A trade-off optimization model of environment impact and manufacturing cost for machining parts
Abstract
Motivation: Throughout the life cycle, the environmental impact and manufacturing costs of a part are largely determined at the design stage. Therefore, a part design optimization method considering these two factors is proposed in this paper. At the same time, the comprehensive benefit is taken as the trade-off of these two factors. The reduction of the comprehensive benefit indicates that the optimized part has achieved better environmental and economic performance results.
Methods: Firstly, the model is reconstructed using the dimension-driven method, and the feature information of the new part is extracted. Then, machining process planning is carried out based on the feature information. Secondly, a design optimization model for the comprehensive benefit is established based on the genetic algorithm. The model takes the dimension parameters of the part as the optimization variables and the reduction of the comprehensive benefit as the optimization objective. With the help of the Simulation plug-in for SolidWorks, the static analysis of the optimized model is conducted to determine whether it meets the performance requirements. Finally, the design optimization prototype system oriented to comprehensive benefit is established. The feasibility and effectiveness of the proposed method are verified by taking the intermediate shaft of the belt conveyor reducer-sixth order step shaft as an example.
Results: The case study shows that the optimization result of comprehensive benefit is 1.63%, which verifies the feasibility and effectiveness of the part design optimization method proposed in this paper.
Keywords
INTRODUCTION
The development of the economy and technology has led to increased energy consumption and pollutant emissions, and the environment is deteriorating[1-3]. In addition, due to the constraints of resources and the environment, the era of high costs is also coming, and the sustainable development of the mechanical parts manufacturing industry is facing significant challenges. Therefore, the resource consumption and environmental impact of parts in the manufacturing process are receiving growing attention. Although the cost of a part design only accounts for 10%-15% of the total, it has a decisive impact on the subsequent 80% cost consumption[4], and 75% of the environmental impact is directly or indirectly caused by the design stage[5].
Life cycle assessment (LCA), an environmental performance evaluation tool, is widely used in part design decisions[6]. However, it usually does not involve the economic or social aspects of the part[7]. Designers cannot make the final decision based only on the environmental assessment results. Therefore, it is necessary to combine LCA with other economic analysis tools. The economic analysis tool mostly used in integrating with LCA is called life cycle costing (LCC). Campbell et al. proposed a technology and economic evaluation method to reduce shielding gas consumption[8]. The other method calculates environmental costs by integrating LCA and LCC. Georgiadis and Besiou use dynamics ideas to analyze environmental and economic sustainability for waste electrical and electronic equipment (WEEE) closed-loop supply chains with recycling[9]. Santos et al. proposed an automatic LCA/LCC analysis within a building information modeling (BIM)-based environment[10]. Hou et al. proposed an integrated LCA-LCC model of environmental and economic factors for highway engineering technical schemes[11]. Moreover, further research on improving and optimizing the initial design after getting the integrated evaluation result has not been mentioned.
For this problem, Xiao et al. established the energy consumption and cost objectives in the manufacturing and further processing of blanks by optimizing the parameters[12]. Ameli et al. proposed an optimization method based on mathematical planning used as a design aid tool that enables a designer to assess the life cycle cost and environmental impact[13]. Deng et al. proposed a method for optimizing initial part design to achieve optimal environmental and economic performance results in initial mechanical part design[14]. Based on the theory of social willingness to pay for potential environmental impacts, Shi et al. identified the resource consumption, environmental emissions, and costs of mechanical part manufacturing from an economic and ecological perspective[15]. They provided theoretical and data support for energy conservation and mechanical part manufacturing emission reduction. Simões et al. used LCA/LCC to evaluate the life cycle environment and economic performance of three different car multimedia solution chassis[16]. Zhang and Meng use a multi-target decision-making method to design the index system, establish the evaluation optimization algorithm model of the green electromechanical part design scheme, and comprehensively evaluate and optimize the green part design scheme from the aspects of the economy[17].
In summary, current research on design optimization often occurs after the design is completed. It fails to utilize the relevant feature information of the solid model fully and requires a significant amount of resources and time to collect environmental impact and cost data. However, with the powerful and comprehensive API interface, SolidWorks allows designers to access part feature information easily through secondary development techniques. In the use of SolidWorks for product design, Hu et al. studied the intelligent and automatic design method of hammer mill parts through dynamic link library (DLL) development with the help of SolidWorks secondary development technology[18]. Xue et al. proposed the development of computer-aided design software for the shell-and-tube heat exchanger based on SolidWorks parameterized design and SQL data management[19]. Reddy et al. proposed a constraint-based SolidWorks modeling design method that can generate automatic and hierarchical SolidWorks models based on constraint relations among geometric objects[20]. Li and Yin extracted the mates feature information of the top-level parts in the structural feature tree of the CAD model in the SolidWorks platform with the help of SolidWorks API technology[21]. The extracted information is then arranged in a certain order and stored in the database. Based on this, a new design structure matrix generation system is constructed. Yuan et al. developed an interactive parametric design system integrating a three-dimensional assembly model and two-dimensional engineering drawing of a static pressure box by using the macro recording function of SolidWorks as a secondary development tool and Visual Basic language, which realized the static pressure box design automation[22].
Based on the above review, this paper proposes a part design optimization method oriented to the comprehensive benefit of environmental impact and manufacturing cost under the SolidWorks environment [Figure 1]. The part feature information is extracted using SolidWorks API functions. Based on the feature information of the part, generative rules are used to realize the machining process planning of the part. Then, by using the process information of the parts, the optimization model oriented to the comprehensive benefit is established, and the comprehensive benefit is improved by optimizing the part design. Finally, based on the SolidWorks software, a design optimization prototype system oriented to the comprehensive benefit is developed to help designers quickly complete part development by considering environmental impact and manufacturing cost comprehensively in the part design stage.
METHODOLOGY
Machining process planning based on part feature information
In this paper, process information is the basis of establishing an optimization model, and process planning is completed based on part feature information. Therefore, this section focuses on the machining process planning based on feature information. The construction of the optimization model will be introduced in Section “Construction of design optimization model for the comprehensive benefit based on genetic algorithm”. The model is the basis of feature information extraction, so this section first uses the dimension-driven method to construct the model. Then, feature extraction and expression of the part are carried out. Finally, machining process planning is realized based on feature information.
