Effect of low-energy laser peening on properties of NiCrBSi-WC/Co coating
Abstract
Low-energy laser peening (LE-LP) is a green and pollution-free surface deformation strengthening technology. In this work, LE-LP was used to improve the properties of NiCrBSi-WC/Co (Ni-WC) coating. The investigation focused on the impact of LE-LP on the coating microstructure, microhardness, residual stress, and tribological properties. The results showed that although laser hot melting damaged the coating surface, the phase structure of the coatings did not change significantly. The coating’s hardness increased yet its surface roughness decreased as a result of the laser peening. Concurrently, after the LE-LP treatment, a residual compressive stress with an average value of -236 MPa was tested on the surface of the coatings. The average wear volume of the coating was reduced from 11.64 × 10-2 to 6.9 × 10-2 mm3, and the average wear rate was reduced from 4.31 × 10-5 to 2.55 × 10-5/N·mm3.
Keywords
INTRODUCTION
Wear failures are generated by the surface of the part[1,2]. Wear-resistant coatings prepared by supersonic plasma spraying can improve the wear resistance of components[3,4]. NiCrBSi-WC/Co (Ni-WC) coating is widely used in aerospace and marine areas due to its excellent mechanical property and wear resistance[5,6]. The enhancement of coating properties has been a hot research topic[7,8].
Heat treatment is a traditional post-treatment method to improve coating properties and eliminate residual stress[9,10]. Compared with traditional heat treatment, surface deformation strengthening has the advantages of low impact on the substrate and introduction of residual compressive stresses on the surface[11,12]. It is an important technology to improve the wear resistance of components[13-16]. With the development of technology, surface deformation strengthening technology is gradually combined with coating’s preparation to improve the properties of coatings[17,18].
Currently, The most widely used surface deformation peening techniques are shot peening, ultrasonic surface rolling and laser peening (LP)[19-21]. The characteristics of the coating are affected differently by different surface deformation peening methods. Li et al. shot-peened the Cr3C2-Al2O3-NiCr coatings and found that the surface microhardness of the coatings increased by 2.9 times[22]. The residual stress on the surface of the coating is -137 ± 7 MPa. And the wear rate of the coating is reduced by 98.7%. Zhao et al. used high temperature-assisted ultrasonic surface rolling to post-treat Ni-WC coating[23]. It is found that the surface roughness of the coating decreased by 49.04%, the surface microhardness of the coating increased by 38.4%, the surface stress changed from tensile stress to compressive stress, and wear amount reduced by 64.23%. Liu et al. found that LP increased the surface microhardness of NiCrBSi clad layers by 40.21%[24]. The surface residual compressive stresses were as high as -538 MPa. However, the surface roughness of the molten layer increased. In summary, it is feasible to use surface deformation strengthening techniques to improve the surface integrity of coatings. LP affects the coating to a depth of up to 2 mm and does not touch the coating, among other advantages[25].
Since the Ni-WC coatings prepared by supersonic plasma spraying have a laminar structure with internal defects such as pores and cracks, the Ni-WC coatings are prone to coating delamination and flaking during friction, so it is necessary to carry out post-treatment to improve the wear resistance of the coatings[26,27]. High-energy LP used energy of about 20 J/pulse and spot sizes fo about 3 to 5 mm. Low-energy LP (LE-LP) uses laser energy about 20 times smaller and a spot size of about 10 times smaller. Meanwhile, high-energy LP affects the metal to a depth of about 2 mm, and LE-LP affects it to a depth of about 100-200 μm. Compared to LP, the absorption layer is removed[1]. It saves costs and allows continuous work underwater[28,29]. Trdan et al. found that LE-LP increased the hardness of 6082-T651 Al alloy from 92 to
In this work, we prepared Ni-WC coatings for the first time by supersonic plasma spraying technique. In order to improve the properties of the coatings, LE-LP was used. The effect of LE-LP on the microstructure and properties of the coatings was investigated.
