The integration of LiNi0.8Co0.1Mn0.1O2 coatings on separators for elevated battery performance
Abstract
Improving the efficiency and safety of lithium-ion batteries (LIBs) with high-energy cathodes is crucial, yet challenging due to the limitations of commercial separators. Herein, we find that “giving” a portion of the Ni-rich LiNi0.8Co0.1Mn0.1O2 (NCM811) positive electrode to the Al2O3-coated polyethylene (PE) (PE/Al2O3) separator as an active and thick ceramic coating (> 10 µm) can more efficiently enhance the separator's wettability and thermal stability compared with the inert and thin (< 5 µm, typically 1~2 µm) Al2O3 coating. The NCM811 coating on the separator can take part in the electrochemical reaction and contribute capacity without increasing the cell dead weight. The NCM811-coated separator has a low thermal shrinkage of 0.8% at 160 °C and a high lithium-ion transfer number of 0.66. Notably, the NCM811-coated separator enhances electrochemical performance, delivering higher capacities compared to traditional PE and PE/Al2O3 separators. Furthermore, it effectively mitigates lithium dendrite formation, thereby bolstering LIB safety. Our findings demonstrate the potential of using active cathode materials as separator coatings to advance LIB technology with high-energy cathodes.
Keywords
INTRODUCTION
Rechargeable batteries with lithium-ion (LIBs) are in high demand for large-scale applications, including portable electronics[1,2], electric automobiles[3-5], and energy storage systems (ESSs)[6-8]. To meet the demand, various cathodes have been explored to increase the energy density of LIBs[9-12]. However, higher energy density also means more electrochemically active material[13,14], which can cause safety problems due to unfavorable reactions during charging and discharging cycles[15,16]. Moreover, high-energy materials can pose a risk to consumers by triggering fires, explosions, and pollution if the batteries are used in abnormal conditions. Therefore, many studies have focused on improving the performance of battery components[17], especially the separator, which acts as a key factor for battery thermal stability[18-20], as it separates the anode and the cathode[21-23]. Currently, most industrial LIBs use polyolefin separators, such as polypropylene (PP), polyethylene (PE), and their blends due to their suitable chemical stability, reasonable cost, and acceptable mechanical strength[24-26]. However, these separators have low porosity, and poor wettability, which limit their electrolyte uptake and ionic conductivity[27,28]. They also have poor thermal stability and low melting points (around 130-170 °C), which compromise the safety of LIBs[29-32]. One of the effective solutions to the above problems is to coat polyolefin separators with ceramic particles[33-37]. Ceramic particles, such as
In this research, we suggest a novel separator design using Ni-rich LiNi0.8Co0.1Mn0.1O2 (NCM811) as a coating component on PE/Al2O3 separators. NCM811 is a high-energy cathode material that has high capacity and energy density but also poses safety risks due to poor thermal stability during repeated cycling, gas evolution, phase transition, and microcracks[44]. By using NCM811 as a coating material on PE/Al2O3 separators, we aim to improve not only the separator properties but also the electrochemical proprieties and safety of the NCM811 cathode. The NCM811 coating layer is directly coated on PE/Al2O3 separators by a simple casting method. Compared with the inert and thin Al2O3 coating, the active NCM811 coating on separators can participate in the electrochemical reactions to contribute capacities, which allow applying thicker ceramic layers (> 10 µm) to more efficiently improve the wettability, thermal stability, ionic diffusion, and Li-ion transfer number of separators.
EXPERIMENTAL AND CALCULATION METHODS
The bare PE separator, the Al2O3 inert ceramic coated PE separator, and NCM811 were all purchased from Canrd New Energy Technology Co., Ltd. The PE/Al2O3 separator has a model of MC112S1D and shows a structure of polyvinylidene fluoride (PVDF)/PE/Al2O3/PVDF with a thickness of 1 + 7 + 2 + 1 μm. The bare PE separator has a model MA-EN-SE-0C011E and a thickness of 12 μm. The NCM811 material was milled by a planetary ball mill for 225 min to reduce the particle size [Supplementary Figure 1A]. The NCM811 coated slurry was prepared using PVDF, NCM811, and Ketjen black (KB) dispersed in N-methyl pyrrolidone (NMP). The weight ratios of NCM811, KB, and PVDF were 90:3:7. The coating slurry was stirred uniformly and coated on a 10 µm thick PE/Al2O3 separator [Supplementary Figure 1B]. The separator was dried in a vacuum oven at 80 °C for one day. The total thicknesses of NCM-unmilled and NCM-crushed coated separators were about 32 and 28 µm, respectively.