Model reconstruction based on the dimension-driven method
The dimension-driven method[23] keeps the model structure of the parts unchanged. All the actual dimensions that affect the model structure are defined as dimension variables, and by assigning different dimension values to these dimension variables, a series of parts with the same structure but diverse dimensions can be obtained. Part modeling using the dimension-driven approach must be supported by a model library[24], which is a set of model files drawn by the user and saved in a specified program directory, and the dimensions required to be modified are marked during the construction of the model library.
When the model requires reconstruction, the “DisplayDimension” interface provided by SolidWorks is used to traverse all the dimensions that necessitate modification, that is, editable dimensions, and display them to the user in the form of a dialog box. For objects such as cylinders, the extracted editable dimension information is shown in Table 1.
The editable dimension information of a cylinder
Dimension name | Value(mm) |
Diameter@Sketch1 | 40 |
Length@Boss-Extrude1 | 60 |
Then, the user enters a new value for the corresponding editable dimension in the dialog box. For example, change the values of “Diameter @ Sketch1” to 41 and “Length@Boss-Extrude1” to 61. The background reads them, and the editable dimensions of the model are modified using the “Parameter” interface provided by SolidWorks to obtain a model that meets the needs. The C# implementation code of the “Parameter” interface is as follows:
{
……
//Modify the model dimensions.
part.Parameter(Diameter@Sketch1).SystemValue = 0.001 * Convert.ToDouble(41);
part.Parameter(Length@Boss-Extrude1).SystemValue = 0.001 * Convert.ToDouble(61);
//Model reconstruction.
part.EditRebuild;
}
The model reconstruction process based on the dimension-driven method is shown in Figure 2.
Part feature identification and expression
Each part contains some features with processing significance, such as holes, slots, faces, chamfers, etc. So, obtaining features is particularly important. The geometric feature information of the part is stored in the geometric entity, which can be obtained using the API interface “GetTypeName” provided by SolidWorks. The basic idea of part feature information identification and extraction is as follows. First, the feature traversal is carried out, and the corresponding feature subroutine module is entered according to the feature type and the location of the orientation plane to obtain geometric parameters and other operations. Finally, the related information is saved in the SQL Server 2014 database. The process of feature object recognition is shown in Figure 3. Table 2 presents information on some of the features and their feature dimensions.
Part of the feature and feature dimension information
Feature | Dimension type 1 | Value 1 | Dimension type 2 | Value 2 | Dimension type 3 | Value 3 |
Cylindrical surface | Diameter | D1 | Length | H1 | - | - |
End face | Diameter | D2 | - | - | - | - |
Keyway | Width | W3 | Length | H3 | Depth | H4 |
All the features of a part constitute the feature set, expressed as:
Where Fi represents the i-th feature of the part, and n represents the total number of features.
In addition, features contain various types of design information, which requires further orderly expression of information. Therefore, the expression of a single feature design information is established as:
Where Ti represents the name of the i-th feature, Pi indicates the feature parameter set of the i-th feature (including the feature dimension type and its specific value), and Ji denotes the machining accuracy requirement of the i-th feature.
Machining process planning based on part feature information
According to the relevant literature research[25-27], the generative rules[28] are used to construct the following table of machining process rules corresponding to different features [Table 3].
A table of machining process rules corresponding to some features
Feature | Machining accuracy (Ra, µm) | Process route | Machining equipment | Machining tool |
Cylindrical surface | Rough (12.5~6.3) | Rough turning | Gold CNC CA6140 horizontal lathe/M1432A Cylindrical grinding machine | YT5/YT15/Grinding wheel |
Semi-finishing (6.3~3.2) | Rough turning, semi-finishing turning | |||
Finishing (0.8~0.2) | Rough turning, semi-finishing turning, rough grinding, finishing grinding | |||
End face | Rough (12.5~6.3) | Rough turning | Gold CNC CA6140 horizontal lathe | YT5/YT15 |
Semi-finishing (6.3~3.2) | Rough turning, semi-finishing turning | |||
Finishing (1.6~0.8) | Rough turning, semi-finishing turning, finishing turning | |||
Keyway | Rough (50~12.5) | Rough milling | X5032 vertical milling machine | High speed steel cylindrical milling cutter |
Semi-finishing (6.3~3.2) | Rough milling, semi-finishing milling | |||
Finishing (3.2~1.6) | Rough milling, semi-finishing milling, finishing milling |
The general form of the generative rule is “IF P THEN Q”. If the P condition is satisfied, the Q action is taken. For example, if “Feature” = “Cylindrical surface” and “Machining accuracy” = “Rough”, then the processing route is “Rough turning”. The determination of subsequent processing equipment and cutting tools is based on the process route. For example, if “Process route” = “Rough turning”/“Semi-finishing turning”/“Finishing turning” then “Machining equipment” = “Gold CNC CA6140 horizontal lathe”. The machining tools are selected according to the different process routes. The “Grinding wheel” and “High speed steel cylindrical milling cutter” are used for grinding and milling, respectively. YT5 is used for rough turning, and YT15 is employed for semi-finishing and finishing turning.
Construction of design optimization model for the comprehensive benefit based on genetic algorithm
Parts will generate environmental impact and cost throughout the life cycle. Their life cycle generally includes raw material acquisition, manufacturing, transportation, use, and waste recycling stages. Environmental impact and cost at the raw material acquisition and manufacturing stages can be obtained through the feature information of parts. However, they are also related to transport vehicles, transport distance, actual working conditions, local environment, and other factors in the remaining three stages. Therefore, the design optimization model considers only the comprehensive benefit of environmental impact and cost at the raw material acquisition and manufacturing stages.
