Impact of compaction pressure on formation and performance of garnet-based solid-state lithium batteries
Abstract
Compaction pressure directly determines the compactness of solid-state electrolytes (SSEs), which is crucial to affect the electrochemical performance of solid-state lithium batteries (SLBs). Herein, Li6.5La3Zr1.5Ta0.5O12 (LLZTO) pellets are compacted under various pressures before sintering to study the impact of compaction pressure on the overall properties of LLZTO SSEs and their SLBs. Notably, the sample pressed at 600 MPa (LLZTO-600) exhibits the highest compactness and the highest ionic conductivity due to improved particle contact and suppressed lithium loss. Consequently, the Li|LLZTO-600|Li symmetric cell exhibits the best performance among the samples, which can stably cycle for 1,500 h without short circuits. Meanwhile, the LiFePO4|LLZTO-600|Li full cell can retain 94.8% of its initial capacity after 150 cycles with the lowest overpotential among the SSEs. This work highlights the importance of tuning compaction pressure in developing high-performance SSEs and related SLBs.
Keywords
INTRODUCTION
With the advancement and growing prominence of energy materials, numerous energy devices have been developed to satisfy the increasing demands of modern society. Solid-state lithium batteries (SLBs) that employ solid-state electrolytes (SSEs) are attractive due to their high energy density and enhanced safety compared to widely used lithium-ion batteries (LIBs)[1-5]. Among them, garnet-type
Elemental doping is widely used to stabilize the phase structure by reducing Li content to induce Li vacancies, thus increasing the ionic conductivity of LLZO SSEs. The main doping methods include
High-temperature sintering is the most critical step for densifying the LLZO pellets, including atmospheric sintering[24], hot pressing[25], electric-field assisted sintering[26], and plasma sintering[27]. Atmospheric sintering enables the mass production of LLZO pellets but is hindered by issues such as non-uniform sintering and material waste. In contrast, methods such as hot pressing, electric-field assisted sintering, and plasma sintering are effective for producing high-quality ceramics, but are not widely adopted due to their complex equipment requirements and high costs. For the widely used atmospheric sintering method, it has been reported that compaction pressure (before sintering) greatly influences the ceramic quality of sulfide electrolytes[28,29]. However, specific studies on oxide SSEs, particularly garnet-based SLBs, remain lacking.
In this work, the LLZTO pellets are compacted under different pressures and then sintered at 1,250 °C for
EXPERIMENTAL
Materials preparation
The LLZTO SSEs were prepared using a solid-state synthesis. The Li2CO3, La2O3, ZrO2, and Ta2O5 precursors were weighed according to the stoichiometry of LLZTO, and 15% excess Li2CO3 was weighed to supplement the Li loss upon high-temperature synthesis. Subsequently, 20 g precursor, 40 g Zr beads, and 30 mL ethanol were added into the ball mill jars, which were placed in a high-energy ball miller (8000D, Spex SamplePrep, USA) and kept at 8,000 r min-1 for 1 h. The mixed powders were transferred to a vacuum oven set at 80 °C and heated for 12 h. The powders were ground after drying, and sintered in a muffle furnace at 950 °C for 10 h with a heating rate of 2 °C min-1. After natural cooling, the ground pre-sintered powders were placed into a mold and pressed under the pressure of 50, 150, 300 and 600 MPa. The compacted pellets were then heated at 1,250 °C for 4 h with a heating rate of 5 °C min-1, and the LLZTO pellets were obtained after natural cooling.
Materials characterization
The crystal structure was analyzed using an X-ray diffraction (XRD) instrument (D8-A25, Bruker AXS, Germany) with Cu Kα radiation. The morphology and element distribution were examined by a scanning electron microscope (SEM) (SU-70, Hitachi, Japan) equipped with an energy dispersive spectroscopy (EDS) detector. The elemental composition and valence states were measured using an X-ray photoelectron spectroscopy (XPS) equipment (Escalab Xi+, Thermo Fisher, USA).
