Thermal degradation of lithium-ion battery cathodes: a machine learning prediction of stability and safety
Abstract
Lithium-ion batteries are extensively utilized due to their diverse applications, but their potential risk of thermal runaway leading to fire or even explosion remains a significant challenge to their sustainable development. The simulation of battery thermal runaway is complex, as it involves multiple reaction mechanisms. This study focuses on the interfacial interactions between reducing gases and cathode materials and explores the factors that influence these interactions during gas crosstalk within the battery. Thermogravimetric analysis coupled with differential scanning calorimetry was used to simulate the thermal attack of argon and hydrogen (
Keywords
INTRODUCTION
Climate change and the global energy transition drive the emerging "green and carbon-neutral" technology development towards a sustainable future. Since the early 1990s, rechargeable batteries have become integral to numerous sectors, driven by technological advancements and growing consumer demand. Among these, lithium-ion batteries (LIBs) stand out due to their high energy density, extended lifespan, eco-friendliness, and renewability. These attributes position LIBs as one of the most promising solutions for energy storage today and are widely used in people's lives[1-3]. As shown in Figure 1, a typical LIB is made of cathode, anode, electrolyte, separator, binders, and current collectors. Li-ions flow repeatedly between the anode and cathode under charging and discharging. This way, chemical energy is stored in and released from the battery, while creating an electric current.
Figure 1. Panoramic view of LIB structure, applications, and failure-induced thermal runaway, fire and explosion.
However, once exposed to external thermal, electrical, or mechanical impacts, battery internal materials will experience considerable structural alterations[4,5]. These changes trigger a series of complex chemical reactions inside the battery, which are accompanied by the release of large amounts of heat[6]. This excessive heat can lead to thermal runaway, potentially causing large-scale fires or even explosions[7-9]. The thermal runaway process of LIBs begins with the decomposition and regeneration of the solid electrolyte interphase (SEI), and then goes through multiple physicochemical stages, such as the reaction between the electrolyte solvent and the lithium intercalated graphite (LiC
The LIB cathode material not only defines the electrochemical performance of the battery by its material composition, but its thermal stability also affects thermal safety and performance of the battery. Ternary nickel cobalt manganese (NCM) cathode materials primarily comprise transition metal (TM) oxides, which contribute to their superior energy density and widespread applications. However, these materials also carry a heightened risk of thermal runaway when exposed to elevated temperatures. NCMs undergo significant phase transitions, beginning with the original layered phase characterized by a
This oxygen release, along with the hydrogen generated from LiH decomposition at the anode solid-electrolyte interphase above 200
The latest machine learning methods[22] show excellent performance at capturing nonlinear relationships and handling high-dimensional data, so they can make effective predictions even with incomplete information. Their powerful modeling capabilities have made machine learning a valuable tool across various fields, including battery material analysis and safety evaluation[23]. Using data from battery current, voltage, electrochemical impedance spectra, and temperature, researchers predicted parameters such as states of charge (SOCs) and battery health in the battery management system (BMS)[24]. Moreover, Artificial Neural Network (ANN) delivers highly precise predictions when applied to complex material behaviors and dynamic reactions[25-27]. The machine learning model provides valuable insights into the influence of factors such as anode and cathode structures, elemental doping, and electrolyte selection on battery performance. This understanding can guide researchers in optimizing material design[28]. Similarly, in the context of TGA, several parameters, such as temperature, heating rate, and heat flow, play crucial roles. The multilayer network structure effectively identifies complex nonlinear features and reveals intricate interactions between the variables. This capability demonstrates significant advantages in TGA data prediction[29].
Many studies have analyzed the thermophysical parameters and heat changes of overall reactions involving cathode materials, anode materials, and electrolytes[30,31]. However, a critical gap remains in linking specific reaction mechanisms to battery thermal failure or runaway, particularly regarding the effects of reducing gases on cathode materials. This study addresses this gap by examining the impact of reducing gases on ternary NCM cathode materials using TGA-DSC to investigate the reaction process and extract key thermal stability parameters. The resulting dataset was used to train an artificial neural network (ANN) model, enabling the prediction and evaluation of cathode thermal stability under varying material characteristics and environmental conditions.
Additionally, a hierarchical analysis method was applied to systematically weigh these key parameters, creating a comprehensive approach for assessing thermal stability. The findings of this research offer valuable insights for optimizing cathode material design to enhance safety, developing effective thermal management strategies for battery systems, and informing material selection in commercial battery manufacturing. By deepening the understanding of cathode stability and providing predictive tools for novel materials, this study addresses critical safety challenges in LIB technology, supporting the development of safer and more reliable next-generation energy storage solutions.