Genetic algorithm
The optimization model constructed in this paper aims to reduce the comprehensive benefits of the parts, which is a single-objective optimization. At present, common single-objective algorithms include genetic algorithm[29], particle swarm optimization[30], colony algorithm[31], etc. All of them can be used as optimization tools in this paper. However, compared with other methods, the genetic algorithm has the following advantages: (1) Powerful global search ability. It can explore the whole search space and has the opportunity to jump out of the local optimal solution to find the global optimal solution or get close to the optimal solution; (2) Powerful adaptability. The genetic algorithm can be adjusted and optimized according to the structure and characteristics of the problem. Setting appropriate parameters and operations can better adapt to the characteristics of the problem and improve the search performance; (3) Powerful parallel performance. The genetic algorithm is inherently parallel. It can achieve multiple individual evolutions through parallel operation, thus speeding up the search process; (4) Powerful interpretability. The running process of the genetic algorithm can be interpreted as the change and evolution of individual adaptability in the population, which exhibits a high degree of interpretability.
Therefore, the genetic algorithm is chosen as the optimization tool of this paper. Figure 4 shows the basic flow of the genetic algorithm. The steps of part design optimization based on the genetic algorithm are as follows:
(1) Initialize the population. Randomly generate N individuals to form a population;
(2) Fitness calculation. The fitness calculation formula is the main means of this algorithm to evaluate individual merits. Population fitness is calculated according to the problem. This paper takes the comprehensive benefit of the part as the fitness function;
(3) Selection. The excellent individuals are selected from the current population and used as the parent population to pass on their excellence to the next generation;
(4) Crossover. Crossover operation can generate new individuals, and the new individuals combine the excellent performance of the parent individuals;
(5) Mutation. Randomly select individuals from the population for mutation. Mutation provides new individuals for the population and develops it for diversification. It is the most important part of the genetic algorithm to avoid local optimality;
(6) Repeat the above steps, and the iteration ends when the maximum number of iterations is reached or the optimal solution is output.
Determination of the objective function
Establish an objective function for the comprehensive benefit of environmental impact and manufacturing cost, obtained as:
Where F represents the comprehensive benefit of the part, which is a trade-off between environmental impact and cost. It can be used to measure the quality of a design. The lower the comprehensive benefit, the better the environmental impact and economic performance results of the design. λ1 indicates the weighting factor of environmental impact. EI means the environmental impact sub-objective function. λ2 denotes the weighting factor of manufacturing cost. C symbolizes the manufacturing cost sub-objective function.
Environmental impact sub-objective function
The environmental impact of the raw material acquisition stage is mainly determined by the mass of the raw material and its environmental impact indicators, and the environmental impact of the manufacturing stage is mainly determined by the electric energy consumption of the machining process and its environmental impact indicators.
This paper used “Global Warming Potential (GWP)”, “Acidification Potential (AP)”, “Photochem. Ozone Creation Potential (POCP)”, “Eutrophication Potential (EP)”, “Ozone Layer Depletion Potential (ODP)”, “Abiotic Depletion elements (ADP e)”, and “Abiotic Depletion fossil (ADP f)” of the Institute of Environmental Sciences evaluation index system to evaluate environmental impact comprehensively. Since there are many kinds of environmental impacts and the quantification unit is not uniform, it is necessary to give varying weights to achieve weighted analysis according to the degree of harm of various environmental impacts. The weight factors of the environmental impact indicators chosen for this paper are the weight factors of environmental impacts in Sphera GaBi software[32] [Table 4].
Weight factors of each environmental impact indicator
Type of environmental impact indicator | Unit | Normalization | Weighting | Weight ωl (nondimensional parameter) |
GWP | kg CO2 eq. | 2.37E-14 | 9.3 | 2.20E-13 |
AP | kg SO2 eq. | 4.18E-12 | 6.1 | 2.55E-11 |
POCP | kg Ethene eq. | 2.72E-11 | 6.5 | 1.77E-10 |
EP | kg Phosphate eq. | 6.33E-12 | 6.6 | 4.18E-11 |
ODP | kg R11 eq. | 4.41E-09 | 6.2 | 2.73E-08 |
ADP e | kg Sb eq. | 2.77E-09 | 6.4 | 1.77E-08 |
ADP f | MJ | 2.63E-15 | 7 | 1.84E-14 |
(1) Environmental impact EIr of the raw material acquisition stage.
Where M represents the mass of the part. fl indicates the l-th environmental impact indicator of the raw material. ωl stands for the weight factor of the l-th environmental impact indicator.
(2) Environmental impact at the manufacturing stage.
The manufacturing stage is processing blanks into finished parts, involving various methods. The processes of casting, forging, heat treatment, and cutting are considered in this paper.
Therefore, the environmental impact EIm of the manufacturing stage can be calculated by:
Where Ez represents the electric energy consumption of the casting process. Ed signifies the electric energy consumption of the forging process. Er denotes the electric energy consumption of the heat treatment process. Ec stands for the electric energy consumption of the cutting process. fel indicates the l-th environmental impact indicator of the electric energy.
The electric energy consumption Ez of the casting process can be calculated by:
Where Cb represents the specific heat capacity of the raw material. ΔTz indicates the temperature difference in the casting process of raw material. ηz denotes the electric energy conversion rate in the casting process.
The electric energy consumption Ed of the forging process can be calculated by:
Where ΔTd represents the temperature difference in the forging process of raw material. Pd indicates the average power of the forging process in a working cycle. Td symbolizes the duration of a working cycle of the forging press. ηd signifies the conversion rate of electric energy in the forging process.
According to ref[33], the electric energy consumption Er of the heat treatment process can be calculated by:
Where Nb represents the standard process energy consumption. k1 denotes the conversion factor of the common heat treatment process. k2 stands for the common heat treatment process heating mode factor. k3 indicates the common heat treatment process part mode factor. k4 symbolizes the common heat treatment process workpiece material factor. k5 points to the common heat treatment process loading factor.
The electric energy consumption Ec of the cutting process can be calculated by:
It is assumed that the part needs to undergo O times of cutting, and Pk is the average power of the equipment used in the k-th cutting. Tk is the time taken for the k-th cutting. Its estimation formulas are as follows, according to reference[34] (Only the calculation of the machining time of the cutting method involved in Table 2 is listed).
