A tiny amount of electrode additive breaks the dilemma of achieving high energy density and fast charging lithium-ion battery cathode
Abstract
It is crucial to achieve high energy density and fast charging simultaneously for automotive lithium-ion batteries. The nickel-rich layered oxide LiNi0.8Co0.1Mn0.1O2 (NCM811) cathode enables high energy density due to its high theoretical capacity and high working voltage. However, the fast charging performance is compromised because the electrode-electrolyte interface kinetics deteriorates when working at high voltage. A new approach is proposed to solve this dilemma, where [60] Fullerenoacetic acid (C60-COOH) is used to tune the interface structure of the NCM811. The carboxylic acid functional group ensures preferential deposition of C60 onto the NCM811 surface through the reaction with the surface residual alkaline species/transition metals. An electronic and ionic conductive thin coating layer is formed on the NCM811 surface, which inhibits electrolyte decomposition and facilitates formation of high voltage stable cathode electrolyte interface. With 0.50 wt.‰ of C60-COOH, the NCM811 cathode exhibits significantly improved electrochemical performance at 4.6 V in terms of reversible capacity, and capacity retention ratio, where an exceptional fast charging/discharging performance at 10 C is demonstrated as well. This work is of great significance for promoting high energy density and fast charging automotive lithium-ion batteries.
Keywords
INTRODUCTION
Lifting energy density and enhancing fast charging/discharging performance are two crucial aspects to promote automotive lithium-ion battery applications[1,2]. Nickel-rich layered cathode LiNi0.8Co0.1Mn0.1O2 (NCM811) holds great promise to overcome both problems because the NCM811 cathode exhibits a high actual capacity and fast lithium ion transport between the layered structure[3,4]. Raising the charging voltage upper limit for NCM811 cathodes (for example, from 4.3 V to 4.6 V) is considered an effective way to increase the energy density. However, raising the voltage upper limit while maintaining fast charging/discharging performance is challenging. At high voltage, phase transitions from layered to spinel structure are extremely easy to occur, which destroys the structure of the cathode material and leads to a sharp reduction in reversible capacity[5]. Besides, high voltage can cause excessive side reactions on the cathode surface, forming an over-thick cathode electrolyte interface (CEI), leading to increased impedance and thus affecting the charging/discharging performance at high current density[6]. Surface modification with electron-conductive carbonaceous materials has been widely used to increase the energy density and improve rate performance of the NCM811 cathode. On the one hand, adverse side reactions are suppressed by the carbon coating at the electrode-electrolyte interface; on the other hand, polarization is reduced because the carbonaceous materials possess good electronic conductivity[7-9]. However, in the practical application of carbon coating in high nickel cathodes, because the transition metal (TM) ions of the NCM811 cathode are easily reduced during the sintering process, leading to structure collapse and performance deterioration[9,10], the application effect of carbon coating is greatly limited.
In this work, [60] Fullerenoacetic acid (C60-COOH) is used to modify NCM811 particles; the schematic illustration is shown in Figure 1. Because C60-COOH is soluble in organic solvents, a solution-based surface coating is possible. The functionalization with carboxylic acid group enhances interactions with the residual alkaline species/TMs at the NCM811 particle surface, thereby ensuring uniform and controllable deposition of C60-COOH onto the NCM811 particle surface. Fullerene has excellent electronic conductivity because of its unique molecular structure and electronic energy levels, which accelerates the transfer of active Li+ at high current density, and promotes continuous adsorption of Li+ and uniform deposition of CEI[11]. In addition, due to the multiple-addition of free radicals on a fullerene, fullerenes are regarded as highly efficient radical sponges; thus, they can protect the electrode by scavenging oxygen and related radicals. Based on this strategy and multiple mechanisms, without traditional and complex sintering process, directional deposition process and a tiny amount of additives break the dilemma of high-voltage and high-rate NCM811 cathodes, and the cathode particle surface is modified with an excellent reproducibility and promising scalability. Compared to the pristine NCM811 (P-NCM), the structure of the modified
EXPERIMENTAL
Preparation and assembly of cells
C60-COOH was synthesized following the procedure of references[12-14], as shown in Supplementary Figure 1. tert-Butyl [60] Fullerenoacetate was synthesized by the cyclopropanation of C60 (99.9 %, Yongxin Technology) with the sulfonium ylide prepared from tert-butyl bromoacetate and dimethyl sulfide, and readily converted to C60-COOH through the cleavage of the ester moiety promoted by trifluoroacetic acid. The total yield is 45%.
