Highly crystalline covalent triazine frameworks modified separator for lithium metal batteries
Abstract
Covalent organic frameworks (COFs) that selectively enable lithium ions transport by their abundant sub-nano or nanosized pores and polar skeleton are considered as emerging coating materials for separators of lithium metal batteries. However, the COF-coated separators that combine high ionic conductivity with excellent lithium ions transference number (
Keywords
INTRODUCTION
Benefiting from the high theoretical specific capacity (3,860 mAh g-1, ten times that of graphite) and low redox potential (-3.04 V, vs. standard hydrogen electrode) of lithium metal anodes, lithium metal batteries (LMBs) are considered as one of the most promising high-energy-density secondary batteries[1-4]. Their main challenge is the irregular lithium metal plating during charging, forming lithium dendrites[5-7]. Generally, uncontrolled lithium dendrite growth leads to the corrosion of metallic lithium and the consumption of liquid electrolyte, resulting in a low Coulombic efficiency (CE) and poor cycling performance. Further, the lithium dendrite can penetrate the separator, causing a short circuit and explosion of the battery[8,9]. Its growth is rooted in the slow mass transport of lithium ions (Li+). When the diffusion rate of Li+ in the electrolyte is slower than that consumed during the electrochemical deposition process, concentration gradients are established, and lithium dendrites tend to grow[10]. Thus, accelerating Li+ transport in the bulk electrolyte is the key to relaxing the concentration gradients and thus achieving homogeneous lithium deposition[11]. Unfortunately, Li+ are usually surrounded by solvent molecules due to their small radius. The bulky solvated Li+ have reduced mobility; meanwhile, they always transport more slowly than the anions in electrolytes, resulting in a low Li+ transference number (
Among the various coating materials, such as inorganic nanoparticles[13,17,18] and polymers with ionic groups[19-21], covalent organic frameworks (COFs) are emerging porous materials with tunable nanoscale pores and tailorable skeletons. They usually contain light elements such as C, H, O, N, and B. Thanks to the nanosized pores and polar functional groups on the pore walls, COFs are expected to greatly promote the selective transport of Li+ by size-confinement effect and electrostatic interactions[22-24]. In addition, their intrinsic insolubility in electrolyte makes them potential candidates for surface modification of separators[25-27]. However, due to the rapid reaction between monomers and the limited reversibility of polymerization reactions, amorphous or poorly crystalline COFs are usually generated. These amorphous COFs would lead to ion pathways with higher tortuosity due to random stacking, thereby resulting in slower ion mobility and lower diffusion flux[28,29]. In addition, partial of the active sites (polar functional groups) are buried due to the limited surface area. Therefore, constructing COFs with good Li+ transport ability remains a huge challenge[30]. To solve this problem, studies have been devoted to the structural engineering of COFs to accelerate the transport of Li+. Cao et al. propose a sulfonate-rich COF with strong electronegativity and large interlayer spacing, which exhibited
This work develops a crystallinity engineering strategy for shortened ion diffusion pathways and more accessible active sites in the COF-coated separator, improving ionic conductivity and
EXPERIMENTAL
Materials
All the materials were obtained from commercial sources and used as received without further purification. The 1-methyl-2-pyrrolidinone (NMP) was obtained from Sinopharm Chemical Reagent Co. (Shanghai, China). Commercial LFP cathode, polyvinylidene fluoride (PVDF, Mw ~1,000,000), LFP, and Super-P were from Canrd New Energy Technology Co. Ltd. (Guangdong, China). PE separators were received from Senior Technology Materials Co. Ltd. (Shenzhen, China). The liquid electrolyte (1 mol L-1 LiPF6) in a mixed solvent of ethylene (EC) and dimethyl carbonate (DMC) with a volume ratio of 1:1 was from Duoduo Chemical Technology Co. Ltd. (Suzhou, China).
Preparation of CTF with different crystallinity
The AM-CTF was prepared through an amidine-based polycondensation method according to the reported literature. Furthermore, the HC-CTF was obtained by controlling the monomer feeding rate. The detailed synthesis methods can be found in Supplementary Material. To uniformly disperse the CTF in the coating slurry, the prepared CTF was stored without vacuum drying.