Cylindrical surface turning processing time:
Where Hk is the height of the cylindrical surface, which indicates the processing length of the k-th cylindrical surface turning of the part. y + ∆ is the in-cut and over-cut amount, which is found in the cutting concise handbook. Nk represents the workpiece speed of the k-th cylindrical surface turning of the part; fk indicates the feed of the k-th cylindrical surface turning.
Cylindrical surface grinding processing time:
Where K represents the correction coefficient, generally 1.2-1.5. Hk is the height of the cylindrical surface, which denotes the processing length of the k-th cylindrical surface grinding of the part. Nk stands for the spindle speed of the part during the k-th cylindrical grinding process. vk indicates the k-th cylindrical grinding feed rate of the part.
End face turning processing time:
Where Dk is the diameter of the end face. Nk represents the rotational speed of the workpiece during the k-th end face turning of the part. fk signifies the feed of the k-th end face turning of the part.
Keyway milling processing time:
Where Lk is the keyway length, which represents the processing length of the k-th keyway milling of the part. vfk points to the feed per second of the k-th keyway milling of the part.
Therefore, the weighted analysis of the overall environmental impact is calculated by:
Where A is a non-dimensional parameter used to adjust the order of magnitude of environmental impact.
Manufacturing cost sub-objective function
In this paper, the manufacturing cost of parts considers the raw material acquisition and manufacturing stages.
(1) The cost Cr of the raw material acquisition stage is mainly determined by the mass and unit price of the raw material, which is calculated by:
Where frc represents the unit price of raw material.
(2) The cost Cm of the manufacturing stage includes the purchase cost of electric energy consumed by the equipment used in each processing process, tool cost, labor cost, and cutting fluid cost. The replacement cycle of the cutting fluid is one to three months, and this paper only considers the machining process of a single part, so the cost of the cutting fluid is not taken into account.
Therefore, the cost of the manufacturing stage is calculated by:
Where Ce represents the purchase cost of electric energy consumed by the equipment used in each manufacturing process. Ct indicates the cost of the cutting tools. Ch stands for the labor cost.
The purchase cost Ce of electric energy consumed by the equipment used in each manufacturing process can be calculated by:
Where fmc represents the unit price of electricity.
The cutting process will cause the consumption of the cutting tools, so the cost Ct of the cutting tools is calculated by:
Where TLk and fk are the tool life and unit price of the corresponding cutting tool at the k-th cutting.
The labor cost Ch can be calculated by:
Where T represents the time required for the part to complete all machining processes, and fh indicates the unit price of the worker.
Therefore, the manufacturing cost calculation is expressed as:
Based on the above content, the final objective function is obtained as:
Selection of optimization variables
In Equation (21), the weighting factor λ1 of environmental impact and the weighting factor λ2 of manufacturing cost are determined by a certain method, so they are fixed values. A is a non-dimensional parameter used to adjust the order of magnitude of environmental impact, which is a fixed value. When the raw materials of the parts are determined, the corresponding specific heat capacity Cb and the environmental impact indicator fl are also established. fel is the environmental impact indicator of electric energy and is also a fixed value. ωl is the weight factor of the environmental impact indicator, as given in Table 2. In the casting process, the casting temperature difference ΔTz is determined by the manufacturing requirements, and the electric energy conversion rate ηz is determined by the technical conditions. ΔTz and
When the material is constant, variations arise in the dimensions of the part and the volume also changes. As the density remains constant, the mass of the part will change as well. The dimensions of the part do not change much before and after optimization. The cutting parameters can be considered fixed, which leads to the conclusion that the part dimensions determine the cutting time. In summary, the comprehensive benefit value is mainly affected by the dimension parameters of the parts. Therefore, the part dimensions are selected as optimization variables, including the diameter parameter D, the length and depth parameter H, and the width parameter W.
Constraints
In the process of optimizing the design of the mechanical part, a range of permissible values for the part dimensions exists, denoted as:
Designing parts ultimately aims to meet the use requirements for the design objectives, so stress is chosen as a measure to verify whether the optimized part can fulfill the use, as determined by:
Where σ is the maximum equivalent stress of the optimized part in the working state, and σmax is the allowable stress of the material used.
Construction of design optimization prototype system under the SolidWorks environment
System development and operating environment
A design optimization prototype system based on SolidWorks is developed to improve the efficiency of part design optimization. The system uses C# language to load the API interface of SolidWorks software. It completes the construction of the human-computer interaction interface for a series of operations, including model reconstruction, feature information extraction, and so on.
The system is built and compiled using Visual Studio 2019 on the Windows 10 operating system. Since optimizing the comprehensive benefit of environmental impact and cost of mechanical parts depends on the underlying data, SQL Server 2014 is integrated to build a basic database for data management and calls. The environment configuration for system development can be found in Table 5.
Environment configuration for system development
Environment configuration | Description |
Operating system | Win10 |
Integrated development tool | Microsoft Visual Studio 2019 |
Development software | SolidWorks 2020 |
Database | SQL Server 2014 |
Programming language | C# |
Processor | Intel(R) Core(TM) i5-10200H CPU @ 2.40GHz |
System structure design
The design goal of the prototype system is to provide users with functions such as part model reconstruction, material setting, dimension information extraction, feature identification, machining process planning, comprehensive benefit calculation, and part design optimization. According to the system design objectives and design principles, the overall structure of the system is established, as shown in Figure 5, including three levels: user, business, and support layers:
(1) The user layer provides designers with a visual front-end operation interface, which can display the trigger buttons that can be operated during the software work process. At the same time, the data processing process of the business and support layers can be visually displayed to the designers in the form of charts;
(2) The business layer performs the system function in the background to realize the data exchange between the user and support layers. Its functions include parts editable dimensions extraction, feature identification, machining process planning, comprehensive benefit calculation, parts design optimization, etc.;
(3) The support layer provides data support for the prototype system, including the feature information database, machining process database, indicator database, etc.