The surface morphologies of the separators were examined by scanning electronic microscopy (SEM). The mechanical strength of the separators was assessed using a mechanical testing system. The separator’s thermal stability was evaluated via an infrared thermal imager (FLIR, model A655sc). The thermal shrinkage was determined by measuring the separator’s areas before and after heating for 30 min at various temperatures. The electrolyte uptake was determined by measuring the separator’s weights before and after being immersed in the electrolyte for 30 min. The separator’s wettability was measured by a surface contact angle test. The ionic conductivities at various temperatures were measured by AC impedance spectroscopy.
The electrochemical performance of the NCM811 cathode with different separators was evaluated by assembling coin-type half-cells (CR2032) in an argon-filled glove box. The positive electrode was prepared by mixing NCM811, PVDF, and KB with a weight ratio of 85:10:5. The negative electrode was a lithium metal foil. The electrolyte was 1.0 M LiPF6 in ethylene carbonate (EC) and ethyl methyl carbonate (EMC) with a weight ratio of 3:7. The cells were cycled between 2.4 and 4.8 V at various current rates using a battery tester (LAND CT2001A). The total active material in both cathode and separator active coatings is included for calculating mass specific capacity. The electrochemical impedance spectroscopy (EIS) measurements were performed on a CHI660E electrochemical workstation in the frequency range from
where ΔV represents the applied DC polarization voltage (0.01 V) in the chronoamperometric step, and I0 and Is denote the initial and steady-state currents, respectively. The initial and steady-state interfacial resistances are denoted by Ro and Rs, respectively.
The interaction between separator layers was studied by determining the atomic configurations and adsorption energies of PE with Al2O3 and NCM811 using density functional theory (DFT) calculation implemented by the Dmol3 package within a generalized gradient approximation (GGA) of the Perdew-Burke-Ernzerhof (PBE) functional. The Double Numeric with polarization (DNP) basis sets with effective core potential were employed for self-consistent field (SCF) calculations with 1 × 10-6 eV/atom SCF tolerance, 1000 Max. SCF cycles, and Gamma K-point was used for molecule and surface model optimization. Butane molecule was used to represent the fragment of the PE polymer chain. Al2O3(001) surface and NCM(100) were created and optimized before absorption calculation. A small Al2O3 cluster was used to calculate the interaction between NCM(100) surface and Al2O3.
RESULTS AND DISCUSSION
As illustrated in Figure 1, the performances of the bare PE separator, Al2O3 inert ceramic coated PE separator, and NCM811 active material coated PE/Al2O3 separators are compared under a high-temperature environment. At higher temperatures, as shown in Figure 1A, PE shrinks and melts, causing short circuits of cells with pure PE separators. Thin Al2O3 ceramic particles in PE/Al2O3 separators [Figure 1B] lost their support and collapse. However, the active material particles remain intact and supported by the Al2O3ceramic layer. The active material coating not only has excellent thermal resistance, but also creates a current path and electrochemical reaction due to the physical contact with the cathode, providing additional capacity [Figure 1D].
Figure 1. Schematic illustrating diagram of the failure mechanism of high-temperature stability of (A) polyolefin-based separator, (B) inert ceramic-coated separator, (C) active material-coated separator. (D) Schematic illustrating capacity increase by using active material coated separator instead of using a thick cathode.
Supplementary Figure 1 illustrates the ball milling process of NCM811 and the preparation process of NCM811 coated separators. Supplementary Figure 2 shows that the NCM-unmilled powders had a larger average particle size of 5.21 µm with some aggregates of smaller particles. The average particle dimension was reduced from 5.21 µm to 2.64 µm after ball milling. Figure 2 exhibits the SEM images of the surfaces and cross-sections of different separators. The SEM image of the bare PE separator in Figure 2A shows uniform submicron pores. A uniform structured layer was formed when Al2O3 was coated on a bare PE separator surface regardless of its shape [Figure 2B]. Similarly, the crushed NCM particles were well distributed when they were coated on a PE/Al2O3 composite separator, as shown in Figure 2C. However, the unmilled NCM particles had some small aggregates due to their large size, which might hinder their uniform distribution in the coating layer [Figure 2D]. The energy dispersive X-Ray spectroscopy (EDX) mapping in
Figure 2. SEM images surface of (A) bare PE, (B) PE/Al2O3, (C) NCM-crushed coated, and (D) NCM-unmilled coated separators. Cross-sectional SEM image of (E) bare PE separator, (F) PE/Al2O3 separator, (G) NCM-crushed coated separator, and (H) NCM-unmilled separator. (I) Contact angle pictures of different separators.
