Fluid-structure analysis and prediction of rectangle duct design: a case of air supply system
Abstract
Since the fluid-structure analysis is widely applied to assess the fluid flow state of electromechanical products, the design of fluid-structure becomes crucial in improving product performance and efficiency. In this study, a numerical prediction method for fluid-structure parameters is proposed to evaluate and optimize the flow state and quality of the flow field in a rectangular duct system. The modular design concept is adopted in this research, where the overall flow of the duct is considered as the sum of local flow fields within the duct modules. By analyzing the structural parameters such as cross-section ratio, pipe length, and flow direction within each duct module, a numerical prediction model for flow based on fluid-structure parameters is developed using numerical fitting techniques. Experimental results show that the flow rate prediction accuracy for normal modules is within 10%, and the flow rate prediction accuracy for modules with irregular structures is within 15%. It validates that this numerical prediction method, based on the flow structure, is a reliable tool for assessing and optimizing the flow state and quality of the flow field in the entire rectangular piping system.
Keywords
INTRODUCTION
In current engineering applications, the analysis of flow fields holds significant importance in assessing and enhancing the performance of electromechanical products. Particularly in air supply systems, the structural design of ducts directly influences the heat transfer efficiency, thereby impacting the overall system performance and energy efficiency. However, existing duct design methods suffer from various limitations, especially in optimizing airflow efficiency, often lacking systematic and quantitative analysis. This leads to inefficient design and difficulty in identifying improvement directions.
In the optimization of duct structures, scholars mainly improve the heat transfer efficiency by modifying the geometric shape and configuration of the ducts. Kumar et al. enhanced the efficiency of solar energy devices such as solar air heaters (SAHs) through duct structure design[1]. Karabulut et al. inserted rectangular baffles into ducts and extensively analyzed the effects of baffle angles and heights on heat transfer and pressure drop characteristics[2]. Wu et al. improved duct structures by adding guide vanes and conducted multi-objective optimization design of the vane profile to maximize the optimization effect of the guide vanes[3]. Cao et al. optimized the rectangular duct at the inlet of a hybrid power battery cooling system, which can reduce fan-induced noise while achieving the expected cooling effect[4].
Some scholars have employed different methods for structural optimization of pipelines. Morelli et al. conducted shape optimization of steam boiler hybrid ducts using surrogate-based optimization (SBO) and multi-objective genetic algorithm (MOGA)[5]. Hanan et al. proposed a comprehensive optimization design approach that combines response surface methodology and genetic algorithm to optimize existing pipeline characteristic data[6]. Czetany et al. presented a simple one-dimensional model to optimize the inlet and outlet of rectangular ducts, obtaining the optimal rectangular duct structure using nonlinear differential equations[7]. Alfaro-Ayala et al. utilized computational fluid dynamics (CFD) to study the transient behavior of small cooling cabinets and proposed three different models to compare and analyze the temperature and velocity distributions inside, validating the accuracy of CFD values with experimental data and proving that fitting temperature polynomials is a better approach[8]. Immonen et al. optimized a given baseline shape design using CFD and high-order polynomial response surface, determining the optimal path for a given S-shaped duct[9]. Wang et al. demonstrated the impact of storage capacity on the design of foundational transportation infrastructure, which can be applied to optimize the structure of large-scale CO2 transportation pipelines[10].
Flow prediction is a crucial aspect of air supply system design. Regarding structure-based flow prediction methods, scholars have conducted the following research: Oyewola and Idowu utilized CFD to investigate the influence of Reynolds number (Re) on the flow state at the inlet section of battery thermal management systems (BTMS)[11]. Kodali and Idem proposed a numerical model to predict the relationship between flow rate and pressure distribution in a three-branch air duct system and the upstream static pressure[12]. They predicted the flow velocity through the initial branch pipe upstream using the secant method and simulated the flow through the remaining branch pipes using the Newton-Raphson method. Avcı et al. modeled and analyzed duct structures using CFD methods and employed artificial neural networks to predict the airflow state inside refrigerators, achieving a 7% improvement in refrigerator performance with the optimal structural design[13]. Tao et al. employed numerical simulation to model the initial duct shape and optimized regions with lower dynamic pressure by adding virtual forces to fluid elements[14]. Kong and Chong determined critical areas of maximum pressure drop by combining static equilibrium rectangular duct design methods with circular rectangular duct grids[15]. To enhance prediction accuracy, Ye et al. studied the accuracy of CFD modeling methods in predicting pipeline flow fields and analyzed the reasons for quantitative differences in model prediction results[16].
Modular design, as one of the green design methods, can shorten the product development and manufacturing cycle, increase product lines, improve product quality, and rapidly respond to market changes. Currently, modular design methods have been widely applied in various fields such as architecture and construction, manufacturing, robotics[17], software development, automotive industry[18], furniture design[19], and medical equipment[20]. However, there is relatively little research and application in the field of structural optimization of air supply systems. By applying the concept of modular design to the optimization process of ducts, the modeling process of air supply systems can be simplified, and the efficiency of duct structure design can be improved. You and Smith proposed a novel multi-objective green modular design method, which utilizes atomic theory and fuzzy clustering to establish modular structures, where each module can meet different design goals[21]. Zhang et al. introduced the concept of modularization for rectangular duct systems and obtained the optimal rectangular duct structure to enhance the uniformity of the flow field[22]. Ji et al. presented a dual-layer optimization model based on constrained genetic algorithm for joint decision-making in technical system modularization (TSM) and material reuse modularization (MRM), constructing a unified framework[23].
