Influences of deposition conditions on atomic layer deposition films for enhanced performance in perovskite solar cells
Abstract
Atomic layer deposition (ALD) is a key technology for fabricating functional layers in perovskite solar cells, as it can deposit pinhole-free films with atomic-level thickness and tunable composition on high-aspect-ratio surfaces. Various deposition conditions have significant effects on the growth, physical, and chemical properties of ALD films, which, in turn, critically influences the performance of associated devices. Here, we review the reaction mechanisms underlying ALD and summarize how variables, such as precursors, deposition temperatures, and substrates, impinge upon the quality of ALD films and the related devices. We emphasize the role of substrate in determining the nucleation and growth behavior of ALD films, which has been overlooked in previous reviews. Finally, we highlight the potential application of ALD in efficient perovskite solar cells in terms of carrier transport, encapsulated, and buffer layers, especially for tandem cells.
Keywords
INTRODUCTION
In recent years, atomic layer deposition (ALD)[1] has aroused much attention in the semiconductor fields such as corrosion[2], catalysis[3] and solar cells[4-8]. As for solar cells, perovskite solar cells (PSCs) have been widely investigated owing to their advantages such as tunable bandgap[9], high absorption coefficient[10] and versatile fabrication methods[11]. For the fabrication of carrier transport, sputtering buffer, and encapsulated layers of PSCs, ALD[12] is a unique technology for growth conformal film growth based on self-limiting surface reactions, as compared with other methods such as spin-coating, thermal evaporation, and magnetron sputtering[13]. As shown in Table 1, compared to other film deposition techniques such as physical (PVD)[14] and chemical vapor deposition (CVD)[6,15], ALD provides the distinctive capability to form monolayer films. This facilitates precise control over film thickness and composition, ensuring exceptional uniformity and conformality at the angstrom level. As illustrated in Figure 1, an ideal ALD process consists of the following four steps: Step 1: The precursor of the first reactant A is pulsed into the reaction chamber and adsorbed on the substrate surface; Step 2: After the surface adsorption is saturated, the surplus precursor and by-products are purged out of the reaction chamber with inert gas; Step 3: The precursor of the second reactant B is pulsed into the reaction chamber and undergoes reaction with precursor A on the surface to grow the AxBy film; and Step 4: After the reaction is complete, the surplus precursor and by-products are purged out of the reaction chamber with inert gas. Based on the above steps, a conformal, pinhole-free film is cyclically deposited layer-by-layer.
Comparison of PVD, CVD, and ALD
Film deposition techniques | Deposition principle | Deposition pattern | Uniformity | Conformality | Expansibility | Degree of vacuum | Film thickness |
PVD | Physical vapor deposition | Nucleation growth | High number of pinholes and particles exist | Low and only for flat substrate | Medium | High requirement for vacuum degree and sensitive to the change of vacuum degree | Nanometer level |
CVD | Gas-phase chemical reaction | Nucleation growth | Low number of pinholes and particles exist | Medium | Low | Medium | Nanometer level |
ALD | Surface saturated reaction | Layer-by-layer growth | Low number of pinholes and no particles | High | High | Low | Angstrom level |
The physical and chemical properties of ALD films are strongly influenced by three main factors: precursors, deposition temperatures, and substrates. Metal and oxygen sources are commonly used as precursors to fabricate metal oxide films in PSCs[16]. The reaction precursors should effectively react with the surface groups of the material[17-20]. Secondly, they must have sufficient chemical stability and cannot decompose due to physical factors (temperature, pressure, etc.) or corrode the underlying material. Deposition temperature is another key factor influencing the quality of ALD films and the performance of devices. Too high deposition temperatures may lead to decomposition of perovskite and deterioration of device performance[21]. As for substrates, the sufficient adsorption of the precursor molecules on the high-aspect-ratio surface is the prerequisite for achieving an ideal ALD film[12], which we also demonstrated in our previous research on the application of ALD for PSCs and tandem solar cells[22]. Therefore, the surface properties of the substrate significantly influence the film quality of ALD, which cannot be ignored.
Previous review articles have examined the benefits of ALD in the realm of PSCs. Brinkmann et al. have investigated functional layers prepared by ALD for PSCs[16]. Very recently, Zhang et al. have discussed ALD-prepared buffer and encapsulation layers for enhancing the stability of PSCs[23]. To fabricate high-quality ALD films in PSCs and their related tandem solar cells, a comprehensive review of the selection of reaction precursors, deposition temperatures, and substrates is necessary. In this mini review, we explore the ALD reaction mechanisms and the effects of different reaction conditions, such as precursors and temperatures, especially the deposition substrates, on the film properties. Additional studies on ALD substrates in the semiconductor field are also summarized, which may have potential impacts and applications on the PSCs.
EFFECT OF ALD REACTION CONDITIONS ON FILM PROPERTIES
Precursor
The underlying mechanism of precursor chemistry in ALD is predicated on the adsorption and subsequent reaction of precursor molecules onto the substrate surface[20]. So, ALD requires using highly reactive precursor molecules to interact selectively with the substrate surface. The chemical structure of the precursors also affects the surface chemistry and the growth rate of the film. As for PSCs, various metal oxides, such as ZnO, TiOx, Al2O3, and SnOx, are prepared by ALD as different functional layers, which respectively correspond to the metal precursors: diethyl zinc (DEZn)[24], titaniumtetrachloride (TiCl4)[25], tetrakis(dimethylamido)titanium (TDMA-Ti)[26], Titanium isopropoxide (TTIP)[27], tris(dimethylamido)methylcyclopentadienyl titanium (Ti(CpMe)(NMe2)3)[28], trimethylaluminium (TMA)[29], and tetrakis(dimethylamido)tin (TDMA-Sn)[30,31]. The common oxygen precursors are H2O,
Figure 2. (A) Image showing perovskite films subjected to partial ALD treatments employing H2O, DEZn, or TDMASn or subjected to complete ALD processes for either ZnO or SnOx. Reprinted with permission from ref.[34]. Copyright 2017 American Chemical Society. (B) XPS pattern of O 1s spectra for three distinct perovskite samples: pristine, post thermal ALD Al2O3, and ZnO treatments. (C) Normalized areas of the MAPbI3 {110} peak and PbI2 {001} peak. Reprinted with permission from ref.[35]. Copyright 2017 Royal Society of Chemistry.