The separator’s wettability was evaluated by measuring the contact angle with the electrolyte and the electrolyte uptake. Figure 2I shows that the Al2O3-coated separator was more hydrophilic than the bare PE separator, as its contact angle reduced from 40° to 15° due to the presence of Al2O3 ceramic particles on its surface. The NCM-coated separator was even more hydrophilic, with a contact angle of 8.5°, because of the NCM powder’s affinity for polar solvents. The electrolyte uptake in Supplementary Table 1 also confirmed this trend. The bare PE separators had low electrolyte uptake because of their hydrophobic nature. While the Al2O3-coated separators exhibited higher electrolyte uptake, the NCM coating can further increase electrolyte uptake because of their hydrophilic nature and compatibility with the electrolyte solution. Figure 3A shows the ionic conductivities of bare PE, Al2O3-coated PE, and NCM-coated PE/Al2O3 separators increased with temperature from 30 to 80 °C. The NCM-coated separator had the highest ionic conductivity at all temperatures. Indicating that Li+ ions could move more easily between the electrodes through the electrolyte. Supplementary Table 1 shows the ionic conductivity of several separators at
Figure 3. (A) The ionic conductivities of pure PE, PE/Al2O3, NCM-crushed and NCM-unmilled separators at different temperatures. (B) Stress-strain profiles of different separators. (C) Force-displacement profiles for punch strength of various separators. (D) Heat shrinkage for different separators under different temperatures.
The mechanical properties of a separator are important for its industrial applications. Figure 3B compares the mechanical properties of separators. NCM-crushed coated separators had a larger tensile strength of 160.3 MPa than the PE/Al2O3 separator (158.5 MPa), as shown in Supplementary Table 1. The NCM-unmilled coated separator had a lower tensile strength and puncture resistance, but a higher elongation, due to the unevenness of the NCM-unmilled particles. Figure 3C and Table 1 show that the NCM-crushed coated separator had a slightly greater puncture property of 4.6 N than the Al2O3-coated separator (4.4 N). The thermal stability of separators was evaluated by measuring their shrinkage after being heated for half an hour, as shown in Figure 3D. The pure PE separator had a high thermal shrinkage ratio of 60% at 160 °C, due to its low melting point and isotropic structure. The Al2O3-coated PE separator had a lower thermal shrinkage ratio of 26.3% at the same temperature. The NCM-unmilled coated and NCM-crushed coated separators had even lower thermal shrinkage ratios of 1% and 0.8%, respectively, because of the improved thermal stability of the NCM particles.
Summary of cell performance with different separators
Separators | PE | PE/Al2O3 | NCM-unmilled | NCM-crushed | |
NCM mass loading on cathode (mg/cm2) | 7.87 | 7.86 | 7.93 | 7.88 | |
NCM mass loading on separator (mg/cm2) | 0 | 0 | 2.79 | 2.77 | |
Discharge capacity (mAh/g) | 0.5 C | 166.5 | 178 | 216.3 | 219 |
1 C | 102.4 | 134.8 | 152.8 | 184.9 | |
2 C | 64.5 | 109.7 | 120.7 | 142.5 | |
4 C | 24.6 | 69.2 | 82.6 | 92.3 |
Figure 4A shows optical images of different separators before and after heating them at 160 °C for 30 min. The pure PE separator shrank significantly. The NCM-unmilled and crushed coated separators, on the other hand, did not change their shape much, because of the thermal stability of NCM. This layer prevented the polyolefin separator’s heat shrinkage effectively. Figure 4B shows the infrared images of different separators. The bare PE separator began to shrink at 80 °C and reached its maximum shrinkage at 140 °C, while Al2O3-coated separators were stable at 80 °C but began to shrink at 120 °C. NCM-unmilled and crushed separators, however, remained stable even above the melting point of the bare PE separator. The NCM layer on the separators improved their thermal stability, because of the superior thermal performances of NCM811. The separator’s physical properties are important for the safety of LIBs, especially for large-scale applications such as electric vehicles[45]. A combustion experiment was performed to compare the flame retardancy of different separators. Figure 4C shows the images of different separators before, during, and after ignition. The bare PE separator blazed fast and disappeared after ignition. The
Figure 4. (A) Photographs of bare PE, PE/Al2O3, NCM-crushed and NCM-unmilled coated separators after being exposed to the temperature from 120-160 °C for 30 min. (B) FLIR thermal photos of the different separators. (C) Combustion photos of several separators.