Due to the increasing application of rectangular duct structures, which exhibit excellent manufacturability, the internal duct systems of refrigerators are commonly designed as rectangular[24]. Based on existing research, the design of air supply efficiency in ducts is typically based on pre-designed structural schemes, and the air supply efficiency is verified through CFD simulations. However, this process suffers from inefficiency issues because every time there is a change in the structural scheme, it requires rebuilding the CFD model and conducting simulations. The direction of scheme modifications relies on the simulated results of air supply efficiency from CFD or the design experience of designers, lacking clear guidance. The influence patterns of duct structure parameters on air supply efficiency have not been clearly defined.
To overcome these limitations, a modular structural analysis method for rectangular ducts has been proposed, aiming to quantitatively study the numerical relationship between duct structural parameters and air supply efficiency. This method involves establishing a mapping function between duct structural parameters and outlet flow rate for specific research objects. Based on the established mapping function, it enables rapid validation of air supply system design schemes, thereby enhancing verification efficiency and shortening the product development cycle. This approach achieves rapid optimization of duct structural parameters with air supply efficiency as the design target, thereby optimizing air supply efficiency and reducing energy consumption. By revealing the mutual relationship between duct structural parameters and air supply efficiency based on the structure of the mapping function, it provides guidance for optimizing and improving air supply system structural schemes. This method reduces the number of experimental validations and physical prototype quantities for air supply system structural schemes, thereby lowering design and prototype manufacturing costs.
Especially in the application of mass-produced home appliance products, cost-effectiveness is an important consideration. Under the demand for multi-model design, modular design optimizes resource use by reducing the cost of air duct structural design and corresponding mold manufacturing. By standardizing and reusing modules, it reduces a variety of spare parts and mold costs, while also reducing material consumption. These measures not only help to reduce overall costs but also ensure effective air distribution efficiency, enhancing the overall performance and market competitiveness of the products.
METHODS
Duct construction affects flow field
In most air supply systems, the air inlet of a rectangular duct is determined by the structure of the upstream room. The upstream room serves as a functional structure that provides high-quality air in terms of temperature, humidity, and other factors. Typically, the air inlet is equipped with a duct fan or pump to draw airflow from the upstream room, such as an evaporator room. Due to the energy consumption associated with duct fans and pumps, the number of air inlets is limited. On the other hand, the outlets of the rectangular ducts are positioned based on the specific requirements of the target room, such as the heat load of a refrigerator compartment. As a result, the structure of rectangular ducts serves as a connection between multiple inlets and multiple outlets in order to meet the varying flow requirements of each outlet. The shape and dimensions of the rectangular ducts can be adjusted to modify the flow rate profile at the outlets. This structural adjustment allows for flexibility in controlling the airflow distribution and achieving the desired performance in different target rooms.
Characterization of the study of the duct flow problem
The entire duct structure is indeed highly complex. Studying the entire duct pipeline, with its various types and numerous structural parameters, can be challenging. Additionally, the presence of multiple outlets in the duct pipeline makes it difficult to conduct specific studies on the flow rate of each outlet when considering the entire pipeline as the object of study. However, it is possible to analyze the duct pipeline by focusing on local sections. The fluid flow within the duct pipeline is unidirectional, with the front fluid domain influencing the back fluid domain while not being affected by it. This characteristic allows for analysis to start from the local sections, with the results of the front fluid domain serving as initial conditions for the study of subsequent sections. Moreover, certain parameters at a specific location can be considered as the accumulation of the fluid domain conditions from previous sections. This approach allows for a more manageable and systematic analysis of the flow and structure within the duct pipeline. By breaking down the study into smaller, interconnected parts, it becomes feasible to comprehensively understand and optimize the performance of the entire duct system.
In a rectangular duct, each outlet’s flow condition is determined by the requirements of the entire air supply system. The airflow is driven by a duct fan, and the fan’s operating speed is adjusted to meet these flow requirements. As the rotating velocity of the duct fan changes, the flow motion within the rectangular duct varies. However, due to the constraints imposed by the duct’s structure on the flow direction, the predominant change in the flow motion is typically the variation in flow velocity. This variation in flow velocity directly affects the distribution of flow pressure within the rectangular duct. Furthermore, these changes in flow pressure also impact flow losses and other related variations. Considering the ease of measuring flow pressure, the variable distribution of flow pressure is often considered as an indicator of changes in the flow field throughout the entire rectangular duct. By analyzing the distribution of flow pressure, one can gain insights into the variations in the flow field and understand how the flow conditions are influenced by changes in the operating parameters of the duct fan.
Propose solutions
Indeed, the complexity and partial irregularity of the piping structure pose challenges for theoretical analysis and optimization of the structural parameters for the entire duct piping. Directly parameterizing the whole duct piping involves a large number and variety of parameters, which are coupled with each other. This complexity makes the structural optimization problem difficult to solve, and it becomes challenging to precisely optimize each structural parameter. To address these challenges, it is often necessary to adopt simplified models or divide the duct piping into smaller sections for analysis and optimization. This approach allows for a more manageable and systematic study of the flow and structure within the duct system. Additionally, advanced optimization techniques, such as numerical methods and computational simulations, can be employed to explore the design space and find optimal solutions within the given constraints. Furthermore, it is important to consider practical constraints, such as manufacturing limitations and cost-effectiveness, when optimizing the structural parameters of the duct piping. A balance must be struck between optimizing performance and ensuring feasibility in real-world applications.