System workflow
The main workflow of the system includes the following links. The system flow is shown in Figure 6.
(1) Connect to SolidWorks. In the Microsoft Visual Studio 2019 integrated environment, C# is used to build the system. First, the connection between the system and SolidWorks software must be established, and SolidWorks can be operated through the system;
(2) Model import and reconstruction. The user selects the part to be studied, and the system sends commands to import it into SolidWorks software. Then, the system obtains all the editable dimension information of the part by calling API functions and reconstructs the model by inputting initial dimensions;
(3) Manufacturing planning. The user will successively set the part material, plan the molding process (including the casting and forging process), and conduct the heat treatment process. After that, the system calls the corresponding API function to traverse the part, identify the features and extract the corresponding feature information. Finally, machining process planning and step sequencing are carried out based on the feature information;
(4) Comprehensive benefit calculation. The quantification equations of environmental impact and cost established in Section “Manufacturing planning” are written into the system to realize the comprehensive benefit calculation;
(5) Part design optimization. The initial design is optimized by taking the allowable dimension range of parts as the constraint condition, taking the dimensions of parts as the optimization variables, and aiming to reduce the comprehensive benefit;
(6) Performance analysis of the optimized model. With the help of the Simulation plug-in for SolidWorks, the working state is simulated for stress check to determine whether the optimized model still meets the requirements.
EXAMPLE VERIFICATION
This paper uses the intermediate shaft of belt conveyor reducer - sixth order step shaft as an example. The main interface of the system constructed in this paper is shown in Figure 7. The system can help designers quickly complete model reconstruction, manufacturing planning, and comprehensive benefit calculation. After that, with the comprehensive benefit as the optimization objective and dimensions as the optimization variables, the genetic algorithm realizes part design optimization. Finally, the performance of the optimized part is evaluated with the help of the Simulation plug-in for SolidWorks.
Model import and reconstruction
Select the sixth order step shaft from the model library and import it into SolidWorks. Click “Get editable dimensions” to get all model dimensions, save them to the SQL Server 2014 database, and then display them in the “dataGridView” control [Figure 8]. Under the premise of meeting the assembly requirements of the reducer, the designer enters the dimensions of the step shaft and its allowable symmetric tolerance. In this example, all symmetric tolerances are set to 1, and the desired model is obtained by clicking “Save”.
Manufacturing planning
Triggering the “Manufacturing planning” first carries out material setting, molding process planning, and heat treatment process planning. The shaft is generally made of carbon steel and alloy steel. Round steel is generally used for shafts with smaller diameters. It is best to use cold-drawn steel directly. Forging blanks are used for shafts with large diameters or large step diameter variations. Because carbon steel is cheaper than alloy steel and less sensitive to stress concentration, heat treatment can improve its wear resistance and fatigue strength. So, most of the shafts are made of carbon steel. This paper selects a common carbon steel from the SolidWorks material library, and its model number is AISI 1045. Its properties are available from the SolidWorks material library, as detailed in Table 6.
AISI 1045 steel properties
Properties | Value | Unit |
Elastic modulus | 205 | GPa |
Poisson’s ratio | 0.29 | N/A |
Shear modulus | 80 | GPa |
Density | 7,850 | kg/m3 |
Tension strength | 0.625 | GPa |
Yield strength | 0.53 | GPa |
Allowable stress [σ] ≤ 173 MPa |
In this paper, the forging process is selected for blank forming. The initial forging temperature is 1,200 °C, and the final forging temperature is 800 °C. For the blank heat treatment process, choose normalizing and quenching treatment. The heat treatment process information is shown in Table 7, according to reference[33].
Heat treatment process information of sixth order step shaft
Type of information | Normalizing | Quenching |
Electrical consumption of standard process/kW·h | 0.28 | 0.28 |
Process conversion factor | 1.1 | 1 |
Heating mode factor | 1 | 1.5 |
Part mode factor | 1.6 | 1.6 |
Workpiece material factor | 1 | 1 |
Loading factor | 1.6 | 1.6 |
Afterward, the part is planned for machining, and the feature identification is performed first. Set the machining accuracy for each feature. Then, the machining process planning is conducted. For the same machining equipment under the same type of machining, the principle of first roughing and then finishing is used to sequence the steps to reduce the time of tool change, equipment change, and workpiece clamping to reduce the cost. The final machining process planning results are shown in Figure 9. The results of the complete machining process are shown in Table 8.
The machining process planning results of step shaft
ID | Machining feature | Machining accuracy | Process route | Machining equipment | Machining tool | Machining time |
1 | Cylinder surface | Finishing | Rough turning | CA6140 | YT5 | 150.94 |
2 | Cylinder surface | Semi-finishing | Rough turning | CA6140 | YT5 | 50.31 |
3 | Cylinder surface | Finishing | Rough turning | CA6140 | YT5 | 322.01 |
4 | Cylinder surface | Semi-finishing | Rough turning | CA6140 | YT5 | 75.47 |
5 | Cylinder surface | Finishing | Rough turning | CA6140 | YT5 | 206.29 |
6 | Cylinder surface | Finishing | Rough turning | CA6140 | YT5 | 150.94 |
7 | End face | Semi-finishing | Rough turning | CA6140 | YT5 | 49.06 |
8 | End face | Semi-finishing | Rough turning | CA6140 | YT5 | 50.31 |
9 | Cylinder surface | Finishing | Semi-finishing turning | CA6140 | YT15 | 64.29 |
10 | Cylinder surface | Semi-finishing | Semi-finishing turning | CA6140 | YT15 | 21.43 |
11 | Cylinder surface | Finishing | Semi-finishing turning | CA6140 | YT15 | 137.14 |
12 | Cylinder surface | Semi-finishing | Semi-finishing turning | CA6140 | YT15 | 32.14 |
13 | Cylinder surface | Finishing | Semi-finishing turning | CA6140 | YT15 | 87.86 |
14 | Cylinder surface | Finishing | Semi-finishing turning | CA6140 | YT15 | 64.29 |
15 | End face | Semi-finishing | Semi-finishing turning | CA6140 | YT15 | 20.89 |
16 | End face | Semi-finishing | Semi-finishing turning | CA6140 | YT15 | 21.43 |
17 | Cylinder surface | Finishing | Rough grinding | M1432A | Grinding wheel | 55.36 |
18 | Cylinder surface | Finishing | Rough grinding | M1432A | Grinding wheel | 118.1 |
19 | Cylinder surface | Finishing | Rough grinding | M1432A | Grinding wheel | 75.66 |
20 | Cylinder surface | Finishing | Rough grinding | M1432A | Grinding wheel | 55.36 |
21 | Cylinder surface | Finishing | Finishing grinding | M1432A | Grinding wheel | 105.08 |
22 | Cylinder surface | Finishing | Finishing grinding | M1432A | Grinding wheel | 224.17 |
23 | Cylinder surface | Finishing | Finishing grinding | M1432A | Grinding wheel | 143.61 |
24 | Cylinder surface | Finishing | Finishing grinding | M1432A | Grinding wheel | 105.08 |
25 | Keyway | Rough | Rough milling | XA5032 | Cylindrical milling cutter | 18 |
26 | Keyway | Rough | Rough milling | XA5032 | Cylindrical milling cutter | 18.32 |
The comprehensive benefit calculation
The environmental impact indicators are from the GaBi database [Table 9].