Firstly, prepare a mixed solution of N, N-dimethylformamide (DMF, 99.9%, Aladding) and
The cathode consists of 80 wt.% active material (NCM811 coated with different amounts of C60-COOH),
The anode consists of 90 wt.% graphite (Neware), 3 wt.% conductive agent, 3 wt.% sodium carboxymethylcellulose (CMC, Daicel Corporation), and 3 wt.% styrene butadiene rubber (SBR, Daicel Corporation). Dissolved them in a quantity of deionized water and mixed them to form a homogeneous slurry. Poured the mixed slurry onto copper foil, air drying at 60 °C for 2 h and vacuum drying at 80 °C for 12 h. The dried electrodes were pressed and cut into 82 × 46 mm2 rectangles for pouch cells. The N/P ratio of the control electrode is about 1.05: 1.
Transferred the electrodes to a glovebox filled with argon gas (O2 < 0.5 ppm, H2O < 0.5 ppm) to assemble the 2032-coin cells and pouch cells. The half-cell used a lithium metal foil as a counter electrode and used
Electrochemical measurements
The assembled cells remained stationary overnight and were tested for their electrochemical performance at the LAND battery test system (Wuhan, China). For cycling testing, 1 C, 3 C, and 5 C cycle cells first undergo three charging/discharging cycles at 0.2 C and 0.5 C, respectively, followed by the remaining cycles (1 C = 200 mAh·g-1). The 10 C cycle cells first undergo two charging/discharging cycles at 0.2 C, 0.5 C and
Sample characterization
The field emission scanning electron microscope (FEI Quanta FEG 250, thermal field) equipped with an energy dispersive spectrometer (EDS, Oxford X-Max) characterized the elemental distribution on the electrode surface. The confocal micro-Raman spectroscopy (Renishaw in Via Reflex) studied the electrode surface state before and after cycling. The crystal structure of electrodes was analyzed using X-ray diffraction (XRD, Bruker D8 Discover), with a scanning range of 5° to 90°.
The cells to be characterized after cycling were disassembled in the glovebox, immersed in DMC for more than 5 h to remove residual lithium salts from the surface, and dried overnight in the glovebox. Field emission scanning electron microscopy (SEM, Hitachi S4800, cold field) was used to characterize the electrode surface morphology after cycling. High-resolution transmission electron microscope (HRTEM, JEOL2100) was used to characterize the CEI morphology and crystal structure of the electrode surface before and after cycling. The cross-sectional morphology of the electrode was characterized by focused ion beam SEM (FIB-SEM, Carl Zeiss/Auriga). X-ray photoelectron spectroscopy (XPS, Kratos Axis Supra) measurement was used to analyze the surface composition of the electrode after cycling. Thermogravimetric analysis-mass Spectroscopy (TG-MS) measurements were performed using the PerkinElmer TGA 8000 Spectrum two-Clarus SQ8T instrument. Place approximately 10 mg of delithium cathode (charged to 4.6 V) into an alumina crucible and transfer it to the instrument. Mass spectrometry was used to characterize gas production during the testing process from room temperature to 600 °C at a heating rate of 10 °C min-1 (nitrogen environment).