Preparation of LFP cathode
First, 0.16 g PVDF, 0.16 g Super-P, and 1.28 g LFP were mixed and ground for 30 min; then, the mixed powders were dispersed in NMP with vigorous stirring for 5 h. The obtained slurry was spread on Al foil by blade coating and further dried at 60 °C. Finally, the cathode-coated Al foil was cut into discs with a diameter of 12 mm.
Preparation of CTF-PE separator
First, 5 mg PVDF was dispersed in NMP with vigorous stirring for ten minutes, and then 45 mg AM-CTF or HC-CTF (dry weight) was dispersed in NMP with ultrasound and stirring for 6 h. Next, the dispersed PVDF and CTF slurry was mixed with further stirring for 30 min. The obtained mixed slurry was coated on the surface of the PE separator using blades with thicknesses of 5, 10 and 20 μm, respectively. After drying at 60 °C for 12 h under vacuum, AM-CTF-PE and HC-CTF-PE separators with distinct thicknesses are obtained. Finally, the one-side coated separator was shaped as discs with a diameter of 19 mm.
Characterization
Fourier-transformed infrared (FT-IR) spectra were obtained by a Fourier-transformed infrared spectrometer (VERTEX 70). The structural information of CTFs was determined by powder X-ray diffraction (XRD, SmartLab-SE) with Cu-Kα radiation. Transmission electron microscopy (TEM) (Tecnai G2 20, FEI Holland) and field emission TEM (FE-TEM) (Talos F200, FEI Holland) were exploited to characterize the morphology of CTFs. The thermal stability of CTFs was characterized by a thermal gravimetric analysis (TGA) instrument (Perkin-Elmer Pyrisl) with a rate of 10 °C/min up to 800 °C under a nitrogen atmosphere. The Brunauer-Emmett-Teller (BET) specific surface area and pore size distribution were evaluated on ASAP2420-4MP at 77 K. Surface morphology and chemical composition of Cu electrodes, CTF powders, and different separators were analyzed using field emission scanning electron microscopy (FE-SEM, Nova NanoSEM 450). The element distribution is illustrated by energy-dispersive X-ray spectroscopy (EDS) mapping. To compare the wetting properties of various separators toward liquid electrolyte, the contact angles were tested using a contact angle tester (OCA20).
The electrolyte uptake (EU) was measured by immersing separators into the liquid electrolyte for one hour, and then the weight of separators was compared before and after absorbing. The electrolyte retention (ER) was evaluated by weighing the separators after they have absorbed the electrolyte and rested for a period of time.
Where W1 is the weight of the original separators, and W2 is the weight of the separators after absorbing the liquid electrolyte, and W3 is the weight of the separator after it has absorbed the electrolyte and rested for a period of time.
The porosity was measured by weighing the separators before and after immersion in n-butanol:
where W4 is the weight of original separators, and W5 is the weight of separators after immersion in
Electrochemical measurements
CR2032 type coin cells were assembled to measure the electrochemical performance with different separators. LFP cathodes (12 mm), lithium metal (14 mm), and separators (19 mm) are used.
Electrochemical stabilization window
Electrolyte-soaked separator was sandwiched between lithium metal and stainless steel (SS) for linear sweep voltammetry (LSV) measurement on an AUTOLAB (PGSTAT302N). The scan rate is 10 mV s-1.
Ionic conductivity (σ)
To calculate the ionic conductivity, electrochemical impedance spectroscopy (EIS) measurement was carried out:
where d is the thickness of the separator, S is the area of the separators, and Rd is the bulk ohmic resistance of the electrolyte.