Environmental impact indicators
Type of environmental impact | AISI 1045 steel | Electricity | Unit |
GWP | 1.74E+00 | 7.91E-01 | kg CO2 eq. |
AP | 3.52E-03 | 2.32E-03 | kg SO2 eq. |
POCP | 6.71E-04 | 2.73E-04 | kg Ethene eq. |
EP | 3.7E-04 | 2.34E-04 | kg Phosphate eq. |
ODP | 1.39E-10 | 3.55E-12 | kg R11 eq. |
ADP e | 2.87E-07 | 5.00E-08 | kg Sb eq. |
ADP f | 1.71E+01 | 7.92E+00 | MJ |
Trigger the “Environmental impact assessment” button to calculate the environmental impact of the step shaft. The results of the environmental impact assessment are presented in Table 10.
The results of the environmental impact assessment
Type of environmental impact | Value | Unit |
GWP | 2.86E+01 | kg CO2 eq. |
AP | 8.00E-02 | kg SO2 eq. |
POCP | 1.00E-02 | kg Ethene eq. |
EP | 1.00E-02 | kg Phosphate eq. |
ODP | 7.23E-10 | kg R11 eq. |
ADP e | 2.61E-06 | kg Sb eq. |
ADP f | 2.85E+02 | MJ |
In this paper, the non-dimensional parameter A is 1012. Trigger the “Quantification of environmental impact” to carry out weighted quantification of environmental impact assessment results. The quantification results are shown in Table 11. The quantified value of the total environmental impact of the step shaft in the raw material acquisition and manufacturing stages is 15.7. The largest impact is GWP, which accounts for about 40.14% of the total environmental impact.
Quantification results of the environmental impact
Type of environmental impact | Value | Percentage |
GWP | 6.29E+00 | 40.14% |
AP | 1.96E+00 | 12.51% |
POCP | 1.80E+00 | 11.48% |
EP | 3.30E-01 | 2.11% |
ODP | 1.97E-05 | 0.00% |
ADP e | 5.00E-02 | 0.32% |
ADP f | 5.24E+00 | 33.44% |
Total environmental impact value | 1.57E+01 | 100% |
Triggering “Manufacturing cost calculation” calculates the cost of the step shaft’s raw material acquisition and manufacturing stages. The manufacturing cost of the step shaft is 67.07 yuan, of which the cost of the raw material acquisition stage is 21.54 yuan, and that of the manufacturing stage is 45.53 yuan.
Finally, trigger the “Comprehensive benefit calculation” to calculate the comprehensive benefit of the step shaft. Set the environmental impact and cost weighting factors as λ1 = 0.53 and λ2 = 0.47, according to reference[35]. The result of the comprehensive benefit calculation is shown in Figure 10. The comprehensive benefit value is 39.83, the environmental benefit value is 8.31, and the manufacturing cost-benefit value is 31.52.
Part design optimization
In this paper, the genetic algorithm is used to optimize part design. The initial population number is 150, the crossover probability between individuals is 0.7, the mutation probability is 0.06, and the termination condition is set to the iteration stops when the optimal solution is output. Trigger “Part design optimization” to start part design optimization. When iterating to the 155th generation, the system outputs the optimal solution. Record the comprehensive benefit and corresponding part dimensions at this time and input the dimensions into the model reconstruction interface [Figure 11]. Click “Save” to get the optimized model.
The results before and after optimization are shown in Table 12. The environmental impact benefit value in the table is obtained by multiplying the environmental impact quantitative value calculated by Equation (14) with λ1. The economic benefit value in the table is obtained by multiplying the cost calculated by Equation (20) with λ2. The comprehensive benefit value is the sum of the environmental impact benefit and cost benefit. After optimization, the comprehensive benefit of the step shaft improved by 1.63%, of which the environmental and economic benefits improved by 1.56% and 1.65%, respectively.
Comparison of comprehensive benefits of step shaft
Type of benefit | Before optimization | Optimized | Improvement |
Environmental | 8.31 | 8.18 | 1.56% |
Economic | 31.52 | 31.00 | 1.65% |
Comprehensive | 39.83 | 39.18 | 1.63% |
Performance analysis of the optimized model
In this paper, the Simulation plug-in for SolidWorks is used to implement the static analysis of the optimized part. The process of static analysis includes: (1) Create an example; (2) Set the material; (3) Add constraints; (4) Add fixes; (5) Delimit the mesh; and (6) Run the analysis. Through the secondary development of the Simulation plug-in, the above steps are realized in code, and the parametric interactive interface is designed. Before conducting the static analysis, it is necessary to calculate the force of the intermediate shaft gear first. The force calculation is as follows.
The motion and dynamic parameters of the belt conveyor reducer are shown in Table 13.