The EIS spectra of the LIB with different separators are shown in Figure 5A. All spectra showed two overlapping semicircles, which represented the resistance of Li+ ions through the surface layer on the electrodes and the charge transport resistance at the electrode/electrolyte interface[46-48]. The cell with the NCM-coated separator had the lowest interface resistances. The cyclic voltammetry (CV) tests were carried out in the voltage range of 2.4-4.7 V at a scan rate of 0.1 mV/ s [Figure 5B]. The CV profiles showed two couple of redox peaks, which corresponded to the redox reaction of Ni2+/Ni4+ in the insertion and extraction of lithium-ions during charge-discharge processes[49,50]. The potential intervals (∆E) between the anodic and cathodic peaks reflected the electrochemical process involving electron transfer across the electrodes and lithium-ion diffusion in the electrode/electrolyte interface. The first anodic peak which represented the extraction of lithium-ions and the oxidation of Ni ions and the first cathodic peak which represented the insertion of Li-ions and the reduction of Ni ions of the cell with pure PE separators were at 3.80 and 3.70 V (∆E = 0.10 V), respectively. The redox peaks of the cell with Al2O3-coated separators were at 3.81 and 3.70 V (∆E = 0.11 V). The redox peaks of the cell with NCM-crushed coated separators were at 3.84 and 3.67 V
Figure 5. (A) Nyquist plot of NCM811/Li cells with the pure PE separator, Al2O3-coated separator, NCM-crushed coated separator, and NCM-unmilled coated separator. (B) Cyclic voltammetry (CV) profiles of NCM811/Li half-cells with various separators. (C-E) Charge/discharge curves of cells between the 1st and 150th cycles at 0.5 C with (C) pure PE separator, (D) PE/Al2O3 separator, and (E) NCM-crushed coated separator, respectively. (F) The rate capability of NCM811/Li cells with various separators. (G) Cycling performances of NCM811/Li cells with several separators in the voltage of 2.4-4.7 V at 0.5 C.
The charge and discharge curves of cells with different separators after the 1st and 150th cycles at 0.5 C are displayed in Figure 5C-E. The voltage hysteresis increased during the charge and discharge process as the cycling increased for all cells. However, the cells with bare PE separators and PE/Al2O3 separators exhibited low discharge capacities compared to the cells with NCM-coated separators. The initial discharge capacities at 0.5 C within 2.4-4.7 V were 166.5, 178, 219.03 and 216.32 mAh g-1 for the bare PE separator, PE/Al2O3 separator, NCM-crushed coated separator, and NCM-unmilled coated separator, respectively. After 150 cycles, the cell discharge capacities were 119.3, 134, 166.7 and 157.56 mAh g-1 for the same separators, respectively. The cell with the NCM-crushed coated separator showed the largest discharge capacity even after 150 cycles compared to cells with the other separators. Figure 5F shows the discharge capacities at different C rates from 0.5 to 4.0 C, changing every five cycles. The relative capacity in this figure is calculated as the difference between the starting discharge capacity at 0.5 C and the discharge capacity at a given C-rate. The cell using the NCM-coated separator exhibited the highest discharge capacities for all the C-rates compared to the cells using bare PE or PE/Al2O3 separators, which agreed with the highest ionic conductivity of the NCM-coated separator. Figure 5G shows the cycling capabilities of the cells with various separators at 0.5 C. The capacity retentions of the cell with the bare PE separator, the Al2O3-coated separator, the NCM-crushed coated separator, and the NCM-unmilled coated separator are 71.6%, 75.3%, 76.1%, and 72.8%, respectively. The cell with an NCM-crushed coated separator exhibits the highest capacity retention compared with the cells with other separators. This was due to the strong interaction between the NCM-crushed layer and the ceramic Al2O3 particle layer. The performances of the cells with various separators are summarized in Table 1. The calculation of cell capacity has included the total mass of active material from both the cathode and the active coating on a separator. The mass loading of NCM on the cathode ranges from 7.87 to 7.93 mg cm-2, while on the separator, it ranges from 2.77 to 2.79 mg cm-2. This indicates that the NCM coating on the separator adds approximately 35% more active material compared to the cathode alone. Supplementary Figure 5 provides charge/discharge profiles of three cells with different configurations and illustrates that NCM811 coating on the separator participates in the electrochemical reaction and contributes additional cell capacity. A comparative analysis of the estimated cost of the various separators is presented in Supplementary Table 1.