METHODS
Powders
The raw material Ni-WC powder developed by Beijing Ryubon New Material Technology Co., Ltd. was used. Figure 1 shows the microstructure and chemical composition of two powders. NiCrBSi powder was prepared by atomized granulation, and hard ceramic WC/Co powder was sintered using 88 wt.% WC and 12 wt.% Co. Ni-WC powder was then prepared by mixing 10% WC/Co with 90% NiCrBSi. As seen in Figure 1, the distribution of NiCrBSi powder particle size is around 40-80 μm, while that of WC powder particle size is around 25 μm. The mass ratio of chemical composition elements of the two powders was analyzed by energy dispersive spectroscopy (EDS).
Coating preparation
Ni-WC coatings were prepared on 45 steel (medium carbon steel) substrates by using an efficient supersonic plasma spraying. The sample size was 10 mm × 10 mm × 10 mm. The substrates were ultrasonically cleaned and sandblasted before spraying. The surface of the substrate was free of impurities and maintained a certain roughness. Figure 2A shows the schematic diagram of the supersonic plasma sprayed Ni-WC coating. After the coating preparation, the coating was strengthened with LE-LP. The schematic diagram of LE-LP is shown in Figure 2B. The parameters of the sprayed and LE-LP prepared coatings are shown in Table 1. Laser energy was 100 mJ, with a pulse width of 10 ns and a spot diameter of 0.4 mm. The power density was 7.96 GW·cm-2, and the repetition rate was 500 Hz. The wavelength was
Figure 2. Coating preparation diagram. (A) Supersonic plasma spraying diagram; (B) LE-LP diagram. LE-LP: Low-energy laser peening.
Coating preparation parameters
Parameters of spraying | Parameters of LE-LP | ||
H2 gas flow | 16 L/min | Laser energy | 100 mJ |
Ar gas flow | 150 L/min | Pulse duration | 10 ns |
Powder feed rate | 40 g/min | Spot diameter | 0.4 mm |
Spraying voltage | 120 V | Power density | 7.96 GW·cm-2 |
Spraying current | 460 A | Repetition rate | 500 Hz |
Spraying distance | 130 mm | Wavelength | 532 ns |
Scanning velocity | 4,000 mm/min | Overlap rate | 50% |
Confining layer | Water |
Microstructure characterization
The three-dimensional (3D) morphology of the coatings was analyzed by using a white light interferometer (WLI) (SuperView W1, Chotest, China). The average value of a 1 mm2 region chosen from three distinct coating locations was used to calculate the coating surface roughness. The surface and cross-section micro-morphology and elemental distribution of the coatings before and after LP were investigated using a scanning electron microscope (Hitachi SU8020, Japan) equipped with an energy spectrometer. The phase structure of the coatings was characterized using an X-ray diffractometer (XRD) (D8 Advance, Bruker, Germany). The Co target method was used to measure the XRD. The scanning rate is 4 °/min, and the wavelength is 0.17902 nm.
Mechanical properties characterization
The microhardness of the substrate and coating was tested using a microindenter (000 ZB, KELETI, China) after mechanical polishing treatment of the coating section. The residual stresses of the coatings were characterized by using an X-ray stress tester (XL-640, ST, China). The Co target method was used to measure the residual stresses.
Tribological properties
A multifunctional wear test equipment was used to perform reciprocating wear tests on the samples. Before the experiment, the coated samples and the pairs of body materials were ultrasonically cleaned. ZrO2 was used for the test, and its specifications were 6 mm in diameter, 50 N load, 3 mm reciprocating distance, 5 Hz frequency, and 30 min duration.
RESULTS
Microstructure
The 3D morphologies before and after LE-LP treatment are displayed in Figure 3. The average surface roughness of the untreated coating is 18.389 μm; after LE-LP treatment, it is
Figure 3. 3D morphology of the coating surface before and after LE-LP treatment. (A) 3D morphology and roughness of untreated coating surface; (B) 3D morphology and roughness of LE-LP treated coating. 3D: Three-dimensional; LE-LP: low-energy laser peening.
In order to understand the thermal effects of the laser on the surface of the coating, the surface shape has been investigated. Figure 4 shows the microscopic morphology of the coating surface before and after
Figure 4. Surface morphology and EDS of coating surface before and after LE-LP treatment. (A) Surface morphology and EDS of untreated coating; (B) Surface morphology and elemental composition of LE-LP treated coating. EDS: Energy dispersive spectroscopy; LE-LP: low-energy laser peening.