EXPERIMENTS AND METHODOLOGIES
Preparation of material
A range of cathode materials purchased from Cardo without further treatment were used to compare the performance of various elemental compositions after being attacked by reducing gases. The compositions of these cathodes are shown in Table 1. CR2032-type coin cells were assembled in an argon-filled glove box to investigate the thermal stability of cathode materials in LIBs with different SOCs under a hydrogen atmosphere. For the fabrication of electrodes, a viscous slurry containing purchased NCM cathode materials, Super P, and polyvinylidene fluoride (PVDF) in a mass ratio of 70:20:10 was prepared. The slurry was cast onto an aluminum foil and dried overnight at 100
Cathode type and composition
Cathode sample (acronym) | Mass fraction (wt.%) | |||
Li | Ni | Co | Mn | |
LiNi | 7.39 | 47.28 | 5.91 | 5.91 |
LiNi | 19.75 | 60.29 | 19.76 | 7.32 |
LiNi | 7.6 | 29.48 | 11.78 | 17.69 |
LiNi | 7.63 | 20 | 20 | 18 |
LiNi | 7.0 | 53.1 | 5.94 | 0.912 |
LiCoO | 7.4 | - | 59.7 | - |
LiMn | 4.21 | - | - | 58.86 |
The charge and discharge tests were performed using a Neware battery measurement system in a voltage range of 2.75-4.2 V (
Thermal analysis setup
Simultaneous thermal analysis (TGA-DSC) was conducted using a PerkinElmer STA6000 under three different hydrogen gas contents of a hydrogen and argon mixture: 5%, 3%, and 1% H
TGA experimental scenarios
Number | SOC (%) | H | Heating rate (K/min) | Gas flow rate (mL/min) |
1 | 0 | 5 | 10 | 100 |
2 | 0 | 3 | 10 | 100 |
3 | 0 | 1 | 10 | 100 |
4 | 0 | 5 | 10 | 50 |
5 | 0 | 5 | 10 | 150 |
6 | 0 | 5 | 30 | 100 |
7 | 0 | 5 | 60 | 100 |
8 | 50 | 5 | 10 | 100 |
9 | 50 | 1 | 10 | 100 |
10 | 100 | 5 | 10 | 100 |
11 | 100 | 1 | 10 | 100 |
Machine learning methods
The ANN model, a commonly used machine learning method for supervised learning tasks, consists of an input layer, hidden layers, and an output layer. In this study, static timing analysis (STA) data is analyzed using the back-propagation (BP) algorithm within an ANN framework, as shown in Figure 2A. The BP algorithm, which iteratively minimizes the error between predicted and actual outputs by adjusting the network's weights, ensures an effective learning process and reliable prediction results. Key information was extracted from the TGA data to establish a database. The input layer consists of seven input variables, namely content of Li, Co, Ni, and Mn; H
Figure 2. (A) Training flow of the TG data prediction model and (B) architecture of the developed ANN model.
The AHP model for cathode thermal risk under hydrogen attack
Target | Category | Parameter | Weight | Specifications |
Cathode thermal risk under hydrogen attack (R) | Critical degradation temperature (T) | T1 | 0.2873 | Onset temperature of decomposition reaction |
T2 | 0.1427 | Onset temperature of reduction reaction | ||
T3 | 0.0894 | Onset temperature of structural collapse | ||
T4 | 0.0503 | Temperature at peak decomposition rate | ||
T5 | 0.0319 | Temperature at peak reduction reaction rate | ||
T6 | 0.0216 | End temperature of reaction | ||
Reaction mass loss (M) | M1 | 0.0225 | Peak decomposition rate | |
M2 | 0.074 | Peak reduction rate | ||
M3 | 0.0408 | Mass remaining | ||
Heat release of reaction (H) | H1 | 0.2053 | Heat Release during decomposition | |
H2 | 0.0342 | Heat absorption during reduction |
For each neuron depicted in Figure 2B, the output is determined by
where
In this study, an ANN model with five hidden layers was developed using the Scikit-Learn library in Python to predict the thermal properties of cathode materials. Firstly, the whole dataset is normalized to improve the convergence speed of the ANN during training. Then the dataset is divided into 70% for training and 30% for testing in order to evaluate the model's prediction accuracy and robustness. Because of the limited dataset size, the leave-one-out cross-validation (LOOCV) technique is utilized for both model selection and parameter optimization. In this technique, each observation in the training set is used once as a validation sample while the remaining samples are used for training. This procedure is repeated for each observation, and the average performance metric is computed. The final model will select the best-performing hyperparameters based on the evaluation performance metrics.
Performance evaluation
The performance of the developed ANN model is evaluated by comparing the predicted values to the actual experimental data. This comparison is quantified using several well-known evaluation metrics.