In the concept of modular analysis in product design, the flow of information or functions is channeled through the input and output interfaces of each module. This allows the entire product to achieve comprehensive information processing or function operation. The design of each module can be independent of others, only needing to consider the specific functional requirements and input/output interface requirements of the current module. Moreover, for modules that are homogeneous in nature, the same set of design parameters can be used for their design. This simplifies the overall design process of the product, as it allows for standardized and reusable module designs. By modularizing the design, it becomes easier to modify or replace individual modules without affecting the entire product. This flexibility and ease of integration are key advantages of the modular approach in product design. Overall, modular analysis enables efficient and effective design by breaking down complex systems into manageable and interchangeable modules, simplifying the design process, and facilitating modular integration.
In line with the modular design concept, the overall flow within the duct can be understood as the sum of the local flow fields within each duct module. The cooling air moves through the inlet and outlet of each duct module as a material flow. The design of the entire duct system can be divided into the coupling design of these individual duct modules, where each part of the duct system corresponds to a different type of module. Modules of the same type can be designed with uniform structural parameters, while different types of modules may have varying structural parameters. The mapping function between the module structural parameters and the duct outlet flow rate is established by data fitting, and experimental verification of the final mapping function is sufficient. The specific modular analysis method is shown in Figure 1. This modular design approach provides significant convenience for the subsequent optimization process. It also facilitates the study of the numerical relationship between the structural parameters and the flow conditions at the outlet of the duct system. This design idea not only simplifies the design process but also enables a more efficient and cost-effective approach for subsequent product design of the same type. By leveraging the numerical relationship between the basic flow prediction and the structural parameters, designers can streamline the design process, enhance design efficiency, and reduce overall design costs.
Overall, the modular design concept allows for a more systematic and efficient approach to designing and optimizing the duct system. It enables a modular integration of the different components and simplifies the study of the relationship between structural parameters and flow conditions, leading to improved design efficiency and cost-effectiveness.
Pressure analysis inside the duct module
Flow pressure is the main factor affecting the changes in fluid mass flow rate, flow velocity, and other state parameters in pipeline structures. By analyzing the distribution of flow pressure along the pipeline, it is possible to understand how these changes influence the flow field and optimize the design accordingly. The fluid pressure situation in the duct module is demonstrated in Figure 2.
The total pressure Pti in the duct module i is expressed as:
Where Pti, Psi, and Pmi are the total pressure, static pressure and dynamic pressure of section I, respectively. The pressure drops from the L(n-1) to L(n) section of the rectangle duct are expressed as:
Based on continuity equation, total pressure drop is described as the accumulation of pressure drops in each duct module, such as:
Based on the previous statement, the entire duct structure can be viewed as a series-parallel combination of rectangular duct modules. The overall change in the flow field of the air supply system is considered as the cumulative effect of flow variations in each duct module [as expressed in Equation (4)]. In the design of the complete air duct piping system, the flow change characteristics of each rectangular air duct module are taken into account. This allows for the optimization and analysis of the structural form of the air duct piping and related structural parameters. The ultimate objective is to improve the flow performance and efficiency of the air supply system. By considering the flow variations in each duct module and their cumulative effects, designers can identify potential areas for improvement and optimize the design accordingly. This may involve adjusting the dimensions, layout, or other parameters of the duct modules to enhance flow efficiency and achieve better air supply performance. Through this iterative design process, the overall flow performance and air supply efficiency of the duct piping system can be improved, leading to a more effective and efficient air supply system. By optimizing the structural parameters based on the flow change characteristics, designers can achieve the desired goals of enhancing flow performance and improving air supply efficiency.
METHODOLOGY IMPLEMENTATION
Modularization of ducts and extraction of structural parameters
In this chapter, the study focuses on a common air-cooled refrigerator with built-in refrigerator air duct piping, which is available in Changhong Meiling Co., Ltd. To begin the analysis, the air duct piping is divided into modules. This modular approach allows for a more detailed examination of the structural parameters within each module. By studying the individual modules, it becomes easier to understand the overall performance and characteristics of the air duct system. The structural parameters of each module are carefully analyzed and studied. This includes parameters such as the dimensions, shape, materials, and other design elements that contribute to the functionality of each module. By investigating these parameters, researchers can gain insights into the relationship between the module’s design and its performance within the air duct system.
The subsequent modular analysis, simulation, and verification experiments are conducted using this air duct as the carrier. This allows researchers to evaluate the performance of the individual modules and the overall air duct system. Through these experiments, the effectiveness of the modular design and the impact of different structural parameters can be assessed and optimized. Overall, this chapter focuses on dividing the air duct piping into modules and thoroughly analyzing the structural parameters of each module. This sets the foundation for subsequent experiments and simulations, which aim to improve the performance and efficiency of the air duct system.
In the analysis of the entire duct piping structure, it has been determined that the duct pipeline can be divided into modules based on its air outlet arrangement [Figure 3]. The duct modules were also categorized into different types.
The first type consists of modules with both inlet and outlet openings, along with air outlets. These modules include LC2, LC3, LC4, RC2, RC3, and RC4. The second type comprises modules with only inlet openings and air outlets. This category includes LC1, RC1, and BW. The third type consists of modules with only inlet and outlet openings. The module C2 falls into this category. The remaining duct modules, C1 and C3, can be considered analogous to the first category of duct modules, as they also have both inlet and outlet openings.