Lithium ions transference number ($$ {t_{L i^{+}} } $$ )
Combining chronoamperometry and EIS analysis with lithium symmetric cells,
where I0 is the initial current, Is is the steady-state current,
RESULTS AND DISCUSSION
CTFs were synthesized by a condensation reaction between 1,4-phthalaldehyde and terephthalamidine dihydrochloride, named CTF-HUST-1, according to reported procedures[38] [Figure 1A]. This one-pot polymerization was carried out at mild conditions (120 oC and ambient pressure at air atmosphere), which is beneficial for large-scale synthesis. By controlling the nucleation and crystal growth rates, the crystallinity of CTFs can be adjusted. When the monomers were fed in one step, the nucleation process is too fast and AM-CTFs are formed. By tuning the feeding rate of 1,4-phthalaldehyde (30 μL min-1), slow nucleation was achieved and CTFs with high crystallinity were generated[39]. The successful formation of the triazine frameworks was illustrated by FT-IR spectra. As shown in Figure 1B, the characteristic vibrations of the triazine units appear at 1,523 cm-1 (C=N) and 1,367 cm-1 (C-N) for both AM-CTF and HC-CTF, which is accordant with that in the literature[38]. The structures of AM-CTF and HC-CTF were characterized by solid-state cross-polarization magic angle spinning carbon-13 nuclear magnetic resonance (CP-MAS 13C NMR), as shown in Supplementary Figure 1. The results demonstrate that there is essentially no difference between the two structures in solid-state CP-MAS 13C NMR spectroscopy. The peaks with chemical shifts at 128 and 138 ppm are attributed to the phenyl carbons, while the peak with chemical shift at 179 ppm is attributed to the carbon in the triazine ring. Powder X-ray diffraction (PXRD) was used to analyze the structural differences between AM-CTF and HC-CTF [Figure 1C]. The PXRD pattern of AM-CTF shows a broad peak at 25.88º, indicating no long-range crystalline order. For the HC-CTF, diffraction peaks at about 7.4º, 12.7º, 14.7º and 26.2º are observed. According to literature, these peaks can be assigned to (100), (110), (200), and (001) facets, respectively, indicating the AA stacking arrangement of crystalline HC-CTF[39].
Figure 1. (A) Schematic synthesis of AM-CTF and HC-CTF; (B) FT-IR spectra; (C) PXRD patterns of AM-CTF and HC-CTF; (D) FE-SEM image and (E) FE-TEM image of AM-CTF; (F) FE-SEM image; (G)FE-TEM image and (H) high-magnification FE-TEM image of HC-CTF; (I) FFT image from the area of interest in (G).
To further study the CTF structures, FE-SEM, TEM, and FE-TEM were exploited to show their morphology and crystallinity. From FE-SEM, particles with no regular morphology are observed for AM-CTF [Figure 1D]. Meanwhile, the FE-TEM image of this sample shows no lattice fringes [Figure 1E]. Interestingly, as shown in Figure 1F and Supplementary Figure 2, particles with a much smoother surface and a more regular shape are observed for HC-CTF, compared to AM-CTF. FE-TEM images reveal their crystalline characteristic and clear lattice fringes with interplanar lattice spacing of 0.42 nm
To evaluate the porosity of AM-CTF and HC-CTF, nitrogen adsorption-desorption isotherms were performed at 77 K [Figure 2A]. The isotherm sorption profile of HC-CTF shows the typical type I characteristics, suggesting the existence of a large number of micropores. Through the nonlocal density functional theory method, the pore size distribution of HC-CTF is close to the reported calculated theoretical values[39] [Figure 2B]. The surface area calculated by the BET model is 652.18 m2 g-1. However, the BET surface area of AM-CTF drops sharply to 55.01 m2 g-1. The regular and interconnected channels with pores can facilitate a large accessible surface area for nitrogen in the BET measurement. And this morphology is suitable for diffusion of ions. Meanwhile, insignificant microporous structures are observed, suggesting structural defects and a rough texture for AM-CTF [Figure 2B]. The TGA measurement
Figure 2. (A) N2 adsorption and desorption isotherms; (B) Pore size distributions and (C) TGA curves of AM-CTF and HC-CTF.
The AM-CTF and HC-CTF were exploited as building blocks for functional layers on commercial PE separators. CTF-modified separators were prepared using the blade coating [Supplementary Figure 3]. This versatile method enables large-scale fabrication of the coated separator [Supplementary Figure 4]. As shown in Supplementary Figure 5A and B, the PE separator has porous and fibrous morphology. For the AM-CTF-modified PE separator (AM-CTF-PE) and the HC-CTF-modified separator (HC-CTF-PE), the CTF particles are uniformly distributed on the surface of the PE separator [Figure 3A and B]; meanwhile, some inevitable voids are observed on the surface of AM-CTF-PE and HC-CTF-PE separators
Figure 3. Top-view SEM images of (A) AM-CTF-PE and (B) HC-CTF-PE separators. Inset is the EDS mapping of N elements; Cross-sectional SEM images of (C) AM-CTF-PE and (D) HC-CTF-PE separators; (E)Photographs of AM-CTF-PE and HC-CTF-PE separators under bending conditions; (F) Photographs of PE, AM-CTF-PE and HC-CTF-PE separators after folding; (G) Contact angle images of PE, AM-CTF-PE and HC-CTF-PE after dropping liquid electrolyte on the surface.