RESULTS AND DISCUSSION
The methodology and characterization
C60-COOH was synthesized following the protocol as references [Supplementary Figure 1][12-14], with the structure shown in Figure 2A. The transmission electron microscope (TEM) image of C60-COOH powder exhibits uniform spherical particle shape as indicated in Figure 2B. The peak centered at 1,573 cm-1 in the Raman spectra [Supplementary Figure 2] originates from the graphitic carbon structure, which enhances electronic conductivity and lithium-ion transport speed. The existence of C60-COOH additive within the
Electrochemical performance
Different amounts of C60-COOH are used to modify the NCM811 surface in order to identify an optimal mass ratio with respect to the electrochemical performance improvement. In Supplementary Figure 5, the cycling performance is clearly influenced by the mass ratio of the C60-COOH additive to the NCM811 cathode. Compared with the pristine NCM811 (P-NCM), the NCM811 electrode modified with 0.50 wt.‰ C60-COOH (C-NCM-0.50) shows the best electrochemical performance. In contrast, the modified electrodes with alternative C60-COOH compositions (0.25 wt.‰ C60-COOH: C-NCM-0.25, 0.75 wt.‰
The rate performance of both samples is evaluated [Figure 3A]. It is found that the advantage of C-NCM is very limited at small current densities, while the performance is more favorable at large current densities. The long cycling performance of both samples at 10 C and a high voltage of 4.6 V [Supplementary Figure 6] is investigated. After 100 cycles, the discharge capacity of P-NCM and C-NCM is 45 mAh·g-1 and 95 mAh·g-1, respectively. The significantly enhanced rate capacity indicates that better electrochemical kinetics is achieved with the C60-COOH additive to the NCM811. Meanwhile, we also tested the electrochemical performance of the two electrodes in high load [Supplementary Figure 7] and low temperature conditions
Figure 3. (A) Rate performance, (B) discharge capacities and coulombic efficiencies of pouch cells at 0.2 C; (C) initial charge/discharge profiles of pouch cells; (D) GITT profiles and Li+ diffusion coefficient of both samples; dQ/dV profiles of (E) P-NCM and (F) C-NCM samples after cycles; (G) O2 and (H) CO2 release from both samples during heating process in the TG-MS testing. GITT: Galvanized intermittent titration technique; TG-MS: thermogravimetric analysis-mass spectroscopy; C-NCM: C60-COOH modified NCM811;
The effects of C60-COOH modification on NCM811 are further tested using the pouch cells [Figure 3B]. For C-NCM, the capacity is up to 153 mAh·g-1 after 500 cycles, and the capacity retention ratio is 78.1%. In contrast, P-NCM has a low capacity (100 mAh·g-1) and decays rapidly (54.3%). The increased reversible capacity and enhanced capacity retention ratio of the NCM cathode in full cells are attributed to less active lithium loss and higher voltage plateau over cycles. The charging/discharging profile of P-NCM and
Electrochemical kinetic analysis
The effect of C60-COOH additive on electrochemical kinetics is studied using CV [Supplementary Figure 9]. In the first cycle, the difference in redox peak potential of C-NCM is smaller (0.271 V) than that of P-NCM (0.315 V). It indicates that C-NCM has a lower polarization and faster reaction rate. The enhancement of electrochemical kinetics is attributed to the electronic and ionic conductive layer formed by C60. The surface C60-COOH layer enhances the affinity between the NCM811 particle and electronic conductive agent, which is beneficial for constructing electronic conductive network between particles.
The Li+ diffusion behavior was characterized by GITT during the cycling process, where voltage variation and diffusion coefficient are functions of time [Figure 3D]. Since the voltage drop is caused by polarization in the stable state, the C60-COOH layer on the surface of C-NCM greatly inhibits the polarization, and the voltage drop is always less than or equal to P-NCM in a complete charging/discharging process. At the same time, the average diffusion coefficient of C-NCM (7.3 × 10-10 cm2·s-1) is always greater than that of P-NCM (5.9 × 10-10 cm2·s-1) during a single charge/discharge, indicating that C60-COOH surface modification can effectively alleviate the electrode polarization under repeated current stimulation, leading to an increase in reversible capacity at high current densities.
It is reported that the cubic phase formed at a high cut-off voltage can inhibit the movement of Li+, resulting in an increase in charge transfer resistance, polarization and capacitance attenuation[5]. The EIS
The dQ/dV plots of both samples during the initial 40 cycles are analyzed to reveal the evolution of the polarization properties and the phase transition, as shown in Figure 3E and F. The oxidation peak of the cycled P-NCM shifts toward high potential and the reduction peak shifts toward low potential during cycling, indicating an increased polarization[19,20]. In contrast, the peak shift observed in C-NCM is significantly smaller, and the excess potential is mitigated by the surface modification of the C60 layer. In addition, due to the poor stability of the H3 phase, the H2 → H3 transition of P-NCM leads to significant contraction of the lattice c-axis, which further leads to anisotropic mechanical strain in the primary particles, and ultimately leading to the formation of intergranular micro-cracks and surface/interface damage[21,22]. The redox peak of C-NCM is well maintained, which further confirms that C60-COOH surface modification can effectively stabilize the CEI, reduce electrode polarization, and suppress the irreversible phase transition caused by Li+ (de)intercalation.