Electrochemical measurements
To measure the ionic and electronic conductivity, the Ag slurry was evenly sprayed on both sides of the polished LLZTO pellet. After drying, the Ag|LLZTO|Ag symmetric cells were tested on an electrochemical workstation (PARSTAT 3000A, Princeton, USA). The electrochemical impedance spectrum (EIS) plots were recorded with an amplitude potential of 10 mV and a frequency range of 106 to 10-1 Hz. The applied voltage of the steady-state current measurement was 200 mV. The LLZTO pellets were polished in an
RESULTS AND DISCUSSION
Figure 1A shows the XRD patterns of the different LLZTO pellets after sintering. It can be seen that all the characteristic peaks of each sample match well with the c-LLZO, and no
Figure 1. (A) XRD patterns of various LLZTO pellets. (B) Calculated grain size and micro-strain of various LLZTO pellets. Cross-section SEM images and related optical photos of (C) LLZTO-50, (D) LLZTO-150, (E) LLZTO-300, and (F) LLZTO-600 pellets.
Despite the similar sintering conditions, obvious morphology differences can be observed between the LLZTO pellets. For the LLZTO-50 pellet [Figure 1C], numerous pores are present in the worm-like structure due to insufficient contact between grains. For the LLZTO-150 pellet [Figure 1D], the grains are in contact with each other but are not completely densified, resulting in irregular hexagonal particles due to the incomplete sintering of the grains. For the LLZTO-300 pellet [Figure 1E], the grains have close contact with each other, and the ceramic is thoroughly densified after sintering. Most of the grain boundaries disappear due to the complete fusion of grains, leaving only a few small pores. For the LLZTO-600 pellet [Figure 1F], the tight contact between grains leads to the densest morphology with absent grain boundaries and few pores.
Based on the energy difference and peak intensity of La 3d peaks of the LLZTO-50 [Figure 2A], the La elements primarily exist in a form similar to metal oxides. The Ta 4f peaks of LLZTO-50 consist of splitting peaks [Figure 2B], indicating the dominance of Ta3+ oxides. In contrast, the Ta 4f peaks of LLZTO-600 shift to higher binding energy, implying greater oxidation of Ta in the high-pressure pellets. Similarly, the Zr 3d peaks of LLZTO-600 also shift to higher binding energy [Figure 2C], suggesting a higher valence of Zr in the high-pressure pellets. The Li 1s peak of LLZTO-50 and LLZTO-600 [Figure 2D] are similar, except for the larger peak area in LLZTO-600, indicating reduced Li loss and complete sintering in high-pressure pellets. These results imply that higher compactness may lead to concentrated oxygen, promoting the stable oxidation of transition metals and increased Li content in SSEs.
The compactness increases with compaction pressure due to the improved contact between particles [Table 1]. All the EIS plots of the symmetric cells [Figure 3A and B] show a semicircle contributed by grain boundary and a straight line related to ionic diffusion. The total resistances of LLZTO-50,
Figure 3. (A) Overall and (B) Magnified EIS plots, (C) Arrhenius curves, and (D) Direct-current polarization curves of various Ag|LLZTO|Ag symmetric cells. (E) Critical current density (CCD) curves of various Li|LLZTO|Li symmetric cells. (F) Performance comparison of this work with the reported results[11,30-37].
Compactness, ionic conductivity, activation energy, and electronic conductivity of various LLZTO pellets
Compaction pressure (MPa) | 50 | 150 | 300 | 600 |
Compactness (%) | 61.08 | 88.88 | 91.58 | 94.00 |
Ionic conductivity (S cm-1) | 1.63 × 10-6 | 4.10 × 10-4 | 5.30 × 10-4 | 6.36 × 10-4 |
Activation energy (eV) | 0.65 | 0.32 | 0.34 | 0.35 |
Electronic conductivity (S cm-1) | 5.77 × 10-9 | 1.14 × 10-8 | 1.36 × 10-8 | 3.11 × 10-8 |
The assembled Li|LLZTO|Li symmetric cells are used for galvanostatic charge/discharge tests to compare the interfacial stability of different samples to lithium metal. The initial polarization voltage of Li|LLZTO-150|Li is ~120 mV [Figure 4A], and it gradually increases at a uniform rate (~0.12 mV per cycle). The short circuit occurs after 487 cycles, and the polarization voltage drops from 180 to 50 mV, indicating that the Li dendrites start to grow along the grain boundary, resulting in a decrease in the “effective thickness” of the SSEs and a large decrease in the internal resistance of the cell. In the subsequent cycles, the polarization voltage stabilizes at 50 mV, exhibiting severe fluctuations up and down until the failure of the cell. Figure 4B shows the voltage-time curves of Li|LLZTO-300|Li, in which the initial polarization voltage is ~80 mV and the cells stably cycle at a current density of 0.2 mA cm-2 without voltage fluctuations. In the 1,190 cycles, the overpotential is stable only with an average increase of 0.06 mV per cycle, which is only half of that in
Figure 4. Cycling performance at various current densities of (A) LLZTO-150, (B) LLZTO-300, and (C) LLZTO-600 Li-symmetric cells. EIS of Li-symmetric cells (D) before cycling and (E) after 1,500 cycles.