Similar to the CTF samples, the BET surface area, pore volume and porosity of the HC-CTF-PE separators are higher than those of the AM-CTF-PE separator [Supplementary Table 1]. The electrolyte wettability of AM-CTF-PE and HC-CTF-PE separators is obviously improved compared with bare PE separators, with contact angles of 46.7°, 41.2° and 65.3°, respectively [Figure 3G]. This improved property of modified separators is mainly due to the CTF layer with nanosized pores and polar skeleton, which feature intrinsic affinity with polar electrolyte. Compared with AM-CTF-PE, the enhanced wettability of HC-CTF-PE separators originates from their larger specific surface area and pore volume. Meanwhile, the EU and ER of the HC-CTF-PE separator are higher than those of the AM-CTF-PE separator [Figure 4A and B]. The well-connected porous structure of HC-CTF can facilitate the penetration and retention of electrolyte, which are beneficial for fast ion transport.
Figure 4. (A) Electrolyte uptake and (B) electrolyte retention of the PE, AM-CTF-PE and HC-CTF-PE separators; (C) EIS plots of the PE, AM-CTF-PE and HC-CTF-PE separators, the inset shows enlarged EIS plots in the high-frequency region; Chronoamperometry profiles of (D) AM-CTF-PE and (E) HC-CTF-PE separators. Inset of (D) is the AC impedance spectra before polarization, and inset of (E) is the AC impedance spectra after polarization; (F) Fitting and evaluation of activation energy using the Nyquist plots.
The electrochemical stability of separators is the basis for the battery safety. As shown in
To evaluate the selective transport ability of Li+ for different separators, the
To further demonstrate the desolvation effect of CTF layers, the activation energy (Ea) of ion desolvation was evaluated using the Arrhenius equation. Based on temperature-dependent EIS measurements
where A, R, and T represent the frequency factor, ideal gas constant, and absolute temperature, respectively. After fitting, as shown in Figure 4F, the Ea values of HC-CTF-PE and AM-CTF-PE are 59.26 and
To investigate the lithium deposition behavior of CTF-modified separators, the long-term galvanostatic discharging and charging voltage profiles of Li//Li symmetric cells were measured. Figure 5A shows the performance of these cells with PE, AM-CTF and HC-CTF separators at a current density of 1 mA cm-2 and a fixed capacity of 1 mAh cm-2. The overpotential of the symmetric cells assembled with PE separators gradually increases as early as 120 h and fluctuates dramatically afterward. This results from the rapid electrolyte consumption and lithium dendrite growth caused by side reactions and polarization phenomena in the cells. The overpotential of symmetric cells with CTF-coated separators is lower than that of PE separators. Moreover, the overpotential of AM-CTF-PE separators gradually increases at about 170 h, while that of HC-CTF-PE separators is stable up to 300 h. From the voltage-time curves at different cycling times [Supplementary Figure 11], it is observed that the Li//Li symmetric cells assembled with HC-CTF-PE separators have the lowest overpotential, followed by AM-CTF-PE separators, while the highest is the PE separator. A higher overpotential suggests a larger nucleation energy barrier for the deposition of metallic lithium. According to literature, it may induce the dendritic lithium growth during plating[49]. Further, at a current density of 2 mA cm-2 and capacity of 2 mAh cm-2, the Li//Li symmetric cells assembled with HC-CTF-PE separators show better cycling stability and lower overpotential. [Supplementary Figure 12]. These results suggest that the CTF layer effectively delays the growth of lithium dendrite. To further study the dendrite suppressing effect of HC-CTF-PE separators, the morphology of the lithium plating onto Cu foils with various separators at a current density of 0.5 mA cm-2 were monitored. As shown in Figure 5B-D, obviously, abundant dendritic lithium grew on the Cu foil with the PE separator [Figure 5B]. Mossy dendrites are observed on the surface of the Cu foil with the AM-CTF-PE separator [Figure 5C]. When using the HC-CTF-PE separator, a much smoother Cu surface was obtained after cycling [Figure 5D]. Thus, due to the nanosized pores and desolvation effect, the HC-CTF-PE separator can regulate the ion flux and suppress the growth of dendritic lithium. And the electrochemical performance of the separators and assembled cells, including
Figure 5. (A) Voltage-time profiles of Li//Li symmetric cells assembled with PE, AM-CTF-PE and HC-CTF-PE separators at 1 mA cm-2 with a capacity of 1 mAh cm-2; SEM images of Cu electrodes from Cu//Li cells assembled with (B) PE, (C) AM-CTF-PE and (D) HC-CTF-PE separators after Li plating at a current density of 0.5 mA cm-2.