Figure 5 shows the cross-sectional morphology and EDS of the coating both before and after LE-LP treatment. As shown in Figure 5, the cross-sectional morphology shows the laminar structure of thermal spraying. The ablation layer only occurs on the surface of the coating, and there is no ablative damage within the coating. Figure 5C and D shows the EDS of the coating cross-section elements. The EDS in the coating cross-sectional shows that there is no obvious mutation point of the O element in the coating. The O element is aggregated due to the presence of cracks at the interface. Combined with Figure 4, the ablation phenomenon only occurs on the surface of the coating and has no obvious effect on the inside of the coating.
Figure 5. Cross-sectional morphology and EDS of coating before and after LE-LP treatment. (A) Cross-sectional morphology of untreated coating; (B) Cross-sectional morphology of LE-LP treated coating; (C) Distribution of elements of line 1; (D) Distribution of elements of line 2. EDS: Energy dispersive spectroscopy; LE-LP: low-energy laser peening.
Figure 6 shows the results of XRD pattern analysis of the coating surface. No noticeable additional diffraction peaks were observed on the coated surface following LE-LP treatment when compared to the XRD pattern of the untreated coating, indicating that the coating did not experience a noticeable phase shift following LE-LP. It is also further shown that the ablation damage of the laser on the coating occurs only on the surface of the coating.
Microhardness
LE-LP can cause elastic-plastic deformation of the material surface and improve the microhardness of the coating. The effect decreases as the depth increases. Figure 7 shows the microhardness of the coating cross-section. The hardness of the coating and the substrate was tested at 50 µm intervals using the bonding surface of the coating and the substrate as a standard reference. The average microhardness of the coating after LE-LP treatment increased from 713.8 to 799.9 HV0.3 [Figure 7]. Furthermore, the hardness of the coating at 50 μm from the interface is around 720 HV0.3, while the substrate’s hardness is approximately
Residual stress
Figure 8 displays the residual compressive stress on the coating surface before and after LE-LP. The average value of residual compressive stress on the surface of the untreated coating is -110 MPa, while after LE-LP treatment it is -236 MPa. Although the laser impact induces a thermal effect, the coating surface still undergoes plastic deformation and generates residual compressive stresses. The surface of the coating is subjected to the thermal effect of the laser, which, in general, causes residual tensile stresses on the surface of the material due to shrinkage after heating by laser irradiation. Nevertheless, there is still an improvement in the residual compressive stress because of the overlap rate of the light spots, which cancels out the residual tensile stress areas by the residual compressive stress areas[36].
Tribological properties
The coefficient of friction of the Ni-WC coating is displayed in Figure 9 both before and after LE-LP treatment. Figure 9 shows that the coating wear may be separated into three primary stages: break-in, steady rising, and steady wear. It is also noted that the friction coefficients of the two coatings appear to have stabilized around 0.5.
Figure 9. Coefficient of friction before and after LE-LP treatment. LE-LP: Low-energy laser peening.
Enhancing the microhardness and surface residual stress of coatings can increase their resistance to wear. Figure 10 demonstrates the tribological properties of Ni-WC coatings. After LE-LP treatment, the width of the front wear mark of coatings was reduced from 1,217.02 to 998.16 μm. The depth of the front wear mark of coatings was reduced from 72.39 to 55.76 μm. The average wear volume of the coating was reduced from 11.64 × 10-2 to 6.9 × 10-2 mm3, and the average wear rate was reduced from 4.31 × 10-5 to 2.55 × 10-5/N·mm3. The wear resistance of the coating is enhanced by the increase in coating hardness and residual compressive stress following LE-LP treatment.
Figure 10. Wear performance of coating before and after LE-LP treatment. (A) Wear scar morphology of untreated coating; (B) Wear scar morphology of LE-LP treated coating; (C) Cross-sectional profile of wear scars; (D) Wear volume and rate. LE-LP: Low-energy laser peening.
