Functionalized polypropylene separator coated with polyether/polyester blend for high-performance lithium metal batteries
Abstract
Commercial polyolefin separators used in lithium metal batteries (LMBs) have the disadvantages of insufficient thermal stability and poor wettability with electrolytes, which causes bad safety and battery performance.
Keywords
INTRODUCTION
Lithium metal as an anode has a high specific energy density of 3,860 mAh g-1 and a low anode potential of
Polyolefin-based microporous separators manufactured by polyethylene (PE) and polypropylene (PP) dominate commercial battery separators due to their low cost for large-scale production, excellent mechanical properties, and good stability. However, the disadvantages of sluggish lithium-ion diffusion and poor wettability with electrolytes lead to safety issues and make satisfactory battery performance hard to achieve[15-21]. Therefore, researchers have conducted numerous studies to modify polyolefin separators, with surface coating being one of the most effective and simplest methods[22]. The commonly coated polymers include poly(vinylidene fluoride) (PVDF)[23], poly(ethylene oxide) (PEO)[24], poly(methyl methacrylate) (PMMA)[25], polyimide (PI)[26], and so on. Wang et al. coated PVDF organic particles on traditional PE separators to achieve good electrolyte wettability. However, the battery capacity based on the coated separator was not high enough (122 mAh g-1 under 1C) and could not involve the long cycle performance of the battery[27]. Tian et al. fabricated a composite separator by coating organic palygorskite and methyl methacrylate (MMA) onto both sides of a polyolefin-based separator. A high lithium-ion transference number (tLi+) of 0.89 and a good discharge capacity of 164 mAh g-1 (0.1C) with only a 77% capacity retention rate (200 cycles) were obtained[28]. Although coating polymers on separators could effectively improve the battery performance, new polymers should be designed to meet the increasing demands of the capacity and long cycling stability of advanced LMBs.
Poly(ε-caprolactone) (PCL) has excellent electrochemical stability (~5 V), high dielectric constant, and weak interaction between carbonyl groups and lithium ions, which has attracted great interest in the field of electrolytes[29-31]. Li et al. reported a self-catalyzed strategy for brush-typed PCL-based polymer electrolyte with a high ionic conductivity [5.53 × 10-2 mS cm-1 at room temperature (RT)] and tLi+ (0.82)[32]. However, due to the poor compatibility of PCL and polyolefin-based microporous separators, there is little research on improving battery performance using the PCL as a constituent of the separator. Although Di Carli et al. made PAN and PCL into separators using an electrospinning procedure, the strategies and electrochemical performance, especially in capacity and cycling stability, need further improvement[33]. As a common polymer electrolyte and separator coating material, PEO not only avoids the risk of delamination between the modified layer and the separator but also adsorbs liquid electrolyte and reduces the reaction between electrolytes and lithium metal[24]. Furthermore, introducing PEO and PCL components into the electrolyte can effectively change the coordination structure of Li+ and improve the ionic conductivity and lithium-ion transference number[29]. Therefore, the polymer coating of blend PEO and PCL on the PP separator can further improve the performance of LMBs.
In this work, we propose a simple but effective strategy to blend PEO and PCL (with a mass ratio of 1:2) as the coating of commercial PP separators to provide a smooth atmosphere for ion migration and enhance the cycle stability of LMBs. The component of PEO can not only assist the transport of lithium ions[3] but also work as a binder to make it more uniform for PCL coating on the PP separator surface. The strong polar ester carbonyl group in PCL plays a key role in promoting the dissociation of lithium salts and improving the interfacial compatibility between electrodes and electrolytes[34-36]. Compared to batteries containing separators with PEO-coated and pure PP separators, the capacity and cycling stability of batteries assembled with PEO/PCL blend-coated PP separator (PP-blended PEO60w/PCL5w) are significantly improved. The Li/LiFePO4 (LFP) cell with the functionalized separator shows a high specific discharge capacity of 146 mAh g-1 under 1C and 103 mAh g-1 under 5C at RT, showing the potential for large-scale production of separators via the simple and effective method.
RESULTS AND DISCUSSION
Structure characterization of separators
A novel functionalized separator coating by blending PEO60w and PCL5w for PP-based separators was prepared using the blade coating method [Figure 1]. Besides, the coating with PEO60w or PCL5w for PP separators was prepared similarly to explore the influencing factors. Fourier-transform infrared spectra
Figure 1. Schematic illustration of functionalized separator coated with polymer blend for the application in LMBs.