To further prove the prominent advantages of the HC-CTF-PE separator, the electrochemical performance of LFP//Li cells was investigated. The stability of the battery with different separators was evaluated by cycling performance tests. As shown in Figure 6A, the capacity of PE separator-assembled cells is only
To further prove the prominent advantages of the HC-CTF-PE separator, the electrochemical performance of LFP//Li cells was investigated. The stability of the battery with different separators was evaluated by cycling performance tests. As shown in Figure 6A, the capacity of PE separator-assembled cells is only
Figure 6. (A) Long-term cycling stability of LFP//Li cells at 1 C with the LiFePO4 loading of 1.58 mg cm-2; (B) Charge-discharge curves at 1 C for 100th revolution with the LiFePO4 loading of 1.58 mg cm-2; (C) Long-term cycling stability at 1 C with an increased LiFePO4 loading of 10.52 mg cm-2; (D) Cycling performance at 3 C with the LiFePO4 loading of 1.58 mg cm-2; (E) Rate performance of PE, AM-CTF-PE and HC-CTF-PE separators assembled cells at various current densities of 0.5-5 C; (F) Charge-discharge curves of HC-CTF-PE separator assembled cells at various current densities of 0.5-5 C; (G) The potential gaps of PE, AM-CTF-PE and HC-CTF-PE separators assembled cells at various rates, respectively.
The CE is further studied to evaluate the cell performance during repeated cycling. As shown in Figure 6D, the CEs of both HC-CTF-PE and AM-CTF-PE separators are around 95% over 300 cycles at 3 C. The HC-CTF-PE also has the highest capacity retention (49.5% after 300 cycles). However, the CE of PE separators is consistently unstable, with a low value of 90%. To clearly illustrate this trend, the enlarged graph of the CE for the first 100 cycles further shows the superior cycling stability of the HC-CTF separator
The rate performance of cells assembled with different separators was evaluated at current rates ranging from 0.5 to 5 C [Figure 6E]. The HC-CTF-PE separator can deliver the average specific capacity of 146, 136, 118, 102, 85 and 69 mAh g-1 at 0.5, 1, 2, 3, 4 and 5 C, respectively. By contrast, the AM-CTF-PE and PE separators show much lower capacities of 56 and 28 mAh g-1 at 5 C. It suggests a faster Li+ transport kinetic in the HC-CTF-PE separator, especially at the high rate. The charge/discharge voltage curves of the corresponding HC-CTF-PE, AM-CTF-PE, and PE separators in Figure 6F,
CONCLUSIONS
In summary, The AM-CTF and HC-CTF were successfully synthesized and coated on the surface of commercial PE separators. It can be found that compared with AM-CTF, the well-connected porous structure of HC-CTF shortens ion diffusion pathways, and a larger specific surface area provides more accessible active sites, enhancing ionic conductivity and
DECLARATIONS
Acknowledgments
The authors acknowledge support from Shenzhen Senior Technology Material Co., Ltd. We also acknowledge access to SEM, FE-TEM, XRD and BET facilities of the Analytical and Testing Center of Huazhong University of Science and Technology.