The Li-ion transference, which indicates the electrolyte's ability to Li-ion transport, was analyzed. A higher Li-ion transference can prevent the lithium dendrite growth and increase the battery capacity and cycle life[51,52]. As shown in Figure 6A, the cell using NCM-coated separators showed a larger tLi+ of 0.66 compared to those using the bare PE and PE/Al2O3 separators, which had
Figure 6. (A) Chronoamperometric of the Li||NCM-crushed||Li cell with a potential step of 0.01 V. (B) rate performances at 0.1, 0.2 and 0.5 mA cm-2. (C) cycle stability Li plating/stripping property with different separators at 0.5 mA cm-2.
DFT computations were used to study the interface interaction of the PE/Al2O3/NCM811-coated separator and the impact of the Al2O3 and NCM811 layers. Figure 7A-C displays the calculated adsorption energies of PE-NCM811(100) surface, PE-Al2O3(100) surface, and Al2O3-NCM811(100) surface, respectively. The results show that PE-Al2O3 has a higher adsorption energy of -0.58 eV than PE-NCM811(-0.30 eV). However, the adsorption energy increases significantly to -6.11 eV between NCM811 and Al2O3, indicating a strong interfacial interaction between them. Therefore, the strong interfacial interactions of PE-Al2O3 and Al2O3-NCM811 confirm the high mechanical proprieties and thermal stability of the PE/Al2O3/NCM811 separator, which ensures the electrochemical proprieties of NCM811/Li cells. Figure 7D-F also shows the strong interfacial contacts of the layers by the bonding electron cloud between atoms for each layer such as PE-NCM811 (C-O, 3.93 Å), PE- Al2O3 (C-O, 3.57 Å), and Al2O3-NCM811 (O-O, 2.54 Å). The stronger the binding between the atoms of Al2O3 and NCM811, the more stable their layers become, enhancing the interfacial interactions between layers and the integrity of the pore framework of the PE/Al2O3/NCM811 separator. The DFT results were consistent with our experimental measurements.
Figure 7. Absorption energy calculation of the PE, Al2O3 and NCM811 in the separator: (A) PE and NCM(100). (B) PE and Al2O3(001). (C) Al2O3 and NCM(100). Slices of the electron density distribution: (D) PE and NCM(100). (E) PE and Al2O3(001). (F) Al2O3 and NCM(100). In the Figure, the gray, white, green, red, steel blue, slate blue, medium purple and pink balls represent C, H, Li, O, Ni, Co, Mn and Al, respectively.
CONCLUSIONS
In this work, we have developed a novel separator design using NCM811 as a coating material on PE/Al2O3 separators for improving the performance and safety of LIBs with high-energy cathodes. The NCM811 coating layer was directly cast on PE/Al2O3 separators. This layer enhances wettability, thermal stability, ionic conductivity, and Li-ion transfer number of the PE/Al2O3 separator. The NCM811|Li half-cell with NCM811-coated separators showed higher capacity retention and better rate performance than those with PE or PE/Al2O3 separators. The NCM811 coating layer also prevented the growth of lithium dendrites on the anode surface during cycling, which enhanced the safety of LIBs. This work demonstrated that using active cathode material as a coating layer on a separator was an effective strategy to improve the performance and safety of LIBs with high-energy cathodes. This work also provided a new perspective for designing separators with active materials for various battery systems.
DECLARATIONS
Authors’ contributions
Investigation, data curation, formal analysis, writing - original draft: Nitou, M. V. M.
Investigation, data curation, writing - review & editing: Fang, X.; Liu, R.; Pang, Y.
Software, simulation, data curation, writing - review & editing: Wang, J.; Qin, W.
Formal analysis, writing - review & editing: Zhang, Z.
Supervision, administration, funding, validation, writing - review & editing: Niu, Y.; Zhao, C.; Chen, Y.; Lv, W.
Availability of data and materials
The raw/processed data required to reproduce these findings cannot be shared at this time due to technical or time limitations.
Financial support and sponsorship
This work was supported by the Natural Science Foundation of China (Grant Nos. 51972043 and 52102212), the fellowship of China Postdoctoral Science Foundation (No. 2022M720653), the Sichuan-Hong Kong Collaborative Research Fund (No. 2021YFH0184) and the Natural Science Foundation of Sichuan Province (Nos. 2023NSFSC0417 and 2023NSFSC0974).
Conflict of interest
All authors declared that there are no conflicts of interest.
Ethical approval and consent to participate
Not applicable.
Consent for publication
Not applicable.
Copyright
© The Author(s) 2025.