By categorizing the duct modules in this way, it becomes easier to analyze and study the structural parameters of each module individually. This modular approach allows for a more systematic understanding of the different types of modules and their specific characteristics within the duct piping structure.
In this study, the first type of duct module, which has the most complex structure, is chosen as the basic module. The structural parameters of this basic module are defined and used as the common structural parameters for all duct modules. By dividing the inlet and outlet by the direction of fluid flow in the duct, the wall of the duct is the air supply outlet, and the surface opposite to the air supply outlet is the bottom surface. Module structure parameters are as follows: a for the inlet area, b for the outlet area, c for the area of the air supply outlet, and l for the length of the air duct module. The exit angle x is the angle between the left and right sides of the duct module, and the inclination angle y is the angle between the vertical line of the air supply port section and the bottom surface (usually 90°, or 0° when the module has no air supply port). These structural parameters are shown in Figure 4, providing a visual representation of the different dimensions and angles that define the basic module and serve as common parameters for all the duct modules.
Using these defined structural parameters, researchers can analyze and optimize the performance of each duct module and the overall air duct system. This approach helps ensure consistency and comparability among the different modules, enabling a systematic evaluation of their impact on airflow characteristics and system efficiency.
Parameters related to outlet flow
In this study, the duct module is set as the structural unit, and its flow field is only influenced by the flow at inlet and outlet. Considering the flow field in each duct module as the independent field, it is necessary to discuss the mapping relationship between the flow variations and structural parameters. According to the principles of fluid dynamics, the relationship between flow loss and pipe structural parameters is expressed as mathematical equations. Among them, the nomenclature used in this study is summarized in Table 1. The flow loss in the duct includes the along-line loss hf and local pressure loss hj, which is expressed as:
Nomenclature
hf | Along-line loss | L0 | Total length of air duct structure (m) |
hj | Local pressure loss | p | Pressure |
g | Gravity (m/s2) | ρ | Fluid density |
Re | Reynolds number | Pt | Total pressure |
l | Length of the air duct (m) | Ps | Static pressure |
v | Velocity in the duct (m/s) | Pm | Dynamic pressure |
τ | Kinematic viscosity of the fluid | K | Thermal conductivity |
ς | Along-travel loss factor | A | Cross-section of the air duct (m2) |
d | Hydraulic diameter of the air duct (m) | Li | Pathway from outlet i to terminal outlet (m) |
φ | Angle between outlet and pipeline | θ | Inclination angle of duct side |
a | Length of the air duct (m) | Q | Mass flow rate |
b | Width of the air duct (m) |
Due to airflow in the duct (Re < 2,300), the flow is laminar, and the along-line loss hf is:
Where Re = vd/τ is the Reynolds number; l is the length of the rectangle duct; v is the velocity of flow; τ is the dynamic viscosity of the fluid; d = 2ab/(a + b) is the hydraulic diameter of the rectangle duct, a is the length of the rectangle duct and b is the width of the rectangle duct; g is the acceleration of gravity. The local pressure loss in the duct, caused by the bending, expansion and reduction structure of the rectangle duct, is expressed as:
Where ζ is the along-travel loss factor and determined by the Colebrook equation. The local pressure loss coefficient is mostly related to the structure, informed by the study of Liu[25], local pressure loss coefficient is only related to the inlet and outlet section and angle of the rectangle duct, and it is expressed as:
Where l is the length of the air duct and L0 is the total length of air duct structure. Besides, considering the relationship between flow loss and mass flow rate, the pressure drop is denoted as:
For module i of the duct piping, the portion of the pressure drop affected by the along-travel loss hf is Phf and the portion of the pressure drop affected by the local pressure loss hj is Phj:
Therefore, the function of mass flow rate is proposed with the structural parameters of the rectangle duct, as:
And the mass flow rate in a rectangle duct is expressed as:
Where
From Equation (11), it can be concluded that:
And the length of the air duct l belongs to the structural parameters D, the velocity in the duct outlet and inlet v can be derived from the inlet flow information QI. So, the relationship of outlet flow QO is:
Among them, the structural parameters of duct module i (Di) mainly include distance from air outlet to the end of pipeline (Li), air duct inlet area (
In conclusion, based on the relationship between the flow field and structural parameters in the duct module, the flow variations (flow loss and volume of flow) are expressed as the function of structural parameters (cross-section, duct length and flow direction). Moreover, comparing the existing equations from the traditional circular duct, it is necessary to discuss this mapping function in rectangle duct, as one evaluation tool with better accuracy.
Function fitting
Data acquisition
In this study, the rectangular duct structure from the air inlet to each air outlet is divided into several duct modules. These modules are taken as samples to investigate the mapping relationship between the structural parameters of the duct modules and the flow field. The structural parameters of each module are measured and recorded, and are presented in Table 2.