Thermal stability analysis
Another important factor to evaluate the applicability of the NCM811 at high voltages is thermal stability. The highly charged cathode surface undergoes a spinel and rock salt phase transition due to Ni migration at high temperatures. Large amount of hazardous gas is released, which further reacts with electrolyte to induce thermal runaway[23-25]. The thermal stability of both samples charged to 4.6 V is analyzed through TG-MS. Figure 3G and H shows the peak intensities of O2 and CO2 production at high temperatures, respectively. It can be found that the amount of O2 and CO2 produced by C-NCM is significantly reduced compared to those by P-NCM, and some of the peaks are even shifted towards higher temperatures. These results demonstrate that the C60-COOH layer can effectively stabilize NCM811 structure at high temperatures. The gas generation is inhibited and battery thermal safety is improved.
Morphological and bulk structural analysis
The capacity attenuation of the high nickel layered oxide cathode is mainly due to its mechanical instability and high surface activity, especially at high state of charge (SOC). During repeated charging/discharging, anisotropic lattice distortion and volume change can lead to the accumulation of internal strain, eventually leading to crack formation or particle crushing[26]. Therefore, HRTEM and SEM are used to characterize the surface morphology of the cycled both samples. Figure 4A1-A4 shows the local structure of CEI on both electrode surfaces after 500 cycles. The CEI on P-NCM surface is not uniformly distributed with the thickness between 10-40 nm; the thick CEI layer leads to high interface resistance and hinders the diffusion of Li+. Additionally, the C-NCM surface exhibits a homogeneous and smooth CEI layer with a thickness of
Figure 4. (A) HRTEM images of both electrodes after cycles; (B) Surface and (C) cross-section images of both electrodes after cycles. HRTEM: High-resolution transmission electron microscope.
The crystal structures of both samples after 500 cycles are visually demonstrated by a HRTEM coupled with fast Fourier transform (FFT) images [Figure 5]. The P-NCM particles exhibit blurry lattice fringes with some lattice distortion, and the corresponding FFT shows the presence of spinel phase (Fd3m). A lattice spacing of 0.206 nm is exhibited in the outer layer, consistent with the (400) crystal plane of the spinel phase. A lattice spacing of 0.480 nm is displayed in the inner layer, corresponding to the (111) crystal plane of the spinel phase. When cycling at 4.6 V, the strain caused by ion migration causes a transition from layered to spinel phase, which extends from the surface to the interior of the particles, and this phase transition is one of the main factors leading to the capacity attenuation and rate performance degradation of the cathode materials[28]. In contrast, the surface and bulk of C-NCM particles still exhibit a good hierarchical structure, with a well-defined and regular lattice in large area regions, without significant disorder domains. The FFT shows the lattice spacing of 0.472 nm, corresponding to the (003) crystal plane of the layered R3m phase. It has been shown that CEI derived from C60-COOH layer can stabilize the crystal structure on the surface and bulk and significantly improve its electrochemical properties.
Figure 5. HRTEM images of the surface and interior of cathode particles of both samples after 500 cycles. HRTEM: High-resolution transmission electron microscope.
XRD has been used to characterize the crystallographic phase change of both samples before and after 200 and 500 cycles. As shown in Figure 6A, all peaks in the XRD patterns of both samples exhibit a layered structure (R3m). The diffraction peaks of P-NCM significantly weaken and shift, indicating that the lattice parameters decrease with the deterioration of the cathode structure order, reflecting the loss of active lithium and the dissolution of TM during the cycle[29]. The peaks of (003), (101), and (104) reflect changes in the length of the c-axis, a-axis, and b-axis, respectively. After 500 cycles, the peak of (003) shifts towards the lower 2θ direction, indicating crystal expansion along the c-axis. Meanwhile, the strong electrostatic repulsion between the oxygen-oxygen interlayer due to active lithium loss yields an increased c-value[22,30]. The peak of (101) shifts towards the higher 2θ direction, indicating that the decrease of parameter a-axis is caused by the reduction of the length of Ni-O bond in the TMO6 octahedron due to oxidation state during the cycle[31,32]. The peak of (104) shifts towards the higher 2θ direction, which is caused by the appearance of vacancies caused by the repeated (de)lithiation of Li+ in the lithium layer, and the occupation of these vacancies by Ni2+[17]. In contrast, the peak shift and intensity reduction are smaller for C-NCM than those for P-NCM. This indicates that the CEI layer derived from C60-COOH layer can effectively suppress phase transitions during charging and discharging, thereby improving the structure stability of NCM811.
Figure 6. (A) XRD patterns and their local enlarged patterns of both samples before and after 200 and 500 cycles; (B) Raman spectra of graphite anodes relative to both cathodes without cycling and after 500 cycles; (C-E) XPS spectra of both samples after 500 cycles; (F-H) XPS spectra of graphite anodes relative to both samples after 500 cycles. XRD: X-ray diffraction; XPS: X-ray photoelectron spectroscopy.