Figure 11 shows the morphology of the wear scar region before and after LE-LP treatment. An analysis of Figure 11 reveals the presence of visible plow furrows, localized spalling areas, and abrasive debris accumulation layers on the wear scar region. The wear mechanism is typical of abrasive wear. Combined with Figure 10, it can be seen that although LE-LP improved the wear resistance of the Ni-WC coating, it did not change the wear mechanism.
DISCUSSION
LE-LP is a surface deformation strengthening technology. Using plasma pressure and temperature generated by a pulsed laser, the metal surface undergoes plastic deformation, causing lattice dislocations, grain refinement, and so on. Residual compressive stresses are generated on the surface[37]. This improves the mechanical and tribological properties of the coating. Figure 12 shows a schematic diagram of the strengthening mechanism after LE-LP. LE-LP thermally affects the metal surface and reduces the roughness of the coating surface through the synergistic effect of thermal effects and plastic deformation, and the results are shown in Figure 3. The technology thermally influences the coating surface [Figure 4] and produces a large number of ablative holes. Due to the high irradiance of the laser, the water is induced to decompose. Oxygen produced by water decomposition reacts with the ablative surface to form an oxide layer[38]. However, the O elements produced due to ablation did not show significant oxidation characteristics at the coating cross section [Figure 5]. Combined with the XRD of the coating surface [Figure 6], it can be seen that the ablation effect of LE-LP on the coating occurs only on the coating surface. It shows that LE-LP on the coating not only retains the coating’s phase structure, but also has a certain improvement effect on its surface roughness.
Figure 12. Schematic diagram of the strengthening mechanism after LE-LP. LE-LP: Low-energy laser peening.
Table 2It is shown that the microhardness of the coating increases under the action of LE-LP [Figure 7], and the residual compressive stress on the coating surface improves [Figure 8], forming a hardened layer[39,40]. According to Archard’s equation, the wear rate decreases with the increase of microhardness[22]. Meanwhile, the presence of the residual stress layer inhibits the generation and extension of wear cracks[41,42]. Coatings have a layered structure and are susceptible to delamination failure. During wear testing, interfacial cracks appearing on the subsurface can lead to delamination and severance of the upper layer. High residual compressive stress can retard the formation of microcracks[43,44]. The results of the wear performance of the coatings before and after LE-LP treatment are displayed in Figure 10, which makes it clear that the coating’s wear resistance has greatly increased. The wear rate and wear volume of the coating are significantly reduced. The wear mechanism is abrasive wear. The work demonstrates that the wear resistance of Ni-WC coatings can be greatly increased using LE-LP, a surface deformation strengthening approach.
Table 2 shows the results of the surface deformation enhanced coating properties. It shows that different surface deformation peening techniques have distinct effects on the results of coating properties. High-Energy shot peening, ultrasonic surface tumbling and LE-LP decrease the surface roughness of the coating, while LP has the opposite effect. This is due to the fact that LP treats the laser-melted cladding layer, which has a low surface roughness. LP has a high irradiance, which produces tough nests on the surface of the coating after the impact, and, therefore, increases the surface roughness of the coating. The comparison also shows that the residual stresses are all manifested as residual compressive stresses. Although the range of coating hardness enhancement by LE-LP is significantly less than that of high-energy shot peening, ultrasonic surface tumbling and LP, there is an enhancement of coating wear resistance. Liu et al. found that the hardness and residual stress of the coatings were enhanced with the laser energy, but critical values existed[24]. LE-LP offers advantages such as a simple process, no contact, etc.
Effect of different surface deformation strengthening techniques on coatings
Technology | Coatings | Surface roughness | Microhardness | Residual stress | Tribological properties | Ref. |
High-energy shot peening | Cr3C2-Al2O3-NiCr | / | From 497.3 to 674 HV | -131.7 MPa | Wear rate is reduced by 98.7% | [22] |
Ultrasonic surface rolling | NiCrBSi + 15% WC | Reduced by 49.04% | From 631.4 to 873.9 HV0.2 | -404.2 MPa | Amount of wear reduced by 64.23% | [23] |
LP | NiCrBSi | Increased by 530.7% | From 388 to 530 HV0.2 | -538 MPa | / | [24] |
LE-LP | NiCrBSi + 10% WC | Reduced by 9.76% | From 704.3 to 797.8 HV0.3 | -236 MPa | Wear volume and wear rate were reduced by 40.72% and 40.83% | This work |
CONCLUSION
In this work, LE-LP was used to improve the properties of Ni-WC coatings. The effect of LE-LP on the microstructure, mechanical properties and wear resistance of the coatings was investigated. The following conclusions were drawn from the work.