As for oxygen precursors, it is worth mentioning that the exposure levels to a single pulse of H2O are very low in the vacuum-based ALD process[35]. Thus, water is usually chosen as the oxygen source in the ALD of metal oxides. The influence of oxygen sources has also been investigated by several studies. Hu et al. reported a comparative study of SnOx films and their devices prepared by ALD using H2O, O3 and plasma precursors as precursors[32]. It is found that the H2O-based devices had the largest electron extraction barriers in the conduction band (CB) between PbI2 and MAPbI3, resulting in the poor ability of electron extraction. Additionally, the considerable gap states were found in H2O-SnOx, which were not found in the O3- and plasma-based SnOx layers. These gap states caused parasitic recombination and poor electron selectivity at the interface, resulting in low efficiency and large hysteretic for the devices based on H2O-
Figure 3. (A) Normalized areas of the MAPbI3 {110} peak and PbI2 {001} peak. Reprinted with permission from ref.[35]. Copyright 2017 Royal Society of Chemistry. (B) The optical absorption spectra of SnOx layers synthesized at various temperatures using either O3 or
Properties of ALD SnOx films using O3 or H2O as oxidants. Reprinted with permission from ref.[37]. Copyright 2015 Wiley
ALD-film | TD [°C] | WVTR average | Density ρ [g cm-3] | σ [S cm-1] | n [cm-3] | μ [cm2 Vs-1] | Carbon content [%] | Nitrogen content [%] | [O]/[Sn] | Eg [eV] | Tav [%] |
SnOx (O3) | 100 | 2.2 × 10-4 | 3.8 | 3 × 10-5 | - | - | 12.8 | 6.7 | 2.6 | 4.23 | 89 |
150 | 8.8 × 10-6 | 4.8 | 2 | 2 × 1018 | 5 | 7.3 | 5.4 | 2.3 | 3.88 | 84 | |
200 | 3.6 × 10-6 | 7.0 | 3 × 102 | 2 × 1020 | 10 | 1.8 | 1.4 | 2.1 | 3.67 | 80 | |
SnOx (H2O) | 100 | 7 × 10-5 | 5.4 | 6 × 10-4 | 1 × 1015 | 4 | 3.6 | 2.1 | 2.2 | 3.80 | 78 |
150 | 3 × 10-5 | 5.3 | 3 × 10-3 | 1 × 1016 | 2 | 3.6 | 1.4 | 2.0 | 3.19 | 67 | |
200 | 3.1 × 10-6 | 5.7 | 6 × 10-5 | - | - | 1.9 | 0.3 | 1.8 | 3.21 | 69 |
In summary, it is necessary to fully understand the compatibility between ALD precursors and the reactant substrate to keep a substrate from decomposition or degradation.
Deposition temperature
The deposition temperature is a critical factor in the growth of ALD films, significantly affecting the reaction kinetics and surface chemistry of the precursor molecules[20]. Notably, the growth rate of ALD films, quantified by the growth per cycle (GPC), is significantly influenced by temperature. It remains consistent within a specific range of deposition temperatures, ensuring adequate thermal energy for the chemical reactions involved in the ALD process. Beyond this range, it increases due to the disruption in the self-limitation caused by the thermal degradation of the metal precursor[40]. However, a contrary phenomenon is occasionally observed, where the growth rate decreases with the increasing growth temperature, possibly owing to insufficient precursor reaction or the condensation of the precursors[41]. Therefore, optimal temperatures are necessary to promote the chemisorption reactions and achieve desirable growth rates. As per previous reports, ALD can occur in different temperature ranges in a limited amount of time. In typical thermal ALD processes for metal oxides, temperatures ranging from 100 to
In summary, the deposition temperature significantly influences the optical and electrical properties of the films. For example, the atoms of amorphous materials form electronic states at the edge of the energy band, which replace the electronic states at the tail of the energy band, leading to higher optical absorption and lower optical band gap[48,51].
THE REACTION SUBSTRATE OF ALD
The substrate type is integral to the deposition process, as it dictates the adsorption and subsequent reactions of precursor molecules[20]. The nature of the substrate can influence the nucleation and growth of the film and its properties, such as composition, crystallinity, and morphology. Variations in the surface structure and chemical makeup of substrates can lead to differential adsorption and reaction behaviors of the precursors, which, in turn, affect the growth rate and the ultimate properties of the film. The ALD procedure relies on self-terminating surface reactions, which are closely linked to the surface functionalities on the deposition substrates. ALD substrates can be classified into two major categories[22,52]: (1) unreactive substrates lacking nucleation sites for deposition; and (2) reactive substrates with abundant reactive sites. Puurunen et al. proposed that the ALD process transitioned into island growth when the substrate was unresponsive to the ALD reactant, a phenomenon also known as substrate-inhibited growth[52]. Compared with island growth, layer-by-layer growth is necessary to shape an extremely pinhole-free, conformal, and smooth surface that improves PSC performances[22,52]. The deposition mode of ALD is nonstatic. For instance, Stranski-Krastanov growth illustrates a scenario where ALD initially proceeds with layer-by-layer growth but transitions to island growth due to stress effects within the film[53,54]. According to the GPC, the growth mode can be further classified into three categories[18,52]: (1) Substrate-inhibited growth, where the GPC is primitively low (island growth) and then reaches a linear growth mode; (2) Linear growth, where the GPC is constant throughout the process of ALD; and (3) Substrate-enhanced growth, wherein the GPC exhibits elevated levels initially before transitioning into linear growth. The last two cases correspond to layer-by-layer growth mode[18].
Brinkmann et al. used a bistratal AZO/SnOx electron transportation layer (ETL) to create excellent resilience against moisture and heat in PSCs. They discovered that the stability of the AZO/SnOx devices was superior to that of the devices with SnOx deposited directly on the surface of [6,6′]-phenyl-C61-butyric acid methyl ester (PCBM), which was attributed to the nonideal ALD growth of SnOx directly on the surface of the unreactive PCBM layer[55]. Furthermore, Yu et al. discovered that ZnO could not nucleate on the PCBM surface. Subsequently, they utilized TMA, a potent Lewis acid, to react with the C=O groups present in PCBM. The Al2O3 could provide nucleation sites for the growth of ZnO[56]. Gong et al. used
Figure 4. (A) Sn content (expressed as atomic percentage, At%) in relation to the number of SnOx cycles. (B) A diagram of different deposition modes. (C) XPS spectra. (D) FTIR spectra. (E-H) AFM images. (I) Diagram of two deposition modes on PCBM and AZO substrates. Reprinted with permission from ref.[22]. Copyright 2023 Wiley.
Polyethyleneimine ethoxylated (PEIE) is an ideal material for ALD, which has a rich density of hydroxyl groups. ALD precursors can penetrate into polymer or small-molecule substrates, leading to sub-surface formation[60]. Instead of a chemically inert C60 surface, Palmstrom et al. used PEIE as a nucleation layer for recombination layers prepared by ALD in all-perovskite tandem cells[60]. Furthermore, metal oxides, including TiO2, Al2O3, and SnOx, were respectively deposited on C60 and PEIE substrates. The former ALD layers degraded significantly in solvents [water and dimethylformamide (DMF)], whereas the latter ALD films remained stable in solvents [Figure 5A]. The solvents-resistance property was enhanced by the more impermeable ALD film grown on the PEIE layer, which provided both hydroxyl and amine functional groups. These groups were suitable for nucleating and reacting with the precursors[60]. Besides, Li et al. introduced PEIE to facilitate the nucleation and crystal growth of perovskite films and provide surface reactive sites for ALD ZnO[61]. Raiford et al. also utilized PEIE to functionalize the surface of C60 for the subsequent deposition of ALD SnOx and VOx films, which served as barrier layers to improve the stability of PSCs[62]. It is seen that the nucleation of ALD SnOx formed a more continuous and denser barrier layer after using PEIE, which exhibited excellent water vapor barrier performance and protected the perovskite film from degradation under high temperature (200 °C) and humidity conditions, as shown in Figure 5B. The unpackaged device with a Ag electrode still maintained 94% of the initial efficiency after 670 h of thermal aging at 85 °C, whereas the efficiency of similar devices without PEIE dropped to 0 at 670 h. In addition, PEIE-based devices also showed better light stability[62]. Indeed, the substrate plays a significant role in determining the growth behavior of ALD films. Therefore, the substrate modification engineering is crucial for improving the quality of ALD films and the performance of PSCs. Table 3 summarizes the properties of ALD films prepared on different substrates and the stability performance of the corresponding PSCs. The modification of the substrate can form denser and smoother ALD thin films, which greatly improves the stability of the PSCs.