Figure 2. Characterization of the separators: (A) FTIR spectra of PP, PP-PEO60w, PP-PCL5w and PP-blended PEO60w/PCL5w separators; (B) Cross-sectional SEM images and the corresponding EDS element mapping of C and O of the PP-blended PEO60w/PCL5w; Top-view SEM images of PP separator (C) and PP-blended PEO60w/PCL5w separator with the coated surface (D) and uncoated surface (E).
Scanning electron microscopy (SEM) was used to observe more visible characterizations of separators. As shown in Figure 2B, the average thickness of blended polymer coating on the top of the PP separator is about 1.3 µm (as calculated from the SEM cross-sectional imaging). The element mapping [Figure 2B] further demonstrates the coating distributed on the surface without clogging the pores of the PP separator. The top-view SEM images of the PP separator and coated separators are shown in Figure 2C-E, indicating that a uniform polymer coating was prepared on the top of the PP separator, and its micrometer porous morphology is retained on the uncoated side.
The result of surface area and pore size distributions in the separators was verified by Brunauer-Emmett-Teller (BET) analyses [Supplementary Figure 3]. Due to the stretching process during the PP separator production, it does not contain homogenously distributed slit pores, and the PP and PP-Blended
Physical property characterization of separators
In advanced LMBs, the thermal stability of the separator is one of the evaluation criteria for safety. As shown in Figure 3A, the decomposition temperature of PP separators is around 400 °C. Although the decomposition temperature of coated separators is slightly decreased to 377 °C because of the lower decomposition temperature of polymer coatings[39,40], they are still enough for battery application. As shown in Figure 3B, the PP-PEO60w (EO:Li+ = 8:1) and PP-blended PEO60w/PCL5w separators show improved thermal stability compared to the commercial PP separator. The PP separator shows a slight irreversible thermal shrinkage of about 5% at 120 °C, while no significant size change is found on the coated separators. Besides, the PP-blended PEO60w/PCL5w separator shows lower thermal shrinkage than a PP separator at higher temperatures [Supplementary Figure 4], indicating the coating can slightly improve the dimensional stability of the separator. The mechanical properties of different separators on drawing directions were also tested. As shown in Supplementary Figure 5, the PP-based separator has a maximum tensile strength of about 137.7 MPa, while the flexible polymer coatings on the PP separators do not significantly reduce their mechanical properties.
Figure 3. Physical and chemical properties of separators: (A) Thermal gravimetric analysis (TGA) curves of PP, PP-PEO60w
Electrolyte wettability of battery separators is crucial for efficient ion conduction in polyolefin separators, and good wettability helps decrease the internal ionic resistance and shorten electrolyte penetration time during the cell assembly[41]. The electrolyte wettability was evaluated using contact angle measurements of a liquid electrolyte (LiPF6 in a carbonate-based electrolyte). As shown in Figure 3C, owing to the hydrophobic nature and low surface energies of the PP separator [Supplementary Figure 6A and B], the PP separator shows a large contact angle of 56° with liquid electrolyte, indicating the poor wettability between the PP separator and electrolyte. Thanks to the enhanced interaction with electrolyte by the polar ester carbonyl in PCL and EO chain in PEO, the contact angle of the PP-blended PEO60w/PCL5w separator reduces to 43° [Figure 3D]. In addition, the PEO and PCL coatings also have promoted contact angles (around 45°) between the coated separators and the electrolyte [Supplementary Figure 6C-E]. Because separators have varying wettability for different electrolytes[42], we further compare the wettability of the separators with the LP-07 electrolyte, and the results are shown in Supplementary Figure 7. The PP-Blend PEO60W/PCL5W separator is well infiltrated by LP-07 electrolyte; meanwhile, the PP separator remains un-infiltrated after
Electrochemical performance
The separators were packaged into cells to investigate the electrochemical properties. The ionic conductivity of cells with PP separators and various coated separators was measured. As shown in Figure 4A, the PP-PEO60w (EO:Li+) and PP-blended PEO60w/PCL5w separators have higher ionic conductivity than PP separators as 0.66 and
Figure 4. Electrochemical properties of separators: (A) Temperature dependence of ionic conductivity of PP, PP-PEO60w (EO:Li+ = 8:1), PP-PCL5w and PP-blended PEO60w/PCL5w separators; (B) Chronoamperometry profile of Li/PP-blended PEO60w/PCL5w separator-LiPF6/Li symmetric battery under a polarization potential of 10 mV and the EIS before and after the polarization (insert); (C) EIS curves of PP and PP-blended PEO60w/PCL5w separators; (D) Electrochemical stability windows of PP, PP-PEO60w (EO:Li+ = 8:1) and PEO60w/PCL5w separators.