Since XRD is difficult to characterize the surface spinel phase, Raman spectra were adopted for acquiring the surface structural information of both samples after 50, 100, 200, 500 cycles [Supplementary Figure 11]. In the Raman spectra, the transition rate from layered to spinel phase is significantly decelerated at the surface of C-NCM, especially after 200 cycles, due to the presence of the stable C60 layer. The combination of XRD and Raman characterization further proves that CEI derived from C60-COOH layer can stabilize the TM ions on the particle surface, playing a crucial role in stabilizing the octahedral and layered structure of TMO6 during long-term cycling[33]. Raman spectra [Figure 6B] were also used to detect structural changes of the graphite anodes. After 500 cycles, the graphite anode corresponding to the P-NCM cathode exhibits a stronger D-band and a weaker G-band; this indicates that graphite structure corresponding to P-NCM cathode deteriorates, while forming more SEI species containing sp3 hybrid carbon[34]. The number of graphite structural defects is estimated by calculating the relative strength ratio between the D and G bands (R = ID/IG). The high-degree structure disorder is indexed by a high R value[34]. With the C60-COOH layer, the R-value of the graphite anode decreases from 0.1915 to 0.0908, indicating that the graphite anode corresponding to the C-NCM cathode maintains a better structural order. In addition, a new D’-band appearing at 1614 cm-1 on the graphite anode corresponds to P-NCM cathode, indicating the presence of oxidized sp2 carbon on the surface defects[31]. This further confirms the occurrence of structural disorder over cycles[35]. Due to the van der Waals force interaction between the atoms of a graphite anode, there is no chemical bonding, and the weak interaction between atoms makes it easy for large-volume solvent molecules to undergo intercalation reactions. The CEI derived from C60-COOH on the cathode surface can effectively reduce the decomposition of the electrolyte, so the phenomenon of solvent molecules (such as PF6-) embedded inside the lattice is significantly reduced in the electrochemical process of graphite anode[36]. Therefore, Raman spectra [Supplementary Figure 11 and Figure 6B] indicate that the C60-COOH layer not only stabilizes the layered structure of NCM811, but also delays the structural degradation of the graphite anode.
Element composition analysis
The composition of the electrode-electrolyte interface layer affects charge transportation. Therefore, the surface chemical composition of both cathodes [Figure 6C-E and Supplementary Figure 12] and their corresponding graphite anodes [Figure 6F-H and Supplementary Figure 13] after 500 cycles are investigated by XPS. In the C 1s spectra [Supplementary Figure 12A], C-NCM exhibits significantly more C-C/C-H peaks than P-NCM after cycling, indicating more C-C/C-H bonding from conductive carbon and PVDF. It means that the structure damage of the electrode during cycling is reduced. In the O 1s spectra
The XPS spectra in Figure 6F-H and Supplementary Figure 13 show the elemental composition on the surface of the graphite anode after 500 cycles. In the C 1s spectra [Figure 6F], it is worth noting that the peak of lithiated graphite species (LiCx) at 283.4 eV in the graphite electrode corresponding to P-NCM has special significance, which means that during the discharge process, some Li+ are not fully removed from the graphite due to high overpotential[43,44], resulting in a large loss of active lithium, corresponding to the results of the pouch full-cell cycle shown in Figure 3A. Compared to P-NCM, the spectra of O 1s [Figure 6G], F 1s [Supplementary Figure 13A], and P 2p [Figure 6H] show that graphite anodes corresponding to C-NCM have fewer C=O/CO32- and fewer F complexes and P compounds, which are decomposition products of electrolyte, such as carbonates and carboxylates[31]. The strong surface of Li compounds in the Li 1s spectra [Supplementary Figure 13B] and the strong Ni peak on the Ni 2p spectra
CONCLUSIONS
In order to solve the dilemma of achieving high energy density and fast charging performance of automotive lithium-ion batteries simultaneously, a simple and effective method is proposed to improve the performance of NCM811 cathodes at high voltage and high current densities. C60-COOH is introduced as an electrode additive to form a thin coating layer onto the NCM811 surface through the reaction with residual alkaline species/TMs. Due to efficient surface coating by the electronic and ionic conductive
DECLARATIONS
Authors’ contributions
Data curation, methodology: Zhang, J.; Cao, L.