Supplementary Materials
REFERENCES
1. Rajaeifar, M. A.; Ghadimi, P.; Raugei, M.; Wu, Y.; Heidrich, O. Challenges and recent developments in supply and value chains of electric vehicle batteries: a sustainability perspective. Resour. Conserv. Recy. 2022, 180, 106144.
2. Zuo, W.; Innocenti, A.; Zarrabeitia, M.; Bresser, D.; Yang, Y.; Passerini, S. Layered oxide cathodes for sodium-ion batteries: storage mechanism, electrochemistry, and techno-economics. ACC. Chem. Res. 2023, 56, 284-96.
3. Murugan, M.; Saravanan, A.; Elumalai, P. V.; et al. Thermal management system of lithium-ion battery packs for electric vehicles: an insight based on bibliometric study. J. Energy. Storage. 2022, 52, 104723.
4. Khan, F. M. N. U.; Rasul, M. G.; Sayem, A. S. M.; Mandal, N. K. Design and optimization of lithium-ion battery as an efficient energy storage device for electric vehicles: a comprehensive review. J. Energy. Storage. 2023, 71, 108033.
5. Chen, S.; Xiong, J.; Qiu, Y.; Zhao, Y.; Chen, S. A bibliometric analysis of lithium-ion batteries in electric vehicles. J. Energy. Storage. 2023, 63, 107109.
6. Qiu, Y.; Dong, T.; Lin, D.; Zhao, B.; Cao, W.; Jiang, F. Fault diagnosis for lithium-ion battery energy storage systems based on local outlier factor. J. Energy. Storage. 2022, 55, 105470.
7. Liu, W.; Cao, J.; Song, F.; et al. A double transition metal Ti2NbC2Tx MXene for enhanced lithium-ion storage. Rare. Met. 2023, 42, 100-10.
8. Nian, Q.; Sun, T.; Liu, S.; Du, H.; Ren, X.; Tao, Z. Issues and opportunities on low-temperature aqueous batteries. Chem. Eng. J. 2021, 423, 130253.
9. Jyoti, J.; Singh, B. P.; Tripathi, S. K. Recent advancements in development of different cathode materials for rechargeable lithium ion batteries. J. Energy. Storage. 2021, 43, 103112.
10. Zhao, S.; Guo, Z.; Yan, K.; et al. Towards high-energy-density lithium-ion batteries: strategies for developing high-capacity lithium-rich cathode materials. Energy. Storage. Mater. 2021, 34, 716-34.
11. Chu, B.; Guo, Y. J.; Shi, J. L.; et al. Cobalt in high-energy-density layered cathode materials for lithium ion batteries. J. Power. Sources. 2022, 544, 231873.
12. Teng, J.; Tang, X.; Li, H.; Wu, Q.; Zhao, D.; Li, J. Al-Li alloys as bifunctional sacrificial lithium sources for prelithiation of high-energy-density Li-ion batteries. J. Power. Sources. 2022, 540, 231642.
13. Zhang, X.; Hui, Z.; King, S.; et al. Tunable porous electrode architectures for enhanced Li-ion storage kinetics in thick electrodes. Nano. Lett. 2021, 21, 5896-904.
14. Chang, J. H.; Pin, M. W.; Kim, I.; et al. Binder migration: frequently observed yet overlooked phenomena in electrode processing for lithium-ion batteries. J. Energy. Storage. 2024, 83, 110729.
15. Ogihara, N.; Itou, Y.; Sasaki, T.; Takeuchi, Y. Impedance spectroscopy characterization of porous electrodes under different electrode thickness using a symmetric cell for high-performance lithium-ion batteries. J. Phys. Chem. C. 2015, 119, 4612-9.
16. Wang, J.; Sun, Q.; Gao, X.; et al. Toward high areal energy and power density electrode for Li-ion batteries via optimized 3D printing approach. ACS. Appl. Mater. Interfaces. 2018, 10, 39794-801.
17. Liu, Z.; Jiang, Y.; Hu, Q.; et al. Safer lithium-ion batteries from the separator aspect: development and future perspectives. Energy. Environ. Mater. 2021, 4, 336-62.
18. Huang, Z.; Chen, Y.; Han, Q.; et al. Vapor-induced phase inversion of poly (m-phenylene isophthalamide) modified polyethylene separator for high-performance lithium-ion batteries. Chem. Eng. J. 2022, 429, 132429.
19. Yu, B.; Chen, X.; Jin, X.; Zhang, X.; Chen, L. Heat-resistant lithium-ion-battery separator using synchronous thermal stabilization/imidization. ACS. Appl. Polym. Mater. 2024, 6, 2464-73.