Belt conveyor motion and power parameter table
Axis name | Power (kW) | Torque (N·m) | Revolution speed (r/min) | ||
Input | Output | Input | Output | ||
Motor shaft | - | 3.67 | - | 36.5 | 960 |
Input shaft | 3.52 | 3.48 | 106.8 | 105.6 | 314.86 |
Intermediate shaft | 3.21 | 3.18 | 450.8 | 446.6 | 68 |
Output shaft | 3.05 | 3.02 | 1525 | 1510 | 19.1 |
The number of big gear teeth on the intermediate shaft is Z1 = 109, the modulus m1 = 2, the number of pinion teeth is Z2 = 27 and the modulus m2 = 4. The force acting on the intermediate shaft gear is calculated by:
Transverse force:
Radial force:
Where Tf is the intermediate shaft torque, d is the intermediate shaft gear indexing circle, and α is the indexing circle pressure angle of 20°.
The calculated force result of the intermediate shaft gear is:
Big gear: transverse force Ft1 = 4,136 N, radial force Fr1 = 1,505 N.
Pinion: transverse force Ft2 = 8,270 N, radial force Fr2 = 3,010 N.
Among them, the force of the large gear is equivalent to the force of the keyway 1, and the force of the small gear is equivalent to the force of the keyway 2.
After the force calculation, the designer enters them into the parametric interactive interface. At the same time, the designer sets the name of the example and enters the mesh size. Click on “Analysis” to achieve static analysis of the step shaft. After the analysis is completed, its stress and displacement will be transferred to the current interface, and the analysis results are shown in Figure 12.
The maximum equivalent stress obtained from the simulation is 67.53316 Mpa, which is smaller than the permissible stress of the material, proving that the optimized shaft can meet the use requirements.
CONCLUSION AND FUTURE WORK
(1) To consider the environmental impact and manufacturing cost in the part design stage, this paper proposes a part design optimization method. It can realize the design optimization of parts from the perspective of the comprehensive benefit. Use the comprehensive benefit to measure whether the optimization of the part design has been realized. Based on this approach, a design optimization prototype system oriented to the comprehensive benefit is constructed. Take the intermediate shaft of the belt conveyor reducer - sixth order step shaft as a specific case. The results show that the comprehensive benefit of the optimized part improved by 1.63%, and the environmental and cost benefits improved by 1.56% and 1.65%, respectively;
(2) Compared with the traditional optimization model, the feature information of parts can be fully utilized in this model. The environmental impact and cost can be calculated using the part model. Through the optimization of part design to improve the environmental impact and economic performance results. The optimization model improves the development efficiency of parts. It has a certain reference significance for realizing energy savings and cost reduction;
(3) During the cutting process, this paper applies the average power of the machine equipment to calculate the energy consumption. However, the power of different machine equipment running stages also varies, including no-load power, cutting power, and additional load power. Future research should improve the calculation of machine equipment energy consumption to obtain more accurate results. In addition, this paper only focuses on the two life cycle stages of raw material acquisition and manufacturing. The following research should solve the problem of the life cycle data collection being difficult to complete and accurate and expand the research boundary to the whole life cycle stage.
DECLARATIONS
Authors’ contributions
Conceptualization, methodology, validation, system construction, original draft preparation: Tao K
Supervision, review and editing, formal analysis: Zhang L
Methodology, investigation: Zheng Y, Zhu K
Data curation, investigation: Fang J, Su J
Availability of data and materials
Not applicable.
Financial support and sponsorship
This study is supported by the Anhui Provincial Major Science and Technology Project (Grant No. 202203f07020006).
Conflicts of interest
All authors declared that there are no conflicts of interest. Zhang L is an Editorial Board Member of the journal Green Manufacturing Open.
Ethical approval and consent to participate
Not applicable.
Consent for publication
Not applicable.
Copyright
© The Author(s) 2024.
REFERENCES
1. Xu R, Lin B. Why are there large regional differences in CO2 emissions? Evidence from China’s manufacturing industry. J Clean Prod 2017;140:1330-43.
2. Al-ayouty I, Hassaballa H, Rizk R. Clean manufacturing industries and environmental quality: the case of Egypt. Environ Dev 2017;21:19-25.
3. Kucukvar M, Cansev B, Egilmez G, Onat NC, Samadi H. Energy-climate-manufacturing nexus: new insights from the regional and global supply chains of manufacturing industries. Appl Energy 2016;184:889-904.
4. Farineau T, Rabenasolo B, Castelain J, Meyer Y, Duverlie P. Use of parametric models in an economic evaluation step during the design phase. Int J Adv Manuf Technol 2001;17:79-86.
6. ISO 14040:2006. Environmental management - Life cycle assessment - Principles and framework. Available from: https://pqm-online.com/assets/files/lib/std/iso_14040-2006.pdf. [Last accessed on 21 March 2024].
7. Nowack M, Hoppe H, Guenther E. Review and downscaling of life cycle decision support tools for the procurement of low-value products. Int J Life Cycle Assess 2012;17:655-65.
8. Campbell SW, Galloway AM, Mcpherson NA. Techno-economic evaluation of reducing shielding gas consumption in GMAW whilst maintaining weld quality. Int J Adv Manuf Technol 2012;63:975-85.
9. Georgiadis P, Besiou M. Environmental and economical sustainability of WEEE closed-loop supply chains with recycling: a system dynamics analysis. Int J Adv Manuf Technol 2010;47:475-93.
10. Santos R, Costa AA, Silvestre JD, Vandenbergh T, Pyl L. BIM-based life cycle assessment and life cycle costing of an office building in Western Europe. Build Environ 2020;169:106568.
11. Hou Y, Qian X, Zhang R, Gu F, Feng P. Study on an integrated LCA-LCC model for assessment of highway engineering technical schemes. Buildings 2022;12:1050.
12. Xiao Y, Gong Q, Chen X. Energy saving and low-cost-oriented design processes of blank’s dimensions based on multi-objective optimization model. Processes 2019;7:811.