Investigation, validation: Zhang, J.; Cao, L.; Yu, J.
Project administration: Gao, J.; Xue, W.; Huang, Y.
Software: Zhang, J.; Yu, J.; Gao, J.
Resources: Tu, Y.; Xue, W.; Xia, Y.
Funding acquisition: Huang, Y.; Cheng, Y. J.
Writing-original draft: Zhang, J.
Writing- review and editing: Cheng, Y. J.; Huang, Y.
Availability of data and materials
The data supporting our work can be found in the Supplementary Materials.
Financial support and sponsorship
This work was financially supported by the National Natural Science Foundation of China (52162036 and 22378342), the Key Project of Natural Science Foundation of Xinjiang Uygur Autonomous Region (2021D01D08), Key Laboratory Project Jointly Built by Xinjiang University (KFKT2022004), the Natural Science Foundation of Zhejiang Province (LD22E020003), the Ningbo Science & Technology Innovation 2025 Major Project (2023Z063), and Zhejiang Key Laboratory of Advanced Fuel Cells and Electrolyzers Technology.
Conflicts of interest
All authors declared that there are no conflicts of interest.
Ethical approval and consent to participate
Not applicable.
Consent for publication
Not applicable.
Copyright
© The Author(s) 2025.
Supplementary Materials
REFERENCES
1. Jiang, M.; Danilov, D. L.; Eichel, R.; Notten, P. H. L. A review of degradation mechanisms and recent achievements for Ni-rich cathode-based Li-ion batteries. Adva. Energy. Mater. 2021, 11, 2103005.
2. Xu, C.; Reeves, P. J.; Jacquet, Q.; Grey, C. P. Phase behavior during electrochemical cycling of Ni-rich cathode materials for Li-ion batteries. Adv. Energy. Mater. 2021, 11, 2003404.
3. Du, B.; Mo, Y.; Jin, H.; et al. Radially microstructural design of LiNi0.8Co0.1Mn0.1O2 cathode material toward long-term cyclability and high rate capability at high voltage. ACS. Appl. Energy. Mater. 2020, 3, 6657-69.
4. Han, J. G.; Kim, K.; Lee, Y.; Choi, N. S. Scavenging materials to stabilize LiPF6-containing carbonate-based electrolytes for Li-ion batteries. Adv. Mater. 2019, 31, e1804822.
5. Liu, S.; Liu, Z.; Shen, X.; et al. Surface Doping to enhance structural integrity and performance of Li-rich layered oxide. Adv. Energy. Mater. 2018, 8, 1802105.
6. Han, J.; Hwang, C.; Kim, S. H.; et al. An antiaging electrolyte additive for high-energy-density lithium-ion batteries. Adv. Energy. Mater. 2020, 10, 2000563.
7. Hou, Q.; Cao, G.; Wang, P.; et al. Carbon coating nanostructured-LiNi1/3Co1/3Mn1/3O2 cathode material synthesized by chemical vapor deposition method for high performance lithium-ion batteries. J. Alloys. Compd. 2018, 747, 796-802.
8. Chen, X.; Ma, F.; Li, Y.; et al. Nitrogen-doped carbon coated LiNi0.6Co0.2Mn0.2O2 cathode with enhanced electrochemical performance for Li-ion batteries. Electrochim. Acta. 2018, 284, 526-33.
9. Hwang, J.; Do, K.; Ahn, H. Highly conductive 3D structural carbon network-encapsulated Ni-rich LiNi0.8Co0.1Mn0.1O2 as depolarized and passivated cathode for lithium-ion batteries. Chem. Eng. J. 2021, 406, 126813.
10. Noh, H.; Youn, S.; Yoon, C. S.; Sun, Y. Comparison of the structural and electrochemical properties of layered Li[NixCoyMnz]O2 (x = 1/3, 0.5, 0.6, 0.7, 0.8 and 0.85) cathode material for lithium-ion batteries. J. Power. Sources. 2013, 233, 121-30.
11. Zhang, Y.; Li, J.; Tan, S.; et al. Fullerene-derivative C60-(OLi)n modified separators toward stable wide-temperature lithium metal batteries. Chem. Eng. J. 2022, 446, 137207.
12. Zhang, X.; Hsu, C. H.; Ren, X.; et al. Supramolecular [60]fullerene liquid crystals formed by self-organized two-dimensional crystals. Angew. Chem. Int. Ed. 2015, 54, 114-7.