One commonly used metric is the mean squared error (MSE), which is defined as
Another important metric is the coefficient of determination (
where
The MSE measures the average of the squared errors between predicted and actual values, providing an indication of the model's prediction accuracy. The
AHP quantitative scoring method
The hierarchical analysis method is employed to establish a risk assessment framework for the hydrogen attack reaction. During the reaction process of hydrogen attack on the cathode, key parameters are classified into secondary indicators, which are further grouped into three primary evaluation indicators: critical degradation temperature of cathode reaction (T), reaction mass loss (M), and heat release of reaction (H). T was divided into six sub-factors (T1-T6), M into three sub-factors (M1-M3), and H into two sub-factors (H1, H2). These primary indicators collectively assess the risk of thermal runaway in the cathode under H
Here,
The normalization of
Calculate the sum of the elements in each row:
Re-normalize to obtain the weight of each factor at this level:
The weight of each evaluation factor in the lowest layer of the evaluation system is derived as follows:
The cathode thermal property judgment matrix can be established [Supplementary Tables 2-5]. The random consensus index RI shown in Supplementary Table 6 is used to evaluate the consistency of the judgment matrix. A secondary evaluation model was developed, as shown in Table 3.
Key parameters of NCM 811 in various atmospheres, where the negative heat of reaction means an exothermic process
Reduction gas | |||||||||||
5%H | 439 | 547 | 568 | 587 | 615 | 623 | 0.25 | 0.22 | 76.1 | -510 | 161 |
3%H | 497 | 574 | 586 | 607 | 624 | 660 | 0.22 | 0.33 | 75.3 | -452 | 59 |
1%H | 513 | 603 | 625 | 657 | 695 | 707 | 0.19 | 0.24 | 76.1 | -335 | 37 |
Key parameters of various cathodes in 5%H
Cathode material | |||||||||||
NCM811 | 439 | 547 | 568 | 587 | 615 | 623 | 0.25 | 0.22 | 76.09 | -510 | 161 |
NCM622 | 524 | 587 | 595 | 610 | 633 | 659 | 0.31 | 0.34 | 77.56 | -465 | 178 |
NCM523 | 555 | 613 | 619 | 627 | 650 | 678 | 0.38 | 0.40 | 76.75 | -261 | 241 |
NCM111 | 551 | 606 | 621 | 627 | 650 | 680 | 0.40 | 0.33 | 74.84 | -179 | 152 |
Key parameters of NCM 811 cathodes at various gas flow and heating rates in 5%H
Heating rate ( | Flow rate (mL/min) | |||||||||||
10 | 50 | 519 | 567 | 576 | 591 | 633 | 674 | 0.27 | 0.30 | 78.7 | -518 | 251 |
10 | 150 | 424 | 532 | 553 | 579 | 606 | 647 | 0.24 | 0.24 | 70.8 | - | - |
30 | 100 | 484 | 617 | 645 | 672 | 703 | 713 | 0.18 | 0.17 | 76.6 | -501 | 136 |
60 | 100 | 534 | 684 | 726 | 749 | 800 | 800 | 0.14 | 0.12 | 76.3 | -443 | 54 |
10 | 100 | 439 | 547 | 568 | 587 | 615 | 623 | 0.25 | 0.22 | 76.1 | -510 | 161 |
RESULTS AND DISCUSSION
Hydrogen attack cathode performance
The properties of NCM cathode materials that have not undergone delithiation remain highly stable. As shown in Figure 3A, the mass loss of NCM811 powder exhibits minimal change when heated in an inert Ar atmosphere from 30-800
Figure 3. Non-isothermal decomposition behavior of cathode in various atmospheres (A) Ar, (B) 5%H
The comparison of Figure 3B-D shows that the cathode curves in the H
Typically, the redox pairs Ni
As hydrogen continues to flow and the temperature increases, the cathode decomposes into a rock-salt phase. Hydrogen then further reduces the cathode to metal. This is reflected by the endothermic peaks in Figure 3. The possible reactions involved in hydrogen attack[34-36] include
The weak differential thermogravimetry (DTG) peaks observed before the cathode mass stabilizes can be attributed to the structural collapse of LiMnO
This is due to the electrochemical inertness of Mn and its low content in NCM. As the experiments did not include crystalline phase analysis or elemental composition characterization of the reaction products, the formulas only suggest the possible presence of these products without precisely determining their content.
To more accurately characterize the cathode decomposition process, key parameters were extracted based on the specific features of the curves, including
Table 4 presents the key reaction parameters of the cathode at varying H
Figure 4 and Table 5 illustrate the non-isothermal decomposition behavior of various cathodes in 5%H
Figure 4. Non-isothermal decomposition behavior of various cathodes in 5%H
This trend suggests a diminishing gap in both temperature and time, resulting in a reduction of oxygen release. This reduction is attributed to the instability of high-valence TM ions under hydrogen attack and elevated temperatures. Such instability leads to the reduction of these ions and the release of oxygen from the lattice to maintain charge neutrality. Notably, Ni ions exhibit the fastest reduction rate, indicating their significant influence on the thermal stability of the cathode[37,38]. For a fixed lithium content, oxygen in the local coordination structure becomes less stable with increased Ni, particularly in higher oxidation states.