Authors’ contributions
Methodology, formal analysis, investigation, writing manuscript: Wang Y
Validation, resources, formal analysis: Chen Y, Wang X, Sun R, Yang Y
Methodology, visualization, investigation: Wang Y
Project administration, conceptualization, funding acquisition, supervision, writing manuscript: Nie H, Wang X, Tan B
Project administration, funding acquisition: Zhou X
Project administration, conceptualization, funding acquisition, supervision: Xie X
Availability of data and materials
The data supporting our work can be found in the Supplementary Materials.
Financial support and sponsorship
This work is supported by the Young Scientists Fund of the National Natural Science Foundation of China (52303084), Major International (Regional) Joint Cooperation Research Project of the National Natural Science Foundation of China (52020105012), the Young Scientists Fund of Natural Science Foundation of Hubei Province (2023AFB220), and the Open Research Fund (No. 2023JYBKF05) of Key Laboratory of Material Chemistry for Energy Conversion and Storage (HUST), Ministry of Education.
Conflicts of interest
All authors declare that there are no conflicts of interest.
Ethical approval and consent to participate
Not applicable.
Consent for publication
Not applicable.
Copyright
© The Author(s) 2024.
Supplementary Materials
REFERENCES
1. Li D, Hu H, Chen B, Lai WY. Advanced current collector materials for high-performance lithium metal anodes. Small 2022;18:e2200010.
3. Cheng XB, Zhang R, Zhao CZ, Wei F, Zhang JG, Zhang Q. A review of solid electrolyte interphases on lithium metal anode. Adv Sci 2016;3:1500213.
4. Zhang K, Lee G, Park M, Li W, Kang Y. Recent developments of the lithium metal anode for rechargeable non-aqueous batteries. Adv Energy Mater 2016;6:1600811.
5. Wang Q, Liu B, Shen Y, et al. Confronting the challenges in lithium anodes for lithium metal batteries. Adv Sci 2021;8:e2101111.
6. Liu K, Wang Z, Shi L, Jungsuttiwong S, Yuan S. Ionic liquids for high performance lithium metal batteries. J Energy Chem 2021;59:320-33.
7. Li G. Regulating mass transport behavior for high-performance lithium metal batteries and fast-charging lithium-ion batteries. Adv Energy Mater 2021;11:2002891.
8. Shen X, Liu H, Cheng X, Yan C, Huang J. Beyond lithium ion batteries: Higher energy density battery systems based on lithium metal anodes. Energy Stor Mater 2018;12:161-75.
9. Li G, Liu Z, Huang Q, et al. Stable metal battery anodes enabled by polyethylenimine sponge hosts by way of electrokinetic effects. Nat Energy 2018;3:1076-83.
10. Chen Y, Dou X, Wang K, Han Y. Lithium dendrites inhibition via diffusion enhancement. Adv Energy Mater 2019;9:1900019.
11. Albertus P, Babinec S, Litzelman S, Newman A. Status and challenges in enabling the lithium metal electrode for high-energy and low-cost rechargeable batteries. Nat Energy 2018;3:16-21.
12. Zhou P, Zhang X, Xiang Y, Liu K. Strategies to enhance Li+ transference number in liquid electrolytes for better lithium batteries. Nano Res 2023;16:8055-71.
13. Liang J, Chen Q, Liao X, et al. A nano-shield design for separators to resist dendrite formation in lithium-metal batteries. Angew Chem 2020;132:6623-8.
14. Wang G, Xiong X, Xie D, et al. Suppressing dendrite growth by a functional electrolyte additive for robust Li metal anodes. Energy Stor Mater 2019;23:701-6.
15. Din MMU, Murugan R. Metal coated polypropylene separator with enhanced surface wettability for high capacity lithium metal batteries. Sci Rep 2019;9:16795.
16. Wang C, Li W, Jin Y, Liu J, Wang H, Zhang Q. Functional separator enabled by covalent organic frameworks for high-performance Li metal batteries. Small 2023;19:e2300023.
17. Chen H, Lin Q, Xu Q, Yang Y, Shao Z, Wang Y. Plasma activation and atomic layer deposition of TiO2 on polypropylene membranes for improved performances of lithium-ion batteries. J Membrane Sci 2014;458:217-24.
