology/medical-devices/orthopedic-devices/worldwide. [Last accessed on 24 Sep 2024].
34. Percentage of senior managers in global medical device companies that faced select challenges in 2020. 2020. Available from: https://www.statista.com/statistics/938852/challenges-for-medical-device-company-managers-global/. [Last accessed on 24 Sep 2024].
35. In your opinion, how effective is the FDA in regulating new medical device technology? 2017. Available from: https://www.statista.com/statistics/870069/fda-effectiveness-in-medical-device-technology-regulation/. [Last accessed on 24 Sep 2024].
36. Gamad LC. Governing company performance agility through strategic quality management principles and lean business practices: evidences and challenges for the business industry in the Philippines. Rev Integr Bus Econ Res 2019;8:17. Available from: https://buscompress.com/uploads/3/4/9/8/34980536/riber_8-4_02_h18-014_17-56.pdf. [Last accessed on 24 Sep 2024]
37. Bocken NMP, Short SW, Rana P, Evans S. A literature and practice review to develop sustainable business model archetypes. J Clean Prod 2014;65:42-56.
38. Tayne EA. How medical device manufacturing organizations apply kaizen and lean philosophies for continuous improvement. 2010. Available from: https://www.proquest.com/docview/375516557/. [Last accessed on 24 Sep 2024].
39. American Society for Quality (ASQ). Quality resources: the world’s most comprehensive library of quality resources. 2023. Available from: https://asq.org/quality-resources. [Last accessed on 24 Sep 2024].
40. Cudney EA, Furterer S, Dietrich D. Lean systems: applications and case studies in manufacturing, service, and healthcare. CRC Press; 2013.
41. El-Haik BS, Mekki KS. Medical device design for six sigma: a road map for safety and effectiveness. John Wiley & Sons; 2008.
42. Marques P, Reis JCG, Sá JC, Mateus RJG, Pinto FMRDCS. (2024). Lean, six sigma and iso management systems standards: an integration framework. (in: Portuguese) Available from: https://comum.rcaap.pt/handle/10400.26/51359. [Last accessed on 24 Sep 2024].
43. Tague NR. Quality toolbox. 2023. Available from: https://www.mencap.org.uk/sites/default/files/2021-04/pdf-quality-toolbox-nancy-r-tague-pdf-download-free-book-c8497d3.pdf. [Last accessed on 24 Sep 2024].
44. Soares V, Navas HVG. New model for creating innovative solutions in continuous improvement environments. Int J Syst Innov 2023;7:10-29.
45. Farooq SU, Quadri SMK, Nesar A. Software measurements and metrics: Role in effective software testing. Int J Eng Sci Technol 2011;3:671-80. Available from: https://www.researchgate.net/publication/50392202_SOFTWARE_MEASUREMENTS_AND_METRICS_ROLE_IN_EFFECTIVE_SOFTWARE_TESTING. [Last accessed on 24 Sep 2024]
46. Sharma S, Srinivasan S. A survey on software design based and project based metrics. Int J Comput Theory Eng 2022;14:54-61. Available from: http://www.ijcte.com/vol14/1310-G2180.pdf. [Last accessed on 24 Sep 2024]
47. AlManei M, Salonitis K, Tsinopoulos C. A conceptual lean implementation framework based on change management theory. Procedia cirp 2018;72:1160-5.
48. Okhovat MA, Ariffin MKAM, Nehzati T, Hosseini SA. Development of world class manufacturing framework by using six-sigma, total productive maintenance and lean. Sci Res Essays 2012;7:4230-41. Available from: https://academicjournals.org/article/article1380728103_Okhovat%20et%20al.pdf. [Last accessed on 24 Sep 2024]
49. Belhadi A, Touriki FE, El fezazi S. A framework for effective implementation of lean production in small and medium-sized enterprises. J Ind Eng Manag 2016;9:786-810.
50. Chong JY, Perumal A. Conceptual framework for lean manufacturing implementation in SMEs with PDCA approach. In: Jamaludin Z, Ali Mokhtar MN, editors. Intelligent manufacturing and mechatronics. SympoSIMM 2019. Lecture notes in mechanical engineering. Singapore: Springer; 2019. pp. 410-8.
51. Mostafa S, Dumrak J, Soltan H. A framework for lean manufacturing implementation. Prod Manuf Res 2013;1:44-64.
52. Siegel R, Antony J, Govindan K, Garza-Reyes JA, Lameijer B, Samadhiya A. A framework for the systematic implementation of Green-Lean and sustainability in SMEs. Prod Plan Control 2024;35:71-89.