Consequently, materials with higher Ni content exhibit lower thermal decomposition temperatures and greater oxygen release. The differences between
In addition to the analysis of the cathode composition, the decomposition reactions influenced by environmental changes are also investigated. The flow rate of 5%H
Figure 5. Non-isothermal decomposition behavior of gas flow and heating rate in 5%H
The onset temperatures of the reaction were 484 and 534
An increased heating rate may prevent the molecules in the sample from achieving the requisite reaction rate, as they may not acquire sufficient energy in time. Consequently, the decomposition reaction commences at a higher temperature. Despite the rapid rise in temperature, the molecules may still lack the necessary energy to overcome the activation barrier for decomposition. This phenomenon further elevates the onset temperature.
Conversely, maximum weight loss rates (
During the battery charging process, Li
Figure 6. Non-isothermal decomposition behavior of NCM811 various SOCs (A) 0% SOC 5%H
Key parameters of various SOC NCM 811 cathodes under 5%H
SOC (%) | Reduction gas | ||||||||||
0% | 5%H | 307 | 380 | 399 | 509 | 657 | 915 | 0.06 | 0.18 | 73.1 | -358.5 |
50% | 5%H | 178 | 237 | 271 | 376 | 415 | 950 | 0.18 | 0.08 | 66.7 | -396.2 |
100% | 5%H | 162 | 239 | 312 | 377 | 495 | 950 | 0.31 | 0.31 | 59.4 | -651.0 |
100% | Ar | 216 | 248 | 278 | 332 | 627 | 854 | 0.16 | 0.11 | 79.0 | - |
The CEI film - mainly composed of Li
Since Ni
Analysis of Pearson correlation coefficient
The thermal decomposition behavior of hydrogen-attacked cathode materials is influenced by several factors, including cathode composition, degree of delithiation, hydrogen content, gas flow rate, and heating rate. Decomposition experiments were also conducted on NCM622, NCM523, and NCM111 under varying conditions, resulting in a dataset comprising 55 entries. To enhance the accuracy of data predictions, relevant features and variables were selected from the dataset, and Pearson correlation analysis was employed to elucidate the relationships between these parameters.
The Pearson correlation coefficient is a statistical measure that quantifies the linear relationship between two real-valued variables. Introduced as the first formal metric for correlation, it remains the most commonly applied method today. This coefficient is particularly useful for evaluating the linear association between two normally distributed continuous variables[44] and can be expressed as:
where
Additionally, to assess whether the correlation coefficient is statistically significant, the
where
Figure 7 presents the half Pearson correlation coefficient (r) matrix, with each row corresponding to a variable in the dataset and each column representing the same variables as the rows. The values in each cell indicate the correlation coefficient between the two associated variables. The lithium content in the cathode exhibits strong correlations with
It is worth noting that the strong correlation may not be apparent in the correlation coefficient plot. This is likely due to the limited variation in the
Evaluation of machine learning prediction
The experimental data and Pearson correlation analysis reveal a distinct correlation among the properties of cathode materials, experimental conditions, and key parameters during the hydrogen attack. This finding suggests the feasibility of developing a machine learning model to predict the thermal decomposition behavior of cathode materials. By using this data-driven approach, the model can analyze and forecast crucial factors such as reaction temperature, mass loss rate, and thermal effects under various reaction conditions. The seven input variables for the model include the atomic ratios of Li, Co, Ni, and Mn, as well as H
The optimal hyperparameters for the models were identified using LOOCV and then applied to retrain the prediction model. For the ANN model, hyperparameters were determined through trial-and-error optimization on the training set. This selection reflects a careful balance to enhance model performance. The tanh activation function was chosen for its effectiveness in handling nonlinear problems, while also mitigating gradient vanishing issues to maintain model stability. A regularization coefficient (alpha) of 0.01 was used to penalize weights moderately, reducing overfitting and improving generalization. The hidden layer architecture, with neurons configured in a five-layer structure (16, 32, 64, 64, 32), was designed to capture high-dimensional data features and process complex information. An initial learning rate of 0.01 allows the model to converge quickly during early training, while also ensuring stability in later stages. With a maximum of 300 iterations, the model has sufficient opportunities to reach optimal convergence. The optimizer, stochastic gradient descent (SGD), is well-suited for large datasets and helps avoid local minima. Finally, the convergence tolerance was set to 1e
Supplementary Figure 3 illustrates the R
Support vector machine (SVM) is also a robust supervised learning algorithm widely utilized in classification and regression tasks. Its fundamental principle involves identifying the optimal hyperplane in high-dimensional space to effectively separate different classes of data points. SVM demonstrates strong performance in managing high-dimensional data and exhibits notable advantages in small-sample learning and resilience to noise. Given the limited sample size of the dataset in this study and the presence of multiple output parameters, the suitability of the SVM model is evident. Therefore, this research develops the SVM model for data prediction, leveraging its strengths in complex data environments[45,46].