(1) The surface roughness of the coating is reduced by a combination of plastic deformation and thermal influences. An oxidation reaction occurs on the surface of the coating, producing an oxide film.
(2) The microhardness of the coating increased from 704.3 to 797.8 after LE-LP treatment. The residual stress on the coating surface with an average value of -110 MPa was transformed into a residual stress with an average value of -236 MPa. A hardened layer of about 140 μm was formed.
(3) The wear resistance of the coating was further improved by LE-LP. The average wear volume of the coating was reduced from 11.64 × 10-2 to 6.9 × 10-2 mm3, and the average wear rate was reduced from 4.31 × 10-5 to 2.55× 10-5/N·mm3. The wear mechanism is abrasive wear.
LE-LP can improve the tribological properties of coatings. The research foundation for LE-LP to enhance tribological characteristics of coatings is supplied by this work. LE-LP is a post-processing method that can be combined with additive manufacturing.
DECLARATIONS
Author’s contributions
Conceptualization: Zhou L, Xing Z
Formal analysis: Zhou L, Cai Z
Methodology: Zhou X, Zhu H
Data curation, writing - original draft: Zhou L
Writing - review and editing: Cai Z
Supervision: Guo W, Liu X
Availability of data and materials
Not applicable.
Financial support and sponsorship
The paper was financially supported by the General program of the National Natural Science Foundation of China (Grant No. 52275227), the National Key Research and Development Program of China (Grant 2022YFB3401901), Key Program of National Natural Science Foundation of China (Grant U2067221), Sichuan Provincial Science and Technology Program (Grants 2022JDJQ0019 and 2022ZYD0029) and Ship Vibration and Noise Key Laboratory Program (Grants 6142204210707 and JCKY2022207CI10).
Conflicts of interest
All authors declared that there are no conflicts of interest.
Ethical approval and consent to participate
Not applicable.
Consent for publication
Not applicable.
Copyright
© The Author(s) 2024.
REFERENCES
1. Yu Y, Gong J, Fang X, et al. Comparison of surface integrity of GH4169 superalloy after high-energy, low-energy, and femtosecond laser shock peening. Vacuum 2023;208:111740.
2. Cai Z, Li Z, Yin M, Zhu M, Zhou Z. A review of fretting study on nuclear power equipment. Tribol Int 2020;144:106095.
3. Zhou L, Li X, He D, et al. Study on properties of potassium sodium niobate coating prepared by high efficiency supersonic plasma spraying. Actuators 2022;11:28.
4. Wang J, Lu Z, Huang Y, et al. The mechanism for the enhanced mechanical and piezoelectricity properties of La2O3 doped BaTiO3 ceramic coatings prepared by plasma spray. J Alloys Compd 2022;897:162944.
5. Sha J, Chen L, Liu Y, et al. Phase transformation-induced improvement in hardness and high-temperature wear resistance of plasma-sprayed and remelted NiCrBSi/WC coatings. Metals 2020;10:1688.
6. Rachidi R, El Kihel B, Delaunois F. Microstructure and mechanical characterization of NiCrBSi alloy and NiCrBSi-WC composite coatings produced by flame spraying. Mater Sci Eng B 2019;241:13-21.
7. Zhou J, Huang Y, Cai Z, et al. Preparation of NiCrBSi-WC/Co coatings by stable magnetic field assisted supersonic plasma spraying and its wear resistance mechanism. Mater Charact 2022;194:112433.
8. Zhou J, Guo W, He D, et al. Study on preparation and wear resistance of NiCrBSi-WC/Co composite coatings by pulsed magnetic field assisted supersonic plasma spraying. Surf Coat Technol 2022;448:128897.