53. Al-Swidi AK, Al-Hakimi MA, Al-Hattami HM. Sustain or perish: how lean manufacturing practices predict the sustainable performance of manufacturing SMEs? A moderated mediation analysis. Int J Lean Six Sigma 2024;Online ahead of print.
54. Kosasih W, Pujawan IN, Karningsih PD. Integrated lean-green practices and supply chain sustainability for manufacturing SMEs: a systematic literature review and research agenda. Sustainability 2023;15:12192.
55. Tiwari P, Sadeghi JK, Eseonu C. A sustainable lean production framework with a case implementation: practice-based view theory. J Clean Prod 2020;277:123078.
56. Aadithya BG, Asokan P, Vinodh S. Lean manufacturing in fabrication industry: literature review and framework proposal. Int J Qual Reliab Manag 2023;40:1485-517.
57. Monden Y. Toyota Production System: an integrated approach to just-in-time, 4th edition. New York: CRc Press; 2011.
58. Calderon-Tellez JA, Bell G, Herrera MM, Sato C. Project management and system dynamics modelling: time to connect with innovation and sustainability. Syst Res Behav Sci 2024;41:3-29.
59. Ruiz M, Orta E, Sánchez J. A simulation-based approach for decision-support in healthcare processes. Simul Model Pract Theory 2024;136:102983.
60. Hasan MR, Molla S, Siddique IM. Next-gen production excellence: a deep simulation perspective on process improvement. J Mech Mach Des Manuf 2024;6:7-20.
61. Krasko AS, Kovalev AA, Filin MA, Mukhin KS, Baranova NS. Optimization of Workpiece maintenance discipline through simulation modeling of the functioning of automated technological complexes. J Mach Manuf Reliab 2023;52:S194-202.
62. Li MH, Indriastuti S. A system dynamics approach of a laptop manufacturing supply chain operation simulation modelling using AnyLogic. 2023. Available from: https://chooser.crossref.org/?doi=10.1049%2Ficp.2023.3343. [Last accessed on 24 Sep 2024].
63. Longo F, Nervoso A, Nicoletti L, Solina V, Solis AO. Modeling & Simulation for assessing production policies: a real case study from a manufacturing company in Canada. Procedia Comput Sci 2024;232:1192-200.
64. Miedviedieva N, Bahrii M. Optimization of the simulation process of product supply from the manufacturer. Sci Based Technol 2023;57:93-100. (in Ukrainian).
65. Naciri L, Gallab M, Soulhi A, Merzouk S, Di Nardo M. Modeling and simulation: a comparative and systematic statistical review. Procedia Comput Sci 2024;232:242-53.
66. Paape N, Van Eekelen JA, Reniers MA. Review of simulation software for cyber-physical production systems with intelligent distributed production control. Int J Comput Integr Manuf 2024;37:589-611.
67. Rösen C. Analysis of simulation modeling: a study of simulation modeling programs in the context of manufacturing processes. 2024. Available from: https://www.diva-portal.org/smash/get/diva2:1886077/FULLTEXT01.pdf. [Last accessed on 24 Sep 2024]
68. Seyyedrezaei MA, Alvandi M. Improving the manufacturing process using Industry 4.0 tool: a simulation-based approach. Int J Process Manag Bench 2023;14:52-83.
69. Popkov T. Business is a field for experiments. But it’s best to run them on simulation models. Available from: https://www.anylogic.com/resources/articles/business-is-a-field-for-experiments-but-it-s-best-to-run-them-on-simulation-models/. [Last accessed on 24 Sep 2024].
70. Stojkovik N, Lazarova LK, Stojanova A, Miteva M, Zlatanovska B, Kocaleva M. Application of agent-based modelling in learning process. Informatica 2024;48:11-20. Available from: https://informatica.si/index.php/informatica/article/viewFile/4086/2720. [Last accessed on 24 Sep 2024]
Cite This Article
How to Cite
Download Citation
Export Citation File:
Type of Import
Tips on Downloading Citation
Citation Manager File Format
Type of Import
Direct Import: When the Direct Import option is selected (the default state), a dialogue box will give you the option to Save or Open the downloaded citation data. Choosing Open will either launch your citation manager or give you a choice of applications with which to use the metadata. The Save option saves the file locally for later use.
Indirect Import: When the Indirect Import option is selected, the metadata is displayed and may be copied and pasted as needed.
About This Article
Copyright
Data & Comments
Data
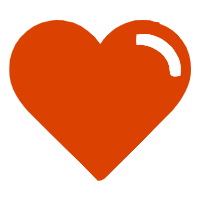
Comments
Comments must be written in English. Spam, offensive content, impersonation, and private information will not be permitted. If any comment is reported and identified as inappropriate content by OAE staff, the comment will be removed without notice. If you have any queries or need any help, please contact us at [email protected].