In this SVM model, C = 10 indicates a stronger penalty that reduces misclassification while maintaining the model's generalization ability. The parameter coef0 = 0.0 ensures that the linear and nonlinear combinations of independent variables remain unbiased in the polynomial kernel function. Additionally, gamma = 0.1 controls the influence range of the data points, with a lower gamma value effectively preventing overfitting and enhancing the model's robustness in high-dimensional space. The choice of kernel = "poly" selects a polynomial kernel, which accommodates the complex structures of nonlinear features, significantly improving classification accuracy. This well-considered combination of hyperparameters ensures the model's efficiency and precision when addressing complex data.
As illustrated in Figure 9, a comprehensive performance evaluation of the established SVM model by comparing predicted and actual values in the test set is established. The distribution of data points indicates that the prediction performance of the SVM model is average; although most points are near the diagonal, significant errors remain. R
Comparison of ANN and SVM model performance
Model | ANN | SVM | ||
Model setting | Parameter | Value | Parameter | Value |
hidden_layer_size | (16, 32, 64, 64, 32) | C | 10 | |
activation function, solver | tanh, Sgd | coef0 | 0.0 | |
max_iter, tol | 300, 1e | gamma | 0.1 | |
learning_rate_init | 0.01 | kernel | poly | |
Accuracy | R | 0.75 | 0.81 | |
R | 0.73 | 0.64 | ||
MSE for training set | 0.022 | 0.015 | ||
MSE for test set | 0.030 | 0.033 |
Table 8 summarizes the performance of the ANN and SVM models. The R
AHP quantitative scoring framework for cathode
Researchers are required to input the elemental composition of the cathode material along with its atomic ratios and provide relevant environmental parameters. These inputs will then be processed through an ANN model to attain accurate predictions. Ultimately, the analytic hierarchy process (AHP) method enables a systematic evaluation and quantitative scoring of the thermophysical parameters of cathode materials, thereby offering a robust scientific basis for assessing their safety.
In this study, all experiments were conducted using the NCM811 battery cathode material with a heating rate of 10
Cathode thermal performance judgment results of NCM 811
Sample | Acronym | Experimental value | Assessed value | Total weight | Score | Total score |
NCM811 | T1 | 439 | 100 | 0.2873 | 28.73 | 100 |
T2 | 568 | 100 | 0.1427 | 14.27 | ||
T3 | 615 | 100 | 0.0894 | 8.94 | ||
T4 | 547 | 100 | 0.0503 | 5.03 | ||
T5 | 587 | 100 | 0.0319 | 3.19 | ||
T6 | 623 | 100 | 0.0216 | 2.16 | ||
M1 | 0.25 | 100 | 0.074 | 7.4 | ||
M2 | 0.227 | 100 | 0.0408 | 4.08 | ||
M3 | 76.09 | 100 | 0.0225 | 2.25 | ||
H1 | 510.53 | 100 | 0.2053 | 20.53 | ||
H2 | 161.41 | 100 | 0.0342 | 3.42 |
T1, the initial thermal decomposition temperature of the battery cathode material, plays a critical role in influencing T2-T6. Due to its significant impact on the overall thermal decomposition process, it has been assigned the highest weight of 0.2873 in the scoring system. Additionally, the heat generated during the thermal decomposition of battery cathode materials after exposure to hydrogen and elevated temperatures is closely related to the heat release during battery thermal runaway, especially when the scale of the study is expanded. As a result, this factor is also recognized as another key parameter influencing the thermal risk of the battery material, which is assigned a weight of 0.2053. During thermal decomposition, heat is released, while heat is absorbed during the reduction phase. As a result, H1 is given a higher weight of 0.074 due to its greater role in heat generation, whereas H2 is assigned a weight of 0.048 in the thermal risk assessment.