Structural parameters of duct module
Modular | Li (m) | Li/L0 | θi | φi | ||
LC-1 | 6.67 | 6.50 | 0 | 0 | 0.4 | 90 |
LC-2 | 7.09 | 6.50 | 0.20 | 0.217 | 0.9 | 90 |
LC-3 | 7.51 | 6.50 | 0.40 | 0.435 | 0.9 | 90 |
LC-4 | 10.19 | 6.50 | 0.60 | 0.652 | 23.8 | 90 |
RC-1 | 6.7 | 6.50 | 0 | 0 | 0.5 | 90 |
RC-2 | 8.95 | 6.50 | 0.20 | 0.217 | 5 | 90 |
RC-3 | 13.76 | 6.50 | 0.40 | 0.435 | 10.5 | 90 |
RC-4 | 15.54 | 6.50 | 0.60 | 0.652 | 11 | 90 |
C-1 | 21.34 | 15.54 | 0.64 | 0.696 | 3.2 | 41.69 |
C-2 | 27.45 | 0 | 0.73 | 0.793 | 14.2 | 0 |
C-3 | 30.90 | 16.74 | 0.90 | 0.978 | 0 | 75.72 |
BW | 16.74 | 4.43 | 0 | 0 | 5.6 | 90 |
After measuring and recording the structural parameters, the modularized duct piping system is simulated. The boundary conditions for the simulation are set as described in Table 3.
Model setting in rectangle duct model
Parameters | Value |
Duct structure | Rectangle duct |
Region of refinement | Rectangle duct and fan |
Type of fan | Axial |
Rotation rate of duct fan | 1,840 r/min |
Inlet | Stagnation inlet |
Outlet | Pressure-outlet |
Back pressure of the outlet | 0 MPa |
By simulating the modularized duct piping system with these boundary conditions, researchers can analyze the flow field and investigate how the structural parameters of the duct modules affect the flow characteristics. This analysis assists in understanding the relationship between the structural parameters and the flow field performance, and can guide the optimization of the duct module design for improved airflow efficiency within the system.
Parametric analysis
(1) The absolute value of the outlet flow rate is related to the inlet flow rate, while the structural parameters only affect the relative value of the outlet flow rate. Therefore, the relationship can be expressed as a fitting function:
(2) The relative value of the inlet and outlet area can provide information about whether the ducting is expanding or contracting along the fluid flow direction. The parameters
(3) Since the inlet flow rate of the back duct module is equal to the outlet flow rate of the front duct module, there is a relationship between the position of the duct module and the percentage of its outlet flow rate. The more forwardly positioned a duct module is, the smaller the percentage of its outlet flow rate compared to the inlet flow rate. This effect can be expressed by the parameter Li/L0.
(4) The shape factor θ can be used to indicate the difference between a straight duct module and an inclined duct module. The shape factor φ, on the other hand, can indicate the difference between a duct module with an air outlet and a duct module without an air outlet. In the standard duct module, both the shape factor θ and φ are 90°. To incorporate these shape factors into a fitting function, the cosine of θ (cosθ) and the cosine of φ (cosφ) can be used. The cosθ and cosφ parameters represent the influence of the respective shape factors on the flow characteristics.
(5) The fitting function used in the solid paper is expressed as:
Determination of the fitting function
A number of polynomial functions can be obtained by combining the primary, quadratic and combined terms of the above parameters. According to the number of coefficients of the polynomial function, the corresponding number of duct module flow data is selected for substitution. The function obtained from the fitting is applied to the remaining data points for verification. The parameters of the fitting function are adjusted based on the verification results until satisfactory fitting accuracy is achieved. The final fitting function is as follows:
The mapping function is numerically fitted with the simulation results, and the values of each coefficient are obtained as: K1 = 7.611; K2 = 2.289; K3 = -1.102; K4 = 2.473; K5 = -8.742. This function takes the form of
Based on the comparison of simulation results with the mapping function shown in Figure 5, the root mean square error (RMSE) of the mapping function is reported to be 0.019. Since the error is less than 10%, it is considered to be within the acceptable error range. Consequently, it can be concluded that the mapping function proposed in the paper is reliable for calculating the flow distribution within rectangular duct modules.
EXPERIMENTAL VERIFICATION
Experimental setup
Still, the experimental equipment for studying flow variations in a rectangular duct is presented based on the laboratory devices at Changhong Meiling Co., Ltd. [Figure 6].
To ensure the validity of the simulation results, the appropriate parameters for the refrigeration system in the duct piping were set according to the simulation content. It was ensured that the inlet conditions of the duct piping matched the settings of the simulation. This experimental result can be used to verify the aforementioned simulation calculation method. The specific parameters related to the refrigeration system are shown in Table 4.
Testing parameters in refrigeration system
Experimental content | Parameter setting |
Refrigerant | R600a |
Compressor | Displacement 9.05 cm3/r |
Compressor’s power | 120 W |
Axial fan | 120 mm |
Fan’s power | 1.5 W |
Rotation rate | 1,840 rpm |
Evaporator | Straight fin |
When the airflow in the entire air supply system is in a steady state, the velocity of flow at each outlet is measured. According to testing standard[26], the average velocity at each outlet is calculated using either the Process Average or Geometric Average Method. In this study, the average velocity is considered as the experimental result to determine the mass flow rate at each outlet.