Figure 5. (A) Images of perovskite samples: before and after exposure to DMF for 60 s. Reprinted with permission from ref.[60]. Copyright 2019 Elsevier. (B) Time-lapse images of water-resistance test. Reprinted with permission from ref.[62]. Copyright 2019 Wiley. (C) AFM images of ALD ZnO films indicated the island-like growth on Si substrate and the layer-by-layer growth on GaN. Reprinted with permission from ref.[64]. Copyright 2012 American Chemical Society.
The properties of ALD films prepared on different substrates and the stability of the corresponding PSCs
ALD thin film | Substrate | Quality of ALD thin film | Storage condition | Stability of devices | Ref. |
SnOx | PCBM | Roughness increased from 0.226 to 0.830 nm after 50 cycles of SnOx deposition | Ambient air (at 25 °C, 30%RH) for 75 h; N2 atmosphere (at 25 °C) for | Normalized PCE decreased to 0.77; Normalized PCE decreased to 0.73; Normalized PCE decreased to 0.81; Normalized PCE decreased to 0.80 | [22] |
AZO | Roughness decreased from 5.780 to 5.320 nm after 50 cycles of SnOx deposition | Ambient air (at 25 °C, 30%RH) for 2,300 h; N2 atmosphere (at 25 °C) for 5,100 h; Heated at 85 °C in N2 atmosphere for 1,580 h; Operated at ambient under 1 sun illumination for 1,000 h | Normalized PCE decreased to 0.84; Normalized PCE decreased to 0.99; Normalized PCE decreased to 0.81; Normalized PCE decreased to 0.84 | ||
SnOx | PCBM | Nonideal growth | Ambient air (at 22 °C, 60%RH) for 150 h | VOC and FF decreased to 0 | [55] |
AZO | Impermeable | Ambient air (at 22 °C, 60%RH) for 150 h | VOC increased from 0.84 to 0.95, and FF decreased from 60% to 50% | ||
SnOx | PCBM | Roughness of 8.32 nm; RS of 64 Ω | Ambient air (at 25 °C, 85%RH) for 600 h | Normalized PCE decreased to 0.77 | [58] |
APTS modified PCBM | Roughness of 4.29 nm; RS of 46 Ω | Ambient air (at 25 °C, 85%RH) for 600 h | Normalized PCE decreased to 0.9 | ||
SnOx | C60 | Large SnOx gains and lower atomic concentrations of Sn and C | Operated in ambient air (at 60 °C, 30%RH) under 0.77 sun illumination at 60 °C for 250 h; Heated at 85 °C in N2 atmosphere for 700 h | Normalized Avg. PMAX decreased to 0.585, Normalized Avg. VOC decreased to 0.231; Normalized PCE decreased to 0 | [62] |
PEIE | Small SnOx gains and higher atomic concentrations of Sn and C | Operated in ambient air (at 60 °C, 30%RH) under 0.77 sun illumination at 60 °C for 250 h; Heated at 85 °C in N2 atmosphere for 670 h | Normalized Avg. PMAX decreased to 0.815, Normalized Avg. VOC decreased to 0.585; Normalized PCE decreased to 0.94 |
In addition to the perovskite field, the research on the ALD substrate is also carried out in other semiconductor fields, which have significant support for improving the performance of PSCs. Labbe et al. used TEM and spectroscopic ellipsometry (SE) to investigate the nucleation behavior of ALD FeOx[53]. During the ALD process, both substrate-enhanced and substrate-inhibited growth modes were observed. They found that layer-by-layer growth did not always occur in the linear growth regime after island coalescence[53]. Moreover, several studies have indicated that the island growth mode is unfavorable for achieving high-quality ALD films. Yun et al. noted that during island growth, the nucleation stage of the ALD process exhibited nonideal behavior, impeding layer-by-layer growth and resulting in delayed nucleation[63]. This behavior was attributed to a deficiency in reaction sites, necessitating additional incubation cycles for nucleus formation. They further explored the nucleation and growth behavior of AlN film on Si and TiN substrates by thermal ALD. The nucleation of AlN films was delayed on the Si substrates, while they grew without any nucleation delay on TiN substrates. The substrate-inhibited growth on Si surfaces was attributed to the scarcity of reactive sites, and ammonia (NH3) pretreatment on Si surfaces was applied to grow uniform AlN films[63]. Baji et al. observed that the island growth occurred on the unreactive substrate Si, while it grew layer-by-layer on the reactive substrate GaN during the ALD deposition of ZnO. The latter had a smoother film than the former[64], as shown in Figure 5C. Uğur et al. also reported that island growth of Al2O3 occurred when the reactant materials were deposited on unreactive substrates. They observed through TEM that ALD Al2O3 could not completely cover the hexagonal boron nitride (hBN) substrate because of an unreactive substrate[65]. Hagen et al. found that the ALD Cu processes varied significantly depending on the substrate materials employed. On Si and TaN surfaces, isolated island formation was observed[66]. Polymers are special substrate materials for ALD processes as well. Wilson showed that Al2O3 films deposited by ALD on various polymer substrates, including polystyrene (PS), polypropylene (PP), poly(methyl methacrylate) (PMMA), polyethylene (PE), and poly(vinyl chloride) (PVC). TMA first diffused into the polymer and then reacts with H2O on the substrate surface to form
THE APPLICATIONS OF ALD FOR ENHANCED PERFORMANCE IN PSCS
As shown in Figure 6, ALD enables the precise and conformal deposition of materials in various types of PSCs, including scalable, flexible and tandem solar cells. The efficiency of the PSCs always suffers from charge recombination loss because of defects in bulk or at interfaces[75-77]. Therefore, surface passivation strategy and interface engineering are needed to reduce the nonradiative recombination and enhance charge carrier transportation and collection. In some aspects, the ALD layer presents a viable approach to address these challenges, improving performance of various types of PSCs.
Figure 6. A scheme of the applications of ALD in different types of PSCs. (A) Perovskite material and encapsulation layer on flexible and scalable substrates. Reprinted with permission from ref.[78]. Copyright 2016 American Chemical Society. (B) Charge extractor and diffusion barrier in all-perovskite tandem solar modules. Reprinted with permission from ref.[80]. Copyright 2022 The American Association for the Advancement of Science. (C) Recombination layer in flexible all-perovskite tandem solar cells. Reprinted with permission from ref.[60]. Copyright 2019 Elsevier.