The evaluation results of the thermal properties of cathodes with varying atomic ratios under 5%H
To enhance accessibility and usability for researchers and industry practitioners, we have developed an open-access online software platform named the Lithium-ion Battery Cathodes Thermal Degradation Prediction & Risk Evaluation System (BCTR). This tool, powered by an advanced ANN model, is designed to facilitate rapid and accurate predictions of cathode thermophysical properties and degradation behaviors under inert argon atmospheres. The software is available at http://cathode.firelabxy.com/. Figure 11 showcases the user interface of the BCTR system, where users can input the elemental composition of LIB cathodes and key environmental parameters (e.g., hydrogen content, gas flow rate, and heating rate). Based on these inputs, the system automatically calculates critical thermophysical properties, predicts DTG curves, and provides a comprehensive risk assessment score for the thermal degradation of the selected cathode material. The BCTR system delivers results through intuitive visualizations, offering clear and actionable insights. Continuous updates will enhance the AI model by incorporating more TGA data, improving accuracy and broadening its applicability. By bridging cutting-edge machine learning with user-friendly design, BCTR represents a significant step forward in enabling the efficient evaluation of thermal safety and performance for LIB cathodes.
Figure 11. User interface of cathodes thermal degradation prediction & risk evaluation system (BCTR) (Available from: http://cathode.firelabxy.com/).
CONCLUSIONS
This study investigates the hydrogen attack process on ternary cathode materials and the associated factors. During the reaction, 11 key parameters were extracted:
Pearson correlation analysis reveals the relationships among the parameters more clearly. Notably, lithium content exhibits a strong correlation (0.79) with the cathode's decomposition, while most of key temperature parameters have correlation coefficients exceeding 0.9. The correlation data establishes a solid basis for developing an ANN model for predictive analysis. After identifying the optimal hyperparameters, the model demonstrated robust predictive performance, achieving an R
Building on these findings, future research should focus on gathering larger, more diverse datasets to enhance model robustness and generalization. Exploring advanced machine learning algorithms, such as ensemble methods or deep learning frameworks, could further enhance predictive accuracy. Incorporating higher-dimensional parameters, including microstructural data (e.g., scanning electron microscopy images, elemental mapping, and crystallographic phase analysis), would provide deeper insights into degradation mechanisms. Additionally, integrating machine learning models with physical or thermodynamic simulations holds promise for incorporating domain-specific knowledge and refining predictions. These advancements will expand the scope of cathode material evaluation and foster innovation in next-generation battery technologies.
DECLARATIONS
Authors' contributions
Investigation, methodology, writing-original draft, formal analysis: Zhou, Y.
Investigation, Methodology: Ding, Y.
Resources, Formal analysis: Chen, Y.; Shen Y.
Methodology, Formal analysis: Wang, Z.
Experimental assistance: Li, X.
Resources, Formal analysis: Xu, J.
Conceptualization, methodology, supervision, writing-review & editing, funding acquisition: Huang, X.
Availability of data and materials
Data will be provided upon request..
Financial support and sponsorship
This work is funded by Key-Area Research and Development Program of Guangdong Province (No. 2023B0909060004).
Conflicts of interest
All authors declared that there are no conflicts of interest.
Ethical approval and consent to participate
Not applicable.
Consent for publication
Not applicable.
Copyright
© The Author(s) 2025.
REFERENCES
1. Huang, W.; Feng, X.; Han, X.; Zhang, W.; Jiang, F. Questions and answers relating to lithium-ion battery safety issues. Cell. Rep. Phys. Sci. 2021, 2, 100285.
2. Liu, K.; Liu, Y.; Lin, D.; Pei, A.; Cui, Y. Materials for lithium-ion battery safety. Sci. Adv. 2018, 4, eaas9820.
3. Ge, S.; Leng, Y.; Liu, T.; et al. A new approach to both high safety and high performance of lithium-ion batteries. Sci. Adv. 2020, 6, eaay7633.
4. Xia, Q.; Ren, Y.; Wang, Z.; et al. Safety risk assessment method for thermal abuse of lithium-ion battery pack based on multiphysics simulation and improved bisection method. Energy 2023, 264, 126228.
5. Han, X.; Lu, L.; Zheng, Y.; et al. A review on the key issues of the lithium ion battery degradation among the whole life cycle. eTransportation 2019, 1, 100005.
6. Liu, J.; Yadav, S.; Salman, M.; Chavan, S.; Kim, S. C. Review of thermal coupled battery models and parameter identification for lithium-ion battery heat generation in EV battery thermal management system. Int. J. Heat. Mass. Transf. 2024, 218, 124748.
7. Feng, X.; Ren, D.; He, X.; Ouyang, M. Mitigating thermal runaway of lithium-ion batteries. Joule 2020, 4, 743-70.
8. Shahid, S.; Agelin-Chaab, M. A review of thermal runaway prevention and mitigation strategies for lithium-ion batteries. Energy. Convers. Man. X. 2022, 16, 100310.
9. Zheng, Y.; Che, Y.; Hu, X.; Sui, X.; Stroe, D.; Teodorescu, R. Thermal state monitoring of lithium-ion batteries: progress, challenges, and opportunities. Prog. Energy. Combust. Sci. 2024, 100, 101120.