13. Tada, T.; Ishida, Y.; Saigo, K. Synthesis and reactions of 2,2-[60]fullerenoalkanoyl chlorides. J. Org. Chem. 2006, 71, 1633-9.
14. Lu, H.; Chen, X.; Li, X.; Sun, W.; Wang, Y.; Tu, Y. Effect of flexible spacer and alkyl tail length on the liquid crystalline phase behavior of fullerene block molecules. Chemistry 2023, 29, e202301015.
15. Castel, E.; Berg, E. J.; El, K. M.; Novák, P.; Villevieille, C. Differential electrochemical mass spectrometry study of the interface of xLi2MnO3·(1 - x)LiMO2 (M=Ni, Co, and Mn) material as a positive electrode in Li-ion batteries. Chem. Mater. 2014, 26, 5051-7.
16. Hong, J.; Lim, H.; Lee, M.; et al. Critical role of oxygen evolved from layered Li-excess metal oxides in lithium rechargeable batteries. Chem. Mater. 2012, 24, 2692-7.
17. Gan, Q.; Qin, N.; Zhu, Y.; et al. Polyvinylpyrrolidone-induced uniform surface-conductive polymer coating endows Ni-rich LiNi0.8Co0.1Mn0.1O2 with enhanced cyclability for lithium-ion batteries. ACS. Appl. Mater. Interfaces. 2019, 11, 12594-604.
18. Guo, F.; Xie, Y.; Zhang, Y. Tuning Li-excess to optimize Ni/Li exchange and improve stability of structure in LiNi0.8Co0.1Mn0.1O2 cathode material for lithium-ion batteries. Nano. Res. 2022, 15, 8962-71.
19. Park, K.; Jung, H.; Kuo, L.; Kaghazchi, P.; Yoon, C. S.; Sun, Y. Improved cycling stability of Li[Ni0.90Co0.05Mn0.05]O2 through microstructure modification by boron doping for Li-ion batteries. Adv. Energy. Mater. 2018, 8, 1801202.
20. Zhang, J.; Li, J.; Cao, L.; et al. Surface-targeted functionalization of nickel-rich cathodes through synergistic slurry additive approach with multi-level impact using minimal quantity. Nano. Res. 2024, 17, 333-43.
21. Liu, H.; Wolfman, M.; Karki, K.; et al. Intergranular cracking as a major cause of long-term capacity fading of layered cathodes. Nano. Lett. 2017, 17, 3452-7.
22. Ni, L.; Chen, H.; Gao, J.; et al. Multiscale crystal field effect for high-performance ultrahigh-Ni layered cathode. ACS. Nano. 2023, 17, 12759-73.
23. Wu, Y.; Liu, X.; Wang, L.; et al. Development of cathode-electrolyte-interphase for safer lithium batteries. Energy. Storage. Mater. 2021, 37, 77-86.
24. Yi, M.; Dolocan, A.; Manthiram, A. Stabilizing the interphase in cobalt-free, ultrahigh-nickel cathodes for lithium-ion batteries. Adv. Funct. Mater. 2023, 33, 2213164.
25. Kim, N.; Moon, J.; Ryou, M.; et al. Amphiphilic bottlebrush polymeric binders for high-mass-loading cathodes in lithium-ion batteries. Adv. Energy. Mater. 2022, 12, 2102109.
26. Li, J.; Manthiram, A. A Comprehensive analysis of the interphasial and structural evolution over long-term cycling of ultrahigh-nickel cathodes in lithium-ion batteries. Adv. Energy. Mater. 2019, 9, 1902731.
27. Zheng, Y.; Chen, L.; Su, Y.; et al. An interfacial framework for breaking through the Li-ion transport barrier of Li-rich layered cathode materials. J. Mater. Chem. A. 2017, 5, 24292-8.
28. Gu, M.; Belharouak, I.; Zheng, J.; et al. Formation of the spinel phase in the layered composite cathode used in Li-ion batteries. ACS. Nano. 2013, 7, 760-7.
29. He, J.; Melinte, G.; Darma, M. S. D.; et al. Surface structure evolution and its impact on the electrochemical performances of aqueous-processed high-voltage spinel LiNi0.5Mn1.5O4 cathodes in lithium-ion batteries. Adv. Funct. Mater. 2022, 32, 2207937.
30. Xie, Q.; Li, W.; Manthiram, A. A Mg-doped high-nickel layered oxide cathode enabling safer, high-energy-density Li-ion batteries. Chem. Mater. 2019, 31, 938-46.