Data comparison and analysis
Based on the modularization of the rectangle duct and the related parameters in the refrigeration system
Numerical comparisons of functions, simulations and experiments
Modular | Mass flow rate (g/s) | Difference (%) | ||||||
Function | Simulation | Experiment | ||||||
Test 1 | Test 2 | Test 3 | Average | F&E | S&E | |||
LC-1 | 2.01 | 1.87 | 1.94 | 1.78 | 2.04 | 1.92 | 4.69 | 2.63 |
LC-2 | 1.67 | 1.64 | 1.74 | 1.32 | 1.68 | 1.58 | 5.70 | 3.94 |
LC-3 | 1.27 | 1.45 | 1.51 | 1.25 | 1.56 | 1.44 | 11.81 | 0.64 |
LC-4 | 1.01 | 1.01 | 0.93 | 0.74 | 0.98 | 0.88 | 14.77 | 14.30 |
RC-1 | 1.94 | 1.72 | 1.81 | 1.55 | 1.76 | 1.70 | 14.12 | 0.93 |
RC-2 | 1.37 | 1.46 | 1.45 | 1.17 | 1.53 | 1.38 | 0.72 | 5.58 |
RC-3 | 1.02 | 1.09 | 1.15 | 1.35 | 1.12 | 1.21 | 15.7 | 9.76 |
RC-4 | 0.93 | 0.96 | 0.82 | 0.75 | 0.97 | 0.85 | 9.41 | 13.06 |
C-1 | 5.26 | 5.23 | 5.23 | 4.82 | 5.38 | 5.14 | 2.33 | 1.75 |
C-2 | - | - | - | - | - | - | - | - |
C-3 | 1.77 | 1.79 | 1.82 | 1.52 | 1.84 | 1.73 | 2.31 | 3.67 |
BW | 1.77 | 1.79 | 1.82 | 1.52 | 1.84 | 1.73 | 2.31 | 3.67 |
In the case of the duct system in this paper, the irregularity of the RC3 module’s structure is relatively high, and the RC1 module follows the RC3 module. Therefore, the flow prediction results of the RC1 module and RC3 module under the mapping function have relatively large errors. As shown in Figure 7, the specific errors of the RC1 module and RC3 module are 14.12% and 15.7%, respectively. On the one hand, there are measurement errors inherent in the experiments themselves. On the other hand, the function fitting in the paper is based on simulation results, which inherently contain errors compared to experiments. In the process of polynomial fitting for the mapping function, the more complex the polynomial pattern, the higher the accuracy of the fitting function, but the narrower the applicable range of this fitting function. In engineering practice, if the accuracy of the prediction method is acceptable, there will be a higher pursuit of the applicability of the fitting function. Therefore, under the premise of pursuing a broader applicable range (using as few structural parameters as possible for the fitting function), this method aims for a flow prediction accuracy within 15% for irregular structure modules and within 10% for normal modules, thereby preliminarily verifying the feasibility of this method.
Furthermore, using the equations [Equation (9)] that relate mass flow rate to pressure drop, the pressure drop in the rectangle duct is calculated based on the function values provided in Table 5. When comparing these calculated pressure drop values to the simulation values [Figure 8], it is observed that the average error is 4.64%. This indicates that the proposed function is feasible and effective in predicting the flow variations in the rectangle duct structure.
Based on the data obtained from the function, simulations, and experiments, it is observed that the flow rate is nonlinearly correlated with various factors such as the distance from the air outlet to the end of the pipeline (Li), the area ratio in the rectangle duct (
On this basis, the method was further utilized to optimize the pipeline design. By analyzing the impact of pipeline size on flow velocity and pressure loss, the optimal dimensions were determined, which not only ensured the even distribution of the refrigerant but also minimized energy consumption. The bends in the ductwork can cause local pressure losses, and the reduction of flow velocity and change in flow direction at these bends lead to significant energy loss. Moreover, the insulation of the pipeline structure has been enhanced, especially in applications such as air-cooled refrigerators, to reduce heat loss, stabilize airflow temperature, and improve cooling capacity and energy efficiency. These measures collectively contribute to a more effective and energy-saving air supply system, highlighting the significance of the predictive function of this method in guiding the design towards green energy solutions.
DISCUSSION AND APPLICATION OF FITTING FUNCTIONS
The mapping function of structural parameters reveals that the outlet flow ratio is influenced by multiple parameters. By analyzing the sensitivity of each structural parameter in this proposed mapping function, a structural optimization method for the refrigerator air duct can be established. This method can help optimize the design of the duct by identifying which parameters have the most significant impact on the outlet flow ratio and adjusting them accordingly.
Furthermore, the mapping function can also be applied as an evaluation method for existing duct structures. By inputting the parameters of the existing duct into the mapping function, it is possible to assess the flow efficiency of the duct system in an inter-cooled refrigerator. This evaluation can identify areas for improvement and guide efforts to enhance the flow efficiency of the duct system.
Parameter sensitivity analysis
In order to analyze the influence of the modularized parameters in the duct system, the sensitivity of each structural parameter is assessed based on the mapping relationship [Equation (17)]. Focusing on the structural parameters in the RC-2 duct module, the baseline values for these parameters are provided in Table 6.
Sensitivity analysis initialization
Parameters | Content | Defaults |
θi | Inclination angle of duct side | 5 |
Li | Pathway from outlet i to terminal outlet | 0.2 |
Cross-section of inlet | 8.95 | |
Cross-section of duct outlet | 6.5 | |
Cross-section of duct modular outlet | 6.7 | |
φi | Angle between outlet and pipeline | 90 |
Additionally, a 10% variation is applied to each structural parameter as a sensitive variable to compare the flow performance of the entire duct system. It is important to note that the parameter φi is directly determined by the location of the duct module and its value remains constant throughout the structural design process. Therefore, no sensitivity analysis is conducted for this parameter. The structure of the analysis is shown in Figure 9.