18. Wu J, Zeng H, Li X, et al. Ultralight layer-by-layer self-assembled MoS2-polymer modified separator for simultaneously trapping polysulfides and suppressing lithium dendrites. Adv Energy Mater 2018;8:1802430.
19. Naren T, Jiang R, Qing P, et al. Stabilizing lithium metal batteries by synergistic effect of high ionic transfer separator and lithium-boron composite material anode. ACS Nano 2023;17:20315-24.
20. Zhang Y, Qiu Z, Wang Z, Yuan S. Functional polyethylene separator with impurity entrapment and faster Li+ ions transfer for superior lithium-ion batteries. J Colloid Interface Sci 2022;607:742-51.
21. Jin R, Fu L, Zhou H, et al. High Li+ ionic flux separator enhancing cycling stability of lithium metal anode. ACS Sustain Chem Eng 2018;6:2961-8.
22. Ding SY, Wang W. Covalent organic frameworks (COFs): from design to applications. Chem Soc Rev 2013;42:548-68.
23. An Y, Tan S, Liu Y, et al. Designs and applications of multi-functional covalent organic frameworks in rechargeable batteries. Energy Stor Mater 2021;41:354-79.
24. Zhou L, Jo S, Park M, et al. Structural engineering of covalent organic frameworks for rechargeable batteries. Adv Energy Mater 2021;11:2003054.
25. Ye H, Zhang C, Li Y, et al. Advanced covalent-organic framework materials for sodium-ion battery. Prog Nat Sci 2023;33:754-66.
26. Sun T, Xie J, Guo W, Li D, Zhang Q. Covalent-organic frameworks: advanced organic electrode materials for rechargeable batteries. Adv Energy Mater 2020;10:1904199.
27. Chang H, Wu Y, Han X, Yi T. Recent developments in advanced anode materials for lithium-ion batteries. Energy Mater 2022;1:100003.
28. Gao Z, Liu Q, Zhao G, Sun Y, Guo H. Covalent organic frameworks for solid-state electrolytes of lithium metal batteries. J Mater Chem A 2022;10:7497-516.
29. Niu C, Luo W, Dai C, Yu C, Xu Y. High-voltage-tolerant covalent organic framework electrolyte with holistically oriented channels for solid-state lithium metal batteries with nickel-rich cathodes. Angew Chem Int Ed 2021;60:24915-23.
30. Cao Y, Wang M, Wang H, Han C, Pan F, Sun J. Covalent organic framework for rechargeable batteries: mechanisms and properties of ionic conduction. Adv Energy Mater 2022;12:2200057.
31. Cao Y, Wu H, Li G, et al. Ion selective covalent organic framework enabling enhanced electrochemical performance of lithium-sulfur batteries. Nano Lett 2021;21:2997-3006.
32. Shi J, Tang W, Xiong B, Gao F, Lu Q. Molecular design and post-synthetic vulcanization on two-dimensional covalent organic framework@rGO hybrids towards high-performance sodium-ion battery cathode. Chem Eng J 2023;453:139607.
33. Wang S, Wang Q, Shao P, et al. Exfoliation of covalent organic frameworks into few-layer redox-active nanosheets as cathode materials for lithium-ion batteries. J Am Chem Soc 2017;139:4258-61.
34. Vadiyar MM, Kim J, Bae J, Nam K. Imidazole linker-induced covalent triazine framework-ZIF hybrids for confined hollow carbon super-heterostructures toward a long-life supercapacitor. Carbon Energy 2023;5:e344.
35. Sun R, Tan B. Covalent triazine frameworks (CTFs): synthesis, crystallization, and photocatalytic water splitting. Chemistry 2023;29:e202203077.
36. Liu M, Guo L, Jin S, Tan B. Covalent triazine frameworks: synthesis and applications. J Mater Chem A 2019;7:5153-72.
37. Zhang Y, Jin S. Recent advancements in the synthesis of covalent triazine frameworks for energy and environmental applications. Polymers 2018;11:31.
38. Wang K, Yang LM, Wang X, et al. Covalent triazine frameworks via a low-temperature polycondensation approach. Angew Chem Int Ed 2017;56:14149-53.
39. Liu M, Jiang K, Ding X, et al. Controlling monomer feeding rate to achieve highly crystalline covalent triazine frameworks. Adv Mater 2019;31:e1807865.