13. Ameli M, Mansour S, Ahmadi-javid A. A sustainable method for optimizing product design with trade-off between life cycle cost and environmental impact. Environ Dev Sustain 2017;19:2443-56.
14. Deng C, Wu J, Shao X. Research on eco-balance with LCA and LCC for mechanical product design. Int J Adv Manuf Technol 2016;87:1217-28.
15. Shi J, Wang Y, Fan S, Ma Q, Jin H. An integrated environment and cost assessment method based on LCA and LCC for mechanical product manufacturing. Int J Life Cycle Assess 2019;24:64-77.
16. Simões CL, Figueirêdo de Sá R, Ribeiro CJ, Bernardo P, Pontes AJ, Bernardo C. Environmental and economic performance of a car component: assessing new materials, processes and designs. J Clean Prod 2016;118:105-17.
17. Zhang Y, Meng Q. Application of decision making algorithm for green electromechanical product design optimization. J Adv Comput Intell Intell Inform 2019;23:293-9.
18. Hu W, Zhuo Y, Wu X, Zhao X, Lan G. Intelligent design of hammer mill based on SolidWorks. J Mech Electr Eng Mag 2013:1063-7. (in Chinese). Available from: https://caod.oriprobe.com/articles/39577378/Intelligent_design_of_hammer_mill_based_on_SolidWo.htm. [Last accessed on 20 Mar 2024]
19. Xue B, Yang Z, Zhou A, Shi B, Yan L. Development of adied design software of shell-and-tube heat exchanger based on SolidWorks and SQL. Mod Manuf Eng 2019:107-112. (in Chinese). Available from: https://caod.oriprobe.com/articles/57729772/Development_of_adied_design_software_of_shell_and_.htm. [Last accessed on 20 Mar 2024]
20. Reddy EJ, Rangadu VP, Ramachandra R, Naidu VNP. Development of a constraint-based approach for knowledge-based system for CAD modeling. Adv Sci Eng Med 2018;10:357-61.
21. LI Z, Yin W. An automatic design structure matrix generation system based on 3D CAD model. Comput Eng Sci 2020;42:483-92. (in Chinese).
22. Yuan F, Lv Y, Wang K, Liu D, Yang H. Parametric design of static pressure box based on top-down. Light Ind Mach 2019:21-24,31. (in Chinese). Available from: https://caod.oriprobe.com/articles/57959401/Parametric_Design_of_Static_Pressure_Box_Based_on_.htm. [Last accessed on 20 Mar 2024]
23. Ji Z. Comparison between methods of further development of solidworks. 2006. Available from: https://api.semanticscholar.org/CorpusID:113319760. [Last accessed on 20 March 2024].
24. Lu J, Mi CY. A new combined parametric design method based on solidworks. J Graph 2013;34:64-8. Available from: http://www.txxb.com.cn/EN/abstract/abstract385.shtml. [Last accessed on 20 Mar 2024]
25. Ren XZ, Ren NF, Wang HJ. Fundamentals of manufacturing technology. Beijing: China Machine Press; 2014. (in Chinese) Available from: http://www.cmpedu.com/books/book/2034703.htm. [Last accessed on 20 March 2024].
26. GB/T 1800.1-2020. Geometrical product specifications (GPS) - ISO code system for tolerances on linear sizes - Part 1: Basis of tolerances, deviations and fits. (in Chinese) Available from: https://img.antpedia.com/standard/files/pdfs_ora/GB2020/GB_T%201800.1-2020.pdf. [Last accessed on 20 March 2024].
27. Li YM. Mechanical manufacturing technology handbook. Beijing: China Machine Press; 2013. (in Chinese) Available from: http://www.cmpedu.com/books/book/2063186.htm. [Last accessed on 20 March 2024].
28. Li BQ, Wang YP, Cao LL, Li XN, Ye YY. Representation method on mold design knowledge. Forg Stamp Technol 2023;48:176-84. (in Chinese).
29. Katoch S, Chauhan SS, Kumar V. A review on genetic algorithm: past, present, and future. Multimed Tools Appl 2021;80:8091-126.
30. Gad AG. Particle swarm optimization algorithm and its applications: a systematic review. Arch Computat Methods Eng 2022;29:2531-61.
31. Chen A, Tao H, Zhu Y. Ant colony optimization algorithm and its application. In: Proc. SPIE 12259, 2nd International Conference on Applied Mathematics, Modelling, and Intelligent Computing (CAMMIC 2022).
32. Sphera. Product Sustainability Solutions Software. Available from: https://gabi.sphera.com/lca/gabi-databases/. [Last accessed on 20 March 2024].
33. GB/T 17358-2009. Power consumption, measurement, and testing in heat treating production. (in Chinese) Available from: http://c.gb688.cn/bzgk/gb/showGb?type=online&hcno=15385A8DCE489AF51E78F446E8225281. [Last accessed on 20 March 2024].
34. Ai X, Xiao SG. Cutting concise handbook (3rd Edition). Beijing: China Machine Press; 2017. (in Chinese) Available from: http://www.cmpedu.com/books/book/2063315.htm. [Last accessed on 20 March 2024].
Cite This Article
How to Cite
Download Citation
Export Citation File:
Type of Import
Tips on Downloading Citation
Citation Manager File Format
Type of Import
Direct Import: When the Direct Import option is selected (the default state), a dialogue box will give you the option to Save or Open the downloaded citation data. Choosing Open will either launch your citation manager or give you a choice of applications with which to use the metadata. The Save option saves the file locally for later use.
Indirect Import: When the Indirect Import option is selected, the metadata is displayed and may be copied and pasted as needed.
About This Article
Special Issue
Copyright
Data & Comments
Data
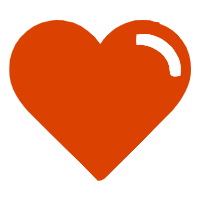
Comments
Comments must be written in English. Spam, offensive content, impersonation, and private information will not be permitted. If any comment is reported and identified as inappropriate content by OAE staff, the comment will be removed without notice. If you have any queries or need any help, please contact us at [email protected].