ALD enables preparation at a low temperature, making it particularly suitable for PSC fabrication. Based on the discussion of the precursor and deposition temperature section, it is known that organic-inorganic hybrid perovskites are nature-sensitive with precursors and deposition temperatures. Zhao et al. also found that perovskite degraded when the deposition temperature was higher than 125 °C and chose 75 °C as the best deposition temperature to grow Al2O3[21]. Then, ALD Al2O3 deposited at 75 °C was used to sufficiently passivate defect states at the surface of perovskite. After interface passivation via ten cycles of the ALD Al2O3 layer, the efficiency of the device enhanced from 18.8% to 20.0%. The ALD Al2O3-based devices can maintain more than 95% of their initial efficiency after being stored in the N2 atmosphere for 150 days[21]. ALD is also a potential technology for fabricating the flexible, compatible, and scalable films. On different substrates (polymers, metals, metal sulfides, and oxides), PbI2 films were first prepared through ALD processes with the deposition temperatures below 90 °C using Pb(btsa)2 and SnI4 as precursors. Moreover, ALD Al2O3 was used as an encapsulation layer which effectively protected the underlying PbI2 film[78].
High-performance flexible PSCs need transparent electrodes with low fabrication temperature and reduced charge recombination losses. ALD layers could meet these requirements. Jin et al. have proposed a flexible electrode structure, silver nanowires (AgNWs)/ZnO/ALD TiO2 with excellent transparency and electrical and mechanical characteristics[28]. The ALD TiO2 layer was applied to effectively passivate the charge recombination defects on the ZnO layer and protect the perovskite layer from decomposition. The power conversion efficiency (PCE) of this flexible PSC reaches 17.11%, comparable to that of 18.26% of rigid devices. Finally, it maintained 77% of initial PCE after 2,000 bending cycles with a radius of 6 mm[28]. Because of the inferior gas barrier properties of plastic substrates, flexible devices often suffer from intrinsic problems of poor stability under ambient environments. Lin et al. investigated the stability of flexible PSCs under illumination for polyisobutylene (PIB)-, 1H,1H,2H,2H-perfluorooctyltriethoxysilane (PFOTES)/ZnO-, and ALD Al2O3-based polyethylene naphthalate/indium tin oxide (PEN/ITO) substrates[79]. Due to the compact and uniform ALD films, ALD Al2O3-based devices showed the best T80 (Normalized PCE of 0.8) value (increased from 80 h to over 350 h) under maximum power point (MPP) tracking under 1 sun illumination in ambient conditions [60%-70% relative humidity (RH)][79].
ALD layers always act as diffusion barriers, buffer layers, and recombination layers in tandem solar cells. Traditionally, all-perovskite tandem solar cells require several spin-coating steps, which limited the device area. For large areas, ALD is a scalable preparation technique to fabricate large area functional layers due to its good expandability. To overcome the problem of reaction between interfacial halide and metal electrode, Xiao et al. introduced a thin conformal diffusion barrier (CDB) consisting of 10 nm ALD SnO2 to an all-perovskite tandem module[80]. The CDB layer could extract vertical electrons and serve as the lateral diffusion barrier between interconnecting subcells. The ITO/ALD SnO2/Ag junction showed good ohmic contact, demonstrating that the CDB layer supported effective electrical interconnection between two subcells. Finally, they achieved a certified PCE of 21.7% with aperture area of 20.25 cm2, and the modules with CDB maintained 75% of their initial efficiency for 500 h upon MPP tracking under 1 sun illumination in ambient conditions while the modules without CDB decreased to less than 50% after 20 h[80]. Yu et al. have developed a new strategy to activate the unreactive PCBM substrate and deposit an impermeable ALD sputtering buffer SnOxlayer[22]. For allowing the near-infrared light to pass through and be absorbed in the bottom subcell, tandem solar cells need the top subcell to be optical transmission; the dense ALD films are vital for the perovskite/silicon tandem solar cells when preparing transparent conductive oxides (TCOs) and avoid damage to the perovskite during sputtering. For demonstration, optimized ALD layers were employed as sputtering buffer layers in semi-transparent (ST) devices. As a result, the ratio of working devices to both working and non-working devices of optimized ST devices was almost 100%, exhibiting the excellent anti-sputtering ability[22]. As for all-perovskite tandem solar cells, the ideal recombination layer could enable voltage addition and optical loss reduction between the subcells. Palmstrom et al. introduced a modified structure with a ALD layer (C60/PEIE/ALD AZO) to enhance the composite between low bandgap and wide bandgap perovskite layers, reducing solvent degradation of the active layer during solution deposition[60]. Recently, ALD SnOx layers provided a promising solution to enhance carrier-selective contacts in tandem PSCs. Xiong et al. controlled the O:Sn ratio by varying the purge time of the oxygen source[81]. They found that the perovskite degraded apparently when the ratio increased, and the electrical properties became worse when the ratio decreased. By modifying the gradient compositions of the ALD SnOx layer, the charge extraction ability was enhanced. Finally, they achieved a PCE of 28.9% and retained 95% of its initial efficiency for 500 h upon MPP tracking under AM 1.5G illumination for a 1.0 cm2 monolithic perovskite/silicon tandem solar cell[81].