The influences of duct modular structural parameters are discussed based on the mapping function. The analysis reveals the following insights:
(1) Inclination angle of duct side (θi) is negatively correlated with the proportion of outlet flow. It shows that this negatively correlation is small, and flow variation (such as velocity, flow loss, etc.) changes little with variable direction of duct side. Thus, inclination angle of duct side (θi) is one insensitivity factor, which should be designed with other structural constrains than flow requirements.
(2) Pathway from outlet i to terminal outlet (Li) is negatively correlated with the proportion of outlet flow. It shows that this positively correlation is obvious, because of the increasing flow loss with shorter pathway of rectangle duct. Thus, pathway from outlet i to terminal outlet (Li) is one sensitivity factor to be considered in design of duct outlet.
(3) Cross-section of inlet (
(4) Cross-section of duct outlet (
(5) Cross-section of duct modular outlet (
Methods for predicting variation in duct flow
With the proposed equation of the fitted function [Equation (17)], it becomes possible to analyze the flow variations of a rectangle duct with a variable structure. This method of flow variation prediction involves three steps:
(1) Modularizing: In order to account for the influence of the rectangular air duct structure on the airflow volume, five dimensionless variables are defined. These variables include the length factor X1(Li/L0), the outlet area factor X2[
(2) Predicting: In the duct system, the flow conditions at the inlets (
(3) Decision-making: In order to meet the flow requirements of each outlet in the air supply system, it is crucial to analyze the flow variations at each outlet. This data serves as a performance indicator to evaluate the structural design of the entire rectangular duct. Additionally, with the predicted results from the aforementioned functions, it is possible to identify and optimize the duct module that exhibits high flow loss and large volume. This optimization process aims to enhance the flow efficiency and overall structure of the duct system.
CONCLUSION
In this paper, a numerical prediction method is proposed to evaluate the flow variation in an air supply system by modularizing the rectangular duct structure. The following conclusions are drawn:
(1) Based on numerical testing of the rectangle duct in a refrigeration appliance, it is observed that the pressure-drop and flow variation are nonlinearly positively correlated with the inclination angle of the duct module side (θ) and cross-section (A), while they are nonlinearly negatively correlated with the duct length
(2) Experimental validation is conducted using a refrigeration appliance. The average error between the proposed function and the experimental data is found to be less than 10%, indicating that the numerical function and related method of flow variation are validated. In the future, this proposed method can be applied as a potential design tool to evaluate the performance of the entire rectangle duct and optimize the duct structure for air supply systems.
(3) The adoption of modular analysis and mapping function methods has facilitated the rapid optimization of duct structural parameters with air supply efficiency as the design target, thereby improving the rate of research and development and shortening the design cycle. However, its accuracy is somewhat lower compared to prototype experiments and whole-system CFD simulations of air supply systems. Additionally, the modular analysis method is highly suitable for relatively regular rectangular ducts, but real duct systems often comprise irregular duct structures, such as the C-1, C-2, C-3, and BW modules, in the case discussed in this paper. Faced with the optimization design of irregular duct structures, this method in the paper has limitations.
(4) This study has clarified the relationship between duct structural parameters and air distribution efficiency through mapping functions, achieving rapid optimization of duct structures. At the same time, the optimized ducts, due to improved flow characteristics, can reduce the working power of compressors and fans or shorten working hours while meeting the same air distribution requirements. The optimization method reduces the need for experimental validation, lowers design costs, and enhances air distribution efficiency. It not only reduces energy consumption but also responds to the demand for green energy and sustainable design.
(5) For future development, the proposed modular design method still requires continuous refinement and expansion. Faced with new forms of duct system modules, by further subdividing modules and using similar mapping functions, it can more effectively adapt to irregular pipe structures.
DECLARATIONS
Authors’ contributions
Conceptualization, methodology, validation, system construction, original draft preparation: Fang D
Supervision, review and editing, formal analysis: Ke Q
Methodology, investigation: Sha J
Data curation, investigation: Cui P
Availability of data and materials
The data that support the findings of this study are available from the corresponding author upon reasonable request.
Financial support and sponsorship
This study is supported by the National Key R&D Program of China (2020YFB1711602) and Scientific and Technological Achievements Cultivation Project of the Intelligent Manufacturing Institute of HFUT (IMIPY2021013). We also acknowledge the assistance provided by the Key Laboratory of Green Design and Manufacturing of Mechanical Industry at Hefei University of Technology.
Conflicts of interest
Cui P is affiliated with Changhong Meiling Co., Ltd., China, while the other authors have declared that they have no conflicts of interest.
Ethical approval and consent to participate
Not applicable.
Consent for publication
Not applicable.
Copyright
© The Author(s) 2024.
REFERENCES
1. Kumar A, Singh AP, Akshayveer, Singh OP. Effect of channel designs and its optimization for enhanced thermo-hydraulic performance of solar air heater. J Sol Energy Eng 2022;144:051009.
2. Karabulut K. The effects of rectangular baffle angles and heights on heat transfer and pressure drop performance in cross-triangular grooved rectangular flow ducts. Int J Heat Fluid Flow 2024;105:109260.
3. Wu Z, Zhou S, Li Y, Jin W, Luo Y. Air duct optimization design based on local turbulence loss analysis and IMOCS algorithm. Machines 2023;11:129.