As shown in Figure 4B and Supplementary Figure 9, the tLi+ of PP-blended PEO60w/PCL5w is significantly enhanced relative to pure PP and PP-PEO60w separators thanks to the PCL component. The tLi+ of PP,
Figure 4C shows the electrochemical impedance spectra (EIS) of the lithium symmetric cell of PP-blended PEO60w/PCL5w and PP separators. It is clear that the interfacial resistance of the PP-blended PEO60w/PCL5w separator (about 220 Ω) is less than the PP separator (about 430 Ω), indicating a better interface between electrolyte and electrode provided by the blended PEO60w/PCL5w coating. Therefore, coating PEO60w/PCL5w on PP separators is beneficial for reducing interfacial resistance. Lower interfacial resistance positively influences electrochemical properties, especially resulting in a higher tLi+[43]. Also, the functionalized separator possesses enough electrochemical stability (4.4 V) for LMBs [Figure 4D].
To sum up, as shown in Figure 5, because the carbonyl and ether oxygen of coatings have generated interaction with solvent molecules[9] and coordinated with lithium ions, promoting the destruction of the solvation sheath of Li+ and increasing the mobility of Li+, the wettability and Li+ conductivity of coated separators have been optimized. The PP-blended PEO60w/PCL5w separator has high ionic conductivity, high
Battery performance
To investigate the interfacial performance between electrolyte and electrodes, the Li//Li symmetric cells with PP-blended PEO60w/PCL5w and PP separators were assembled and measured through the lithium plating-stripping measurements. Figure 6A shows the long-term performance of lithium symmetric cells with a current density of 0.5 mA cm-2 and a cycling capacity of 0.5 mAh cm-2 for the two kinds of separators. The overpotential of Li//Li symmetric cells with PP separators is stabilized at about 70 mV and short-circuited after 170 h due to the growth of lithium dendrites. On the contrary, the lithium symmetric cell with a PP-blended PEO60w/PCL5w separator has a lower initial overpotential of 60 mV and maintains stable cycling for 200 h without a short circuit. Besides, the top-view images of lithium anode from Li-Li symmetrical battery assembled with PP and PP-Blended PEO60w/PCL5w separators were observed after lithium plating/striping for 100 h at 0.5 mA cm-2 by SEM [Supplementary Figure 10]. It is obvious that the lithium anode assembled with a PP separator shows a large number of mossy lithium dendrites; meanwhile, the lithium anode assembled with a PP-Blended PEO60w/PCL5w separator exhibits a batter lithium metal surface. It indicates that the PP-blended PEO60w/PCL5w separator has better compatibility and interfacial stability with lithium anode thanks to the high tLi+, which help form a stable interface and suppress the growth of Li dendrites in LMBs[44].
Figure 6. Performance of battery with different separators: (A) Polarization potential voltage-time curves of the Li//Li symmetric cells with PP-blended PEO60w/PCL5w separator and PP separator; (B) C-rate capability of the cells with PP-PEO60w and PP-PEO60w
To explore the specific capacity and cycling stability of separators, Li/LFP cells were assembled mentioned above and tested. Firstly, the impact of lithium salts on battery performance in PP-PEO60w separators is shown in Figure 6B. Compared to PP-PEO60w separators without lithium salt, the Li//LFP cell with
Figure 6D shows the rate capability of Li//LFP cells with distinct separators, in which the Li//LFP cell with a PP-blended PEO60w/PCL5w separator delivers excellent performance, and the detailed specific capacities are 140.0, 128.8, 119.8, 112.1, and 103.6 mAh g-1, at 1C, 2C, 3C, 4C, and 5C, respectively, which have a great improvement compared with the commercial PP separator. The long cycling properties of Li//LFP cells were explored at RT, as shown in Figure 6E. A PP separator has a poor ability to tolerate Li dendrite growth[47], and the lack of pore connection may cause an uneven Li+ concentration gradient across the separator, accelerating local lithium dendrite growth. The Li//LFP cell with a PP separator owns the lowest initial discharge specific capacity of 124 mAh g-1 and rapidly degrades after 450 times cycling at 1C. With the coating of PEO60w (EO:Li+ = 8:1), the initial discharge specific capacity of Li//LFP cells increases to
In order to further enhance the energy density, high-voltage cathodes such as Ni-rich LiNi0.8Co0.1Mn0.1O2 (NCM811)[52] were also tested at a current density of 0.5C from 2.5 to 4.2 V at RT. As shown in
CONCLUSIONS
In summary, we designed a novel separator coating by blending PEO60w and PCL5w (with a mass ratio of 1:2) for the commercial PP separator. Compared to the PP separator, functionalized separators obtained in this study have excellent electrochemical properties such as great ionic conductivity (0.63 mS cm-1, 30 °C), high
DECLARATIONS
Authors’ contributions
Methodology, investigation, and writing manuscript: Ye W
Methodology, investigation, and writing manuscript: Fan Z
Project administration and funding acquisition: Zhou X
Conceptualization and supervision: Xue Z
Availability of data and materials
The data supporting our work can be found in the Supplementary Materials.