Stability issues in moisture, oxygen, and light exposure are key challenges for PSCs. As shown in Table 4, ALD could act as encapsulation barriers against external environmental factors, thereby improving the long-term stability of PSCs. As for p-i-n structure PSCs, Brinkmann et al. prepared 20 nm ALD SnOx with water vapor transmittance as low as 7 × 10-5 g m2 d-1, showing the excellent water vapor barrier properties[55]. The ALD SnOx layer could prevent decomposition products from being expelled from perovskite. Under inert atmosphere, the unencapsulated perovskite underwent thermal decomposition, as observed by characteristic peaks of PbI2 [Figure 7A and B]. However, the ALD SnOx-based device effectively hindered the outer diffusion of the decomposition products, significantly improving the thermal stability of the PSCs [Figure 7C][55]. Li et al. used the modified ALD SnOxby ester groups of poly(ethylene-co-vinyl acetate) as a self-encapsulated interface, resulting in retaining 85% of the initial PCE after storage 85 °C with RH of 85% for over 800 h[82]. The choice of ALD materials is essential for the long-term stability level of PSCs. Recently, Zheng et al. systematically investigated the long-term stability and the underlying decomposition mechanisms of ALD SnOx-based PSCs[83]. It was found that ALD SnOx-based PSCs exhibited higher susceptibility to degradation, surpassing even the degradation levels observed with bathocuproine (BCP) under humid conditions. It further revealed that the ALD SnOx layer triggered a phase transition in the perovskite when exposed to moisture, transitioning from the black cubic phase to the yellow δ phase despite the presence of a thin layer of fullerene between the SnOx and the perovskite. Instead of SnOx, ALD AlOx layers emerged as a transformative strategy, sufficiently bolstering the humidity and thermal stability of the cells without affecting device efficiency. The optimized ALD AlOx PSCs exhibited a PCE of 24.61% and maintained 88% of its initial efficiency after MPP tracking under 1 sun illumination for 1,350 h at 65°C in ambient air[83]. As for n-i-p PSCs, ALD V2O5-x deposited on the top of a Spiro-OMeTAD layer was utilized to block the moisture and oxygen, enhancing the stability by preserving the photovoltaic α-FAPbI3 phase and eliminating the leakage of both Li ions from the intermediate layer and Au ions from the electrode
Figure 7. (A and B) XRD analysis of PSC with AZO and AZO/SnOx before and after being heated in N2 atmosphere for six days. (C) Thermal stability test (N2 atmosphere at 60 °C). Reprinted with permission from ref.[55]. Copyright 2017 Nature Publishing Group. (D) Performance and structure of ALD V2O5-x based-PSC. (E) Ambient stability test (20%RH at 24 °C). (F) Operated stability test under AM
Recent studies on improving the stability of perovskite devices by ALD
Buffer layer | Architecture | Efficiency | Storage condition | Stability of devices | Ref. |
BCP | ITO/NiOx/PTAA/Al2O3/FAMACs/PCBM/BCP/Ag | N/A | Under UV light (365 nm) in air for 20 days; N2 atmosphere (at | A strong diffraction peak of PbI2 was detected, and the color of the film faded from dark brown to yellow; Normalized PCE decreased to 0.70; Normalized PCE decreased to 0.73; Normalized PCE decreased to 0.22 | [82] |
ALD SnOx | ITO/NiOx/PTAA/Al2O3/FAMACs/PCBM/ALD SnOx/Ag | 21.10% | Under UV light (365 nm) in air for 40 days; N2 atmosphere (at | A strong diffraction peak of PbI2 was detected, and the color of the film faded from dark brown to yellow; Normalized PCE decreased to 0.82; Normalized PCE decreased to 0.85; Normalized PCE decreased to 0.38 | |
Modified-ALD SnOx | ITO/NiOx/PTAA/Al2O3/FAMACs/PCBM:EVA/ ALD SnOx/Ag | 22.06% | Under UV light (365 nm) in air for 40 days; N2 atmosphere (at | A slight diffraction peak of PbI2 was detected, and the color of the film showed no big change; Normalized PCE decreased to 0.90; Normalized PCE decreased to 0.92; Normalized PCE decreased to 0.85 | |
BCP | FTO/NiOx/Me-4PACz/perovskite/C60/BCP/Cu | 24.29% | N2 atmosphere (85%RH) for 10 h; MPP tracking at 85 °C in ambient air for 15 h; 85%RH at 85 °C for 150 h; Operated under 1 sun illumination in ambient air (30%~50%RH at 65 °C) for | Normalized PCE decreased to 0.65; Normalized PCE decreased to 0.61; Normalized PCE decreased to 0.78; Normalized PCE decreased to 0.90 | [83] |
ALD SnOx | FTO/NiOx/Me-4PACz/perovskite/C60/ALD SnOx/Cu | 24.42% | N2 atmosphere (85%RH) for 10 h; MPP tracking at 85 °C in ambient air for 15 h; 85%RH at 85 °C for 150 h; Operated under 1 sun illumination in ambient air (30%~50%RH at 65 °C) for 140 h | Normalized PCE decreased to 0.45; Normalized PCE decreased to 0.85; Normalized PCE decreased to 0.80; Normalized PCE decreased to 0.90; | |
ALD AlOx | FTO/NiOx/Me-4PACz/perovskite/C60/ALD AlOx /Cu | 24.61% | N2 atmosphere (85%RH) for 10 h; MPP tracking at 85 °C in ambient air for 15 h; 85%RH at 85 °C for 150 h; Operated under 1 sun illumination in ambient air (30%~50%RH at 65 °C) for | Normalized PCE decreased to 0.80; Normalized PCE decreased to 0.97; Normalized PCE decreased to 0.90; Normalized PCE decreased to 0.90 | |
Spiro-OMeTAD | FTO/ ALD SnO2/perovskite/Spiro-OMeTAD/ALD V2O5-x/Au | 23.15% | Ambient air (at 24 °C, 20%RH) for 576 h; Operated under continuous AM 1.5G light illumination and a constant bias of | Normalized PCE decreased to 0.318; Normalized PCE decreased to 0.712 | [84] |
ALD V2O5-x | FTO/ ALD SnO2/perovskite/Spiro-OMeTAD/ALD V2O5-x/Au | 23.02% | Ambient air (at 24 °C, 20%RH) for 576 h; Operated under continuous AM 1.5G light illumination and a constant bias of | Normalized PCE decreased to 0.905; Normalized PCE decreased to 0.949 | |
Spiro-OMeTAD | F:SnO2/SnO2/perovskite/Spiro-OMeTAD/Au | 19.1% | Ambient air for 300 days | Normalized PCE decreased to 0.38 | [85] |
ALD Al2O3 | F:SnO2/SnO2/perovskite/Spiro-OMeTAD/ALD Al2O3/Au | 19.4% | Ambient conditions for 300 days | Normalized PCE decreased to 0.84 | |
Spiro-OMeTAD | FTO/ALD SnO2/SnO2 NPs/perovskite/Spiro-OMeTAD/Au | 21.29% | Operated under continuous AM 1.5G light illumination and a constant bias of 0.85 V without a UV cutoff filter for 120 h | Normalized PCE decreased to 0.832 | [86] |
ALD TiO2 | FTO/ALD SnO2/SnO2 NPs/perovskite/Spiro-OMeTAD/ALD TiO2/Au | 20.68% | Operated under continuous AM 1.5G light illumination and a constant bias of 0.85 V without a UV cutoff filter for 120 h | Normalized PCE decreased to 0.965 |
CONCLUSION AND OUTLOOK
This paper reviews the influences of atomic layer precursors, deposition temperatures and reaction substrates on the physical and chemical properties of ALD films and the performance of PSCs. For the precursor, some metal sources may damage the substrate (such as perovskite, carrier transport layer, etc.). The physical properties (such as density, permeability, and resistivity) of the films prepared with different oxygen sources may change. Moreover, oxygen sources may also influence the device performance of PSCs, especially on FF. The deposition temperature also influences the characteristics of ALD films and the performance of ALD devices. The optimal deposition temperature can be obtained by testing the band gap, resistivity and absorptivity of the films prepared at different temperatures. The ALD substrate is also a crucial factor in the process of ALD. In the field of non-perovskite, there have been many studies on the substrate-inhibited island growth mode of ALD film. However, in perovskite, the reaction mechanism of ALD on different substrates is unclear, and most relevant studies are related to the stability of ALD perovskite devices prepared on various substrates and the water vapor barrier ability of ALD films.
At present, ALD is increasingly used in the carrier transport and encapsulation layers of PSCs. Therefore, this paper summarizes the influential factors (Especially for the reaction substrates) that need attention in preparing ALD films for PSCs, along with related solutions, which are conducive to the efficient and large-scale fabrication of PSCs and the related tandem cells.