9. Li GJ, Li J, Luo X. Effects of high temperature treatment on microstructure and mechanical properties of laser-clad NiCrBSi/WC coatings on titanium alloy substrate. Mater Charact 2014;98:83-92.
10. Liu L, Xu H, Xiao J, Wei X, Zhang G, Zhang C. Effect of heat treatment on structure and property evolutions of atmospheric plasma sprayed NiCrBSi coatings. Surf Coat Technol 2017;325:548-54.
11. Liu W, Yang X, Wan Z, Xia G, Li D, Wang S. Surface strengthening technology for mechanical parts. Surf Rev Lett 2021;28:2030006.
12. Li M, Liu D, Bai Z, et al. Hot salt corrosion behavior of Ti–6Al–4V alloy treated with different surface deformation strengthening processes. Mater Chem Phys 2023;309:128410.
13. Yin M, Cai Z, Li Z, Zhou Z, Wang W, He W. Improving impact wear resistance of Ti-6Al-4V alloy treated by laser shock peening. T Nonferr Metal Soc 2019;29:1439-48.
14. Li Z, Guo X, Yang Z, Cai Z, Jiao Y. Effect of ultrasonic surface rolling process on the microstructure and corrosion behavior of zirconium alloy in high-temperature water condition. Mater Chem Phys 2024;311:128546.
15. Yin M, Cai Z, Zhang Z, Yue W. Effect of ultrasonic surface rolling process on impact-sliding wear behavior of the 690 alloy. Tribol Int 2020;147:105600.
16. Olugbade TO, Lu J. Literature review on the mechanical properties of materials after surface mechanical attrition treatment (SMAT). Nano Mater Sci 2020;2:3-31.
17. Yao H, Hu X, Yi Z, et al. Microstructure and improved anti-corrosion properties of cold-sprayed Zn coatings fabricated by post shot-peening process. Surf Coat Technol 2021;422:127557.
18. Zhang Y, Li L, Wang X, et al. Experimental study on aluminum bronze coating fabricated by electro-spark deposition with subsequent ultrasonic surface rolling. Surf Coat Technol 2021;426:127772.
19. Chen X, Xie X, Zhang Y, Wang H, Liang Z. Tungsten carbide coating prepared by ultrasonic shot peening to improve the wear properties of magnesium alloys. J Mater Res Technol 2023;26:2451-64.
20. Cui Z, Qin Z, Dong P, Mi Y, Gong D, Li W. Microstructure and corrosion properties of FeCoNiCrMn high entropy alloy coatings prepared by high speed laser cladding and ultrasonic surface mechanical rolling treatment. Mater Lett 2020;259:126769.
21. Lu JZ, Xue KN, Lu HF, Xing F, Luo KY. Laser shock wave-induced wear property improvement and formation mechanism of laser cladding Ni25 coating on H13 tool steel. J Mater Process Tech 2021;296:117202.
22. Li F, Zhang C, Pang Q, Fang G, Xu G. Effect of high-energy shot peening on properties of high-velocity oxygen-fuel spraying. Coatings 2023;13:872.
23. Zhao Y, He Y, Zhang J, Meng C, Zhang X, Zhang S. Effect of high temperature-assisted ultrasonic surface rolling on the friction and wear properties of a plasma sprayed Ni/WC coating on #45 steel substrate. Surf Coat Technol 2023;452:129049.
24. Liu G, Xue W, Cao Y, et al. Influence of laser shock peening on microstructure and property of Ni60 cladding layer and the combined area of 20CrNiMo alloy. J Laser Appl 2023;35:022009.
25. Lin Y, Cai Z, Li Z, et al. Study on the abrasive wear behavior of laser shock peening Ti-6Al-4V titanium alloy under controlled cycling impact. Wear 2019;426-7:112-21.
26. Dong T, Zhou X, Li G, Liu L, Wang R. Microstructure and corrosive wear resistance of plasma sprayed Ni-based coatings after TIG remelting. Mater Res Express 2018;5:026411.
27. Geng Z, Hou S, Shi G, Duan D, Li S. Tribological behaviour at various temperatures of WC-Co coatings prepared using different thermal spraying techniques. Tribol Int 2016;104:36-44.