10. Feng, X.; Zheng, S.; Ren, D.; et al. Investigating the thermal runaway mechanisms of lithium-ion batteries based on thermal analysis database. Appl. Energy. 2019, 246, 53-64.
11. Feng, X.; Ouyang, M.; Liu, X.; Lu, L.; Xia, Y.; He, X. Thermal runaway mechanism of lithium ion battery for electric vehicles: a review. Energy. Storage. Mater. 2018, 10, 246-67.
12. Gustafsson, O.; Kullgren, J.; Brant, W. R. Low-temperature cation ordering in high voltage spinel cathode material. ACS. Appl. Energy. Mater. 2023, 6, 5000-8.
13. Duan, Y.; Chen, S.; Zhang, L.; Guo, L.; Shi, F. Review on oxygen release mechanism and modification strategy of nickel-rich NCM cathode materials for lithium-ion batteries: recent advances and future directions. Energy. Fuels. 2024, 38, 5607-31.
14. Li, Y.; Liu, X.; Wang, L.; et al. Thermal runaway mechanism of lithium-ion battery with LiNi0.8Mn0.1Co0.1O2 cathode materials. Nano. Energy. 2021, 85, 105878.
15. Shadike, Z.; Lee, H.; Borodin, O.; et al. Identification of LiH and nanocrystalline LiF in the solid-electrolyte interphase of lithium metal anodes. Nat. Nanotechnol. 2021, 16, 549-54.
16. Nam, K.; Bak, S.; Hu, E.; et al. Combining in situ synchrotron X‐ray diffraction and absorption techniques with transmission electron microscopy to study the origin of thermal instability in overcharged cathode materials for lithium‐ion batteries. Adv. Funct. Mater. 2013, 23, 1047-63.
17. Liu, X.; Ren, D.; Hsu, H.; et al. Thermal runaway of lithium-ion batteries without internal short circuit. Joule 2018, 2, 2047-64.
18. Wang, Y.; Ren, D.; Feng, X.; Wang, L.; Ouyang, M. Thermal runaway modeling of large format high-nickel/silicon-graphite lithium-ion batteries based on reaction sequence and kinetics. Appl. Energy. 2022, 306, 117943.
19. Wu, Y.; Feng, X.; Liu, X.; et al. In-built ultraconformal interphases enable high-safety practical lithium batteries. Energy. Storage. Mater. 2021, 43, 248-57.
20. Qiu, B.; Zhang, M.; Wu, L.; et al. Gas-solid interfacial modification of oxygen activity in layered oxide cathodes for lithium-ion batteries. Nat. Commun. 2016, 7, 12108.
21. Wang, Y.; Feng, X.; Peng, Y.; et al. Reductive gas manipulation at early self-heating stage enables controllable battery thermal failure. Joule 2022, 6, 2810-20.
22. Qamar, R.; Ali, Zardari, B. Artificial neural networks: an overview. Mesopotamian. J. Comput. Sci. 1993, 30.
23. Chen, J.; Qi, G.; Wang, K. Synergizing machine learning and the aviation sector in lithium-ion battery applications: a review. Energies 2023, 16, 6318.
24. Liang, L.; Li, X.; Zhao, F.; et al. Construction and operating mechanism of high-rate Mo-doped Na3V2(PO4)3@C nanowires toward practicable wide-temperature-tolerance Na-ion and hybrid Li/Na-ion batteries. Adv. Energy. Mater. 2021, 11, 2100287.
25. Liu, Z.; Yang, X. Thermal stability enhancement and prediction by ANN model. Energy. AI. 2024, 16, 100348.
26. Burgaz, E.; Yazici, M.; Kapusuz, M.; Alisir, S. H.; Ozcan, H. Prediction of thermal stability, crystallinity and thermomechanical properties of poly(ethylene oxide)/clay nanocomposites with artificial neural networks. Thermochim. Acta. 2014, 575, 159-66.
27. Kurucan, M.; Özbaltan, M.; Yetgin, Z.; Alkaya, A. Applications of artificial neural network based battery management systems: a literature review. Renew. Sustain. Energy. Rev. 2024, 192, 114262.
28. Ng, M.; Sun, Y.; Seh, Z. W. Machine learning-inspired battery material innovation. Energy. Adv. 2023, 2, 449-64.
29. Chen, Y.; Wang, Z.; Lin, S.; Qin, Y.; Huang, X. A review on biomass thermal-oxidative decomposition data and machine learning prediction of thermal analysis. Clean. Mater. 2023, 9, 100206.
30. Ren, D.; Liu, X.; Feng, X.; et al. Model-based thermal runaway prediction of lithium-ion batteries from kinetics analysis of cell components. Appl. Energy. 2018, 228, 633-44.