Several challenges associated with ALD processing in perovskites need to be addressed:
Precursor selection and compatibility
Precursor selection is influenced by various factors, including chemical stability, vapor pressure, and reactivity. In the context of perovskite ALD, the choice of precursors must strike a delicate balance between providing the desired chemical composition and ensuring compatibility with the substrate material. For instance, while highly reactive precursors may offer enhanced film growth rates, they may also pose challenges in terms of substrate damage or film quality degradation due to uncontrolled reactions at the substrate surface. The compatibility between precursors and substrates encompasses several aspects, including adsorption kinetics, surface diffusion, and reaction kinetics. A precursor that exhibits favorable interactions with the substrate surface, such as strong adsorption and controlled surface diffusion, is more likely to result in uniform film growth. Conversely, mismatches in precursor-substrate compatibility can lead to non-uniform film coverage, defects, and reduced film quality. More experimental characterizations and computational models are needed to provide deeper insights into precursor-substrate interactions, guiding the optimization of ALD processes for diverse applications in PCSs.
Interfacial engineering
ALD enables the deposition of ultrathin, conformal layers with atomic-level precision, making it well-suited for interface engineering applications. It also offers opportunities for interface modification at the interface between the charge transport layers and electrodes. By depositing thin interfacial layers to promote adhesion, reduce interfacial resistance, and enhance charge collection efficiency, ALD can improve the overall device performance and stability. Achieving precise control over interfacial properties, such as energy level alignment and interface roughness, is essential for maximizing device efficiency and stability.
Film uniformity
Achieving uniform deposition of functional layers using ALD across large-area substrates is crucial for scalability. Addressing issues such as precursor diffusion, surface coverage, and reaction kinetics to ensure uniform film deposition is essential.
Scalability and cost
Scaling up ALD processes for PSC production requires the development of high-throughput deposition methods compatible with large-area substrates. Addressing challenges related to deposition rate, precursor utilization, and equipment scalability is essential for transitioning ALD from laboratory-scale research to industrial-scale production. Cost-effective deposition techniques are necessary for the commercialization of PSCs. Optimizing ALD processes to minimize precursor consumption, reduce deposition time, and increase equipment efficiency can help lower production costs and make PSCs more competitive with traditional silicon-based photovoltaics.
DECLARATIONS
Authors’ contributions
Proposed the topic of this mini review: Yu B, Yang Y
Performed literature survey: Yu B, Zhang J
Prepared the manuscript: Yu B, Zhang J
Collectively discussed and revised the manuscript: Yang Y, Yu D
Review, conceptualization, and supervision: Mai Y, Chen X
Availability of data and materials
Not applicable.
Financial support and sponsorship
This work was supported by Grant named the “One-Hundred Young Talents” of Guangdong University of Technology (No. 263113845).
Conflicts of interest
All authors declared that there are no conflicts of interest.
Ethical approval and consent to participate
Not applicable.
Consent for publication
Not applicable.
Copyright
© The Author(s) 2024.
REFERENCES
2. Santinacci L. Atomic layer deposition: an efficient tool for corrosion protection. Curr Opin Colloid Interface Sci 2023;63:101674.
3. O’Neill BJ, Jackson DHK, Lee J, et al. Catalyst design with atomic layer deposition. ACS Catal 2015;5:1804-25.
4. Bakke JR, Pickrahn KL, Brennan TP, Bent SF. Nanoengineering and interfacial engineering of photovoltaics by atomic layer deposition. Nanoscale 2011;3:3482-508.
5. Hossain MA, Khoo KT, Cui X, et al. Atomic layer deposition enabling higher efficiency solar cells: a review. Nano Mater Sci 2020;2:204-26.
6. Raiford JA, Oyakhire ST, Bent SF. Applications of atomic layer deposition and chemical vapor deposition for perovskite solar cells. Energy Environ Sci 2020;13:1997-2023.
7. Xing Z, Xiao J, Hu T, et al. Atomic layer deposition of metal oxides in perovskite solar cells: present and future. Small Methods 2020;4:2000588.
8. Sinha S, Nandi DK, Pawar PS, Kim SH, Heo J. A review on atomic layer deposited buffer layers for Cu(In,Ga)Se2(CIGS) thin film solar cells: past, present, and future. Solar Energy 2020;209:515-37.
9. Eperon GE, Stranks SD, Menelaou C, Johnston MB, Herz LM, Snaith HJ. Formamidinium lead trihalide: a broadly tunable perovskite for efficient planar heterojunction solar cells. Energy Environ Sci 2014;7:982.
10. De Wolf S, Holovsky J, Moon SJ, et al. Organometallic halide perovskites: sharp optical absorption edge and its relation to photovoltaic performance. J Phys Chem Lett 2014;5:1035-9.
11. Saliba M, Matsui T, Domanski K, et al. Incorporation of rubidium cations into perovskite solar cells improves photovoltaic performance. Science 2016;354:206-9.
13. Yang Y, Luo Y, Ma S, Zhu C, Zhu L, Guo X. Advances of electron transport materials in perovskite solar cells: synthesis and application. Prog Chem 2021;33:281-302.
14. Lobe S, Bauer A, Uhlenbruck S, Fattakhova-Rohlfing D. Physical vapor deposition in solid-state battery development: from materials to devices. Adv Sci 2021;8:e2002044.
15. Wang M, Carmalt CJ. Film fabrication of perovskites and their derivatives for photovoltaic applications via chemical vapor deposition. ACS Appl Energy Mater 2022;5:5434-48.
16. Brinkmann KO, Gahlmann T, Riedl T. Atomic layer deposition of functional layers in planar perovskite solar cells. Solar RRL 2020;4:1900332.
17. Gordon RG, Hausmann D, Kim E, Shepard J. A kinetic model for step coverage by atomic layer deposition in narrow holes or trenches. Chem Vap Depos 2003;9:73-8.
18. Puurunen RL. Surface chemistry of atomic layer deposition: a case study for the trimethylaluminum/water process. J Appl Phys 2005;97:121301.
19. Putkonen M, Niinistö L. Organometallic precursors for atomic layer deposition. In: Precursor chemistry of advanced materials, Fischer RA, editor. Berlin: Springer; 2005. pp. 125-45.
20. Richey NE, de Paula C, Bent SF. Understanding chemical and physical mechanisms in atomic layer deposition. J Chem Phys 2020;152:040902.
21. Zhao R, Zhang K, Zhu J, et al. Surface passivation of organometal halide perovskites by atomic layer deposition: an investigation of the mechanism of efficient inverted planar solar cells. Nanoscale Adv 2021;3:2305-15.
22. Yu B, Tang F, Yang Y, et al. Impermeable atomic layer deposition for sputtering buffer layer in efficient semi-transparent and tandem solar cells via activating unreactive substrate. Adv Mater 2023;35:e2202447.
23. Zhang Y, Yang Y, Mbumba MT, et al. Research progress of buffer layer and encapsulation layer prepared by atomic layer deposition to improve the stability of perovskite solar cells. Solar RRL 2022;6:2200823.
24. Lee KM, Chang SH, Wang KH, et al. Thickness effects of ZnO thin film on the performance of tri-iodide perovskite absorber based photovoltaics. Solar Energy 2015;120:117-22.