28. Fang X, Gong J, Yu Y, et al. Study on the fretting wear performance and mechanism of GH4169 superalloy after various laser shock peening treatments. Opt Laser Technol 2024;170:110301.
29. Abeens M, Muruganandhan R, Thirumavalavan K. Effect of Low energy laser shock peening on plastic deformation, wettability and corrosion resistance of aluminum alloy 7075 T651. Optik 2020;219:165045.
30. Trdan U, Porro JA, Ocaña JL, Grum J. Laser shock peening without absorbent coating (LSPwC) effect on 3D surface topography and mechanical properties of 6082-T651 Al alloy. Surf Coat Technol 2012;208:109-16.
31. Praveenkumar K, Swaroop S, Manivasagam G. Effect of multiple laser shock peening without coating on residual stress distribution and high temperature dry sliding wear behaviour of Ti-6Al-4 V alloy. Opt Laser Technol 2023;164:109398.
32. Wang H, Keller S, Chang Y, et al. Effect of laser shock peening without protective coating on the surface mechanical properties of NiTi alloy. J Alloys Compd 2022;896:163011.
33. Petronić S, Čolić K, Đorđević B, Milovanović D, Burzić M, Vučetić F. Effect of laser shock peening with and without protective coating on the microstructure and mechanical properties of Ti-alloy. Opt Laser Eng 2020;129:106052.
34. Yang Y, Zhou W, Guo Y, et al. Effect of laser shock peening without protective coating on surface integrity of titanium-based carbon-fibre/epoxy laminates. Opt Laser Technol 2023;167:109685.
35. Park C, Jung D, Chun E, Ahn S, Jang H, Kim Y. Effect of laser shock peening without coating on fretting corrosion of copper contacts. Appl Surf Sci 2020;514:145917.
36. Sano Y, Akita K, Sano T. A mechanism for inducing compressive residual stresses on a surface by laser peening without coating. Metals 2020;10:816.
38. Xue D, Jiao Y, He W, Shen X, Gao Y, Wang L. Investigations into the improvement of the mechanical properties of Ti-5Al-4Mo-4Cr-2Sn-2Zr titanium alloy by using low energy laser peening without coating. Materials 2020;13:1398.
39. Wang H, Jürgensen J, Decker P, et al. Corrosion behavior of NiTi alloy subjected to femtosecond laser shock peening without protective coating in air environment. Appl Surf Sci 2020;501:144338.
40. Jiao Y, He W, Shen X. Enhanced high cycle fatigue resistance of Ti-17 titanium alloy after multiple laser peening without coating. Int J Adv Manuf Technol 2019;104:1333-43.
41. Troiani E, Zavatta N. The effect of laser peening without coating on the fatigue of a 6082-T6 aluminum alloy with a curved notch. Metals 2019;9:728.
42. Chen Z, Wang Z, Liu J, et al. Enhancing the tribological properties of TA1 pure titanium by modulating the energy of pulsed laser nitriding. Opt Laser Technol 2024;169:110118.
43. Cao Y, Sun J, Ma F, et al. Effect of the microstructure and residual stress on tribological behavior of induction hardened GCr15 steel. Tribol Int 2017;115:108-15.
Cite This Article
How to Cite
Download Citation
Export Citation File:
Type of Import
Tips on Downloading Citation
Citation Manager File Format
Type of Import
Direct Import: When the Direct Import option is selected (the default state), a dialogue box will give you the option to Save or Open the downloaded citation data. Choosing Open will either launch your citation manager or give you a choice of applications with which to use the metadata. The Save option saves the file locally for later use.
Indirect Import: When the Indirect Import option is selected, the metadata is displayed and may be copied and pasted as needed.
About This Article
Copyright
Data & Comments
Data
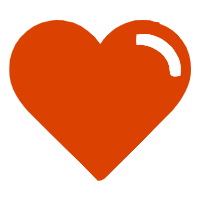
Comments
Comments must be written in English. Spam, offensive content, impersonation, and private information will not be permitted. If any comment is reported and identified as inappropriate content by OAE staff, the comment will be removed without notice. If you have any queries or need any help, please contact us at [email protected].