Financial support and sponsorship
The authors gratefully acknowledge the National Natural Science Foundation of China (Grant No. 51973073), the Innovation and Talent Recruitment Base of New Energy Chemistry and Device (B21003), and the Analysis and Testing Center of HUST for their assistance in analysis and testing and support of this work.
Conflicts of interest
All authors declared that there are no conflicts of interest.
Ethical approval and consent to participate
Not applicable.
Consent for publication
Not applicable.
Copyright
© The Author(s) 2024.
Supplementary Materials
REFERENCES
1. Yan M, Wang CY, Fan M, et al. In situ derived mixed ion/electron conducting layer on top of a functional separator for high-performance, dendrite-free rechargeable lithium-metal batteries. Adv Funct Mater 2023;34:2301638.
2. Seo J, Im J, Kim M, Song D, Yoon S, Cho KY. Recent progress of advanced functional separators in lithium metal batteries. Small 2024:e2312132.
3. Xue Z, He D, Xie X. Poly(ethylene oxide)-based electrolytes for lithium-ion batteries. J Mater Chem A 2015;3:19218-53.
4. Wang J, Li S, Zhao Q, Song C, Xue Z. Structure code for advanced polymer electrolyte in lithium-ion batteries. Adv Funct Mater 2021;31:2008208.
5. Zhang Y, Wang J, Xue Z. Electrode protection and electrolyte optimization via surface modification strategy for high-performance lithium batteries. Adv Funct Mater 2024;34:2311925.
6. Wu F, Maier J, Yu Y. Guidelines and trends for next-generation rechargeable lithium and lithium-ion batteries. Chem Soc Rev 2020;49:1569-614.
7. Lopez J, Mackanic DG, Cui Y, Bao Z. Designing polymers for advanced battery chemistries. Nat Rev Mater 2019;4:312-30.
8. Terella A, De Giorgio F, Rahmanipour M, et al. Functional separators for the batteries of the future. J Power Sources 2020;449:227556.
9. Li D, Shi D, Feng K, Li X, Zhang H. Poly (ether ether ketone) (PEEK) porous membranes with super high thermal stability and high rate capability for lithium-ion batteries. J Membr Sci 2017;530:125-31.
10. Francis CFJ, Kyratzis IL, Best AS. Lithium-ion battery separators for ionic-liquid electrolytes: a review. Adv Mater 2020;32:e1904205.
11. Yu J, Dong N, Liu B, Tian G, Qi S, Wu D. A newly-developed heat-resistance polyimide microsphere coating to enhance the thermal stability of commercial polyolefin separators for advanced lithium-ion battery. Chem Eng J 2022;442:136314.
12. Liu H, Banerjee A, Ziv B, et al. Elucidating the Li-ion battery performance benefits enabled by multifunctional separators. ACS Appl Energy Mater 2018;1:1878-82.
13. Song YZ, Yuan JJ, Yin X, et al. Effect of polyphenol-polyamine treated polyethylene separator on the ionic conduction and interface properties for lithium-metal anode batteries. J Electroanal Chem 2018;816:68-74.
14. Song YZ, Zhang Y, Yuan JJ, et al. Fast assemble of polyphenol derived coatings on polypropylene separator for high performance lithium-ion batteries. J Electroanal Chem 2018;808:252-8.
15. Wang H, Pan L, Wu C, Gao D, Chen S, Li L. Pyrogallic acid coated polypropylene membranes as separators for lithium-ion batteries. J Mater Chem A 2015;3:20535-40.