As shown in Figure 5A, the initial discharge capacity of LFP|LLZTO-150|Li [Figure 5B] is 158.9 mAh g-1, and the initial Coulomb efficiency (CE) is as high as 99.9%. However, the capacity decays severely in the subsequent cycles. The overcharging occurs in the 78th cycle, and the capacity retention rate is only 83.4% after 100 cycles. The initial discharge capacity of LFP|LLZTO-300|Li [Figure 5B] is 157.9 mAh g-1, and the initial CE is 96.3%. The reversible capacity remains at 143.8 mAh g-1 after 150 cycles, and the capacity retention rate is 91.1%. The initial discharge capacity of LFP|LLZTO-600|Li [Figure 5B] is 158.4 mAh g-1, and the capacity retention rate after 150 cycles is 94.8%, which is the highest among all the full cells. This is because the highest ionic conductivity facilitates the stable Li+ transport inside the cell, and the dense morphology facilitates stable cathode/electrolyte/anode interfaces. In the 50th cycle [Figure 5C], the LFP|LLZTO-150|Li cell exhibits the largest overpotential, even with severe voltage fluctuations in the 100th cycle [Figure 5D]. The stable voltage plateaus and the lowest overpotential of LFP|LLZTO-600|Li confirm the feasibility of enhancing the SLB performance by increasing the compaction pressure of SSEs.
CONCLUSIONS
In this paper, LLZTO pellets are prepared with different compaction pressures and sintered at 1,250 °C for
DECLARATIONS
Authors’ contributions
Made substantial contributions to the conception and design of the study and performed data analysis and interpretation: Zhu, J.; Wu, Y.; Wang, L.; Lin, J.
Performed data acquisition: Zhu, J.; Wu, Y.; Zhang, H.; Xie, X.; Wang, L.; Lin, J.
Provided technical and material support: Yang, Y.; Peng, H.; Liang, X.; Qi, Q.; Lin, W.; Peng, D. L.
Wrote the first version of the manuscript: Zhu, J.; Wu, Y.; Lin, J.
All authors revised the manuscript.
Availability of data and materials
The data are available upon request from the authors.
Financial support and sponsorship
This work was supported by the National Natural Science Foundation of China (Nos. 52101273 and U22A20118) and Fundamental Research Funds for Central Universities of China (No. 20720220106). Financial support from the IEST (Initial Energy Science and Technology) (No. 20223160A0088) is also gratefully acknowledged.
Conflicts of interest
All authors declared that there are no conflicts of interest.
Ethical approval and consent to participate
Not applicable.
Consent for publication
Not applicable.
Copyright
© The Author(s) 2025
REFERENCES
1. Zhu, Y.; He, X.; Mo, Y. Origin of outstanding stability in the lithium solid electrolyte materials: insights from thermodynamic analyses based on first-principles calculations. ACS. Appl. Mater. Interfaces. 2015, 7, 23685-93.
2. Diederichsen, K. M.; Mcshane, E. J.; Mccloskey, B. D. Promising routes to a high Li+ transference number electrolyte for lithium ion batteries. ACS. Energy. Lett. 2017, 2, 2563-75.
3. Li, J.; Ma, C.; Chi, M.; Liang, C.; Dudney, N. J. Solid electrolyte: the key for high-voltage lithium batteries. Adv. Energy. Mater. 2015, 5, 1401408.
4. Takada, K. Progress in solid electrolytes toward realizing solid-state lithium batteries. J. Power. Sources. 2018, 394, 74-85.
5. Fuller, T. F.; Doyle, M.; Newman, J. Simulation and optimization of the dual lithium ion insertion cell. J. Electrochem. Soc. 1994, 141, 1.
6. Wu, J. F.; Pang, W. K.; Peterson, V. K.; Wei, L.; Guo, X. Garnet-type fast Li-ion conductors with high ionic conductivities for all-solid-state batteries. ACS. Appl. Mater. Interfaces. 2017, 9, 12461-8.
7. Jia, L.; Zhu, J.; Zhang, X.; Guo, B.; Du, Y.; Zhuang, X. Li-solid electrolyte interfaces/interphases in all-solid-state Li batteries. Electrochem. Energy. Rev. 2024, 7, 12.