31. Ren, D.; Feng, X.; Liu, L.; et al. Investigating the relationship between internal short circuit and thermal runaway of lithium-ion batteries under thermal abuse condition. Energy. Storage. Mater. 2021, 34, 563-73.
32. Manthiram, A.; Song, B.; Li, W. A perspective on nickel-rich layered oxide cathodes for lithium-ion batteries. Energy. Storage. Mater. 2017, 6, 125-39.
33. Manthiram, A.; Vadivel, Murugan, A.; Sarkar, A.; Muraliganth, T. Nanostructured electrode materials for electrochemical energy storage and conversion. Energy. Environ. Sci. 2008, 1, 621.
34. Huang, Z.; Yu, D.; Makuza, B.; Tian, Q.; Guo, X.; Zhang, K. Hydrogen reduction of spent lithium-ion battery cathode material for metal recovery: mechanism and kinetics. Front. Chem. 2022, 10, 1019493.
35. Zhang, Y.; Wang, H.; Li, W.; Li, C.; Ouyang, M. Size distribution and elemental composition of vent particles from abused prismatic Ni-rich automotive lithium-ion batteries. J. Energy. Storage. 2019, 26, 100991.
36. Wu, C.; Wu, Y.; Feng, X.; et al. Ultra-high temperature reaction mechanism of LiNi0.8Co0.1Mn0.1O2 electrode. J. Energy. Storage. 2022, 52, 104870.
37. Zheng, J.; Liu, T.; Hu, Z.; et al. Tuning of thermal stability in layered Li(NixMnyCoz)O2. J. Am. Chem. Soc. 2016, 138, 13326-34.
38. Bak, S.; Nam, K.; Chang, W.; et al. Correlating structural changes and gas evolution during the thermal decomposition of charged LixNi0.8Co0.15Al0.05O2 cathode materials. Chem. Mater. 2013, 25, 337-51.
39. Li, K.; Huang, X.; Fleischmann, C.; Rein, G.; Ji, J. Pyrolysis of medium-density fiberboard: optimized search for kinetics scheme and parameters via a genetic algorithm driven by kissinger's method. Energy. Fuels. 2014, 28, 6130-9.
40. Lee, S. H.; Moon, J.; Lee, M.; Yu, T.; Kim, H.; Park, B. M. Enhancing phase stability and kinetics of lithium-rich layered oxide for an ultra-high performing cathode in Li-ion batteries. J. Power. Sources. 2015, 281, 77-84.
41. Hatsukade, T.; Schiele, A.; Hartmann, P.; Brezesinski, T.; Janek, J. Origin of carbon dioxide evolved during cycling of nickel-rich layered NCM cathodes. ACS. Appl. Mater. Interfaces. 2018, 10, 38892-9.
42. Li, M.; Lu, J.; Chen, Z.; Amine, K. 30 Years of lithium-ion batteries. Adv. Mater. 2018, 30, e1800561.
43. Bonnick, P.; Muldoon, J. The quest for the holy grail of solid-state lithium batteries. Energy. Environ. Sci. 2022, 15, 1840-60.
44. Choi, J. Investigation of the correlation of building energy use intensity estimated by six building performance simulation tools. Energy. Build. 2017, 147, 14-26.
45. Anifowose, F.; Labadin, J.; Abdulraheem, A. Improving the prediction of petroleum reservoir characterization with a stacked generalization ensemble model of support vector machines. Appl. Soft. Comput. 2015, 26, 483-96.
Cite This Article
How to Cite
Zhou, Y.; Ding, Y.; Chen, Y.; Shen, Y.; Wang, Z.; Li, X.; Xu, J.; Huang, X. Thermal degradation of lithium-ion battery cathodes: a machine learning prediction of stability and safety. Energy Mater. 2025, 5, 500077. http://dx.doi.org/10.20517/energymater.2024.200
Download Citation
Export Citation File:
Type of Import
Tips on Downloading Citation
Citation Manager File Format
Type of Import
Direct Import: When the Direct Import option is selected (the default state), a dialogue box will give you the option to Save or Open the downloaded citation data. Choosing Open will either launch your citation manager or give you a choice of applications with which to use the metadata. The Save option saves the file locally for later use.
Indirect Import: When the Indirect Import option is selected, the metadata is displayed and may be copied and pasted as needed.
About This Article
Copyright
Data & Comments
Data
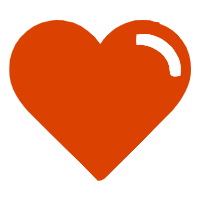
Comments
Comments must be written in English. Spam, offensive content, impersonation, and private information will not be permitted. If any comment is reported and identified as inappropriate content by OAE staff, the comment will be removed without notice. If you have any queries or need any help, please contact us at [email protected].