25. Matsui T, Bivour M, Hermle M, Sai H. Atomic-layer-deposited TiOx nanolayers function as efficient hole-selective passivating contacts in silicon solar cells. ACS Appl Mater Interfaces 2020;12:49777-85.
26. Correa Baena JP, Steier L, Tress W, et al. Highly efficient planar perovskite solar cells through band alignment engineering. Energy Environ Sci 2015;8:2928-34.
27. Zardetto V, di Giacomo F, Lifka H, et al. Surface fluorination of ALD TiO2 electron transport layer for efficient planar perovskite solar cells. Adv Mater Inter 2018;5:1701456.
28. Jin TY, Li W, Li YQ, et al. High-performance flexible perovskite solar cells enabled by low-temperature ALD-assisted surface passivation. Adv Opt Mater 2018;6:1801153.
29. Choudhury D, Rajaraman G, Sarkar SK. Self limiting atomic layer deposition of Al2O3 on perovskite surfaces: a reality? Nanoscale 2016;8:7459-65.
30. Kuang Y, Zardetto V, van Gils R, et al. Low-temperature plasma-assisted atomic-layer-deposited SnO2 as an electron transport layer in planar perovskite solar cells. ACS Appl Mater Interfaces 2018;10:30367-78.
31. Lee Y, Lee S, Seo G, et al. Efficient planar perovskite solar cells using passivated tin oxide as an electron transport layer. Adv Sci 2018;5:1800130.
32. Hu T, Becker T, Pourdavoud N, et al. Indium-free perovskite solar cells enabled by impermeable tin-oxide electron extraction layers. Adv Mater 2017;29:1606656.
33. Ren N, Zhu C, Li R, et al. 50 °C low-temperature ALD SnO2 driven by H2O2 for efficient perovskite and perovskite/silicon tandem solar cells. Appl Phys Lett 2022;121:033502.
34. Hultqvist A, Aitola K, Sveinbjörnsson K, et al. Atomic layer deposition of electron selective SnOx and ZnO films on mixed halide perovskite: compatibility and performance. ACS Appl Mater Interfaces 2017;9:29707-16.
35. Zardetto V, Williams BL, Perrotta A, et al. Atomic layer deposition for perovskite solar cells: research status, opportunities and challenges. Sustain Energy Fuels 2017;1:30-55.
36. Kruszyńska J, Ostapko J, Ozkaya V, et al. Atomic layer engineering of aluminum-doped zinc oxide films for efficient and stable perovskite solar cells. Adv Mater Inter 2022;9:2200575.
37. Behrendt A, Friedenberger C, Gahlmann T, et al. Highly robust transparent and conductive gas diffusion barriers based on tin oxide. Adv Mater 2015;27:5961-7.
38. Wang H, Liu Y, Liu H, et al. Effect of various oxidants on reaction mechanisms, self-limiting natures and structural characteristics of Al2O3 films grown by atomic layer deposition. Adv Mater Inter 2018;5:1701248.
39. Lee SU, Park H, Shin H, Park NG. Atomic layer deposition of SnO2 using hydrogen peroxide improves the efficiency and stability of perovskite solar cells. Nanoscale 2023;15:5044-52.
40. Kim H. Characteristics and applications of plasma enhanced-atomic layer deposition. Thin Solid Films 2011;519:6639-44.
41. Kim H. Atomic layer deposition of metal and nitride thin films: current research efforts and applications for semiconductor device processing. J Vac Sci Technol B 2003;21:2231-61.
42. Johnson RW, Hultqvist A, Bent SF. A brief review of atomic layer deposition: from fundamentals to applications. Mater Today 2014;17:236-46.
43. Potts SE, Keuning W, Langereis E, Dingemans G, van de Sanden MCM, Kessels WMM. Low temperature plasma-enhanced atomic layer deposition of metal oxide thin films. J Electrochem Soc 2010;157:P66.
44. Muñoz-Rojas D, Macmanus-Driscoll J. Spatial atmospheric atomic layer deposition: a new laboratory and industrial tool for low-cost photovoltaics. Mater Horiz 2014;1:314-20.
45. Poodt P, Knaapen R, Illiberi A, Roozeboom F, van Asten A. Low temperature and roll-to-roll spatial atomic layer deposition for flexible electronics. J Vac Sci Technol A 2012;30:01A142.
46. Illiberi A, Roozeboom F, Poodt P. Spatial atomic layer deposition of zinc oxide thin films. ACS Appl Mater Interfaces 2012;4:268-72.
47. Lindahl J, Hägglund C, Wätjen JT, Edoff M, Törndahl T. The effect of substrate temperature on atomic layer deposited zinc tin oxide. Thin Solid Films 2015;586:82-7.
48. Chistiakova G, Mews M, Wilks RG, Bär M, Korte L. In-system photoelectron spectroscopy study of tin oxide layers produced from tetrakis(dimethylamino)tin by plasma enhanced atomic layer deposition. J Vac Sci Technol A 2018;36:02D401.
49. Köhnen E, Jošt M, Morales-Vilches AB, et al. Highly efficient monolithic perovskite silicon tandem solar cells: analyzing the influence of current mismatch on device performance. Sustain Energy Fuels 2019;3:1995-2005.
50. Hultqvist A, Jacobsson TJ, Svanström S, et al. SnOx atomic layer deposition on bare perovskite-an investigation of initial growth dynamics, interface chemistry, and solar cell performance. ACS Appl Energy Mater 2021;4:510-22.
51. Schulze TF, Korte L, Ruske F, Rech B. Band lineup in amorphous/crystalline silicon heterojunctions and the impact of hydrogen microstructure and topological disorder. Phys Rev B 2011;83:165314.
52. Puurunen RL, Vandervorst W. Island growth as a growth mode in atomic layer deposition: a phenomenological model. J Appl Phys 2004;96:7686-95.
53. Labbe M, Cadien K, Ivey DG. Growth of multiple island layers during iron oxide atomic layer deposition: an electron microscopy and spectroscopic ellipsometry investigation. J Phys Chem C 2022;126:19883-94.
55. Brinkmann KO, Zhao J, Pourdavoud N, et al. Suppressed decomposition of organometal halide perovskites by impermeable electron-extraction layers in inverted solar cells. Nat Commun 2017;8:13938.
56. Yu X, Yan H, Peng Q. Improve the stability of hybrid halide perovskite via atomic layer deposition on activated phenyl-C61 butyric acid methyl ester. ACS Appl Mater Interfaces 2018;10:28948-54.
57. Gong J, Adnani M, Jones BT, et al. Nanoscale encapsulation of hybrid perovskites using hybrid atomic layer deposition. J Phys Chem Lett 2022;13:4082-9.
58. Wang W, Yang Z, Ding J, Kong J, Li X. Improving water-resistance of inverted flexible perovskite solar cells via tailoring the top electron-selective layers. Solar Energy Mater Solar Cells 2022;238:111609.
59. Liu J, Wu Y, Zhao Z, et al. Reducing damage of sputtering and improving conductivity of transparent electrodes for efficient semi-transparent perovskite solar cells. J Phys D Appl Phys 2023;56:365101.