8. Li, B.; Chao, Y.; Li, M.; et al. A review of solid electrolyte interphase (SEI) and dendrite formation in lithium batteries. Electrochem. Energy. Rev. 2023, 6, 7.
9. Zhang, J.; Wang, C.; Zheng, M.; et al. Rational design of air-stable and intact anode-electrolyte interface for garnet-type solid-state batteries. Nano. Energy. 2022, 102, 107672.
10. Rettenwander, D.; Blaha, P.; Laskowski, R.; et al. DFT study of the role of Al3+ in the fast ion-conductor Li7-3xAl3+xLa3Zr2O12 garnet. Chem. Mater. 2014, 26, 2617-23.
11. El-Shinawi, H.; Paterson, G. W.; Maclaren, D. A.; Cussen, E. J.; Corr, S. A. Low-temperature densification of Al-doped Li7La3Zr2O12: a reliable and controllable synthesis of fast-ion conducting garnets. J. Mater. Chem. A. 2017, 5, 319-29.
12. Wagner, R.; Redhammer, G. J.; Rettenwander, D.; et al. Fast Li-ion-conducting garnet-related Li7-3xFexLa3Zr2O12 with uncommon I4̅3d structure. Chem. Mater. 2016, 28, 5943-51.
13. Wu, J. F.; Chen, E. Y.; Yu, Y.; et al. Gallium-Doped Li7La3Zr2O12 garnet-type electrolytes with high lithium-ion conductivity. ACS. Appl. Mater. Interfaces. 2017, 9, 1542-52.
14. Deviannapoorani, C.; Shankar, L. S.; Ramakumar, S.; Murugan, R. Investigation on lithium ion conductivity and structural stability of yttrium-substituted Li7La3Zr2O12. Ionics 2016, 22, 1281-9.
15. Rangasamy, E.; Wolfenstine, J.; Allen, J.; Sakamoto, J. The effect of 24c-site (A) cation substitution on the tetragonal-cubic phase transition in Li7-xLa3-xAxZr2O12 garnet-based ceramic electrolyte. J. Power. Sources. 2013, 230, 261-6.
16. Ohta, S.; Kobayashi, T.; Asaoka, T. High lithium ionic conductivity in the garnet-type oxide Li7-xLa3(Zr2-x, Nbx)O12 (x=0-2). J. Power. Sources. 2011, 196, 3342-5.
17. Thompson, T.; Sharafi, A.; Johannes, M. D.; et al. A tale of two sites: on defining the carrier concentration in garnet-based ionic conductors for advanced Li batteries. Adv. Energy. Mater. 2015, 5, 1500096.
18. Mukhopadhyay, S.; Thompson, T.; Sakamoto, J.; et al. Structure and stoichiometry in supervalent doped Li7La3Zr2O12. Chem. Mater. 2015, 27, 3658-65.
19. Dhivya, L.; Murugan, R. Effect of simultaneous substitution of Y and Ta on the stabilization of cubic phase, microstructure, and Li+ conductivity of Li7La3Zr2O12 lithium garnet. ACS. Appl. Mater. Interfaces. 2014, 6, 17606-15.
20. Inada, R.; Yasuda, S.; Tojo, M.; Tsuritani, K.; Tojo, T.; Sakurai, Y. Development of lithium-stuffed garnet-type oxide solid electrolytes with high ionic conductivity for application to all-solid-state batteries. Front. Energy. Res. 2016, 4, 28.
21. Chen, C.; Sun, Y.; He, L.; et al. Microstructural and electrochemical properties of Al- and Ga-doped Li7La3Zr2O12 garnet solid electrolytes. ACS. Appl. Energy. Mater. 2020, 3, 4708-19.
22. Cao, Z.; Cao, X.; Liu, X.; et al. Effect of Sb-Ba codoping on the ionic conductivity of Li7La3Zr2O12 ceramic. Ceram. Int. 2015, 41, 6232-6.
23. Meesala, Y.; Liao, Y. K.; Jena, A.; et al. An efficient multi-doping strategy to enhance Li-ion conductivity in the garnet-type solid electrolyte Li7La3Zr2O12. J. Mater. Chem. A. 2019, 7, 8589-601.
24. Murugan, R.; Thangadurai, V.; Weppner, W. Fast lithium ion conduction in garnet-type Li7La3Zr2O12. Angew. Chem. Int. Ed. 2007, 46, 7778-81.