31. Pham, H. Q.; Mirolo, M.; Tarik, M.; El, K. M.; Trabesinger, S. Multifunctional electrolyte additive for improved interfacial stability in Ni-rich layered oxide full-cells. Energy. Storage. Mater. 2020, 33, 216-29.
32. Qian, R.; Liu, Y.; Cheng, T.; et al. Enhanced surface chemical and structural stability of Ni-rich cathode materials by synchronous lithium-ion conductor coating for lithium-ion batteries. ACS. Appl. Mater. Interfaces. 2020, 12, 13813-23.
33. Li, S.; Yang, L.; Liu, Z.; et al. Surface Al-doping for compromise between facilitating oxygen redox and enhancing structural stability of Li-rich layered oxide. Energy. Storage. Mater. 2023, 55, 356-63.
34. Tang, Y.; Deng, J.; Li, W.; et al. Water-soluble sericin protein enabling stable solid-electrolyte interphase for fast charging high voltage battery electrode. Adv. Mater. 2017, 29.
35. Zhang, J.; Li, Q.; Wang, Y.; Zheng, J.; Yu, X.; Li, H. Dynamic evolution of cathode electrolyte interphase (CEI) on high voltage LiCoO2 cathode and its interaction with Li anode. Energy. Storage. Mater. 2018, 14, 1-7.
36. Syzdek, J.; Marcinek, M.; Kostecki, R. Electrochemical activity of carbon blacks in LiPF6-based organic electrolytes. J. Power. Sources. 2014, 245, 739-44.
37. Mu, P.; Zhang, H.; Jiang, H.; et al. Bioinspired antiaging binder additive addressing the challenge of chemical degradation of electrolyte at cathode/electrolyte interphase. J. Am. Chem. Soc. 2021, 143, 18041-51.
38. Rong, H.; Xu, M.; Zhu, Y.; et al. A novel imidazole-based electrolyte additive for improved electrochemical performance of high voltage nickel-rich cathode coupled with graphite anode lithium ion battery. J. Power. Sources. 2016, 332, 312-21.
39. Shi, X.; Zheng, T.; Xiong, J.; Zhu, B.; Cheng, Y. J.; Xia, Y. Stable electrode/electrolyte interface for high-voltage NCM 523 cathode constructed by synergistic positive and passive approaches. ACS. Appl. Mater. Interfaces. 2021, 13, 57107-17.
40. Wu, Z.; Xue, L.; Ren, W.; Li, F.; Wen, L.; Cheng, H. A LiF nanoparticle-modified graphene electrode for high-power and high-energy lithium ion batteries. Adv. Funct. Mater. 2012, 22, 3290-7.
41. Chen, Z.; Kim, G.; Chao, D.; et al. Toward greener lithium-ion batteries: aqueous binder-based LiNi0.4Co0.2Mn0.4O2 cathode material with superior electrochemical performance. J. Power. Sources. 2017, 372, 180-7.
42. Li, L.; Fu, L.; Li, M.; et al. B-doped and La4NiLiO8-coated Ni-rich cathode with enhanced structural and interfacial stability for lithium-ion batteries. J. Energy. Chem. 2022, 71, 588-94.
43. He, M.; Su, C.; Feng, Z.; et al. High voltage LiNi0.5Mn0.3Co0.2O2/graphite cell cycled at 4.6 V with a FEC/HFDEC-based electrolyte. Adv. Energy. Mater. 2017, 7, 1700109.
Cite This Article

How to Cite
Download Citation
Export Citation File:
Type of Import
Tips on Downloading Citation
Citation Manager File Format
Type of Import
Direct Import: When the Direct Import option is selected (the default state), a dialogue box will give you the option to Save or Open the downloaded citation data. Choosing Open will either launch your citation manager or give you a choice of applications with which to use the metadata. The Save option saves the file locally for later use.
Indirect Import: When the Indirect Import option is selected, the metadata is displayed and may be copied and pasted as needed.
About This Article
Copyright
Data & Comments
Data
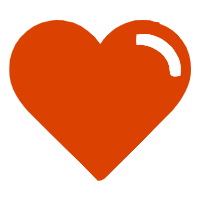
Comments
Comments must be written in English. Spam, offensive content, impersonation, and private information will not be permitted. If any comment is reported and identified as inappropriate content by OAE staff, the comment will be removed without notice. If you have any queries or need any help, please contact us at [email protected].