4. Cao Y, Wang D, He Y, Lu Y, Mao J, Hou H. Resolution of HEV battery cooling system inlet noise issue by optimizing duct design and fan speed control strategy. SAE Int J Engines 2018;11:67-78.
5. Morelli A, Baldrani R, Ghidoni A, Noventa G. Steam boiler mixing channel optimization with a surrogate based multi objective genetic algorithm. Therm Sci Eng Prog 2022;29:101169.
6. Hanan L, Qiushi L, Shaobin L. An integrated optimization design method based on surrogate modeling applied to diverging duct design. Int J Turbo Jet Eng 2016;33:395-405.
7. Czetany L, Szantho Z, Lang P. Rectangular supply ducts with varying cross section providing uniform air distribution. Appl Therm Eng 2017;115:141-51.
8. Alfaro-Ayala JA, Uribe-Ramírez AR, Minchaca-Mojica JI, Ramírez-Minguela JDJ, Alvarado-Alcalá BU, López-Núñez OA. Numerical prediction of the unsteady temperature distribution in a cooling cabinet. Int J Refrigeration 2017;73:235-45.
9. Immonen E. Shape optimization of annular S-ducts by CFD and high-order polynomial response surfaces. EC 2018;35:932-54.
10. Wang Z, Fimbres Weihs G, Neal P, Wiley D. Effect of storage capacity on CO2 pipeline optimisation. Energy Proced 2014;63:2757-63.
11. Oyewola OM, Idowu ET. Effects of step-like plenum, flow pattern and inlet flow regime on thermal management system. Appl Therm Eng 2024;243:122637.
12. Kodali C, Idem S. Modeling flow and pressure distributions in multi-branch light-commercial duct systems. Sci Technol Built Environ 2021;27:240-52.
13. Avcı H, Kumlutaş D, Özer Ö, Özşen M. Optimisation of the design parameters of a domestic refrigerator using CFD and artificial neural networks. Int J Refrigeration 2016;67:227-38.
14. Tao M, Guo K, Liu H, Liu C. An evolutionary optimization method to design shapes of flow channels. Chem Eng Trans 2017;61:1513-8.
15. Kong KH, Chong WT. Static balance duct design method and temperature dependent variable air volume systems. Build Serv Eng Res Technol 2019;40:698-713.
16. Ye J, Wargocki P, Ai Z. Improving the CFD predictive accuracy of particle fate in turbulent duct flows: four key issues and applications in in-duct UVGI system. J Build Eng 2023;80:108010.
17. Zhou J, Liu J, Qi H, Shan W. Cross-phase automated structural design of modular buildings using a unified matrix method and multi-objective optimization. Expert Syst Appl 2024;249:123788.
18. Gupta S, Gupta S, Agrawal A, Singla E. A novel modular approach for kinematic modeling and analysis of planar hybrid manipulators. J Mech Des 2021;143:093302.
19. Chen Y, Chen WZ, Chen K, Shao JY, Zhang WM. Mechanism configuration of super-redundant robot. AMR 2013;744:68-73.
20. Bertran MO, Babi DK. Exploration and evaluation of modular concepts for the design of full-scale pharmaceutical manufacturing facilities. Biotechnol Bioeng 2024;121:2241-57.
21. You ZH, Smith S. A multi-objective modular design method for creating highly distinct independent modules. Res Eng Des 2016;27:179-91.
22. Zhang Y, Zhang K, Liu J, Kosonen R, Yuan X. Airflow uniformity optimization for modular data center based on the constructal T-shaped underfloor air ducts. Appl Therm Eng 2019;155:489-500.
23. Ji Y, Jiao RJ, Chen L, Wu C. Green modular design for material efficiency: a leader-follower joint optimization model. J Clean Prod 2013;41:187-201.
24. Ke Q, Shang S, Jiang F, Huang H, Wei B. Optimization design of duct fan and evaporator module in refrigeration system with heat exchange and fan power. J Adv Mech Des Syst Manuf 2021;15:JAMDSM0034.
25. Li Q, Zhang M, Ouyang Y, Wen Z. Numerical investigation on flow and heat transfer of supercritical CO2 in variable cross-section tubes under precooler working conditions. Appl Therm Eng 2023;235:121419.
26. Household and similar refrigerating appliances. Beijing: Standards Press of China; 2016. (in Chinese) Available from: https://www.nssi.org.cn/nssi/front/106407736.html. [Last accessed on 12 Oct 2024].
Cite This Article
How to Cite
Download Citation
Export Citation File:
Type of Import
Tips on Downloading Citation
Citation Manager File Format
Type of Import
Direct Import: When the Direct Import option is selected (the default state), a dialogue box will give you the option to Save or Open the downloaded citation data. Choosing Open will either launch your citation manager or give you a choice of applications with which to use the metadata. The Save option saves the file locally for later use.
Indirect Import: When the Indirect Import option is selected, the metadata is displayed and may be copied and pasted as needed.
About This Article
Copyright
Data & Comments
Data
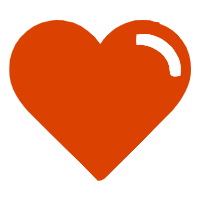
Comments
Comments must be written in English. Spam, offensive content, impersonation, and private information will not be permitted. If any comment is reported and identified as inappropriate content by OAE staff, the comment will be removed without notice. If you have any queries or need any help, please contact us at [email protected].