20. Lagadec, M. F.; Zahn, R.; Wood, V. Characterization and performance evaluation of lithium-ion battery separators. Nat. Energy. 2019, 4, 16-25.
21. Deng, J.; Cao, D.; Yang, X.; Zhang, G. Cross-linked cellulose/carboxylated polyimide nanofiber separator for lithium-ion battery application. Chem. Eng. J. 2022, 433, 133934.
22. Min, Y.; Guo, L.; Wei, G.; Xian, D.; Zhang, B.; Wang, L. Enhancing the safety and cyclic performance of lithium-ion batteries using heat resistant and wettable separator based on covalent organic framework and polybenzimidazole. Chem. Eng. J. 2022, 443, 136480.
23. Zhong, S.; Yuan, B.; Guang, Z.; et al. Recent progress in thin separators for upgraded lithium ion batteries. Energy. Storage. Mater. 2021, 41, 805-41.
24. Long, M. C.; Duan, P. H.; Gao, Y.; Wang, X. L.; Wu, G.; Wang, Y. Z. Boosting safety and performance of lithium-ion battery enabled by cooperation of thermotolerant fire-retardant composite membrane and nonflammable electrolyte. Chem. Eng. J. 2022, 432, 134394.
25. Yu, Y.; Jia, G.; Zhao, L.; et al. Flexible and heat-resistant polyphenylene sulfide ultrafine fiber hybrid separators for high-safety lithium-ion batteries. Chem. Eng. J. 2023, 452, 139112.
26. Babiker, D. M. D.; Usha, Z. R.; Wan, C.; Hassaan, M. M. E.; Chen, X.; Li, L. Recent progress of composite polyethylene separators for lithium/sodium batteries. J. Power. Sources. 2023, 564, 232853.
27. Han, C.; Cao, Y.; Zhang, S.; et al. Separator with nitrogen-phosphorus flame-retardant for LiNixCoyMn1-x-yO2 cathode-based lithium-ion batteries. Small 2023, 19, e2207453.
28. Nitou, M. V. M.; Tang, M.; Niu, Y.; et al. Separator with active coating for fast and stable Li-ion batteries. J. Power. Sources. 2024, 602, 234406.
29. Dong, G.; Liu, B.; Kong, L.; et al. Neoteric polyimide nanofiber encapsulated by the TiO2 armor as the tough, highly wettable, and flame-retardant separator for advanced lithium-ion batteries. ACS. Sustain. Chem. Eng. 2019, 7, 17643-52.
30. Ding, L.; Zhang, C.; Wu, T.; et al. Effect of temperature on compression behavior of polypropylene separator used for Lithium-ion battery. J. Power. Sources. 2020, 466, 228300.
31. Lu, Z.; Sui, F.; Miao, Y. E.; et al. Polyimide separators for rechargeable batteries. J. Energy. Chem. 2021, 58, 170-97.
32. Lingappan, N.; Lee, W.; Passerini, S.; Pecht, M. A comprehensive review of separator membranes in lithium-ion batteries. Renew. Sustain. Energy. Rev. 2023, 187, 113726.
33. Parikh, D.; Jafta, C. J.; Thapaliya, B. P.; et al. Al2O3/TiO2 coated separators: roll-to-roll processing and implications for improved battery safety and performance. J. Power. Sources. 2021, 507, 230259.
34. Wu, S.; Ning, J.; Jiang, F.; Shi, J.; Huang, F. Ceramic nanoparticle-decorated melt-electrospun PVDF nanofiber membrane with enhanced performance as a lithium-ion battery separator. ACS. Omega. 2019, 4, 16309-17.
35. Wang, W.; Yuan, Y.; Wang, J.; et al. Enhanced electrochemical and safety performance of lithium metal batteries enabled by the atom layer deposition on PVDF-HFP separator. ACS. Appl. Energy. Mater. 2019, 2, 4167-74.
36. Valverde, A.; Gonçalves, R.; Silva, M. M.; et al. Metal-organic framework based PVDF separators for high rate cycling lithium-ion batteries. ACS. Appl. Energy. Mater. 2020, 3, 11907-19.
37. Babiker, D. M. D.; Wan, C.; Mansoor, B.; et al. Superior lithium battery separator with extraordinary electrochemical performance and thermal stability based on hybrid UHMWPE/SiO2 nanocomposites via the scalable biaxial stretching process. Compos. Part. B. Eng. 2021, 211, 108658.