25. Zhang, J.; Li, J.; Zhai, H.; Tan, G.; Tang, X. One-step processing of soft electrolyte/metallic lithium interface for high-performance solid-state lithium batteries. ACS. Appl. Energy. Mater. 2020, 3, 6139-45.
26. Ihrig, M.; Mishra, T. P.; Scheld, W. S.; et al. Li7La3Zr2O12 solid electrolyte sintered by the ultrafast high-temperature method. J. Eur. Ceram. Soc. 2021, 41, 6075-9.
27. Zhu, Y.; Zhang, J.; Li, W.; Xue, Y.; Yang, J.; Li, S. Realization of superior ionic conductivity by manipulating the atomic rearrangement in Al-doped Li7La3Zr2O12. Ceram. Int. 2023, 49, 10462-70.
28. Cronau, M.; Szabo, M.; König, C.; Wassermann, T. B.; Roling, B. How to measure a reliable ionic conductivity? The stack pressure dilemma of microcrystalline sulfide-based solid electrolytes. ACS. Energy. Lett. 2021, 6, 3072-7.
29. Lee, C.; Han, S. Y.; Lewis, J. A.; et al. Stack pressure measurements to probe the evolution of the lithium-solid-state electrolyte interface. ACS. Energy. Lett. 2021, 6, 3261-9.
30. Hosokawa, H.; Takeda, A.; Inada, R.; Sakurai, Y. Tolerance for Li dendrite penetration in Ta-doped Li7La3Zr2O12 solid electrolytes sintered with Li2.3C0.7B0.3O3 additive. Mater. Lett. 2020, 279, 128481.
31. Janani, N.; Ramakumar, S.; Kannan, S.; Murugan, R. Optimization of lithium content and sintering aid for maximized Li+ conductivity and density in Ta-doped Li7La3Zr2O12. J. Am. Ceram. Soc. 2015, 98, 2039-46.
32. Ni, K. H.; Chen, Z. L.; Li, C. C. Densification and stress distribution within the sintered structure of ceramic electrolytes for all-solid-state Li-ion batteries. Acta. Mater. 2024, 275, 120057.
33. Shen, F.; Guo, W.; Zeng, D.; et al. A simple and highly efficient method toward high-density garnet-type LLZTO solid-state electrolyte. ACS. Appl. Mater. Interfaces. 2020, 12, 30313-9.
34. Xu, B.; Li, W.; Duan, H.; et al. Li3PO4-added garnet-type Li6.5La3Zr1.5Ta0.5O12 for Li-dendrite suppression. J. Power. Sources. 2017, 354, 68-73.
35. Yamada, H.; Ito, T.; Hongahally, B. R. Sintering mechanisms of high-performance garnet-type solid electrolyte densified by spark plasma sintering. Electrochim. Acta. 2016, 222, 648-56.
36. Zhang, H.; Wu, Y.; Zhu, J.; et al. Fusing Ta-doped Li7La3Zr2O12 grains using nanoscale Y2O3 sintering aids for high-performance solid-state lithium batteries. Nanoscale 2024, 16, 14871-8.
Cite This Article

How to Cite
Zhu, J.; Wu, Y.; Zhang, H.; Xie, X.; Yang, Y.; Peng, H.; Liang, X.; Qi, Q.; Lin, W.; Peng, D. L.; Wang, L.; Lin, J. Impact of compaction pressure on formation and performance of garnet-based solid-state lithium batteries. Energy Mater. 2025, 5, 500034. http://dx.doi.org/10.20517/energymater.2024.201
Download Citation
Export Citation File:
Type of Import
Tips on Downloading Citation
Citation Manager File Format
Type of Import
Direct Import: When the Direct Import option is selected (the default state), a dialogue box will give you the option to Save or Open the downloaded citation data. Choosing Open will either launch your citation manager or give you a choice of applications with which to use the metadata. The Save option saves the file locally for later use.
Indirect Import: When the Indirect Import option is selected, the metadata is displayed and may be copied and pasted as needed.
About This Article
Special Issue
Copyright
Data & Comments
Data
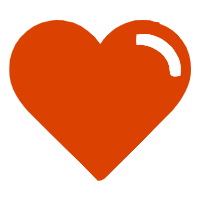
Comments
Comments must be written in English. Spam, offensive content, impersonation, and private information will not be permitted. If any comment is reported and identified as inappropriate content by OAE staff, the comment will be removed without notice. If you have any queries or need any help, please contact us at support@oaepublish.com.