16. Zhang SS. A review on the separators of liquid electrolyte Li-ion batteries. J Power Sources 2007;164:351-64.
17. Fang LF, Shi JL, Zhu BK, Zhu LP. Facile introduction of polyether chains onto polypropylene separators and its application in lithium ion batteries. J Membr Sci 2013;448:143-50.
18. Cao C, Tan L, Liu W, Ma J, Li L. Polydopamine coated electrospun poly(vinyldiene fluoride) nanofibrous membrane as separator for lithium-ion batteries. J Power Sources 2014;248:224-9.
19. Jiang F, Nie Y, Yin L, Feng Y, Yu Q, Zhong C. Core-shell-structured nanofibrous membrane as advanced separator for lithium-ion batteries. J Membr Sci 2016;510:1-9.
20. Lee JY, Shin SH, Moon SH. Flame retardant coated polyolefin separators for the safety of lithium ion batteries. Korean J Chem Eng 2016;33:285-9.
21. Lagadec MF, Zahn R, Wood V. Characterization and performance evaluation of lithium-ion battery separators. Nat Energy 2019;4:16-25.
22. Sohn JY, Im JS, Shin J, Nho YC. PVDF-HFP/PMMA-coated PE separator for lithium ion battery. J Solid State Electrochem 2012;16:551-6.
23. Kim G, Noh JH, Lee H, Shin J, Lee D. Roll-to-roll gravure coating of PVDF on a battery separator for the enhancement of thermal stability. Polymers 2023;15:4108.
24. Chen Y, Wang K, Zhang L, et al. Oriented carbon fiber/PEO functional modified polyethylene separator for high-performance lithium metal batteries. Mater Lett 2023;332:133511.
25. Jeong YB, Kim DW. The role of an adhesive gel-forming polymer coated on separator for rechargeable lithium metal polymer cells. Solid State Ion 2005;176:47-51.
26. Wang Z, Li X, Dong N, et al. Novel ZrO2@Polyimde nano-microspheres-coated polyethylene separators for high energy density and high safety Li-ion battery. Mater Today Energy 2022;30:101155.
27. Wang Y, Yin C, Song Z, et al. Application of PVDF organic particles coating on polyethylene separator for lithium ion batteries. Materials 2019;12:3125.
28. Tian L, Xiong L, Huang C, Wang M, Zhang H, Chen X. Gel hybrid copolymer of organic palygorskite and methyl methacrylate electrolyte coated onto Celgard 2325 applied in lithium ion batteries. J Appl Polym Sci 2019;136:47970.
29. Guo K, Wang J, Shi Z, Wang Y, Xie X, Xue Z. One-step in situ polymerization: a facile design strategy for block copolymer electrolytes. Angew Chem Int Ed 2023;62:e202213606.
30. Zuo C, Chen G, Zhang Y, et al. Poly(ε-caprolactone)-block-poly(ethylene glycol)-block-poly(ε-caprolactone)-based hybrid polymer electrolyte for lithium metal batteries. J Membr Sci 2020;607:118132.
31. Eriksson T, Mindemark J, Yue M, Brandell D. Effects of nanoparticle addition to poly(ε-caprolactone) electrolytes: crystallinity, conductivity and ambient temperature battery cycling. Electrochim Acta 2019;300:489-96.
32. Li S, Guo K, Chen G, et al. A self-catalyzed strategy towards facile fabrication of bottlebrush polyester-based solid polymer electrolytes. Energy Stor Mater 2022;46:461-71.
33. Di Carli M, Aurora A, Rinaldi A, Fiaschini N, Prosini PP. Preparation of electrospun membranes and their use as separators in lithium batteries. Batteries 2023;9:201.
34. Li Y, Zhu K, Bu H, et al. Miktoarm PEG-PCL star copolymer (AB6) blend composite solid electrolyte for all-solid-state lithium metal battery. Macromolecules 2023;56:7921-30.
35. Rosenwinkel MP, Andersson R, Mindemark J, Schönhoff M. Coordination effects in polymer electrolytes: fast Li+ transport by weak ion binding. J Phys Chem C 2020;124:23588-96.
36. Lee TK, Andersson R, Dzulkurnain NA, Hernández G, Mindemark J, Brandell D. Polyester-ZrO2 nanocomposite electrolytes with high Li transference numbers for ambient temperature all-solid-state lithium batteries. Batteries Supercaps 2021;4:653-62.
37. Sun M, Zeng Z, Peng L, et al. Ultrathin polymer electrolyte film prepared by in situ polymerization for lithium metal batteries. Mater Today Energy 2021;21:100785.