38. Park, J.; Kwon, Y. J.; Yun, J.; et al. Ultra-thin SiO2 nanoparticle layered separators by a surface multi-functionalization strategy for Li-metal batteries: highly enhanced Li-dendrite resistance and thermal properties. Energy. Storage. Mater. 2024, 65, 103135.
39. Feng, G.; Li, Z.; Mi, L.; Zheng, J.; Feng, X.; Chen, W. Polypropylene/hydrophobic-silica-aerogel-composite separator induced enhanced safety and low polarization for lithium-ion batteries. J. Power. Sources. 2018, 376, 177-83.
40. Zhang, S. S.; Fan, X.; Wang, C. Preventing lithium dendrite-related electrical shorting in rechargeable batteries by coating separator with a Li-killing additive. J. Mater. Chem. A. 2018, 6, 10755-60.
41. Hyun, D. E.; Jung, Y. J.; Kim, T. W.; et al. Multi-functional Al2O3-coated separators for high-performance lithium-ion batteries: critical effects of particle shape. Ceram. Int. 2023, 49, 30147-55.
42. Khan, Z. A.; Salaberri, P. A. G.; Heenan, T. M. M.; et al. Probing the structure-performance relationship of lithium-ion battery cathodes using pore-networks extracted from three-phase tomograms. J. Electrochem. Soc. 2020, 167, 040528.
43. Roh, Y.; Jin, D.; Kim, E.; et al. Highly improved thermal stability of the ceramic coating layer on the polyethylene separator via chemical crosslinking between ceramic particles and polymeric binders. Chem. Eng. J. 2022, 433, 134501.
44. Feng, Z.; Rajagopalan, R.; Sun, D.; Tang, Y.; Wang, H. In-situ formation of hybrid Li3PO4-AlPO4-Al(PO3)3 coating layer on
45. Kim, M.; Park, J. H. Inorganic thin layer coated porous separator with high thermal stability for safety reinforced Li-ion battery. J. Power. Sources. 2012, 212, 22-7.
46. Liu, T.; Garsuch, A.; Chesneau, F.; Lucht, B. L. Surface phenomena of high energy Li(Ni1/3Co1/3Mn1/3)O2/graphite cells at high temperature and high cutoff voltages. J. Power. Sources. 2014, 269, 920-6.
47. Jin, X.; Cai, Z.; Zhang, X.; et al. Transferring liquid metal to form a hybrid solid electrolyte via a wettability-tuning technology for lithium-metal anodes. Adv. Mater. 2022, 34, e2200181.
48. Shin, W. K.; Kannan, A. G.; Kim, D. W. Effective suppression of dendritic lithium growth using an ultrathin coating of nitrogen and sulfur codoped graphene nanosheets on polymer separator for lithium metal batteries. ACS. Appl. Mater. Interfaces. 2015, 7, 23700-7.
49. Xiong, C.; Liu, F.; Gao, J.; Jiang, X. One-spot facile synthesis of single-crystal LiNi0.5Co0.2Mn0.3O2 cathode materials for Li-ion batteries. ACS. Omega. 2020, 5, 30356-62.
50. Li, J.; Yao, R.; Cao, C. LiNi1/3Co1/3Mn1/3O2 nanoplates with {010} active planes exposing prepared in polyol medium as a high-performance cathode for Li-ion battery. ACS. Appl. Mater. Interfaces. 2014, 6, 5075-82.
51. Kim, D.; Liu, X.; Yu, B.; et al. Amine-functionalized boron nitride nanosheets: a new functional additive for robust, flexible ion gel electrolyte with high lithium-ion transference number. Adv. Funct. Mater. 2020, 30, 1910813.
Cite This Article
How to Cite
Download Citation
Export Citation File:
Type of Import
Tips on Downloading Citation
Citation Manager File Format
Type of Import
Direct Import: When the Direct Import option is selected (the default state), a dialogue box will give you the option to Save or Open the downloaded citation data. Choosing Open will either launch your citation manager or give you a choice of applications with which to use the metadata. The Save option saves the file locally for later use.
Indirect Import: When the Indirect Import option is selected, the metadata is displayed and may be copied and pasted as needed.
About This Article
Copyright
Data & Comments
Data
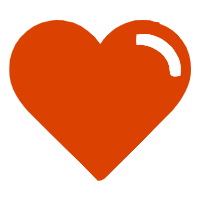
Comments
Comments must be written in English. Spam, offensive content, impersonation, and private information will not be permitted. If any comment is reported and identified as inappropriate content by OAE staff, the comment will be removed without notice. If you have any queries or need any help, please contact us at [email protected].