40. Evans J, Vincent CA, Bruce PG. Electrochemical measurement of transference numbers in polymer electrolytes. Polymer 1987;28:2324-8.
41. Chen Y, Mickel P, Pei H, et al. Bioinspired separator with ion-selective nanochannels for lithium metal batteries. ACS Appl Mater Interfaces 2023;15:18333-42.
42. Guo Y, Niu P, Liu Y, et al. An Autotransferable g-C3N4 Li+-modulating layer toward stable lithium anodes. Adv Mater 2019;31:e1900342.
43. Zhang R, Chen XR, Chen X, et al. Lithiophilic sites in doped graphene guide uniform lithium nucleation for dendrite-free lithium metal anodes. Angew Chem Int Ed 2017;56:7764-8.
44. Zhou T, Zhao Y, Choi JW, Coskun A. Lithium-salt mediated synthesis of a covalent triazine framework for highly stable lithium metal batteries. Angew Chem 2019;131:16951-5.
45. Bai P, Li J, Brushett FR, Bazant MZ. Transition of lithium growth mechanisms in liquid electrolytes. Energy Environ Sci 2016;9:3221-9.
46. Sand HJ. III. On the concentration at the electrodes in a solution, with special reference to the liberation of hydrogen by electrolysis of a mixture of copper sulphate and sulphuric acid. Lond Edinb Dublin Philos Mag J Sci 1901;1:45-79.
47. Kim D, Liu X, Yu B, et al. Amine-functionalized boron nitride nanosheets: a new functional additive for robust, flexible ion gel electrolyte with high lithium-ion transference number. Adv Funct Mater 2020;30:1910813.
48. Li L, Wang M, Wang J, et al. Asymmetric gel polymer electrolyte with high lithium ion conductivity for dendrite-free lithium metal batteries. J Mater Chem A 2020;8:8033-40.
49. Ghazi ZA, Sun Z, Sun C, et al. Key aspects of lithium metal anodes for lithium metal batteries. Small 2019;15:e1900687.
50. Xiao J, Li Q, Bi Y, et al. Understanding and applying coulombic efficiency in lithium metal batteries. Nat Energy 2020;5:561-8.
Cite This Article
Export citation file: BibTeX | EndNote | RIS
OAE Style
Wang Y, Sun R, Chen Y, Wang X, Yang Y, Wang X, Nie H, Zhou X, Tan B, Xie X. Highly crystalline covalent triazine frameworks modified separator for lithium metal batteries. Energy Mater 2024;4:400056. http://dx.doi.org/10.20517/energymater.2023.133
AMA Style
Wang Y, Sun R, Chen Y, Wang X, Yang Y, Wang X, Nie H, Zhou X, Tan B, Xie X. Highly crystalline covalent triazine frameworks modified separator for lithium metal batteries. Energy Materials. 2024; 4(5): 400056. http://dx.doi.org/10.20517/energymater.2023.133
Chicago/Turabian Style
Yun Wang, Ruixue Sun, Yi Chen, Xuyang Wang, Yufei Yang, Xiaoyan Wang, Hui Nie, Xingping Zhou, Bien Tan, Xiaolin Xie. 2024. "Highly crystalline covalent triazine frameworks modified separator for lithium metal batteries" Energy Materials. 4, no.5: 400056. http://dx.doi.org/10.20517/energymater.2023.133
ACS Style
Wang, Y.; Sun R.; Chen Y.; Wang X.; Yang Y.; Wang X.; Nie H.; Zhou X.; Tan B.; Xie X. Highly crystalline covalent triazine frameworks modified separator for lithium metal batteries. Energy Mater. 2024, 4, 400056. http://dx.doi.org/10.20517/energymater.2023.133
About This Article
Special Issue
Copyright
Data & Comments
Data
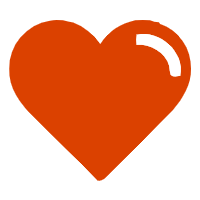
Comments
Comments must be written in English. Spam, offensive content, impersonation, and private information will not be permitted. If any comment is reported and identified as inappropriate content by OAE staff, the comment will be removed without notice. If you have any queries or need any help, please contact us at support@oaepublish.com.