38. Mu X, Zhou X, Wang W, et al. Design of compressible flame retardant grafted porous organic polymer based separator with high fire safety and good electrochemical properties. Chem Eng J 2021;405:126946.
39. Nainggolan G, Gea S, Marpongahtun, Harahap M, Dellyansyah, Situmorang SA. Promoting electrospun lignin/PEO nanofiber for high-performance CO filtration. J Nat Fibers 2023;20:2160402.
40. Bezerra GSN, De Lima GG, Colbert DM, Halligan E, Geever J, Geever L. Micro-injection moulding of PEO/PCL blend-based matrices for extended oral delivery of fenbendazole. Pharmaceutics 2023;15:900.
41. Huang X. Separator technologies for lithium-ion batteries. J Solid State Electrochem 2011;15:649-62.
42. Huang X, He R, Li M, Chee MOL, Dong P, Lu J. Functionalized separator for next-generation batteries. Mater Today 2020;41:143-55.
43. Zhang Y, Yuan JJ, Song YZ, et al. Tannic acid/polyethyleneimine-decorated polypropylene separators for Li-Ion batteries and the role of the interfaces between separator and electrolyte. Electrochim Acta 2018;275:25-31.
44. Fan P, Liu H, Marosz V, et al. High performance composite polymer electrolytes for lithium-ion batteries. Adv Funct Mater 2021;31:2101380.
45. Andersson EKW, Sångeland C, Berggren E, et al. Early-stage decomposition of solid polymer electrolytes in Li-metal batteries. J Mater Chem A 2021;9:22462-71.
46. Nitou MVM, Pang Y, Wan Z, et al. LiFePO4 as a dual-functional coating for separators in lithium-ion batteries: a new strategy for improving capacity and safety. J Energy Chem 2023;86:490-8.
47. An H, Roh Y, Jo Y, et al. Separator dependency on cycling stability of lithium metal batteries under practical conditions. Energy Environ Mater 2023;6:e12397.
48. Pei D, Li Y, Huang S, et al. Polycaprolactone-poly(vinylidene fluoride) blended composite polymer electrolyte with enhanced high power performance and interfacial stability for all-solid-state Li metal batteries. Chem Eng J 2023;461:141899.
49. Diederichsen KM, Mcshane EJ, Mccloskey BD. Promising routes to a high Li+ transference number electrolyte for lithium ion batteries. ACS Energy Lett 2017;2:2563-75.
50. Li Y, Wang F, Huang B, et al. A high power density solid electrolyte based on polycaprolactone for high-performance all-solid-state flexible lithium batteries. Electrochim Acta 2022;424:140624.
51. Liu J, Wang S, Qie Y, Sun Q. Identifying lithium fluorides for promising solid-state electrolyte and coating material of high-voltage cathode. Mater Today Energy 2021;21:100719.
Cite This Article
Export citation file: BibTeX | EndNote | RIS
OAE Style
Ye W, Fan Z, Zhou X, Xue Z. Functionalized polypropylene separator coated with polyether/polyester blend for high-performance lithium metal batteries. Energy Mater 2024;4:400049. http://dx.doi.org/10.20517/energymater.2023.129
AMA Style
Ye W, Fan Z, Zhou X, Xue Z. Functionalized polypropylene separator coated with polyether/polyester blend for high-performance lithium metal batteries. Energy Materials. 2024; 4(4): 400049. http://dx.doi.org/10.20517/energymater.2023.129
Chicago/Turabian Style
Weixin Ye, Zixin Fan, Xingping Zhou, Zhigang Xue. 2024. "Functionalized polypropylene separator coated with polyether/polyester blend for high-performance lithium metal batteries" Energy Materials. 4, no.4: 400049. http://dx.doi.org/10.20517/energymater.2023.129
ACS Style
Ye, W.; Fan Z.; Zhou X.; Xue Z. Functionalized polypropylene separator coated with polyether/polyester blend for high-performance lithium metal batteries. Energy Mater. 2024, 4, 400049. http://dx.doi.org/10.20517/energymater.2023.129
About This Article
Special Issue
Copyright
Data & Comments
Data
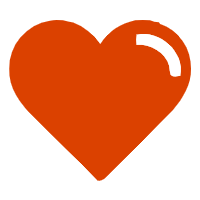
Comments
Comments must be written in English. Spam, offensive content, impersonation, and private information will not be permitted. If any comment is reported and identified as inappropriate content by OAE staff, the comment will be removed without notice. If you have any queries or need any help, please contact us at support@oaepublish.com.