60. Palmstrom AF, Eperon GE, Leijtens T, et al. Enabling flexible all-perovskite tandem solar cells. Joule 2019;3:2193-204.
61. Li W, Xu YX, Wang D, Chen F, Chen ZK. Inorganic perovskite light emitting diodes with ZnO as the electron transport layer by direct atomic layer deposition. Org Electron 2018;57:60-7.
62. Raiford JA, Boyd CC, Palmstrom AF, et al. Enhanced nucleation of atomic layer deposited contacts improves operational stability of perovskite solar cells in air. Adv Energy Mater 2019;9:1902353.
63. Yun HJ, Kim H, Choi BJ. Nucleation and growth behavior of aluminum nitride film using thermal atomic layer deposition. Ceram Int 2020;46:13372-6.
64. Baji Z, Lábadi Z, Horváth ZE, et al. Nucleation and growth modes of ALD ZnO. Cryst Growth Des 2012;12:5615-20.
65. Uğur A, Savacı U, Ay N, Turan S. Growth of ultrathin Al2O3 islands on hBN particles by atomic layer deposition in a custom fluidized bed reactor using Al(CH3) 3 and H2O. Appl Surf Sci 2021;537:147665.
66. Hagen DJ, Connolly J, Povey IM, Rushworth S, Pemble ME. Island coalescence during film growth: an underestimated limitation of Cu ALD. Adv Mater Inter 2017;4:1700274.
67. Wilson CA, Grubbs RK, George SM. Nucleation and growth during Al2O3 atomic layer deposition on polymers. Chem Mater 2005;17:5625-34.
68. Jur JS, Spagnola JC, Lee K, Gong B, Peng Q, Parsons GN. Temperature-dependent subsurface growth during atomic layer deposition on polypropylene and cellulose fibers. Langmuir 2010;26:8239-44.
69. Demelius L, Blatnik M, Unger K, Parlanti P, Gemmi M, Coclite AM. Shedding light on the initial growth of ZnO during plasma-enhanced atomic layer deposition on vapor-deposited polymer thin films. Appl Surf Sci 2022;604:154619.
70. Weiß A, Goldmann J, Kettunen S, et al. Conversion of ALD CuO thin films into transparent conductive p-type CuI thin films. Adv Mater Inter 2023;10:2201860.
71. Zhou J, Huang Q, Zhao Q, et al. Performance promotion of aluminum oxide capping layer through interface engineering for tunnel oxide passivating contacts. Solar Energy Mater Solar Cells 2022;245:111865.
72. Hagedorn S, Knauer A, Weyers M, Naumann F, Gargouri H. AlN and AlN/Al2O3 seed layers from atomic layer deposition for epitaxial growth of AlN on sapphire. J Vac Sci Technol A 2019;37:020914.
73. Lin G, Zhao MQ, Jia M, et al. Performance enhancement of monolayer MoS2 transistors by atomic layer deposition of high- k dielectric assisted by Al2O3 seed layer. J Phys D Appl Phys 2020;53:105103.
74. Yang H, Xiang D, Mao H, et al. Native oxide seeded spontaneous integration of dielectrics on exfoliated black phosphorus. ACS Appl Mater Interfaces 2020;12:24411-8.
75. Wolff CM, Caprioglio P, Stolterfoht M, Neher D. Nonradiative recombination in perovskite solar cells: the role of interfaces. Adv Mater 2019;31:e1902762.
76. Xia J, Sohail M, Nazeeruddin MK. Efficient and stable perovskite solar cells by tailoring of interfaces. Adv Mater 2023;35:e2211324.
77. Zhao W, Duan Y. Advanced applications of atomic layer deposition in perovskite-based solar cells. Adv Photonics Res 2021;2:2100011.
78. Popov G, Mattinen M, Hatanpää T, et al. Atomic layer deposition of PbI2 thin films. Chem Mater 2019;31:1101-9.
79. Lin J, He Y, Mo H, et al. Substrate modifications for stability improvements of flexible perovskite solar cells. Energy Technol 2024;12:2300958.
80. Xiao K, Lin YH, Zhang M, et al. Scalable processing for realizing 21.7%-efficient all-perovskite tandem solar modules. Science 2022;376:762-7.
81. Xiong Z, Wu L, Zhou X, et al. Constructing tin oxides interfacial layer with gradient compositions for efficient perovskite/silicon tandem solar cells with efficiency exceeding 28. Small 2024;20:e2308024.
82. Li J, Xing Z, Li D, et al. Suppressed ion migration in FA-rich perovskite photovoltaics through enhanced nucleation of encapsulation interface. Small 2024;20:e2305732.
83. Zheng Z, Xue Z, Zhao K, et al. Unveiling and overcoming instabilities in perovskite solar cells induced by atomic-layer-deposition tin oxide. Solar RRL 2024;8:2301076.
84. Park H, Jeong S, Kim E, Shin S, Shin H. Hole-transporting vanadium-containing oxide (V2O5-x) interlayers enhance stability of α-FAPbI3-based perovskite solar cells (~23%). ACS Appl Mater Interfaces 2022;14:42007-17.
85. Singh R, Ghosh S, Subbiah AS, Mahuli N, Sarkar SK. ALD Al2O3 on hybrid perovskite solar cells: unveiling the growth mechanism and long-term stability. Solar Energy Mater Solar Cells 2020;205:110289.
Cite This Article
Export citation file: BibTeX | RIS
OAE Style
Yu B, Zhang J, Yang Y, Yu D, Mai Y, Chen X. Influences of deposition conditions on atomic layer deposition films for enhanced performance in perovskite solar cells. Energy Mater 2024;4:400045. http://dx.doi.org/10.20517/energymater.2023.150
AMA Style
Yu B, Zhang J, Yang Y, Yu D, Mai Y, Chen X. Influences of deposition conditions on atomic layer deposition films for enhanced performance in perovskite solar cells. Energy Materials. 2024; 4(4): 400045. http://dx.doi.org/10.20517/energymater.2023.150
Chicago/Turabian Style
Bohao Yu, Jiawen Zhang, Yuzhao Yang, Dingshan Yu, Yaohua Mai, Xudong Chen. 2024. "Influences of deposition conditions on atomic layer deposition films for enhanced performance in perovskite solar cells" Energy Materials. 4, no.4: 400045. http://dx.doi.org/10.20517/energymater.2023.150
ACS Style
Yu, B.; Zhang J.; Yang Y.; Yu D.; Mai Y.; Chen X. Influences of deposition conditions on atomic layer deposition films for enhanced performance in perovskite solar cells. Energy Mater. 2024, 4, 400045. http://dx.doi.org/10.20517/energymater.2023.150
About This Article
Copyright
Data & Comments
Data
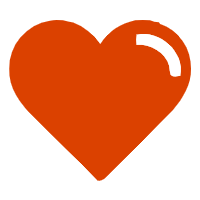

Comments
Comments must be written in English. Spam, offensive content, impersonation, and private information will not be permitted. If any comment is reported and identified as inappropriate content by OAE staff, the comment will be removed without notice. If you have any queries or need any help, please contact us at support@oaepublish.com.